SOFTEC MICROSYSTEMS INDART-ST72C334
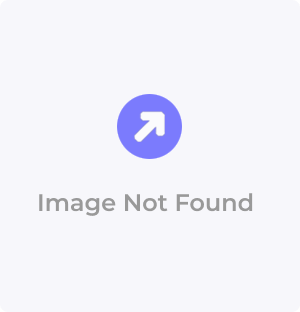
Description
KIT DESIGN FOR ST7
Part Number
INDART-ST72C334
Price
Request Quote
Manufacturer
SOFTEC MICROSYSTEMS
Lead Time
Request Quote
Category
PRODUCTS - I
Datasheet
Extracted Text
® inDART -ST7C In-Circuit Debugger for STMicroelectronics ST72CXXX FLASH Devices User’s Manual ® Copyright © 2001 SofTec Microsystems DC00326 SofTec Microsystems E-mail (general information): info@softecmicro.com E-mail (marketing department): marketing@softecmicro.com E-mail (technical support): support@softecmicro.com Web: http://www.softecmicro.com Important ® SofTec Microsystems reserves the right to make improvements to the inDART Series In-Circuit Debuggers, their documentation and software routines, without notice. Information in this manual is intended to be accurate and reliable. However, SofTec Microsystems assumes no responsibility for its use; nor for any infringements of rights of third parties which may result from its use. SOFTEC MICROSYSTEMS WILL NOT BE LIABLE FOR DAMAGES RESULTING FROM LOSS OF DATA, PROFITS, USE OF PRODUCTS, OR INCIDENTAL OR CONSEQUENTIAL DAMAGES, EVEN IF ADVISED OF THE POSSIBILITY THEREOF. Trademarks inDART is a trademark of SofTec Microsystems. ST is a trademark of STMicroelectronics. Microsoft and Windows are trademarks or registered trademarks of Microsoft Corporation. PC is a registered trademark of International Business Machines Corporation. Other products and company names listed are trademarks or trade names of their respective companies. Written by Paolo Xausa inDART- 1. Overview 5 What is inDART-ST7C? 5 Naming Conventions 5 What is In Situ Programming (ISP)? 6 Supported Devices 7 Demo Boards 7 IDB-ST7C254 Demo Board 8 IDB-ST7C334 Demo Board 9 STVD7 Integrated Development Environment 10 Hiware and Cosmic Demo Versions 11 Recommended Reading 11 Software Upgrades 11 2. Getting Started13 inDART-ST7C Components 13 Host System Requirements 14 Installing the Hardware 14 Installing the Software 15 Application Tutorial 16 3. i- 21 inDART-ST7C Working Principles 21 Limitations 22 Breakpoints Notes 22 Program Execution Notes 23 Real-Time Execution 25 Step Mode Execution 25 Online Assembler Notes 25 Stop Execution Notes 26 Configuring the MCU 26 Programming Capabilities 29 DataBlaze Programming Utility 30 31 Installing the inDART-ST7 User Interface under Windows NT 31 4. Troubleshooting ST7C OperationsnDART Contents ST7C User's Manual Common Problems and Solutions 31 Communication can’t be established with inDART-ST7C 31 A communication error is returned on a program execution command (Run, Continue, Step, etc.) 32 When debugging, the program runs too slowly 32 The “Stop Program” command doesn’t work 32 The program execution stops at the beginning of user’s code 33 Interrupt handling routines are not executed 33 The program seems not to work correctly 33 Getting Technical Support 33 35 - 37 -ST7C334 Demo Board 39 SchematicAppendix C: IDB ST7C254 Demo Board SchematicAppendix B: IDB Appendix A: Target Reset Topics Contents inDART- 1 What is inDART-ST7C? inDART-ST7C is a powerful entry-level tool for STMicroelectronics ST7-based systems. inDART-ST7C takes advantage of STMicroelectronics’ STVD7 (STMicroelectronics Visual Debug) Integrated Development Environment and the ISP (In Situ Programming) feature to program the FLASH memory of the ST7 family of microcontrollers. Together with STVD7, inDART-ST7C provides you with everything you need write, compile, download, in-circuit emulate and debug user code. Full speed program execution allows you to perform hardware and software testing in real time. inDART-ST7C is connected to the host PC through a parallel port, while the 10-pin probe of the product fits into the target's standard ISP connector. On Design Kits packages, a full-featured experiment board for a specific ST7 microcontroller is also included. inDART-ST7C offers you the following benefits: § Real-time code execution without probes–works with all packages; § In-circuit debugging; § Built-in FLASH programmer; § 3.3 V to 5.0 V operating voltage; § Operation from voltage supplied by the target application; § Standard chip used–no bondouts, 100% electrical characteristics guaranteed; § Working frequency up to the microcontroller’s maximum; § STMicroelectronics Visual Debug user interface (the same user interface of all STMicroelectronics ST7 tools), with integrated C compiler and assembler and source level and symbolic debugging. Naming Conventions Throughout this manual, the following naming conventions are used: § inDART-ST7C is the inDART in-circuit debugger (specific for the STMicroelectronics ST72CXXX devices); 5 Page 1. Overview ST7C User's Manual § inDART-ST7 user interface is the user interface common to all of the 1 inDART-ST7 series in-circuit debuggers. What is In Situ Programming (ISP)? The ISP feature allows you to update the content of FLASH program memory when the chip is already plugged on the application board. ISP programming uses a serial protocol to interface a programming tool like inDART. The ISP feature can be implemented with a minimum number of added components and board area impact. inDART-ST7C uses the standard, 10-pin ST7 ISP connector to program and in- circuit emulate the target device. You must therefore provide such connector (see the diagram below) on your target board. The ST7 ISP Interface ISP Mode Pin Name ISPDATA ISPCLK ISPSEL RESET V V ISP Connector Pin # 2 4 8 6 1, 3, 5 7 The ST7 ISP Connector 6 Page DDSS Overview1. inDART- Supported Devices 1 inDART-ST7C currently supports all EEPROM-like ST7 FLASH devices, in all packages. Device Package Notes ST72C104G1B SDIP32 ST7 FLASH MCUs (FLASH=4Kx8) ST72C104G1M SOIC28 ST7 FLASH MCUs (FLASH=4Kx8) ST72C104G2B SDIP32 ST7 FLASH MCUs (FLASH=8Kx8) ST72C104G2M SOIC28 ST7 FLASH MCUs (FLASH=8Kx8) ST72C124J2B SDIP42 ST7 FLASH MCUs (FLASH=8Kx8) ST72C124J2T TQFP44 ST7 FLASH MCUs (FLASH=8Kx8) ST72C171K2B SDIP32 ST7 FLASH MCUs (FLASH=8Kx8) ST72C171K2M SOIC34 ST7 FLASH MCUs (FLASH=8Kx8) ST72C215G2B SDIP32 ST7 FLASH MCUs (FLASH=8Kx8) ST72C215G2M SOIC28 ST7 FLASH MCUs (FLASH=8Kx8) ST72C216G1B SDIP32 ST7 FLASH MCUs (FLASH=4Kx8) ST72C216G1M SOIC28 ST7 FLASH MCUs (FLASH=4Kx8) ST72C254G1B SDIP32 ST7 FLASH MCUs (FLASH=4Kx8) ST72C254G1M SOIC28 ST7 FLASH MCUs (FLASH=4Kx8) ST72C254G2B SDIP32 ST7 FLASH MCUs (FLASH=8Kx8) ST72C254G2M SOIC28 ST7 FLASH MCUs (FLASH=8Kx8) ST72C314J2T TQFP44 ST7 FLASH MCUs (FLASH=8Kx8) ST72C314J4B SDIP42 ST7 FLASH MCUs (FLASH=16Kx8) ST72C314J4T TQFP44 ST7 FLASH MCUs (FLASH=16Kx8) ST72C314N2B SDIP56 ST7 FLASH MCUs (FLASH=8K ST72C314N2T TQFP64 ST7 FLASH MCUs (FLASH=8Kx8) ST72C314N4B SDIP56 ST7 FLASH MCUs (FLASH=16Kx8) ST72C314N4T TQFP64 ST7 FLASH MCUs (FLASH=16Kx8) ST72C334J2B SDIP42 ST7 FLASH MCUs (FLASH=8Kx8, EEPROM=256x8) ST72C334J2T TQFP44 ST7 FLASH MCUs (FLASH=8Kx8, EEPROM=256x8) ST72C334J4B SDIP42 ST7 FLASH MCUs (FLASH=16Kx8, EEPROM=256x8) ST72C334J4T TQFP44 ST7 FLASH MCUs (FLASH=16Kx8, EEPROM=256x8) ST72C334N2B SDIP56 ST7 FLASH MCUs (FLASH=8Kx8, EEPROM=256x8) ST72C334N2T TQFP64 ST7 FLASH MCUs (FLASH=8Kx8, EEPROM=256x8) ST72C334N4B SDIP56 ST7 FLASH MCUs (FLASH=16Kx8, EEPROM=256x8) ST72C334N4T TQFP64 ST7 FLASH MCUs (FLASH=16Kx8, EEPROM=256x8) inDART-ST7C Supported Devices Demo Boards On Design Kits packages, a full-featured experiment board for a specific ST7 microcontroller (ST7C254 or ST7C334) is also included. Each demo board can be used for evaluation/experiments in the absence of a target application board. 7 Page x8) ST7C User's Manual IDB-ST7C254 Demo Board 1 The IDB-ST7C254 Demo Board has the following hardware features: 1. An ST72C254G2B microcontroller (in SDIP32 package, already programmed with a demo application—in addition, you can also use the following microcontrollers: ST72C104G1B, ST72C104G2B, ST72C215G2B, ST72C216G1B, ST72C254G1B); 2. A standard ISP connector; 3. Eight jumpers to connect/disconnect each of the eight LEDs to/from their respective Port A pin; 4. Eight high-efficiency (low-current) LEDs connected to Port A; 5. A potentiometer, together with a jumper to connect/disconnect it to/from PC5; 6. A push-button switch connected to RESET; 7. A push-button switch, together with a jumper to connect/disconnect it to/from PC4; 8. Eight jumpers to connect/disconnect each of the eight DIP-switches to/from their respective Port A/Port B pin; 9. Eight general-purpose DIP switches (four connected to PB and four connected to Port C); 10. A provision for an external oscillator, together with a jumper to select the microcontroller’s internal oscillator or the external oscillator; 11. A connector for a 9-12V, 100 mA power supply; 12. A connector area to access the I/O pins of the microcontroller for expansion prototyping; 13. A prototyping area. 8 Page Overview1. inDART- 1 2 3 1 4 8 5 9 6 7 -ST7C254 Demo Board IDB-ST7C334 Demo Board The IDB-ST7C334 Demo Board has the following hardware features: 1. An ST72C334N4B microcontroller (in SDIP56 package, already programmed with a demo application—in addition, you can also use the following microcontrollers: ST72C314N2B, ST72C314N4B, ST72C334N2B); 2. A standard ISP connector; 3. Eight jumpers to connect/disconnect each of the eight LEDs to/from their respective Port B pin; 4. Eight high-efficiency (low-current) LEDs connected to Port B; 5. A potentiometer, together with a jumper to connect/disconnect it to/from PD7; 6. A push-button switch connected to RESET; 7. A push-button switch, together with a jumper to connect/disconnect it to/from PD0; 8. Eight jumpers to connect/disconnect each of the eight DIP-switches to/from their respective Port A pin; 9. Eight general-purpose DIP switches connected to Port A; 9 Page The IDB 12 13 10 11 ST7C User's Manual 10. A provision for an external oscillator, together with a jumper to select the 1 microcontroller’s internal oscillator or the external oscillator; 11. A connector for a 9-12V, 100 mA power supply; 12. A connector area to access the I/O pins of the microcontroller for expansion prototyping; 13. A prototyping area. 2 3 1 4 8 5 9 6 7 -ST7C334 Demo Board STVD7 Integrated Development Environment The inDART-ST7 user interface is based on the ST7 Visual Debug Integrated Development Environment (STVD7). STVD7 enables programs to be executed and stopped where desired, while viewing the memory contents. It offers the ability to step through and examine code at the C source level and the Assembly instruction level. You can introduce breakpoints and run or single-step the executable, while viewing the source and observing current program values. All registers and memory locations are accessible for both read and write operations. This documentation covers the basic setup and operation of the STVD7, but it does not cover all of its functions. For further information, please refer to the STVD7 on-line help. 10Page The IDB 1213 10 11 Overview1. inDART- Hiware and Cosmic Demo Versions 1 These two third-party companies have developed a C compiler for use with ST7 microcontrollers. A demo version of each compiler can be directly installed on the PC using the STMicroelectronics “MCU ON CD” CD-ROM. Recommended Reading This documentation describes how to use inDART together with the STVD7 Integrated Development Environment. Additional information can be found on the following documents: § STVD7 On-line Help—The ST7 Visual Debug on-line help. § AST7-LST7.PDF— This user’s guide describes how to use the STMicroelectronics assembler, linker, formatter and librarian for the ST7 family. § ST7 FAMILY 8-BIT MCUs Programming Manual—Programming reference containing the description of the full ST7 instruction set. § ST7 Family Data Sheets—The complete set of device data sheets can be found on the “MCU ON CD” CD. § RELEASE.TXT—Contains notes and known problems about the STVD7 user interface. Software Upgrades The latest version of the inDART-ST7 user interface is always available for free at our download page on the web: http://www.softecmicro.com/download.html. 11Page ST7C User's Manual inDART- 2 inDART-ST7C Components The inDART-ST7C package includes the following items: 1. The inDART-ST7C in-circuit debugger; 2. A 20-cm, 10-conductor ISP cable; 3. A parallel cable; 4. The inDART-ST7 CD-ROM; 5. The STMicroelectronics “MCU ON CD” CD; 6. On Design Kits packages, a full-featured experiment board for a specific ST7 microcontroller (ST7C254 or ST7C334) is also included. 3 1 2 4 6 5 The inDART-ST7C package 13Page 2. Getting Started ST7C User's Manual Host System Requirements The inDART-ST7C in-circuit debugger is controlled by a PC user interface running under Windows. The following hardware and software is required to 2 run the inDART-ST7 user interface: § An Intel Pentium 100 or above running Windows 95, Windows 98, Windows 2000 or Windows NT; § 32 MB of random-access memory (RAM) plus 20 MB of available disk space. Installing the Hardware The inDART-ST7C in-circuit debugger is connected through the parallel port to a PC which runs the inDART-ST7 user interface as explained later. Connection steps are numbered below in the recommended flow order: 1. Turn off the PC; 2. Insert the male D-Sub connector of the parallel cable into a free PC parallel interface (LPT1 or LPT2); 3. Insert the other end of the parallel cable into the LPT connector on the inDART-ST7C board; 4. Insert one end of the ISP cable into the ISP connector on the inDART-ST7C board; 5. Insert the other end of the ISP cable into the ISP connector of the demo board or target application; 6. Turn on the PC; 7. Turn on the power to the demo board/target application which also powers the inDART-ST7C board. 14Page StartedGetting2. inDART- Note: inDART-ST7C can be powered by the demo board/target application via the ISP cable. In this case, the power supply is taken from the Vcc pin of the ISP connector, and MUST BE 5 V, 10 mA. In the case your target application is not able to provide the required voltage and current, you must power the 2 inDART-ST7C board via its power connector. inDART-ST7C uses a 9-12 V DC, 10 mA (unregulated) wall plug-in power supply with a 2.1 mm pin and sleeve plug with positive in the center and sleeve as ground. Installing the Software The inDART-ST7 user interface setup program is located on the SofTec Microsystems “System Software” CD-ROM provided with the instrument. The setup program will copy the required files to your hard drive. Additionally, an uninstall program will be copied, giving you the option to uninstall the inDART- ST7 user interface at any time. To install the inDART-ST7 user interface: 1. Insert the “System Software” CD-ROM into your computer’s CD-ROM drive. 2. A startup window should automatically appear (if the startup window doesn’t appear automatically, manually run the file located on the CD-ROM root). Choose “Install Instrument Software” from the main menu. 3. A list of available software should appear. Click on the “Install inDART- ST7 Toolchain” option. 4. Follow the on-screen instructions. 15Page Setup.exe ST7C User's Manual Note: if you are installing the inDART-ST7 user interface from Windows NT, you must have logged in as Administrator. 2 Application Tutorial This section will provide a step-by-step guide on how to launch your first inDART-ST7 project and get started with the inDART-ST7 user interface. The example provided requires that inDART-ST7 be used with the IDB-ST7C254 Demo Board or the IDB-ST7C334 Demo Board. The sample application configures the A/D peripheral to convert on the A/D channel connected to the potentiometer and displays the results on the LEDs. Note: this tutorial is based on an Assembly example. Additional examples in C (based on the Cosmic C compiler) are also provided. § Ensure that inDART-ST7 is connected to the PC (via the parallel cable), to the demo board (via the ISP) connector, and that the demo board is powered on. § Make sure that the “OSC SEL” jumper on the demo board selects the “INT” mode. § Make sure that all of the “LED ENABLE” jumpers and the “POTENTIOMETER ENABLE” jumpers are inserted. § Start the inDART-ST7 user interface by selecting Start > Programs > SofTec inDART-ST7 > inDART-ST7. The first time you launch the inDART-ST7 user interface you are prompted to enter the toolchain paths to be used by STVD7’s integrated development environment. Click “Yes”. The following dialog box will appear. 16Page StartedGetting2. inDART- 2 The Toolchain Path Dialog Box § This step-by-step tutorial requires that the ST7 Assembler path be defined. Make sure that the ST7 Assembler path that appears on the Toolchain Path Dialog Box corresponds to the location where the ST7 Assembler has been installed (please note that you may modify the toolchain path at any time from within STVD7—simply select Project > Toolchain Paths from the main menu to access the dialog box above). Click “OK”. The inDART- ST7 user interface will open. § From the main menu, choose File > Open Workspace. Select the “adc.wsp” workspace file that is located under the “\Program Files\inDART-ST7\STVD7\Sample\Asm\254\Adc” directory if you are using the IDB-ST7C254 Demo Board. If you are using the IDB-ST7C334 Demo Board, look for the same file under the “\334\Adc” directory. Click “Open”. § As the application has already been assembled and the executable file generated, from the main menu, choose Emulator > Emulator Settings and select the LPT port the inDART-ST7C board is connected to. Click “OK”. § From the main menu, choose Debug > Start Debugging. The user interface will display the source code with the Program Counter pointing to the first instruction, alongside of the Disassembly window. 17Page ST7C User's Manual 2 Debugging Session Started § From the main menu, select Debug > Run. The program will be executed in real-time. By rotating the potentiometer, you affect the results of the A/D conversion, and the binary value of each conversion is displayed on the LEDs. § From the main menu, select Debug > Stop Program. The application will stop, and the Program Counter arrow will point to the next instruction to be executed. § From the main menu, select View > ST7 Registers. A small window displaying the current value of all of the ST7 registers (Program Counter, Stack Pointer, Index Registers, etc.) will appear. § From the main menu, select View > Peripheral Registers. A small window displaying the current status of all of the ST7 built-in peripherals (I/O ports, Timers, A/D converter registers, etc.) will appear. § On the source code window, set a breakpoint on the “ ” instruction. To do so click on the line containing that instruction and then, 18Page ld A, ADCDR StartedGetting2. inDART- from the main menu, select Edit > Insert/Remove Breakpoint. A solid, red circle will appear on the leftmost column indicating that the breakpoint has been set. § From the main menu, select Debug > Run. The application will restart, and will automatically stop at the previously set breakpoint. 2 § From the main menu, select Debug > Step Into. This command will execute the “ ” instruction. On the ST7 Registers window, you can see how that instruction affected the value contained on the Accumulator. This value is the result of the A/D conversion. § Issue another Step Into command (Debug > Step Into). The Accumulator value will be displayed on the LEDs. Congratulations! You have successfully completed this tutorial! You can continue to experiment with the inDART-ST7 user interface and discover by your own its potentialities. For an in-depth guide of all of the user interface features, select Help > Search from the main menu. 19Page ld A, ADCDR ST7C User's Manual inDART- - inDART-ST7C Working Principles inDART-ST7C is an in-circuit debugger as well as a programming tool. It programs files into the ST72CXXX microcontrollers and offers debugging 3 features like real-time code execution, stepping, and breakpoint. Its debugging features are achieved thanks to a small portion of monitor code which is automatically and transparently added to the user code and programmed into the target microcontroller. The monitor communicates with the host PC through a bi-directional command-based protocol via the ISPDATA and ISPCLK lines of the microcontroller. For this reason, the ISPDATA and ISPCLK lines (which are the standard lines used by the microcontroller’s ISP peripheral) are reserved during debugging sessions. The same two lines are also used during device programming. Contrariwise to traditional in-circuit emulation (where the target application is executed and emulated inside the emulator), inDART-ST7C uses the very same target microcontroller to carry on in-circuit execution. This means that all microcontroller’s peripherals (timers, A/D converters, I/O pins, etc.) are not reconstructed or simulated by an external device, but are the very same target microcontroller’s peripherals. Moreover, the inDART-ST7C debugging approach ensures that the target microcontroller’s electrical characteristics (pull-ups, low- voltage operations, I/Os thresholds, etc.) are 100% guaranteed. The trade-off, however (in electronics miracles don’t exist, after all—do they?), is that the target microcontroller must be properly configured and ready to execute target applications. “Start Debugging” Command (Download Program Code + Monitor) EDITING DEBUGGING “Stop Debugging” Command Monitor Download 21Page ST7C Operations3. inDART ST7C User's Manual - Limitations Since inDART-ST7C is based on the ISP feature of the ST7, some on-chip resources are wasted for debugging purposes. In particular: § 7 stack levels (bytes) are wasted; § 288 bytes are reserved for the monitor (from address FEC0H to address 3FFE0H); § ISPDATA and ISPCLK lines are reserved for programming and in-circuit debugging (i.e., PB5 and PB6 I/O lines are reserved on ST72C254 devices; PC4 and PC6 lines are reserved on ST72C334 devices; PB3 and PB5 lines are reserved on ST72C171 devices); § SPI peripheral and the SPI interrupt vector are reserved (since the SPI I/O lines share the ISPDATA and ISPCLK lines); § The TRAP instruction and the TRAP interrupt vector are reserved for the monitor; § Global interrupts must be enabled to allow the STOP command to be implemented; § Peripherals run even in STOP mode. Breakpoints Notes inDART-ST7C can handle an unlimited number of breakpoints within program memory. When you set a breakpoint on a source code line, inDART-ST7C automatically (and transparently) replaces the opcode of the instruction where the breakpoint is set with the opcode of the TRAP instruction (this explains why the TRAP instruction—and the TRAP vector—is reserved and should not be used in user applications). The difference between inDART-ST7C and a standard emulator is that the latter can set/reset breakpoints under all conditions, while inDART-ST7C (since it needs to change the opcode of the instruction where the breakpoint is set with the TRAP instruction) needs to program the FLASH memory of the target microcontroller to perform this operation. To program the FLASH memory, inDART-ST7C needs to enter the ISP mode and, consequentely, to reset the target microcontroller. inDART-ST7C actually programs breakpoints only when an execution command that resets the target microcontroller (e.g., the “Run” command) is issued. In all of the other cases breakpoint information is stored 22Page OperationsST7CinDART3. inDART- inside the host PC, program execution switches to “step mode” (see below) and breakpoint programming occurs next time an execution command that resets the target microcontroller is issued. Program Execution Notes inDART-ST7C executes in real-time mode or in step mode. 3 § Step mode execution occurs when you launch the emulation, then stop it, then set/modify breakpoints, and then continue the emulation; § Real-time execution occurs in all other cases. The following table summarizes (for the most common emulation commands) which command causes inDART-ST7C to execute in real-time mode or in step mode. Emulation Command Execution Mode Real-time Restart Real-time Continue Real-time if no breakpoints have been set/modified since the “Stop Program” command. Step mode otherwise. Step Into Step mode Step Over Step mode Step Out Step mode Run to Cursor Step mode Execution Mode Summary The following FSM (Finite State Machine) diagram illustrates in detail the behaviour of inDART-ST7C. In the diagram, each state transition is caused by one or more events, explained below. § Reset. The Reset event is caused by the “Chip Reset” command, an external Reset event, or a peripheral Reset event. § Restart. Include either the “Run” command or the “Restart” command. § Stop. The Stop event is caused either by the “Stop Program” command or by a breakpoint hit. § Continue. Is caused by the “Continue” command. 23Page Run ST7C User's Manual - § Single-step command. Is caused by the “Step Into” and “Step Into ASM” commands. § Multiple-step command. One of the following commands: “Step Out”, “Step Over”, “Step Over ASM”, “Run To Cursor”. Please note that, in some cases, the “Step Over” and “Step Over ASM” commands have the same effect of the “Step Into” and “Step Into ASM” commands, respectively, depending on whether there is a function call to be executed or not. 3 § Modify Breakpoints. One of the following commands: “Insert/Remove Breakpoint”, “Enable/Disable Breakpoint”, “Remove All Breakpoints”. § Edit Data/Registers. One of the following events: memory editing, registers editing, watch variables editing, peripherals editing, Program Counter editing. START DEBUGGING Multiple-Step Cmd Reset Single-Step Cmd Single-Step Cmd Multiple-Step Cmd Edit Data/Registers Reset Multiple-Step Cmd Single-Step Cmd Mod. Brkpts Edit Data/Registers Mod. Brkpts RESET STOP (A) STOP (B) Reset Edit Data/Registers Reset Restart Continue Mod. Brkpts Restart Restart Stop Continue Continue Reset Stop RUN RUN (Real Time) (Step Mode) STEP MODE inDART-ST7C Execution Modes 24Page OperationsST7CinDART3. inDART- Real-Time Execution When inDART-ST7C runs in real time, instructions are executed just as the microcontroller would without the debugger. inDART-ST7C executes in real time until a breakpoint is encountered or until the “Stop Program” command is issued. Subsequent “Continue” commands are still performed in real time only if you do not set/modify breakpoints. Step Mode Execution 3 In step mode, program execution is supervised by the host PC and performed (automatically) step by step. Note: in step mode, peripherals are still truly handled by the target microcontroller. However, interrupts are not handled (that is, interrupt events never occur). This affects execution of instructions like and —since these instructions require interrupts to work, in step mode their behaviour is different than in real-time mode. In particular, the instruction loops forever on itself (no interrupts ever occur), and after executing an instruction, program execution cannot continue (same reason). Note: in step mode, program execution speed is affected by the host PC speed—in particular, in step mode, program execution is slower than real-time program execution. This can affect the program execution speed when, for example, commands such as “Step Over”, “Step Out” or “Run to Cursor” are executed, since it can take a long time to perform the action (especially when the code contains loops to be executed many times). Online Assembler Notes During a debugging sessions, every time assembly instructions are modified in the Assembly window (through the Online Assembler), a reset condition occurs (even though the Program Counter arrow still points to the same instruction). Subsequent debugging commands will be therefore executed from a reset state. 25Page halt wfi haltwfi ST7C User's Manual - Stop Execution Notes During debugging, user program execution will stop if one of the following conditions occur: 1. A breakpoint has been encountered (or a TRAP instruction has been executed); 32. The microcontroller RESET line has been driven active; 3. A microcontroller internal RESET state has been triggered (by, for example, a Watchdog event, or an internal low-voltage detection); 4. The “Stop Program” emulation command has been issued from the inDART-ST7 user interface. Please note that, during real-time execution, the “Stop Program” command only works if interrupts are enabled in the user application. Note: when executing in real-time mode, the “Stop Program” command only works if interrupts are enabled on the user program (the RIM instruction must be present at the beginning of user’s code). The RIM instruction is only needed if users want to stop the program by using the “Stop Program” from the user interface—and does not affect any other debugging feature. In particular, the RIM instruction does not affect breakpoints. Configuring the MCU Before to start a debugging session, you must define and configure the target device (MCU) you wish inDART-ST7C to emulate. The target device is defined and configured from the MCU Configuration dialog box. To access it, select Tools > MCU Configuration from the main menu. The following dialog box will appear. 26Page OperationsST7CinDART3. inDART- 3 The MCU Configuration Dialog Box § First of all, verify that the inDART model corresponds to “inDART-ST7C”. § By clicking the “Settings” button you can modify the “RESET Rise Time” parameter to make it suitable for your target application. This parameters depends on your target application’s reset circuitry. If you use inDART- ST7C in connection with an inDART demo board, you don’t need to change this parameter. For more information on this parameter, please refer to “Appendix A: Target Reset Topics”. § The “Device Code” parameter specifies the target microcontroller used in your target application. You must specify the exact device code of the microcontroller you are working with. § The “Set Option Bytes” button allows you to access the Edit Option Bytes dialog box. The following figure illustrates an example of the Edit Option Bytes dialog box (every microcontroller has its own specific Option Bytes). 27Page ST7C User's Manual - 3 The Edit Option Bytes dialog box Particular attention must be paid in correctly setting each of the Option Bytes parameters. Improper settings may cause the target microcontroller not to work correctly (or not to work at all). In particular, the following parameters must be carefully set: § FMP (Full Memory Protection). Must be always set to “Not Protected”. § WDG SW (Watchdog Activation). If set to “Hardware”, you must refresh the Watchdog in your target application. You can leave it to “Software” when working with the provided sample applications. § OSC (Oscillator Selection). Specify the oscillator source used by your target application. inDART-ST7C demo boards, by default, work with the internal, 4-Mhz RC oscillator. § CFC (Clock Filter Control). When enabled, allows an internal, security clock to be used should the main oscillator source (specified by the OSC parameter) not be present, or set incorrectly, or not work correctly. It is suggested to set this parameter to “Enabled”—since otherwise, if due to a bad OSC parameter setting (or other reason) the target microcontroller can’t work, it will not be possible to reprogram the Option Bytes. Note: the Option Bytes value specified in the Edit Option Bytes dialog box will be used when programming the device (see “Programming Capabilities” below). 28Page OperationsST7CinDART3. inDART- Programming Capabilities inDART-ST7C feature ISP programming capabilities. A programming utility is built-in in the inDART-ST7 user interface. When in Debugging mode, the Tools > Program command in the main menu is enabled, and allows you to program the target microcontroller with your target application code but without any debugging code. A typical programming procedure is made of a series of programming steps, as indicated in the figure below. You can choose whether to 3 perform or not each single step. Please note that the programming steps are performed in the exact order as shown in the Program dialog box. The Program Dialog Box § Clear Read-Out Protection. Clears the Read-Out Protection bit. Check this programming step when you are programming a device which has been programmed with the Read-Out Protection bit set. § Erase Device. Erases the entire Code memory area. § Program FLASH Memory. Writes the application code into the Code memory area. § Verify FLASH Memory. Verifies that the application code has been correctly written into the Code memory. § Program Option Bytes. Programs the Option Bytes according to the parameters specified in the Edit Option Bytes dialog box. § Set Read-Out Protection. Set the Read-Out Protection bit. Check this programming step if you want to protect the application code from external reading operations. 29Page ST7C User's Manual - § Run. After programming, resets the microcontroller and executes the application program. Note: after programming the device, you will not able to continue with the current debugging session. To continue debugging, you must stop the current debugging session and start a new one. 3 DataBlaze Programming Utility A standalone, full-featured programming utility (DataBlaze) is also provided with inDART-ST7. To start the DataBlaze utility select Start > Programs > SofTec inDART-ST7 > Programmer > DataBlaze. DataBlaze offers the following advanced features: § Code memory editing; § Data memory (EEPROM) editing; § Blank check/erase/verify operations on Code memory, Data memory and Option Bytes; § Read operations from Code memory, Data memory and Option Bytes; § Project handling. 30Page OperationsST7CinDART3. inDART- Installing the inDART-ST7 User Interface under Windows NT In order to install the inDART-ST7 user interface under Windows NT, you must have logged in as Administrator. 4 Common Problems and Solutions Communication can’t be established with inDART-ST7C 1. Make sure the inDART-ST7C in-circuit debugger is powered on. inDART- ST7C can be powered by the demo board/target application via the ISP cable. In this case, the power supply is taken from the Vcc pin of the ISP connector, and MUST BE 5 V, 10 mA. In the case your target application is not able to provide the required voltage and current, you must power the inDART-ST7C board via its power connector. inDART-ST7C use a 9-12 V DC, 10 mA (unregulated) wall plug-in power supply. 2. Make sure that the parallel cable is connected. Also make sure you selected the LPT port number to which the instrument is connected to. To view/change the LPT port in use, choose Emulator > Emulator Settings from the inDART-ST7 user interface’s main menu. 3. Make use you are working with the correct inDART hardware model. To view/change the inDART hardware model in use, choose Tools > MCU Configuration from the inDART-ST7 user interface’s main menu. 4. Make sure the demo board/target application board is powered on and the target microcontroller is working. Programming and debugging rely on an ISP serial communication between the inDART-ST7C board and the demo board/target application. This means that, in order to work correctly, the target microcontroller must be running. In particular, make sure that: § The ISP cable is connected to the demo board/target application’s ISP connector. § The target microcontroller is in place. § All of the ISP connector signals (ISPSEL, ISPDATA, ISPCLK, RESET, VDD and VSS) are correctly tied to the target microcontroller. 31Page 4. Troubleshooting ser's ManualST7C U § The microcontroller’s Reset circuitry is working (for more information please refer to “Appendix A: Target Reset Topics”). § The oscillator circuitry is working according to the Option Bytes specifications. To view/change the Option Bytes, choose Tools > MCU Configuration from the inDART-ST7 user interface’s main menu. From the dialog box which will appear, click the “Set Option Bytes” button. A communication error is returned on a program execution command (Run, Continue, Step, etc.) Make sure that your program doesn’t use the SPI peripheral and that the I/O bits corresponding to the ISPDATA and ISPCLK ISP signals are set to input 4 mode. When debugging, the program runs too slowly This problem can have two causes: § If not correctly set (via Option Bytes), the target microcontroller may run at a frequency lower than that specified. On some ST7 microcontrollers (if specified on the Option Bytes), the working frequency is automatically set to a safe value (< 1 MHz) when the specified oscillator source can’t be found (or doesn’t work properly). In this conditions, the low working frequency affects the ISP communication and, therefore, the inDART-ST7 user interface performances. § Under some conditions, program execution is not performed in real time. As a consequence, program execution may slow down. Please read “Program Execution Notes” on Chapter 3 for more information. The “Stop Program” command doesn’t work When executing in real-time mode, the “Stop Program” command only works if interrupts are enabled on the user program (the RIM instruction must be present at the beginning of user’s code). The RIM instruction is only needed if users want to stop the program by using the “Stop Program” from the user interface—and does not affect any other debugging feature. In particular, the RIM instruction does not affect breakpoints. Also make sure that your program doesn’t use the SPI peripheral and that the I/O bits corresponding to the ISPDATA and ISPCLK ISP signals are set to input mode. 32Page Troubleshooting4. inDART- The program execution stops at the beginning of user’s code A Reset condition occurred. This can be due to an external Reset condition (microcontroller’s RESET line driven low) or an internal Reset condition (e.g., due to a Watchdog event). For more information on causes that can trigger a Reset condition, please refer to the specific ST7 microcontroller device data sheet. Interrupt handling routines are not executed Under some conditions, program execution is not performed in real time. As a consequence, interrupts are not handled. Please read “Real-Time Execution Notes” on Chapter 3 for more information. 4 The program seems not to work correctly When debugging your program with inDART-ST7C, some target microcontroller’s resources are reserved for debugging purposes. In particular, 288 bytes are reserved for the monitor (from address FEC0H to address FFE0H). Therefore, you must pay attention that your program doesn’t use this range of memory locations. Also, please remember that 7 stack levels are reserved by inDART-ST7C as well. Getting Technical Support Technical assistance is provided free to all customers. For technical assistance, documentation and information about products and services, please refer to your local SofTec Microsystems partner. SofTec Microsystems offers its customers a free technical support service at support@softecmicro.com. 33Page ser's ManualST7C U inDART- During debugging and programming, inDART-ST7C communicates with the target microcontroller through the target microcontroller’s ISP capability. Both debugging and programming capabilities thus require that the ISP mode be selected on the target microcontroller. In order to enter the ISP mode, the microcontroller ISPSEL line must be correctly driven during the microcontroller RESET phase. inDART-ST7C automatically and transparently performs such operation: however, since inDART-ST7C must drive the ISPSEL line in the correct timings, you must specify (in the inDART-ST7 user interface—see “Configuring the MCU” on chapter 3) a parameter called “RESET Rise Time” (T in the diagram below), according to the limits depicted on the diagram RISE itself. A T0 T1 T2 RESET 0,7 V DD T T RISE ISP ISPSEL T2 – T1 = 256 CPU Clocks (32 us @ 16 MHz) TISP = 4 us T1 < TRISE < T2 - TISP T Parameter Constraints 35Page RISE Appendix A: Target Reset Topics ST7C User's Manual The following table lists some values of the “RESET Rise Time” parameter based on the most common RC configurations. In the table, Rs is the serial resistor, which we suggest to use. f = 16 MHz, Vcc = 5 V RESET Rise RESET Rise RC RC 4,7 K * 100 pF su 4,7 K * 100 pF 0 4,7 K * 10 nF 4,7 K * 10 nF 0 4,7 K * 22 nF 4,7 K * 22 nF 0 4,7 K * 47 nF 4,7 K * 47 nF 0 4,7 K * 100 nF 4,7 K * 100 nF 0 4,7 K * 1 uF 4,7 K “RESET Rise Time” Vs. RC Values A Pa36 ge us10 us490 4,7 Kus10 us202 4,7 Kus10 us76 4,7 Kus10 us35 4,7 Kus10 us10 4,7 K10 RsTimeRsTime TopicsResetTargetA:Appendix inDART- - B -ST7C254 Demo Board Schematic 37Page IDB Board Schematic ST7C254 Demo Appendix B: IDB ST7C User's Manual inDART- - C -ST7C334 Demo Board Schematic 39Page IDB Board Schematic ST7C334 Demo Appendix C: IDB ST7C User's Manual
Frequently asked questions
What makes Elite.Parts unique?

What kind of warranty will the INDART-ST72C334 have?

Which carriers does Elite.Parts work with?

Will Elite.Parts sell to me even though I live outside the USA?

I have a preferred payment method. Will Elite.Parts accept it?

What they say about us
FANTASTIC RESOURCE
One of our top priorities is maintaining our business with precision, and we are constantly looking for affiliates that can help us achieve our goal. With the aid of GID Industrial, our obsolete product management has never been more efficient. They have been a great resource to our company, and have quickly become a go-to supplier on our list!
Bucher Emhart Glass
EXCELLENT SERVICE
With our strict fundamentals and high expectations, we were surprised when we came across GID Industrial and their competitive pricing. When we approached them with our issue, they were incredibly confident in being able to provide us with a seamless solution at the best price for us. GID Industrial quickly understood our needs and provided us with excellent service, as well as fully tested product to ensure what we received would be the right fit for our company.
Fuji
HARD TO FIND A BETTER PROVIDER
Our company provides services to aid in the manufacture of technological products, such as semiconductors and flat panel displays, and often searching for distributors of obsolete product we require can waste time and money. Finding GID Industrial proved to be a great asset to our company, with cost effective solutions and superior knowledge on all of their materials, it’d be hard to find a better provider of obsolete or hard to find products.
Applied Materials
CONSISTENTLY DELIVERS QUALITY SOLUTIONS
Over the years, the equipment used in our company becomes discontinued, but they’re still of great use to us and our customers. Once these products are no longer available through the manufacturer, finding a reliable, quick supplier is a necessity, and luckily for us, GID Industrial has provided the most trustworthy, quality solutions to our obsolete component needs.
Nidec Vamco
TERRIFIC RESOURCE
This company has been a terrific help to us (I work for Trican Well Service) in sourcing the Micron Ram Memory we needed for our Siemens computers. Great service! And great pricing! I know when the product is shipping and when it will arrive, all the way through the ordering process.
Trican Well Service
GO TO SOURCE
When I can't find an obsolete part, I first call GID and they'll come up with my parts every time. Great customer service and follow up as well. Scott emails me from time to time to touch base and see if we're having trouble finding something.....which is often with our 25 yr old equipment.
ConAgra Foods