ORIENTAL MOTOR UDK5114NW2-M
Specifications
Motor operating current adjustment switch motor stop current adjustment swi
The motor current is easy to adjust with digital switches and no ammeter necessary.
O.H
Overheat output display
Oriental Motor
UDK5114NW2-M
Power
Power input display
Power Supply Terminals
Drivers are available for use with single-phase 100-115VAC15% (50/60 Hz) and 200-230VAC(50/60 Hz) models.
Pulse input mode switch
Switches between 1-pulse input and 2-pulse input.
Run
Can be adjusted the motor running current.
Signal monitor display
Easy to confirm I/O signals.
Step angle switch
Switches the motor’s step angle. Full: 0.72°/step, Half: 0.36°/step
Stop
Can be adjusted the current at the motor standstill.
TIM
Excitation timing output display
Features
- (15kHz).
- (50/60 Hz) power input, the product line also has 200-230VAC (50/60 Hz) models.
- Compact drivers: The UPK W series drivers are only 5.31 inch (135mm) high and therefore keep the installation area small. They also come with a buitin mounting bracket for easy
- High Torque: The UPK W series is based on the UPK series of high-torque, 5-phase
- installation.
- Low Noise: The motor is designed on a new principle to produce excellent sound performance. The motor components are more rigid and the motor structure has been redesigned to achieve a significant red
- Low Vibration: The UPK W series does more than provide higher torque. It is also designed so that the motor produces less vibration, and a new driver has been developed to include a vibration control
- speed types only accept single-phase 100-115 VAC input.
- Standard certified products: These products are certified to meet the world's most common
- standards. Also, the product has been CE marked according to the low voltage directive. (Certification for some products is pending, so for a list of certified products).
- stepping motor package, so they have the same high torque. Now devices can be made smaller and more lightweight.
- The models with installation dimensions of 1.65inch (42mm)square and the high-
- Wide range of power supply voltage: In addition to single-phase 100-115VAC 15%
Datasheet
Extracted Text
5� with AC Driver 5� with DC Driver 2� with Driver 2� Low-Speed Stepping Synchronous STEPPING MOTORS Motors UPK•W UPK UFK•W PMU RFK CSK PMC UMK CSK Controllers Motors Accessories ORIENTAL MOTOR CATALOG 5-PHASE HIGH-TORQUE STEPPING MOTOR AND DRIVER PACKAGE • UPK W Series Features B-62 Product Line B-66 Standard Type, High-Speed Type B-68 Geared Type B-80 List of Motor and Driver Combinations B-102 Wiring Diagrams B-103 Description of Input/Output Signals B-105 2000-2001 ORIENTAL MOTOR GENERAL CATALOG B-61 ···················· ················································· ··············· ························································· ························· ························································· ······························································· RE- EASY PLC SAFETY PACK- AC GENER- GEAR • WIRING DIRECT STD. AGE INPUT UPK W Series ATION The UPK•W series is a new generation of compact, high torque, low vibration, 5-phase stepping motor and driver packages. � FEATURES 1. Compact Drivers 4. Low Noise The UPK•W series drivers are only 5.31 inch (135mm) high The motor is designed on a new principle to produce excellent and therefore keep the installation area small. sound performance. The motor components are more rigid and They also come with a buitin mounting bracket for easy the motor structure has been redesigned to achieve a significant installation. reduction in audible noise. 2. High Torque 5. Wide range of power supply voltage The UPK•W series is based on the UPK series of high-torque, In addition to single-phase 100-115VAC �15% (50/60 Hz) power �10% 5-phase stepping motor package, so they have the same high input, the product line also has 200-230VAC (50/60 Hz) �15% torque. models. Now devices can be made smaller and more lightweight. The models with installation dimensions of 1.65inch (42mm) square and the high-speed types only accept single-phase 100-115 VAC input. 3. Low Vibration The UPK•W series does more than provide higher torque. It is 6. Standard certified products also designed so that the motor produces less vibration, and a new driver has been developed to include a vibration control These products are certified to meet the world's most common circuit to dramatically reduce vibration in the mid-speed range standards. Also, the product has been CE marked according to (1�5kHz). the low voltage directive. (Certification for some products is pending, so for a list of certified products, see Page D-15.) B-62 2000-2001 ORIENTAL MOTOR GENERAL CATALOG � UPK•W SYSTEM CONFIGURATION A high-torque 5-phase stepping motor and driver are combined to make high- precision positioning with open loop control possible. Driver Cable (Sold separately) Page B-307 Driver Programmable Controller Controller (Sold separately) Stepping Motor and Driver SC8800, SC8800E Package Page B-260 Controller (Sold separately) SG8030J Page B-264 5-Phase Stepping Motor � ACCESSORIES (Sold separately) Motor Mounting Bracket Clean Damper Extension Cable Flexible ● Driver Cables Coupling Page B-307 Flat cable for connecting the driver and controller. ● Motor Mounting Brackets ● Flexible Couplings ● Clean Dampers ● Extension Cables Page B-298 Page B-301 Page B-300 Page B-306 MC Motor Couplings Effective at suppressing motor 16.4 feet (5m), 32.8 feet (10m), vibration and inproving 65.6 feet (20m) long performance. Motor mounting bracket and flexible coupling cannot be fitted on to geared type. 2000-2001 ORIENTAL MOTOR GENERAL CATALOG B-63 • The UPK W series has four types of drivers. The • The UPK W Series Drivers. functions listed below are common to all types. The drivers shown below are the UDK5114NW2 and the Designed with User-Friendly UDK5214NW. Functions. A full range of driver functions are on the front panel. Driver operating status is visible at a glance Pulse input mode switch c Signal monitor display Switches between 1-pulse input and 2-pulse input. z Easy to confirm I/O signals. Step angle switch v POWER: Power input display Switches the motor’s step angle. TIM.: Excitation timing output display FULL: 0.72˚/step, HALF: 0.36˚/step O.H.: Overheat output display Automatic current off function switch b When the temperature inside the driver reaches 176˚F (80˚C), this function automatically switches the motor current off. The function can be set and released with this switch. Motor operating current adjustment switch Power Supply Terminals n x Motor stop current adjustment switch Drivers are available for use with single-phase 100- �10% 115VAC�15% (50/60 Hz) and 200-230VAC The motor current is easy to adjust with digital switches. �15% (50/60 Hz) models. No ammeter necessary. RUN : Can be adjusted the motor running current. STOP : Can be adjusted the current at the motor standstill. Protective Earthing Terminal m z z x c x v c b v b n n m m Single-Phase 100-115VAC Input Driver Single-Phase 200-230VAC Input Driver B-64 2000-2001 ORIENTAL MOTOR GENERAL CATALOG 2000-2001 ORIENTAL MOTOR GENERAL CATALOG B-65 • UPK W Series Product Line TH : Maximum Holding Torgue Mounting Frame Size inch (mm) 1.65(42) Standard Type TH✽oz-in (N•m) 18 (0.13) 24.9 (0.18) 33.3 (0.24) 58.3 (0.42) Page B-68 Single-Phase UPK543AW UPK544AW UPK545AW UPK564AW2 100V-115VAC Input UPK543BW UPK544BW UPK545BW UPK564BW2 Single-Phase UPK564AJW 200V-230VAC Input UPK564BJW High-Speed Type Page B-68 Single-Phase 100V-115VAC Input TH Geared Type TH✽lb-in (N•m) 3.03 (0.35) 6.07 (0.7) 8.67 (1) 13 (1.5) 10.8 (1.25) Page B-80 UPK543AW-T3.6 UPK543AW-T7.2 UPK543AW-T10 UPK543AW-T20 UPK564AW-T3.6 Single-Phase UPK543BW-T3.6 UPK543BW-T7.2 UPK543BW-T10 UPK543BW-T20 UPK564BW-T3.6 100V-115VAC Input UPK543AW-T30 UPK543BW-T30 UPK564AJW-T3.6 Single-Phase UPK564BJW-T3.6 200V-230VAC Input ✽ PN Geared Type TH lb-in (N•m) Page B-80 Single-Phase 100V-115VAC Input Single-Phase 200V-230VAC Input B-66 2000-2001 ORIENTAL MOTOR GENERAL CATALOG ✽ 2.36(60) 3.35(85)/3.54(90) 115 (0.83) 230 (1.66) 291 (2.1) 569 (4.1) 874 (6.3) UPK566AW2 UPK569AW2 UPK596AW2 UPK599AW2 UPK5913AW2 UPK566BW2 UPK569BW2 UPK596BW2 UPK599BW2 UPK5913BW2 UPK566AJW UPK569AJW UPK596AJW UPK599AJW UPK5913AJW UPK566BJW UPK569BJW UPK596BJW UPK599BJW UPK5913BJW UPK569AHW2 UPK596AHW2 UPK599AHW2 UPK5913AHW2 UPK569BHW2 UPK596BHW2 UPK599BHW2 UPK5913BHW2 21.6 (2.5) 26 (3) 30.3 (3.5) 34.7 (4) 39 (4.5) 78.1 (9) 104 (12) UPK564AW-T7.2 UPK564AW-T10 UPK564AW-T20 UPK564AW-T30 UPK596AW-T3.6 UPK596AW-T7.2 UPK596AW-T20 UPK564BW-T7.2 UPK564BW-T10 UPK564BW-T20 UPK564BW-T30 UPK596BW-T3.6 UPK596BW-T7.2 UPK596BW-T20 UPK596AW-T10 UPK596AW-T30 UPK596BW-T10 UPK596BW-T30 UPK564AJW-T7.2 UPK564AJW-T10 UPK564AJW-T20 UPK564AJW-T30 UPK596AJW-T3.6 UPK596AJW-T7.2 UPK596AJW-T20 UPK564BJW-T7.2 UPK564BJW-T10 UPK564BJW-T20 UPK564BJW-T30 UPK596BJW-T3.6 UPK596BJW-T7.2 UPK596BJW-T20 UPK596AJW-T10 UPK596AJW-T30 UPK596BJW-T10 UPK596BJW-T30 30.3 (3.5) 52 (6) UPK566AW-N5 UPK564AW-N25 UPK566BW-N5 UPK564BW-N25 UPK566AW-N7.2 UPK564AW-N36 UPK566BW-N7.2 UPK564BW-N36 UPK566AW-N10 UPK564AW-N50 UPK566BW-N10 UPK564BW-N50 UPK566AJW-N5 UPK564AJW-N25 UPK566BJW-N5 UPK564BJW-N25 UPK566AJW-N7.2 UPK564AJW-N36 UPK566BJW-N7.2 UPK564BJW-N36 UPK566BJW-N10 UPK564BJW-N50 UPK566BJW-N10 UPK564BJW-N50 2000-2001 ORIENTAL MOTOR GENERAL CATALOG B-67 • UPK W Standard Type • UPK W High-Speed Type The UPK•W series of 5-phase stepping motor and � FEATURES driver packages are compact and provide high torque with low vibration. ● Standard Type Available in three frame sizes of 1.65 inch (42mm) square, 2.36 They are optimal for controlling vibration and inch (60mm) square and 3.35 inch (85mm) square. reducing noise. ● High-Speed Type This product is suitable for applications requiring higher speed operation and smaller sized equipment. � SAFETY STANDARDS AND CE MARKING Authorizing Products Applicable Standards CE Marking File No. Organization UL1004, UL519 CAN/CSA-C22.2 No. 100 UL E64199 CAN/CSA-C22.2 No. 77 Low Voltage Stepping Motor Directive EN60950 EN60034-1 VDE 6763üG EN60034-5 UL508C UL E17146 Driver for CAN/CSA-C22.2 No. 14 Low Voltage Stepping Motor Directive EN60950, EN50178 DEMKO See page D-15 ●See page D-9 for more information on operating conditions of EN/IEC standards. ● The EN/IEC standard certification depends on the type and installation size. For details, see Page D-15. ●Motors and drivers are recognized individually. � PRODUCT NUMBER CODE UPK 5 6 9 A H W 2 Revision Number • UPK W Series Product Type Blank: 100V-115VAC Input Standard Type H: 100V-115VAC Input High-Speed Type J: 200V-230VAC Input Standard Type Shaft Type A: Single Shaft B: Double Shaft Motor Case Length Motor Frame Size 4: 1.65 in. (42mm) sq. 6: 2.36 in. (60mm) sq. 5-phase 9: 3.35 in. (85mm) sq. 5-phase High-Torque Stepping Motor and Driver Package B-68 2000-2001 ORIENTAL MOTOR GENERAL CATALOG � SPECIFICATIONS STANDARD TYPE Single-Phase 100-115VAC Input Single Shaft UPK543AW UPK544AW UPK545AW Package Model Double Shaft UPK543BW UPK544BW UPK545BW oz-in 18 24.9 33.3 Maximum Holding Torque N •m 0.13 0.18 0.24 2 oz-in 0.192 0.296 0.372 Rotor Inertia 2 �7 �7 �7 kg •m � � � 35 10 54 10 68 102 Rated Current 0.75 A /phase 0.72° Basic Step Angle Class B [266°F (130°C)] Recognized as Class A [221°F (105°C)] by UL standard. Insulation Class Power Source Single-Phase100 115V 15% 60Hz 1.5A Output Current A/phase 0.75 ● Full Step (4 phase excitation): 0.72°/step Excitation Mode ● Half Step (4-5 phase excitation): 0.36°/step (Switch selectable) Photocoupler input, Input resistance 220Ω, Input current 20mA maximum Input Signal Circuit Signal voltage Photocoupler ON: �4��5V, Photocoupler OFF: 0��0.5V CW direction step command pulse signal (Step command signal at 1-pulse input mode) ● CW Pulse Signal (Pulse Signal) Pulse width: 5µs minimum, Pulse rise/fall: 2µs maximum Motor moves when the photocoupler state changes from ON to OFF. CCW direction step command signal (Rotation direction signal at 1-pulse input mode, Photocoupler ON: CW, Photocoupler OFF: CCW) ● CCW Pulse Signal Pulse width: 5µs minimum, Pulse rise/fall: 2µs maximum (Rotation Direction Signal) Motor moves when the photocoupler state changes from ON to OFF. When in the "photocoupler ON" state, the current to the motor is cut off and the motor shaft can be rotated manually. ● All Windings Off Signal When in the "photocoupler OFF" state, the current level set by the RUN switch is supplied to the motor. Photocoupler, Open-Collector Output (Emitter common) Output Signal Circuit External use condition: 24V DC maximum, 10mA maximum The signal is output every time the excitation sequence returns to the initial stage "0". (Photocoupler : ON) ● Excitation Timing Signal Full step: signal output every 10 pulses, Half step: signal output every 20 pulses The signal is output when the internal temperature of the driver rises above approximately 176°F (80°C). (Photocoupler: ON) ● Overheat Signal The motor stops automatically if the "Automatic Current Off" function is ON. Functions Automatic current cutback, All windings off, Pulse input mode switch, Step angle switch Indicator (LED) Power source input, Excitation timing signal output, Overheat signal output Driver Cooling Method Natural Ventilation 0.67 (0.3) Motor lb. (kg) 0.56 (0.25) 0.89 (0.4) Waight (Mass) Driver lb. (kg) 2.1 (0.95) 100M Ωminimum under normal temperature and humidity, when measured by a DC500V megger between the Motor motor coils and the motor casing. 100M Ωminimum under normal temperature and humidity, when measured by a DC500V megger between the Insulation Resistance following places: Driver ● Power input terminal — Protective earthing terminal ● Motor output terminal — Protective earthing terminal ● Signal input/output terminal — Power input terminal ● Signal input/output terminal — Motor output terminal Sufficient to withstand 1.0kV, 60Hz applied between the motor coils and casing for one minute, under normal Motor temperature and humidity. Sufficient to withstand the following for one minute, under normal temperature and humidity. ● Power input terminal — Protective earthing terminal AC1.5kV 60Hz Dielectric Strength Driver ● Motor output terminal — Protective earthing terminal AC1.5kV 60Hz ● Signal input/output terminal — Power input terminal AC3.0kV 60Hz ● Signal input/output terminal — Motor output terminal AC3.0kV 60Hz Motor �14°F��122°F (�10°C��50°C) Ambient Temperature Range � � � Driver 32°F� 122°F (0°C� 50°C) ●Maximum holding torque refers to the holding torque at motor standstill when the rated current is supplied to the motor (5-phase excitation). Use this value to compare motor torque performance. When using the motor with the dedicated driver, the driver's "Automatic Current Cutback" function at motor standstill reduces maximum holding torque by approximately 50%. ●The power source input current value represents the maximum current. (The input current varies according to the pulse frequency.) Note : Do not measure insulation resistance or perform the dielectric strength test while the motor and driver are connected. 2000-2001 ORIENTAL MOTOR GENERAL CATALOG B-69 Output Signals Input Signals c STANDARD TYPE Single-Phase 100-115VAC Input / Single Shaft UPK564AW2 UPK566AW2 UPK569AW2 UPK596AW2 UPK599AW2 UPK5913AW2 Package Model Double Shaft UPK564BW2 UPK566BW2 UPK569BW2 UPK596BW2 UPK599BW2 UPK5913BW2 oz-in 58.3 115 230 291 569 874 Maximum Holding Torque N •m 0.42 0.83 1.66 2.1 4.1 6.3 2 oz-in 0.96 1.53 3.07 7.66 14.8 21.9 Rotor Inertia 2 �7 �7 �7 �7 �7 �7 � � � � � � kg •m 175 10 280 10 560 10 1400 10 2700 10 4000 10 Rated Current 1.4 A /phase Basic Step Angle 0.72° Class B [266°F (130°C)] Insulation Class Recognized as Class A [221°F (105°C)] by UL and CSA standards. Power Source Single-Phase100 115V 15% 60Hz 5.5A Output Current A/phase 1.4 ● Full Step (4 phase excitation): 0.72°/step Excitation Mode ● Half Step (4-5 phase excitation): 0.36°/step (Switch selectable) Photocoupler input, Input resistance 220Ω, Input current 20mA maximum Input Signal Circuit Signal voltage Photocoupler ON: �4��5V, Photocoupler OFF: 0��0.5V CW direction step command pulse signal (Step command signal at 1-pulse input mode) ● CW Pulse Signal (Pulse Signal) Pulse width: 5µs minimum, Pulse rise/fall: 2µs maximum Motor moves when the photocoupler state changes from ON to OFF. CCW direction step command signal (Rotation direction signal at 1-pulse input mode, Photocoupler ON: CW, Photocoupler OFF: CCW) ● CCW Pulse Signal Pulse width: 5µs minimum, Pulse rise/fall: 2µs maximum (Rotation Direction Signal) Motor moves when the photocoupler state changes from ON to OFF. When in the "photocoupler ON" state, the current to the motor is cut off and the motor shaft can be rotated manually. ● All windings Off Signal When in the "photocoupler OFF" state, the current level set by the RUN switch is supplied to the motor. Photocoupler, Open-Collector Output (Emitter common) Output Signal Circuit External use condition: 24V DC maximum, 10mA maximum The signal is output every time the excitation sequence returns to the initial stage "0". (Photocoupler : ON) ● Excitation Timing Signal Full step: signal output every 10 pulses, Half step: signal output every 20 pulses The signal is output when the internal temperature of the driver rises above approximately 176°F (80°C). (Photocoupler: ON) ● Overheat Signal The motor stops automatically if the "Automatic Current Off" function is ON. Automatic current cutback, All windings off, Pulse input mode switch, Step angle switch Functions Power source input, Excitation timing signal output, Overheat signal output Indicator (LED) Natural Ventilation Driver Cooling Method 1.33 (0.6) 1.77 (0.8) 2.87 (1.3) 3.75 (1.7) 6.18 (2.8) 8.38 (3.8) Motor Ib. (kg) Weight (Mass) 2.1 (0.95) Driver Ib. (kg) 100M Ωminimum under normal temperature and humidity, when measured by a DC500V megger between the Motor motor coils and the motor casing. 100M Ωminimum under normal temperature and humidity, when measured by a DC500V megger between the Insulation Resistance following places: Driver ● Power input terminal — Protective earthing terminal ● Motor output terminal — Protective earthing terminal ● Signal input/output terminal — Power input terminal ● Signal input/output terminal — Motor output terminal Sufficient to withstand 1.5kV, 60Hz applied between the motor coils and casing for one minute, under normal Motor temperature and humidity. Sufficient to withstand the following for one minute, under normal temperature and humidity. ● Power input terminal — Protective earthing terminal AC1.5kV 60Hz Dielectric Strength Driver ● Motor output terminal — Protective earthing terminal AC1.5kV 60Hz ● Signal input/output terminal — Power input terminal AC3.0kV 60Hz ● Signal input/output terminal — Motor output terminal AC3.0kV 60Hz � �14°F��122°F ( 10°C��50°C) Motor Ambient Temperature Range �32°F��122°F (0°C��50°C) Driver ●Maximum holding torque refers to the holding torque at motor standstill when the rated current is supplied to the motor (5-phase excitation). Use this value to compare motor torque performance. When using the motor with the dedicated driver, the driver's "Automatic Current Cutback" function at motor standstill reduces maximum holding torque by approximately 50%. ●The power source input current value represents the maximum current. (The input current varies according to the pulse frequency.) B-70 2000-2001 ORIENTAL MOTOR GENERAL CATALOG Input Signals Output Signals c STANDARD TYPE Single-Phase 200-230VAC Input / Single Shaft UPK564AJW UPK566AJW UPK569AJW UPK596AJW UPK599AJW UPK5913AJW Package Model Double Shaft UPK564BJW UPK566BJW UPK569BJW UPK596BJW UPK599BJW UPK5913BJW oz-in 58.3 115 230 291 569 874 Maximum Holding Torque N •m 0.42 0.83 1.66 2.1 4.1 6.3 2 oz-in 0.96 1.53 3.07 7.66 14.8 21.9 Rotor Inertia 2 �7 �7 �7 �7 �7 �7 � � � � � � kg •m 175 10 280 10 560 10 1400 10 2700 10 4000 10 Rated Current A /phase 1.4 Basic Step Angle 0.72° Insulation Class Class B [266°F (130°C)] Recognized as Class A [221°F (105°C)] by UL and CSA standards. �10% � Power Source Single-Phase200 230V 60Hz 3.5A �15% Output Current A/phase 1.4 ● Full Step (4 phase excitation): 0.72°/step ● Half Step (4-5 phase excitation): 0.36°/step Excitation Mode (Switch selectable) Photocoupler input, Input resistance 220Ω, Input current 20mA maximum Input Signal Circuit Signal voltage Photocoupler ON: �4��5V, Photocoupler OFF: 0��0.5V CW direction step command pulse signal (Step command signal at 1-pulse input mode) ● CW Pulse Signal (Pulse Signal) Pulse width: 5µs minimum, Pulse rise/fall: 2µs maximum Motor moves when the photocoupler state changes from ON to OFF. CCW direction step command signal (Rotation direction signal at 1-pulse input mode, Photocoupler ON: CW, Photocoupler OFF: CCW) ● CCW Pulse Signal Pulse width: 5µs minimum, Pulse rise/fall: 2µs maximum (Rotation Direction Signal) Motor moves when the photocoupler state changes from ON to OFF. When in the "photocoupler ON" state, the current to the motor is cut off and the motor shaft can be rotated manually. ● All windings Off Signal When in the "photocoupler OFF" state, the current level set by the RUN switch is supplied to the motor. Photocoupler, Open-Collector Output (Emitter common) Output Signal Circuit External use condition: 24V DC maximum, 10mA maximum The signal is output every time the excitation sequence returns to the initial stage "0". (Photocoupler : ON) ● Excitation Timing Signal Full step: signal output every 10 pulses, Half step: signal output every 20 pulses The signal is output when the internal temperature of the driver rises above approximately 176°F (80°C). (Photocoupler: ON) ● Overheat Signal The motor stops automatically if the "Automatic Current Off" function is ON. Automatic current cutback, All windings off, Pulse input mode switch, Step angle switch Functions Power source input, Excitation timing signal output, Overheat signal output Indicator (LED) Natural Ventilation Driver Cooling Method 1.33 (0.6) 1.77 (0.8) 2.87 (1.3) 3.75 (1.7) 6.18 (2.8) 8.38 (3.8) Motor Ib. (kg) Weight (Mass) 2.1 (0.95) Driver Ib. (kg) 100M Ωminimum under normal temperature and humidity, when measured by a DC500V megger between the Motor motor coils and the motor casing. 100M Ωminimum under normal temperature and humidity, when measured by a DC500V megger between the Insulation Resistance following places: Driver ● Power input terminal — Protective earthing terminal ● Motor output terminal — Protective earthing terminal ● Signal input/output terminal — Power input terminal ● Signal input/output terminal — Motor output terminal Sufficient to withstand 1.5kV, 60Hz applied between the motor coils and casing for one minute, under normal Motor temperature and humidity. Sufficient to withstand the following for one minute, under normal temperature and humidity. ● Power input terminal — Protective earthing terminal AC1.8kV 60Hz Dielectric Strength Driver ● Motor output terminal — Protective earthing terminal AC1.8kV 60Hz ● Signal input/output terminal — Power input terminal AC3.2kV 60Hz ● Signal input/output terminal — Motor output terminal AC3.2kV 60Hz �14°F��122°F (�10°C��50°C) Motor Ambient Temperature Range � � � 32°F� 122°F (0°C� 50°C) Driver ●Maximum holding torque refers to the holding torque at motor standstill when the rated current is supplied to the motor (5-phase excitation). Use this value to compare motor torque performance. When using the motor with the dedicated driver, the driver's "Automatic Current Cutback" function at motor standstill reduces maximum holding torque by approximately 50%. ●The power source input current value represents the maximum current. (The input current varies according to the pulse frequency.) 2000-2001 ORIENTAL MOTOR GENERAL CATALOG B-71 Output Signals Input Signals c HIGH-SPEED TYPE Single-Phase 100-115VAC Input / Single Shaft UPK569AHW2 UPK596AHW2 UPK599AHW2 UPK5913AHW2 Package Model Double Shaft UPK569BHW2 UPK596BHW2 UPK599BHW2 UPK5913BHW2 oz-in 230 291 569 874 Maximum Holding Torque N •m 1.66 2.1 4.1 6.3 2 oz-in 3.06 7.66 14.8 21.9 Rotor Inertia 2 �7 �7 �7 �7 � � � � kg •m 560 10 1400 10 2700 10 4000 10 Rated Current A /phase 2.8 Basic Step Angle 0.72° Insulation Class Class B [266°F (130°C)] Recognized as Class A [221°F (105°C)] by UL and CSA standards. Single-Phase100�115V�15% 50/60Hz 8A Power Source Output Current 2.8 A/phase ● Full Step (4 phase excitation): 0.72°/step Excitation Mode ● Half Step (4-5 phase excitation): 0.36°/step (Switch selectable) Photocoupler input, Input resistance 220Ω, Input current 20mA maximum Input Signal Circuit Signal voltage Photocoupler ON: �4��5V, Photocoupler OFF: 0��0.5V CW direction step command pulse signal (Step command signal at 1-pulse input mode) ● CW Pulse Signal (Pulse Signal) Pulse width: 5µs minimum, Pulse rise/fall: 2µs maximum Motor moves when the photocoupler state changes from ON to OFF. CCW direction step command signal (Rotation direction signal at 1-pulse input mode, Photocoupler ON: CW, Photocoupler OFF: CCW) ● CCW Pulse Signal Pulse width: 5µs minimum, Pulse rise/fall: 2µs maximum (Rotation Direction Signal) Motor moves when the photocoupler state changes from ON to OFF. When in the "photocoupler ON" state, the current to the motor is cut off and the motor shaft can be rotated manually. ● All Windings Off Signal When in the "photocoupler OFF" state, the current level set by the RUN switch is supplied to the motor. Photocoupler, Open-Collector Output (Emitter common) Output Signal Circuit External use condition: 24V DC maximum, 10mA maximum The signal is output every time the excitation sequence returns to the initial stage "0". (Photocoupler : ON) ● Excitation Timing Signal Full step: signal output every 10 pulses, Half step: signal output every 20 pulses The signal is output when the internal temperature of the driver rises above approximately 176°F (80°C). (Photocoupler: ON) ● Overheat Signal The motor stops automatically if the "Automatic Current Off" function is ON. Automatic current cutback, All windings off, Pulse input mode switch, Step angle switch Functions Power source input, Excitation timing signal output, Overheat signal output Indicator (LED) Internal Fan Driver Cooling Method 2.87 (1.3) 3.75 (1.7) 6.18 (2.8) 8.38 (3.8) Motor lb.(kg) Waight (Mass) 2.43 (1.1) Driver lb.(kg) 100M Ωminimum under normal temperature and humidity, when measured by a DC500V megger between the Motor motor coils and the motor casing. 100M Ωminimum under normal temperature and humidity, when measured by a DC500V megger between the Insulation Resistance following places: Driver ● Power input terminal — Protective earthing terminal ● Motor output terminal — Protective earthing terminal ● Signal input/output terminal — Power input terminal ● Signal input/output terminal — Motor output terminal Sufficient to withstand 1.5kV, 60Hz applied between the motor coils and casing for one minute, under normal Motor temperature and humidity. Sufficient to withstand the following for one minute, under normal temperature and humidity. ● Power input terminal — Protective earthing terminal AC1.5kV 60Hz Dielectric Strength Driver ● Motor output terminal — Protective earthing terminal AC1.5kV 60Hz ● Signal input/output terminal — Power input terminal AC3.0kV 60Hz ● Signal input/output terminal — Motor output terminal AC3.0kV 60Hz � Motor 14°F��122°F (�10°C��50°C) Ambient Temperature Range Driver �32°F��122°F (0°C��50°C) ●Maximum holding torque refers to the holding torque at motor standstill when the rated current is supplied to the motor (5-phase excitation). Use this value to compare motor torque performance. When using the motor with the dedicated driver, the driver's "Automatic Current Cutback" function at motor standstill reduces maximum holding torque by approximately 50%. ●The power source input current value represents the maximum current. (The input current varies according to the pulse frequency.) B-72 2000-2001 ORIENTAL MOTOR GENERAL CATALOG Input Signals Output Signals � SPEED vs. TORQUE CHARACTERISTICS fs: Maximum Starting Pulse Rate ●Standard Type UPK543BW UPK564BW2 2 –7 2 2 –7 2 With Damper D6CL-8.0: JL=1.01oz-in (185�10 kg·m ) With Damper D4CL-5.0: JL=0.22oz-in (40�10 kg·m ) 0.30 Power Input: AC100V-115V Power Input: AC100V–115V 100 40 14 0.7 7 Full Step 0.72˚/step Current: 1.4A/Phase (4Phases ON) Current: 0.75A/Phase (4Phases ON) Full Step 0.72˚/step Half Step 0.36˚/step 0.25 12 6 0.6 80 Half Step 0.36˚/step 30 10 0.5 5 0.20 Pullout Torque 60 8 0.4 4 Pullout Torque 0.15 20 6 0.3 3 40 0.10 4 0.2 2 10 20 0.05 2 0.1 1 Current Current fs fs fs fs 0 0 0 0 0 0 0.1 1 10 100 0.1 1 10 100 [ ] [ ] Pulse Speed kHz Pulse Speed kHz 0 12 120 1200 Full Step 0 12 120 1200 Full Step (6) (60) (600) (Half Step) (6) (60) (600) (Half Step) [ ] [ ] Speed r/min Speed r/min UPK544BW UPK566BW2 2 –7 2 2 –7 2 With Damper D4CL-5.0: JL=0.22oz-in (40�10 kg·m ) With Damper D6CL-8.0: JL=1.01oz-in (185�10 kg·m ) 0.30 Power Input: AC100V-115V 40 200 Power Input: AC100V-115V 7 14 1.4 Current: 0.75A/Phase (4Phases ON) Full Step 0.72˚/step ( ) Current: 1.4A/Phase 4Phases ON Full Step 0.72˚/step 0.25 Half Step 0.36˚/step 6 12 1.2 Half Step 0.36˚/step 30 150 5 0.20 Pullout Torque 10 1.0 Pullout Torque 4 8 0.8 0.15 20 100 3 6 0.6 0.10 2 4 0.4 10 50 0.05 1 2 0.2 Current Current fs fs fs fs 0 0 0 0 0 0 0.1 1 10 100 0.1 1 10 100 [ ] Pulse Speed kHz Pulse Speed [kHz] 0 12 120 1200 Full Step 0 12 120 1200 Full Step (6) (60) (600) (Half Step) ( ) ( ) ( ) ( ) 6 60 600 Half Step Speed [r/min] Speed [r/min] UPK545BW UPK569BW2 2 –7 2 2 –7 2 ( ) With Damper D4CL-5.0: JL=0.22oz-in 40�10 kg·m ( ) With Damper D6CL-8.0: JL=1.01oz-in 185�10 kg·m 3.0 100 Power Input: AC100V-115V 400 Power Input: AC100V-115V 7 0.7 14 ( ) Current: 0.75A/Phase 4Phases ON ( ) Current: 1.4A/Phase 4Phases ON Full Step 0.72˚/step 2.5 6 0.6 Full Step 0.72˚/step 12 Half Step 0.36˚/step 80 Half Step 0.36˚/step 300 5 0.5 10 2.0 Pullout Torque 60 4 0.4 8 1.5 200 3 0.3 Pullout Torque 6 40 1.0 2 0.2 4 100 20 0.5 1 0.1 2 Current Current fs fs fs fs 0 0 0 0 0 0 0.1 1 10 100 0.1 1 10 100 Pulse Speed [kHz] Pulse Speed [kHz] 0 12 120 1200 Full Step 0 12 120 1200 Full Step ( ) ( ) ( ) ( ) 6 60 600 Half Step ( ) ( ) ( ) ( ) 6 60 600 Half Step [ ] Speed r/min [ ] Speed r/min Note: ●Pay attention to heat dissipation from the motor and driver. The motor will produce a considerable amount of heat under certain conditions. Be sure to keep the temperature of the motor case under 212˚F (100˚C). [Under 167˚F (75˚C) is required to comply with UL or CSA standards. UPK54�W is under application.] ●When using the motor with the dedicated driver, the driver's "Automatic Current Cutback" function at motor standstill reduces maximum holding torque by approximately 50%. 2000-2001 ORIENTAL MOTOR GENERAL CATALOG B-73 [ ] [ ] Torque [oz-in] Torque oz-in Torque oz-in Torque oz-in Torque oz-in Torque oz-in [ ] Driver Input Current [A] [ ] Driver Input Current A Driver Input Current A [ ] [ ] [ ] Torque N·m Torque N·m Torque N·m [ ] Driver Input Current [A] Driver Input Current A Driver Input Current [A] Torque [N·m] [ ] Torque [N·m] Torque N·m [ ] [ ] [ ] � SPEED vs. TORQUE CHARACTERISTICS fs: Maximum Starting Pulse Rate ●Standard Type UPK596BW2 UPK564BJW 2 –7 2 2 –7 2 With Damper D9CL-14: JL=4.76oz-in (870�10 kg·m ) With Damper D6CL-8.0: JL=1.01oz-in (185�10 kg·m ) Power Input: AC100V-115V Full Step 0.72˚/step 3.0 400 ( ) 100 Power Input: AC200V-230V Current: 1.4A/Phase 4Phases ON Half Step 0.36˚/step 14 14 0.7 Full Step 0.72˚/step ( ) Current: 1.4A/Phase 4Phases ON 2.5 Half Step 0.36˚/step 12 12 0.6 80 300 10 2.0 10 0.5 Pullout Torque Pullout Torque 60 8 8 0.4 1.5 200 6 6 0.3 40 1.0 4 4 0.2 100 20 0.5 2 Current 2 0.1 Current fs fs fs fs 0 0 0 0 0 0 0.1 1 10 100 0.1 1 10 100 [ ] [ ] Pulse Speed kHz Pulse Speed kHz 0 12 120 1200 Full Step 01 12 20 1200 Full Step (6) (60) (600) (Half Step) (6) (60) (600) (Half Step) Speed [r/min] Speed [r/min] UPK599BW2 UPK566BJW 2 –7 2 2 –7 2 ( ) ( ) With Damper D9CL-14: JL=4.76oz-in 870�10 kg·m With Damper D6CL-8.0: JL=1.01oz-in 185�10 kg·m Power Input: AC100V-115V 1000 200 Power Input: AC200V-230V 14 7 14 1.4 Current: 1.4A/Phase (4Phases ON) ( ) Full Step 0.72˚/step Current: 1.4A/Phase 4Phases ON Full Step 0.72˚/step 12 6 Half Step 0.36˚/step 12 1.2 Half Step 0.36˚/step 800 Pullout Torque 150 Pullout Torque 10 5 10 1.0 600 8 8 4 0.8 100 6 6 0.6 3 400 4 2 4 0.4 50 200 Current 2 1 2 0.2 fs Current fs fs fs 0 0 0 0 0 0 0.1 1 10 100 0.1 1 10 100 Pulse Speed [kHz] Pulse Speed [kHz] 01 12 20 1200 Full Step 01 12 20 1200 Full Step (6) (60) (600) (Half Step) (6) (60) (600) (Half Step) [ ] Speed r/min Speed [r/min] UPK5913BW2 UPK569BJW 2 –7 2 2 –7 2 ( ) With Damper D6CL-8.0: JL=1.01oz-in (185�10 kg·m ) With Damper D9CL-14: JL=4.76oz-in 870�10 kg·m 3.0 Power Input: AC100V-115V 400 Power Input: AC200V-230V 2000 14 14 14 Current: 1.4A/Phase (4Phases ON) Current: 1.4A/Phase (4Phases ON) Full Step 0.72˚/step Full Step 0.72˚/step 2.5 12 Half Step 0.36˚/step 12 12 Half Step 0.36˚/step 300 1500 10 10 2.0 10 Pullout Torque Pullout Torque 8 8 8 1.5 1000 200 6 6 6 1.0 4 4 4 500 100 Current 0.5 2 2 2 Current fs fs fs fs 0 0 0 0 0 0 0.1 1 10 100 0.1 1 10 100 [ ] Pulse Speed [kHz] Pulse Speed kHz 0 12 120 1200 Full Step 01 12 20 1200 Full Step ( ) ( ) ( ) ( ) (6) (60) (600) (Half Step) 6 60 600 Half Step [ ] [ ] Speed r/min Speed r/min Note: ●Pay attention to heat dissipation from the motor and driver. The motor will produce a considerable amount of heat under certain conditions. Be sure to keep the temperature of the motor case under 212˚F (100˚C). [Under 167˚F (75˚C) is required to comply with UL or CSA standards.] ●When using the motor with the dedicated driver, the driver's "Automatic Current Cutback" function at motor standstill reduces maximum holding torque by approximately 50%. B-74 2000-2001 ORIENTAL MOTOR GENERAL CATALOG [ ] Driver Input Current A [ ] Driver Input Current [A] Driver Input Current A Torque [N·m] [ ] Torque [N·m] Torque N·m [ ] Torque oz-in Torque [oz-in] [ ] Torque oz-in [ ] Driver Input Current [A] Driver Input Current [A] Driver Input Current A [ ] Torque [N·m] Torque N·m Torque [N·m] [ ] Torque [oz-in] Torque oz-in Torque [oz-in] ●High-Speed Type UPK596BJW UPK569BHW2 2 –7 2 With Damper D6CL-8.0: JL=1.01oz-in (185�10 kg·m ) 2 –7 2 ( ) With Damper D9CL-14: JL=4.76oz-in 870�10 kg·m 3.0 Power Input: AC200V-230V Full Step 0.72˚/step 3.0 400 Power Input: AC100V-115V 400 Current: 1.4A/Phase (4Phases ON) Half Step 0.36˚/step 14 14 Current: 2.8A/Phase (4Phases ON) Full Step 0.72˚/step 2.5 2.5 12 Half Step 0.36˚/step 12 300 300 10 2.0 Pullout Torque 10 2.0 Pullout Torque 8 8 1.5 1.5 200 200 6 6 1.0 1.0 4 4 100 100 0.5 Current 0.5 2 2 Current fs fs fs fs 0 0 0 0 0 0 0.1 1 10 100 0.1 1 10 100 [ ] Pulse Speed kHz Pulse Speed [kHz] 01 12 20 1200 Full Step 01 12 20 1200 Full Step ( ) ( ) ( ) ( ) 6 60 600 Half Step (6) (60) (600) (Half Step) [ ] Speed r/min Speed [r/min] UPK596BHW2 UPK599BJW 2 –7 2 With Damper D9CL-14: JL=4.76oz-in (870�10 kg·m ) 2 –7 2 ( ) With Damper D9CL-14: JL=4.76oz-in 870�10 kg·m 3.0 Power Input: AC100V-115V Full Step 0.72˚/step 400 ( ) 14 Current: 2.8A/Phase 4Phases ON Half Step 0.36˚/step Power Input: AC200V-230V 1000 14 7 Current: 1.4A/Phase (4Phases ON) 2.5 Full Step 0.72˚/step 12 12 6 Half Step 0.36˚/step 300 800 Pullout Torque 10 2.0 Pullout Torque 10 5 8 600 1.5 8 200 4 6 6 3 1.0 400 4 100 4 2 0.5 Current 200 2 2 1 Current fs fs 0 0 0 fs fs 0.1 1 10 100 0 0 0 0.1 1 10 100 [ ] Pulse Speed kHz Pulse Speed [kHz] 01 12 20 1200 Full Step 0 12 120 1200 Full Step ( ) ( ) ( ) ( ) 6 60 600 Half Step (6) (60) (600) (Half Step) Speed [r/min] [ ] Speed r/min UPK599BHW2 UPK5913BJW 2 –7 2 With Damper D9CL-14: JL=4.76oz-in (870�10 kg·m ) 2 –7 2 ( ) With Damper D9CL-14: JL=4.76oz-in 870�10 kg·m 1000 Power Input: AC100V-115V 14 7 Power Input: AC200V-230V 2000 ( ) Full Step 0.72˚/step 14 14 Current: 2.8A/Phase 4Phases ON Current: 1.4A/Phase (4Phases ON) Half Step 0.36˚/step Full Step 0.72˚/step 12 6 800 12 12 Half Step 0.36˚/step Pullout Torque 1500 10 5 10 10 600 Pullout Torque 8 4 8 8 1000 6 3 400 6 6 4 2 4 4 500 200 Current 2 1 2 Current 2 fs fs fs fs 0 0 0 0 0.1 1 10 100 0 0 0.1 1 10 100 [ ] Pulse Speed kHz Pulse Speed [kHz] 01 12 20 1200 Full Step 01 12 20 1200 Full Step (6) (60) (600) (Half Step) ( ) ( ) ( ) ( ) 6 60 600 Half Step Speed [r/min] [ ] Speed r/min UPK5913BHW2 2 –7 2 With Damper D9CL-14: JL=4.76oz-in (870�10 kg·m ) 2000 Power Input: AC100V-115V 14 14 ( ) Current: 2.8A/Phase 4Phases ON Full Step 0.72˚/step 12 12 Half Step 0.36˚/step 1500 10 10 Pullout Torque 8 8 1000 6 6 4 4 500 Current 2 2 fs fs 0 0 0 0.1 1 10 100 [ ] Pulse Speed kHz 01 12 20 1200 Full Step (6) (60) (600) (Half Step) Speed [r/min] Note: ●Pay attention to heat dissipation from the motor and driver. The motor will produce a considerable amount of heat under certain conditions. Be sure to keep the temperature of the motor case under 212˚F (100˚C). [Under 167˚F (75˚C) is required to comply with UL or CSA standards.] ●When using the motor with the dedicated driver, the driver's "Automatic Current Cutback" function at motor standstill reduces maximum holding torque by approximately 50%. 2000-2001 ORIENTAL MOTOR GENERAL CATALOG B-75 [ ] [ ] Driver Input Current [A] Driver Input Current A Driver Input Current A [ ] Torque [N·m] Torque [N·m] Torque N·m [ ] [ ] Torque oz-in Torque oz-in Torque [oz-in] Driver Input Current [A] Driver Input Current [A] Driver Input Current [A] [ ] Driver Input Current A [ ] Torque [N·m] Torque [N·m] Torque N·m Torque [N·m] [ ] Torque [oz-in] Torque oz-in [ ] [ ] Torque oz-in Torque oz-in � DIMENSIONS scale 1/4, unit = inch (mm) ●MOTOR (Standard and High-Speed Type) UPK543AW (Single shaft) UPK564AW2, UPK564AJW (Single shaft) Motor Model: PK543AW Weight 0.56 lb. (Mass 0.25kg) Motor Model: PK564AW Weight 1.33 lb. (Mass 0.6kg) UPK543BW (Double shaft) UPK564BW2, UPK564BJW (Double shaft) Motor Model: PK543BW Weight 0.56 lb. (Mass 0.25kg) Motor Model: PK564BW Weight 1.33 lb. (Mass 0.6kg) M3 P0.5 .83�.04 1.91�.04 .94�.04 �.014 1.97 .17 (4.5) DEEP MIN. �1 �1 �1 (21 ) (48.5 ) (24 ) (50�0.35) 4 PLACES .79�.01 .28 .06 .79�.01 .59�.04 1.3�.04 .79�.04 .18 DIA. (� 4.5), 4 HOLES □ 1.65�1.65�.04( 42�1) �0.25 (7) (1.5) �0.25 (20 ) (20 ) �1 �1 �1 (15 ) (33 ) (20 ) �.004 1.22✽.59�.01 .59�.01 (31�0.1) (15�0.25) (15�0.25) A A A' A' .08 (2) .59 23.6 2 23.6 2 (600)(50) (15) .48 (600) (50) 1.22 1.02 (12.2) (26) (31) CABLE .21 DIA.(� 5.4) 5 LEADS 5 LEADS AWG22 AWG26 .295�.006 CABLE .28 DIA. (� 7) (7.5�0.15) ✽ .59�.01(15�0.25) indicates the length of milling on motor shaft. •Shaft Cross Section A-A' UPK544AW (Single shaft) UPK566AW2, UPK566AJW (Single shaft) Motor Model: PK544AW Weight 0.67 lb. (Mass 0.3kg) Motor Model: PK566AW Weight 1.77.lb. (Mass 0.8kg) UPK544BW (Double shaft) UPK566BW2, UPK566BJW (Double shaft) Motor Model: PK544BW Weight 0.67 lb. (Mass 0.3kg) Motor Model: PK566BW Weight 1.77.lb. (Mass 0.8kg) M3 P0.5 �.04 �.04 �.04 .83 2.34 .94 .17 (4.5) DEEP MIN. �.014 1.97 (21�1) (59.5�1) (24�1) 4 PLACES (50�0.35) �.04 �.04 �.04 .59 1.54 .79 �.01 .28 .06 .79 □ �1 .79�.01 1.65�1.65�.04( 42 ) .18 DIA. (�4.5), 4 HOLES (15�1) (39�1) (20�1) (7) (1.5) (20�0.25) �0.25 (20 ) �.004 1.22✽.01 �.01 .59� .59 �0.1 (31 ) �0.25 �0.25 (15 ) (15 ) A A A' A' .08 (2) .59 23.6 2 23.6 2 (600)(50) .48 (15) (600) (50) 1.02 (12.2) 1.22 (26) (31) CABLE .21 DIA.(� 5.4) 5 LEADS 5 LEADS AWG22 AWG26 .295�.006 CABLE .28 DIA. (� 7) (7.5�0.15) ✽.59�.01(15�0.25) indicates the length of milling on motor shaft. •Shaft Cross Section A-A' UPK545AW (Single shaft) UPK569AW2, UPK569AJW (Single shaft) Motor Model: PK545AW Weight 0.89 lb. (Mass 0.4kg) Motor Model: PK569AW Weight 2.87 lb. (Mass 1.3kg) UPK545BW (Double shaft) UPK569AHW2 (Single shaft) Motor Model: PK545BW Weight 0.89 lb. (Mass 0.4kg) Motor Model: PK569AHW Weight 2.87 lb. (Mass 1.3kg) UPK569BW2, UPK569BJW (Double shaft) Motor Model: PK569BW Weight 2.87 lb. (Mass 1.3kg) M3 P0.5 .17 (4.5) DEEP MIN. UPK569BHW2 (Double shaft) 4 PLACES �.04 �.04 �.04 Motor Model: PK569BHW Weight 2.87 lb. (Mass 1.3kg) .59 1.85 .79 □ �1 1.65�1.65�.04( 42 ) �1 �1 �1 (15 ) (47 ) (20 ) �.04 �.04 �.04 1.97�.014 .83 3.5 .94 1.22�.004✽.01 .59�.01 .59� ( �1) (89�1) ( �1) (50�0.35) 21 24 �0.1 (31 ) �0.25 (15�0.25) .79�.01 (15 ) .28 .79�.01 .18 DIA. (� 4.5), 4HOLES .06 ( �.025) 20 ( ) ( ) ( �0.25) 7 1.5 20 A A .08 (2) A' A' 23.6 2 .48 (600)(50) (12.2) 1.02 .59 23.6 2 (26) (15) (600)(50) 5 LEADS CABLE .21 DIA.(� 5.4) AWG26 1.22 (31) 5 LEADS AWG22 .295�.006✽.59�.01(15�0.25) indicates the length of milling on motor shaft. CABLE .28 DIA. (� 7) ( �0.15) 7.5 ●These external appearance drawings are for double shaft models. For a single •Shaft Cross shaft, ignore the colored areas. Section A-A' See page B-36 for information on motor installation. B-76 2000-2001 ORIENTAL MOTOR GENERAL CATALOG 90˚ 90˚ 90˚ .1968 DIA. .1968 DIA. .1968 DIA. 0 0 0 .1964 DIA.(� 5�0.012) � � .1964 DIA.(� 5 0.012) .1964 DIA.(� 5 0.012) .177�.006 �6.006 .177 �.006 .177 �0.15 (4.5 ) (4.5�0.15) (4.5�0.15) .177�.006 �.006 �.006 .177 .177 (4.5�0.15) (4.5�0.15) (4.5�0.15) .1968 DIA. .1968 DIA. .1968 DIA. .1964 DIA. 0 .1964 DIA. .1964 DIA. 0 (� 5�0.012) (� 5�0.012) 0 (� 5�0.012) .8661 DIA. .8661 DIA. 0 0 .8661 DIA. .8648 DIA. � (� 22 0.033) 0 .8648 DIA. (� 22�0.033) .8648 DIA. � (� 22 0.033) .33 �.004 1.22 �.004 .33 1.22 .33 1.22�.004 �0.1 (8.5) (31 ) (31�0.1) (8.5) (31�0.1) (8.5) .3150 DIA. 0 � .3144 DIA.(� 8 0.015) .3150 DIA. .3150 DIA. 0 0 � � .3144 DIA. (� 8 0.015) .3144 DIA.(� 8 0.015) .3150 DIA. .3150 DIA. .3150 DIA. .3144 DIA. .3144 DIA. .3144 DIA. 0 0 0 � (�8 0.015) (�8�0.015) (� 8�0.015) 1.4173 DIA. 1.4173 DIA. 1.4173 DIA. 1.4158 DIA. .295�.006 1.4158 DIA. 1.4158 DIA. 0 �.04 ( �0.15) 2.36�2.36 0 0 7.5 (� 36�0.039) 2.36�2.36�.04 �.04 2.36�2.36 (�36�0.039) � (�36 0.039) (□ �1) 60 □ �1 □ ( 60 ) ( 60�1) �.006 �.006 .295 .295 �0.15 �0.15 (7.5 ) (7.5 ) �.014 .49 1.97 �.014 .49 1.97 .49 1.97�.014 (12.5) ( �0.35) 50 �0.35 (12.5) (50 ) �0.35 (12.5) (50 ) UPK596AW2, UPK596AJW (Single shaft) UPK596BW2, UPK596BJW (Double shaft) Motor Model: PK596AW Weight 3.75 lb. (Mass 1.7kg) Motor Model: PK596BW Weight 3.75 lb. (Mass 1.7kg) UPK596AHW2 (Single shaft) UPK596BHW2 (Double shaft) Motor Model: PK596AHW Weight 3.75 lb. (Mass 1.7kg) Motor Model: PK596BHW Weight 3.75 lb. (Mass 1.7kg) �.014 2.76 �.04 �.04 1.46�.04 1.26 2.68 (70�0.35) ( �1) (68�1) (37�1) 32 .39 �.01 .26 DIA. (� 6.5), 4HOLES .98�.01 .08 .98 ( ) ( ) ( �0.25) (25�.025) 10 2 25 A A A' A' �.006 .512 (13�0.15) .59 23.6 2 (15) (600)(50) •Shaft Cross Section A-A' 1.22 5 LEADS AWG22 (31) ( ) CABLE .28 DIA. � 7 UPK599AW2, UPK599AJW (Single shaft) UPK599BW2, UPK599BJW (Double shaft) Motor Model: PK599AW Weight 6.18 lb. (Mass 2.8kg) Motor Model: PK599BW Weight 6.18 lb. (Mass 2.8kg) UPK599AHW2 (Single shaft) UPK599BHW2 (Double shaft) Motor Model: PK599AHW Weight 6.18 lb. (Mass 2.8kg) Motor Model: PK599BHW Weight 6.18 lb. (Mass 2.8kg) 2.76�.014 �.04 �.04 �.04 1.26 3.86 1.46 ( �0.35) 70 ( �1) ( �1) (32�1) 98 37 �.01 ( ) �.01 .39 .08 .98 .26 DIA. � 6.5 , 4HOLES .98 ( �0.25) (25�.025) (10) (2) 25 A A A' A' .512�.006 ( �0.15) 13 .59 23.6 2 ( ) ( )( ) 15 600 50 •Shaft Cross Section A-A' 1.22 ( ) 5 LEADS AWG22 31 ( ) CABLE .28 DIA. � 7 UPK5913AW2, UPK5913AJW (Single shaft) UPK5913BW2, UPK5913BJW (Double shaft) Motor Model: PK5913AW Weight 8.38 lb. (Mass 3.8kg) Motor Model: PK5913BW Weight 8.38 lb. (Mass 3.8kg) UPK5913AHW2 (Single shaft) UPK5913BHW2 (Double shaft) Motor Model: PK5913AHW Weight 8.38 lb. (Mass 3.8kg) Motor Model: PK5913BHW Weight 8.38 lb. (Mass 3.8kg) 2.76�.014 1.26�.04 5.04�.04 �.04 1.46 �0.35 (70 ) �1 (32�1) (128 ) (37�1) .98�.01 .39 .08 .98�.01 .26 DIA. (� 6.5), 4 HOLES �0.25 (25 ) (10) (2) �0.25 (25 ) A A A' A' �.006 .512 �0.15 (13 ) 23.6 2 •Shaft Cross .59 (600) (50) (15) Section A-A' 1.22 5 LEADS AWG22 (31) CABLE .28 DIA. (� 7) ●These external appearance drawings are for double shaft models. For a single shaft, ignore the colored areas. See page B-36 for information on motor installation. 2000-2001 ORIENTAL MOTOR GENERAL CATALOG B-77 90˚ 90˚ 90˚ .5512 DIA. .5512 DIA. 0 0 .5505 DIA.(� 14�0.018) .5505 DIA.(� 14�0.018) .5512 DIA. 0 � .5505 DIA.(� 14 0.018) .5512 DIA. .5505 DIA. .5512 DIA. 0 � (� 14 0.018) .5505 DIA. 0 2.3622 DIA. (� 14�0.018) 2.3604 DIA. .5512 DIA. 2.3622 DIA. 0 �.04 .5505 DIA. � 3.35�3.35 (� 60 0.046) 2.3604 DIA. 0 (□85�1) 0 � ( � 14 0.018) 3.35�3.35�.04 ( � 60�0.046) □ ( 85�1) 2.3622 DIA. 2.3604 DIA. 0 (� 60�0.046) 3.35�3.35�.04 (□85�1) .49 2.76�.014 ( �0.35) (12.5) 70 �.014 .49 2.76 ( ) (70�0.35) 12.5 �.006 .512 ( �0.15) 13 .512�.006 ( �0.15) 13 .49 (12.5) 2.76�.014 (70�0.35) .512�.006 (13�0.15) � DIMENSIONS scale 1/4, unit = inch (mm) ●Driver Single-Phase 100-115VAC Input Standard Type □ □ □ For UPK543 W, UPK544 W, UPK545 W Driver Model: UDK5107NW2 Weight 2.1 lb. (Mass 0.95kg) □ □ □ For UPK564 W2, UPK566 W2, UPK569 W2, □ □ □ UPK596 W2, UPK599 W2, UPK5913 W2 Driver Model: UDK5114NW2 Weight 2.1 lb. (Mass 0.95kg) SLITS .3 .79 (20) (7.5) .18 DIA.(� 4.5) 2 HOLES 1.61MAX. (41MAX.) M3 -7 PLACES .2MAX. (5MAX.) M3 -2PLACES M4 4.57 (116) .18(4.5) .18(4.5) .59MAX. (15MAX.) 4.72(120) .3(7.5) .79 (20) 2.24 (57) � I/O Connector (Included) Connector: 54306-2011 (MOLEX) Connector: 54331-1201 (MOLEX) Single-Phase 200-230VAC Input Standard Type □ □ □ For UPK564 JW, UPK566 JW, UPK569 JW □ □ □ UPK596 JW, UPK599 JW, UPK5913 JW Driver Model: UDK5214NW Weight 2.1 lb. (Mass 0.95kg) SLITS .3 .79 .18 DIA.(� 4.5) (7.5) (20) 2 HOLES 1.61MAX. (41MAX.) M3 9 PLACES .2MAX. (5MAX.) M4 4.57 (116) .59MAX. .18(4.5) .18(4.5) (15MAX.) 4.72(120) .3(7.5) (20) .79 2.24 (57) � I/O Connector (Included) Connector: 54306-2011 (MOLEX) Connector: 54331-1201 (MOLEX) See page B-38 for information on driver installation. B-78 2000-2001 ORIENTAL MOTOR GENERAL CATALOG 5.31 5.31(135) (135) .59 .59 .59 .59 (15) (15) (15) (15) 5.91 (150) .3 .3 5.91 (150) .3 .3 (7.5) (7.5) PITCH.3(7.62) (7.5) (7.5) PITCH.3(7.62) .3(7.62) Single-Phase 100-115VAC Input High-Speed Type □ □ For UPK569 HW2, UPK596 HW2, □ □ UPK599 HW2, UPK5913 HW2 Driver Model: UDK5128NW2 Weight 2.43 lb. (Mass 1.1kg) SLITS .3 .79 (20) (7.5) .18 DIA.(� 4.5) 1.61MAX. 2 HOLES (41MAX.) M3 -7 PLACES .2MAX. (5MAX.) M4 M3 -2PLACES 5.75 (146) .59MAX. .18(4.5) .18(4.5) (15MAX.) 5.91(150) .3(7.5) .79 (20) 2.24 (57) COOLING FAN (INTAKE SIDE) � I/O Connector (Included) Connector: 54306-2011 (MOLEX) Connector: 54331-1201 (MOLEX) See page B-38 for information on driver installation. 2000-2001 ORIENTAL MOTOR GENERAL CATALOG B-79 5.31 (135) .59 .59 (15) (15) 5.91 (150) .3 .3 (7.5) (7.5) PITCH.3(7.62) .3(7.62) � LIST OF MOTOR AND DRIVER COMBINATIONS Stepping Motor Driver Package Model Type Current Model Model A/phase UPK543�W PK543�W UPK544�W PK544�W UDK5107NW2 0.75 UPK545�W PK545�W UPK564�W2 PK564�W UPK566�W2 PK566�W UPK569�W2 PK569�W 1.4 UDK5114NW2 UPK596�W2 PK596�W Standard UPK599�W2 PK599�W UPK5913�W2 PK5913�W UPK564�JW PK564�W UPK566�JW PK566�W UPK569�JW PK569�W 1.4 UDK5214NW UPK596�JW PK596�W UPK599�JW PK599�W UPK5913�JW PK5913�W UPK569�HW2 PK569�HW UPK596�HW2 PK596�HW High-Speed UDK5128NW2 2.8 UPK599�HW2 PK599�HW UPK5913�HW2 PK5913�HW UPK543�W-T3.6 PK543�W-T3.6 UPK543�W-T7.2 PK543�W-T7.2 UPK543�W-T10 PK543�W-T10 UDK5107NW2 0.75 UPK543�W-T20 PK543�W-T20 UPK543�W-T30 PK543�W-T30 UPK564�W-T3.6 PK564�W-T3.6 UPK564�W-T7.2 PK564�W-T7.2 UPK564�W-T10 PK564�W-T10 UPK564�W-T20 PK564�W-T20 UPK564�W-T30 PK564�W-T30 1.4 UDK5114NW2 UPK596�W-T3.6 PK596�W-T3.6 UPK596�W-T7.2 PK596�W-T7.2 TH Geared UPK596�W-T10 PK596�W1-T10 UPK596�W-T20 PK596�W1-T20 UPK596�W-T30 PK596�W1-T30 UPK564�JW-T3.6 PK564�W-T3.6 UPK564�JW-T7.2 PK564�W-T7.2 UPK564�JW-T10 PK564�W-T10 UPK564�JW-T20 PK564�W-T20 UPK564�JW-T30 PK564�W-T30 1.4 UDK5214NW UPK596�JW-T3.6 PK596�W-T3.6 UPK596�JW-T7.2 PK596�W-T7.2 UPK596�JW-T10 PK596�W-T10 UPK596�JW-T20 PK596�W-T20 UPK596�JW-T30 PK596�W-T30 UPK566�W-N5 PK566�W-N5 UPK566�W-N7.2 PK566�W-N7.2 UPK566�W-N10 PK566�W-N10 1.4 UDK5114NW2 UPK564�W-N25 PK564�W-N25 UPK564�W-N36 PK564�W-N36 UPK564�W-N50 PK564�W-N50 PN Geared UPK566�JW-N5 PK566�W-N5 UPK566�JW-N7.2 PK566�W-N7.2 UPK566�JW-N10 PK566�W-N10 UDK5214NW 1.4 UPK564�JW-N25 PK564�W-N25 UPK564�JW-N36 PK564�W-N36 UPK564�JW-N50 PK564�W-N50 Enter A (single shaft) or B (double shaft) in the � within the model numbers. B-102 2000-2001 ORIENTAL MOTOR GENERAL CATALOG � WIRING DIAGRAMS ●Single-Phase 100-115VAC Input Driver User's Controller V0 (�DC5V~24V) CN-1 Twisted Pair Line 1 CW Pulse Signal (Pulse Signal) 2 R1 3 Input CCW Pulse Signal 5-Phase Stepping Motor Signals (Rotation Direction 4 Signal) R1 10 All Winding Motor Lead Wires Off Signal TB2 5 R1 Blue BLUE Red RED V0 (�DC5V~24V) Orange ORANGE R Green GREEN R2 Black 11 BLACK Excitation Timing Signal R NC Output R2 NC Signals 12 Overheat Signal 20 GND TB-1 L 100– Single-Phase 100–115V AC ±15% 115V AC 50/60Hz N Protective Earth (P.E.) � Power Supply Caution Use a power supply that can supply sufficient input current. The driver incorporates double-pole/neutral fusing for the power input. If the When power supply capacity is insufficient, a decrease in motor output can cause driver POWER LED is off, it is possible that only the neutral fuse is tripped. High the following malfunctions: voltage supplied on the hot side may cause electric shock. Turn the power off ●Motor does not rotate properly at high-speed (insufficient torque) immediately and request service. ●Motor startup and stopping is slow. Note: ● Keep the voltage Vo between DC 5V and DC 24V. When they are equal to DC 5V, the external resistances R1 and R2 are not necessary. When they are above DC 5V, connect R1 to keep the current bellow 20mA, and connect R2 to keep the current bellow 10mA. �4 2 2 ● Use twisted-pair wire of 3�10 in (0.2mm ) or thicker and 6.6 feet (2m) or iess in length for the signal line. �4 2 2 ● Use wire 7.8�10 in (0.5mm ) or thicker for motor lines (when extended) and �3 2 2 power supply lines, and use 1.2�10 in (0.75mm ) or thicker for the wire for the protective earthing line. ● Use spot grounding for the grounding of the driver and external controller. ● Signal lines should be kept at least 3.94inch (10cm) away from power lines (power supply lines and motor lines). Do not bind the signal line and power line together. Use open collector transistors (sink type) for the signal output sections of the controller. 2000-2001 ORIENTAL MOTOR GENERAL CATALOG B-103 � WIRING DIAGRAMS ●Single-Phase 200-230VAC Input Driver Controller V0 (�DC5V~24V) CN1 Twisted Pair Line 1 CW Pulse Signal 5 Phase Stepping Motor (Pulse Signal) 2 R1 3 Input CCW Pulse Signal Signals Lead Wire TB1 (Rotation Direction 4 Signal) R1 Blue BLUE 10 Red RED All Winding Off Signal Orange 5 ORANGE R1 Green GREEN Black BLACK V0 (�DC5V~24V) NC R NC R2 11 Single Phase L Excitation Timing 200� �10% 200–230V AC �15% 230V AC Signal R N 50/60Hz Output Signals R2 12 Overheat Signal 20 GND Protective Earth (P.E.) � Power Supply Caution The driver incorporates double-pole/neutral fusing for the power input. If the Use a power supply that can supply sufficient input current. driver POWER LED is off, it is possible that only the neutral fuse is tripped. High When power supply capacity is insufficient, a decrease in motor output can cause voltage supplied on the hot side may cause electric shock. Turn the power off the following malfunctions: immediately and request service. ●Motor does not rotate properly at high-speed (insufficient torque) ●Motor startup and stopping is slow. Note: ● Keep the voltage Vo between DC 5V and DC 24V. When they are equal to DC 5V, the external resistances R1 and R2 are not necessary. When they are above DC 5V, connect R1 to keep the current bellow 20mA, and connect R2 to keep the current bellow 10mA. �4 2 2 ● Use twisted-pair wire of 3�10 in (0.2mm ) or thicker and 6.6 feet (2m) or iess in length for the signal line. �4 2 2 ● Use wire 7.8�10 in (0.5mm ) or thicker for motor lines (when extended) and �3 2 2 power supply lines, and use 1.2�10 in (0.75mm ) or thicker for the wire for the protective earthing line. ● Use spot grounding for the grounding of the driver and external controller. ● Signal lines should be kept at least 3.94inch (10cm) away from power lines (power supply lines and motor lines). Do not bind the signal line and power line together. Use open collector transistors (sink type) for the signal output sections of the controller. B-104 2000-2001 ORIENTAL MOTOR GENERAL CATALOG � DESCRIPTION OF INPUT/OUTPUT SIGNALS 1. Pulse Input � Input circuit and sample connection • Keep the pulse signal at "photocoupler OFF" when no pulse is being input. Driver Controller V0 • The minimum interval time when changing rotation direction is 10µs. CN1 Open-collector 220ΩThis value varies greatly depending on the motor type, pulse frequency Output 1 and load inertia. It may be necessary to increase this time interval. • In 1-pulse input mode, leave the pulse signal at rest ("photocoupler R CW(Pulse) 2 OFF") when changing rotation directions. 20mA max. 220Ω 3 2. A.W.OFF (All Windings Off) Input R CCW(CW/CCW) � Input circuit and sample connection 4 20mA max. Driver Controller VO Open-collector CN1 220ΩOutput 10 Keep the voltage between DC 5V and DC 24V. When voltage is equal to DC 5V, external resistance (R) is not necessary. When voltage is above DC 5V, connect external resistance (R) and keep the input current R A.W.OFF below 20mA. 5 20mA max. 1. 1-Pulse Input Mode Pulse Signal "Pulse" signal is input to the pulse signal terminal. When the photocoupler state changes from "ON" to "OFF", the motor rotates one Keep the voltage between DC 5V and DC 24V. step. The direction of rotation is determined by the following rotation When voltage is equal to DC 5V, external resistance (R) is not necessary. When direction signal. voltage is above DC 5V, connect external resistance (R) and keep the input current below 20mA. Rotation Direction Signal The "Rotation Direction" signal is input to the rotation direction signal input terminal. A "photocoupler ON" signal input commands a When the "All Windings Off" signal is in the "photocoupler ON" state, the clockwise direction rotation. A "photocoupler OFF" signal input current to the motor is cut off and motor torque is reduced to zero. The commands a counterclockwise direction rotation. motor output shaft can then be rotated freely by hand. 2. 2-Pulse Input Mode CW Pulse Signal When the "All Windings Off" signal is in the "photocoupler OFF" state, the When the photocoupler state changes from "ON" to "OFF", the motor motor holding torque is proportional to the current set by the current rotates one step in the clockwise direction. adjustment rotary switches. During motor operation, be sure to keep the CCW Pulse Signal signal in the "photocoupler OFF" state. When the photocoupler state changes from "ON" to "OFF", the motor This signal is used when moving the motor by external force or manual rotates one step in the counterclockwise direction. home position is desired. If this function is not needed, it is not necessary to connect this terminal. CW and CCW refer to clockwise and counterclockwise direction respectively, from a reference point of facing the motor output shaft. Switching the "All Windings Off" signal from "photocoupler ON" to � Pulse Waveform Characteristics "photocoupler OFF" does not alter the excitation sequence. (Photocoupler state corresponding the input pulse) When the motor shaft is manually adjusted with the "All Windings Off" µ signal input, the shaft will shift up to �3.6˚ from the position set after minimum Pulse Signal the "All Windings Off"f signal is released. Photocoupler ON 90% 10% Photocoupler OFF � Manual Setting of the Home Position 2µs maximum 2µs maximum 10µs 10µs Input the "All Windings Off" signal, set the motor to the desired position, 5µs minimum minimum minimum then release the "All Windings Off" signal. Rotation Direction Signal Photocoupler ON All Windings Off Signal Input Photocoupler OFF The shaded area indicates when the photocoupler is ON. The motor moves when the photocoupler state changes from ON to OFF as indicated by the arrow. Pulse Signal Characteristics All Windings Off • The pulse voltage is 4~5V in the "photocoupler ON" state, and 0~0.5V in Home Position Set Signal Release Photocoupler ON the "photocoupler OFF" state. All Windings Off OFF ON OFF Signal • Input pulse signals should have a pulse width over 5µs, pulse rise/fall Photocoupler OFF below 2µs, and a pulse duty below 50%. 2000-2001 ORIENTAL MOTOR GENERAL CATALOG B-105 3. TIM. (Excitation Timing) Output 4. O. HEAT (Overheat) Output � Output circuit and sample of connection � Output Circuit and Sample Connection Controller Controller V0 V0 Driver Driver CN1 CN1 R R 12 11 20 20 10mA max. 10mA max. Keep the voltage between DC 5V and DC 24V. Keep the voltage between DC 5V and DC 24V. Keep the current below 10mA. If the current exceeds 10mA, connect external Keep the current below 10mA. If the current exceeds 10mA, connect external resistance (R). resistance (R). The "Excitation Timing" signal is output to indicate when the motor The "Overheat" signal is output to protect the driver from heat damage excitation (current flowing through the winding) is in the initial stage if the internal temperature of the driver rises above 176˚F (80˚C). (step "0" at power up). When connected as shown in the example connection, the signal will The "Excitation Timing" signal can be used to increase the accuracy of be "photocoupler OFF" during normal conditions, and "photocoupler home position detection by setting the mechanical home position of ON" when the temperature exceeds 176˚F (80˚C). your equipment (for example, a photo-sensor) to coincide with the excitation sequence initial stage (step "0"). When the "Overheat" signal is output, turn the driver power OFF, then The motor excitation stage changes simultaneously with pulse input, adjust the operating conditions (ambient temperature, driver/ and returns to the initial stage for each 7.2˚ rotation of the motor controller settings), or use a fan to cool the driver. After taking output shaft. appropriate measures, turn the power ON. Turning the power ON will When power is turned ON, the excitation sequence is reset to step "0". reset the "Overheat" signal and release the "Automatic Current Off" condition. The TIM. LED lights when the "Excitation Timing" signal is output. While the motor is rotating, the LED will turn ON and OFF at a high speed and will appear to be continuously lit. The "Excitation Timing" signal is output simultaneously with a pulse input each time the excitation sequence returns to step "0". The excitation sequence will complete one cycle for every 7.2˚ rotation of the motor output shaft. Full Step (the switch is set to F position): Signal is output once every 10 pulses. Half Step (the switch is set to H position): Signal is output once every 20 pulses. Timing Chart at Full Step 12 3 4 5 6 78 9101112 CW Pulse 12 CCW Pulse Excitation Timing Output (Step) 0123456789012 10 B-106 2000-2001 ORIENTAL MOTOR GENERAL CATALOG
Frequently asked questions
What makes Elite.Parts unique?

What kind of warranty will the UDK5114NW2-M have?

Which carriers does Elite.Parts work with?

Will Elite.Parts sell to me even though I live outside the USA?

I have a preferred payment method. Will Elite.Parts accept it?

Why buy from GID?
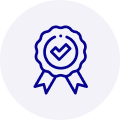
Quality
We are industry veterans who take pride in our work
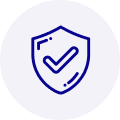
Protection
Avoid the dangers of risky trading in the gray market
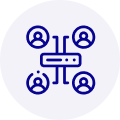
Access
Our network of suppliers is ready and at your disposal
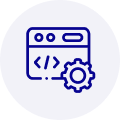
Savings
Maintain legacy systems to prevent costly downtime
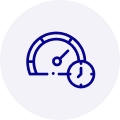
Speed
Time is of the essence, and we are respectful of yours
What they say about us
FANTASTIC RESOURCE
One of our top priorities is maintaining our business with precision, and we are constantly looking for affiliates that can help us achieve our goal. With the aid of GID Industrial, our obsolete product management has never been more efficient. They have been a great resource to our company, and have quickly become a go-to supplier on our list!
Bucher Emhart Glass
EXCELLENT SERVICE
With our strict fundamentals and high expectations, we were surprised when we came across GID Industrial and their competitive pricing. When we approached them with our issue, they were incredibly confident in being able to provide us with a seamless solution at the best price for us. GID Industrial quickly understood our needs and provided us with excellent service, as well as fully tested product to ensure what we received would be the right fit for our company.
Fuji
HARD TO FIND A BETTER PROVIDER
Our company provides services to aid in the manufacture of technological products, such as semiconductors and flat panel displays, and often searching for distributors of obsolete product we require can waste time and money. Finding GID Industrial proved to be a great asset to our company, with cost effective solutions and superior knowledge on all of their materials, it’d be hard to find a better provider of obsolete or hard to find products.
Applied Materials
CONSISTENTLY DELIVERS QUALITY SOLUTIONS
Over the years, the equipment used in our company becomes discontinued, but they’re still of great use to us and our customers. Once these products are no longer available through the manufacturer, finding a reliable, quick supplier is a necessity, and luckily for us, GID Industrial has provided the most trustworthy, quality solutions to our obsolete component needs.
Nidec Vamco
TERRIFIC RESOURCE
This company has been a terrific help to us (I work for Trican Well Service) in sourcing the Micron Ram Memory we needed for our Siemens computers. Great service! And great pricing! I know when the product is shipping and when it will arrive, all the way through the ordering process.
Trican Well Service
GO TO SOURCE
When I can't find an obsolete part, I first call GID and they'll come up with my parts every time. Great customer service and follow up as well. Scott emails me from time to time to touch base and see if we're having trouble finding something.....which is often with our 25 yr old equipment.
ConAgra Foods