MOTION CONTROL ENGINEERING Motion 4000
Datasheet
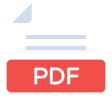
Motion-Control-Engineering-Motion-2000-Traction-Elevator-Controller-datasheet1-1231111759.pdf
109 KiB
Extracted Text
Specification Document SD002 A1, 02/09 MOTION 4000 Traction Elevator Control Motion Control Engineering 11380 White Rock Road Rancho Cordova, CA 95742 Voice: 916 463 9200 FAX: 916 463 9201 www.mceinc.com This specification is for the MCE Motion 4000 Traction Elevator Controller and includes: Product photographs Product specifications table Compliance Motion Control Engineering corporate information Controller features Specifications Text Monitoring options Building Management System interface Product Photographs Product Specifications Table Maximum car speed 400 fpm, 2.0 m/s Configuration Simplex, Duplex, Group up to 6 cars Landings 32 landings, 64 openings maximum Motor control (induction or permanent magnet capable) TorqMax F5 VVVF Drive Landing/Positioning system Encoded tape, absolute position, full distance feedback Call Registration Serial COP or Discrete COP, Discrete Hall Call Power requirement 208 – 600 VAC, 50/60 Hz, 3-phase Environment 32 - 104º F, 0 - 40º C; Humidity 95% non-condensing *Standard enclosure (height includes floor mount legs) 42” w x 72” h x 16” d (1067 x 1829 x 406 mm) with knock-outs **Machine room-less enclosure 16” w x 75.5” h x 8” d (406 x 1918 x 203 mm) with knock-outs **Drive enclosure for machine room-less 16” w x 24.5” h x 13” d (406 x 622 x 330 mm) handles folded Available NEMA enclosures NEMA 4, 4X, 12 * Variations available * * Machine room-less cabinets can be sized to include drive if desired. Contact MCE. Page 1 of 15 Specification Document SD002 A1, 02/09 MOTION 4000 Traction Elevator Control Motion Control Engineering 11380 White Rock Road Rancho Cordova, CA 95742 Voice: 916 463 9200 FAX: 916 463 9201 www.mceinc.com Compliance ASME A17.1-2007/CSA B44-07 ASME A17.5-2007/CSA B44.1-07 NEC C22.1 CEC C22.1 BS 5655/EN 81 AS 1735 EN12015, EN12016 Title III, Americans with Disabilities Act CE MCE Corporate Information MCE, Motion Control Engineering, is an established provider of elevator controls and peripheral equipment, boasting a track record of steady growth and industry-leading innovation for nearly thirty years. MCE’s primary manufacturing facility in Rancho Cordova, California, service and sales offices, and contract manufacturing facilities around the world provide a time-tested, global presence. MCE is part of a family of companies operating under the Kinetek corporate banner. Kinetek companies are major players in many industrial arenas, stretching from elevator controls and lift machines to door operators and small industrial motors and controls to electric vehicle and consumer product components. Kinetek’s manufacturing strength and global presence help ensure the long term durability of the MCE brand. MCE is the largest manufacturer of non-proprietary elevator controls, with an installed base of over 150,000 worldwide. Non-proprietary means that building owners are not locked into a specific service provider by long-term contracts and special, proprietary tools. Our non-proprietary philosophy ensures building owners the freedom to choose the installer and service provider of their choice, without constraint. MCE controls never require special, proprietary tools and MCE technical support is available to all service providers, without regard to their corporate affiliation. Over the life of a building, our non-proprietary approach to elevator controls by itself can save a large building owner hundreds of thousands of dollars but MCE quality and MCE controls provide many other important benefits as well. Page 2 of 15 Specification Document SD002 A1, 02/09 MOTION 4000 Traction Elevator Control Motion Control Engineering 11380 White Rock Road Rancho Cordova, CA 95742 Voice: 916 463 9200 FAX: 916 463 9201 www.mceinc.com Controller Features High Level Non-Proprietary (open architecture, universally serviceable, manuals/drawings provided) Minimized hoistway switch requirements (slowdown, emergency terminal, hoistway access limit switches and leveling magnets not required) Hoistway and System Configuration (on board interface or optional CAN wired hand held) Diagnostics (on board interface or optional CAN wired hand held) CAN Bus communication between boards and between major components Universal I/O (24V, 48V, 110V, or 120V AC or DC), electrically protected Status Indicators (LCD messages and individual status LEDs) External communications: TCP/IP Ethernet, CAN Operating Modes Simplex/Duplex/Group Automatic: Selective Collective/Single Button Collective/Single Automatic Push Button Inspection: Machine Room, In Car, Car Top, Access Fire Service Operation (multiple pre-configured code-specific selections) Hospital Operation Massachusetts EMT Operation Sabbath Swing Operation (from group or duplex control) Recall Operation Attendant Operation Earthquake Operation (ASME/ANSI or California) Emergency Power Operation Car Recall Capture for Test Test Mode Emergency Power Options Building Emergency Generator MCE Traction Auxiliary Power Supply (TAPS) Monitoring Options iMonitor: Local, LAN/WAN, Remote (high-speed Internet) Cars/Groups/Sites iReport: System logging, report generation, archiving, automated notification BMS-LINK: Monitoring and control through Building Management System software Page 3 of 15 Specification Document SD002 A1, 02/09 MOTION 4000 Traction Elevator Control Motion Control Engineering 11380 White Rock Road Rancho Cordova, CA 95742 Voice: 916 463 9200 FAX: 916 463 9201 www.mceinc.com Load Weighing Rope Strain Gauge, analog or discrete inputs K-Tech crosshead flex weigher, analog Code Compliance The elevator controller shall use a microprocessor based logic system and shall comply with all applicable elevator and electrical safety codes including: (Contact MCE if a necessary code is not listed below.) For the United States and Canada: ASME A17.1-2007/CSA B44-07 ASME A17.5-2007/CSA B44.1-2007 NEC C22.1 CEC C22.1 CSA Certification CE Marking For Australia: AS 1735 For the United Kingdom: BS 5655 For Europe EN 81 ADA Requirements The elevator shall comply with ICC/ANSI A117.1, the American National Standard for Accessible and Usable Buildings and Facilities. Leveling Accuracy: The controller shall have a self-leveling feature that shall automatically bring the car to floor landings within a tolerance of 0.25" (6.35 mm) or better under all loading conditions up to the rated load. Hall Lanterns: The controller shall have outputs to drive the visible and audible signals that are required at each hoistway entrance to indicate which elevator car is answering a call. Audible signals shall sound once for up, twice for down. (In-car lanterns located in cars, visible from the vicinity of hall call buttons, and conforming to the above requirements, shall be acceptable.) Car Position Indicators: The controller shall have a position indicator output to drive the required position indicator which shall indicate the corresponding floor numbers as the car passes or stops at a floor. An audible signal shall sound as the position indicator changes floors. Page 4 of 15 Specification Document SD002 A1, 02/09 MOTION 4000 Traction Elevator Control Motion Control Engineering 11380 White Rock Road Rancho Cordova, CA 95742 Voice: 916 463 9200 FAX: 916 463 9201 www.mceinc.com Optional: The controller shall have a voice annunciator output to facilitate announcement of car direction and floor number. (Voice annunciator is required for destination-based dispatching elevators or for elevators with speeds greater than 200 fpm). General All power feed lines to the brake shall be opened by an electro-mechanical switch. A single ground, short circuit or solid- state control failure shall not prevent application of the brake. The automatic leveling zone shall not extend more than 6" (152.4 mm) above or below the landing level, nor shall the doors begin to open until the car is within 6" (152.4 mm) of the landing. In addition, the inner leveling zone shall not extend more than 3" (76.2 mm) above or below the landing. The car shall not move if it stops outside the inner leveling zone unless the doors are fully closed and locked. The system shall use an automatic two-way leveling device to control the leveling of the car to within 0.25" (6.35 mm) or better above or below the landing sill. Overtravel, undertravel or rope stretch must be compensated for and the car brought level to the landing sill. The closed loop feedback power control shall be arranged to continuously monitor the actual elevator speed signal from the velocity transducer and compare it with the intended speed signal to verify proper and safe operation of the elevator. During operation of the elevator with an overhauling load (empty car up or loaded car down), precision speed control shall be obtained by the regulation system used in the power control. The power control shall have the capability to maintain regulation under varying loads. The controller shall provide stepless acceleration and deceleration and smooth operation at all speeds. The system shall provide the required electrical operation of the elevator control system including automatic application of the brake, which shall bring the car to rest in the event of a power failure. The controller shall include absolute floor encoding which, upon power up, shall move the car to the closest floor to identify the position of the elevator. With absolute floor encoding it is not necessary to travel to a terminal to establish floor position. The controller shall use a variable voltage, variable frequency drive to control three-phase AC induction and Permanent Magnet AC motors. The drive shall use a three-phase, full-wave bridge rectifier and capacitor bank to provide a DC voltage bus for the solid- state inverter. The drive shall use power semiconductor devices and pulse width modulation with a carrier frequency of not less than 8 kHz to synthesize the three-phase, variable voltage, variable frequency output to operate the hoist motor in an essentially synchronous mode. Page 5 of 15 Specification Document SD002 A1, 02/09 MOTION 4000 Traction Elevator Control Motion Control Engineering 11380 White Rock Road Rancho Cordova, CA 95742 Voice: 916 463 9200 FAX: 916 463 9201 www.mceinc.com The drive shall have the capability of being adjusted or programmed to achieve the required motor voltage, current and frequency to properly match the characteristics of the AC elevator hoist motor. The drive shall not create excessive audible noise in the elevator motor. The drive shall be a heavy-duty type, capable of delivering sufficient current to accelerate the elevator to contract speed with rated load. The drive shall provide speed regulation appropriate to the motor type. A means shall be provided for removing regenerated power from the drive DC power supply during dynamic braking. This power shall be dissipated in a resistor bank which is an integral part of the controller. Failure of the system to remove the regenerated power shall cause drive output to be removed from the hoist motor. A contactor shall be used to disconnect the hoist motor from the output of the drive unit each time the elevator stops. This contactor shall be monitored. The elevator shall not start again if the contactor has not returned to the de-energized position when the elevator stops. All power feed lines to the brake shall be opened by an electro-mechanical switch. A single ground, short circuit or solid- state control failure shall not prevent application of the brake. The controller shall provide stepless acceleration and deceleration and smooth operation at all speeds. The controls shall be arranged to continuously monitor the performance of the elevator so that, if car speed exceeds 150 fpm during access, inspection, or leveling, the car shall shut down immediately, requiring a reset operation. The controller shall include absolute floor encoding which, upon power up, shall move the car to the closest floor to identify the position of the elevator. With absolute floor encoding it is not necessary to travel to a terminal to establish floor position. The controller shall have an RFI Filter to reduce EMI and RFI noise. Optional - Failure of the brake to lift as detected by a mechanical switch (if provided) shall cause the control system to take the elevator out of service at the next stop where it shall remain out of service until the condition is corrected. Hoistway Equipment Minimization The control system shall allow slowdown, emergency terminal, and hoistway access limit switches to be eliminated. These switches shall exist as virtual switches in system software. The control system shall allow leveling magnets and/or vanes to be eliminated. Page 6 of 15 Specification Document SD002 A1, 02/09 MOTION 4000 Traction Elevator Control Motion Control Engineering 11380 White Rock Road Rancho Cordova, CA 95742 Voice: 916 463 9200 FAX: 916 463 9201 www.mceinc.com Programmable Logic All available programming options (consult your MCE Sales Representative) or parameters shall be field programmable, without need for any external device or knowledge of any programming languages. Programmable options and parameters shall be stored in nonvolatile memory. At a minimum, there shall be a 32-character alphanumeric display used for programming and diagnostics. Programmable parameters and options shall include, but are not limited to, the following: Number of Stops/Openings Served (Each Car) Simplex/Duplex/Group Single Automatic PushbuttonSelective Collective/Single Button Collective Programmable Fire Code Options/Fire Floors (Main, Alternates) Floor Encoding (Absolute PI) Digital Position Indicators/Single Wire Position Indicators Programmable CE Microcom floor labels Programmable Door Times Programmable Motor Limit Timer Programmable Car Fan and Light Timer Door Nudging, Automatic and Fire Operation Emergency Power Parking Floors Lobby Floor Door Pre-opening Hall or Car Gong Selection Retiring Cam Option for Freight Doors Independent Rear Doors Standard Security Emergency Hospital Service Attendant Service Anti-nuisance - Light Load Weighing and Photo Eye High Speed Inspection Enable Door behavior selections Door type selection Fault Bypass – Inspection Operation Fault Bypass – Automatic Operation Page 7 of 15 Specification Document SD002 A1, 02/09 MOTION 4000 Traction Elevator Control Motion Control Engineering 11380 White Rock Road Rancho Cordova, CA 95742 Voice: 916 463 9200 FAX: 916 463 9201 www.mceinc.com Field selectable, preprogrammed Fire Service operations compliant with the following Fire Codes: ASME A17.1 California Hawaii Massachusetts 34 PA Code CH7 Chicago 2001 Chicago Old City of Denver City of Detroit City of Houston New York City Veterans Administration Washington DC Australia British Standard Canadian B44 Non-Proprietary Equipment Only universally “Serviceable and Maintainable,” Non-proprietary elevator control equipment shall be accepted. Non- proprietary standards recognize specific owner’s rights: The right to all information needed for diagnosis, service, and repair. The right to access on-board computers, including the information they store and the ability to diagnose, repair, and/or reprogram these systems. The right to select from among multiple sources for maintenance and repair in a competitive marketplace. Environmental Considerations The elevator control shall be capable of operating within the following environmental conditions: Ambient temperature: 32°F to 104°F (0°C degrees to 40°C degrees). Humidity: Non-condensing up to 95% Altitude: Up to 7500 feet (2286 m) Motion Control Engineering specializes in control products for adverse environmental conditions. For example, dust-proof, water-proof, corrosion-resistant, or air conditioned controller cabinets can be engineered to meet specific applications. Higher temperature range compatibility is available. Please contact MCE Sales Engineering for details. Page 8 of 15 Specification Document SD002 A1, 02/09 MOTION 4000 Traction Elevator Control Motion Control Engineering 11380 White Rock Road Rancho Cordova, CA 95742 Voice: 916 463 9200 FAX: 916 463 9201 www.mceinc.com Building and System Configuration The elevator controller shall be microprocessor based and designed specifically for elevator applications. Elevator and drive logic shall be implemented independently of safety functions. Elevator logic shall be implemented to facilitate tight coordination between subsystems and enhance reliability. The implementation shall utilize a real-time, multi-tasking operating system to allow the processors to simultaneously execute elevator control logic, drive control logic, operator interface logic, and communication support. The elevator controller shall have an independent safety system in order to implement safety features required by code. The safety system shall incorporate check redundant, multi-processor, multi-path, solid-state, ASME compliant implementation that meets CSA and CE standards. The elevator controller shall be configured and packaged in such a way that external “jumpers” cannot be used (intentionally or unintentionally) while the elevator is running in any passenger mode of operation. Non-passenger modes of operation shall be provided, along with means to bypass safety functionality, to allow inspection testing and other setup and/or troubleshooting operations. The elevator control logic configuration shall be fully field programmable. Changes in number of floors, I/O configuration, starter setup, eligibility etc. shall not require the replacement/reprogramming of EEPROMs or other storage devices. Further, changes in the controller configuration shall be user adjustable in the field. Diagnostics The control system shall provide comprehensive means of accessing the computer memory for elevator diagnostic purposes. It shall have permanent indicators for important elevator status conditions as an integral part of the controller. The microprocessor boards shall be equipped with on-board diagnostics for ease of troubleshooting and field programmability of specific control variables. Field changes shall be stored permanently, using nonvolatile memory. The microprocessor board shall provide the features listed below: On-board diagnostic switches and an alphanumeric display to provide user friendly interaction between the mechanic and the controller. An on-board event log shall store and display time-stamped events for diagnostic purposes. (Viewable only with monitoring software.) An on-board real time clock shall display the time and date and be adjustable by means of on-board switches. Field programmability of specific timer values (i.e., door times, etc.) may be viewed and/or altered through on- board switches and pushbuttons. Page 9 of 15 Specification Document SD002 A1, 02/09 MOTION 4000 Traction Elevator Control Motion Control Engineering 11380 White Rock Road Rancho Cordova, CA 95742 Voice: 916 463 9200 FAX: 916 463 9201 www.mceinc.com The elevator controller shall have extensive diagnostic capability. A built-in LCD display or equivalent shall allow access to major user functions and diagnostic features. The display shall be a multi-character, multi-line type with associated keypad to allow users to enter information. The display shall show data and menus in readily understood character format. No numeric, hexadecimal, or binary codes are acceptable. Dedicated indicators shall be provided in a conspicuous location on the elevator controller to indicate important system statuses, such as when the safety string is made, when the door locks are made, when the elevator is on Inspection/Access, etc. In addition, other special or error conditions detected by the main processor or safety subsystem shall be displayed. CAN Bus Connectivity Circuit boards within the controller shall communicate through CAN Bus connections for reliable performance and simplified board replacement. Power for individual circuit boards shall also be distributed through the CAN Bus connection. Communication and power connection shall radiate from a central, multi-connection point such that single- point board failure shall not affect operation of other boards. Universal I/O Field I/O boards shall be universal in that 24V to 120V AC or DC connections shall be accepted without requirement for unique circuit boards for each. I/O boards shall provide built-in current limiting protection. Intended Operation of Critical Components Failure of any single magnetically operated switch, contactor, or relay to release in the intended manner; the failure of any static control device, speed measuring circuit, or speed pattern generating circuit to operate as intended; the occurrence of a single accidental ground or short circuit shall not permit the car to start or run if any hoistway door or gate interlock is unlocked or if any hoistway door or car door or gate contact is not in the made position. Furthermore, while on car top inspection or hoistway access operation, failure of any single magnetically operated switch, contactor or relay to release in the intended manner, failure of any static control device to operate as intended or the occurrence of a single accidental ground, shall not permit the car to move even with the hoistway door locks and car door contacts in the closed or made position. Page 10 of 15 Specification Document SD002 A1, 02/09 MOTION 4000 Traction Elevator Control Motion Control Engineering 11380 White Rock Road Rancho Cordova, CA 95742 Voice: 916 463 9200 FAX: 916 463 9201 www.mceinc.com Status Indicators Dedicated permanent status indicators shall be provided on the controller to indicate when the safety string is made, when the door locks are made, when the elevator is operating at high speed, when the elevator is on independent service, when the elevator is on Inspection or Access, when the elevator is on fire service, when the elevator out of service timer has elapsed, and when the elevator has failed to successfully complete its intended movement. A means shall be provided to display other special or error conditions detected by the microprocessor. Every field connection input or output shall have a dedicated LED such that no volt meter or other test equipment is required to see when and input or output is active. Out of Service Timer An out of service timer (T. O. S.) shall be provided to take the car out of service if the car is delayed in leaving the landing while calls exist in the system. High or Low Speed Inspection A selection shall be provided on the controller to select high or low speed during access or inspection operation as long as contract speed does not exceed 150 feet per minute. Door Operation Door protection timers shall be provided for both opening and closing directions to protect the door motor and help prevent the car from getting stuck at a landing. The door open protection timer shall cease attempting to open the door after a predetermined time if the doors are prevented from reaching the open position. In the event that the door closing attempt fails to make up the door locks after a predetermined time, the door close protection timer shall reopen the doors for a short time. If, after a predetermined number of attempts, the doors cannot successfully be closed, the doors shall be opened and the car removed from service. A minimum of four different door standing open times shall be provided. A car call time value shall predominate when only a car call is canceled. A hall call time value shall predominate whenever a hall call is canceled. In the event of a door reopen caused by the safety edge, photo eye, etc., a separate short door time value shall predominate. A separate door standing open time shall be available for lobby return. If the doors are prevented from closing for longer than a predetermined time, door nudging operation shall cause the doors to move at slow speed in the closed direction. A buzzer shall sound during nudging operation. Page 11 of 15 Specification Document SD002 A1, 02/09 MOTION 4000 Traction Elevator Control Motion Control Engineering 11380 White Rock Road Rancho Cordova, CA 95742 Voice: 916 463 9200 FAX: 916 463 9201 www.mceinc.com Door Pre-opening When selected, this option shall start to open the doors when the car is in final leveling, 3" (76.2 mm) from the floor. If pre- opening is not selected, the doors shall remain closed until the car is at the floor, at which time the doors shall commence opening. Car and Hall Call Registration Car and hall call registration and lamp acknowledgment shall be by means of a single wire per call, in addition to the ground and the power bus. Systems that register the call with one wire, and light the call acknowledgment lamp with a separate wire can be accommodated. The user shall be able to register car calls via the on-board LCD display and keypad. Fire Service Operation Fire Phase I emergency recall operation, alternate level Phase I emergency recall operation and Phase II emergency in- car operation shall be provided according to applicable local codes. Independent Service Independent service operation shall be provided in such a way that actuation of a key switch in the car operating panel will cancel any existing car calls, and hold the doors open at the landing. The car will then respond only to car calls. Car and hoistway doors will only close with constant pressure on a car call pushbutton or door close button. While on independent service, hall arrival lanterns or jamb mounted arrival lanterns shall be inoperative. Simplex Selective Collective Operation Simplex selective collective automatic operation shall be provided for all single car installations. Operation of one or more car or hall call pushbuttons shall cause the car to start and run automatically, provided the hoistway door interlocks and car door contacts are closed. The car shall stop at the first car or hall call set for the direction of travel. Stops shall be made in the order in which car or hall calls set for the direction of travel are reached, regardless of the order in which they were registered. If only hall calls set for the opposite direction of travel of the elevator exist ahead of the car, the car shall proceed to the most distant hall call, reverse direction, and start collecting the calls. Single Automatic Pushbutton Operation Single automatic pushbutton operation shall be user selectable if desired. Single Button Collective Operation Single button collective operation shall be user selectable if desired. Page 12 of 15 Specification Document SD002 A1, 02/09 MOTION 4000 Traction Elevator Control Motion Control Engineering 11380 White Rock Road Rancho Cordova, CA 95742 Voice: 916 463 9200 FAX: 916 463 9201 www.mceinc.com Simplex Home Landing Operation Optional: If no calls are registered, this operation shall cause the car to travel to a predetermined home landing floor and stop without door operation. If the car is traveling to the home landing and a call appears from the opposite direction, the car shall slow down, stop, and then accelerate in the opposite direction, toward the call. The home landing function shall cease instantly upon the appearance of a normal call and the car shall proceed nonstop in response to any normal call. Duplex Operation For duplex configurations, each elevator shall have its own computer and dispatching algorithm. Should one computer lose power or become inoperative, the other shall be capable of accepting and answering all hall calls. When both computers are in operation, only one shall assume the role of dispatching hall calls to both elevators. Leveling The car shall be equipped with two-way leveling to automatically bring the car level at any landing, within the required range of leveling accuracy, with any load up to full load. Test Switch A controller test switch shall be provided. In the test position, this switch shall allow independent operation of the elevator with the door open function deactivated for purposes of adjusting or testing the elevator. The elevator shall not respond to hall calls and shall not interfere with any other car in a duplex or group installation. Inspection To enhance safety, an inspection switch, enable switch, and an up/down toggle switch shall be provided in the controller and on the car top to place the elevator on inspection operation and allow the user to move the car. Activation of the car top inspection switch shall render the controller inspection switch inoperative. Uncanceled Call Bypass A timer shall be provided to limit the amount of time a car is held at a floor due to a defective hall call or car call, including stuck pushbuttons. Call demand at another floor shall cause the car, after a predetermined time, to ignore the defective call and continue to provide service in the building. Anti-nuisance (Photo Eye) The controller shall cancel all remaining car calls, if a user-determined number of car calls are answered without the computer detecting a change in the photo eye input (indicating that no one is passing through the car door). Page 13 of 15 Specification Document SD002 A1, 02/09 MOTION 4000 Traction Elevator Control Motion Control Engineering 11380 White Rock Road Rancho Cordova, CA 95742 Voice: 916 463 9200 FAX: 916 463 9201 www.mceinc.com Absolute Floor Encoding The controller shall include absolute floor encoding, which upon power up, shall move the car to the closest floor to identify the position of the elevator. Controller Optional Features Hand-held User Interface A hand-held user interface with all the functionality of the on-board LCD display and keypad shall be available. The hand- held interface shall allow the user system access via any system CAN Bus connection in the controller, from the car top, or in the car (if a CAN connection has been made available here). The hand-held interface shall connect to a standard PC, allowing system software updates to be delivered to the PC via Internet download or email attachment, transferred to the hand-held and uploaded to the elevator or group controller. Peripherals As an integral part of the controller, the capability shall be provided to connect onsite or remote computer peripherals via Ethernet for additional adjustment, diagnostic, monitoring, or control capabilities. Landing/Positioning System Information The landing/positioning system shall use a Gray code, magnetically permanent encoded tape and two, independent sensor heads in a single housing for absolute position control under all powered conditions. The tape shall provide a unique code for every 1mm of travel. A third, independent system shall provide speed feedback directly from the hoist motor. The system shall continuously compare inputs from the three independent systems to assure accuracy and safety. NEMA Landing/Positioning System NEMA rated landing/positioning systems are available for harsh hoistway conditions. Monitoring Options MCE iMonitor A PC-based system monitoring application shall be available. At a minimum, monitoring shall be capable of providing system status, car location and travel direction, operating mode, and door operation indication via Ethernet connection. The monitoring system shall be capable of remotely registering car and hall calls. The monitoring system shall be capable of initiating recall of any car in the group to the lobby floor and of placing the car into Independent Service or placing it out of service upon arrival. Page 14 of 15 Specification Document SD002 A1, 02/09 MOTION 4000 Traction Elevator Control Motion Control Engineering 11380 White Rock Road Rancho Cordova, CA 95742 Voice: 916 463 9200 FAX: 916 463 9201 www.mceinc.com Optional: A site view, with three-dimensional representations of site buildings, visual indicators of elevator status in buildings so equipped, and the ability to show status details upon indicator selection shall be available. (This option requires additional graphics development as agreed upon by MCE and the customer.) MCE iReport An Ethernet client/server based report collection and generation application shall be available. Based on historical data collected by the server, the report application shall provide, at a minimum, hall call analysis, traffic analysis, hall call log, car call log, event log, emergency log, maintenance log, and percent in service reports. The report application shall also be capable of emergency notification and report distribution through email service. Building Management System Interface An interface to a Tridium technology client Building Management System shall be available. At a minimum, this interface shall allow the management system to view car location, call status, and door operation. The interface shall also allow the management system to set any of three levels of demand-response operation, each of which shall specify a set of cars to continue running in response to curtailed energy availability or if the building owner is voluntarily reducing energy demand. The interface shall also allow selected cars to be removed from and/or returned to service as desired through the building management system. (Depending on Building Management System software, modification of system code may be required.) Third Party Monitoring Optional: An interface to an IDS Liftnet monitoring system shall be available. Service Enhancements The manufacturer shall reduce requirements for service agency spare board stocks by using common major circuit assemblies in both Traction and Hydraulic controls of the same design series. The manufacturer shall make software updates for controller and/or group control available via Internet download, email attachment, or physical EEPROM shipment. Internet download and email attachment deliveries require an optional, hand- held user interface to facilitate software transfer from the user’s PC to the elevator or group. Page 15 of 15
Frequently asked questions
What makes Elite.Parts unique?

What kind of warranty will the Motion 4000 have?

Which carriers does Elite.Parts work with?

Will Elite.Parts sell to me even though I live outside the USA?

I have a preferred payment method. Will Elite.Parts accept it?

What they say about us
FANTASTIC RESOURCE
One of our top priorities is maintaining our business with precision, and we are constantly looking for affiliates that can help us achieve our goal. With the aid of GID Industrial, our obsolete product management has never been more efficient. They have been a great resource to our company, and have quickly become a go-to supplier on our list!
Bucher Emhart Glass
EXCELLENT SERVICE
With our strict fundamentals and high expectations, we were surprised when we came across GID Industrial and their competitive pricing. When we approached them with our issue, they were incredibly confident in being able to provide us with a seamless solution at the best price for us. GID Industrial quickly understood our needs and provided us with excellent service, as well as fully tested product to ensure what we received would be the right fit for our company.
Fuji
HARD TO FIND A BETTER PROVIDER
Our company provides services to aid in the manufacture of technological products, such as semiconductors and flat panel displays, and often searching for distributors of obsolete product we require can waste time and money. Finding GID Industrial proved to be a great asset to our company, with cost effective solutions and superior knowledge on all of their materials, it’d be hard to find a better provider of obsolete or hard to find products.
Applied Materials
CONSISTENTLY DELIVERS QUALITY SOLUTIONS
Over the years, the equipment used in our company becomes discontinued, but they’re still of great use to us and our customers. Once these products are no longer available through the manufacturer, finding a reliable, quick supplier is a necessity, and luckily for us, GID Industrial has provided the most trustworthy, quality solutions to our obsolete component needs.
Nidec Vamco
TERRIFIC RESOURCE
This company has been a terrific help to us (I work for Trican Well Service) in sourcing the Micron Ram Memory we needed for our Siemens computers. Great service! And great pricing! I know when the product is shipping and when it will arrive, all the way through the ordering process.
Trican Well Service
GO TO SOURCE
When I can't find an obsolete part, I first call GID and they'll come up with my parts every time. Great customer service and follow up as well. Scott emails me from time to time to touch base and see if we're having trouble finding something.....which is often with our 25 yr old equipment.
ConAgra Foods