SEW EURODRIVE MKS51A010-503-00
Specifications
Amperage
10A
Phase
3
Type
Servo Drive
Voltage
500 VAC
Datasheet
Extracted Text
Edition ® MOVIDYN Servo Controllers 11/2000 Operating Instructions 09223711 / EN SEW-EURODRIVE Contents 1 Important Notes ...................................................................................... 4 2 Safety Instructions..................................................................................6 3 Unit Design .............................................................................................. 7 3.1 MPR / MPB ..................................................................................... 7 3.2 MAS / MKS ..................................................................................... 8 3.3 Unit Designation ............................................................................. 9 3.4 Type Designations .......................................................................... 9 4 Mechanical Installation.........................................................................10 4.1 Design of an Axis System............................................................. 10 4.2 Installation of Option Cards .......................................................... 11 5 Electrical Installation ............................................................................ 13 5.1 Assembly Instructions for Shield Clamps ..................................... 13 5.2 Supply, Inverter, and Motor Connection ....................................... 14 5.3 Control of the Mechanical Brake................................................... 17 5.4 Electronic Lines and Signal Generation........................................ 19 5.5 EMC-Compliant Installation .......................................................... 19 5.6 UL-Compliant Installation.............................................................. 22 5.7 Wiring Diagrams ........................................................................... 23 5.8 Description of Terminal Functions ................................................ 26 5.9 RS-485 Interface Connection ....................................................... 29 6 Startup...................................................................................................30 I 6.1 Initial Settings ............................................................................... 30 6.2 List of Parameters......................................................................... 34 0 0 7 Operation and Service.......................................................................... 38 7.1 Status LEDs.................................................................................. 38 7.2 Reset Options............................................................................... 38 7.3 List of Fault Messages.................................................................. 39 7.4 SEW Electronics Service .............................................................. 41 8 Technical data.......................................................................................42 n kVA 8.1 General Technical Data ................................................................ 42 f i 8.2 Technical Data of Basic Units....................................................... 43 P Hz 9 Index.......................................................................................................46 Addresses........................................................................................................49 fi 3 MOVIDYN Servo Controller Operating Instructions 1 1 Important Notes Warnings and Always follow warnings and safety instructions in this publication! Safety Electrical hazard Instructions Possible effects: Serious or fatal injury. Immediate danger Possible effects: Serious or fatal injury. Dangerous situation Possible effects: Minor injury. Harmful situation Possible effects: Damage to equipment or surroundings. Application hints and useful information. Operating It is required to follow these instructions for fault-free operation and fulfillment of any Instructions rights to claim under warranty. Read these instructions carefully before you start working with the unit! These operating instructions contain vital servicing information and should be kept in close proximity to the drive unit. ® Intended Use MOVIDYN servo controllers are devices for industrial and commercial systems for operation of permanent-field AC servomotors. These motors must be suitable for operation with frequency inverters. Other loads must not be operated with these inverters. ® MOVIDYN servo controllers are units intended for stationary installation in switch cabinets. All information pertaining to technical data and required conditions at the site must strictly be followed. Startup (beginning of normal use) is not permitted until it is determined that the machine meets the EMC directive 89/336/EWG and the conformity of the finished product with the machine directive 89/392/EWG is established (observe EN 60204). ® 4 MOVIDYN Servo Controller Operating Instructions 1 The following are prohibited unless expressly stated otherwise: • operation in areas subjected to explosion hazards • operation in the vicinity of harmful oils, acids, gases, vapors, dust, radiation, etc. • operation in non-stationary systems where mechanical vibration and impact loads occur that exceed the requirements of EN50178 • operation in applications in which the inverter itself (without higher-level safety systems) performs safety functions that must ensure the protection of equipment and life Disposal Please observe all applicable waste disposal regulations: Carry out the disposal according to the materials used and relevant regulations, such as: Electronics waste (circuit boards), plastic (housing), sheet metal, copper, etc. Documentation Title Order no. DFS/DFY Synchronous Motors Operating Instructions 0922 7113 Communications Interfaces Manual 0922 8764 Parameter List Manual 0921 2868 IPOS Positioning Control Manual 0922 341X APA12 / API12 Single-Axis Positioning Control Manual 0922 8713 MD_SHELL Manual 0921 9315 MD_SCOPE Manual 0921 9412 Fieldbus Unit Profile Manual 0922 761X "CAN-Bus" AFC11A Option Manual 0922 6567 "INTERBUS" AFI11A Option Manual 0922 7717 "PROFIBUS" AFP11A Option Manual 0922 856X "DeviceNet" AFD11A Option Manual 0919 6818 Fieldbus Interfaces Documentation Package 0922 7814 APA12/API12 Positioning Control Documentation Package 0921 6774 Drive Engineering – Practical Implementation, Volume 7, "Servo Drives: Basics, Characteristics, Project 0922 4610 Planning" This documentation can be obtained from SEW by using the respective order number. ® 5 MOVIDYN Servo Controller Operating Instructions 2 2 Safety Instructions Installation and • In compliance with existing regulations (e.g., EN 60204, VBG 4, DIN-VDE 0100/ Startup 0113/0160), only electrical specialists with accident prevention training are permitted to perform installation, startup, and service work on the unit. • Observe the respective instructions for installation and startup of motor and brake! • Preventive measures and protection devices must correspond to the existing regulations (e.g., VDE 0100 T410 / VDE 0112 T1 or DIN 60204 / VDE 0160). Necessary protective measures: Grounding of unit Necessary protection devices: Overcurrent protective device (fuses) • Use appropriate measures (e.g., removing the electronic terminal block) to ensure that the connected motor does not start automatically when the inverter is powered up. Operation and • Before removing the protective cover, disconnect the unit from the supply system. Service Dangerous voltages may still be present for up to 10 minutes after shutdown. • If the protective cover is removed, the unit enclosure type is IP 00. All modules except for the control electronics feature dangerous voltages. During operation, the unit must be closed. • In the energized state, dangerous voltages occur at the output terminals and the attached cables and motor terminals. This also applies if the unit is inhibited and the motor is stopped. • The fact that the Status LED and other display elements are no longer illuminated does not indicate that the unit has been disconnected from the power supply and does not carry any voltage. • Unit-based safety functions or mechanical blocking can result in motor standstill. Removing the cause of this problem or resetting the drive can result in the drive re- starting on its own. If this is not permissible for safety reasons: Before correcting the fault, the unit must be disconnected from the supply system. In these cases it is also prohibited to activate the function “Auto-Reset” (P630). ® 6 MOVIDYN Servo Controller Operating Instructions MPR / MPB 3 3 Unit Design 3.1 MPR / MPB 12 4 3124 5 5 6 8 8 9 9 10 10 17 11 13 12 12 13 14 14, 11 24 24 17 16 15 16 15 00249CXX Figure 1: System overview of MPR / MPB power supply module 1 Nameplate 2 Protective conductor connection 3 Protective cover 4 Shield ground connection 5 Supply system connection (X1; MPx: 1, 2, 3; MKS: L1, L2, L3) 6 Braking resistor connection (MPB: X4; MKS: X1; +, R) 7 DFS/DFY motor connection (X1; MAS: 1, 2, 3; MKS: U, V, W) 8 Protective conductor connection 9 DC link connection (X1) 10 24 V bus (MPx: X3 (output); MAS: X2 (input), X3 (output)) 11 External 24 V connection (MPR: X2; MPB: X02 (5, 6); MKS: X41 (5, 6)) 12 MKS: X2/MPR: X01: ABG11 or USS11A can be connected; MPB: X01: RS-232 serial interface 13 Status LEDs ® 7 MOVIDYN Servo Controller Operating Instructions MAS / MKS 3 3.2 MAS / MKS 56 2 312 4 4 7 7 8 9 23 10 12 10 24 1 18 22 19 18 21 14, 11 22 19 21 20 16 20 24 23 15 15 00250BXX Figure 2: System overview of MAS axis module / MKS compact servo controller 14 RS-485 serial interface (MPR: X02; MPB X02 (1, 2, 3); MKS: X41 (1, 2, 3)) 15 Shield ground connection (electronic leads) (X0) 16 Data bus connector (underside of unit) (X5) 17 Heat sink fan connector (MPR: X6; MPB: X2) 18 7-segment display 19 Resolver connection (X31) 20 Encoder simulation output (X32) 21 X21: output 10 V (1, 4), analog differential input (2, 3), binary inputs (5 ... 8), binary outputs (9, 10), output 24 V (11, 12) 22 S1 button 23 Option card slot 24 Service label MKS: Illustration without protective cover ® 8 MOVIDYN Servo Controller Operating Instructions TYP: MKS51A005-503-00 SACH.NR.: 8260443 SERIEN-NR: 02912 Unit Designation 3 3.3 Unit Designation Nameplate Example: 00277AXX Figure 3: Sample nameplate ® CE Designation MOVIDYN servo controllers meet the guidelines of the low voltage directive 73/23/ EWG and the EMC directive 89/336/EWG. 3.4 Type Designations ® MOVIDYN MAS51A005-503-00 Design 00 = Standard 50 = IPOS unit Connection 3 = 3-phase Voltage supply 50 = 500 V (380 ... 500 V ) AC AC 005 = 5 A MAS/MKS: rated current AC 011 = 11 kW MPR/MPB: rated power Version A Series 51 Type MAS (MPB/MPR/MKS) 00278DEN Figure 4: Sample type designation Examples: MAS 51A 015-503-00 axis module with 15 A rated output current, 3 x 500 V, standard design MPB 51A 027-503-00 power supply module with brake chopper with 27 kW rated output power, 3 x 500 V, standard design ® 9 MOVIDYN Servo Controller Operating Instructions Design of an Axis System 4 4 Mechanical Installation 4.1 Design of an Axis System Switch Cabinet Installation in a switch cabinet with application-specific enclosure Avoid dust accumulation and moisture condensation. Provide for installation of ventilation filter mats in the case of forced air-cooling. Minimum Above and below the units: at least 100 mm (3.94 in) Clearance for Cooling Heat Sink Clean the surfaces of the heat sinks and the backs of the power supply and axis modules with a dry cloth. Fasten the power supply and axis modules onto the heat sinks. The heat sinks feature tapped holes in a 35-mm (1.38 inch) grid for this purpose. Munting is carried out without heat sink compound. Tightening torque of screws: max. 3.5 Nm. Each module must be installed completely on one heat sink, i.e., do not mount a module over the joint of two heat sinks. incorrect correct DKF 05 DKF 05 DKF 05 DKF 07 Vie Blicw k from von oben top MD0018BE Figure 5: Installation of heat sinks The MKS compact servo controllers feature integrated heat sinks. If several heat sinks are used in a multi-axis block, care must also be taken that they 2 2 feature a (large-size, ≥ 10 mm [0.155 in ]) conducting connection. If this is not the case with coated mounting surfaces, the connection must be ensured by using a bridge (litz ® wire with corresponding cross-section) between the mounting screws of the MOVIDYN modules from one heat sink to the next one. Line Chokes Mount the line chokes close to the corresponding unit, but outside of the minimum cooling clearance. The MKS compact servo controllers do not require line chokes. Braking They should be mounted in a well-ventilated location, e.g., on top of the switch cabinet. Resistors The resistor surface reaches high temperatures under load with rated power. Axis Modules Mount the axis modules to the right of the power supply modules; otherwise, the 24 V DC connection is difficult to mount. ® 10 MOVIDYN Servo Controller Operating Instructions MPB 51A 027-503-00 MAS 51A 015-503-00 -00 MAS 51A 015-503-00 MAS 51A 015-503-00 MPB 51A 027-503-00 MAS 51A 015-503-00 -00 MAS 51A 015-503-00 MAS 51A 015-503-00 Installation of Option PCBs 4 4.2 Installation of Option PCBs Before You Begin • Keep the option pcb in its original packaging and remove it only when you are ready to exchange it. • Grasp only the edge of the pcb and do not handle it too often. Do not touch any components. • Also observe the addendum to the operating instructions that accompanies the pcb. • The pcb is supplied with the necessary voltage via rear panel connector. The required power may make it necessary to connect an external 24 V supply. Installation of • Disconnect the supply voltage of the servo controller. Switch off the supply voltage Option PCB and the 24 V supply, if necessary. Cover plate A special cover plate is delivered for use on the MKS compact servo controller. Option PCB Guide rails Rear connector Screws MD0054CE Figure 6: Installation of option pcb ® 11 MOVIDYN Servo Controller Operating Instructions Installation of Option PCBs 4 • MAS: Remove the black front left cover plate: Remove both the crosstip screws. MKS: Remove the lower part of the protective cover. Caution: In its open state, the unit features enclosure rating IP00. Dangerous voltages may still be present for up to 10 minutes after shutdown. • Take appropriate ESD measures (anti-static band, conductive shoes, etc.) before touching the option pcb. Insert the pcb into the guide rails of the slot with the back of the connector pointing backwards. Ensure that the pcb is also properly inserted in the rear guide rails. • Press the rear connectors on the pcb into the sockets in the housing. The connector housings of the front of the pcb must be flush with the cover of the axis module / compact servo controller. • MAS: Fit the included cover plate over the pcb slot (2 screws). MKS: Depending on the option pcb, the protective cover may not be mountable for the compact servo controller. In this case, affix the included cover plate instead. Startup of Option • Detach connector X21 (binary inputs/binary outputs) to prevent unintentional motor Card start. • Connect the unit to supply voltage or 24 V supply. • Verify by means of the corresponding menu items whether the computer “recognized” the option card (if necessary, check the function of the pcb). • Program the terminal assignment to the corresponding function before startup of the drive. • If necessary, switch off the supply voltage and the 24 V supply. • Attach connector X21. ® 12 MOVIDYN Servo Controller Operating Instructions Assembly Instructions for Shield Clamps 5 5 Electrical Installation For electrical installation, the section on Safety Notes must be strictly observed! ® The following sections describe the installation of MOVIDYN servo controllers. To achieve interference-free operation under all conditions, it is recommended to perform EMC-compliant installation. 5.1 Assembly Instructions for Shield Clamps Shield clamps provide for simple connection of motor, braking resistor, and signal cable shields. Assembly can be especially simplified with EMC-compliant cabling. In addition, the shields are flat and, therefore, placed very effectively. 03843AXX Figure 7: Shield clamps Assembly • The illustration shows correctly installed shield clamps for supply and brake connection on a power supply module, motor connection on an axis module, and connection of electronic cables on an axis module. The shield clamps on a compact servo controller should be connected in the same way. • Do not perform the assembly of motor and braking resistor cable with the terminal attached as parts of the braid shield may fall into the unit. ® 13 MOVIDYN Servo Controller Operating Instructions Supply, Inverter, and Motor Connection 5 • Expose approximately 30 mm of the shield so that the cable has the correct connection length. Prefabricated cable from SEW is correctly exposed. • Fasten the shield clamp onto the unit using the supplied screws. Do not use longer screws. • Connect the cable at this time only. This prevents the shield from being stressed and parts of the shield from becoming detached. 5.2 Supply, Inverter, and Motor Connection Power Supply Connect the power supply module and axis module(s) to the supplied conductor rail. Module – Axis Firmly tighten all connections, including PE protective conductor. Module Tightening torque: max. 3.5 Nm Connection • For the electronics voltage supply, attach connector X3 of a module to connector X2 of the following module using the supplied cables. 2 Cross-section: 1.5 mm (AWG#16) • Attach the X5 connectors of the module (bottom side of unit) with the DBK data bus cable. Important: Do not cut off the unused connectors of the DBK but, instead, fold them over and tie them down. Braking Resistor Connect the braking resistor to terminals X4.+ and X4.R at the MPB... power supply Connection module or to terminals X1.+ and X1.R at the compact servo controller. Use two cables located close to each other (e.g., twisted pair). The line cross section should be dimensioned for maximum brake current. Caution: The leads to the braking resistor carry high DC voltages (up to approx. 900 V ) in rated operation! DC DKF Heat Sink Connect the fan to terminals X2.2 and X2.3 of the MPB... power supply module or to terminals X6.1 and X6.2 of the MPR... power supply module. Important: Observe the polarity: X2.2 / X6.2: black cable / X2.3 / X6.1: red cable ® 14 MOVIDYN Servo Controller Operating Instructions Supply, Inverter, and Motor Connection 5 24 V Supply The MPB and MPR power supply modules and the MKS compact servo controller have DC their own internal 24 V voltage supply which can provide the following power levels: DC Type MPB51A MPR51A MKS51A P [W] 240 50 29 max, 24 V The 24 Vdc supply in the MPB/MPR supplies the MAS axis modules connected, whereas in the MKS, only the option pcbs are supplied. To provide the supply for the output stage, the MAS51A axis modules require the following power supply which they always draw from the internal 24 V supply of the DC power supply module. MAS51A 005 010 015 030 060 type P 5 5 5 7.5 15 24 V, internal [W] If the fans in the DKF heat sinks are supplied via a power supply module, the required power must also be taken into consideration. Type DKF05 DKF07 DKF09 P [W] 69 24 V The control and evaluation pcb present in every MAS/MKS or the option pcb in MAS/ MKS have the following power consumptions: Type Control / AIO11 AFC11 AFI11 AFP11 AFD11 APA/ evaluation API11/12 1) 2) P [W ] typ./max. 12 / 16.3 8 / 13.1 1 / 1.5 1.5 / 2.3 1.3 / 1.8 0.8 / 1.0 10 / 110 24 V 1) A relay current of approximately 30 mA was used as an example for a typical load of a binary output. 2) In general, an external 24 V supply is necessary if the binary outputs of the API are loaded correspondingly! Internal 24 V If the power of the internal 24 V voltage supply is insufficient, an external 24 V DC DC DC supply insufficient power supply must be connected. It should be noted that the 24 V switch cabinet DC supply is frequently insufficient in the case of larger systems. If the capacity of the internal 24 V voltage supply is insufficient, the voltage range of the external voltage DC supply measures 24 ... 30 V . DC 24 V supply for If the capacity of the internal 24 V voltage supply is sufficient and the external 24 V DC DC DC power off voltage supply is used, for example, to maintain communication, position detection, etc., during power off, then the voltage range of the external supply voltage measures 18 ... 30 V . DC Example The power demand of a system consisting of MPB, MAS51A010 with AIO11 and MAS51A030 with API12 is calculated as follows: 5 + 12 + 8 + 7.5 + 12 + 10 = 54.5 W typical 5 + 16.3 + 13.1 + 7.5 + 16.3 + 110 = 168.2 W max. ® 15 MOVIDYN Servo Controller Operating Instructions Supply, Inverter, and Motor Connection 5 24 V supply of DC MPR... With the external 24 V supply (+ 24 V ... + 30 V ) DC DC DC MPR... MAS... MAS... X2 X3 X2 X3 X2 X3 1 1 1 1 1 1 2 2 2 2 2 2 + 24 V ext. DC 3 3 3 3 3 3 0V24 ext. Without the external 24 V supply DC Not on (permissible with 2 axis modules without option pcb or 1 axis module with option pcb) MPB... ! MPR... MAS... MAS... X2 X3 X2 X3 X2 X3 1 1 1 1 1 1 2 2 2 2 2 2 3 3 3 3 3 3 MD0164DE Figure 8: 24 V supply of MPR… DC SEW strongly recommends using a separate 24 V power supply for the MPR modules DC since the 24 V switch cabinet supply is frequently insufficient, especially in the case DC of extended systems. Supply System • Designate supply system leads with L1, L2, L3 in accordance with IEC 445. Lead, Input Fuses • Firmly tighten all connections, including PE protective conductor. Tightening torque: max. 3.5 Nm. • Install the F1/F2/F3 input fuses directly behind the conductor branch of the supply system cable. • Always install the supply contactor in front of an input filter, if present (→ EMC- compliant installation). Motor Lead • Cable length: max. 100 m (325 ft). • Designate motor leads with U, V, W in accordance with IEC 445. • Firmly tighten all connections, including PE. Tightening torque: max. 3.5 Nm. Important: Observe the phase sequence (→ wiring diagrams)! • The motor lead must be routed separately from all other lines. If a minimum distance of 20 cm (8 in) cannot be maintained over longer distances (20 m [65 ft]), it is recommended to shield the motor lead. If shielding cannot be achieved, please consult SEW. • Output filters between servo controller and motor are not permitted. ® 16 MOVIDYN Servo Controller Operating Instructions Control of the Mechanical Brake 5 Resolver Cable • Use a shielded cable with twisted pairs (1/2, 3/4, 5/6) (→ wiring diagrams). Length: max. 100 m (325 ft) 8-core: 3 x 2 for resolver, 1 x 2 for motor protection 2 Cross-section: l > 50 m (164 ft): 0.50 mm (AWG#20) 2 l ≤ 50 m (164 ft): 0.25 mm (AWG#24) • Ground the shield flat on both sides. For this purpose, connect the complete cross- section of the braid shield as a short section, i.e., without extension, to the X0 shield terminal. Motor and Device • To protect the motor, connect the TH winding thermostat or TF PTC thermistor (→ Protection wiring diagrams). A motor protection switch is not suitable. • Protect the braking resistor (not for MPR… power supply module) with a thermal overcurrent protection switch (F16) from an excessive cyclic duration factor. The thermal overcurrent protection switch must act directly on the K11 supply system contactor. 5.3 Control of the Mechanical Brake (only for Important: Observe the operating instructions for DFS/DFY motor and the following operation with block diagram! motor types DFS/ In addition, observe the following notes to ensure proper functioning of the mechanical DFY ... B) brake. • Control the brake via X21.9 binary output “brake” and not via PLC (brake control system by the PLC can lead to uncontrolled system conditions)! • The binary output X21.9 is not suited for direct activation of the brake! It is implemented as a relay driver with a control voltage of 24 V / 3.6 W / max. 150 mA. It is recommended to connect the following (observe the switching capability of the brake relay or the miniature contactor): – an external K13 braking relay that is suitable for control of K12 auxiliary contactors (e.g., contact rating of 250 V / 0.25 A / AC11 or 24 V / 0.6 A AC AC DC DC / DC11 in accordance with IEC 337-1). The contact of K13 braking relay is connected in series with the other closure contacts on the system side that control the K12 auxiliary contactor for brake excitation. It is also possible to use relays with internal rectifiers. The braking relay may not be used for direct switching of the brake excitation without using an auxiliary contactor! – or a K12 miniature contactor (= auxiliary contactor) (24 V / 3.6 W / 150 mA) as direct brake control system. • If BME brake rectifiers are used: Connect the BME to a separate supply system lead; do not supply it via motor voltage! Route the connecting line brake - BME separately from the motor lead and shield it, if possible. • If the BSG brake control unit (24 V supply voltage) is used: DC The voltage supply for terminals X21.. of the unit and for the BSG must be implemented separately! • The reaction of the brake through cut-off of the brake rectifier can be carried out in the AC circuit (reaction time t or in the DC and AC circuit (reaction time t ). 2I) 2II ® 17 MOVIDYN Servo Controller Operating Instructions Control of the Mechanical Brake 5 For hoists, use only the disconnection on the DC side and the AC side! Brake Reaction Times 1) DFS/DFY type brake 56B 71B 90B 112B motor Brake torque [Nm] 2.5 3 6 10 15 6 12 20 30 40 17.5 35 60 90 [in-lb] 22 26 53 88 133 53 106 177 265 354 155 309 530 796 Releasing the brake 2) Response time t [ms] 7 10121620 11 13151822 11 142235 1 Reaction of the brake 3) Reaction time t [ms] 5400 220 120 65 200 140 90 55 42 440 315 230 170 2I 4) Reaction time t [ms] 95 45 20 8 40 28 20 13 10 130 60 32 20 2II 1) For type DFS56B, use disconnection on DC side only since 24 V brake without brake rectifier is used. 2) With BME brake rectifier or BSG brake control unit 3) Disconnection on AC side 4) Disconnection on DC and AC side Block Diagram DY..B brake motor with BME brake rectifier via K13 brake relay and K12 auxiliary contactor. Cut-off in both DC and AC circuit (t ) 2II Cut-off in the AC circuit (t ) only 2I V V AC AC X21.9 X21.9 K13 K13 X21.11 X21.11 K12 K12 1 1 MAS ... / MAS ... / 2 2 MKS ... MKS ... 3 3 BME BME 4 4 13 13 14 14 PE PE 15 15 Switch cabinet Switch cabinet 1 1 2 bl 2 bl DFS/ DFS/ 3 3 wh wh DFY DFY PE PE rd rd Brake Brake Brake Brake connector connector MD0032CE Figure 9: Brake control system ® 18 MOVIDYN Servo Controller Operating Instructions Electronic Lines and Signal Generation 5 5.4 Electronic Lines and Signal Generation 2 • The electronic terminals are suitable for line cross-sections up to 1.5 mm (AWG16). • Unshielded lines should only be used with twisted-pair wires for feed and return lines. Route them separately from power-carrying lines, auxiliary control lines or braking resistor lines. • OV lines should never be connected for signal generation. • OV lines inside an axis system are connected via the data bus (0V5, X5) and the 24 V bus (0V24, X2). • OV lines of several axis systems should not be looped from system to system but, instead, wired point-to-point. • Binary input instructions can be issued from machine control as a direct “0”↔“1” instruction. For this purpose, connect the reference potential of binary input X21/11 with the reference potential (0V) of the machine control. • If coupling relays are necessary, use only those featuring enclosed, dust-proof electronic contacts. The coupling relays must be able to switch small voltages and currents (5 - 20 V; 0.1 - 20 mA). 5.5 EMC-Compliant Installation ® The MOVIDYN units meet the requirements for maintaining the EMC directive 89/336/ EC if the instructions for EMC-compliant installation are observed. ® Interference MOVIDYN servo controllers meet all requirements of EN50082-2 with interference Immunity immunity. Interference Higher interference levels are permissible in industrial areas. Dependent upon the Emission condition of the supply system and the system configuration, some or several of the measures described below may be omitted. Maintaining SEW recommends the following measures in order to adhere to the limits of interference interference limits emission in residential, commercial, and industrial areas (Limit Class B in accordance with EN55011): ® Input Filter • For all MOVIDYN , use a suitable NF input filter on the input side and an HD00X output choke or shielded motor lead on the output side. ® • Install NF input filters close to the MOVIDYN outside of the minimum clearance area. ® • Limit the line between input filter and MOVIDYN to the absolute minimum length required; maximum permissible length is 400 mm (15.75 in). Unshielded twisted cables are sufficient. Also use only unshielded cables for the supply system lead. • If several inverters are connected to an input filter, this input filter must be mounted directly at the cable entry of the switch cabinet or in the immediate proximity of the inverter. The selection of the input filter is determined by the total current of the inverter. ® • Carry out HF-compliant earthing of the MOVIDYN (flat metallic contact of the unit housings with earth, e.g., uncoated mounting plate of switch cabinet). ® 19 MOVIDYN Servo Controller Operating Instructions EMC-Compliant Installation 5 Shielding • The control lines and motor leads must be shielded. If an HD00X output choke is used, the shielding is not mandatory. • Routing all lines separately in individual, earthed metal ducts or metal pipes also qualifies as shielding. • Earth the shield on both sides using the shortest distance and flat contacts. • To avoid ground loops, one end of the shield can be earthed via a suppression ® capacitor. With double-shielded cable, earth the outer shield on the MOVIDYN side and the inner shield at the other end. ® 20 MOVIDYN Servo Controller Operating Instructions EMC-Compliant Installation 5 EMV-Compliant Connection MD0033FE Figure 10: EMC-compliant installation in residential areas (in accordance with Limit Class B) On the output side, a regular cable with HD00X output choke can be used for the motor connection instead of the shielded cable. ® 21 MOVIDYN Servo Controller Operating Instructions UL-Compliant Installation 5 HD00X Output Choke for Motor Lead UV W MKS... 12 3 MAS... ® MOVIDYN HD... output choke 5 windings Terminals of the UV WPE output choke motor cable to the motor 03859ADE Figure 11: HD00X output choke All three output phases must always be routed together through the toroid core. PE and the shield of shielded cables are not routed through the toroid core! 5.6 UL-Compliant Installation The following information applies only in connection with UL-listed devices that are identified by the UL designation on the nameplate. Observe the following information for U ® L UL-compliant installation: • Only use copper cables with the temperature range 60/75 °C as connection lead: ® • The permissible tightening torques of the MOVIDYN power terminals are: U C ® L MPB51A, MPR51A, MAS51A → 3.5 Nm (31 in.-lbs.) MKS51A → 1.5 Nm (13.3 in.-lbs.) ® • MOVIDYN drive inverters are suitable for operation in voltage networks that can deliver a maximum current according to the following table and carry a maximum voltage of 500 V . The rating for the fuses is not to exceed the values listed in the AC table: Maximum Values for Installation in ® MOVIDYN type Max. current Max. supply voltage Fuses Accordance with MPB51Axxx-503-xx 5000 A 500 V - UL/cUL MPR51Axxx-503-xx MAS51Axxx-503-xx MKS51A005-503-xx MKS51A010-503-xx MKS51A015-503-xx 10000 A 500 V 30 A / 600 V ® 22 MOVIDYN Servo Controller Operating Instructions Wiring Diagrams 5 5.7 Wiring Diagrams MPB.../ MAS... Wiring Diagram 3 x 380 ... 500 V Thermal PE L1 L2 L3 overload protection F11 F16 F12 F13 DFS/DFY R ND BW K11 Supply system contactor y y 132+ X1 X4R 1 2 3 X1 Supply Braking resistor Motor system Axis module Power supply MAS module MPB yy y DC link DC link A A B DC link A B BB B X1 X1 X1 DKF 1 1 1 1 Fan 2 2 2 2 Heat sink 3 3 3 3 X2 X3 X2 X3 24 V 24 V 24 V MD_SHELL 1 MD_SCOPE * = Factory setting 2 3 4 1 + 10 V Setpoint 5 Brake 2 Analog input+ (based on X01 6 PC connection 3 Analog input - difference) BME 4 0V10 Resolver X31 RS-232 5 Controller inhibit RS-485 6 Enable/rapid stop* A 1 K12 1 RS-485 + 7 /limit switch Right* A 2 2 RS-485 - 8 /limit switch Left* B 3 0V RS-485 3 9 /Brake B 4 F14 F15 4 Not assigned K13 10 Ready for operation C 5 5 0V 24 V ext. 11 0V24 C 6 + 24 V ext. 6 Relay 12 24 V 0V5 7 VAC max. 150 mA X02 24 V ext. Incremental encoder X21 X32 simulation Data bus Data bus X5 X5 DBK 02991BEN Figure 12: MPB/MAS wiring diagram ® 23 MOVIDYN Servo Controller Operating Instructions Wiring Diagrams 5 MPR.../MAS... Wiring Diagram 3 x 380 ... 500 V PE L1 L2 L3 F11 F12 F13 DFS/DFY R Supply system contactor K11 ND y y 13 2 X1 1 2 3 X1 Supply system Motor Power supply Axis module module MAS MPR yy y DC link DC link A A B DC link A B BB B X1 X1 X1 1 0V 24 V ext. 1 1 1 ⇒ 2 + 24 V ext. 2 2 2 3 3 3 3 X2 24 V ext. X3 X2 24 V X3 24 V 24 V 1 ABG11 2 * = Factory setting 3 4 1 + 10 V Set point 5 Brake 2 Analog input + (based on 6 3 Analog input - difference) Connection for BME 4 0V10 Resolver X31 or ABG11 5 Controller inhibit or 6 Enable/rapid stop A 1 USS21 / PC X01 K12 0V5 - + 7 /Limit switch Right A 2 RS485 8 /Limit switch Left* B 3 RS232 9 /Brake B 4 F14 F15 1 RS-485 + K13 10 Ready for operation C 5 USS21 2 RS-485 - 11 0V24 C 6 3 0V RS-485 Relay 12 24 V 0V5 7 V max. 150 mA AC X02 RS-485 Incremental encoder X21 X32 simulation Fan Data bus Heat sink Data bus MD_SHELL MD_SCOPE X5 X6 3 2 1 X5 DKF DBK 02992BEN Figure 13: MPR/MAS wiring diagram ⇒ Bridge required on last axis module if no external 24 V is present. ® 24 MOVIDYN Servo Controller Operating Instructions Wiring Diagrams 5 MKS... Wiring Diagram 3 x 380 ... 500 V PE L1 L2 L3 F11 F16 F12 F13 DFS/DFY R BW K11 ND ABG11 yy 132+R U V W X1 Supply Braking resistor Motor system ABG11 or USS21 / PC MKS Compact Servocontroller connection X2 0V5 - + RS485 RS232 RS-485 USS21 RS-485 + 1 RS-485 - 2 0V RS-485 3 not assigned 4 0V 24 V ext. 5 + 24 V ext. 6 MD_SHELL MD_SCOPE 24 V ext. X41 1 2 3 4 1 + 10 V Setpoint 5 Brake Analog input+ 2 (based on 6 difference) 3 Analog input- BME 4 0V10 Resolver X31 5 /Controller inhibit 6 Enable/rapid stop* A 1 K12 7 /Limit switch Right* A 2 8 B 3 /Limit switch Left* 9 /Brake B 4 F15 F14 K13 10 Ready for operation C 5 11 0V24 C 6 Relay 12 24 V 0V5 7 V max. 150 mA AC Incremental encoder X21 X32 * = Factory setting simulation 02993BEN Figure 14: MKS wiring diagram ® 25 MOVIDYN Servo Controller Operating Instructions Description of Terminal Functions 5 5.8 Description of Terminal Functions Terminals on the MPB Power Supply Module 51A xxx-503-00 Function Plug Terminal Data Shield earth X0 RS-232 serial interface X01 2 TXD = transmit data line Shielded cable, max. PC connection 3 RXD = receive data line length 5 m (15 ft) 9-pole sub D connector 4 DTR = send/receive switchover 5 0V5 = RS-232 reference potential RS-485 serial interface X02 1 RS-485 + Shielded cable, max. alternative PC connection 2 RS-485- length 200 m (650 ft) 3 0V5 = RS-485 reference potential Not assigned 4 Connection of external 24 V 5 0V24 = external 24 V reference potential Power consumption: supply 6 + 24 V (+ 18 V ... + 30 V ) see Electrical Installation DC DC Supply voltage connection X1 1 V = 3 x 380 ... 500 V 10 % in AC 2 3 DC link potentials +V V = 700 V / V = 900 V Z Z DC Zmax DC Axis module connection with bus -V Z barsyPE (protective conductor) Internal voltage X2 1 Connection not allowed, unit may be damaged Fan connection for DKF.. type heat 2 0V24 sink 3 +24 V DC Axis modules electronics voltage X3 Supplied cable supply output (24 V bus) BW braking resistor connection X4 +R Select type according to technical data Cable length: max. 100 m (325 ft) Data bus connector (underside of X5 Data bus cable connection unit) Terminals on the MPR Power Supply Module 51A xxx-503-00 Function Plug Terminal Data Shield earth X0 RS-485 serial interface X02 1 RS-485+ shielded cable, alternative PC connection 2 RS-485- max. length 200 m 3 0V5 = RS-485 reference potential (650 ft) Supply voltage connection X1 1 V = 3 x 380 ... 500 V 10 % in AC 2 3 DC link potentials +V V = 700 V / V = 900 V Z Z DC Zmax DC Axis module connection with bus -V Z barsyPE (protective conductor) Connection of external 24 V X2 1 24 V (+18 V ... + 30 V ) (see Ch. xx) Power consumption: DC DC supply (VDE 19240) see Electrical Installation 2 0V24 = 24 V reference potential 3 not assigned Axis modules electronics voltage X3 Supplied cable supply output (24 V bus) Data bus connector (underside of X5 DBK.. data bus cable connection unit) Fan connection for DKF type heat X6 1 +24 V DC sink 2 0V24 Internal voltage 3 Connection not allowed, unit may be damaged ® 26 MOVIDYN Servo Controller Operating Instructions Description of Terminal Functions 5 Terminals on the MAS Axis Module 51A xxx-503-xx Function Plug Terminal Data Shield earth X0 DC link potentials X1 +V V = 700 V / V = 900 V Z Z DC Zmax DC Connection with bus bars -V Z yPE (protective conductor) Connection of DFS/DFY 1 V = V Max. length 100 m max in permanent-field synchronous 2 (325 ft) motor 3 yPE (protective conductor) Electronics voltage supply input X2 Supplied cable (24 V bus) 10 V voltage supply, e.g., for X21 1 +10 V , max. 3 mA DC setpoints 4 0 V 10 = reference potential 10 V DC Analog differential input 2 V setpoint 1: -10 V ... + 10 V R ≥ 20 kΩ A1 DC DC i 3 Binary inputs Selection of 10 functions: Enable / ramp generator switchover / controller inhibit / hold control / external fault / reset / external trigger / limit switch CCW / limit switch CW / no function (with IPOS also: reference travel / ref. cam) Fixed 5 /Controller inhibit “1” : +13 V .. + 30.2 DC V 1) DC User-programmable 6 Enable typically + 24 V (6 mA) 1) “0” : -3 V .. +5 V User-programmable 7 /Limit switch CW DC DC (DIN 19240) 1) User-programmable 8 /Limit switch CCW Binary Outputs Selection of 9 functions: Ixt warning / ready for operation / failure / brake / speed reference / current reference / setpoint actual value comparison / motor standstill / no function (with IPOS also: in position / pos. output 1 ... 8 / IPOS reference) Fixed 9 Relay driver for brake relay “1”: + 24 V ; max.150 mA DC 1) User-programmable 10 Ready for operation “1”: + 24 V ; max. 50 mA DC Voltage output 24 V, 11 0V24 = 24 V reference potential DC e.g., for binary inputs 12 + 24 V max. 200 mA DC Electronics voltage supply output X3 Supplied cable (24 V bus) Motor resolver connection X31 1, 2 Resolver signals Twisted pair, shielded, 3, 4 max. length 100 m (325 5, 6 ft) Output incremental encoder X32 1, 2 A, /A RS-422 level, 1024 simulation 3, 4 B, /B pulses/revolution 5, 6 C, /C 7 0V5 = incremental encoder simulation reference potential Data bus connector (underside of X5 DBK.. data bus cable unit) 1) Factory Setting ® 27 MOVIDYN Servo Controller Operating Instructions Description of Terminal Functions 5 Terminals on the MKS Compact Servo Controller 51A xxx-503-xx Function Plug Terminal Data Power connection X1 L1 Supply system: V = 3 x 380 ... 500 V 10 % in AC L2 L3 + Braking resistor R Connection of DFS/DFY U V = V Max. length 100 m max in permanent-field synchronous V (325 ft) motor W Connection for hand-held terminal X2 or serial interface 10 V voltage supply, e.g., for X21 1 +10 V , max. 3 mA DC setpoints 4 0V10 = 10 V reference potential DC Analog differential input 2 V setpoint 1: -10 V ... +10 V R ≥ 20 kΩ A1 DC DC i 3 Binary inputs Selection of 10 functions: Enable / ramp generator switchover / controller inhibit / hold control / external fault / reset / external trigger / limit switch CCW / limit switch CW / no function (with IPOS also: reference travel / ref. cam) Fixed 5 /Controller inhibit “1”: +13 V ... DC + 30.2 V 1) DC User-programmable 6 Enable Typically: +24V (6mA) DC 1) “0”: -3 V ... +5 V User-programmable 7 /Limit switch CW DC DC (DIN 19240) 1) User-programmable 8 /Limit switch CCW Binary Outputs Selection of 9 functions: Ixt warning / ready for operation / failure / brake / speed reference / current reference / setpoint actual value comparison / motor standstill / no function (with IPOS also: in position / pos. output 1 ... 8 / IPOS reference) Fixed 9 Relay driver for brake relay “1”: +24 V ; max. 150 mA DC 1) User-programmable 10 Ready for operation “1”: +24 V ; max. 50 mA DC 24 V voltage output, e.g., for binary 11 0V24 = 24 V reference potential max. 200 mA DC inputs 12 +24 V DC Motor resolver connection X31 1, 2 Resolver signals Twisted pair 3, 4 Shielded cable 5, 6 Max. length 100 m (325 ft) Output incremental encoder X32 1, 2 A, /A RS-422 level, 1024 simulation 3, 4 B, /B pulses/revolution 5, 6 C, /C 7 0V5 = incremental encoder simulation reference potential RS-485 serial interface X41 1 RS-485+ 2 RS-485- 3 0 V reference potential Connection of external 24 V 4 Not assigned Power consumption: supply 5 0 V reference potential see Electrical Installation 6 +24 V (18... 30 V ) DC DC 1) Factory setting ® 28 MOVIDYN Servo Controller Operating Instructions RS-485 Interface Connection 5 5.9 RS-485 Interface Connection ® Using the RS-485 interface, a maximum of 32 MOVIDYN units, for example, for ® master-slave operation, or a maximum of 31 MOVIDYN units and a higher-level control system (PLC) can be connected with each other. MPB/MPR MKS X02: X41: RS-485+ RS-485+ 1 1 RS-485- RS-485- 2 2 0V5 3 0V5 3 yy 02241AXX Figure 15: RS-485 cabling Important • Use a 4-core and shielded cable, twist the two signal cables, and place the shield flat ® on both sides of the electronic shield clamp of MOVIDYN or earth it at the higher- level control system. • Route the 0V5 reference potential through the second cable pair. Potential shift may occur between the units connected by RS-485. • The maximum total line length is 200 m (660 ft). • Dynamic terminating resistors are permanently built in. Do not connect any external terminating resistors! ® 29 MOVIDYN Servo Controller Operating Instructions I Initial Settings 6 0 0 6 Startup Observe the Safety Notes! 6.1 Initial Settings Perform the following to be able to program the units and set parameters: • Connect the power supply module or compact servo controller and PC with the interface cable (compact servo controller via USS21A option). Important: Power supply module/compact servo controller and PC must be disconnected. • Ensure that the cabling complies with the wiring diagram! • Set the axis address at the axis modules or the compact servo controllers. Each axis module must have a unique address. • Install and start the MD_SHELL PC user interface (→ Configuring MD_SHELL User Interface). ® 30 MOVIDYN Servo Controller Operating Instructions I Initial Settings 6 0 0 Setting the Axis On delivery and after calling up the factory setting (→ P610, Set parameters), the units Address feature the address “00.” For multi-axis operation, SEW does not recommend using the axis address “00.” After calling up the factory setting, avoid using axis modules with identical addresses. The S1 button is used to set the address to address 0 … 59: With external 24 V dc Without external 24 V dc voltage supply voltage supply Switch on external voltage supply. Terminal X21.5 controller inhibit must Do not switch on the mains be active (0). power supply system! Switch on power supply system 7 segment display: b 7 segment display: 4 Press button S1 briefly. Display of the current axis address: A, tens digit, units digit (for instance A, 1, 9: Axis address 19) Press and hold down S1 button longer than 2 seconds. Display of the actual axis address,subsequently flashing for 2 seconds each: H, L Release S1 button: at H to set tens digit (0 ... 5) / at L to set unit digit (0 ... 9) To adjust the numbers: Press or hold down S1 button. When the required number appears, release S1 button. The number has now been set, the actual address is displayed. Subsequently is displayed and then the operating status. To verify address, press S1 briefly. Is address No correct? yes End 02153AEN Figure 16: Setting or changing the address Configuring the • Install and start MD_SHELL. MD_SHELL User • Select the [Interface] menu. Interface • Under the “PC Interface” menu item, select the serial interface on which the axis system is connected to the PC (COM1, COM2). • Under the “Inverter Interface” menu item, select the serial interface that is used for communication on the axis system. – RS-232 via USS, RS-485 – RS-232 via MP/MPB – RS-232 via AIO • Under the “Inverter Address” menu item, set the address that is used by the PC. ® 31 MOVIDYN Servo Controller Operating Instructions I Initial Settings 6 0 0 Limit Switch Important: On delivery, the terminals X21.7 and X21.8 are programmed as limit switch inputs. If you do not connect any limit switches, you must change the programming of the terminals in MD_SHELL or bridge both terminals to X21.12 (+ 24 V); otherwise, fault 27 occurs (→ List of Fault Messages). Setting the MD_SHELL allows for a rapid startup. For this purpose, MD_SHELL calculates an initial Controller setting of the speed controller using system-specific data (→ MD_SHELL). • In the [Parameter] menu, select the “Startup” menu item. • Enter the required data completely: Menu item Comment “Motor Type” Enter the motor type (nameplate). “Rated Motor Voltage” Enter the correct rated voltage of the motor (nameplate). “Rated Speed” Enter the correct rated speed of the motor (nameplate). “Brake” This entry is used for correct determination of the motor moment of inertia (nameplate). “Speed Control Loop Damping” The damping is a measure for the transient response of the speed control loop. The standard setting is 1.0 (aperiodic n transient condition); range of values: 0.5...2.0. Small values lead to higher overshooting (the inherent instability increases), larger values to a creeping shape (the inherent instability d=0,7 decreases). d=1 d=1,5 t “Speed Control Loop Stiffness” The stiffness is a measure for the velocity of the speed control loop. The standard setting is 1.0; range of values is 0.5…2.0. n Increasing the stiffness leads to an increase in the control speed; the control system starts oscillating at a critical value. S=1.2 Reducing the stiffness leads to a slowdown of the control, and the lag fault increases. Recommendation: Increase the stiffness S=1 in small steps (e.g., 0.05) (practical range of values: 0.8 – 1.2)! S=0.8 surge torque 80 % M N t “Positioning Control Time Interval” Corresponds to the cycle time of a higher level positioning control and, therefore, to the resulting time-discrete setpoint changes. “Drive” Only enter “Backlash-Free” if the drive is truly backlash-free; otherwise, it may result in uneven running. “Moment of Inertia at Motor Shaft” Enter the resulting load moment of inertia referenced to the motor shaft using the listed unit. If the value is not known, you must enter an estimated value; a more exact value may be determined later using MD_SCOPE. “Shortest Required Ramp Time” The ramp generators are set to the listed value if the acceleration capacity of the drive allows for this option. It is practical to enter the next shortest time than the one preset by the higher-level positioning control. “Rated Current” Indicates the rated current. ® 32 MOVIDYN Servo Controller Operating Instructions I Initial Settings 6 0 0 • Pressing [F5] opens the parameter list. Pressing [F2] performs a calculation of all required parameters and the setting of limits (Setting parameters). The drive can be started up using the displayed initial setting of the speed controller. • Transfer the calculated values to the inverter by pressing [F3]. In general, the initial setting delivers satisfactory results. However, the following aids are available if further optimization is required: Checking and There are two options available to optimize the initial setting of the controller parameters optimizing and to visualize the process data: controller • You are using the MD_SCOPE program. It is used to display the time characteristic setting,visualizing of setpoints, actual values, etc. on the PC monitor, save and print them, as well as process data change controller parameters. • Without the MD_SCOPE utility program, the AIO11 option pcb and an oscilloscope can be used to optimize the controller parameters. For this purpose, you must program the analog outputs on the AIO11 option pcb accordingly (→ Param. 340). Programming the If any other than the factory terminal assignment is to be used, you must reprogram the Terminals terminals (→ MD_SHELL; → Param. 300). ® 33 MOVIDYN Servo Controller Operating Instructions I List of Parameters 6 0 0 6.2 List of Parameters *) The marked parameters can automatically be determined and transferred by executing the MD_SHELL startup function. A forward slash “/” in front of the assignment designates a “0” active function. Param. Designation Adjustment range Factory setting No. min. ... increment ... max. 0__ Display values 000...084 Process values for monitoring during operation 1__ Setpoints/ramp generators 10_ Operating mode 100 Operating mode SPEED CONTROL · TORQUE CONTROL (with SPEED CONTROL IPOS also: POSITIONING) 101 Factor for analog setpoints 0.10 ... 0.01 ... 10.00 1.00 102 Offset for analog value 1 [mV] -500 ... 1 ... 500 0 103 Operating mode of analog input 2 EXT. I-LIMIT · NO FUNCTION · RESERVED EXT. I-LIMIT 11_ Setpoint source 110 Setpoint source ANALOG INPUT · OPT. API·APA · PC ANALOG INPUT INTERFACE · FIELDBUS 111 PC setpoint speed [1/min] -5000.00 ... 0.20 ... +5000.00 0.00 12_ Ramp generator 1 120 Ramp 1 up CW [s]* 1.00 0.00 ... 0.02 ... 0.50 121 Ramp 1 down CW [s]* 0.50 ... 0.10 ... 3.00 3.00 ... 0.50 ... 10.00 122 Ramp 1 up CCW [s]* 10.00 ... 2 ... 30 123 Ramp 1 down CCW [s]* 13_ Ramp generator 2 130 Ramp 2 up CW [s]* 1.00 0.00 ... 0.02 ... 0.50 131 Ramp 2 down CW [s]* 0.50 ... 0.10 ... 3.00 3.00 ... 0.50 ... 10.00 132 Ramp 2 up CCW [s]* 10.00 ... 2 ... 30 133 Ramp 2 down CCW [s]* 14_ Rapid stop ramp 140 Rapid stop ramp [s] 0.00 ... 0.02 ... 0.50 1.00 0.50 ... 0.10 ... 3.00 3.00 ... 0.50 ... 10.00 10.00 ... 2 ... 30 15_ Emergency stop ramp 150 Emergency stop ramp [s] 0.00 ... 0.02 ... 0.50 0.10 0.50 ... 0.10 ... 3.00 3.00 ... 0.50 ... 10.00 2__ Controller parameter 20_ Speed controller 200 Gain n-controller* 0.10 ... 0.01 ... 32.00 2.00 201 Time constant n-controller [ms]* 0 ... 0.50 ... 0.50 10.00 0.50 ... 0.10 ... 50.00 50.00 ... 1 ... 300 202 D component n-controller* 0.00 ... 0.10 ... 32.00 0.00 203 Feedforward threshold [1/min/ms]* 0 ... 0.2 ... 3000 3000 204 Gain accel. feedforward* 0.00 ... 0.01 ... 1.00 0.00 1.00 ... 0.02 ... 80.00 205 Filter accel. feedforward [ms]* 0 ... 1 ... 1 0 1 ... 0.10 ... 100.00 206 Filter speed setpoint [ms]* ® 34 MOVIDYN Servo Controller Operating Instructions I List of Parameters 6 0 0 Param. Designation Adjustment range Factory setting No. min. ... increment ... max. 207 Filter speed actual value [ms]* 0 ... 1 ... 1 0 1 ... 0.10 ... 32.00 208 7-segment test display OFF · ON OFF 209 Controller test function OFF · ON OFF 21_ Limitings 210 Max. speed CW [1/min]* 0 ... 1 ... 5000 3000 211 Max. speed CCW [1/min]* 212 Maximum current [%I ]* 5 ... 1 ... 150 100 N 22_ Hold controller 220 Gain of hold controller* 0.10 ... 0.10 ... 32.00 0.50 3__ Terminal assignment 30_ Binary inputs of basic unit 300 Terminal X21.6 ENABLE · RAMP GEN. SWITCH MODE · / ENABLE CONTROLLER INHIBIT · HOLD CONTROL · / 301 Terminal X21.7 /LIMIT SWITCH CW EXT. FAULT · RESET · EXT. TRIGGER · /LIMIT SWITCH CW · /LIMIT SWITCH CCW · NO 302 Terminal X21.8 /LIMIT SWITCH CCW FUNCTION (with IPOS also: REF. CAM · REFERENCE TRAVEL) 31_ Binary inputs AIO 310 Terminal X13.2 same as P300 RESET 311 Terminal X13.3 INTEG. SWITCH MODE 312 Terminal X13.4 NO FUNCTION 313 Terminal X13.5 NO FUNCTION 314 Terminal X13.6 NO FUNCTION 315 Terminal X13.7 NO FUNCTION 316 Terminal X13.8 EXT. TRIGGER 32_ Binary outputs of basic unit 320 Terminal X21.10 IxT WARNING · READY FOR OPERATION · / READY FOR OPERATION FAILURE · /BRAKE · SPEED REFERENCE · CURRENT REFERENCE · SETPOINT ACTUAL VALUE COMP. · MOTOR STANDSTILL · NO FUNCTION (with IPOS also: IN POSITION · POS. OUTPUT 1 ... 8 · IPOS REFERENCE) 33_ Binary outputs AIO 330 Terminal X12.1 same as P320 /FAILURE 331 Terminal X12.2 IxT WARNING 332 Terminal X12.3 IxT WARNING 333 Terminal X12.4 IxT WARNING 334 Terminal X12.5 IxT WARNING 335 Terminal X12.6 IxT WARNING 34_ Analog outputs AIO 340 Analog output 1 (X14.6) CURRENT SETPOINT · SPEED ACTUAL CURRENT SETPOINT VALUE · INTEGR. SETPOINT · INTEGR. ACTUAL VALUE · IxT CAPACITY UTILIZATION 341 Assessment factor 1 -5.00 ... 0.10 ... 5.00 1.00 342 Analog output 2 (X14.7) same as P340 SPEED ACTUAL VALUE 343 Assessment factor 2 -5.00 ... 0.10 ... 5.00 1.00 4__ Reference messages 40_ Speed reference value 400 Reference speed [1/min] 0 ... 1 ... 5000 1500 401 Hysteresis 1 [+/- 1/min] 0 ... 1 ... 500 100 ® 35 MOVIDYN Servo Controller Operating Instructions I List of Parameters 6 0 0 Param. Designation Adjustment range Factory setting No. min. ... increment ... max. 402 Deceleration [s] 0.00 ... 0.10 ... 9.00 1.00 403 Message = “1” at: n < n ref · n > n ref n < n ref 41_ Current reference value 410 Reference current I [%I ] 0 ... 1 ... 150 100 ref N 411 Hysteresis 2 [+/- %] 0.00 ... 1.00 ... 10 2.00 412 Deceleration [s] 0.00 ... 0.10 ... 9.00 1.00 413 Message = “1” at: I < I ref · I >I ref I < I ref 42_ Setpoint actual value comparison 420 Deceleration [s] 0.00 ... 0.10 ... 9.00 1.00 421 Message = “1” at: n <> n setpoint · n = n setpoint n <> n setpoint 43_ Ixt reference value 430 Ixt reference value [%In] 0 ... 1 ... 100 100 5__ Control functions 50_ Brake function 500 Brake function NO · YES NO 501 Brake reaction time [ms] 0 ... 1 ... 1000 200 51_ Speed monitoring 510 Speed monitoring NO · YES YES 511 Control time n-monitoring [s] 0.00 ... 0.10 ... 10.00 1.00 6__ Special functions 60_ Ready for operation message 600 Message delay [s] 0 ... 1 ... 9 1 61_ Factory setting 610 Factory setting NO · YES NO 62_ Fault reaction 620 Fault reaction INSTANT DISCONNECT · EMERGENCY INSTANT DISCONNECT STOP RAMP 63_ Reset behavior 630 Auto reset NO · YES NO 631 Restart time [s] 3 ... 1 ... 30 3.0 632 Manual reset NO · YES NO 633 Reaction to MP reset NONE · RESET NONE 634 RESET button of axis module ENABLED · INHIBITED ENABLED 64_ Parameter lock 640 Parameter lock NO · YES NO 65_ Save EEPROM 650 Save EEPROM OFF · ON ON 66_ MOVIDYN response time 660 Response time [ms] 0 ... 5 ... 200 0.0 7__ Control functions 78_ Fieldbus PD description 780 PO1 Setpoint description NO FUNCTION · SPEED · CURRENT · CONTROL WORD 1 POSITION LOW · POSITION HIGH · MAX. SPEED · MAX. CURRENT · SLIP · RAMP · CONTROL WORD 1 · CONTROL WORD 2 · SPEED [%] ® 36 MOVIDYN Servo Controller Operating Instructions I List of Parameters 6 0 0 Param. Designation Adjustment range Factory setting No. min. ... increment ... max. 781 PI1 Actual value description NO FUNCTION · SPEED · APPARENT STATUS WORD 1 CURRENT · ACTIVE CURRENT · POSITION LOW · POSITION HIGH · STATUS WORD 1 · STATUS WORD 2 · SPEED [%] 782 PO2 Setpoint Description same as P780 SPEED 783 PI2 Actual value description same as P781 SPEED 784 PO3 Setpoint description same as P780 NO FUNCTION 785 PI3 Actual value description same as P781 NO FUNCTION 79_ Fieldbus parameter 790 Enable fieldbus setpoints YES · NO YES 791 Fieldbus timeout [s] 0.01 ... 0.01 ... 1.00 0.50 1 ... 1 ... 650 792 Timeout response RAPID STOP · EMERGENCY STOP · RAPID STOP INSTANT DISCONNECT · RAPID STOP/ FAILURE · EMERGENCY STOP/FAILURE · INSTANT DISCONNECT/FAILURE · STANDARD MODE · NO RESPONSE 793 CAN synchronization ID 0 ... 1 ... 2047 1 794 DeviceNet PD configuration 1 PD + PARAM · 1 PD · 2 PD + PARAM · 2 PD · 3 PD + PARAM 3 PD + PARAM · 3 PD ® 37 MOVIDYN Servo Controller Operating Instructions Status LEDs 7 7 Operation and Service 7.1 Status LEDs Power Supply Module (LEDs) LED Meaning ON (green) ON Ready for operation, no fault and DC link voltage and internal 24 V electronic voltage supply within permissible limits OFF Not ready for operation 24 V (green) ON 24 V electronic voltage supply (internal or external) ensured OFF No 24 V supply TRIP (red) ON Failure (fault is displayed at the axis modules and in MD_SHELL) OFF No failure Axis Module / Compact Servo Status Display Meaning Controller (7- Operating state 1 Speed control, enabled Segment Display) 2 Torque control, enabled 3 Rapid stop is carried out 4 Controller inhibit is active (output stage is inhibited) 5 Approached limit switch CW 6 Approached limit switch CCW 7 Option card API/APA 11 positioning control in operation 8 Executing factory setting (only displayed with operational axis module) 9 Hold control is active b Not ready for operation IPOS A IPOS in operation c IPOS performs reference travel Fault F A fault is indicated by a flashing “F” and the two digits of the fault code. The display remains until the fault is reset (P63. and List of Fault Messages) 7.2 Reset Options • Power supply module • Switch power supply on/off • A reset at any of the axis modules also resets the power supply module. Observe P633! • Axis module / Compact servo controller • Switch power supply on/off and, if present, also switch external 24 V voltage supply on/off • Reset command via binary input terminal (→ P30.) • Auto reset (→ P630) • Reset via serial interface (→ P632) • Pressing S1 (→ P634) ® 38 MOVIDYN Servo Controller Operating Instructions List of Fault Messages 7 7.3 List of Fault Messages Important All fault messages can be reset with a reset command. Faults recognized in the power supply module (F03, F06, F07, F15) are displayed by all attached axis modules! Other fault numbers may occur during the operation with options (→ corresponding documentation). With a fault reset, the incremental encoder simulation is also reset. A review of the position encoder information is necessary. Fault Reaction The “Reaction” column contains the reaction of the drive to the respective fault: S = Instant disconnect, i.e., the output stage is inhibited (controller inhibit), and the brake is applied. N = Emergency stop ramp (→ P150) P = Programmable Caution: Motors without a mechanical brake can continue moving uncontrolled (e.g., coast to stop) because of load conditions! Display Fault Reaction Unit MD_SHELL Cause Solution F01 MAS... / MKS... Overcurrent in output stage due to: Repair the short circuit. S overcurrent • Short circuit in the motor/cable If the fault cannot be reset afterward, exchange • Ground fault the unit. • Defective output stage F03 MPx… Thermal overload of the power supply Reduce the power output and/or ensure N overtemperature module sufficient cooling. F05 Message bus Data bus cable is not properly connected Check the connections. S connection to X5 F06 Earth fault Earth fault in: Check motor leads or motor for earth fault. S • Power supply module • Axis module(s) • Motor(s) F07 DC link Generating power too high, overvoltage in • Check leads to the braking resistor S the DC link • Check technical data of the braking resistor • Extend deceleration ramps, if necessary F08 Speed Speed control operates through the • Extend ramps, increase P511, if necessary S monitoring adjusting limit • Check power limitation • Overload • Check motor • Phase fault in the power supply or • Check motor lead motor • Check power supply phases • Incorrect connection of resolver • Check cabling of resolver F09 S1 AI011 current S1 slide switch on AIO11 is set incorrectly Move S1 slide switch on AIO11 to “U” position. S F11 MAS... / MKS... Thermal overload of axis module / Reduce the power output and/or ensure N overtemperature compact servo controller sufficient cooling. F14 Resolver fault • Resolver cable or shield is not Check resolver cable and shield for correct S connected correctly connection, short circuit, and cable break • Short circuit or cable break in resolver cable • Resolver defective F15 Internal 24 V Internal supply voltage in the power supply Exchange the unit S MPx... / MKS... module / compact servo controller is missing F17... Displays System faults Reset (→ Reset options) S 24 detailed fault If the fault cannot be reset, please consult SEW. indicators Indicate fault number and MD_SHELL fault message ® 39 MOVIDYN Servo Controller Operating Instructions List of Fault Messages 7 Display Fault Reaction Unit MD_SHELL Cause Solution F25 EEPROM Error while accessing EEPROM Call up the factory setting (→ Observe S P610!) and reset the fault. Perform a new startup. If the fault occurs again: Exchange the unit F26 External External fault signal was read in via Remove the respective fault source, reprogram P terminal programmable input the terminal, if necessary F27 ES cable Cable break or both limit switches missing Check cabling and limit switches, reprogram N missing terminals, if necessary F28 Fieldbus timeout Fault during process data transfer Check fieldbus connection, see the P corresponding manual F29 Limit switch Limit switches are reversed with respect to Reverse connections of limit switches at X21.7 N reversed rotational direction of motor and X21.8. F31 Short circuit Short circuit or overload of one or several Check cabling and wiring, limit current to 50 S output binary outputs mA, if necessary F32 Setpoint source Setpoint source not defined Set correct setpoint source with P110 S n.a. F34 Fieldbus timeout Fault during communication data transfer Check fieldbus connection, see the P corresponding manual F36 Required Attempted to use a non-existing option • Insert correct option card or S hardware card • Select correct setpoint source with P110 missing F39, Fault of IPOS positioning control See IPOS manual N 41, 42, 58, 72, 76-78 F40- Fault of APA/API positioning control See APA/API manual N 42,50- 74 F43 PC control time Monitoring for communication of PC / axis [Parameter] menu, “Panel” menu item: Increase S system active, monitoring time exceeded the value for “PC time monitoring” or deactivate time monitoring by entering “0.” F87 Fieldbus timeout Communications fault during fieldbus Check fieldbus connection, see the P operation corresponding manual Displays System fault Reset (→ Reset options) S undefined Exchange the unit if this reoccurs. messages ® 40 MOVIDYN Servo Controller Operating Instructions SEW Electronics Service 7 7.4 SEW Electronics Service If a fault cannot be solved, please consult the SEW Electronics Service (→ Addresses in “Customer and Spare Parts Service”). Upon consulting the SEW Electronics Service, please indicate the digits of the service code which will help the service personnel to assist you more efficiently. 00276AEN Figure 17: Service label If you send in the unit for testing or repair services, please provide the following information: • Type of fault • Accompanying circumstances • Your own thoughts about the cause of the fault • preceeding unusual circumstances, etc. ® 41 MOVIDYN Servo Controller Operating Instructions n kVA f General Technical Data 8 i P Hz 8 Technical data 8.1 General Technical Data ® The following table lists the technical data that applies to all MOVIDYN servo controllers, independent of type, design, and power. ® MOVIDYN All types Interference immunity meets EN 61800-3 Interference emission with EMC-compliant meets EN 61800-3 according to limit B pursuant to EN installation 55011 and EN 55014 Ambient temperature ϑ 0 °C ... 45 °C without output reduction amb 45 °C ... max. 60 °C output reduction 3 % per K Climatic category EN 60721-3-3, class 3K3 1) Storage temperature ϑ -25 °C ... + 70 °C (EN 60721-3-3, class 3K3) st ABG diagnostics and memory module: - 20 °C ... +60 °C Enclosure IP20 (EN 60529) Operating mode DB (continuous duty) (EN 60149-1-1 and -1-3) Installation altitude h ≤ 1,000 m (3,300 ft) I reduction: 1 % per 100 m (330 ft) N from 1,000 m (3,300 ft) up to 2,000 m (6,600 ft) 1) During long-term storage, connect the unit to supply voltage every two years for at least 5 minutes since the unit’s useful life may otherwise be reduced. ® 42 MOVIDYN Servo Controller Operating Instructions n kVA f Technical Data of Basic Units 8 i P Hz 8.2 Technical Data of Basic Units MPB... / MPR power supply module ® MOVIDYN power supply modules MPB51A (brake chopper) MPR51A (regenerative power supply unit) Basic unit 011-503-00 027-503-00 055-503-00 015-503-00 037-503-00 Part number 826 074 5 826 075 3 826 076 1 825 865 1 825 866 X Supply system Nominal voltage V 3 x 380 V -10% ... 500 V +10% 3 x 380 V -10% in AC AC AC for UL: 380 V -10 % ... 480 V +10 % ... 500 V +10% AC AC AC Frequency f 50 Hz/60 Hz 5 % in Current I 16 A 40 A 80 A 21 A 53 A in AC AC AC AC AC DC link V = 400 V in No-load voltage V 560 V at 400 V Z DC AC 1) Peak current I 20 A 50 A 100 A 27 A 67 A ZN eff eff eff eff eff Rated current I 40 A 100 A 200 A 40 A 100 A Zmax eff eff eff eff eff Rated power P 11 kW 27 kW 55 kW 15 kW 37 kW ZN 1) Ratd power P 22 kW 54 kW 110 kW 22 kW 55 kW Zmax Braking resistor external R (± 10%) 47 Ω 18 Ω 15 Ω not applicable Peak braking power P 14 kW 38 kW 45 kW BRCMAX internal 24 V supply (switch-mode power 240 W 50 W 2) supply) Type of cooling (DIN 41 751) KF (forced-cooling) KS (self-cooling) Chassis m 5.5 kg (12.1 lb) 7 kg (15.4 lb) 7 kg (15.4 lb) 5.5 kg (12.1 lb) 7 kg (15.4 lb) MP Dimensions Chassis dimensions [mm] 105x380x250 140x380x250 140x380x250 105x380x250 140x380x250 W x H x D [in] (4.1x15.0x9.8) (5.5x15.0x9.8) (5.5x15.0x9.8) (4.1x15.0x9.8) (5.5x15.0x9.8) Depth with heat sink D 340 mm (10.83 in) (DKF, DKS), 275 mm (10.83 in) (DKE) K Width in component units W 34434 TE (1 TE = 35 mm = 1.38 in) Line choke type ND 020-013 ND 045-013 ND 085-013 ND 045-013 ND 085-013 Braking resistor type BW x47 BW 018-... BW x15 not required Input filter type V ≤ 400 V NF 025-443 NF 050-443 NF 080-443 NF 036-443 NF 080-443 in Input filter type V ≤ 500 V NF 025-503 NF 050-503 NF 080-503 NF 036-503 NF 080-503 in 1) The MPB power supply modules may be loaded with peak current/peak power for a maximum of 5 s. With an attached heat sink, the MPR power supply modules may be loaded continually with peak current/peak power. 2) The utilization of the switch-mode power supply and the connection of an external 24 V voltage supply is covered in the chapter DC "Electrical Installation." ® 43 MOVIDYN Servo Controller Operating Instructions n kVA f Technical Data of Basic Units 8 i P Hz MAS… axis module ® MOVIDYN axis module MAS51A IPOS design: MAS51A xxx-503-50 Basic unit 005-503-00 010-503-00 015-503-00 030-503-00 060-503-00 Part number 826 069 9 826 070 2 826 071 0 826 072 9 826 073 7 Part number of IPOS unit 826 255 1 826 256 X 826 257 8 826 258 6 826 259 4 Input voltage = V = 700 V (V = 500 V ) Z DC in AC DC link voltage V V = 900 V Z Zmax DC V = 680 V (V = 480 V ) Z DC in AC Output voltage V 0 ... V S in Rated output current I 5 A 10 A 15 A 30 A 60 A S AC AC AC AC AC with attached heat sink Maximum output current I 7.5 A 15 A 22.5 A 45 A 90 A max AC AC AC AC AC with attached heat sink, max 0.3 s for n ≤ 30 1/min, continually for n > 30 1/min Type of cooling (DIN 4175) KS (self-cooling) Chassis m 3.5 kg (7.7lb) 3.5 kg (7.7 lb) 3.5 kg (7.7 lb) 5.5 kg (12.1 lb) 7 kg (15.4 lb) MA Dimensions Chassis dimensions [mm] 70x380x250 70x380x25 70x380x250 105x380x250 140x380x250 W x H x D [in] (2.8x15.0x9.8) (2.8x15.0x9.8) (2.8x15.0x9.8) (4.1x15.0x9.8) (5.5x15.0x9.8) Depth with heat sink D 340 mm (13.38 in) (DKF, DKS), 275 mm (10.83 in) (DKE) K Width in component units W 22234 TE (1 TE = 35 mm = 1.38 in) ® 44 MOVIDYN Servo Controller Operating Instructions n kVA f Technical Data of Basic Units 8 i P Hz MKS… Compact Servo Controller ® MOVIDYN compact servo MKS51A controller IPOS design: MKS51A xxx-503-50 Basic unit 005-503-00 010-503-00 015-503-00 Part number 826 044 3 826 045 1 826 429 5 Part number of IPOS unit 826 260 8 826 261 6 826 430 9 Supply system Voltage V 3 x 380 V -10% ... 500 V +10 % in AC AC Frequency f 50/60 Hz 5 % in Rated current I 4.5 A 9 A 13.5 A in AC AC AC Output Rated current I 5 A 10 A 15 A N AC AC AC Maximum current I 7.5 A 15 A 22.5 A max AC AC AC max. 0.3 s for n ≤ 30 1/min, continually for n > 30 1/min Voltage V 0 ... V O in Braking resistor external R (± 10%) 47 Ω Peak braking power P 5 kW 10 kW 14 kW BRCMAX 1) Switch-mode power supply 29 W Type of cooling (DIN 41 751) KF – forced-cooling Chassis m 4.5 kg (9.9 lb) 4.5 kg (9.9 lb) 6.5 kg (14.3 lb) Ma Chassis dimensions [mm] 105 x 275 x 275 130 x 336 x 325 WxHxD [in] (4.13 x 10.83 x 10.83) (5.12 x 13.23 x12.80) Braking resistor type BW 047-004 / BW 047-005 BW 147 / BW 247 / BW 347 Input filter type V ≤ 400 V NF 008-443 NF 025-443 in Input filter type V ≤ 500 V NF 008-503 NF 025-503 in 1) The utilization of the switch-mode power supply and the connection of an external 24 V voltage supply is covered in section DC “Electrical Installation.” ® 45 MOVIDYN Servo Controller Operating Instructions 9 Index DKF heat sink, electrical connection 14 Documentation 5 0V lines 19 24 V (LED) 38 E 24 V supply 15, 43 EEPROM (F25) 40 7-segment display 38 Electronic lines 19 A Electronic terminals 19 Electronics service 41 AIO11 39 Electronics voltage supply, connection 14 Ambient temperature 42 EMC Analog outputs AIO P34_ 35 Input filter 19 Auto reset 38 Interference emission 19 Axis address 31 Interference immunity 19 Axis module 10 Output choke 22 Axis module – power supply module connection 14 Shielding 20 Axis module, 7-segment display 38 Wiring diagram 21 B EMC-compliant installation 19 Emergency stop ramp 39 Binary inputs AIO P31_ 35 Emergency stop ramp P15_ 34 Binary inputs of basic unit P30_ 35 Enclosure 42 Binary outputs AIO P33_ 35 ES cable missing (F27) 40 Binary outputs of basic unit P32_ 35 external 24 V supply 43 BME 17 External terminal (F26) 40 BME brake rectifier 17 External voltage supply 15 Brake circuit diagram 18 Brake function P50_ 36 F Brake reaction times 18 Factory setting P61_ 36 Brake release time 18 Fault messages 39 Brake, block diagram 18 Fault reaction 39 Braking relay 17 Fault reaction P62_ 36 Braking resistor, connection 14 Fieldbus parameter P79_ 37 Braking resistors 10 Fieldbus PD description P78_ 36 Braking torque 18 Fieldbus timeout (F28) 40 BSG 17 Fieldbus timeout (F34) 40 BSG brake control unit 17 Fieldbus timeout (F87) 40 C G CE designation 9 Ground fault (F06) 39 Climatic category 42 Compact servo controller, 7-segment display 38 H Connecting the PC 30 Heat sink 10 Connection, EMC-compliant 21 Heat sink installation 10 Control functions P5__ 36 Heat sink mounting 10 Control functions P7__ 36 Hoists, brake connection 18 Controller parameter P2__ 34 Hold controller P22_ 35 Cooling 10 Current reference value P41_ 36 I D Input filter 16, 19 Input fuse 16 Data bus cable 14, 39 Installation 10 DC link (F07) 39 Installation altitude 42 DC link connection 14 Installation of axis module 10 Device protection 17 Installation of braking resistors 10 Display values P0__ 34 Installation of line chokes 10 Disposal 5 Installation, EMC-compliant 19 ® 46 MOVIDYN Servo Controller Operating Instructions Installation, UL-compliant 22 Output choke 22 Installing an axis system 10 Output filter 16 Instant disconnect 39 Overcurrent (F01) 39 Intended Use 4 Overcurrent circuit breaker 17 Interference emission 19, 42 Overtemperature (F02) 39 Interference immunity 19, 42 Overtemperature (F11) 39 Internal 24 V (F15) 39 P Ixt reference value P43_ 36 Parameter L Control functions 36 LEDs, power supply module 38 Brake function 36 Limit switch 32, 40 Fieldbus parameter 37 Limit switch reversed (F29) 40 Fieldbus PD description 36 Limitings P21_ 35 Speed monitoring 36 Line chokes 10 Controller parameter 34 List of parameters 34 Hold controller 35 Limitings 35 M Speed controller 34 MAS terminals 27 Display values 34 MAS, technical data 44 Reference messages 35 MAS/MKS unit design 8 Current reference value 36 MAS/MKS, unit design 8 Ixt reference value 36 Master-slave function 29 Setpoint actual value comparison 36 MD_SCOPE 33 Speed reference value 35 MD_SHELL 31 Setpoints/ramp generators 34 Mechanical installation 10 Emergency stop ramp 34 Message bus connection (F05) 39 Operating mode 34 Minimum clearance for cooling 10 Ramp generator 1/2 34 MKS terminals 28 Rapid stop ramp 34 MKS, technical data 45 Setpoint source 34 MKS, wiring diagram 25 Special functions 36 Monitoring time 40 Factory setting 36 Motor lead 16 Fault reaction 36 Motor protection 17 MOVIDYN response time 36 Mounting of axis module 10 Parameter lock 36 Mounting of braking resistors 10 Ready for operation message 36 Mounting of line chokes 10 Reset behavior 36 MOVIDYN response time P66_ 36 Save EEPROM 36 MPB terminals 26 Terminal assignment 35 MPB, technical data 43 Analog outputs AIO 35 MPB/MAS, wiring diagram 23 Binary inputs AIO 35 MPR terminals 26 Binary inputs of basic unit 35 MPR, technical data 43 Binary outputs AIO 35 MPR, voltage supply, external 16 Binary outputs of basic unit 35 MPR/MAS, wiring diagram 24 Parameter lock P64_ 36 MPR/MPB unit design 7 PC control time (F43) 40 MPR/MPB, unit design 7 PLC 29 Power demand of components 15 N Power supply module – axis module connection 14 Nameplate 9 Power supply module, LEDs 38 Programmable fault reaction 39 O Programming the terminals 33 ON (LED) 38 R Operating mode 42 Operating mode P10_ 34 Ramp generator 1/2 P12_/P13_ 34 Option card 40 Rapid stop ramp P14_ 34 Option card, startup 12 Reaction time (brake) 17 ® 47 MOVIDYN Servo Controller Operating Instructions Reaction time, brake 18 U Ready for operation message P60_ 36 UL maximum values 22 Reference messages P4__ 35 UL-compliant installation 22 Required hardware missing (F36) 40 Use, intended 4 Reset 38 User interface 31 Reset behavior P63_ 36 Resolver cable 17 V Resolver fault (F14) 39 Visualizing process data 33 RS-485 interface 29 Voltage supply, external 15 S W S1 AIO11 current (F09) 39 Warning Instructions 4 Safety Notes 4, 6 Wiring diagram Save EEPROM P65_ 36 MKS 25 Service 41 MPB/MAS 23 Setpoint actual value comparison P42_ 36 MPR/MAS 24 Setpoint source (F32) 40 Setpoint source P11_ 34 Setpoints/ramp generators P1__ 34 Setting the controller 32 Shield clamps 13 Shielding 13, 20 Short circuit output (F31) 40 Signal generation 19 Special functions P6__ 36 Speed controller 32 Speed controller P20_ 34 Speed monitoring (F08) 39 Speed monitoring P51_ 36 Speed reference value P40_ 35 Startup of option card 12 Status LEDs 38 Storage temperature 42 Supply contactor 16, 17 Supply system lead 16 Switch cabinet 10 Switch-mode power supply 43 T Technical data MAS… axis module 44 MKS 45 MPB/MPR power supply module 43 Terminal assignment 33 Terminal assignment P3__ 35 Terminals MAS 27 MKS 28 MPB 26 MPR 26 TF temperature sensor 17 TH thermostat 17 Tightening torque 14, 16 TRIP (LED) 38 Type designation 9 ® 48 MOVIDYN Servo Controller Operating Instructions Address list Address List Germany Headquarters Bruchsal SEW-EURODRIVE GmbH & Co Tel. (0 72 51) 75-0 Production Ernst-Blickle-Straße 42 Fax (0 72 51) 75-19 70 Sales D-76646 Bruchsal http://www.SEW-EURODRIVE.de Service P.O. Box sew@sew-eurodrive.de Postfach 3023 · D-76642 Bruchsal Production Graben SEW-EURODRIVE GmbH & Co Tel. (0 72 51) 75-0 Ernst-Blickle-Straße 1 Fax (0 72 51) 75-29 70 D-76676 Graben-Neudorf Telex 7 822 276 P.O. Box Postfach 1220 · D-76671 Graben-Neudorf Assembly Garbsen SEW-EURODRIVE GmbH & Co Tel. (0 51 37) 87 98-30 Service (near Hannover) Alte Ricklinger Straße 40-42 Fax (0 51 37) 87 98-55 D-30823 Garbsen P.O. Box Postfach 110453 · D-30804 Garbsen Kirchheim SEW-EURODRIVE GmbH & Co Tel. (0 89) 90 95 52-10 (near München) Domagkstraße 5 Fax (0 89) 90 95 52-50 D-85551 Kirchheim Langenfeld SEW-EURODRIVE GmbH & Co Tel. (0 21 73) 85 07-30 (near Düsseldorf) Siemensstraße 1 Fax (0 21 73) 85 07-55 D-40764 Langenfeld Meerane SEW-EURODRIVE GmbH & Co Tel. (0 37 64) 76 06-0 (near Zwickau) Dänkritzer Weg 1 Fax (0 37 64) 76 06-30 D-08393 Meerane Additional addresses for service in Germany provided on request! France Production Haguenau SEW-USOCOME SAS Tel. 03 88 73 67 00 Sales 48-54, route de Soufflenheim Fax 03 88 73 66 00 Service B. P. 185 http://www.usocome.com F-67506 Haguenau Cedex sew@usocome.com Assembly Bordeaux SEW-USOCOME SAS Tel. 05 57 26 39 00 Sales Parc d’activités de Magellan Fax 05 57 26 39 09 Service 62, avenue de Magellan - B. P. 182 F-33607 Pessac Cedex Lyon SEW-USOCOME SAS Tel. 04 72 15 37 00 Parc d’Affaires Roosevelt Fax 04 72 15 37 15 Rue Jacques Tati F-69120 Vaulx en Velin Paris SEW-USOCOME SAS Tel. 01 64 42 40 80 Zone industrielle Fax 01 64 42 40 88 2, rue Denis Papin F-77390 Verneuil I’Etang Additional addresses for service in France provided on request! Argentina Assembly Buenos Aires SEW EURODRIVE ARGENTINA S.A. Tel. (3327) 45 72 84 Sales Centro Industrial Garin, Lote 35 Fax (3327) 45 72 21 Service Ruta Panamericana Km 37,5 sewar@sew-eurodrive.com.ar 1619 Garin Australia Assembly Melbourne SEW-EURODRIVE PTY. LTD. Tel. (03) 99 33 10 00 Sales 27 Beverage Drive Fax (03) 99 33 10 03 Service Tullamarine, Victoria 3043 Sydney SEW-EURODRIVE PTY. LTD. Tel. (02) 97 25 99 00 9, Sleigh Place, Wetherill Park Fax (02) 97 25 99 05 New South Wales, 2164 Austria Assembly Wien SEW-EURODRIVE Ges.m.b.H. Tel. (01) 6 17 55 00-0 Sales Richard-Strauss-Strasse 24 Fax (01) 6 17 55 00-30 Service A-1230 Wien sew@sew-eurodrive.at 07/2001 Address list Belgium Assembly Brüssel CARON-VECTOR S.A. Tel. (010) 23 13 11 Sales Avenue Eiffel 5 Fax (010) 2313 36 Service B-1300 Wavre http://www.caron-vector.be info@caron-vector.be Brazil Production Sao Paulo SEW DO BRASIL Tel. (011) 64 60-64 33 Sales Motores-Redutores Ltda. Fax (011) 64 80 33 28 Service Rodovia Presidente Dutra, km 208 sew@sew.com.br CEP 07210-000 - Guarulhos - SP Additional addresses for service in Brazil provided on request! Bulgaria Sales Sofia BEVER-DRIVE GMBH Tel. (92) 9 53 25 65 Bogdanovetz Str.1 Fax (92) 9 54 93 45 BG-1606 Sofia bever@mbox.infotel.bg Canada Assembly Toronto SEW-EURODRIVE CO. OF CANADA LTD. Tel. (905) 7 91-15 53 Sales 210 Walker Drive Fax (905) 7 91-29 99 Service Bramalea, Ontario L6T3W1 Vancouver SEW-EURODRIVE CO. OF CANADA LTD. Tel. (604) 9 46-55 35 7188 Honeyman Street Fax (604) 946-2513 Delta. B.C. V4G 1 E2 Montreal SEW-EURODRIVE CO. OF CANADA LTD. Tel. (514) 3 67-11 24 2555 Rue Leger Street Fax (514) 3 67-36 77 LaSalle, Quebec H8N 2V9 Additional addresses for service in Canada provided on request! Chile Assembly Santiago de SEW-EURODRIVE CHILE Tel. (02) 6 23 82 03+6 23 81 63 Sales Chile Motores-Reductores LTDA. Fax (02) 6 23 81 79 Service Panamericana Norte No 9261 Casilla 23 - Correo Quilicura RCH-Santiago de Chile China Production Tianjin SEW-EURODRIVE (Tianjin) Co., Ltd. Tel. (022) 25 32 26 12 Assembly No. 46, 7th Avenue, TEDA Fax (022) 25 32 26 11 Sales Tianjin 300457 Service Colombia Assembly Bogotá SEW-EURODRIVE COLOMBIA LTDA. Tel. (0571) 5 47 50 50 Sales Calle 22 No. 132-60 Fax (0571) 5 47 50 44 Service Bodega 6, Manzana B sewcol@andinet.com Santafé de Bogotá Croatia Sales Zagreb KOMPEKS d. o. o. Tel. +385 14 61 31 58 Service PIT Erdödy 4 II Fax +385 14 61 31 58 HR 10 000 Zagreb Czech Republic Sales Praha SEW-EURODRIVE S.R.O. Tel. 02/20 12 12 34 + 20 12 12 36 Business Centrum Praha Fax 02/20 12 12 37 Luná 591 sew@sew-eurodrive.cz 16000 Praha 6 Denmark Assembly Kopenhagen SEW-EURODRIVEA/S Tel. 4395 8500 Sales Geminivej 28-30, P.O. Box 100 Fax 4395 8509 Service DK-2670 Greve http://www.sew-eurodrive.dk sew@sew-eurodrive.dk Estonia Sales Tallin ALAS-KUUL AS Tel. 6 59 32 30 Paldiski mnt.125 Fax 6 59 32 31 EE 0006 Tallin 07/2001 Address list Finland Assembly Lahti SEW-EURODRIVE OY Tel. (3) 589 300 Sales Vesimäentie 4 Fax (3) 780 6211 Service FIN-15860 Hollola 2 Great Britain Assembly Normanton SEW-EURODRIVE Ltd. Tel. 19 24 89 38 55 Sales Beckbridge Industrial Estate Fax 19 24 89 37 02 Service P.O. Box No.1 GB-Normanton, West- Yorkshire WF6 1QR Greece Sales Athen Christ. Boznos & Son S.A. Tel. 14 22 51 34 Service 12, Mavromichali Street Fax 14 22 51 59 P.O. Box 80136, GR-18545 Piraeus Boznos@otenet.gr Hong Kong Assembly Hong Kong SEW-EURODRIVE LTD. Tel. 2-7 96 04 77 + 79 60 46 54 Sales Unit No. 801-806, 8th Floor Fax 2-7 95-91 29 Service Hong Leong Industrial Complex sew@sewhk.com No. 4, Wang Kwong Road Kowloon, Hong Kong Hungary Sales Budapest SEW-EURODRIVE Kft. Tel. +36 1 437 06 58 Service H-1037 Budapest Fax +36 1 437 06 50 Kunigunda u. 18 India Assembly Baroda SEW-EURODRIVE India Pvt. Ltd. Tel. 0 265-83 10 86 Sales Plot No. 4, Gidc Fax 0 265-83 10 87 Service Por Ramangamdi · Baroda - 391 243 sew.baroda@gecsl.com Gujarat Ireland Sales Dublin Alperton Engineering Ltd. Tel. (01) 8 30 62 77 Service 48 Moyle Road Fax (01) 8 30 64 58 Dublin Industrial Estate Glasnevin, Dublin 11 Italy Assembly Milano SEW-EURODRIVE di R. Blickle & Co.s.a.s. Tel. (02) 96 98 01 Sales Via Bernini,14 Fax (02) 96 79 97 81 Service I-20020 Solaro (Milano) Japan Assembly Toyoda-cho SEW-EURODRIVE JAPAN CO., LTD Tel. (0 53 83) 7 3811-13 Sales 250-1, Shimoman-no, Fax (0 53 83) 7 3814 Service Toyoda-cho, Iwata gun Shizuoka prefecture, P.O. Box 438-0818 Korea Assembly Ansan-City SEW-EURODRIVE KOREA CO., LTD. Tel. (031) 4 92-80 51 Sales B 601-4, Banweol Industrial Estate Fax (031) 4 92-80 56 Service Unit 1048-4, Shingil-Dong Ansan 425-120 Luxembourg Assembly Brüssel CARON-VECTOR S.A. Tel. (010) 23 13 11 Sales Avenue Eiffel 5 Fax (010) 2313 36 Service B-1300 Wavre http://www.caron-vector.be info@caron-vector.be Macedonia Sales Skopje SGS-Skopje / Macedonia Tel. (0991) 38 43 90 "Teodosij Sinactaski” Fax (0991) 38 43 90 6691000 Skopje / Macedonia Malaysia Assembly Johore SEW-EURODRIVE SDN BHD Tel. (07) 3 54 57 07 + 3 54 94 09 Sales No. 95, Jalan Seroja 39, Taman Johor Jaya Fax (07) 3 5414 04 Service 81000 Johor Bahru, Johor West Malaysia 07/2001 Address list Netherlands Assembly Rotterdam VECTOR Aandrijftechniek B.V. Tel. +31 10 44 63 700 Sales Industrieweg 175 Fax +31 10 41 55 552 Service NL-3044 AS Rotterdam http://www.vector.nu Postbus 10085 info@vector.nu NL-3004 AB Rotterdam New Zealand Assembly Auckland SEW-EURODRIVE NEW ZEALAND LTD. Tel. 0064-9-2 74 56 27 Sales P.O. Box 58-428 Fax 0064-9-2 74 01 65 Service 82 Greenmount drive sales@sew-eurodrive.co.nz East Tamaki Auckland Christchurch SEW-EURODRIVE NEW ZEALAND LTD. Tel. (09) 3 84 62 51 10 Settlers Crescent, Ferrymead Fax (09) 3 84 64 55 Christchurch sales@sew-eurodrive.co.nz Norway Assembly Moss SEW-EURODRIVE A/S Tel. (69) 2410 20 Sales Solgaard skog 71 Fax (69) 2410 40 Service N-1599 Moss sew@sew-eurodrive.no Peru Assembly Lima SEW DEL PERU MOTORES REDUCTORES Tel. (511) 349-52 80 Sales S.A.C. Fax (511) 349-30 02 Service Los Calderos # 120-124 sewperu@terra.com.pe Urbanizacion Industrial Vulcano, ATE, Lima Poland Sales Lodz SEW-EURODRIVE Polska Sp.z.o.o. Tel. (042) 6 16 22 00 ul. Pojezierska 63 Fax (042) 6 16 22 10 91-338 Lodz sew@sew-eurodrive.pl Portugal Assembly Coimbra SEW-EURODRIVE, LDA. Tel. (0231) 20 96 70 Sales Apartado 15 Fax (0231) 20 36 85 Service P-3050-901 Mealhada infosew@sew-eurodrive.pt Romania Sales Bucuresti Sialco Trading SRL Tel. (01) 2 30 13 28 Service str. Madrid nr.4 Fax (01) 2 30 71 70 71222 Bucuresti sialco@mediasat.ro Russia Sales St. Petersburg ZAO SEW-EURODRIVE Tel. (812) 3 26 09 41 + 5 35 04 30 P.O. Box 193 Fax (812) 5 35 22 87 193015 St. Petersburg sewrus@post.spbnit.ru Singapore Assembly SEW-EURODRIVE PTE. LTD. Tel. 8 62 17 01-705 Sales No 9, Tuas Drive 2 Fax 8 61 28 27 Service Jurong Industrial Estate Telex 38 659 Singapore 638644 Slovenia Sales Celje Pakman - Pogonska Tehnika d.o.o. Tel. 00386 3 490 83 20 Service UI. XIV. divizije 14 Fax 00386 3 490 83 21 SLO – 3000 Celje pakman@siol.net 07/2001 Address list South Africa Assembly Johannesburg SEW-EURODRIVE (PROPRIETARY) LIMITED Tel. + 27 11 248 70 00 Sales Eurodrive House Fax +27 11 494 23 11 Service Cnr. Adcock Ingram and Aerodrome Roads Aeroton Ext. 2 Johannesburg 2013 P.O.Box 90004 Bertsham 2013 Capetown SEW-EURODRIVE (PROPRIETARY) LIMITED Tel. +27 21 552 98 20 Rainbow Park Fax +27 21 552 98 30 Cnr. Racecourse & Omuramba Road Telex 576 062 Montague Gardens Cape Town P.O.Box 36556 Chempet 7442 Cape Town Durban SEW-EURODRIVE (PROPRIETARY) LIMITED Tel. +27 31 700 34 51 2 Monaceo Place Fax +27 31 700 38 47 Pinetown Durban P.O. Box 10433, Ashwood 3605 Spain Assembly Bilbao SEW-EURODRIVE ESPAÑA, S.L. Tel. 9 44 31 84 70 Sales Parque Tecnológico, Edificio, 302 Fax 9 44 31 84 71 Service E-48170 Zamudio (Vizcaya) sew.spain@sew-eurodrive.es Sweden Assembly Jönköping SEW-EURODRIVE AB Tel. (036) 34 42 00 Sales Gnejsvägen 6-8 Fax (036) 34 42 80 Service S-55303 Jönköping www.sew-eurodrive.se Box 3100 S-55003 Jönköping Switzerland Assembly Basel Alfred lmhof A.G. Tel. (061) 4 17 17 17 Sales Jurastrasse 10 Fax (061) 4 17 17 00 Service CH-4142 Münchenstein bei Basel http://www.imhof-sew.ch info@imhof-sew.ch Thailand Assembly Chon Buri SEW-EURODRIVE (Thailand) Ltd. Tel. 0066-38 21 40 22 Sales Bangpakong Industrial Park 2 Fax 0066-38 21 45 31 Service 700/456, Moo.7, Tambol Donhuaroh Muang District Chon Buri 20000 Turkey Assembly Istanbul SEW-EURODRIVE Tel. (0216) 4 41 91 63 + 4 41 91 64 + 3 Sales Hareket Sistemleri San. ve Tic. Ltd. Sti 83 80 14 + 3 83 80 15 Service Bagdat Cad. Koruma Cikmazi No. 3 Fax (0216) 3 05 58 67 TR-81540 Maltepe ISTANBUL seweurodrive@superonline.com.tr USA Production Greenville SEW-EURODRIVE INC. Tel. (864) 4 39 75 37 Assembly 1295 Old Spartanburg Highway Fax Sales (864) 439-78 30 Sales P.O. Box 518 Fax Manuf. (864) 4 39-99 48 Service Lyman, S.C. 29365 Fax Ass. (864) 4 39-05 66 Telex 805 550 Assembly San Francisco SEW-EURODRIVE INC. Tel. (510) 4 87-35 60 Sales 30599 San Antonio St. Fax (510) 4 87-63 81 Service Hayward, California 94544-7101 Philadelphia/PA SEW-EURODRIVE INC. Tel. (856) 4 67-22 77 Pureland Ind. Complex Fax (856) 8 45-31 79 200 High Hill Road, P.O. Box 481 Bridgeport, New Jersey 08014 Dayton SEW-EURODRIVE INC. Tel. (9 37) 3 35-00 36 2001 West Main Street Fax (9 37) 4 40-37 99 Troy, Ohio 45373 Dallas SEW-EURODRIVE INC. Tel. (214) 3 30-48 24 3950 Platinum Way Fax (214) 3 30-47 24 Dallas, Texas 75237 07/2001 Address list USA Additional addresses for service in the USA provided on request! Venezuela Assembly Valencia SEW-EURODRIVE Venezuela S.A. Tel. +58 (241) 8 32 98 04 Sales Av. Norte Sur No. 3, Galpon 84-319 Fax +58 (241) 8 38 62 75 Service Zona Industrial Municipal Norte sewventas@cantr.net Valencia sewfinanzas@cantr.net 07/2001 10/2000 SEW-EURODRIVE GmbH & Co · P.O. Box 3023 · D-76642 Bruchsal/Germany · Phone +49-7251-75-0 Fax +49-7251-75-1970 · http://www.sew-eurodrive.com · sew@sew-eurodrive.com
Frequently asked questions
What makes Elite.Parts unique?

What kind of warranty will the MKS51A010-503-00 have?

Which carriers does Elite.Parts work with?

Will Elite.Parts sell to me even though I live outside the USA?

I have a preferred payment method. Will Elite.Parts accept it?

Why buy from GID?
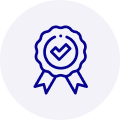
Quality
We are industry veterans who take pride in our work
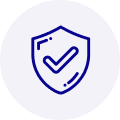
Protection
Avoid the dangers of risky trading in the gray market
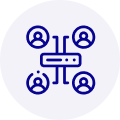
Access
Our network of suppliers is ready and at your disposal
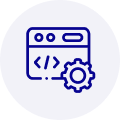
Savings
Maintain legacy systems to prevent costly downtime
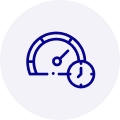
Speed
Time is of the essence, and we are respectful of yours
What they say about us
FANTASTIC RESOURCE
One of our top priorities is maintaining our business with precision, and we are constantly looking for affiliates that can help us achieve our goal. With the aid of GID Industrial, our obsolete product management has never been more efficient. They have been a great resource to our company, and have quickly become a go-to supplier on our list!
Bucher Emhart Glass
EXCELLENT SERVICE
With our strict fundamentals and high expectations, we were surprised when we came across GID Industrial and their competitive pricing. When we approached them with our issue, they were incredibly confident in being able to provide us with a seamless solution at the best price for us. GID Industrial quickly understood our needs and provided us with excellent service, as well as fully tested product to ensure what we received would be the right fit for our company.
Fuji
HARD TO FIND A BETTER PROVIDER
Our company provides services to aid in the manufacture of technological products, such as semiconductors and flat panel displays, and often searching for distributors of obsolete product we require can waste time and money. Finding GID Industrial proved to be a great asset to our company, with cost effective solutions and superior knowledge on all of their materials, it’d be hard to find a better provider of obsolete or hard to find products.
Applied Materials
CONSISTENTLY DELIVERS QUALITY SOLUTIONS
Over the years, the equipment used in our company becomes discontinued, but they’re still of great use to us and our customers. Once these products are no longer available through the manufacturer, finding a reliable, quick supplier is a necessity, and luckily for us, GID Industrial has provided the most trustworthy, quality solutions to our obsolete component needs.
Nidec Vamco
TERRIFIC RESOURCE
This company has been a terrific help to us (I work for Trican Well Service) in sourcing the Micron Ram Memory we needed for our Siemens computers. Great service! And great pricing! I know when the product is shipping and when it will arrive, all the way through the ordering process.
Trican Well Service
GO TO SOURCE
When I can't find an obsolete part, I first call GID and they'll come up with my parts every time. Great customer service and follow up as well. Scott emails me from time to time to touch base and see if we're having trouble finding something.....which is often with our 25 yr old equipment.
ConAgra Foods