PCB PIEZOTRONICS 112A03
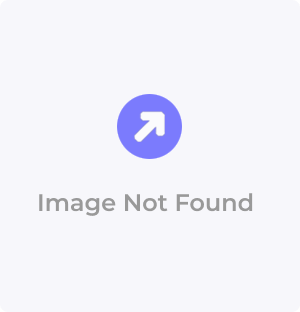
Description
PCB Piezotronics 112A03 Quartz Pressure Sensor - General Purpose, Dynamic Range 0.02 to 10,000PSI
Part Number
112A03
Price
Request Quote
Manufacturer
PCB PIEZOTRONICS
Lead Time
Request Quote
Category
PRODUCTS - 1
Datasheet
Extracted Text
PIEZOELECTRIC SENSORS FOR DYNAMIC PRESSURE MEASUREMENTS PRESSURE CATALOG PRESSURE AND FORCE SENSORS DIVISION ® ® Helping you make better dynamic measurements Helping you make better dynamic measurements Precision Quartz Shear ICP Accelerometers Precision Quartz Shear ICP Accelerometers ...with quality, innovative instruments! ...with quality, innovative instruments! Pressure and Force Sensors Group For 30 years, PCB has been manufacturing piezoelectric sensors for dynamic pressure, force, vibration, and shock measurements. This extensive experience in the world of dynamic measurements has made PCB a leader in high quality piezoelectric instrumentation. PCB’s commitment to customer satisfaction through the continued investment in research, development, and manufacturing capabilities has enabled us to obtain significant roles in these and other important test situations: G Ge en ne er ra all M Mo otto or rs s/ /H Ha ar rr riis so on n — research on air-conditioning compressor pressure dynamics G Ge en ne er ra all E Elle ec cttr riic c — measure power cogeneration plant pressure R Ro ou us sh h T Te ec ch hn no ollo og giie es s — analysis of automotive engine combustion pressure S So ou utth hw we es stt R Re es se ea ar rc ch h IIn ns sttiittu utte e — measure underwater blast W We es sttiin ng gh ho ou us se e — sense acoustic noise in closed- loop, high-temperature cooling systems U U..S S.. A Ar rm my y — measure large gun ballistic and free-field blast pressures R Ro oc ck ke ettd dy yn ne e — measure pressures in space shuttle rocket motors V Va allm me ett — monitor paper slurry dynamic pressures N NA AS SA A ((M MS SF FC C)) — measure free field space shuttle acoustics 2 24 4-h ho ou ur r “ “S Se en ns so or rL Liin ne e” ” ~ ~ C Ca allll 7 71 16 6-6 68 84 4-0 00 00 01 1 R Re es se ea ar rc ch h a an nd d D De ev ve ello op pm me en ntt Recognizing that dynamic measurements are seldom routine, Working along with customers, PCB continually improves PCB has introduced a 24-hour sensor hotline. When you and develops new products to meet more demanding experience an unexpected measurement problem, call the PCB dynamic pressure measurement applications. Improved “SensorLine” Saturday, Sunday, or after hours to talk with an methods of dynamic calibration have been developed to application specialist. evaluate the performance characteristics of new sensors. S Sa attiis sffa ac cttiio on n G Gu ua ar ra an ntte ee e Q Qu ua alliitty y We stand behind our products to ensure they operate PCB is an ISO-9001 facility registered by the Underwriters properly for your application. If for any reason you are not Laboratory, Inc. All quality concerns are addressed by a satisfied, contact us immediately to discuss repair, exchange, quality committee consisting of members from each or credit. Our standard product warranty is one year. If at any department of PCB. Responsibility is assigned for resolving time, however, our products do not meet your expectations, the concern to the customer’s satisfaction, corrective action is feel free to call and talk with a application specialist. initiated, and the customer is notified of concern resolution. ® ® IIC CP P S Se en ns so or rs s C Ca ap pa ab biilliittiie es s PCB offers the broadest piezoelectric line of charge and ICP PCB, a self-sufficient, fully-equipped manufacturing facility, sensors for dynamic pressure, force, shock, and vibration strives to provide you with what you want, when you want it, measurements. What is ICP? It is a registered trademark that at a reasonable price. Do not hesitate to call to ask one of uniquely identifies PCB’s sensors incorporating built-in our applications engineers for product modifications to electronics. Many manufacturers of FFT analyzers and data better suit your application, or to talk to our customer service collectors incorporate “ICP-Inputs” for coupling directly to personnel for expedited delivery or sample hardware needs. our ICP sensors. Other Products and Services Other Products and Services In addition to the dynamic pressure sensors featured in this Selection Guide, PCB offers a broad line of piezoelectric sensors and signal conditioners for measuring dynamic force, shock, and vibration. Consult the factory or a field representative for additional information or assistance on the complete line of products offered by PCB. P PC CB B P PR RO OD DU UC CT TS S A AN ND D S SE ER RV VIIC CE ES S: : C CU US ST TO OM M P PR RO OD DU UC CT TS S PCB offers product modification, special mounting adaptors, F FO OR RC CE E S SE EN NS SO OR RS S-P PF FS S D DIIV VIIS SIIO ON N special tests and calibration services to make PCB sensors bet- ter suited to your application needs. Call, fax, or E-mail your Toll Free: 888-684-0011 request to one of our applications engineers (see page vi). E-mail: pfssales@pcb.com FAX: 716-686-9129 T TH HE E M MO OD DA AL L S SH HO OP P IIN NC C ((T TM MS S)) Dynamic quartz force sensors monitor compression, tension, and impact forces involved with the forming, crimping, Toll Free: 800-860-4867 stressing, welding, machining, or testing of mechanical E-mail: sales@modalshop.com parts, structures, machines, and tablet presses. A full line of FAX: 513-458-2172 ® ICP and charge mode models are available. The Modal Shop, located in Cincinnati to maintain close technical ties with the Structural Dynamic Research Lab of University of Cincinnati, recently became a PCB Group A AC CC CE EL LE ER RO OM ME ET TE ER RS S-S SV VS S D DIIV VIIS SIIO ON N Company. The Modal Shop technology is primarily focused Toll Free: 888-684-0013 to serve the modal and vibro-acoustics structural test markets E-mail: svssales@pcb.com with a broad line of modal sensors, structural excitation prod- FAX: 716-685-3886 ucts, sonic digitizers, precision microphones, low cost PCB offers the broadest commercial line of piezoelectric vibra- acoustic arrays, calibration equipment and rental systems for tion and shock accelerometers. Shear structured quartz and large channel testing. ceramic designs incorporating integral electronics include envi- ronmental stress screening, high frequency, miniature, shock, T TM MS S S ST TR RU UC CT TU UR RA AL L T TE ES ST TIIN NG G P PR RO OD DU UC CT TS S pyroshock, ring-shaped, triaxial, flight-tested, low profile, high temperature, seismic, low cost and industrial. PCB also Lightweight sensors and computer-controlled signal condition- i i now offers capactive accelerometers for measurements down ers provide an integrated systems approach at a lower cost to DC for low frequency steady-state applications. per-channel. A complete range of impulse hammers are avail- able for testing very small turbine blades and PC boards to extremely large structures, such as buildings, floors, or A AC CT TU UA AT TO OR RS S-A AV VC C D DIIV VIIS SIIO ON N bridges. These products, manufactured at the PCB Piezotronics Toll Free: 888-684-0013 factory in Depew, NY, are engineered and marketed by The PCB’s Active Vibration Control (AVC) Division provides Modal Shop, a PCB Group Company. piezoelectric vibration generators (actuators) for structural research and testing. When implemented in a computer-con- T TM MS S M MIIC CR RO OP PH HO ON NE ES S A AN ND D A AC CO OU US ST TIIC C A AR RR RA AY YS S trolled feedback loop, piezo actuators offer active vibration control for vibration reduction and silencing applications. The The Gunnar Rasmussen "Signature Series" precision con- new ICP piezoelectric strain sensor is now available for denser microphones, preamps and power modules are measuring small dynamic strain on top of large static loads. offered through The Modal Shop. These microphones incor- porate four decades of proven design experience in M MA AC CH HIIN NE ER RY Y V VIIB BR RA AT TIIO ON N M MO ON NIIT TO OR RIIN NG G acoustic measurement technology. The Modal Shop also offers the "Acousticel"™, a low cost microphone for large Industrial Monitoring Instrumentation (IMI), a division of channel vibro acoustic testing. PCB, provides rugged, industrial-grade vibration sensors, electronics, and accessories for predictive maintenance and machinery health-monitoring applications. O OC CE EA AN NA A S SE EN NS SO OR R T TE EC CH HN NO OL LO OG GIIE ES S,, IIN NC C.. Phone: 757-426-3678 S SIIG GN NA AL L C CO ON ND DIIT TIIO ON NE ER RS S Oceana Sensor Technologies (OST), a PCB Group Company, located in Virginia Beach, specializes in the automated assem- A complete line of ICP sensor signal conditioners and bly of high volume, low cost sensors for automotive, appli- charge amplifiers is offered by PCB. Signal conditioners are ance, industrial machinery and OEM instrument markets. offered with battery or line power, in single or multichannel configurations, and with or without gain adjust. Additional meters, switches, relays, integrators, and computer-con- P PC CB B P PIIE EZ ZO OT TR RO ON NIIC CS S E EU UR RO OP PE E G Gm mb bH H trolled modules are also available. Fax: 4-924-627-4099 PCB Piezotronics Europe GmbH located in Germany C CA AL LIIB BR RA AT TO OR RS S provides stock in Europe with overnight delivery service. PCB, and its Modal Shop division, offers a wide variety of calibration systems including low and high pressure T TE ES ST TIIN NG G S SE ER RV VIIC CE ES S dynamic calibrators, shock tube, integrated accelerometer Virtually all PCB sensors are supplied with an individual calibration workstation and microphone acoustic array NIST-traceable calibration certificate. PCB’s calibration sys- calibrators. See Page 49 for further information on pres- tem complies with ISO-9001 and ISO-10012-1. sure calibrators. P PR RE ES SS SU UR RE E A AN ND D F FO OR RC CE E S SE EN NS SO OR R D DIIV VIIS SIIO ON N T TO OL LL L F FR RE EE E: : 8 88 88 8-6 68 84 4-0 00 01 11 1 Numerical Model Number Page Listing Numerical Model Number Page Listing M Mo od de ell N Nu um mb be er r P Pa ag ge e M Mo od de ell N Nu um mb be er r P Pa ag ge e M Mo od de ell N Nu um mb be er r P Pa ag ge e 101A . . . . . . . . . . . . . . . . . . .2, 4 134A02 . . . . . . . . . . . . . . .16, 22 112A21 . . . . . . . . . . . .3, 4, 8, 10 101A02 . . . . . . . . . . . . . . . . .2, 5 134A22 . . . . . . . . . . . . . . .16, 22 112A22 . . . . . . . . . . . .3, 4, 8, 10 101A03 . . . . . . . . . . . . . . . . .2, 5 134A23 . . . . . . . . . . . . . . .16, 22 112A23 . . . . . . . . . . . .3, 4, 8, 10 101A04 . . . . . . . . . . . . . . . . .2, 5 134A24 . . . . . . . . . . . . . . .16, 22 112B10 . . . . . . . . . . . . . . .34, 35 101A05 . . . . . . . . . . . . . . . . .2, 4 112B11 . . . . . . . . . . . . . . .34, 35 134A27 . . . . . . . . . . . . . . .16, 22 101A06 . . . . . . . . . . . . . . . . .2, 4 112B13 . . . . . . . . . . . . . . .34, 35 136A . . . . . . . . . . . . . . . . . . . .55 102A . . . . . . . . . . . . . . . . .14, 17 113A . . . . . . . . . . . . . . . .14, 18 137A . . . . . . . . . . . . . . . . . . . .16 102A02 . . . . . . . . . . . .2, 4, 8, 10 113A02 . . . . . . . . . . . . . . .14, 18 137A21 . . . . . . . . . . . . . . .16, 23 102A03 . . . . . . . . . . . . . . .14, 17 113A03 . . . . . . . . . . . . . . .14, 18 137A22 . . . . . . . . . . . . . . .16, 23 102A04 . . . . . . . . . . . . . . .14, 17 113A21 . . . . . . . . . . . . . . .14, 17 137A23 . . . . . . . . . . . . . . .16, 23 102A05 . . . . . . . . . . . .2, 4, 8, 10 113A22 . . . . . . . . . . . . . . .14, 17 138A01 . . . . . . . . . . . . . . .16, 24 102A06 . . . . . . . . . . . . . . .14, 17 113A23 . . . . . . . . . . . . . . .14, 17 138A02 . . . . . . . . . . . . . . .16, 24 102A07 . . . . . . . . . . . .2, 4, 8, 10 113A24 . . . . . . . . . . . . . . .14, 17 138A05 . . . . . . . . . . . . . . .16, 24 102A09 . . . . . . . . . . . . . . . .8, 10 113A26 . . . . . . . . . . . . . . .14, 17 138A06 . . . . . . . . . . . . . . .16, 24 102A10 . . . . . . . . . . . . . . .38, 40 113A31 . . . . . . . . . . . . . . .14, 17 102A11 . . . . . . . . . . . . . . .38, 40 138A10 . . . . . . . . . . . . . . .16, 24 113A32 . . . . . . . . . . . . . . .14, 17 102A12 . . . . . . . . . . . . . . .14, 17 113A33 . . . . . . . . . . . . . . .14, 17 138A11 . . . . . . . . . . . . . . .16, 24 102A13 . . . . . . . . . . . . . . .38, 40 113A34 . . . . . . . . . . . . . . .14, 17 138A25 . . . . . . . . . . . . . . .16, 24 102A14 . . . . . . . . . . . . . . .38, 40 113A36 . . . . . . . . . . . . . . .14, 17 138A26 . . . . . . . . . . . . . . .16, 24 102A15 . . . . . . . . . . . . . . .14, 17 116B . . . . . . . . . . . . . . . . .38, 39 138A50 . . . . . . . . . . . . . . .16, 24 103A . . . . . . . . . . . . . . . . . .9, 12 116B02 . . . . . . . . . . . . . . .38, 39 138A51 . . . . . . . . . . . . . . .16, 24 103A02 . . . . . . . . . . . . . . . .9, 12 117B . . . . . . . . . . . . . . . . .28, 29 140A14 . . . . . . . . . . . . . . . . . .36 103A11 . . . . . . . . . . . . . . . .9, 12 118A02 . . . . . . . . . . . . . . . . .3, 6 140A18 . . . . . . . . . . . . . . . . . .36 ii 103A12 . . . . . . . . . . . . . . . .9, 12 ii 118B11 . . . . . . . . . . . . . . .27, 31 145A01 . . . . . . . . . . . . . . .34, 35 105A . . . . . . . . . . . . . . . . .42, 43 118B13 . . . . . . . . . . . . . . .27, 31 145A05 . . . . . . . . . . . . . . .34, 35 105B02 . . . . . . . . . . . . . . .42, 43 119A . . . . . . . . . . . . . . . . 15, 20 M165A01 . . . . . . . . . . . . .26, 30 105B03 . . . . . . . . . . . . . . .42, 43 119A02 . . . . . . . . . . . . . . 15, 20 105B12 . . . . . . . . . . . . . . .42, 43 165A02 . . . . . . . . . . . . . . .26, 30 119A11 . . . . . . . . .15, 20, 27, 31 105B13 . . . . . . . . . . . . . . .42, 43 119A12 . . . . . . . . .15, 20, 27, 31 M165A03 . . . . . . . . . . . . .26, 30 105B22 . . . . . . . . . . . . . . .42, 43 121A . . . . . . . . . . . . . . . . . . .3, 4 165A05 . . . . . . . . . . . . . . .26, 30 105B23 . . . . . . . . . . . . . . .42, 43 121A02 . . . . . . . . . . . . . . . . .3, 5 167A11 . . . . . . . . . . . . . . .28, 29 105B33 . . . . . . . . . . . . . . .42, 43 121A03 . . . . . . . . . . . . . . . . .3, 5 65A . . . . . . . . . . . . . . . . . . . . .36 105B43 . . . . . . . . . . . . . . .42, 43 121A04 . . . . . . . . . . . . . . . . .3, 5 901A10 . . . . . . . . . . . . . . . . . .50 106B . . . . . . . . . . . . . . . . . .9, 11 122A . . . . . . . . . . . . . . . . .46, 48 903B02 . . . . . . . . . . . . . . . . . .51 106B10 . . . . . . . . . . . . . . . .9, 11 122A21 . . . . . . . . . . . . . . .46, 47 905C . . . . . . . . . . . . . . . . . . .52 106B50 . . . . . . . . . . . . . . . .9, 11 122A22 . . . . . . . . . . . . . . .46, 47 907A . . . . . . . . . . . . . . . . . . . .53 108A02 . . . . . . . . . . . . . . . . .3, 5 122A24 . . . . . . . . . . . . . . .46, 47 907A02 . . . . . . . . . . . . . . . . . .53 108B11 . . . . . . . . . . . . . . .27, 32 123A . . . . . . . . . . . . . . . . .46, 48 907A05 . . . . . . . . . . . . . . . . . .53 108B13 . . . . . . . . . . . . . . .27, 32 123A21 . . . . . . . . . . . . . . .46, 47 109B11 . . . . . . . . .15, 19, 27, 32 907A07 . . . . . . . . . . . . . . . . . .53 123A22 . . . . . . . . . . . . . . .46, 47 109B12 . . . . . . . . .15, 19, 27, 32 123A24 . . . . . . . . . . . . . . .46, 47 913A10 . . . . . . . . . . . . . . . . . .54 111A21 . . . . . . . . . . . . . . . . .2, 4 124A . . . . . . . . . . . . . . . . .46, 48 913B02 . . . . . . . . . . . . . . . . . .55 111A22 . . . . . . . . . . . . . . . . .2, 5 124A21 . . . . . . . . . . . . . . .46, 47 111A23 . . . . . . . . . . . . . . . . .2, 5 124A22 . . . . . . . . . . . . . . .46, 47 111A24 . . . . . . . . . . . . . . . . .2, 5 124A24 . . . . . . . . . . . . . . .46, 47 111A26 . . . . . . . . . . . . . . . . .2, 4 132A31 . . . . . . . . . . . . . . .15, 21 112A . . . . . . . . . . . . . . . . . . .2, 6 132A32 . . . . . . . . . . . . . . .15, 21 112A02 . . . . . . . . . . . . . . . . .2, 6 132A35 . . . . . . . . . . . . . . .15, 21 112A03 . . . . . . . . . . . . . . . . .2, 6 132A36 . . . . . . . . . . . . . . .15, 21 112A04 . . . . . . . . . . . . . . .38, 39 132A37 . . . . . . . . . . . . . . .15, 21 112A05 . . . . . . . . . . . . . . .38, 39 134A . . . . . . . . . . . . . . . . .16, 22 P PC CB B P PIIE EZ ZO OT TR RO ON NIIC CS S,, IIN NC C.. 7 71 16 6-6 68 84 4-0 00 00 01 1 Table of Contents Table of Contents Other Products and Services . . . . . . . . . . . . . . . . . . . . . . . . . . . . . . . .i Numerical List of Model Numbers . . . . . . . . . . . . . . . . . . . . . . . . . . . .ii Pressure Catalog Introduction . . . . . . . . . . . . . . . . . . . . . . . . . . . . . .iv Pressure Application Inquiry Form . . . . . . . . . . . . . . . . . . . . . . . . . . . .vi Sensor Kits . . . . . . . . . . . . . . . . . . . . . . . . . . . . . . . . . . . . . . . . . . .74 Conversion Table . . . . . . . . . . . . . . . . . . . . . . . . . . . . . . . . . . . . . .89 TYPICAL PRESSURE SENSORS: Features and Specifications . . . . . . . .1 DYNAMIC PRESSURE G Ge en ne er ra all P Pu ur rp po os se e P Pr re es ss su ur re e S Se en ns so or rs s . . . . . . . . . . . . . . . . . . . . . . . . . . .1 APPLICATIONS H Hiig gh h S Se en ns siittiiv viitty y . . . . . . . . . . . . . . . . . . . . . . . . . . . . . . . . . . . . . . . . .7 H Hiig gh h F Fr re eq qu ue en nc cy y S Sh ho oc ck k W Wa av ve e/ /B Blla as stt/ /E Ex xp pllo os siio on n . . . . . . . . . . . . . . . . . . .13 Air Bags General Purpose . . . . . . . . . . . . . . . . . . . . . . . . . . . . . . . . . . .14 Ballistics Mini-Pressure Probes . . . . . . . . . . . . . . . . . . . . . . . . . . . . . . . . .14 Blast High Frequency Acceleration-Compensated Quartz Pressure Probes . . .15 ® Time of Arrival, ICP Micro Pressure Sensors . . . . . . . . . . . . . . . .15 Cavitation Tourmaline Pressure Bar . . . . . . . . . . . . . . . . . . . . . . . . . . . . . .16 Cryogenics Free-Field Blast Pressure "Pencil" Probe . . . . . . . . . . . . . . . . . . . .16 Tourmaline Underwater Blast . . . . . . . . . . . . . . . . . . . . . . . . . . .16 Closed-Bombs B Ba alllliis sttiic cs s . . . . . . . . . . . . . . . . . . . . . . . . . . . . . . . . . . . . . . . . . . . . .25 Compressors Interchangeable Quartz . . . . . . . . . . . . . . . . . . . . . . . . . . . . . .26 Cylinder Combustion ® ICP and Charge Mode . . . . . . . . . . . . . . . . . . . . . . . . . . . . . .27 Conformal . . . . . . . . . . . . . . . . . . . . . . . . . . . . . . . . . . . . . . . .28 Gas and Steam Turbines E En ng giin ne e C Co om mb bu us sttiio on n . . . . . . . . . . . . . . . . . . . . . . . . . . . . . . . . . . . . .33 Engine Combustion General Purpose . . . . . . . . . . . . . . . . . . . . . . . . . . . . . . . . . . .34 iii iii Explosives Knock Sensor . . . . . . . . . . . . . . . . . . . . . . . . . . . . . . . . . . . . . .36 Headbolt Sensor . . . . . . . . . . . . . . . . . . . . . . . . . . . . . . . . . . . .36 Flight Dynamics Spark Plug Adaptor . . . . . . . . . . . . . . . . . . . . . . . . . . . . . . . . . .36 Fluid-Borne Noise H Hiig gh h T Te em mp pe er ra attu ur re e a an nd d C Cr ry yo og ge en niic c . . . . . . . . . . . . . . . . . . . . . . . . . . .37 Flow Instabilities M Miin niia attu ur re e . . . . . . . . . . . . . . . . . . . . . . . . . . . . . . . . . . . . . . . . . . . .41 R Ro oc ck ke ett M Mo otto or r . . . . . . . . . . . . . . . . . . . . . . . . . . . . . . . . . . . . . . . . .45 High-Intensity Sound PRESSURE CALIBRATORS . . . . . . . . . . . . . . . . . . . . . . . . . . . . . .49 Hydraulic and Pneumatics Shock Tube . . . . . . . . . . . . . . . . . . . . . . . . . . . . . . . . . . . . . . . . . . .50 Pulsations Low Pressure Pulse . . . . . . . . . . . . . . . . . . . . . . . . . . . . . . . . . . . . . .51 High Pressure Static . . . . . . . . . . . . . . . . . . . . . . . . . . . . . . . . . . . . .52 Pump/Valve Dynamics Aronson Step Pressure Generator . . . . . . . . . . . . . . . . . . . . . . . . . . .53 Waterline Acoustics High Pressure Impulse . . . . . . . . . . . . . . . . . . . . . . . . . . . . . . . . . . .54 Water Hammer Hydraulic Pressure Impulse . . . . . . . . . . . . . . . . . . . . . . . . . . . . . . . .55 Shock Waves RELATED PRODUCTS . . . . . . . . . . . . . . . . . . . . . . . . . . . . . . . . .57 Mounting Adaptors . . . . . . . . . . . . . . . . . . . . . . . . . . . . . . . . . . . . .58 Turbulence Installation Preparation & Accessories . . . . . . . . . . . . . . . . . . . . . . . .61 Underwater Blast Custom Cables and Connectors . . . . . . . . . . . . . . . . . . . . . . . . . . . .63 Wind Tunnels Standard Stock Cables . . . . . . . . . . . . . . . . . . . . . . . . . . . . . . . . . . .64 Connector Descriptions . . . . . . . . . . . . . . . . . . . . . . . . . . . . . . . . . .68 Connector Adaptors . . . . . . . . . . . . . . . . . . . . . . . . . . . . . . . . . . . .69 Signal Conditioners/Power Supplies . . . . . . . . . . . . . . . . . . . . . . . . .70 TECHNICAL INFORMATION . . . . . . . . . . . . . . . . . . . . . . . . . . .75 Introduction to Dynamic Pressure Sensors . . . . . . . . . . . . . . . . . . . . .75 Driving Long Cables . . . . . . . . . . . . . . . . . . . . . . . . . . . . . . . . . . . .82 APPENDIX Article Reprints . . . . . . . . . . . . . . . . . . . . . . . . . . . . . . . . . . . . . . . .84 Glossary of Terms . . . . . . . . . . . . . . . . . . . . . . . . . . . . . . . . . . . . . .85 Ordering Information . . . . . . . . . . . . . . . . . . . . . . . .Inside Back Cover P PR RE ES SS SU UR RE E A AN ND D F FO OR RC CE E S SE EN NS SO OR R D DIIV VIIS SIIO ON N T TO OL LL L F FR RE EE E: : 8 88 88 8-6 68 84 4-0 00 01 11 1 Quartz, Tourmaline, and Quartz, Tourmaline, and Ceramic Crystal Ceramic Crystal For dynamic pressure measurements, piezo-type tions above 275° F. They pressure sensors incorporate generate a high-impedance self-generating quartz, tour- charge signal (pC/psi) that maline, or ceramic sensing couples to readout instru- elements. Naturally piezo- ments through a low-noise electric, quartz is the most Cultured Quartz Crystal SiO cable and charge amplifier. 2 commonly used crystal; (See Fig. B on page v). The however, certain specialized charge amplifier serves to convert the sensor’s high- sensors, such as underwater blast sensors, incorporate impedance charge output signal to a usable low-imped- volumetrically-sensitive tourmaline. PCB micro-pressure ance voltage signal, normalize the signal, and provide| sensors are structured with piezo-ceramic elements. for gain, ranging, and filtering. High-impedance charge Our broad commercial line of standard piezoelectric mode systems must be kept very clean. Consequently, pressure sensors are used for a variety of dynamic pres- they do not operate well in applications requiring long sure measurements, including: compression, pulsations, input cables in factory, field, outdoor, or humid environ- surges, ballistics, detonation, engine cylinder combustion, ments. shock and blast waves, explosives, high-intensity sound, ® The more popular Integrated Circuit Piezoelectric (ICP ) iv iv and other dynamic acoustic and hydraulic processes from voltage mode sensors (see Fig. A on page v) incorporate <0.001 to >100,000 psi. The capability to measure a built-in microelectronic signal conditioner and output a small pressure fluctuations, such as fluid-borne noise at low-impedance voltage signal (mV/psi). ICP sensors high static levels, is a unique characteristic of piezo pres- operate from a low-cost, constant-current signal condi- sure sensors. tioner or may connect directly to a readout instrument PCB sensors are manufactured at our sensor technology with a built-in constant-current source. center using high-precision CNC machinery. For her- ICP sensors are well-suited for continuous operation in metic sealing, both laser and electron beam welding dirty factory environments, underwater, and through long processes are used. Sensors are also modified and tai- cables in field test applications. Since special low-noise lored to meet specific customer requirements. Standard cable and charge amplifiers are not required, ICP sensor and special adaptors can be provided to facilitate sensor systems are substantially lower in cost per channel. installation in existing mounting ports. Because of the ICP sensor’s low-impedance output, superi- Although piezo pressure sensors are primarily recom- or signal to noise, capability to drive long ordinary coaxi- mended for dynamic pressure measurements, some al cables, and lower cost per channel, they are suitable quartz pressure sensors have long discharge time con- for virtually all dynamic pressure applications where sen- stants that extend low-frequency capability to permit stat- sor temperatures do not exceed 275° F. ic calibration and measurement of quasi-static pressures If you would like to discuss your application, or if it is not over a period of a few seconds. Virtually all sensors are listed, please call, fax, e-mail or write to PCB for provided with an individual NIST-traceable calibration assistance. certificate. Dynamic pressure calibrators are available for our customers who prefer the convenience of on-site recalibration of their sensors. Piezo pressure sensors may be categorized as either ® charge mode or ICP voltage mode output. Charge mode sensors are generally used for higher temperature applica- Typical Mini Quartz Pressure Sensor P PC CB B P PIIE EZ ZO OT TR RO ON NIIC CS S,, IIN NC C.. 7 71 16 6-6 68 84 4-0 00 00 01 1 Piezoelectric Pressure Sensors Piezoelectric Pressure Sensors OUTSTANDING CHARACTERISTICS OF PCB PIEZOELECTRIC PRESSURE SENSORS Flush diaphragms accurately measure high-frequency, Wide operating temperature ranges from -400 to > 600° F. non-resonant response of shock and blast waves. Rugged, durable solid state construction withstands ® ICP pressure sensors operate in dirty field, factory, shock and vibration to tens of thousands of g's. or underwater environments through long, ordinary PCB mini pressure sensor Series 111, 112, and 113 coaxial cable without loss of signal strength or noise install in a variety of standard or custom-made adaptors increase. for simplified installation in pre-existing mounting ports. A single quartz pressure sensor has a very wide linear Two linear calibration graphs are furnished with most dynamic operating range. Several strain or piezore- PCB quartz pressure sensors, one for the full-scale sisitive type sensors with narrow measuring ranges range and one for 10% of full scale. would be required to make the range of measurements English or metric installation configurations available. that can be made by one quartz piezoelectric sensor. 3.5 7.5E-6 3.0 2.5 5.0E-6 2.0 1.5 1.0 2.5E-6 0.5 v v 0.0 0.0 0.0s 50.0us 100.0us 150.0us 0 Hz 1.0MHz 2.0MHz 3.0MHz 4,0MHz 4.0MHz TIME Frequency Shockwave Measurement With Microsecond Rise FFT Microsecond Shockwave Non-Resonant Time and Non-Resonant Response Response ® Typical ICP Sensor System Figure A Typical High Impedance Charge System Figure B Standard Coaxial Cable P PR RE ES SS SU UR RE E A AN ND D F FO OR RC CE E S SE EN NS SO OR R D DIIV VIIS SIIO ON N T TO OL LL L F FR RE EE E: : 8 88 88 8-6 68 84 4-0 00 01 11 1 Amplitude (volts) FFT,134 REFLECTED 700 PSI VOLTS/Hz TO: PCB Piezotronics Pressure Application Pressure Application Pressure and Force Sensors Division Fax: (716) 686-9129 Inquiry Form Inquiry Form The pressure sensors listed in this catalog represent our most popular sensors, which are only a fraction of the sensors we offer. In addition to our standard sensors, PCB can customize sensors to meet your specific needs. Please fill out this inquiry form with any information available to you, so that we may help you with your dynamic measurement application. If you would like to discuss your application, or if it is not listed, please call, fax, Email or write to PCB for suggestions. Name: Date: Company: Phone: Ext: Dept.: Fax: Address: City/State Zip 1. NATURE OF REQUEST ❏ Inquiry ❏ Order ❏ Quotation ❏ Delivery Information ❏ Complaint ❏ Service or Repair ❏ Trouble with Equipment ❏ Equipment Operation ❏ Visit required from PCB or Sales Representative in your area 2. DESCRIBE YOUR APPLICATION Note: Please indicate priority from 10 (highest) to 1 (lowest) 3. DYNAMIC What is the approximate DYNAMIC range? vi vi What is the maximum STATIC + DYNAMIC range? Is the event ❏ oscillatory or ❏ a pulse event? Will you be continuously monitoring? ❏ yes ❏ no What is the event pulse duration? How quickly will the event occur? (rise time or time to peak) What is the high and low frequency range you want to measure? Will the sensor be exposed to high shock or vibration? 4. ENVIRONMENTAL What is the environment temperature range? °F Will the temperature be cycling? ❏ yes❏no What is the maximum operating temperature the sensor will be exposed to? For how long? What type of environment will the sensor be used in? ❏ Air ❏ Underwater ❏ Salt Water ❏ Field ❏ Lab ❏ Humid ❏ Corrosive ❏Vacuum ❏ Other (please specify): For how long? 5. ELECTRICAL What length of cable will you need from the test structure to the readout instrument? What is the desired noise floor or resolution? What is the desired output? ❏ 5V ❏ 10V ❏ Other (specify) What is the readout device? ❏ A to D ❏ Scope ❏ Other (specify) What is the input impedance of the readout device (if applicable)? ® Does the readout instrument have a constant current signal conditioner for ICP sensors? ❏ yes ❏ no What kind of signal conditioner would you like? ❏ Single ❏ Multiple channel How many? Does your readout instrument have gain adjust? ❏ yes ❏ no Would you like to have ❏ AC and/or ❏ DC coupling? (Note: DC coupling, as provided by the 484B06 or B11 Signal conditioners, is recommended for pressure sensors with long time constants to provide for quasi static calibration.) 6. SPECIAL PHYSICAL CONSIDERATIONS Are there any physical sensor dimension requirements? Is electrical ground isolation needed? P PC CB B P PIIE EZ ZO OT TR RO ON NIIC CS S,, IIN NC C.. 7 71 16 6-6 68 84 4-0 00 00 01 1 General Purpose Quartz General Purpose Quartz Pressure Sensors Pressure Sensors General purpose quartz pressure sensors are designed for Dynamic phenomena dynamic measurements of compression, combustion, explosion, pulsation, cavitation, blast, pneumatic, Industrial pump pressure hydraulic, fluid and other such pressures. ® monitoring ICP pressure sensors, structured with naturally piezoelectric, stable quartz sensing elements and integral electronics, are well suited to measure rapidly changing Hydraulic and pneumatic pressure pressure fluctuations over a wide amplitude and frequency range. Solid-state construction, hermetically-sealed line monitoring housings, and laser-welded flush diaphragms provide undistorted high frequency response, ruggedness and Fluid borne noise durability, even in adverse environmental conditions. The result is a quality sensor that offers a repeatable, linear, low impedance voltage output making the sensor suitable Pulsations, surges, water hammer, for measurements in a variety of gaseous, fluid, and oil switching transients, cavitation environments. 1 1 Operating from a low-cost constant-current signal conditioner, ICP sensors provide a clean, high-voltage, low-impedance linear output over a very wide operating range. They drive long, inexpensive, ordinary coaxial cables in field or factory environments without signal degradation. ICP sensors are supplied with hardware and seals for mounting. For convenience in mounting pressure probes, standard and special thread adaptors can be supplied to match specific nonstandard mounting ports (see Mounting Adaptors, page 58). To allow the user to take advantage of the wide dynamic range capability, many ICP sensors are supplied with two linear calibrations, one at full scale and one 10% of full scale. This means, for example, model 111A24, 5 mV/psi sensor may be used for accurate measurements ranging from 0 to 1000 psi or 0 to 100 psi, or anywhere in between. In fact, a user can measure 1 psi fluctuations at any static level up to 10 000 psi. Large overange capabilities are possible because a pressure sensor's diaphragm is backed by a rigid column of quartz. P R E S S U R E A N D F O R C E S E N S O R S D I V I S I O N P PC CB B 716-684-0001 P PF FS S T To ollll F Fr re ee e 888-684-0011 F Fa ax x 716-686-9129 E Em ma aiill pfssales@pcb.com W We eb b S Siitte e www.pcb.com General Purpose Quartz General Purpose Quartz ® ® ICP and Charge mode ICP and Charge mode ® ® M MIIN NIIG GA AG GE E IIC CP P P PR RO OB BE E D DE ES SIIG GN NS S S Se er riie es s 1 11 11 1A A2 20 0 A AN ND D 1 11 12 2 Minigages are a popular choice for applications requiring a minimum case diameter (0.218 inch dia) and a flush diaphragm. They install in a threaded stepped hole (5/16-24 or optional 7 mm thread) via the supplied floating clamp nut. See pages 58, 59 and 61 for S Se er riie es s 1 11 11 1A A2 20 0 a an nd d 1 11 12 2 mounting options. Also see higher frequency (500 kHz) series 113A20 on page 14. 1 11 11 1A A2 20 0 S Se er riie es s is a general purpose economy ICP sensor that contains a rigid, multiplate, compression design quartz element, with an internal compensating accelerometer (in most models) to minimize vibration sensitivity. ICPsensors with integral microelectronics produce a high quality signal that is virtually independent of cable length and motion. When connected to a PCB signal conditioner, these sensors generate a low-noise, low-impedance analog output signal proportional to the measurand and compatible with most readout instruments. This series contains models 111A21, A22, A23, A24 and A26 that measures dynamic pressures from full vacuum to 10 000 psi. See specifications on pages 4 and 5. M Mo od de ells s 1 11 12 2A A,, A A0 02 2,, a an nd d A A0 03 3 acceleration compensated, 1pC/psi minigages are charge mode sensors that measure dynamic pressures 2 2 from full vacuum to 10 000 psi. The charge signal from these M Mo od de ells s 1 10 01 1A A,, 1 10 02 2A A0 02 2 acceleration compensated quartz sensors is converted into a voltage a an nd d 1 10 02 2A A0 07 7 signal by a PCB or other similar charge amplifier. Charge mode sensors may be used at higher temperatures, since the temperature is limited only by the quartz sensing element. System sensitivities depend upon the charge or in-line amplifier used. See specifications on page 6. ® ® T TH HR RE EA AD DE ED D G GR RO OU UN ND D IIS SO OL LA AT TE ED D IIC CP P D DE ES SIIG GN NS S M Mo od de ells s 1 10 01 1A A,, 1 10 02 2A A0 02 2 a an nd d 1 10 02 2A A0 07 7 ground isolated designs incorporate a continuous 3/8-24 mounting thread to accommodate different wall thicknesses. Once the sensor is mounted with the diaghram flush, the combined floating clamp nut/seal locks it in place. See specifications on page 4. ® ® T TH HR RE EA AD DE ED D G GE EN NE ER RA AL L P PU UR RP PO OS SE E IIC CP P D DE ES SIIG GN NS S Acceleration compensated ICP pressure sensors, Models 101A02, A03, M Mo od de ell 1 10 01 1A A0 02 2,, A A0 03 3,, A A0 04 4,, A A0 05 5,, A A0 06 6 a an nd d 1 10 02 2A A0 05 5 A04, A05, A06 and 102A05 are ground isolated designs with a 3/8-24 fixed mounting thread length for a positive pressure seal at higher pressures. Five ranges are available from 100 to 10 000 psi, with sensitives from 50 to 0.5 mV/psi, for routine hydraulic and pneumatic fluctuating pressure applications. See specifications on pages 4 and 5. P PC CB B P PIIE EZ ZO OT TR RO ON NIIC CS S,, IIN NC C.. 7 71 16 6-6 68 84 4-0 00 00 01 1 General Purpose Quartz General Purpose Quartz ® ® ICP and Charge mode ICP and Charge mode R RE EP PE ET TIIT TIIV VE E H HY YD DR RA AU UL LIIC C M Mo od de ells s 1 10 08 8A A0 02 2 a an nd d 1 11 18 8A A0 02 2 One of the toughest applications for sensors of any kind is measuring high pressure, repetitive pulses, such as those encountered in fuel injection systems or hydraulic tube endurance testing. These two models are designed to continuously measure repetitive pressures such as those involved in diesel fuel injection or hydraulic tube “torture” testing. M Mo od de ells s 1 10 08 8A A0 02 2 a an nd d 1 11 18 8A A0 02 2 Ordinary diaphragm-type sensors usually fatigue quickly in such applications. For this tough service, PCB pioneered the integral machined diaphragm, devoid of thin diaphragm or flexures susceptible to fatigue failure. The expected life of this sensor is millions of cycles and they are capable of continuously monitoring the processes mentioned above. M Mo od de ell 1 10 08 8A A0 02 2 is an ICP quartz sensor containing integral electronics with a sensitivity of 0.5 mV/psi. It can measure repetitive dynamic pressures up to 10 000 psi. See specifications on page 5. M Mo od de ell 1 11 18 8A A0 02 2 is a charge mode version of the 108A02 above. It has a sensitivity of 0.1 pC/psi and is ideal for higher temperature applications to 400°F. See specifications on page 6. IIN ND DU US ST TR RIIA AL L,, R RU UG GG GE ED D S Se er riie es s 1 12 21 1 3 3 Designed specifically for industrial applications, this ICP sensor is a more rugged industrial version of the miniature quartz sensor. Standard S Se er riie es s 1 12 21 1 features of the series 121 include a leak proof, long life integral machined diaphragm, welded construction and a large rugged industrial type connector. This sensor is available in a number of standard ranges and can be readily adapted to meet a variety of special requirements. Type 012 cable with a TNC connector is recommended for use with this sensor. See “Custom Cable Ordering Guide” on page 63. See specifications on page 4. ® ® M MIIN NIIA AT TU UR RE E H HIIG GH H S SE EN NS SIIT TIIV VIIT TY Y IIC CP P P PR RO OB BE ES S.. S Se er riie es s 1 11 12 2A A2 20 0 Used to measure small dynamic hydraulic and pneumatic pressures such as turbulence, noise, sound, cavitation and pulsations, especially in adverse environments. Capable of measuring high intensity sound pressures from 0.001 psi (111 dB {air}) to 100 psi (210 dB {air}) at any S Se er riie es s 1 11 12 2A A2 20 0 static level from full vacuum to 2 000 psi. Internal acceleration compensation minimizes vibration sensitivity and an internal discharging resistor automatically eliminates static (DC) signal components. See specifications on page 4. M Mo od de ell 1 11 12 2A A2 21 1 is a 50mV/psi general purpose sensor suitable for most low pressure applications. M Mo od de ell 1 11 12 2A A2 22 2 has 100mV/psi sensitivity for greater signal strength. M Mo od de ell 1 11 12 2A A2 23 3 incorporates special low noise microelectronics for improved resolution. P PR RE ES SS SU UR RE E A AN ND D F FO OR RC CE E S SE EN NS SO OR R D DIIV VIIS SIIO ON N T TO OL LL L F FR RE EE E: : 8 88 88 8-6 68 84 4-0 00 01 11 1 ® ® ICP General Purpose Quartz ICP General Purpose Quartz With integral electronics With integral electronics Dimensions shown in inches except where noted. ® Operate with ICP power/signal conditioners Mounting Adaptors on Page 58 Models 101A, 102A02 and 102A07 Models 101A02, A03, A04, A05, A06, 102A05 Models 111A21, A22, A23, A24, A26, 112A21, A22, A23 Thread Mount with Floating Clamp Nut Thread Mount Design Probe Designs Dynamic Range (2) psi 0.01 to 50 0.02 to 100 125 0.1 to 500 MODEL NUMBERS 102A07 112A23 102A02, 102A05 101A, 101A05 121A 101A06 112A22 112A21 111A21 111A26 Sensitivity (10) mV/psi 100 50 ± 10 40 ± 20 10 ± 1 Resolution psi 0.001 0.002 0.003 0.01 Range (for 5V output) (3) psi 50 50 (±2.5v) 100 125 500 Range (for 10V output) (4) psi 100 200 250 1000 Maximum Pressure psi 500 1000 5000 Linearity (5) %FS ≤ 1 ≤ 2 4 4 Resonant Frequency kHz ≥ 250 ≥ 200 ≥ 400 Rise Time µs ≤ 2 ≤ 2 ≤ 1 Discharge Time Constant (6) s ≥ 1 ≥ 50 Low Frequency (-5%) (6) Hz 0.5 0.01 Shock (max) g pk 20 000 Acceleration Sensitivity psi/g ≤ 0.002 ≤ 0.01 ≤ 0.04 ≤ 0.002 Temperature Range °F -100 to +275 Temperature Coefficient %/°F ≤ 0.03 ≤ 0.04 ≤ 0.03 Flash Temperature °F 3000 Polarity (positive pressure) positive Output Impedance ohm ≤ 100 Output Bias +volt 8 to 14 3 to 8 8 to 14 Power Required: Voltage + VDC 20 to 30 11 to 30 20 to 30 Constant Current mA 2 to 20 Ground Isolation model 102A07 n/a 102A02, A05 101A, 101A05 n/a 101A06 Sensing Element material quartz Case (7) material 17-4 PH ® Diaphragm (7) (8) material Invar 17-4 PH (9) Invar Connector (8) type 10-32 coax TNC 10-32 coax Sealing (8) type epoxy Hermetic Seal (8) prefix H n/a H Stainless Steel Diaphragm prefix S n/a S Emralon Gnd. Isolation Coating prefix E (111A20 & 112A20 probe series) n/a E (111A26) Negative Polarity prefix N Water-resistant Cable prefix W (specify length) Notes: 1. For recess mount, Model 065A05 sleeve is available. 4. ≥24 VDC supply required for 10V output. If optional calibration to 10V range is required, 2. Measures dynamic pressures from full vacuum to rated maximum. linearity spec may change. If negative pressure is applied, the output may be limited by the 3. Supplied with two calibrations: 0 to 100% and 0 to 10% of full dynamic range. output bias. 5. % FS any calibration range; zero-based best straight line. P PC CB B P PIIE EZ ZO OT TR RO ON NIIC CS S,, IIN NC C.. 7 71 16 6-6 68 84 4-0 00 00 01 1 OPTIONS ELECTRICAL ENVIRONMENT FREQ RESP AMPLITUDE PHYSICAL ® ® ICP General Purpose Quartz ICP General Purpose Quartz With integral electronics With integral electronics Dimensions shown in inches except where noted. Models 121A, 121A02, A03, A04 Model 108A02 Industrial Design Hydraulic Pump Design Dynamic Range (2) psi 0 .2 to 1000 1 to 5000 2 to 10 000 MODEL NUMBERS 101A04 121A02 101A02 121A03 101A03 121A04 108A02 111A24 111A22 111A23 Sensitivity (10) mV/psi 5 ± 0.5 5 ± 2 1 ± 0.1 1 ± 0.5 0.5 ± 0.05 0.5 ± 0.2 0.5 Resolution psi 0.02 0.1 0.2 Range (for 5V output) (3) psi 1000 5000 10 000 Range (for 10V output) (4) psi 2000 10 000 20 000 Maximum Pressure psi 10 000 15 000 10 000 20 000 50 000 Linearity (5) %FS ≤ 2 5 Resonant Frequency kHz ≥ 400 ≥ 200 ≥ 400 ≥ 200 ≥ 400 ≥ 200 ≥ 250 5 Rise Time µs ≤ 1 ≤ 2 ≤ 1 ≤ 2 ≤ 1 ≤ 2 Discharge Time Constant (6) s ≥ 100 ≥ 500 ≥ 100 ≥ 1 000 ≥ 100 ≥ 500 Low Frequency (-5%) (6) Hz 0.005 0.001 0.005 0.0005 0.005 0.001 Shock (max) g pk 20 000 Acceleration Sensitivity psi/g ≤ 0.002 ≤ 0.04 ≤ 0.002 ≤ 0.04 ≤ 0.002 ≤ 0.04 ≤ 0.01 Temperature Range °F -100 to +275 Temperature Coefficient %/°F ≤ 0.03 ≤ 0.04 ≤ 0.03 ≤ 0.04 ≤ 0.03 ≤ 0.04 ≤ 0.03 Flash Temperature °F 3000 Polarity (positive pressure) positive Output Impedance ohm ≤ 100 Output Bias +volt 8 to 14 Power Required: Voltage +VDC 20 to 30 Constant Current mA 2 to 20 Ground Isolation model 101A04 n/a 101A02 n/a 101A03 n/a Sensing Element material quartz Case (7) material 17-4 PH C-300 Diaphragm (7) (8) material Invar 17-4 PH (9) Invar 17-4 PH (9) Invar 17-4 PH (9) C-300 (9) Connector (8) type 10-32 coax TNC 10-32 coax TNC 10-32 coax TNC 10-32 coax Sealing (8) type epoxy hermetic Hermetic Seal (8) prefix H n/a H n/a H n/a Stainless Steel Diaphragm prefix S n/a S n/a S n/a Emralon Gnd. Isolation Coating prefix E (111 only) n/a E (111 only) n/a E (111 only) n/a Negative Polarity prefix N Water-resistant Cable prefix W (specify length) 6. Discharge Time Constant (DTC) relates low-frequency to signal lost during transient 9. Diaphragms are integral. events at room temperature. See technical section on page 78. 10. Unless otherwise designated, sensitivities are ±15% 7. Special diaphragm or case material available. 8. Diaphragms of all sensors are welded or integral. Hermetic option specifies a fused-glass electrical connector and welded joints. P PR RE ES SS SU UR RE E A AN ND D F FO OR RC CE E S SE EN NS SO OR R D DIIV VIIS SIIO ON N T TO OL LL L F FR RE EE E: : 8 88 88 8-6 68 84 4-0 00 01 11 1 OPTIONS PHYSICAL ELECTRICAL ENVIRONMENTAL FREQ RESP AMPLITUDE General Purpose General Purpose Quartz Pressure Sensors Quartz Pressure Sensors Dimensions shown in inches except where noted. Operate with charge amplifiers and low-noise input cables Mounting Adaptors on Page 58 Models 112A, A02, A03 Model 118A02 Dynamic Range (1) psi 0.02 to 100 0.02 to 3 000 0.02 to 10 000 2 to 20 000 MODEL NUMBERS 112A02 112A 112A03 118A02 Sensitivity (8) -pC/psi 1 0.1 Resolution (2) psi 0.002 0.2 Maximum Pressure psi 1000 10 000 15 000 50 000 (5) 6 6 Linearity (3) %FS ≤ 1 ≤ 2 Resonant Frequency kHz ≥ 250 Rise Time µs ≤ 2 Shock (max) g pk 20 000 Acceleration Sensitivity psi/g ≤ 0.002 ≤ 0.01 Temperature Range °F - 400 to + 400 Temperature Coefficient %/°F ≤ 0.03 ≤ 0.04 Flash Temperature °F 3000 Polarity (positive pressure) (7) negative Capacitance pF 18 10 12 Insulation Resistance at 70° F ohm ≥ 10 Sensing Element material quartz Case (4) (6) material 17-4 PH C-300 Welded Diaphragm (4) (6) material Invar C-300 (9) Connector type 10-32 coaxial Sealing (6) type epoxy Hermetic Seal (6) prefix H n/a Stainless Steel Diaphragm prefix S n/a Emralon Gnd. Isolation Coating prefix E n/a Positive Polarity prefix P Water-resistant Cable prefix W (specify length) Notes: 1. Measures dynamic pressures from full vacuum to rated maximum. 6. Diaphragms of all sensors are hermetic welded or integral. Hermetic option specifies a 2. Resolution determined by system noise and cable length. fused-glass electrical connector and welded joints.. 3. % FS any calibrated range; zero-based best straight line. 7. Charge amplifier inverts the signal. 4. Special case and diaphragm material available. 8. Unless otherwise designated, sesitivities are ±15%. 5. Not for continuous, repetitive use at maximum pressure. 9. Diaphragm is integral. P PC CB B P PIIE EZ ZO OT TR RO ON NIIC CS S,, IIN NC C.. 7 71 16 6-6 68 84 4-0 00 00 01 1 FREQ OPTIONS ELECTRICAL ENVIRONMENTAL PHYSICAL AMPLITUDE RESP High Sensitivity High Sensitivity Pressure Sensors Pressure Sensors PCB and The Modal Shop, a PCB Group Company, offer Acoustic a wide range of microphones and pressure sensors for acoustic, turbulence and high intensity sound Turbulence measurements in a wide variety of laboratory, field and flight applications. All sensors in this section are structured with High-intensity sound acceleration-compensated sensing elements to minimize vibration sensitivity. They incorporate built-in ® Aircraft flight tests microelectronic circuitry and operate with standard ICP sensor signal conditioners. Output is a high voltage low impedance signal compatible with standard readout Paper slurry pressure instruments. measurement ICP quartz pressure sensors are structured with a diaphragm that is supported by a rigid column of quartz. They have the unique capability to measure low Valve dynamics acoustic pressure changes under high static loading as 7 7 might be involved with fluid borne noise measurements in hydraulic systems. The static component of the signal is eliminated from the sensor output due to the discharge time constant of the sensor. Options for the high sensitivity acoustic sensors include special filtering, biasing, powering and physical configurations. Also offered by The Modal Shop, are precision Gunner Rasmussen "Signature Series" condenser microphones. The Modal Shop also supplies low cost ICP microphones for large channel vibro-acoustic array sensing applications. For more information, see page i of this catalog. See pages 37 to 39 for information on high-temperature charge mode acoustic pressure sensors Models 112A04, 112A05, 116B and 116B02. P R E S S U R E A N D F O R C E S E N S O R S D I V I S I O N P PC CB B 716-684-0001 P PF FS S T To ollll F Fr re ee e 888-684-0011 F Fa ax x 716-686-9129 E Em ma aiill pfssales@pcb.com W We eb b S Siitte e www.pcb.com ® ® ICP High Sensitivity ICP High Sensitivity With integral electronics With integral electronics ® ® M MIIN NIIA AT TU UR RE E H HIIG GH H S SE EN NS SIIT TIIV VIIT TY Y IIC CP P Q QU UA AR RT TZ Z P PR RO OB BE ES S S Se er riie es s 1 11 12 2A A2 20 0 Used to measure small dynamic pressures such as turbulence, noise, sound, cavitation, and pulsations in fluids that commonly occur in aerodynamic, hydraulic and blast applications. Capable of measuring M Mo od de ells s 1 11 12 2A A2 21 1,, 1 11 12 2A A2 22 2,, a an nd d 1 11 12 2A A2 23 3 high intensity sound pressures from 0.01 psi (130 dB [air]) to 100 psi (210 dB [air]) fluctuating on high static pressures especially in adverse environments. Internal acceleration compensation minimizes vibration sensitivity. A discharging resistor automatically eliminates static (DC) signal components. This sophisticated instrument contains a high- sensitivity multi-plate quartz element and a selected unity gain amplifier to impart a high signal-to-noise ratio. Operating from a PCB signal conditioner, this sensor generates a high- level, low-impedance analog output signal proportional to the measurand. The analog output is compatible with most readout instruments. A 5/16-24 floating clamp nut or optional Metric (M7 x .75) thread isolates the sensor against strain and facilitates installation/removal of the sealed sensor assembly. The assembly mounts directly in the test object or in a variety of threaded mounting adaptors. See specifications on page 10. M Mo od de ell 1 10 02 2A A0 02 2,, 1 10 02 2A A0 07 7 a an nd d 1 10 02 2A A0 09 9 M Mo od de ell 1 11 12 2A A2 21 1 is a general purpose 50 mV/psi sensor with a wide 8 8 dynamic range suitable for most applications. M Mo od de ell 1 11 12 2A A2 22 2 is a higher sensitivity model with 100 mV/psi output. M Mo od de ell 1 11 12 2A A2 23 3 is a 50 mV/psi sensor with special low noise, low bias electronics for improved resolution. ® ® G GR RO OU UN ND D-IIS SO OL LA AT TE ED D H HIIG GH H S SE EN NS SIIT TIIV VIIT TY Y IIC CP P S Se er riie es s 1 10 02 2 These sensors are used for monitoring low-level dynamic pressures such as turbulence, noise, cavitation, pulsations, sonic boom, and aerodynamic phenomenon. The 3/8-24 threaded housing isolates the sensor from electrical noise in the mounting structure. They incorporate high-resolution electronics, offering fast response, excellent signal-to- M Mo od de ell 1 10 02 2A A0 05 5 noise ratio, and low-impedance output. See specifications on page 10. M Mo od de ells s 1 10 02 2A A0 02 2,, A A0 07 7,, a an nd d A A0 09 9 have a 3/8-24 threaded housing and a floating clamp nut to allow the sensor to be mounted at various depths. M Mo od de ell 1 10 02 2A A0 05 5 offers a 3/8-24 threaded housing for ease of mounting in closed vessels or chambers. P PC CB B P PIIE EZ ZO OT TR RO ON NIIC CS S,, IIN NC C.. 7 71 16 6-6 68 84 4-0 00 00 01 1 ® ® ICP High Sensitivity ICP High Sensitivity With integral electronics With integral electronics ® ® IIC CP P S SO OU UN ND D P PR RE ES SS SU UR RE E S SE EN NS SO OR RS S S Se er riie es s 1 10 03 3 Developed by a leading aeronautical research laboratory, this sophisticated sensor has played a major role in the development of rockets, supersonic bombers and modern weapon systems. These tiny instruments measure transient events, turbulence, and other such acoustic phenomena on Models 103A, 103A11 structures and aerodynamic models. They are structured with a ceramic crystal element, a microelectronic amplifier and an accelerometer to virtually eliminate vibration sensitivity. A thin, recessed Invar diaphragm and a bender mode crystal element make this sensor useful for very low pressure measurements. With a rise time of less than one millisecond, series 103 will faithfully follow transient events up to several hundred milliseconds duration, such as a step function calibration pressure. See specifications on Models 103A02, page 12. 103A12 M Mo od de ell 1 10 03 3A A has a 2 psi range, 1500 mV/psi sensitivity, a flat surface for adhesive mounting, and 12 inch pigtail wire solder connection. M Mo od de ell 1 10 03 3A A0 02 2 has the same range and sensitivity of the 103A, with a 10- 32 threaded electrical connection. M Mo od de ell 1 10 03 3A A1 11 1 has a 6 psi range and a 500 mV/psi sensitivity with the same external configuration as the 103A. Model 106B M Mo od de ell 1 10 03 3A A1 12 2 has a high 6 psi range, 500 mV/psi sensitivity, with a 9 9 10-32 threaded electrical connection. ® ® IIC CP P H HIIG GH H-IIN NT TE EN NS SIIT TY Y S SO OU UN ND D Q QU UA AR RT TZ Z P PR RE ES SS SU UR RE E S SE EN NS SO OR RS S S Se er riie es s 1 10 06 6 M Mo od de ell 1 10 06 6B B a an nd d 1 10 06 6B B5 50 0 are high sensitivity, acceleration compensated ICP quartz pressure sensors suitable for measuring low pressure acoustic phenomena in hydraulic and pneumatic systems. They have the unique capability to measure small pressure changes of less than 0.001 psi under high static conditions. They install in a stepped hole, seal at a shoulder and are retained by a hollow clamp nut. Optional ground-isolated installations ® Model 106B50 are available with nylon-type plastic hardware or Emralon coating (refer to page 58 and 60 for additional information on mounting adaptors). See specifications on page 11. M Mo od de ell 1 10 06 6B B, the smaller unit, has a 300 mV/psi sensitivity and a resolution of 91dB (0.0001 psi). M Mo od de ell 1 10 06 6B B5 50 0 has 500 mV/psi sensitivity with a resolution to 86 dB (0.00007 psi). ® P PA AP PE ER R M MA AC CH HIIN NE E H HE EA AD DB BO OX X,, IIC CP P Q QU UA AR RT TZ Z S SE EN NS SO OR R M Mo od de ell 1 10 06 6B B1 10 0 Measures dynamic slurry pressure in the headbox of a paper machine. Model 106B10 features high sensitivity (300 mV/psi) and is capable of measuring Model 106B10 minute dynamic pressure fluctuations down to 0.0001 psi. Critical to the (Photo 1/3 Actual Size) application, it features a stainless steel corrosion-resistant diaphragm and a low frequency response down to 0.05 Hz. A floating clamp nut/seal and etched length markings on the housing enable the user to insert the sensor at repeatable depths into the headbox where the measurement is made. See specifications on page 11. P PR RE ES SS SU UR RE E A AN ND D F FO OR RC CE E S SE EN NS SO OR R D DIIV VIIS SIIO ON N T TO OL LL L F FR RE EE E: : 8 88 88 8-6 68 84 4-0 00 01 11 1 ® ICP Acoustic/Turbulence-Low Pressure With integral electronics Dimensions shown in inches except where noted. Mounting Adaptors on Page 58 Models 102A02, A07 and A09 Models 112A21, A22 and A23 Model 102A05 Thread Mount with Floating Clamp Mini Probes Thread Mount Dynamic Range (2) psi 0.1 to 100 0.01 to 50 MODEL NUMBERS 102A02, A05 112A21 102A07, 112A22 102A09, 112A23 Sensitivity (8) mV/psi 50 ± 10 100 50 ± 10 Resolution psi 0.002 0.001 Range (output Voltage) psi 100 (5V) 50 (5V) 50 (2.5V) Maximum Pressure psi 1000 500 1000 Linearity (3) %FS ≤ 1 Resonant Frequency kHz ≥ 250 Rise Time µs ≤ 2 Discharge Time Constant (4) s ≥ 1 10 10 Low Frequency (-5%) (4) Hz 0.5 Shock (max) g 20 000 Acceleration Sensitivity psi/g ≤ 0.002 Temperature Range °F -100 to +275 Temperature Coefficient %/°F ≤ 0.03 Flash Temperature (max) (7) °F 3000 Polarity (positive pressure) positive Output Impedance ohm < 100 Output Bias + volt 8 to 14 3 to 8 Power Required: Voltage +VDC 20 to 30 11 to 30 Constant Current mA 2 to 20 Ground Isolation models 102A02, A05 102A07 102A09 Sensing Element material quartz Case (5) material 17-4-PH Diaphragm (5) (6) material Invar Connector (6) type 10-32 coax Sealing (6) type epoxy (conn) Hermetic Seal (6) prefix H Stainless Steel Diaphragm prefix S Emralon Gnd. Isolation Coating prefix E (112 only) Water-resistant Cable prefix W (specify length) Notes: 1. For recess mount, Model 065A05 seal sleeve is available. 5. Special diaphragm or case material available. 2. Measures dynamic pressures from full vacuum to rated maximum. 6. Diaphragms of all sensors are welded or integral. Hermetic option specifies a fused-glass 3. % FS of any calibration range; zero-based best straight line. electrical connector and welded joints. 4 Discharge Time Constant (DTC) relates low-frequency to signal lost during transient 7. Flash temperatures associated with shock waves or combustion. events at room temperature. See technical section on page 78. 8. Unless otherwise designated, sensitivities are ±15%. P PC CB B P PIIE EZ ZO OT TR RO ON NIIC CS S,, IIN NC C.. 7 71 16 6-6 68 84 4-0 00 00 01 1 FREQ ENVIRONMENTAL AMPLITUDE OPTIONS PHYSICAL ELECTRICAL RESP ® ® ICP Acoustic/Turbulence-Low Pressure ICP Acoustic/Turbulence-Low Pressure With integral electronics With integral electronics Mounting Adaptors on Page 58 Model 106B Model 106B10 Model 106B50 Dynamic Range (2) psi 0.001 to 8.3 0.0001 to 5 0.001 to 8.3 MODEL NUMBERS 106B 106B50 106B10 Sensitivity (6) mV/psi (mV/Pa) 300 (0.04) 500 (0.07) 300 (0.04) Resolution psi (dB) 0.0001 (91) 0.00007 (86) 0.0001 (91) Range (± 2.5V output) psi (dB) 8.3 (186) 5 (182) 8.3 (186) Maximum Pressure (step) psi 200 100 100 Maximum Pressure (static) psi 2 000 500 200 Linearity (2) %FS ≤ 1 11 Resonant Frequency kHz ≥ 60 ≥ 40 ≥ 60 11 Rise Time µs ≤ 9 ≤ 12 ≤ 9 Discharge Time Constant (3) s ≥ 1 ≥ 10 Low Frequency (-5%) (3) Hz 0.5 0.05 Shock (max) g 2000 1000 2000 Acceleration Sensitivity psi/g ≤ 0.002 ≤ 0.05 Temperature Range °F -65 to +250 Temperature Coefficient %/°F ≤ 0.03 Polarity (positive pressure) positive Output Impedance ohm ≤ 100 Output Bias + volt 3 to 8 Power Required: Voltage +VDC 11 to 30 Constant Current mA 2 to 20 Ground Isolation models see options Sensing Element material quartz Case material 17-4-PH 316L Diaphragm (4) material 316L Connector (4) type 10-32 coax TNC coax Sealing (4) type welded hermetic environmental Hermetic Seal (4) prefix standard n/a Stainless Steel Diaphragm prefix standard Emralon Gnd. Isolation Coating prefix E n/a Water-resistant Cable prefix W (specify length) Notes: 4. Diaphragms of all sensors are welded or integral. Hermetic option specifies a 1. Measures dynamic pressures from full vacuum to rated maximum. fused-glass electrical connector and welded joints. 2. % FS of any calibration range; zero-based best straight line. 5. Flash temperatures associated with shock waves. 3. Discharge Time Constant (DTC) relates low-frequency to signal lost during transient 6. Unless otherwise designated, sensitivities are ±15%. events at room temperature. See technical section on page 78. P PR RE ES SS SU UR RE E A AN ND D F FO OR RC CE E S SE EN NS SO OR R D DIIV VIIS SIIO ON N T TO OL LL L F FR RE EE E: : 8 88 88 8-6 68 84 4-0 00 01 11 1 ELECTRICAL ENVIRONMENTAL FREQ RESP AMPLITUDE OPTIONS PHYSICAL ® ® ICP Acoustic/Turbulence-Low Pressure ICP Acoustic/Turbulence-Low Pressure With integral electronics With integral electronics Dimensions shown in inches except where noted. Models 103A and 103A11 Models 103A02 and 103A12 Dynamic Range (1) psi 0.0001 to 2 0.007 to 6 MODEL NUMBERS 103A 103A02 103A11 103A12 Sensitivity (5) mV/psi (mv/Pa) 1 500 (0.22) 500 (0.07) Resolution psi (dB) 0.00002 (78) 0.0007 (88) Range (for 3V output) psi(dB) 2 (177) 6 (186) Maximum Pressure (step) psi 25 Maximum Pressure (static) psi 25 Linearity (2) %FS ≤ 2 Resonant Frequency kHz ≥ 13 Rise Time µs ≤ 25 12 12 Discharge Time Constant (3) s ≥ 0.1 Low Frequency (-5%) (3) Hz 5 Shock (max) g 1000 Acceleration Sensitivity psi/g ≤ 0.0005 Temperature Range °F -100 to +175 Temperature Coefficient %/°F ≤ 0.03 Flash Temperature (4) °F 1000 Polarity (positive pressure) positive Output Impedance 0hm ≤ 100 Output Bias + volt 3 to 8 Power Required: Voltage +VDC 11 to 30 Constant Current mA 2 to 20 Sensing Element material ceramic Case material Invar Diaphragm material Invar Connector type pigtail 10-32 coax pigtail 10-32 coax Sealing type epoxy Notes: 1. Measures dynamic pressures from full vacuum to rated maximum. 4. Flash temperatures associated with shock waves or combustion. 2. % FS of any calibration range; zero-based best straight line. 5. Unless otherwise specified, sensitivities are ±15%. 3. Discharge Time Constant (DTC) relates low-frequency to signal lost during transient events at room temperature. See technical section on page 78. P PC CB B P PIIE EZ ZO OT TR RO ON NIIC CS S,, IIN NC C.. 7 71 16 6-6 68 84 4-0 00 00 01 1 PHYSICAL ELECTRICAL ENVIRONMENTAL FREQ RESP AMPLITUDE High Frequency Shock High Frequency Shock Wave/Blast/Explosion Wave/Blast/Explosion Pressure Sensors Pressure Sensors PCB offers a complete line of ultra-high frequency Shock tube pressure sensors with quartz, ceramic and tourmaline sensing elements for a wide array of shock wave, blast Free-field blast and explosive testing. Typical applications include measurement of shock and blast waves; combustion, detonation and explosions in closed bombs; projectile Projectile and time of arrival velocity; free field and underwater explosive testing; and squib lot acceptance testing. All of these applications require high frequency response and durability; ability to Underwater blast drive long cables and operate in adverse environments may also be important. For those involved in explosive blast applications, “Soroka’s Air Blast Tables” compile free-air incident and reflected blast data from Bare Spherical Pentotlite; this information is available from PCB. 13 13 In applications involving long input cables, care must be exercised to assure the measurement system has adequate frequency response. Capacitance associated with the long cables can act as a low pass filter. Sensor output voltage, cable capacitance and constant current are factors to be considered. More current is required to drive higher voltages over longer cables. Selecting a sensor to provide about 1 V full scale for the expected pressure to be measured, rather than 5V, will provide 5 times greater frequency response for a given current and cable length. PCB signal conditioners can be adjusted up to 20 mA to drive long cables. Most of the sensors listed in this section incorporate acceleration-compensating sensing elements with integral electronics, which provide a frequency-tailored, non- resonant response. Frequency tailored sensors have microsecond rise time and suppressed resonance to faithfully follow shock wave events without the characteristic “ringing” common in other sensors. See typical test results on page v, “Microsecond Shockwave Non-Resonant Response.” The cable driving nomograph listed on pages 82 and 83 will help determine the Voltage/Cable Length/Constant Current requirements and provide information on testing long cables. P R E S S U R E A N D F O R C E S E N S O R S D I V I S I O N P PC CB B 716-684-0001 P PF FS S T To ollll F Fr re ee e 888-684-0011 F Fa ax x 716-686-9129 E Em ma aiill pfssales@pcb.com W We eb b S Siitte e www.pcb.com High Frequency Shock Wave/Blast/Explosion High Frequency Shock Wave/Blast/Explosion G GE EN NE ER RA AL L P PU UR RP PO OS SE E S SE EN NS SO OR RS S S Se er riie es s 1 10 02 2 ® 500 kHz ICP sensors are designed to provide frequency-tailored, non- resonant output when subjected to instantaneous, reflected (face-on) shock wave inputs. They are structured with acceleration-compensated M Mo od de ells s 1 10 02 2A A,, A A0 03 3,, quartz elements and integral microelectronics. Because of their clean, A A0 04 4,, A A0 06 6,, A A1 15 5 non-resonant output, Series 102A ICPsensors are well suited for high- frequency measurements in shock tubes, closed bombs, and squib (explosive bolt actuators) lot acceptance testing. Their high-voltage, low- impedance output is electrically isolated from ground. Solid-state construction provides ruggedness and durability. See specifications on page 17. M Mo od de ells s 1 10 02 2A A,, A A0 03 3,, A A0 04 4,, A A0 06 6 a an nd d A A1 15 5 are available in 5 standard ranges from 100 to 10 000 psi, with sensitivities from 25 to 0.5 mV/psi. Two linear NIST-traceable calibration certificates, Full Scale (FS) and 10% of FS, are supplied with each sensor. M Mo od de ell 1 10 02 2A A1 12 2 has an adjustable floating clamp nut, to vary the depth of the sensor in the mounting port. ® ® M MIIN NII-P PR RE ES SS SU UR RE E P PR RO OB BE ES S C CH HA AR RG GE E A AN ND D IIC CP P S Se er riie es s 1 11 13 3 M Mo od de ell 1 10 02 2A A1 12 2 14 14 500 kHz mini-gauges are designed to excel in shock tube and other high-frequency applications where minimum sensor diameter is required. With frequency-tailored microsecond rise time, these acceleration-compensated sensors follow incident and reflected shock waves without the “ringing” characteristic of most other sensors. Five ranges are available to 10 000 psi. Utilizing a floating clamp nut, they can install in a 5/16-24 or M7 x 0.75 port. If miniature size is not required, the Series 113 High Frequency Sensors are incorporated in off-ground 3/8-24 threaded housings. as the Series (See 102A description above). S Se er riie es s 1 11 13 3 are acceleration-compensated 0.35 pC/psi charge mode sensors for use in adverse environmental conditions. The charge signal from this conventional piezoelectric sensor is converted into a voltage signal using a PCB or similar charge amplifier. See specifications on S Se er riie es s 1 11 13 3 page 18. S Se er riie es s 1 11 13 3A A2 20 0 sensors are ICP voltage mode sensors that convert pressure input to a clean, high resolution output which is virtually insensitive to cable length. Five ranges and sensitivities are available. See specifications on page 17. N Ne ew w S Se er riie es s 1 11 13 3A A3 30 0 ICP mini-gauges with Invar housing and diaphragm for reduced thermal transient sensitivity are recommended for most shock and blast wave measurements. See specifications on page 17. P PC CB B P PIIE EZ ZO OT TR RO ON NIIC CS S,, IIN NC C.. 7 71 16 6-6 68 84 4-0 00 00 01 1 High Frequency Shock Wave/Blast/Explosion High Frequency Shock Wave/Blast/Explosion H HIIG GH H F FR RE EQ QU UE EN NC CY Y,, A AC CC CE EL LE ER RA AT TIIO ON N-C CO OM MP PE EN NS SA AT TE ED D Q QU UA AR RT TZ Z P PR RE ES SS SU UR RE E P PR RO OB BE ES S S Se er riie es s 1 10 09 9B B,, 1 11 19 9A A a an nd d 1 11 19 9A A1 10 0 Designed for high-pressure, high-frequency response applications, such as shock wave, blast, explosion, detonation, and ballistics. The sensors feature an acceleration-compensated quartz element, high resonant frequency, and a rugged ceramic-coated integral diaphragm. N Ne ew w! ! M Mo od de ells s 1 11 19 9A A1 11 1 a an nd d 1 11 19 9A A1 12 2 N Ne ew w M Mo od de ells s 1 11 19 9A A1 11 1 a an nd d 1 11 19 9A A1 12 2 are charge mode sensors designed for pressure measurements up to 80 000 and 120 000 psi. They feature a floating clamp nut that reduces strain sensitivity on the sensor body due to mounting torque. See specifications on page 20. N Ne ew w M Mo od de ells s 1 10 09 9B B1 11 1 a an nd d 1 10 09 9B B1 12 2 have integral electronics and are designed for 80 000 and 100 000 psi measurements, respectively. They feature a floating clamp nut mount which creates less strain on the body if the sensor is not installed in a precision mounting port. These sensors contain shock protected electronics for applications where the sensor may see high shock. See specifications on page 19. M Mo od de ells s 1 11 19 9A A a an nd d 1 11 19 9A A0 02 2 are charge mode sensors for use in harsh N Ne ew w! ! or high temperature environments, with integral mounting threads. They M Mo od de ells s 1 10 09 9B B1 11 1 a an nd d B B1 12 2 have dynamic ranges of 80 000 and 120 000 psi, respectively. See specifications on page 20. 15 15 ® ® T TIIM ME E O OF F A AR RR RIIV VA AL L,, IIC CP P M MIIC CR RO O-P PR RE ES SS SU UR RE E S SE EN NS SO OR RS S S Se er riie es s 1 13 32 2A A3 30 0 High-Sensitivity Micro-Pressure Sensors are well suited for short wavelength acoustic and shock wave measurements associated with high-frequency projectile detection systems. Incorporating a 1mm diameter sensing element and integral microelectronics in a 3mm housing, these sensors have very high sensitivity and microsecond M Mo od de ells s 1 11 19 9A A a an nd d 1 11 19 9A A0 02 2 response capable of measuring the bow and stern wave from a passing projectile. An internal 8 kHz high-pass filter eliminates low-frequency inputs. Series 132 Microsensors are available in five different physical configurations to accommodate a wide range of application requirements. See page 21 for specifications. S Se er riie es s 1 13 32 2A A3 30 0 Microsensors all have a sensitivity of 100 mV/psi and come in a variety of external configurations to suit your specific application. 699.0 mV Velocity Data from PCB 2" ID Shock Tube T Ty yp piic ca all 1 13 32 2 M Miic cr ro os se en ns so or r 599.0 mV ((P Ph ho otto o iis s ttw wo o ttiim me es s a ac cttu ua all s siiz ze e)) 499.0 mV 399.0 mV 299.0 mV 199.0 mV 99.00 mV -1.000 mV -101.- mV -524.2 uS 269.4 uS 1.063 mS 1.856 mS 2.650 mS T Ty yp piic ca all M Miic cr ro os se en ns so or r IIn nc ciid de en ntt P Pr re es ss su ur re e R Re ec co or rd d ffr ro om m 2 2"" II..D D.. S Sh ho oc ck k T Tu ub be e P PR RE ES SS SU UR RE E A AN ND D F FO OR RC CE E S SE EN NS SO OR R D DIIV VIIS SIIO ON N T TO OL LL L F FR RE EE E: : 8 88 88 8-6 68 84 4-0 00 01 11 1 High Frequency Shock Wave/Blast/Explosion High Frequency Shock Wave/Blast/Explosion T TO OU UR RM MA AL LIIN NE E P PR RE ES SS SU UR RE E B BA AR R S Se er riie es s 1 13 34 4 a an nd d 1 13 34 4A A2 20 0 This unique non-resonant sensor is designed for instantaneous, reflected (face-on) shock wave pressure measurements. A shock wave pressure S Se er riie es s 1 13 34 4 impacting the tourmaline crystal element dissipates in the special silver bar to which it is bonded without reflecting or “ringing” back through the crystal structure. The sensor has a 0.2-microsecond rise time. Since the sensor diaphragm end is coated with a conductive silver epoxy, the sensor should not be used in water or chemical environments. See specifications on page 22. S Se er riie es s 1 13 34 4 sensors are charge output versions of the tourmaline 3.5 pressure bar and are available in 10k and 20k psi ranges. These 3.0 sensors can be ordered with in-line amplifiers (see below) or used with 2.5 a conventional laboratory type charge amplifier. 2.0 The 1 13 34 4A A2 20 0 S Se er riie es s consists of a 134 style sensor in series with a 402 1.5 style in-line amplifier to provide a convenient voltage output. 1.0 0.5 ® ® IIC CP P F FR RE EE E-F FIIE EL LD D B BL LA AS ST T P PR RE ES SS SU UR RE E “ “P PE EN NC CIIL L” ” P PR RO OB BE E 0.0 0.0s 50.0us 100.0us 150.0us S Se er riie es s 1 13 37 7 TIME “Pencil” Probes were originally developed at Aberdeen Proving Ground S Sh ho oc ck kw wa av ve e M Me ea as su ur re em me en ntt w wiitth h M Miic cr ro os se ec co on nd d R Riis se e T Tiim me e a an nd d N No on n-R Re es so on na an ntt R Re es sp po on ns se e for measuring blast effects on structures and humans. Although early 16 16 Models 137A, 137A11 and 137A12 were structured with ceramic elements, the new Series 137A20 incorporates acceleration- compensated quartz elements and integral microelectronics for long cable driving, improved stability and low thermal sensitivity. See page 23 S Se er riie es s 1 13 37 7A A2 20 0 for a typical long-cable, field-blast measurement system. ((P Ph ho otto o iis s 1 1/ /1 10 0 a ac cttu ua all s siiz ze e)) S Se er riie es s 1 13 37 7A A2 20 0 ICP pencil probes are available in three models with ranges of 50, 500, and 1000 psi. See specifications on page 23. N Ne ew w! ! ® ® IIC CP P T TO OU UR RM MA AL LIIN NE E U UN ND DE ER RW WA AT TE ER R B BL LA AS ST T S SE EN NS SO OR R Q Qu ua ar rttz z s sttr ru uc cttu ur re ed d S Se er riie es s 1 13 38 8 Series 138 Sensors measure shock wave pressures associated with underwater explosion testing. The sensors are structured with a volumetrically sensitive tourmaline crystal, suspended and sealed in an insulating, oil-filled vinyl tube. They have integral microelectronics. These underwater shock wave sensors provide a clean, non-resonant high-voltage output through long cables in adverse underwater S Se er riie es s 1 13 38 8 environments. They can be supplied with a sealed cable of appropriate ((P Ph ho otto o iis s 1 1/ /2 2 a ac cttu ua all s siiz ze e)) length, ready to operate. Two physical configurations are available. See specifications on page 24. M Mo od de ells s 1 13 38 8A A0 01 1,, A A0 05 5,, A A1 10 0,, A A2 25 5 a an nd d A A5 50 0 are 7.6 inches in length and contain a weight attachment hole to suspend the sensor in water at a given depth. M Mo od de ells s 1 13 38 8A A0 02 2,, A A0 06 6,, A A1 11 1,, A A2 26 6 a an nd d A A5 51 1 are 4.2 inches long. They can be taped to a structure or used in restricted locations. P PC CB B P PIIE EZ ZO OT TR RO ON NIIC CS S,, IIN NC C.. 7 71 16 6-6 68 84 4-0 00 00 01 1 Amplitude (volts) ® ® ICP High Frequency-General Purpose ICP High Frequency-General Purpose With integral electronics With integral electronics Dimensions shown Optional o-ring isolation mounting adaptor is available for blast applications; see page 59. in inches except where noted. Mounting Adaptors on Page 58 Model 102A12 Models 102A, A03, A04, A06, A15 Models 113A21, A22, A23, A24, A26 Ground Isolated Ground Isolated NEW all Invar Models 113A31, A32, A33, A34, A36 Dynamic Range (2) psi 0.05 to 200 0.1 to 500 0.2 to 1000 1 to 5000 2 to 10 000 102A12, A15 102A06 102A04 102A 102A03 MODELNUMBERS 113A21 113A26 113A24 113A22 113A23 113A31 113A36 113A34 113A32 113A33 Sensitivity (9) mV/psi 25 10 ± .5 5 ± .25 1 ± .05 0.5 ± .03 Resolution psi 0.003 0.010.02 0.1 0.2 Range (for 5V output) psi 200 500 1000 5000 10 000 Range (for 10V output) (3) psi 400 1000 2000 10 000 20 000 Maximum Pressure psi 1000 15 000 20 000 10 000 Linearity (4) %FS ≤ 1 Resonant Frequency (5) kHz ≥ 500 Rise Time µs ≤ 1 17 17 Discharge Time Constant (6) sec ≥ 1 ≥ 50 ≥ 100 ≥ 500 ≥ 1 000 Low Frequency (-5%) (6) Hz 0.5 0.01 0.005 0.001 0.0005 Shock (max) g pk 20 000 Acceleration Sensitivity psi/g 0.002 Temperature Range °F -100 to +275 Temperature Coefficient %/°F ≤ 0.03 Flash Temperature °F 3000 Polarity (positive pressure) positive Output Impedance ohm ≤ 100 Output Bias +volts 8 to 14 Power Required: Voltage +VDC 20 to 30 Constant Current mA 2 to 20 Ground Isolation model 102A12, A15 102A06 102A04 102A 102A03 Sensing Element material quartz Case (7) material 17-4PH (113A30 series : Invar) Diaphragm (8) material Invar Connector (8) type 10-32 coaxial Sealing (8) type epoxy Hermetic Seal (8) prefix H Stainless Steel Diaphragm prefix S (for series 113A20 only) Emralon Gnd. Isolation Coating prefix E (for series 113 only) Negative Polarity prefix N Momentum Trap prefix T Water-resistant Cable prefix W (specify length) NOTES: 6. Discharge Time Constant (DTC) relates low-frequency to signal lost during transient events at room temperature. 1. For recess mount, Model 065A05 seal sleeve is available. See technical section on page 78. 2. Measures dynamic pressures from full vacuum to rated maximum. 7. Special diaphragm or case material available. 3. ≥+24 VDC supply required for 10V output. If optional calibration to 10V range is required, linearity specs may 8. Diaphragms of all sensors are welded or integral. Hermetic option specifies a fused-glass electrical connector and change. welded joints. 4. % FS any calibrated range; zero-based best straight line. 9. Unless otherwise designated, sensitivities are ± 15%. 5. Suppressed resonance. P PR RE ES SS SU UR RE E A AN ND D F FO OR RC CE E S SE EN NS SO OR R D DIIV VIIS SIIO ON N T TO OL LL L F FR RE EE E: : 8 88 88 8-6 68 84 4-0 00 01 11 1 OPTIONS PHYSICAL ELECTRICAL ENVIRONMENTAL FREQ RESP AMPLITUDE High Frequency-General Purpose High Frequency-General Purpose Charge mode Charge mode Dimensions shown in inches except where noted. Mounting Adaptors on Page 58 Models 113A, A02 and A03 Dynamic Range (8) psi 0.01 to 100 0.1 to 3000 1 to 15 000 MODEL NUMBERS 113A02 113A 113A03 Sensitivity (7) -pC/psi 0.35 Resolution (2) psi 0.01 Maximum Pressure psi 1000 10 000 20 000 Linearity (3) %FS ≤ 1 ≤ 2 18 18 Resonant Frequency (5) kHz ≥ 500 Rise Time µs ≤ 1 Shock (max) g pk 20 000 Acceleration Sensitivity psi/g 0.002 Temperature Range °F -400 to +400 Temprature Coefficient %/°F ≤ 0.03 Flash Temperature °F 3000 Polarity (positive pressure) (6) negative Capacitance pF 12 12 Insulation Resistance at 70°F ohm ≥ 10 Sensing Element material quartz Case (4) material 17-4PH Diaphragm (4) material Invar Connector type 10-32 coaxial Sealing type epoxy Hermetic Seal prefix H Stainless Steel Diaphragm prefix S Emralon Gnd Isolation Coating prefix E Positive Polarity prefix P NOTES: 1. For recess mount, Model 065A05 seal sleeve is available. 5. Suppressed resonance. 2. Resolution determined by system noise and cable length. 6. Charge amplifier inverts the signal. 3. % FS of any calibration range; zero-based best straight line. 7. Unless otherwise designated, sensitivities are ±15%. 4. Special case and diaphragm material available. 8. Measures dynamic pressures from full vacuum to rated maximum. P PC CB B P PIIE EZ ZO OT TR RO ON NIIC CS S,, IIN NC C.. 7 71 16 6-6 68 84 4-0 00 00 01 1 OPTIONS PHYSICAL ELECTRICAL ENVIRONMENTAL FREQ AMPLITUDE RESP ® ® ICP High Frequency-High Pressure ICP High Frequency-High Pressure With integral electronics With integral electronics Dimensions shown in inches except where noted. Dimensions shown in inches except where noted. Models 109B11 and 109B12 Dynamic Range (1) psi 20 to 80 000 20 to 100 000 MODEL NUMBERS 109B11 109B12 Sensitivity (3) mV/psi 0.07 Resolution psi 2 Range psi 80 000 (6V) 100 000 (7V) Maximum Pressure psi 125 000 19 19 Linearity (2) %FS ≤ 2 Suppressed Resonant kHz ≥ 400 Rise Time µs ≤ 1 Discharge Time Constant (4) sec ≥ 2000 Low Frequency (-5%) (5) Hz 0.0003 Shock (max) g pk 80 000 Acceleration Sensitivity psi/g 0.004 Temperature Range °F -100 to +275 Temperature Coefficient %/°F ≤ 0.03 Flash Temperature °F 3000 Polarity (positive pressure) positive Output Impedance ohm ≤ 100 Output Bias +volts 8 to 14 Power Required: Voltage +VDC 20 to 30 Constant Current mA 2 to 20 Sensing Element material quartz Case material st stl Diaphragm (integral) material stainless steel ceramic coated Connector type 10-32 coaxial Sealing type epoxy Water-resistant Cable prefix W (specify length) NOTES: 1. Measures dynamic pressures from full vacuum to rated maximum. 4. Discharge Time Constant (DTC) relates low-frequency to signal lost during transient 2. % FS of any calibration range; zero-based best straight line. events at room temperature. See technical section on page 78. 3. Unless otherwise designated, sensitivities are ±15%. 5. For special system requirements to achieve low-frequency response, contact factory. P PR RE ES SS SU UR RE E A AN ND D F FO OR RC CE E S SE EN NS SO OR R D DIIV VIIS SIIO ON N T TO OL LL L F FR RE EE E: : 8 88 88 8-6 68 84 4-0 00 01 11 1 OPT PHYSICAL ELECTRICAL ENVIRONMENTAL FREQ RESP AMPLITUDE High Frequency-High Pressure High Frequency-High Pressure Charge mode Charge mode Dimensions shown in inches except where noted. Models 119A11 and 119A12 Models 119A and 119A02 NEW High Shock Models Dynamic Range (1) psi 10 to 80 000 20 to 120 000 MODEL NUMBERS 119A 119A11 119A02 119A12 Sensitivity (5) -pC/psi 0.25 Resolution (2) psi 1 2 Range psi 80 000 120 000 20 20 Maximum Pressure psi 100 000 125 000 Linearity (3) %FS ≤ 2 Resonant Frequency kHz ≥ 400 Rise Time µs ≤ 1 Shock (max) g pk 80 000 Acceleration Sensitivity psi/g 0.004 Temperature Range °F -400 to +400 Temperature Coefficient %/°F ≤ 0.03 Flash Temperature °F 4000 Polarity (positive pressure) negative Capacitance pF 20 12 Insulation Resistance at 70°F ohm ≥ 10 Sensing Element material quartz Case material stainless steel Diaphragm (integral) (4) material stainless steel ceramic coated Connector type 10-32 coaxial Sealing type epoxy Positive Polarity prefix P Water-resistant Cable prefix W (specify length) NOTES: 1. Measures dynamic pressures from full vacuum to rated maximum. 2. Resolution determined by system noise and cable length. 3. % FS of any calibration range; zero-based best straight line. 4. Diaphragm integral with housing and is ceramic coated. 5. Unless otherwise designated, sensitivities are ±15%. P PC CB B P PIIE EZ ZO OT TR RO ON NIIC CS S,, IIN NC C.. 7 71 16 6-6 68 84 4-0 00 00 01 1 FREQ OPT’L PHYSICAL ELECTRICAL ENVIRONMENTAL AMPLITUDE RESP ® ® ICP Time of Arrival Microsensor ICP Time of Arrival Microsensor With integral electronics With integral electronics Dimensions shown in inches except where noted. Dimensions shown in inches except where noted. Models 132A36 Models 132A31 Models 132A32 Models 132A35 NOTE: Diameter of the ceramic sensing element in all models is 0.03 inches. Models 132A37 Dynamic Range (1) psi 0.05 to 50 MODEL NUMBERS 132A31 132A32 132A35 132A36 132A37 (5) Sensitivity (4) mV/psi 130 to 180 21 21 Resolution psi 0.001 Range (for 5V output) psi 50 Maximum Pressure (6) psi 800 Resonant Frequency MHz ≥ 1 Rise Time (reflected) µs ≤ 0.5 Rise Time (incident, in air) (7) µs ≤ 3 Discharge Time Constant (8) µs ≥ 45 Low Frequency (-5%) (8) kHz 11 Temperature Range °F 0 to +175 Polarity (positive pressure) positive Output Impedance ohm ≤ 100 Output Bias +volts 8 to 14 Power Required: Voltage +VDC 20 to 30 Constant Current mA 2 to 20 Sensing Element material ceramic Case material stainless steel Sensing Surface (coating) material conductive epoxy Connector type pigtail (2) 10-32 plug (3) pigtail (2) 10-32 jack pigtail (2) Sealing type epoxy NOTES: 1. Measures dynamic pressures from full vacuum to rated maximum. 6. Maximum pressure applies to listed models only with clamp nut. 2. 10-32 solder connector supplied. 7. Mach I 3. On end of attached cable. 8. Discharge Time Constant (DTC) relates low-frequency to signal lost during transient 4. Unless otherwise designated, sensitivities are ±15%. events at room temperature. See technical section on page 78. 5. Adaptor installs with press fit and should not be used at pressures greater than 20 psi unless properly supported from back side to prevent sensor from being blown out at higher pressures. P PR RE ES SS SU UR RE E A AN ND D F FO OR RC CE E S SE EN NS SO OR R D DIIV VIIS SIIO ON N T TO OL LL L F FR RE EE E: : 8 88 88 8-6 68 84 4-0 00 01 11 1 PHYSICAL ELECTRICAL FREQ RESP AMPLITUDE Tourmaline Pressure Bar Tourmaline Pressure Bar Dimensions shown in inches except where noted. NOTE: Models 134A and 134A02 Series 134A20 Refer to test data plots on page v. Dynamic Range (1) psi to 10 000 to 20 000 MODEL NUMBERS 134A 134A02 Sensitivity (3) pC/psi 0.125 Resolution (2) psi 1 Maximum Pressure psi 15 000 40 000 Linearity (2) (4) %FS ≤ 2 Resonant Frequency kHz 1500 Rise Time (reflected) µs ≤ 0.2 Temperature Range °F +32 to +120 Flash Temperature °F 5 000 Polarity (positive pressure) positive 10 Insulation Resistance at 70°F > ohm ≥ 10 22 22 Capacitance pF 10 Sensing Surface material tourmaline Case material 303 stainless steel Sensing Surface material conductive epoxy with ablative tape Connector type 10-32 S Sp pe ec ciiffiic ca attiio on ns s ffo or r 1 13 34 4A A2 20 0 S Se er riie es s T To ou ur rm ma alliin ne e P Pr re es ss su ur re e B Ba ar r ® ® C Co ou up plle ed d tto o 4 40 02 2 S Stty ylle e IIC CP P IIn n-L Liin ne e V Vo olltta ag ge e A Am mp plliiffiie er r ((IIllllu us sttr ra atte ed d A Ab bo ov ve e)) Dynamic Range (1) psi 1000 5000 10 000 20 000 MODEL NUMBERS 134A24 (5) 134A22 (5) 134A23 (5) 134A27 (5) Tourmaline Pressure Bar Model Number 134A In-Line Voltage Amplifier Model Number 402A 402A02 402A16 402A17 Sensitivity (3) mV/psi 5 1 0.5 0.25 Range (for 5V output) psi 1000 5000 10 000 20 000 Maximum Pressure psi 15 000 20 000 Discharge Time Constant (4) sec ≥ 2 ≥ 0.2 ≥ 1 ≥ 0.5 Output Impedance ohm ≤ 100 Output Bias +volts 8 to 14 Power Required: Voltage +VDC 20 to 30 Constant Current mA 2 to 20 NOTES: 1. Calibrated as a system for voltage sensitivity. 5. All specifications not listed in this table can be found in the table above for the 134A 2. % FS of any calibration range; zero-based best straight line. and 134A02. 3. Unless otherwise designated, sensitivities are ±15%. 4. Discharge Time Constant (DTC) relates low-frequency to signal lost during transient events at room temperature. See technical section on page 78. P PC CB B P PIIE EZ ZO OT TR RO ON NIIC CS S,, IIN NC C.. 7 71 16 6-6 68 84 4-0 00 00 01 1 FREQ PHYSICAL ELECTRICAL ENV’L AMPLITUDE RESP ® ® ICP Free Field Blast Pencil Probe- ICP Free Field Blast Pencil Probe- With integral electronics With integral electronics Dimensions shown in inches except where noted. Typical Field Blast Installation Single or Multichannel Single or Multichannel Series 137A20 Blast Probe Constant Current Power Constant Current Power READOUT Series 482,583 or 584 (not supplied) Series 482, 583 or 584 Mount Long RG-62U Coaxial 13.5 pF/ft Recommended or RG-58U 4 *10 Pa 9.00 8.00 7.00 6.00 5.00 4.00 3.00 2.00 BNC Jack 1.00 Connector Typical Free Field 0.00 Blast Record from 137 -1.00 Series Blast Probe. -2.00 Models 137A21, A22 and A23 0 .5 1 1.5 2 2.5 3 TIME Time (ms) 23 23 Dynamic Range (1) psi 0.05 to 50 0.1 to 500 1 to 1000 MODEL NUMBERS 137A23 137A22 137A21 Sensitivity (5) mV/psi 100 10 1 Resolution psi 0.005 0.01 0.1 Range (for 5V output) psi 50 500 1000 (1V) Range (for 10V output) (2) psi 100 1000 5000 (5V) Maximum Pressure psi 1000 5000 Linearity (3) %FS ≤ 1 Resonant Frequency kHz ≥ 500 Rise Time (incident) µs ≤ 4 Discharge Time Constant (4) sec ≥ 0.2 Temperature Range °F -100 to +275 Temperature Coefficient %/°F ≤ 0.03 Polarity (positive pressure) positive Output Impedance ohm ≤ 100 Output Bias +volts 8 to 18 8 to 14 Power Required: Voltage +VDC 20 to 30 Constant Current mA 2 to 20 Sensing Element material quartz Probe Case material aluminum alloy Diaphragm (sensing element) material Invar Connector type BNC jack Sealing type epoxy Water-resistant Cable prefix W (specify length) NOTES: 1. Measures dynamic pressures from full vacuum to rated maximum. 4. Discharge Time Constant (DTC) relates low-frequency to signal lost during transient 2. ≥+24 VDC supply required for 10V output. If optional calibration to 10V range is events at room temperature. See technical section on page 78. required, linearity spec may change. 5. Unless otherwise designated, sensitivities are ±15%. 3. % FS any calibrated range; zero-based best straight line. P PR RE ES SS SU UR RE E A AN ND D F FO OR RC CE E S SE EN NS SO OR R D DIIV VIIS SIIO ON N T TO OL LL L F FR RE EE E: : 8 88 88 8-6 68 84 4-0 00 01 11 1 Overpressure OPT PHYSICAL ELECTRICAL ENV’L FREQ RESP AMPLITUDE ® ® ICP Tourmaline Underwater Blast Sensor ICP Tourmaline Underwater Blast Sensor With integral electronics With integral electronics Dimensions shown in inches except where noted. Models 138A01, A05, A10, A25, A50 5000 Standard Length 4000 2000 0.0000 000 -2000 -4000 -5000 0.0020 0.0022 0.0024 0.0026 0.0028 0.0030 0.0032 0.0034 SECONDS Typical Underwater Blast Record Models 138A02, A06, A11, A26, A51 from a 138 Type Sensor Short Length Dynamic Range (1) psi 1 000 5 000 10 000 25 000 50 000 24 24 MODEL NUMBERS long 138A01 138A05 138A10 138A25 138A50 short 138A02 138A06 138A11 138A26 138A51 Sensitivity (5) mV/psi 5 1 0.5 0.2 0.1 Resolution psi 0.02 0.1 0.2 0.5 1 Range (for 5V output) psi 1000 5000 10 000 25 000 50 000 Range (for 10V output) (2) psi 2000 10 000 20 000 50 000 n/a Maximum Pressure psi 50 000 Linearity (3) %FS ≤ 2 Resonant Frequency MHz ≥ 1 Rise Time (in water) µs ≤ 1.5 Discharge Time Constant (4) s ≥ 0.2 Low Frequency (-5%) (4) Hz 2.5 Shock (max) g pk 20 000 Temperature Range °F 0 to 100 Polarity (positive pressure) positive Output Impedance ohm ≤ 100 Output Bias +volts 8 to 14 Power Required: Voltage +VDC 20 to 30 Constant Current mA 2 to 4 Sensing Element material tourmaline Connector/Amplifier Housing material stainless steel ® Body Housing material Tygon tube, nylon tie, Delrin plug (where applicable) Connector type 10-32 coaxial Sealing (connector/amplifier) type welded/hermetic Water-resistant Cable prefix W (specify length) NOTES: 1. Measures dynamic pressures from full vacuum to rated maximum. 4. Discharge Time Constant (DTC) relates low-frequency to signal lost during transient 2. ≥+24 VDC supply required for 10V output. If optional calibration to 10V range is events at room temperature. See technical section on page 78. reqiured, linearity spec may change. 5. Unless otherwise designated, sensitivities are ±15%. 3. % FS of any calibrated range; zero-based best straight line. P PC CB B P PIIE EZ ZO OT TR RO ON NIIC CS S,, IIN NC C.. 7 71 16 6-6 68 84 4-0 00 00 01 1 PSI OPT PHYSICAL ENVIRONMENTAL FREQ RESP AMPLITUDE Ballistic Ballistic Pressure Sensors Pressure Sensors Over 20 years ago, PCB worked with members of the Ammunition and gun Sporting Arms and Ammunition Manufacturers’ Institute (SAAMI) to develop a durable ballistic pressure sensor testing suitable for implementation into a standardized test method for rapid-fire production testing of ammunition. Explosives testing Out of this cooperative effort, the highly successful PCB series patented 117B Conformal Ballistic Sensor was developed. In this tradition, PCB offers a complete line of Closed bombs sensors for conformal and case mouth measurements. The 117 Series conformal sensor measures true gun Recoil mechanisms chamber pressure directly through an unmodified shell case. Since the sensor diaphragm is machined to conform flush with the specific chamber diameter, the measurement Ultra high-frequency process is not altered or changed in any way. There are no cartridges to be drilled or troublesome gas passages to detonation be cleaned when using the conformal method. Conformal sensors have proven to be rugged, stable instruments, lasting hundreds of thousands of rounds. Since the same 25 25 sensor may outlast the life of many barrels, it is possible to start and finish ammunition batch qualification testing without experiencing sensor failure during the test. Our 118 Series with a ceramic coated integral diaphragm has been upgraded with an even more stable, linear sensing element. This series features a floating clamp nut that reduces strain sensitivity on the sensor body due to mounting torque. The 119 Series is an acceleration compensated version of the 118 Series. The 108 and 109 ® Series are upgraded ICP versions of the 118 and 119’s. The integral electronics in the 109 Series are shock protected, for use in high shock applications. PCB introduces the new high performance 165 Series which features an improved design for more stable, reliable measurements. Our new 165 Series was designed to retrofit popular existing mounting port styles. The new series contains a variety of models for different pressure ranges, mounting and sealing requirements. PCB also offers a high pressure static calibrator Model 905C and a high pressure dynamic calibrator Model 913A10. Side-by-side dynamic/static comparison calibration services are offered for PCB’s and competitors’ ballistic sensors. P R E S S U R E A N D F O R C E S E N S O R S D I V I S I O N P PC CB B 716-684-0001 P PF FS S T To ollll F Fr re ee e 888-684-0011 F Fa ax x 716-686-9129 E Em ma aiill pfssales@pcb.com W We eb b S Siitte e www.pcb.com Interchangeable Quartz Ballistic Sensors Interchangeable Quartz Ballistic Sensors Charge mode Charge mode N NE EW W! ! IIn ntte er rc ch ha an ng ge ea ab blle e N NA AT TO O M M1 10 0 x x 1 1..0 0 M Mo ou un ntt S Se er riie es s 1 16 65 5 Retrofits common mounting ports for drilled cartridge and case mouth installations in small and large-caliber M Mo od de ell M M1 16 65 5A A0 01 1 weapons. The improved design incorporates a more stable structure with diaphragm end seal for better accuracy, reliability, and lower thermal response. The captivated floating clamp nut reduces strain sensitivity and simplifies sensor installation. Detailed installation drawings are available for all of these models. See specifications on page 30. T Th he e M M1 16 65 5A A0 01 1 Ballistic Sensor has been extensively tested and evaluated by both static and dynamic methods. M10 mounting thread and end seal design retrofits common ports. It has been test-fired for hundreds of rounds to 60 000 and 90 000 psi in a .308 caliber proof barrel. M Mo od de ell 1 16 65 5A A0 02 2 Before shipment, each sensor goes through a factory stabilization process involving static and dynamic cycling to 100K psi and is fired 20 rounds (minimum) in our .308 caliber test barrel. 26 26 M Mo od de ell 1 16 65 5A A0 02 2 Ballistic Pressure Sensor is designed for case mouth shot shell applications to 20 000 psi. It supersedes the earlier PCB Model 167A. This model has an improved structure for better stability and dynamic-to- static response correlation. Sensitivity is stabilized by pressure cycling to 70 000 psi. M Mo od de ell M M1 16 65 5A A0 03 3 M Mo od de ell M M1 16 65 5A A0 03 3 Ballistic Pressure Sensor has a shoulder or end-seal mount and is designed for ballistic pressures of up to 80 000 psi. It features a thermal shield for extremely low thermal shock sensitivity. Two mounting methods are available: shoulder seal for flush mount, or end sealing, using the thermal shield. Both seals are supplied with each sensor. T Th he e 1 16 65 5A A0 05 5 Ballistic Sensor is manufactured to retrofit weapons which have the conical end seal mounting port. The 165A05 incorporates a specially designed integral diaphragm that reduces thermal output due to transient M Mo od de ell 1 16 65 5A A0 05 5 temperature effects. Because mounting forces are concentrated near the diaphragm, conical end seal sensors require closely controlled mounting torque. P PC CB B P PIIE EZ ZO OT TR RO ON NIIC CS S,, IIN NC C.. 7 71 16 6-6 68 84 4-0 00 00 01 1 Ballistic Ballistic ® ® ICP and charge mode ICP and charge mode C CH HA AR RG GE E M MO OD DE E Q QU UA AR RT TZ Z B BA AL LL LIIS ST TIIC C S SE EN NS SO OR RS S S Se er riie es s 1 11 18 8/ /1 11 19 9 Charge Mode Pressure Sensors are well suited for high-pressure ballistics, detonation, and explosive research and test applications. These sensors incorporate stable quartz-sensing elements, a durable- machined ceramic-coated integral diaphragm and floating clamp nut. They retrofit previous Model 118A (3/8-24 and M10) shoulder-seal designs for drilled cartridge and case mouth installations in small and IIm mp pr ro ov ve ed d! ! large-caliber weapons. The new design incorporates a more stable M Mo od de ells s 1 11 18 8B B1 11 1,, B B1 13 3 structure for improved accuracy, reliability, and lower thermal transient a an nd d 1 11 19 9A A1 11 1,, A A1 12 2 response. See specifications on page 31. Add prefix “M” to the sensor model number to specify M10 x 1.0 metric mounting (e.g., M109B11). M Mo od de ells s 1 11 18 8B B1 11 1 a an nd d 1 11 18 8B B1 13 3 sensors have been redesigned for improved stability, accuracy, reliability, and lower thermal transient response. Each sensor is factory stabilized by static and dynamic high- pressure cycling and actual test firing in a .223 caliber test barrel. They are available in ranges of 80 000 and 125 000 psi, respectively. M Mo od de ells s 1 11 19 9A A1 11 1 a an nd d 1 11 19 9A A1 12 2 are unique, acceleration-compensated, high resolution ballistic sensors designed for high-pressure, high-energy ballistics, detonation, and explosive applications under high-shock conditions, such as those that might be encountered in howitzer and liquid-propellant weapons. Two dynamic ranges of 80 000 and 27 27 125 000 psi are available. N Ne ew w! ! ® ® II C CP P B BA AL LL LIIS ST TIIC C S SE EN NS SO OR RS S M Mo od de ells s 1 10 08 8B B1 11 1 a an nd d 1 10 08 8B B1 13 3 S Se er riie es s 1 10 08 8/ /1 10 09 9 PCB offers a complete line of high pressure ballistic sensors with integral electronics. They operate from a PCB constant-current signal conditioner and provide a high-voltage, low-impedance output. ICP sensors are well suited for applications involving long cables and operation in dirty factory or field environments. These new sensors incorporate a captivated floating clamp nut and a more stable structure for improved accuracy, reliability, and lower thermal transient sensitivity. They are structured with quartz sensing elements, built-in microelectronics, and an integral machined ceramic-coated diaphragm for greater durability, overrange capability, higher-frequency response, and improved linearity. See specifications on page 32. Add prefix “M” to the sensor model number to specify M10 x 1.0 metric mounting (e.g., M109B11). N Ne ew w! ! M Mo od de ells s 1 10 08 8B B1 11 1 a an nd d 1 10 08 8B B1 13 3 are ICP integral electronic M Mo od de ells s 1 10 09 9B B1 11 1 a an nd d 1 10 09 9B B1 12 2 versions of the charge Models 118B11 and 118B13. They are suitable for routine ammunition, explosive, and reactive measurements. M Mo od de ells s 1 10 09 9B B1 11 1 a an nd d 1 10 09 9B B1 12 2 are acceleration-compensated ICP sensors for high-energy, high-frequency applications, such as detonation, closed bomb combustion, and explosive blast measurements under extreme shock conditions. P PR RE ES SS SU UR RE E A AN ND D F FO OR RC CE E S SE EN NS SO OR R D DIIV VIIS SIIO ON N T TO OL LL L F FR RE EE E: : 8 88 88 8-6 68 84 4-0 00 01 11 1 Conformal Ballistics Conformal Ballistics Charge mode Charge mode U.S. and Foreign Patents C CO ON NF FO OR RM MA AL L B BA AL LL LIIS ST TIIC C S SE EN NS SO OR RS S S Se er riie es s 1 11 17 7B B Conformal ballistic sensors measure true gun chamber pressure directly through the cartridge case. The diaphragm of the conformal sensor is contoured to match a specific chamber diameter. An alignment guide and spacers help the user to install the sensor flush with the gun chamber walls. The conformal ballistic sensor, when correctly installed, has a proven life expectancy of hundreds of thousands of rounds, outlasting many test barrels. Rapid-fire testing is possible since there are no cartridges to drill and align, no diaphragm ablatives to apply, and no gas passages to clean. The conformal sensor does not affect operation of the test barrel, nor change the measurement process. Proven long life • Allows rapid-fire testing Developed in cooperation with members of SAAMI to provide an Outlasts life of many barrels No drilled cases or recessed accurate rapid-fire electronic production test method to replace the passages SAAMI-approved test method mechanical “copper crusher,” the conformal sensor has experienced 20 Cost effective years of proven performance. Conformal calibration through an unfired, unmodified empty cartridge 40 shell case with PCB Series 090B Calibration Adaptor accounts for the 35 effects of the cartridge case. Output from the conformal sensor is 30 compatible with any charge amplifier. The PCB Model 400A20 Digital 25 Peak Holding System with simplified single-range charge amplifier and auto-reset peak meter facilitates rapid-fire testing of production 20 ammunition. See page 72 for more information on PCB Model 400A20 15 28 28 Digital Peak Holding System. 10 The two machined flats near the connector end, an alignment guide, 5 and a captive retaining nut facilitate installation. The nut automatically 0 extracts the sensor when it is unscrewed. Series 090B Calibration (µs) Adaptor permits static calibration of the Model 117B Sensor, with pressures to be applied to the empty cartridge case. Spacer set is Conformal vs. Standard Case Mouth Installation supplied to facilitate flush installation of the sensor. See specifications on page 29. Typical Conformal Calibration Adaptor System Typical Conformal Sensor Installation S SH HO OT TS SH HE EL LL L P PR RE ES SS SU UR RE E S SE EN NS SO OR R cartridge. The floating clamp nut design reduces torque sensitivity. The thermal sensitivity is minimized due to M Mo od de ell 1 16 67 7A A1 11 1 welded diaphragm design. For production testing of shotshell ammunition per SAAMI See specifications recommendations, this upgraded sensor measures on page 29. chamber pressure through the case wall of an unmodified 1 16 67 7A A1 11 1 S Sh ho otts sh he ellll S Se en ns so or r P PC CB B P PIIE EZ ZO OT TR RO ON NIIC CS S,, IIN NC C.. 7 71 16 6-6 68 84 4-0 00 00 01 1 PRESSURE (PSI x 1000) Conformal Ballistics Conformal Ballistics Charge mode Charge mode Dimensions shown in inches except where noted. Side View for 117’s Drawing A: Drawing B: Drawing C: Models 117B01 to B65 and 117B101 and Models 117B66 to 117B100 Model 167A11 Shot Shell Sensor up (>.350 dia. diaphragm curvature) (<.350 dia. diaphragm curvature) Notes: Series 117 Conformal Sensor diaphragms are machine-contoured to match specific gun chamber calibers. Each caliber has its own specific model number. Contact PCB. DO NOT machine mounting ports without a detailed Installation Drawing for the specific caliber location. Dynamic Range psi 60 000 (3) 35 000 (3) 15 000 Model 117B (4) Model 167A11 MODEL NUMBERS Riffle and Handgun Calibers Shotshell 29 29 Drawing A [.248 dia] Drawing B [.194 dia] Drawing C Sensitivity (2) - pC/psi 0.1 0.2 Resolution psi 0.04 0.02 Maximum Pressure psi 80 000 40 000 70 000 Linearity (1) %FS ≤ 2 ≤ 1 Resonant Frequency kHz ≥ 300 ≥ 250 Rise Time µs ≤ 2 Capacitance pF 5 12 Insulation Resistance at 70°F ohm ≥ 10 Shock (max) g pk 20 000 5000 20 000 Acceleration Sensitivity psi/g ≤ 0.02 ≤ 0.01 Temperature Range °F -100 to +400 -50 to +325 Temperature Coefficient %/°F ≤ 0.03 Flash Temperature °F 3000 Sensing Element material quartz Case/Diaphragm (integral) material 17-4 C-300/17-7 Connector type 10-32 coaxial Sealing (connector insulators) type epoxy Mounting Thread inch 3/8-24 5/16-24 3/8-24 Diaphragm Diameter inch 0.248 0.194 0.248 NOTES: 1. % FS of any calibration range; zero-based best straight line. 2. Unless otherwise designated, sensitivities are ±15%. 3. Calibration data supplied starting at 10 000 psi. 4. Contact PCB for model number to match specific caliber. P PR RE ES SS SU UR RE E A AN ND D F FO OR RC CE E S SE EN NS SO OR R D DIIV VIIS SIIO ON N T TO OL LL L F FR RE EE E: : 8 88 88 8-6 68 84 4-0 00 01 11 1 FREQ PHYSICAL ENVIRONMENTAL ELEC AMPLITUDE RESP Interchangeable Ballistic Quartz Sensors Interchangeable Ballistic Quartz Sensors Charge mode Charge mode Dimensions shown in inches except where noted. Model M165A01 Model 165A05 M165A03 End Seal Mount 30 30 Model 165A02 Model M165A03 M165A03 Flush Mount Dynamic Range (1) psi (MPa) 70 000 (483) 15 000 (103) 70 000 (483) MODEL NUMBERS M165A01 165A05 165A02 M165A03 Sensitivity (3) (4) -pC/psi (-pC/MPa) 0.135 (19.6) 0.2 (29) Resolution psi 0.01 0.02 Maximum Pressure psi (MPa) 80 000 (552) 70 000 (483) 80 000 (552) Linearity (2) % FS ≤ 2.0 ≤ 1.0 ≤ 2.0 Resonant Frequency kHz ≥ 250 Rise Time µs ≤ 2.0 Capacitance pF 5 12 Insulation Resistance at 70°F ohm ≥ 10 Acceleration Sensitivity psi/g ≤ 0.02 ≤ 0.01 Operating Temperature Range °F (°C) -100 to +400 (-73 to +204) -50 to +325 (-46 to +163) Temp Coefficient of Sensitivity %/°F (%/°C) ≤ 0.03 (0.054) 2 Maximum Shock g pk (m/s pk) 20 000 (196 200) Weight oz (grams) 0.4 (11) 0.52 (15) 0.7 (19) Mounting Thread size M10 x 1.0 3/8 - 24 M10 x 1.0 Connector type 10-32 Coaxial TNC Metric Mounting prefix n/a M n/a English Mounting model 165A01 n/a NOTES 1. Measures dynamic pressures from full vacuum to rated maximum. 3. Charge amplifier inverts the signal. 2. % FS of any calibration range; zero-based best straight line. 4. Unless otherwise designated, sensitivities are ±15%. P PC CB B P PIIE EZ ZO OT TR RO ON NIIC CS S,, IIN NC C.. 7 71 16 6-6 68 84 4-0 00 00 01 1 FREQ OPT PHYSICAL ENVIRONMENTAL ELEC AMPLITUDE RESP Ballistics Ballistics Charge mode Charge mode Dimensions shown in inches except where noted. Models 118B11 and 118B13 Models 119A11 and 119A12 General Purpose Ballistics Acceleration-Compensated Dynamic Range psi 20 to 80 000 20 to 120 000 20 to 80 000 20 to 120 000 MODEL NUMBERS 118B11 118B13 119A11 119A12 Sensitivy -pC/psi 0.1 (4) 0.25 (3) 31 31 Resolution psi 0.02 1 2 Maximum Pressure psi 100 000 125 000 100 000 125 000 Linearity (2) %FS ≤ 2 Resonant Frequency kHz ≥ 250 ≥ 400 (1) Rise Time µs ≤ 2 ≤ 1 Capacitance pF 5 20 12 Insulation Resistance at 70°F ohm ≥ 10 Shock (max) g pk 20 000 80 000 Acceleration Sensitivity psi/g 0.01 0.004 Temperature Range °F -400 to +400 Temperature Coefficient %/°F ≤ 0.03 Flash Temperature °F 4000 Sensing Element material quartz Case/Diaphragm (integral) material C-300 Connector type 10-32 coaxial Sealing (connector insulators) type epoxy 6.0E+4 Notes: 1. Suppressed resonance. 5.0E+4 2.% FS of any calibration range; zero-based straight line. 3. Unless otherwise designated, sensitivities are ±15%. 4.0E+4 4. Sensitivity is +25% / -15% 3.0E+4 ➔ Case Mouth Location 2.0E+4 Test Results .308 Caliber 1.0E+4 0.0 -1.0ms 0.0s 1.0ms 2.0ms TIME P PR RE ES SS SU UR RE E A AN ND D F FO OR RC CE E S SE EN NS SO OR R D DIIV VIIS SIIO ON N T TO OL LL L F FR RE EE E: : 8 88 88 8-6 68 84 4-0 00 01 11 1 Pressure (psi) FREQ PHYSICAL ENVIRONMENTAL ELEC AMPLITUDE RESP ® ® ICP Ballistics ICP Ballistics With integral electronics With integral electronics Dimensions shown in inches except where noted. Models 109B11 and 109B12 Models 108B11 and 108B13 High Shock Acceleration-Compensated General Purpose Ballistics Dynamic Range psi 20 to 80 000 20 to 100 000 20 to 80 000 20 to 100 000 MODEL NUMBERS 108B11 108B13 109B11 109B12 Sensitivity (4) mV/psi 0.07 Resolution psi 2 Maximum Pressure psi 125 000 Linearity (3) %FS ≤ 2 32 32 Resonant Frequency kHz ≥ 250 ≥ 400 (1) Rise Time µs ≤ 2 ≤ 1 Discharge Time Constant (2) sec ≥ 2000 Low Frequency (-5%) (2) Hz 0.0003 Shock (max) g pk 20 000 80 000 Acceleration Sensitivity psi/g ≤ 0.01 ≤ 0.004 Temperature Range °F -100 to +275 Temperature Coefficient %/°F ≤ 0.03 Flash Temperature °F 3000 Output Impedance ohm ≤ 100 Output Bias +volts 8 to 14 Power Required: Voltage +VDC 20 to 30 Constant Current mA 2 to 20 Sensing Element material quartz Case/Diaphragm (integral) material stainless steel Connector type 10-32 type Sealing (connector insulators) type epoxy Notes: 1. Suppressed resonance. 2. Discharge Time Constant (DTC) relates low-frequency to signal lost during transient events at room temperature. See technical section on page 78. 3. % FS of ant calibration range; zero-based best straight line. 4. Unless otherwise designated, sensitivities are ±15%. Typical Case Mouth and Drilled Cartridge Locations P PC CB B P PIIE EZ ZO OT TR RO ON NIIC CS S,, IIN NC C.. 7 71 16 6-6 68 84 4-0 00 00 01 1 PHYSICAL ELECTRICAL ENVIRONMENTAL FREQ RESP AMPLITUDE Engine Combustion Engine Combustion Pressure Sensors Pressure Sensors PCB manufactures a wide variety of engine combustion Combustion sensors for research applications requiring high precision and accuracy to general purpose peak Compression pressure and spark plug measurements. The new 145 Series engine combustion sensors have a Knock specially designed quartz sensing element to provide high sensitivity and low measurement error due to temperature transients. They are rugged, accurate and Thermodynamic analysis designed to fit into previously machined popular mounting ports. Peak pressures The 112 Series of engine combustion sensors are designed for routine combustion measurements at an economical price. Many models are offered, to provide a variety of measurement and installation options. PCB can modify standard spark plugs to accommodate 112 33 33 type sensors for routine combustion measurements, which eliminates the need to machine the cylinder head. Other models are available for “In-head” installations including 5/16-24 and 3/8-24 mounting threads. All models in this section feature an uncooled operating range of 600°F or higher. P R E S S U R E A N D F O R C E S E N S O R S D I V I S I O N P PC CB B 716-684-0001 P PF FS S T To ollll F Fr re ee e 888-684-0011 F Fa ax x 716-686-9129 E Em ma aiill pfssales@pcb.com W We eb b S Siitte e www.pcb.com Engine Combustion Engine Combustion Charge mode Charge mode Q QU UA AR RT TZ Z E EN NG GIIN NE E C CO OM MB BU US ST TIIO ON N S SE EN NS SO OR RS S S Se er riie es s 1 14 45 5 a an nd d 1 11 12 2B B1 10 0 Used for engine testing under laboratory and test-track conditions, these M Mo od de ell 1 14 45 5A A0 01 1 sensors feature an acceleration-compensated quartz element that provides clean, noise-free measurement data. Special crystals are used to accommodate operation up to 660°F. The 1 pC/psi output is compatible with standard commercial charge amplifiers. Try our new M Mo od de ell 1 14 45 5A A0 01 1 for engine research applications where precision measurements are required. This sensor is designed specifically to provide stability under the extreme thermodynamic conditions encountered during the combustion process. This high performance precision-engineered sensor utilizes an advanced design quartz sensing element for thermal stability and operation to 660°F. It M Mo od de ell 1 14 45 5A A0 05 5 fits conveniently into existing popular mounting port styles. Ground isolation is standard. M Mo od de ell 1 14 45 5A A0 05 5 is a high performance sensor for applications where high knock and harsher environments are present. Designed without the groove between the heat shield and quartz element to prevent clogging in applications where richer fuels produce carbon build-up between the heat shield and element. This version of the Series 145 also fits interchangeably with the Model 112B13 and other popular mounting port styles. 34 34 M Mo od de ell 1 11 12 2B B1 10 0 is designed to be used in conjunction with the Series M Mo od de ells s 1 11 12 2B B1 10 0 a an nd d 1 11 12 2B B1 11 1 65A Spark Plug Adaptor to monitor cylinder pressure in spark ignition engines, without engine modifications (see page 36). These sensors incorporate a special flame-resistant baffle for low-thermal transient sensitivity and minimum base-line distortion. They offer small size, low vibration noise pickup, high sensitivity and resonant frequency, all at an economical price. M Mo od de ell 1 11 12 2B B1 11 1 measures pressure in both gasoline and diesel engines. It has all the features of the 112B10 above, but can be mounted in the base of the head, which is especially useful for multivalve engines. A variety of spacer sleeves are supplied with this sensor allowing for installation at varying depths. M Mo od de ell 1 11 12 2B B1 13 3 M Mo od de ell 1 11 12 2B B1 13 3 retrofits existing ports with a more economical, general purpose combustion sensor. This model offers the performance, durability, and economy of the Model112B11, conveniently packaged in a 3/8-24 (145 series type) threaded housing. P PC CB B P PIIE EZ ZO OT TR RO ON NIIC CS S,, IIN NC C.. 7 71 16 6-6 68 84 4-0 00 00 01 1 Engine Combustion Engine Combustion Charge mode Charge mode Dimensions shown in inches except where noted. *Specifically designed for use with the 65A spark plug adaptor. See page 36. ** Model 112B11 can be mounted in walls of varying thickness from .620 to 1.700 using a series of supplied spacers. Contact PCB for installation drawing. Model 112B13 Model 112B11** Model 145A01 and145A05(6) Model 112B10* Dynamic Range (1) psi 3000 4000 MODEL NUMBERS 112B10 112B11 112B13 145A01 145A05 For Reaseach Applications Sensitivity (5) -pC/psi 1 0.9 Resolution (2) psi 0.01 Maximum Pressure psi 5000 10 000 5000 Linearity (3) %FS ≤ 2 ≤ 1 35 35 Resonant Frequency kHz ≥ 200 ≥ 60 ≥ 90 Rise Time µs ≤ 3 ≤ 8 ≤ 6 Shock (max) g pk 10 000 5000 Acceleration Sensitivity psi/g 0.002 0.05 Temperature Range °F -100 to +600 -65 to +660 Temperature Coefficient %/°F ≤ 0.03 Flash Temperature °F 4500 3000 Polarity (positive pressure) negative Capacitance pF 20 8 12 Insulation Resistance at 70°F ohms ≥ 10 Sensing Element material quartz Case material Invar (4) 17-4 Diaphragm material Invar (with flame baffle) (4) 17-4 Connector type 10-32 coaxial Sealing type welded/hermetic Ground Isolation prefix n/a standard Positive Polarity prefix P Removal Tool model n/a 039A05 NOTES: 1. For recess mount, Model 065A05 seal sleeve is available. 4. Invar minimizes thermal shock error for general purpose use. 2. Measures dynamic pressures from full vacuum to rated maximum. 5. Unless otherwise designated, sensitivities are ±15%. 3. % FS of any calibration range; zero-based best straight line. 6. The external configuration of the 145A05 is the same as the 145A01 (shown) except it does not have a groove between the heat shield and the quartz element. P PR RE ES SS SU UR RE E A AN ND D F FO OR RC CE E S SE EN NS SO OR R D DIIV VIIS SIIO ON N T TO OL LL L F FR RE EE E: : 8 88 88 8-6 68 84 4-0 00 01 11 1 FREQ OPTIONS ENVIRONMENTAL AMPLITUDE PHYSICAL ELECTRICAL RESP Engine Combustion Engine Combustion 1 14 40 0 K KN NO OC CK K S SE EN NS SO OR R-C CH HA AR RG GE E M MO OD DE E Series 140 Knock Detection Sensors offer a unique approach to M Mo od de ells s 1 14 40 0A A1 14 4 a an nd d analyzing engine combustion severity of knock. The sensor is designed 1 14 40 0A A1 18 8 K Kn no oc ck k S Se en ns so or r to fit securely in place of a spark plug washer or engine headbolt washer. In this position, it yields an output voltage that corresponds to cylinder combustion pressure. The stable quartz piezoelectric element, packaged in a welded, stainless steel housing, is mounted in a pre-loaded condition. In applications where the sensor is mounted in place of a spark plug washer, the pre- load on the quartz element is released, in proportion to the combustion pressure, as cylinder combustion occurs. The charge generated by releasing the pre-load can be converted to a voltage through the use of an in-line or lab style charge amplifier. The Knock detection sensors are available for 14mm and 18mm spark plug mount. ® ® IIC CP P H HE EA AD DB BO OL LT T S SE EN NS SO OR R PCB’s low impedance headbolt sensors are designed to mount in place of the large headbolt washer without any rework to the engine head. H He ea ad db bo olltt S Se en ns so or r These thin load washers are an economical way to help measure ((P Ph ho otto o iis s 2 2/ /3 3 a ac cttu ua all s siiz ze e)) compression and peak pressure as well as pressure rise. The integration of a quartz piezoelectric sensing element and a 36 36 customized housing to replace specific washer sizes, provides a rugged, reliable tool for engine diagnostic and control applications. S SP PA AR RK K P PL LU UG G A AD DA AP PT TO OR R S Se er riie es s 6 65 5A A A convenient and low-cost method of monitoring or measuring normal and abnormal combustion and compression pressures in an unmodified internal combustion engine. The spark plug adaptor S Se er riie es s 6 65 5A A S Sp pa ar rk k features: P Pllu ug g A Ad da ap ptto or r external hollow retaining nut accessible passage and port for cleaning ease easy installation and removal of sensor most standard spark plugs can be modified to accept a 112 style sensor acceleration-compensated sensor that reduces vibration sensitivity ® compressed air directed to sensor housing via the supplied Teflon sleeve to keep sensor within the specified operating range The spark plug adaptor coupled with a 112 type sensor is sensitive to pressure but insensitive to vibratory motion and strain. The results are exceptionally sharp, clean and free of spurious signals which often times mask or obscure the actual pressure signal. The passage diameter and diaphragm clearance are proportioned to impart near critical damping, which means nearly nonresonant acoustic behavior in the tube or probe. Almost any standard commercial or experimental spark plug can be modified to accommodate most standard quartz mini-probe style sensor. P PC CB B P PIIE EZ ZO OT TR RO ON NIIC CS S,, IIN NC C.. 7 71 16 6-6 68 84 4-0 00 00 01 1 High Temperature High Temperature and Cryogenic and Cryogenic Pressure Sensor Pressure Sensor PCB high-temperature quartz sensors measure dynamic High Temperature pressures in reactors, compressors, engines, turbines, heat exchangers, steam pipes, and combustion Gas turbines chambers. They excel in measuring low-pressure acoustic fluctuations at high static pressure levels. Exhaust manifolds Series 112 and 116 type sensors are specifically designed for operation at the highest temperature which Combustion quartz elements will functionally tolerate. They provide a high impedance charge output and connect to charge or Reactor heat exchangers voltage signal amplifiers through low noise cables. When driving long cables, use a short distance of low noise cable between the in-line charge or voltage converters for optimum performance. Cryogenic Although high-temperature sensors can be installed with 37 37 the floating clamp nut and seals supplied, PCB can Gas or fluid dynamics supply the sensors in threaded adaptors custom-made to fit your specific mounting ports. Flow instabilities Series 102A10 Cryogenic Sensors incorporate Pulsations acceleration-compensated quartz elements and special low-temperature microelectronics to measure dynamic pressures in cryogenic environments. They feature solid- Fluid-borne noise state construction, have flush-welded diaphragms, and withstand high shock and overload pressure. ® ICP cryogenic sensors use an internal high-pass filter to eliminate the static component of the signal, allowing measurement of low-pressure fluid-borne noise, oscillations, and surges under high static load conditions. These sensors were the first to successfully detect and measure uneven fuel flow in rocket engines that caused a “pogo” effect, a vibratory motion in multistage rockets caused by uneven fuel burning. P R E S S U R E A N D F O R C E S E N S O R S D I V I S I O N P PC CB B 716-684-0001 P PF FS S T To ollll F Fr re ee e 888-684-0011 F Fa ax x 716-686-9129 E Em ma aiill pfssales@pcb.com W We eb b S Siitte e www.pcb.com High Temperature - Cryogenic High Temperature - Cryogenic ® ® ICP and charge mode ICP and charge mode H HIIG GH H T TE EM MP PE ER RA AT TU UR RE E P PR RE ES SS SU UR RE E S SE EN NS SO OR RS S Designed for operation at the highest temperatures, these laser welded, hermetically sealed sensors are constructed with quartz sensing M Mo od de ells s 1 11 12 2A A0 04 4 a an nd d 1 11 12 2A A0 05 5 elements and fused ceramic insulation connectors. They contain an integral accelerometer to reduce vibration sensitivity. These features insure reliable operation in high temperature environments. The temperature coefficient is supplied with each sensor. Hard-line cables (PCB model numbers 008 and 028) are recommended for operating temperatures above 500°F. The cable can be welded to the sensor for operation in pressurized environments. M Mo od de ells s 1 11 12 2A A0 04 4 a an nd d 1 11 12 2A A0 05 5 high temperature sensors are suited for applications where small size and high frequency are important. They operate to 600°F, have a 1 pC/psi sensitivity and dynamic ranges of 100 and 5000 psi, respectively. The floating clamp nut design isolates against strain and facilitates installation and removal of the sensor. These sensors install either flush of slightly recessed directly in the test object or in a variety of threaded or cooled mounting adaptors. Typical applications include dynamic pressures in gas and steam turbines, heat exchangers and high-intensity acoustics from exhausts. See M Mo od de ells s 1 11 16 6B B a an nd d 1 11 16 6B B0 02 2 specifications on page 39. M Mo od de ells s 1 11 16 6B B a an nd d 1 11 16 6B B0 02 2 are structured with delta compression quartz 38 crystals and operate without cooling to 600°F on engines, compressors, 38 pumps, manifolds, pipes and steam or gas turbines. For use with charge or in-line amplifiers, these high sensitivity, hermetically-sealed sensors have welded joints and a fused ceramic insulated connector. Options include integral hard-line cables to 40 ft for demanding applications such as in nuclear power plants. Special mounting adaptors can be supplied to fit existing mounting holes. Calibration supplied is at room temperature with coefficients given at 600°F. Optional linear calibration can be furnished at any pressure level to 3000 psi, e. g. 6 pts to 3000 psi or ±50 psi at 1200 psi static. See specifications on page 39. ® ® C CR RY YO OG GE EN NIIC C IIC CP P S SE EN NS SO OR RS S S Se er riie es s 1 10 02 2A A1 10 0 These sensors are a special version of PCB’s high-resolution, low- impedance, quartz sensors designed for cryogenic environments. Model S Se er riie es s 1 10 02 2A A1 10 0 102A10 measures dynamic pressures from 0.01 to 100 psi at any static level from full vacuum to 2000 psi. They consistently follow transient events lasting a few percent of the discharge time constant. Since the special cryogenic microelectronics used in the Series 102A10 sensor are current-sensitive (sensitivity changes about 1% per mA), they should be used and calibrated w/4mA constant current. The four models in the series (102A10, 102A11, 102A13 and 102A14) offer a variety of ranges and sensitivities. A S Se er riie es s 1 10 02 2A A1 10 0 Sensor operates best in a thermally stabilized environment. If measurements are to be made under thermal shock (ambient or cryogenic) conditions, some type of ablative coating must be used on the sensor diaphragm to prevent or delay the thermal shock. See specifications on page 40. P PC CB B P PIIE EZ ZO OT TR RO ON NIIC CS S,, IIN NC C.. 7 71 16 6-6 68 84 4-0 00 00 01 1 High Temperature High Temperature Charge mode Charge mode Dimensions shown in inches except where noted. Mounting Adaptors on Page 58 (1) Models 112A04 and 112A05 Models 116B and 116B02 Dynamic Range (2) psi 100 5000 MODEL NUMBERS 116B02 (5) 112A04 112A05 Sensitivity (6) -pC/psi 7 1 Resolution (3) psi 0.0003 0.004 Range psi 100 5000 Maximum Pressure psi 3000 5000 10 000 Linearity (4) %FS ≤ 1 39 39 Resonant Frequency kHz ≥ 60 ≥ 250 Rise Time µs ≤ 5 ≤ 2 Shock (max) g pk 2000 10 000 Acceleration Sensitivity psi/g 0.002 Temperature Range °F -400 to +600 Temperature Coefficient %/°F ≤ 0.04 ≤ 0.03 Flash Temperature °F 3000 Polarity (positive pressure) negative Capacitance pF 30 18 11 Insulation Resistance at 70°F ohm ≥ 10 9 Insulation Resistance at 600°F ohm ≥ 10 Sensing Element material quartz Case material 316L 17-4 PH Diaphragm material stainless steel Connector type 10-32 coaxial Sealing type laser welded hermetic Optional Model model 116B (5) n/a NOTES: 1. Installs interchangeably with 0.218 diameter quartz mini gages. A 5/16-24 clamp nut is standard; M7 x .75 installation is available. 2. Measures dynamic pressures from full vacuum to rated maximum. 3. Resolution determined by system noise and cable length. 4. % FS of any calibration range; zero-based best straight line. 5. Model 116B has an extended temperature range to 650°F. 6. Unless otherwise designated, sensitivities are ±15%. P PR RE ES SS SU UR RE E A AN ND D F FO OR RC CE E S SE EN NS SO OR R D DIIV VIIS SIIO ON N T TO OL LL L F FR RE EE E: : 8 88 88 8-6 68 84 4-0 00 01 11 1 FREQ PHYSICAL ELECTRICAL ENVIRONMENTAL AMPLITUDE RESP ® ® ICP Cryogenic ICP Cryogenic With integral electronics With integral electronics Dimensions shown in inches except where noted. Models 102A10, A11, A13, A14 Dynamic Range (1) psi 0.02 to 100 0.2 to 1000 1 to 5000 2 to 10 000 MODEL NUMBERS 102A10 102A11 102A14 102A13 Sensitivity (5) (6) mV/psi 50 5 1 0.5 Resolution psi 0.002 0.02 0.1 0.2 Range (for 5V output) (2) psi 100 1000 5000 10 000 Range (for 10V output) (2) psi 200 2000 10 000 15 000 (7.5V) Maximum Pressure psi 2000 15 000 Linearity (3) %FS ≤ 1 ≤ 2 40 40 Resonant Frequency kHz ≥ 250 Rise Time µs ≤ 2 Discharge Time Constant (4) s ≥ 1 ≥ 2 ≥ 5 Low Frequency (-5%) (4) Hz 0.5 0.25 0.1 Shock (max) g pk 20 000 Acceleration Sensitivity psi/g 0.002 Temperature Range °F -423 to +212 Temperature Coefficient %/°F ≤ 0.06 Flash Temperature °F 3000 Polarity (positive pressure) positive Output Impedance ohm ≤ 500 Power Required: Voltage +VDC 11 to 30 Constant Current mA 2 to 20 Output Bias (2) +VDC 3 to 8 Sensing Element material quartz Case material stainless steel Diaphragm material stainless steel Connector type 10-32 coaxial Sealing type welded hermetic NOTES: 1. Measures dynamic pressures from full vacuum to rated maximum. 4. Discharge Time Constant (DTC) relates low-frequency to signal lost during transient 2. Negative dynamic output limited to -2.5 volts. events at room temperature. See technical section on page 78. 3. % FS of any calibration range; zero-based best straight line. 5. Calibrated using 4 mA constant current. 6. Unless otherwise designated, sensitivities are ±15%. P PC CB B P PIIE EZ ZO OT TR RO ON NIIC CS S,, IIN NC C.. 7 71 16 6-6 68 84 4-0 00 00 01 1 PHYSICAL ELECTRICAL ENVIRONMENTAL FREQ RESP AMPLITUDE Miniature Pressure Miniature Pressure Sensors Sensors This sub-miniature sensor series is recommended in Space-constrained locations applications with very restricted mounting space or where diaphragm diameter is critical. The sensor is Gas or fluid dynamics designed for compression, actuation, pulsation, cavitation, ultrasonic, hydraulic, fluidic, turbulence and other such thermally stable pressure measurements. Flow instabilities High-frequency response and low-impedance output, similar to standard-size sensors, is typical. Pulsations, spikes ® These quartz ICP pressure sensors are available in three mounting styles and various dynamic ranges from 100 psi to 30 000 psi. Care must be taken to follow the user manual mounting instructions closely. Series 105 sensors operate using the same signal- conditioning requirements standard for ICP sensors. Signal conditioners are available from PCB in single- 41 41 and multiple-channel versions with various options. P R E S S U R E A N D F O R C E S E N S O R S D I V I S I O N P PC CB B 716-684-0001 P PF FS S T To ollll F Fr re ee e 888-684-0011 F Fa ax x 716-686-9129 E Em ma aiill pfssales@pcb.com W We eb b S Siitte e www.pcb.com ® ® ICP Miniature ICP Miniature With integral electronics With integral electronics ® ® IIC CP P M MIIN NIIA AT TU UR RE E P PR RE ES SS SU UR RE E S SE EN NS SO OR RS S S Se er riie es s 1 10 05 5 The Series 105 Quartz Sensors measure slow and fast dynamic pressure from full vacuum to 30 000 psi M Mo od de ell 1 10 05 5A A (relative to the initial or average pressure level). The ((P Ph ho otto o iis s o on ne e a an nd d a a h ha allff ttiim me es s a ac cttu ua all s siiz ze e)) structure of this tiny instrument contains two quartz disks operating in a thickness-compression mode. An internal, microelectronic, unity-gain amplifier generates a high- level, low-impedance analog output signal. This signal is proportional to the pressure change when the sensor is connected, using a coaxial or two-wire cable, to a PCB signal conditioner. Three external configurations and a variety of sensitivities and ranges offer many mounting and application possibilities. Miniature sensors operate best in thermally stable environments. When used in any application involving flash or transient thermal inputs, a diaphragm ablative coating (RTV, silicone grease, etc) should be used. M Mo od de ells s 1 10 05 5B B0 02 2,, B B1 12 2 a an nd d B B2 22 2 P Ph ho otto o iis s o on ne e a an nd d a a h ha allff ttiim me e M Mo od de ell 1 10 05 5A A is designed for applications where a ac cttu ua all s siiz ze e)) mounting room is strictly limited. This sensor without 42 42 integral threads for minimum body size is mounted via a clamp nut on the shoulder of the back of the sensor for minimum mounting space requirements. A lightweight ribbon cable can be easily soldered directly to the sensor (signal to center pin and ground to a flat on the sensor body). It is recommended that a 070A09 or a 070B09 solder connector adaptor be used with the ribbon cable. See page 69 for details. M Mo od de ells s 1 10 05 5B B0 02 2,, B B1 12 2 a an nd d B B2 22 2 are the most popular design for applications where a 10-32 threaded mounting port is preferred. This mounting configuration M Mo od de ells s 1 10 05 5B B0 03 3,, B B1 13 3,, B B2 23 3,, B B3 33 3 a an nd d B B4 43 3 comes in a variety of ranges, including 100, 1000 and 5000 psi versions. M Mo od de ells s 1 10 05 5B B0 03 3,, B B1 13 3,, B B2 23 3,, B B3 33 3 a an nd d B B4 43 3 are available for applications where a 5/16-24 threaded clamp nut is preferred. This mounting configuration comes in a variety of pressure ranges, including 100, 1000, 5000, 10 000 and 30 000 psi versions. P PC CB B P PIIE EZ ZO OT TR RO ON NIIC CS S,, IIN NC C.. 7 71 16 6-6 68 84 4-0 00 00 01 1 ® ® ICP Miniature ICP Miniature With integral electronics With integral electronics Dimensions shown in inches except where noted. Model 105A Model 105B02, 105B12, and 105B22 Model 105B03, B13, B23, B33, B43 Dynamic Range (1) psi 100 1000 5000 10 000 30 000 MODEL NUMBERS 105A 105B02 105B03 105B12 105B13 105B22 105B23 105B33 105B43 Sensitivity (6) mV/psi 50 (+10/-20) 10 5 1 0.5 0.2 Resolution psi 0.005 0.01 0.02 0.1 0.2 0.5 Range psi 100 1000 5000 10 000 30 000 Maximum Pressure psi 250 500 2000 7500 15 000 40 000 Linearity (2) %FS ≤ 2 43 43 Resonant Frequency kHz ≥ 250 Rise Time µs ≤ 2 Discharge Time Constant (3) s ≥ 1 ≥ 10 ≥ 100 Low Frequency (-5%) (3) Hz 0.5 0.05 0.005 Shock (max) g pk 5000 Acceleration Sensitivity psi/g 0.005 Temperature Range °F -100 to +250 Temperature Coefficient %/°F ≤ 0.09 Flash Temperature °F 3000 Polarity (positive pressure) positive Output Impedance ohm < 100 Power Required: Voltage +VDC 20 to 30 Constant Current mA 2 to 20 Sensing Element material quartz Case material 17-4PH Diaphragm (4) material 17-4PH Connector (5) type solder pin 5-44 coax 10-32 coax 5-44 coax 10-32 coax 5-44 coax 10-32 coax Sealing (5) type welded epoxy Hermetic Seal (5) prefix n/a H n/a H n/a H Negative Polarity prefix N Water-resistant Cable prefix n/a W n/a W n/a W NOTES: 1. Measures dynamic pressures from full vacuum to rated maximum. 4. Diaphragms are integral. 2. % FS of any calibration range; zero-based best straight line. 5. Diaphragms of all sensors are hermetic and integral. Hermetic option specifies a fused- 3. Discharge Time Constant (DTC) relates low-frequency to signal lost during transient glass electrical connector and welded joints. events. See technical section on page 78. 6. Unless otherwise designated, sensitivities are ±15%. P PR RE ES SS SU UR RE E A AN ND D F FO OR RC CE E S SE EN NS SO OR R D DIIV VIIS SIIO ON N T TO OL LL L F FR RE EE E: : 8 88 88 8-6 68 84 4-0 00 01 11 1 OPTIONS PHYSICAL ELECTRICAL ENVIRONMENTAL FREQ RESP AMPLITUDE PCB’s Commitment To You: PCB’s Commitment To You: LASER WELDER: PCB utilizes both laser and electron beam welding techniques to hermetically seal sensors from outside contamination . . . helping to ensure reliability and longevity. 44 44 SKILLED TECHNICIANS: Under a microscope technicians meticulously assemble sensor elements and microelectronic circuitry. . . assuring sensor quality and performance. CNC DUAL SPINDLE LATHE: A machinist prepares a completely automatic lathe to perform both primary and secondary machining operations, increasing productivity of precision parts . . . to meet customer delivery schedules. Our machine shop produces over 70 000 precision PRODUCTION MACHINE SHOP: Precision Hardinge, machine parts each month. computer-controlled automatic lathes and multiple wire EDM machines produce close tolerance parts essential to dynamic sensing instrumentation. PCB's precision machine shop is fully equipped to perform all metal-working operations . . . allowing PCB to fully control the manufacturing process. P PC CB B P PIIE EZ ZO OT TR RO ON NIIC CS S,, IIN NC C.. 7 71 16 6-6 68 84 4-0 00 00 01 1 Rocket Rocket Motor Pressure Sensors Motor Pressure Sensors Series 120 Helium Bleed Sensors are designed for Combustion dynamics measuring dynamic pressures in intense heat flow associated with high-temperature rocket motor Instabilities environments. Outstanding features of this series include: ability to withstand intense heat at sensor tip Pulsations sensor enveloped in cool, helium gas reduced vibration sensitivity and integral acceleration compensation helium flow increases frequency response of the short connecting passage. “Helium Bleed” design, an idea originated at the Forrestal Lab of Princeton University during the 1960’s, involves enveloping the case and diaphragm of a miniature quartz sensor with a cool flow of helium gas. The gas cools the sensor and insulates the unit from hot 45 45 combustion gases, while cleaning and improving the response of the connecting passage. P R E S S U R E A N D F O R C E S E N S O R S D I V I S I O N P PC CB B 716-684-0001 P PF FS S T To ollll F Fr re ee e 888-684-0011 F Fa ax x 716-686-9129 E Em ma aiill pfssales@pcb.com W We eb b S Siitte e www.pcb.com Rocket Motor Rocket Motor R RO OC CK KE ET T M MO OT TO OR R S SE EN NS SO OR RS S S Se er riie es s 1 12 20 0 PCB’s quartz rocket motor sensors measure combustion instability in rocket engines. These sensors are structured with acceleration-compensated quartz sensing elements and are S Se er riie es s 1 12 22 2 ® available in both charge and ICP voltage mode output versions. Three physical configurations are available with helium bleed, helium bleed and water-cooling, and water-cooling only. Helium bleed serves to protect the quartz sensor from the intense heat. Helium being less dense than air also increases the frequency response of the recess gas passage. See specifications on pages 47 and 48. S Se er riie es s 1 12 22 2 helium-bleed sensor is well suited for short- duration combustion instability measurements in solid rocket S Se er riie es s 1 12 23 3 motors. This sensor features a 10-micron helium filter to control the helium flow rate to the sensor body and connecting passage. The element is acceleration compensated 46 and has a two-microsecond rise time, enabling it to capture 46 fast pressure fluctuations. Series 122 is available in both ICP and charge mode models. Special long designs have been supplied to accommodate mounting wall depth up to 18 inches. S Se er riie es s 1 12 23 3 rocket motor sensor is designed to measure combustion instability on some of the highest-energy rocket engines. The unit is suited for long duration measurements, or environments where severe temperature increase in the sensor mounting wall (or high soak temperature after shut down) S Se er riie es s1 12 24 4 exists. The unit incorporates helium-bleed, water cooling and two piece construction. Available in ICP and charge designs, a ceramic-coated end piece protects the sensor from the intense flow and environment. S Se er riie es s 1 12 24 4 ICP and charge mode watercooled sensors are designed for operation in high-heat transfer, high-vibration environments. They incorporate durable water cooling tubes with AN fittings and a special ceramic-coated end piece. P PR RE ES SS SU UR RE E A AN ND D F FO OR RC CE E S SE EN NS SO OR R D DIIV VIIS SIIO ON N T TO OL LL L F FR RE EE E: : 8 88 88 8-6 68 84 4-0 00 01 11 1 ® ® ICP Rocket Motor ICP Rocket Motor With integral electronics With integral electronics Dimensions shown in inches except where noted. Series 122A20 Series 123A20 Series 124A20 Helium Bleed Water Cooled & Helium Bleed Water Cooled Dynamic Range (1) psi 250 1 000 3 000 5 000 122A21 122A24 122A22 124A22 MODEL NUMBERS 123A21 123A24 123A22 124A21 124A24 Sensitivity (6) mV/psi 20 5 1 47 47 Resolution psi 0.005 0.02 0.1 Range psi 250 (5V) 1 000 (5V) 3 000 (3V) 5 000 (5V) Maximum Pressure psi 5 000 7 000 Linearity (2) %FS ≤ 1 Resonant Frequency kHz ≥ 25 (for 122 and 123), ≥ 15 (for 124) Rise Time µs ≤ 20 (for 122 and 123), ≤ 30 (for 124) Discharge Time Constant (3) s ≥ 1 ≥ 100 ≥ 500 Low Frequency (-5%) (3) Hz 0.5 0.005 0.001 Shock (max) g pk 10 000 Acceleration Sensitivity psi/g 0.002 Temperature Range (4) °F -100 to +250 Temperature Coefficient %/°F ≤ 0.03 Flash Temperature (5) °F 4 000 (for 122), 10 000 (for 123), 5 000 (for 124) Polarity (positive pressure) positive Output Impedance ohm < 100 Power Required : Voltage +VDC 20 to 30 Constant Current mA 2 to 20 Sensing Element material quartz Case material 17-4PH Diaphragm material Invar Connector type 10-32 coaxial Sealing type epoxy (for 122 and 123), welded (for 124) Supplied Accessories 4 ft Cable Model 005AA004AA Model 031A Filter for Models 122A 123A NOTES: 1. Measures dynamic pressures from full vacuum to rated maximum. 4. Temperature range refers to operating range of sensing element without extra cooling 2. % FS of any calibration range; zero-based best straight line. and helium flow. Environment temperature range may be higher, depending on 3. Discharge Time Constant (DTC) relates low-frequency to signal lost during transient application conditions, water cooling, or helium flow. events at room temperature. See technical section on page 78. 5. Flash temperature is defined as having a duration <10 milliseconds. 6. Unless otherwise designated, sensitivities are ±15%. P PR RE ES SS SU UR RE E A AN ND D F FO OR RC CE E S SE EN NS SO OR R D DIIV VIIS SIIO ON N T TO OL LL L F FR RE EE E: : 8 88 88 8-6 68 84 4-0 00 01 11 1 ELECTRICAL ENVIRONMENTAL FREQ RESP AMPLITUDE PHYSICAL Rocket Motor Rocket Motor Charge mode Charge mode Dimensions shown in inches except where noted. Model 122A Model 123A Model 124A Helium Bleed Water Cooled & Helium Bleed Water Cooled Dynamic Range (1) psi 3000 MODEL NUMBERS 122A 123A 124A Sensitivity (6) pC/psi 1 Resolution (2) psi 0.02 0.01 48 48 Maximum Pressure psi 5000 Linearity (3) %FS ≤ 1 Resonant Frequency kHz ≥ 25 ≥ 15 Rise Time µs ≤ 20 ≤ 30 Shock (max) g pk 10 000 Acceleration Sensitivity psi/g 0.002 Temperature Range (4) °F -450 to +500 Temperature Coefficient %/°F ≤ 0.01 Flash Temperature (5) °F 4 000 10 000 5 000 Polarity (positive pressure) negative Capacitance pF 18 12 Insulation Resistance at 70°F ohm ≥ 10 Sensing Element material quartz Case material 17-4 Diaphragm material Invar Connector type 10-32 coaxial Sealing type epoxy Optional with Positive Polarity prefix P Supplied Accessories Model 031A filter n/a 4 ft Model 006AA004AA BNC Accessories NOTES: 1. Measures dynamic pressures from full vacuum to rated maximum. 5. Flash temperature is defined as having a duration >10 milliseconds. 2. Resolution determined by system noise and cable length. 6. Unless otherwise designated, sensitivities are ±15%. 3. % FS of any calibration range; zero-based best straight line. 4. Temperature range refers to operating range of sensing element without extra cooling and helium flow. Environment temperature range may be higher, depending on application conditions, water cooling, or helium flow. P PC CB B P PIIE EZ ZO OT TR RO ON NIIC CS S,, IIN NC C.. 7 71 16 6-6 68 84 4-0 00 00 01 1 FREQ ELECTRICAL PHYSICAL ENVIRONMENTAL AMPLITUDE RESP Pressure Calibrators Pressure Calibrators and and Services Services P PR RE ES SS SU UR RE E C CA AL LIIB BR RA AT TO OR RS S & & S SE ER RV VIIC CE E Each PCB pressure sensor is provided with an individual calibration certificate traceable to the N.I.S.T. (National Institute of Standards & Technology). All instrumentation and reference standards used in the calibration process are traceable to NIST. Both static and dynamic methods are used in the calibration process. Special hydraulic and pneumatic impulse and step pressure generators, developed for in-house calibration of PCB sensors, are offered as standard commercial products. PCB also offers NIST traceable calibration services for other commercial piezoelectric sensors from acoustic levels to greater than 100 000 psi. Calibration services include shock tube amplitude/frequency response testing with microsecond step function pressures. Our new high pressure impulse calibrator, Model 913A10, allows for dynamic versus static response comparison of pressures to 100 000 psi. 49 49 Calibration data supplied by various sensor manufacturers may differ considerably. Some manufacturers may provide sensor sensitivity only at specific data points which makes non-linearity less obvious. PCB provides linearity graphs with sensitivity at specific data points. It is a recommended practice to request a copy of the calibration certificate before you purchase so you will be aware of the data being supplied. See page 56 for a copy of a typical calibration certificate. Call, fax, or email a PCB application engineer if Test engineer calibrates sensor using 913B02 Hydraulic Impulse Calibrator with tourmaline reference standard. you have any questions or need more information relating to pressure sensor calibration. C Ca alliib br ra atto or r S Se elle ec cttiio on n C Ch ha ar rtt: : PCB CALIBRATOR SELECTION CHART Calibrator Model # Type Rise Time Pressure Range Page # (psi) Shock Tube 901A10 Dynamic-step 1 ns 7 to 1400 50 Low Pressure Pulse Calibrator 903B02 Dynamic-step 5 ms 0 to 150 51 High Pressure Static Calibrator 905C Static n/a 10 000 to 100 000 52 Aronson Step Pressure Generator 907 Series Dynamic 30-50 µs 0 to 1000 53 High Pressure Impulse Calibrator 913A10 Dynamic 3.5 ms 10 000 to 125 000 54 Hydraulic Impulse Calibrator 913B02 Dynamic 3 ms 200 to 20 000 55 P R E S S U R E A N D F O R C E S E N S O R S D I V I S I O N P PC CB B 716-684-0001 P PF FS S T To ollll F Fr re ee e 888-684-0011 F Fa ax x 716-686-9129 E Em ma aiill pfssales@pcb.com W We eb b S Siitte e www.pcb.com Shock Tube - Model 901A10 Shock Tube - Model 901A10 7-1400 PSI 7-1400 PSI For shock and blast wave sensor testing and calibration S SH HO OC CK K T TU UB BE E M Mo od de ell 9 90 01 1A A1 10 0 is a gas-driven shock tube designed for the testing and calibration of high frequency pressure sensors, such as piezoelectric shock/blast wave sensors. The unit features: nanosecond rise time generates step pressures to 1400 psi 7 feet long x 2 inch I.D. gas driven: helium, air, nitrogen Preselected aluminum diaphragms are inserted in the flanges between the driver section and the expansion chamber. Compressed gas pressurizes the driver section, bursting the diaphragm, and sending a well-formed shock SUPPLIED ACCESSORIES Wooden Stand (3 pieces) wave to the test sensor mounted in the reflection end plate. 134A Tourmaline Reference Sensor Brass Valve Series 132A Incident Anti-Rotation Plate By knowing the atmospheric pressure, temperature, and Pressure Sensor Compression Plate relative humidity, and by measuring the shock wave velocity Power Supply for ICP Sensors Reflection Plate Diaphragms - (24) Aluminum Misc: Bolts, Nuts, Gaskets, O-Rings via the supplied incident sensor, the precise shock wave - (12) Mylar amplitude is calculated. Approximate Shock Pressures as a Function of Diaphragm Material and Burst Pressure 50 Shock Reflected Diaphragm Driver Diaphragm Burst 50 Over Pressure Over Pressure Material Gas* Pressure 699.0 mV psi psi Thickness (inch) psig Velocity Data from PCB 2" ID Shock Tube 599.0 mV 1100-0 Aluminum 499.0 mV 180 1050 0.064 Helium 1400 399.0 mV 144 790 0.04 Helium 880 130 690 0.032 Helium 760 299.0 mV 90 435 0.02 Helium 423 199.0 mV Mylar 99.00 mV 32 110 0.01 Nitrogen 225 -1.000 mV 3 6.6 0.0005 Air 7 -101.- mV -524.2 uS 269.4 uS 1.063 mS 1.856 mS 2.650 mS * Customer supplied; Bottled gas recommended (≈ 2 500 psi). Velocity Record from a PCB Shock Tube Diaphragms P PC CB B P PIIE EZ ZO OT TR RO ON NIIC CS S,, IIN NC C.. 7 71 16 6-6 68 84 4-0 00 00 01 1 Low Pressure Pulse Calibrator - Model 903B02 Low Pressure Pulse Calibrator - Model 903B02 0-150 PSI 0-150 PSI D DY YN NA AM MIIC C P PR RE ES SS SU UR RE E,, S ST TE EP P F FU UN NC CT TIIO ON N P PU UL LS SE E C CA AL LIIB BR RA AT TO OR R W WIIT TH H Q QU UIIC CK K-O OP PE EN NIIN NG G V VA AL LV VE E M Mo od de ell 9 90 03 3B B0 02 2 is an aperiodic dynamic pressure source that applies known step changes to pressure sensors within the range of 0 to 150 psi. It determines sensitivity and transient response characteristics. This unit generates known step-function increase or decrease in pressure for the dynamic calibration of miniature pressure sensors, according to American National Standard ANSI B88.1. This unit features the following characteristics: Measures step pressures to 150 psi Offers 5 millisecond rise time Exhibits little or no gas resonance Provides NIST-traceable calibration Operates from shop air supply Accomodates two sensors Model 903B02 Calibration Pressure Range psi 0 to 150 A manually operated, quick-opening, 3-way valve Pressure Step Rise Time (nominal) m s 5 switches the manifold (sensor) pressure from atmospheric to a precisely known (reservoir) pressure in about 5 Reference Gage Range* psi FS 0 to 150 milliseconds. The reservoir tank air pressure, displayed on Reference Gage Accuracy % FS 0.2 a precision digital reference gauge, is controlled by inlet 51 51 Size (l x w x h) inch 22 x 24 x 24 and bleed valves. The sensor output signal is recorded Weight lb 50 and measured on an oscilloscope, as illustrated. Reservoir Maximum Pressure psi 200 Pressure sensors install directly in 3/8-24 threaded ports Manifold Sensor Ports (qty) size (2) 3/8-24 thd. in the manifold or in appropriate mounting adaptors. A * Digital Precision Reference Gage second port in the manifold (normally plugged) ** Accessories supplied: Model 061A21Thread Adaptor (2), Blank Thread Adaptor (4), Seal (4) accommodates an optional reference pressure sensor for comparison calibration. 672.0 mV 572.0 mV 472.0 mV 372.0 mV 272.0 mV 172.0 mV 72.00 mV -28.00 mV -128.0 mV -540.0 uS 9.380 mS 19.30 mS 29.22 mS 39.14 mS TIME P PR RE ES SS SU UR RE E A AN ND D F FO OR RC CE E S SE EN NS SO OR R D DIIV VIIS SIIO ON N T TO OL LL L F FR RE EE E: : 8 88 88 8-6 68 84 4-0 00 01 11 1 PRESSURE High Pressure Static Calibrator - Model 905C High Pressure Static Calibrator - Model 905C 10 000-100 000 PSI 10 000-100 000 PSI H HIIG GH H P PR RE ES SS SU UR RE E C CA AL LIIB BR RA AT TIIO ON N S SY YS ST TE EM M M Mo od de ell 9 90 05 5C C statically calibrates high-pressure piezolectric sensors to 100 000 psi. It consists of a hand- operated hydraulic pressure pump, precision reference ® standard and auxiliary gages, an ICP sensor signal conditioner, and a digital voltmeter. This system features: static pressure range to 100 000 psi self-contained hydraulic system precision digital readout reference gage calibration traceable to NIST through reference gage excitation for low-impedance sensors point-by-point static calibration of high- pressure sensors The manually operated pump quickly generates a static pressure that is applied to the sensor being calibrated and is measured by the precision reference standard and auxiliary gages. The output signal from the ICP sensor being calibrated and the signal conditioner (or charge mode sensor and associated charge amplifier) are displayed and measured on the digital voltmeter. The Model 905C 52 52 digital voltmeter features a (BNC) scope output and a Reference Standard Gage Range psi 10 000 to 100 000* GPIB (General Purpose Interface Bus) output. Measurement Step Increments psi 5000 The sensor being calibrated is installed into a mounting Reference Standard Gage Accuracy % FS ≤ 0.10 adaptor that threads into the manifold. A furnished Auxiliary Gage Range psi 0-150 000 adaptor accommodates PCB Series 108, 109, 117, 118, Maximum Pump Pressure psi 150 000 119, and some 165 ballistic sensors. Special plugs or Power (60 Hz) volt 110 (optional 220) adaptors can be supplied for other sensors. Approximate Shipping Weight lb 200 To increase longevity, the precision reference standard *For calibration below 10 000 psi, an optional model 100M32 calibration gage may be shut off with a valve while the auxiliary adaptor is available. gage is used as a reference for pressure cycling. Supplied Accessories: Model 061A19 Adaptor (for PCB Series 108, 109, 117, 118, 119, and 167) Model 061M47 Blank Thread Adaptor Model 012A05 Coaxial Cable ® Monoplex -DOS (1 gallon) P PC CB B P PIIE EZ ZO OT TR RO ON NIIC CS S,, IIN NC C.. 7 71 16 6-6 68 84 4-0 00 00 01 1 Aronson Step Pressure Generator - Model 907A02 Aronson Step Pressure Generator - Model 907A02 0-1 000 PSI 0-1 000 PSI Developed by P. Aronson for U.S. Naval Ordinance Laboratory D DY YN NA AM MIIC C S ST TE EP P P PR RE ES SS SU UR RE E G GE EN NE ER RA AT TO OR R M Mo od de ell 9 90 07 7A A0 02 2 Pressure Step Generator is a simplified precision-calibration device which produces positive going step pressures to 1000 psi, with rise times 30 to 50 microseconds. It may also be used to compare static vs. dynamic calibration, to determine sensor and system discharge time constants and rise times of some lower frequency-type pressure sensors. M Mo od de ell 9 90 07 7A A is available to calibrate small pressure changes at higher static levels. It features additional valves and plumbing to allow control of the initial pressure against the sensor diaphragm, under the poppet valve, including a vacuum. Model 907A incorporates six 22-turn fine-adjusting metering valves for precise pressure control. External gas supplies are required to operate Models 907A02 or 907A. An accurate external pressure reference gage is required to measure the initial and final reservoir static pressures. A second external reference gage is required for Model 907A. Model 907A07 is a version of Model 907A02 supplied complete with the external reference gage and plumbing ready to connect to the user’s pressure source. Model 907A05 is a version of Model 907A supplied with two 53 53 external pressure reference gages and plumbing. 2 Channel Reference Gage Supplied with Model 907A05 Model 907A02 Pressure Step Amplitude psi 0 to 1000 (1) Step Rise Time µs ≤ 50 Maximum Reservoir Pressure psi ≤ 2000 Working Medium Non-corrosive gas (i.e. helium) Maximum Sensor Size inch dia. 1 Operating Mode Manual Calibration Modes Dynamic and static (in place) Locking Mechanism Keeps poppet valve open or closed Trigger Signal Generator Impacts sensor to trigger recording device SUPPLIED ACCESSORIES Three poppet valves Material Stainless steel and aluminum one blank for sensors to 1 inch dia. Gas Pressure Controls (3) each type 316L manual valves one for sensors under 0.5 inch dia. one for sensors under 0.25 inch dia. ® Gas Access Ports 2 Swagelok -type AN connectors; 1 for gas pressure/vacuum Three sensor mounting adaptors sources; 1 for external static reference gages one with 3/8-24 thread one for PCB standard 5/16-24 thd. Size dia. x h 12 x 21 inch one blank plug to accommodate up Weight lb 75 to 1-inch diameter sensors. NOTES: 1. Negative Pressure ≤ 14 psi. P PR RE ES SS SU UR RE E A AN ND D F FO OR RC CE E S SE EN NS SO OR R D DIIV VIIS SIIO ON N T TO OL LL L F FR RE EE E: : 8 88 88 8-6 68 84 4-0 00 01 11 1 High Pressure Impulse Calibrators - Model 913A10 High Pressure Impulse Calibrators - Model 913A10 10 000-125 000 PSI 10 000-125 000 PSI H HIIG GH H P PR RE ES SS SU UR RE E D DY YN NA AM MIIC C IIM MP PU UL LS SE E C CA AL LIIB BR RA AT TO OR R M Mo od de ell 9 91 13 3A A1 10 0 is a reliable, easy-to-use, pneumatically-operated high pressure dynamic calibrator. The Model 913A10 utilizes a rugged, ® stable, and repeatable PCB quartz shear ICP accelerometer to accurately determine pressure. This unit features a 42-inch high drop-test fixture with a 53- pound tungsten mass. The mass is lifted and released by a pneumatically controlled carriage and piston. The pneumatic control panel features two safety palm buttons for releasing the drop weight. A free-falling known mass is dropped onto a piston, creating a hydraulic pressure pulse in the pressure calibration cell. The accelerometer measures the deceleration of the free-falling mass after it strikes the piston. The deceleration of the mass/piston, coupled with the geometries of the piston and cylinder, determine the pressure. This method eliminates the need for complicated drop-mass velocity measurements or uncertainties from referencing another pressure sensor. 54 54 The supplied pressure calibration cell, consisting of a precision-machined piston/manifold, is ported for two PCB Series 118/119 Ballistic Pressure Sensors. Various models of high-pressure sensors may be calibrated by interchanging the available drop-in pressure calibration cells. Model 913A10 SYSTEM PERFORMANCE DESCRIPTION Range (maximum) psi 125 000 Rise Time ms 3.5 Pulse Duration ms 7 Estimated Accuracy % + 0.3 PHYSICAL DESCRIPTION -10ms 0.0ms 10.0ms Drop Mass Material Tungsten Sample Pressure Pulse Generated by Model 913A10 Drop Weight lb 53 Calibrator ² 8 ms rise time. Required Air Pressure psi 70 to 110 SUPPLIED COMPONENTS to lift mass OPTIONAL ACCESSORIES Pressure Calibration Cell Steel Drop Mass-22 lb Drop Test Fixture Reference (ICP) Shear Accelerometer (with (Shortens pulse duration to 5 msec.) NIST-traceable calibration certificate) (Max. Pressure 85 000 psi) Size (h x dia) inch 42 x 12 Accelerometer Cable (2) Eye Hook/Rope (for changing mass) Weight lb 220 Accelerometer Signal Conditioner Pressure Calibration Cells with Optional Space Pistons with Caps (4) Mounting Ports Pneumatics Control Enclosure Space Air Filter Glycerine (1 pint) Size (h x w x d) inch 42 x 25 x 9 Rubber Floor Pad Weight lb 45 Spare 5/32-inch OD Nylon Tubing-10 ft Spare 1/4-inch OD Polyethylene Tubing-10 ft Instruction Manual P PC CB B P PIIE EZ ZO OT TR RO ON NIIC CS S,, IIN NC C.. 7 71 16 6-6 68 84 4-0 00 00 01 1 Hydraulic Impulse Calibrator - Model 913B02 Hydraulic Impulse Calibrator - Model 913B02 200-20 000 PSI 200-20 000 PSI H HY YD DR RA AU UL LIIC C IIM MP PU UL LS SE E C CA AL LIIB BR RA AT TO OR R PCB Model 913B02 M Mo od de ell 9 91 13 3B B0 02 2 is a hydraulic impulse calibrator utilizing a mass dropped onto a piston in a fluid filled cylinder for comparison calibration of dynamic pressure sensors against a PCB Model 136A tourmaline transfer standard. The pressure cylinder is fitted with the tourmaline reference standard and an installation port for the sensor to be calibrated. Typical performance specifications are 2-3 millisecond rise time with a pulse duration of about 5-6 milliseconds. 1.0E+5 7.5E+4 5.0E+4 2.5E+4 0.0 0.0S 5.0mS 10.0mS TIME 55 55 Typical Pressure Pulse Generated by Model 913B02 SUPPLIED COMPONENTS T TR RA AN NS SF FE ER R S ST TA AN ND DA AR RD D Calibration Stand Drop Tube and Mass M Mo od de ell 1 13 36 6A A is a linear volumetric tourmaline pressure Model 136A Reference Transfer Sensor Model 462A37 Charge Amplifier sensor designed to accurately measure rapidly changing 3 FS0 Calibrations (0 to 1 000, 10 000, and 20 000 psi) traceable to NIST hydraulic pressures to 20 000 psi. It is used as the NOTE: Because of seal design considerations, Model 136A should not be reference transfer standard in the PCB 913B02 Hydraulic statically pressurized above 5 000 psi. Impulse Calibrator. The Model 136A is structured with a single tourmaline crystal, suspended between two steel posts. Since there is Model 136A Tourmaline Transfer Standard no diaphragm or housing to affect the inherent linearity of Dynamic Range, full scale* psi 20 000 the tourmaline crystal, this sensor makes an excellent Maximum Dynamic Pressure psi 20 000 calibration transfer standard for use in hydraulic impulse- Resolution psi 0.5 type calibrators. The crystal is epoxy- Sensitivity pC/psi 0.2 sealed and is recommended for use Resonant Frequency MHz ≥ 1 only in electrically non- Rise Time µs ≤ 1 conductive oil Linearity (all ranges) % ≤ 0.5 environments. Capacitance (nominal) pF 10 12 Insulation Resistance ohm ≥ 10 Model 136A Polarity negative Temperature Range °F 0 to 100 Sealing epoxy Case material stainless steel Sensing Element material tourmaline Size (hex x lg) inch 0.56 x 1.7 Mounting Connector (micro) thread 1/2 - 20 NF Connector (micro) (signal) coaxial 10-32 P PR RE ES SS SU UR RE E A AN ND D F FO OR RC CE E S SE EN NS SO OR R D DIIV VIIS SIIO ON N T TO OL LL L F FR RE EE E: : 8 88 88 8-6 68 84 4-0 00 01 11 1 High Pressure Generator #2 Typical Calibration Certificate Typical Calibration Certificate A single quartz pressure sensor has a very wide linear Illustrated below are two typical NIST traceable dynamic operating range. Several strain or piezoresistive calibration certificates furnished with model 113A24 type sensors with narrow measuring ranges would be pressure sensor (1000 psi range). The two linear required to make the range of measurements that can be calibrations provided with this sensor are 0 to 1000 psi, made by one piezoelectric sensor. full scale and 0 to 100 psi, 10% of full scale. Because of its exceptional linearity and high (5 mV/psi) output, the To make use of their exceptional linear dynamic range, same sensor can be used for measurements 0 to 5 psi, 0 most PCB pressure sensors are furnished with two to 1000 psi, or anywhere in between. There is no need calibrations. The first calibration is performed over the to buy a new sensor each time it is desired to measure a entire operating range of the sensor, while the second different range. calibration is performed over the first 10% of the operating range. 56 56 Sample Calibration Certificate Sample Calibration Certificate 0 to 1000 PSI 0 to 100 PSI Full Scale 10% Full Scale P PC CB B P PIIE EZ ZO OT TR RO ON NIIC CS S,, IIN NC C.. 7 71 16 6-6 68 84 4-0 00 00 01 1 Related Products Related Products Mounting adaptors Standard cables Custom cable ordering guide Cable description Connectors Signal conditioners 57 57 Typical 4 Channel Model 442A04 ® Line Powered ICP Sensor Power/Signal Conditioner with gain x1, x10, x100. marked P R E S S U R E A N D F O R C E S E N S O R S D I V I S I O N P PC CB B 716-684-0001 P PF FS S T To ollll F Fr re ee e 888-684-0011 F Fa ax x 716-686-9129 E Em ma aiill pfssales@pcb.com W We eb b S Siitte e www.pcb.com Mounting Adaptors Mounting Adaptors Watercooled adaptors provide for sensor installation in W Wh ha att a ar re e m mo ou un nttiin ng g a ad da ap ptto or rs s? ? high temperature applications for dynamic measurements Most quartz pressure probes are designed for precision on exhaust manifolds and jet engines. installation in restricted locations. When minimum ® Watercooled adaptors allow ICP and charge mode dimensions are not required, thread adaptors provide pressure sensors to operate well above their maximum convenient sensor mounting. It is less complicated to drill rated temperature range. For example, an ICP sensor, and tap a 3/8-24 hole for a thread adaptor than it is to rated to 250°F maximum temperature, will not generally machine a precision sensor mounting port. Standard and reach 150°F when operating in a Model 64 watercooled special adaptors can be supplied to fit specific mounting adaptor on a 1200°F engine exhaust manifold. ports. Most mounting adaptors are made of high-strength 17-4 W Wh hy y u us se e m mo ou un nttiin ng g a ad da ap ptto or rs s? ? PH stainless steel. Care should be exercised to observe maximum pressured thermal environment, when using When space permits, mounting adaptors offer several adaptors made of lesser-strength materials. For example, advantages. First, the use of an adaptor reduces the need Delrin, a type of plastic used to provide sensor ground for precision machining in “sensor only” installations. In isolation, should not be used above 500 psi. Low-carbon, locations where necessary machining steps are 316L stainless is often used for brine and other corrosive impossible, impractical, or simply inconvenient, the environments, LOX (liquid oxygen), and GOX (gaseous adaptor can be mounted with a few simple steps. oxygen) environments. The sensor can be electrically insulated in some adaptors In sensor applications involving exposure to flash to minimize interference from ground loop noise involved temperatures, an ablative protective diaphragm coating is with operation on electrical machinery. Special adaptor beneficial. To captivate the ablative, the sensor may be materials, sensor coatings and insulating seals can be slightly recessed in an adaptor approximately 0.01 inches factory installed to isolate the sensor from ground induced 58 58 with the recess filled with an ablative. noise. S Se er riie es s 0 06 61 1 A Ad da ap ptto or rs s have straight English or metric C Co on nn ne ec ctto or r E Ex xtte en nd de er r ffo or r S Se er riie es s 1 11 11 1,, 1 11 12 2,, a an nd d 1 11 13 3 threads, of specific length, and a shoulder seal. Thicker Model 074A “X” Connector Extender walls can be counterbored for flush installations. Sensors (Specify dimension “X”. Example 074A1.75 is an may be installed flush with end of adaptor or slightly extender whose “X” dimension=1.75 inches)* recessed to contain an ablative coating. S Se er riie es s 0 06 62 2 P Piip pe e T Th hr re ea ad d A Ad da ap ptto or rs s provide for convenient sensor installation in pumps and hydraulic systems. Since pipe thread adaptors seal on the threads, it is difficult to achieve a flush mount. For both safety and measurement reasons, “ganging” pipe thread adaptors to adapt up or down is not recommended, especially at high pressures. S Se er riie es s 0 06 64 4 W Wa atte er r-C Co oo olle ed d A Ad da ap ptto or rs s facilitate sensor installation of sensor in high-temperature applications, such as turbines, jet, internal combustion and engine exhaust. For example, normal water line pressure to WC adaptor keeps an ICP sensor mounted on a 1000°F exhaust manifold well below its 250°F maximum rated temperature. Water cooling should be maintained during the engine shutdown phase to avoid over-heating from heat soak. *Dimension “X” = Mounting wall thickness minus C CA AU UT TIIO ON N: : Observe maximum pressure limits for 0.28 (flush mtg). Available “X” dims: 0.75 to 4.50 adaptors; these limits may be less than the sensors inches in 0.05 inch increments. maximum pressure rating. P PC CB B P PIIE EZ ZO OT TR RO ON NIIC CS S,, IIN NC C.. 7 71 16 6-6 68 84 4-0 00 00 01 1 Mounting Adaptors Mounting Adaptors ADAPTORS FOR 111, 112, 113 PRESSURE SENSORS 1. Sensor diaphragms are flush mounted unless otherwise noted. 2. Always contact the factory for a detailed installation drawing before preparing mounting ports. BENEFITS LIMITATIONS M Mo od de ells s 1 11 11 1,, 1 11 12 2,, 1 11 13 3 M Miin nii P Pr ro ob be e S Stty ylle e S Se en ns so or r Requires precision machining steps. Needs a (17-4 Ph SS) 5/16-24 thd: Direct mount using minimum 0.75 wall thickness or counterbore floating clamp nut. Use when there is limited thicker walls to install. space available to install sensor or a flush diaphragm mount is desired. Sensor can be Use 074A connector extender for thicker walls installed using 5/16-24 or optional M7 x 0.75 (see page 58). clamp nut. 59 59 061A Series Thread Adaptor 062A Series NPT PipeThread Adaptor 064 Series Watercooled Adaptor O-ring Style Adaptor Simplified installation by drilling Conveniently adapts mini Adapts mini probe style sensor 0 06 61 1A A5 50 0: : (303 SS) Adaptor and tapping 3/8-24 mounting probe style sensors to hydraulic to high temp combustion and provides acceleration, strain hole. Eliminates precision 1/8” NPT mounting ports. exhaust manifold environments. and ground isolation in field machining mounting ports. blast applications. Adapts mini probe style sensor to 0 06 62 2A A0 01 1: : (17-4 PH SS) 1/8-27 0 06 64 4B B0 01 1: : (17-4 PH SS) 1/2-20 thin walled applications. NPT: fits standard 1/8-27 NPT thd: sensor recessed - isolates mounting port. sensor from environment. 0 06 61 1A A0 01 1: : (17-4 PH SS) 3/8-24 thd: installs in common 3/8-24 0 06 62 2A A0 05 5: : (316L) 1/8-27 NPT: 0 06 64 4B B0 02 2: : (17-4 PH SS) 1/2-20 mounting port. corrosive resistance (use with thd: sensor flush - better high 0 06 61 1A A0 09 9: : (316L) 3/8-24 thd: 316L sensor). frequency response. corrosive resistance (use with 316L sensor). 0 06 61 1A A5 59 9: : (Delrin) 3/8-24 thd: Delrin material electrically isolates sensor from ground*. 0 06 61 1A A5 57 7: : (17-4 PH SS) 1/2-20 thd 0 06 61 1A A5 58 8: : (17-4 PH SS) 3/8-24 thd: dummy plug - plugs port when not testing - (other size plugs are also available). Limited to thinner wall or counterbore Since the tapered pipe thread Requires greater mounting area. Adaptor installs with press fit thicker walls to install. seals on the thread itself, it is and should not be used at more difficult to achieve flush Recessed sensor: reduced pressures greater than 20 psi Requires more area to prepare mounting diaphragm mount. frequency capabilities. unless properly supported from port than mini probe style sensor alone. back side to prevent sensors Requires more area to prepare Flush sensor: diaphragm is from being blown out at higher *Lower strength of Delrinlimits use to mounting port than probe style susceptible to flash thermal pressures. lower pressure applications (<500 psi). sensor alone. effects. P PR RE ES SS SU UR RE E A AN ND D F FO OR RC CE E S SE EN NS SO OR R D DIIV VIIS SIIO ON N T TO OL LL L F FR RE EE E: : 8 88 88 8-6 68 84 4-0 00 01 11 1 ADAPTOR TYPE PROBE STYLE SENSOR LIMITATIONS BENEFITS Mounting Adaptors Mounting Adaptors ADAPTORS FOR 106B, 116B02, 116B PRESSURE SENSORS 1. Sensor diaphragms are flush mounted unless otherwise noted. 2. Always contact the factory for a detailed installation drawing before preparing mounting ports. BENEFITS LIMITATIONS M Mo od de ells s 1 10 06 6B B,, 1 11 16 6B B0 02 2,, 1 11 16 6B B P Pr ro ob be e S Stty ylle e Requires precision machining steps. Needs S Se en ns so or r a minimum 0.75 wall thickness or (17-4 PH SS) 3/4-16 thd: Direct mount counterbore thicker walls to install. sensor using floating clamp nut. Use when there is limited space available to install sensor or a flush diaphragm mount is desired. Sensor can be installed using a 3/4-16 clamp nut. 60 60 062A Series NPT Pipe Thread Adaptor 064 Series Watercooled Adaptor 061A Series Thread Adaptor Simplified installation by drilling and 0 06 62 2A A0 06 6: : (17-4 PH SS) 1/2-24 NPT: Adapts sensor probe to exhaust manifold and tapping 3/4-16 mounting hole. Eliminates Conveniently adapts probe style sensors to other high temperature environments. precision machining mounting ports. Adapts hydraulic 1/2-14 NPT mounting ports. probe style sensor to thin walled application. 0 06 64 4B B0 06 6 (17-4 PH SS) M20 x 1.50g thd: sensor recessed - isolates sensor from environment. 0 06 61 1A A6 60 0: : (316L) 3/4-16 thd: corrosive resistance (use with 316L sensor). 0 06 64 4B B0 05 5 (17-4 PH SS) 7/18-14 thd: sensor flush - better high frequency response. ® 0 06 61 1A A6 61 1: : (Delrin) 3/4-16 thd: Delrin material electrically isolates sensor from Requires greater mounting area. ground. Limited to thinner wall or counterbore thicker Since the tapered pipe thread seals on the walls to install. thread itself, it is more difficult to achieve flush Recessed sensor: reduced frequency diaphragm mount. capabilities. Requires more area to prepare mounting port than probe style sensor alone. Requires more area to prepare mounting port Flush sensor: diaphragm is susceptible to flash than probe style sensor alone. thermal effects. Lower strength of Delrin limits use to lower pressure applications (<500 psi). P PC CB B P PIIE EZ ZO OT TR RO ON NIIC CS S,, IIN NC C.. 7 71 16 6-6 68 84 4-0 00 00 01 1 LIMITATION BENEFITS ADAPTOR TYPE PROBE STYLE SENSOR Installation Preparation & Accessories Installation Preparation & Accessories THIS SECTION IS FOR REFERENCE ONLY. BEFORE PREPARING A MOUNTING HOLE, CONTACT PCB FOR A CURRENT INSTALLATION DRAWING. Models 040A10 and 040A20 Installation Tooling Kits used. The kits provide the tooling necessary for precision- are available to assist in machining mounting ports for machining mounting ports for applicable sensors. Refer to the standard design and high-pressure ballistics sensors "Technical Information" section of this catalog for a detailed for applications where PCB mounting adaptors are not description of flush versus recess sensor installation. IIn ns stta alllla attiio on n K Kiitt M Mo od de ell 0 04 40 0A A1 10 0 ((ffo or r S Se er riie es s 1 11 11 1,, 1 11 12 2,, 1 11 13 3 p pr re es ss su ur re e p pr ro ob be es s)).. K Kiitt iin nc cllu ud de es s a allll tto oo olliin ng g lliis stte ed d b be ello ow w.. Flush Mounting Installation Recess Mounting Installation Tool Required: Tool Required: Center Drill #4 (0.312 dia) Center Drill #4 (0.312 dia) Drill #3 (0.213 dia) Drill “C” (0.242 dia) Ream #2 (0.221 dia) Ream “1/4” (0.250 dia) Drill “C” (0.242 dia) Flat Bottom Ream “1/4” (0.250 dia) Ream “1/4” (0.250 dia) Drill “1” (0.272 dia) Flat Bottom Ream “1/4” (0.250 dia) Tap 5/16-24 UNF-2B Drill “1” (0.272 dia) Tap 5/16-24 UNF-2B Kit items may be ordered separately. Contact factory for installation drawing for specific model. F Fllu us sh h M Mo ou un nttiin ng g H Ho olle e P Pr re ep pa ar ra attiio on n ffo or r S Se er riie es s 1 11 11 1,, 1 11 12 2 a an nd d 1 11 13 3 P Pr re es ss su ur re e P Pr ro ob be es s Center Drill #4 Center Drill #3 Ream #2 Drill “C” ➔ Ø .312 (Ø7.92) to full Ø Ø.213 (Ø5.41) Thru Ø.2210 (Ø5.613) Thru Ø.242 (Ø6.15) x .400 (10.16) .75 (19.1) 61 61 Ream 1/4 Drill “I” Tap Flat Bottom Ream 1/4➔➔➔➔ Ø.2500 (Ø6.350) x .420 (10.67) Ø.272 (Ø6.91) x .480 (12.19) 5/16-24 UNF-2B x .400 (10.16) Ø.2500 (Ø6.350) x .520 (13.21) R Re ec ce es ss s M Mo ou un nttiin ng g H Ho olle e P Pr re ep pa ar ra attiio on n ffo or r S Se er riie es s 1 11 11 1,, 1 11 12 2 a an nd d 1 11 13 3 P Pr re es ss su ur re e P Pr ro ob be es s Center Drill #4 Drill Ø Drill “C” Ream 1/4 ➔➔ Ø.312 (Ø7.92) to Full Ø To Suit User Requirements Ø.242 (Ø6.15) x .600 (15.24) Ø.2500 (Ø6.350) x .600 (16.51) To suit user requirements. Flat Bottom Ream 1/4 Drill “I” Tap ➔➔➔ Ø.2500 (Ø6.350) x .750 (19.05) Ø0.272 (Ø6.91) x .480 (12.19) 5/16-24 UNF-2B x .400 (10.16) .75 (19.1) To suit user requirements P PR RE ES SS SU UR RE E A AN ND D F FO OR RC CE E S SE EN NS SO OR R D DIIV VIIS SIIO ON N T TO OL LL L F FR RE EE E: : 8 88 88 8-6 68 84 4-0 00 01 11 1 Installation Preparation & Accessories Installation Preparation & Accessories THIS SECTION IS FOR REFERENCE ONLY. BEFORE PREPARING A MOUNTING HOLE, CONTACT PCB FOR A CURRENT INSTALLATION DRAWING. IIn ns stta alllla attiio on n K Kiitt M Mo od de ell 0 04 40 0A A2 20 0 ((ffo or r S Se er riie es s 1 10 08 8,, 1 11 18 8,, 1 10 09 9 a an nd d 1 11 19 9 B Ba alllliis sttiic c P Pr re es ss su ur re e S Se en ns so or rs s)) K Kiitt iin nc cllu ud de es s a allll tto oo olliin ng g lliis stte ed d b be ello ow w.. Flush Mounting Installation Recess Mounting Installation Tools Required: Tools Required: Center Drill #5 (0.437 dia) Center Drill #5 (0.437 dia) Drill “B” (0.238 dia) Drill “B” (0.238 dia) Drill “P” (0.323 dia) Drill “P” (0.323 dia) (1) (3) Flat Bottom Ream (0.323 dia) (2) Flat Bottom Ream (0.323 dia) Drill “Q” (0.332 dia) Drill “Q” (0.332 dia) Ream “1/4” (0.250 dia) Tap 3/8-24 UNF-2B Tap 3/8-24 UNF-2B (1) Ream “1/4” (0.250 dia) (2) Flat Bottom Ream (0.323 dia) (1) Model 041A Pilot Bushing, (2) Model 040A06, (3) Model 040A Kit items may be ordered separately. Contact factory for installation drawing for specific model. F Fllu us sh h M Mo ou un nttiin ng g H Ho olle e P Pr re ep pa ar ra attiio on n ffo or r S Se er riie es s 1 10 08 8,, 1 11 18 8,, 1 10 09 9 a an nd d 1 11 19 9 B Ba alllliis sttiic c S Se en ns so or rs s Flat Bottom Ream ➔ Center Drill #5 Drill “B” Drill “P” Ø .323 (Ø8.20) x .540(13.72) ➔ Ø .437 (Ø11.10) to full Ø.0375 (Ø9.52) Ø.238 (Ø6.04) Thru Ø.323 (Ø8.20) x .500(12.70) Use Model 040A06 reamer Dia 1.375 (9.52) (1) .800 (20.32) 62 62 Ream “1/4” (1) Counterbore for thicker Drill “Q” Tap Ø.2500(Ø6.350) Thru walls to obtain this dimension➔ Ø .332 (Ø8.43) x .510 (12.95) 3/8-24 UNF-2B x .470(11.94) Use Model 041A Pilot Bushing R Re ec ce es ss s M Mo ou un nttiin ng g H Ho olle e P Pr re ep pa ar ra attiio on n ffo or r S Se er riie es s 1 10 08 8,, 1 11 18 8,, 1 10 09 9 a an nd d 1 11 19 9 B Ba alllliis sttiic c S Se en ns so or rs s Drill Ø Center Drill #5 (Ø 0.09 to Ø 0.250) Drill “B” Drill “P” ➔➔ Ø .437(Ø11.10) to Full Ø .375(Ø9.52) To Suit User Requirements Ø .238(Ø6.04) x .750(19.05) Ø .323 (Ø8.20) x .500 (12.7) Dia. .375 (9.52) Ream 1/4” Flat Bottom Ream 1/4” Flat Bottom Ream ➔➔➔ Drill “Q” Ø.2500 (Ø 6.350)x .750 (19.05) Ø.2500 (Ø 6.350) x .800 (20.32) Ø.323 (Ø8.20) x .540 (13.72) Tap➔➔ Ø.323 (Ø8.43) x .510 (12.95) Use Model 041A pilot bushing Use 041A plot bushing, 040A reamer Use Model 040A06 Reamer 3/8-24 UNF-2B x .470 (11.94) .800 (20.32) To suit user requirements. P PC CB B P PIIE EZ ZO OT TR RO ON NIIC CS S,, IIN NC C.. 7 71 16 6-6 68 84 4-0 00 00 01 1 Custom Cable Ordering Guide Custom Cable Ordering Guide T TO O O OR RD DE ER R C CU US ST TO OM M C CA AB BL LE ES S: : 1. First designate whether the cable shall be ordered in English or Metric units. 2. Choose the desired cable. (See pages 66 and 67 for cable specifications.) 3. Find the connector that mates to the sensor. (See page 68 for connector outline drawings.) 4. Determine the length of cable required. 5. Choose the cable termination connector. (See page 68.) 6. Fill the squares with appropriate letter or number designation: EXAMPLE BELOW: 25 ft low-noise cable with 10-32 plug connection to the sensor. The cable terminates in a right angle 10-32 plug. 2 AK 0 0 3 AA 0 5 ENGLISH – BLANK CABLE LENGTH Metric – M English – Feet Metric – Meters SENSOR CONNECTOR CABLE TERMINATION STANDARD CABLE TYPES STANDARD CONNECTOR TYPES NO. COAXIAL LETTER CONNECTOR RECOMMENDED 63 63 002 General purpose white (392°F/200°C) CABLES 003 Blue low noise/high temp. (550°F/288°C) 10-32 Coaxial 004 Industrial Teflon, high temp. (392°F/200°C) AA 10-32 coaxial plug (standard) 030,033,Groups 1, 3 005 Ruggedized 002 type (275°F/135°C) AW 10-32 coaxial solder adaptor plug (repairable) 007, 031, 035 006 Ruggedized 003 type (275°F/135°C) AH 10-32 coaxial plug (wire lock hex) Groups 1 & 3 012 General purpose RG-58/U (140°F/60°C) AK 10-32 coaxial plug (right angle) Groups 1 & 3 015 Neoprene jacketed (225°F/107°C) AL 10-32 coaxial jack (standard) Groups 1 & 3 018 Lightweight black (221°F/105°C) 025 Ruggedized Tefzel jacketed (390°F/199°C) 5-44 COAXIAL 030 Blue miniature, low noise (400°F/204°C) AG 5-44 coaxial plug (standard) 030, Groups 1 & 3 033 Underwater, polyurethane (250°F/121°C) AF 5-44 coaxial plug (right angle) Groups 1 & 3 CX 5-44 coaxial jack (standard) Groups 1 & 3 TWISTED/SHIELDED PAIR 024 Industrial, polyurethane (250°F/121°C) “LOCKING” 020 High temperature Teflon (392°F/200°C) AB BNC jack Groups 1, 2 & 3 032 General use, lightweight (400°F/204°C) AC BNC plug Groups 1, 2, 3 & 5 AQ TBNC plug (2-pin) 020, 024, 032 MISCELLANEOUS AR TBNC jack (2-pin) 020, 024, 032 007 2-conductor red/black ribbon (176°F/80°C) AT TNC plug (threaded) 012, 015, 033 014 Coiled 2-conductor, 8 ft only (176°F/80°C) AU TNC jack (threaded) 012, 015, 033 031 Twisted pair, red/white Teflon (400°F/204°C) 035 Mini, red/black twisted pair (400°F/204°C) INDUSTRIAL AE Environmentally Sealed 2-pin MS3106 004, 012, 024 HARDLINE AM 2-pin military style (MS3106) Groups 1, 2 & 5 008 SiO Dielectric (1 500°F/816°C) 26 pF/ft AP 2-pin military style (MS3106) w/strain relief Group 2 2 027 MgO Dielectric (1 500°F/816°C) 66 pF/ft 028 SiO Dielectric (1 500°F/816°C) 15 pF/ft MISCELLANEOUS 2 029 SiO Dielectric(1 500°F/816°C) 27 pF/ft AD Pigtail (no connector) All 2 AS Spade lug (specify size) All (except Group 4) AO Integral hardline weld to sensor (consult PCB) Group 4 The combination of cables and connectors listed are only recommended AZ Conhex plug 004 configurations; other configurations may be available. Group 1: 002, 003, 005, 006, 018, 025 Consult PCB before ordering. See cable and connector descriptions on Group 2: 004, 012, 020,024,033 page 66 thru 68. Group 3: 010, 034,059 (Terminates in three 6 inch (15cm) 002 cables with specified connector). Group 4: 008, 027, 028, 029 Group 5: 014, 015 P PR RE ES SS SU UR RE E A AN ND D F FO OR RC CE E S SE EN NS SO OR R D DIIV VIIS SIIO ON N T TO OL LL L F FR RE EE E: : 8 88 88 8-6 68 84 4-0 00 01 11 1 Standard Cables Standard Cables S ST TO OC CK K C CA AB BL LE ES S A AR RE E A AV VA AIIL LA AB BL LE E F FO OR R Q QU UIIC CK KE ES ST T D DE EL LIIV VE ER RY Y! ! The following pages list stock cables that are generally available for overnight delivery. Should your application require a cable not shown, consult the Custom Cable Ordering Guide on page 63 for ordering information. S Se er riie es s 0 00 02 2–– G Ge en ne er ra all P Pu ur rp po os se e W Wh hiitte e C Co oa ax xiia all S Se er riie es s 0 00 03 3–– L Lo ow w-n no oiis se e B Bllu ue e C Co oa ax xiia all General purpose coaxial cable with an extruded High-temperature, low-noise cable with Teflon-wrapped waterproof Teflon insulation jacket: 29 pF/ft cable insulation. Internal lubricant reduces noise induced by capacitance, 400°F (204°C) maximum temperature, cable motion: 29 pF/ft , 550°F (288°C) maximum 0.071 inch (1,8 mm) cable diameter. Suitable for most temperature, 0.079 inch (2,0 mm) diameter. For use with ® ICP sensor applications. charge or ICP sensors. Standard 10-32 coaxial plug for connection to the sensor and terminates in a standard 10-32 coaxial plug. Coaxial Low-Noise Length Model No. Model No. 1 ft (0,3m) — — 003A01 3 ft (0,9m) 002A03 003A03 5 ft (1,5m) 002A05 003A05 10-32 Coaxial Plug 10-32 Coaxial Plug 10 ft (3,0m) 002A10 003A10 20 ft (6,1m) 002A20 003A20 30 ft (9,1m) 002A30 003A30 50 ft (15,2m) 002A50 — — Standard 10-32 coaxial plug for connection to the sensor and terminates in a BNC jack. 64 64 L Le en ng gtth h M Mo od de ell N No o.. M Mo od de ell N No o.. 1 ft (0,3m) 002B01 003B01 3 ft (0,9m) 002B03 003B03 10-32 Coaxial Plug BNC Jack Standard 10-32 coaxial plug for connection to the sensor and terminates in a BNC plug. L Le en ng gtth h M Mo od de ell N No o.. M Mo od de ell N No o.. 3 ft (0,9m) 002C03 003C03 5 ft (1,5m) 002C05 003C05 10 ft (3,0m) 002C10 003C10 20 ft (6,1m) 002C20 003C20 30 ft (9,1m) 002C30 003C30 10-32 Coaxial Plug BNC Plug BNC plug to BNC plug extension cable. L Le en ng gtth h M Mo od de ell N No o.. M Mo od de ell N No o.. 3 ft (0,9m) 002T03 003D03 10 ft (3,0m) 002T10 003D10 20 ft (6,1m) 002T20 003D20 BNC Plug BNC Plug Standard 5-44 coaxial plug for connection to the sensor and terminates in a BNC plug. L Le en ng gtth h M Mo od de ell N No o.. M Mo od de ell N No o.. 3 ft (0.9m) 002P03 003P03 5 ft (1,5m) 002P05 003P05 10 ft (3,0m) 002P10 003P10 20 ft (6,1m) 002P20 003P20 5-44 Coaxial Plug BNC Plug 30 ft (9,1m) 002P30 003P30 Other cables should be ordered according to the Custom Cable Ordering Guide on page 63. P PC CB B P PIIE EZ ZO OT TR RO ON NIIC CS S,, IIN NC C.. 7 71 16 6-6 68 84 4-0 00 00 01 1 Standard Cables Standard Cables S Se er riie es s 0 00 07 7–– 2 2-C CO ON ND DU UC CT TO OR R R RIIB BB BO ON N S Se er riie es s 0 03 31 1 - 2 2-C CO ON ND DU UC CT TO OR R T TW WIIS ST TE ED D P PA AIIR R Flexible, 2-conductor ribbon cable (AWG 30) with Flexible, 2-conductor twisted pair (AWG 30) with red/black PVC insulation: 10 pF/ft, 176°F (80°C) red/white Teflon insulation: 7 pF/ft, 400°F (204°C) maximum temperature. Single strand diameter 0.028 inch maximum temperature. Single strand diameter 0.03 inch ® (0,71 mm). Excellent for high-shock applications with ICP (0,8 mm). Excellent for high-shock applications with ICP sensors. User-repairable. sensors. User-repairable. 10-32 coaxial solder adaptor for connection to sensor and terminates in 10-32 coaxial solder adaptor. L Le en ng gtth h M Mo od de ell N No o.. M Mo od de ell N No o.. (031 Type) 5 ft (1,5 m) 007A05 031A05 10ft (3,0 m) 007A10 031A10 20ft (6,1 m) 007A20 031A20 (007 Type) 10-32 Solder Adaptor 10-32 Solder Adaptor S Se er riie es s 0 01 18 8–– L LIIG GH HT TW WE EIIG GH HT T C CO OA AX XIIA AL L Lightweight coaxial cable with black vinyl insulation jacket: 48 pF/ft cable capacitance, 221°F (105°C) maximum temperature, 0.051 inch (1,3 mm) cable diameter. For use with miniature ICP sensors to reduce cable strain. Standard 5-44 coaxial plug for connection to the sensor and terminates in a BNC plug. L Le en ng gtth h M Mo od de ell N No o.. 65 65 3 ft (0,9m) 018C03 5 ft (1,5m) 018C05 10 ft (3,0m) 018C10 20 ft (6,1m) 018C20 5-44 Coaxial Plug BNC Plug 30 ft (9,1m) 018C30 Standard 5-44 coaxial plug for connection to the sensor and terminate a standard 10-32 coaxial plug. L Le en ng gtth h M Mo od de ell N No o.. 3 ft (0,9m) 018G03 5-44 Coaxial Plug 10-32 Coaxial Plug 5 ft (1,5m) 018G05 10 ft (3,0m) 018G10 20 ft (6,1m) 018G20 30 ft (9,1m) 018G30 S Se er riie es s 0 01 12 2–– S ST TA AN ND DA AR RD D B BL LA AC CK K C CO OA AX XIIA AL L Low-cost, black coaxial cable (RG-58/U) similar to standard television cable: 29 pF/ft capacitance, 140°F (60°C) maximum temperature, 0.195 inch (4,95 mm) cable diameter. Ideal for transmitting low-impedance signals over long cables. BNC plug to BNC plug extension cable. L Le en ng gtth h M Mo od de ell N No o.. 3 ft (0,9m) 012A03 10 ft (3,0m) 012A10 20 ft (6,1m) 012A20 BNC Plug BNC Plug 50 ft (15,2m) 012A50 P PR RE ES SS SU UR RE E A AN ND D F FO OR RC CE E S SE EN NS SO OR R D DIIV VIIS SIIO ON N T TO OL LL L F FR RE EE E: : 8 88 88 8-6 68 84 4-0 00 01 11 1 Cable Descriptions Cable Descriptions 0 00 07 7 - L LIIG GH HT TW WE EIIG GH HT T 2 2-C CO ON ND DU UC CT TO OR R R RIIB BB BO ON N C CA AB BL LE E 0 00 02 2 - G GE EN NE ER RA AL L P PU UR RP PO OS SE E W WH HIIT TE E C CO OA AX XIIA AL L PVC Insulation Shield (ground) Dielectric Conductor #1 (signal-red) White Conductor #2 (ground-black) Conductor Teflon (signal) Jacket 007 - CABLE: Lightweight, flexible, 2-conductor ribbon cable (AWG 30) with red/black PVC insulation: 10 pF/ft, max. temp. 002 CABLE: General purpose, white coaxial cable with 176°F (80°C), 0.028 inch (0.71 mm) single strand diameter. waterproof, extruded Teflon jacket: 29 pF/ft, 400°F (204°C) Use with 10-32 solder adaptor plug, “W” Suitable for use with max. temperature, 0.071 inch (1,8mm) diameter. Suitable for ICP sensors. User-repairable. ICPsensor applications. 0 00 03 3 - B BL LU UE E L LO OW W-N NO OIIS SE E/ /H HIIG GH H-T TE EM MP PE ER RA AT TU UR RE E C CO OA AX XIIA AL L 0 00 08 8 - S SIIL LIIC CO ON N D DIIO OX XIID DE E H HA AR RD DL LIIN NE E C CA AB BL LE E Graphite Dielectric Dielectric Shield (ground) Lubricant Teflon OuterJacket Wrapped Conductor Conductor (ground) Outer (signal) Jacket 008 - CABLE: Hardline coaxial cable with Inconel 600 outer 003 CABLE: Blue low-noise, high-temperature coaxial cable with jacket and SiO Dielectric: 26 pF/ft, max. temp. 1500°F 2 Teflon-wrapped insulation jacket: 29 pF/ft, 550°F (288°C) (816°C), 0.125 inch (3,18mm) diameter. Low-cost cable for use maximum temperature, 0.079 inch (2,0mm) cable diameter. with charge mode or ICPsensors when running cable through Recommended for use with either ICP or charge mode high-temperature environments. piezoelectric sensors. 0 01 12 2 - S ST TA AN ND DA AR RD D R RG G-5 58 8/ /U U C CO OA AX XIIA AL L C CA AB BL LE E 0 00 04 4 - IIN ND DU US ST TR RIIA AL L H HIIG GH H-T TE EM MP PE ER RA AT TU UR RE E C CO OA AX XIIA AL L Extruded Brown Teflon Jacket Shield (ground) Dielectric Shield (ground) Dielectric 66 66 Conductor Black Vinyl Conductor (signal) Outer Jacket (signal) 004 CABLE: Industrial coaxial cable with extruded waterproof, 012 - CABLE: Standard RG-58/U coaxial cable with a brownTeflon insulation jacket: 15 pF/ft, 392°F (200°C) polyethylene dielectric and black vinyl insulation jacket: 29 maximum temperature, 0.140 inch (3,6mm) cable diameter. For pF/ft, max. temperature 140°F (60°C), 0.195 inch (4,95mm) use with ICP sensors in high temperature or corrosive industrial cable diameter. For use as standard extension cable with low- environment. impedance signals. 0 00 05 5 - R RU UG GG GE ED DIIZ ZE ED D 0 00 02 2-T TY YP PE E C CO OA AX XIIA AL L C CA AB BL LE E 0 01 18 8 - M MIIN NIIA AT TU UR RE E,, L LIIG GH HT TW WE EIIG GH HT T C CO OA AX XIIA AL L Shield (ground) Dielectric Tin-plated White Copper Braid Teflon Jacket Shield (ground) Dielectric Black Conductor Clear PVC (signal) Heat- conductor Jacket Shrink (signal) Tubing 018 CABLE: Lightweight, flexible coaxial cable with PVC insulation jacket: 48 pF/ft, 221°F (105°C) max temperature, 0.051 inch (1,3 mm) diameter. Generally for use with 5-44 005 CABLE: Ruggedized, 002 cable with tin-plated copper coaxial connectors on miniature ICP sensors. braid and heat-shrink tubing: 29 pF/ft, maximum temperature 275°F (135°C), 0.089 inch (2,3mm) diameter. For use with ICP sensors. 0 02 20 0-H HIIG GH H-T TE EM MP PE ER RA AT TU UR RE E,, T TW WIIS ST TE ED D S SH HIIE EL LD DE ED D P PA AIIR R 0 00 06 6 - R RU UG GG GE ED DIIZ ZE ED D 0 00 03 3-T TY YP PE E C CO OA AX XIIA AL L C CA AB BL LE E Conductor #1 Teflon Cover Tin-plated Wrapped Teflon Shield Graphite Lubricant (signal-red) Copper Braid Outer Jacket (ground) Dielectric Clear Heat- Conductor Conductor #2 Shrink (signal) Foil Shield and Ground Strap (ground-black) Tubing 020 - CABLE: Twisted shielded pair covered with Teflon 006 - CABLE: Ruggedized 003 low-noise cable with insulation jacket: 78 pF/ft, max temperature 392°F (22°C), tin-plated copper braid and heat-shrink tubing: 29 pF/ft, 0.16 inch (4,06mm) diameter. For use with ICP sensors in high maximum temperature 275°F (135°C), 0.103 inch (2,62mm) RFI and EMI environments. 100% foil shield. diameter. Recommended for charge mode or ICP sensors requiring a durable cable. P PC CB B P PIIE EZ ZO OT TR RO ON NIIC CS S,, IIN NC C.. 7 71 16 6-6 68 84 4-0 00 00 01 1 Cable Descriptions Cable Descriptions 0 02 24 4 - S ST TA AN ND DA AR RD D IIN ND DU US ST TR RIIA AL L,, T TW WIIS ST TE ED D S SH HIIE EL LD DE ED D P PA AIIR R 0 03 31 1–– R RE ED D/ /W WH HIIT TE E T TW WIIS ST TE ED D P PA AIIR R Polyurethane Jacket Shield Conductor #1 (signal-red) Conductor #1 Insulating Jackets (ground-white) Conductor #2 Conductor #2 (ground-blue) (signal-red) 031-CABLE: Red/white two-conductor, twisted pair 024-CABLE: Polyurethane-jacketed, twisted shielded pair: (AWG 30) with Teflon insulation: 7 pF/ft, maximum 31 pF/ft, 250°F (121°C), maximum temperature, 0.25 temperature 400°F (204°C), 0.03 inch (0,8mm) single inch (6,35mm) cable diameter. For use with industrial, ® diameter. Use with the repairable 10-32 solder connector ruggedized ICP sensors in factory environments where adaptor “AW”. Suitable for use with ICP sensors. RFI and EMI are present. 0 03 32 2 - T TW WIIS ST TE ED D S SH HIIE EL LD DE ED D,, G GE EN NE ER RA AL L U US SE E 2 2-C CO ON NN NE EC CT TO OR R 0 02 25 5 - S SH HIIE EL LE ED D T TE EF FZ ZE EL L-J JA AC CK KE ET TE ED D C CO OA AX XIIA AL L Tefzel Outer Shield Insulation Ground Jacket Dielectric 032 - CABLE: General purpose, twisted, shielded, 2- conductor cable with Teflon jacket: 20pF/ft, 400°F Conductor (signal) (204°C) maximum temperature, 0.075 inch, (1,9mm) diameter. Use with case-isolated sensors. ® 025-CABLE: White RG178 coaxial with rugged Tefzel Conductor #1 Teflon Jacket Shield outer insulating jacket: 37 pF/ft, 390°F (199°C), maximum (signal-white) temperature, 0.116 inch (2,95mm) diameter. For use with ICP sensors in industrial or Teflon-prohibitive environments. Conductor #2 (ground-black) 67 67 0 02 27 7,, 0 02 28 8 A AN ND D 0 02 29 9 - H HA AR RD DL LIIN NE E C CA AB BL LE ES S 0 03 33 3–– P PO OL LY YU UR RE ET TH HA AN NE E-J JA AC CK KE ET TE ED D C CO OA AX XIIA AL L Dielectric Outer Jacket Conductor (ground) (signal) Polyurethane Jacket Shield (ground) Dielectric Conductor (signal) 027-CABLE: ARI Hardline coaxial cable with Inconel 600 outer MgO dielectric: 17pF/ft, maximum temperature 1500°F (816°C), 0.125 inch (3,18mm) diameter. Use with standard ICP sensors when running cables through 033-CABLE: Polyurethane-jacketed coaxial cable: 26 pF/ft, extremely high-temperature environment. 250°F (121°C) maximum temperature, 0.115 inch (2,9mm) diameter. Suitable for long term underwater testing applications 028 - CABLE: Hardline coaxial cable with an Inconel 600 with ICP sensors. outer conducting jacket, SiO dielectric: 15 pF/ft, maximum 2 temperature 1 500 °F (816°C), 0.125 inch (3,18mm) diameter. For running high-quality, low-or high-impedance 0 03 35 5–– M MIIN NIIA AT TU UR RE E R RE ED D/ /B BL LA AC CK K T TW WIIS ST TE ED D P PA AIIR R signals through high-temperature environments. Conductor #1 029 - CABLE: Hardline coaxial cable, 304 stainless steel Insulating Jackets (ground-white) outer jacket, SiO dielectric: 27 pF/ft nominal, maximum 2 temperature 1 500°F (816°C), 0.125 inch (3,18mm) Conductor #2 (signal-red) diameter. For running high-quality, low-or high-impedance signals through high-temperature environments. 035-CABLE: Miniature red/black twisted pair (AWG 36) with Teflon insulation: 10pF/ft, maximum temperature 400°F 0 03 30 0–– M MIIN NIIA AT TU UR RE E,, L LO OW W-N NO OIIS SE E C CO OA AX XIIA AL L (204°C), 0.012 inch (0,3mm) single strand diameter. Use with the user-repairable 10-32 solder connector adaptor “AW”. Shield (ground) Lubricant Dielectric Conductor Teflon Jacket (signal) Suitable for use with ICP sensors. 030-CABLE: Blue low-noise, miniature coaxial cable: 30 pF/ft, maximum temperature 400°F (204°C), 0.031 diameter (0,79mm). Use with either charge of ICP sensors requiring a miniature, lightweight cable. P PR RE ES SS SU UR RE E A AN ND D F FO OR RC CE E S SE EN NS SO OR R D DIIV VIIS SIIO ON N T TO OL LL L F FR RE EE E: : 8 88 88 8-6 68 84 4-0 00 01 11 1 Connector Descriptions Connector Descriptions See the catalog cable ordering guide on page 63 to determine cable connector compatibility. Standard connectors are listed below: A AA A.. A AM M.. 2 2-p piin n M Miilliitta ar ry y S Stty ylle e 1 10 0-3 32 2 C Co oa ax xiia all P Pllu ug g ((M MS S3 31 10 06 6)) ((s stta an nd da ar rd d)) A AB B.. B BN NC C J Ja ac ck k A AO O.. IIn ntte eg gr ra all H Ha ar rd dlliin ne e W We elld d Sensor ((s stta an nd da ar rd d)) tto o S Se en ns so or r Weld ((c co on ns su ulltt P PC CB B)) Cable A AC C.. B BN NC C P Pllu ug g ((s stta an nd da ar rd d)) A AP P.. 2 2-p piin n M Miilliitta ar ry y S Stty ylle e ((M MS S3 31 10 06 6)) w wiitth h s sttr ra aiin n r re elliie eff A AD D.. P Piig gtta aiill ((lle ea ad ds s s sttr riip pp pe ed d a an nd d ttiin nn ne ed d)) A AQ Q.. T TB BN NC C P Pllu ug g ((2 2-p piin n)) A AE E.. E En nv viir ro on nm me en ntta alllly y S Se ea alle ed d C Co on nn ne ec ctto or r ((2 2-p piin n M MS S3 31 10 06 6)) 68 68 A AR R.. T TB BN NC C J Ja ac ck k ((2 2-p piin n)) A AF F.. 5 5-4 44 4 C Co oa ax xiia all P Pllu ug g ((r riig gh htt a an ng glle e)) A AG G.. 5 5-4 44 4 C Co oa ax xiia all P Pllu ug g A AS S.. S Sp pa ad de e L Lu ug g ((s stta an nd da ar rd d)) ((s sp pe ec ciiffy y llu ug g s siiz ze e)) A AH H.. 1 10 0-3 32 2 C Co oa ax xiia all P Pllu ug g ((w wiir re e-llo oc ck kiin ng g h he ex x)) A AT T.. T TN NC C P Pllu ug g ((tth hr re ea ad de ed d)) C CX X.. 5 5-4 44 4 C Co oa ax xiia all J Ja ac ck k ((s stta an nd da ar rd d)) A AK K.. 1 10 0-3 32 2 C Co oa ax xiia all P Pllu ug g A AU U.. T TN NC C J Ja ac ck k ((r riig gh htt a an ng glle e)) ((tth hr re ea ad de ed d)) A AL L.. 1 10 0-3 32 2 C Co oa ax xiia all J Ja ac ck k ((s stta an nd da ar rd d)) A AW W.. 1 10 0-3 32 2 S So olld de er r A Ad da ap ptto or r ((u us se er r-r re ep pa aiir ra ab blle e)) C CC C.. 1 10 0-3 32 2 C Co oa ax xiia all J Ja ac ck k H Ha ar rd dlliin ne e ffo or r 0 00 08 8,, 0 02 27 7,, 0 02 28 8,, 0 02 29 9 c ca ab blle e A AZ Z.. C Co on nh he ex x P Pllu ug g P PC CB B P PIIE EZ ZO OT TR RO ON NIIC CS S,, IIN NC C.. 7 71 16 6-6 68 84 4-0 00 00 01 1 Connector Adaptors Connector Adaptors 0 07 70 0A A0 01 1 0 07 70 0A A0 02 2 0 07 70 0A A0 03 3 S SC CO OP PE E IIN NP PU UT T T T C CO ON NN NE EC CT TO OR R: : BNC plug C CO ON NN NE EC CT TO OR R A AD DA AP PT TO OR R: : S SC CO OP PE E IIN NP PU UT T A AD DA AP PT TO OR R: : 10-32 coaxial 10-32 coaxial to two 10-32 coaxial jacks. Used for jack to BNC plug. For adapting BNC plug to BNC jack. Converts 10-32 splitting low-impedance signals. connectors for use with 10-32 coaxial plugs. connectors for use with BNC plugs. Ground 0 07 70 0A A0 05 5 Signal Power 1 10 0-3 32 2 C CO OA AX XIIA AL L F FE EE ED D-T TH HR RU U C CO ON NN NE EC CT TO OR R: : 10-32 coaxial jack to 0 07 70 0A A0 08 8 10-32 THD. 10-32 coaxial jack. Joins two cables coaxial terminating in 10-32 coaxial plugs. C CA AB BL LE E A AD DA AP PT TO OR R: : 10-32 coaxial jack to plug BNC jack. Joins cables terminating in a 0 07 70 0A A0 09 9 0 07 70 0B B0 09 9 BNC plug and a 10-32 coaxial plug. S SO OL LD DE ER R C CO ON NN NE EC CT TO OR R A AD DA AP PT TO OR RS S: : 10-32 coaxial plug to solder terminals. Excellent for high-shock applications. User-repairable. 0 07 70 0A A1 11 1 69 69 0 07 70 0A A1 12 2 B BN NC C T T C CO ON NN NE EC CT TO OR R: : BNC plug to two BNC jacks. Used as a cable splitter. 1/8” max wall thk B BN NC C C CO OU UP PL LE ER R: : BNC jack to BNC jack. 1/4” max 1/2” mtg thd Joins two cables terminating in BNC plugs. wall thk 5/15”-32 mtg thd 0 07 70 0A A1 13 3 0 07 70 0A A1 14 4 0 07 70 0A A2 20 0 F FE EE ED D-T TH HR RU U A AD DA AP PT TO OR R: : 1 10 0-3 32 2 H HE ER RM ME ET TIIC C F FE EE ED D-T TH HR RU U: : 10-32 10-32 coaxial jack to BNC jack. Bulkhead 1 10 0-3 32 2 C CO OA AX XIIA AL L R RIIG GH HT T A AN NG GL LE E coaxial jack to 10-32 coaxial jack. connects BNC plug to 10-32 coaxial plug. C CO ON NN NE EC CT TO OR R A AD DA AP PT TO OR R: : 10-32 Coaxial Tapped 5/16-32. jack to 10-32 coaxial plug. For use in confined locations. 0 07 76 6A A2 25 5 S Sttr ra aiin n R Re elliie eff C Co oa ax xiia all C Co on nn ne ec ctto or r 0 07 76 6B B0 06 6 a an nd d 0 07 76 6B B0 07 7 0 08 85 5A A1 18 8 0 07 76 6B B0 06 6 1 10 0-3 32 2 C CO OA AX XIIA AL L C CO ON NN NE EC CT TO OR R: : P PL LA AS ST TIIC C P PR RO OT TE EC CT TIIV VE E C CA AP P: : Provides strain Microdot connector crimp-on type. 0 07 76 6A A0 05 5 relief for solder connector adaptors, as Requires tool contained in 076B31 kit. well as protects cable ends. 0 07 76 6A A0 05 5 1 10 0-3 32 2 C CO OA AX XIIA AL L P PL LU UG G: : Microdot connector screw-on type. 0 07 76 6B B0 07 7 C CA AB BL LE E S ST TR RA AIIN N R RE EL LIIE EF F: : For 076B06 microdot connectors. 0 07 76 6A A2 25 5 C CO ON NN NE EC CT TO OR R T TO OO OL L: : Used to install 076A05 screw-on type microdot connector. M MO OD DE EL L 0 07 76 6B B3 31 1 M MIIC CR RO OD DO OT T C CR RIIM MP P-O ON N C CO ON NN NE EC CT TO OR R K KIIT T: : Includes 1 pin 0 08 85 5A A4 40 0 M MO OD DE EL L 0 07 76 6A A3 30 0 M MIIC CR RO OD DO OT T S SC CR RE EW W- crimping tool, 1 sleeve-crimping tool, and O ON N C CO ON NN NE EC CT TO OR R K KIIT T: : One Model 20 Model 076B06/B07 connectors/cable 1 10 0-3 32 2 C CO OA AX XIIA AL L G GR RO OU UN ND DIIN NG G C CA AP P: : 076A25 Tool and 20 Model 076A05 10- strain relief’s. (Tools not shown) (Wire 32 coaxial connectors for emergency Used to short charge mode sensors during stripper and soldering iron not included). repair of 002 or 003 type cables. storage and transportation. P PR RE ES SS SU UR RE E A AN ND D F FO OR RC CE E S SE EN NS SO OR R D DIIV VIIS SIIO ON N T TO OL LL L F FR RE EE E: : 8 88 88 8-6 68 84 4-0 00 01 11 1 Signal Conditioners Signal Conditioners ® ICP sensor signal conditioners provide the necessary constant Power units have either a color-coded circuit check-out meter current excitation voltage to ICP sensors and decouple the or LEDs for monitoring bias voltage on the signal lead. On sensor bias voltage from the output. A wide selection of signal the check-out meter, green indicates normal operation, red conditioners are available with battery or line power, with or indicates a short, and yellow indicates an open circuit. without gain, in single or multi-channel configurations, and Single-channel power units are available in sensor kits, with manual or computer controlled operation. complete with the pressure sensor of your choice, ready to connect and operate. These kits are provided ready to B BA AT TT TE ER RY Y-P PO OW WE ER RE ED D S SIIG GN NA AL L C CO ON ND DIIT TIIO ON NE ER R connect and operate. See page 74 for detailed information on sensor kits. Battery signal conditioners provide 27 volt, 2 mA constant- current power to ICP sensors. Features include the color- coded circuit check-out meter, a battery test button, and inputs for both an external battery source and a rechargeable battery option. Unity gain and selectable gain units are available. 4 48 80 0C C0 02 2 Unity gain 4 48 80 0E E0 09 9 Selectable gain of x1, x10 or x100 To specify recharge option, add prefix “R” to the model number (e.g., R480C02 indicates a Model 480C02 Signal Conditioner supplied with model 488A02 battery 4 48 80 0C C0 02 2 4 48 80 0E E0 09 9 charger and three 9-volt NICAD batteries. ® ® L LIIN NE E-T TY YP PE E IIC CP P S SE EN NS SO OR R S SIIG GN NA AL L 70 C CO ON ND DIIT TIIO ON NE ER R 70 AC-type conditioners power ICP low-impedance sensors and couple them to readout instruments. Output current is adjustable from 2 to 20 mA. The higher current is an advantage when driving high-frequency sensor signals over long cables (more than 100 ft.). Line-power units are factory set at 4 mA, which is adequate for most applications. 4 48 82 2A A0 06 6 Single channel, unity gain 4 48 82 2A A2 21 1 Single channel, unity gain, low noise, marked 4 48 82 2A A2 21 1 4 48 82 2A A2 22 2 4 48 82 2A A0 05 5 Four channel, unity gain 4 48 82 2A A2 22 2 Four channel, unity gain, low noise, marked 4 48 82 2B B1 11 1 Single channel, selectable gain of x1, x10 or x100 4 44 42 2A A0 02 2 Single channel, gain x1, x10 or x100, low noise, marked 4 48 84 4B B0 06 6 Single channel, provides DC coupling 4 48 82 2B B1 11 1 Single channel, gain x1, x10 or x100 4 48 82 2A A1 16 6 Four channel, push-button gain of x1, x10 or x100, overload and fault lights 4 44 42 2A A0 04 4 Four channel, gain x1, x10 or x100, low noise, marked 4 48 82 2A A1 17 7 Same as 482A16 with switchable output to one BNC jack 4 48 82 2A A1 16 6 Four channel, gain x1, x10 or x100, overload and fault lights 4 48 82 2A A1 18 8 Eight channel, push-button gain of x1, x10 or x100, overload and fault 4 48 82 2A A1 17 7 Four channel, gain x1, x10 or x100, 4-1 switchable output to one BNC jack lights, 8-1 switchable output to a single BNC jack 4 44 42 2A A0 06 6 Single channel, gain x1, x10 or x100, AC/DC selectable, 4 48 82 2A A1 19 9 Same as 482A18, dual 4-1 switchable output to two BNC jacks low noise, marked 4 48 82 2A A2 20 0 Eight channel, push-button gain of x1, x10 or x100, overload and fault lights. 4 48 82 2A A1 18 8 Eight channel, gain x1, x10 or x100, 8-1 switchable output to one BNC jack, overload and fault lights To specify operation from 220-volts, add prefix “F” to the model number (e. g., F482A06 indicates a Model 482A06 Signal Conditioner with 220-volt power operation). To specify operation from 220-volts, add prefix “F” to the model number (e. g., F482A16 indicates a Model 482A16 Signal Conditioner with 220-volt power operation). 4 48 82 2A A1 16 6 M MU UL LT TIIC CH HA AN NN NE EL L S SIIG GN NA AL L C CO ON ND DIIT TIIO ON NE ER R M MO OD DE EL L 4 48 81 1A A0 02 2 4 44 42 2A A0 06 6 ® For powering piezoelectric ICP sensors, this signal conditioner provides an effective method for managing large numbers of sensor channels. Standard features include gain of x1, x10 and x100 with autoranging and RS232 and RS485 computer-control interface. Additionally, LED indicators monitor normal and faulty operation as well as overload conditions. Power to the sensors is in the form of a 24 VDC, 4mA (adj. from 2 to 20 mA) constant current excitation. Sixteen BNC output jacks are also located on the front panel and 16 BNC input jacks/multipin input/output connectors on the rear panel. 4 48 81 1A A0 02 2 P PC CB B P PIIE EZ ZO OT TR RO ON NIIC CS S,, IIN NC C.. 7 71 16 6-6 68 84 4-0 00 00 01 1 Signal Conditioners Signal Conditioners PCB charge amplifiers have a three-position selectable L LA AB BO OR RA AT TO OR RY Y-S ST TY YL LE E C CH HA AR RG GE E A AM MP PL LIIF FIIE ER RS S input time constant (TC) switch. The long TC position The basic function of a laboratory charge amplifier is to allows for static calibration of quartz sensors as well as convert the high-impedance charge from a piezoelectric quasi-static measurements in thermally stable sensor into a low-impedance voltage signal compatible environments; the medium TC provides for drift-free with readout instruments. Signal normalization and gain dynamic operation; and the short TC position is used for adjust features allow the user to take advantage of the operation with ceramic-type sensors. very wide dynamic range of a piezoelectric sensor. See the PCB Electronics for Piezoelectric Sensors catalog for complete information on these products. B BA AS SIIC C “ “D DIIA AL L S SE EN NS SIIT TIIV VIIT TY Y” ” C CH HA AR RG GE E A AM MP PL LIIF FIIE ER R M Mo od de ell 4 46 62 2A A is an economically priced multi-range charge amplifier designed for use with quartz and ceramic piezoelectric sensors. This unit has 11 selectable ranges from 5 to 1000 000 pC, accommodating very large inputs from high-range quartz pressure sensors. The sensitivity dial is adjustable for sensors in 0.1 to 1.1 pC range, which matches most quartz pressure sensors. Sensor sensitivities greater than 1.1 pC/psi can be accomodated. A rear panel CAL INPUT provides for checking range and sensitivity settings. Other features include a switch-type ground to prevent ESD damage when connecting long cables. A 71 71 4 46 62 2A A three-position time constant switch can be set on “Long” for static calibration and quasi-static measurements, “Medium” for drift-free dynamic operation, and “Short” for use with ceramic sensors. Options include plug-in filters, a remote ground relay, and rack mounting. D DU UA AL L M MO OD DE E C CH HA AR RG GE E A AM MP PL LIIF FIIE ER RS S M Mo od de ells s 4 46 63 3A A a an nd d 4 46 64 4A A operate with charge mode piezoelectric sensors and provide a current source for ® coupling to ICP voltage mode sensors. M Mo od de ell 4 46 63 3A A is a multi-range “Dial-Cal” charge amplifier similar to the Model 464A with many of the same features. The significant operational differences of model 463A are the built-in calibration features and ranges expressed in psi, g, or lb Full Scale, instead of units per volt. M Mo od de ell 4 46 64 4A A is multi-range “Dial-Sensitivity” model 4 46 63 3A A similar to the Model 462A described above. Operation simply involves switching to the “Charge” or “ICP” mode, dialing in the sensor sensitivity, and switching to the desired range, which reads in units per volt. Plug-in filters, calibration input, and remote ground are standard features. P PR RE ES SS SU UR RE E A AN ND D F FO OR RC CE E S SE EN NS SO OR R D DIIV VIIS SIIO ON N T TO OL LL L F FR RE EE E: : 8 88 88 8-6 68 84 4-0 00 01 11 1 Signal Conditioners Signal Conditioners M MO OD DE EL L 4 46 62 2B B5 52 2 L LA AB BO OR RA AT TO OR RY Y-S ST TY YL LE E B BA AL LL LIIS ST TIIC CS S C CH HA AR RG GE E A AM MP PL LIIF FIIE ER R M Mo od de ell 4 46 62 2B B5 52 2 Designed for use with quartz ballistic sensors, this laboratory-style charge amplifier features a digital dial switch for inputting sensor sensitivity and standardizing the signal sensitivity at 10 000 psi/volt. Other features include: manual or remote grounding, a built-in calibration capacitor, and a three-position discharge time constant switch. S SY YS ST TE EM MS S 4 40 00 0A A2 20 0 A AN ND D 4 40 00 0A A2 21 1 A AM MM MU UN NIIT TIIO ON N T TE ES ST TIIN NG G M MO ON NIIT TO OR R This Ammunitions Testing Monitor combines a Ballistics Charge Amplifier and a Model 451A07 Digital Peak Meter conveniently packaged together for conducting automated testing of ammunition. S Sy ys stte em m 4 40 00 0A A2 20 0 utilizes a Model 462B52 Charge Amplifier standardized at 10 000 psi/volt, while S Sy ys stte em m 4 40 00 0A A2 21 1 utilizes a Model 462B53 Charge Amplifier standardized at 1000 MPa/volt. The charge amplifier portion converts the high-impedance signal from a quartz, charge mode ballistic pressure sensor into a low-impedance voltage signal compatible with readout instruments. The digital ballistics charge amplifier standardizes the measuring system sensitivity by M Mo od de ell 4 40 00 0A A2 20 0 setting the sensor sensitivity on the easy-to-read digital switch. Resetting 72 72 or zeroing can be accomplished manually or remotely. Other features of this charge amplifier include an external calibration jack and a three- position discharge time constant switch for static-pressure sensor calibration. M Mo od de ell 4 45 51 1A A0 07 7 Digital Peak Meter prominently displays the peak voltage or operates in standard digital voltmeter mode. As implemented in the Model 400A20 or 400A21 Testing Monitor System, these values directly correlate to the peak pressure. Additional features of the meter include a DC offset adjustment, range switching, and manual, remote, or automatic resetting. An output jack is provided for connection to an oscilloscope or analyzer. Specify Models F400A20 or F400A21 (the system model number with an “F” prefix) for optional operation with 210 to 250 VAC power. Each of the units, Models 462B52, 462B53, and 451A07 may be purchased separately. They operate from 100 to 130 VAC power. IIN N-L LIIN NE E C CH HA AR RG GE E A AN ND D V VO OL LT TA AG GE E A AM MP PL LIIF FIIE ER RS S S Se er riie es s 4 42 22 2D D Operate with charge output sensors and constant-current signal conditioners over standard coaxial cable. Compared to expensive laboratory-style charge amplifiers, in-line models increase signal-to-noise ratio, improve resolution, simplify operation, and substantially lower cost per channel. 4 42 22 2D D1 11 1 In-line, low-noise charge converter, 100 mV/pC 4 42 22 2D D1 12 2 In-line, low-noise charge converter, 10 mV/pC 4 42 22 2D D1 13 3 In-line, low-noise charge converter, 1 mV/pC High resolution 422E Series is also available. P PC CB B P PIIE EZ ZO OT TR RO ON NIIC CS S,, IIN NC C.. 7 71 16 6-6 68 84 4-0 00 00 01 1 Signal Conditioners Signal Conditioners C CO ON NN NE EC CT TO OR R A AN ND D IIN N-L LIIN NE E V VO OL LT TA AG GE E F FO OL LL LO OW WE ER RS S The S Se er riie es s 4 40 01 1 a an nd d 4 40 02 2 act as a voltage amplifier to convert the high-impedance output from charge mode sensors to a low-impedance non-inverting voltage signal compatible with readout instruments when coupled with S Se er riie es s 4 40 02 2 ® ((P Ph ho otto o iis s ttw wo o ttiim me es s a ac cttu ua all s siiz ze e)) an ICP signal conditioner. Series 401 Impedance Converters attach directly to the 10-32 coaxial jack on To determine the sensitivity (and consequently, the range) most sensors. Series 402 Voltage Followers connect to the of the system, use the law of: sensor in line, over a short, low-noise input cable. V = Q/C, where V=Voltage Sensitivity (volts/unit) 4 40 01 1A A Impedance Converter connects to 10-32 Jack Q = Charge Sensitivity (pC/unit) 4 40 02 2A A Source follower connects in line through a C = Total capacitance of input cable, sensor, and short length of low-noise cable, converts to amplifier unit. low-impedance signal, 5pF Sensor ranging can be accomplished by adding or 4 40 02 2A A0 02 2 In-line Voltage Follower, 100 pF subtracting capacitance. 4 40 02 2A A0 03 3 In-line Voltage Follower, 1000 pF ® ® ® ® IIC CP P S SE EN NS SO OR R S SIIM MU UL LA AT TO OR R IIC CP P S SE EN NS SO OR R S SIIM MU UL LA AT TO OR R M Mo od de ell 4 40 01 1A A0 04 4 consists of a unity gain, non-inverting, Installed in place of an ICP sensor, impedance-converting voltage amplifier similar to those M Mo od de ell 4 49 92 2B B provides a total 73 73 found in many ICP sensors. When used in conjunction system calibration prior to with a signal generator, the electrical characteristics of actual testing. The unit long cables may be easily transforms an adjustable output determined. Testing long cables internal or external test signal is especially important into a simulated sensor signal when attempting to for calibrating recording systems measure microsecond or tuning long cable lines. It is response during shock structured with a square wave and blast testing. oscillator, a precision attenuator, and a line-drive amplifier like 4 40 01 1A A0 04 4 input those found in ICP sensors. 492B C CH HA AR RG GE E C CA AL LIIB BR RA AT TIIO ON N R RE EF FE ER RE EN NC CE E S SO OU UR RC CE E S SU UM MM MA AT TIIO ON N/ /D DIIF FF FE ER RE EN NT TIIA AT TIIO ON N A AM MP PL LIIF FIIE ER R M Mo od de ell 4 49 92 2B B0 03 3 provides a known charge (pC) or voltage (V) square pulse for calibrating entire measurement Working in conjunction with a PCB multi Channel Signal systems. This device incorporates a three-position voltage Conditioner and PCB pressure sensors, the M Mo od de ell selector switch (0.1, 1.0, 10 volt) and precison attenuator 4 49 90 0M M0 02 2 allows exact timing of measurements of a shock to provide an adjustable voltage pulse from 0 to 10 volts wave traveling through a shock tube. The Model 490M02 for calibrating low-impedance systems and checking long takes the output from a multichannel ICP Signal cables. Engaging high-precision capacitors Conditioner and differentiates each sensor signal (100, 1000, and 10 000pF) converts into a sharp peak. The channels are then summed the known voltage level to a charge and sent through a single output jack. The resulting signal according to: Q = VC. This consecutive sharp peaks of the pulse may then be charge signal provides a means for fed into a single channel storage scope and calibrating charge amplifiers, as well accurately measured for time. The Model 490M02 as for determining range and trigger also features a timing pulse output jack to trigger settings. The unit operates from one the scope. (Item not shown) standard 9V battery and one standard “AA” (1.5V) battery. 4 49 92 2B B0 03 3 P PR RE ES SS SU UR RE E A AN ND D F FO OR RC CE E S SE EN NS SO OR R D DIIV VIIS SIIO ON N T TO OL LL L F FR RE EE E: : 8 88 88 8-6 68 84 4-0 00 01 11 1 Sensor Kits Sensor Kits For voltage-mode sensors with built-in amplifiers For voltage-mode sensors with built-in amplifiers S SE EN NS SO OR R K KIIT TS S: : Especially for test evaluation, any voltage-mode sensor T Ty yp piic ca all K Kiitt w wiitth h S Se en ns so or r,, S Siig gn na all C Co on nd diittiio on ne er r,, C Ca ab blle es s,, with built-in amplifier can be supplied in convenient kit a an nd d A Ac cc ce es ss so or riie es s form, as illustrated. Packed in a handsome vinyl case, these kits are supplied complete with sensor, signal contains cables, power unit & conditioner, cables, adaptors and accessories ready to accessories as shown with connect to your read-out instrument and operate. specified sensor expedites ordering Sensor kits are available in a variety of choices with battery or line power, with and without built-in gain. simplifies set-up time New battery power units feature gain, higher voltage ready to operate source, 27 volt (extends battery life and dynamic range assures correct power & ® of many ICP sensors to full +10V), and an input jack for connections connecting the Model 073A05 long life (1 year) external battery pack. Options include built-in NICAD batteries and recharger 488A02. T TO O O OR RD DE ER R A A B BA AT TT TE ER RY Y-P PO OW WE ER RE ED D S SE EN NS SO OR R K KIIT T: : T TO O O OR RD DE ER R A A L LIIN NE E-P PO OW WE ER RE ED D S SE EN NS SO OR R K KIIT T: : Select the ICP voltage-model sensor of your choice. Add Select the ICP voltage-model sensor of your choice. Add prefix K, KR, GK or GKR in front of sensor model number prefix KL, GKL or DKL in front of sensor model number (eg. (eg. K102A) and add kit cost to the sensor price. Specify KL102A) and add kit cost to the sensor price. Specify input cable length if other than 10 feet, up to 50 feet input cable length if other than 10 feet, up to 50 feet supplied at no additional charge. supplied at no additional charge. 74 74 482B06, Battery-Powered Kit Line-Powered Kit (105-125 V; 50-60 Hz) for 220 V option, use prefix F BATTERY-POWER KITS LINE-POWER KITS Models: Models: K 480C02 battery power kit, unity GK 480E09 battery power kit with KL 482B06 line power kit, unity gain, DKL 484B06 Line power kit with DC gain, BNC input/output gain X1, X10, X100, BNC/BNC BNC input/output coupling, unity gain, BNC/BNC KR 480C02 rechargeable kit with GKR 480E09 rechargeable kit with GKL 482B11 line power kit with gain GDKL 484B11 line power kit with NICAD batteries and 488A02 charger NICAD batteries and 488A02 X1, X10, X100, BNC/BNC DC coupling and gain X1, X10, recharger X100, BNC/BNC C CA AB BL LE E O OR RD DE ER RIIN NG G IIN NF FO OR RM MA AT TIIO ON N: : S SIIG GN NA AL L C CO ON ND DIIT TIIO ON NE ER R K KIIT TS S: : When a signal conditioner kit is ordered, add kit Model 002C10 Input Cable, 10 foot (10-32 to BNC prefix to signal conditioner model number (eg. Plug) and 012A03 output cable, 3 foot (BNC plug to K480C02 is a signal conditioner, input cable and BNC plug) are supplied unless otherwise indicated. output cable). For applications involving sensor cable lengths greater than 100 feet, the line powered “KL” Kits are recommended because of their higher adjustable excitation current supply capacity (2 to 20mA). Refer to page 82 for information on driving long cables. P PC CB B P PIIE EZ ZO OT TR RO ON NIIC CS S,, IIN NC C.. 7 71 16 6-6 68 84 4-0 00 00 01 1 Technical Information Technical Information F Fiig gu ur re e 1 1 illustrates the cross-section of a typical quartz IIN NT TR RO OD DU UC CT TIIO ON N T TO O D DY YN NA AM MIIC C P PR RE ES SS SU UR RE E pressure sensor. This particular sensor is a General S SE EN NS SO OR RS S Purpose Series with built-in electronics. P Piie ez zo oe elle ec cttr riic c P Pr re es ss su ur re e S Se en ns so or rs s m me ea as su ur re e d dy yn na am miic c p pr re es ss su ur re es s.. T Th he ey y a ar re e g ge en ne er ra alllly y n no ott s su uiitte ed d ffo or r s stta attiic c p pr re es ss su ur re e m me ea as su ur re em me en ntts s.. D Dy yn na am miic c p pr re es ss su ur re e m me ea as su ur re em me en ntts s iin nc cllu ud diin ng g ttu ur rb bu ulle en nc ce e,, b blla as stt,, b ba alllliis sttiic cs s a an nd d e en ng giin ne e c co om mb bu us sttiio on n u un nd de er r v va ar ry yiin ng g c co on nd diittiio on ns s m ma ay y r re eq qu uiir re e s se en ns so or rs s w wiitth h s sp pe ec ciia all c ca ap pa ab biilliittiie es s.. F Fa as stt r re es sp po on ns se e,, r ru ug gg ge ed dn ne es ss s,, h hiig gh h s sttiiffffn ne es ss s,, e ex xtte en nd de ed d r ra an ng ge es s,, a an nd d tth he e a ab biilliitty y tto o a alls so o m me ea as su ur re e q qu ua as sii-s stta attiic c p pr re es ss su ur re es s a ar re e s stta an nd da ar rd d ffe ea attu ur re es s a as ss so oc ciia atte ed d w wiitth h P PC CB B q qu ua ar rttz z p pr re es ss su ur re e s se en ns so or rs s.. T Th he e ffo ollllo ow wiin ng g iin nffo or rm ma attiio on n p pr re es se en ntts s s so om me e o off tth he e d de es siig gn n a an nd d o op pe er ra attiin ng g c ch ha ar ra ac ctte er riis sttiic cs s o off P PC CB B p pr re es ss su ur re e s se en ns so or rs s tto o h he ellp p y yo ou u b be etttte er r u un nd de er rs stta an nd d h ho ow w tth he ey y ffu un nc cttiio on n,, w wh hiic ch h,, iin n ttu ur rn n,, h he ellp ps s y yo ou u m ma ak ke e b be etttte er r d dy yn na am miic c m me ea as su ur re em me en ntts s.. 75 75 T TY YP PE ES S O OF F P PR RE ES SS SU UR RE E S SE EN NS SO OR RS S This catalog describes two modes of operation for pressure sensors manufactured by PCB. Charge mode pressure sensors generate a high-impedance charge ® output. ICP (Integrated Circuit Piezoelectic) voltage mode- Diaphragm type sensors feature built-in microelectronic amplifiers, which convert the high-impedance charge into a low- Figure 1. Typical ICP Quartz Pressure Sensor impedance voltage output. (ICP is a registered trademark of PCB Piezotronics.) C CH HA AR RG GE E M MO OD DE E S SE EN NS SO OR RS S S SE EN NS SO OR R C CO ON NS ST TR RU UC CT TIIO ON N When the crystal is stressed, a charge is generated. This Piezoelectric pressure sensors are available in various high-impedance output must be routed through a special shapes and thread configurations to allow suitable low-noise cable to an impedance-converting amplifier, mounting for various types of pressure measurements. such as a laboratory charge amplifier or source follower. Quartz crystals are used in most sensors to ensure stable, High insulation resistances must be maintained in the repeatable operation. The quartz crystals are usually cables and connections. preloaded in the housings to ensure good linearity. Tourmaline, another stable naturally piezoelectric crystal, is used in some PCB sensors where volumetric sensitivity is required. P R E S S U R E A N D F O R C E S E N S O R S D I V I S I O N P PC CB B 716-684-0001 P PF FS S T To ollll F Fr re ee e 888-684-0011 F Fa ax x 716-686-9129 E Em ma aiill pfssales@pcb.com W We eb b S Siitte e www.pcb.com Technical Information Technical Information The primary function of the charge or voltage amplifier is Environmental contaminants on the connector, such as to convert the high-impedance output to a usable low- moisture, dirt, oil, or grease contribute to reduced impedance voltage signal for recording purposes. insulation, resulting in signal drift and inconsistent results. Laboratory charge amplifiers provide added versatility for Use of special low-noise cable is required with charge signal normalization, ranging, and filtering. PCB’s mode pressure sensors. Standard, two-wire, or coaxial charge amplifiers have additional input adjustments for cable, when flexed, generates a charge between the quasi-static measurements, static calibration, and drift- conductors. This is referred to as triboelectric noise and free dynamic operation. Miniature in-line amplifiers are cannot be distinguished from the sensor’s charge output. generally of fixed range and frequency. Low-noise cables have a special graphite lubricant Charge mode quartz pressure sensors may be used at between the dielectric and the braided shield, which ® higher temperatures than ICP sensors, since the minimizes the triboelectric effect and improves the quality temperature limitation is determined by the temperature of the sensor’s charge output signal. limit of the crystals (for charge mode sensors) rather ® ® than built-in electronics (for ICP sensors). IIC CP P L LO OW W-IIM MP PE ED DA AN NC CE E Q QU UA AR RT TZ Z P PR RE ES SS SU UR RE E S SE EN NS SO OR RS S When considering the use of charge mode systems, remember that the output from the crystals is a high ICP pressure sensors incorporate a built-in MOSFET impedance charge. The internal components of the microelectronic amplifier to convert the high-impedance pressure sensor and the external electrical connector charge output into a low-impedance voltage signal. An 13 maintain a very high (typically 10 e ohm) insulation ICP sensor is powered from a constant-current source and resistance. Consequently, any connectors, cables, or can operate over long coaxial or ribbon cable without amplifiers used must also have a very high insulation signal degradation. The low-impedance voltage signal is resistance to maintain signal integrity. not affected by triboelectric cable noise or insulation resistance-degrading contaminants. 76 76 Power to operate ICP sensors generally takes the form of a low-cost, 24 to 27 VDC, 2 to 20 mA constant-current supply. F Fiig gu ur re e 4 4 schematically illustrates a typical ICP sensor system. PCB offers a number of AC or battery- powered, single or multi-channel signal conditioners, with or without gain capabilities for use with pressure sensors. (See the Related Products Section of this catalog for available models). Some data acquisition systems incorporate constant-current power for directly powering ICP sensors. PCB manufactures DC coupled signal conditioners for use during static calibration or quasi- static measurement applications. Figure 2. Charge Mode System Schematic Figures 2 and 3 show a typical charge amplifier system schematic, including sensor, low-noise cable, and charge amplifier. Figure 4. ICP Sensor System Schematic Figure 3. Charge Mode System P PC CB B P PIIE EZ ZO OT TR RO ON NIIC CS S,, IIN NC C.. 7 71 16 6-6 68 84 4-0 00 00 01 1 Technical Information Technical Information H HIIG GH H F FR RE EQ QU UE EN NC CY Y R RE ES SP PO ON NS SE E ® In addition to ease of operation, ICP pressure sensors Most PCB piezoelectric pressure sensors are constructed offer advantages over charge mode types in terms of cost with either compression mode quartz crystals preloaded per channel, since multi-channel ICP signal conditioners in a rigid housing, or unconstrained tourmaline crystals. are often available for the cost of a single channel These designs give the sensors microsecond response laboratory charge amplifier. times and resonant frequencies in the hundreds of kHz, For some severe environments, use of a “hybrid” system, with minimal overshoot or ringing. Small diaphragm using a charge mode pressure sensor in conjunction with an diameters ensure spatial resolution of narrow shockwaves. in-line miniature charge or voltage amplifier and an ICP High-frequency response and rise time can be affected by signal conditioner, can still offer cost savings. F Fiig gu ur re e 5 5 mounting port geometry and associated electronics. shows various complete two-wire system configuration. (Limitations of driving long cables at high frequencies are discussed on page 82). Check all system component specifications before making measurements, or contact PCB for application assistance. W WH HY Y O ON NL LY Y D DY YN NA AM MIIC C P PR RE ES SS SU UR RE E C CA AN N B BE E M ME EA AS SU UR RE ED D W WIIT TH H P PIIE EZ ZO OE EL LE EC CT TR RIIC C P PR RE ES SS SU UR RE E S SE EN NS SO OR RS S The quartz crystals of a piezoelectric pressure sensor generate a charge when pressure is applied. However, even though the electrical insulation resistance is quite large, the charge eventually leaks to zero. The rate at which the charge leaks back to zero is dependent on the electrical insulation resistance. 77 77 In a charge mode pressure sensor used with a voltage amplifier, the leakage rate is fixed by values of capacitance and resistance in the sensor, by low-noise cable, and by the external source follower voltage amplifier used. In the case of a charge mode pressure sensor used with a charge amplifier, the leakage rate is fixed by the electrical feedback resistor and capacitor in the charge amplifier. In a pressure sensor with built-in ICP electronics, the resistance and capacitance of the crystal and the built-in ICP electronics normally determine the leakage rate. D DIIS SC CH HA AR RG GE E T TIIM ME E C CO ON NS ST TA AN NT T ((D DT TC C)) When leakage of a charge (or voltage) occurs in a Figure 5. Typical Sensor Systems resistive-capacitive circuit, the leakage follows an exponential decay. A piezoelectric pressure sensor system behaves similarly. The value of the electrical capacitance of the system (in farads) multiplied by the P PO OL LA AR RIIT TY Y value of the electrical resistance (in ohms) is called the Discharge Time Constant (in seconds). When a positive pressure is applied to an ICP pressure sensor, the sensor yields a positive voltage. The polarity of DTC is defined as the time required for a sensor or measuring system to discharge its signal to 37% of the PCB charge mode pressure sensors is just the opposite: when a positive pressure is applied, the sensor yields a original value from a step change of measure. The DTC of a system relates to the low-frequency monitoring negative output. Charge output sensors are usually used with external charge amplifiers that invert the signal. capabilities of a system. A long discharge time constant is useful because it allows quasi-static operation during Therefore, the resulting system output polarity of a charge output sensor used with a charge amplifier will produce an calibration or measurement of certain long-duration pressure pulses. output that is the same as an ICP sensor. (Reverse polarity sensors are also available.) P PR RE ES SS SU UR RE E A AN ND D F FO OR RC CE E S SE EN NS SO OR R D DIIV VIIS SIIO ON N T TO OL LL L F FR RE EE E: : 8 88 88 8-6 68 84 4-0 00 01 11 1 Technical Information Technical Information D DT TC C C CH HA AR RG GE E M MO OD DE E S SY YS ST TE EM M In a charge mode system, the DTC is usually determined by the settings on an external charge amplifier. PCB Series 460 Charge Amplifiers feature a short, medium, and long time constant switch from which DTC is selected. It is assumed that the electrical insulation resistance is large; otherwise, drift occurs. Therefore, to minimize this drift, the pressure sensor connection point and cable must be kept clean and dry. ® ® L LO OW W-F FR RE EQ QU UE EN NC CY Y R RE ES SP PO ON NS SE E O OF F IIC CP P S SY YS ST TE EM MS S ® With ICP sensors, there are three factors that must be considered when making low-frequency measurements. These are: Figure 6. Piezoelectric Signal Exponential Decay 1. The discharge time constant characteristic of the pressure sensor. The product of R and C represents the DTC (in seconds) of 2. The discharge time constant of the AC coupling the sensor. Sensor time constants vary from just a few circuit used in the signal conditioner with the seconds to >2000 seconds for standard sensors. Special readout instrument. (If DC coupling is used, only time constants can be supplied by altering the resistor the above [1] needs to be considered.) value, R, in the sensor’s built-in microelectronic amplifier. 3. ICP signal conditioner. S SE EN NS SO OR R/ /S SY YS ST TE EM M T TIIM ME E C CO ON NS ST TA AN NT T It is important that all factors be readily understood by the It is important to determine the discharge time constant 78 78 user to assure accurate low-frequency measurements. (DTC) of an ICP sensor system, as the DTC determines the ® ® system’s low-frequency response. The DTC of a sensor D DT TC C IIN N IIC CP P P PR RE ES SS SU UR RE E S SE EN NS SO OR RS S system is usually dominated by the shortest DTC of either In PCB pressure sensors featuring built-in ICP electronics, the sensor or signal conditioner. the discharge time constant of the sensor is set at a fixed The sensor DTC is fixed and is specified in this catalog for value by the built-in circuit. Specifications for the ICP each sensor. In ICP signal conditioners featuring internal pressure sensors shown in this catalog list the DTC for buffer amplifiers, the DTC is fixed by various internal each pressure sensor. components and is not affected by the input impedance of When an ICP sensor is subjected to a step function input, the readout instrument. PCB signal conditioners with a quantity of charge, Δq, is produced proportional to the capacitively coupled outputs have a DTC fixed by a mechanical input. Output voltage is ΔV = Δq/C where C shunting resistor across the capacitor. This fixes the DTC is the total capacitance of the sensing element, amplifier, in the signal conditioner (usually at 10 seconds), unless and ranging capacitor. This voltage is then amplified by the input impedance of the readout instrument is less than the MOSFET amplifier to determine final sensor sensitivity. 1 megaohm. If the input impedance of the readout is less After the initial step input, the charge signal decays than 1 megaohm, the DTC is shortened. ((-tt/ /R RC C)) q q = = Q Qe e according to the equation where: After determining the shortest DTC in the system, the value q = instantaneous charge (pC) can be used to determine the low frequency cutoff of the Q = initial quantity of charge (pC) sensor system. The system time constant is analogous to R = bias resistor value (ohms) a first order high pass RC filter. The theoretical lower- C = total capacitance (pF) corner cutoff frequency (fc) is illustrated in F Fiig gu ur re e 7 7 and is t = time after t o calculated from the following relationships: e = base of natural log (2.718) 3 dB down: fc = 0.16/DTC The equation used to determine signal decay is 10% down: fc = 0.34/DTC F Fiig gu ur re e 6 6 graphically represented in : 5% down: fc = 0.5/DTC P PC CB B P PIIE EZ ZO OT TR RO ON NIIC CS S,, IIN NC C.. 7 71 16 6-6 68 84 4-0 00 00 01 1 Charge Technical Information Technical Information Left unchanged, the signal naturally decays toward zero. Decay back to zero (or baseline) takes approximately 5 DTC. Notice that after the original step impulse signal is removed, the output signal dips below the base line reference point (t + .01 TC). This negative value is the o same value as that which has decayed from the original impulse. Further observation reveals that the signal, left untouched, decays upwards toward zero until equilibrium in the system is achieved. T TY YP PIIC CA AL L P PIIE EZ ZO OE EL LE EC CT TR RIIC C S SY YS ST TE EM M O OU UT TP PU UT T The output characteristic of piezoelectric pressure sensor Figure 7. Transfer Characteristics of an ICP Sensor systems is that of an AC-coupled system, where repetitive signals decay until there is an equal area above and below the original base line. As magnitude levels of the L LO ON NG G D DU UR RA AT TIIO ON N E EV VE EN NT TS S A AN ND D D DT TC C monitored event fluctuate, the output remains stabilized It is sometimes desirable to measure a pressure lasting a around the base line with the positive and negative areas few seconds in duration. This is especially true with high of the curve remaining equal. F Fiig gu ur re e 9 9 represents an AC pressure sensor applications where static calibration takes signal following this curve. (Output from sensors place. (Before performing tests of this nature, it is operating in DC mode follow this same pattern but over important to DC-couple the entire monitoring system to an extended time frame associated with system discharge prevent rapid signal loss. PCB Series 484 Signal time constant values.) Conditioners have AC and DC coupling modes of operation and are designed for such applications). 79 79 The general rule of thumb for such measurements is that the output signal loss and time elapsed over the first 10% of a DTC have a one-to-one relationship. If a sensor has Figure 9. Repetitive Pulse, AC Signal a 500 second DTC, over the first 50 seconds, 10% of the original input signal decays. For 1% accuracy, data should be taken in the first 1% of the DTC. If 8% accuracy For example, assume that a 0 to 2 volt output signal is is acceptable, the measurement should be taken within generated from an AC-coupled pressure application with 8% of the DTC, and so forth. F Fiig gu ur re e 8 8 graphically a one-second steady-state pulse rate and one second demonstrates this event. between pulses. The frequency remains constant, but the signal quickly decays negatively until the signal centers around the original base line (where area A = area B). Peak to peak output remains the same. IIN NS ST TA AL LL LA AT TIIO ON N Precision mounting of pressure sensors is essential for good pressure measurements. Although some mounting information is shown in this catalog, always check the installation drawings supplied in the manual with the sensor, or contact PCB to request detailed mounting instructions. Use good machining practices for the drilling and threading of mounting ports, and torque the sensors to the noted values. Mounting hardware is supplied with PCB sensors. Various standard thread adaptors are available to simplify some sensor installations. For free field blast applications, try to use Figure 8. Step Function Response “aerodynamically clean” mounts, minimizing unwanted reflections from mounting brackets or tripods. P PR RE ES SS SU UR RE E A AN ND D F FO OR RC CE E S SE EN NS SO OR R D DIIV VIIS SIIO ON N T TO OL LL L F FR RE EE E: : 8 88 88 8-6 68 84 4-0 00 01 11 1 Output dB Technical Information Technical Information The sensing crystals of many pressure sensors described in this catalog are located in the diaphragm end of the sensor. Side loading of this part of the sensor during a pressure measurement creates distortions in the signal output. See F Fiig gu ur re e 1 10 0.. Figure 11. Typical Recess Mount Consider ordering enough spare seal rings or sleeves, particularly in applications that require frequent removal and reinstallation of the pressure sensor. Before reinstalling a pressure sensor, be sure to check the mounting port to be sure that an old, distorted seal ring is 80 80 not still in the mounting hole. If you are using PCB Figure 10. Flush Mount Pressure Alignment pressure sensors and find that you have lost or misplaced the seals, call PCB and request that the needed items be Also important is the avoidance of unusual side loading sent out as no-charge samples. stresses and strains on the upper body of the sensor. In this catalog, various mounting adaptors are described Proper installation minimizes distortions in the output that often facilitate mounting of the pressure sensors. See signal. A taut cable pulling at right angles to the pages 58 to 60 for details. Note that pressure sensors electrical connector is an example of putting a side strain and adaptors with straight machined threads use a seal into the body. Another is the use of a heavy adaptor with ring as a pressure seal. Pipe thread adaptors have a cable attached to the small electrical connector in an tapered thread, which results in the threads themselves environment with high transverse vibration. creating the pressure seal. In some types of applications, such as free-field blast Control of the location of the pressure sensor diaphragm measurements, a pressure sensor mounted in a thin plate is achieved with a straight thread/seal ring mount. Pipe can be subjected to side loading stresses when the thread mounts do not allow a precision positioning of the pressure causes the plate to flex. Use of an O-ring mount depth of the sensor since the seal is provided by minimizes this effect. progressive tightening of threads in the tapered hole until F FL LU US SH H V VS S.. R RE EC CE ES SS S M MO OU UN NT TIIN NG G the required thread engagement is reached. However, Flush mounting of pressure sensors in a plate or wall is pipe threads do offer a convenience of an easier sometimes desirable for minimizing turbulence, avoiding machined port than straight threads. Pipe thread mounts a cavity effect, or avoiding an increase in a chamber are well suited for some general applications. volume. Recess mounting is more desirable in T TH HE ER RM MA AL L S SH HO OC CK K applications where the diaphragm end of the pressure Automotive in-cylinder pressures, ballistic pressures, and sensor is likely to be subjected to excessive flash free-field blasts are a few examples of applications that temperatures or particle impingement. have a thermal shock accompanying the pressure pulse. Most PCB pressure sensors are supplied with seal rings The thermal shock can be in the form of a radiant heat, for flush mounting. Certain models, such as Series 111, such as the flash from an explosion, heat from convection 112, and 113 can be provided with seal sleeves for of hot gasses passing over a pressure sensor’s diaphragm, recess mounting ports. Request seal sleeves when or conductive heat from a hot liquid. ordering. P PC CB B P PIIE EZ ZO OT TR RO ON NIIC CS S,, IIN NC C.. 7 71 16 6-6 68 84 4-0 00 00 01 1 Technical Information Technical Information Virtually all pressure sensors are sensitive to thermal shock. When heat strikes the diaphragm of a piezoelectric pressure sensor that has crystals contained in an outer housing, the heat can cause an expansion of the case surrounding the internal crystals. Although quartz crystals are not significantly sensitive to thermal shock, the case expansion causes a lessening of the preload force on the crystals, usually causing a negative- signal output. To minimize this effect, various methods are used. Certain PCB quartz pressure sensors feature internal thermal isolation designs to minimize the effects of thermal shock. Some feature baffled diaphragms. Other models designed for maximizing the frequency response may require thermal protection coating, recess mounting, or a combination to lessen the effects of thermal shock. Examples of coatings include silicone grease, which may also be used to fill a recess mounting hole, RTV silicone rubber, vinyl electrical tape, and ceramic coatings. The RTV and tape are used as ablatives, while the ceramic coating is also used to protect some diaphragms from corrosive gasses and particle impingements. 81 81 Crystals other than quartz are used in some PCB sensors. Though sensitive to thermal shock, tourmaline is used for shock tube and underwater blast sensors. In shock tube measurements, the duration of the pressure measurement is usually so short that a layer of vinyl tape is sufficient to delay the thermal effects for the duration of the measurement. In underwater blast applications, heat transfer through the water is not significant. Note that thermal shock effects do not relate to the pressure sensor specification called “temperature coefficient” used in this catalog. The temperature coefficient specification refers to the change in sensitivity of the sensor relative to the static temperature of the sensor. Unfortunately, since the thermal shock effects cannot be easily quantified, they must be anticipated and minimized by one of the above mentioned techniques in order to ensure better measurement data. P PR RE ES SS SU UR RE E A AN ND D F FO OR RC CE E S SE EN NS SO OR R D DIIV VIIS SIIO ON N T TO OL LL L F FR RE EE E: : 8 88 88 8-6 68 84 4-0 00 01 11 1 Cable Driving Cable Driving C CA AB BL LE E C CO ON NS SIID DE ER RA AT TIIO ON NS S A AN ND D C CO ON NS ST TA AN NT T maximum output range of 5 volts and the constant current C CU UR RR RE EN NT T L LE EV VE EL L signal conditioner is set at 2 mA, the ratio on the vertical axis can be calculated to equal 5. The intersection of the total Operation over long cables may affect frequency response cable capacitance and this ratio result in a maximum and introduce noise and distortion when an insufficient frequency of approximately 10.2 kHz. current is available to drive cable capacitance. The nomograph does not indicate whether the frequency Unlike charge mode systems, where the system noise is a ® amplitude response at a point is flat, rising or falling. For function of cable length, ICP sensors provide a high voltage, precautionary reasons, it is good general practice to increase low impedance output well-suited for driving long cables the constant current (if possible) to the sensor (within its through harsh environments. While there is virtually no maximum limit) so that the frequency determined from the increase in noise with ICP sensors, the capacitive loading of nomograph is approximatley 1.5 to 2 times greater than the the cable may distort or filter higher frequency signals maximum frequency of interest. depending on the supply current and the output impedance of the sensor. Note that higher current levels will deplete battery-powered signal conditioners at a faster rate. Also, any current not used ® by the cable goes directly to power the internal electronics ICP Pressure and will create heat. This may cause the sensor to exceed its Long Extension Cable Sensor maximum temperature specification. For this reason, do not with Standard Connectors supply excessive current over short cable runs or when testing BNC at elevated temperatures. E EX XP PE ER RIIM ME EN NT TA AL LL LY Y T TE ES ST TIIN NG G L LO ON NG G C CA AB BL LE ES S To more accurately determine the effect of long cables, it is Power Readout Unit recommended to experimentally determine the high Short Adaptor Cable (1m) frequency electrical characteristics. Figure 12 Long Extension Cable Schematic F Fiig gu ur re e 1 13 3 The method illustrated in involves connecting the output from a standard signal generator into a unity gain, low-output impedance (<5 ohm) instrumentation amplifier in Generally, this signal distortion is not a problem with lower series with the ICP sensor. The extremely low output 82 82 frequency testing within a range up to 10 000 Hz. However, impedance is required to minimize the resistance change for higher frequency vibration, shock or transient testing over when the signal generator/amplifier is removed from the cables longer than 100 ft. (30 m.), the possibility of signal system. distortion exists. The maximum frequency that can be transmitted over a given 073A cable length is a function of both the cable capacitance and the ratio of the peak signal voltage to the current available from the signal conditioner according to: 9 f = 10 max 2πCV / (I -1) c where, f = maximum frequency (hertz) max C= cable capacitance (picofarads) V= maximum peak output from sensor (volts) I = constant current from signal conditioner (mA) Figure 13 Long Cable Testing c 9 10 = scaling factor to equate units In order to check the frequency/amplitude response of this Note that in this equation, 1 mA is subtracted from the total system, set the signal generator to supply the maximum current supplied to sensor (I ). This is done to compensate for c amplitude of the expected measurement signal. Observe the powering the internal electronics. Some specialty sensor ratio of the amplitude from the generator to that shown on the electronics may consume more or less current. Contact the scope. If this ratio is 1:1, the system is adequate for your test. manufacturer to determine the correct supply current. (If necessary, be certain to factor in any gain in the signal When driving long cables, the equation above shows that as conditioner or scope.) If the output signal is rising the length of cable, peak voltage output or maximum (1:1.3 for example), add series resistance to attenuate the frequency of interest increases, a greater constant current will signal. Use of a variable 100 ohm resistor will help set the be required to drive the signal. correct resistance more conveniently. Note that this is the only The nomograph on the facing page provides a simple, condition that requires the addition of resistance. If the signal graphical method for obtaining the expected maximum is falling (1:0.75 for example), the constant current level must frequency capability of an ICP measurement system. The be increased or the cable capacitance reduced. maximum peak signal voltage amplitude, cable capacitance It may be necessary to physically install the cable during and supplied constant current must be known or presumed. cable testing to reflect the actual conditions encountered For example, when running a 100 ft. cable with a during data acquisition. This will compensate for potential capacitance of 30 pF/ft, the total capacitance is 3000 pF. inductive cable effects that are partially a function of the This value can be found along the diagonal cable geometry of the cable route. capacitance lines. Assuming the sensor operates at a P PC CB B P PIIE EZ ZO OT TR RO ON NIIC CS S,, IIN NC C.. 7 71 16 6-6 68 84 4-0 00 00 01 1 Cable Driving Cable Driving V I - 1 c (Ratio of Maximum Output Voltage from Sensor to Available 83 Constant Current) 83 F Fr re eq qu ue en nc cy y ((H Hz z)) fmax = Maximum frequency given the following characteristics C= Cable capacitance (pF) I = Constant current level from power unit (mA) c 9 V= Maximum output voltage from sensor (volts) 10 = Scale factor to equate units P PR RE ES SS SU UR RE E A AN ND D F FO OR RC CE E S SE EN NS SO OR R D DIIV VIIS SIIO ON N T TO OL LL L F FR RE EE E: : 8 88 88 8-6 68 84 4-0 00 01 11 1 Article Reprints Article Reprints T To o o or rd de er r c co op piie es s o off tth he e ffo ollllo ow wiin ng g a ar rttiic clle es s,, s siim mp plly y r re eq qu ue es stt tth he e “ “A AR R” ” n nu um mb be er r p pr re ec ce ed diin ng g e ea ac ch h a ar rttiic clle e; ; jju us stt w wr riitte e o or r c ca allll tth he e M Ma ar rk ke ettiin ng g D De ep pa ar rttm me en ntt a att: : 7 71 16 6-6 68 84 4-0 00 00 01 1.. A AR R-1 1 A Ap pp plliic ca attiio on n o off IIn ntte eg gr ra atte ed d-C Ciir rc cu uiitts s tto o P Piie ez zo oe elle ec cttr riic c S Se en ns so or rs s,, P Pa ap pe er r P P4 4-2 2 P PH HY YM MIID D 6 67 7.. ® ICP Sensor - Basic operation & application/Cornell Aeronautical Lab, Robert Lally, 1967. ® ® A AR R-2 2 IIC CP P C Co on nc ce ep ptt Integrated-Circuit Piezoelectric. Low impedance, voltage mode system, PCB, 1967. A AR R-3 3 P Piie ez zo oe elle ec cttr riic c A An na allo og giie es s Electrostatic vs. hydrostatic system. Piezoelectric vs. hydraulic circuit, Robert Lally, 1967. ® ® A AR R-4 4 G Gu uiid de e tto o IIC CP P IIn ns sttr ru um me en ntta attiio on n Voltage vs. charge systems. Effect of coupling & time constant on response. Powering ICP system, Robert Lally, 1971. A AR R-5 5 C Co on nffo or rm ma all B Ba alllliis sttiic c S Se en ns so or rs s Model 117A Pressure Sensor/Calibration System (Model 090A); Report presented to Frankford Arsenal Meeting of NATO, PCB, 1971. A AR R-1 11 1 T Tr ra an ns sd du uc cttiio on n The effect of sensor mass and/or stiffness on the quantity being measured, Robert Lally, 1982. A AR R-1 12 2 P Pr re es ss su ur re e M Me ea as su ur re em me en ntts s ffo or r 9 9m mm m P Piis stto oll A Am mm mu un niittiio on n Model 117B Conformal Ballistic Sensor/Test results vs Kistler 6203 (only PCB 117B able to measure correct pressure values); Nobel Chemicals Division Report, Sven-Eric Johansson, 1983. A AR R-1 18 8 IIn nttr ro od du uc cttiio on n tto o P Piie ez zo oe elle ec cttr riic c S Se en ns so or rs s Basic accelerometer, pressure, and force sensor design considerations & typical applications, Jim Lally, 1985. A AR R-1 19 9 C Ca alliib br ra attiio on n o off P Piie ez zo o S Se en ns so or rs s 84 84 Calibration systems for dynamic pressure sensors, force sensors and accelerometers with typical calibration results, Jim Lally, 1985. A AR R-2 25 5 E Elle ec cttr riic ca all IIs so olla attiio on n o off U Un nd de er rw wa atte er r E Ex xp pllo os siio on n S Se en ns so or rs s Model 138 Blast Sensor Modified (completely shielded); ISA Transactions, BW Vanzant, GK Wolfe, GL Roark, D Jaros (PCB), 1987. A AR R-2 26 6 M Me ea an n & & F Fllu uc cttu ua attiin ng g P Pr re es ss su ur re e M Me ea as su ur re em me en ntts s B Be en ne ea atth h IIm mp piin ng giin ng g T Tu ur rb bu ulle en ntt J Je etts s Model 112A21, Pressure Sensor, 483A Peak Meter, ISA Transaction, MR Wells, 1987. A AR R-3 30 0 P Piie ez zo oe elle ec cttr riic c P Pr re es ss su ur re e S Se en ns so or rs s Acceleration compensated pressure sensor, Measurements & Control, Jim Lally (PCB), 1987. A AR R-3 34 4 H Ho ott/ /C Co olld d A Am mm mo o PCB 118A Pressure Sensor/ Test of ammunition, Guns & Ammo, Bob Forker, 1988. A AR R-3 35 5 F Fr re eq qu ue en nc cy y R Re es sp po on ns se e C Co on ns siid de er ra attiio on ns s ffo or r P Piie ez zo oe elle ec cttr riic c S Se en ns so or rs s a an nd d R Re ella atte ed d IIn ns sttr ru um me en ntts s Time constant and AC coupling or DC coupling effects on frequency response. Time constant vs, shock pulse input duration, PCB, Ray Limburg (PCB), 1988. A AR R-3 38 8 B Ba as siic cs s o off P Piie ez zo oe elle ec cttr riic c S Se en ns so or rs s ICP Sensor features. Upright, Inverted Compression, Shear Mode Sensors, Roy Maines (Reliable Measurements), 1989. A AR R-4 43 3 T Tr ro ou ub blle e w wiitth h C Ca ab blle es s Cables for voltage & charge mode systems. Cable management system, Test, Jim Lally, 1990. A AR R-4 46 6 R Re effe er re en nc ce e S Stta an nd da ar rd ds s: : T Th he er re e iis s S Sttiillll a a N Ne ee ed d ffo or r D Dy yn na am miic c P Pr re es ss su ur re e T Tr ra ac ce ea ab biilliitty y.. Pressure step generator, shock tube techniques to calibrate pressure sensors, Measurements & Control, MT Riggs (PCB), 1990. A AR R-5 51 1 D Dy yn na am miic c S Stte ep p-P Pr re es ss su ur re e C Ca alliib br ra attiio on n 913A Impulse Calibrator, 901A10 shock tube, 907A pressure-step-generator - Comprehensive calibration for pressure sensor 113A24. A AR R-5 53 3 G Gu uiid de elliin ne e ffo or r IIn ntte er rn na all C Co om mb bu us sttiio on n E En ng giin ne e P Pr re es ss su ur re e M Me ea as su ur re em me en ntts s ICP and charge type sensors from PCB for various mounting choices and engine types. Typical installations included, Jim Lally, 1992. A AR R-5 59 9 R Re ec co om mm me en nd de ed d P Pr ra ac cttiic ce es s: : A Ac cc ce elle er ro om me ette er r,, W Wiir riin ng g a an nd d C Co on nn ne ec cttiio on ns s Reliability of ICP, charge mode systems based upon selection of cables and connectors/long cable use with cable drive nomograph. A AR R-6 60 0 D Dy yn na am miic c P Pr re es ss su ur re e C Ca alliib br ra attiio on n iin ns sttr ru um me en ntts s a an nd d S Se en ns so or r T Tr ra an ns siie en ntt R Re es sp po on ns se e Surveys commercially available dynamic calibration instruments. Proceedings: 17th Sensor Workshop, San Diego CA, Jim Lally, 1993. P PC CB B P PIIE EZ ZO OT TR RO ON NIIC CS S,, IIN NC C.. 7 71 16 6-6 68 84 4-0 00 00 01 1 Glossary of Terms Glossary of Terms As relates to PCB Piezo Pressure Sensors As relates to PCB Piezo Pressure Sensors A Ab bs so ollu utte e P Pr re es ss su ur re e - Pressure measured relative to absolute vacuum. D Diia ap ph hr ra ag gm m - The sensing membrane of a sensor that transmits pres- sure to the sensing element. A Ac cc ce elle er ra attiio on n C Co om mp pe en ns sa attiio on n - An added internal crystal element technique that reduces the sensitivity of a pressure sensor to D Diig giitta all O Ou uttp pu utt - Providing a readout in numerical digits. vibration and shock. D Diis sc ch ha ar rg ge e T Tiim me e C Co on ns stta an ntt ((D DT TC C)) - Time required for a sensor or A Ac cc ce elle er ra attiio on n S Se en ns siittiiv viitty y - The output of a pressure sensor due to measuring system to discharge its signal to 37% of the original vibration or shock. Typically measured in psi/g. value following a step change of measurand. The discharge time constant directly relates to the low-frequency measuring A Am mb biie en ntt N No oiis se e - The total background noise level in a specified capability for both transient and sinusoidal events (should not be environment. confused with rise time or time constant). A An na allo og g O Ou uttp pu utt - The continuous real time output of a piezoelectric D Du ua all M Mo od de e C Ch ha ar rg ge e A Am mp plliiffiie er r - An amplifier that can be used with sensor or instrument within its specified dynamic range. either high-impedance charge mode sensors or low-impedance A Am mb biie en ntt P Pr re es ss su ur re e - The total pressure level in a specified ICP voltage mode sensors. environment. D Dy yn na am miic c C Ca alliib br ra attiio on n - Applying a known step input to a pressure A Atttte en nu ua attiio on n - The effect of reducing signal sensitivity. sensor, usually in milliseconds or microseconds. ® B Biia as s V Vo olltta ag ge e - A DC voltage at the output of an ICP -type sensor E Elle ec cttr ro o-M Ma ag gn ne ettiic c IIn ntte er rffe er re en nc ce e ((E EM MII)) - A condition in which an on which an AC measurement signal is superimposed. electromagnetic field produces an unwanted noise. C Ca alliib br ra attiio on n - The process of measuring and documenting a sensor’s F FF FT T A An na ally yz ze er r - Frequency Spectrum Analyzer computes discrete sensitivity relative to a known input. Data is usually taken at several frequency components as a function of frequency from sampled points to plot linearity. time data. C Ca av viitta attiio on n - The sudden formation and collapse of small pressure F Fiilltte er r - A mechanical or electrical device designed to pass or reject bubbles in liquids. a specific frequency band. C Ch ha ar rg ge e A Am mp plliiffiie er r - A capacitive feedback amplifier that converts F Flla as sh h T Te em mp pe er ra attu ur re e - Refers to the fast (usually lasting no longer the high-impedance output from a charge mode sensor to a than a few milliseconds) temperature change associated with low-impedance voltage signal. explosive combustion, detonation, blast, or shock wave 85 85 measurements. Sensors usually require ablative coating on the C Ch ha ar rg ge e C Co on nv ve er rtte er r - A charge converter is a small, in-line amplifier diaphragm to reduce flash temperature sensitivity. that is used in close proximity to the sensor to convert the high- impedance output of a charge mode sensor into a low- F Fllu us sh h M Mo ou un ntt - A sensor mounting technique where the diaphragm impedance voltage signal (mV/pC), usually at fixed gain. of the sensor is installed flush with the inside surface of the test chamber. C Ch ha ar rg ge e M Mo od de e - A piezoelectric sensor that outputs a high- impedance charge signal (pC). F Fr re ee e F Fiie elld d B Blla as stt - Measurement of a shock wave in an open area. C Ch ha ar rg ge e S Se en ns siittiiv viitty y - The amount of charge produced by a charge F Fr re eq qu ue en nc cy y R Re es sp po on ns se e - The amplitude ratios of output-to-input mode sensor per unit of pressure; expressed in pC/psi (pico signals and the phase relationships at different frequencies. coulomb per psi). F Fr re eq qu ue en nc cy y-T Ta aiillo or re ed d R Re es sp po on ns se e - A combination of mechanical and C Clla am mp pe ed d O Ou uttp pu utt - Output automatically re-zeroed between electrical damping in Series 113A20 and certain Series 102 repetitive events; keeps signal ground-based, positive-going. (500kHz) pressure sensors to produce a non-resonant response. C Clliip pp piin ng g - Output limitation preventing a signal amplitude from G Ga au ug ge e P Pr re es ss su ur re e - A pressure measurement that is referenced exceeding the limits imposed by the amplifier, supply voltage, relative to atmospheric pressure. Most piezo sensors measure or system. gauge pressure. C Co on nffo or rm ma all B Ba alllliis sttiic c S Se en ns so or r - A pressure sensor with a curved G Gr ro ou un nd d IIs so olla attiio on n - Refers to a condition where a sensor’s signal diaphragm machined to conform to the chamber diameter of the ground is electrically isolated from the test structure. gun. It measures pressure directly, through an unmodified G Gr ro ou un nd d L Lo oo op p - A condition where sensor and signal shell case. conditioner/readout grounds are of different electrical potential. C Co on ns stta an ntt C Cu ur rr re en ntt - Electric current independent of either voltage or Such conditions cause ground loop “noise” at frequencies resistances and fixed at a specific value. Also called excitation typically between 50 and 60 Hz, as well as multiples thereof. current for ICP sensors. Constant current is provided by all PCB H He er rttz z ((H Hz z)) - One cycle or oscillation per second. power and amplifying power units, as well as vibration and ® ® digital peak meters (required for proper ICP sensor operation). IIC CP P ((IIn ntte eg gr ra atte ed d C Ciir rc cu uiitt P Piie ez zo oe elle ec cttr riic c)) - A trademark identifying PCB Some commercial FFT analyzers and data collectors also provide voltage mode sensors combining an integrated circuit and a constant current for ICP sensors. piezoelectric sensing element in a single housing to provide a voltage output. Also referred to as “voltage mode sensor.” ICP D De ec ciib be ell ((d dB B))- A logarithmic representation of a ratio, expressed as is a registered trademark of PCB Piezotronics, Inc. 10 times the log of a power ratio or 20 times the log of a voltage, current or units (pressure, force, acceleration) ratio. IIm mp pe ed da an nc ce e C Co on nv ve er rtte er r - See Charge Amplifier, Charge Converter, and Source Follower. D Diiffffe er re en nttiia all P Pr re es ss su ur re e - The difference in pressure between two measurements. P PR RE ES SS SU UR RE E A AN ND D F FO OR RC CE E S SE EN NS SO OR R D DIIV VIIS SIIO ON N T TO OL LL L F FR RE EE E: : 8 88 88 8-6 68 84 4-0 00 01 11 1 Glossary of Terms Glossary of Terms As relates to PCB Piezo Pressure Sensors As relates to PCB Piezo Pressure Sensors IIn n-lliin ne e C Ch ha ar rg ge e C Co on nv ve er rtte er r - See Charge Converter. R Re ep pe ea atta ab biilliitty y - The ability of a sensor to provide the same output signal corresponding to the same measurand input under the IIn nc ciid de en ntt S Sh ho oc ck k W Wa av ve e M Me ea as su ur re em me en ntt - A shock wave traveling same environmental conditions. across the sensor’s diaphragm, 90° to the sensitive axis. R Re es so ollu uttiio on n - The smallest discernible signal from a measurement IIn ns su ulla attiio on n R Re es siis stta an nc ce e - The resistance in ohms between signal and system; also referred to as threshold. ground of a sensor or cable. R Re es so on na an ntt F Fr re eq qu ue en nc cy y - Frequency where a structure readily vibrates M Me ea as su ur ra an nd d - Physical quantity being measured, such as pressure at its natural frequency. psi or kPa. R Riis se e T Tiim me e - Time required for output of a pressure sensor to rise N NIIS ST T (National Institute of Standards and Technology) - Formerly from 10% to 90% of its final value when subjected to a step NBS (National Bureau of Standards), a U.S. national standards input. lab that provides certification for calibration reference standards. S Sh ho oc ck k W Wa av ve e - Pressure wave exceeding the speed of sound in gas, solid, or liquid medium. N No oiis se e - Any signal in a measurement system other than the signal generated by the measurand. Noise sources include EMI, RFI, S Siig gn na all C Co on nd diittiio on niin ng g/ /P Po ow we er r U Un niitt - A power source that supplies ® triboelectric, and geophysical phenomena. constant current to ICP sensors and removes the bias voltage (may also amplify, attenuate, filter, or normalize.) N No on n-R Re es so on na an ntt R Re es sp po on ns se e - See Frequency-Tailored Response. ® S Siig gn na all-tto o-N No oiis se e R Ra attiio o - A sensor’s output signal relative to its O Ou uttp pu utt B Biia as s V Vo olltta ag ge e - A DC voltage at the output of an ICP output noise. sensor on which the signal is superimposed. S So ou ur rc ce e F Fo ollllo ow we er r - Converts a high-impedance input signal to a low- P PC CB B - Taken from the word Pico Coulomb, a quantity of electrical -12 impedance voltage output. Also referred to as Impedance charge. (one Pico Coulomb is equal to 1 x 10 coulomb). Converter, generally a voltage gain of one. P Pe ea ak k M Me ette er r - An instrument that records a peak pulse or highest S Stta an nd da ar rd diiz ze ed d S Se en ns siittiiv viitty y - Refers to standardization (or peak in a pulse train. normalization) of sensor output to a specified value and 86 86 P Ph ha as se e - Time relationship of an event to some reference. tolerance (e.g., 10 mV/psi ± 2%). P Ph ha as se e S Sh hiifftt - The difference in phase angle between the output and S Stta attiic c C Ca alliib br ra attiio on n - Calibration using dead weights as a pressure input; typically, a function of frequency. reference source. -12 P Piic co o C Co ou ullo om mb b - A measure of charge; equal to 1 x 10 S Stta attiic c P Pr re es ss su ur re e - Steady state or slowly changing pressure, normally coulombs. measured with strain gauge or other DC-measuring instruments. P Piie ez zo ottr ro on niic cs s - Combining the piezoelectric properties of a crystal T Te em mp pe er ra attu ur re e C Co oe effffiic ciie en ntt - The percent change in the sensitivity of a with the science of electronics. sensor as a result of a unit change in the operating temperature P Po olla ar riitty y - The positive or negative output from a sensor of the sensor; expressed as percent per degree (i.e., %/°F or compared to that of the measurand: i.e., positive-going output %/°C). for increasing pressure. Charge mode sensors usually have T Tr riib bo oe elle ec cttr riic c N No oiis se e - A charge-generated noise caused by friction in negative output which is inverted to positive output by a charge a cable. A common source of this noise is the separation and amplifier. motion between the dielectric and shield of a cable. P Py yr ro oe elle ec cttr riic c O Ou uttp pu utt - Unwanted thermally generated output from a T Tu ur rb bu ulle en nc ce e - The motion of a fluid having local velocities and piezoelectric crystal due to a varying thermal input. pressures that fluctuate randomly. Q Qu ua ar rttz z - An intrinsically piezoelectric silicon dioxide monocrystal. U Us se effu ull O Ov ve er rr ra an ng ge e - The maximum operating range of a pressure Generally recognized as the most stable of all piezoelectric sensor determined by either maximum electrical output or materials. maximum mechanical input; in some cases, useful overrange is R Re ec ce es ss se ed d M Mo ou un ntt - A type of mounting technique where the equal to range. diaphragm of the sensor is not flush with the surface of the test V Vo olltta ag ge e M Mo od de e - A sensor that incorporates impedance conversion chamber. Although it affects frequency response, this technique within the sensor package, powered by a constant-current protects the sensor diaphragm from the effects of high flash sensor supply, and providing a low impedance output signal. temperatures or particle impingement due to blast effects, Z Ze er ro o S Sh hiifftt - The change in the base line level of the output voltage thereby prolonging sensor life. of a sensor after a measurement due to mechanical, electrical, or R Re efflle ec cttiiv ve e S Sh ho oc ck k W Wa av ve e M Me ea as su ur re em me en ntt - A shock wave thermal effects. instantaneously impacting the diaphragm of a pressure sensor, face on. R RF FII - Abbreviation for Radio Frequency Interference. P PC CB B P PIIE EZ ZO OT TR RO ON NIIC CS S,, IIN NC C.. 7 71 16 6-6 68 84 4-0 00 00 01 1 Notes Notes 87 87 P PR RE ES SS SU UR RE E A AN ND D F FO OR RC CE E S SE EN NS SO OR R D DIIV VIIS SIIO ON N T TO OL LL L F FR RE EE E: : 8 88 88 8-6 68 84 4-0 00 01 11 1 Notes Notes 88 88 P PC CB B P PIIE EZ ZO OT TR RO ON NIIC CS S,, IIN NC C.. 7 71 16 6-6 68 84 4-0 00 00 01 1 Conversions/Equivalencies Table Conversions/Equivalencies Table P PR RE ES SS SU UR RE E A AC CC CE EL LE ER RA AT TIIO ON N 2 a attm mo os sp ph he er re es s a ac cc ce ell o off g gr ra av viitty y ((g g)) 9.80665 meters/second 1.01325 bars 2 32.174 feet/second 33.90 feet of H O 2 2 386.088 inches/second 29.92 inches of Hg 760.0 mm of Hg (torr) 2 2 2 2 101.325 kN/m (k Pa) ffe ee ett/ /s se ec co on nd d 0.3048 meters/second 14.696 pounds/sq. inch b ba ar r 2 2 2 75.01 cm of Hg iin nc ch he es s/ /s se ec co on nd d 0.02540 meters/second 5 2 10 N/m (Pa) 14.50 pounds/sq. inch F FO OR RC CE E 2 k kiillo og gr ra am m ((ffo or rc ce e)) 9.80665 newtons iin nc ch he es s o off H H O O 248.84 N/m (Pa) 2 2 1.00 kilopound 0.07355 inches of Hg 5 2 n ne ew wtto on n 10 dynes m mm m o off H Hg g ((tto or rr r)) 133.32 N/m (Pa) 0.1020 kilogram (force) 0.01933 pounds/sq. inch 3.597 ounce (force) 13.595 mm of H O 2 0.2248 pound (force) 89 89 7.2330 poundal n ne ew wtto on ns s/ /s sq q.. c ce en nttiim me ette er r 1.450 pounds/sq. inch p po ou un nd d ((ffo or rc ce e)) 16.00 ounce (force) p po ou un nd ds s/ /s sq q.. ffo oo ott 0.19242 inches of H O 2 0.45359 kilogram (force) 2 47.880 N/m (Pa) 4.448 newtons p ps sii 0.06805 atmospheres T TE EM MP PE ER RA AT TU UR RE E 0.06895 bars 2.036 inches of Hg C Ce ells siiu us s tto o F Fa ah hr re en nh he eiitt °F = 9/5 °C +32 27.708 inches of H O F Fa ah hr re en nh he eiitt tto o C Ce ells siiu us s °C = (°F –32) 5/9 2 703.77 mm of H O F Fa ah hr re en nh he eiitt tto o K Ke ellv viin n °K = 5/9(°F + 459.67) 2 51.72 mm of Hg F Fa ah hr re en nh he eiitt tto o R Ra an nk kiin n °R = °F + 459.67° 2 0.68948 N/cm C Ce ells siiu us s tto o K Ke ellv viin n °K = °C + 273.15° 2 6 894.8 N/m (Pa) 2 7.031 x 10-4 kg (f) mm C Co om mm mo on nlly y U Us se ed d P Pr re effiix xe es s -6 9 µmicro 10 G giga 10 -6 d dB B (sound pressure-air) 20 log P/P P = .0029 x 10 psi -9 o o 6 n nano 10 M mega 10 -12 3 p pico 10 kkilo 10 -2 c centi 10 -3 m milli 10 P PR RE ES SS SU UR RE E A AN ND D F FO OR RC CE E S SE EN NS SO OR R D DIIV VIIS SIIO ON N T TO OL LL L F FR RE EE E: : 8 88 88 8-6 68 84 4-0 00 01 11 1 Warranty Information Warranty Information W WA AR RR RA AN NT TY Y P PC CB B o offffe er rs s a an n u un nc co on nd diittiio on na all g gu ua ar ra an ntte ee e ffo or r c cu us stto om me er r s sa attiis sffa ac cttiio on n.. Should you at any time find yourself dissatisfied with any PCB product for any reason, consult a PCB applications engineer to discuss repair, refund, or exchange procedures. PCB instrumentation is warranted against defective material and workmanship for one year, unless otherwise expressly specified. Damage to instruments caused by incorrect power or misapplication is not covered by warranty. If there is any question regarding power, 90 90 intended application, or general usage, please contact a PCB applications engineer (if outside U.S., contact your local representative or distributor). Batteries and other expendable hardware items are not covered by warranty. Catalog specifications are subject to change; before machining installation ports request a copy of the current installation drawing. Registered trademarks of PCB Piezotronics, Inc. include: PCB, ICP, Flexcel, Structcel, Data Harvester and Modally Tuned. Invar is a registered trademark of Metalimphy Inc. Emralon is a registered trademark of Acheson Industries Inc. Teflon, Delrin and Tefzel are registered trademarks of DuPont. Monoplex is a registered trademark of C.P. Hall Company. Swagelok is a registered trademark of Swagelok Co. Pressure Selection Guide 100A 11/98 © Copyright 1997, PCB Piezotronics, Inc. PCB Quality is ISO-9001 certified PCB is an EOE/AAP Employer Printed in USA WS597 P PC CB B P PIIE EZ ZO OT TR RO ON NIIC CS S,, IIN NC C.. 7 71 16 6-6 68 84 4-0 00 00 01 1 Ordering Information Ordering Information If you have questions, need more information, or would like to discuss an application in detail, please call the factory or field representative in your area. A reply card is also enclosed for your convenience. Our staff of experienced applications engineers are glad to provide you with technical assistance, order and delivery expediting, quoting, sample hardware, and other information you may require. PFS TOLL FREE: 888-684-0011 IMI Worldwide Headquarters 716-684-0001 FAX: 716-686-9129 PCB PIEZOTRONICS, INC. 3425 Walden Avenue Depew, NY 14043-2495 USA ™ 24-hour “SensorLine” Call the “SensorLine” day or night to discuss your immediate dynamic instrumentation needs. When an unexpected measurement problem occurs, help is available Saturday, Sunday, or after work hours. A Customer Service Representative is only a phone call away: SensorLine 716-684-0001 Our company mission: helping you make better dynamic measurements. Piezoelectric Technology Center Your dynamic pressure, force, shock, and vibration measurement needs, all under one roof . . . ISO 9001 CERTIFIED You are invited to visit our modern manufacturing and technology center whenever you are in the Buffalo or Niagara Falls area. PCB is located convenient to the Buffalo International Airport and near Niagara Falls. PCB PIEZOTRONICS, INC. 3425 WALDEN AVENUE DEPEW, NEW YORK U.S.A. 14043-2495 PCB: 716-684-0001 PFS Toll Free: 888-684-0011 FAX: 716-686-9129 E-mail: pfssales@pcb.com Web Site: www.pcb.com PSG604A1097 Printed in U.S.A.
Frequently asked questions
What makes Elite.Parts unique?

What kind of warranty will the 112A03 have?

Which carriers does Elite.Parts work with?

Will Elite.Parts sell to me even though I live outside the USA?

I have a preferred payment method. Will Elite.Parts accept it?

What they say about us
FANTASTIC RESOURCE
One of our top priorities is maintaining our business with precision, and we are constantly looking for affiliates that can help us achieve our goal. With the aid of GID Industrial, our obsolete product management has never been more efficient. They have been a great resource to our company, and have quickly become a go-to supplier on our list!
Bucher Emhart Glass
EXCELLENT SERVICE
With our strict fundamentals and high expectations, we were surprised when we came across GID Industrial and their competitive pricing. When we approached them with our issue, they were incredibly confident in being able to provide us with a seamless solution at the best price for us. GID Industrial quickly understood our needs and provided us with excellent service, as well as fully tested product to ensure what we received would be the right fit for our company.
Fuji
HARD TO FIND A BETTER PROVIDER
Our company provides services to aid in the manufacture of technological products, such as semiconductors and flat panel displays, and often searching for distributors of obsolete product we require can waste time and money. Finding GID Industrial proved to be a great asset to our company, with cost effective solutions and superior knowledge on all of their materials, it’d be hard to find a better provider of obsolete or hard to find products.
Applied Materials
CONSISTENTLY DELIVERS QUALITY SOLUTIONS
Over the years, the equipment used in our company becomes discontinued, but they’re still of great use to us and our customers. Once these products are no longer available through the manufacturer, finding a reliable, quick supplier is a necessity, and luckily for us, GID Industrial has provided the most trustworthy, quality solutions to our obsolete component needs.
Nidec Vamco
TERRIFIC RESOURCE
This company has been a terrific help to us (I work for Trican Well Service) in sourcing the Micron Ram Memory we needed for our Siemens computers. Great service! And great pricing! I know when the product is shipping and when it will arrive, all the way through the ordering process.
Trican Well Service
GO TO SOURCE
When I can't find an obsolete part, I first call GID and they'll come up with my parts every time. Great customer service and follow up as well. Scott emails me from time to time to touch base and see if we're having trouble finding something.....which is often with our 25 yr old equipment.
ConAgra Foods