POSYS 804-B
Specifications
Acceleration and deceleration ranges
-32,768 to +32,767 counts/sample² with a resolution of 1/65,536 counts/ sample²
Analog input
8 x 10-bit analog inputs (0 - 4.096 V)
Available configurations
4 axes (POSYS 824-B, 804-B), 2 axes (POSYS 822-B, 802-B) fully compliant PC104-Bus card
Communication modes
16/16 parallel, RS232/RS485
Commutation rate (822-B, 824-B only)
20 KHz
Electronic gear ratio range
-32,768 to +32,767 with a resolution of 1/65,536 (negative and positive direction)
Emergency stop
5V TTL input (either for smooth stop, abrupt stop or motor off) uses the AxisIn signal
Filter modes (not for step motor versions)
Scalable PID + Velocity feedforward + Acceleration feedforward +Bias. Also integration limit, settable derivative sampling time, and output motor command limiting
Filter parameter resolution (not for step motor versions)
16 bits
Hall sensor inputs (822-B, 824-B version only)
3 Hall effect inputs per axis (TTL level signals)
I/Os
8 digital inputs / TTL, active low, 4 axis specific inputs, 8 digital outputs / TTL, active low, 4 digital outputs for amplifier enable, 4 axis specific outputs, 8 analog inputs (0 - 4.096 Volts)
Jerk range
0 to ½ counts/sample³, with a resolution of 1/4,294,967,296 counts/sample³
Limit switches
2 per axis: one for each direction of travel, digitally filtered
Master/Slave change
Automatic Master/Slave change possible if programmed in user-defined software
max. Number of traceable variables to compare at the same time
4
Maximum encoder rate
Incremental (up to 5 Mcounts/sec; optionally 8 Mcounts/s.) Parallel-word (up to 160 Mcounts/sec). optional interpolation module allows increase of encoder resolution up to x16000
Motor output modes
DAC: 16 bits ±10V output. PWM: 10-bit resolution at 20 KHz or 8-bit at 80 KHz. 50/50 supports 1, 2 or 3 phase motors (multiple phase only 822-B, 824-B). Sign magnitude supports 1 & 2 phase motors only (multiply phase only 822-B, 824-B)
Number of host instructions
180-200
Number of trace variables
28
On the fly control
of profile and filter parameters with pre-load and individual axis or simultaneous multi-axes update
Operating modes
Closed loop (motor command is driven from output of servo filter). Open loop (motor command is driven from user-programmed register)
Operating temperature extended
-40° - +85° C (option).
Other digital signals (per axis)
1 AxisIn signal per axis, 1 AxisOut signal per axis
Parallel encoder read rate
20 KHz (reads all axes every 50 µsec)
Parallel encoder word size
16 bits
Position error tracking
Motion error window (allows axis to be stopped upon exceeding programmable window). Tracking window (allows flag to be set if axis exceeds a programmable position window)
Position range
2,147,483,648 to +2,147,483,647 counts
Position-capture triggers: 2 per axis
index and home signals (high speed position latch)
Power
5 VDC, 1
Profile modes
S-curve point-to-point (Velocity, acceleration, jerk and position parameters Trapezoidal point-to-point (Velocity, acceleration, deceleration, and position parameters) Velocity-contouring (Velocity, acceleration, and deceleration parameters) Electronic Gear (Encoder or trajectory position of one axis used to drive a second axis. Master and slave axes and gear ratio parameters)
RAM memory support
512 single port RAM. Trace modes:one-time, continuous
Servo loop timing range
1 axis: 102.4 µsec, 2 axes: 204.8 µsec, 3 axes; 307.2 µsec, 4 axes: 409.6 µsec minimum cycle time.
Software-invertable signals
Encoder A, Encoder B, Index, Home, AxisIn, AxisOut, PositiveLimit, NegativeLimit (all individually programmable per axis)
Special profile mode combinations
Trapezoidal mode with Electronic gearing. S-curve mode with Electronic gearing
Velocity range
32,768 to +32,767 counts/sample with a resolution of 1/65,536 counts/ sample
Datasheet
Extracted Text
SPECIFICATIONS • Available configurations: Sign magnitude supports 1 & 2 phase motors only (multiply phase only 822-B, 4 axis specific inputs 4 axes (POSYS® 824-B, 804-B), 2 axes (POSYS® 822-B, 802-B) fully 824-B) 8 digital outputs / TTL, active low compliant PC104-Bus card 4 digital outputs for amplifier enable • Hall sensor inputs (822-B, 824-B version only): 4 axis specific outputs • Operating modes: 3 Hall effect inputs per axis (TTL level signals) 8 analog inputs (0 - 4.096 Volts) Closed loop (motor command is driven from output of servo filter) • Commutation rate (822-B, 824-B only): Open loop (motor command is driven from user-programmed register) • Special profile mode combinations: 20 KHz Trapezoidal mode with Electronic gearing • Communication modes: • Maximum encoder rate: S-curve mode with Electronic gearing 16/16 parallel, RS232/RS485 Incremental (up to 5 Mcounts/sec; optionally 8 Mcounts/s.) • Master/Slave change: • Position range: Parallel-word (up to 160 Mcounts/sec) Automatic Master/Slave change possible if programmed in user-defined -2,147,483,648 to +2,147,483,647 counts optional interpolation module allows increase of encoder resolution up to software x16000 • Velocity range: • Motor check: -32,768 to +32,767 counts/sample with a resolution of 1/65,536 counts/ • Parallel encoder word size: programmable max. motion error with or without automatic motor shutdown sample 16 bits • Connectors: • Acceleration and deceleration ranges: • Parallel encoder read rate: 2x 50-position IDC connector and 1x additional 50-position IDC connector on -32,768 to +32,767 counts/sample² with a resolution of 1/65,536 counts/ 20 KHz (reads all axes every 50 µsec) 822-B/824-B sample² • Servo loop timing range: • Dimensions: • Jerk range: 1 axis = 102.4 µsec, 2 axes = 204.8 µsec, 3 axes = 307.2 µsec, 4 axes = half size PC104-Bus card; (110 x 96 mm) 0 to ½ counts/sample³, with a resolution of 1/4,294,967,296 counts/sample³ 409.6 µsec minimum cycle time. • Temperature range: • Profile modes: • Limit switches: Operating temperature standard; 0° - 70° C S-curve point-to-point (Velocity, acceleration, jerk and position parameters 2 per axis: one for each direction of travel, digitally filtered Operating temperature extended: -40° - +85° C (option) Trapezoidal point-to-point (Velocity, acceleration, deceleration, and position • Position-capture triggers: parameters) • Power: 2 per axis: index and home signals (high speed position latch) Velocity-contouring (Velocity, acceleration, and deceleration parameters) 5 VDC, 1A • Other digital signals (per axis): Electronic Gear (Encoder or trajectory position of one axis used to drive a 1 AxisIn signal per axis, 1 AxisOut signal per axis second axis. Master and slave axes and gear ratio parameters) OPTIONS: • Software-invertable signals: • On the fly control: Encoder A, Encoder B, Index, Home, AxisIn, AxisOut, PositiveLimit, Cable800-B of profile and filter parameters with pre-load and individual axis or simultaneous NegativeLimit (all individually programmable per axis) Matching flat cable, 50 positions to 50 positions, 1m long; 1, 2 or 3 needed multi-axes update depending on model and # of axes • Analog input: • Electronic gear ratio range: 8 x 10-bit analog inputs (0 - 4.096 V) -32,768 to +32,767 with a resolution of 1/65,536 (negative and positive IO700/800-1 Interface direction) • RAM memory support: interface and interconnect board (1 for each set of 4 axes); 512 single port RAM • Filter modes (not for step motor versions): Mounting: Phoenix EN snap-on rail Scalable PID + Velocity feedforward + Acceleration feedforward +Bias. Also • Trace modes: integration limit, settable derivative sampling time, and output motor command one-time MotionScript® Software limiting continuous for servo-tuning, maintenance, diagnostics and system performance check with graphical output • Filter parameter resolution (not for step motor versions): • Number of trace variables: 28 16 bits • max. Number of traceable variables to compare at the same time: 4 Windows Software • Position error tracking: • Number of host instructions: 180-200 GUI sample program Motion error window (allows axis to be stopped upon exceeding programmable DLL for Delphi & C/C++ • Emergency stop: window) Driver for Windows XP/Vista/7 optionally also for Linux 5V TTL input (either for smooth stop, abrupt stop or motor off) uses the AxisIn Tracking window (allows flag to be set if axis exceeds a programmable position signal window) • I/Os: • Motor output modes: 8 digital inputs / TTL, active low DAC: 16 bits ±10V output PWM: 10-bit resolution at 20 KHz or 8-bit at 80 KHz 50/50 supports 1, 2 or 3 phase motors (multiple phase only 822-B, 824-B)
Frequently asked questions
What makes Elite.Parts unique?

What kind of warranty will the 804-B have?

Which carriers does Elite.Parts work with?

Will Elite.Parts sell to me even though I live outside the USA?

I have a preferred payment method. Will Elite.Parts accept it?

Why buy from GID?
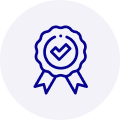
Quality
We are industry veterans who take pride in our work
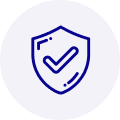
Protection
Avoid the dangers of risky trading in the gray market
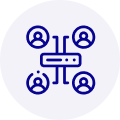
Access
Our network of suppliers is ready and at your disposal
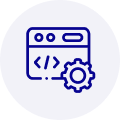
Savings
Maintain legacy systems to prevent costly downtime
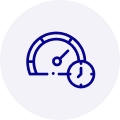
Speed
Time is of the essence, and we are respectful of yours
What they say about us
FANTASTIC RESOURCE
One of our top priorities is maintaining our business with precision, and we are constantly looking for affiliates that can help us achieve our goal. With the aid of GID Industrial, our obsolete product management has never been more efficient. They have been a great resource to our company, and have quickly become a go-to supplier on our list!
Bucher Emhart Glass
EXCELLENT SERVICE
With our strict fundamentals and high expectations, we were surprised when we came across GID Industrial and their competitive pricing. When we approached them with our issue, they were incredibly confident in being able to provide us with a seamless solution at the best price for us. GID Industrial quickly understood our needs and provided us with excellent service, as well as fully tested product to ensure what we received would be the right fit for our company.
Fuji
HARD TO FIND A BETTER PROVIDER
Our company provides services to aid in the manufacture of technological products, such as semiconductors and flat panel displays, and often searching for distributors of obsolete product we require can waste time and money. Finding GID Industrial proved to be a great asset to our company, with cost effective solutions and superior knowledge on all of their materials, it’d be hard to find a better provider of obsolete or hard to find products.
Applied Materials
CONSISTENTLY DELIVERS QUALITY SOLUTIONS
Over the years, the equipment used in our company becomes discontinued, but they’re still of great use to us and our customers. Once these products are no longer available through the manufacturer, finding a reliable, quick supplier is a necessity, and luckily for us, GID Industrial has provided the most trustworthy, quality solutions to our obsolete component needs.
Nidec Vamco
TERRIFIC RESOURCE
This company has been a terrific help to us (I work for Trican Well Service) in sourcing the Micron Ram Memory we needed for our Siemens computers. Great service! And great pricing! I know when the product is shipping and when it will arrive, all the way through the ordering process.
Trican Well Service
GO TO SOURCE
When I can't find an obsolete part, I first call GID and they'll come up with my parts every time. Great customer service and follow up as well. Scott emails me from time to time to touch base and see if we're having trouble finding something.....which is often with our 25 yr old equipment.
ConAgra Foods