LENNOX M1-8
Description
Lennox M1-8 Module - The IMC BACnet Module (BP1) allows communication between the Lennox IMC M1-8 controller and a BACnet MS/TP network.
Part Number
M1-8
Price
Request Quote
Manufacturer
LENNOX
Lead Time
Request Quote
Category
PRODUCTS - M
Specifications
BACnet MS/TP
See PIC statement on Page 24.
Baud Rate
Selectable 9.6, 19.2, 38.4, 76.8K
Bus Termination
120 ohms on last module in chain. (Set jumper S1 on BP1 board if it is the last module in the chain.)
Cable Type
Twisted pair w/shield, 22AWG min. Belden type 88761 or 8761. Lennox 27M19, 94L63 or 68M25
Connector
Three-position terminal block ( + G ? )
Dimensions
1.25 x 2 x 1.25 in. (WxDxH)
Max. Cable Length
4000 ft. repeater is required for longer lengths.
Mounting
Snap-in using four nylon standoffs
Operating Temperature Range
-40F to 155F
PCB Material
FR4 Conformal coated (blue)
RH
10-95% RH non-condensing
Storage temperature Range
-40F to 185F
Transceiver
RS-485
Weight
0.7 oz. (400 grams)
Datasheet
Extracted Text
® IMC BACnet Corp. 0808−L6 Module 04/09 Supersedes 06/08 Service Literature General Table of Contents General . . . . . . . . . . . . . . . . . . . . . . . . . . . . . . . . . . . . . . 1 ® The IMC BACnet Module (BP1) allows communication Hardware Specifications . . . . . . . . . . . . . . . . . . . . . . . . 1 ® between the Lennox IMC M1−8 controller and a BACnet Network Limitations . . . . . . . . . . . . . . . . . . . . . . . . . . . . 2 Network Cable . . . . . . . . . . . . . . . . . . . . . . . . . . . . . . . . 2 MS/TP network. This module is mounted directly to the Network Bus Termination . . . . . . . . . . . . . . . . . . . . . . . 2 M1−8 Integrated Modular Controller and is not compatible Recommendations . . . . . . . . . . . . . . . . . . . . . . . . . . . . 3 with M1−7 IMC and earlier versions. Replacement for earli- Configuring IMC Unit Controller . . . . . . . . . . . . . . . . . 3 ® er remote mounted IMC BACnet modules requires re- Data Update Rate . . . . . . . . . . . . . . . . . . . . . . . . . . . . . 4 Start Up Unit Operation . . . . . . . . . . . . . . . . . . . . . . . . 4 placing existing parts with the M1−8 IMC and the new IMC Normal Unit Operation . . . . . . . . . . . . . . . . . . . . . . . . . 4 BACnet Module. Communication Check Out . . . . . . . . . . . . . . . . . . . . . 4 Connection Failure . . . . . . . . . . . . . . . . . . . . . . . . . . . . 5 ® The IMC BACnet Module has been developed to commu- Default Settings . . . . . . . . . . . . . . . . . . . . . . . . . . . . . . . 5 nicate with building automation systems that support the Device Object . . . . . . . . . . . . . . . . . . . . . . . . . . . . . . . . . 5 Analog Output Objects . . . . . . . . . . . . . . . . . . . . . . . . . 5 BACnet Application Specific Controller (B−ASC) device Analog Input Objects . . . . . . . . . . . . . . . . . . . . . . . . . . 6 profile. Analog Value Objects . . . . . . . . . . . . . . . . . . . . . . . . . . 7 Zone Sensor Setpoints . . . . . . . . . . . . . . . . . . . . . . . . . 7 ® A Lennox zone sensor, a BACnet network zone sensor, or IMC Alarm Codes . . . . . . . . . . . . . . . . . . . . . . . . . . . . . 7 ® a BACnet thermostat may be used to send the zone tem- Application Details . . . . . . . . . . . . . . . . . . . . . . . . . . . . 8 ® perature or thermostat demands to the IMC. BACnet PIC Statement . . . . . . . . . . . . . . . . . . . . . . . 24 ® Table 1. IMC BACnet Module Hardware Specifications Environment Operating Temperature Range −40F to 155F Storage temperature Range −40F to 185F RH 10−95% RH non−condensing Field Connections ® See PIC statement on Page 24. BACnet MS/TP Transceiver RS−485 Connector Three−position terminal block ( + G ˘ ) Baud Rate Selectable 9.6, 19.2, 38.4, 76.8K Cable Type Twisted pair w/shield, 22AWG min. Belden type 88761 or 8761. Lennox 27M19, 94L63 or 68M25 Max. Cable Length 4000 ft. repeater is required for longer lengths. Bus Termination 120 ohms on last module in chain. (Set jumper S1 on BP1 board if it is the last module in the chain.) Physical Dimensions 1.25 x 2 x 1.25 in. (WxDxH) Weight 0.7 oz. (400 grams) PCB Material FR4 Conformal coated (blue) Mounting Snap−in using four nylon standoffs ©2009 Lennox Industries Inc. Page 1 connect the network cable shield to the earth ground at the Network Limitations control panel, and at the G terminal of each BACnet mod- ® The Lennox IMC BACnet module does not support the ule in the chain. COV (change of value) service. Network Bus Termination ® A BACnet gateway should not be used with the L Connec- ® ® When the IMC BACnet Module is at the end of a daisy tion network if using the IMC BACnet module. chain, connect the jumper across the pins of S1 for bus ter- Network Cable ® mination (see figure 1, Detail A). Every BACnet MS/TP ® chain must have a termination at each end of the chain (ex- The IMC BACnet Module is compatible with MS/TP actly two terminations; see figure 2). EIA−485 daisy−chain networks communicating at 9.6, 19.2, ® 38.4, and 76.8 kbps. Connect the BACnet MS/TP net- ® work cable to the IMC BACnet module. It is compatible IMPORTANT with twisted pair, shielded 22AWG minimum cable such as Install S1 jumper on the END module only. Do not Belden 8761, 88761 and Lennox catalog numbers 27M19, add a resistor to each module. ® 94L63 or 68M25. A maximum of 32 IMC BACnet modules can be included per network. Up to 127 units can be con- nected using repeaters between networks. IMPORTANT The network cable should be routed using best practices to A qualified systems integrator with adequate train- avoid induced noise. Do not route alongside high voltage ing and experience is required to integrate and com- wiring or in proximity to high−voltage or high−frequency de- mission the IMC BACnet Module into a third party vices, such as ignition controls and variable frequency BACnet building automation system. A BACnet con- drives. The BACnet MS/TP recommended maximum total figuration software tool is required to commission bus length (without repeater) is 4000 ft. (1219m) applies to the BACnet network. this device. Daisy−chain each module to the network and DETAIL A BACnet RS−485 MS/TP NETWORK Jumper Jumper CONNECTION position for position for all but the the END BACnet end module module in NETWORK in daisy daisy chain chain BACNET BUS ADDRESS UNIT MODE TX IMC 1 UNIT TEST 1 HP BACnet RX S1 RECALL 2 GAS module ECTO 4 OPT1 TEMP 8 1PH BP1 OPT2 16 Jumper XMIT SHIFT (see de- HB tail A) G W1 W2 Y1 Y2 OCP P110 1 1 1 1 ® Figure 1. IMC BACnet Module (BP1) Corp. 0808−L6 04/09 Page 2 (not termi- (not termi- nated) nated) CONTROLLER/ ROUTER (terminated) (not terminated) (not terminated) (terminated) (not terminated) The configuration shown above has terminations on the IMC BACnet modules at either end and ONLY at the ends of the chain. (not termi- The configuration shown to the right has a termina- nated) tion at the controller/router on one end and a termina- CONTROLLER/ tion at the IMC BACnet module on the other end; ROUTER terminations are ONLY at the ends of the chain. (terminated) (not terminated) (terminated per mfg instructions) Figure 2. Terminating ends of daisy−chained networks IMC Settings Recommendations 1. Be sure the occupied 24 VAC input is energized by adding a jumper wire between TB1−8 and 9. In the 1. Set all BACnet devices on an MS/TP network to con- event that communication is lost between the IMC secutive MAC addresses, starting at 1, so that there BACnet module and the IMC, the IMC will operate in are no gaps between MAC address values. the occupied mode and use the occupied backup set- 2. Set Max_Master device property on all devices to points. match the largest MAC address on the network. Note, 2. By default, the IMC BACnet MAC address is set by the this could be larger than existing network to allow for address DIP switches (see figure 3). This can be any adding devices to the network with out the need to ad- value between 1 − 31. Note that a value of zero will dis- just the Max_Master property. able all IMC BACnet communications including the 3. Use ReadPropertyMultiple service instead of Read- MS/TP layer. Property service when reading multiple analog inputs A second option for setting the IMC BACnet MAC ad- or values dress is ECTO 7.26. This has the entire range of 0 − Configuring the IMC Unit Controller 127 for possible MAC addresses. A value of 128 indi- cates that the address DIP switches are used for set- ECTO Settings ting the MAC address. 3. The baud rate setting (38.4 kbps by default) can be Use the IMC pushbutton and DIP switches to manually ad- changed locally by using the mode DIP switches and just the following control parameters (see IMC manual). A pushbutton (see IMC manual). PC can also be used with Unit Controller software and a PC converter. The value of the five switches on the address DIP switch are labeled on the printed circuit board (1, 2, 4, 8, or 16). Lennox Zone Sensor Installed: Add the values of the five switches set to the ON position. 1. Set ECTO 6.01 to option 3 (zone sensor system mode See figure 3. with return air sensor back−up). 2. Set ECTO 6.17 to option 1 (continuous blower during occupied). 1 +1 3. Set ECTO 6.02−6.05 as specified (back−up occupied 2 0 EXAMPLE OF and unoccupied heating and cooling setpoints). 4 0 ADDRESS 1 8 0 ® BACnet Zone Sensor Installed: 16 0 Address is the sum 1. Set ECTO 6.01 to option 3 (zone sensor system mode =1 of values printed on with return air temperature back−up). circuit board. 2. Set ECTO 6.17 to option 1 (continuous blower during 1 +1 occupied). 2 0 EXAMPLE OF 4 +4 3. Set ECTO 5.27 to option 2 (network zone sensor op- ADDRESS 13 tion). 8 +8 16 0 BACnet Thermostat Installed: =13 Set ECTO 6.01 to option 6 (remote demand system mode with return air sensor back−up). Figure 3. Address DIP Switch ® IMC BACnet Module Page 3 IMC Version Normal Unit Operation − After BACnet Net- This module requires a M1−8 controller board. M1−7 and work Is Commissioned earlier controller boards are not compatible and parts will not assemble together. Lennox recommends replacing The occupancy of the space can be determined using any previous IMCs and BACnet modules using the latest M1−8 combination of the following control points: IMC and BACnet module. For additional information, con- � BACnet Network scheduling tact Lennox Technical Support at 800−453−6669. � Manual override The IMC scrolling display will show software version, L � Space occupancy sensor Connection address, and BACnet MAC address. Lennox Zone Sensor Installed: Data Update Rate The unit is off for up to two minutes after power−up (ECTO ® If the following BACnet variables are not updated for a pe- 5.25) unless the BACnet Network sends a setpoint. The riod of 5 minutes, the IMC will go into the back up modes unit will operate based on this setpoint and the tempera- described in the BACnet Connection Failure Section. ture from the Lennox zone sensor. Application Mode Control AO:101 (when ECTO 6.01=4−7) In addition to control points, space occupancy can be Space Temperature Input AO:113 (when ECTO 5.27=2) manually overridden using a Lennox zone sensor When either of these ECTO selections are made, it is equipped with an optional after hours switch. highly recommended the IMC get updated in less than BACnet Zone Sensor Installed: 2 minutes. The unit is off for up to five minutes after power−up unless Start Up Unit Operation − Before BACnet the BACnet Network sends a setpoint and BACnet zone Network is Commissioned sensor data. The unit will operate based on this setpoint and temperature data. Lennox Zone Sensor Installed: BACnet Thermostat Installed: Prior to commissioning, no BACnet setpoint is available. The unit remains off for up to five minutes after power−up The unit will be off. unless the BACnet Network sends a thermostat command. Two minutes after power−up (ECTO 5.25), the IMC will op- The unit will operate based on the most recently received erate the unit based on the IMC ECTO unoccupied backup thermostat command. setpoints (heating = 60°F, cooling = 85°F) and current zone temperature read by the Lennox zone sensor. Communication Check BACnet Zone Sensor Installed: Use the following table as a guide once the BACnet net- Prior to commissioning, neither BACnet setpoint nor sen- work is set up and operating. sor data are available. The unit will be off. Five minutes after power−up, the IMC will operate the unit LED Action based on the IMC ECTO unoccupied backup setpoints BACnet communication None. Indicates normal commu- (heating = 60°F, cooling = 85°F) and the current zone tem- transmit and receive nication. perature read by an additional Lennox zone sensor if LEDs flash. installed. If the Lennox zone sensor is not installed, the BACnet communication 1.Check BACnet network IMC return air temperature sensor is used as backup LEDs are off or intermit- connections. (ECTO 6.01). tently go off for periods 2. Make sure BACnet net- BACnet Thermostat Installed: of 1 second or longer. work is commissioned. Prior to commissioning, no BACnet thermostat command 3. Make sure IMC address is available. The unit will be off. DIP switches are not set to Five minutes after power−up, if no application mode com- zero. mand has been received, the IMC will operate the unit 4. Make sure each unit has a based on the IMC ECTO unoccupied backup setpoints unique MAC address in the (heating = 60°F, cooling = 85°F) and the current zone tem- range of 0 to 127. perature read by the Lennox zone sensor or the IMC return 5. Verify same baud rate on air temperature sensor depending on the choice of backup all devices. (ECTO 6.01). Corp. 0808−L6 04/09 Page 4 Connection Failure Default Settings Control following a connection failure depends on where device Max_Master = 127 the failure occurs, and which input device has been used. device Max_Info_Frames = 1 Lennox 1− During the 5 minutes following a failure, the device Object_Identifier = MAC address Zone IMC cycles on last setpoint. device Object_Name = �Lennox_IMC" + MAC address Sensor 2− IMC resets. No heating or cooling during 2 device Location = �US" minutes (ECTO 5.25) following reset. 3 − IMC cycles based on ECTO backup setpoints. device Description = �Lennox HVAC Controller" 4− Occupancy is determined by hardware input baud rate = 38.4k at TB1. Device Object BACnet 1− During 5 minutes following failure, IMC contin- Zone ues current operation: heat, cool, or off. Optional Properties Supported: Sensor 2− IMC resets. No heating or cooling during 5 Location minutes following reset. Description 3− IMC uses ECTO backup setpoints. Optional Writable Properties: 4− IMC attempts to use Lennox zone sensor as Object_Identifier backup. If this fails, IMC uses return air sensor Object_Name backup. Max_Master 5− Occupancy is determined by hardware input Max_Info_Frames at TB1. Location BACnet 1− During 5 minutes following failure, IMC contin- Description Thermo- ues current operation: heat, cool, or off. stat Property Range Restrictions: 2− IMC changes mode to use return air sensor as Object_Identifier:0−4194302 backup control method. Object_Name: up to max. 32 characters (ANSI X3.4) 3− IMC uses ECTO backup setpoints. Max_Master: 1−127 4− IMC uses return−air−sensor backup. Max_Info_Frames: 1−65535 5− Occupancy is determined by hardware input Location: up to max. 32 characters at TB1. Description: up to max. characters Analog Output Objects Optional Properties Supported: Min_Pres_Value, Max_Pres_Value Optional Writable Properties: Out_Of_Service Analog output object’s Overridden status flag set if the equivalent setpoint in the IMC is written to by some Sbus device. Table 2. Analog Output Objects List Object ID Object Name Units Min. Value Max. Value Valid Values within Range 101 Application Mode Control None 0 255 0,1,3,6,9,208,209,216,217,218,224-254,255* 102 Outdoor Air Min Pos Control Percent 0 255 all 103 Occupancy Override Control None 0 255 all 104 Occupancy Scheduler Control None 0 255 all 107 Occupancy Sensor Input None 0 255 all 108 Space Dehumidification Setpoint Percent 0 100 all 109 Temperature Setpoint (abs) Deg. F 36.25 100 all 110 Temperature Setpoint Offset Deg. F −32 31.75 all 113 Space Temperature Input Deg. F 36.25 100 all 114 Emergency Override Control None 0 255 all 115 Compressor Enable Control None 0 255 all 117 Primary Heat Enable Control None 0 255 all 119 Auxiliary Heat Enable Control None 0 255 all 123 Duct Static Setpoint In. of water 0 5 all 124 Building Static Setpoint In. of water −0.5 0.5 all 125 Discharge Air Cooling Setpoint Deg. F 40 80 −9,40-80* 126 Discharge Air Heating Setpoint Deg. F 80 140 −9,80-140* 127 Supply Fan Capacity Input Percent 33 255 all* 128 Exhaust Fan Capacity Input Percent 33 255 all 129 Set Economizer Outdoor Air Suitable None 0 255 all * see Application Details section for limitations on data ranges. ® IMC BACnet Module Page 5 Analog Input Objects Optional Properties Supported: None Optional Writable Properties: Out_Of_Service (AI239 − AI252, AI274 − AI285 only) Table 3. Analog Input Objects List Object ID Object Name Units Data Range 198 Mac Address None 0 − 127 199 IMC Address None 1−31 200* IMC Version[4] None 0 − 127 201* IMC Version[5] None 0 − 127 202* IMC Version[6] None 0 − 127 203* IMC Version[7] None 0 − 127 204* IMC Version[8] None 0 − 127 205* IMC Version[9] None 0 − 127 206* IMC Version[10] None 0 − 127 207* IMC Version[11] None 0 − 127 231 Unit ID None 0 − 127 232 Unit Status None 0 − 255 239 Space Temperature Deg. F 63.75 − 100.00 240 Discharge Air Temperature Deg. F −8.7 – 164.4 241 Effective Occupancy None 0 − 2 242 Local Outside Air Temperature Deg. F −30.6 – 131.6 243 Local Space Temperature Deg. F 63.75 – 100.00 244 Outside Air Damper Percent 0 − 100, 255 245 Heat Primary Percent 0 – 100 246 Heat Secondary Percent 0 – 100 247 Cool Primary Percent 0 – 100 248 Economizer Enabled Percent 0, 1, 255 250 Supply Fan Status Percent 0 − 100 252 Space Temperature Set Point (Eff) Deg. F 40.0 – 95.0 253 Current Error None 0 − 255 254 Error Pointer None 0 – 83 255 Most recent Error 1 None 1 − 255 256 Most recent Error 2 None 1 − 255 257 Most recent Error 3 None 1 − 255 258 Most recent Error 4 None 1 − 255 259 Most recent Error 5 None 1 − 255 260 Most recent Error 6 None 1 − 255 261 Most recent Error 7 None 1 − 255 262 Most recent Error 8 None 1 − 255 263 Most recent Error 9 None 1 − 255 264 Most recent Error 10 None 1 − 255 274 Space CO2 Sensor (Eff) Parts−per−million 0 − 2000 275 Space CO2 Sensor (Local) Parts−per−million 0 − 2000 276 Space Humidity (Eff) Percent 0 − 100 277 Space Humidity (Local) Percent 0 − 100 278 Dehumidification Set Point (Eff) Percent 0 − 100 279 Dehumidification Status None 0 − 2 281 Return Air Temperature Deg. F −8.7 – 164.4 282 Building Static Pressure Inches of water −0.5 − 0.5 283 Duct Static Pressure Inches of water 0 – 5.00 285 Exhaust Fan Status Percent 0 − 100 * Not recommended for new installations; legacy support only Corp. 0808−L6 04/09 Page 6 Analog Value Objects Optional Properties Supported: None Optional Writable Properties: Present_Value Table 4. Analog Value Objects List Min. Max. Valid Values Object ID Object Name Units Value Value within Range Note 1 Baud Rate Setting None 9600 76800 9600, 19200, 38400, 76800 For occupied and unoc- 130 Heating Occupied Setpoint Deg. F 40 95 all cupied setpoints consid- ered separately, the heating setpoint must be 131 Cooling Occupied Setpoint Deg. F 40 95 all lower than the cooling setpoint by at least the 132 Heating Unoccupied Setpoint Deg. F 40 95 all auto−changeover dead- band value set in IMC ECTO 6.15 (default 3 133 Cooling Unoccupied Setpoint Deg. F 40 95 all degF). Zone Sensor Setpoints The IMC typically uses four setpoints and the zone temper- See figure 4 for an example of setpoints when the IMC is ature to operate the unit when a zone sensor is installed. operating using ECTO default values. When using the AO:109 single setpoint input, the IMC will As an alternative, the individual setpoints AV:130−133 may use the zone temperature setpoint and ECTO 6.15 to de- be used. The IMC uses whatever were the last setpoints termine the heat / cool setpoint in the occupied mode. Dur- received, whether from AO:109−110, or AV:130−133. ing the unoccupied mode, the IMC will use the zone tem- perature setpoint and the difference between ECTO 6.05 and 6.03. Unocc. Clg. Setpoint 82.5°F 95°F IMC Cooling Maximum Setpoint Occ. Clg. Setpoint 71.5°F 25°F (ECTO 6.05−6.03) BACnet 3°F (ECTO 6.15) Difference between unoccupied Autochangeover Network 70°F heating and cooling backup set- deadband Input points. (setpoint + offset) 68.5°F Occ. Htg. Setpoint 40°F IMC Heating Minimum Setpoint 57.5°F Unocc. Htg. Setpoint Figure 4. IMC Default Setpoint Example (Zone Sensor Installed) IMC Alarm Codes See the IMC user guide for a list of alarm codes. ® IMC BACnet Module Page 7 Application Details Object Name: Application Mode Control Object Type: AO (Analog Output) Object ID: 101 Object Units: (95) No_Units Value = (See tables below) Set the application mode input to Value. The IMC controller can be set locally during commissioning to operate in either of two modes: remote zone sensor con- trol mode (with local or remote zone sensor), or remote thermostat control mode. Several application mode command values are recognized by either IMC mode, while some can only be used when the IMC is in the remote thermostat control mode. Common Application Mode Values Value Mode Description 0 $00 AUTO Heating or cooling. Default after reset. 1 $01 HEAT Heating only. 3 $03 COOL Cooling only. 6 $06 OFF Unit off. 9 $09 FAN ONLY No heating or cooling allowed. 255 $FF NUL Same as AUTO. 208 $D0 FAN AUTO Main fan (blower) auto. Default after reset. 209 $D1 FAN ON Main fan (blower) on. 216 $D8 EXHAUST AUTO Power exhaust fan auto. Default after reset. 217 $D9 EXHAUST1 ON 1st stage power exhaust fan on. 218 $DA EXHAUST1 OFF 1st stage power exhaust fan off. 219 $DB EXHAUST2 ON 2nd stage power exhaust fan on. 220 $DC EXHAUST2 OFF 2nd stage power exhaust fan off. 221 $DD EXHAUST ON Both stages of power exhaust fan on. 222 $DE EXHAUST OFF Both stages of power exhaust fan off. 254 $FE RESET Force controller reset. The four command groups (0−9), (208−209), (216−222), and (224−236, see below) are independent of each other. Se- lecting a command from one group does not affect any previously sent command from another group. Except for OFF and RESET, which also set FAN AUTO, EXHAUST AUTO, and heat/cool demand IDLE. AUTO is the default application mode input. When in a remote zone sensor mode, AUTO allows the IMC control to gen- erate heating and cooling demands based on zone temperature and zone temperature setpoint. Auxiliary functions such as dehumidification or emergency override (i.e. smoke mode) will still operate as needed. Also the blower and ex- haust fan functions operate. HEAT and COOL allow the servicing of only heating or cooling demands. These set a mode only, and do not generate a demand. Application mode OFF is a unit−disable state, causing the controller to become idle, and clearing all outputs and timers. All outputs are kept off while application mode is OFF. Since this is a complete unit−disable command, it should not be used to turn off heating and cooling demands as part of remote thermostat operation − use 224 IDLE for that purpose. See below. Application mode FAN ONLY disables heating and cooling operation. No effect on fan operation. Return to normal op- eration with AUTO, HEAT, or COOL. Application modes FAN ON and FAN AUTO are used to turn on the main unit fan (blower), or return it to automatic op- eration. Application modes for EXHAUST ON are used to turn on/off a power exhaust fan, or to return it to automatic operation. The IMC may delay up to 30 seconds before responding to an exhaust command. These commands apply to single−, two−, and variable-speed power exhausts. A variable-speed exhaust is enabled here, while the speed is adjusted using AO:128, the Exhaust Fan Capacity Input. Application mode RESET causes the system to reset itself and go through the controller’s startup and initialization rou- tines. This takes about 8 seconds in an IMC controller, during which time the analog and digital inputs are settling to correct values. The controller will return to AUTO operation. AUTO, FAN AUTO and EXHAUST AUTO are the defaults after reset. Corp. 0808−L6 04/09 Page 8 Application Modes Specific To Remote Thermostat Operation These values are only recognized if the IMC control is placed in a remote thermostat mode of operation (set locally dur- ing commissioning). Value Mode Y2 Y1 W2 W1 Description 224 $E0 IDLE 0000 Heat / Cool off. Default after reset. 228 $E4 COOL1 0100 Cool 1. 232 $E8 COOL2 1000 Cool 2. 236 $EC COOL3 1100 Cool 3. Full cooling. 225 $E1 HEAT1 0001 Heat 1. 226 $E2 HEAT2 0010 Heat 2. 227 $E3 HEAT3 0011 Heat 3. Full heating. 229 $E5 REHEAT LO 0101 Supermarket Reheat (lo) 230 $E6 REHEAT HI 0111 Supermarket Reheat (hi) For all $Ex values the fan runs if it is already on, otherwise the fan turns on after a fan on−delay. For $E0 the fan turns off after a fan off−delay. COOL2 and COOL3 are equivalent unless 3−stage cooling has been selected locally at the controller during commis- sioning. HEAT2 and HEAT3 are equivalent except in heat pump equipment types, when HEAT2 acts as �emergency heat", run- ning auxiliary strip heat and turning off the compressor(s). So in a heat pump, normal heating is commanded using HEAT1 or HEAT3. REHEAT LO and REHEAT HI can only be used if Supermarket Reheat is enabled for the IMC using ECTO 4.24. If a mode not defined in the above list is sent, then the application mode is not changed. ® When an IMC is commissioned for BACnet gateway remote thermostat operation, it will wait for 5 minutes following startup to receive application mode data. The IMC will remain in AUTO mode until data is received, or until the 5 minute period has expired. If 5 minutes passes without data being received, then the IMC will enter the backup mode of operation (set locally dur- ing commissioning). It is recommended that the application mode data be updated at intervals of no more than 2 minutes to be sure that a single missed−data event will not constitute an application mode data failure. Any application mode data will serve as a valid update; either common or remote thermostat values. If application mode data appears while the IMC is in a backup mode, then the IMC will reset and normal operation will resume. Object Name: Outdoor Air Min Pos Control Object Type: AO (Analog Output) Object ID: 102 Object Units: (98) Percent Value = 0 − 255 0 −100: Set the minimum position of the outdoor air economizer damper; % open. 101 − 255: Relinquish to local control. Min damper position depends on the setting in IMC ECTO 5.24: ECTO 5.24 =101: Min damper position set by potentiometer on economizer control. <101: Min damper position set by ECTO 5.24. The minimum damper position is only effective when the system is occupied and the main blower is running. Otherwise the damper remains closed. Default value following reset is 101 (local). ® IMC BACnet Module Page 9 Object Name: Occupancy Override Control Object Type: AO (Analog Output) Object ID: 103 Object Units: (95) No_Units Value = 0−255 0: space occupied 1: space unoccupied (IMC does not support; gives auto operation) 2: refresh space occupied timer defined at local controller 3−255: auto; clear timer and return to occupancy scheduler state Default value following reset is 255 (auto). Object Name: Occupancy Scheduler Control Object Type: AO (Analog Output) Object ID: 104 Object Units: (95) No_Units Value = 0 − 255 0: space occupied 1−255: space unoccupied Default value following reset is determined by a 24VAC input at the controller (signal present = occupied). Once a value for AO:104 is received, the 24VAC input is ignored. Object Name: Occupancy Sensor Input Object Type: AO (Analog Output) Object ID: 107 Object Units: (95) No_Units Value = 0 − 255 0: occupancy sensor indicates space occupied 1: occupancy sensor indicates space unoccupied (IMC does not support; gives auto operation) 2−255: auto; return to occupancy scheduler state Default value following reset is 255 (auto). The occupancy inputs are logically �OR"; if any one is �OCCUPIED" then the space is occupied, otherwise the space is �UNOCCUPIED". No single input can force the space �UNOCCUPIED". Object Name: Space Dehumidification Setpoint Object Type: AO (Analog Output) Object ID: 108 Object Units: (98) Percent Value = 0 − 100 0−100: % relative humidity setpoint Dehumidification begins when the effective space relative humidity rises to this setpoint value. The default following re- set is local control. Once an executive controller has sent a setpoint for AO:108, there is no way to return to the local setpoint except by controller reset. Dehumidification ends when the effective space relative humidity falls below this setpoint value minus a dehu- midification deadband that is typically 3%. The deadband value is set locally during commissioning. Corp. 0808−L6 04/09 Page 10 Object Name: Temperature Setpoint (abs) Object Type: AO (Analog Output) Object ID: 109 Object Units: (64) Degrees−Fahrenheit Value = 36.25 – 100.00 degF, in 0.25 degF increments The single−point �Temperature Setpoint (abs)" (including offset; see below) is converted locally to occupied and unoccu- pied heating and cooling setpoints. The occupied and unoccupied heating and cooling setpoints are computed to be centered (if possible) on the effective single−point setpoint. This is done while preserving the occupied and unoccupied deadbands, as well as any local restrictions on minimum or maximum values. The default following reset is 70 degF, but local values are used for the heating and cooling (occupied and unoocupied) setpoints until a value is received for AO:109. As an alternative method of establishing setpoints, the individual setpoints AV:130−133 may be used. The IMC uses whatever were the last setpoints received, whether from AO:109−110, or AV:130−133. The occupied heat/cool auto−changeover deadband value is set locally during commissioning. The unoccupied heat/cool auto−changeover deadband value is set locally during commissioning by adjusting the back- up unoccupied heating and cooling setpoints. The difference between these setpoints will be used as the unoccupied heat/cool auto−changeover deadband value. Object Name: Temperature Setpoint Offset Object Type: AO (Analog Output) Object ID: 110 Object Units: (64) Degrees−Fahrenheit Value = −32.00 – 31.75 degF, in 0.25 degF increments A signed value added to the Temperature Setpoint (abs) value to provide an effective temperature setpoint. See above regarding deadbands and limits. The default following reset is 0. Object Name: Space Temperature Input Object Type: AO (Analog Output) Object ID: 113 Object Units: (64) Degrees−Fahrenheit Value = 36.25 – 100.00 degF, in 0.25 degF increments A network value for the space temperature. Heating and cooling demands are generated based on the �Space Temper- ature Input", and the �Temperature Setpoint (abs)" and �Temperature Setpoint Offset" values. See above. The default following reset is 72.5 degF. ® When an IMC is commissioned for BACnet gateway remote room sensor operation, it will wait for 5 minutes following startup to receive space temperature data. The IMC will remain in a no−run mode until data is received, or until the 5 minute period has expired. If 5 minutes passes without data being received, then the IMC begins to use local data for the space temperature. If a local sensor is connected then it will be used. If not, then a failed−sensor error is recorded and the IMC will enter the backup mode of operation (set locally during commissioning). It is recommended that network data be updated at intervals of no more than 2 minutes to be sure that a single missed− data event will not constitute a data update failure. If data appears after a sensor failure is processed, it will be treated as an intermittent sensor. Normal operation will re- sume. If the IMC is in a backup mode, then it will reset before resuming. ® IMC BACnet Module Page 11 Object Name: Emergency Override Control Object Type: AO (Analog Output) Object ID: 114 Object Units: (95) No_Units Value = 0 − 255 Set the emergency mode defined by value, decoded as: Supply Exhaust Outdoor Value Mode Fan Fan Damper 0 NORMAL auto auto auto 1 PRESSURIZE on off open 2 DEPRESSURIZE off on (speed) closed 3 PURGE on on (speed) open 4 SHUTDOWN off off closed 5 FIRE 6 DEPRESSURIZE off on (pressure) closed 7 PURGE on on (pressure) open >7 NUL (normal) auto auto auto auto − normal operation (speed) − exhaust fan runs at speed pre−selected at equipment (pressure) − exhaust fan runs to maintain building press setpoint; local or remote Mode 5, FIRE, is a locally defined operation (set at commissioning). For units without VFD exhaust fans, modes 6−7 are the same as 2−3. �Emergency Override Control" input takes precedence over local smoke input. The default following reset is 0 (NORMAL). Object Name: Compressor Enable Control Object Type: AO (Analog Output) Object ID: 115 Object Units: (98) Percent Value = 0 − 255 0: output disabled 1−100: output limited to 1 – 100% of maximum 101−255: maximum output permitted The following table shows the value where the indicated compressor stage is disabled, for equipment having the indi- cated maximum number of compressor stages: Maximum Stage Disabled When Value < x Stages 1234 1 Value < 50 2 Value < 33 Value < 66 3 Value < 25 Value < 50 Value < 75 4 Value < 20 Value < 40 Value < 60 Value < 80 Free cooling using an economizer with outdoor air is not considered a stage. Only compressors are considered to be stages. All compressors installed are included, however they are being used; sensible cooling, condenser reheat (latent cooling), or heat pump heating. The default following reset is 100%. Disabled stages are re−enabled at the above values plus 3% hysteresis. Corp. 0808−L6 04/09 Page 12 Object Name: Primary Heat Enable Control Object Type: AO (Analog Output) Object ID: 117 Object Units: (98) Percent Value = 0 − 255 0: output disabled 1−100: output limited to 1 – 100% of maximum 101−255: maximum output permitted The table shown above for �Compressor Enable Control" can also be applied here to the �Primary Heat Enable Con- trol". It shows the value where the indicated primary heating stage is disabled, for equipment having the indicated maxi- mum number of primary heating stages. The default following reset is 100%. In heat pump systems during heating operation, the lower value of �Compressor Enable Control" and �Primary Heat Enable Control" is used to establish the compressors that can run. Object Name: Auxiliary Heat Enable Control Object Type: AO (Analog Output) Object ID: 119 Object Units: (98) Percent Value = 0 − 255 0: output disabled 1−100: output limited to 1 – 100% of maximum 101−255: maximum output permitted The table shown above for �Compressor Enable Control" can also be applied here to the �Auxiliary Heat Enable Con- trol". It shows the value where the indicated auxiliary heating stage is disabled, for equipment having the indicated max- imum number of auxiliary heating stages. The default following reset is 100%. The �Auxiliary Heat Enable Control" is only used in heat pump systems. Object Name: Duct Static Setpoint Object Type: AO (Analog Output) Object ID: 123 Object Units: (58) Inches−of−water Value = 0.0 − 5.0 inWC The setpoint for control of duct static pressure, in inches of water column. The main blower speed or bypass damper setting is varied to maintain this value. The setpoint can be selected from the range of 0.0 to 5.0 inches of water col- umn. The default following reset is local control. Once an executive controller has sent a setpoint for AO:123, there is no way to return to the local setpoint except by controller reset. Object Name: Building Static Setpoint Object Type: AO (Analog Output) Object ID: 124 Object Units: (58) Inches−of−water Value = −0.5 − 0.5 inWC The setpoint for control of building static pressure, in inches of water column. The exhaust blower is cycled or, if a VFD is used, its speed is varied to maintain this value. The setpoint can be selected from the range of −0.5 to +0.5 inches of water column. The default following reset is local control. Once an executive controller has sent a setpoint for AO:124, there is no way to return to the local setpoint except by controller reset. ® IMC BACnet Module Page 13 Object Name: Discharge Air Cooling Setpoint Object Type: AO (Analog Output) Object ID: 125 Object Units: (64) Degrees−Fahrenheit Value = 40 − 80 degF, and −9 degF The setpoint for control of discharge (or supply) air temperature during cooling. When the controller is in the correct mode of operation, sending this setpoint will cause cooling components to cycle, or vary their output, in order to main- tain this temperature in the leaving air stream. The setpoint can be selected from the range of 40 to 80 degrees Fahren- heit. Selecting a value of −9 degF causes the control to revert to the use of its locally programmed setpoint. Default val- ue following reset is −9 (local). Object Name: Discharge Air Heating Setpoint Object Type: AO (Analog Output) Object ID: 126 Object Units: (64) Degrees−Fahrenheit Value = 80 − 140 degF, and −9 degF The setpoint for control of discharge (or supply) air temperature during heating. When the controller is in the correct mode of operation, sending this setpoint will cause heating components to cycle, or vary their output, in order to main- tain this temperature in the leaving air stream. The setpoint can be selected from the range of 80 to 140 degrees Fahr- enheit. Selecting a value of −9 degF causes the control to revert to the use of its locally programmed setpoint. Default value following reset is −9 (local). Object Name: Supply Fan Capacity Input Object Type: AO (Analog Output) Object ID: 127 Object Units: (98) Percent Value = 33 − 255 33 − 100: Set the supply fan capacity as a % of maximum speed. 101 − 255: Relinquish to local control. Supply fan capacity depends on IMC ECTO values. Supply fan capacity is only effective when the main blower is running. if compressor(s) are on or heat is on, min. value is limited to ECTO 0.06 or ECTO 0.07, respectively. Maximum supply air is limited by IMC ECTO value 0.08, although the relinquish default range of 101−255 is always available. Default value following reset is 255 (local). Object Name: Exhaust Fan Capacity Input Object Type: AO (Analog Output) Object ID: 128 Object Units: (98) Percent Value = 33 − 255 33 − 100: Set the exhaust fan capacity as a % of maximum speed. 101 − 255: Relinquish to local control. Exhaust fan capacity depends on IMC ECTO values. Exhaust fan capacity is only effective when the exhaust fan is running. Default value following reset is 255 (local). Corp. 0808−L6 04/09 Page 14 Object Name: Set Economizer Outdoor Air Suitable Object Type: AO (Analog Output) Object ID: 129 Object Units: (95) No_Units Value = 0−255 0: Economizer disable 1: Economizer enable >1: Economizer to auto When outdoor air is determined to be suitable for free cooling, the economizer feature will operate (if installed) on a first stage cooling call to use outdoor air instead of mechanical cooling. AO:129 is used to allow an executive controller to set the state of outdoor air suitability (OAS). It can be enabled, disabled, or left for the local controller to determine. BACnet control of the economizer requires the economizer board A56 (EM1) to have switches selected to TMP temper- ature mode. See the IMC manual for additional information on economizer operation. Default value following reset is 255 (auto). Object Name: MAC Address Object Type: AI (Analog Input) Object ID: 198 Object Units: (95) No_Units Value = 0−127 Selectable BACnet address. Also shown on IMC scrolling display. By default, this is set using IMC DIP switches, and is equal to the IMC address. The address can also be selected using ECTO 7.26 of the IMC. Object Name: IMC Address Object Type: AI (Analog Input) Object ID: 199 Object Units: (95) No_Units Value = 1−31 Selectable through IMC address DIP switches (1−31). This is the address for L Connection network. Object Name: IMC Version[04], IMC Version[05], �, IMC Version[11] Object Type: AI (Analog Input) Object ID: 200, 201, …, 207 Object Units: (95) No_Units Value = 0, 46, 48 − 57 0: end of string 46: �." 48: �0" … 57: �9" Each value is the ASCII code of a character in the IMC version number. The version number is found in a null−termi- nated string, most−significant−character first, beginning in IMC Version[04]. Maximum length is 8 chars, including null. NOTE − Not recommended for new installations. Read device object property Application_Software_Version instead. For BACnet version read device object property Firmware_Revision. ® IMC BACnet Module Page 15 Object Name: Unit ID Object Type: AI (Analog Input) Object ID: 231 Object Units: (95) No_Units Value = 0 − 255 48−63: gas heat, electric cool 64−79: electric heat, electric cool 80−95: electric heat pump, with or without electric resistive heat These are the currently defined IMC unit types. Object Name: Unit Status Object Type: AI (Analog Input) Object ID: 232 Object Units: (95) No_Units Value = 0 − 255 0 – HVAC off 1 – HVAC heat. 2 – HVAC morning warmup. 3 – HVAC cool. 5 – HVAC pre−cool. 6 – HVAC off. 7 – HVAC test. 8 – HVAC emergency heat. 9 – HVAC fan only. 12 – HVAC max heat. 14 – HVAC dehumidification. 129 – HVAC fresh air heating. 131 – HVAC fresh air cooling. 145 – HVAC defrost compressor 1. 161 – HVAC defrost compressor 2. 177 – HVAC defrost compressor 1 & 2. These are the currently defined IMC unit status. Object Name: Space Temperature Object Type: AI (Analog Input) Object ID: 239 Object Units: (64) Degrees−Fahrenheit Value = 63.75 – 100.00 degF, in 0.25 degF increments Space temperature from local IMC sensor, or from �Space Temperature Input". This is the actual value being used by the IMC. Its source is either a locally wired temperature sensor (see �Local Space Temperature") or the network input (see �Space Temperature Input"). Object Name: Discharge Air Temperature Object Type: AI (Analog Input) Object ID: 240 Object Units: (64) Degrees−Fahrenheit Value = −8.7 – 164.4 degF, in 0.7 degF increments Discharge air temperature measurement from IMC sensor. Corp. 0808−L6 04/09 Page 16 Object Name: Effective Occupancy Object Type: AI (Analog Input) Object ID: 241 Object Units: (95) No_Units Value = 0 − 2 0: space occupied 1: space unoccupied 2: space occupied (timed override) The occupancy override timer is established locally for each controller during system commissioning. The �Effective Occupancy" depends on the �Occupancy Scheduler Control", the �Occupancy Override Control", and the �Occupancy Sensor Input. The �Effective Occupancy" is occupied if any of these inputs are in the occupied state. Other- wise �Effective Occupancy" is unoccupied. ® The local IMC occupied input is ignored when a BACnet module is used. Object Name: Local Outside Air Temperature Object Type: AI (Analog Input) Object ID: 242 Object Units: (64) Degrees−Fahrenheit Value = −30.6 – 131.6 degF, in 0.6 degF increments Outdoor air temperature measurement from IMC sensor. Object Name: Local Space Temperature Object Type: AI (Analog Input) Object ID: 243 Object Units: (64) Degrees−Fahrenheit Value = 63.75 – 100.00 degF, in 0.25 degF increments Space temperature from IMC sensor. Object Name: Outdoor Air Damper Object Type: AI (Analog Input) Object ID: 244 Object Units: (98) Percent Value = 0 – 100, 255 0 − 100: Outdoor air damper position. Percent−open. 255: No damper. Object Name: Heat Primary Object Type: AI (Analog Input) Object ID: 245 Object Units: (98) Percent Value = 0 – 100 0 − 100: Current level of the primary heating capacity. This is based on the number of gas stages operating in a gas/electric unit, or compressors operating in a heat pump, or electric resistance stages operating in an electric/electric unit. ® IMC BACnet Module Page 17 Object Name: Heat Secondary Object Type: AI (Analog Input) Object ID: 246 Object Units: (98) Percent Value = 0 – 100 0 − 100: Current level of the secondary heating capacity. This is auxiliary (electric resistance �strip") heat in a heat pump. Whether it is on in addition to the primary heat (com- pressor), or as emergency heat while the compressor is locked−out. Object Name: Cool Primary Object Type: AI (Analog Input) Object ID: 247 Object Units: (98) Percent Value = 0 – 100 0 − 100: Current level of the primary cooling capacity. This is based on the number of compressors operating. There is no secondary cooling. Object Name: Economizer Enabled Object Type: AI (Analog Input) Object ID: 248 Object Units: (95) No_Units Value = 0 – 1, 255 0: Economizer is disabled. 1: Economizer is enabled (outdoor air is suitable for free cooling). 255: No economizer. The enabled state only indicates that the IMC has determined that the outdoor air is suitable for free cooling. The unit is actually executing free cooling operation if �Economizer Enabled" is 1, and �Unit Status" is 3, 5, or 131. Object Name: Supply Fan Status Object Type: AI (Analog Input) Object ID: 250 Object Units: (98) Percent Value = 0 – 100 0: Supply fan off. 1: Supply fan on (single−speed fan). 2 − 100: Supply fan on (variable−speed fan; percent of full speed). Corp. 0808−L6 04/09 Page 18 Object Name: Space Temperature Setpt (Eff) Object Type: AI (Analog Input) Object ID: 252 Object Units: (64) Degrees−Fahrenheit Value = 40.0 – 95.0 degF, in 0.25 degF increments The effective space temperature setpoint, which depends on: current �Temperature Setpoint (abs)", current �Temperature Setpoint Offset", current �Effective Occupancy", most recent heating or cooling demand indicated by �Unit Status", any local setpoint adjustment, and heating and cooling deadbands and differentials set at system commissioning. Object Name: Current Error Object Type: AI (Analog Input) Object ID: 253 Object Units: (95) No_Units Value = 0 − 255 This is the code for the currently occurring alarm condition, if any. If no alarm is currently in progress, then the value is 0. If the value is not zero, then �Current Error" and �Most Recent Error 1" (see below) will be equal. Refer to the IMC User’s Guide for alarm code descriptions. Object Name: Error Pointer Object Type: AI (Analog Input) Object ID: 254 Object Units: (95) No_Units Value = 0 − 83 This value points to the next available alarm code location. It runs from 0 to 83, and then rolls−over to 0. Tracking this value and using the ten−most−recent−error−codes (see below) allows an application to determine when new errors are logged by the IMC, what those errors are, and if any errors have been missed due to network delays or for any other reason. To correct for an error in some early versions, if the reported value is in the range of 164−247 then it is necessary to subtract it from 247 in order to get the 0−83 value described above. ® IMC BACnet Module Page 19 Object Name: Most recent Error 1, Most recent Error 2 Most recent Error 10 Object Type: AI (Analog Input) Object ID: 255, 256, …, 264 Object Units: (95) No_Units Value = 1 − 255 These are the ten most recently occurring diagnostic codes; �Most recent Error 1" is the most recent. The IMC does not time−stamp error codes. This must be done by the master controller. This is a first−in first−out buffer. Error codes are stored as they occur, and no filtering is done with respect to duplication or error code severity or priority. When another error code is logged at �Most recent Error 1", the value in �Most recent Error 10" is lost, being replaced by �Most recent Error 9". Refer to the IMC User’s Guide for alarm code descriptions. Object Name: Space CO2 Sensor (Eff) Object Type: AI (Analog Input) Object ID: 274 Object Units: (96) Parts−per−million Value = 0 − 2000 0 − 6: no sensor 7 − 1992: valid CO measurement 2 1993 − 2000: sensor error This is the actual value being used by the IMC, and is the value measured at the IMC. Object Name: Space CO2 Sensor (Local) Object Type: AI (Analog Input) Object ID: 275 Object Units: (96) Parts−per−million Value = 0 − 2000 0 − 6: no sensor 7 − 1992: valid CO measurement 2 1993 − 2000: sensor error This is the actual value being used by the IMC, and is the value measured at the IMC. Corp. 0808−L6 04/09 Page 20 Object Name: Space Humidity (Eff) Object Type: AI (Analog Input) Object ID: 276 Object Units: (98) Percent Value = 0 − 100 0: no sensor 1 − 99: valid relative humidity measurement 100: sensor error This is the actual value being used by the IMC, and is the value measured at the IMC. Object Name: Space Humidity (Local) Object Type: AI (Analog Input) Object ID: 277 Object Units: (98) Percent Value = 0 − 100 0: no sensor 1 − 99: valid relative humidity measurement 100: sensor error This is the actual value being used by the IMC, and is the value measured at the IMC. Object Name: Dehumidification Set Point (Eff) Object Type: AI (Analog Input) Object ID: 278 Object Units: (98) Percent Value = 0 − 100 Relative humidity setpoint for dehumidification operation. Deadband is set locally during commissioning. Object Name: Dehumidification Status Object Type: AI (Analog Input) Object ID: 279 Object Units: (95) No_Units Value = 0 – 2 0: No dehumidification installed. 1: Dehumidification installed but not running. 2: Dehumidification installed and running. ® IMC BACnet Module Page 21 Object Name: Return Air Temperature Object Type: AI (Analog Input) Object ID: 281 Object Units: (64) Degrees−Fahrenheit Value = −8.7 – 164.4 degF, in 0.7 degF increments Unit return air temperature measurement from IMC sensor. Object Name: Building Static Pressure Object Type: AI (Analog Input) Object ID: 282 Object Units: (58) Inches−of−water Value = −0.500 – 0.500 inWC, in 0.004 inWC increments Building (space) static pressure measurement from IMC sensor. Object Name: Duct Static Pressure Object Type: AI (Analog Input) Object ID: 283 Object Units: (58) Inches−of−water Value = 0.00 – 5.00 inWC, in 0.02 inWC increments Duct (supply) static pressure measurement from IMC sensor. Object Name: Exhaust Fan Status Object Type: AI (Analog Input) Object ID: 285 Object Units: (98) Percent Value = 0 – 100 0: Exhaust fan off. 1: Exhaust stage 1 on. 2: Exhasut stage 2 on. 33−100: Exhaust variable speed %on. 255: No exhaust. Corp. 0808−L6 04/09 Page 22 Object Name: Baud Rate Setting Object Type: AV (Analog Value) Object ID: 1 Object Units: (95) No Units Value = 9600, 19200, 38400, 76800 Baud rate change only takes affect after IMC resets. Default value following reset is 38400, but this can be changed at the unit. See IMC manual for details. Object Name: Heating Occupied Setpoint Object Type: AV (Analog Value) Object ID: 130 Object Units: (64) Degrees-Fahrenheit Value = 40 − 95 Occupied heating setpoint. Default value following reset is local (ECTO 6.02). As an alternative method of establishing setpoints, the single setpoint AO:109 and offset AO:110 may be used. The IMC uses whatever were the last setpoints received, whether from AO:109−110, or AV:130−133. To be considered in range the values for AV:130, 131, 132, and 133 must be in the range 40−95, and the heating set- point must be less than the corresponding (occupied or unoccupied) cooling setpoint by at least the auto−changeover deadband value set in IMC ECTO 6.15 (default 3 degF, 2−10 degF range). If any of these conditionis are violated, BAC- net will return an out of range message. The AV’s 130−133 can be used instead of the single setpoint and offset AO:109 and AO:110. Object Name: Cooling Occupied Setpoint Object Type: AV (Analog Value) Object ID: 131 Object Units: (64) Degrees-Fahrenheit Value = 40 − 95 Occupied cooling setpoint. Default value following reset is local (ECTO 6.04). See description for AV:130 for details on valid range. Object Name: Heating Unoccupied Setpoint Object Type: AV (Analog Value) Object ID: 132 Object Units: (64) Degrees-Fahrenheit Value = 40 − 95 Unoccupied heating setpoint. Default value following reset is local (ECTO 6.03). See description for AV:130 for details on valid range. Object Name: Cooling Unoccupied Setpoint Object Type: AV (Analog Value) Object ID: 133 Object Units: (64) Degrees-Fahrenheit Value = 40 − 95 Unoccupied cooling setpoint. Default value following reset is local (ECTO 6.05). See description for AV:130 for details on valid range. ® IMC BACnet Module Page 23 ® BACnet Protocol Implementation Conformance (PIC) Statement Date . . . . . . . . . . . . . . . . . . . . . . April 16, 2009 Vendor Name . . . . . . . . . . . . . . Lennox Industries, Inc. Product Name . . . . . . . . . . . . . IMC (Integrated Modular Controller) Product Model Number . . . . . M1−8 Firmware Revision . . . . . . . . . BACnet v1.0xx Application Software Version . IMC v6.xx BACnet Protocol Revision . . . 4 Product Description The Integrated Modular Control (IMC) with optional IMC BACnet Module is a microprocessor−based unit controller de- signed to control Lennox’ commercial rooftop units. ® BACnet Standardized Device Profile (Annex L) BACnet Operator Workstation (B−OWS) x BACnet Application Specific Controller (B−ASC) BACnet Building Controller (B−BC) BACnet Smart Sensor (B−SS) BACnet Advanced Application Controller (B−AAC) BACnet Smart Actuator (B−SA) ® BACnet Interoperability Building Blocks (BIBBs) Supported (Annex K) Data Sharing: DS−RP−B(ReadProperty), DS−RPM−B(ReadPropertyMultiple), DS−WP−B(WriteProperty) Device Management: DM−DDB−B(Dynamic Device Binding), DM−DOB−B(Dynamic Object Binding), DM−DCC−B(DeviceCommunicationControl), DM−RD−B(ReinitializeDevice) Which of the following device binding methods does the product support? (check one or more) Send Who−Is, receive I−Am (BIBB DM−DDB−A) x Receive Who−Is, send I−Am (BIBB DM−DDB−B) Send Who−Has, receive I−Have (BIBB DM−DOB−A) x Receive Who−Has, send I−Have (BIBB DM−DOB−B) Manual configuration of recipient device’s network number and MAC address None of the above Standard Object Types Supported x Device Object Binary Output x Analog Input Binary Value x Analog Output File x Analog Value Multi−State Input Binary Input Multi−State Output Data Link Layer Options ® BACnet IP, (Annex J) BACnet IP, (Annex J), Foreign Device ISO 8802−3, Ethernet (Clause 7) ANSI/ATA 878.1, 2.5 Mb. ARCNET (Clause 8) ANSI/ATA 878.1, RS−485 ARCNET (Clause 8), baud rate(s) x MS/TP master (Clause 9), baud rate(s): 9.6K, 19.2K, 38.4K, 76.8K MS/TP slave (Clause 9), baud rate(s): Point−To−Point, EIA 232 (Clause 10), baud rate(s): Point−To−Point, modem, (Clause 10), baud rate(s): LonTalk, (Clause 11), medium: Other: Dynamically Creatable Objects: None Dynamically Deletable Objects: None Proprietary Properties: None Networking Options: None Segmentation Capability: None Character Sets Supported: x ANSI X3.4 ISO 10646 (UCS−2) IBM�/Microsoft� DBCS ISO 10646 (UCS−4) ISO 8859−1 JIS C 6226 Corp. 0808−L6 04/09 Page 24
Frequently asked questions
What makes Elite.Parts unique?

What kind of warranty will the M1-8 have?

Which carriers does Elite.Parts work with?

Will Elite.Parts sell to me even though I live outside the USA?

I have a preferred payment method. Will Elite.Parts accept it?

Why buy from GID?
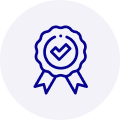
Quality
We are industry veterans who take pride in our work
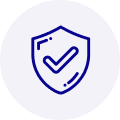
Protection
Avoid the dangers of risky trading in the gray market
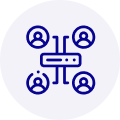
Access
Our network of suppliers is ready and at your disposal
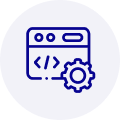
Savings
Maintain legacy systems to prevent costly downtime
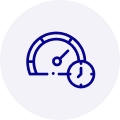
Speed
Time is of the essence, and we are respectful of yours
What they say about us
FANTASTIC RESOURCE
One of our top priorities is maintaining our business with precision, and we are constantly looking for affiliates that can help us achieve our goal. With the aid of GID Industrial, our obsolete product management has never been more efficient. They have been a great resource to our company, and have quickly become a go-to supplier on our list!
Bucher Emhart Glass
EXCELLENT SERVICE
With our strict fundamentals and high expectations, we were surprised when we came across GID Industrial and their competitive pricing. When we approached them with our issue, they were incredibly confident in being able to provide us with a seamless solution at the best price for us. GID Industrial quickly understood our needs and provided us with excellent service, as well as fully tested product to ensure what we received would be the right fit for our company.
Fuji
HARD TO FIND A BETTER PROVIDER
Our company provides services to aid in the manufacture of technological products, such as semiconductors and flat panel displays, and often searching for distributors of obsolete product we require can waste time and money. Finding GID Industrial proved to be a great asset to our company, with cost effective solutions and superior knowledge on all of their materials, it’d be hard to find a better provider of obsolete or hard to find products.
Applied Materials
CONSISTENTLY DELIVERS QUALITY SOLUTIONS
Over the years, the equipment used in our company becomes discontinued, but they’re still of great use to us and our customers. Once these products are no longer available through the manufacturer, finding a reliable, quick supplier is a necessity, and luckily for us, GID Industrial has provided the most trustworthy, quality solutions to our obsolete component needs.
Nidec Vamco
TERRIFIC RESOURCE
This company has been a terrific help to us (I work for Trican Well Service) in sourcing the Micron Ram Memory we needed for our Siemens computers. Great service! And great pricing! I know when the product is shipping and when it will arrive, all the way through the ordering process.
Trican Well Service
GO TO SOURCE
When I can't find an obsolete part, I first call GID and they'll come up with my parts every time. Great customer service and follow up as well. Scott emails me from time to time to touch base and see if we're having trouble finding something.....which is often with our 25 yr old equipment.
ConAgra Foods