ICS ADVENT Endeavor Plus
Specifications
BIOS
AMI system BIOS with 4Mbit Firmware Hub to support DMI, PnP, APM, and ACPI
Bus Interface
Follows PICMG standard (32-bit PCI and 16-bit ISA ), fully complies with PCI bus specification V2.1
Chipset
Intel 810e Chipset
CPU Core/Bus Clock Ratio
x2 to x8
CPU Front Side Bus Clock
66/100MHz
Floppy Drive Interface
Supports up to two floppy disk drives, capacities of 360K to 2.88MB
IR Interface
one 6-pin header for serial standard infrared wireless communication
Main Memory
Two 168-pin DIMM sockets, supporting 3.3V SDRAM up to 512MB (system will run ECC but will not utilize the ECC advantage; the system will not POST if a registered (buffered) DIMM is installed )
Main processor
Intel Celeron 333/366/400/433/466/500/533MHz processor or Intel Pentium III FC-370 500/550/700/800/850MHz processor.
Parallel Port
Supports SPP, Bi-direction, EPP/ECP mode
PCI IDE Interface
Supports two enhanced IDE ports up to four HDD devices with PIO mode 4 and Ultra DMA/33, Ultra DMA/66 mode transfer
PS/2 Mouse and Keyboard Interface
two 6-pin Mini-DIN connectors and one 5-pin shrouded connector for PS/2 mouse, keyboard, and backplane connections(on Legacy backplanes only)
Serial Ports
two high speed 16C550 compatible UARTs with 16-byte T/R FIFOs
USB Interface
two USB (Universal Serial Bus) ports for high speed I/O peripheral devices
Features
- adapter, 3D Graphics display, and fast Ethernet interface provides full functionality and high performance to all segments of the PC market.
- PC/AT. It is perfect for building up high performance systems. The onboard Ultra-160/m SCSI
- performance Socket-370 Pentium III based CPU and is compatible with high-end computer
- systems with PCI Local Bus architecture. It is designed to meet todayís demanding speeds,
- The Endeavor Plus all-in-one single board computer accepts either a Celeron or a high
- while maintaining complete compatibility with hardware and software designed for the IBM
Datasheet
Extracted Text
The Endeavor Plus Single Board Computer Users Guide Manual PN: 931-0000-03-A February 2002 Customer Service Mailing Address: ICS Advent 6260 Sequence Drive San Diego, CA 92121-4371 Post-Sales Technical Support: 858-677-0877, option 1 800-480-0044, option 1 (in the U.S. and Canada) +44 1243 523505 (UK) 0800-91-29-04 (France) 0800-18-30-095 (Germany) Visit our site at: www.icsadvent.com Information in this document is subject to change without notice. © 2000 ICS Advent, a California Corporation. All rights reserved. The information in this document is provided for reference only. ICS Advent does not assume any liability arising out of the application or use of the information or products described herein. This document may contain or reference information and products protected by copyrights or patents and does not convey any license under the patent rights of ICS Advent, nor the rights of others. ICS Advent is a Trademark of ICS Advent. All trademarks and registered trademarks are the property of their respective owners. All rights reserved. Printed in the United States of America. No part of this publication may be reproduced, stored in a retrieval system, or transmitted, in any form or by any means, electronic, mechanical, photocopying, recording, or otherwise, without the prior written permission of the publisher. Contents Preface How to Use This Guide . . . . . . . . . . . . . . . . . . . . . . . . . . . xi Customer Comments . . . . . . . . . . . . . . . . . . . . . . . . . . . . xii Advisory Conventions . . . . . . . . . . . . . . . . . . . . . . . . . . . xiii Safety Instructions . . . . . . . . . . . . . . . . . . . . . . . . . . . . . xiv When Working Inside a Computer. . . . . . . . . . . . . . xiv Protecting Against Electrostatic Discharge. . . . . . . xvi When Operating a Computer . . . . . . . . . . . . . . . . . xvii Rack Stability . . . . . . . . . . . . . . . . . . . . . . . . . . . . . xviii Safety Standards. . . . . . . . . . . . . . . . . . . . . . . . . . . xviii Regulatory Compliance Statements . . . . . . . . . . . . . . . . xix Guarantee and Warranty Policy. . . . . . . . . . . . . . . . . . . xx Guarantee . . . . . . . . . . . . . . . . . . . . . . . . . . . . . . . . . xx Limited Warranty . . . . . . . . . . . . . . . . . . . . . . . . . . . xx Return Procedure . . . . . . . . . . . . . . . . . . . . . . . . . . . xxi Limitation of Liability. . . . . . . . . . . . . . . . . . . . . . . xxii Chapter 1 Introduction System Features . . . . . . . . . . . . . . . . . . . . . . . . . . . . . . . 1-3 Checklist . . . . . . . . . . . . . . . . . . . . . . . . . . . . . . . . . . . . . 1-6 Product Specifications . . . . . . . . . . . . . . . . . . . . . . . . . . . 1-7 System Architecture . . . . . . . . . . . . . . . . . . . . . . . . . . . 1-10 System Block Diagram . . . . . . . . . . . . . . . . . . . . . . . . . 1-12 Chapter 2 Hardware Settings Overview . . . . . . . . . . . . . . . . . . . . . . . . . . . . . . . . . . . . . 2-3 Jumpers . . . . . . . . . . . . . . . . . . . . . . . . . . . . . . . . . . . . . . 2-3 CPU Jumper Settings . . . . . . . . . . . . . . . . . . . . . . . . 2-4 Connectors . . . . . . . . . . . . . . . . . . . . . . . . . . . . . . . . . . . . 2-6 Pin Assignments . . . . . . . . . . . . . . . . . . . . . . . . . . . . 2-9 Manual PN: 931-0000-03-A, February 2002 iii Chapter 3 System Installation Overview . . . . . . . . . . . . . . . . . . . . . . . . . . . . . . . . . . . . . 3-3 Socket 370 Celeron/Pentium III Processor . . . . . . . . . . 3-3 Installing a CPU. . . . . . . . . . . . . . . . . . . . . . . . . . . . 3-3 Removing a CPU . . . . . . . . . . . . . . . . . . . . . . . . . . . 3-3 Configuring the System Bus . . . . . . . . . . . . . . . . . . 3-4 Main Memory . . . . . . . . . . . . . . . . . . . . . . . . . . . . . . . . . 3-5 Installing the Single Board Computer. . . . . . . . . . . . . . 3-6 AIC-7892 Ultra-160/m SCSI Host Adapter. . . . . . . 3-6 Onboard Intel 810e Graphics Controller. . . . . . . . . 3-7 Intel 82559 Fast Ethernet Controller . . . . . . . . . . . 3-7 Onboard LED Indicator . . . . . . . . . . . . . . . . . . . . . . 3-8 810e Chipset & ATA-66 . . . . . . . . . . . . . . . . . . . . . . 3-8 Winbond Hardware Doctor Software . . . . . . . . . . . 3-9 Flash BIOS . . . . . . . . . . . . . . . . . . . . . . . . . . . . . . . . 3-9 M-systems Flash Disk . . . . . . . . . . . . . . . . . . . . . . . . . 3-10 Installing DiskOnChip (DOC) . . . . . . . . . . . . . . . . 3-10 Watchdog Timer (WDT) Programming . . . . . . . . . . . . 3-11 Enable WDT Function . . . . . . . . . . . . . . . . . . . . . . 3-11 Initialize, Re-trigger, and Stop WDT . . . . . . . . . . 3-11 Clear CMOS Operation . . . . . . . . . . . . . . . . . . . . . . . . 3-12 Power Switch Setup . . . . . . . . . . . . . . . . . . . . . . . . . . . 3-13 Chapter 4 BIOS Setup Information Overview . . . . . . . . . . . . . . . . . . . . . . . . . . . . . . . . . . . . . 4-3 Entering Setup . . . . . . . . . . . . . . . . . . . . . . . . . . . . . . . . 4-3 Main Menu . . . . . . . . . . . . . . . . . . . . . . . . . . . . . . . . . . . 4-5 Advanced CMOS Setup Reference Tables . . . . . . . . . . . 4-6 Standard CMOS Setup Menu. . . . . . . . . . . . . . . . . . . . 4-17 Advanced CMOS Setup Menu . . . . . . . . . . . . . . . . . . . 4-17 Advanced Chipset Setup Menu . . . . . . . . . . . . . . . . . . 4-20 Power Management Setup Menu. . . . . . . . . . . . . . . . . 4-23 ACPI Standby State . . . . . . . . . . . . . . . . . . . . . . . . 4-23 S1 Sleeping State . . . . . . . . . . . . . . . . . . . . . . . . . . 4-23 S3 Sleeping State . . . . . . . . . . . . . . . . . . . . . . . . . . 4-23 PCI/Plug-n-Play (PnP) Setup . . . . . . . . . . . . . . . . . . . . 4-27 Peripheral Setup . . . . . . . . . . . . . . . . . . . . . . . . . . . . . . 4-29 Hardware Monitor Setup . . . . . . . . . . . . . . . . . . . . . . . 4-32 iv BIOS POST Check Point List . . . . . . . . . . . . . . . . . . . . 4-33 Uncompressed Initialization Codes . . . . . . . . . . . . 4-34 Bootblock Recovery Codes . . . . . . . . . . . . . . . . . . . 4-35 Uncompressed Initialization Codes . . . . . . . . . . . . 4-36 Flash BIOS Utility. . . . . . . . . . . . . . . . . . . . . . . . . . . . . 4-43 Chapter 5 Troubleshooting Overview . . . . . . . . . . . . . . . . . . . . . . . . . . . . . . . . . . . . . 5-3 BIOS Settings . . . . . . . . . . . . . . . . . . . . . . . . . . . . . . . . . 5-3 Loading the Default Optimal Setting . . . . . . . . . . . 5-3 Auto Detect Hard Disks . . . . . . . . . . . . . . . . . . . . . . 5-3 Improper Disable Operation. . . . . . . . . . . . . . . . . . . 5-4 OS Diagnostics. . . . . . . . . . . . . . . . . . . . . . . . . . . . . . . . . 5-6 ACPI Function in Windows 98 . . . . . . . . . . . . . . . . . 5-6 Display Setup . . . . . . . . . . . . . . . . . . . . . . . . . . . . . . 5-6 Network Setup . . . . . . . . . . . . . . . . . . . . . . . . . . . . . 5-6 Appendix A WDT Programming General Description. . . . . . . . . . . . . . . . . . . . . . . . . . . . A-3 Related CR for WDT Programming . . . . . . . . . . . . . . . A-5 WDT Programmimg Guide . . . . . . . . . . . . . . . . . . . . . . A-6 v This page intentionally left blank. vi Figures Figure 1-1. Endeavor Plus . . . . . . . . . . . . . . . . . . . . . . . . . . 1-5 Figure 2-1. Endeavor Plus Jumper Locations . . . . . . . . . . . 2-3 Figure 2-2. Endeavor Plus Connectors . . . . . . . . . . . . . . . . 2-6 Figure 3-1. JP3, AT/ATX Power Select, Jumper Pins. . . . 3-13 Figure 3-2. JP3, AT/ATX Power Select, Jumper Pins. . . . 3-14 vii This page intentionally left blank. viii Preface Contents How to Use This Guide . . . . . . . . . . . . . . . . . . . . . . . . . . . ix Customer Comments . . . . . . . . . . . . . . . . . . . . . . . . . . . . . x Advisory Conventions . . . . . . . . . . . . . . . . . . . . . . . . . . . . xi Safety Instructions . . . . . . . . . . . . . . . . . . . . . . . . . . . . . xii When Working Inside a Computer. . . . . . . . . . . . . . xii Protecting Against Electrostatic Discharge . . . . . . xiv When Operating a Computer . . . . . . . . . . . . . . . . . . xv Rack Stability . . . . . . . . . . . . . . . . . . . . . . . . . . . . . . xvi Safety Standards. . . . . . . . . . . . . . . . . . . . . . . . . . . . xvi Regulatory Compliance Statements . . . . . . . . . . . . . . . xvii Guarantee and Warranty Policy. . . . . . . . . . . . . . . . . . xviii Guarantee . . . . . . . . . . . . . . . . . . . . . . . . . . . . . . . . xviii Limited Warranty . . . . . . . . . . . . . . . . . . . . . . . . . . xviii Return Procedure . . . . . . . . . . . . . . . . . . . . . . . . . . . xix Limitation of Liability. . . . . . . . . . . . . . . . . . . . . . . . xx This page intentionally left blank. x Preface Preface How to Use This Guide This manual describes how to configure your Endeavor Plus single board computer to meet various operating requirements. Note: Additional technical information, BIOS updates, and drivers are available from the ICS Advent Web site, www.icsadvent.com, under Technical Support. The following is a summary of the chapter contents: � Chapter 1: Introduction provides an overview of the system features, product specifications, and basic system architecture. � Chapter 2: Hardware Configuration Setting provides definitions and locations of jumpers and connectors. � Chapter 3: System Installation describes how to properly mount the CPU, main memory, and DiskOnChip for safe installation and provides a programming guide for the Watchdog Timer. � Chapter 4: BIOS Setup Information provides definitions of setup parameters and describes how to get advanced BIOS performance and update the BIOS with the new release available from the ICS Advent Web site. In addition, a POST checkpoint list is provided to help with troubleshooting. � Chapter 5: Troubleshooting provides a few helpful tips to quickly get the Endeavor Plus single board computer running without failure and some operating system (OS) diagnostics. � Appendix A: WDT Programming provides a general description of watchdog timer programming, configuration register definitions, and and some guidelines. How to Use This Guide xi Customer Comments If you experience any problems with this manual or just want to provide some feedback, please send us a message using the online form under Contact Us on our Web site (www.icsadvent.com) under Technical Support. Detail any errors you find. We will correct the errors or problems as soon as possible and post the revised manual in our online Support Library. Thank you. Note: You may also use the online form on our Web site to submit comments or concerns about our products, or request technical support. xii Preface Preface Advisory Conventions Three types of advisories are used throughout the manuals to provide helpful information or to alert you to the potential for hardware damage or personal injury. They are Notes, Cautions, and Warnings. The following is an example of each type of advisory. Use caution when servicing any electrical component. Note: A Note indicates information that will help you make better use of the system. . CAUTION A CAUTION indicates potential damage to hardware and tells you how to avoid the problem. WARNING A WARNING indicates the potential for bodily harm and tells you how to avoid the problem. Disclaimer: We have tried to identify all situations that may pose a warning or caution condition in this manual. However, ICS Advent does not claim to have covered all situations that might require the use of a Caution or Warning. Advisory Conventions xiii Safety Instructions Before handling the Endeavor Plus single board computer, read the following instructions and safety guidelines to prevent damage to the product and to ensure your own personal safety. Refer to the Advisories section for advisory conventions used in this manual, including the distinction between Warnings, Cautions, and Notes. � Always use caution when handling/operating the computer. Only qualified, experienced, authorized electronics service personnel should access the interior of the computer. The power supplies produce high voltages and energy hazards, which can cause bodily harm. � Use extreme caution when installing or removing components. Refer to the installation instructions in this manual for precautions and procedures. If you have any questions, please contact ICS Advent Post-Sales Technical Support. WARNING High voltages are present inside the chassis when the units power cord is plugged into an electrical outlet. Turn off system power, turn off the power supply, and then disconnect the power cord from its source before removing the chassis cover. Turning off the system power switch does not remove power to components. When Working Inside a Computer Before taking covers off a computer, perform the following steps: 1) Turn off the computer and any peripherals. 2) Disconnect the computer and peripherals from their power sources to prevent electric shock or system board damage. xiv Preface Preface 3) Follow the guidelines provided in Protecting Against Electrostatic Discharge on the following page. 4) Disconnect any telephone or telecommunications lines from the computer. In addition, take note of these safety guidelines when appropriate: � To help avoid possible damage to system boards, wait five seconds after turning off the computer before removing a component, removing a system board, or disconnecting a peripheral device from the computer. � When you disconnect a cable, pull on its connector or on its strain-relief loop, not on the cable itself. Some cables have a connector with locking tabs. If you are disconnecting this type of cable, press in on the locking tabs before disconnecting the cable. As you pull connectors apart, keep them evenly aligned to avoid bending any connector pins. Also, before connecting a cable, make sure both connectors are correctly oriented and aligned. CAUTION Do not attempt to service the system yourself except as explained in this manual. Follow installation and troubleshooting instructions closely. Safety Instructions xv Protecting Against Electrostatic Discharge Static electricity can harm system boards. Perform service at an ESD workstation and follow proper ESD procedure to reduce the risk of damage to components. ICS Advent strongly encourages you to follow proper ESD procedure, which can include wrist straps and smocks, when servicing equipment. You can also take the following steps to prevent damage from electrostatic discharge (ESD): � When unpacking a static-sensitive component from its shipping carton, do not remove the components antistatic packing material until you are ready to install the component in a computer. Just before unwrapping the antistatic packaging, be sure you are at an ESD workstation or grounded. � When transporting a sensitive component, first place it in an antistatic container or packaging. � Handle all sensitive components at an ESD workstation. If possible, use antistatic floor pads and workbench pads. � Handle components and boards with care. Dont touch the components or contacts on a board. Hold a board by its edges or by its metal mounting bracket. xvi Preface Preface When Operating a Computer When operating a computer, observe the following operating guidelines: � To help prevent electric shock, plug computer power cables into properly grounded power sources. Use cables equipped with three-prong plugs to ensure proper grounding. Do not use adapter plugs or remove the grounding prong from the cable. � Be sure nothing rests on chassis cables and that cables are not located where they can be stepped on or tripped over. � Keep objects out of chassis openings. This can cause fire or electric shock by shorting out interior components. � Keep chassis away from radiators and heat sources. Do not block cooling vents or place chassis in a closed-in wall unit. � To help protect chassis from sudden, transient increases and decreases in electrical power, use a surge suppressor, line conditioner, or uninterruptible power supply (UPS). � Consideration should be given to the connection of the equipment to the supply circuit and the effect that circuit overloading might have on overcurrent protection and supply wiring. Appropriate consideration of equipment nameplate ratings should be used when addressing this concern. � The ambient temperature within the rack may be greater than room ambient temperature. Installation should be such that the amount of air flow required for safe operation is not compromised. Consideration should be given to the maximum rated ambient temperature. Safety Instructions xvii Rack Stability Installation should be such that a hazardous stability condition is not achieved due to uneven loading. The chassis should be secured to the rack frame with retaining screws when it is slid in the rack. This will prevent the chassis from sliding forward on the slide rails if the cabinet is tilted or vibrated, resulting in possible mechanical or electrical damage to the system or injury to personnel. WARNING There is a real danger of a rack toppling if a heavy chassis is extended on its slide rails from the rack. ICS Advent strongly recommends you anchor the mounting rack to the floor or wall to prevent this from happening. Safety Standards The product(s) described in this manual has met the safety requirements of Underwriters Laboratories (UL) for the US and Canadian market based on ULs published Standards for Safety. xviii Preface Preface Regulatory Compliance Statements This section provides the FCC compliance statement for Class A devices and describes how to keep the system CE compliant. FCC Compliance Statement for Class A Devices The product(s) described in this manual has been tested and found to comply with the limits for a Class A digital device, pursuant to Part 15 of the FCC Rules. These limits are designed to provide reasonable protection against harmful interference when the equipment is operated in a commercial environment. This equipment generates, uses, and radiates radio frequency energy and, if not installed and used in accordance with the instructions, may cause harmful interference to radio communications. Operation of this equipment in a residential area is likely to cause harmful interference, in which case the user will be required to correct the interference at his or her own expense. Changes or modifications not expressly approved by the party responsible for compliance could void the user's authority to operate the equipment. Note: The assembler of a personal computer system may be required to test the system and/or make necessary modifications if a system is found to cause harmful interference or to be noncompliant with the appropriate standards for its intended use. CE Certification The product(s) described in this manual complies with all applicable European Union (CE) directives. For computer systems to remain CE compliant, only CE-compliant parts may be used. Maintaining CE compliance also requires proper cable and cabling techniques. Although ICS Advent offers accessories, the customer must ensure that these products are installed with proper shielding to maintain CE compliance. ICS Advent does not offer engineering services for designing cabling systems. In addition, ICS Advent will not retest or recertify systems or components that have been reconfigured by customers. Regulatory Compliance Statements xix Guarantee and Warranty Policy Guarantee A thirty day money-back guarantee is provided on all standard products sold. Special order products are covered by our Limited Warranty, however they may not be returned for refund or credit. EPROMs, RAM, Flash EPROMs or other forms of solid electronic media are not returnable for credit - but for replacement only. An extended warranty is available. Consult the factory. Refunds In order to receive a refund on a product for the purchase price, the product must not have been damaged by the customer or by the common carrier chosen by the customer to return the goods and the product must be returned complete (meaning all manuals, software, cables, etc.) within 30 days of receipt and in an as-new and resalable condition. The Return Procedure must be followed to assure a prompt refund. Restocking Charges Product returned after 30 days, and before 60 days, of the purchase will be subject to a minimum 20% restocking charge and charges for any damaged or missing parts. Products not returned within 60 days of purchase, or products which are not in an as-new and resaleable condition, are not eligible for a credit return and will be returned to the customer. Limited Warranty Effective April 1, 1998, all products carry a 2-year limited warranty. Within 2 years of purchase, ICS Advent will repair or replace, at our option, any defective product. ICS Advent will service the warranty for all standard catalog products for the first two years from the date of shipment. Please note: The 2-year warranty may not apply to special promotion items. Please consult the factory for warranty verification. xx Preface Preface The limited warranty is void if the product has been subjected to alteration, neglect, misuse, or abuse; if any repairs have been attempted by anyone other than ICS Advent or its authorized agent; or if the failure is caused by accident, acts of God, or other causes beyond the control of ICS Advent or the manufacturer. Neglect, misuse, and abuse shall include any installation, operation, or maintenance of the product other than in accordance with the users manual. No agent, dealer, distributor, service company, or other party is authorized to change, modify, or extend the terms of this Limited Warranty in any manner whatsoever. ICS Advent reserves the right to make changes or improvements in any product without incurring any obligation to similarly alter products previously purchased. Return Procedure For any Guarantee or Limited Warranty return, please contact ICS Advent Customer Service at 800-480-0044 or 858-677-0877 and obtain a Return Material Authorization (RMA) Number. All product(s) returned to ICS Advent for service or credit must be accompanied by a Return Material Authorization (RMA) Number. Freight on all returned items must be prepaid by the customer who is responsible for any loss or damage caused by common carrier in transit. Returns for Warranty must include a Failure Report for each unit, by serial number(s), as well as a copy of the original invoice showing the date of purchase. To reduce risk of damage, returns of product must be in an ICS Advent shipping container. If the original container has been lost or damaged, new shipping containers may be obtained from ICS Advent Customer Service at a nominal cost. ICS Advent owns all parts removed from repaired products. ICS Advent uses new and reconditioned parts made by various manufacturers in performing warranty repairs and building replacement products. If ICS Advent repairs or replaces a product, its warranty term is not extended. ICS Advent will normallly return your replacement or repaired items via Second Day Air. Overnight delivery or delivery via other carriers is available at an additional charge. Shipments not in compliance with this Guarantee and Limited Warranty Return Policy will not be accepted by ICS Advent. Guarantee and Warranty Policy xxi Limitation of Liability In no event shall ICS Advent be liable for any defect in hardware, software, loss, or inadequacy of data of any kind, or for any direct, indirect, incidental, or consequential damages in connection with or arising out of the performance or use of any product furnished hereunder. ICS Advents liability shall in no event exceed the purchase price of the product purchased hereunder. The foregoing limitation of liability shall be equally applicable to any service provided by ICS Advent or its authorized agent. Some sales items and customized systems are not subject to the guarantee and limited warranty. However in these instances, any deviations will be disclosed prior to sales and noted in the original invoice. ICS Advent reserves the right to refuse returns or credits on software or special order items. xxii Preface Chapter 1 Introduction Contents System Features . . . . . . . . . . . . . . . . . . . . . . . . . . . . . . . 1-3 Checklist . . . . . . . . . . . . . . . . . . . . . . . . . . . . . . . . . . . . . 1-6 Product Specifications . . . . . . . . . . . . . . . . . . . . . . . . . . . 1-7 System Architecture . . . . . . . . . . . . . . . . . . . . . . . . . . . 1-10 System Block Diagram . . . . . . . . . . . . . . . . . . . . . . . . . 1-12 Introduction System Features The Endeavor Plus all-in-one single board computer accepts either a Celeron or a high performance Socket-370 Pentium III based CPU and is compatible with high-end computer systems with PCI Local Bus architecture. It is designed to meet todays demanding speeds, while maintaining complete compatibility with hardware and software designed for the IBM PC/AT. It is perfect for building up high performance systems. The onboard Ultra-160/m SCSI adapter, 3D Graphics display, and fast Ethernet interface provides full functionality and high performance to all segments of the PC market. The Endeavor Plus single board computer will work with Intel Celeron and Pentium III processors, and supports up to 512MB of DIMM memory. The enhanced onboard PCI/IDE interface can support four drives up to PIO mode 4 and Ultra DMA/33/66 sync mode. The onboard Super I/O Chipset integrates one floppy controller, two serial ports, one keyboard controller, one hardware monitor, one IrDA port, and one parallel port. Two high performance 16C550-compatible UARTs provide 16-byte transmit/receive FIFOs, and the multi-mode parallel port supports SPP/EPP/ECP function. In addition, two USB (Universal Serial Bus) ports provide high speed data communications between peripherals and the computer. The Endeavor Plus works with standard PICMG and Legacy ISA backplanes. The onboard 32-pin DIP socket supports the M-systems DiskOnChip (DOC) 2000 product up to 144MB. The Watchdog Timer function can monitor your system status. Two 6-pin Mini-DIN connectors are provided to connect PS/2 compatible mice and keyboards. The Flash ROM BIOS can be easily updated in the field. A standard 5.25-inch drive power connector is reserved for more power for large power applications, and the additional 5-pin shrouded connector is provided for connecting to a keyboard interface on certain backplanes. The high precision Real Time Clock/ Calendar is built-in for accurate scheduling and storing configuration information. One 4-pin header is designed to support ATX power function on certain backplanes. All of these features make the Endeavor Plus excellent for stand-alone applications. System Features 1-3 There are three models related to the Endeavor Plus, as shown below: Table 1-1.Endeavor Plus Family Feature Onboard 7892 Onboard 10/100 Onboard PCI- Ultra 160/m BaseT 82559 to-ISA Bridge , SCSIHost Adapter Ethernet Controller DOC, and ISA BUS support, Model video 810 chipset Endeavor Plus VES Yes Yes Yes Endeavor Plus VE No Yes Yes Endeavor Plus V No No Yes 1-4 Introduction Introduction Two IDE Parallel port connector connectors SCSI connector Two 168-pin DIMM sockets Floppy drive connector (optional) Two serial ports Socket for Intel 810E chipset Disk-On-Chip ® Socket 370 for Pentium III or Celeron processor Intel 82559 10/100 Ultra 160 SCSI Base-T Ethernet controller (optional) VGA PS/2 display 10/100 Base-T keyboard PS/2 Ethernet (optional) mouse Figure 1-1. Endeavor Plus System Features 1-5 Checklist The Endeavor Plus package includes the following basic items: � One Endeavor Plus single board computer � One 26-to-DSUB25 Parallel cable � One Serial cable with two COM ports � One FDC cable � One ATA/66 IDE cable � One Dual USB Port Cable � One USB connector filler panel � One Ultra-160/m SCSI 68-pin cable with SE/LVD terminator (VES model only) � One CD with the 810e Graphic drivers (supporting Windows 95/98/NT 4.0, Linux, OS/2, Windows 3.1), LAN driver (supporting Windows 95/98/NT 4.0), and SCSI drivers � Four diskettes for SCSI drivers (supporting Windows 95/98/NT 4.0, Linux) (VES model only) If any of these items are damaged or missing, contact ICS Advent and save all packing materials for future replacement and maintenance. 1-6 Introduction Introduction Product Specifications � Main processor: Intel Celeron 333/366/400/433/466/500/533MHz processor or Intel Pentium III FC-370 500/550/700/800/850MHz processor. � CPU Front Side Bus Clock: 66/100MHz � CPU Core/Bus Clock Ratio: x2 to x8 � BIOS: AMI system BIOS with 4Mbit Firmware Hub to support DMI, PnP, APM, and ACPI � Main Memory: Two 168-pin DIMM sockets, supporting 3.3V SDRAM up to 512MB (system will run ECC but will not utilize the ECC advantage; the system will not POST if a registered (buffered) DIMM is installed ) � Chipset: Intel 810e Chipset � Bus Interface: Follows PICMG standard (32-bit PCI and 16-bit ISA ), fully complies with PCI bus specification V2.1 � PCI IDE Interface: Supports two enhanced IDE ports up to four HDD devices with PIO mode 4 and Ultra DMA/33, Ultra DMA/66 mode transfer � Floppy Drive Interface: Supports up to two floppy disk drives, capacities of 360K to 2.88MB � Serial Ports: two high speed 16C550 compatible UARTs with 16-byte T/R FIFOs � IR Interface: one 6-pin header for serial standard infrared wireless communication � Parallel Port: Supports SPP, Bi-direction, EPP/ECP mode � USB Interface: two USB (Universal Serial Bus) ports for high speed I/O peripheral devices � PS/2 Mouse and Keyboard Interface: two 6-pin Mini-DIN connectors and one 5-pin shrouded connector for PS/2 mouse, keyboard, and backplane connections (on Legacy backplanes only) Product Specifications 1-7 � ATX Power Control Interface: One 4-pin header to support ATX power control with Modem Ring-On and Wake-On-LAN function � Auxiliary I/O Interfaces: System reset switch, external speaker, keyboard lock and HDD activity LED � Real-Time Clock/Calendar (RTC): Real-Time Clock/Calendar with battery backup for 7-year data retention � Watchdog Timer: 1, 8, 16, 32 second and 1, 10, 30, 60 minute time-out intervals through BIOS setting or 255 intervals from 0.5 sec/min to 254.5 sec/min through software programming � DiskOnChip (DOC) Feature: Reserves one 32-pin socket for M-systems Flash Disk up to 144MB � System Monitoring Feature: Monitors CPU and system temperature, operating voltage, and fan status � High Driving Capability: Supports high driving capability for multi-slot ISA bus � External Power Connector: Supports one standard 5.25-inch disk power connector to enhance power driving � Onboard VGA: Intel 82810E integrated graphics controller with 4MB display cache � Onboard Ultra-160/m SCSI: Uses Adaptec AIC-7892 Ultra-160/m SCSI controller to support one 68-pin interface � Onboard Ethernet: Utilizes Intel 82559 Fast Ethernet controller to support RJ-45 interface at 10/100 BASE-T speed � Power Good: Onboard power good generator with 300ms to 500ms reset duration � MTBF: 100,000 hours 1-8 Introduction Introduction � Endeavor Plus Physical and Environmental Requirements: � Outline Dimension (L X W) : 338.5mm (13.32) X 121.5mm (4.78) � PCB Layout: Six layers � Power Requirements: +5V @ 6.0A (typ.), +12V @ 100mA, -12V @ 30mA o o o o � Operating Temperature: 0 C to 60 C (32 F to 140 F) o o o o � Storage Temperature: -20 C to 80 C (-68 F to 176 F) � Relative Humidity: 5% to 95%, non-condensing Product Specifications 1-9 System Architecture The Endeavor Plus provides a highly integrated system solution. The latest system architecture of the Endeavor Plus includes two main VLSI chips, 82810E GMCH (Graphics and Memory Controller Hub), and 82801AA ICH (I/O controller hub) to support Celeron and Pentium III processors, SDRAM, 3D graphics display, PCI bus interface, APM, ACPI compliant power 1 management , USB port, SMBus communication, and Ultra DMA/33/66 IDE Master. The onboard super I/O chip, W83627HF, supports a PS/2 keyboard/mouse, two UARTs, FDC, Hardware Monitor, Parallel Port, Watchdog Timer, and Infrared interface. In addition, two onboard devices (such as SCSI and LAN) give the user a more flexible and reliable application in a highly integrated environment. The CPU socket adopts the Socket 370 type to support high availability, reliability, and easy operation in general industry applications. The 82810E Hub provides an integrated memory controller and graphics capability (Direct AGP). To deliver AGP class graphics performance to computers at a reduced cost. It dynamically allocates and de-allocates system memory for complex 3D textures, preserving the benefits of standard AGP add-in solutions. Its 64-bit AGTL+ based host bus interface, optimized 64-bit DRAM interface supports two 3.3V DIMMs at the maximum bus frequency of 100 MHz. The 32-bit PCI bus interface supports four PCI masters for external backplane support. The 82801AA Hub employs the Accelerated Controller Hub architecture which makes a direct connection from the graphics and memory to the IDE controllers, the Dual USB ports, and the PCI cards. It supports two-channel dedicated Ultra DMA-33/66 IDE master interfaces, full Plug-n-Play compatibility, APIC (Advanced Programmable Interrupt Controller) interface, and internal real-time clock (RTC) to maintain the time and date of a system. It also supports a two- port USB (Universal Serial Bus) interface and PCI 2.1 Compliance operation. The Hub fully supports Operating System Directed Power Management via the Advanced Configuration and Power Interface (ACPI) specification. It is also linked via the Firmware Hub Link bus to 82802AB Firmware Hub to support BIOS read/write access. Through the PCI bus, the PC87200 PCI-to-ISA bridge is built as a highly integrated PCI-to-ISA bridge solution for the best industry applications. 1 This option is available with Omnix backplanes only. This option must be disabled in 7000, 8000, and 9000 Series systems. 1-10 Introduction Introduction The Super I/O chip W83627HF integrates two high speed serial ports, one parallel port, an SIR interface, a Watchdog Timer (WDT) which is enabled by jumper settings and triggered by software, H/W monitoring, FDD interface, and an 8042 keyboard controller with PS/2 mouse ports. This parallel port supports one PC-compatible printer port (SPP, bi-direction), Enhanced Parallel Port (EPP), and Extended Capabilities Port (ECP). The PCI-to-ISA bridge supports a standard 16-bit ISA bus interface. The Endeavor Plus supports the DiskOnChip (DOC) for the M-systems Flash Disk, ISA buffer driving for special I/ O applications and multi-ISA slots. In addition, an advanced feature is used on the Endeavor Plus to support detection and monitoring of the system temperature, operating voltage, and fan status. The 82802 Firmware Hub stores system BIOS and video BIOS, eliminating a redundant, non-volatile memory component. There are two onboard PCI devices (VES model only): the Ultra-160/m SCSI interface and the Fast Ethernet port. These devices support the full functionality of the Endeavor Plus all-in-one single board computer. The onboard SCSI device uses an Adaptec AIC-7892B Ultra-160/m SCSI controller to support one 68-pin condensed connector with 160MB/sec maximum data transfer. The other onboard PCI device (VE and VES models only), the LAN port, is powered by the Intel 82559 10/100 Ethernet Controller supports Fast Ethernet interface through the RJ- 45 port. The 810e built-in Graphics Controller supports high end graphics accelerators. It is implemented with high performance SGRAM 4MB to support color depths and high resolution up to 1600 x 1200 with 256 colors. System Architecture 1-11 System Block Diagram CELERON or PENTIUM III CLOCK GENERATOR PROCESSOR (Socket-370) AGTL+ HOST BUS TERM. 1 82810E MEMORY 2 2 SDRAM DIMM GMCH DISPLAY (421 BGA) Cache Memory Hub Link PCI BUS ULTRA 66 Dual Channel 82801AA IDE Bus Master AIC-7892 ULTRA- ICH 160/m SCSI (241 BGA) IDE 2 IDE 1 Intel 82559 10/100 BASE-T TWO USB PORTS PC87200 PCI-to-ISA Bridge 82802AB FWH LPC DiskOnChip BUFFER 2UART/LPT/FDD/IR ISA BUS SUPER I/O W83627HF Keyboard Golden Connectors Hardware WDT Mouse Monitor 1-12 Introduction Chapter 2 Hardware Settings Contents Overview . . . . . . . . . . . . . . . . . . . . . . . . . . . . . . . . . . . . . 2-3 Jumpers . . . . . . . . . . . . . . . . . . . . . . . . . . . . . . . . . . . . . . 2-3 CPU Jumper Settings . . . . . . . . . . . . . . . . . . . . . . . . 2-4 Connectors . . . . . . . . . . . . . . . . . . . . . . . . . . . . . . . . . . . . 2-6 Pin Assignments . . . . . . . . . . . . . . . . . . . . . . . . . . . . 2-9 Hardware Settings Overview This chapter provides jumper, header, and connector definitions and positions. Default settings from the factory are marked with an asterisk (*). Jumpers In general, jumpers on the Endeavor Plus single board computer are used to select feature options (Figure 2-1). Some jumpers are designed to be user-configurable, allowing for system enhancement. The others are used for testing purposes only and should not be altered. SCSI Termination (JP8) FWH Write Protection (JP7) Safe Mode (JP6) SCSI Enable/Disable (JP4) 23 12 1 21 2 CMOS Clear Function (JP1) 2 DIMM2 DIMM1 ATX Power Button (JP2) 2 AT/ATX Power Select (JP3) 82810E 2 4 6 AIC-7892B W83627HF 3 5 82801AA 82559 Socket 370 PC87200 Ethernet (JP15) 2 4 6 8 23 Disk-On-Chip (JP12) Watchdog Timer (JP16) 3 5 2 Figure 2-1. Endeavor Plus Jumper Locations Overview 2-3 CPU Jumper Settings Note: There is no hardware jumper for CPU core/bus ratio. This configuration is handled through the BIOS. (Hardware Monitoring Setup Menu) Note: To enable the Watchdog Timer (WDT), and have WDT ready for trigger, cover the jumper cap for JP16 then configure the Watchdog Timer Controller option in BIOS Advanced Chipset Setup to determine when the first WDT trigger should be activated. Please refer to Chapter 3 for details. Note: The FWH (Firmware Hub) Write Protection option jumper enables/disables the BIOS chip as a flashable ROM. Note: Refer to Chapter 3 for correct clear CMOS operation. Note: Enabling JP6 will force the system to run with x2 core/bus ratio. Note: Enabling JP8 will produce a SCSI termination onboard. 2-4 Hardware Settings Hardware Settings JP1: CMOS Clear Function JP3: AT/ATX Power Select NA: Normal operation* 3-5, 4-6:Select ATX Power Supply Short: Clear CMOS contents 1-3, 2-4: Select AT Power Supply* JP4: Onboard SCSI Enable/Disable JP4: Onboard SCSI Enable/Disable 1-2: Enable* 1-2: Enable* 2-3: Disable 2-3: Disable JP6: Safe Mode Enable/Disable JP7: FWH Write Protection Short: Enable Short: Disabled (flashable)* NA: Disable* NA: Enabled (non-flashable) JP8: SCSI Termination JP12: DiskOnChip Settings Short: Disable 1-2: D8000-D9FFF* NA: Enable* 3-4: DA000-DBFFF 5-6: DC000-DDFFF 7-8: DE000-DFFFF JP15: Onboard Ethernet Enable/Disable JP16: Watchdog Timer Enable/Disable 1-2: Enable* Short: Enabled hardware WDT function 2-3: Disable NA: Disabled hardware WDT function* JP2: ATX Power Button Interface 1: Power Button Control Signal 2: Momentary Switch Control Signal Jumpers 2-5 Connectors Connect the optional I/O peripheral devices and the Flash disk to the following connectors and the DOC socket on the Endeavor Plus. CAUTION Your Endeavor Plus single board computer will be permanently damaged if you install USB cables backwards into the two-port USB connector. Refer to the drawing below for the correct orientation. Note red wires should be on opposite sides. IDE 2 (Secondary) (J6) Parallel Port (J7) Floppy Drive (J4) IDE 1 (Primary) (J3) SCSI Interface (J2) COM1 (J9) 1 DIMM2 2 COM2 (J10) 1 DIMM1 2 Speaker (J5) 3 ATX Power Cntrl (J11) 4 IrDA (infrared) (J13) 1 82810E 2 16 3 AIC-7892B 4 5 W83627HF 1 IDE1/IDE2/SCSI 82801AA 82559 2 Active LED (J12) VGA (J15) Socket 370 PC87200 PS/2 mouse (J17) CPU Fan Pwr (J20) 2 3 PS/2 keyboard (J22) External USB (J16) M-systems Flash Disk (U38) (Red) 1 9 2 10 (Red) 5.25 Drive Pwr (J19) Chassis Fan Pwr (J21) 3 2 10/100 Base-T PS/2 Ethernet keyboard VGA display (optional) PS/2 mouse Figure 2-2. Endeavor Plus Connectors 2-6 Hardware Settings Hardware Settings Table 2-1. Connector Descriptions Connector Function Remark J1 System reset J2 Onboard Ultra-160/m SCSI interface One 68-pin connector (VES model only) J3 IDE 1 (Primary) interface J4 Floppy connector J5 External speaker interface J6 IDE2 (Secondary) interface J7 Parallel port connector J8 Keyboard lock and power indicator J9 COM1 serial port 2 x 5 shrouded header J10 COM2 serial port 2 x 5 shrouded header J11 ATX power control interface Connect to ACPI compliant backplane JP2 ATX power button interface J12 IDE1/IDE2/SCSI Active LED Header LED Indicator J13 IrDA (infrared) port J14 Onboard Ethernet interface connector RJ-45 (VE and VES models only) J15 Onboard VGA connector D-SUB 15 J16 Two-port USB interface Optional cable not included J17 PS/2 mouse connector 6 pin Mini-DIN Connectors 2-7 Connector Function Remark J18 External keyboard interface Connect to backplane (Legacy backplane only with special cable) J19 Standard 5.25-inch disk drive power Connect to power Connector supply J20 CPU Fan power connector J21 Chassis Fan power connector Monitors one tach fan. J22 PS/2 keyboard connector 6 pin Mini-DIN U28 Socket 370 PGA/FCPGA Celeron/P-III CPU U38 M-system Flash Disk DIP 32 pin chip DIMM 1 2 DIMM socket 3.3V SDRAM PC 100 2-8 Hardware Settings Hardware Settings Pin Assignments J1: Reset Header Pin Pin 1 Reset 2 Ground J2: Ultra-160/m SCSI Connector (high density J3/J6: IDE 2/IDE 1 Interface Connector 68-pin) Pin Pin Pin Pin 1 RESET# 2 Ground 1 LVDP12 2 Data 0 3 Data 7 4 Data 8 3 Data 4 Data 2 5 Data 6 6 Data 9 5 Data 3 6 Data 4 7 Data 5 8 Data 10 7 Data 5 8 Data 6 9 Data 4 10 Data 11 9 Data 7 10 Acknowledge # 11 Data 3 12 Data 12 11 Busy 12 Paper Empty 13 Data 2 14 Data 13 13 Printer Select 14 Auto Form Feed # 15 Data 1 16 Data 14 15 Error # 16 Initialization # 17 Data 0 18 Data 15 17 Printer Select IN # 18 Ground 19 Ground 20 NA 19 Ground 20 Ground 21 DMA REQ 22 Ground 21 Ground 22 Ground 23 IOW# 24 Ground 23 Ground 24 Ground 25 IOR# 26 Ground 25 Ground 26 NA 27 IOCHRDY 28 Pull-down 27 LVSELP 28 LVCDP 29 DMA ACK# 30 Ground 29 LVREQP 30 LVIOP 31 INT REQ 32 NA 31 LVDP8 32 LVDP9 33 SA1 34 NA 33 LVDP10 34 LVDP11 35 SA0 36 SA2 35 LVDP12 36 LVDP13 37 HDC CS0# 38 HDC CS1# 37 LVDP14 38 LVDP15 39 HDD Active# 40 Ground 39 LVDPHM 40 LVDM0 41 LVDM1 42 LVDM2 43 LVDM3 44 LVDM4 45 LVDM5 46 LVDM6 47 LVDM7 48 LVDPLM 49 Ground 50 SENSE_A(Pull-up) 51 LVTRMPWR 52 LVTRMPWR 53 NA 54 Ground 55 LVATNM 56 Ground 57 LVBSYM 58 LVACKM 59 LVRSTM 60 LVMSGM 61 LVSELM 62 LVCDM 63 LVREQM 64 LVIOM 65 LVDM8 66 LVDM9 67 LVDM10 68 LVDM11 Connectors 2-9 J4: FDC Interface Controller J7: Parallel Port Connector Pin Pin Pin Pin 1 Ground 2 Density Select 1 Strobe # 2 Data 0 3 Ground 4 NA 3 Data 1 4 Data 2 5 Ground 6 NA 5 Data 3 6 Data 4 7 Ground 8 Index# 7 Data 5 8 Data 6 9 Ground 10 Motor ENA# 9 Data 7 10 Acknowledge # 11 Ground 12 Drive Select B# 11 Busy 12 Paper Empty 13 Ground 14 Drive Select A# 13 Printer Select 14 Auto Form Feed # 15 Ground 16 Motor ENB# 15 Error # 16 Initialization # 17 Ground 18 Direction# 17 Printer Select IN# 18 Ground 19 Ground 20 Step# 19 Ground 20 Ground 21 Ground 22 Write Data# 21 Ground 22 Ground 23 Ground 24 Write Gate# 23 Ground 24 Ground 25 Ground 26 Track 0# 25 Ground 26 NA 27 Ground 28 Write Protect # 29 NA 30 Read Data # 31 Ground 32 Head Select # 33 NA 34 Disk Change # J5: External Speaker Header J8: Keyword Lock Header Pin Pin 1 Speaker signal 1 +5V (220 ohm pull-up for power LED) 2 NA 2 NA 3 Ground 3 Ground 4 +5V 4 Keyboard inhibit 5 Ground J9/J10: Serial Port 2x5 Shrouded Connector J11: ATX Power Control Connector Pin Pin Pin 1 Data Carrier Detect 2 Receive Data 1 ATX Power Good Signal (DCD) (RXD) 2 ATX 5 V Standby 3 Transmit Data 4 Data Term Ready 3 ATX Power On Control (TXD) (DTR) 4 Ground 5 Ground 6 Data Set Ready (GND) (DSR) 7 Request to Send 8 Clear to Send (RTS) (CTS) 9 Ring Indicator 10 NA (RI) 2-10 Hardware Settings Hardware Settings J12: IDE 1/IDE 2/SCSI Active LED Header J13: Standard IrDA Header Pin Pin 1 +5V (470 ohm pull-up for HDD LED) 1 VCC ( +5V) 2 HDD Active # (LED cathode terminal) 2 IOVSB 3 IRRX 4 Ground 5 IRTX 6 NA J14: Ethernet RJ-45 Interface Connector J15: VGA DSUB-15 Connector Pin Pin 1 TX+ 1 R 2 TX- 2 G 3 RX+ 3 B 4 Termination to Ground 4 NA 5 Termination to Ground 5 Ground 6 RX- 6 Ground 7 Termination to Ground 7 Ground 8 Termination to Ground 8 Ground 9 NA 10 Ground 11 NA 12 MONID1 13 HSYNC 14 VSYNC 15 MONID2 J16: External USB Interface Connector J17: PS/2 Mouse Connector (6-pin Mini- DIN) Pin Pin Pin 1 +5V 2NA 1 Mouse Data 3 SBD0- (USBP0-) 4 Ground 2 NA 5 SBD0+ (USBP0+) 6 SBD1+ (USBP1+) 3 Ground 7 Ground 8 SBD1- (USBP1-) 4 +5V 9 NA 10 +5V 5 Mouse Clock 6 NA J18: External Keyboard Connector J19: Standard 5.25-inch Disk Drive Connector Pin Pin Pin 1 Keyboard Clock 1 +12V 2 Ground 2 Keyboard Data 3 Ground 4 +5V 3 NA 4 Ground 5 +5V Connectors 2-11 J20: CPU Fan Power Connector J21: Chassis Fan Power Connector Pin Pin 1 Ground 1 Ground 2 +12V 2 +12V 3 FAN_status (pull-up 5V) 3 FAN status (pull-up 5V) J22: PS/2 Keyboard Connector (6-pin Mini-DIN) Pin 1 Keyboard Data 2 NA 3 GND 4 +5V 5 Keyboard Clock 6 NA 2-12 Hardware Settings Chapter 3 System Installation Contents Overview . . . . . . . . . . . . . . . . . . . . . . . . . . . . . . . . . . . . . 3-3 Socket 370 Celeron/Pentium III Processor. . . . . . . . . . . 3-3 Installing a CPU . . . . . . . . . . . . . . . . . . . . . . . . . . . . 3-3 Removing a CPU . . . . . . . . . . . . . . . . . . . . . . . . . . . . 3-3 Configuring the System Bus. . . . . . . . . . . . . . . . . . . 3-4 Main Memory. . . . . . . . . . . . . . . . . . . . . . . . . . . . . . . . . . 3-5 Installing the Single Board Computer . . . . . . . . . . . . . . 3-6 AIC-7892 Ultra-160/m SCSI Host Adapter . . . . . . . 3-6 Onboard Intel 810e Graphics Controller . . . . . . . . . 3-7 Intel 82559 Fast Ethernet Controller . . . . . . . . . . . 3-7 Onboard LED Indicator . . . . . . . . . . . . . . . . . . . . . . 3-8 810e Chipset & ATA-66 . . . . . . . . . . . . . . . . . . . . . . 3-8 Winbond Hardware Doctor Software. . . . . . . . . . . . 3-9 Flash BIOS . . . . . . . . . . . . . . . . . . . . . . . . . . . . . . . . 3-9 M-systems Flash Disk . . . . . . . . . . . . . . . . . . . . . . . . . . 3-10 Installing DiskOnChip (DOC) . . . . . . . . . . . . . . . . 3-10 Watchdog Timer (WDT) Programming . . . . . . . . . . . . 3-11 Enable WDT Function . . . . . . . . . . . . . . . . . . . . . . 3-11 Initialize, Re-trigger, and Stop WDT . . . . . . . . . . . 3-11 Clear CMOS Operation . . . . . . . . . . . . . . . . . . . . . . . . . 3-12 Power Switch Setup. . . . . . . . . . . . . . . . . . . . . . . . . . . . 3-13 System Installation Overview This chapter describes how to set up and configure the Endeavor Plus single board computer, M-systems Flash Disk, onboard PCI devices, and the onboard Watchdog Timer (WDT). Socket 370 Celeron/Pentium III Processor Installing a CPU After shutting down the system, disconnecting power, and taking the CPU board to an ESD workstation, follow the these steps: 1) Lift the lever of the CPU socket outwards and upwards to the fully open position. 2) Align the processor pins with the pin holes on the socket. Make sure that the notched corner or dot mark (pin 1) of the CPU corresponds to the sockets bevel end. Then press the CPU gently until it fits into place. If this operation is not easy or smooth, dont do it forcibly. 3) Push down the lever to lock the processor chip (CPU) into the socket. 4) Follow the installation guide for the CPU cooling fan or heat sink to mount the fan or heat sink on the CPU surface and lock it on the socket 370. Removing a CPU After shutting down the system, disconnecting power, and taking the CPU board to an ESD workstation, follow the these steps: 1) Unlock the cooling fan first. 2) Lift the lever of the CPU socket outwards and upwards to the fully open position. Overview 3-3 3) Carefully lift up the existing CPU to remove it from the socket. 4) Follow the steps of installing a CPU to install another one, or push the handling bar down to close the opened socket. Configuring the System Bus Please note that the Endeavor Plus will automatically detect the system bus based on the CPU used. 3-4 System Installation System Installation Main Memory The Endeavor Plus has two 168-pin DIMM slots that hold up to 512MB of 3.3V SDRAM. Memory must be a PC100-compliant memory chip at a FSB clock frequency of 100MHz. For best compatibility, procure tested memory modules from ICS Advent. If you need to source memory from an outside vendor, choose well known suppliers such as Micron, Kingston, or Crucial. A single or double-sided DIMM can be used. The two DIMMs can be any size up to 256MB. Ensure adequate memory module contact and lock integrity with the DIMM socket. This will impact the system reliability. Follow the normal procedure to install an SDRAM module into the memory socket. Before locking the DIMM into place, make sure that the module has been fully inserted into the DIMM slot. Note: (1) For maintaining system stability, do not change any of the SDRAM parameters in BIOS setup to upgrade your system performance without acquiring technical information. (2) Due to the Intel 810e chipset, ECC or buffered (registered) SDRAM is not supported. If ECC SDRAM is used, the system will respond with a warning message indicating that this type of SDRAM will not benefit the system. Buffered (registered) SDRAM will simply freeze up the system if installed. Main Memory 3-5 Installing the Single Board Computer CAUTION Be sure to take proper care electrostatic precautions before starting any work. CAUTION Ensure the single board computer is properly inserted and secured to the chassis so contacts remain in place. To install the Endeavor Plus single board computer into a standard chassis or a proprietary environment, perform the following steps: 1) Ensure that all jumper settings are in their proper position. 2) Install and configure the CPU and memory module(s) in the right position. 3) Place the Endeavor Plus into the determined position in your system. 4) Attach cables to existing peripheral devices as appropriate and secure them to the . chassis with the screw on the L-bracket AIC-7892 Ultra-160/m SCSI Host Adapter The following table shows how to enable and disable the onboard Ultra-160 SCSI function using JP4. The 7892 SCSI driver is in the SCSI directory of the Endeavor Plus CD. JP4 FUNCTION 1-2 Enable onboard SCSI 2-3 Disable onboard SCSI 3-6 System Installation System Installation Onboard Intel 810e Graphics Controller The Intel 810e chipset is the result of a new design approach to optimize the shared memory architecture while maintaining the cost benefits of integration through Direct AGP and Dynamic Video Memory Technology. If no additional VGA card is inserted in any of the ISA/PCI slots, the onboard Intel 810e graphics controller will provide the system display output. However, the system will, by default, switch to an external VGA adapter if one is present. The VGA driver is in the VGA directory of the Endeavor Plus CD. � For Windows 95/98, use the installation files in Drivers\Graphics\Win9x. Execute setup.exe to complete driver installation. � For Windows NT 4.0, user the installation files in Drivers\Graphics\Winnt4. Execute setup.exe to complete driver installation. Intel 82559 Fast Ethernet Controller The following table shows how to enable and disable the onboard Intel 82559 LAN function using JP15. The 82559 LAN driver is in the Ethernet directory of the Endeavor Plus CD. JP15 FUNCTION 1-2 Enable onboard LAN 2-3 Disable onboard LAN Installing the Single Board Computer 3-7 Onboard LED Indicator The Endeavor Plus has three LED indicators for LAN interface status. LAN speed LED (left side) : ON = 100Mbps activity OFF = 10Mbps activity LAN active LED (middle) : ON = Tx/Rx activity OFF = no activity LAN Link Integrity LED (right side) : ON = link is good in either 10 or 100 Mbps OFF = link is bad 810e Chipset & ATA-66 A few hardware features of the 810e chipset are, by default, not recognized by Windows 95/98. Load the 810e INF (Incremental Fix) patches to bring up the drivers so the operating system will recognize these hardware features. The INF driver is in the IDE/INF directory of the Endeavor Plus CD. (Note: This driver only supports Windows 95, Windows 98, and Windows 98 Second Edition). Execute setup.exe to complete the driver installation. Also, the 810e chipset supports the ATA-66 mode, which requires the ATA-66 driver for the real ATA-66 to function properly. The ATA-66 driver is in the IDE directory. After installation, simply select from the Windows Start menu as Program / Intel Ultra ATA Storage / Companion to bring up the user interface. Click on the device available at the left pane and it will simply prompt the corresponding device information at the right pane. Note: (1) This driver only supports Windows 98, Windows 98 Second Edition, and Windows NT 4.0. (2) For correct operation of ATA-66, use an 80-pin IDE cable instead of a 40-pin IDE cable for IDE devices to avoid unstable performance. 3-8 System Installation System Installation Winbond Hardware Doctor Software The hardware monitor software, HWDOCTOR, is provided on the CD. This software detects system information and reports it through a GUI. Information detected includes: � CPU Vcore, Vcc1.8, Vcc3.3, and system DC voltage � System and CPU temperature A warning message and beeping will occur if the current reading is outside of the upper and lower boundary values. System information, may be monitored and boundary values can be configured online through the graphical user interface (GUI). This software works with Windows 95/98 and Windows NT 4.0. Flash BIOS The following table shows how to enable and disable the Firmware Hub protection using JP7. To flash in a new BIOS file into the BIOS chip, disable the protection first. JP7 FUNCTION NA Enable protection Short Disable protection Installing the Single Board Computer 3-9 M-systems Flash Disk The Endeavor Plus includes one 32-pin DIP socket for installing an M-systems Flash Disk from 2MB to 144MB.The DiskOnChip is not a Plug-n-Play device; its address must be manually selected using JP12. Before installing, make certain that the memory window address jumper setting (JP12) is set on the right position to prevent system conflicts. Follow the DOC (DiskOnChip) installation procedure below. Otherwise, the Flash chip may be damaged due to incorrect installation. Installing DiskOnChip (DOC) Align the DiskOnChip (DOC) with the pin holes on the socket. Ensure that the notched corner or dot mark (pin 1) of the DOC corresponds to the notched corner of the socket. Press down on the DOC gently until it fits into place. If the installation procedure is correctly performed, the Flash disk can be viewed as a normal hard disk to access read/write data. CAUTION Ensure that the DOC is inserted properly. Inserting the DOC backwards will damage it. The Endeavor Plus will instruct the user to install and utilize DOC for practical application. If you want to boot from this Flash disk, refer to the application note from M-systems. You can easily get relatively advanced information from M-systems shipping package (such as the product manual) or their Web site http://www.m-sys.com. 3-10 System Installation System Installation Watchdog Timer (WDT) Programming System will reset if no retrigger signal has been given after the set time interval Enable WDT Function The following table shows how to enable and disable the Watchdog Timer (WDT) circuit using JP16. JP16 FUNCTION Short Enable WDT NA Disable WDT This will prepare the WDT circuit to be ready for the trigger. The WDT is now in standby mode. Without adding this jumper, the WDT circuit is always turned off. Initialize, Re-trigger, and Stop WDT With the WDT enabled, you may configure the Watchdog Timer Controller option in BIOS to determine when the WDT will be initialized. Enabled = Automatically initialize WDT when booting up. Disabled = Manually initialize WDT by software at run-time After you initialize the WDT, the system will reboot if no re-trigger signal is given within a time-out interval. There are two methods to program the time-out interval. One is to specify it in the BIOS (Advanced Chipset Setup) and the other is through software programming over the super I/O W83627HF chip. The first way is recommended and easier but has fewer choices of time-out intervals. BIOS provides only eight possible ranges of timeout intervals ranging from 1 second to 60 minutes. The second method is more difficult and complicated, but provides more choices of time-out intervals. A test program is available in Appendix A, "WDT Programming". The program allows users to specify a refresh interval and the system will simply stay on if the selected refresh interval is less than the time-out interval specified in BIOS. Otherwise, the system will reboot. A programming guide is also included in Appendix A. Watchdog Timer (WDT) Programming 3-11 Clear CMOS Operation The following table will show you how to enable and disable the CMOS Clear Function hardware circuit using JP1. JP1 FUNCTION NA Normal Operation Short Clear CMOS To correctly operate the Clear CMOS function, apply a jumper over JP1. This will not consume any power. Then configure the (Advanced Chipset Setup) CMOS RAM Clear Function in the BIOS to Enabled. Reboot the system to produce a CMOS Check Sum Error message and hold up the system. You may then follow the displayed message to load the BIOS default setting. 3-12 System Installation System Installation Power Switch Setup * Momentary Power Switch Setup To configure the single board computer to accommodate Omnix chassis with a momentary on/off switch, follow these steps: 1) Select jumper pins 3-5 and 4-6 on JP3, AT/ATX Power Select (Figure 3-1). 2) Connect JP2, ATX Power Button Interface, to the momentary power switch on the chassis. 3) Route ATX signals from the power supply to J11, ATX Power Control Connector. JP3 6 2 4 Select Jumper Pins 3-5 and 4-6 5 1 3 Figure 3-1. JP3, AT/ATX Power Select, Jumper Pins * See Wiring Diagrams in your chassis users guide. Power Switch Setup 3-13 * On/Off Power Switch Setup To configure the single board computer to accommodate Omnix chassis with an on/off switch, follow these steps: 1) Select jumper pins 1-3 and 2-4 on JP3, AT/ATX Power Select (Figure 3-2). 2) Make sure that JP2, ATX Power Button Interface, is not connected. 3) Make sure that J11, ATX Power Control Connector, is not connected. JP3 2 4 6 Select Jumper Pins 1-3 and 2-4 1 3 5 Figure 3-2. JP3, AT/ATX Power Select, Jumper Pins * See Wiring Diagrams in your chassis users guide. 3-14 System Installation Chapter 4 BIOS Setup Information Contents Overview . . . . . . . . . . . . . . . . . . . . . . . . . . . . . . . . . . . . . 4-3 Entering Setup. . . . . . . . . . . . . . . . . . . . . . . . . . . . . . . . . 4-3 Main Menu. . . . . . . . . . . . . . . . . . . . . . . . . . . . . . . . . . . . 4-5 Advanced CMOS Setup Reference Tables . . . . . . . . . . . 4-6 Standard CMOS Setup Menu . . . . . . . . . . . . . . . . . . . . 4-17 Advanced CMOS Setup Menu . . . . . . . . . . . . . . . . . . . 4-17 Advanced Chipset Setup Menu. . . . . . . . . . . . . . . . . . . 4-20 Power Management Setup Menu . . . . . . . . . . . . . . . . . 4-23 ACPI Standby State . . . . . . . . . . . . . . . . . . . . . . . . 4-23 S1 Sleeping State . . . . . . . . . . . . . . . . . . . . . . . . . . 4-23 S3 Sleeping State . . . . . . . . . . . . . . . . . . . . . . . . . . 4-23 PCI/Plug-n-Play (PnP) Setup . . . . . . . . . . . . . . . . . . . . 4-27 Peripheral Setup . . . . . . . . . . . . . . . . . . . . . . . . . . . . . . 4-29 Hardware Monitor Setup . . . . . . . . . . . . . . . . . . . . . . . 4-32 BIOS POST Check Point List . . . . . . . . . . . . . . . . . . . . 4-33 Uncompressed Initialization Codes . . . . . . . . . . . . 4-34 Bootblock Recovery Codes . . . . . . . . . . . . . . . . . . . 4-35 Uncompressed Initialization Codes . . . . . . . . . . . . 4-36 Flash BIOS Utility. . . . . . . . . . . . . . . . . . . . . . . . . . . . . 4-43 BIOS Setup Overview The Endeavor Plus is equipped with the AMIBIOS, stored in Flash ROM. This BIOS has a built-in setup program that allows users to modify the basic system configuration. This type of information is stored in CMOS RAM so that it is retained during power-off periods. When the system is turned on, the Endeavor Plus communicates with peripheral devices and checks its hardware resources against the configuration information stored in the CMOS memory. If any error is detected, or the CMOS parameters need to be initially defined, the diagnostic program will prompt the user to enter the Setup program. Some errors are significant enough to abort the startup. Entering Setup Turn on or reboot the computer. When the message Hit [DEL] if you want to run SETUP appears, press the [Del] key immediately to enter BIOS Setup program. If the message disappears before you respond, but you still wish to enter Setup, please restart the system to access COLD START again by turning the system OFF and then ON or touch the [RESET] button. You may also restart from WARM START by pressing the [Ctrl+Alt+Delete] keys simultaneously. If you do not press the keys at the same time the system will not boot, and the following error message will be displayed and you will again be asked to, Press [F1] to Run Setup or Resume In HIFLEX BIOS Setup, the keyboard can be used to choose among options or modify the system parameters to match the options with your system. The table below will show you all of the keystroke functions in BIOS Setup. Overview 4-3 Table 4-1. Keystroke Functions in BIOS Setup EDITING KEYS FUNCTION [Tab] Move to the next field Move the next field to the left, above, below, or right [Enter] Select in the current field [+ / -] Increases / Decreasess a value [Esc] Close the current operation and return to previous level [PgUp] Returns to the previous option [PgDn] Advances to the next option [F2]/[F3] Select background color [F10] Shows Save current settings and exit (Y/N) in main menu 4-4 BIOS Setup Information BIOS Setup Main Menu Once in the Endeavor Plus AMIBIOS CMOS Setup Utility, the main menu will appear. From the main menu you can select from eleven Setup functions and two exit choices. Use the arrow keys to switch the items and press the [Enter] key to accept or enter the sub-menu. AMIBIOS HIFLEX SETUP UTILITY-VERSION 1.23 (C) 1999 American Megatrends , Inc. All Rights Reserved Standard CMOS SETUP Advanced CMOS SETUP Advanced Chipset SETUP Power Management SETUP PCI/Plug and Play SETUP Peripheral SETUP Hardware Monitor SETUP Auto-Detect Hard Disks Change User Password Change Supervisor Password Auto Configuration with Optimal Settings Auto Configuration with Fail Safe Settings Save Settings and Exit Exit Without Saving Standard CMOS SETUP for changing time, date, hard disk type, etc. ESC : Exit ??: Sel F2/F3 : Color F10 : Save & Exit Note: Note: It is strongly recommended to reload Optimal Setting if CMOS is lost or the BIOS is updated. Main Menu 4-5 Advanced CMOS Setup Reference Tables These Setup reference tables include all of the Optimal, Failsafe, and Other Options settings in each BIOS Setup item. It is very easy to cross reference. For details, you can refer to the item description in the sub-section. Table 4-2. Advanced CMOS Setup Defaults BIOS Setup Items Optimal Default Failsafe Other Options Default Quick Boot Enabled Disabled 1st Boot Device IDE-0 IDE-0 IDE-1, IDE-2, IDE-3, Floppy, CDROM, ATAPI ZIP, LS-120, SCSI, SetupNetwork 2nd Boot Device Floppy Floppy IDE 1, CDROM 3rd Boot Device CDROM CDROM IDE-1, ATAPI ZIP 4th Boot Device Disabled Disabled IDE-1, CDROM Try Other Boot Device Yes Yes No S.M.A.R.T. for Hard Disabled Disabled Enabled Disks BootUp On On Off Num-Lock PS/2 Mouse Support Enabled Enabled Disabled System Keyboard Absent Absent Present Primary Display VGA/EGA Absent VGA/EGA, Mono 4-6 BIOS Setup Information BIOS Setup Table 4-2. Advanced CMOS Setup Defaults (Continued) BIOS Setup Items Optimal Default Failsafe Other Options Default Password Check Setup Setup Always Boot To OS/2 > 64MB No No Yes L1 Cache WriteBack WriteBack WriteThru, Disabled L2 Cache WriteBack Disabled WriteThru System BIOS Enabled Disabled Cacheable C000, 16K Shadow Cached Cached Enabled, Disabled D000, 16K Shadow Disabled Disabled Cached, Enabled Advanced CMOS Setup Reference Tables 4-7 Table 4-3. Advanced Chipset Defaults BIOS Setup Items Optimal Failsafe Other Options Default Default USB Function Disabled Disabled Enabled USB Keyboard Enabled Enabled Disabled Legacy Support DRAM Page Closing Closed Closed Open Policy Memory Hole Disabled Disabled 15MB-15MB DRAM Tras/Trc Cycle 5/7 5/7 6/8 Time Address Setup Time 1s 1 0 (SCLKs) CAS# Latency 3 SCLKs 3 SCLKs 2 SCLKs SDRAM RAS# to CAS# 2 SCLKs 2 SCLKs 3 SCLKs delay SDRAM RAS# Precharge 2 SCLKs 2 SCLKs 3 SCLKs Graphics Mode Select UMA 1MB UMA 1MB UMA 512MB Display Cache 64MB 64MB 32MB Window Size ICH Delayed Transaction Disabled Disabled Enabled Local Memory Frequency 100 Mhz 100 Mhz 133 Mhz 4-8 BIOS Setup Information BIOS Setup Table 4-4. Display Cache Function BIOS Setup Items Optimal Failsafe Other Options Default Default Initialize Display Cache Enabled Enabled Disabled Memory Paging Mode Control Open Open Close RAS-to-CAS Default Default Override CAS Latency Slow Slow Fast RAS Timing Slow Slow Fast RAS Precharge Timing Slow Slow Fast Watch Dog Timer Disabled Disabled Enabled Controller Watch Dog Timer Setting 8 sec. 8 sec. 16 ,32 sec., 1,10,30,60 min. CMOS RAM Clear Disabled Disabled Enabled Function Advanced CMOS Setup Reference Tables 4-9 Table 4-5. Power Management Setup Defaults BIOS Setup Items Optimal Default Failsafe Other Options Default ACPI Standard State Disabled S1/POS S3/STR Power Management / Disabled Disabled APM Video Power Down Suspend Disabled Stand By Mode Hard Disk Power Stand By Disabled Stand By Down Mode Standby Time Out Disabled Disabled 1, 2, 4, 8, 10, (Minutes) 20, 30, 40, 50, 60 Min. Suspend Time Out Disabled Disabled 1, 2, 4, 8, 10, (Minutes) 20, 30, 40, 50, 60 Min. Throttle Slow Clock 50 % 50 % 12.5%, 25%, Ratio 37.5%, 62.5%, 75%, 87.5% Keyboard & PS/2 Monitor Monitor Ignore Mouse Access FDC/LPT/COM Ports Monitor Monitor Ignore Access Primary Master IDE Monitor Monitor Ignore Access Primary Slave IDE Ignore Ignore Monitor Access Secondary Master IDE Monitor Monitor Ignore Access 4-10 BIOS Setup Information BIOS Setup Table 4-5. Power Management Setup Defaults (Continued) BIOS Setup Items Optimal Default Failsafe Other Options Default Secondary Slave IDE Ignore Ignore Monitor Access PIRQ[A] IRQ Active Ignore Ignore Monitor PIRQ[B] IRQ Active Ignore Ignore Monitor PIRQ[C] IRQ Active Ignore Ignore Monitor PIRQ[D] IRQ Active Ignore Ignore Monitor Power Button Function On / Off On / Off Suspend Resume On Ring Enabled Enabled Disabled PME Function Support Disabled Disabled Enabled Resume On RTC Disabled Disabled Enabled Alarm RTC Alarm Date 15 15 1-14, 16-31 RTC Alarm Hour 12 12 0-11, 13-23 RTC Alarm Minute 30 30 0-29, 31-59 RTC Alarm Second 30 30 0-29, 31-59 Advanced CMOS Setup Reference Tables 4-11 Table 4-6. Peripheral Setup Defaults BIOS Setup Items Optimal Failsafe Other Default Default Options OnBoard IDE Both Both Primary, Secondary, Disabled OnBoard FDC Auto Auto Enabled, Disabled OnBoard Serial Port A Auto Auto 3F8h/COM1, 2F8h/COM2, 3E8h/COM3, 2E8h/COM4, Disabled Onboard Serial Port B Auto Auto 3F8h/COM1, 2F8h/COM2, 3E8h/COM3, 2E8h/COM4, Disabled Serial Port B Mode Normal Normal IrDA 1.6us, ASK-IR, IrDA 3/16 Baud IR Duplex Mode Half Duplex Half Duplex Full Duplex IR Pin Select IRRX/IRTX IRRX/IRTX SINB/SOUTB Onboard Parallel Port Auto Auto Disabled, 378h, 278h, 3BCh Parallel Port Mode Bi-Dir Bi-Dir EPP, ECP, Normal 4-12 BIOS Setup Information BIOS Setup Table 4-6. Peripheral Setup Defaults (Continued) BIOS Setup Items Optimal Failsafe Other (Continued) Default Default Options EPP Version N/A N/A 1.7 , 1.9 Parallel Port IRQ Auto Auto Parallel Port DMA Channel N/A N/A Auto Mouse Power On Function Disabled Disabled Left-button, Right-button Keyboard Power On Disabled Disabled Any key, Function Power Key, Specific Key Specific key for Power On N/A N/A Password Advanced CMOS Setup Reference Tables 4-13 Table 4-7. PCI/PnP Setup Defaults BIOS Setup Items Optimal Failsafe Default Other Options Default Primary Graphics Add-on VGA Add-on VGA OnBoard VGA Adapter PCI VGA Palette Disabled Disabled Enabled Snoop PCI IDE BusMaster Disabled Disabled Enabled PCI Slot1 IRQ Priority Auto Auto 3, 4, 5, 7, 9, 10, 11 PCI Slot2 IRQ Priority Auto Auto 3, 4, 5, 7, 9, 10, 11 PCI Slot3 IRQ Priority Auto Auto 3, 4, 5, 7, 9, 10, 11 PCI Slot4 IRQ Priority Auto Auto 3, 4, 5, 7, 9, 10, 11 DMA Channel 0 PnP PnP ISA/ EISA DMA Channel 1 PnP PnP ISA/ EISA DMA Channel 3 PnP PnP ISA/ EISA DMA Channel 5 PnP PnP ISA/ EISA DMA Channel 6 PnP PnP ISA/ EISA DMA Channel 7 PnP PnP ISA/ EISA IRQ3 PCI/ PnP PCI/ PnP ISA/ EISA IRQ4 PCI/ PnP PCI/ PnP ISA/ EISA IRQ5 PCI/ PnP PCI/ PnP ISA/ EISA IRQ7 PCI/ PnP PCI/ PnP ISA/ EISA 4-14 BIOS Setup Information BIOS Setup Table 4-7. PCI/PnP Setup Defaults (Continued) BIOS Setup Items Optimal Failsafe Default Other Options (Continued) Default IRQ9 PCI/ PnP PCI/ PnP ISA/ EISA IRQ10 PCI/ PnP PCI/ PnP ISA/ EISA IRQ11 PCI/ PnP PCI/ PnP ISA/ EISA IRQ12 PCI/ PnP PCI/ PnP ISA/ EISA IRQ14 PCI/ PnP PCI/ PnP ISA/ EISA IRQ15 PCI/ PnP PCI/ PnP ISA/ EISA Advanced CMOS Setup Reference Tables 4-15 * Table 4-8. Hardware Monitor Setup Defaults BIOS Setup Items Optimal Failsafe Other Default* Default Options CPU Ratio Selection 5.0x 2.0x 3-4.5x, (Safe) 5.5-8x **** System Hardware Monitor **** Current CPU Temperature Current System Temperature Current CPU Fan Speed Current Chassis Fan Speed CPU VID Vcore Vcc1.8 Vcc3.3 + 5.000V +12.000V -12.000V - 5.000V Vbat +5V SB * Optimal default depends on the CPU and is set to Auto detect 4-16 BIOS Setup Information BIOS Setup Standard CMOS Setup Menu This Setup page includes all the items in a standard compatible BIOS. Use the arrow keys to highlight the item and then use the [PgUp]/[PgDn] or [+/-] keys to select the value or number you want in each item and press the [Enter] key to certify it. Follow the command keys in the CMOS Setup tables to change Date, Time, Drive type, and Boot Sector Virus Protection Status. Advanced CMOS Setup Menu This Setup includes all of the advanced features in the system. The detailed descriptions are specified below. Quick Boot Select Disabled for normal booting, or for quicker booting, select Enabled, to skip minor BIOS test items. Boot Up Sequence Six items determine which drive the computer searches for to find the Disk Operating System (DOS). The default ARMD (ATAPI Removable Media Device) emulation type is set to popular drive type LS-120 and ATAPI ZIP. There are many devices available to boot up the system: Disabled, IDE-0, IDE-1, IDE-2, IDE-3, Floppy, LS-120, ATAPI ZIP, CD-ROM, SCSI, and NETWORK. Boot Up Num-Lock Select On to enable the numeric function of the numeric keypad, or Off to disregard it. PS/2 Mouse Support Select Enabled to enable the PS/2 mouse function, or Disabled to make the IRQ12 interrupt available to other ISA-bus I/O devices. Standard CMOS Setup Menu 4-17 System Keyboard This option is used to override a keyboard error message. Choose the Absent setting in BIOS Setup when the system has no keyboard attached. Primary Display Choose Absent, VGA/EGA, CGA40x25, CGA80x25, or Mono to set your monitor type. If you select Absent, the CMOS Display Type Wrong message will be ignored despite the mismatched display card. Password Check This option checks the system during boot up or CMOS Setup. It only takes effect after changing the setting Supervisor Password. � Entering the current user password in Change User Password will force the system to check the password before running Setup. The system will be able to boot, but will deny access to Setup. � The password prompt appears every time the system boots up. The system will not boot and will deny access to Setup with an invalid password. Clear CMOS or try reloading BIOS Setup to boot up the system. Boot to OS/2>64MB Set this option to Yes to support the OS/2 environment. L1 Cache This option turns the CPUs Level 1 built-in cache on or off. L2 Cache This option turns the CPUs Level 2 built-in cache on or off. 4-18 BIOS Setup Information BIOS Setup System BIOS Cacheable This option enhances the systems performance by shadowing and caching the system BIOS. When disabled, this BIOS shadow function will be ignored. Shadow Memory Each segment provides three options for a faster adapters ROM execution: Disabled, Enabled, and Cached. This shadow function is chipset-oriented and depends on your systems hardware features. In general, C000 64K will be allocated for VGA BIOS and set to Cached to get higher display performance by shadowing and caching feature. If you choose the Enabled setting, only the BIOS shadow function is active. Advanced CMOS Setup Menu 4-19 Advanced Chipset Setup Menu This Setup is very important to maintain system stability. If you are not a technical person, do not attempt to change any parameters. The optimal default setting is recommended. USB Function This option enables the on-chip Universal Serial Bus (USB) function to support the USB peripheral devices when the Enabled setting is selected. USB Keyboard Legacy Support This option is only available when the USB Function option is set to Enabled. Enabling this option provides support for a USB keyboard without the auxiliary driver in the DOS environment. DRAM Page Closing Policy This option controls whether the graphics and memory controller hub will pre-charge one or all banks after a page miss. Memory Hole This option allows the end user to specify the location of a memory hole for memory space requirements from ISA-bus cards. DRAM Tras/Trc Cycle Time (SCLKs) This option controls the number of SDRAM clocks (SCLKs) used per access cycle. Address Setup Time (SCLKs) This option controls the SDRAM address Setup delay time. CAS# Latency (SCLKs) This option controls the number of SCLKs between the time a read command is sampled by the SDRAMs and the time the GMCH samples transfer the data from the SDRAMs. 4-20 BIOS Setup Information BIOS Setup SDRAM RAS# to CAS# delay (SCLKs) This option controls the number of SCLKs (SDRAM Clocks) from a row that activate a command to Read or Write. If your system has good quality SDRAM, you can set this option to 2 SCLKs to obtain better memory performance. Normally, the option is set to 2 SCLKs. SDRAM RAS# Precharge This option controls the number of SCLKs for RAS# precharge. If your system installs good quality SDRAM, you can set this option to 2 SCLKs to obtain better memory performance. Graphics Mode Select This option selects memory space that is used by the video BIOS for handling support of VGA when no GMCH graphics driver is present (e.g., a DOS boot). Display Cache Window Size This option allows you to select the size of mapped memory for AGP graphical data. ICH Delayed Transaction Choose the Enabled option to obtain higher PCI bus performance for I/O controllers and bridges in the system. ClkGen Spread Spectrum This option turns the spread spectrum for EMI control on or off. Local Memory Frequency This option selects the operating frequency for the Local Memory Controller. Initialize Display Cache Memory This option enables or disables Display Cache Memory. Advanced Chipset Setup Menu 4-21 Paging Mode Control This option controls the GMCH memory controller, which tends to close open pages. RAS-to-CAS This option indicates the RAS#-to-CAS# delay in units of display cache clock periods. CAS# Latency This option selects clock periods in units of local memory. RAS# Timing This option controls the RAS# active to precharge, and refresh to RAS# active delay. RAS# Precharge Timing This option controls the RAS# precharge in local memory clocks. Watchdog Timer Controller (WDT) This option turns the Watchdog Timer on or off. Watchdog Timer Setting This option selects the WDT Timeout Interval Setting. CMOS RAM Clear Function If your system supports Y2K RTC, set this option to Enabled to support hardware CMOS clearing operation. 4-22 BIOS Setup Information BIOS Setup Power Management Setup Menu This APM (Advanced Power Management) determines how much power can be saved by setting the items below to handle the system power resource. The following descriptions specify the definition of each item in detail. ACPI Standby State This option supports ACPI standby state S1(POS) and S3(STR) and is not supported by Legacy backplanes. S1 Sleeping State Places the processor into the STPCLK grant state.Throttles the processors input clock to run the duty cycle (See Throttle Slow Clock Ratio), placing the processor into the stop clock state. The system clocks (PCI and CPU) continue to run during the sleeping state. Any wakeup event should cause the hardware to de-assert the STPCLK# signal to the processor. S3 Sleeping State All devices on the computer are turned off except for the system RAM. Power Management/APM Advanced Power Management (APM) controls the systems power resources. Set this option to Enabled to enable the power management function. It will operate based on parameter settings. This option is not supported by Legacy backplanes. Video Power Down Mode This option activates the power-conserving state that the VESA VGA video subsystem enters after the specified period of display inactivity. Power Management Setup Menu 4-23 Hard Disk Power Down Mode This option specifies the power management state that the HDD enters after the specified period of hard drive inactivity. This is similar to the video power control function. If the user chooses Standby or Suspend, it will depend on the period specified in the parameters Standby Timeout or Suspend Timeout. Standby Time out (Minutes) This option specifies the length of time the system is inactive while the computer is in its full- on power state before the computer is placed in Standby mode. When this time expires, the computer enters Standby Timeout state. In Standby mode, some power use is curtailed. Suspend Timeout (Minutes) This option is the same as the Standby Timeout function. These two features must monitor the power of sub-items Display Activity, Serial Port, Parallel Port, Floppy, Pri-HDD, and Sec- HDD independently. It is also used to control the CPU throttle running function. None of the sub-items will operate when either Stanby Timeout or Suspend Timeout are disabled, even if they are selected in the BIOS Setup menu. Throttle Slow Clock Ratio This option indicates whether the speed at which the system clock runs in system power-saving modes. The settings are expressed as a duty cycle of the STPCLK# signal. This duty cycle indicates the percentage of time the STPCLK# signal is asserted in the throttle mode. Display Activity This option specifies if the BIOS is set to monitor activity on the display monitor for power conservation purposes. If it is set to Monitor and the computer is in a power saving state, BIOS watches for video display activity. The computer enters the full-on power state if any activity occurs. BIOS reloads the Standby and Suspend timeout timers if activity occurs on the specified IRQ lines. If set to Ignore, video display monitor activity is not monitored. 4-24 BIOS Setup Information BIOS Setup Keyboard & PS/2 Mouse, FDC/LPT/COM Ports, Pri/Sec HDD Access When set to Monitor, these options enable event monitoring on the specified hardware device. If set to Monitor and the computer is in a power saving state, BIOS watches for activity on the device with the specified IRQ line. The computer enters the full-on power state if any activity occurs. BIOS reloads the Standby and Suspend timeout timers if activity occurs on the specified device. No monitoring activity occurs if the option is set to Ignore. The settings for each of these options are Monitor or Ignore. PIRQ [A/B/C/D] IRQ Active When set to Monitor, these options enable event monitoring on the specified IRQ. If set to Monitor and the computer is in a power saving state, BIOS watches for activity on the device with the specified IRQ line. The computer enters the full-on power state if any activity occurs. BIOS reloads the Standby and Suspend timeout timers if activity occurs on the specified IRQ. No monitoring activity occurs if the option is set to Ignore. The settings for each of these options are Monitor or Ignore. Power Button Function This item is used to handle Soft Power On/Off regardless of time counting (generally speaking, it is 4 sec) if you set it to on/off. You can easily turn the system on/off by pressing the power button (toggle switch) directly. This feature is only available on a system with an ATX power control interface. If a standard AT power supply is used, this option will be ignored. However, if you choose the Suspend setting, the system will be forced into suspend mode when you turn it off, unless you can continuously press the power button for more than 4 seconds to access the Soft Off function. Resume On Ring This item will be used to wake up the system from the remote ringing control under the Soft Off function. If you choose the Disabled setting, the system will not be resumed by a modem ring. PME Function Support Enable this option to allow your computer to be booted from another computer via a network, by sending a wake-up frame or signal. Power Management Setup Menu 4-25 Resume On RTC Alarm This option controls an unattended or automatic system power up. � RTC Alarm Date � RTC Alarm Hour � RTC Alarm Minute � RTC Alarm Second 4-26 BIOS Setup Information BIOS Setup PCI/Plug-n-Play (PnP) Setup This section describes configuring the PCI bus system. PCI (Peripheral Component Interconnect) is a system which allows I/O devices to operate at speeds nearing the CPUs speed when they communicate with their own special components. All of the options described in this section are important and technically complex. It is strongly recommended that only experienced users make changes to the default settings. Plug-n-Play Aware O/S Set this option to Yes if the operating system installed in the computer is Plug-n-Play aware. BIOS only detects and enables PnP ISA adapter cards that are required for system boot. The Windows 95 operating system detects and enables all other PnP-aware adapter cards. Windows 95 is PnP-aware. Set this option to No if the operating system (such as DOS, OS/2, Windows 3.x) does not use PnP. You must set this option correctly or PnP-aware adapter cards installed in your computer will not be configured properly. Clear NVRAM This option is used to clear NVRAM and to check or update ESCD (Extended System Configuration Data) data after a System Power On. Set this option to No; it will not clear NVRAM. The operation of update ESCD is effective in a different ESCD data comparision. If you select the Yes setting, the BIOS will update ESCD each time the system powers on. PCI Latency Timer (PCI Clocks) This option is used to control the PCI latency timer period (follow the PCI clocks). Based on PCI specification 2.1 or later and the PCI bus frequency in the system, users can select different timers to meet their PCI bus environment. Primary Graphics Adapter This option allows you to specify a primary VGA display from two options: Onboard VGA or a PCI VGA card. PCI/Plug-n-Play (PnP) Setup 4-27 PCI VGA Palette Snoop Some display cards that are nonstandard VGA, such as graphics accelerators or MPEG video cards, may not show colors properly. Choose the Enabled setting to correct this display mis-match problem. The computer requires VGA palette snooping to support any ISA adapter card installed. PCI IDE BusMaster Set this option to Enabled to specify that the IDE controller on the PCI local bus has a bus-mastering capability. PCI Slot 1/2/3/4 IRQ Priority These options specify the IRQ priority to be used for any PCI devices installed in PCI expansion slots 1 through 4. The settings are (IRQ) 3, 4, 5, 7, 9, 10, 11, and Auto (AMIBIOS automatically determines the IRQ priority). DMA Channel 0/1/3/5/6/7\ These options specify whether the named DMA channel is available for use on the ISA/EISA bus or PnP (Plug-n-Play). IRQ 3/4/5/7/9/10/11/12/14/15 These options specify the bus that the named interrupt request lines (IRQs) are used on. These options allow you to specify IRQs for use by legacy ISA adapter cards. These options determine if AMIBIOS should remove an IRQ from the pool of available IRQs passed to devices that are configurable by the system BIOS. The available IRQ pool is determined by reading the ESCD NVRAM. If more IRQs must be removed from the pool, the end user can use the PCI/PnP Setup to remove the IRQ by assigning the option to the ISA/EISA setting. All IRQs used by onboard I/O are configured as PCI/PnP. 4-28 BIOS Setup Information BIOS Setup Peripheral Setup This section describes I/O resource assignments for all onboard peripheral devices. Onboard IDE This option specifies the onboard IDE controller channels that will be used. The settings are Disabled, Primary, Secondary, and Both. Onboard FDC If you want to install a different add-on super I/O card to connect floppy drives, set this field to Disabled. Otherwise, set it to Auto to have BIOS automatically determine if the floppy controller should be enabled. Onboard Serial Port A/Port B These fields control the resource assignments of two onboard serial interfaces SIO1 and SIO2. The following lists show current options in Onboard Serial Port A/ Port B : Auto � cannot set serial I/O resources by manual operation Disabled � indicates onboard COM port function is ineffective 3F8h/COM1 � assign I/O address 3F8h to COM1 2F8h/COM2 � assign I/O address 2F8h to COM2 3E8h/COM3 � assign I/O address 3E8h to COM3 2E8h/COM4 � assign I/O address 2E8h to COM4 Serial Port B Mode This option controls the resource assignments of onboard Serial Port B. The Serial Port B Mode Select has four settings: Normal, IrDA 1.6us, IrDA 3/16 Baud, and ASK IR. IR Duplex Mode IR Duplex Mode has two settings: Half Duplex and Full Duplex. IR Pin Select IR Pin Select has two options: IRRX/IRTX and SINB/SOUTB. Peripheral Setup 4-29 Onboard Parallel Port There are four optional parallel port modes used to control the onboard parallel port interface when the user selects the I/O base address manually: Parallel Port Mode, EPP Version, Parallel Port IRQ, and Parallel Port DMA Channel. The following are available options of the onboard parallel port: Auto � user can not control all of LPT port I/O resources Disabled � onboard parallel port function is ineffective and NA 378h � locate IRQ7 for this default I/O address 278h � assign this I/O address to LPT1 3BCh � assign this I/O address to LPT1 Parallel Port Mode: This option specifies the Parallel Port Mode. ECP and EPP are both bi- directional data transfer schemes that adhere to the IEEE P1284 specifications. This Parallel Port Mode includes four options: Normal, Bi- Dir, EPP, and ECP. Table 4-9. Parallel Port Settings Setting Description Normal Uni-directional operation at normal speed Bi-Dir Bi-directional operation at normal speed EPP The parallel port can be used with devices that adhere to the Enhanced Parallel Port (EPP) specification. EPP uses the existing parallel port signals to provide asymmetric bi- directional data transfer driven by the host device. ECP The parallel port can be used with devices that adhere to the Extended Capabilities Port (ECP) specification. ECP uses the DMA protocol to achieve data transfer rates up to 2.5MB per second. ECP provides symmetric bi-directional communication. 4-30 BIOS Setup Information BIOS Setup EPP Version : This option is only valid if the Parallel Port Mode option is set to EPP. This option specifies the version of the Enhanced Parallel Port specification that will be used by AMIBIOS. Parallel Port IRQ : This option is only valid if the Onboard Parallel Port option is not set to Disabled. This option sets the IRQ used by the parallel port. Parallel Port DMA Channel : This option is only available if Onboard Parallel Port is set to a fixed I/O address and the setting of Parallel Port Mode is ECP. This option sets the DMA channel used by an ECP-capable parallel port. Mouse/Keyboard Power On Function This option enables either a mouse click or keystroke to power up the computer in Soft Off mode. Peripheral Setup 4-31 Hardware Monitor Setup This Setup describes current system status detected by the hardware monitor controller. The status showed on the screen will include: � CPU Ratio Selection � This option is for unlocked processors only. If your socket 370 processors Frequency Multiple is locked, setting the Frequency Multiple here will have no effect. This option sets the Frequency Multiple between the CPUs internal and external frequencies. This must be set in conjunction with CPU Bus Frequency to match the speed of your CPU. � Current System Temperature (Generally indicates the inside temperature of the chassis or surface temperature of the SBC) � Current CPU Fan Speed � Current Chassis Fan Speed, if connected to a tach fan � System operating voltage (choices include CPU Vcore, CPU Vtt, Vcc3, +5V, +12V, -12V, and -5V.) 4-32 BIOS Setup Information BIOS Setup BIOS POST Check Point List AMIBIOS provides all IBM standard Power On Self Test (POST) routines as well as enhanced AMIBIOS POST routines. The POST routines support CPU internal diagnostics. The POST checkpoint codes are accessible via the Manufacturing Test Port (I/O port 80h). Whenever a recoverable error occurs during the POST, the system BIOS will display an error message describing the message and explaining the problem in detail so that the problem can be corrected. During the POST, the BIOS signals a checkpoint by issuing one code to I/O address 80H. This code can be used to establish how far the BIOS has executed through the power-on sequence and what test is currently being performed. This is done to help troubleshoot a faulty system board. If the BIOS detects a terminal error condition, it will halt the POST process and attempt to display the checkpoint code written to port 80H. If the system hangs before the BIOS detects the terminal error, the value at port 80H will be the last test performed. In this case, the terminal error cannot be displayed on the screen. The following POST checkpoint codes are valid for all AMIBIOS products with a core BIOS date of 07/15/95 version 6.27 (Enhanced). BIOS POST Check Point List 4-33 Uncompressed Initialization Codes The uncompressed initialization checkpoint hex codes are listed in order of execution: Table 4-10.Uncompressed Initialization Codes Code Description NMI is disabled. CPU ID saved. INIT code check sum verification will D0 be started. Initializing the DMA controller, performing the keyboard controller BAT D1 test, starting memory refresh, and going to 4GB flat mode. Beginning memory sizing. D3 Returning to real mode. Executing any OEM patches and setting the stack D4 next. Passing control to the uncompressed code in shadow RAM at D5 E000:0000h. The INIT code is copied to segment 0 and control will be transferred to segment 0. Control is in segment 0. Next, checking that [Ctr+Home] was pressed and D6 verifying the system BIOS check sum. If either [Ctrl+Home] was pressed or the system BIOS checksum is bad, go to checkpoint code E0h. Otherwise, go to checkpoint code D7h. Passing control to interface module. D7 D8 Main BIOS runtime code is to be decompressed. Passing control to the main system BIOS in shadow RAM. D9 4-34 BIOS Setup Information BIOS Setup Bootblock Recovery Codes The bootblock recovery checkpoint hex codes are listed in order of execution: Table 4-11.Bootblock Recovery Codes Code Description The onboard floppy controller, if available, is initialized. Beginning the base E0 512kB memory test. Initializing the interrupt vector table. E1 Initializing the DMA and Interrupt controllers. E2 Enabling the floppy drive controller and Timer IRQs. Enabling internal E6 cache memory. Initializing the floppy drive. ED Looking for a diskette in drive A: and reading first sector of the diskette. EE A read error occurred while reading the floppy disk in drive A: . EF Searching for the AMIBOOT.ROM file in the root directory. F0 The AMIBOOT.ROM file is not in the root directory. F1 Reading and analyzing the floppy diskette FAT to find the clusters F2 occupied by the AMIBOOT.ROM file. Begin reading AMIBOOT.ROM file, cluster by cluster. F3 The AMIBOOT.ROM file is not the correct size. F4 Disabling internal cache memory. F5 Detecting the type of Flash ROM. FB Erasing the Flash ROM. FC Programming the Flash ROM FD Flash ROM programming was successful. Restarting the system BIOS. FF BIOS POST Check Point List 4-35 Uncompressed Initialization Codes The following runtime checkpoint hex codes are listed in order of execution. These codes are uncompressed in F0000h shadow RAM. Table 4-12.Uncompressed Initialization Codes Code Description The NMI is disabled. Checking for a soft reset or a power on condition. 03 The BIOS stack has been built. Disabling cache memory. 05 Uncompressing the POST code. 06 Initializing the CPU and the CPU data area. 07 The CMOS checksum calculation. 08 Performing any required initialization before the keyboard BAT 0B command is issued. The keyboard controller input buffer is free. Issuing the BAT 0C command to the keyboard controller. The keyboard controller BAT command result has been verified. 0E Performing any necessary INIT after the K/B controller BATcommand test. The keyboard command byte is written. 0F Issuing pins 23 and 24 for blocking and unblocking commands. 10 Checking if the [End] or [Ins] keys were pressed during power on. 11 To initialize CMOS if the initialize CMOS RAM in every boot is set or the 12 [End] key is pressed. Disabling DMA and Interrupt controllers. The video display has been disabled. Port B has been initialized. 13 Initializing the chipset. The 8254 timer test. 14 The 8254 timer test is over. Starting the memory refresh test. 19 4-36 BIOS Setup Information BIOS Setup Table 4-12.Uncompressed Initialization Codes (Continued) Code Description The memory refresh line is toggling. Checking the 15us on/off time. 1A Reading the 8042 input port and disabling the MEGAKEY Green PC 23 feature. Making the BIOS code segment writable and performing any necessary configuration before initializing the interrupt vectors. The configuration or Setup required before interrupt vector initialization 24 has completed. Interrupt of vector initialization is about to begin. Interrupt vector initialization is done. Clearing the password if the POST 25 DIAG switch is on. Any initialization before setting video mode. 27 28 Going for monochrome mode and color mode settings. 2A Bus initialization system, static, output devices, if present. Passing control to the video ROM to perform any required configuration 2B before the video ROM test. To look for optional video ROM and transfer control. 2C The video ROM has returned control to BIOS POST. Performing any 2D required processing after the video ROM had control. Completed post-video ROM test processing. If the EGA/VGA controller 2E is not found, perform the display memory read/write test. EGA/VGA not found. Display memory R/W test is about to begin. 2F Display memory R/W test passed. Look for retrace checking. 30 Display memory R/W test or retrace checking failed. Perform alternate 31 display retrace checking. Alternate display memory R/W test passed. Look for the alternate display 32 retrace checking. Video display test is over. Setting the display mode. 34 BIOS POST Check Point List 4-37 Table 4-12.Uncompressed Initialization Codes (Continued) Code Description The display mode is set. Displaying the power on message. 37 Initializing the bus input, IPL, and general devices, if present. 38 39 Displaying bus initialization error message. The new cursor position has been read and saved. Displaying the Hit 3A [DEL] message. Preparing the descriptor tables. 40 Entering protected mode for the memory test. 42 Entered protected mode. Enabling interrupts for diagnostics mode. 43 Interrupts enabled if the diagnostics switch is on. Initializing data to 44 check memory wraparound at 0:0. Data initialized. Checking for memory wrap-around at 0:0 and finding the 45 total system memory size. The memory wrap-around test has been completed. The memory size 46 calculation has been done. Writing patterns to test memory. The memory pattern has been written to extended memory. Writing 47 patterns to the base 640 kB memory test. Patterns written in base memory. Determining the amount of memory 48 below 1MB. The amount of memory below 1MB has been found and verified. 49 Determining the amount of memory above 1MB memory. The amount of memory above 1MB has been found and verified. 4B Checking for a soft reset and clearing the memory below 1MB for the soft reset. If this is a power on situation, go to checkpoint 4Eh next. The memory below 1MB has been cleared via a soft reset. Clearing the 4C memory above 1MB. 4-38 BIOS Setup Information BIOS Setup Table 4-12.Uncompressed Initialization Codes (Continued) Code Description The memory above 1MB has been cleared via soft reset. Saving the 4D memory size. Going to checkpoint 52h. The memory test started, but not as the result of a soft reset. Displaying 4E the first 64kB memory size. Memory size display started. This will be updated during the memory 4F test. Performing the sequential and random memory test. Memory testing/initialization below 1MB completed. Adjust displayed 50 memory size for relocation and shadowing. The memory size display was adjusted for relocation and shadowing. 51 Testing the memory above 1MB. The memory above 1MB has been tested and initialized. Saving the mem- 52 ory size information. The memory size information and the CPU registers are saved. Entering 53 real mode. Shutdown was successful. The CPU is in real mode. Disabling the Gate 54 A20 line, parity, and the NMI. The A20 address line, parity, and the NMI are disabled. Adjusting the 57 memory size depending on relocation and shadowing. The memory size was adjusted for relocation and shadowing. Clearing 58 the Hit [DEL] message. The Hit [DEL] message is cleared. The [WAIT ] message is 59 displayed. Starting the DMA and interrupt controller test. The DMA page register test passed. DMA#1 base register test. 60 DMA#1 base register test passed. DMA#2 base register test. 62 65 DMA#2 base register test passed. To program DMA unit 1 and 2. DMA unit 1 and 2 programming over. Initializing the 8259 interrupt 66 controller. BIOS POST Check Point List 4-39 Table 4-12.Uncompressed Initialization Codes (Continued) Code Description 7F Extended NMI sources enabling is in progress. The keyboard test has started. Clearing the output buffer and checking for 80 stuck keys. Issuing the keyboard reset command. A keyboard reset error or stuck key was found. Issuing the keyboard 81 controller interface test command. The keyboard controller interface test completed. Writing the command 82 byte and initializing the circular buffer. Command byte written, Global data initialization done. Check for locked 83 key. Locked key checking is over. Checking for a memory size mismatch with 84 CMOS RAM data. The memory size check is done. Displaying a soft error and checking for 85 a password or bypassing Setup. Password checked. About to do programming before Setup. 86 The programming before Setup has completed. Uncompressing the Setup 87 code and executing the AMIBIOS Setup utility. Returned from CMOS Setup program and screen is cleared. 88 Programming after Setup. The programming after Setup has completed. Displaying the power on 89 screen message next. The first screen message has been displayed. The [WAIT ] message 8B is displayed. Performing the PS/2 mouse check and extended BIOS data area allocation check. Programming the Setup options next. 8C 8D Going for hard disk controller reset. Hard disk controller reset done. Floppy Setup is next. 8F 4-40 BIOS Setup Information BIOS Setup Table 4-12.Uncompressed Initialization Codes (Continued) Code Description The floppy drive controller has been configured. Configuring the hard 91 disk drive controller. Initializing the bus option ROMs from C800. 95 96 Initializing before passing control to the adaptor ROM at C800. Initialization before the C800 adaptor ROM gains control has been 97 completed. The adaptor ROM check is next. The adaptor ROM had control and has now returned control to BIOS 98 POST. Performing any required processing after the option ROM regained control. Any initialization required after the option ROM test has completed. 99 Configuring the timer data area and printer base address. Return from setting the timer and printer base address. Setting the RS-232 9A base address. Returned from setting the RS-232 base address. Performing any required 9B initialization before the coprocessor test. Required initialization before the coprocessor test is over. Initializing the 9C coprocessor. Coprocessor initialized. Performing initialization after coprocessor is 9D tested. Initialization after the coprocessor test is complete. Checking the 9E extended keyboard, keyboard ID, and Num Lock key. Issuing the keyboard ID command. Displaying any soft errors. A2 A3 Soft error display complete. Going to set keyboard typematic rate. Keyboard typematic rate set. Programming memory wait states. A4 BIOS POST Check Point List 4-41 Table 4-12.Uncompressed Initialization Codes (Continued) Code Description Memory wait state programming is over. Clearing the screen and A5 enabling parity and the NMI. NMI and parity enabled. Performing any initialization required before A7 passing control to the adaptor ROM at E000. Initialization before passing control to the adaptor ROM at E000h A8 completed. Passing control to the adaptor ROM at E000h. Returned from adaptor ROM at E000h control. Performing any A9 initialization required after the E000 option ROM had control. Initialization after E000 option ROM control has completed. Displaying AA the system configuration. AB Building the multiprocessor table, if necessary. Uncompressing the DMI data and initializing DMI POST. AC B0 The system configuration is displayed. Copying code to specific areas. B1 Code copying to specific areas is done. Passing control to INT 19h boot 00 loader. 4-42 BIOS Setup Information BIOS Setup Flash BIOS Utility Utilize the AMI Flash BIOS programming utility to update the onboard BIOS for future BIOS versions. Please contact ICS Advent to get this utility if necessary. Note: Remark or delete any installed Memory Management Utility (such as HIMEM.SYS, EMM386.EXE, QEMM.EXE, etc.) in the CONFIG.SYS files before running the Flash BIOS programming utility. Flash BIOS Utility 4-43 Chapter 5 Troubleshooting Contents Overview . . . . . . . . . . . . . . . . . . . . . . . . . . . . . . . . . . . . . 5-3 BIOS Settings . . . . . . . . . . . . . . . . . . . . . . . . . . . . . . . . . 5-3 Loading the Default Optimal Setting . . . . . . . . . . . 5-3 Auto Detect Hard Disks . . . . . . . . . . . . . . . . . . . . . . 5-3 Improper Disable Operation. . . . . . . . . . . . . . . . . . . 5-4 OS Diagnostics. . . . . . . . . . . . . . . . . . . . . . . . . . . . . . . . . 5-6 ACPI Function in Windows 98 . . . . . . . . . . . . . . . . . 5-6 Display Setup . . . . . . . . . . . . . . . . . . . . . . . . . . . . . . 5-6 Network Setup . . . . . . . . . . . . . . . . . . . . . . . . . . . . . 5-6 Troubleshooting Overview This chapter gives you a few useful tips to quickly get the Endeavor Plus single board computer running without failure. Since basic hardware installation is addressed in Chapter 3, this chapter focuses on system integration issues in terms of backplane setup, BIOS settings, and Operating System diagnostics. BIOS Settings It is assumed that the user has correctly adopted the modules and connected all the device cables required before turning on AT power. The CPU, the CPU fan, the CPU fan power cable, the 168-pin SDRAM, the keyboard, the mouse, the floppy drive, the IDE hard disk, the printer, the VGA connector, the device power cables, ATX accessories, and P8/P9 power cables are good examples. With no assurance that these modules and devices are properly accomodated, it is very possible to have system failures that result in the malfunction of any devices applied. To ensure a successful first-run with the Endeavor Plus, it is recommended that you proceed to the boot-up sequence, by pressing the [DEL] key and entering the BIOS Setup menu to set up a stable BIOS configuration. Loading the Default Optimal Setting When prompted with the main setup menu, please scroll down to Auto Configuration with Optimal Settings, press [Enter] and [Y] to load the default optimal BIOS Setup. This will force your BIOS setting back to the initial factory configuration. This is recommended to ensure that the system is running with the BIOS setting that ICS Advent has highly recommended. A user can load the default BIOS setting any time the system appears to be unstable in the boot-up sequence. Auto Detect Hard Disks It is common for a user to proceed with Auto Detect Hard Disks to read the hard drive status information into BIOS memory to reduce the time spent in the boot-up hard disk detection process. However, if this is done and another hard drive is applied without redoing the Auto Detect Hard Disks procedure, the system will fail to identify the hard disks that are actually connected. A quick way to fix this problem is to enter the BIOS Setup menu for the second time and redo Auto Detect Hard Disks. Overview 5-3 There is also another way to prevent this detour. Go to Standard CMOS Setup and tune in the hard disk status, the Primary Master, and Primary Slave to Auto with their 32 bit mode being tuned to ON. This will force your system to automatically detect the current attached hard disks during each boot-up sequence. It is then no longer necessary to manually detect the hard disks each time the boot-up sequence is tried. Note that loading the default optimal BIOS setting will not change the hard disk detection status back to Auto. You may find that when you load the default BIOS setting, the hard disk detection status remains unchanged. Additionally, it is also recommended to double check the hard disk or CD-ROM setting in the event of connecting two IDE devices through one IDE port. One of these two devices needs to be configured as a slave device to prevent a detection failure of the IDE devices. There cannot be two IDE devices configured as the master devices at the same time. Improper Disable Operation There are many occasions in BIOS Setup where users disable a certain device/feature in one application, but do not enable it before manipulating another application where the disabled device is needed. Users fail to detect this device/feature and end up with a system failure. Please check the BIOS setting so that the devices or ports that you need are not disabled. These include the floppy drive, COM1/COM2 ports, parallel port, USB ports, external cache, and on-chip VGA display mode. It is also very common that users would like to disable a certain device/port to release IRQ resources. A few good examples are: � Disable COM1 serial port to release IRQ #4 � Disable COM2 serial port to release IRQ #3 � Disable parallel port to release IRQ #7 � Disable PS/2 mouse to release IRQ #12 5-4 Troubleshooting Troubleshooting A quick review of basic IRQ mapping is given below. Table 5-1. Basic IRQ Mapping IRQ # Description 0 System Counter 1 Keyboard 2 Cascade IRQ 3COM2 4COM1 5 Nothing 6 Floppy Disk Controller 7 Printer Port (Parallel Port) 8CMOS Clock 9 Nothing 10 Nothing 11 Nothing 12 PS/2 mouse 13 Data Processor 14 Primary IDE Controller 15 Secondary IDE Controller Note: Onboard PCI devices will occupy resources as assigned by BIOS or the operating system. It is very easy to find out which IRQ resource is ready for additional peripherals. If IRQ resources are insufficient, disable some of the devices listed above to release additional resources. BIOS Settings 5-5 OS Diagnostics This is a brief guide to properly storing the driver for any Microsoft Windows 95/98/NT device, as well as starting special functions in a specific operating system. For other operating systems, please refer to the the operating system (OS) manual/guidebook. ACPI Function in Windows 98 Windows 98/2000 are the only operating systems that supports the ACPI function, in terms of activating the suspend-to-RAM feature. This feature is not supported by ICS Advent Legacy backplanesTo enable Windows 98 to search for this feature, a special installation command is required : (1) setup (standard installation) (2) setup [space] /p [space] j (support ACPI feature) Display Setup By default, any Windows Operating System starts with a resolution of 640 x 480 pixels and a 16-color display. Please load the display driver provided in the Endeavor Plus CD to maximize the VGA performance. If you are using a monitor that Windows cannot identify, you will need to set up a system monitor to correctly retrieve display output, found in the display setup menu. For Windows NT 4.0 users, as the Endeavor Plus provides an AGP type on-chip display feature, Service Pack 3.0 or above is required to activate the AGP VGA display feature. Network Setup Windows 95/98 users Perform the following steps: 1) Install an ISA/PCI network card into an ISA/PCI slot. 2) Start Windows 95/98 and let Window 95/98 automatically detect your network adapter. 3) Provide the driver and complete installation. 4) After you come back to Windows, restart your Windows system. 5-6 Troubleshooting Troubleshooting 5) Go to Control Panel > System > Device Manager and verify your network adapter has been installed properly. A warning sign will be displayed if the network adapter has not been installed properly. 6) If the network adapter has not been installed properly, remove this network device from the system Setup menu and restart Windows to detect the network adapter again. 7) When the hardware installation is completed, go to Control Panel > Network to set up the networking configuration. This includes DNS, IP, and Gateway. Appropriate protocols are required to carry out networking activities. Refer to your system administrator for additional assistance. Windows NT 4.0 users Perform the following steps: 1) If there is no onboard ethernet capability, or to install a second network interface card (NIC), insert the NIC into the backplane or single board computer. 2) Install the network adapter manually in the Control Panel > Network > Adapter directory. Drivers are required at this stage. 3) Proceed Binding after you load the driver. 4) Change to Protocol Label and load the desired protocols (generally, TCP/IP). Configuring IP, gateway, and DNS is required for TCP/IP protocol. 5) When the protocol loading is complete, proceed again to Binding. 6) Restart the system. 7) If there is a situation where the installed network adapter is not working anymore, or the old network driver stays in the system after the network card is changed, remove all the network adapters and protocols from the network setup menu and reload the driver and protocols again. Network setup within Windows NT 4.0 is not as easy as within Windows 95/98. Special familiarity and care are required to have a successful installation. 8) Reapply Service Pack. OS Diagnostics 5-7 Appendix A WDT Programming Contents General Description. . . . . . . . . . . . . . . . . . . . . . . . . . . . A-3 Related CR for WDT Programming . . . . . . . . . . . . . . . A-5 WDT Programming Guide . . . . . . . . . . . . . . . . . . . . . . A-6 WDT Programming General Description Winbond has a WDT feature inside its W83627HF chip. There are many configuration Registors (CR ) in the W83627HF. The following sequence must be followed for CR programming: 1) Enter the extended function mode. 2) Configure the configuration registers. 3) Exit the extended function mode. For instance: 1) Enter extended function mode. MOV DX,3F0H MOV AL,87H CLI ; disable interrupt OUT DX,AL JMP $+2 OUT DX,AL STI ; enable interrupt 2) Configurate logical device 1, configuration register CRF0. MOV DX,3F0H MOV AL,07H OUT DX,AL ; point to Logical Device Number Register MOV DX,3F1H MOV AL,01H OUT DX,AL ; select logical device 1 ; MOV DX,3F0H MOV AL,0F0H OUT DX,AL MOV DX,3F1H MOV AL,3CH OUT DX,AL ; update CRF0 with value 3Ch General Description A-3 3) Exit extended function mode. MOV DX,3F0H MOV AL,0AAH OUT DX,AL The Configuration Register (CR) Definition : � Chip (Global) Control Register (CCR): CR02 -->CR2F. CR07 = Logical Device Number Register (LDNR) � Logical Device 0 (LD0) = FDC , with CR: CR30 -->CRF5 . � When LDNR (= CR07) = 00h , you can program the CR30 --CRF5 related to FDC feature . � Logical Device 1 (LD1) = Parallel Port, with CR: CR30 -->CRF0. � LD2 = UART A (Serial Port 1) , with CR :CR30 -->CRF0. � LD3 = UART B (Serial Port 2) , with CR :CR30 -->CRF0. � LD5 = KBC, with CR: CR30 -->CRF0. � LD6 = IR , with CR: CR30 -->CRF0. � LD7 = GP I/O Port I, with CR: CR30 -->CRF1. � LD8 = GP I/O Port II, with CR: CR30 -->CRF4. � LD9 = GP I/O Port III, with CR: CR30 -->CRF1. � LDA = ACPI, with CR: CR30 -->CRFF. A-4 WDT Programming WDT Programming Related CR for WDT Programming CR2C-Bit 3,2 ; [1,0] for WDT function LD8-CRF2 ; WDT time-out period , 00h = disabled 01h = 30 seconds 02h = 1.5 minutes 03h = 2.5 minutes 04h = 3.5 minutes 05h = 4.5 minutes .......... FEh = 253.5 minutes FFh = 254.5 minutes When writing a non-zero value to LD8-CRF2 , this value will be loaded into WD counter and start to count down .Read this register can not get the WDT time-out period (the orginal one written into), but the current value in WD counter . Enable and Refresh WDT : program LD8-CRF2 a non-zero value. Disable WDT: program LD8-CRF2 with 00h. LD8-CRF4- Bit 0 : WDT Status 1 = WDT time-out happened 0 = WDT counting Related CR for WDT Programming A-5 WDT Programming Guide 1) Enter extended function mode as mentioned on the previous page. 2) Program WDT related CR: a) CR2C-b[3,2]P[1,0] ; Set pin output as WDT function b) CR07-P08h ; Point to LD8 c) CRF2-Pxyh ; Program WDT time-out period and start count down. xy = 00 ; No WDT time-out and counting xy = 01 ; WDT time-out = 30 sec. and starts counting ............ d) Read CRF4-b0 if needed; 0 : WDT counting 1 : WDT time-out happened 3) Exit extended function mode as mentioned on the previous page. Example ( ENABLE WDT AND SET WDT time-out = 1.5 minutes ) Step 1. MOV DX,3F0H MOV AL,87H CLI ; disable interrupt OUT DX,AL JMP $+2 OUT DX,AL STI ; enable interrupt A-6 WDT Programming WDT Programming Step 2 . MOV DX,3F0H MOV AL,2CH OUT DX,AL MOV DX,3F1H IN AL,DX ; READ CR2C OR AL,08H AND AL,0FBH MOV AH,AL MOV DX,3F0H MOV AL,2CH OUT DX,AL MOV DX,3F1H MOV AL,AH OUT DX,AL ; CR2C-b[3,2]P[1,0] MOV DX,3F0H MOV AL,07H OUT DX,AL ; point to Logical Device Number Register MOV DX,3F1H MOV AL,08H OUT DX,AL ; select logical device 8 ; MOV DX,3F0H MOV AL,0F2H OUT DX,AL MOV DX,3F1H MOV AL,02H OUT DX,AL ; LD8-CRF2-P02h WDT Programmimg Guide A-7 Step 3 . Exit extended function mode MOV DX,3F0H MOV AL,0AAH OUT DX,AL REMARK: **** I/O PORT 3F0h --> Index port for programming CR . 3F1h --> Data port for programming CR . **** LD8-CRF2-P02h : Program CR index F2h of Logical Device 8 with the value "02h" . A-8 WDT Programming Declaration of Conformity Information Technology Equipment 6260 Sequence Drive San Diego, CA 92121-4371 800 523-2320 / 858-677-0877 The product(s) covered by this declaration: Endeavor Plus single board computer: model numbers SBC-SCPIII-V, SBC-SCPIII-VE, and SBC-SCPIII-VES The European Union directives covered by this declaration: EMC Directive 89/336/EEC and Low Voltage Directive 73/23/EEC The basis on which conformity is declared: EN 50081-1:1992 Emissions, Generic Requirements -EN 55022 Limits and Methods of Measurement of Radio Disturbance Characteristics of Information Technology Equipment EN 50082-1:1992 Immunity, Generic Requirements - EN61000-4-2: 1995 Electrostatic Discharge (ESD) Immunity - EN61000-4-3: 1995 Radiated RF Field Immunity - EN61000-4-4: 1995 EFT Immunity for AC and I/O Lines EN 60950:1992 Safety of Information Technology Equipment The technical documentation required to demonstrate this product meets the requirements of the EMC Directive and the Low Voltage Directive has been compiled by ICS Advent and is available for inspection by the relevant enforcement authorities. Attention The attention of the specifier, purchaser, installer, or user is drawn to special measures and limitations for use which must be observed when the product is taken into service to maintain compliance with the above directives. Details of these special measures and limitations are in the product manual. Mr. Jim Jameson President & Chief Executive Officer ICS Advent Europe Ben Turner Industrial Estate Oving Road Chichester, West Sussex PO19 4ET, UK
Frequently asked questions
What makes Elite.Parts unique?

What kind of warranty will the Endeavor Plus have?

Which carriers does Elite.Parts work with?

Will Elite.Parts sell to me even though I live outside the USA?

I have a preferred payment method. Will Elite.Parts accept it?

Why buy from GID?
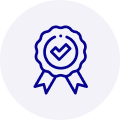
Quality
We are industry veterans who take pride in our work
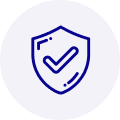
Protection
Avoid the dangers of risky trading in the gray market
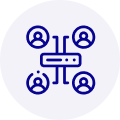
Access
Our network of suppliers is ready and at your disposal
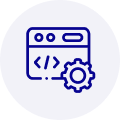
Savings
Maintain legacy systems to prevent costly downtime
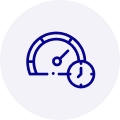
Speed
Time is of the essence, and we are respectful of yours
Related Products
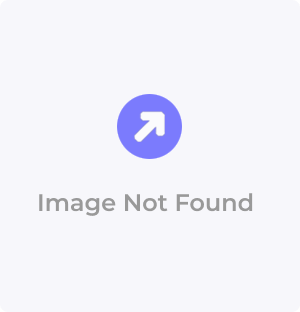
ICS Advent Endeavor Plus PICMG 1.0 Full-Size CPU Board with Optional 7892 Ultra 160/m SCSIHost Adapt...
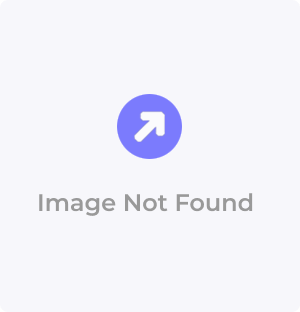
ICS Advent Endeavor Plus PICMG 1.0 Full-Size CPU Board with Optional 7892 Ultra 160/m SCSIHost Adapt...
What they say about us
FANTASTIC RESOURCE
One of our top priorities is maintaining our business with precision, and we are constantly looking for affiliates that can help us achieve our goal. With the aid of GID Industrial, our obsolete product management has never been more efficient. They have been a great resource to our company, and have quickly become a go-to supplier on our list!
Bucher Emhart Glass
EXCELLENT SERVICE
With our strict fundamentals and high expectations, we were surprised when we came across GID Industrial and their competitive pricing. When we approached them with our issue, they were incredibly confident in being able to provide us with a seamless solution at the best price for us. GID Industrial quickly understood our needs and provided us with excellent service, as well as fully tested product to ensure what we received would be the right fit for our company.
Fuji
HARD TO FIND A BETTER PROVIDER
Our company provides services to aid in the manufacture of technological products, such as semiconductors and flat panel displays, and often searching for distributors of obsolete product we require can waste time and money. Finding GID Industrial proved to be a great asset to our company, with cost effective solutions and superior knowledge on all of their materials, it’d be hard to find a better provider of obsolete or hard to find products.
Applied Materials
CONSISTENTLY DELIVERS QUALITY SOLUTIONS
Over the years, the equipment used in our company becomes discontinued, but they’re still of great use to us and our customers. Once these products are no longer available through the manufacturer, finding a reliable, quick supplier is a necessity, and luckily for us, GID Industrial has provided the most trustworthy, quality solutions to our obsolete component needs.
Nidec Vamco
TERRIFIC RESOURCE
This company has been a terrific help to us (I work for Trican Well Service) in sourcing the Micron Ram Memory we needed for our Siemens computers. Great service! And great pricing! I know when the product is shipping and when it will arrive, all the way through the ordering process.
Trican Well Service
GO TO SOURCE
When I can't find an obsolete part, I first call GID and they'll come up with my parts every time. Great customer service and follow up as well. Scott emails me from time to time to touch base and see if we're having trouble finding something.....which is often with our 25 yr old equipment.
ConAgra Foods