MOOG T161
Datasheet
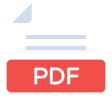
MOOG-T161-Series-Digital-Motion-Control-for-Brushless-Motors-datasheet1-1939550258.pdf
311 KiB
Extracted Text
Digital Motion Control
for Brushless Motors
T 161 and T 164 Series
Introduction
Leading Edge Technology MOOG brushless servo drives are In addition, multi-axis power
Guarantees Succes specifically designed to meet the supplies together with all the
requirements of the modern pro- necessary accessories (ventilation
Modern industrial production is duction environment. units, heat-sinks, cables, etc.)
characterised by continuing de- The combination of compact, high completes the package for every
velopment in production auto- performance servomotors with application.
mation. This development is vital in advanced digital servo controllers
ensuring the production process results in the optimum price/ This catalogue contains information
remains efficient and economical in performance solution for your on the MOOG range of servo-
a fast changing world. Servo drives application. amplifiers, powersupplies and
play a critical role in the develop- interface cards. The servoamplifiers
ment of automation systems. Mo- The product range comprises ser- are available in two package
dern servo drives must provide high vomotors of different dimensions variants and in various different
performance solutions to improve with matched servo controllers for power ranges. Interface cards are
production effiency while keeping the commutation and control of available for the Siemens Simatic S5
costs at a minimum. the motors. and PC host control systems.
164 Series
Panel mounting box
Package form
±10 V; CAN (Option)
Demand signal
325
DC Bus Voltage [V]
7 to 80
Continuous Current [A ]*
s
14 to 200
Peak Current [A ]*
s
*All current values are peak of sine. A = √2A
s eff
Components of a MOOG Servo Drive System
MOOG Other MOOG Controllers
Matching Power
Transformer Supply
L 1
325 V DC
L 2
N S
230 V AC
L 3
Bleed Resistor
PE
Command
Resolver
Signal
MOOG
MOOG
Controller
Brushless Servomotor
Our quality system is certified to ISO This catalogue is intended for purpose and meet all required
9001 suitably qualified personnel only. safety regulations. Please consult
The user is responsible to ensure the factory if in doubt.
that the components described
herein are fit for their intended
2
T 161 and T 164 Series
Introduction
Typical Applications
• Robots
• Handling Systems
• Transfer Lines
• Textile Machines
• Packaging Machines
• Plastic Machines
• Paper and Woodworking
• Flying Shears and Saws
• Punching and Stumping
Machines
MOOG Brushless Servomotors MOOG Digital Servoamplifiers
offer the following features: The performance advantage of
• Very compact dimensions MOOG Servomotors can be fully
• Low inertia for dynamic achieved using the latest generation
performance of digital servoamplifiers from
• Low weight MOOG.
• Reliable and robust
Setting Standards in Technology and Service
Advances in technology have led to sales and service coverage provided
an ever increasing use of digita- by MOOG Subsidiaries together
lisation. MOOG servodrives are no with a growing network of Sales
exception. Speed, winding tem- Partners.
perature and other physical
MOOG supplies complete
quantities are sampled periodically
Servodrive Systems
by a fast microprocessor and this
data is used to commutate, control
and protect the drive system. This
allows complex algorithms to be
realised which give better motor
performance and easy set-up.
Apart from the development and
manufacture of brushless Servo-
motors, MOOG also offers the
hardware and software compo-
nents necessary to implement
complete drive systems. MOOG
Customers benefit from world-wide
3
T 161 Series
Technical Data
Model T 161-901 T 161-902
Continuous Current [A ]* 3,5 / 6** 4,7 / 11**
S
Peak Current [A ]* 8 20
S
Continuous Power [kW]
Dimensions W x D x H [mm] 60,96 x 226,9 x 262,9 60,96 x 226,9 x 262,9
*All current values are peak of sine. A = √2A
s eff
The T161 Series tor performance. The T161 Series is
optimised for motors up to 2.5 kW.
consists of modules which are
plugged into a 19”rack contai- Encoder Simulation Option
ning a backplane. Up to 6 servo-
amplifiers may be plugged into An incremental position signal with
one rack. Each rack also requires a a programmable resolution of up to
T160 power supply which supplies 8192 lines per motor revolution is
high voltage DC and logic level generated from the resolver
voltages for up to 6 amplifiers. The position feedback. The incremental
servoamplifier features digital position is transmitted as differential
speed control, commutation and quadrature pulse outputs and a
fault monitoring. Analogue current differential marker pulse output
loops guarantee the highest pos- which may be set at any motor
sible bandwidth for dynamic mo- position.
User Interfaces
Analogue Inputs
±10 V Demand Input
0-10 V Torque Limit
Digital Inputs
Enable, Speed Limit
Speed / Torque Mode Select
Limit Switches
Analogue Outputs
Current Monitor
Speed Monitor
Digital Outputs
Thermal Limit
Drive Fault
System Ready
Encoder Simulation (Option)
Status Display
LED’s on the front panel show drive
status
Communication
RS232 / 485 Interface
CAN Bus (Option)
4
T 161 Series
Technical Data
T 161-903 T 161-904 T 160-901/2
6,5 / 15** 18** Power Supply
30 60
0,8/2,5** ( 1 x 230 V AC )
2,5/7,5** ( 3 x 230 V AC )
60,96 x 226,9 x 262,9 91,44 x 226,9 x 262,9 60,96 x 226,9 x 262,9
3
** Forced air cooling Q ‡35 m / h
CAN Interface Option no encoder feedback cables and no itself, allowing point to point 160 Power Supply
additional RS232/RS422 cables motions and electronic gearing
The use of a high speed CAN digital
required. between axes. Two versions of the 160 power
interface to replace the old ±10V
MOOG CAN drives offer two The functionality of MOOG CAN supply are available, one which
demand signal opens up the full
modes of operation. In both cases, drives allow cost effective and generates the logic voltage supply
potential of digital drive technology.
the position control loop is closed reliable system solutions to be from the main bus and one which
By integrating higher level motion
on the servodrive eliminating the quickly realised. uses a seperate 24 V DC input. The
control functions in the drive, the
need for a seperate position control The 19" rack plug-in system and latter version allows communication
advantages of distributed control
card. With the Interpolation Mode the parameter download over CAN with the drive to function even after
systems can be exploited in full.
version, the motion profile is allow fast and reliable exchange of removal of the high voltage supply.
Only a single twisted-pair cable is
generated on the host controller T161 drives in the field thereby
needed between the Host
allowing complex path control. reducing machine downtime.
Controller and the servodrives.
With the Profile Mode version, the
There are no analog control cables,
profile is generated on the drive
Block Diagram of the T 161 Digital Servo Controller
MOOG Motor
Power Stage Temperature
Power
DC-Bus-
Stage
Voltage
Motor Temperature
Thermistor
A/D-Converter
Velocity
Resolver
Setpoint
Digital I/0
I/0 Pulse Width
COMPUTER-
Unit Modulator
SYSTEM
Monitor
Outputs
Resolver Signal
Processing
Encoder
Commutation
Position
Simulation
Controller
Velocity Loop
Current
System Controller
Monitoring
Host
Digital
System
Interface
Position Controller
PC
Position D/A-Converter
Controller
Program- Digital Bus
mable I/0
Options
5
T 164 Series
Technical Data
Model T 164-901 T 164-903
Continuous Current [A ]* 7 14
S
Peak Current [A ]* 14 28
S
Continuous Power [kW]
Dimensions W x D x H [mm] 76 x 254 x 312 76 x 254 x 312
*All current values are peak of sine. A = √2A
s eff
The T164 Series series. In addition, a single-axis
position control card is available
features a panel mounting which plugs into the T164 servo-
construction and covers the amplifier. High power DC voltage is
complete range of MOOG motors supplied by the 150 Power Supply
up to 10 kW. Screw terminal which also features a ballast circuit
connectors allow easy system to absorb energy regenerated by
installation. A built-in fan is the motor. For large loads, an
included for optimum heat external ballast resistor, (up to
dissipation. The T164 series offers 2.5 kW continuous, 36 kW peak),
the same functionality and is available as an option.
expansion options as the T161
User Interfaces Digital Outputs
Thermal Limit
Analogue Input Drive Fault
±10 V Demand, switchable System Ready (Option)
between speed and torque control Encoder Simulation (Option)
Digital Inputs Status Display
Drive Enable LED's on the front panel show drive
Limit Switch Inputs (Option) status
Torque / Speed mode select
(Option) Communication
Automatic / Manual mode select RS 232 / 485 Interface
(Option) CAN-Bus (Option)
Analogue Outputs
Two programmable test points on
the front panel. e.g. to monitor
speed or current.
6
T 164 Series
Technical Data
T 164-905 T 164-907 T 164-909 T 150-901
28 56 80 Power Supply
56 112 200
5 ( 1 x 230 V AC )
15 ( 3 x 230 V AC )
76 x 254 x 312 127 x 254 x 312 127 x 254 x 312 76 x 254 x 312
CAN Interface Option Point Card Option wide variety of motion tasks to be
programmed. A program develop-
The CAN functionality described for Point is a complete single axis ment environment is provided and
the T161 Controller Series is also motion control card which plugs user programs may stored on the
available for the T164 Series. into the drive and allows the drive Point card in EEPROM.
to operate as a standalone motion An encoder input, high speed regis-
controller. The card also contains 9 tration input and a CAN interface
digital inputs, 5 digital outputs and are also available as options.
a serial interface.
A powerful motion control
language based on BASIC allows a
7
®
S5 SERVOLINK
®
Simatic S5 Interface
for Digital Servodrives
Description positioning card in the PLC. Up to
47 axes may be controlled from
The S5 ServoLink card from MOOG one PLC.
offers a high speed serial interface
between the Simatic S5 from The S5-ServoLink card is a standard
Siemens and the MOOG digital plug-in card for the 115U, 135U
servodrives. Using the high speed and 155U S5 PLC’s. The card
CAN interface to replace the ±10 V implements all the necessary
analogue demand signal opens up protocol to allow MOOG intelligent
the full potential of digital control. servodrives to be directly accessed
Integrating higher level motion from PLC programs using a library
control functions in the servodrive of Step 5 function blocks provided.
allows the advantages of distributed
control systems to be fully realised.
Highly synchronised motion control
is possible without any additional
Features:
•
Point to point motions • Up to 16 drives may be
•
Electronic gearing and camming controlled by one card, up to 3
functions cards in one PLC
•
Motion parameters freely pro- • Compatible with all S5-115U,
grammable from the S5 Program 135U and 155U PLC’s (a version
•
Servodrive data (position, status, for 95U and 100U is in prepara-
etc.) available to the PLC program tion)
Advantages
Intelligent servodrives networked via CAN bus have the following
advantages compared with servodrives having an analog speed interface:
k
•No extra position controller Reduced costs.
necessary. One S5 ServoLink card can
control up to 16 axes.
k
• Lower installation and wiring costs Less possibility of wiring errors.
using a serial bus.
k
• No more analog interfaces. No noise or drift problems.
k
• Status and diagnostic information Higher availability and easier to
available in the PLC. service.
k
• Step5 motion functions available. Easy to program.
k
• Modular decentralised concept. Simplifies testing and com-
missioning.
8
®
S5 SERVOLINK
®
Simatic S5 Interface
for Digital Servodrives
Details of Operation the PLC program calls the MOVE- other drives can be configured as control mode with a programmable
ABSOLUTE function block and sets slave axes. The relationship of the acceleration ramp or in torque
Generation of motion profiles, the required acceleration, max. slave position to the master is control mode with a programmable
transmission of data for electronic speed and target position. Actual defined by a table which is stored in maximum speed.
gearing and CAM functions and position and status information is each slave drive. This allows
position loop closure is performed sent every cycle from the servodrive electronic gearing or CAM
on the servo amplifier. The PLC to the PLC. This allows the PLC to functions to be programmed.
parameterises these functions using determine the position of the drive
the library of function blocks and when the motion profile has Gear ratios may be set on the
provided, (see example below). Pro- been completed. master and on each slave. The
gramming can be done either amplitude and offset of the CAM
directly in Instruction List or gra- To perform electronic gearing any table can be changed every CAM
phically using function plans and one axis can be configured as a cycle allowing very flexible systems
ladder logic. gearing master. This master axis will to be realised.
then broadcast its position on the
To perform a point to point move, CAN bus every 2 ms. Any of the The drives can also be run in speed
Example DJS1:
L KB 0 ;Check DRIVE_JOB_STATUS (D_J_S) A DB 201 ;Data block for drive 1
L MB 101 ;MB101 = D_J_S L DW 3 ;Load status word
Frequently asked questions
What makes Elite.Parts unique?

What kind of warranty will the T161 have?

Which carriers does Elite.Parts work with?

Will Elite.Parts sell to me even though I live outside the USA?

I have a preferred payment method. Will Elite.Parts accept it?

What they say about us
FANTASTIC RESOURCE
One of our top priorities is maintaining our business with precision, and we are constantly looking for affiliates that can help us achieve our goal. With the aid of GID Industrial, our obsolete product management has never been more efficient. They have been a great resource to our company, and have quickly become a go-to supplier on our list!
Bucher Emhart Glass
EXCELLENT SERVICE
With our strict fundamentals and high expectations, we were surprised when we came across GID Industrial and their competitive pricing. When we approached them with our issue, they were incredibly confident in being able to provide us with a seamless solution at the best price for us. GID Industrial quickly understood our needs and provided us with excellent service, as well as fully tested product to ensure what we received would be the right fit for our company.
Fuji
HARD TO FIND A BETTER PROVIDER
Our company provides services to aid in the manufacture of technological products, such as semiconductors and flat panel displays, and often searching for distributors of obsolete product we require can waste time and money. Finding GID Industrial proved to be a great asset to our company, with cost effective solutions and superior knowledge on all of their materials, it’d be hard to find a better provider of obsolete or hard to find products.
Applied Materials
CONSISTENTLY DELIVERS QUALITY SOLUTIONS
Over the years, the equipment used in our company becomes discontinued, but they’re still of great use to us and our customers. Once these products are no longer available through the manufacturer, finding a reliable, quick supplier is a necessity, and luckily for us, GID Industrial has provided the most trustworthy, quality solutions to our obsolete component needs.
Nidec Vamco
TERRIFIC RESOURCE
This company has been a terrific help to us (I work for Trican Well Service) in sourcing the Micron Ram Memory we needed for our Siemens computers. Great service! And great pricing! I know when the product is shipping and when it will arrive, all the way through the ordering process.
Trican Well Service
GO TO SOURCE
When I can't find an obsolete part, I first call GID and they'll come up with my parts every time. Great customer service and follow up as well. Scott emails me from time to time to touch base and see if we're having trouble finding something.....which is often with our 25 yr old equipment.
ConAgra Foods