WAGO 750-404/000-003
Specifications
Counter depth
32 Bit
Current consumption max.
75 mA at DC 5 V
Dimensions (mm)
W x H x L 12 x 64* x 100, from upper edge of 35 DIN rail
Input current typ.
5 mA
Internal bit width
32 bits data. 8 bits control /status
Isolation
500 V (System/Supply)
Number of counters
1
Number of outputs
2
Output current
0.5 A short-circuit-protected
Pulse width min.
10 µs
Signal voltage
(0): DC ñ3 V ... +5 V. (1): DC +15 V ... +30 V
Switching rate max.
100 kHz
Voltage via power jumper contacts
DC 24 V (-15 % ... + 20 %)
Weight
ca. 55 g
Datasheet
Extracted Text
Fieldbus Independent I/O Modules Counter Modules 750-404, (/xxx-xxx) Manual Version 1.1.2 ii General Copyright © 2006 by WAGO Kontakttechnik GmbH & Co. KG All rights reserved. WAGO Kontakttechnik GmbH & Co. KG Hansastraße 27 D-32423 Minden Phone: +49 (0) 571/8 87 0 Fax: +49 (0) 571/8 87 1 69 E-Mail: info@wago.com Web: http://www.wago.com Technical Support Phone: +49 (0) 571/8 87 5 55 Fax: +49 (0) 571/8 87 85 55 E-Mail: support@wago.com Every conceivable measure has been taken to ensure the correctness and com- pleteness of this documentation. However, as errors can never be fully ex- cluded, we would appreciate any information or ideas at any time. E-Mail: documentation@wago.com We wish to point out that the software and hardware terms as well as the trademarks of companies used and/or mentioned in the present manual are generally trademark or patent protected. WAGO-I/O-SYSTEM 750 I/O Modules Content iii Content 1 Important Comments .................................................................................5 1.1 Legal Principles........................................................................................5 1.1.1 Copyright.............................................................................................5 1.1.2 Personnel Qualification.......................................................................5 1.1.3 Intended Use........................................................................................5 1.2 Symbols....................................................................................................6 1.3 Number Notation......................................................................................6 1.4 Safety Notes.............................................................................................7 1.5 Scope........................................................................................................7 2 I/O Modules .................................................................................................8 2.1 Specialty Modules....................................................................................8 2.1.1 Overview Counter Modules 750-404, (/xxx-xxx) ...............................8 2.1.2 750-404 [Up/Down Counter /100 kHz]...............................................9 2.1.2.1 Variations........................................................................................9 2.1.2.2 View................................................................................................9 2.1.2.3 Description......................................................................................9 2.1.2.4 Display Elements..........................................................................11 2.1.2.5 Schematic Diagram.......................................................................11 2.1.2.6 Technical Data..............................................................................12 2.1.2.7 Process Image...............................................................................13 2.1.2.7.1 Control- / Status byte 750-404 .................................................14 2.1.2.7.2 Control- / Status byte 750-404/000-002...................................15 2.1.2.7.3 Control- / Status byte 750-404/000-004...................................16 2.1.2.8 Examples.......................................................................................17 2.1.2.8.1 750-404....................................................................................17 2.1.2.8.2 750-404/000-002......................................................................19 2.1.2.8.3 750-404/000-004......................................................................20 2.1.3 750-404/000-001 [Up Counter / Enable Input] ................................. 21 2.1.3.1 View..............................................................................................21 2.1.3.2 Description....................................................................................21 2.1.3.3 Display Elements..........................................................................22 2.1.3.4 Schematic Diagram.......................................................................23 2.1.3.5 Technical Data..............................................................................24 2.1.3.6 Process Image...............................................................................25 2.1.3.7 Example........................................................................................26 2.1.4 750-404/000-003 [Frequency Counter 0.1 Hz-100 kHz] ..................28 2.1.4.1 View..............................................................................................28 2.1.4.2 Description....................................................................................28 2.1.4.3 Display Elements..........................................................................30 2.1.4.4 Schematic Diagram.......................................................................30 2.1.4.5 Technical Data..............................................................................31 2.1.4.6 Functional Description..................................................................32 2.1.4.7 Process Image...............................................................................33 2.1.4.8 Example........................................................................................36 2.1.5 750-404/000-005 [2 Up Counter/16 Bit/5 kHz] ................................38 2.1.5.1 View..............................................................................................38 WAGO-I/O-SYSTEM 750 I/O Modules iv Content 2.1.5.2 Description....................................................................................38 2.1.5.3 Display Elements..........................................................................40 2.1.5.4 Schematic Diagram.......................................................................40 2.1.5.5 Technical Data..............................................................................41 2.1.5.6 Process Image...............................................................................42 2.1.5.7 Example........................................................................................43 WAGO-I/O-SYSTEM 750 I/O Modules Important Comments 5 Legal Principles 1 Important Comments To ensure fast installation and start-up of the units described in this manual, we strongly recommend that the following information and explanations are carefully read and abided by. 1.1 Legal Principles 1.1.1 Copyright This manual is copyrighted, together with all figures and illustrations contained therein. Any use of this manual which infringes the copyright provisions stipulated herein, is not permitted. Reproduction, translation and electronic and photo-technical archiving and amendments require the written consent of WAGO Kontakttechnik GmbH & Co. KG. Non-observance will entail the right of claims for damages. WAGO Kontakttechnik GmbH & Co. KG reserves the right to perform modifications allowed by technical progress. In case of grant of a patent or legal protection of utility patents all rights are reserved by WAGO Kontakttechnik GmbH & Co. KG. Products of other manufacturers are always named without referring to patent rights. The existence of such rights can therefore not be ruled out. 1.1.2 Personnel Qualification The use of the product detailed in this manual is exclusively geared to specialists having qualifications in PLC programming, electrical specialists or persons instructed by electrical specialists who are also familiar with the valid standards. WAGO Kontakttechnik GmbH & Co. KG declines all liability resulting from improper action and damage to WAGO products and third party products due to non-observance of the information contained in this manual. 1.1.3 Intended Use For each individual application, the components supplied are to work with a dedicated hardware and software configuration. Modifications are only permitted within the framework of the possibilities documented in the manuals. All other changes to the hardware and/or software and the non- conforming use of the components entail the exclusion of liability on part of WAGO Kontakttechnik GmbH & Co. KG. Please direct any requirements pertaining to a modified and/or new hardware or software configuration directly to WAGO Kontakttechnik GmbH & Co. KG. WAGO-I/O-SYSTEM 750 I/O Modules 6 Important Comments Symbols 1.2 Symbols Danger Always abide by this information to protect persons from injury. Warning Always abide by this information to prevent damage to the device. Attention Marginal conditions must always be observed to ensure smooth operation. ESD (Electrostatic Discharge) Warning of damage to the components by electrostatic discharge. Observe the precautionary measure for handling components at risk. Note Routines or advice for efficient use of the device and software optimization. More information References on additional literature, manuals, data sheets and internet pages. 1.3 Number Notation Number Code Example Note Decimal 100 normal notation Hexadecimal 0x64 C notation Binary '100' within inverted commas, '0110.0100' nibble separated with dots WAGO-I/O-SYSTEM 750 I/O Modules Important Comments 7 Safety Notes 1.4 Safety Notes Warning Switch off the system prior to working on bus modules! In the event of deformed contacts, the module in question is to be replaced, as its functionality can no longer be ensured on a long-term basis. The components are not resistant against materials having seeping and insulating properties. Belonging to this group of materials is: e.g. aerosols, silicones, triglycerides (found in some hand creams). If it cannot be ruled out that these materials appear in the component environment, then additional measures are to be taken: - installation of the components into an appropriate enclosure - handling of the components only with clean tools and materials. Attention Cleaning of soiled contacts may only be done with ethyl alcohol and leather cloths. Thereby, the ESD information is to be regarded. Do not use any contact spray. The spray may impair the functioning of the contact area. The WAGO-I/O-SYSTEM 750 and its components are an open system. It must only be assembled in housings, cabinets or in electrical operation rooms. Access must only be given via a key or tool to authorized qualified personnel. The relevant valid and applicable standards and guidelines concerning the installation of switch boxes are to be observed. ESD (Electrostatic Discharge) The modules are equipped with electronic components that may be destroyed by electrostatic discharge. When handling the modules, ensure that the environment (persons, workplace and packing) is well grounded. Avoid touching conductive components, e.g. gold contacts. 1.5 Scope This manual describes the Special Module 750-404, (/xxx-xxx) Counter Modules of the modular WAGO-I/O-SYSTEM 750. Handling, assembly and start-up are described in the manual of the Fieldbus Coupler/Controller. Therefore this documentation is valid only in the connection with the appropriate manual. WAGO-I/O-SYSTEM 750 I/O Modules 8 Overview Counter Modules 750-404, (/xxx-xxx) 2 I/O Modules 2.1 Specialty Modules 2.1.1 Overview Counter Modules 750-404, (/xxx-xxx) 750-404/ 750-404/ 750-404/ 750-404/ 750-404/ I/O Module 750-404 000-001 000-002 000-003 000-004 000-005 Function Up / Up Peak Time Frequency Up / Down 2 Up Down Counter / Counter Counter Counter / Counter Counter Enable Switch Input Output Channels 1 1 1 1 1 2 Switching rate max. max. max. 0,1 Hz ... max. max. 100 kHz 100 kHz 10 kHz 100 kHz 100 kHz 5 kHz Counter depth 32 bit 32 bit 32 bit 32 bit 32 bit 16 bit WAGO-I/O-SYSTEM 750 I/O Modules 750-404 [Up/Down Counter /100 kHz] 9 Variations 2.1.2 750-404 [Up/Down Counter /100 kHz] Up/Down Counter, DC 24 V, 100 kHz 2.1.2.1 Variations Item-No. Designation Description 750-404 Up/Down Counter / Up/Down Counter, DC 24 V, 100 kHz 100 kHz 750-404/000-002 Peak Time Counter Peak Time Counter, DC 24 V, 10 kHz 750-404/000-004 Up / Down Counter / Up/Down Counter, 24 V, 100kHz, Switch Output Switch Output 2.1.2.2 View 13 14 Status Status A U/D C CLOCK B DO 1 D DO 2 U/D CLK Data contacts U/D CLOCK ++ 24V -- 0V A1 A2 DO 1 DO 2 750-404 Power jumper contacts Fig. 2.1.2-1: Up/Down Counter 750-404 g040400e 2.1.2.3 Description The Up/Down counter 750-404 and the variation 750-404/000-004 is capable of counting binary pulses of DC 24 V at the input CLOCK and then transmits the data to the fieldbus. The counter module 750-404/000-002 begins processing with pulses at the CLOCK input and counts the pulses in a special time span. The time span is given as 10 s. The changes from 0 V to 24 V are counted The counter counts up, if the input U/D is set at 24 V. With an open circuit input or 0 V the counter counts backwards. WAGO-I/O-SYSTEM 750 I/O Modules 10 750-404 [Up/Down Counter /100 kHz] Description The counter can be set or reset with the control byte. The digital outputs DO 1 and DO 2 of the counter module 750-404 and the variation 750-404/000-002 are activated through bits in the control byte. The digital outputs DO 1 and DO 2 of the counter module 750-404/000-004 are activated depending on the counter reading or through bits in the control byte. The outputs are short-circuit-protected. The high states of the inputs U/D and CLOCK and the digital output channels are each indicated by a green LED. An optocoupler is used for electrical isolation between the bus and the field side. Any configuration of the counter modules is possible when designing the fieldbus node. Grouping of module types is not necessary. The field side supply voltage of 24 V for the counter module is derived from adjacent I/O modules or from a supply module. The supply voltage for the field side is made automatically through the individual I/O modules by means of power jumper contacts. Warning The maximum current of the internal power jumper contacts is 10 A. When configuring the system it is important not to exceed the maximum/sum current. However, if such a case should occur, another supply module must be added. Attention This module has no power contacts for receiving and transmitting the ground (earth) potential. A supply module is required, if the adjacent modules need to be connected to the ground. Note Use an appropriate supply module (e.g. 750-602) if an electrically isolated voltage supply is required! The module 750-404 and the variations 750-404/000-002 and 750-404/000- 004 can be used with all couplers/controllers of the WAGO-I/O-SYSTEM 750 (except for the economy types 750-320, 750-323, 750-324 and 750-327 and the ModBus controllers 750-812, 750-812/025-000 and 750-814). WAGO-I/O-SYSTEM 750 I/O Modules 750-404 [Up/Down Counter /100 kHz] 11 Display Elements 2.1.2.4 Display Elements LED Channel Meaning State Input U/D: Signal voltage (0), off Backwards counting A Status green U/D Input U/D: Signal voltage (1), on Forward counting 13 14 off Input CLOCK: Signal voltage (0) A B Status C A C B Input CLOCK: Signal voltage (1) green CLOCK B D D on Counting pulse Fig. 2.1.2-2: Display off Digital Output DO 1 reset C Status Elements g041402x green DO 1 on Digital Output DO 1 setting off Digital Output DO 2 reset D Status green DO 2 on Digital Output DO 2 setting 2.1.2.5 Schematic Diagram 5V U/D 1 5 270pF U/D CLOCK CLOCK 2 6 270pF 24V 24V 10nF 10nF U/D Logic 3 7 0V 0V 10nF CLOCK 270pF 4 8 DO 2 DO DO 1 DO 750-404 Fig. 2.1.2-3: Up/Down Counter 750-404 g040401e WAGO-I/O-SYSTEM 750 I/O Modules 12 750-404 [Up/Down Counter /100 kHz] Technical Data 2.1.2.6 Technical Data Module Specific Data Number of outputs 2 Number of counters 1 Output current 0.5 A short-circuit-protected Current consumption (internal) 15 mA Voltage via power jumper contacts DC 24 V (-15 % ... + 20 %) Signal voltage (0): DC 3 V ... +5 V (1): DC +15 V ... +30 V Switching rate 100 kHz (750-404, 750-404/000-004) max. 10 kHz (750-404/000-002) Input current 6 mA typ. Counter depth 32 bits data Isolation 500 V (System/Supply) Internal bit width 32 bits data 8 bits control /status Dimensions (mm) W x H x L 12 x 64* x 100 * from upper edge of 35 DIN rail Weight ca. 55 g Standards and Regulations (cf. Chapter 2.2 of the Coupler/Controller Manual) EMC-Immunity to interference (CE) acc. to EN 50082-2 (96) EMC-Emission of interference (CE) acc. to EN 50081-1 (93) Approvals (cf. Chapter 2.2 of the Coupler/Controller Manual) UL (UL508) C US ABS (American Bureau of Shipping) BV (Bureau Veritas) (applied for) DNV (Det Norske Veritas) Cl. B GL (Germanischer Lloyd) (applied for) Cat. A, B, C, D KR (Korean Register of Shipping) LR (Lloyd's Register) Env. 1, 2, 3, 4 NKK (Nippon Kaiji Kyokai) Class I Div2 ABCD T4A UL (UL1604) C US II 3 G EEx nA II T4 KEMA Conformity Marking WAGO-I/O-SYSTEM 750 I/O Modules 750-404 [Up/Down Counter /100 kHz] 13 Process Image More Information Detailed references to the approvals are listed in the document "Overview Approvals WAGO-I/O-SYSTEM 750", which you can find on the CD ROM ELECTRONICC Tools and Docs (Item-No.: 0888-0412) or in the internet under: www.wago.com ! Documentation ! WAGO-I/O-SYSTEM 750 ! System Description 2.1.2.7 Process Image Using the I/O module 750-404, a 5 byte input and output process image can be transferred to the fieldbus coupler / controller via one logical channel. The transfer of the setting counter value in binary format is made via 4 output bytes (D0 ... D3) and the transfer of the counter reading in binary format is made via 4 input bytes (D0 ... D3). The control byte C0 serves for setting the counter and the outputs. The status byte S0 shows the status of the counter and the inputs and outputs. Attention The representation of the process data of some I/O modules or their variations in the process image depends on the fieldbus coupler/-controller used. Please take this information as well as the particular design of the respective control/status bytes from the section "Fieldbus Specific Design of the Process Data" included in the description concerning the process image of the corresponding coupler/controller. Input data Output data S0 Status byte 0 C0 Control byte 0 D0 Counter value byte 0 (LSB) D0 Set value byte 0 (LSB) D1 Counter value byte 1 D1 Set value byte 1 D2 Counter value byte 2 D2 Set value byte 2 D3 Counter value byte 3 (MSB) D3 Set value byte 3 (MSB) WAGO-I/O-SYSTEM 750 I/O Modules 14 750-404 [Up/Down Counter /100 kHz] Process Image 2.1.2.7.1 Control- / Status byte 750-404 The control byte C0 serves for setting and locking the counter and for setting the outputs. The status byte S0 shows the status of the counter and the inputs and outputs. Control byte B7 B6 B5 B4 B3 B2 B1 B0 0 0 Set Lock Set Set 0 0 counter counter output output DO 2 DO 1 0 This constant must be set to zero. Status byte B7 B6 B5 B4 B3 B2 B1 B0 X X Counter Counter actual actual actual actual is set is signal at signal at signal at signal at blocked output output input input DO 2 DO 1 U/D CLOCK X This value is not evaluated. With the control and status byte the following tasks are possible: Set Counter: Put Bit 5 into the control byte. The counter with the 32 bit value is loaded into output bytes 0-3. As long as the bits are set, the counter can stop and information is stored. The ensuing data of the counter will be conveyed to the status byte. Lock Counter: Bit 4 is set into the control byte, then the count process is suppressed. Bit 4 in the status byte communicates the suppression of the counter. Set/ Reset Outputs: Bits 2 and 3 set the additional two outputs of the counter module. WAGO-I/O-SYSTEM 750 I/O Modules 750-404 [Up/Down Counter /100 kHz] 15 Process Image 2.1.2.7.2 Control- / Status byte 750-404/000-002 The control byte C0 serves for starting the periodic counter pulse measurement and for setting the outputs. The status byte S0 shows the status of the counter and the inputs and outputs. Control byte B7 B6 B5 B4 B3 B2 B1 B0 0 0 Start of 0 Set Set 0 0 the output output periodic DO 2 DO 1 counting 0 This constant must be set to zero. Status byte B7 B6 B5 B4 B3 B2 B1 B0 X X Counting X actual actual actual Toggelbit starting signal at signal at signal at for end of output output input the DO 2 DO 1 U/D record X This value is not evaluated. The counter begins processing with pulses at the CLOCK input and counts the pulses in a special time span. The time span is given as 10 s. The state of the counter is stored in the process image until the next period. After the recording the counting starts again at 0. The activation of the counting and the synchronization with the SPS is made by a handshake in the control and status byte. The end of the counting period and thus the new process data is signaled by a toggle bit in the status byte. WAGO-I/O-SYSTEM 750 I/O Modules 16 750-404 [Up/Down Counter /100 kHz] Process Image 2.1.2.7.3 Control- / Status byte 750-404/000-004 The control byte C0 serves for setting and locking the counter and for setting the outputs dependent or independently on the counter reading. The status byte S0 shows the status of the counter and the inputs and outputs. Control byte B7 B6 B5 B4 B3 B2 B1 B0 0 0 Set Lock Set Set Output Output counter Counter output output O2 O1 DO 2 DO 1 activated activated dependin dependin g of the g of the counter counter value value 0 This constant must be set to zero. Status byte B7 B6 B5 B4 B3 B2 B1 B0 X X Counter Counter actual actual actual actual is set is signal at signal at signal at signal at blocked output output input input DO 2 DO 1 U/D CLOCK X This value is not evaluated. With the control and status byte the following tasks are possible: Set Counter: Put Bit 5 into the control byte. The counter with the 32 bit value is loaded into output bytes 0-3. As long as the bits are set, the counter can stop and information is stored. The ensuing data of the counter will be conveyed to the status byte. Lock Counter: Bit 4 is set into the control byte, then the count process is suppressed. Bit 4 in the status byte communicates the suppression of the counter. Switching the outputs dependent of the counter: The bits 0 and 1 activate the function: output dependent setting of binary outputs. If the counter reading 0x80000000 is exceeded, output DO 1 is activated. For the output DO 2 only the bottom 16 bits of the counter reading are taken into account, which means that output DO 2 is activated as soon as the counter reading 0x8000 is exceeded. Having reached 0 again, the outputs are reset. WAGO-I/O-SYSTEM 750 I/O Modules 750-404 [Up/Down Counter /100 kHz] 17 Examples Set Outputs: Bits 2 and 3 set the digital outputs DO 1 and DO 2 of the counter module. If bits 2 or 3 are also set, they have priority before bits 0 and 1, so that the corresponding output is set independent of the counter reading. 2.1.2.8 Examples 2.1.2.8.1 750-404 Set Counter: First of all the counter reading is set to 100 by "Setting counter", i. e. to the hexadecimal value: 0x64. 1. Enter the counter reading in the output data. The data bytes D0 to D3 of the output data then read as follows: Data bytes Output data D3 D2 D1 D0 Value 0x00 0x00 0x00 0x64 2. Validate the counter reading in the control byte with bit 5 (setting counter) to have it adopted as an output value. The control byte has the following bits: Control byte Output bit B7 B6 B5 B4 B3 B2 B1 B0 Value 0 X 1 X X X X X 3. Wait for the feedback from the counter module in the status byte, bit 5 (counter set). The status byte has the following bits: Status byte Input bit B7 B6 B5 B4 B3 B2 B1 B0 X X 1 X X X X X Value 4. Delete bit 5 (setting counter) in the control byte in order to finish the Handshake. The bits in the control byte read as follows: Control byte Output bit B7 B6 B5 B4 B3 B2 B1 B0 Value 0 X 0 X X X X X 5. The set counter reading then appears in the input data with the following data bytes D0 to D3: Data bytes Input bit D3 D2 D1 D0 Wert 0x00 0x00 0x00 0x64 X is used if a value is not relevant. WAGO-I/O-SYSTEM 750 I/O Modules 18 750-404 [Up/Down Counter /100 kHz] Examples Up counting: Attention For counting up, 24 V must be applied to input U/D. 6. Wait for the first and further count pulses. During counting, the data bytes D0 to D3 of the input data appear as follows: Data bytes Remark D3 D2 D1 D0 no count pulse 0x00 0x00 0x00 0x64 received 1st count pulse 0x00 0x00 0x00 0x65 received 2nd count pulse 0x00 0x00 0x00 0x66 received Further count pulses ........ ........ ........ ........ Max. counter reading 0xFF 0xFF 0xFF 0xFF reached the next count pulse 0x00 0x00 0x00 0x00 causes a number overflow One further count 0x00 0x00 0x00 0x01 pulse received WAGO-I/O-SYSTEM 750 I/O Modules 750-404 [Up/Down Counter /100 kHz] 19 Examples 2.1.2.8.2 750-404/000-002 1. The counter counts up (the input U/D is set at 24 V). The counter reading is 0. The timer interrupts. No count pulse received on the input CLOCK. Control byte Input bit B7 B6 B5 B4 B3 B2 B1 B0 Value 0 0 0 0 X X 0 0 Status byte Output bit B7 B6 B5 B4 B3 B2 B1 B0 Value 0 0 0 0 X X 1 0 2. The cyclic period measurement is requested. The counter reading is 0. The timer interrupts. No count pulse received on the input CLOCK. Control byte Input bit B7 B6 B5 B4 B3 B2 B1 B0 0 0 1 0 X X 0 0 Value Status byte Output bit B7 B6 B5 B4 B3 B2 B1 B0 Value 0 0 0 0 X X 1 0 3. The cyclic period measurement is started. The counter reading is 0. The timer runs with the parameterized cycle time. Count pulses received on the input CLOCK. Control byte Input bit B7 B6 B5 B4 B3 B2 B1 B0 Value 0 0 1 0 X X 0 0 Status byte Output bit B7 B6 B5 B4 B3 B2 B1 B0 0 0 1 0 X X 1 0 Value 4. The cyclic period measurement is running. The counter reading is reset and the timer is started again. The process data supply the number of impulses, which were registered in the previous cycle. Control byte Input bit B7 B6 B5 B4 B3 B2 B1 B0 Value 0 0 1 0 X X 0 0 Status byte Output bit B7 B6 B5 B4 B3 B2 B1 B0 Value 0 0 1 0 X X 1 1 5. The cyclic period measurement is running. The counter reading is reset and the timer is started again. The process data supply the number of impulses, which were registered in the previous cycle. Control byte Input bit B7 B6 B5 B4 B3 B2 B1 B0 Value 0 0 1 0 X X 0 0 Status byte Output bit B7 B6 B5 B4 B3 B2 B1 B0 Value 0 0 1 0 X X 1 0 WAGO-I/O-SYSTEM 750 I/O Modules 20 750-404 [Up/Down Counter /100 kHz] Examples 6. The cyclic period measurement is running. Stopping the cyclic recording was requested. The process data supply the counter reading, which was registered in the previous cycle. Control byte Input bit B7 B6 B5 B4 B3 B2 B1 B0 0 0 0 0 X X 0 0 Value Status byte Output bit B7 B6 B5 B4 B3 B2 B1 B0 Value 0 0 1 0 X X 1 X 7. The cyclic period measurement is stopped. The counter reading is reset. The process data supply the value 0. Control byte Input bit B7 B6 B5 B4 B3 B2 B1 B0 Value 0 0 0 0 X X 0 0 Status byte Output bit B7 B6 B5 B4 B3 B2 B1 B0 0 0 0 0 X X 1 0 Value 2.1.2.8.3 750-404/000-004 Set the digital output DO 1 after 4.000 pulses have been counted. There are several possibilities to set an output. If DO 1 is used as an automatic switching output and if the counter is to count up, set the counter to 0x80000000 - 4000 = 0x7FFFF060 and apply + 24V to the U/D input. Furthermore, activate bit 0 in the control byte. After 4000 pulses, the counter reading of 0x80000000 is reached and output DO 1 activated. If you wish the counter to count down, pre-set 0x80000000 + 4000 = 0x80000FA0 and apply 0V to U/D. After 4000 pulses the counter reading 0x80000000 is reached and output DO 1 deactivated. If DO 2 is to be used as a switching output, load the counter with 0x8000 - 4000 = 0x7060 or 0x8000 + 4000 = 0x8FA0 respectively, because only the bottom 16 bits of the counter are used for switching output DO 2. Instead of bit 0 now activate bit 1 in the control byte. The binary output not involved each time can be directly addressed by the controls via bit 2 and 3. WAGO-I/O-SYSTEM 750 I/O Modules 750-404/000-001 [Up Counter / Enable Input] 21 View 2.1.3 750-404/000-001 [Up Counter / Enable Input] Up Counter / Enable Input, DC 24 V, 100 kHz 2.1.3.1 View 13 14 Status Status A GATE C CLOCK B DO 1 D DO 2 GAT CLK Data contacts GATE CLOCK ++ 24V -- 0V A1 A2 DO 1 DO 2 750-404 /000-001 Power jumper contacts Fig. 2.1.3-1: Up Counter 750-404/000-001 g040404e 2.1.3.2 Description The Up counter is capable of counting binary pulses of DC 24 V at the input CLOCK and then transmits the data to the fieldbus. The changes from 0 V to 24 V are counted. The counter is locked with an open circuit or 0 V on input GATE. With +24 V on input GATE, the counter is enabled. The counter can be set or reset with the control byte. The digital outputs DO 1 and DO 2 are activated through bits in the control byte. The outputs are short-circuit-protected. The high states of the inputs GATE and CLOCK and the digital output channels are each indicated by a green LED. An optocoupler is used for electrical isolation between the bus and the field side. Any configuration of the counter modules is possible when designing the fieldbus node. Grouping of module types is not necessary. WAGO-I/O-SYSTEM 750 I/O Modules 22 750-404/000-001 [Up Counter / Enable Input] Display Elements The field side supply voltage of 24 V for the counter module is derived from adjacent I/O modules or from a supply module. The supply voltage for the field side is made automatically through the individual I/O modules by means of power jumper contacts. Warning The maximum current of the internal power jumper contacts is 10 A. When configuring the system it is important not to exceed the maximum/sum current. However, if such a case should occur, another supply module must be added. Attention This module has no power contacts for receiving and transmitting the ground (earth) potential. A supply module is required, if the adjacent modules need to be connected to the ground. Note Use an appropriate supply module (e.g. 750-602) if an electrically isolated voltage supply is required! The module 750-404/000-001 can be used with all couplers/controllers of the WAGO-I/O-SYSTEM 750 (except for the economy types 750-320, 750-323, 750-324 and 750-327 and the ModBus controllers 750-812, 750-812/025-000 and 750-814). 2.1.3.3 Display Elements LED Channel Meaning State Input GATE: Signal voltage (0), off Counting closed A Status green GATE Input GATE: Signal voltage (1), on Counting approved 13 14 A off Input CLOCK: Signal voltage (0) B Status A C C B green CLOCK B D D on Input CLOCK: Signal voltage (1) Fig. 2.1.3-2: Display off Digital Output DO 1 reset C Status Elements g041402x green DO 1 on Digital Output DO 1 setting off Digital Output DO 2 reset D Status green DO 2 on Digital Output DO 2 setting WAGO-I/O-SYSTEM 750 I/O Modules 750-404/000-001 [Up Counter / Enable Input] 23 Schematic Diagram 2.1.3.4 Schematic Diagram 5V GATE 1 5 GATE CLOCK 270pF CLOCK 2 6 270pF 24V 24V 10nF 10nF GATE Logic 3 7 0V 0V 10nF CLOCK 270pF 4 8 DO DO 1 DO 2 DO 750-404 /000-001 Fig. 2.1.3-3: Up Counter 750-404/000-001 g040405e WAGO-I/O-SYSTEM 750 I/O Modules 24 750-404/000-001 [Up Counter / Enable Input] Technical Data 2.1.3.5 Technical Data Module Specific Data Number of outputs 2 Number of counters 1 Output current 0.5 A short-circuit-protected Current consumption (internal) 15 mA Voltage via power jumper contacts DC 24 V (-15 % ... + 20 %) Signal voltage (0): DC 3 V ... +5 V (1): DC +15 V ... +30 V Switching rate 100 kHz max. Input current 6 mA typ. Counter depth 32 bits data Isolation 500 V (System/Supply) Internal bit width 32 bits data 8 bits control /status Dimensions (mm) W x H x L 12 x 64* x 100 * from upper edge of 35 DIN rail Weight ca. 55 g Standards and Regulations (cf. Chapter 2.2 of the Coupler/Controller Manual) EMC-Immunity to interference (CE) acc. to EN 50082-2 (96) EMC-Emission of interference (CE) acc. to EN 50081-1 (93) Approvals (cf. Chapter 2.2 of the Coupler/Controller Manual) UL (UL508) C US Class I Div2 ABCD T4A UL (UL1604) C US DNV (Det Norske Veritas) Cl. B II 3 G EEx nA II T4 KEMA Conformity Marking More Information Detailed references to the approvals are listed in the document "Overview Approvals WAGO-I/O-SYSTEM 750", which You can find on the CD ROM ELECTRONICC Tools and Docs (Item-No.: 0888-0412-0001-0101) or in the Internet under: www.wago.com -> Service /Downloads /Documentation /WAGO-I/O-SYSTEM 750/System Description/. WAGO-I/O-SYSTEM 750 I/O Modules 750-404/000-001 [Up Counter / Enable Input] 25 Process Image 2.1.3.6 Process Image Using the I/O module 750-404/000-001, a 5 byte input and output process image can be transferred to the fieldbus coupler / controller via two logical channels. The transfer of the setting counter value in binary format is made via 4 output bytes (D0 ... D3) and the transfer of the counter reading in binary format is made via 4 input bytes (D0 ... D3). The control byte C0 serves for setting and locking the counter and for setting the outputs. The status byte S0 shows the status of the counter and the inputs and outputs. Attention The representation of the process data of some I/O modules or their variations in the process image depends on the fieldbus coupler/-controller used. Please take this information as well as the particular design of the respective control/status bytes from the section "Fieldbus Specific Design of the Process Data" included in the description concerning the process image of the corresponding coupler/controller. Input data Output data S0 Status byte 0 C0 Control byte 0 D0 Counter value byte 0 (LSB) D0 Set value byte 0 (LSB) D1 Counter value byte 1 D1 Set value byte 1 D2 Counter value byte 2 D2 Set value byte 2 D3 Counter value byte 3 (MSB) D3 Set value byte 3 (MSB) Control byte B7 B6 B5 B4 B3 B2 B1 B0 0 0 Set Lock Set Set 0 0 counter counter output output DO 2 DO 1 0 This constant must be set to zero. Status byte 0 B7 B6 B5 B4 B3 B2 B1 B0 X X Counter Counter actual actual actual actual is set is signal at signal at signal at signal at blocked output output input input DO 2 DO 1 U/D CLOCK X This value is not evaluated. WAGO-I/O-SYSTEM 750 I/O Modules 26 750-404/000-001 [Up Counter / Enable Input] Example With the control and status byte the following tasks are possible: Set Counter: Put Bit 5 into the control byte. The counter with the 32 bit value is loaded into output bytes 0-3. As long as the bits are set, the counter can stop and information is stored. The ensuing data of the counter will be conveyed to the status byte. Lock Counter: Bit 4 is set into the control byte, then the count process is suppressed. Bit 4 in the status byte communicates the suppression of the counter. Set Outputs: Bits 2 and 3 set the additional two outputs of the counter module. 2.1.3.7 Example Set Counter: First of all the counter reading is set to 100 by "Setting counter", i. e. to the hexadecimal value: 0x64. 8. Enter the set value in the output data. The data bytes D0 to D3 of the output data then read as follows: Data bytes Output data D3 D2 D1 D0 Value 0x00 0x00 0x00 0x64 9. Validate the counter reading in the control byte with bit 5 (setting counter) to have it adopted as an output value. The control byte has the following bits: Control byte Output bit B7 B6 B5 B4 B3 B2 B1 B0 Value 0 X 1 X X X X X 10.Wait for the feedback from the counter module in the status byte, bit 5 (counter set). The status byte has the following bits: Status byte Input bit B7 B6 B5 B4 B3 B2 B1 B0 Value X X 1 X X X X X 11.Delete bit 5 (setting counter) in the control byte in order to finish the Handshake. The bits in the control byte read as follows: Control byte Output bit B7 B6 B5 B4 B3 B2 B1 B0 Value 0 X 0 X X X X X 12.The set counter reading then appears in the input data with the following data bytes D0 to D3: Data bytes Input bit D3 D2 D1 D0 Value 0x00 0x00 0x00 0x64 X is used if a value is not relevant. WAGO-I/O-SYSTEM 750 I/O Modules 750-404/000-001 [Up Counter / Enable Input] 27 Example Up counting: Attention For counting up, 24 V must be applied to input GATE. 13.Wait for the first and further count pulses. During counting, the data bytes D0 to D3 of the input data appear as follows: Data bytes Remark D3 D2 D1 D0 no count pulse 0x00 0x00 0x00 0x64 received 1st count pulse 0x00 0x00 0x00 0x65 received 2nd count pulse 0x00 0x00 0x00 0x66 received Further count pulses ........ ........ ........ ........ Max. counter reading 0xFF 0xFF 0xFF 0xFF reached the next count pulse 0x00 0x00 0x00 0x00 causes a number overflow One further count 0x00 0x00 0x00 0x01 pulse received WAGO-I/O-SYSTEM 750 I/O Modules 28 750-404/000-003 [Frequency Counter 0.1 Hz-100 kHz] View 2.1.4 750-404/000-003 [Frequency Counter 0.1 Hz-100 kHz] Frequency Counter 0.1 Hz ... 100 kHz, DC 24 V 2.1.4.1 View 13 14 Status Status A GATE C CLOCK B DO 1 D DO 2 GATCLK Data contacts GATE CLOCK ++ 24V -- 0V A1 A2 DO 1 DO 2 750-404 /000-003 Power jumper contacts Fig. 2.1.4-1: Frequency Counter 750-404/000-003 g040408e 2.1.4.2 Description The counter module also can be ordered as frequency counter module with 750-404/000-003. The counter module 750-404/000-003 measures the period of the 24 V DC input signal at the input CLOCK and converts it into a corresponding frequency value. The measurement is enabled if the input GATE is an open circuit input or 0V. To disable processing, the GATE input is to be set to 24 V DC. To recognize low frequency or near zero frequency signals, the maximum time between two data updates is parameterizable. The digital outputs DO1 and DO2 can be activated via specific bits in the Control byte. The outputs are short-circuit-protected. The high states of the inputs GATE and CLOCK and the output channels are each indicated by a LED. An optocoupler is used for electrical isolation between the bus and the field side. Any configuration of the counter modules is possible when designing the fieldbus node. Grouping of module types is not necessary. WAGO-I/O-SYSTEM 750 I/O Modules 750-404/000-003 [Frequency Counter 0.1 Hz-100 kHz] 29 Description The field side supply voltage of 24 V for the counter module is derived from adjacent I/O modules or from a supply module. The supply voltage for the field side is made automatically through the individual I/O modules by means of power jumper contacts. Warning The maximum current of the internal power jumper contacts is 10 A. When configuring the system it is important not to exceed the maximum/sum current. However, if such a case should occur, another supply module must be added. Attention This module has no power contacts for receiving and transmitting the ground (earth) potential. A supply module is required, if the adjacent modules need to be connected to the ground. Note Use an appropriate supply module (e.g. 750-602) if an electrically isolated voltage supply is required! The module 750-404/000-003 can be used with all couplers/controllers of the WAGO-I/O-SYSTEM 750 (except for the economy types 750-320, 750-323, 750-324 and 750-327 and the ModBus controllers 750-812, 750-812/025-000 and 750-814). WAGO-I/O-SYSTEM 750 I/O Modules 30 750-404/000-003 [Frequency Counter 0.1 Hz-100 kHz] Display Elements 2.1.4.3 Display Elements LED Channel Meaning State Input GATE: Signal voltage (0), off Measurement released A Status green GATE Input GATE: Signal voltage (1), on Measurement disabled 13 14 off Input CLOCK: Signal voltage (0) A B Status A C C B Input CLOCK: Signal voltage (1), green CLOCK B D D on Counting pulse Fig. 2.1.4-2: Display off Digital Output DO 1 reset C Status Elements g041402x green DO 1 on Digital Output DO 1 setting off Digital Output DO 2 reset D Status green DO 2 on Digital Output DO 2 setting 2.1.4.4 Schematic Diagram 5V GATE 1 5 CLOCK GATE 270pF CLOCK 2 6 270pF 24V 24V 10nF 10nF GATE Logic 3 7 0V 0V 10nF CLOCK 270pF 4 8 DO 1 DO 2 DO DO 750-404 /000-003 Fig. 2.1.4-3: Frequency Counter 750-404/000-003 g040409e WAGO-I/O-SYSTEM 750 I/O Modules 750-404/000-003 [Frequency Counter 0.1 Hz-100 kHz] 31 Technical Data 2.1.4.5 Technical Data Module Specific Data 2 Number of outputs 1 Number of counters 0.5 A short-circuit-protected Output current Current consumption 75 mA at DC 5 V max. Voltage via power jumper contacts DC 24 V (-15 % ... + 20 %) (0): DC 3 V ... +5 V Signal voltage (1): DC +15 V ... +30 V 100 kHz Switching rate max. Pulse width 10 µs min. 5 mA Input current typ. 32 Bit Counter depth 500 V (System/Supply) Isolation 32 bits data Internal bit width 8 bits control /status Dimensions (mm) W x H x L 12 x 64* x 100 * from upper edge of 35 DIN rail ca. 55 g Weight Maximum frequency range Integration time = 1 period 0.1 Hz - 8 kHz, resolution 0.001 Hz Integration time = 4 period 0.25 Hz - 32 kHz, resolution 0.01 Hz Integration time = 16 period 1 Hz - 100 kHz, resolution 0.1 Hz (1 Hz) Measuring error at the maximum frequency range Range 0.1 Hz - 8 kHz < ± 1 % Range 0.25 Hz - 32 kHz < ± 1.5 % Range 1 Hz - 100 kHz < ± 1.5 % Lower frequency range* Integration time = 1 period 0,1 Hz - 100 Hz, resolution 0.001 Hz Integration time = 4 period 1 Hz - 1 kHz, resolution 0.01 Hz Integration time = 16 period 10 Hz - 10 kHz, resolution 0.1 Hz (1 Hz) Measuring error at the lower frequency range * Range 0,1 Hz - 100 Hz < ± 0.05 % Range 1 Hz - 1 kHz < ± 0.05 % Range 10 Hz - 10 kHz < ± 0.2 % * For Measurements in a lower frequency range, the measuring error is lower than the measuring error using the maximum frequency rang. Standards and Regulations (cf. Chapter 2.2 of the Coupler/Controller Manual) EMC-Immunity to interference (CE) acc. to EN 50082-2 (96) EMC-Emission of interference (CE) acc. to EN 50081-1 (93) WAGO-I/O-SYSTEM 750 I/O Modules 32 750-404/000-003 [Frequency Counter 0.1 Hz-100 kHz] Functional Description Approvals (cf. Chapter 2.2 of the Coupler/Controller Manual) UL (UL508) C US Class I Div2 ABCD T4A UL (UL1604) C US DNV (Det Norske Veritas) Cl. B II 3 G EEx nA II T4 KEMA Conformity Marking More Information Detailed references to the approvals are listed in the document "Overview Approvals WAGO-I/O-SYSTEM 750", which You can find on the CD ROM ELECTRONICC Tools and Docs (Item-No.: 0888-0412-0001-0101) or in the Internet under: www.wago.com -> Service /Downloads /Documentation /WAGO-I/O-SYSTEM 750/System Description/. 2.1.4.6 Functional Description The counter module acquires the time between one or more rising edges of the CLOCK input signal and calculates the frequency of the applied signal. The calculation and process image update are initiated every 1st, every 4th or every 16 th rising edge depending on the integration time selected via the CONTROL byte. The first detection of a rising edge starts the cyclic period measurement and cannot provide a valid frequency value. In this case the module will send 0xFFFFFFFFH for input information. The same input value is returned when a static high or static low signal is applied to the CLOCK input. If there are no signal changes seen at the CLOCK input, the module can be forced to update the process image after defined parameterizable time spans (Watchdog time). In this state the module will send the non valid value 0xFFFFFFFFH too. The following figures illustrate a process data cycle. WAGO-I/O-SYSTEM 750 I/O Modules 750-404/000-003 [Frequency Counter 0.1 Hz-100 kHz] 33 Process Image TP T1 Input frequency Data valid Process 0xFFFFFFFF D0..D3 D0..D3 0xFFFFFFFF D0..D3 data D0..D3 D0..D3 D0..D3 Input Data TP = 1/f Current period T1 Maximum data hold time (parameterizable) Fig. 2.1.4-4: Timing diagram for process data update sequence g040402e (integration time = 1 period) 4TP T1 Input frequency Data valid Process 0xFFFFFFFF D0..D3 D0..D3 0xFFFFFFFF data D0..D3 Input Data TP = 1/f Current period T 1 Maximum data hold time (parameterizable) Fig. 2.1.4-5: Timing diagram for process data update sequence g040403e (integration time = 1 period) 2.1.4.7 Process Image Using the I/O module 750-404/000-003, a 5 byte input and output process image can be transferred to the fieldbus coupler / controller via two logical channels. The two output bytes (D0, D1) contain the setting Watchdog time in binary format. The other output bytes (D2, D3) are not used. The four input bytes (D0 ... D3) contain the frequency value in binary format. The control byte C0 serves for setting the integration time, the Watchdog time, the representation of the measured frequency value and the outputs. The status byte S0 displays the acknowledgement of the settings and shows the status of the inputs and outputs. Attention The representation of the process data of some I/O modules or their variations in the process image depends on the fieldbus coupler/-controller used. Please take this information as well as the particular design of the respective control/status bytes from the section "Fieldbus Specific Design of the Process Data" included in the description concerning the process image of the corresponding coupler/controller. WAGO-I/O-SYSTEM 750 I/O Modules 34 750-404/000-003 [Frequency Counter 0.1 Hz-100 kHz] Process Image Input data Output data S0 Status byte C0 Control byte D0 Frequency value byte 0 (LSB) D0 Watchdog-time byte 0 (LSB) D1 Frequency value byte 1 D1 Watchdog-time byte 1 (MSB) D2 Frequency value byte 2 D2 reserved D3 Frequency value byte 3 (MSB) D3 reserved Control byte B7 B6 B5 B4 B3 B2 B1 B 0 0 0 0 T REQ Set Set RANGE_ RANGE_ VD output output SEL SEL DO 2 DO 1 REQ1 REQ0 T REQ Request to change the Watchdog time (T ) with valid data. VD VD RANGE_SEL REQ1 Selection of the integration time and the representation of measured frequency value. RANGE_SEL REQ0 Selection of the integration time and the representation of measured frequency value. 0 This constant must be set to zero. Status byte B7 B6 B5 B4 B3 B2 B1 B0 X X ST_ T ACK Status Status RANGE_ RANGE_ VD GATE output output SEL SEL DO 2 DO 1 ACK1 ACK0 ST_GATE Status of the GATE input (0=enabled, 1=disabled) T ACK Acknowledgement T changed. VD VD RANGE_SEL ACK1 Acknowledgment to Range Selection, Frequency values are valid. RANGE_SEL ACK0 Acknowledgment to Range Selection, Frequency values are valid. X This value is not evaluated. With the control and status byte the following tasks are possible: Setting the Method of Measuring, Frequency Range and Representation: The method of measuring and the representation depends on the RANGE_SEL REQ bits in the CONTROL byte. Dependent on the adjusted measuring method also the maximum frequency range changes. The following table illustrates the different modes. WAGO-I/O-SYSTEM 750 I/O Modules 750-404/000-003 [Frequency Counter 0.1 Hz-100 kHz] 35 Process Image Measuring RANGE_ RANGE_ Maximum Measured method SEL1 SEL0 frequency range value display Integration over ... 0.1 Hz ... 8 kHz 0 0 1 period Frequency in 1/1000 Hz 0.25 Hz ... 32 kHz 0 1 4 periods Frequency in 1/100 Hz 1 Hz ... 100 kHz 1 0 16 periods Frequency in 1/10 Hz 1 1 16 periods 1 Hz ... 100 kHz Frequency in Hz Attention When a new frequency range is requested, the application has to wait for valid data until the RANGE_SEL ACK bits contain the new frequency range. The maximum delay can be calculated using the following formula: number of periods to be integrated T = 2 Dmax actual frequency If the gate is enabled the input data contains the last valid frequency value. In this state the application cannot request a new range. Attention If the maximum possible frequency of the different ranges is raised (see the table with maximum frequency ratings), the module will return the non valid data 0xFFFFFFFFH. Set Watchdog time: To recognize static CLOCK signals, a watchdog timer is implemented. The standard value for the timer is 10s. The timer resets on every Power On. The application is able to change the watchdog time during operation by using the CONTROL byte. This can be initiated by writing the corresponding value into the output bytes D 1 and D 0 before setting the T REQ bit in the CONTROL byte. VD The success of the parameter transfer is acknowledged by the module via the T ACK bit in the STATUS information. VD WAGO-I/O-SYSTEM 750 I/O Modules 36 750-404/000-003 [Frequency Counter 0.1 Hz-100 kHz] Example Attention The range of the watchdog timer stretches from 0 to 16383ms (0x0000 to 0x3FFF) in steps of 1ms per digit. Values which raise the permitted range of the watchdog timer are masked with 0x3FFF. Set Outputs: Bits 2 and 3 set the additional two outputs of the counter module. 2.1.4.8 Example Changing the Method of Measurement, Frequency and Representation: The frequency counter is set to a measurement range of 1 Hz ... 100 kHz with a resolution of 1/10 Hz and 16 measurement periods. 14.Set the new measurement range with the bits 0 and 1 (RANGE_SEL REQ 0 and 1) in the control byte. Control byte Output bit B7 B6 B5 B4 B3 B2 B1 B0 Value 0 X X X X X 0 1 15.Wait for the feedback from the counter module in the status byte, bit 0 and 1 (RANGE_SEL ACK 1 and 0). The status byte has the following bits: Status byte Input bit B7 B6 B5 B4 B3 B2 B1 B0 Value X X X X X X 0 1 16.After the expiration of the delay the current frequency value with the adjusted resolution then appears in the input data with the following data bytes D0 to D3: Data bytes Input data D3 D2 D1 D0 Value 0x.. 0x.. 0x.. 0x.. WAGO-I/O-SYSTEM 750 I/O Modules 750-404/000-003 [Frequency Counter 0.1 Hz-100 kHz] 37 Example Change the Watchdog Time: The Watchdog time is change to 5000 ms (hexadecimal value 0x1388). 17.Write the new Watchdog time value into the output bytes. The data bytes D0 to D3 of the output data then read as follows: Data bytes Output data D3 D2 D1 D0 0x00 0x00 0x13 0x88 Value 18.With bit 4 (T REQ) in the Control byte the changes are adopted. VD Control byte Output bit B7 B6 B5 B4 B3 B2 B1 B0 Value 0 X X 1 X X X X 19.After feedback of the counter module with bit 4 (T ACK) in the status VD byte the counter works with the new Watchdog time. Status byte Input sbit B7 B6 B5 B4 B3 B2 B1 B0 Value X X X 1 X X X X 20.Reset bit 4 in the control byte. Control byte Outout bit B7 B6 B5 B4 B3 B2 B1 B0 Value 0 X X 0 X X X X 21.The resetting is acknowledged with bit 4 in the status byte. Status byte Input sbit B7 B6 B5 B4 B3 B2 B1 B0 Value X X X 0 X X X X X is used if a value is not relevant. WAGO-I/O-SYSTEM 750 I/O Modules 38 750-404/000-005 [2 Up Counter/16 Bit/5 kHz] View 2.1.5 750-404/000-005 [2 Up Counter/16 Bit/5 kHz] 2 Up Counter 16 Bit, DC 24 V, 5 kHz 2.1.5.1 View 13 14 Status Status A CLOCK 2 C CLOCK 1 B DO 1 D DO 2 CL2 CL1 Data contacts CLOCK 2 CLOCK 1 ++ 24V -- 0V A1 A2 DO 1 DO 2 750-404 /000-005 Power jumper contacts Fig. 2.1.5-1: Up Counter 750-404/000-005 g040412e 2.1.5.2 Description The counter module also can be ordered as two Up Counters with 16 bits counter values; 750-404/000-005. The Up counters are capable of counting binary pulses of DC 24 V at the inputs CLOCK 1 and CLOCK 2 and then transmit the data to the fieldbus. The changes from 0 V to 24 V are counted. The counter can be set or reset with the control byte. The digital outputs DO1 and DO2 can be activated via specific bits in the Control byte. The outputs are short-circuit-protected. The high states of the inputs CLOCK 1 and CLOCK 2 and the output channels are each indicated by a LED. WAGO-I/O-SYSTEM 750 I/O Modules 750-404/000-005 [2 Up Counter/16 Bit/5 kHz] 39 Description An optocoupler is used for electrical isolation between the bus and the field side. Any configuration of the counter modules is possible when designing the fieldbus node. Grouping of module types is not necessary. The field side supply voltage of 24 V for the counter module is derived from adjacent I/O modules or from a supply module. The supply voltage for the field side is made automatically through the individual I/O modules by means of power jumper contacts. Warning The maximum current of the internal power jumper contacts is 10 A. When configuring the system it is important not to exceed the maximum/sum current. However, if such a case should occur, another supply module must be added. Attention This module has no power contacts for receiving and transmitting the ground (earth) potential. A supply module is required, if the adjacent modules need to be connected to the ground. Note Use an appropriate supply module (e.g. 750-602) if an electrically isolated voltage supply is required! The module 750-404/000-005 can be used with all couplers/controllers of the WAGO-I/O-SYSTEM 750 (except for the economy types 750-320, 750-323, 750-324 and 750-327 and the ModBus controllers 750-812, 750-812/025-000 and 750-814). This description is valid for the XXXX3A05... hardware and software versions. The version is specified in the manufacturing number, which is part of the lateral marking on the module. WAGO-I/O-SYSTEM 750 I/O Modules 40 750-404/000-005 [2 Up Counter/16 Bit/5 kHz] Display Elements 2.1.5.3 Display Elements LED Channel Meaning State off Input CLOCK 2: Signal voltage (0) A Status Input CLOCK 2: Signal voltage (1), green CLOCK 2 on Counting pulse 2 13 14 off Digital Output DO 1 reset B Status A green DO 1 A C C on Digital Output DO 1 setting B D B D off Input CLOCK 1: Signalspannung (0) C Status Fig. 2.1.5-2: Display Input CLOCK 1: Signalspannung (1), green CLOCK 1 Elements g041402x on Counting pulse 1 off Digital Output DO 2 setting D Status green DO 2 on Digital Output DO 2 reset 2.1.5.4 Schematic Diagram 5V CLOCK 2 1 5 CLOCK 2 CLOCK 1 270pF CLOCK 1 270pF 2 6 24V 24V 10nF CLK 2 Logic 3 7 0V 0V 10nF CLK 1 270pF 4 8 DO 2 DO DO 1 DO 750-404 /000-005 Fig. 2.1.5-3: Up Counter 750-404/000-005 g040413e WAGO-I/O-SYSTEM 750 I/O Modules 750-404/000-005 [2 Up Counter/16 Bit/5 kHz] 41 Technical Data 2.1.5.5 Technical Data Module Specific Data Number of outputs 2 Number of counters 2 Output current 0.5 A short-circuit-protected Current consumption 75 mA Voltage via power jumper contacts DC 24 V (15 % ... + 20 %) Signal voltage (0): DC 3 V ... +5 V (1): DC +15 V ... +30 V Switching rate 5 kHz (pulse width > 100 µs) max. Input current 5 mA typ. Counter depth 2 x 16 bits data Isolation 500 V (System/Supply) Internal bit width 2 x 16 bits data 8 bits control /status Dimensions (mm) W x H x L 12 x 64* x 100 * from upper edge of 35 DIN rail Weight ca. 55 g Standards and Regulations (cf. Chapter 2.2 of the Coupler/Controller Manual) EMC-Immunity to interference (CE) acc. to EN 50082-2 (96) EMC-Emission of interference (CE) acc. to EN 50081-1 (93) Approvals (cf. Chapter 2.2 of the Coupler/Controller Manual) UL (UL508) C US Class I Div2 ABCD T4A UL (UL1604) C US DNV (Det Norske Veritas) Cl. B II 3 G EEx nA II T4 KEMA Conformity Marking More Information Detailed references to the approvals are listed in the document "Overview Approvals WAGO-I/O-SYSTEM 750", which You can find on the CD ROM ELECTRONICC Tools and Docs (Item-No.: 0888-0412-0001-0101) or in the Internet under: www.wago.com -> Service /Downloads /Documentation /WAGO-I/O-SYSTEM 750/System Description/. WAGO-I/O-SYSTEM 750 I/O Modules 42 750-404/000-005 [2 Up Counter/16 Bit/5 kHz] Process Image 2.1.5.6 Process Image Using the I/O module 750-404/000-005, a 5 byte input and output process image can be transferred to the fieldbus coupler / controller via two logical channels. The transfer of the setting counter values in binary format is made via 4 output bytes (D0, D1) or (D2, D3) and the transfer of the counter reading in binary format is made via 4 input bytes (D0, D1) or (D2, D3). The control byte C0 serves for setting and locking the counters and for setting the outputs. The status byte S0 shows the status of the counters and the inputs and outputs. Attention The representation of the process data of some I/O modules or their variations in the process image depends on the fieldbus coupler/-controller used. Please take this information as well as the particular design of the respective control/status bytes from the section "Fieldbus Specific Design of the Process Data" included in the description concerning the process image of the corresponding coupler/controller. Input data Output data S0 Status byte C0 Control byte D0 Counter value 1 byte 0 (LSB) D0 Set value 1 byte 0 (LSB) D1 Counter value 1 byte 1 (MSB) D1 Set value 1 byte 1 (MSB) D2 Counter value 2 byte 0 (LSB) D2 Set value 2 byte 0 (LSB) D3 Counter value 2 byte 1 (MSB) D3 Set value 2 byte 1 (MSB) Control byte B7 B6 B5 B4 B3 B2 B1 B0 0 0 Set Set Set Set 0 0 counter 1 counter 2 output output DO 2 DO 1 0 This constant must be set to zero. Status byte B7 B6 B5 B4 B3 B2 B1 B0 X X Counter Counter actual actual actual actual is set is set signal at signal at signal at signal at output output input input DO 2 DO 1 CLOCK CLOCK 2 1 X his value is not evaluated. WAGO-I/O-SYSTEM 750 I/O Modules 750-404/000-005 [2 Up Counter/16 Bit/5 kHz] 43 Example With the control and status byte the following tasks are possible: Set Counter: Put Bit 5 (4) into the control byte. The counter 1 (2) with the 16 bit value is loaded into output bytes 0 (1) or 2 (3). As long as the bit is set, the counter can stop and information is stored. The ensuing data of the counter will be conveyed to the status byte. Bit 5 (4) in the status byte communicates the successful load of the counter. Set Outputs: Bits 2 and 3 set the additional two outputs of the counter module. 2.1.5.7 Example Set Counter 1: First of all the counter reading is set to 100 by "Setting counter", i. e. to the hexadecimal value: 0x64. 22.Enter the set value in the output data. The data bytes D0 to D3 of the output data then read as follows: Datenbytes Output data D3 D2 D1 D0 Value 0x00 0x00 0x00 0x64 23.Validate the counter reading in the control byte with bit 5 (setting counter 1) to have it adopted as an output value. The control byte has the following bits: Steuerbyte Output bit B7 B6 B5 B4 B3 B2 B1 B0 Value 0 X 1 X X X X X 24.Wait for the feedback from the counter module in the status byte, bit 5 (counter 1 set). The status byte has the following bits: Statusbyte Input bit B7 B6 B5 B4 B3 B2 B1 B0 Value X X 1 X X X X X 25.Delete bit 5 (setting counter 1) in the control byte in order to finish the Handshake. The bits in the control byte read as follows: Steuerbyte Output bit B7 B6 B5 B4 B3 B2 B1 B0 Value 0 X 0 X X X X X 26.The set counter reading then appears in the input data with the following data bytes D0 to D3: Data bytes Input data D3 D2 D1 D0 Value 0x00 0x00 0x00 0x64 WAGO-I/O-SYSTEM 750 I/O Modules 44 750-404/000-005 [2 Up Counter/16 Bit/5 kHz] Example 27.Wait for the first and further count pulses. During counting, the data bytes D0 to D3 of the input data appear as follows: Data bytes Remark D3 D2 D1 D0 no count pulse 0x00 0x00 0x00 0x64 received 1st count pulse 0x00 0x00 0x00 0x65 received 2nd count pulse 0x00 0x00 0x00 0x66 received Further count pulses ........ ........ ........ ........ Max. counter reading 0x00 0x00 0xFF 0xFF reached the next count pulse 0x00 0x00 0x00 0x00 causes a number overflow One further count 0x00 0x00 0x00 0x01 pulse received X is used if a value is not relevant. WAGO-I/O-SYSTEM 750 I/O Modules 750-404/000-005 [2 Up Counter/16 Bit/5 kHz] 45 Example WAGO-I/O-SYSTEM 750 I/O Modules WAGO Kontakttechnik GmbH & Co. KG Postfach 2880 G-32385 Minden Hansastraße 27 G-32423 Minden Phone: 05 71/8 87 0 Fax: 05 71/8 87 1 69 E-Mail: info@wago.com Internet: http://www.wago.com
Frequently asked questions
What makes Elite.Parts unique?

What kind of warranty will the 750-404/000-003 have?

Which carriers does Elite.Parts work with?

Will Elite.Parts sell to me even though I live outside the USA?

I have a preferred payment method. Will Elite.Parts accept it?

Why buy from GID?
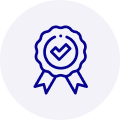
Quality
We are industry veterans who take pride in our work
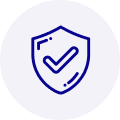
Protection
Avoid the dangers of risky trading in the gray market
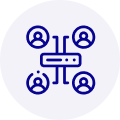
Access
Our network of suppliers is ready and at your disposal
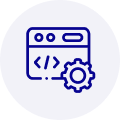
Savings
Maintain legacy systems to prevent costly downtime
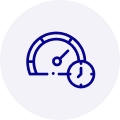
Speed
Time is of the essence, and we are respectful of yours
What they say about us
FANTASTIC RESOURCE
One of our top priorities is maintaining our business with precision, and we are constantly looking for affiliates that can help us achieve our goal. With the aid of GID Industrial, our obsolete product management has never been more efficient. They have been a great resource to our company, and have quickly become a go-to supplier on our list!
Bucher Emhart Glass
EXCELLENT SERVICE
With our strict fundamentals and high expectations, we were surprised when we came across GID Industrial and their competitive pricing. When we approached them with our issue, they were incredibly confident in being able to provide us with a seamless solution at the best price for us. GID Industrial quickly understood our needs and provided us with excellent service, as well as fully tested product to ensure what we received would be the right fit for our company.
Fuji
HARD TO FIND A BETTER PROVIDER
Our company provides services to aid in the manufacture of technological products, such as semiconductors and flat panel displays, and often searching for distributors of obsolete product we require can waste time and money. Finding GID Industrial proved to be a great asset to our company, with cost effective solutions and superior knowledge on all of their materials, it’d be hard to find a better provider of obsolete or hard to find products.
Applied Materials
CONSISTENTLY DELIVERS QUALITY SOLUTIONS
Over the years, the equipment used in our company becomes discontinued, but they’re still of great use to us and our customers. Once these products are no longer available through the manufacturer, finding a reliable, quick supplier is a necessity, and luckily for us, GID Industrial has provided the most trustworthy, quality solutions to our obsolete component needs.
Nidec Vamco
TERRIFIC RESOURCE
This company has been a terrific help to us (I work for Trican Well Service) in sourcing the Micron Ram Memory we needed for our Siemens computers. Great service! And great pricing! I know when the product is shipping and when it will arrive, all the way through the ordering process.
Trican Well Service
GO TO SOURCE
When I can't find an obsolete part, I first call GID and they'll come up with my parts every time. Great customer service and follow up as well. Scott emails me from time to time to touch base and see if we're having trouble finding something.....which is often with our 25 yr old equipment.
ConAgra Foods