CISSELL PT46
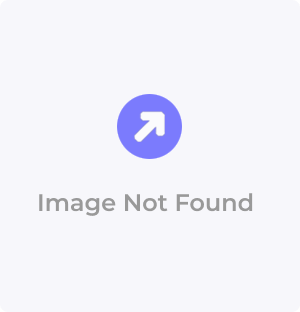
Description
Cissell PT46 Spring Negator, electric motor 1/3 H.P., 115V. or 230V., 60 cycle, AC,
1 phase 220V., 50 cycle, AC, and 1 phase. Operating steam pressure of 100 P.S.I.G.
(5.8 bars) maximum, boiler horsepower (approximate) of 3/4 (7.3kw), steam supply
line consist of 1/2” pipe (1.3 cm), and the steam return line consist of 1/2” pipe
(1.3 cm). Air supply connection consist of 1/8” pipe (.32 cm) and the air supply requirement of 80 P.S.I.G., 6 C.F.M. (4.4 bar and 2 C.M.M.).
Part Number
PT46
Price
Request Quote
Manufacturer
CISSELL
Lead Time
Request Quote
Category
PRODUCTS - P
Datasheet
Extracted Text
Pants Topper Model A Model B 24 Volt OWNER’S MANUAL CISSELL MANUFACTURING COMPANY HEADQUARTERS PHONE: (502) 587-1292 831 SOUTH FIRST ST. SALES FAX: (502) 585-3625 P.O. BOX 32270 SERVICE/PARTS FAX: (502) 681-1275 LOUISVILLE, KY 40232-2270 THIS MANUAL MUST BE GIVEN TO THE EQUIPMENT OWNER. MAN594 05/00 Page 1 WARRANTY The Cissell Manufacturing Company (Cissell) warrants all new equipment (and the original parts thereof) to be free from defects in material or workmanship for a period of one (1) year from the date of sale thereof to an original purchaser for use, except as hereinafter provided. With respect to non-durable parts normally requiring replacement in less than one (1) year due to normal wear and tear, including, but not limited to, cloth goods, valve discs, hoses, and iron cords, and with respect to all new repair or replacement parts for Cissell equipment for which the one (1) year warranty period has expired, or for all new repair or replacement parts for equipment other than Cissell equipment, the warranty period is limited to ninety (90) days from date of sale. The warranty period on each new replacement part furnished by Cissell in fulfillment of the warranty on new equipment or parts shall be for the unexpired portion of the original warranty period on the part replaced. With respect to electric motors, coin meters and other accessories furnished with the new equipment, but not manufactured by Cissell, the warranty is limited to that provided by the respective manufacturer. Cissell's total liability arising out of the manufacture and sale of new equipment and parts, whether under the warranty or caused by Cissell's negligence or otherwise, shall be limited to Cissell repairing or replacing, at its option, any defective equipment or part returned f.o.b. Cissell's factory, transportation prepaid, within the applicable warranty period and found by Cissell to have been defective, and in no event shall Cissell be liable for damages of any kind, whether for any injury to persons or property or for any special or consequential damages. The liability of Cissell does not include furnishing (or paying for) any labor such as that required to service, remove or install; to diagnose troubles; to adjust, remove or replace defective equipment or a part; nor does it include any responsibility for transportation expense which is involved therein. The warranty of Cissell is contingent upon installation and use of its equipment under normal operating conditions. The warranty is void on equipment or parts; that have been subjected to misuse, accident, or negligent damage; operated under loads, pressures, speeds, electrical connections, plumbing, or conditions other than those specified by Cissell; operated or repaired with other than genuine Cissell replacement parts; damaged by fire, flood, vandalism, or such other causes beyond the control of Cissell; altered or repaired in any way that effects the reliability or detracts from its performance, or; which have had the identification plate, or serial number, altered, defaced, or removed. No defective equipment or part may be returned to Cissell for repair or replacement without prior written authorization from Cissell. Charges for unauthorized repairs will not be accepted or paid by Cissell. CISSELL MAKES NO OTHER EXPRESS OR IMPLIED WARRANTY, STATUTORY OR OTHERWISE, CONCERNING THE EQUIPMENT OR PARTS INCLUDING, WITHOUT LIMITATION, A WARRANTY OF FITNESS FOR A PARTICULAR PURPOSE, OR A WARRANTY OF MERCHANTABILITY. THE WARRANTIES GIVEN ABOVE ARE EXPRESSLY IN LIEU OF ALL OTHER WARRANTIES, EXPRESS OR IMPLIED. CISSELL NEITHER ASSUMES, NOR AUTHORIZES ANY PERSON TO ASSUME FOR IT, ANY OTHER WARRANTY OR LIABILITY IN CONNECTION WITH THE MANUFACTURE, USE OR SALE OF ITS EQUIPMENT OR PARTS. For warranty service, contact the Distributor from whom the Cissell equipment or part was purchased. If the Distributor cannot be reached, contact Cissell. Page 2 TABLE OF CONTENTS ——————————————————————————————————————————— Warranty ....................................................................................................................................2 Specifications, General Information ........................................................................................... 4 Dimension Drawings .................................................................................................................. 5 Steam Connection Instructions ...................................................................................................6 Steam Connections Illustration ................................................................................................... 7 Electrical Connections ................................................................................................................ 8 Maintenance Instructions ............................................................................................................ 9 Operating Instructions ......................................................................................................... 10-12 Replacing Control Switches Instructions .................................................................................. 13 Air Pressure Control Operation ................................................................................................ 14 Installation of Bag and Boots ...................................................................................................15 Pants Topper Bag, Steam Leaks .............................................................................................. 16 Pleat Setter Cover Assembly and Adjustment .......................................................................... 17 Plastic Sleeve, Bearing Adjustment .......................................................................................... 18 Motor and Blower Assembly Removal ..................................................................................... 19 Belt Tension Adjustment, Pulley Alignment ............................................................................. 19 Installation of Foot Switch ........................................................................................................ 20 ILLUSTRATED PARTS Overall View ............................................................................................................................. 21 Overall View ............................................................................................................................. 22 Motor and Blower Assembly .................................................................................................... 23 Control Switches and Air Cylinder ...................................................................................... 24-26 Piping and Tubing .................................................................................................................... 27 Solenoid Valve Parts ................................................................................................................. 28 Air Line Assembly .................................................................................................................... 29 Electric Control Box ................................................................................................................. 30 Wiring Diagram ........................................................................................................................ 31 Page 3 SPECIFICATIONS Electric Motor........................................ 1/3 H.P., 115V. or 230V., 60 Cycle, AC, 1 Phase ........................................................... 220V., 50 Cycle, AC, 1 Phase Operating Steam Pressure..................... 100 P.S.I.G. (5.8 Bars) Maximum Boiler Horsepower (Approx.).................. 3/4 (7.3 kw) Steam Supply Line................................. 1/2” Pipe (1.3 cm) Steam Return Line............................................. 1/2” Pipe (1.3 cm) *Air Supply Connection................................... 1/8” Pipe (.32 cm) *Air Supply Requirement................................. 80 P.S.I.G., 6 C.F.M. (4.4 Bar, 2 C.M.M.) Net Weight Model A......................................... 200 Pounds (100 kg) Net Weight Model B.......................................... 230 Pounds (104.5 kg) Note: Specifications are subject to change without prior notice. GENERAL INFORMATION *IMPORTANT: The air line filter was removed from the machine for shipping. When installing the unit, fasten the air line filter to the regulator as shown in the “Air Line Assenbly” drawing in the Parts section of this manual. UNCRATING: Set crate upright, remove sides and top. Remove the two rear base bolts and lift from crate. PROTECTIVE PLASTIC COVER: Do not remove plastic cover from the nylon pants topper bag until machine is installed and is ready for operation. AUTOMATIC STEAM TIMER: The Automatic Steam Timer (A) is adjustable from 0 to 60 seconds, and is set at the factory for 4 seconds normal steaming. Adjust as required. AUTOMATIC AIR TIMER: The Automatic Air Timer (B) is adjustable for 0 to 60 seconds and is factory set for 25 seconds for normal drying. Adjust as required. *MODEL B ONLY Page 4 PANTS TOPPER - DIMENSION DRAWINGS Dimensions given in inches plus/minus 1/2” and are subject to change without prior notice Page 5 STEAM CONNECTIONS Make Steam Supply and Steam Return connections as shown in Figure 2. All horizontal runs must drain by gravity to respective Steam Header. Portions that connot drain to Header must drain by gravity to machine, without water pockets. Each Steam Header must drain, by gravity, to boiler or condensate return tank. To prevent condensate draining from Steam Headers to machine, make steam connections (to each respective Header) with a 12 inch or more vertical riser. Do not make steam connections to a Header with a horizontal or downwardly facing tee or elbow. Water pockets, or an improperly drained steam line (or header), will provide wet steam, causing unnecessary wetting-out of buck padding. Before installing check valve, trap and strainer, connect steam supply to machine from globe valve (A). Open globe valve (A) to flush any foreign matter that may be in castings or pipes; open globe valve (C) to flush foreign matter from return connections, then connect steam return from valve (C) to machine with check valve, trap, and strainer as shown. If steam is gravity returned to boiler, omit trap. NOTE: For successful operation of machine, install trap as close to floor and as near machine as possible. Inspect trap carefully for inlet and outlet marks and install according to manufacturer’s instructions. IMPORTANT: A separate steam trap must be used with each machine. CAUTION BEFORE OPERATING PANTS TOPPER, OPEN GLOBE VALVES IN STEAM LINES. CHECK CAREFULLY FOR STEAM LEAKS, AND SEE THAT TRAP IS OPERATING PROP- ERLY. UNDER NO CIRCUMSTANCES SHOULD MACHINE BE OPERATED UNTIL HOT. OPERATING THE MACHINE COLD WILL WET THE NYLON BAG AND PADDING. TO DRY A WET BAG OR PAD, DEPRESS THE “ON” MANUAL AIR SWITCH. AIR WILL OPERATE CONTINOUSLY UNTIL “OFF” AIR SWITCH IS DEPRESSED. Page 6 Page 7 ELECTRICAL CONNECTIONS THE STANDARD Pants Topper has single phase motors. Before installation, check nameplates on motor and control box for rated voltage and current specifications. MAKE ELECTRICAL CONNECTIONS as indicated on wiring diagram attached to inside cover of electrical junction box on Topper. Voltage and current of power line must be the same as the Electrical Specifications of the motor, timers, relays, and solenoid. FOR SINGLE PHASE CURRENT, connect power leads, L1 and L2, to an approved fused discon- nect switch in power line. TO CONNECT STANDARD, SINGLE PHASE MACHINE TO THREE PHASE CURRENT, con- nect power leads, L1 and L2, to any two terminals of an approved fused disconnect switch in the three phase power line. FOR THREE PHASE CURRENT, connect power leads L1, L2, and L3 to the three terminals of an approved fused disconnect switch in the three phase power line. The motor must rotate clockwise when facing the belt and pulley. If rotation is incorrect, transpose any two leads connecting the power line, and rotation of motor will reverse. IMPORTANT: Consult your local electrical code before making any electrical connections; be certain that the electrical installation conforms with all local requirements. Always check wiring before closing the disconnect switch. Page 8 MAINTENANCE INSTRUCTIONS IMPORTANT - Shut-off steam and electric power before performing Maintenance Operations. Compressed air should also be cut off. ELECTRIC MOTOR LUBRICATION: SLEEVE BEARINGS: Motors with wool-packed sleeve bearings are oiled at the factory for two years normal operation. After two years normal operation, add annually 1/2 teaspoon electric motor oil or SAE-10 to each bearing. For 24 hours per day operation, add one teaspoon of oil annually. BALL BEARING: Motors having ball bearings are packed with sufficient grease for approxi- mately TEN YEARS of normal operation. After ten years of normal operation, the bearings and housing should be cleaned thoroughly. Repack each bearing and the cavity back of the bearing 1/ 3 full with G. E. Ball Bearing grease. CHECK VOLTAGE AND CURRENT: Your Topper is wired for a given voltage and current as stamped on name plate. Motor, Timers, Relays and Solenoid are for Single Voltage and Single current only. If machine is to be operated on any voltage and current, other than apecified above, THE MOTOR, RELAYS, TIMERS AND SOLENOID MUST BE REPLACED WITH UNITS CORRESPONDING TO THE VOLTAGE AND CURRENT ON WHICH THEY ARE TO BE OPERATED. GENERAL CLEANING: Every six months remove top cover, rear panel, front panel, blower and belt guards and clean thoroughly with a vacuum cleaner or air hose. AIR LINE OIL LUBRICATOR (MODEL B) Check Air Line Oil Lubricator and refill when less than half full. Use #10 weight oil. Page 9 POSITIONING PANTS ON TOPPER OPERATING INSTRUCTIONS (A) At “Start-Up” (or after “Idle Periods” of operation) preheat before operating: a. Lower pleat clamps onto padded buck; Operate Topper on “Manual Air” continuously for about one (1) minute. (B) Either PRE-STEAM or AUTOMATIC Steam-Air cycle may be cancelled by pushing “OFF” Air Switch fully down. (C) For Suede, Chamois or leather trimmed trousers, use manual air switch to provide air “while steaming”, as full air pressure is required to hold pants taut during steaming cycle. (D) Tops Trousers, slacks, shorts (Lightweight or Heavyweight) sizes 28 to 50. NOTE: Top small sizes, (including boys pants and small size ladies slacks) on 1M Puff Iron. Top large sizes on end of utility press. Page 10 OPERATING INSTRUCTIONS MODEL A CAUTION: Timer Adjustments STEAM: Must not be greater than 6 seconds AIR: Must not be less than 20 seconds (Average setting 4-5 Seconds) (Average Setting 25 Seconds) NOTE: Straighten Pockets; Button Pocket Flaps; Button or Snap front of Waist Band, But Do Not Close Zipper. 1. Grip rear top portion of bag and puff waist expander forward until it locks. 2. Lift trousers onto form, placing back center of waist band high onto waist expander. Pull trousers forward; hook, button or snap front of waist band. Do not close zipper of pants. 3. Continue to hold forward tension on trousers and push “bag release” knob. Allow automatic tension of waist expander to draw front of trousers onto face of buck. 4. Adjust and center pants to highest position on buck. Align crotch; do not raise pants too high as crotch must remain loose in buck opening to prevent wrinkling of crotch area. 5. To soften pleats (Before making respective pleat lays), push PRE-STEAM BUTTON. Steam Timer controls pre-steaming automatically. NOTE: Excessive moisture will de-lusterize Rayon acetates. This may be minimized by using “air” while steaming; or shortening of steam cycle by depressing fully “off” air switch. Do not use the pre-steaming operation on rayon acetates. 6. Smooth out material and lay each pleat separately, working from fly toward pleat being layed. Align pleat with leg crease; close pleat holder. If too much material is encountered during laying of pleats, trousers are too high on the buck and too low on the rear expander. If too little material is available to lay the pleat properly, the trousers may be too low on the buck and too high on the expander. 7. Push AUTOMATIC Button. Steam and Air Timers control steam followed by air automatically. Leg-out during the final phase of the automatic cycle of the Topper. 8. Place creased trousers on hanger and make necessary touch-ups on Puff Iron before placing pants on finish rail. Page 11 OPERATING INSTRUCTIONS MODEL B CAUTION: Timer Adjustments STEAM: Must not be greater than 6 seconds AIR: Must not be less than 20 seconds (Average setting 4-5 Seconds) (Average Setting 25 Seconds) NOTE: Straighten Pockets; Button Pocket Flaps; Button or Snap front of Waistband if you desire, But Do Not Close Zipper. 1. Step on foot switch and the waist expander moves forward automatically. 2. Lift trousers onto form, placing back center of waist band high onto waist expander. Pull trousers forward holding taught at fly. 3. Continue to hold forward tension on trousers, step off foot switch. Allow automatic tension of waist expander to draw front of trousers onto face of buck. 4. Lower waist clamp, clamp trousers to buck. 5. Adjust and center pants to highest position on buck. Align crotch; do not raise pants too high as crotch must remain loose in buck opening to prevent wrinkling of crotch area. 6. To soften pleats (Before making respective pleat lays), push PRE-STEAM BUTTON. Steam Timer controls pre-steaming automatically. NOTE:Excessive moisture will de-lusterize Rayon acetates. This may be minimized by using “air” while steaming; or shortening of steam cycle by depressing fully “off” air switch. Omit pre-steaming operation. 7. Smooth out material and lay each pleat separately, working from fly toward pleat being layed. Align pleat with leg crease; close pleat holder. If too much material is encountered during laying of pleats, trousers are too high on the buck and too low on the rear expander. If too little material is available to lay the pleat properly, the trousers may be too low on the buck and too high on the expander. 8. Push AUTOMATIC Button. Steam and Air Timers control steam followed by air automatically. 9. Leg-out during the final phase of the automatic cycle of the Topper. To remove trouser from buck step on foot switch again. 10. Place creased trousers on hanger and make necessary touch-ups on Puff Iron before placing pants on finish rail. Page 12 REPLACING THE CONTROL SWITCHES 1. Refer to illustration. 2. Cut off steam and electrical supply. Allow machine to cool. 3. Remove top panel. 4. Disconnect switch leads. 5. Remove switch mounting screws. 6. Remove old switches and nylon spacers. 7. Install new switches and spacers in reverse order. Page 13 AIR PRESSURE CONTROL OPERATION Normally, set the air pressure control knob horizontally in the position illustrated, (Fig. 1). For light weight materials (which may be stretched), set the control knob in the LOW position, (or to any intermediate position), to give the desired air pressure. If desired, the topper may be operated continuously with the control knob set in a postion providing the air pressure found most suitable by the operator. INSTRUCTIONS FOR OPERATING AIR PRESSURE CONTROL 1. Turn off electric power and remove Top Cover. Note: Check to see that the set screw of the Knob is tighten securely against the flat on the end of the rod. 2. Place the pointer of the control knob at the low position (Fig. 2), with damper fully closed, push the pin on the damper stop (in center of rod) down until it hits the damper, tighten set screw securely. 3. Rotate the pointer upward until the knob is in a horizontal position (Fig. 3), push the pin on the control knob stop (on the end of rod) against the damper frame as shown in Fig. 3. Tighten set screw securely. Page 14 INSTALLATION OF BAG & BOOTS 1. Place bag in position on buck, Fig. 1. Center top edge of Pants Topper bag with center of waist clamp (A). Install retainer (B) over drawstring sheath (X), Fig. 2 or 2A. Tighten three sheet metal screws. Open zipper (C) Fig. 1. 2. Loop drawstring over spool (N) Fig. 2 or 2A. Place drawstring sheath in groove (Y). Loop drawstring around spool (P) as shown; pull loose ends of drawstring tightly and tie-off at(Z). 3. Place expander assembly (D) Fig. 4 inside of bag on slide stud (E) and fasten securely with wing nut (F). 4. Align Pants Topper Bag (G) on buck (Fig. 1). Slip drawstring (M) over spool (J)Fig. 3. Pull drawstrings tight toward top of buck so that drawstring sheath (K) is equally distributed around outer edges of perforated metal buck (H). Holding strings tight, tie-off to eyelet (L). 5. Install Buck springs (S) by placing hooks over drawstring through sheath (K) as illustrated in Fig. 3. INSTALLATION OF BOOTS Pull boots (R) Fig. 3 up for removal. To install new boots, pull down over frames. See that boot frames are tight against buck. Page 15 PANTS TOPPER BAG KEEP BAG CLEAN. In operation, bag collects dust, lint, etc., greatly reducing its efficiency. Launder bag at frequent intervals as determined by its soiled condition. The Cissell Pants Topper bag has a double liner to extend pad life and to distribute steam uniformily. REPAIR HOLES OR WORN SPOTS in bag to extend its useful life: REPLACE when worn be- yond repair. A defective or worn bag will cause topper to operate unsatisfactorily. KEEP A SPARE BAG IN STOCK. CAUTION Use only genuine CISSELL bags. The fabric for the Cissell Bag is especially woven (and cut to an exact pattern) to give the correct porosity and shape for proper steaming and drying. Rember, your CISSELL PANTS TOPPER depends on the bag for proper operation. Correct padding is necessary to obtain proper finishing. The Cissell buck pad is constructed of a high, heat-resisting synthetic air foam, and perforated for rapid steaming and full air flow through entire buck area. Replace a worn-out pad only with a Cissell perforated pad. Keep a spare pad in stock. Do not use more than 1 pad. RESEALING EDGES FOR STEAM & CONDENSATE LEAKS When leak appears: 1. Remove top. 2. Using sealing compound Permatex #2 or equivalent; (3 oz. tubes available from factory). Generously apply sealing compound evenly along area of “Leak”. Allow sealing compound to set and air dry for approx. 2 hours before putting topper back in service. Sealing compound will not harden. If necessary, remove switches from control box in Nose, when fixing leaks in this area. Page 16 PLEAT SETTER COVER ASSEMBLY INSTALLATION 1. Place cover over pleat clamp (E), pull draw strings (K) tight and tie. See illustration below. 2. Hook one end of each pleat clamp spring (M) on left side of cover, pull tight and hook on right side. Adjustable Clamp Support OVAL PLEAT CLAMP ADJUSTMENT WITH ADJUSTABLE CLAMP SUPPORT REFER TO ILLUSTRATION ABOVE. 1. Remove cover from side of unit. Loosen cap screw (A) in arm expander and cap screw (B) in adjustable support. 2. Rotate and slide arm (C) in counterweight (D) to position pleat clamp (E) on buck. Place pleat clamp in vertical position and align inside edge of pleat clamp with edge of buck crotch (F). 3. Apply pressure on arm knob (G) to provide pressure between pleat clamp (E) and buck. Hold pressure and retighten cap screw (A) of arm expander. 4. With a thin card (H) check uniformity of pressure between edges of pleat clamp (E) and buck. If unequal, rotate pleat clamp slightly to obtain a uniform pressure around all edges. 5. Re-tighten nut (B) of adjustable support. Note: Whenever tightening nut (B), do not apply pressure to knob (G) or arm (C), as this will distrub the pleat clamp setting. 6. Top a pair of trousers. A. If pleat clamp (E) makes an impression (too tight), loosen cap screw (B) and rotate adjustment nut (J) counter-clockwise to reduce pressure. Retighten cap screw (B). B. If pleat clamp does not hold pleat (too loose), loosen cap screw (B) and rotate adjustment nut (J) clockwise to increase pressure. Retighten cap screw (B). NOTE: Each pleat clamp must engage the padded buck uniformily with a slight pressure. Heavy pressure may produce a hard finish and show seam imprinting. A very light pressure may allow pleat lay to shift during the air cycle, and show wrinkles with an improperly shaped pleat. Adequate holding of the pleat lay during the air cycle is aided by the surface texture of the pleat clamp and the buck cover. Page 17 PLASTIC SLEEVE, BEARING ADJUSTMENT PLASTIC SLEEVE POSITION AND TAPING FIG. 1 1. Position plastic sleeve on arm in center of arm guide, and align slot with hole in arm. Fasten plastic sleeve securely with #8 Tap Tight Screw at “A” (Fig. 1). 2. Position end of cloth arm cover in contact with end of plastic sleeve. 3. Using Scotch Brand pressure sensitive Tape #471 or equivalent; (Tape available from Factory) Tape Plastic Sleeve at “B” securely attaching end of Sleeve to cloth arm cover. (Minimum 2-3 wraps) Pull end of cloth arm cover at “C” to remove slack. Tape cloth arm cover at “C” securely attaching end of cover to arm. BEARING ADJUSTMENT FIG. 1 To Adjust Bearing: 1. Remove Top 2. Loosen 1/4" machine screw holding the bearing rod to the metal bracket. 3. Slide screw in hole of bracket to bring the plastic sleeve into contact with the outer face of the arm guide. 4. Hold the “E” Ring on the Bearing Rod against outer face of counterweight and retighten 1/4" screw. 5. Re-install top on machine. RESEALING EDGES FOR STEAM & CONDENSATE LEAKS FIG. 2 When Leak Appears: 1. Remove Top 2. Using sealing compound Permatex #2 or equivalent: (3 oz. tubes available from factory) Generously apply sealing compound evenly along of “Leak”. Allow sealing compound to set and air dry for approx. 2 hours before putting Topper back in service. Sealing compound will not harden. If necessary, remove switches from control box in Nose, when fixing leaks in this area. Page 18 MOTOR AND BLOWER ASSEMBLY REMOVAL IMPORTANT: Before performing service, turn off power, close steam lines and allow machine to cool. 1. Remove Blower Guard (A) and Belt Guard (B). 2. Remove Belt (C) and Sheaves (D) & (E). 3. Remove wires from motor. 4. Remove Screw, Lockwasher, and Washer (F) from both ends of Motor Support (G). Remove Motor and Support from Housing (X). 5. Remove Rear Access Panel (H). 6. Remove Thrust Collar (I) from Blower Shaft (J). 7. Remove Blower Housing (K). 8. Remove Cut-Off Panel (L) and lift Blower Wheel (M). NOTE: To re-install, reverse procedure. When placing Blower Wheel in Housing, be sure blades are cupped towards rectangular opening. Be sure that the two sheaves have the set screws facing the outside. BELT TENSION ADJUSTMENT AND PULLY ALIGNMENT Improper belt tension or misalignment of pulleys may cause bearing and/or belt failures The illustration at the right indicates recommended belt tension, determined by grasping the belt as shown and when normal pressure is applied, a deflection of approximately one inch will occur. If the deflection is much more than indicated, slippage may occur and wear out the belt. If deflection is less than indicated, the belt is too tight and will shorten the life of the bearings. Excessive tension will actually pull the shaft through the oil film and allow metal to metal contact. Noisy blower operation will also occur. The illustration at the right shows the preferred method for checking correct alignment of the pulleys. Excessive misalignment produces increased belt wear and can produce lateral motion of the wheel and shaft to the point that considerable noise can develop. Page 19 FOOT SWITCH REPLACEMENT (Part No. AF177) INSTRUCTIONS - Refer to illustration. 1. Turn Switch upside down and remove screws (A). 2. Lift off base plate pad. 3. Remove screws (B). 4. Remove washers, plate, insulation, and switch. 5. Remove wires from old switch and install on new switch. 6. Re-install switch, insulation, plate, washers, screws, base plate, screws. Foot Switch Assembly - Part No. PT527 Page 20 OVERALL VIEW Ref. No. Part No. Description Ref. No. Part No. Description 1 PT143 Steam Seals 22 PT153 Steam Coil Support 2 PT500 Damper Frame 23 PT97 Steam Chamber 3 PT499 Damper 24 F226 Pipe, 1/2” x 7” (2,3,hdwr)PT502 Damper Frame Asm 25 F225 Spacer Ring 4 V345 Spring 26 TU8013 Cissell Nameplate 5 PT116 Spring Glands & Sleeve 27 PT29 Steam Coil 6 PT22 Large Steam Boot 28 PT596 Housing 7 PT20 Large Boot Rod 29 PT109H Air Adjustment Plate 8 PT548 Small Steam Boot 34 PT108 Valve Bracket 9 PT52 Spring 35 F1289 Solenoid Valve, 24V 10 PT146 Damper Adjustment Knob 36 PT706 Control Box, 120V 11 PT113 Damper Stop w/screw 37 PT398 3\8” x 5” cable 12 PT144 Damper Adjustment Rod 38 PT2 Housing Top 13 PT127 Steam Shield 14 PT474 Bag/Pad Assembly 15 PT75 Bag Retainer 16 PT3 Front Panel 18 PT8 Spool Guide 19 AT348 Buck 20 PT23 Coil Clamp 21 PT6 Coil Holder Page 21 OVERALL VIEW Ref. No. Part No. Description Ref. No. Part No. Description 1 PT549 Left Arm Cover 17 PT596 Housing 2 PT613 Right Arm Cover 3 PT551 Counterweight 18 PT559 Belt Guard 4 PT57 Arm Expander 19 PT557 Left Arm 5 PT563 Pivot Spacer 20 TU7733 #8 x 1/2” Screw 6 PT552 Shaft 21 PT31 Plastic Sleeve 7 P104 Washers 22 PT589 Arm Cover 8 TU4934 1/4” Hex Nut 23 TP165 Long Spider 9 IB76 Bearings 24 PT166 Support Assembly 10 PT211 “E” Ring 25 PT32 Oval Pleat Clamp 11 SG053 “E” Ring 26 PT42 Arm Knob 12 PT595 Pin 27 601603103 1/4 - 28 x 1/2" Hex Screw 13 PT594 Spring 28 PT52 Clamp Spring 14 TU2105 Activator Spring 29 PT588 Right Arm 15 PT624 Arm Latch 30 FG267 1/4 - 20 x 1 1/4" Hex Screw 16 PT558 Blower Guard Page 22 MOTOR AND BLOWER ASSEMBLY Ref.No. Part No. Description 1 TU2318 Motor Sheave (110V) F1034 Motor Sheave (220V) 2 F1033 Gear Sheave (60HZ) PT219 Gear Sheave (50HZ) 3 PT87 V-Belt (60HZ) PT227 V-Belt (50HZ) 4 PT80 Blower Assembly 5 F374 Thrust Washer 6 F371 Bearing Assembly 7 F373 Bearing Insulator Cup z 8 F372 Thrust Collar 9 F366 Shaft, 3/4” x 16 1/2” 10 PT89 Blower Housing 11 F368 Blower Wheel 12 F367 Cut-Off Assembly 13 PT180 Rear Access Panel 14 PTA47 Motor Support 15 F365 Belt Adjustment Assembly MTR74 110V/60HZ MTR88 220V/50-60HZ Page 23 MODEL A Ref. No. Part No. Description Ref. No. Part No. Description 1 PT49 Release Latch Spring 12 PT71 Spring Bobbin w/bearings 2 PT68 Release Latch Assembly 13 TU49 Bearings 3 PT164 Drawstring Tie-off 14 PT28 Slide Assembly 4 TU9028 Push Button Switch 15 PT152 Bearing Spacer 5 PT142 Air Switch Support Plate 16 PT46 Negator Spring 6 PT107 Switch Spacer 17 PT61 Spring Guide 7 PT74 Manual Air Switch 18 PT27 Track 8 PT18 Control Plate 19 PT63 Slide Stop 9 OP182 Control Knob 20 PT62 Spring Lock Pivot Screw 10 PT44 Bag Release Rod 21 AT397 Waist Expander Assy. 11 PT72 Bobbin Mounting Bracket 22 PT34 Wing Nut Page 24 MODEL B Ref.No. Part No. Description 1 653227045 Track Support 2 TU3486 #8 x 1-1/4” Screw 3 PT27 Track 4 PT657 Slide Channel 5 PT357 1/4” - 20 x 3/4” Bolt 6 PT28 Slide Assembly 7 TU2846 1/4” Split Lock Washer 8 PT62 Spring Lock Pivot Screw 9 TU2847 1/4” Flat Washer 10 PT693 Bracket, Attachment 11 TU4934 1/4” - 20 Hex Nut 12 PT696 Nut, Mounting Cylinder Page 25 CONTROL SWITCHES MODEL B Ref.No. Part No. Description 1 TU9028 Push Button Switch 2 PT518 Support Plate 3 PT164 Drawstring Tie Off 4 PT74 Manual Air Switch 5 PT517 Control Plate 6 TU7733 #8 x 1/2” Self-Drill Screw 7 PT526 Waist Clamp Arm Assembly 8 PT524 Waist Clamp PT530 Cloth Cover 9 PT34 Wing Nut 10 PT107 Switch Spacer Page 26 PIPING AND TUBING Ref. No. Part No. Description Ref. No. Part No. Description 1 PT9 Spray Bin Pipe w/Elbow 12 SF59 1/4 x 3/8 Straight Conn. (3) & Adapter 13 FB75 3/8 x 1/2 Straight Conn. (4) 2 PT17 Spray Gun Manifold 14 J 3 Small Hose Clamp 3 PT45 Control Switch Conduit 15 OP329 Large Hose Clamp w/Connectors 16 SG37 Water Hose Assembly (5’) 4 PT91 Buck Steam Coil Assembly 17 SG38 Suspension Spring 5 PT92 3/8” Upsteam & Preheat Tube 18 SGP42 Spray Gun-Pistol Type 6 PT533 3/8” Pre-Steam Return Tube 19 PT923 1/2” Copper Tube 7 PT94 1/2” Steam Return Tube 20 PT343 Strainer Assembly 8 PT95 1/4” Water Supply Tube PT342 Strainer Body 9 PT98 Motor Cable PT131 Strainer Cap 10 PT99 1/2 x 1/2 Elbow Fitting PT132 Strainer Gasket PT133 Strainer Screen Note “A”: Location of PT-23 coil header, to attach PT-91 coil to inside surface of AT348 Buck. Page 27 SOLENOID VALVE PARTS Ref.No. Part No. Description 1 F1289 Valve - 24V, 50/60 Hz. 2 PT344 Elbow - 3/8” M.P.T. x 1/2” O.D.T. w/Fittings 3 PT340 1/2” O.D. Tube 4 PT342 Strainer Body 5 PT133 Strainer Screen 6 PT132 Strainer Gasket 7 PT131 Strainer Cap 8 PT343 Strainer (Complete) 9 PT345 Pipe Nipple - 2” x 3/8” 10 P279 1/2” Compression Nut 11 FB145 1/2” Compression Bead Page 28 MODEL B Ref.No. Part No. Description Ref.No. Part No. Description 1 PT663 Filter/Regulator 12 136158394 21” Tubing 2 OP433 Pressure Gauge 13 136158394 16” Tubing 3 PT659 Air Solenoid Valve-110V 14 P23 Coil Clamp PT674 Air Solenoid Valve-220V 15 TU7733 Self-Tapping Screw 4 PT662 Conduit Connector 16 PT665 Support Air Supply 5 PT661 Speed Control Muffler 17 OP437 90° Fitting 6 FG142 90° Street Elbow (1/8”) 18 PT691 Cylinder, Air 7 PT666 3” Lg. 1/8” Blk. Pipe Nipple 19 OP437 90° Fitting 8 BR61 1/4” to 1/8” Red. Bushing 20 PT690 Bracket, Mounting 9 OP297 Fitting * PT665 Air Piping Asm - 120v 10 OP436 90° Fitting * PT675 Air Piping Asm - 220v 11 PU135 90° Fitting 1/4” Page 29 PT706 24V CONTROL BOX Ref.No. Part No. Description 1 EA-00606-0 Terminal Board 2 F1300 Motor Relay 3 PT681 Cover 4 PT698 Electronic Controller 5 PT699 Pottentiometer (2 req’d) 6 PT700 Knob (2 req’d) 7 PT701 Layout (Steam) 8 PT702 Layout (Air) 9 PT705 Cover 10 TU15138 Transformer (115/208-240/24V) PTH100 Wire Harness (Not Shown) Page 30 Page 31
Frequently asked questions
What makes Elite.Parts unique?

What kind of warranty will the PT46 have?

Which carriers does Elite.Parts work with?

Will Elite.Parts sell to me even though I live outside the USA?

I have a preferred payment method. Will Elite.Parts accept it?

What they say about us
FANTASTIC RESOURCE
One of our top priorities is maintaining our business with precision, and we are constantly looking for affiliates that can help us achieve our goal. With the aid of GID Industrial, our obsolete product management has never been more efficient. They have been a great resource to our company, and have quickly become a go-to supplier on our list!
Bucher Emhart Glass
EXCELLENT SERVICE
With our strict fundamentals and high expectations, we were surprised when we came across GID Industrial and their competitive pricing. When we approached them with our issue, they were incredibly confident in being able to provide us with a seamless solution at the best price for us. GID Industrial quickly understood our needs and provided us with excellent service, as well as fully tested product to ensure what we received would be the right fit for our company.
Fuji
HARD TO FIND A BETTER PROVIDER
Our company provides services to aid in the manufacture of technological products, such as semiconductors and flat panel displays, and often searching for distributors of obsolete product we require can waste time and money. Finding GID Industrial proved to be a great asset to our company, with cost effective solutions and superior knowledge on all of their materials, it’d be hard to find a better provider of obsolete or hard to find products.
Applied Materials
CONSISTENTLY DELIVERS QUALITY SOLUTIONS
Over the years, the equipment used in our company becomes discontinued, but they’re still of great use to us and our customers. Once these products are no longer available through the manufacturer, finding a reliable, quick supplier is a necessity, and luckily for us, GID Industrial has provided the most trustworthy, quality solutions to our obsolete component needs.
Nidec Vamco
TERRIFIC RESOURCE
This company has been a terrific help to us (I work for Trican Well Service) in sourcing the Micron Ram Memory we needed for our Siemens computers. Great service! And great pricing! I know when the product is shipping and when it will arrive, all the way through the ordering process.
Trican Well Service
GO TO SOURCE
When I can't find an obsolete part, I first call GID and they'll come up with my parts every time. Great customer service and follow up as well. Scott emails me from time to time to touch base and see if we're having trouble finding something.....which is often with our 25 yr old equipment.
ConAgra Foods