POROUS MEDIA LE6439HSCV
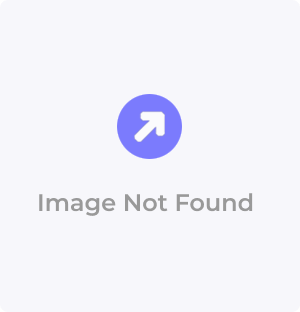
Description
Porous Media LE6439HSCV Genesis Coreless Filter Element
Part Number
LE6439HSCV
Price
Request Quote
Manufacturer
POROUS MEDIA
Lead Time
Request Quote
Category
PRODUCTS - L
Datasheet
Extracted Text
369
MOTOR
PROTECTION SySTEM
Integrated protection and control
for medium sized AC motors
KEy BENEFITS
• Enhanced Thermal Model including RTD and Current • Field upgradable settings and firmware
Unbalance Biasing
• Suitable for hazardous locations - UL certification for Class
• Complete Asset monitoring with programmable RTD inputs 1 Division 2 applications (option MOD502)
for Stator, Bearing and Ambient temperature protection
• Installation flexibility - Remote display and remote RTD
• Enhanced reporting - Motor Health Reports provide critical options
information for preventative maintenance
• Safe and reliable motor re-start on “Down Hole” pump
• Reduce troubleshooting time and maintenance costs applications - Unique back spin detection feature detects
-Event reports, waveform capture, motor start data logger flow reversal on a pump motor, enabling timely and safe
motor restarting
• Multiple communication protocols - Modbus RTU, Profibus,
DeviceNet, Modbus TCP/IP • User definable parameters and data size for DeviceNet
polling
TM
• Simplified programming with the EnerVista 369 Motor
Settings Auto-Configurator • User definable parameters and data size for Profibus DPV1
cyclic data
• Optional Conformal coating for exposure to chemically
corrosive or humid environments (option) • Motor learned data on historical start characteristics
APPLICATIONS
• Protection and control for medium sized AC motors • Suitable for applications involving Variable Frequency
Drives
• “Down Hole” pump applications
• Two Speed motor application
FEATURES
Monitoring and Metering
Protection and Control
• Metering - current, voltage, power, energy, frequency, RTD
• Enhanced thermal model
Temperature, Remote RTD
• Stall / Jam protection
• Fault diagnosis, - Event Record, Oscillography, Motor Starting
• Undervoltage, overvoltage
Data Logger
• Underfrequency
• Motor Health Report
• Thermal overload
• Statistical information & learned motor data
• Undercurrent/current unbalance
• Voltage/frequency/power display (M option)
• Variable lockout time
• 4 analog outputs (M option)
• Overtemperature 12 RTDs (R option)
Communications
• Starts/hour, time between starts
• Front Panel RS232 port for programming and troubleshooting
• Voltage Phase Reversal (M option)
• Optional embedded Ethernet port
• Current based phase reversal
• Optional Profibus DP/DPV1 or DeviceNet via dedicated port
• Undervoltage Auto-restart
• Multiple Protocols - Modbus RTU, Modbus TCP/IP
User Interface
TM
EnerVista Software
• 40 Character LCD Display
• State of the art software for configuration and
• 10 System and Motor Status LED’s
commissioning GE Multilin products
• Keypad for configuration and viewing metered values
• Document and software archiving toolset to ensure
reference material and device utilities are up-to-date
• 4 programmable analog outputs
TM
• EnerVista Integrator providing easy integration of data
• 369 Motor Settings Auto-Configurator
in the 369 into new or existing monitoring and control
systems
Digital Energy
Multilin
g 407
Motor Protection
369 Motor Protection System
6500 H P, 138 00 Volt INDUCED DRAFT FAN M OTOR
Protection & Control 10000
10,000
The 369 is a digital motor protection
1 PROGRAMMED 369 CUSTOM CURVE
RUNNING SAFETIME (STATOR LIMITED)
2
system designed to protect and manage
3 ACCELERATION SAFETIME (ROTOR LIMITED )
medium sized AC motors and their driven
4 MOTOR CURRENT @ 100% VO LTAGE
1000
5 MOTOR CURRENT @ 80% VO LTAGE
equipment. It contains a full range of
selectively enabled, self contained
1,000
1
protection and control elements as
2
100
detailed in the Functional Block Diagram
and Features table.
100
3
Motor Thermal Model
10
The primary protective function of the
369 is the thermal model with six key
4
elements:
CU RVE
5
15
1.0
12
10
9
• 7
Overload Curves
4
•
Unbalance Biasing
3
2 0.1
•
Hot/Cold Safe Stall Ratio
MULTIPLE OF FULL LOAD CURRENT SETPOINT
1
• 1
Motor Cooling Time Constants
1 TM
0.1 10
Typical FlexCurve
Ful l Load
•
Start Inhibit and Emergency Restart
S etpoint
PHASE CURRENT
(MULTIPLES OF FULL LOAD)
•
RTD Biasing
Fifteen standard overload curves
FlexCurves™
Overload Curves
A smooth custom overload curve is created
determines where the running overload
The curves can take one of two formats: using FlexCurves™. These curves can
curve begins.
standard or custom. For all curve styles, the be used to protect motors with different
The 369 standard overload curves are of
369 retains thermal memory in a thermal rotor damage and stator damage curves,
standard shape with a multiplier value of
capacity used register which is updated allowing total motor design capacity with
1 to 15.
every 0.1 second. The overload pickup complete protection.
Functional Block Diagram
BACKUP ANSI Device Numbers & Functions
Device
52
50 50G
Function
Number
OPTIONAL METERING (M)
14 Speed Switch
4 ISOLATED
METERING 27P/59P Undervoltage/Overvoltage
BUS
55
V, W, Var, VA , P F, Hz
ANALOG
37 Undercurrent/Underpower
V V
OUTPUTS
38 Bearing RTD
27P 47 59P
46 Current Unbalance
47 Phase Reversal
BREAKER
OR FUSED AUXILIARY
TRIP 49 Stator RTD
CONTACTOR RELAY
50 Short Circuit and Short Circuit Backup
50G/51G Ground Overcurrent and Ground
Overcurrent backup
74
49 Overload
ALARM
RELAY 51R Mechanical Jam
52a/b
55 Power Factor
METERING
66 Starts/Hour & Time Between Starts
3 50 49 37 66 46 51R
A , Celsius
81O/U Frequency
S TA RT
CONTROL
AMBIENT AIR 86 Overload Lockout
87M Differential
51G 50G
SPEED DEVICE
14 14
INPUTS
86
369
LOA D
RTD s M OTOR
Motor Management System
RS232
DIFFERENTIAL
87 87M
RS485
Relay Contacts
RS485
Comm. to
RS485
RTD Module
BEARING
Optional RTD (R)
STATOR 49 38
12 RTD Inputs
AMBIENT
S TATOR
Remote RTD
(Fiber Optic)
Module BEARING
(Option F)
(12 RTD Inputs)
AMBIENT
408 408 408
Motor Protection
TRIP TIME (seconds)
TIME TO TRIP IN SECOND S
0.5
0.6
0.7
0.8
0.9
1
2
3
4
5
6
7
8
9
10
20
30
40
50
60
70
80
90
100
200
300
400
500
600
700
800
900
1000
369 Motor Protection System
Thermal Capacity Used
Unbalance (Negative Sequence
Current) Biasing
100
Negative sequence current, which causes
rotor heating, is not accounted for in 90
the thermal limit curves supplied by the
80
motor manufacturer. The 369 relay can
FLC Reduction S et @ 20 %
70
be programmed to calculate the negative & 100% FLC .
60
sequence current, and bias the thermal
model to reflect the additional heating.
50
FLC Reduction Set @ 8%
& 40% FLC
40
RTD Biasing (Relay Option R)
30
The thermal overload curves are based
solely on measured current, assuming a
20
normal 40°C ambient and normal motor
10
cooling. If the motor cooling systems fail,
0.00
or if the ambient temperature is unusually
TIME
( S econds X 10)
0.00 27 55 82 110 137 165 192 220 247
high, standard overload protection will not
Motor cooling curves
detect the increase in temperature.
When ordered with the RTD option, the 369
ground or residual ground currents. The
Undercurrent (Minimum Load)
can monitor the actual motor temperature,
ground fault trip can be instantaneous or
and calculate the Thermal Capacity Used
The undercurrent function is used to detect
time delayed by up to 255 seconds. A low
(TCU) based on the RTD Bias curve. This
a decrease in motor current caused by a
level of ground fault pickup is desirable to
TCU value will then be compared with the
decrease in motor load. This is especially
protect as much of the stator winding as
TCU determined by the overload curve.
useful for indication of conditions such as
possible. A 50:0.025 A CT, 1 A or 5 A CT may
The higher of the two values will be used.
loss of suction for pumps, loss of airflow
be used for ground fault detection.
For RTD temperatures below the RTD
for fans, or a broken belt for conveyors. A
BIAS MINIMUM setting, no biasing occurs.
separate undercurrent alarm level may be
Rapid Trip/Mechanical Jam
For maximum stator RTD temperatures
set to provide early warning.
During Overload conditions, quick motor
above the RTD BIAS MAXIMUM setting, the
Ground Overcurrent shut down can reduce damage to gears,
thermal memory is fully biased and forced
bearings, and other mechanical parts
to 100%.
For zero sequence ground overcurrent
associated with the drive combination. The
protection, all three of the motor
Cool Time Constants Mechanical Jam protection will operate
conductors must pass through a separate
for currents above a user-programmable
The 369 has a true exponential cooldown
ground CT. CTs may be selected to detect
pickup level.
characteristic which mimics actual motor
either high-impedance zero sequence
cooling rates, provided that motor cooling
time constants are available for both the
stopped and running cases. when ordered
with the RTD option, the stopped and
100%
running cool time constants will can be
calculated by the 369 based on the cooling
rate of the hottest stator RTD, the hot/cold
stall ratio, the ambient temperature (40
75%
Factory Preset Curve
° C if no ambient RTD), the measured
THERMAL
Min.= 40C,
CAPACIT Y
motor load and the programmed
USED
Center = 110C
service factor or overload pickup. & Max.= 155C
Center Thermal Capacity = 15%
50%
Start Inhibit
The Start Inhibit function prevents starting
25% RTD BIAS
CENTER T.C.
of a motor when insufficient thermal
15%
capacity is available or a motor start
MAXIMUM
supervision function dictates the start
STATOR
TEMPERATUR E
0%
inhibit.
0C 40C 80C 120C 160C 200C
110C 155C
RTD BIAS
RTD BIAS RTD BIAS
MIN. VALUE
CENTER VALUE MAX. VALUE
RTD bias curve sample
409 409 409
Motor Protection
369 Motor Protection System
position of the breaker (open or closed),
RTD Protection (Relay Option R)
Inputs and Outputs
and should be used with any synchronous
The 369 R option provides a total of 12
The 369 features a variety of digital
machine, or induction motor that may run
programmable RTD inputs that are used
input and output channels. Any of the
unloaded.
for monitoring the Stator, Bearing and
programmable digital inputs may be
ambient temperatures. Each RTD input
selected and programmed as a separate
Remote Reset
has 3 operational levels: alarm, high alarm
General Switch, Digital Counter, or
This input can be used for remote or
and trip. The 369 supports RTD trip voting
Waveform Capture Input. In addition the
automatic reset from a control switch, a
and provides open and short RTD failure
programmable digital inputs may be
PLC, or a DCS output.
alarms. Alternatively, a remote RTD module
selected and programmed to perform
(RRTD) can also be used with the 369 for
Outputs
one of the following functions: Emergency
temperature monitoring.
Restart, Differential Switch, Speed Switch,
The 369 has four output relay contacts. The
or Remote Reset as described below.
trip relay acts as the main latched output
Back-Spin Detection (Option B)
relay. An alarm and two auxiliary output
The Back-Spin Detection option is used Setpoint Access
relays are also provided. The Alarm and
to detect flow reversal of a pump motor
These terminals must be shorted together
Auxiliary 1 relays may be programmed for
when check valves are not functioning
in order to store new setpoints using the
latched or unlatched modes. All relays may
or are non-existent. Once the pump has
relay keypad.
be programmed fail-safe or non fail-safe.
stopped rotating, the Back-Spin Detection
option will allow the pump to safely restart,
Emergency Restart
Analog Outputs (Option M)
minimizing downtime and preventing
It may be necessary to restart a faulted
Three optional isolated analog outputs
motor damage.
motor for reasons of production or safety.
are provided (in addition to the single
The Back-Spin Detection option uses
To override a start inhibit or overload
analog output available in the base
sensitive circuits to detect the voltage
trip lockout condition, the emergency
model). Use the configurable analog
produced by the back-spinning motor.
restart feature can be used. This clears
outputs to provide standard transducer
Digital signal processing techniques
the thermal memory, allowing a manual
signals to local monitoring equipment.
determine the direction of rotation and
reset and restart. The 369 can also be
They can be field selected as 0 to 1,
predict the pump stop time. The metering
programmed to provide a single shot
0 to 20 or 4 to 20 mA outputs. The
option (M) is included in the Back-Spin
emergency restart following an overload
analog outputs can be configured to
Detection option (B) option.
trip. The accumulated thermal capacity
provide suitable outputs based on
used value is automatically reduced to
any measured analog value, or any
VFD Applications
a level that will allow a restart. After the
calculated quantity.
The 369 is capable of protecting motors
restart attempt, if the relay trips the motor
fed from variable frequency drives (VFDs),
again on running overload, it will remain
including pulse width modulated (PWM) Monitoring and Metering
latched for the appropriate lock-out time.
drives. The 369 has been extensively
The 369 offers a choice of optional
tested with varying current waveforms and Speed Switch Input
monitoring and metering functions
frequencies ranging from 20 to 100Hz.
The speed switch input terminals allow use
including:
of an external speed device. This is typically
Two Speed Motor Applications
Actual Values
used to allow a locked rotor condition to be
The 369 is capable of protecting two speed
distinguished from a normal start, and to
Actual values can be viewed for:
motors. The 369 has dual overload curves
shut down following a short delay.
for two speed motor application so that
• Average and individual phase currents
each speed is adequately protected. Differential Relay Input
• RTD temperatures (hottest, individual,
The differential input accepts contact
maximum) (R Option)
Undervoltage Auto-restart
closure from an external differential relay
• Current Unbalance
This feature can be used to restart a motor
to trip the protected motor via the 369.
after an undervoltage trip caused by a
• Ground leakage current
Spare Input
momentary power loss. When enabled,
• Thermal capacity remaining / estimated
the 369 will issue a re-start command to
The spare input terminals can be
time to trip at present overload level
the motor If the system power is restored
configured to represent either a standard
• Motor load as a percent of full load
to above the Pickup / Restoration setting.
or a specific contact input. The Spare input
• Phase-to-phase or phase-to-neutral
This element includes two independent
is generally used as the starter status
voltage (M option)
sets of power loss and restart delay timers
contact. The 52b contact from a circuit
to allow customization of the scheme.
breaker gives positive identification of the • W, var, MWhr, PF, Hz (M option)
410 410 410
Motor Protection
369 Motor Protection System
Metering (Option M)
The 369 metering option provides
monitoring of quantities such as PF,
kW, and frequency. Several protection
functions can be performed based on
these parameters, including:
• Voltage
• Watts ( kW, MW )
• Vars ( kVar, MVar)
• Power factor
• Frequency
Track changes in motor starting characteristics, identifying potential failures before they become critical
• Energy (MWh)
occur during starting, as well as planning
Statistical Data
Pre-Trip Alarms
preventative maintenance.
The 369 records the following statistical
The 369 can trigger an alarm prior to a trip
• Acceleration time
data:
caused by the following conditions:
•
Total running hours • Starting Current
• Immediate overload/stall warning
• • Thermal capacity used during start
Number of motor starts
• Ground fault •
Total number of motor trips • Cool time Constants
• Mechanical jam
• • Unbalance K factor
Breakdown of types of motor trips
• Unbalance •
Total accumulated mega-watt hours • Average Motor Load
(with the M option)
• Undercurrent
Motor Start Data Logger
• RTD overtemperature, broken RTD
This information can help diagnose
In addition to the learned information
sensor, low temperature RTD
common motor faults, as well as assist in
captured for every start, the Motor Start
• Internal Self-test planning preventative maintenance.
Data Logger will record up to 30 seconds
• Under/overvoltage (M option)
of digital and analog waveforms during
Learned Information
• Low power factor (M option) motor starts. Captured information
The 369 learns the starting characteristics
includes:
of the motor, providing information that
Event Recorder
will assist with troubleshooting faults that
After a trip, the cause of the trip, measured
current values, unbalance, and temperature
present at the time of trip are displayed.
If the M or B options have been ordered,
information will also include voltages,
power, and frequency. This information
helps facilitate troubleshooting. An event
record of the last 512 events helps identify
persistent problems.
Oscillography
The 369 will record up to three waveform
records , each capturing 16 cycles of data.
The oscillography will be triggered when a
trip is issued by the 369 relay. Information
captured includes phase and ground
currents, phase voltages (M option) and the
status of contact inputs and outputs. Each
record will be time and date stamped, and
will include the cause of trip.
Troubleshoot faults that occur during motor starts using the Motor Start Data logger.
411 411 411
Motor Protection
369 Motor Protection System
integrate the 369 to Local or Wide Area
LED Indicators
• Average Phase Current
Networks replaces a multidrop-wired
Ten LED indicators on the front panel
• Current Unbalance
network (e.g., serial Modbus®), and
provide quick visual indication of the motor
• Ground Current
eliminates expensive leased or dial-up
status.
connections, reducing operating costs.
• Average Voltages
Remote Display
• Thermal Capacity Used
The 369 can be installed with the display
TM
• System Frequency EnerVista Software
mounted remotely, reducing the required
• Breaker Status contact
The EnerVista™ Suite is an industry
mounting space within the panel.
leading set of software programs that
Testing
will simplify every aspect of using the 369
Communications
relay. Tools to monitor the status of the
A simulation mode allows forcing relay
A front RS232 port is provided for
motor, maintain the relay, and integrate
contacts and analog outputs without the
downloading setpoints and interrogating
information measured by the 369 into
need for a relay test set. This is an ideal
TM
the relay using the EnerVista 369.
HMI or SCADA monitoring systems are
tool during commissioning for system
Three independent rear RS485 ports offer
available. Also provided are the utilities
functional testing.
the customer flexibility and performance
to analyze the cause of faults and system
for their communication network. The
disturbances using the powerful waveform
369 can communicate at baud rates up
User Interfaces
and Sequence of Event viewers that come
to 19,200 bps using the industry standard
TM
with the EnerVista 369 Setup Software
Modbus® RTU protocol. Fiber optic (option
Display and Keypad
that is included with each relay.
F) Profibus interface (option P), DeviceNet
The 40-character display and keypad
(option D), and Ethernet (option E) ports
EnerVista™ Launchpad
provide convenient local communications
are also available. The optional direct
EnerVista™ Launchpad is a powerful
and control. Setpoints can be adjusted
connect RJ45 Ethernet port can be used
software package that provides users
using the keypad and display. To help
to connect the 369 to 10 Mbps Ethernet
with all of the setup and support tools
prevent unintentional setting changes,
networks. The communication system of
needed for configuring and maintaining
a setpoint access input must be shorted
the 369 is designed to allow simultaneous
GE Multilin products. Launchpad allows
before changes can be made. The display
communication via all ports.
configuring devices in real-time by
module can be separated from the relay
Using Ethernet as the physical media to
communicating using serial, Ethernet, or
and mounted remotely.
Power System Troubleshooting
The 369 contains many tools and reports that simplify and reduce the amount of time required for troubleshooting power system events.
The Motor Heath Report allows you to easily “see” Track changes to settings in the 369 with the built-in setting security
how your motor is doing: audit trail report
• Start/stop history
• Comprehensive trip details
• Learned acceleration time and starting current
• Many other motor health details
412 412 412
Motor Protection
369 Motor Protection System
file, as well as provide documentation
indicating which settings were enabled,
along with an explanation of the specific
parameters entered.
Motor Health Report
This reporting function is included
with every 369 relay, providing critical
information on the historical operating
characteristics of your motor during motor
starting and stopping operations. Included
in the report are:
• Motor operation historical timeline,
displaying start, emergency restart,
stop, trip, and alarm operations.
Create complete settings files for your 369 in 6 simple steps using the Motor Settings Auto-Configurator.
• Historical record of motor trips
modem connections, or offline by creating
• Wiring Diagrams • Extensive trending of motor learned
setting files to be sent to devices at a later
information (trending information up
• FAQs
time. Included in Launchpad is a document
to a maximum of 1250 motor start
• Service Bulletins
archiving and management system
operations)
that ensures critical documentation is
• High Speed motor start data logger
Motor Settings Auto-Configurator
up-to-date and available when needed.
trends, including current, current
Documents made available include: Included with every 369 relay is the
unbalance, voltage, frequency, TCU and
Motor Settings Auto-Configurator. This
breaker contact status during start
configurator will generate a complete 369
• Manuals
settings file based on motor nameplate
• Application Notes
Viewpoint Maintenance
and system information entered by the
• Guideform Specifications
Viewpoint Maintenance provides tools
user. Once all information is entered, the
that will increase the security of your 369,
• Brochures
auto-configurator will generate the settings
create reports on the operating status
of the relay, and simplify the steps to
troubleshoot protected motors.
Front Panel
Tools available in Viewpoint Maintenance
Display
include:
40 Character LCD display for
• Settings Audit Trail Report
viewing actual values and
programming setpoints
• Device Health Report
Rugged, corrosion and flame
• Comprehensive Fault Diagnostics
retardant case
Status Indicators
EnerVista™ Integrator
4 LEDs indicate when an output
TM
is activated. EnerVista Integrator is a toolkit that
Motor Status Indicators
allows seamless integration of GE Multilin
LEDs indicate if motor Stopped,
devices into new or existing automation
Starting, Running, Overloaded, or
systems.
Locked out due to an active Start
Included in EnerVista Integrator is:
Inhibit element.
Keypad
• OPC/DDE Server
Used to display actual values,
• GE Multilin Drivers
causes of alarms, causes of trips,
fault diagnosis information, and to
• Automatic Event Retrieval
program setpoints
• Automatic Waveform Retrieval
Computer Interface
RS232 comm port for connecting
to a PC. Use for downloading
setpoints, monitoring, data
collection & printing reports
413 413 413
Motor Protection
369 Motor Protection System
Technical Specifications
PROTECTION MONITORING POWER SUPPLy
OVERLOAD CURVES TRIP TIME WAVEFORM CAPTURE CONTROL POWER
Curves: 15 curves, fixed shape/prog. Length: 3 buffers containing 16 cycles of all Input: LO: 20 – 60 VDC
FlexCurve™ current and voltage channels
20 – 48 VAC: 50 / 60 Hz
Overload pickup: 1.0 – 1.25 x FLA Trigger position: 1 – 100% pre-trip to post-trip HI: 50 – 300 VDC
Accuracy :Pickup: ±1% of full scale Trigger: trip, manually via communications or 40 – 265 VAC: 50 / 60 Hz
Time: ±100 ms or ±2% of total trip time digital input Power: Nominal: 20 VA
SHORT CIRCUIT AND GROUND TRIP Maximum: 65 VA
Ground trip level: 0.25 – 25.00 A (50:0.025 CT)
Holdup: Non-failsafe trip: 200 ms
INPUTS
10 – 100% (1 A/5 A CT)
Failsafe trip: 100 ms
RTDS INPUTS (OPTION R):
S/C trip level: 2 – 20 x CT, OFF
Wire type: 3-wire
Sensor type: 100 W platinum (DIN 43760)
Intentional delay: INST. or 10 ms to 2000 ms OUTPUTS
100 W nickel, 120 ž nickel
(S/C) (GROUND) ANALOG OUTPUT (OPTION M)
10 W Copper
Instantaneous: 45 ms
PROGRAMMABLE
RTD sensing 3 mA
START PROTECTION
current:
OUTPUT 0 – 1 mA 0 – 20 mA 4 – 20 mA
Thermal: Separate start and run protection
Range: -40 to 200° C or -40 to 424° F
Activation: Inrush current increases 5% to
MAX LOAD 2400 W 600 W 600 W
Lead resistance: 25 W max for Pt and Ni type
>101% FLC in 1 sec
MAX OUTPUT 1.01 mA 20.2 mA 20.2 mA
3 W max for Cu type
Deactivation: Current drops
Frequently asked questions
What makes Elite.Parts unique?

What kind of warranty will the LE6439HSCV have?

Which carriers does Elite.Parts work with?

Will Elite.Parts sell to me even though I live outside the USA?

I have a preferred payment method. Will Elite.Parts accept it?

What they say about us
FANTASTIC RESOURCE
One of our top priorities is maintaining our business with precision, and we are constantly looking for affiliates that can help us achieve our goal. With the aid of GID Industrial, our obsolete product management has never been more efficient. They have been a great resource to our company, and have quickly become a go-to supplier on our list!
Bucher Emhart Glass
EXCELLENT SERVICE
With our strict fundamentals and high expectations, we were surprised when we came across GID Industrial and their competitive pricing. When we approached them with our issue, they were incredibly confident in being able to provide us with a seamless solution at the best price for us. GID Industrial quickly understood our needs and provided us with excellent service, as well as fully tested product to ensure what we received would be the right fit for our company.
Fuji
HARD TO FIND A BETTER PROVIDER
Our company provides services to aid in the manufacture of technological products, such as semiconductors and flat panel displays, and often searching for distributors of obsolete product we require can waste time and money. Finding GID Industrial proved to be a great asset to our company, with cost effective solutions and superior knowledge on all of their materials, it’d be hard to find a better provider of obsolete or hard to find products.
Applied Materials
CONSISTENTLY DELIVERS QUALITY SOLUTIONS
Over the years, the equipment used in our company becomes discontinued, but they’re still of great use to us and our customers. Once these products are no longer available through the manufacturer, finding a reliable, quick supplier is a necessity, and luckily for us, GID Industrial has provided the most trustworthy, quality solutions to our obsolete component needs.
Nidec Vamco
TERRIFIC RESOURCE
This company has been a terrific help to us (I work for Trican Well Service) in sourcing the Micron Ram Memory we needed for our Siemens computers. Great service! And great pricing! I know when the product is shipping and when it will arrive, all the way through the ordering process.
Trican Well Service
GO TO SOURCE
When I can't find an obsolete part, I first call GID and they'll come up with my parts every time. Great customer service and follow up as well. Scott emails me from time to time to touch base and see if we're having trouble finding something.....which is often with our 25 yr old equipment.
ConAgra Foods