PROSOFT MVI56103M
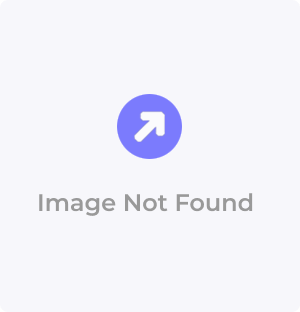
Description
MODULE
Part Number
MVI56103M
Price
Request Quote
Manufacturer
PROSOFT
Lead Time
Request Quote
Category
PRODUCTS - M
Datasheet
Extracted Text
MVI56-AFC
ControlLogix Platform
Liquid and Gas Flow Computer
February 25, 2011
USER MANUAL
Your Feedback Please
We always want you to feel that you made the right decision to use our products. If you have suggestions, comments,
compliments or complaints about our products, documentation, or support, please write or call us.
How to Contact Us
ProSoft Technology
5201 Truxtun Ave., 3rd Floor
Bakersfield, CA 93309
+1 (661) 716-5100
+1 (661) 716-5101 (Fax)
www.prosoft-technology.com
support@prosoft-technology.com
Copyright © 2011 ProSoft Technology, Inc., all rights reserved.
MVI56-AFC User Manual
February 25, 2011
® ® ® ® ®
ProSoft Technology , ProLinx , inRAx , ProTalk , and RadioLinx are Registered Trademarks of ProSoft
Technology, Inc. All other brand or product names are or may be trademarks of, and are used to identify products
and services of, their respective owners.
®
ProSoft Technology Product Documentation
In an effort to conserve paper, ProSoft Technology no longer includes printed manuals with our product shipments.
User Manuals, Datasheets, Sample Ladder Files, and Configuration Files are provided on the enclosed CD-ROM,
and are available at no charge from our web site: www.prosoft-technology.com
Important Installation Instructions
Power, Input, and Output (I/O) wiring must be in accordance with Class I, Division 2 wiring methods, Article 501-4 (b)
of the National Electrical Code, NFPA 70 for installation in the U.S., or as specified in Section 18-1J2 of the Canadian
Electrical Code for installations in Canada, and in accordance with the authority having jurisdiction. The following
warnings must be heeded:
A WARNING - EXPLOSION HAZARD - SUBSTITUTION OF COMPONENTS MAY IMPAIR SUITABILITY FOR
CLASS I, DIV. 2;
B WARNING - EXPLOSION HAZARD - WHEN IN HAZARDOUS LOCATIONS, TURN OFF POWER BEFORE
REPLACING OR WIRING MODULES
C WARNING - EXPLOSION HAZARD - DO NOT DISCONNECT EQUIPMENT UNLESS POWER HAS BEEN
SWITCHED OFF OR THE AREA IS KNOWN TO BE NON-HAZARDOUS.
D THIS DEVICE SHALL BE POWERED BY CLASS 2 OUTPUTS ONLY.
MVI (Multi Vendor Interface) Modules
WARNING - EXPLOSION HAZARD - DO NOT DISCONNECT EQUIPMENT UNLESS POWER HAS BEEN
SWITCHED OFF OR THE AREA IS KNOWN TO BE NON-HAZARDOUS.
AVERTISSEMENT - RISQUE D'EXPLOSION - AVANT DE DÉCONNECTER L'ÉQUIPEMENT, COUPER LE
COURANT OU S'ASSURER QUE L'EMPLACEMENT EST DÉSIGNÉ NON DANGEREUX.
Warnings
North America Warnings
Power, Input, and Output (I/O) wiring must be in accordance with Class I, Division 2 wiring methods, Article 501-4 (b)
of the National Electrical Code, NFPA 70 for installation in the U.S., or as specified in Section 18-1J2 of the Canadian
Electrical Code for installations in Canada, and in accordance with the authority having jurisdiction. The following
warnings must be heeded:
A Warning - Explosion Hazard - Substitution of components may impair suitability for Class I, Division 2.
B Warning - Explosion Hazard - When in hazardous locations, turn off power before replacing or rewiring modules.
C Warning - Explosion Hazard - Do not disconnect equipment unless power has been switched off or the area is
known to be non-hazardous.
Avertissement - Risque d'explosion - Avant de déconnecter l'équipement, couper le courant
ou s'assurer que l'emplacement est désigné non dangereux.
D Suitable for use in Class I, Division 2 Groups A, B, C and D Hazardous Locations or Non-Hazardous Locations.
ATEX Warnings and Conditions of Safe Usage
Power, Input, and Output (I/O) wiring must be in accordance with the authority having jurisdiction.
A Warning - Explosion Hazard - When in hazardous locations, turn off power before replacing or wiring modules.
B Warning - Explosion Hazard - Do not disconnect equipment unless power has been switched off or the area is
known to be non-hazardous.
C These products are intended to be mounted in an IP54 enclosure. The devices shall provide external means to
prevent the rated voltage being exceeded by transient disturbances of more than 40%. This device must be used
only with ATEX certified backplanes.
D DO NOT OPEN WHEN ENERGIZED.
Battery Life Advisory
The MVI46, MVI56, MVI56E, MVI69, and MVI71 modules use a rechargeable Lithium Vanadium Pentoxide battery to
backup the real-time clock and CMOS. The battery should last for the life of the module. The module must be
powered for approximately twenty hours before the battery becomes fully charged. After it is fully charged, the battery
provides backup power for the CMOS setup and the real-time clock for approximately 21 days. When the battery is
fully discharged, the module will revert to the default BIOS and clock settings.
Note: The battery is not user replaceable.
Markings
Electrical Ratings
Backplane Current Load: 800 mA @ 5.1 Vdc; 3 mA @ 24 Vdc
Operating Temperature: 0°C to 60°C (32°F to 140°F)
Storage Temperature: -40°C to 85°C (-40°F to 185°F)
Shock: 30 g, operational; 50 g, non-operational; Vibration: 5 g from 10 Hz to 150 Hz
Relative Humidity: 5% to 95% with no condensation
All phase conductor sizes must be at least 1.3 mm(squared) and all earth ground conductors must be at least
4mm(squared).
Label Markings
ATEX
II 3 G
EEx nA IIC T6
0°C <= Ta <= 60°C
cULus
E183151
Class I Div 2 Groups A,B,C,D
T6
-30°C <= Ta <= 60°C
Agency Approvals and Certifications
Agency Applicable Standard
RoHS
CE EMC-EN61326-1:2006; EN61000-6-4:2007
ATEX EN60079-15:2003
cULus UL508; UL1604; CSA 22.2 No. 142 & 213
CB Safety CA/10533/CSA
IEC 61010-1 Ed.2; CB 243333-2056722 (2090408)
GOST-R EN 61010
CSA EN 61010
243333 ME06 E183151
MVI56-AFC ♦ ControlLogix Platform Contents
Liquid and Gas Flow Computer User Manual
Contents
Your Feedback Please ........................................................................................................................ 2
How to Contact Us .............................................................................................................................. 2
®
ProSoft Technology Product Documentation .................................................................................... 2
Important Installation Instructions ....................................................................................................... 3
MVI (Multi Vendor Interface) Modules ................................................................................................ 3
Warnings ............................................................................................................................................. 3
Battery Life Advisory ........................................................................................................................... 3
Markings .............................................................................................................................................. 4
1 Introduction 11
1.1 Update Notice .......................................................................................................... 12
1.2 MVI56-AFC Module ................................................................................................. 14
1.3 Configuration Modification Lockout and Seal .......................................................... 15
2 Quick Start 17
2.1 Install AFC Manager ................................................................................................ 18
2.1.1 System Requirements ............................................................................................. 18
2.2 Starting AFC Manager ............................................................................................. 19
2.3 Using AFC Manager ................................................................................................ 20
2.3.1 Starting a New Project ............................................................................................. 20
2.3.2 Loading an Existing project ..................................................................................... 21
2.3.3 Printing the Configuration Report ............................................................................ 21
2.3.4 Converting a Project ................................................................................................ 22
2.3.5 Resetting Configuration Parameters ....................................................................... 23
2.3.6 Downloading the Project to the Module .................................................................. 24
2.3.7 Verifying Correct Operation ..................................................................................... 25
2.4 Ladder Logic Implementation .................................................................................. 26
2.5 Setting the Wallclock ............................................................................................... 28
2.6 Module Initialization ................................................................................................. 29
3 Meter Channel Functionality 31
3.1 Meter Channels ....................................................................................................... 32
3.2 Linear (Pulse) Meter Overview ................................................................................ 33
3.2.1 Primary Input = Pulse Count ................................................................................... 33
3.2.2 Primary Input = Pulse Frequency ............................................................................ 33
3.3 Differential (Orifice) Meter Overview ....................................................................... 34
3.3.1 Primary Input = Differential Pressure ...................................................................... 34
3.3.2 Primary Input = Flow Rate ....................................................................................... 34
3.4 Gas Product Overview ............................................................................................ 35
3.5 Liquid Product Overview ......................................................................................... 36
3.5.1 To use a densitometer ............................................................................................. 36
3.5.2 Module Configuration .............................................................................................. 36
3.5.3 Density Units ........................................................................................................... 36
3.5.4 Measuring Water Diluent ......................................................................................... 36
3.6 General Features .................................................................................................... 37
3.6.1 Process Variable Interface ...................................................................................... 37
ProSoft Technology, Inc. Page 5 of 316
February 25, 2011
Contents MVI56-AFC ♦ ControlLogix Platform
User Manual Liquid and Gas Flow Computer
3.6.2 Meter Scan Time..................................................................................................... 37
3.6.3 Multiple Meter Accumulators .................................................................................. 37
3.6.4 Product Batching .................................................................................................... 37
3.6.5 Data Archiving......................................................................................................... 38
3.6.6 Event Log Function ................................................................................................. 38
3.6.7 Measurement Units ................................................................................................. 38
3.6.8 Process Input Scaling ............................................................................................. 39
4 Meter Proving 41
4.1 Prover Configuration ............................................................................................... 42
4.1.1 Prover Type ............................................................................................................ 42
4.1.2 Prover Options ........................................................................................................ 46
4.1.3 Run Counts ............................................................................................................. 47
4.1.4 Run Input Setup ...................................................................................................... 47
4.1.5 Prover Characteristics ............................................................................................ 49
4.2 Setting up the AFC module for Meter Proving ........................................................ 51
4.2.1 Initial Requirements ................................................................................................ 53
4.2.2 Meter Proving Alarms ............................................................................................. 54
4.2.3 Prover Operation (How to do a Prove) ................................................................... 57
4.3 Meter Proving Reports ............................................................................................ 63
4.4 Protected Meter Proving Data in the AFC's Input Register Bank ........................... 64
4.4.1 Latest Prove Results ............................................................................................... 64
4.4.2 Meter Previous Prove Summary ............................................................................. 67
5 Modbus Database 69
5.1 AFC Modbus Address Space ................................................................................. 70
5.1.1 Accessing the Data ................................................................................................. 70
5.2 Primary Slave.......................................................................................................... 71
5.2.1 Modbus Address References ................................................................................. 71
5.2.2 Modbus Address Examples .................................................................................... 71
5.2.3 Meter-relative Data ................................................................................................. 72
5.2.4 Scratchpad .............................................................................................................. 73
5.3 Virtual Slave ............................................................................................................ 74
5.3.1 Virtual Slave Example Application .......................................................................... 75
6 Modbus Communication 77
6.1 Communication Parameters ................................................................................... 78
6.2 Port Options ............................................................................................................ 79
6.3 Modbus Master ....................................................................................................... 80
6.3.1 Example .................................................................................................................. 81
6.4 Modbus Pass-Through ........................................................................................... 82
7 Accumulators 83
7.1 Accumulator Totalizer and Residue ........................................................................ 84
7.2 Accumulator Types ................................................................................................. 85
7.2.1 Non-Resettable Accumulators ................................................................................ 85
7.2.2 Resettable Accumulators ........................................................................................ 85
7.2.3 Archive Accumulators ............................................................................................. 88
Page 6 of 316 ProSoft Technology, Inc.
February 25, 2011
MVI56-AFC ♦ ControlLogix Platform Contents
Liquid and Gas Flow Computer User Manual
7.3 Net Accumulator Calculation ................................................................................... 89
7.4 Frequently Asked Questions ................................................................................... 90
8 Archives 91
8.1 Archive Overview .................................................................................................... 92
8.2 Archive Generation .................................................................................................. 93
8.3 Archive Types .......................................................................................................... 94
8.4 Archive Order .......................................................................................................... 95
8.5 Archive Options ....................................................................................................... 97
8.6 Archive Locations .................................................................................................... 98
8.7 Editing the Archive Structure ................................................................................. 100
8.8 Extended Archives ................................................................................................ 102
8.8.1 Retrieving Extended Archives ............................................................................... 102
8.9 Archive Reports ..................................................................................................... 105
8.10 Archive Monitor ..................................................................................................... 107
9 Events 113
9.1 The Event Log ....................................................................................................... 114
9.2 Event Log Structures ............................................................................................. 115
9.3 Event Id Tag .......................................................................................................... 116
9.4 Event-triggered Archives and Accumulator Resets .............................................. 117
9.5 Downloading the Event Log in Firmware Version 2.07 and Later ......................... 118
9.5.1 Basic Principles of Implementation ....................................................................... 125
9.5.2 Data Elements ....................................................................................................... 127
9.5.3 Virtual Slave Precedence Relations ...................................................................... 129
9.5.4 Security and Optimization ..................................................................................... 130
9.5.5 The Log-Download Window (LDW) ....................................................................... 131
9.5.6 Modbus Transaction Sequencing and Constraints ............................................... 132
9.5.7 Access by Multiple Hosts ...................................................................................... 137
9.5.8 Other Considerations ............................................................................................ 138
9.6 Period-end Events ................................................................................................. 139
9.7 Loggable Events .................................................................................................... 140
9.8 Special Events ....................................................................................................... 141
9.9 Site Data Point Events .......................................................................................... 142
9.10 Meter Data Point Events ....................................................................................... 143
9.11 Stream Data Point Events ..................................................................................... 146
9.12 Prover Data Point Events ...................................................................................... 148
9.13 "Rkv" Notes ........................................................................................................... 151
9.14 Downloading the Event Log in Firmware Version 2.05 and Earlier ...................... 152
10 Security (Passwords) 155
10.1 Hard Password ...................................................................................................... 157
11 MVI56-AFC Backplane Communication 159
11.1 MVI56-AFC Module Data Transfer ........................................................................ 160
11.1.1 Input/Output Blocks for Data Transfer ................................................................... 160
11.1.2 Input/Output Transactions ..................................................................................... 162
11.2 MVI56-AFC Function Block Interface .................................................................... 167
ProSoft Technology, Inc. Page 7 of 316
February 25, 2011
Contents MVI56-AFC ♦ ControlLogix Platform
User Manual Liquid and Gas Flow Computer
11.2.1 Function Block Structure ....................................................................................... 168
11.2.2 Function Block Definition - 0: Null ......................................................................... 171
11.2.3 Function Block Definition - 1: Wall Clock .............................................................. 172
11.2.4 Function Block Definition - 4, 5, 6 & 7: Modbus Pass Through ............................ 173
11.2.5 Function Block Definition - 8: Meter Process Variables........................................ 175
11.2.6 Function Block Definition - 9: Meter Analysis, 16-bit ............................................ 184
11.2.7 Function Block Definition - 10: Meter Type Fetch ................................................. 186
11.2.8 Function Block Definition - 11: Meter Analysis, 32-bit .......................................... 187
11.2.9 Function Block Definition - 12: Site/Meter Signals ................................................ 190
11.2.10 Function Block Definition - 14: Meter Archive Fetch............................................. 192
11.2.11 Function Block Definition - 16/17/18/19: Modbus Gateway Read ........................ 193
11.2.12 Function Block Definition - 20, 21: Modbus Gateway Write ................................. 196
11.2.13 Function Block Definition - 24, 25, 26: Modbus Master ........................................ 199
11.2.14 Function Block Definition - 28, 29: Disable/Enable Meters .................................. 203
12 MVI56-AFC Sample Logic 205
12.1 Sample Logic Overview ........................................................................................ 206
12.1.1 Process Block (uses Transaction Numbers from 1 to 16) .................................... 208
12.1.2 Modbus Gateway Block (uses Transaction Numbers from 17 to 25) ................... 209
12.1.3 Wallclock Block (uses Transaction Number =99) ................................................. 209
12.1.4 Sample MVI56-AFC Logic Tasks.......................................................................... 210
12.2 Using the Sample Add-On Instruction .................................................................. 211
12.2.1 Import Procedure .................................................................................................. 211
12.2.2 Adjust the Input and Output Array Sizes (Optional).............................................. 217
12.3 ControlLogix Sample Logic Details ....................................................................... 220
12.3.1 Enable/Disable Status .......................................................................................... 220
12.3.2 Disable Meter ........................................................................................................ 220
12.3.3 Enable Meter......................................................................................................... 221
12.3.4 Wallclock ............................................................................................................... 222
12.3.5 Meter Profile .......................................................................................................... 223
12.3.6 Meter Process Variables ....................................................................................... 224
12.3.7 Meter Calculation Results ..................................................................................... 227
12.3.8 Meter Signals ........................................................................................................ 229
12.3.9 Molar Analysis (For Gas Product Only) ................................................................ 231
12.3.10 Set the Processor Time ........................................................................................ 236
12.3.11 Checking Meter Alarms ........................................................................................ 237
12.3.12 Site Status ............................................................................................................. 239
12.3.13 Modbus Master ..................................................................................................... 239
12.3.14 Modbus pass-through ........................................................................................... 244
12.3.15 Modbus Gateway .................................................................................................. 245
13 Diagnostics and Troubleshooting 255
13.1 User LEDs ............................................................................................................. 256
13.1.1 App Status LED .................................................................................................... 256
13.1.2 BP Act and P1, P2, or P3 ..................................................................................... 256
13.2 BBRAM LEDs ....................................................................................................... 257
13.3 Meter Alarms ......................................................................................................... 258
13.4 Checksum Alarms ................................................................................................. 262
13.5 Events ................................................................................................................... 263
13.6 Audit Scan ............................................................................................................. 264
Page 8 of 316 ProSoft Technology, Inc.
February 25, 2011
MVI56-AFC ♦ ControlLogix Platform Contents
Liquid and Gas Flow Computer User Manual
14 Reference 269
14.1 General Specifications .......................................................................................... 270
14.1.1 On-line Communication & Configuration ............................................................... 271
14.1.2 Reports .................................................................................................................. 271
14.1.3 Modbus Interface ................................................................................................... 271
14.1.4 Configurable Options ............................................................................................. 272
14.1.5 Supported Meters .................................................................................................. 272
14.1.6 Hardware Specifications........................................................................................ 273
14.2 Measurement Standards ....................................................................................... 274
14.2.1 Basic Metering According to Meter type ............................................................... 275
14.2.2 Liquid Correction Factor Details ............................................................................ 277
14.3 Wedge Meter Applications .................................................................................... 279
14.4 Configurable Archive Registers ............................................................................. 280
14.4.1 Information for Users of AFC Manager Versions Older Than 2.01.000 ................ 284
14.5 Archive Data Format ............................................................................................. 286
14.5.1 Timestamp Date and Time Format ....................................................................... 286
14.5.2 Pre-defined Header ............................................................................................... 287
14.5.3 Orifice (Differential) Meter with Gas Product......................................................... 288
14.5.4 Pulse (Linear) Meter with Gas Product ................................................................. 289
14.5.5 Orifice (Differential) Meter with Liquid Product...................................................... 289
14.5.6 Pulse (Linear) Meter with Liquid Product .............................................................. 290
14.5.7 Flow Rate Integration with Gas Product ................................................................ 290
14.5.8 Pulse Frequency Integration with Gas Product ..................................................... 291
14.5.9 Flow Rate Integration with Liquid Product............................................................. 291
14.5.10 Pulse Frequency Integration with Liquid Product .................................................. 292
14.6 Modbus Addressing Common to Both Primary and Virtual Slaves ....................... 293
14.7 Modbus Port configuration .................................................................................... 296
14.8 Startup Basics and Frequently Asked Questions .................................................. 298
14.9 Cable Connections ................................................................................................ 299
14.9.1 RS-232 Configuration/Debug Port ........................................................................ 299
14.9.2 RS-232 Application Port(s) ................................................................................... 299
14.9.3 RS-422 .................................................................................................................. 302
14.9.4 RS-485 Application Port(s) .................................................................................... 302
14.9.5 DB9 to RJ45 Adaptor (Cable 14) .......................................................................... 303
15 Support, Service & Warranty 305
Contacting Technical Support ......................................................................................................... 305
15.1 Return Material Authorization (RMA) Policies and Conditions.............................. 307
15.1.1 Returning Any Product .......................................................................................... 307
15.1.2 Returning Units Under Warranty ........................................................................... 308
15.1.3 Returning Units Out of Warranty ........................................................................... 308
15.2 LIMITED WARRANTY ........................................................................................... 309
15.2.1 What Is Covered By This Warranty ....................................................................... 309
15.2.2 What Is Not Covered By This Warranty ................................................................ 310
15.2.3 Disclaimer Regarding High Risk Activities ............................................................ 310
15.2.4 Intellectual Property Indemnity .............................................................................. 311
15.2.5 Disclaimer of all Other Warranties ........................................................................ 311
15.2.6 Limitation of Remedies ** ...................................................................................... 312
15.2.7 Time Limit for Bringing Suit ................................................................................... 312
15.2.8 No Other Warranties ............................................................................................. 312
15.2.9 Allocation of Risks ................................................................................................. 312
ProSoft Technology, Inc. Page 9 of 316
February 25, 2011
Contents MVI56-AFC ♦ ControlLogix Platform
User Manual Liquid and Gas Flow Computer
15.2.10 Controlling Law and Severability .......................................................................... 312
Index 313
Page 10 of 316 ProSoft Technology, Inc.
February 25, 2011
MVI56-AFC ♦ ControlLogix Platform Introduction
Liquid and Gas Flow Computer User Manual
1 Introduction
In This Chapter
Update Notice ........................................................................................ 12
MVI56-AFC Module ............................................................................... 14
Configuration Modification Lockout and Seal ........................................ 15
The MVI56-AFC Flow Computer module performs measurement of hydrocarbon
gases and liquids using currently accepted industry measurement standards. The
module consists of a single-slot solution for Rockwell Automation chassis. To
obtain its process inputs for calculations, the module uses the process data
collected by analog and pulse I/O modules. The processor transfers this data to
the AFC module, which then calculates flow rates, accumulated volumes, and
accumulated mass. The results of the calculations are transferred back to the
processor for use in the application logic, or for transfer to a SCADA host.
The module has two communication ports for Modbus communication allowing
easy access to a remote Modbus device. The module works as a Modbus slave
or master device.
As discussed later in this manual, the internal Modbus database can be
accessed by a Modbus Master device and by the processor (using the Modbus
Gateway Function).
The AFC Manager software can be used for easy meter configuration and
application monitoring. Refer to the AFC Manager User Manual for complete
information about this tool.
The following section provides a sample application where input data is
transferred from the transmitters to analog input cards on the Rockwell
Automation rack and the values are transferred from the processor to the module
(the module supports floating-point, scaled integer, or 4 to 20 mA format).
For Pulse meter applications, the pulse count and pulse frequency values are
typically transmitted through high-speed counter modules in the rack.
The module performs the flow calculation based on the values transferred
through the backplane. The calculation results can be read to the processor or
polled from a remote Modbus master unit connected to one of the communication
ports.
ProSoft Technology, Inc. Page 11 of 316
February 25, 2011
Introduction MVI56-AFC ♦ ControlLogix Platform
User Manual Liquid and Gas Flow Computer
1.1 Update Notice
If your module measures liquids, please read this notice before upgrading from
version 2.04 (or earlier) to 2.05 (or later).
For compliance with new measurement standards, the AFC version 2.05 has
introduced several new liquid product groups. In particular, the two non-refined
liquid product groups of version 2.04, which covered the entire density range of
crudes and NGLs, have each been split into two separate product groups, one
for the higher density range of crudes and the other for the lower density range of
NGLs. If your module has meter channels configured for either "Crude, NGL" or
"Oil-water emulsion", you should decide before upgrading the firmware the
new product group (light or heavy) to which each such channel should be
assigned. This assignment will be performed during the upgrade process and will
preserve all other configuration and historical records including accumulator
values and archives, in contrast to changing a product group after the upgrade
which resets the meter configuration and erases all historical records. Meter
channels configured for "Gas" or "Refined products" are not affected.
AFC Manager exhibits the same behavior when converting a project between
versions 2.04 (or earlier) and 2.05 (or later).
The criterion for assigning the new product group depends on the density units
and the Default Reference Density, as described in the following tables:
Density Units = kg/m3
Version 2.04 Product Group Default Reference Density Version 2.05 Product Group
Crude, NGL = 0 OR ≥ 610.0 Crude oils, JP4
Crude, NGL > 0 AND < 610.0 NGLs, LPGs
Oil Water Emulsion Oil-water emulsion (Crd)
= 0 OR ≥ 610.0
Oil Water Emulsion > 0 AND < 610.0 Oil-water emulsion (NGL)
Density Units = Rd/60
Version 2.04 Product Group Default Reference Density Version 2.05 Product Group
Crude, NGL Crude oils, JP4
= 0 OR ≥ 0.6100
Crude, NGL > 0 AND < 0.6100 NGLs, LPGs
Oil Water Emulsion Oil-water emulsion (Crd)
= 0 OR ≥ 0.6100
Oil Water Emulsion > 0 AND < 0.6100 Oil-water emulsion (NGL)
Due to roundoff error of numeric conversions, a Relative Density very close to
the cutoff value of 0.6100 may cause the module to assign the new product
group opposite to the one that was intended. Before upgrading, change the
Default Reference Density to a number significantly different from 0.6100, such
as 0.6110 (to target Crude) or 0.6090 (to target NGLs). You may change it back
to the correct value after the upgrade.
Page 12 of 316 ProSoft Technology, Inc.
February 25, 2011
MVI56-AFC ♦ ControlLogix Platform Introduction
Liquid and Gas Flow Computer User Manual
Density Units = API Gravity
Version 2.04 Product Group Default Reference Density Version 2.05 Product Group
Crude, NGL Crude oils, JP4
= 0 OR ≤ 100.0
Crude, NGL > 0 AND > 100.0 NGLs, LPGs
Oil Water Emulsion Oil-water emulsion (Crd)
= 0 OR ≤ 100.0
Oil Water Emulsion > 0 AND > 100.0 Oil-water emulsion (NGL)
ProSoft Technology, Inc. Page 13 of 316
February 25, 2011
Introduction MVI56-AFC ♦ ControlLogix Platform
User Manual Liquid and Gas Flow Computer
1.2 MVI56-AFC Module
Page 14 of 316 ProSoft Technology, Inc.
February 25, 2011
MVI56-AFC ♦ ControlLogix Platform Introduction
Liquid and Gas Flow Computer User Manual
1.3 Configuration Modification Lockout and Seal
The MVI56-AFC application configuration can be certified and sealed with a user-
installable Lockout jumper and a tamper-evident lead seal. The Lockout jumper
and seal are commonly required for Weights & Measures certification, or custody
transfer applications.
Important: When the jumper is installed, the module will not accept configuration changes to
Sealable Parameters, which are parameters that affect the accuracy of flow calculation. Before
breaking the seal to remove the jumper, you should verify the steps required to recertify the module
with the appropriate regulatory agency.
For more information on sealing procedures, refer to "Sealing Provisions", on
page 8 of the MVI56-AFC Custody Transfer Certification document, which is
available from the ProSoft Technology web site at http://www.prosoft-
technology.com/content/view/full/4613
ProSoft Technology, Inc. Page 15 of 316
February 25, 2011
Introduction MVI56-AFC ♦ ControlLogix Platform
User Manual Liquid and Gas Flow Computer
To install the Lockout jumper and seal, follow these steps.
1 Locate the Lockout Jumper pins and Lockout Block,
labeled "W & M Lock" inside the module door, and
below the BBRAM ERR and OK LEDs.
1 Install the provided Lockout Jumper to connect the two
pins.
1 Carefully slide the Lockout Block up through the hole in
the Lockout Jumper. Be careful not to bend or break
the jumper block pins.
1 When the Lockout Block is positioned correctly, it will
expose a hole in the block, through which you may
pass the seal wire.
1 Slide the seal wire through the hole in the Lockout
Block. Pass the wire through the slot in the lead seal,
and then crimp the lead seal around the wire.
Once sealed, the Lockout block and jumper cannot be removed without
damaging the seal, the block, or the jumper.
Page 16 of 316 ProSoft Technology, Inc.
February 25, 2011
MVI56-AFC ♦ ControlLogix Platform Quick Start
Liquid and Gas Flow Computer User Manual
2 Quick Start
In This Chapter
Install AFC Manager .............................................................................. 18
Starting AFC Manager ........................................................................... 19
Using AFC Manager .............................................................................. 20
Ladder Logic Implementation ................................................................ 26
Setting the Wallclock ............................................................................. 28
Module Initialization ............................................................................... 29
This section provides a general overview of the steps required to install and
configure the module. You should read the AFC Manager User Manual to obtain
a clear understanding of the steps outlined in this section.
ProSoft Technology, Inc. Page 17 of 316
February 25, 2011
Quick Start MVI56-AFC ♦ ControlLogix Platform
User Manual Liquid and Gas Flow Computer
2.1 Install AFC Manager
The AFC Manager application is included on the CD-ROM shipped with your
module. Before you can use the application, you must install it on your computer.
2.1.1 System Requirements
The following system requirements are the recommended minimum
specifications to successfully install and run AFC Manager:
Microsoft Windows compatible PC
Windows 2000 with Service Pack 2 or higher, or Windows XP Professional
with Service Pack 2 or higher, or Windows 2003 or Windows Vista, or
Windows 7.
300 mHz Pentium processor (or equivalent)
128 megabytes of RAM
20 megabytes of free disk space
Available serial port (COM port) or USB to Serial adapter cable with
necessary drivers, required for communication between AFC Manager
software and the AFC module.
DB9 adapter cable (included with module), required for connection between
PC serial port and AFC module (PTQ-AFC module does not require an
adapter).
To install the AFC Manager application
1 Insert the ProSoft Solutions CD in your CD-ROM drive. On most computers,
a menu screen will open automatically. If you do not see a menu within a few
seconds, follow these steps:
a Click the Start button, and then choose Run.
b In the Run dialog box, click the Browse button.
c In the Browse dialog box, click "My Computer". In the list of drives,
choose the CD-ROM drive where you inserted the ProSoft Solutions CD.
d Select the file prosoft.exe, and then click Open.
e On the Run dialog box, click OK.
2 On the CD-ROM menu, click Documentation and Tools. This action opens a
Windows Explorer dialog box.
3 Open the Utilities folder, and then open the AFCManager folder.
4 Double-click the file Setup.exe. If you are prompted to restart your computer
so that files can be updated, close all open applications, and then click OK.
When your computer has finished restarting, begin again at Step 1.
5 Click OK or Yes to dismiss any confirmation dialog boxes.
6 It may take a few seconds for the installation wizard to start. Click OK on the
AFC Manager Setup dialog box to begin installing AFC Manager.
7 Follow the instructions on the installation wizard to install the program with its
default location and settings.
8 When the installation finishes, you may be prompted to restart your computer
if certain files were in use during installation. The updated files will be
installed during the restart process.
Page 18 of 316 ProSoft Technology, Inc.
February 25, 2011
MVI56-AFC ♦ ControlLogix Platform Quick Start
Liquid and Gas Flow Computer User Manual
2.2 Starting AFC Manager
To start AFC Manager
1 Click the START button, and then choose PROGRAMS.
2 In the Programs menu, choose ProSoft Technology.
3 In the ProSoft Technology menu, choose AFC Manager.
ProSoft Technology, Inc. Page 19 of 316
February 25, 2011
Quick Start MVI56-AFC ♦ ControlLogix Platform
User Manual Liquid and Gas Flow Computer
2.3 Using AFC Manager
The AFC module is configured with configuration files that you create using AFC
Manager. A configuration file is called a Project.
2.3.1 Starting a New Project
To start a new project
1 Start AFC MANAGER, and then open the File Menu.
2 On the File Menu, choose NEW, and then select your module and firmware
version number.
The version number refers to the firmware version of your module. If you do
not know the firmware version number, follow these steps:
a) Open the Project menu.
b) Choose SITE CONFIGURATION. This action opens the Site Configuration
dialog box.
c) Click the READ button. The firmware version is listed below the serial
number, in the upper right part of the dialog box.
Important: You must be connected to the module and "online" to read data from the module.
3 Follow the steps in the remainder of this User Guide to configure your module
and your AFC device.
4 Before closing the program, open the File menu and choose SAVE AS, to
save your project so you can open it again later.
Page 20 of 316 ProSoft Technology, Inc.
February 25, 2011
MVI56-AFC ♦ ControlLogix Platform Quick Start
Liquid and Gas Flow Computer User Manual
2.3.2 Loading an Existing project
You can open and edit a project you have previously saved. Do this if you have
started, but not completed, the configuration of your project, or if you need to
modify the settings for a project that has already been downloaded to the
module.
To load an existing project
1 Start AFC MANAGER, and then open the File menu.
2 On the File menu, choose LOAD. This action opens a dialog box that shows a
list of AFC Manager project files (AFC files) in the current folder.
3 Choose the project to load, and then click OPEN.
2.3.3 Printing the Configuration Report
You can print a report of your configuration for future reference, or for archival
purposes.
To print the configuration report
1 Open the File menu, and then select PRINT REPORT. This action opens the
Print Configuration dialog box.
2 On the Print Configuration dialog box, select (check) the items to include in
the printed report.
3 Click PRINT to send the report to your default printer.
Note: The size of the report depends on items you choose to include, and may require 75 pages or
more. Consider this before printing.
ProSoft Technology, Inc. Page 21 of 316
February 25, 2011
Quick Start MVI56-AFC ♦ ControlLogix Platform
User Manual Liquid and Gas Flow Computer
2.3.4 Converting a Project
You can convert an existing project (configuration file) to use it with a different
module or firmware version. Do this if:
You want to reuse an application created for a different AFC module, for
example a project that was created for a PTQ-AFC that you want to use for
an MVI69-AFC.
You apply a firmware upgrade to a module.
To convert a project:
1 Open the File menu, and then choose OPEN.
2 Open the project (configuration file) to convert.
3 Open the Project menu, and then choose CHANGE MODULE TYPE.
4 Choose the module type and firmware version from the menu.
5 Save your project.
Note: AFC Manager will save your updated configuration file with the same name as the file you
loaded. If you need to keep your original configuration, change the file name of your updated
configuration before saving.
Page 22 of 316 ProSoft Technology, Inc.
February 25, 2011
MVI56-AFC ♦ ControlLogix Platform Quick Start
Liquid and Gas Flow Computer User Manual
2.3.5 Resetting Configuration Parameters
If you have modified your project (configuration file), or if you have loaded a
configuration file from disk, but you want to start a new project, you can reset the
configuration parameters back to their defaults without having to close and
reopen the AFC Manager.
To reset configuration parameters
1 Close any dialog boxes that are open.
2 Save the configuration file you were working on, if you would like to load it
again later.
3 On the File menu, choose RESET.
Note: This procedure has the same effect as choosing File / New / None.
If you have made changes to the configuration that have not yet been saved, a
confirmation dialog box will open.
Answer Yes to save your changes, or No to discard your changes and begin
working on a new configuration. Click Cancel to abandon the attempted action
that caused this message.
ProSoft Technology, Inc. Page 23 of 316
February 25, 2011
Quick Start MVI56-AFC ♦ ControlLogix Platform
User Manual Liquid and Gas Flow Computer
2.3.6 Downloading the Project to the Module
1 Click PROJECT / DOWNLOAD PROJECT.
2 This action opens the Local Port Settings window. Enter the port parameters
to use, and then click DONE.
3 During the download operation, the following progress window is displayed:
4 When the file transfer is complete, the following window is displayed:
Note: The virtual slave remapping data (page 74) is not downloaded during the procedure because
it requires a separate download operation.
Troubleshooting Tip: If the AFC Manager displays an "Illegal Data Value" message, it typically
indicates an invalid meter type or product group configuration. The module does not accept a
configuration file that attempts to change a meter type or product group for a meter that is currently
enabled. Disable all meters, change the meter types and product groups, and then enable the
meters again.
Page 24 of 316 ProSoft Technology, Inc.
February 25, 2011
MVI56-AFC ♦ ControlLogix Platform Quick Start
Liquid and Gas Flow Computer User Manual
2.3.7 Verifying Correct Operation
When all of the configuration steps have been completed, the module should be
ready to perform measurement calculations. To verify that the module is
configured correctly, follow these steps:
1 Enable all meters that will be used, as any meter will only perform
calculations if it is enabled. Any meter can be enabled either with ladder logic
(MVI56-AFC modules), function blocks (PTQ modules) or with AFC Manager.
2 Make sure that the wallclock is running, and that it has valid date and time
information. After power-up, the wallclock will be stopped, therefore the
module will not perform any time-scheduled operations, such as writing
period-end archives, and will not timestamp records written to the event log
until it receives a wallclock command from the ladder logic.
The sample ladder logic programs the wallclock update command upon
detecting "power-up" status from the AFC. The date/time information used is
the same as the processor, therefore you should use the configuration tool for
your processor to verify that the processor has valid date/time data. If the
processor wallclock is not valid (for example if the year = 1900), the module
will not accept the command. You may easily determine if the wallclock is
running by performing two consecutive read operations in the Meter Monitor.
3 Make sure that the meter does not have any alarms. A meter alarm may
affect flow calculation. Look at the Meter Monitor dialog box for alarms.
4 Make sure that the input parameters transferred from the processor are
correct. You can look at these values in the Meter Monitor dialog box.
5 When using a pulse meter, make sure that the pulse input rollover parameter
in Meter Configuration matches the actual input rollover value used in the
high speed counter module.
ProSoft Technology, Inc. Page 25 of 316
February 25, 2011
Quick Start MVI56-AFC ♦ ControlLogix Platform
User Manual Liquid and Gas Flow Computer
2.4 Ladder Logic Implementation
The sample ladder logic performs tasks that are covered in the Ladder Logic
sections of this manual. The most important task is to continuously write meter
process input variables from the processor to the module, and read calculation
results from the module to the processor.
Refer to the Ladder Logic sections for instructions on how to transfer the meter
process variables from the processor to the module. Ladder logic is required to
move the process variables to the correct data file or controller tag in the
processor.
The Meter Monitor window (Process Inputs field) displays the values that are
transferred from the processor.
Page 26 of 316 ProSoft Technology, Inc.
February 25, 2011
MVI56-AFC ♦ ControlLogix Platform Quick Start
Liquid and Gas Flow Computer User Manual
The values calculated by the module are continuously transferred to the
processor. You can refer to the Meter Monitor window to verify results
calculated by the module.
Refer to the Ladder Logic section for more information regarding the data files
and controller tags that store the calculation results transferred from the module
(for example, accumulator, flow rate, and so on).
ProSoft Technology, Inc. Page 27 of 316
February 25, 2011
Quick Start MVI56-AFC ♦ ControlLogix Platform
User Manual Liquid and Gas Flow Computer
2.5 Setting the Wallclock
After power-up, the module must receive valid wallclock data from the ladder
logic to perform time-scheduled operations and to properly timestamp historical
records. The sample ladder logic automatically writes the wallclock upon
detecting power-up status from the AFC using the processor’s date and time
information. You should ensure that the processor contains valid date and time
information. If it does not, the module may not accept the wallclock block.
You can verify the wallclock information using the Meter Monitor section as
shown in the following example:
Refer to the Sample Ladder Logic section for more information on this topic.
Page 28 of 316 ProSoft Technology, Inc.
February 25, 2011
MVI56-AFC ♦ ControlLogix Platform Quick Start
Liquid and Gas Flow Computer User Manual
2.6 Module Initialization
When the module is powered up for the first time, both the OK and ERR BBRAM
LEDs are illuminated. This indicates that the module is in the Cold Start state and
is not yet ready to perform calculations. The following steps initialize the module:
Enable at least one meter
Set the processor to RUN mode
After these two steps are accomplished, the state is changed from Cold Start to
Released. This indicates that that module is ready to perform flow calculations.
When in the Released state, the OK LED is ON and the ERR LED is off.
When the module is ready, you will use AFC Manager to monitor meter
operation, archives, and events. The AFC Manager User Manual contains
detailed information on these tasks.
ProSoft Technology, Inc. Page 29 of 316
February 25, 2011
Quick Start MVI56-AFC ♦ ControlLogix Platform
User Manual Liquid and Gas Flow Computer
Page 30 of 316 ProSoft Technology, Inc.
February 25, 2011
MVI56-AFC ♦ ControlLogix Platform Meter Channel Functionality
Liquid and Gas Flow Computer User Manual
3 Meter Channel Functionality
In This Chapter
Meter Channels ..................................................................................... 32
Linear (Pulse) Meter Overview .............................................................. 33
Differential (Orifice) Meter Overview ..................................................... 34
Gas Product Overview........................................................................... 35
Liquid Product Overview........................................................................ 36
General Features .................................................................................. 37
ProSoft Technology, Inc. Page 31 of 316
February 25, 2011
Meter Channel Functionality MVI56-AFC ♦ ControlLogix Platform
User Manual Liquid and Gas Flow Computer
3.1 Meter Channels
Each meter channel can be assigned as a linear meter (e.g. a pulse meter) input
or as a differential meter (e.g an orifice meter) input for flow measurement using
either SI (metric) or US units. Selecting the differential meter causes the module
to use the AGA 3 standard for flow calculation (for a gas orifice meter you may
optionally choose ISO 5167-2 instead). Selecting the linear meter causes the
module to use the AGA 7 standard for gas flow calculation.
Each meter channel can be configured for gas or liquid (crude or refined)
product. The Product Group essentially selects the API/AGA Standards to be
used in calculating flow rates/increments.
Selecting "Gas" causes use of AGA8 and either AGA3 or AGA7 Standards.
Selecting any liquid group causes use of API MPMS Chapter 11(tables
23/24/53/54) and related Standards. "Crude oils, JP4" and "Oil-water emulsion
Crd)" use the, "A", tables. “NGLs, LPG’s” and “Oil-water emulsion (NGL) use the
“E” tables. "Refined Products" use the "B" tables. "Lubricating oils" use the "D"
tables, and "Special applications" use the "C" tables. "Crude oils, JP4" and
"NGLs/LPG" are used for propane, butane, NGLs (natural gas liquids), and crude
oils which are relatively water-free (less than 5 percent). The two "Oil-water
emulsion" groups are used for crude and NGL/LPG that might have a high
concentration of water for which API MPMS Chapter 20.1 is applicable. "Refined
products (xJP4)” is used for lighter refined liquids such as gasolines, jet fuels
(except JP4), and fuel oils. "Lubricating oils” is used for heavier refined liquids.
"Special applications" is used for those liquids that cannot reasonably be
assigned to one of the other groups; for this product group an explicit coefficient
of thermal expansion must be supplied.
The following table provides a brief overview of the standards used according to
the Meter Type and Product Group:
Meter Type Product Group Standards
Differential Gas AGA8, AGA3/ISO5167
Differential Liquid MPMS ch 11 AGA3/ISO5167
Linear Gas AGA8, AGA7
Linear Liquid MPMS ch 11, MPMS ch12.2
Note: The meter channel must be disabled in order to change its meter type and product group.
Page 32 of 316 ProSoft Technology, Inc.
February 25, 2011
MVI56-AFC ♦ ControlLogix Platform Meter Channel Functionality
Liquid and Gas Flow Computer User Manual
3.2 Linear (Pulse) Meter Overview
The module typically receives the pulse count and pulse frequency values from a
high-speed counter module. The module uses these values to perform
calculations.
You can configure the primary input to be used for volume calculation. You can
configure it as Pulse Count or Pulse Frequency.
3.2.1 Primary Input = Pulse Count
If you select Pulse Count as the primary input, the module uses the pulse count
value transferred through the backplane as the primary input for volume
calculation. In this case, the pulse frequency will be used for flow rate calculation
only.
3.2.2 Primary Input = Pulse Frequency
If you select Pulse Frequency as the primary input, the module uses the pulse
frequency value transferred through the backplane as the primary input for both
flow accumulation and flow rate calculation. The pulse count value is ignored by
the module.
ProSoft Technology, Inc. Page 33 of 316
February 25, 2011
Meter Channel Functionality MVI56-AFC ♦ ControlLogix Platform
User Manual Liquid and Gas Flow Computer
3.3 Differential (Orifice) Meter Overview
The static pressure of the gas stream can be measured either upstream of the
meter (before the differential pressure drop), or downstream of the meter (after
the pressure drop). Both AGA3 and AGA8 require the upstream static pressure
for their calculations, where:
upstream pressure = downstream pressure + differential pressure
If the pressure is measured from a downstream tap (typical), the Downstream
Static Pressure option should be set through the AFC Manager.
The module also supports the V-Cone device. You can configure V-Cone meters
and downstream selections in AFC Manager, on the Meter Configuration /
Calculation Options dialog box.
3.3.1 Primary Input = Differential Pressure
The primary input parameter configures the value used as source for the
accumulator calculation. If the parameter is set to Differential Pressure, the
module uses the differential pressure value transferred through the backplane for
accumulator calculation.
3.3.2 Primary Input = Flow Rate
You can configure the primary input parameter as flow rate in order to use this
value for the accumulator calculation.
Note: The flow rate can be converted to a different unit.
The AFC Manager software supports the following parameters:
Orifice Plate and Meter Tube Measured Diameter
Orifice Plate and Meter Tube Measurement Temperature
Orifice Plate and Meter Tube, Coefficient of Thermal Expansion
DP Flow Threshold (kPa)
DP Alarm Threshold (kPa)
Page 34 of 316 ProSoft Technology, Inc.
February 25, 2011
MVI56-AFC ♦ ControlLogix Platform Meter Channel Functionality
Liquid and Gas Flow Computer User Manual
3.4 Gas Product Overview
The gas compressibility calculations are based on molar analysis concentrations
of up to 21 components, using the Detail Characterization Method of AGA8
(1992). The module automatically generates alarms if the sum of the molar
concentrations is not 100%
Configure the analysis settings using the AFC Manager (Meter Configuration /
Analysis Config) as follows. This window allows the selection of the
components(Component Selection Map) and analysis precision (Precision and
Stream Assignment – version 2.06.000 or higher). The sample ladder logic
assumes that all components are selected so check all components at the
Component Selection Map window.
Enter the gas analysis concentrations by clicking the Analysis button.You can
also update the concentrations through the backplane as will be later shown in
this User Manual.
The module records events every time a molar concentration value changes. For
applications that involve gas chromatograph devices, this feature might not be
desirable because it is expected that the values should frequently change. You
can disable this feature using AFC Manager (Meter Configuration / Control
Options / Treat Analysis as Process Input).
ProSoft Technology, Inc. Page 35 of 316
February 25, 2011
Meter Channel Functionality MVI56-AFC ♦ ControlLogix Platform
User Manual Liquid and Gas Flow Computer
3.5 Liquid Product Overview
The module supports applications involving crude or refined oil such as crude oil,
oil/water emulsion, propane, butane, NGLs, LPGs, gasoline, jet fuels and
lubricating oils.
When measuring liquids with density correction, density at flowing conditions is
required. This value may be provided directly as a process input, or the module
can calculate a density from the frequency provided by a densitometer device.
3.5.1 To use a densitometer
Follow the steps below to use a densitometer.
1 Configure it, entering all configuration parameters directly from the calibration
data sheet supplied by the densitometer manufacturer.
2 Supply the frequency output from the densitometer in Hz as a floating-point
value in the "Flowing density" process-input location over the backplane
(refer to the Backplane Communication section for your platform in the
MVI56-AFC manual to determine the correct location). The AFC then
calculates a flowing density value, which is then validated by the range check
mandated by the "Density" values of "Process Input Scaling" of the meter
configuration. The "Scaling" sub-selection is not used against the frequency
input, however; the frequency is always input as floating-point.
Note: If using the Densitometer feature, select the Density Process Input Scaling for 4 to 20mA
and enter the densitometer frequency as a floating-point value.
3.5.2 Module Configuration
3.5.3 Density Units
The liquid density units can be expressed as:
3
Density is in kg/m
Relative density 60ºF/60ºF
API gravity
3.5.4 Measuring Water Diluent
For liquid measurement applications, the optional automatic calculation of Net Oil
Volume and mass based on the Sediment and Water (S&W) percent input is
supported. Only provide the S&W percent value in the specified controller
register. The module puts the gross standard (or gross clean oil), net oil and
water accumulations in separate accumulators. Refer to Net Accumulator
Calculation (page 89).
Page 36 of 316 ProSoft Technology, Inc.
February 25, 2011
MVI56-AFC ♦ ControlLogix Platform Meter Channel Functionality
Liquid and Gas Flow Computer User Manual
3.6 General Features
3.6.1 Process Variable Interface
Process variables for each of the meter runs must be produced by the controller
for consumption by the AFC module. A versatile architecture for backplane
transfer of process variables and other data and signals allow you to easily
implement the data transfer. The sample ladder logic automatically transfers the
process variables to the module and reads the calculation results to the
processor.
3.6.2 Meter Scan Time
For good measurement, the process I/O must be sampled, and the flow
calculations completed quickly in order to avoid losing process information and
measurement accuracy. The process I/O scan time for the module is under one
second for all meter runs.
Note: This is time-dependent on design of the ladder logic implemented to support the two-way
data transfer between the AFC module and the controller. The meter calculation scan independent
of the process I/O scan may take longer.
3.6.3 Multiple Meter Accumulators
Each meter channel supports the following set of full 32-bit accumulators that
may be configured in binary or split decimal format with user-defined rollover
values:
Gross Volume
Gross Standard Volume (liquid only)
Net Volume
Mass
Water (liquid only)
Energy (gas only)
Access to the above accumulators is available directly from the Modbus Slave
communications ports.
3.6.4 Product Batching
Any or all of the available meter runs may be configured for field installation that
requires shipping and/or receiving product batches of predetermined size. The
configuration utility option of selecting resettable accumulators provides a simple
way to use the power of ladder logic to design product batching, monitoring, and
control tailored to suit specific field requirements.
The Meter Signals feature can be used to create an archive or reset an
accumulator after the batch is concluded. Refer to the Ladder Logic section for
your platform for more information on using this feature.
ProSoft Technology, Inc. Page 37 of 316
February 25, 2011
Meter Channel Functionality MVI56-AFC ♦ ControlLogix Platform
User Manual Liquid and Gas Flow Computer
3.6.5 Data Archiving
The module supports the archiving of data for each meter channel. Each time,
one record consisting of all the associated data is date and time stamped and
archived. This option allows for archiving each hour for 2 days (48 records per
meter run) and every day for 35 days (35 daily records per meter run) for each
meter channel. Each record consists of up to 40 process and other variables.
Archives are mapped to the local Modbus Table. Refer to Archives (page 91) for
more information about this topic.
3.6.6 Event Log Function
The module can log up to 1999 critical events in an Event Log File stored as a
set of easily accessible Modbus registers in non-volatile RAM. Changing critical
parameters, such as orifice plate size, Meter Base K factors, and Meter
Correction Factors, are time stamped and logged. Refer to Events for more
information about this topic.
3.6.7 Measurement Units
This option is provided for each meter channel to be configured with SI or US
units of measurement. Units for flow totalization (volumetric and mass) and flow
rate monitoring are configurable for each meter channel separately if the default
configuration is not applicable. Each meter channel may be configured to use
any of the standard units from liters/gallons to thousand cubic meters/barrels.
The flow rate period of each meter channel may be selected from flow rate per
second, per minute, per hour, or per day.
Page 38 of 316 ProSoft Technology, Inc.
February 25, 2011
MVI56-AFC ♦ ControlLogix Platform Meter Channel Functionality
Liquid and Gas Flow Computer User Manual
3.6.8 Process Input Scaling
The module allows you to either pre-scale the process inputs via ladder logic for
use in the measurement calculations, or provide unscaled values from the analog
input modules directly. In the second case, the scaling is done internally. You can
directly enter the zero-scale, the full-scale, and the default values for each of the
process variable inputs through the configuration window. Pre-scaled values may
be transferred as floating point or as scaled integer.
When selecting scaled integer, the integer values are scaled as follows:
Scaled Integer
Variable Format Example
Temperature Two decimal places implied A value of 1342 would be
equivalent to 13.42°C
Pressure No decimal places implied for SI A value of 200 would be
units (kPa) and one decimal equivalent to 200kPag
place implied for U.S. units (psi).
Differential Pressure Two decimal places implied for A value of 35142 would be
inches of H2O and 3 places for equivalent to 35.142kPa
kPa
Density (kg/m3) One implied decimal place A value of 5137 would be
equivalent to 513.7 kg/m3
Density (Relative Density) Four implied decimal places A value of 10023 would be
equivalent to 1.0023 60F/60F.
Density (API) Two implied decimal places A value of 8045 would be
equivalent to 80.45 °API.
When selecting the 4 to 20mA process input scaling, the module uses the
following ranges:
4 to 20mA
Processor Module 0% 100%
SLC MVI46-AFC 3277 16384
ControlLogix MVI56-AFC 13107 65535
CompactLogix MVI69-AFC 6241 31206
PLC MVI71-AFC 819 4095
Quantum PTQ-AFC 4000 20000
The module uses the configured values for zero and full scale to interpret the
process input scaling.
In the Meter Monitor window, the raw values as transferred from the processor
are shown at the "Last Raw" column and the converted values are shown at the
"Scaled Avg" column.
ProSoft Technology, Inc. Page 39 of 316
February 25, 2011
Meter Channel Functionality MVI56-AFC ♦ ControlLogix Platform
User Manual Liquid and Gas Flow Computer
Page 40 of 316 ProSoft Technology, Inc.
February 25, 2011
MVI56-AFC ♦ ControlLogix Platform Meter Proving
Liquid and Gas Flow Computer User Manual
4 Meter Proving
In This Chapter
Prover Configuration ............................................................................. 42
Setting up the AFC module for Meter Proving ....................................... 51
Meter Proving Reports........................................................................... 63
Protected Meter Proving Data in the AFC's Input Register Bank .......... 64
As meters continue to be used over time, the meter’s measurement accuracy
deteriorates. Many things can cause the flow sensor bearings to wear down
beyond specified limits so that meters are measuring lower volume levels
causing producers to pump more oil than the consumer is buying. Meter Provers
have a “Known Traceable Volume” which allows using actual flowing and
operating conditions to establish a meter correction factor to restore
measurement accuracy.
There are 4 types of provers. This chapter will give a basic overview for each
type, its options, and configuration.
The Unidirectional Pipe Prover
The Bidirectional Pipe Prover
The Compact Prover
The Master Meter
ProSoft Technology, Inc. Page 41 of 316
February 25, 2011
Meter Proving MVI56-AFC ♦ ControlLogix Platform
User Manual Liquid and Gas Flow Computer
4.1 Prover Configuration
Prover type is a parameter that identifies the basic type of the prover. It's values
are:
NO PROVER CONFIGURED
UNIDIRECTIONAL PIPE PROVER (You may also choose this selection for an
atmospheric tank prover.)
BIDIRECTIONAL PIPE PROVER
COMPACT (SHORT, SMALL VOLUME) PROVER
MASTER METER
4.1.1 Prover Type
Prover characteristics and configurations will vary based on the type of prover
and options you select. The following topics describe each type of prover.
Page 42 of 316 ProSoft Technology, Inc.
February 25, 2011
MVI56-AFC ♦ ControlLogix Platform Meter Proving
Liquid and Gas Flow Computer User Manual
Unidirectional Pipe Prover
This is a long pipe, with a ball or piston that fills the pipe and moves with the
fluid flow. At each end of the pipe is a switch that is tripped when the ball
passes it. A proving run counts the pulses occurring between the switch trips.
A run is prepared by positioning the ball in a cul-de-sac upstream of the first
switch, ready to be injected into the stream. At the end of the run, the ball is
extracted from the stream and returned via another path to the upstream end.
In order to calculate a meter factor with sufficient precision, the prover volume
must be large enough to count sufficient pulses. Therefore, unidirectional
provers can be quite large.
ProSoft Technology, Inc. Page 43 of 316
February 25, 2011
Meter Proving MVI56-AFC ♦ ControlLogix Platform
User Manual Liquid and Gas Flow Computer
Bidirectional Pipe Prover
This is similar to a unidirectional prover, except that use is made of the deadhead
transfer of the ball back to its starting point. Instead of returning the ball via a
separate path, valves are swung to reverse the direction of flow in the prover and
the ball is returned along its original path to trip the switches a second time in the
opposite order. The first pass of the ball is called the forward leg and the second
is called the backward or return leg. The pulse count for the run is then the sum
of the counts for the two legs. Because the run's pulse count arises from two
passes between the switches, a bidirectional prover need be only half the volume
of its unidirectional counterpart and can be correspondingly smaller.
Page 44 of 316 ProSoft Technology, Inc.
February 25, 2011
MVI56-AFC ♦ ControlLogix Platform Meter Proving
Liquid and Gas Flow Computer User Manual
Compact (short, small volume) Prover
A compact prover, or small volume prover (SVP), has a short barrel or tube with
a piston that travels the length of the tube. The piston has a valve that is opened
to allow it to return to its starting point without stopping the flow in the tube. Most
SVPs do not mount the switches to be tripped inside the tube. They mount the
switches externally on a bar that moves with the piston outside the tube and the
switches trip when they move past a fixed point. Each forth and back passage is
called a pass. SVPs can be much less expensive than LVPs, so they are often
preferred. Due to their small size they can collect at most a few hundred pulses
during a pass. The number of pulses in a single pass is a number too small for
calculating a meter factor with sufficient precision. The technique of double
chronometry is then used to determine a fractional pulse count of sufficient
precision. Even though a single pass in a SVP with double chronometry can yield
a pulse count similar in precision to that from a single run of a LVP, it is often the
practice to accumulate several passes into a single run so that the pulses
totalized for all passes of the run yield a number large enough for calculating the
required meter factor with sufficiently high precision.
ProSoft Technology, Inc. Page 45 of 316
February 25, 2011
Meter Proving MVI56-AFC ♦ ControlLogix Platform
User Manual Liquid and Gas Flow Computer
Master Meter
This proving technique proves a meter by comparing its behavior to that of
another master meter whose behavior is deemed to be accurate. A master meter
itself must be proved to a high precision by using a conventional prover.
4.1.2 Prover Options
There are several options affecting the handling and representation of data, as
well as affecting the relevance and availability of some configuration items. Not
all options are available for all prover types. If an option does not apply to a
particular prover type, it cannot be selected. For a description of each option
listed below see the corresponding Modbus dictionary address in parenthesis
below.
Dual transmitters, temperature (65011.0)
Dual transmitters, pressure (65011.1)
Input meter density (65011.2)
Return leg pulse count is round –trip count (65011.4)
Prover is double-walled (65011.5)
External switch bar (65011.6)
Calculation method: Average Meter Factor (else Average Data) (65011.8)
Page 46 of 316 ProSoft Technology, Inc.
February 25, 2011
MVI56-AFC ♦ ControlLogix Platform Meter Proving
Liquid and Gas Flow Computer User Manual
4.1.3 Run Counts
Runs per prove (65012)
The total number of completed runs that constitute a single prove. This value
must be at least 2 and must not exceed 8. If Maximum attempted runs before
abort (register 65014) is non-zero, this value must not exceed that value.
Runs per prove, selected
The total number of completed runs to be selected for contribution to the prove
calculations. This value must be at least 2 and not exceed Runs per prove,
(register 65012). This value is automatically updated when you edit the Runs per
prove field.
Maximum attempted runs before abort (65014)
The total number of runs to be attempted before abandoning a prove as
incomplete, which permits an automatic proving sequence to automatically
terminate itself under exceptionally variable conditions. If this value is zero, no
limit is imposed. Otherwise, the value must be at least as large as Runs per
prove, (register 65012) and must not exceed 65535.
4.1.4 Run Input Setup
Minimum pulses per run (thousands) (65016)
The minimum number of pulses required for a run to be considered for
contribution to the prove, represented in thousands. This value must lie between
10 (representing 10,000 pulses) and 1000 (representing 1,000,000 pulses). Runs
counting 10,000 pulses or more have sufficient precision to enable calculation of
4-digit meter factors. For all prover types except compact SVPs, the AFC rejects
any LVP run that does not meet this condition. Since SVPs can deliver fractional
pulse counts that provide sufficient precision with only a small number of pulses,
the AFC does not impose this limitation on prover calculation using SVPs.
Maximum seconds per run (65017)
This parameter is a timeout for the duration of a run. A timer is started when the
run is started, and if the timer value equals or exceeds this value before the run
is completed, then the AFC automatically cancels the run. This allows an
automatic prove to recover from conditions that put the AFC and the proving
hardware out of step, such as a missed switch signal. This value must lie
between 0 and 10000, where zero means that no timeout is imposed.
ProSoft Technology, Inc. Page 47 of 316
February 25, 2011
Meter Proving MVI56-AFC ♦ ControlLogix Platform
User Manual Liquid and Gas Flow Computer
Input format: line meter pulse count (65020)
This parameter is a code that specifies the format in which pulse counts for the
line meter are delivered to the AFC at the ends of runs or passes. These values
are:
Value Format Description
0 None No pulse counts are delivered. Used only when no prover is configured
1 32-bit Pulse counts are delivered as 32-bit (double) integers
2 Split-double Pulse counts are delivered as split-double values, in which the actual
value is (MSW * 10,000 + LSW)
3 Floating point Pulse counts are delivered as IEEE 32-bit floating point values
When a prover is configured, the default setting is 1 (32-bit), except for compact
provers, for which it is 3 (floating point).
Input format: master meter pulse count (65021)
This parameter is a code that specifies the format in which pulse counts for the
master meter are delivered to the AFC at the ends of runs or passes. These
values are:
Value Format Description
0 None No pulse counts are delivered. Used when the prover is not a
master meter.
1 32-bit Pulse counts are delivered as 32-bit (double) integers.
2 Split-double Pulse counts are delivered as split-double values, in which the
actual value is (MSW * 10,000 + LSW).
3 Floating point Pulse counts are delivered as IEEE 32-bit floating point values.
When a master meter is configured, the default setting is 1 (32-bit). This
parameter is meaningful only when using master meter provers.
Page 48 of 316 ProSoft Technology, Inc.
February 25, 2011
MVI56-AFC ♦ ControlLogix Platform Meter Proving
Liquid and Gas Flow Computer User Manual
4.1.5 Prover Characteristics
Prover Characteristics will vary based on the type of prover and options you
select. The following topics describe each field and its operating range.
Prover size units (65018.L)
This parameter sets the units in which the prover's base volume is represented.
This parameter is not meaningful for master meter provers.
Meter factor precision (65028+)
This parameter is a number between 0.00000001 and 0.0001. The default setting
is 0.0001
Pulse interpolation ratio (65030+)
Meter-proving pulse counts delivered to the AFC may be fractional, such as
when double chronometry is used with a SVP. This value is the number of
delivered counts that constitute a single actual pulse, so that the actual pulse
count is determined by dividing the delivered count by this. The default value is
1000.0 for compact provers and 1.0 for other types. This parameter is meaningful
only for non-master meter provers.
Flow tube linear coefficient of thermal expansion (65032+)
Holds the coefficient of thermal expansion of the prover barrel material,
meaningful only for non-master-meter provers. Here are some typical materials
and their expansion coefficients.
Stainless steel 304 or 316 9.3e-6/°F 16.7e-6/°C
Monel 7.9e-6/°F 14.3e-6/°C
Carbon steel 6.2e-6/°F 11.2e-6/°C
Invar .8e-6/°F 1.4e-6/°C
The default value is that of carbon steel, 6.2e-6/°F 11.2e-6/°C.
Switch bar linear coefficient of thermal expansion (65034+)
Holds the coefficient of thermal expansion of the external switch bar material,
meaningful only for non-master-meter provers with option External switch bar
(register 65011 bit 6) set. Here are some typical materials and their expansion
coefficients.
Stainless steel 304 or 316 9.3e-6/°F 16.7e-6/°C
Monel 7.9e-6/°F 14.3e-6/°C
Carbon steel 6.2e-6/°F 11.2e-6/°C
Invar .8e-6/°F 1.4e-6/°C
The default value is that of invar .8e-6/°F 1.4e-6/°C.
ProSoft Technology, Inc. Page 49 of 316
February 25, 2011
Meter Proving MVI56-AFC ♦ ControlLogix Platform
User Manual Liquid and Gas Flow Computer
Base prover volume (65036+)
Holds the base volume of the prover barrel as determined by the water-draw
method, in the units specified by Prover size units (register 65018.L). This
parameter is meaningful only for non-master meter provers.
The accepted standards mandate that the base volume of a bidirectional prover
be that registered by a round trip of the displacer.
Flow tube inside diameter (mm) (65038+)
This parameter is the measured inside diameter of the prover barrel at standard
(base) conditions and is meaningful only for non-master meter provers with the
option Prover is double-walled (register 65011 bit 5) clear.
Flow tube wall thickness (mm) (65040+)
This parameter is the measured thickness of the prover barrel wall, and is
meaningful only for non-master meter provers with the option Prover is double-
walled (register 65011 bit 5) clear.
Flow tube modulus of elasticity (65042+)
This parameter is the prover barrel material modulus of elasticity, and is
meaningful only for non-master meter provers with the option Prover is double-
walled (register 65011 bit 5) clear. The default value is that of carbon steel,
206.8e+6 kPa or 30.00e+6 psi.
Page 50 of 316 ProSoft Technology, Inc.
February 25, 2011
MVI56-AFC ♦ ControlLogix Platform Meter Proving
Liquid and Gas Flow Computer User Manual
4.2 Setting up the AFC module for Meter Proving
First, configure the parameters in the Prover Configuration dialog box. A
Bidirectional Pipe Prover is shown in this example.
Note: Changing prover type will reset all prover configuration
Meter Proving dialog box
This window is used to connect to the module to manage the prove and/or
monitor prove status and results from the Modbus database.
ProSoft Technology, Inc. Page 51 of 316
February 25, 2011
Meter Proving MVI56-AFC ♦ ControlLogix Platform
User Manual Liquid and Gas Flow Computer
This is a typical configuration for a meter proving setup. Your application may
vary from the example shown.
Page 52 of 316 ProSoft Technology, Inc.
February 25, 2011
MVI56-AFC ♦ ControlLogix Platform Meter Proving
Liquid and Gas Flow Computer User Manual
4.2.1 Initial Requirements
In its current version, the AFC supports proving of only liquid products, measured
with linear devices that use pulse counts as the primary input variable, where
each pulse represents a specific liquid volume.
In the Meter Configuration dialog box above, Meter 1 is used in this example as
the meter selected to be proved. It can be proved using any one of the four
provers that the AFC supports. These provers are described in the Prover
Configuration section. There is an Identification button which opens an editable
options window, shown below. Text entered here appears on the proving report.
ProSoft Technology, Inc. Page 53 of 316
February 25, 2011
Meter Proving MVI56-AFC ♦ ControlLogix Platform
User Manual Liquid and Gas Flow Computer
4.2.2 Meter Proving Alarms
These alarms are transient and any one might exist only for a single scan, so
they might be missed when viewing this register directly. However, alarms are
also accumulated into the results database, so alarms that have occurred during
any run may be viewed by inspecting that database.
To Check for Alarms
1 Activate Meter Monitor dialog box
2 Select METER to be proved
3 Click on the [READ] button
Note: Verify that the meter is not generating any alarms. Meter proving cannot proceed while any
alarm is displayed.
This is accomplished by providing PROCESS PARAMETER values that are within
the range of the Process Input Scaling Dialog box.
There are two sources of alarms:
1 From the meter, which occur whether or not a prove is in progress. These are
illustrated above.
2 From the prove, and there are 2 kinds:
a) Variation Limit Alarms
b) Prove Calculation Alarms
Note: Any alarm will always make a run not able to be selected.
Page 54 of 316 ProSoft Technology, Inc.
February 25, 2011
MVI56-AFC ♦ ControlLogix Platform Meter Proving
Liquid and Gas Flow Computer User Manual
Variation Limit Alarms
These alarms are due to variation outside the configured limits:
Bit/Byte Description Modbus Dictionary Address
01 Prover inlet temperature 65050
02 Prover outlet temperature 65052
03 Prover inlet-outlet temperature 65054
04 Prover temperature 65056
05 Prover-meter temperature 65058
06 Switch bar temperature 65060
07 Meter pressure 65062
08 Prover inlet pressure 65064
09 Prover outlet pressure 65066
10 Prover inlet-outlet pressure 65068
11 Prover pressure 65070
12 Prover-meter pressure 65072
13 Meter density 65074
14 Prover density 65076
15 Prover-meter density 65078
16 Water content 65080
17 Meter flow rate 65082
18 Prover flow rate 65084
19 Pulses over runs 65086
20 Pulses over passes 65088
21 Not enough pulses in run N/A
22-31 [Reserved] N/A
ProSoft Technology, Inc. Page 55 of 316
February 25, 2011
Meter Proving MVI56-AFC ♦ ControlLogix Platform
User Manual Liquid and Gas Flow Computer
Prove Calculation Alarms
These alarms arise from prove calculations (e.g. outside API limits):
Bit/Byte Description
00 [Reserved]
01 CTS prover
02 CPS prover
03 [Reserved]
04 High water
05 CTW
06 CPW
07 Density correction
08 CTL prover
09 CPL prover
10 CSW prover
11 Vapor pressure prover
12 CTL meter
13 CPL meter
14 CSW meter
15 Vapor pressure meter
16 Repeatability
17 Change in factor
18-22 [Reserved]
23 Divide by zero
24-31 [Reserved]
Page 56 of 316 ProSoft Technology, Inc.
February 25, 2011
MVI56-AFC ♦ ControlLogix Platform Meter Proving
Liquid and Gas Flow Computer User Manual
4.2.3 Prover Operation (How to do a Prove)
You must first configure a prover, and configure the channel of a Configurable
Flow Meter (CFM) or High Speed Counter (HSC) module for proving.
Note: CFM modules are available for the 1756 platform from Rockwell Automation, and the
Quantum platform via Spectrum. Any HSC card will work for the other modules, but if you use an
HSC, you will need extra ladder logic in the PLC to implement proving.
Once the parameters for the proving session have been configured, (pipe
diameter, water-draw volume, wall thickness, tolerances and limits on the
variation of temperature, flow rate, and other process variables), and the prove
setup has been completed, the entire proving session can be completely
automated within the PLC ladder logic.
Steps for proving a meter
a Enter the prover parameters and variation limits (configuration)
b Enter the number of the meter to be proved (setup)
c Set the enable prove signal bit. This function verifies that the selected
meter is provable (a liquid pulse meter), and clears the proving results for
a new proving session.
d Enable the counter card channel for proving, and launch the ball. When
the first switch is tripped, set the run start signal bit. During the run,
continuously copy the prover temperature, pressure, density, etc, to the
AFC, so that it may monitor their variation and accumulate them for final
averaging. For the same purpose, the AFC module itself retrieves meter
process variables directly from the meter input from the PLC without PLC
intervention.
e When the second switch is tripped, copy the final pulse count from the
counter card channel to the proper location and set the run stop signal bit
This function computes results for the completed run (averages of
process variables, variation limit alarms, etc.), and also computes results
for the entire prove over all completed runs (averages of run averages,
variation limit alarms, API calculations and calculation alarms, final meter
factor and change in meter factor, and number of completed runs). Upon
a run start or accept prove signal, any bad runs are deleted from the
prove before continuing with the remainder of the signaled function.
f When a sufficient number of runs have been completed , set either the
accept prove or the reject prove signal, which function marks the data in
the prover results accordingly.
ProSoft Technology, Inc. Page 57 of 316
February 25, 2011
Meter Proving MVI56-AFC ♦ ControlLogix Platform
User Manual Liquid and Gas Flow Computer
Missed Switch
It is possible that the tripping of the second switch to end a run is not seen by
the PLC (due to a broken wire or poorly lubricated switch), leaving the AFC and
the physical prover in inconsistent states. You may recover from this condition
with the Run Cancel signal, which clears any active run and resets the AFC to be
ready to start a new run. Data from any bad run will also be deleted by the Run
Cancel.
Proving Controls
These bits supply parameter information to the Enable prove and Accept prove
signals (register 65308 bits 1 and 2 respectively). Control bits 0 through 7
parameterize the Enable and bits 8 through 15 parameterize the Accept. Controls
are latched into the results database upon receipt of a signal. Changes thereafter
have no effect on the state of these control bits.
Proving Signals
A prover signal instructs the AFC to immediately perform a particular function
once. A signal bit is latched by the process issuing the signal (for example, the
PLC) and is unlatched by the AFC when the function has been performed. Prover
signals are discharged upon the next proving scan, before which several Modbus
transactions may be completed. Modbus transactions to read the status of these
signal bits may, therefore, show uncleared bits for functions that have already
been scheduled but not discharged yet.
Prover Sequencing
This parameter reports the state of the proving hardware, making it available to
the prove-management software for display of prove status and possible control
of the prove. The prove-management feature of AFC Manager uses it only for
display. This value usually comes from the proving hardware integrated into the
PLC platform, therefore it is normally supplied by the PLC.
Page 58 of 316 ProSoft Technology, Inc.
February 25, 2011
MVI56-AFC ♦ ControlLogix Platform Meter Proving
Liquid and Gas Flow Computer User Manual
Prover Phase
These bits report the state of the run as known by the proving hardware. These
values are chosen specifically for compatibility with several kinds of proving
hardware, so that the work necessary for the PLC to translate hardware register
values into these values required by the AFC is minimized and in many cases
can be reduced to a simple mask-and-copy. There are 8 values ranging from 0-
7. These values are:
Value Name Description
0 Prover not selected (not ready) This is the normal value when no proving run is in
progress.
1 Prover active, not yet counting The counter card has been initialized for a proving
run, but the ball or piston has not yet passed the
first switch. Counting of the pulses for the run has
not yet begun.
2 Prover active, past first switch and The ball or piston has passed the first switch but not
counting
yet passed the second switch, and the run counter
is counting pulses. For bidirectional provers, this is
the forward leg.
3 Prover active, past second switch This state is for bidirectional provers only. The ball
or piston has passed the second switch of the
forward leg, the run counter has been stopped, and
the intermediate count for the forward leg is
available. During this state
the proving hardware should be swinging valves to
reverse the stream's direction of flow through the
prover, preparing it for the return leg.
4 Prover active, past first switch return This state is for bidirectional provers only. The ball
leg or piston has passed the first switch on the return
leg but not yet passed the second switch, and the
run counter is counting pulses.
5 Run Complete The ball or piston has passed the second switch
(for bidirectional provers, the second switch of the
return leg), the run counter has been stopped, and
the count for the run is available. For a bidirectional
prover, this count may be either the count for only
the return leg or the count for the entire run; use
prover option "Return leg pulse count is round-trip
count" (register 65011 bit 4) to specify which.
6 Prover not selected (not ready) Some kinds of proving hardware report this value
for a counting mode unrelated to proving. The AFC
treats this value the same as value 0.
7 Prover not selected (not ready) Some kinds of proving hardware report this value
for a counting mode unrelated to proving. The AFC
treats this value the same as value 0.
Prover Position: Ready for Launch
The prover's ball or piston is ready for launching into the stream. For a
bidirectional prover, this is the launch of the forward leg.
ProSoft Technology, Inc. Page 59 of 316
February 25, 2011
Meter Proving MVI56-AFC ♦ ControlLogix Platform
User Manual Liquid and Gas Flow Computer
Prover Position: Ready for Return
For bidirectional provers only, the prover's ball or piston is ready for launching
into the stream for the return leg.
Prover Position: Valve Sealed Behind Ball
The prover's ball or piston has been launched into the stream and the sealing
valve has been closed behind it. For a bidirectional prover, this is the start of the
forward leg.
Prover Position: Valve Sealed Behind Ball, Return Leg
For bidirectional provers only, the prover's ball or piston has been launched into
the stream for the return leg and the sealing valve has been closed behind it.
Prover Temperature
Absolute
This value is the process input temperature of the prover (traditional or master
meter) in units relative to absolute zero, and is required for some calculations.
This value is meaningful only while a prove is active.
Conventional
This value is the process input temperature of the prover (traditional or master
meter) in conventional units. For a traditional prover with dual transmitters, this is
the average of the two inputs. This value is meaningful only while a prove is
active.
Prover Pressure
Absolute
This value is the process input pressure of the prover (traditional or master
meter) in absolute units. This value is calculated as (gauge pressure ) +
(barometric pressure). This value is meaningful only while a prove is active.
Gauge
This value is the process input pressure of the prover (traditional or master
meter) in gauge units. For a traditional prover with dual transmitters, this is the
average of the two inputs. This value is meaningful only while a prove is active.
Page 60 of 316 ProSoft Technology, Inc.
February 25, 2011
MVI56-AFC ♦ ControlLogix Platform Meter Proving
Liquid and Gas Flow Computer User Manual
Prove-enable Error Code
This code reports the result of the most recent attempt to enable a prove. If the
code is zero, the prove was successfully enabled; a non-zero code reports the
reason for failure. The values are:
Value Name Description
0 The new prove has been The new prove has been enabled
enabled
21 Requested meter number The Requested meter number (register 65300) is out
of range, or, for a master meter prover, is the same
as that of the master meter (an attempt to self-prove
the master meter)
22 Line meter not liquid pulse At the present time, the meter to be proved may only
be a liquid pulse meter.
23 Incompatible measurement At the present time, the configuration of both the
standard prover and the line meter to be proved must specify
the same system of measurement units (US, SI) and
the same liquid density units selection (kg/m3, Rd/60,
°API).
24 Unimplemented product group Because of the nature of the proving calculations at
the present time, not all product groups are provable.
Meters configured for these product groups are
provable:
Liquid (crude oils and JP4)
Liquid (refined products: gasolines, jet fuels, fuel
oils, except JP4)
Liquid (NGLs and LPGs)
Liquid (lubricating oils)
Liquid (special applications)
Meters configured for these product groups are not
provable:
Gas
Liquid (oil-water emulsion of crudes)
Liquid (oil-water emulsion of NGLs)
25 Unimplemented measured At the present time, only pulse meters whose pulse
quantity train represents gross volume can be proved.
28 Line meter in calibration The meter to be proved has at least one process
input in calibration mode. Ensure that all process
inputs are live before attempting to prove the meter.
29 Line meter not enabled The meter to be proved is not enabled.
32 Master meter not liquid pulse At the present time, a master meter prover must be a
liquid pulse meter.
ProSoft Technology, Inc. Page 61 of 316
February 25, 2011
Meter Proving MVI56-AFC ♦ ControlLogix Platform
User Manual Liquid and Gas Flow Computer
33 Master meter incompatible For a master meter prover, both the line meter and
configuration the master meter must be compatibly configured,
including identical settings of:
System of measurement units (US, SI)
Liquid density units (kg/m3, Rd/60, °API)
Product group
Measured quantity (gross volume pulses)
Reference conditions (base temperature and
pressure)
API calculation options (selection of density,
temperature, and pressure corrections)
For product group 8, Special applications, the
coefficient of thermal expansion Alpha
38 Master meter in calibration The master meter has at least one process input in
calibration mode. Ensure that all process inputs are
live before attempting to use the master meter for
proving.
39 Master meter not enabled The master meter is not enabled.
51 Invalid prover parameter For a traditional (non-master-meter) prover, the base
prover volume (register 65036) must be greater than
zero, and, if the prover is single-walled, the inside
diameter, wall thickness, and modulus of elasticity
(registers 65038, 65040, and 65042) must all be
greater than zero.
52 Invalid prover controls Some undefined bits in the at-enable controls
(register 65306 bits 0 through 7) have been set.
Page 62 of 316 ProSoft Technology, Inc.
February 25, 2011
MVI56-AFC ♦ ControlLogix Platform Meter Proving
Liquid and Gas Flow Computer User Manual
4.3 Meter Proving Reports
Clicking on the REPORT button generates a report with such information as:
Manufacturer
Model Number
Serial Number
Material Type
Prover Tag
Results of the prove will appear in this report, along with the static data
entered in the text window during setup. For more information, see Initial
Requirements (page 53).
The Meter Proving window above shows the system during a prove using a
Master Meter. Notice the differences in the example of the information that is
available before and after connecting to the module.
ProSoft Technology, Inc. Page 63 of 316
February 25, 2011
Meter Proving MVI56-AFC ♦ ControlLogix Platform
User Manual Liquid and Gas Flow Computer
4.4 Protected Meter Proving Data in the AFC's Input Register Bank
The data concerned with Meter Proving is maintained in the Input Register Bank,
(Modbus 3xxxxx read-only Input Register Addresses), protected from change
from outside. There are two areas:
a Latest Prove Results (3x63400 to 3x63709)
b Meter Previous Prove Summary (3x61600 to 3x62399, 50 registers per
meter)
These two areas are described in better detail in the following two topics.
4.4.1 Latest Prove Results
This area contains complete details of the latest prove that has been enabled,
including
Prove setup
Prover and proved-meter configuration summary
Prove state
Prove-level calculations
Run-level input and calculations for each run of the prove
This area supplies almost all the information presented on the proving report (the
remaining info comes from the proved meter’s Previous Prove Summary; see
next). The contents of this area persist until a new prove is enabled, so a proving
report may be regenerated at any time after the prove has been completed and
before the next one is started. There is only one such area for all meters on the
AFC module; therefore enabling a new prove for any meter resets the Prove
Results from the last completed prove, regardless of which meters were involved.
Page 64 of 316 ProSoft Technology, Inc.
February 25, 2011
MVI56-AFC ♦ ControlLogix Platform Meter Proving
Liquid and Gas Flow Computer User Manual
The Latest Prove Results is a block of 1310 registers, starting at input register
62400 and proceeding through register 63709. The table below explains these
sub-areas.
Name Module Memory Description
Address
Prove Status 62400 to 62409 Occupies 10 registers
Prove Setup 62410 to 62553 Occupies 140 registers and protects meter
configuration and prove setup information
for use by proving calculations and report
generation; this information remains
unchanged from the moment of enable,
regardless of how the original source
information might be altered during or after
the prove
Prove Acceptance 62554 to 62575 Occupies 22 registers and records
timestamps associated with the prove,
accumulator totalizer values, and details of
the disposition of the new meter factor upon
acceptance of the prove.
Prover Configuration 62576 to 62655 Occupies 80 registers and has the same
purpose as Prove Setup, to protect the
prover configuration against subsequent
changes so that proving can proceed under
reliably constant parameters, and so that the
proving report can be generated and
regenerated according to the original
conditions of the prove.
Prove Only Calculations 62656 to 62665 Occupies 10 registers and contains a few
calculated values that are applicable only for
the prove as a whole.
Reading and Calculations for 62666 to 62781 Occupies 116 registers and the "readings"
Prove part contains the averages of the
corresponding readings for all runs of the
prove. The "calculations" part contains
calculations performed upon the prove-level
readings if calculation method "average
data" was chosen.
Reading and Calculations for 62782 to 63709 Occupies 166 registers for each of up to 8
Runs runs of the prove. The layout of each block
of 116 registers is identical to that of the
Readings and Calculations for Prove block.
The "readings" part contains the weighted
averages or snapshots of all process input
and counter card input for the duration of the
run. The "calculations" part contains
calculations performed upon the run-level
readings if calculation method "average
meter factor" was chosen.
ProSoft Technology, Inc. Page 65 of 316
February 25, 2011
Meter Proving MVI56-AFC ♦ ControlLogix Platform
User Manual Liquid and Gas Flow Computer
The Latest Prove Results area has a fixed layout so that any point can always be
found at the same location regardless of setup, and with a collection of points
intended to be sufficient for a variety of setups. Consequently, many points will
be irrelevant for a given combination of prover configuration, meter configuration,
and prove setup. Those irrelevant points will have zero values in the Results area
and can be ignored. AFC Manager’s Meter Proving window does not show
irrelevant points.
Page 66 of 316 ProSoft Technology, Inc.
February 25, 2011
MVI56-AFC ♦ ControlLogix Platform Meter Proving
Liquid and Gas Flow Computer User Manual
4.4.2 Meter Previous Prove Summary
This area contains summary data for the previous prove of each of the AFC’s
meter runs. Each time a new prove is enabled and before the Prove Results
area is reset, summary prove information for the meter previously proved (if any)
is copied to the meter’s Previous Prove Summary block, overwriting the old
information. This area supplies a small amount of the information presented in
the proving report.
The Previous Prove Summary block for each meter occupies 50 registers. Meter
#1’s block begins at input register 61600, so that Meter #2’s block is at 61650,
and so on; registers 61600 to 62399 are allocated to the Previous Prove
Summary blocks for up to 16 meter runs.
ProSoft Technology, Inc. Page 67 of 316
February 25, 2011
Meter Proving MVI56-AFC ♦ ControlLogix Platform
User Manual Liquid and Gas Flow Computer
Page 68 of 316 ProSoft Technology, Inc.
February 25, 2011
MVI56-AFC ♦ ControlLogix Platform Modbus Database
Liquid and Gas Flow Computer User Manual
5 Modbus Database
In This Chapter
AFC Modbus Address Space ................................................................ 70
Primary Slave ........................................................................................ 71
Virtual Slave .......................................................................................... 74
The module supports two individual Modbus slaves (Primary and Virtual) to
optimize the polling of data from the remote SCADA system, or from the
processor (through the backplane). Refer to the Modbus Dictionary dialog box in
AFC Manager for information about Modbus addressing.
ProSoft Technology, Inc. Page 69 of 316
February 25, 2011
Modbus Database MVI56-AFC ♦ ControlLogix Platform
User Manual Liquid and Gas Flow Computer
5.1 AFC Modbus Address Space
Addressable Modbus registers are divided into four banks as shown in the
following table.
MODBUS Address Space Allocation: Total Modbus Registers: 131,072
Primary Slave Banks Virtual Slave Banks
(131072 registers) (20,000 registers)
Holding Registers Input Registers Holding Registers Input Registers
From: 0 From: 0 From: 0 From: 0
To: 65535 To: 65535 To: 9999 To: 9999
The first 100 registers of the virtual slave (registers 0 through 99) are predefined
to map to the first 100 registers of the primary slave. This mapping cannot be
changed. Also, the Virtual Slave Input Registers can be accessed as Virtual
Slave Holding Registers by adding 10000 to the Modbus register address; for
example, Input Register 2386 is the same as Holding Register 12386.
5.1.1 Accessing the Data
The AFC Manager provides an easy way to read and write data from both slaves
through the Modbus Master Interface.
Page 70 of 316 ProSoft Technology, Inc.
February 25, 2011
MVI56-AFC ♦ ControlLogix Platform Modbus Database
Liquid and Gas Flow Computer User Manual
5.2 Primary Slave
The Primary Slave contains the main AFC database that consists of 131,072
Modbus registers. The Site and Meter configuration, as well as all live process
data and ongoing calculations are kept in the Primary Slave address space. This
address space is divided equally between the Input Register Bank (65,536
registers) and the Holding Register Bank (65,536).
The register addressing is shown in the Modbus Dictionary dialog box in AFC
Manager.
5.2.1 Modbus Address References
In these documents (the AFC Manager User’s Guide and the User’s Guide for
your platform) you will occasionally see Modbus address references like
Ph00018 or Mh00162. The first two characters of such references indicate how
to convert the following number into an absolute Modbus address in the module.
This table shows the possible values for the first identification character:
Address Translation ID Description
P Absolute Modbus address, Primary Slave
M Meter-relative Modbus address, Primary Slave
V Absolute Modbus address, Virtual Slave
This table shows the possible values for the second identification character:
Register Bank ID Description
h Holding register
i Input register
5.2.2 Modbus Address Examples
Ph02000 = holding register located at address 2000 in the primary slave
Pi02000 = input register located at address 2000 in the primary slave
Mh00100 = Meter-relative holding register located at offset 100 in the block of the
primary slave that contains the data for the meter
ProSoft Technology, Inc. Page 71 of 316
February 25, 2011
Modbus Database MVI56-AFC ♦ ControlLogix Platform
User Manual Liquid and Gas Flow Computer
5.2.3 Meter-relative Data
Meter-relative data starts at absolute holding register address 8000 and occupies
2000 words of data for each meter channel.
The meter-relative addresses are offsets within each meter data area. The
correct absolute address is calculated by the following formula (assumes meters
are numbered starting with 1):
(absolute address) = (2000 * (meter number-1)) + 8000 + (meter relative
address)
In the Modbus Dictionary dialog box, addresses listed for the selected meter are
absolute addresses, so you should subtract the appropriate multiple of 8000 to
calculate the meter-relative address.
Page 72 of 316 ProSoft Technology, Inc.
February 25, 2011
MVI56-AFC ♦ ControlLogix Platform Modbus Database
Liquid and Gas Flow Computer User Manual
Example: Find the orifice diameter address for the first 5 meter channels.
The meter 1 orifice diameter registers are located at the holding register address
8162 and 8163 as follows:
8160 8161 Float Parameter: orifice plate: measurement temperature
8162 8163 Float Parameter: orifice plate: measured diameter
8164 8165 Float Parameter: orifice plate: coef of thermal expansion
8166 8167 Float Parameter: meter tube: measurement temperature
8168 8169 Float Parameter: meter tube: measured diameter
8170 8171 Float Parameter: meter tube: coef of thermal expansion
8172 8173 Float Parameter: differential pressure flow threshold
The meter-relative addresses are Mh00162 and Mh00163
The addresses for meters 1 to 5 are listed on the following table.
Meter Registers
1 8162 and 8163
2 10162 and 10163
3 12162 and 12163
4 14162 and 14163
5 16162 and 16163
5.2.4 Scratchpad
The Primary Modbus Slave contains a scratchpad area that can be used to store
any data required by each application. This area is "empty" by default and
contains 6000 words of data starting at holding register 2000 in the Primary
Modbus Slave.
ProSoft Technology, Inc. Page 73 of 316
February 25, 2011
Modbus Database MVI56-AFC ♦ ControlLogix Platform
User Manual Liquid and Gas Flow Computer
5.3 Virtual Slave
The module also provides a Virtual Address Space of 20,000 Modbus registers.
This address space is divided equally between the Input Register Bank (10,000
registers) and the Holding Register Bank Holding Register Bank (10,000). This is
where you can create a virtual re-map by cross-referencing any of the 130,072
Primary Slave Modbus registers to the 20,000 Modbus registers in the Virtual
Slave Banks, thereby making it easy for a SCADA Master to poll only the
necessary Modbus addresses in contiguous blocks. The virtual slave can also be
used for data polling from the processor through the backplane.
Modbus access to the Virtual Modbus Slave is disabled by default since its
Modbus address is originally set as 0. To use the Virtual Modbus Slave, you
must initially configure a Modbus address greater than zero in order to enable it.
Refer to Site Configuration for more information about enabling the Virtual Slave
and using the remapping feature. The PLC may always access the Virtual Slave,
whether or not it has a non-zero slave address and thus is available via Modbus.
A download operation will not transfer the Virtual Slave Remapping configuration.
You must click on the Write button on the Indirect Address Remapping dialog
box to transfer the data.
Note: The first 100 registers in the Virtual Slave Holding Register Bank have been pre-assigned
and cannot be remapped. They map directly to the first 100 holding registers of the Primary Slave.
Page 74 of 316 ProSoft Technology, Inc.
February 25, 2011
MVI56-AFC ♦ ControlLogix Platform Modbus Database
Liquid and Gas Flow Computer User Manual
5.3.1 Virtual Slave Example Application
Assume that an application requires a remote Modbus Master to poll the orifice
diameters for the first 5 channels. Continuing the previous example, the holding
register addresses are listed again the following table.
Meter Registers
1 8162 and 8163
2 10162 and 10163
3 12162 and 12163
4 14162 and 14163
5 16162 and 16163
Because these addresses are not contiguous, the Modbus Master would have to
use five commands to poll all the data directly from the Primary Modbus Slave as
follows:
However, using the Virtual Modbus Slave optimizes the polling of data because
the registers can be remapped in any order using the AFC Manager (Site
Configuration window). The following illustration shows how the orifice diameter
registers could be remapped to the Virtual Slave starting at address Vh00100:
ProSoft Technology, Inc. Page 75 of 316
February 25, 2011
Modbus Database MVI56-AFC ♦ ControlLogix Platform
User Manual Liquid and Gas Flow Computer
The following table shows how the addresses would be remapped between both
slaves:
Primary Modbus Slave Addresses Virtual Modbus Slave Addresses
8162 and 8163 100 and 101
10162 and 10163 102 and 103
12162 and 12163 104 and 105
14162 and 14163 106 and 107
16162 and 16163 108 and 109
Therefore, instead of sending five Modbus commands (2 words each) to the
Primary Modbus Slave, the Modbus Master device can now send one single
Modbus command (10 words) to the Virtual Modbus Slave in order to poll the
same data from the module:
This example demonstrates the benefits of using the Virtual Slave instead of
accessing the data directly from the Primary Modbus Slave. The same procedure
can be used when polling data from the processor (through the backplane)
because the Modbus Gateway block also requires the data to be listed in a
contiguous order.
Page 76 of 316 ProSoft Technology, Inc.
February 25, 2011
MVI56-AFC ♦ ControlLogix Platform Modbus Communication
Liquid and Gas Flow Computer User Manual
6 Modbus Communication
In This Chapter
Communication Parameters .................................................................. 78
Port Options .......................................................................................... 79
Modbus Master ...................................................................................... 80
Modbus Pass-Through .......................................................................... 82
A remote Modbus Master device can be connected to any one of the
communication ports for data polling. The module accepts the following Modbus
command functions according to the Modbus protocol specification:
Modbus Function Code Description
3 Read Holding Registers
4 Read Input Registers
6 Preset (Write) Single Register
16 Preset (Write) Multiple Registers
Ports 2 and 3 support RS-232, RS-422, or RS-485 communications. The
Configuration/Debug port (Port 1) supports RS-232 only.
Refer to Cable Connections (page 299) for wiring instructions.
The Modbus Master command can be sent to either the Primary or Virtual
Modbus Slaves in the module. Each slave has individual Modbus addresses that
you can configure (Project / Site Configuration). The Primary Slave address is
configured as 244 by default.
ProSoft Technology, Inc. Page 77 of 316
February 25, 2011
Modbus Communication MVI56-AFC ♦ ControlLogix Platform
User Manual Liquid and Gas Flow Computer
6.1 Communication Parameters
The module supports the following communication parameters for each
communication port:
Parameter Values
Baud Rate 300, 600, 1200, 2400, 4800, 9600 or 19200
Data Bits 7 or 8
Stop Bits 1 or 2 Bits
Mode RTU or ASCII
Parity None, Even or Odd
Note: Do not configure a port for both RTU mode and 7 data bits as this combination is not
supported by the Modbus protocol.
You must configure the communication parameters for each communication port
using the AFC Manager software (Site Configuration):
Page 78 of 316 ProSoft Technology, Inc.
February 25, 2011
MVI56-AFC ♦ ControlLogix Platform Modbus Communication
Liquid and Gas Flow Computer User Manual
6.2 Port Options
The following options can be configured:
Port Options Description
Hide Primary Slave Protects the Primary Slave from any read or write operation from a remote
master. Only the virtual slave is visible on this port.
Swap Modbus Bytes Swap the Modbus bytes transferred through this port (Not implemented)
Swap Modbus Words Swap the Modbus words transferred through this port. This parameter is
only applicable to those data points that hold 32-bit quantities (long
integers, floats, totalizers),
Disable Pass-Thru Disables the pass-thru feature on this port
Modbus Master Enables the Modbus Master for the port (Port 3 only)
Authorization waiver Each port can be individually configured to waive the authorization
requirement. This feature allows each port to have a different access level.
Not all options are available on every port:
Port 1 is restricted, so that AFC Manager can always communicate with the
Primary Slave using this port.
Modbus Master option is available only on Port 3.
ProSoft Technology, Inc. Page 79 of 316
February 25, 2011
Modbus Communication MVI56-AFC ♦ ControlLogix Platform
User Manual Liquid and Gas Flow Computer
6.3 Modbus Master
Port 3 can be configured for Modbus Master operation (Project / Site
Configuration / Port 3).
The Modbus Master command is generated from the processor using ladder
logic (Modbus master block). After the Modbus Master transaction is completed
the module is ready to receive another Modbus Master request from the ladder
logic:
The following Modbus functions are supported for Modbus Master operation:
Modbus Function Code Description
1 Read Coil Status
2 Read Input Status
3 Read Holding Registers
4 Read Input Registers
15 Force (Write) Multiple Coils
16 Preset (Write) Multiple Registers
The module offers considerable flexibility for Modbus Master operation, allowing
the ladder logic to select one of the following data types:
Bit (packed 16 to a word)
Word (16-bit register)
Long (32-bit items as register pairs)
Long Remote (32-bit items as single registers)
Note: Long data type implements each data unit as one pair of 16-bit registers (words). Each
register contains two bytes. Long remote data type implements each data unit as one 32-bit
register. Each register contains four bytes. The proper choice depends on the remote slave’s
Modbus implementation.
Page 80 of 316 ProSoft Technology, Inc.
February 25, 2011
MVI56-AFC ♦ ControlLogix Platform Modbus Communication
Liquid and Gas Flow Computer User Manual
6.3.1 Example
The following table shows how the data types are implemented if a write function
is selected and the item count is configured with a value of 10 (decimal):
Data Type Register Modbus Number of Number of Number of Number of words
Type Function Coils Bytes Registers (16-bits)
transferred
Bit Coil 15 10 2 - 1
Word Holding 16 - 20 10 10
Long Holding 16 - 40 20 20
Long Remote Holding 16 - 40 10 20
Note: The number of coils, bytes, and registers are part of the Modbus request (functions 15 and
16) according to the Modbus specification.
The following table shows how the data types are implemented if a read function
is selected and the item count is configured with a value of 10 (decimal):
Data Type Register Type Modbus Function Number of Registers
Bit Coil 1 10
Bit Input 2 10
Word Holding 3 10
Word Input 4 10
Long Holding 3 20
Long Input 4 20
Long Remote Holding 3 10
Long Remote Input 4 10
Note: The number of registers is part of the Modbus request according to the Modbus
specification.
Refer to the ladder logic section for your module for more information about the
Modbus Master block.
ProSoft Technology, Inc. Page 81 of 316
February 25, 2011
Modbus Communication MVI56-AFC ♦ ControlLogix Platform
User Manual Liquid and Gas Flow Computer
6.4 Modbus Pass-Through
The Modbus pass-through feature allows you to configure a Modbus pass-
through region in the Virtual Slave (Project / Site Configuration). After the
module receives a holding register write command (Modbus functions 6 or 16) or
a bit write command (Modbus functions 5 or 15) to this region, it will generate a
pass-through block to be sent to the processor containing the Modbus command
data. You may define a word pass-through region (for Modbus functions 6 and
16) and a bit pass-through region (for Modbus functions 5 and 15).
Important: You must enable the virtual slave by configuring a Modbus address greater than 0
(Project / Site Configuration).
You can control which communication ports will support the pass-through
(Project / Site Configuration / Port X button).
This feature requires ladder logic to read the pass-through block from the module
to the processor. Refer to the Ladder Logic section for more information about
the pass-through feature.
Page 82 of 316 ProSoft Technology, Inc.
February 25, 2011
MVI56-AFC ♦ ControlLogix Platform Accumulators
Liquid and Gas Flow Computer User Manual
7 Accumulators
In This Chapter
Accumulator Totalizer and Residue ....................................................... 84
Accumulator Types ................................................................................ 85
Net Accumulator Calculation ................................................................. 89
Frequently Asked Questions ................................................................. 90
The accumulators store the current amount of measured quantity for a meter
channel. This section provides detailed information about the accumulators.
ProSoft Technology, Inc. Page 83 of 316
February 25, 2011
Accumulators MVI56-AFC ♦ ControlLogix Platform
User Manual Liquid and Gas Flow Computer
7.1 Accumulator Totalizer and Residue
The accumulators are expressed as the totalizer and residue parts. This
implementation allows the accumulation of a wide range of increments, while
keeping a high precision of fractional part with an approximately constant and
small round off error.
The totalizer stores the integral part of an accumulator as a 32-bit (or split)
integer. The residue is the fractional part (always less than 1.0) expressed as a
32-bit IEEE floating point.
The Total Accumulator is given by the formula:
ACCUMULATOR = TOTALIZER + RESIDUE
Example
If the meter monitor window shows the following values for the accumulators:
The total resettable accumulator 1 value (net) is 12.8031153.
The accumulator totalizer values can be configured to "split" with the low-order
word rolling over from 9999 to 0000 at which time the high-order word is
incremented. Refer to the AFC Manager (AFC Manager / Meter Configuration /
Split Double Accumulators) to select this feature.
A 32-bit value is more suited to computation and has a greater range than a split
value, whereas a split value is easier to read when it is represented as a pair of
16-bit numbers, as in a processor data file.
Page 84 of 316 ProSoft Technology, Inc.
February 25, 2011
MVI56-AFC ♦ ControlLogix Platform Accumulators
Liquid and Gas Flow Computer User Manual
7.2 Accumulator Types
The module supports a total of 12 accumulators per meter channel divided into
the following categories:
These 3 accumulator types are independent. For example, resetting a resettable
accumulator does not affect the other accumulators.
For multiple-stream firmware (version 2.05 and later), each stream also has its
own set of ten accumulators (six non-resettable and four resettable). Increments
are applied both to the meter accumulators and to the accumulators for the active
stream.
7.2.1 Non-Resettable Accumulators
The non-resettable accumulators are only reset when the accumulator rollover
value is reached. The accumulator rollover value, and the accumulator unit must
be configured using the AFC Manager. Refer to the AFC Manager User Manual
for more information about this topic.
The module supports six non-resettable accumulators in order to show the
measured quantity to be totalized:
Non-resettable accumulator mass
Non-resettable accumulator energy (Gas applications only)
Non-resettable accumulator net
Non-resettable accumulator gross
Non-resettable accumulator gross standard (Liquid applications only). For Oil-
Water Emulsion, this is non-resettable accumulator gross clean oil.
Non-resettable accumulator water (Liquid applications only)
Refer to the Modbus Dictionary dialog box in AFC Manager for more information
about the Modbus addresses for these registers.
7.2.2 Resettable Accumulators
The resettable accumulators are referred to as:
Resettable Accumulator 1
Resettable Accumulator 2
Resettable Accumulator 3
Resettable Accumulator 4
ProSoft Technology, Inc. Page 85 of 316
February 25, 2011
Accumulators MVI56-AFC ♦ ControlLogix Platform
User Manual Liquid and Gas Flow Computer
Configuring Resettable Accumulators
Resettable Accumulators are configured from the Resettable Accumulator Select
dialog box. To open this dialog box, click the Resettable Accum button on the
Meter Configuration dialog box.
Each Resettable Accumulator can be configured to represent a different quantity
as follows:
Accumulator Modbus address for accumulator Default Value
select (Meter-relative)
Resettable accumulator 1 136 Net (code 3)
Resettable accumulator 2 137 Gross (code 4)
Resettable accumulator 3 138 Gross Standard (code 5)
Resettable accumulator 4 139 Mass (code 1)
Valid Configuration Codes
The valid codes are:
Code Quantity
0 None
1 Mass
2 Energy (Gas Only)
3 Net
4 Gross
5 Gross Standard (Liquid Only)
6 Water (Liquid Applications Only).
For example, moving a value of 4 to holding register 8136 will configure Meter 1’s
resettable accumulator 1 as "Gross Volume". Moving "0" to holding register
10138 configures Meter 2’s Resettable Accumulator 3 to accumulate nothing
(takes it out of service).
The resettable accumulators are reset when one of the following situations occur.
Reset from AFC Manager
You may reset any of the resettable accumulators using the AFC Manager
(Meter Monitor):
Page 86 of 316 ProSoft Technology, Inc.
February 25, 2011
MVI56-AFC ♦ ControlLogix Platform Accumulators
Liquid and Gas Flow Computer User Manual
Reset from Ladder Logic
The ladder logic may send a meter signals block to command one or more
resettable accumulators to be reset. This feature is especially important for
applications involving field installations that require shipping and/or receiving
product batches of predetermined size. Refer to the Ladder Logic section for your
module type for more information.
Reset Upon Archive Period End or Reset Upon Event
Use AFC Manager to configure the resettable accumulator to be reset when the
archive period ends or when an event occurs. Refer to Event Log in the AFC
Manager User Guide for more information on configuring and monitoring events.
Refer to Archives (page 91) for more information.
Reset When the Accumulator Rollover Value is Reached
The resettable accumulator is reset when the accumulator rollover value is
reached. You must configure the accumulator rollover value using the AFC
Manager software (Meter Configuration). Refer to the AFC Manager User Manual
for more information about this subject.
For multiple-stream firmware (version 2.05 or later), resetting a resettable
accumulator resets that accumulator for both the meter and for all its streams.
ProSoft Technology, Inc. Page 87 of 316
February 25, 2011
Accumulators MVI56-AFC ♦ ControlLogix Platform
User Manual Liquid and Gas Flow Computer
7.2.3 Archive Accumulators
The archive accumulators are part of the current archive (archive 0) data. These
accumulators are automatically reset when a new archive is generated. The
following Modbus holding registers are used:
Daily Archive Hourly Archive
Meter Accumulator: Totalizer Accumulator: Residue Accumulator: Totalizer Accumulator: Residue
1 8890 to 8891 8892 to 8893 8894 to 8895 8896 to 8897
2 10890 to 10891 10892 to 10893 10894 to 10895 10896 to 10897
3 12890 to 12891 12892 to 12893 12894 to 12895 12896 to 12897
4 14890 to 14891 14892 to 14893 14894 to 14895 14896 to 14897
5 16890 to 16891 16892 to 16893 16894 to 16895 16896 to 16897
6 18890 to 18891 18892 to 18893 18894 to 18895 18896 to 18897
7 20890 to 20891 20892 to 20893 20894 to 20895 20896 to 20897
8 22890 to 22891 22892 to 22893 22894 to 22895 22896 to 22897
You can view the addresses, datum types and descriptions in the Modbus
Dictionary dialog box.
You may configure the accumulator quantity to be used for each archive
accumulator using the AFC Manager (Meter Configuration / Archive Config /
Accumulator Select):
Page 88 of 316 ProSoft Technology, Inc.
February 25, 2011
MVI56-AFC ♦ ControlLogix Platform Accumulators
Liquid and Gas Flow Computer User Manual
7.3 Net Accumulator Calculation
The Net Accumulator Calculation depends on the product group (gas or liquid).
For gas applications, the Net Accumulator is calculated as follows:
For liquid applications (all except Emulsion), the Net Accumulator is calculated as
follows:
For liquid applications (Oil-Water Emulsion), the net accumulator is calculated as
follows, using API ch 20.1:
ProSoft Technology, Inc. Page 89 of 316
February 25, 2011
Accumulators MVI56-AFC ♦ ControlLogix Platform
User Manual Liquid and Gas Flow Computer
7.4 Frequently Asked Questions
I need the accumulators to be reset upon period end. Which accumulator
should my application use? Resettable Accumulator or Archive
Accumulator?
You can use either one. The Archive Accumulators are reset every time a new
archive is created and you configure whether the archive should be created upon
period end and/or upon events.
There are some applications that may require the archives to be generated upon
period end and upon event while the accumulators should be reset only upon
period end. For these applications, you should consider the Resettable
Accumulator (configured to be reset upon period end only) because the Archive
Accumulators will also be reset when an event occurs.
Page 90 of 316 ProSoft Technology, Inc.
February 25, 2011
MVI56-AFC ♦ ControlLogix Platform Archives
Liquid and Gas Flow Computer User Manual
8 Archives
In This Chapter
Archive Overview .................................................................................. 92
Archive Generation ................................................................................ 93
Archive Types ........................................................................................ 94
Archive Order ........................................................................................ 95
Archive Options ..................................................................................... 97
Archive Locations .................................................................................. 98
Editing the Archive Structure ............................................................... 100
Extended Archives .............................................................................. 102
Archive Reports ................................................................................... 105
Archive Monitor ................................................................................... 107
ProSoft Technology, Inc. Page 91 of 316
February 25, 2011
Archives MVI56-AFC ♦ ControlLogix Platform
User Manual Liquid and Gas Flow Computer
8.1 Archive Overview
An archive is a set of data that records relevant process values that occurred
during a certain period of time (per meter channel). The archives are
automatically generated by the module and no further action is required. The
process values can include:
Net flow rate (average)
Total accumulator
Temperature (average)
Alarms occurred during the period
The process values will depend on the meter type and product group as listed
later in this section.
Each archive contains two values that exhibits the period of time about that
archive:
opening timestamp = starting date and time for archive
closing timestamp = ending date and time for archive
The example described in this chapter is of the default archive configuration as is
present for a newly allocated meter. Version 2.01 of the firmware and AFC
Manager allows the default configuration to be changed. Refer to Editing the
Archive Structure.
Page 92 of 316 ProSoft Technology, Inc.
February 25, 2011
MVI56-AFC ♦ ControlLogix Platform Archives
Liquid and Gas Flow Computer User Manual
8.2 Archive Generation
The archives can be generated during one of the following situations:
Upon period end
Upon event
Upon processor command
You can configure if the archives should be generated upon period end and/or
event using the AFC Manager (Meter Configuration / Archive Config /
Options)
Refer to the AFC Manager User Manual for more information about this topic. By
default the archives are generated upon period end and event.
If the archive is configured to be created upon period end, it will be periodically
(daily or hourly) generated at the time configured by the End-of-day minute and
End-of-hour minute parameters (Project / Site Configuration).
If the archive is configured to be created upon event, it will be generated every
time an event occurs. For example, if an operator changes the orifice diameter
for Meter 1, the module would automatically generate a new archive to save the
relevant data to this point. Refer to this User Manual for the Events section for
more information about events.
Note: Changing a meter type, product group, system of units, or primary input parameter will erase
all archives for that meter.
ProSoft Technology, Inc. Page 93 of 316
February 25, 2011
Archives MVI56-AFC ♦ ControlLogix Platform
User Manual Liquid and Gas Flow Computer
8.3 Archive Types
The module supports two types of archives: hourly archives and daily archives:
Archive Type Period Period End Number of 30-Word
Archives Stored Locally
Hourly 60 minutes (1 hour) Set by End-of-Hour Minute parameter 48
Daily 1440 minutes (1 day) Set by End-of-Day Minute parameter 35
The Period End parameters must be set using the AFC Manager (Site
Configuration). The default value is zero for both archive types which means that:
Daily Archives are generated every day at midnight (00:00)
Hourly Archives are generated every hour on the hour (1:00, 2:00, 3:00, 4:00)
For example, if the parameters are configured as follows:
End-of-day minute = 480
The daily archives would be created every day at 08:00.
End-of-hour minute = 30
The hourly archives would be created every hour at 1:30, 2:30, 3:30, 4:30, and
so on.
Page 94 of 316 ProSoft Technology, Inc.
February 25, 2011
MVI56-AFC ♦ ControlLogix Platform Archives
Liquid and Gas Flow Computer User Manual
8.4 Archive Order
An important concept regarding this topic is the archive order. Understanding this
simple concept is essential when reading archive data (through the backplane or
Modbus Master). Each archive has a number (its "age") that labels its position in
the archive queue. The following table shows the archive numbering scheme
(both daily and hourly archives):
Archive Age Register Types Description
0 Holding Register Current archive.
1 Input Register Most recent archive
2 Input Register Second most recent archive
3 Input Register Third most recent archive
4 Input Register Fourth most recent archive
(and so forth)
The archive 0 is the current archive. Because its period has not been concluded
its closing timestamp and values (such as accumulator, average temperature,
etc…) will be continuously updated. After the period is over (or an event occurs
depending on the archive configuration) the data in archive 0 will be saved as the
"new" archive 1. The data in the "old" archive 1 will be saved as the new archive
2 and so forth.
The current archive is stored in the primary slave's holding register bank. The
past archives are stored in the primary slave's input register bank.
The following illustration shows an example for hourly archives:
Where:
OT = Opening Time Stamp
CT = Closing Time Stamp
The previous figure shows an example where the hourly archives are configured
to be generated upon period-end at the minute "0" (1:00, 2:00, 3:00, etc…).
Therefore, at 09:59:59 the archive 0 (current archive) is just about to be saved as
the "new" archive 1.
ProSoft Technology, Inc. Page 95 of 316
February 25, 2011
Archives MVI56-AFC ♦ ControlLogix Platform
User Manual Liquid and Gas Flow Computer
When the clock changes to 10:00:00 the following illustration shows how the
latest four archives are modified:
Where:
OT = Opening Time Stamp
CT = Closing Time Stamp
Page 96 of 316 ProSoft Technology, Inc.
February 25, 2011
MVI56-AFC ♦ ControlLogix Platform Archives
Liquid and Gas Flow Computer User Manual
8.5 Archive Options
The module also allows you to configure whether the resettable accumulator
should be reset upon period end and/or event. Most applications will require the
resettable accumulators to be reset just after the archive is generated. The AFC
Manager (version 2.01.000 or later) supports this feature through the archive
options window as shown in the following example:
By default, the module is configured to generate archives upon period end and
event. The module is not configured by default to reset the resettable
accumulators upon period end.
ProSoft Technology, Inc. Page 97 of 316
February 25, 2011
Archives MVI56-AFC ♦ ControlLogix Platform
User Manual Liquid and Gas Flow Computer
8.6 Archive Locations
Click the Modbus Addresses button on the Archive Configuration dialog box to
learn how to fetch an archive record of a specific age (procedure and Modbus
location), and even the actual Modbus address of a specific file archived datum
point (if you have highlighted the item in the archive record template).
The following table shows the current archive (Archive 0) location in the Primary
Modbus Slave for each of the first 8 meters. These addresses refer to the holding
register bank.
Archive 0 - Current Archives
Meter Start Daily Archive End Daily Archive Start Hourly Archive End Hourly Archive
1 9900 9939 9950 9989
2 11900 11939 11950 11989
3 13900 13939 13950 13989
4 15900 15939 15950 15989
5 17900 17939 17950 17989
6 19900 19939 19950 19989
7 21900 21939 21950 21989
8 23900 23939 23950 23989
Refer to the Modbus Dictionary dialog box for the current archive addressing.
The following table shows the past archives location in the Primary Modbus
Slave for each of the first 8 meters. These addresses refer to the input register
bank.
Archives 1 to n - Past Archives
Meter Start Daily Archive End Daily Archive Start Hourly Archive End Hourly Archive
1 0 1059 1060 2499
2 2500 3559 3560 4999
3 5000 6059 6060 7499
4 7500 8559 8560 9999
5 10000 11059 11060 12499
6 12500 13559 13560 14999
7 15000 16059 16060 17499
8 17500 18559 18560 19999
Page 98 of 316 ProSoft Technology, Inc.
February 25, 2011
MVI56-AFC ♦ ControlLogix Platform Archives
Liquid and Gas Flow Computer User Manual
The default configuration sets 30 words per meter archive. For example, the
Meter 1 daily archives are addressed as follows:
Daily Archive Number Start Address End Address
1 0 29
2 30 59
3 60 89
4 90 119
… … …
35 1020 1049
The Meter 1 hourly archives are addressed as follows:
Hourly Archive Number Start Address End Address
1 1060 1089
2 1090 1119
3 1120 1149
4 1150 1179
… … …
48 2470 2499
ProSoft Technology, Inc. Page 99 of 316
February 25, 2011
Archives MVI56-AFC ♦ ControlLogix Platform
User Manual Liquid and Gas Flow Computer
8.7 Editing the Archive Structure
Note: The features presented on this section are only available for AFC firmware version 2.01.000
or later. Please contact the tech support team for more information about the module upgrade.
For advanced applications, you can edit the archive contents, the record size, the
order of the registers in the archive, and the archive accumulator quantity.
The Archive Configuration window (Meter Configuration / Archive Config)
allows you to fully configure the meter archive (daily or hourly). The data to be
inserted in the archive must be copied from the Dictionary Section on the right
half of the window.
Refer to the AFC Manager User Manual for more information about this topic.
Page 100 of 316 ProSoft Technology, Inc.
February 25, 2011
MVI56-AFC ♦ ControlLogix Platform Archives
Liquid and Gas Flow Computer User Manual
The module reserves 1060 words for daily archives and 1440 words for hourly
archives. Because the default configuration sets the record size for 30 words, it
means that the maximum (default) number of archives per meter channel is 35
daily archives and 48 hourly archives. However, because you can change the
number of words per archive, the actual maximum number of archives per meter
channel will depend on the configured number of words per archive as follows:
Number of Words per Number of Daily Archives Number of Hourly Archives
Archive
10 106 daily archives 144 hourly archives
20 53 daily archives 72 hourly archives
30 35 daily archives 48 hourly archives
40 26 daily archives 36 hourly archives
You may also configure the accumulator type for each archive. You must
configure one of the following options:
Mass
Energy (Gas product only)
Net Volume
Gross Volume
Gross Standard
Water Volume (Liquid product only)
The following topics show the default archive structure when you configure a new
meter. You can edit this structure according to your own requirements.
ProSoft Technology, Inc. Page 101 of 316
February 25, 2011
Archives MVI56-AFC ♦ ControlLogix Platform
User Manual Liquid and Gas Flow Computer
8.8 Extended Archives
This feature is only supported on firmware versions 2.01.000 or newer, and
requires a Compact Flash card to be installed.
The module supports the extended archive feature that allows you to configure
more archives than the regular 35 daily archives and 48 hourly archives. The
module supports the following number of extended archives:
Daily Archives Hourly Archives
Max Number of Archives 350 (version 2.04 and earlier) 1260 (version 2.04 and earlier)
1440 (version 2.05 and newer) 1440 (version 2.05 and newer)
Refer to Extended File Size entry on the Archive Configuration window for
more information.
Note: The maximum number of extended archives is not dependent on the number of words per
archive. Extended archives are stored on a Compact Flash card which must be installed for
Extended Archive configuration to be effective.
8.8.1 Retrieving Extended Archives
The module implements an easy way to retrieve extended archives from the
Modbus database. To learn how to retrieve extended archives, click Archive
Config on the Meter Configuration dialog box, and then click Modbus Addresses.
For each archive file the module reserves a block of 50 Input registers to hold the
"selected Archive", as listed in the following table.
Meter Daily Archive Start Daily Archive End Hourly Archive Start Hourly Archive End
(Input Register) (Input Register) (Input Register) (Input Register)
1 60000 60049 60050 60099
2 60100 60149 60150 60199
3 60200 60249 60250 60299
4 60300 60349 60350 60399
5 60400 60449 60450 60499
6 60500 60549 60550 60599
7 60600 60649 60650 6069 9
8 60700 60749 60750 60799
9 60800 60849 60850 60899
10 60900 60949 60950 60999
11 61000 61049 61050 61099
12 61100 61149 61150 61199
13 61200 61249 61250 61299
14 61300 61349 61350 61399
15 61400 61449 61450 61499
16 61500 61549 61550 61599
Note: Meters 9 through 16 are only available for the PTQ-AFC and MVI56-AFC modules.
Page 102 of 316 ProSoft Technology, Inc.
February 25, 2011
MVI56-AFC ♦ ControlLogix Platform Archives
Liquid and Gas Flow Computer User Manual
The Selected Archive start address can be calculated as (assumes meters are
numbered starting at 1):
Daily Archive Start Address = 60000 + ((Meter Number -1) * 100)
Hourly Archive Start Address = 60000 + (((Meter Number -1) * 100) + 50)
Note: When using processor logic to retrieve extended archives, when possible, use unsigned 16-
bit integer data type variables to hold archive addresses. Unsigned 16-bit integers display data in
the range 0 to 65535.
®
If your programming software (such as Rockwell Automation RSLogix™5000) does not support
unsigned integer data types, there are a couple of possible alternatives. If your programming
software supports signed 32-bit double integer data types, you may use that type of variable to
hold the addresses above.
If you must use signed 16-bit integer data type variables to contain addresses (such as in the case
of Rockwell Automation RSLogix5 or RSLogix500), you will not be able to enter the values in the
previous table as positive numbers. This is because 16-bit signed integers display values only in
the range -32768 to +32767. But, it is the underlying bit pattern and not the displayed decimal
value that is important to the AFC module.
To enter the correct bit pattern for these addresses into a signed 16-bit integer, you will need to
enter them as negative numbers. To determine the correct negative number, simply subtract 65536
from the address in the table, which will result in a negative number being displayed in the signed
integer variable. This negative number (a binary twos-compliment form of the archive address) will
contain the equivalent bit pattern for the value in the chart if it were held in an unsigned integer
variable.
Use these modified versions of the above formulas to calculate the address values for signed 16-
bit integer variables:
Daily Archive Start Address = ((60000 + ((Meter Number -1) * 100)) - 65536)
Hourly Archive Start Address = ((60000 + (((Meter Number -1) * 100) + 50)) - 65536)
ProSoft Technology, Inc. Page 103 of 316
February 25, 2011
Archives MVI56-AFC ♦ ControlLogix Platform
User Manual Liquid and Gas Flow Computer
The Selected Archive is continuously maintained to be a copy of the archive
record having the age given in the corresponding "Archive Select" holding
register, as listed in the following table. This means that the Selected Archive
changes whenever either (a) the age in the Open Archive Select register is
changed or (b) when the posting of a new archive causes the ages of all archives
to be increased by 1.
Meter Open Daily Archive Open Hourly Archive
Select Address Select Address
1 8300 8301
2 10300 10301
3 12300 12301
4 14300 14301
5 16300 16301
6 18300 18301
7 20300 20301
8 22300 22301
9 24300 24301
10 26300 26301
11 28300 28301
12 30300 30301
13 32300 32301
14 34300 34301
15 36300 36301
16 38300 38301
Note: Meters 9 through 16 are only available for the PTQ-AFC and MVI56-AFC modules.
Use the following procedure to retrieve extended archives:
1 Copy the archive age to the correct Open Archive Select register.
2 Read the archive data from the 60000-range input addresses.
Example
To read Meter 2 Hourly Archive Number 277:
1 Write a value of 277 to Modbus Holding Register 10301.
2 Read the archive record data starting at input register 60150.
Note: This procedure can also be used to retrieve regular archives.
Page 104 of 316 ProSoft Technology, Inc.
February 25, 2011
MVI56-AFC ♦ ControlLogix Platform Archives
Liquid and Gas Flow Computer User Manual
8.9 Archive Reports
Use the Archive Monitor in AFC Manager to generate an archive report or print it
to a local printer. You can also save the archive report in two formats:
Text
Comma Separated
A report saved in text format (.log) contains a complete archive description. The
following illustration shows an example of a text format report.
ProSoft Technology, Inc. Page 105 of 316
February 25, 2011
Archives MVI56-AFC ♦ ControlLogix Platform
User Manual Liquid and Gas Flow Computer
Saving the archive report in comma-separated (.csv) format allows it to be
imported to an Excel spreadsheet. The following example shows a portion of
the .CSV report imported into Excel:
Page 106 of 316 ProSoft Technology, Inc.
February 25, 2011
MVI56-AFC ♦ ControlLogix Platform Archives
Liquid and Gas Flow Computer User Manual
8.10 Archive Monitor
The Archive Monitor dialog box opens when you open the Monitor menu, and
then choose Archive.
The module can archive data for each meter channel. The archives are
periodically generated according to the period end defined in the Site
Configuration.
There are hourly archives (48 archives) and daily archives (35 archives).
For example the daily archives will be stored as:
Archive 0 = current archive
Archive 1 = Archive created yesterday
Archive 2 = Archive created 2 days ago
Archive 3 = Archive created 3 days ago
And so on.
ProSoft Technology, Inc. Page 107 of 316
February 25, 2011
Archives MVI56-AFC ♦ ControlLogix Platform
User Manual Liquid and Gas Flow Computer
Control
Description
Select Meter Select the meter number
Select Archives Select the archive type
Ages Select the first archive to be added or removed
To Select the last archive to be added or removed
Add Add the selected archives to the grid, fetching as necessary
Remove Remove the selected archives from the grid
Connect Connect to the module, if necessary
Upd Current Update the current archive
Update All Update all archives in the grid
Clear Clear the grid
Log Create a log file containing the archived data
Print Print the archives to the local printer
Plot Display a plot of two datum points from archives in the grid
The following shows an example of an archive report generated by the AFC
Manager:
AFC-56(16) Daily Archive Date: 16-09-2002 16:26:41
Site Name: MVI Flow Station
Project: AFC
___________________________________________________________________________
Meter 1:
Tag M01
Archive 0
Closing timestamp of archive 2002-04-27.23:59:08
Opening timestamp of archive 2002-04-27.00:00:02
Status bitmap (details below) 00h
Alarms bitmap (details below) 0000h
Flowing period 86346
Event counter 53
Net accumulator (x f3) 604
Net accumulator residue (x f3) 0,6703186
Net flow rate (x f3/h) 40247,93
Temperature (°F) 14,99997
Pressure (psig) 999,9995
Differential pressure (hw) 21,99997
Relative density (60°F/60°F) 0,7404
Reference compressibility 0,9989
Flowing compressibility 0,9051
Fpv 1,0505
Velocity of approach factor Ev 1,0328
Expansion factor Y 0,9997
Discharge coefficient 0,6043
Alarm Bits
bit 0 Temperature input out of range -
bit 1 Pressure input out of range -
Page 108 of 316 ProSoft Technology, Inc.
February 25, 2011
MVI56-AFC ♦ ControlLogix Platform Archives
Liquid and Gas Flow Computer User Manual
bit 2 Diff. pressure input out of range -
bit 3 Flowing density input out of range -
bit 4 Water content input out of range -
bit 5 Diff. pressure low -
bit 8 Orifice characterization error -
bit 9 Analysis total zero -
bit 10 Analysis total not normalized -
bit 11 AGA8 calculation error -
bit 12 API calculation error, density correctio -
bit 13 API calculation error, Ctl -
bit 14 API calculation error, vapor pressure -
bit 15 API calculation error, Cpl -
Status Bits
bit 11 Meter was enabled -
bit 12 Backplane communication fault -
bit 13 Measurement configuration changed -
bit 14 Power up -
bit 15 Cold start -
AFC-56(16) Daily Archive Date: 16-09-2002 16:26:41
Site Name: MVI Flow Station
Project: AFC
___________________________________________________________________________
Meter 1:
Tag M01
Archive 1
Closing timestamp of archive 2002-04-27.00:00:02
Opening timestamp of archive 2002-04-26.23:59:42
Status bitmap (details below) 00h
Alarms bitmap (details below) 0000h
Flowing period 20
Event counter 53
Net accumulator (x f3) 234
Net accumulator residue (x f3) 0,1092186
Net flow rate (x f3/h) 40248,01
Temperature (°F) 15
Pressure (psig) 1000
Differential pressure (hw) 22
Relative density (60°F/60°F) 0,7404
Reference compressibility 0,9989
Flowing compressibility 0,9051
Fpv 1,0505
Velocity of approach factor Ev 1,0328
Expansion factor Y 0,9997
Discharge coefficient 0,6043
Alarm Bits
bit 0 Temperature input out of range -
bit 1 Pressure input out of range -
bit 2 Diff. pressure input out of range -
bit 3 Flowing density input out of range -
ProSoft Technology, Inc. Page 109 of 316
February 25, 2011
Archives MVI56-AFC ♦ ControlLogix Platform
User Manual Liquid and Gas Flow Computer
bit 4 Water content input out of range -
bit 5 Diff. pressure low -
bit 8 Orifice characterization error -
bit 9 Analysis total zero -
bit 10 Analysis total not normalized -
bit 11 AGA8 calculation error -
bit 12 API calculation error, density correctio -
bit 13 API calculation error, Ctl -
bit 14 API calculation error, vapor pressure -
bit 15 API calculation error, Cpl -
Status Bits
bit 11 Meter was enabled -
bit 12 Backplane communication fault -
bit 13 Measurement configuration changed -
bit 14 Power up -
bit 15 Cold start -
AFC-56(16) Daily Archive Date: 16-09-2002 16:26:44
Site Name: MVI Flow Station
Project: AFC
___________________________________________________________________________
Meter 1:
Tag M01
Archive 2
Closing timestamp of archive 2002-04-26.23:59:42
Opening timestamp of archive 2002-04-26.06:16:34
Status bitmap (details below) 60h
Alarms bitmap (details below) 0000h
Flowing period 1019877652
Event counter 53
Net accumulator (x f3) 174811
Net accumulator residue (x f3) 0,9399567
Net flow rate (x f3/h) 40247,88
Temperature (°F) 15,00736
Pressure (psig) 1000,416
Differential pressure (hw) 22,00479
Relative density (60°F/60°F) 0,7404
Reference compressibility 0,9989
Flowing compressibility 0,9053
Fpv 1,0506
Velocity of approach factor Ev 1,0331
Expansion factor Y 1,0001
Discharge coefficient 0,6045
Alarm Bits
bit 0 Temperature input out of range -
bit 1 Pressure input out of range -
bit 2 Diff. pressure input out of range -
bit 3 Flowing density input out of range -
bit 4 Water content input out of range -
bit 5 Diff. pressure low -
Page 110 of 316 ProSoft Technology, Inc.
February 25, 2011
MVI56-AFC ♦ ControlLogix Platform Archives
Liquid and Gas Flow Computer User Manual
bit 8 Orifice characterization error -
bit 9 Analysis total zero -
bit 10 Analysis total not normalized -
bit 11 AGA8 calculation error -
bit 12 API calculation error, density correctio -
bit 13 API calculation error, Ctl -
bit 14 API calculation error, vapor pressure -
bit 15 API calculation error, Cpl -
Status Bits
bit 11 Meter was enabled -
bit 12 Backplane communication fault -
bit 13 Measurement configuration changed yes
bit 14 Power up yes
bit 15 Cold start -
AFC-56(16) Daily Archive Date: 16-09-2002 16:26:51
Site Name: MVI Flow Station
Project: AFC
___________________________________________________________________________
Meter 1:
Tag M01
Archive 3
Closing timestamp of archive 2002-04-26.06:16:34
Opening timestamp of archive 2002-04-26.06:14:08
Status bitmap (details below) 20h
Alarms bitmap (details below) 0000h
Flowing period 146
Event counter 50
Net accumulator (x f3) 1633
Net accumulator residue (x f3) 6,271362E-02
Net flow rate (x f3/h) 40248,02
Temperature (°F) 14,99999
Pressure (psig) 1000,002
Differential pressure (hw) 22,00003
Relative density (60°F/60°F) 0,7404
Reference compressibility 0,9989
Flowing compressibility 0,9051
Fpv 1,0505
Velocity of approach factor Ev 1,0328
Expansion factor Y 0,9997
Discharge coefficient 0,6043
Alarm Bits
bit 0 Temperature input out of range -
bit 1 Pressure input out of range -
bit 2 Diff. pressure input out of range -
bit 3 Flowing density input out of range -
bit 4 Water content input out of range -
bit 5 Diff. pressure low -
bit 8 Orifice characterization error -
bit 9 Analysis total zero -
ProSoft Technology, Inc. Page 111 of 316
February 25, 2011
Archives MVI56-AFC ♦ ControlLogix Platform
User Manual Liquid and Gas Flow Computer
bit 10 Analysis total not normalized -
bit 11 AGA8 calculation error -
bit 12 API calculation error, density correctio -
bit 13 API calculation error, Ctl -
bit 14 API calculation error, vapor pressure -
bit 15 API calculation error, Cpl -
Status Bits
bit 11 Meter was enabled -
bit 12 Backplane communication fault -
bit 13 Measurement configuration changed yes
bit 14 Power up -
bit 15 Cold start -
Page 112 of 316 ProSoft Technology, Inc.
February 25, 2011
MVI56-AFC ♦ ControlLogix Platform Events
Liquid and Gas Flow Computer User Manual
9 Events
In This Chapter
The Event Log ..................................................................................... 114
Event Log Structures ........................................................................... 115
Event Id Tag ........................................................................................ 116
Event-triggered Archives and Accumulator Resets ............................. 117
Event Log Download ............................... Error! Bookmark not defined.
Period-end Events ............................................................................... 139
Loggable Events .................................................................................. 140
Special Events ..................................................................................... 141
Site Data Point Events......................................................................... 142
Meter Data Point Events...................................................................... 143
Stream Data Point Events ................................................................... 146
Stream Data Point Events ................................................................... 148
"Rkv" Notes ......................................................................................... 151
Event Numbers .................................................................................... 152
ProSoft Technology, Inc. Page 113 of 316
February 25, 2011
Events MVI56-AFC ♦ ControlLogix Platform
User Manual Liquid and Gas Flow Computer
9.1 The Event Log
An "event" is any occurrence that may affect the manner in which, or whether,
measurement is performed. Events include, for example:
Any change to a sealable parameter.
Power-up (product may have been lost during the power-down period).
A change in PLC operating mode (programming changes may alter
measurement).
A download of the event log (for audit trail purposes).
The Event Log occupies a block of 16000 Input registers in the Modbus table
starting at address 40000 and proceeding through address 55999. It consists of a
5-register "header" at address 40000 followed by 1999 8-register "event" records
starting at address 40008. As they are Input registers (read with Modbus function
code 4), no part of the Event Log can be written from outside the module, but it is
maintained exclusively by the AFC firmware.
As events occur they are recorded in the Log, which acts as a circular file. Each
new event record overwrites the oldest one, hence the log stores up to 1999 of
the most recent events. As each record is written the values in the header are
updated to reflect the new status of the log.
Auditors may require the Log to be "downloaded" from time to time; events are
read from the module and stored in a more permanent database, and the events
so copied and archived are marked in the module as "downloaded".
If all record positions contain events that have not yet been downloaded, the log
is full. In this case, the handling of a new event depends on the value of the
"Event log unlocked" site option:
If the option is set, then the log-full condition is ignored and the new event
overwrites the oldest one. Since the overwritten event was never
downloaded, it is permanently lost.
If the option is clear, then the Event Log is "locked", and the new event is
rejected if possible and otherwise ignored. Controllable events, that is,
changes to sealable parameters, are not allowed to occur; such datum points
remain unchanged retaining their current values and a Modbus command
that attempts such a change receives an "illegal data" exception response.
Uncontrollable events, such as PLC mode change, are simply not recorded.
The Log must be downloaded in order to unlock it for further events.
Page 114 of 316 ProSoft Technology, Inc.
February 25, 2011
MVI56-AFC ♦ ControlLogix Platform Events
Liquid and Gas Flow Computer User Manual
9.2 Event Log Structures
The Event Log header contains housekeeping information for maintaining the
Log. Its layout is:
Address Description
40000 Number of records maximum ( == 1999 )
40001 Next new record position ( 0 thru maximum-1 )
40002 Next new event number ( 0 thru 65535, wrapping to 0 )
40003 Oldest event number on file
40004 Oldest event number on file not yet downloaded
40005-40007 [reserved]
Each event record is an 8-register quantity laid out as four 32-bit items (big-
endian):
Registers Contents
0 to 1 Event Id Tag (page 116)
2 to 3 Timestamp of event
In our standard "packed bit-field" format.
4 to 5 Old item value
For a Datum Point event, format depends on the "datum type" field of the
Event Id Tag.
6 to 7 New item value
For a Datum Point event, format depends on the "datum type" field of the
Event Id Tag.
Each value is right-justified in its field and sign-extended or padded with zeros (0)
if necessary, according to the source data type.
ProSoft Technology, Inc. Page 115 of 316
February 25, 2011
Events MVI56-AFC ♦ ControlLogix Platform
User Manual Liquid and Gas Flow Computer
9.3 Event Id Tag
This 32-bit field has the following structure:
Bits N Meaning
31 1 0 Special, 1 Datum Point (e.g. sealable parameter)
If this bit is clear, then bits 19-00 contain a value from the Special event
tag list below; if the bit is set, then bits 19-00 have the interpretation
given here.
30 1 PLC offline; timestamp may not be accurate
This bit may also be set for a Special event.
29 1 [reserved]
28 to 24 5 Meter number, or 0 for Site
This field may also be set for a Special event.
23 to 20 4 [Meter] Stream number or 0; [Site] 0
This field may also be set for a Special event.
19 to 16 4 Data type:
Value Mnemonic Format
0 Ubyt Unsigned byte
1 Usht Unsigned short integer
2 [reserved]
3 Ulng Unsigned long integer
4 Sbyt Signed byte
5 Ssht Signed short integer
6 [reserved]
7 Slng Signed long integer
8 Bbyt Bitmap (up to 8 bits)
9 Bsht Bitmap (up to 16 bits)
10 Bm24 Bitmap (up to 24 bits)
11 Blng Bitmap (up to 32 bits)
12 Bool Boolean (value 0 or 1)
13 DiBy Dibyte (both high and low)
14 B448 Bitfield nybble/nybble/byte
15 Flot Floating point
15 to 12 4 [reserved]
11 to 08 4 Group code
This value is one of the "measurement configuration changed" bit
numbers.
07 to 04 4 Subgroup code
This value is the ordinal number (starting at 0) of the subgroup of
parameters in the specified group.
03 to 00 4 Subgroup item code
Since a parameter subgroup may contain more than one item, this value
identifies the particular item; items are numbered from 0.
Page 116 of 316 ProSoft Technology, Inc.
February 25, 2011
MVI56-AFC ♦ ControlLogix Platform Events
Liquid and Gas Flow Computer User Manual
9.4 Event-triggered Archives and Accumulator Resets
Each archive file (two for each meter) contains an Archive Options bitmap whose
configuration specifies the actions to be scheduled (write archive and/or reset
resettable accumulator(s)) when an event occurs (daily or hourly period-end, or
most loggable events). Archives and/or resets are scheduled only for enabled
meters (with one important clarification; see "Rkv" notes (page 151)). The actions
to be taken upon period-end and those to be taken upon loggable events are
configured separately.
Several archive/reset-triggering events can occur simultaneously. In such cases
the archive or reset occurs only once (an archive is written only when archivable
data has been accumulated for at least one meter scan; additional resets of
already-reset accumulators have no effect).
Scheduled accumulator resets are performed at the top of the meter scan. This
permits their final values to be inspected/fetched/archived while the AFC rotates
its scan among the other meters.
Scheduled archives are written at the top of the meter scan, at its bottom, or
between successive scans, depending on the nature of the triggering event.
Archives written at the top of the scan are written before any accumulator resets.
ProSoft Technology, Inc. Page 117 of 316
February 25, 2011
Events MVI56-AFC ♦ ControlLogix Platform
User Manual Liquid and Gas Flow Computer
9.5 Downloading the Event Log in Firmware Version 2.07 and Later
The following is an example of the Event Log Download.
In the Site Configuration window, the Event log download timeout has been
changed from the default of 60 seconds, to 300 seconds (5 minutes).
In the Site Configuration window above there are no active download sessions.
This is indicated by the value of zero in Event log download sessions field.
Click the box to show the Event log sessions window.
After opening the Event log sessions window from the ON-LINE/EVENT LOG menu;
you will see instructions in green in the lower right area of the window.
Page 118 of 316 ProSoft Technology, Inc.
February 25, 2011
MVI56-AFC ♦ ControlLogix Platform Events
Liquid and Gas Flow Computer User Manual
Click POLL to fetch status and to prepare the session:
After polling, you are prompted to download:
ProSoft Technology, Inc. Page 119 of 316
February 25, 2011
Events MVI56-AFC ♦ ControlLogix Platform
User Manual Liquid and Gas Flow Computer
Before downloading you might want to modify the parameters of your download.
Reasons for modification include such things as a need to re-fetch recent events
that were already downloaded and committed in a previous session, or to limit
the amount of download.
To change the download parameters, check the box MANUAL SELECTION in the
Event Log window, and make any desired changes.
After the parameters are set to the chosen values click DOWNLOAD.
Page 120 of 316 ProSoft Technology, Inc.
February 25, 2011
MVI56-AFC ♦ ControlLogix Platform Events
Liquid and Gas Flow Computer User Manual
The requested events are fetched and displayed in the scrollable grid. The
events displayed in this screenshot are of changes to configuration (sealable
parameters):
The Download action opens an Event log sessions window, which will be closed
only when either (a) it is Committed, or (b) it is Abandoned, or (c) it times out due
to no activity. this can be seen by viewing again the Event log download
sessions information from Site Configuration window (you will have to re-Poll the
site information to see the update):
Committing a download tells the AFC module to purge the downloaded events,
that is, to move its download pointer past the downloaded events and allow those
events to be overwritten. Event log management standards mandate that
downloaded events must be saved to more permanent storage before they can
be purged from the module. In the earlier screenshot you can see that the
COMMIT button is grayed out because the saving action has not yet been
accomplished. AFC Manager considers the events to have been saved when
they have been either logged to a file or printed.
ProSoft Technology, Inc. Page 121 of 316
February 25, 2011
Events MVI56-AFC ♦ ControlLogix Platform
User Manual Liquid and Gas Flow Computer
Click the LOG button and save the downloaded events to a text file of type ".log":
The COMMIT button is now enabled.
Page 122 of 316 ProSoft Technology, Inc.
February 25, 2011
MVI56-AFC ♦ ControlLogix Platform Events
Liquid and Gas Flow Computer User Manual
Click COMMIT, and the AFC then moves its download pointer (Next event to be
downloaded in the Event Log Status panel):
ProSoft Technology, Inc. Page 123 of 316
February 25, 2011
Events MVI56-AFC ♦ ControlLogix Platform
User Manual Liquid and Gas Flow Computer
To download again, click POLL. This will prompt you to start the next download
starting from the new download pointer (First event in the Set Up Session panel).
Once downloading all outstanding events is completed, there will be no more
events to be downloaded as shown here by a 0 in the Events not yet downloaded
field
For AFC firmware versions prior to 2.07, Event Log Download uses this same
interface, but because the new firmware implementation is not present some
features are not available or behave slightly differently. However, the same basic
sequence of poll, download, and commit/abandon is the same.
Page 124 of 316 ProSoft Technology, Inc.
February 25, 2011
MVI56-AFC ♦ ControlLogix Platform Events
Liquid and Gas Flow Computer User Manual
9.5.1 Basic Principles of Implementation
A properly committed log-download session has three phases:
Phases
Setup Phase
This phase opens the session by a single Modbus transaction to the AFC that
specifies the first event to be downloaded in the session. This event may be
identified explicitly by event number, or it may be conveniently identified as the
earliest event not yet previously downloaded.
Download Phase
This phase transfers event data during an open session by a sequence of zero or
more fetch-and-acknowledge (F&A) cycles. A first Modbus transaction reads a
short block of consecutive chronologically-ordered events from the AFC, and a
second transaction writes sufficient data to inform the AFC that the events just
read have been received without error; this pair of Modbus transactions
constitutes a single F&A cycle. The starting event of the first F&A cycle is the
event identified in the Setup phase. Each successful F&A cycle causes the
subsequent cycle, if any, to begin with the earliest event not included in the
previous cycle. The block of data read from the AFC includes, besides the events
themselves, information that identifies the first event in the block, the number of
events in the block, and the number of not-yet-downloaded events that remain in
the AFC following those in the block. A failed F&A cycle does not cause the
starting event to change, so it may be repeated as many times as is necessary to
accomplish success. All F&A Modbus transactions access a block of registers
beginning at the same address.
Completion Phase
This phase closes the session by a single Modbus transaction that updates the
download point in the event log header with the earliest non-downloaded event
and posts the Download event.
ProSoft Technology, Inc. Page 125 of 316
February 25, 2011
Events MVI56-AFC ♦ ControlLogix Platform
User Manual Liquid and Gas Flow Computer
Dynamic Context
In order for the AFC to manage the log-download session, it maintains a
"dynamic context" for the session, which includes in particular the number of the
earliest event to be retrieved by the next F&A cycle. The dynamic context exists
only while the session is open; the Setup phase opens the session and creates
the context, and the Completion phase closes the session and discards the
context. The dynamic context must not persist (the session remain open)
indefinitely. Therefore, in case that a session is abandoned before completion, or
otherwise fails due to problems such as loss of communication, a timeout is
implemented that automatically abandons the session (closes it without
completion) after a short period of inactivity; all Modbus transactions for the
session must occur at a rate faster than this timeout for the session to be
completed successfully.
One dynamic context is maintained for each port, permitting multiple hosts to
perform download sessions simultaneously; see Section 8 for more on this. The
backplane is deemed to be "port #0", so that a session may also be performed by
the PLC via the Modbus Gateway feature.
To ensure maximum possible security, strict constraints are placed on the
sequencing, addressing, and lengths of all Modbus transactions for the session.
Violation of these constraints causes the offending transaction, depending on its
nature, to be either rejected with a Modbus exception code or accepted but
ignored; in no case does an offending transaction cause change of state in the
AFC.
Page 126 of 316 ProSoft Technology, Inc.
February 25, 2011
MVI56-AFC ♦ ControlLogix Platform Events
Liquid and Gas Flow Computer User Manual
9.5.2 Data Elements
Modbus Points
Point in Mandatory or Value Description
Modbus Optional
Table
slave Mandatory P Primary Slave
selection
V Virtual Slave
register Mandatory h holding registers
bank
i input registers
register Mandatory nnnnn A register address has
address the form "nnnnn" which
or,
is the 5-digit offset (0-
+nnn
based) of the register in
the selected bank; a
register address may
also have the form
"+nnn" where "nnn" is
the 3-digit offset (0-
based) of the register in
a block of registers
which block is located
more globally by
accompanying text.
byte Optional L low-order byte
selection
H high-order byte
bit number Optional /nn Bit number, if present, is
"/nn" where "nn" is the
number of the bit in the
16-bit register or 8-bit
byte, with bits numbered
from 0 at the low-order
end of the register or
byte.
"Ph00146" identifies the 16-bit register at offset 146 in the Primary Slave’s
holding register bank.
"Ph00006H/01" identifies bit 1 of the high-order byte of Primary Slave holding
register 6; this byte is already allocated in the AFC as the Site Extended
Status byte. This bit can be alternately addressed as "Ph00006/09", but the
AFC internally treats the two bytes as distinct.
"Ph00200/05" identifies bit 5 of Primary Slave holding register 200; this bit is
an as-yet unallocated bit in the Site Signals register.
"LDW+000" identifies the first of a block of registers in the Primary Slave
holding register bank and optionally in the Virtual Slave holding register bank,
which block’s absolute location is determined according to accompanying
text.
ProSoft Technology, Inc. Page 127 of 316
February 25, 2011
Events MVI56-AFC ♦ ControlLogix Platform
User Manual Liquid and Gas Flow Computer
Primary Slave Elements
These elements comprise configuration and status items required for the
implementation, as well as the Log-Download Window (LDW) itself. If a host
must access only the Virtual Slave for a log-download session, these points can
be mapped to the Virtual Slave using the existing mapping functionality. As
accesses to the LDW are severely restricted (every Modbus transaction to the
LDW must be addressed to offset 0 of the LDW), a shortcut mapping is available
that maps the entire LDW with a single data point.
Log-Download Window (LDW) Allocation
This is a block of 116 registers beginning at Primary Slave holding register 65400
and having a predefined layout. See Section 6 for the layout of this window. See
Section 4 for how this window, when mapped to the Virtual Slave, is coordinated
with other components of the Virtual Slave.
Site Configuration Items
1 Event Log Download Session Timeout Configuration word at Ph00146. This
timeout is in seconds, which must be at least 5 and may not exceed 300 (5
minutes). Default value is 60 (1 minute).
2 Virtual Slave LDW Location Configuration word at Ph00147. This is the
address in the Virtual Slave’s holding register bank of the first register of the
LDW. This value need not be limited to the 9900-register range of the
mappable Virtual Slave but may be located anywhere in the Virtual Slave’s
address space from register 100 up to 65420 (which address places the last
register of the LDW, at offset 115, at Virtual Slave register 65535). If this
value is 0, the LDW is not available in the Virtual Slave (a conventionally
mapped LDW is not visible).
Status
Event Log Download Active Session Map
Byte at Ph00007H (same word as Ph00007L, "PLC Offline Code").
This byte, previously unallocated, is a bitmap of the ports that currently have
event-log download sessions active. Bits are numbered by the 1-based port
number (where "Port #0" is the backplane), so that, for example, if a session is
active on Port #2, the middle of the three front-panel ports, bit 2 of Ph00007H is
set. The relevant bit is set when a download session is opened by the Setup
phase, and is cleared when the session is committed by the Completion phase or
when it is abandoned by timeout or explicit command. This byte Ph00007H is
already available in the premapped portion of the Virtual Slave at Vh00007H.
Page 128 of 316 ProSoft Technology, Inc.
February 25, 2011
MVI56-AFC ♦ ControlLogix Platform Events
Liquid and Gas Flow Computer User Manual
9.5.3 Virtual Slave Precedence Relations
Addressing conflicts (collisions) can arise among three distinct regions of the
Virtual Slave holding register bank. These regions are:
The defined range of 9900 registers to which Primary Slave registers may be
mapped.
The word region of the pass-thru configuration, significant for Modbus write
commands only.
The LDW, specified in this document, when mapped to the Virtual Slave via
Ph00147.
An addressing collision arises when the address of a holding register falls within
more than one region. The AFC resolves such collisions as follows:
Each address is deemed to fall into one of (i) the pass-thru word region, (ii) the
LDW, or (iii) the 9900-register defined range, whichever occurs first.
All Virtual Slave registers addressed by a single Modbus transaction must reside
in the same region; no region-spanning is permitted. A region-spanning
transaction is rejected with Modbus exception code 2, Illegal Address.
ProSoft Technology, Inc. Page 129 of 316
February 25, 2011
Events MVI56-AFC ♦ ControlLogix Platform
User Manual Liquid and Gas Flow Computer
9.5.4 Security and Optimization
Two features are available that can improve security and throughput of a log-
download session. These are:
1 Session ID - This is a value between 0 and 255 that is chosen by the host at
the opening of the session and must be used in all transactions of the
session. While a session is open, transactions that do not supply the correct
Session ID are rejected. The AFC never displays the ID of the open session,
so only the initiating host knows its value.
2 Collapsed Acknowledgement - This allows the Acknowledgement
transaction of one F&A cycle to be embedded in the Fetch transaction of the
next, reducing by almost half the number of transactions required for the
session.
Use of either of these features, excepting only the use of Session ID 0, requires
non-standard tweaking of the Modbus command packets of Fetch transactions,
hence applications that cannot perform such tweaking are limited to the use of
Session ID 0 and the non-Collapsed acknowledgement methods.
All session transactions except Fetch are Modbus writes; in those, the Session
ID is included as an element of the written data. Fetch transactions are Modbus
reads, which contain no data in their command packets; in those, the Session ID
and (if used) the Collapsed Acknowledgement are encoded in the high-order 9
bits of the "number of registers" field, so that:
Bits 0 thru 6 contain the true "number of registers", which 7 bits are, for holding
register access, sufficient to carry any value that is valid according to the
standard Modbus protocol.
Bit 7 is used for the Collapsed Acknowledgement.
Bits 8 thru 15 contain the Session ID.
The tweaking of the Modbus read command packet is performed before
calculation of the CRC or LRC. See Sections 6 and 7 for more detail.
All Modbus transactions of a log-download session, whether read or write,
address offset 0 of the LDW, either to its Primary Slave location of 65400 or to its
Virtual Slave mapped location configured by Ph00147, hence validation of
Session ID, and recognition of tweaked Modbus command packets, are
performed only for commands that address that location. Any attempt to address
any other offset into the LDW is rejected with a Modbus exception code.
Page 130 of 316 ProSoft Technology, Inc.
February 25, 2011
MVI56-AFC ♦ ControlLogix Platform Events
Liquid and Gas Flow Computer User Manual
9.5.5 The Log-Download Window (LDW)
The LDW, located at Primary Slave holding register 65400 and optionally
mapped to the Virtual Slave by register Ph00147 consists of a header of 4
registers followed by up to fourteen 8-register event records. Accordingly, the
size of the block may be as large as (4+14*8) registers, that is, 116. The block is
returned as the data in the Fetch transaction of a F&A cycle. Certain subsets of
the block may be read or written at other times.
Layout
The header has this layout:
1 LDW+000: Function and Session ID
When written, this register is interpreted as two bytes, where:
The low-order byte contains a function code:
0: Acknowledge Fetch
1: Open Session
2: Commit Session
3: Abandon Session
All other function codes are rejected with Modbus exception 3, "Illegal Data".
The high-order byte contains the Session ID. This ID is specified by the host
upon opening the session and it must be matched by all subsequent accesses
during the session.
When read, this register is always zero.
LDW+001: Starting Event Number
This value is initialized to the number of the event selected by the Setup phase.
After every successful F&A cycle, it is advanced by the number of events fetched
by that cycle.
LDW+002: Number of Events This Block
This is the number of events returned by the Fetch transaction of a F&A cycle. It
never exceeds the number of events that can fit inside the size of the data block
requested, but it may be smaller, such as when fewer events are available than
the number requested. In the latter case, the extra unreturned event records are
all zero.
LDW+003: Number of Non-Downloaded Events After This Block
This is the number of events remaining in the log that have not yet been
downloaded, not counting the events in the current Fetch.
ProSoft Technology, Inc. Page 131 of 316
February 25, 2011
Events MVI56-AFC ♦ ControlLogix Platform
User Manual Liquid and Gas Flow Computer
9.5.6 Modbus Transaction Sequencing and Constraints
This section describes the details of the Modbus transactions that manage a log-
download session, including full specifications of transaction contents and the
conditions under which they are permitted. Also considered is smooth recovery
from failed transactions, as might happen over an intermittently failing
communication link; the general principle is that an otherwise valid transaction
may be repeated as many times as is necessary to ensure success.
Page 132 of 316 ProSoft Technology, Inc.
February 25, 2011
MVI56-AFC ♦ ControlLogix Platform Events
Liquid and Gas Flow Computer User Manual
Setup Phase
This phase, which opens a download session, may be accomplished in one of
two ways:
The Detailed Method
Issue a Modbus write of two registers to offset 0 of the LDW, specifying function
Open Session (1) and the desired Session ID followed by the number of the
desired starting event.
The Quick Method
Issue a Modbus write of a single register to offset 0 of the LDW, specifying
function Open Session (1) and the desired Session ID. This is equivalent to the
Detailed method in which the starting event is copied from the download pointer
in the event log header.
The dynamic context for the session includes two event numbers: one is the
Session Download Pointer (SDP), which is the number of the first event to be
retrieved by the next F&A cycle, and the other is the File Download Pointer
(FDP), which is the number of the earliest event on file that has not yet been
downloaded. The Setup phase specifies, explicitly or implicitly, the SDP, and
initializes the FDP from the download pointer in the event log header, so the SDP
and FDP need not be the same number.
Download Phase
This phase performs the actual retrieval of logged events as a sequence of F&A
cycles. All transactions must place the Session ID into the first register of data
(writes), or into the "number of registers" field of the Modbus command packet
(reads), as described in Section 5.
Fetch Transaction
Issue a Modbus holding-register read (function 3) addressed to offset 0 of the
LDW and with length calculated as (4+n*8), where n is the number of events to
be read and must lie between 0 and 14 inclusive; any other length constitutes an
error. Note that a read of 0 events is permitted, so that the LDW header can be
inspected without changing the session’s dynamic context; however, such a fetch
must still be acknowledged in the manner described next. The response is a
block of the requested length formatted as described in Section 6, whose second
register at offset 1 is the current value of the SDP.
ProSoft Technology, Inc. Page 133 of 316
February 25, 2011
Events MVI56-AFC ♦ ControlLogix Platform
User Manual Liquid and Gas Flow Computer
Acknowledge Transaction
There are four methods of acknowledgement, three of which may be used at any
time, and a session need not use any one consistently, even when repeating an
acknowledgement that has apparently failed:
1 Collapsed method - This method embeds the acknowledgement of the
previous Fetch transaction into the next Fetch transaction, as described in
Section 5.A Collapsed Acknowledgement bit value of 1 acknowledges the
previous Fetch; a 0, if the previous Fetch has not been explicitly
acknowledged by one of the other methods, elicits a repeat of the previous
block of events. The Collapsed Acknowledgement bit of the first Fetch of a
session must be 0.
2 Brief method - Issue a Modbus write of a single register to offset 0 of the
LDW, specifying function "Acknowledge Fetch" (0) with the correct Session
ID. Use this method to conserve bandwidth when use of the Collapsed
method is not possible.
3 Verbose method - Issue a Modbus write of (4+n*8) registers to offset 0 of
the LDW, that echoes the complete data block read by the Fetch transaction
except for insertion of the correct Session ID. The AFC verifies that all
register values, except those at offsets 0 and 3 of the LDW header, are the
same as were transmitted. Use this method for greater confidence of
acknowledgement when bandwidth is less of a concern.
4 Implicit method - The final Fetch transaction of a session can be implicitly
acknowledged by the Completion phase (7.3, next). Because of the potential
for undetected data corruption with the LRC of ASCII mode, only the Verbose
method is recommended for an ASCII-mode Modbus channel.
A successful F&A cycle adjusts the session’s dynamic context as follows:
A The SDP is advanced by the number of events returned by the fetch transaction.
B If at any time the SDP reaches the FDP, the FDP becomes "locked" to the SDP, thereafter
tracking the SDP so that it keeps the same value, until the end of the session.
This ensures that any update of the download pointer in the event log header
during Completion (7.3, next) is done only when it is guaranteed that all newly
downloaded events have been retrieved by the host.
Page 134 of 316 ProSoft Technology, Inc.
February 25, 2011
MVI56-AFC ♦ ControlLogix Platform Events
Liquid and Gas Flow Computer User Manual
Completion Phase
This phase commits a session by determining a final FDP for the event log
header, closing the session, and discarding the dynamic context. If the value of
the final FDP differs from its original value in the event log header, then the
header is updated with the new value and, provided that Site Option "Event Log
Locked" is set, the Download event is written. If the FDP has not changed, no
Download event is written, so the download state of the log remains unchanged.
The session is then closed and its dynamic context discarded. The final FDP is
determined by one of two methods:
1 Implicit Completion: Issue a Modbus write of a single register to offset 0 of
the LDW, specifying function "Commit Session" (2) with the correct Session
ID. This method takes the final FDP from the dynamic context at the moment
of completion.
2 Explicit Completion: Issue a Modbus write of two registers to offset 0 of the
LDW, the same as Implicit Completion but passing in the second register the
desired final FDP as an explicit value. If at any time during the session the
FDP of the dynamic context reached this value, this value becomes the final
FDP for the session completion, in preference to that of the dynamic context.
If the explicit FDP was not reached, this phase is equivalent to session
abandonment (next). An Explicit Completion never marks more events as
"downloaded" than an Implicit Completion.
A Completion of either method can implicitly acknowledge the final Fetch
transaction.
Abandonment
This action explicitly abandons a session by closing it and discarding the
dynamic context, without updating the log header or writing a Download event. In
this case, therefore, adjustment of the log’s download state implied by a changed
FDP is not performed. It is equivalent to waiting for the session timeout to occur
except that its effect is immediate. Issue a Modbus write of a single register to
offset 0 of the LDW, specifying function "Abandon Session" (3) with the correct
Session ID.
ProSoft Technology, Inc. Page 135 of 316
February 25, 2011
Events MVI56-AFC ♦ ControlLogix Platform
User Manual Liquid and Gas Flow Computer
Error Recovery
During a session, the AFC maintains sufficient context information to accept not
only the next expected Modbus transaction of the sequence but also a repeat of
the previous one, except for the Commit Session and Abandon Session actions
(see below). This is to permit simple repetition of a transaction that has
succeeded from the point of view of the AFC but has failed from that of the host,
which would occur when the Modbus response transmitted by the AFC is not
received by the host. (If the host uses Collapsed Acknowledgement, it must take
care to set the acknowledgement bit correctly in a repeated Fetch.) Other than in
such a case, any Modbus transaction that does not comply strictly with the
conditions and sequencing described above is rejected with a Modbus exception
code (typically code 2, Illegal Address, if not addressing LDW offset 0, otherwise
code 3, Illegal Data).
Because both the Commit Session and the Abandon Session actions close the
session, there is afterwards no session context to allow recognition of a repeated
Commit or Abandon. In this case, a repeated Commit elicits a Modbus exception
of 3, Illegal Data, and a repeated Abandon is accepted without error regardless
of its Session ID.
Session Timeout
All transactions of a session must succeed frequently enough so that the duration
between successful transactions does not exceed the session timeout. Each
successful transaction restarts the timeout. If the timeout expires, the session is
automatically abandoned. Other Modbus activity, unrelated to the log-download
session, is not considered, and its only effect upon the timeout would be delays
of session transactions imposed by bandwidth usage.
Page 136 of 316 ProSoft Technology, Inc.
February 25, 2011
MVI56-AFC ♦ ControlLogix Platform Events
Liquid and Gas Flow Computer User Manual
9.5.7 Access by Multiple Hosts
The functionality specified in this document can permit complete event-log
retrieval by multiple hosts, provided that these conditions are satisfied:
1 As the session’s dynamic context is local to the accessed port, multiple hosts
may perform sessions simultaneously provided that they access separate
ports. The Session ID is part of the dynamic context, so separate-port
sessions may use the same Session ID without ambiguity.
2 For multiple hosts that access the same port (using Modbus Master
arbitration or a similar scheme), all must perform their sessions at times
sufficiently separated so that one host does not interfere by disturbing the
dynamic context of another host’s session in an unpredictable manner. The
Session ID can provide significant protection against inadvertent infringement
of this condition.
3 One host must be the Active host, performing the Completion phase that
updates the AFC’s event log state (download pointer). All other hosts must
be Passive, failing to Complete their sessions but instead Abandoning them.
If this condition is disregarded, so that multiple Active hosts perform
simultaneous sessions each ending with the Completion phase, the AFC’s
Event Log, which is global, manages any updating of the download pointer
and posting of the Download event in a globally consistent manner, but each
host cannot be sure that the Download event written upon Completion, if any,
is exactly what it expected.
4 Each host must, in one way or another, have access to its own long-term
download context, which is the number of the earliest event not yet
downloaded by that host. All Passive hosts must maintain this context locally.
The Active host may let the AFC maintain its long-term context, using the
download pointer in the event log header for this purpose; in such a case the
same host must always be the Active one. If, however, each host regardless
of role maintains its own long-term context, the role of Active host may be
passed around among hosts.
5 All hosts must perform download sessions sufficiently often so that events are
not lost by being overwritten by newer ones before those events have been
downloaded by that host.
ProSoft Technology, Inc. Page 137 of 316
February 25, 2011
Events MVI56-AFC ♦ ControlLogix Platform
User Manual Liquid and Gas Flow Computer
9.5.8 Other Considerations
Expired Events
If the starting event number is sufficiently small relative to the events on file (in
particular, if it is 1999 or more before the number of the next event to be
recorded), then that event is no longer on file and has already been overwritten.
In this case, the event returned by a Fetch is all zero. This is not an issue for the
Active host, especially when the event log is configured to be locked, as the
Active host is interested only in non-downloaded events and those always remain
on file with a locked log. But for Passive hosts, and when the event log is
configured as unlocked, download sessions must be performed frequently
enough so that the requested events still remain on file. Because event numbers
wrap from 65535 to 0, and because events that have not yet been written do not
in fact exist and have never existed, an event number that is numerically equal to
or greater than the number of the next event to be recorded is deemed to be the
number of an event from the previous wrap cycle.
Persistence
A log-download session does not survive a reset of the module (e.g. power
cycle).
Page 138 of 316 ProSoft Technology, Inc.
February 25, 2011
MVI56-AFC ♦ ControlLogix Platform Events
Liquid and Gas Flow Computer User Manual
9.6 Period-end Events
A "period-end" event is detected by the wallclock. There are two such:
a) "End-of-hour" occurs when the minute of the hour steps into the "End-of-
hour minute" of Site Configuration.
b) "End-of-day" occurs when the minute of the day steps into the "End-of-day
minute" of Site Configuration.
A wallclock change that skips forward over an end-of-period minute will cause
that period-end to be missed, and a change that skips backward over that minute
will cause that period-end to be repeated, so wallclock adjustments should be
performed at times well-removed from either end-of-period minute.
Though a period-end event is not recorded in the event log, it does cause
archives and resets to be scheduled for all enabled meters according to their
configured "period-end" Archive Options. Archives and resets scheduled by
period-end are delayed in their action until at least one meter scan has occurred
after the event (the archive data accumulation that takes place at the end of the
meter scan also records the latest timestamp, so the written archive then reflects
the fact that the period-end has occurred).
ProSoft Technology, Inc. Page 139 of 316
February 25, 2011
Events MVI56-AFC ♦ ControlLogix Platform
User Manual Liquid and Gas Flow Computer
9.7 Loggable Events
The tables below give full details of all events that are recorded in the Event Log.
For the Special events (page 141), columns are:
Tag Numeric value that identifies the event.
Rkv Effect on archives and accumulator resets (see next).
Description Lists:
The event name, identifying its triggering condition.
Contents and meaning of the old and new value fields.
Relevant additional information.
For the Data Point (page 143, page 142, page 146) events, columns are:
Group Group code.
Sbgp Subgroup code.
Item Item code.
Dtyp Datum type code (mnemonic).
Rkv Effect on archives and accumulator resets (see next).
Datum point The corresponding writable Modbus point.
In these tables, the "Rkv" columns specify how archives and accumulator resets
are scheduled upon occurrence of the corresponding loggable events.
Column values are:
Value Meaning
* Upon this event archives and resets are scheduled according to the
configured "event" Archive Options, provided that the applicable
meter(s) is(are) enabled. Applicable meters depend upon the event
class:
(a) Special (non-meter-specific) and Site Datum Point events:
All meters.
(b) Meter events (including meter-specific Specials):
The addressed meter.
(c) Stream events:
The addressed meter, provided that the addressed stream is active.
Scheduled archives are always written before completing any change to
data or module state implied by the event; this ensures that the data
contributing to an archive is limited to that which was available before
the event.
- This event has no effect on archives and resets.
(n) Upon this event archives and resets are scheduled as for "*", modified
by the conditions and actions given in "Note (n)" in "Rkv" notes (page
151).
Page 140 of 316 ProSoft Technology, Inc.
February 25, 2011
MVI56-AFC ♦ ControlLogix Platform Events
Liquid and Gas Flow Computer User Manual
9.8 Special Events
Tag Rkv Description
0 - Never Used
Value: Always 0.
Notes: This entry in the Event Log has never been written.
The number of such entries starts at 1999 upon cold start and
decreases as events are written until none remain, after which oldest
events are overwritten with new ones.
1 - Event Log Download
Value: Number of last-downloaded event.
Notes: Triggered by a purge of the Event Log, which marks older events
as available to be overwritten by new ones.
2 - Cold Start
Value: Always 0.
Notes: This event is obsolete and is never written.
3 (1) Power-Up
Value: "Old" value is the last-saved wallclock from the previous session;
"new" value is always 0 (clock not yet set).
Notes: The last event written upon restart of the application and before
entering the meter scan. This event may be preceded by Checksum
Alarm and/or PLC Mode Change events.
4 - PLC Mode Change
Value: PLC mode (0 on line, 1 off line).
Notes: Logs changes to PLC connectivity as reported by the backplane
procedures. Typically caused by switching the PLC between "run" and
"program" modes.
5 - Checksum Alarm
Value: Checksum alarm word (datum type "Bsht").
Notes: Logs changes to the checksum alarm bitmaps.
Includes site/meter identification (bits 28-24).
Upon power-up:
Written automatically upon power up when a checksum failure is
detected. In this case the event is written even if the bitmap does not
change, such as when an affected bit is already set from a previous
failure that was never cleared.
Upon Modbus write to the bitmap:
Records changes to the bitmap only, typically when clearing bits, though
setting bits is also permitted.
6 (2) Wallclock Change
Value: Wallclock (packed bitfields).
Notes: Triggered when the wallclock is set for the first time, or when it is
reset to a value that differs from its current value by five minutes or
more. These two cases can be distinguished by the "old value" in the
event entry: for the initial setting this value is zero ("clock not set").
7 * Stream Select
Value: Stream number.
Notes: Triggered by a "select active stream" meter signal.
Includes meter identification (bits 28-24).
ProSoft Technology, Inc. Page 141 of 316
February 25, 2011
Events MVI56-AFC ♦ ControlLogix Platform
User Manual Liquid and Gas Flow Computer
9.9 Site Data Point Events
Group Sbgp Item DTyp Rkv Data point
0 0 0 Bsht (3) Site options
1 Site parameter value
0 0 Flot * Barometric pressure
8 n 0 Usht - Arbitrary event-logged value "n" ("n" = 0 thru 9)
15 PLC image address (Quantum platform only)
0 0 Usht * Supervisory, get
1 0 Usht * Supervisory, put
2 0 Usht * Wallclock, get & put
3 0 Usht * Modbus gateway, get & put
4 0 Usht * Modbus pass-thru, put
5 0 Usht * Modbus master, get & put
Page 142 of 316 ProSoft Technology, Inc.
February 25, 2011
MVI56-AFC ♦ ControlLogix Platform Events
Liquid and Gas Flow Computer User Manual
9.10 Meter Data Point Events
Group Sbgp Item DTyp Rkv Data point
0 0 Process input calibration
0 Flot * Temperature
1 Flot * Pressure
2 Flot * Primary input
3 Flot * Flowing density
4 Flot * Water content
0 1 Process input alarm
0 Flot - Temperature range
1 Flot - Pressure range
2 Flot - Primary input range
3 Flot - Flowing density range
4 Flot - Water content range
1 0 Meter classification
0 Bsht * Meter device and engineering units
1 Usht * Product group
2 Reference conditions
0 0 Flot * Temperature
1 0 Flot * Pressure
3 Meter options
0 0 Blng * Calculation options
1 0 Blng (4) Control options
4 Input scaling
0 Temperature
0 Flot * Range low end
1 Flot * Range high end
2 Flot * Default
3 Sbyt * Module id code
1 Pressure
0 Flot * Range low end
1 Flot * Range high end
2 Flot * Default
3 Sbyt * Module id code
2 Primary input
0 Flot * Range low end
1 Flot * Range high end
2 Flot * Default
3 Sbyt * Module id code
3 Flowing density
0 Flot * Range low end
ProSoft Technology, Inc. Page 143 of 316
February 25, 2011
Events MVI56-AFC ♦ ControlLogix Platform
User Manual Liquid and Gas Flow Computer
Group Sbgp Item DTyp Rkv Data point
1 Flot * Range high end
2 Flot * Default
3 Sbyt * Module id code
4 Water content
0 Flot * Range low end
1 Flot * Range high end
2 Flot * Default
3 Sbyt * Module id code
5 0 0 Bm24 * Analysis component selection map
6 0 0 Ulng * Pulse input rollover
7 Units
0 0 B448 * Primary input (period, quantity, units)
1 0 Ubyt * Mass flow rate period
2 0 Ubyt * Mass flow rate units
3 0 Ubyt * Mass accumulator units
4 0 Ubyt * Energy flow rate period
5 0 Ubyt * Energy flow rate units
6 0 Ubyt * Energy accumulator units
7 0 Ubyt * Volume flow rates period
8 0 Ubyt * Volume flow rates units
9 0 Ubyt * Volume accumulators units
8 Accumulator rollovers
0 0 Ulng * Mass
1 0 Ulng * Energy
2 0 Ulng * Volumes
9 Meter parameter value
0 0 Flot * Orifice plate measurement temperature
1 0 Flot * Orifice plate measured diameter
2 0 Flot * Orifice plate coefficient of thermal expansion
3 0 Flot * Meter tube measurement temperature
4 0 Flot * Meter tube measured diameter
5 0 Flot * Meter tube coefficient of thermal expansion
6 0 Flot * Primary input flow threshold
7 0 Flot * Primary input alarm threshold
8 0 Flot * V-cone/Wedge coefficient of discharge
10 [reserved]
11 0 Densitometer
0 Usht * Densitometer type
1 Flot * Calibration temperature
2 Flot * Calibration pressure
Page 144 of 316 ProSoft Technology, Inc.
February 25, 2011
MVI56-AFC ♦ ControlLogix Platform Events
Liquid and Gas Flow Computer User Manual
Group Sbgp Item DTyp Rkv Data point
3 Flot * Calibration constant K0
4 Flot * Calibration constant K1
5 Flot * Calibration constant K2
6 Flot * Calibration constant 6
7 Flot * Calibration constant 7
8 Flot * Calibration constant 8
9 Flot * Calibration constant 9
10 Flot * Calibration constant 10
11 Flot * Calibration constant 11
12 Flot * Calibration constant 12
13 Flot * Calibration constant 13
14 Flot * Calibration constant 14
15 PLC image address (Quantum platform only)
0 0 Usht * Meter process input &c, get
1 0 Usht * Meter results, put
2 0 Usht * Meter archive fetch, put
ProSoft Technology, Inc. Page 145 of 316
February 25, 2011
Events MVI56-AFC ♦ ControlLogix Platform
User Manual Liquid and Gas Flow Computer
9.11 Stream Data Point Events
Group Sbgp Item DTyp Rkv Data point
0 0 0 Bsht * Stream options
1 Stream parameter value
0 0 Flot * Default relative density (gas) at reference
1 0 Flot * Viscosity
2 0 Flot * Isentropic exponent
3 0 Flot * Default Fpv
4 0 Flot * K/meter factor
5 0 Flot * Default energy content
6 0 Flot * Default reference density (liquid)
7 0 Flot * Default vapor pressure
8 0 Flot * Water density at API reference
9 0 Flot * Default Ctl
10 0 Flot * Default Cpl
11 0 Flot * Shrinkage factor
12 0 Flot * Precalculated alpha
2 0 Meter factor curve
0 Flot * Datum point 1, meter factor
1 Flot * Datum point 1, flow rate
2 Flot * Datum point 2, meter factor
3 Flot * Datum point 2, flow rate
4 Flot * Datum point 3, meter factor
5 Flot * Datum point 3, flow rate
6 Flot * Datum point 4, meter factor
7 Flot * Datum point 4, flow rate
8 Flot * Datum point 5, meter factor
9 Flot * Datum point 5, flow rate
3 0 Analysis mole fraction
** Because the item code extends into the subgroup
field, this can be the only subgroup of group 3 !
(Pending any future reformat of the Event Id Tag)
0 Usht (5) Component 1, scaled molar fraction
1 Usht (5) Component 2, scaled molar fraction
2 Usht (5) Component 3, scaled molar fraction
3 Usht (5) Component 4, scaled molar fraction
4 Usht (5) Component 5, scaled molar fraction
5 Usht (5) Component 6, scaled molar fraction
6 Usht (5) Component 7, scaled molar fraction
7 Usht (5) Component 8, scaled molar fraction
8 Usht (5) Component 9, scaled molar fraction
9 Usht (5) Component 10, scaled molar fraction
Page 146 of 316 ProSoft Technology, Inc.
February 25, 2011
MVI56-AFC ♦ ControlLogix Platform Events
Liquid and Gas Flow Computer User Manual
Group Sbgp Item DTyp Rkv Data point
10 Usht (5) Component 11, scaled molar fraction
11 Usht (5) Component 12, scaled molar fraction
12 Usht (5) Component 13, scaled molar fraction
13 Usht (5) Component 14, scaled molar fraction
14 Usht (5) Component 15, scaled molar fraction
15 Usht (5) Component 16, scaled molar fraction
16 Usht (5) Component 17, scaled molar fraction
17 Usht (5) Component 18, scaled molar fraction
18 Usht (5) Component 19, scaled molar fraction
19 Usht (5) Component 20, scaled molar fraction
20 Usht (5) Component 21, scaled molar fraction
21 Usht (5) Component 22, scaled molar fraction
22 Usht (5) Component 23, scaled molar fraction
23 Usht (5) Component 24, scaled molar fraction
ProSoft Technology, Inc. Page 147 of 316
February 25, 2011
Events MVI56-AFC ♦ ControlLogix Platform
User Manual Liquid and Gas Flow Computer
9.12 Prover Data Point Events
Note: Currently, this function is only available on the MVI56- AFC. For all other platforms continue
to use AFC Manager 2.05 or earlier.
Group Sbgp Item DTyp Rkv Data point
0 0 Process input calibration ** not implemented
0 Flot - (Inlet) temperature
1 Flot - Outlet temperature
2 Flot - Switch bar temperature
3 Flot - (Inlet) pressure
4 Flot - Outlet pressure
0 1 Process input alarm ** not implemented
0 Flot - (Inlet) temperature range
1 Flot - Outlet temperature range
2 Flot - Switch bar temperature range
3 Flot - (Inlet) pressure range
4 Flot - Outlet pressure range
1 0 Prover classification
0 Diby - Prover type, master meter number
1 Diby - Measurement system, density selection
2 0 0 Bsht - Prover options
3 0 Prover run counts
0 Usht - Runs per prove, total
1 Usht - Runs per prove, selected
2 Usht - Max total runs before abort
3 Usht - Passes per run (short prover)
4 Usht - Min pulses per run * 1000
5 Usht - Max seconds per run
4 Prover input format codes
0 0 Usht - Pulse count for run/pass
1 0 Usht - Master meter pulse count
5 Prover reference conditions
0 0 Flot * Temperature
1 0 Flot * Pressure
6 Prover parameter value
0 0 Flot - Meter factor precision
1 0 Flot - Pulse interpolation ratio
2 0 Flot - Flow tube linear thermal expansion coefficient
3 0 Flot - Switch bar linear thermal expansion coefficient
4 0 Flot - Calibrated prover volume
Page 148 of 316 ProSoft Technology, Inc.
February 25, 2011
MVI56-AFC ♦ ControlLogix Platform Events
Liquid and Gas Flow Computer User Manual
Group Sbgp Item DTyp Rkv Data point
5 0 Flot - Flow tube inside diameter
6 0 Flot - Flow tube wall thickness
7 0 Flot - Flow tube modulus of elasticity
7 0 Prover variation limits
0 Flot - Meter temperature
1 Flot - Prover inlet temperature
2 Flot - Prover outlet temperature
3 Flot - Prover inlet-outlet temperature
4 Flot - Prover temperature
5 Flot - Prover-Meter temperature
6 Flot - Switch bar temperature
7 Flot - Meter pressure
8 Flot - Prover inlet pressure
9 Flot - Prover outlet pressure
10 Flot - Prover inlet-outlet pressure
11 Flot - Prover pressure
12 Flot - Prover-meter pressure
13 Flot - Density
14 Flot - Water content
15 Flot - Meter flow rate
16 Flot - Prover flow rate
17 Flot - Pulses over runs
18 Flot - Pulses over passes
19 Flot - Repeatability
20 Flot - Change in factor
8 Prover process input scaling
0 (Inlet) temperature
0 Flot * Range low end
1 Flot * Range high end
2 Flot * Default
3 Sbyt * Module ID code
1 Outlet temperature
0 Flot * Range low end
1 Flot * Range high end
2 Flot * Default
3 Sbyt * Module ID codes
2 Switch bar temperature
0 Flot * Range low end
1 Flot * Range high end
2 Flot * Default
ProSoft Technology, Inc. Page 149 of 316
February 25, 2011
Events MVI56-AFC ♦ ControlLogix Platform
User Manual Liquid and Gas Flow Computer
Group Sbgp Item DTyp Rkv Data point
3 Sbyt * Module ID codes
3 (Inlet) pressure
0 Flot * Range low end
1 Flot * Range high end
2 Flot * Default
3 Sbyt * Module ID codes
4 Outlet pressure
0 Flot * Range low end
1 Flot * Range high end
2 Flot * Default
3 Sbyt * Module ID codes
15 PLC image address (Quantum/Unity platform only)
0 0 Usht - Prover, get
1 0 Usht - Prover, put
Page 150 of 316 ProSoft Technology, Inc.
February 25, 2011
MVI56-AFC ♦ ControlLogix Platform Events
Liquid and Gas Flow Computer User Manual
9.13 "Rkv" Notes
1 Archives (only, not resets) are forced regardless of configuration, capturing
any unarchived data from the previous session.
2 Archives and resets are scheduled (immediately, without a "period-end"
delay) only for the initial setting of the wallclock; a "five-minute" event causes
no scheduling. This ensures capture of any flow that has occurred prior to the
initial clock-set.
3 Event occurs only when one or more of the following bits are changed:
o Bit 2, "Barometric pressure units"
o Bit 5, "Process input out of range use last good"
o Bit 12, "Analysis is packed in module"
o Bit 13, "Analysis is packed over backplane" (1756 and 1769 platforms
only)
4 A change to Meter Control Options bit 15, "Meter enable", imposes these
adjustments to the normally-scheduled archives/resets:
o Upon meter enable, cancel any scheduled archives (no data yet to be
archived), but leave in place any scheduled resets.
o Upon meter disable, cancel any resets (for inspection and so on.; reset
will be rescheduled upon subsequent enable), and force archiving of both
files regardless of configuration (so that a disabled meter never has any
pending unarchived data).
5 Events occur only if Meter Control Options bit 10, "Treat analysis as process
input", is clear.
ProSoft Technology, Inc. Page 151 of 316
February 25, 2011
Events MVI56-AFC ♦ ControlLogix Platform
User Manual Liquid and Gas Flow Computer
9.14 Downloading the Event Log in Firmware Version 2.05 and Earlier
For auditing purposes, each event has a "number" assigned sequentially, starting
at 0 for the first event written and increasing up through 65535 then wrapping to
0 again.
An event record properly includes its event number along with the information
listed in the preceding sections. To conserve space, and to make transmittal
more efficient, the event number is not stored as part of the event record.
Instead, the Event Log header contains sufficient information to calculate for any
event its event number from the position of its record in the Log and vice versa.
The following procedures use these terms:
Term Meaning
my_record Known record position.
Input to procedures (A) and (C)
event_number Desired event number.
Output from procedure (A).
Modbus_address Desired Modbus address.
Output from procedure (C).
my_event Known event number.
Input to procedure (B).
record_position Desired record position.
Output from procedure (B).
number_of_records Maximum number of records.
Contents of register 40000. In this version of the AFC
"number_of_records" is 1999; however, to be compatible with future
versions that may store a different number of events, an application
should use the value from the header instead of a constant 1999.
next_record Next new record position.
Contents of register 40001.
next_event Next new event number.
Contents of register 40002.
oldest_event Oldest event number on file.
Contents of register 40003.
oldest_not_downloaded Oldest event number not yet downloaded.
Contents of register 40004.
events_on_file Total number of events on file.
Calculated. This value starts at 0 upon cold start, then, as events are
logged, it rises to a maximum of "number_of_records" and stays there.
downloadable_event Event number of event being downloaded.
Calculated.
event_age The age of the event in question.
Calculated. The next event to be written (which of course is not yet on
file) has age 0; the newest event already on file has age 1, the next
older event has age 2, and so on up to age "number_of_records".
Page 152 of 316 ProSoft Technology, Inc.
February 25, 2011
MVI56-AFC ♦ ControlLogix Platform Events
Liquid and Gas Flow Computer User Manual
Also in these procedures:
a) The expression "AND 0x0000FFFF" means "take the low-order 16 bits of
the result, discarding all other higher-order bits"; it is equivalent to "(non-
negative) remainder upon dividing by 65536" (A traditionally negative
remainder that would result from dividing a negative dividend by 65536
must be made positive by subtracting its absolute value from 65536)
b) The operator ":=" means "assignment"; that is, "assign" the expression on
the right to the object on the left by calculating the value of the expression
on the right and making the object on the left assume that value. The
operator "==" means "is equal to".
c) Words in all caps and the other arithmetic operators have their expected
meanings.
d) Text enclosed in brackets ("[ ]") are comments only.
Procedure (A): Calculate event number from record position.
1 Calculate number of events on file.
events_on_file := ( next_event - oldest_event ) AND 0x0000FFFF
2 Determine whether desired record is on file.
IF ( my_record < 0 OR my_record ≥ events_on_file ) THEN
[record is not on file]
EXIT this procedure
3 Calculate age of desired record.
event_age := ( next_record - my_record )
IF ( event_age ≤ 0 ) THEN
event_age := event_age + number_of_records
4 Calculate event number of desired record.
event_number := ( next_event - event_age ) AND 0x0000FFFF
Procedure (B): Calculate record position from event number.
1 Calculate number of events on file.
events_on_file := ( next_event - oldest_event ) AND 0x0000FFFF
2 Calculate age of desired event.
event_age := ( next_event - my_event ) AND 0x0000FFFF
3 Determine whether desired event is on file.
IF ( event_age == 0 OR event_age > events_on_file ) THEN
[event is not on file]
EXIT this procedure
4 Calculate record position of desired event.
record_position := ( next_position - event_age )
IF ( record_position < 0 ) THEN
record_position := record_position + number_of_records
Procedure (C): Calculate Modbus address of record from record position.
1 Calculate number of events on file.
events_on_file := ( next_event - oldest_event ) AND 0x0000FFFF
2 Determine whether desired record is on file.
ProSoft Technology, Inc. Page 153 of 316
February 25, 2011
Events MVI56-AFC ♦ ControlLogix Platform
User Manual Liquid and Gas Flow Computer
IF ( my_record < 0 OR my_record ≥ events_on_file ) THEN
[record is not on file]
EXIT this procedure
3 Calculate Modbus address.
Modbus_address := ( my_record * 8 ) + 40008
Procedure (D): Download all events not yet downloaded.
The downloading application should download the entire Log, starting at the
oldest event not yet downloaded and extending through all newer events.
1 Fetch event number of oldest event not yet downloaded.
downloadable_event := oldest_not_downloaded
2 Determine whether any more events remain to be downloaded.
IF ( downloadable_event == next_event ) THEN
[all events have been downloaded]
EXIT this procedure
3 Download this event.
a) Calculate record number.
my_event := downloadable_event
record_position := { via Procedure (B) }
b) Calculate Modbus address.
my_record := record_position
Modbus_address := { via Procedure (C) }
c) Download the event with Modbus.
Set Modbus Function Code := 4, Read Input Registers
Set Modbus Number of Registers := 8
Set Modbus Register Address := Modbus_address
Execute
Copy the returned data to permanent storage
4 Step to next event and loop.
downloadable_event := ( downloadable_event + 1 ) AND 0x0000FFFF
GOTO step 2.
When the download is complete, and the downloaded events have been logged
to disk, the AFC should be told of this fact by issuing the "download complete"
Site Signal. This signal updates the header to show that all records have been
downloaded, unlocking the Log for further events, and (if "Event log unlocked" is
clear) posts a "download" event. A download may be performed at any time; it is
not necessary to wait for the log-full condition in order to download.
An application that downloads the event log should explicitly include the event
number in any copy of the event that it stores in its own database.
Page 154 of 316 ProSoft Technology, Inc.
February 25, 2011
MVI56-AFC ♦ ControlLogix Platform Security (Passwords)
Liquid and Gas Flow Computer User Manual
10 Security (Passwords)
In This Chapter
Hard Password .................................................................................... 157
The passwords are intended for interrogation by application software in order to
verify an operator’s authorization to make configuration changes and to view
measurement results. The passwords are resident in the module so that different
operators using different copies of the application software must use the same
password. Passwords cannot be retrieved in "Hard Password" mode. The
password protection is not used by default.
Passwords can be numbers between -32768 and 32767. For example, 1234. A
password of 0 (zero) is interpreted as "No password present".
The module supports two passwords: Write-Enable and Read-Only. Each
password is enabled when you write a non-zero value to the corresponding
register.
Password Holding Register Address Description
Write-Enable 9 Protects the module from write operations from the
AFC Manager
Read-Only 19 Protects the module from read or write operations
from the AFC Manager
ProSoft Technology, Inc. Page 155 of 316
February 25, 2011
Security (Passwords) MVI56-AFC ♦ ControlLogix Platform
User Manual Liquid and Gas Flow Computer
The following table shows how the passwords affect the AFC Manager operation
depending on the values that you configure:
Protection Level Read-Only Write-Enable Read Operation: Requires Write Operation: Requires
Password Password Authorization? Authorization?
No protection Zero Zero No No
Write Protection Zero Non-zero No Yes (Use Write-Enable
password)
Read and Write Non-zero Zero Yes (Use Read-Only Yes (Use Read Only password)
Protection password)
Read and Write Non-zero Non-zero Yes (Use Read-Only or Yes (Use Write-Enable
Protection Write-Enable password) password)
Each port can be assigned to different password protection levels. Refer to the
Port Configuration Section for more information about this topic.
Page 156 of 316 ProSoft Technology, Inc.
February 25, 2011
MVI56-AFC ♦ ControlLogix Platform Security (Passwords)
Liquid and Gas Flow Computer User Manual
10.1 Hard Password
The hard password feature offers further protection against unauthorized access
to the module.
If the Hard Password option is cleared, these registers can be read either from
an external Modbus device, from the processor or using the Modbus Master
interface in the AFC Manager. This operation mode is called "Soft Password"
mode. It is then the responsibility of a compatible application (such as AFC
Manager) to verify the password given by the operator against those fetched
from the module in order to determine the access granted.
If the Hard Password option is selected, a read of a password register will return
zero regardless of the password’s actual value. In this case, read or write access
is obtained by writing a candidate password to the Password Test register
(register 18), the module itself verifies the password, and the access granted is
determined by reading back that same register 18 (called the Accessed Port and
Authorization register when read) and examining its contents. The access is
granted to the port over which the request was made; other ports remain
unaffected. If the port remains idle with no Modbus activity for two minutes, then
the granted access is removed and can be regained only by writing a new
password to the test register. For highest security, you can explicitly revoke your
own password-obtained authorization before it times out by writing zero to the
Password Test register.
Access granted by password, whether Soft or Hard, is to the module as a whole,
including the password registers themselves. That is, in order to change a stored
Hard password you must first obtain write access to the module by giving the
correct Write-Enable password. However, some registers are exempt from
authorization. There are a very few registers that are exempt from write
authorization and are always writable; the Password Test register 18 is one such
for the obvious reason. Similarly, some registers are exempt from read
authorization and are always readable; they include most of the first 20 holding
registers, including the Firmware Product and Group codes in registers 0 and 1
(so an application like AFC Manager can learn whether it is talking to an AFC
without being trapped in a catch-22), the Site Status in register 6 (so the
application can learn whether the password mode is Soft or Hard and verify the
operator’s password entry using the proper method), and the Accessed Port and
Authorization register 18 (so the application can learn whether access was
granted in Hard-password mode even if the wrong read password was entered).
ProSoft Technology, Inc. Page 157 of 316
February 25, 2011
Security (Passwords) MVI56-AFC ♦ ControlLogix Platform
User Manual Liquid and Gas Flow Computer
The Accessed Port and Authorization register is a bit-mapped word defined as
follows:
Bits Description
0 to 3 The number of the accessing port (0 for Modbus Gateway)
4 Read Authorization Waived
5 Write Authorization Waived
6 Read Access Granted
7 Write Access Granted
8 to 15 Reserved
A waived authorization means that password entry is not required for this action
even if a non-zero password has been configured. Authorization waivers are
configured separately for each port, so, for example, a SCADA system
connected to port 2 can be allowed to read measurement results without having
to supply a password while an operator connecting AFC Manager to port 1 still
must enter the correct password. The backplane is always given both waivers, so
the PLC never has to supply a password.
To set a hard password in AFC Manager:
1 Open the Site Configuration Dialog box
2 Click in the Site Options field. This action opens the Site Options dialog box
3 Select (check) option 4, Hard Passwords
When this option is selected, any authorization granted using Hard Passwords
times out after two minutes of inactivity, and the user will be required to re-enter
the password to continue.
Page 158 of 316 ProSoft Technology, Inc.
February 25, 2011
MVI56-AFC ♦ ControlLogix Platform MVI56-AFC Backplane Communication
Liquid and Gas Flow Computer User Manual
11 MVI56-AFC Backplane Communication
In This Chapter
MVI56-AFC Module Data Transfer ...................................................... 160
MVI56-AFC Function Block Interface .................................................. 167
ProSoft Technology, Inc. Page 159 of 316
February 25, 2011
MVI56-AFC Backplane Communication MVI56-AFC ♦ ControlLogix Platform
User Manual Liquid and Gas Flow Computer
11.1 MVI56-AFC Module Data Transfer
11.1.1 Input/Output Blocks for Data Transfer
When you configure the MVI56-AFC module to the I/O configuration of your
ControlLogix controller, the tags of the Output Block Array (OBA) and the Input
Block Array (IBA) for the module are automatically created as controller tags by
the RSLogix5000 programming software.
Output Block Array
Size: 248 elements Data type: Integer (2 bytes)
The OBA is used for transferring process variables from individual meter runs
and other data that are available in the ControlLogix processor memory to your
AFC module via the backplane. This array is made up of a block of 248
contiguous integer elements.
Element Attribute
Local 3.O (slot number) Local.O.Data[0]
Local.O.Data[1]
Local.O.Data[2]
………………..
Local.O.Data[n]
………………..
Local.O.Data[247]
The meter run process variables such as temperature, pressure, differential
pressure, meter pulses, and so on. may come from other I/O modules in the rack
or from other sources like an HMI and so on. These variables must be copied to
predefined structured function blocks which transfer them to the AFC module as
part of one or more OBAs.
Page 160 of 316 ProSoft Technology, Inc.
February 25, 2011
MVI56-AFC ♦ ControlLogix Platform MVI56-AFC Backplane Communication
Liquid and Gas Flow Computer User Manual
Input Block Array
Size: 250 elements Data type: Integer (2 bytes)
The AFC consumes the process variable inputs received in the OBAs and
returns calculated variables such as process flowrate, accumulated product
volume, and so on. by populating the IBA and returning it to the ControlLogix
processor via the backplane. This array is made up of a block of 250 contiguous
integer elements.
Element Attribute
Local 3.I (slot number) Local.I.Data[0]
Local.I.Data[1]
Local.I.Data[2]
………………..
Local.I.Data[n]
………………..
Local.I.Data[249]
The following section describes in detail how the MVI56-AFC module facilitates
the two-way data transfer by conveniently partitioning the Input/Output blocks
into smaller function blocks to allow flexibility in designing and implementing the
logic to support the AFC module.
ProSoft Technology, Inc. Page 161 of 316
February 25, 2011
MVI56-AFC Backplane Communication MVI56-AFC ♦ ControlLogix Platform
User Manual Liquid and Gas Flow Computer
11.1.2 Input/Output Transactions
The MVI56-AFC module runs automatically on power up. It receives the process
variables from the ControlLogix controller through the associated output block
array and returns the calculated results back through the Input Block Array.
The data transfer to and from the MVI56-AFC module is implemented through
processor logic, using the concept of Transactions to establish an interface
between the AFC module and the ControlLogix Controller. A transaction is a
transfer of a pre-assembled block of data words between the controller and the
AFC module. The AFC module supports a block multiplexing scheme whereby
you may set up a number of Output Block Arrays (OBAs) with corresponding
Input Block Arrays (IBAs) for two way data transfer. This is done by giving each
OBA a unique non-zero Transaction Identifier number. The AFC module will not
process an OBA unless the Transaction Identifier number of the current OBA is
different from the previous one.
Output (Transaction) Block Array Definition
The 248 integer elements of the OBA that must be formatted in the controller
ladder logic program are defined as follows:
Element # Attribute
0 Sentinel (Transaction Number)
1
Output Block Array Length (≤245)
2
3
4 Space for User Allocated Sub Blocks
. (Total Available Elements = 245)
.
.
.
244
245
246
247 Anchor (Transaction Number)
The AFC module recognizes an OBA as valid only if all three of the following
conditions are true:
1 The values of the sentinel and the anchor are the same (this is called the
"transaction number").
2 The transaction number (sentinel & anchor) is non-zero.
3 The transaction number is different from the preceding one.
AFC Response to an OBA
Each time the AFC module receives an OBA, it processes this array and returns
a corresponding Input Block Array (IBA) with the same transaction number so
that the processor logic can act upon the AFC's response to the data it received
in the OBA. The OBA description follows.
Page 162 of 316 ProSoft Technology, Inc.
February 25, 2011
MVI56-AFC ♦ ControlLogix Platform MVI56-AFC Backplane Communication
Liquid and Gas Flow Computer User Manual
Sentinel & Anchor (Transaction Number)
In order to allow the AFC to tell each Output Block Array apart, a unique
Transaction Identifier number is assigned to each transmit block. This
Transaction Identifier number is assigned to the top and bottom elements of the
transaction block to ensure data transfer integrity. The top transaction identifier is
called the Transaction Number Sentinel and the bottom transaction identifier is
called the Transaction Number Anchor.
Output Block Length
The element immediately following the sentinel contains the length of the data
portion, not including the sentinel, the anchor, or the Output Block Length
element itself; hence its maximum value is 245. If the output data block you
configured is less than 245 elements, unused elements between the end of the
data block and the anchor are ignored on output (to the AFC) and returned as
zero on input (from the AFC).
ProSoft Technology, Inc. Page 163 of 316
February 25, 2011
MVI56-AFC Backplane Communication MVI56-AFC ♦ ControlLogix Platform
User Manual Liquid and Gas Flow Computer
Output Function Blocks (OFB)
The architecture of the Output Block Array provides you with a flexible and
powerful way to interface the process and other data to the AFC module. A
number of pre-defined Output Function Blocks are at your disposal to implement
as required. Each Output Function Block type carries out a specific function. For
example, the Meter Process Variable Output Function Block transfers the
process variables (temperature, pressure, meter pulses, and so on) to a specific
target meter channel in the AFC module. The calculated flow rates, product
accumulators, and so on are returned to the controller by the AFC in the
associated Input Function Block (IFB) as part of the Input Block Array (IBA). In
the same way a Wall Clock Function Block allows you to synchronize the AFC
Wall Clock to the processor Wall Clock. Like Lego blocks of various sizes, these
function blocks can be stacked together in the data portion of the Output Block
Array as shown in the following diagram:
Element # Attribute
0 Sentinel (Transaction Number)
1 Output Block Length (OBL<=245)
2
Global 3
Wall Clock
Function Block: 7
Elements
Meter 2 . Space for User Allocated Function Blocks
Process Variable
Function Block:
12 Elements
Meter 3 . (Total Available Elements = 245)
Process Variable
Function Block:
12 Elements
Meter 3 57
Analysis
Function Block:
25 Elements
.
.
244
245
246
247 Anchor (Transaction Number)
Page 164 of 316 ProSoft Technology, Inc.
February 25, 2011
MVI56-AFC ♦ ControlLogix Platform MVI56-AFC Backplane Communication
Liquid and Gas Flow Computer User Manual
Input (Transaction) Block Array Definition
The Input Block Array is where the AFC returns the (processed and calculated
data) responses to all function blocks received in the Output Block Array from the
controller. It returns Input Function Blocks in locations and sizes matching those
of the OFBs in the OBA. The AFC completes the actions implied by all function
blocks before responding with the IBA to the controller. If the AFC is unable to
determine the size of any function block, or the implied size overlaps the block
array’s anchor, then that and all following function blocks are not processed and
a format alarm is raised.
The 250 integer elements of the Input (Transaction) Block Array (IBA) that are
returned to the controller to the AFC module are defined as follows:
Element Attribute
0 Sentinel Echo (Transaction Number)
1 Block length echo (IBL) (Negative if formatting error present)
2
3
4 Space for Input Image of User Allocated Function Blocks
. (Total Available Elements = 245)
.
.
.
244
245
246
247 Site Status
Bit # Site Status
0 MVI56-AFC Released and Active
1 Checksum Alarm
2 Reserved
3 Reserved
4 Processor Halted, Offline or Missing
5 Measurement Configuration Changed
6 Set upon Power-Up & cleared when the Wall Clock is set for the first
time
7 Cold Start: remains set until first enabled meter is detected
8 Modbus Master poll pending
9 Modbus Master poll complete, results waiting
10 Pass-Thru input pending
11 version 2.06 or later
12 to 15 Reserved
248 Meter Alarm Map: Bit
Frequently asked questions
What makes Elite.Parts unique?

What kind of warranty will the MVI56103M have?

Which carriers does Elite.Parts work with?

Will Elite.Parts sell to me even though I live outside the USA?

I have a preferred payment method. Will Elite.Parts accept it?

What they say about us
FANTASTIC RESOURCE
One of our top priorities is maintaining our business with precision, and we are constantly looking for affiliates that can help us achieve our goal. With the aid of GID Industrial, our obsolete product management has never been more efficient. They have been a great resource to our company, and have quickly become a go-to supplier on our list!
Bucher Emhart Glass
EXCELLENT SERVICE
With our strict fundamentals and high expectations, we were surprised when we came across GID Industrial and their competitive pricing. When we approached them with our issue, they were incredibly confident in being able to provide us with a seamless solution at the best price for us. GID Industrial quickly understood our needs and provided us with excellent service, as well as fully tested product to ensure what we received would be the right fit for our company.
Fuji
HARD TO FIND A BETTER PROVIDER
Our company provides services to aid in the manufacture of technological products, such as semiconductors and flat panel displays, and often searching for distributors of obsolete product we require can waste time and money. Finding GID Industrial proved to be a great asset to our company, with cost effective solutions and superior knowledge on all of their materials, it’d be hard to find a better provider of obsolete or hard to find products.
Applied Materials
CONSISTENTLY DELIVERS QUALITY SOLUTIONS
Over the years, the equipment used in our company becomes discontinued, but they’re still of great use to us and our customers. Once these products are no longer available through the manufacturer, finding a reliable, quick supplier is a necessity, and luckily for us, GID Industrial has provided the most trustworthy, quality solutions to our obsolete component needs.
Nidec Vamco
TERRIFIC RESOURCE
This company has been a terrific help to us (I work for Trican Well Service) in sourcing the Micron Ram Memory we needed for our Siemens computers. Great service! And great pricing! I know when the product is shipping and when it will arrive, all the way through the ordering process.
Trican Well Service
GO TO SOURCE
When I can't find an obsolete part, I first call GID and they'll come up with my parts every time. Great customer service and follow up as well. Scott emails me from time to time to touch base and see if we're having trouble finding something.....which is often with our 25 yr old equipment.
ConAgra Foods