HC STARCK Thermal Spray Powder
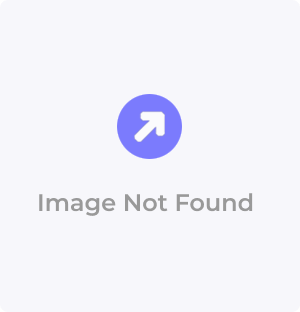
Description
HC Starck Amperit Thermal Spray Powders
Part Number
Thermal Spray Powder
Price
Request Quote
Manufacturer
HC STARCK
Lead Time
Request Quote
Category
PRODUCTS - T
Datasheet
Extracted Text
Thermal Spray Powders Engineered Material Solutions Edition 2001 ® AMPERIT Thermal Spray Powders Table of Content Subject Page H.C. Starck - Material Specialists Serving the Thermal Spray Industry 3 Preferred Grain Sizes in µm for today’s Thermal Spray processes 4 ® Application Engineering AMPERIT 5 ® AMPERIT Thermal Spray Powders Carbides 6 - 8 Oxides 9 - 11 Pure Metals, Alloys and Blends, Miscellaneous 12 - 14 Conversion Tables 15 2 H.C. Starck - Materials Specialists Serving the Thermal Spray Industry ® In 1920 Hermann C. Starck H.C. Starck has been manu- The AMPERIT product line is con- founded his company, which orig- facturing a full range of powder stantly revised and supplemented inally traded in ferroalloys and ore materials for thermal spraying through the new products and ® concentrates. In subsequent years under the trade name AMPERIT developments from our own re- ® he purchased several production for more than 30 years: AMPERIT search efforts or resulting from facilities to diversify the company’s thermal spray powders are well cooperation with our customers. product range and strengthen its known in the market for their con- Tests analyzing the coating and market position. After Bayer AG sistent high quality certified by processing properties are per- acquired a majority holding in ISO 9001 and for a works report formed in our modern in-house H.C. Starck in 1986, the company according to DIN EN 10204 sup- spray laboratory. expanded into one of the world’s plied with every delivery. Today leading manufacturers of metal, H.C. Starck produces more than carbide and ceramic powders. 500 powder material variations for flame, plasma and HVOF spraying. ® This brochure only covers the most important standard powders of our AMPERIT product line. Please do not hesitate to ask us about other powder types or grain sizes. Benefit from Our Materials and Coating Expertise Over the years H.C. Starck has accumulated a wide range knowledge in the fields of powder and materials for spraying. Our latest know-how is presented at international conferences around the world. We can supply reprints of our presentations on request. Powder selection, characterization and application: Powders for Thermal Spraying Ceramics for Atmospheric Plasma Spraying (APS): Al 0 -TiO Coatings: 2 3 2 An Alternative to Cr O ? 2 3 Oxides for Thermal Spraying: Multicomponent Oxides - Opportunities and Resulting Coating Properties Materials for High Velocity Oxygen Fuel Spraying Carbide Materials for HVOF Applications Cermets for HVOF Processes Advanced Carbides and Borides for Wear-Resistant Coatings Requirements of Carbide-Based Thermal Spray Powders and Ways to Obtain Optimized Coatings • Effect of Powder Types on the Structure and Properties of Chromium Carbide/Nickel Chromium Coatings 3 ® AMPERIT Thermal Spray Powders Preferred Grain Sizes in µm for today’s Thermal Spray Processes: Process Metals and Alloys Carbides Oxides Flame spraying 75/20 90/45 - 53/20 45/10 Plasma spraying 90/45 90/45 90/16 45/10 (APS) 45/10 45/10 45/20 125/45 25/10 25/10 HVOF Jet Kote 45/22 45/15 45/22 45/15 - D J (Hybrid) 38/10 38/15 38/10 38/15 15/5 12/2 JP 5000 53/20 45/22 53/20 45/15 - Top Gun 45/15 45/10 38/10 45/15 45/10 38/10 15/5 12/2 ® SEM-Photographs of AMPERIT Powders gas atomized porous coated water atomized fused sintered agglomerated sintered dense coated ® AMPERIT technical information, product data sheets and spray parameters are available on request. 4 ® Applications Engineering AMPERIT Our Applications Engineering includes a modern thermal spray laboratory and a specialized metallographic laboratory (see Web site*). These labs are used to modify and improve ® our AMPERIT products with regard to our customer needs and to develop new materials. The close cooperation with our R+D group gives the benefit of a complete material know-how support. All equipment is also available for customer tests and on order basis. Our customer service includes: Technical advice Technical product information Powder characterization Coating analyses Spray parameters *www.hcstarck.com/index.cfm?PAGE_ID=198 Coating Analyses Powder analyses Equipment Metallographic Examination Powder Characterization Plasma- Technik F4 Macro- / Microhardness Deposition Rate UTP Top Gun Bond Strength Flowability DJ 2600 Hybrid Surface Roughness Processing Metco 5P Coating Thickness Others on request UTP Uni Spray- Jet Corrosion Castolin Eutectic Rototec Wear Others on request Others on request 5 ® AMPERIT Thermal Spray Powders Carbides Alternative to ... Grain Size in µm ® AMPERIT Powder Type Application or Specification (Chemistry only) 515.0 WC-Co 88/12 22/5 ! see WC-Co aggl. sintered 71 NS/VF-NS/ 515.1 sintered 45/22 ! typically applied by air plasma VF-NS-1 515.2 90/45 spraying 2003 ® 515.203 MTS 1055B ! C: 3.9 - 4.3 % AMDRY 301/302 ® 515.400 AMS 7879 C ! max. operating temperature: AMDRY 301/302 515.401 PWA 1302 500 °C WC-104/106 515.949 DMS 2049 C-2 Al-1001/1002/1101/1102 516.2 WC-Co 88/12 90/45 ! C: min. 5.1% JK 114/112 516.280 sintered GE B50TF27 CI.A ! in finer grain size also used WC-114/489-1 for HVOF 2004 72F-NS 1320 Q 518.054 WC-Co 88/12 45/10 ! hard and dense coatings with WC-616 518.059 agglomerated 30/5 excellent bonding properties JK 7112/7113 P 518.074 sintered 45/15 ! resistant to abrasion, erosion 1342 VM/1342 VF 518.088 53/20 and sliding wear Sulzer Metco 5812 ! max. operating temperature: 500 °C ® 522.2 WC-Co 88/12 90/45 ! see AMPERIT 516, typically 522.3 dense coated 45/5 applied by air plasma spraying coarse carbides ® 525.2 WC-Co 83/17 90/45 ! see AMPERIT 526, typically sintered applied by air plasma spraying ! in finer grain size also used for HVOF 526.054 WC-Co 83/17 45/10 ! dense, hard and with 17% Co 73 F-NS-1/F-NS-2/SF-NS 526.062 agglomerated 53/10 also tough coatings 2005 NS/2006 ® 526.074 sintered 45/15 ! resistant against particle erosion, AMDRY 9830/9831 526.077 63/32 abrasion and fretting WC-619/558 526.223 MTS 1058 B ! max. operating temperature: 1343 V/1343 VM/1343 VF 526.350 MSRR 9507/1 500 °C JK 117/117-SP/ 526.382 MSRR 9507/69 7117/7118 P 533.3 WC-Co 80/20 45/5 ! lower hardness but increased 76 F-NS ® dense coated toughness AMDRY 5670 ! excellent finishing properties ! max. operating temperature: 500 °C Additional grain sizes on request 6 Carbides Alternative to ... Grain Size in µm ® AMPERIT Powder Type Application or Specification (Chemistry only) 544.059544.3WC-Ni 83/17 30/545/5 ! good bond strength and WC-624 544.6 dense coated 125/45 improved corrosion protection in comparison to Co matrix ® ® 551.074 WC-CrC-Ni 45/15 ! see AMPERIT 552 see AMPERIT 552 551.088 73/20/7 53/20 WC-645 agglomerated 1356 VM sintered 552.072 WC-CrC-Ni 38/10 ! wear, corrosion and oxidation WC-496 552.074 73/20/7 45/15 resistant JK 125/7175/7176 sintered 553.065 WC-Co-Cr 30/10 ! wear and corrosion resistant 553.074 86/10/4 45/15 in watery solutions sintered ! hard, dense coatings with high bond strength ! C: 3.5 - 4.5% ® 554.065 WC-Co-Cr 30/10 ! see AMPERIT 553, but WC-436-1/113 ® 554.074 86/10/4 45/15 higher hardness AMDRY 5843 sintered ! C: 5 - 6% JK 120/7109 557.074 WC-Co-Cr 45/15 ! wear protection in corrosive -/- 557.087 86/6/8 38/15 environment especially in sintered paper mills ® ® 558.074 WC-Co-Cr 45/15 ! see AMPERIT 554 see AMPERIT 554 558.088 86/10/4 53/20 WC-636 agglomerated Sulzer Metco 5847 sintered 1350 VM/1350 VF ® 559.074 WC-Co-Cr 45/15 ! see AMPERIT 557 -/- 86/6/8 agglomerated sintered 560.062 WC-Co(83/17) 53/10 ! protection against abrasive -/- 560.077 -NiSF 50/50 63/32 wear blended Additional grain sizes on request 7 ® AMPERIT Thermal Spray Powders Carbides Alternative to ... Grain Size in µm ® Powder Type AMPERIT Application or Specification (Chemistry only) 580.2 Cr C 90/45 ! usually blended with metallic 70C-NS/F-NS 3 2 580.054 sintered 45/10 matrix material for wear CRC-107/105 580.402 PWA 1304 resistant coatings 580.404 PWA 1306 ! service temperature up to 900 °C max. 583.2 Cr C -Ni 90/45 ! hard and wear resistant with 3007 3 2 583.054 83/17 45/10 higher CrC-content than ® dense coated AMPERIT 584 ® 584.1 Cr C -NiCr 45/22 ! wear and oxidation resistant AMDRY 5260 3 2 584.054 75/25 45/10 up to 900 °C 1375 VF/1376 T/1375 VM 584.072 agglomerated 38/10 ! sliding properties JK 135/7184/7185 sintered 585.1 Cr C -NiCr 45/22 ! application properties 81 NS/VF-NS 3 2 585.3 75/25 45/5 comparable to 3004 ® 585.351 blended MSRR 9507/2 AMPERIT 584 CRC-106/108 585.357 MSRR 9507/17 585.435 AMS 7875 586.1 Cr C -NiCr 45/22 ! hard and wear/oxidation 3 2 586.054 80/20 45/10 resistant agglomerated sintered 591.294 Cr C -Ni / GE B50TF28 ! blend of nickel cladded CrC 430 NS 3 2 CoNiCr / CI.A and matrix alloys as erosion NiAl blended resistant coating 593.775 Cr C -NiCr GE B50TF281 ! erosion resistant for 3 2 90/10 CI.A turbine applications sintered 599.063 Mo C 75/45 ! hard ingredient in powder 64 2 599.074 agglomerated 45/15 blends for sliding wear sintered protection Additional grain sizes on request 8 Oxides Alternative to ... Grain Size in µm ® Powder Type AMPERIT Application or Specification (Chemistry only) ® 704.0 Cr O 99.5% 22/5 ! corrosion and wear resistant AMDRY 6417/6420 2 3 704.1 fused 45/22 ceramic CRO-131/167/ 704.053 25/10 ! insoluble in acid and alkali 167-1/172/174/179 704.054 45/10 solutions #3030/#3031/ 704.092 75/25 ! typical application: anilox #3032/#3033 704.216 MTS 1231A rolls for printing machines ® 706.072 Cr O 38/10 ! high purity Cr O see AMPERIT 704 2 3 2 3 agglomerated ! spherical powder particle shape sintered 710.0 Cr O -TiO 22/5 ! hard, dense and wear resistant 2 3 2 710.1 60/40 blended 45/22 for extremely smooth surfaces 710.7 90/16 712.062 Cr O -TiO 53/10 2 3 2 ® 712.066 75/25 fused 53/15 ! see AMPERIT 704 716.0 Cr O -TiO - 22/5 136 CP/F 2 3 2 716.1 SiO 92/3/5 45/22 CRO-192 2 716.3 blended 45/5 #340/#341 716.054 45/10 ! resistant to wear and corrosion 716.066 53/15 716.076 12/2 ! mechanical shock resistant 740.0 Al O 22/5 ! resistant to corrosion, abrasion 105 NS/SF/SFP 2 3 740.1 fused 45/22 erosion and sliding wear ALO-101/114 740.2 90/45 ! excellent dielectric properties Al-1010 HP/FHP/ 740.3 45/5 ! max. service temperature: 1110 HP 740.066 53/15 1000 °C #150/#153 740.207 MTS 1062 B #182/#183/#184 ® 740.355 MSRR 9507/9 AMDRY 356 740.406 PWA 1310 740.416 PWA 1356-1 742.0 Al O -TiO 22/5 ! grey alumina for use as 101 NS/BNS/SF 2 3 2 ® 742.1 97/3 fused 45/22 corrosion, abrasion, erosion AMDRY 187 742.2 90/45 and sliding wear resistant Al-1011F 742.298 GE A50TF87 coating ALO-105/159 CI.B ! high temperature resistant #110/#112/#114/#115 742.407 PWA 1311 ! typical applications in textile #116/#117/#119 machines Additional grain sizes on request 9 ® AMPERIT Thermal Spray Powders Oxides Alternative to ... Grain Size in µm ® Powder Type AMPERIT Application or Specification (Chemistry only) ® 744.0 Al O -TiO 22/5 ! compared with AMPERIT 742 130/130SF 2 3 2 744.1 87/13 45/22 less hard and corrosion ALO-187/188 744.2 blended 90/45 resistant #103/#106/#107 744.3 45/5 745.0 Al O -TiO 22/5 ! wear resistant for household #108/#109 2 3 2 745.1 60/40 45/22 applications ALO-121 745.3 blended 45/5 ! good grindability Al-1070 ! polished coatings with reduced wettability ® 746.4 Al O -TiO 63/16 ! spherical powder, alternative see AMPERIT 745 2 3 2 ® 746.074 60/40 45/15 to AMPERIT 745 with finer 131 VF agglomerated microstructure ® 748.1 Al O -TiO 45/22 ! wear resistant for household see AMPERIT 744 2 3 2 748.054 87/13 45/10 applications agglomerated 750.054 Al O -ZrO 45/10 ! high toughness 2 3 2 60/40 fused ! good abrasion and erosion resistance 755.1 Al TiO 45/22 ! thermal shock improved -/- 2 5 755.054 agglomerated 45/10 ceramic sintered 782.1 TiO 45/22 ! moderate corrosion and wear 102 2 ® 782.2 fused 90/45 resistant compared with Al O AMDRY 6505 2 3 782.3 45/5 or Al O -TiO #1000/#1001 2 3 2 782.8 20/5 ! decorative black coatings 782.054 45/10 ! slightly conductive Additional grain sizes on request 10 Oxides Alternative to ... Grain Size in µm ® Powder Type AMPERIT Application or Specification (Chemistry only) ® 825.0 ZrO -Y O 22/5 ! blocky particle shape see AMPERIT 827 2 2 3 ® 825.1 93/7 45/22 ! properties see AMPERIT 827 825.218 fused MTS 1198 B -/- 825.242 MTS 1342 B 825.381 MSRR 9507/72 827.6 ZrO -Y O 125/45 ! thermal barrier for turbine and 204 NS/204 B-NS 2 2 3 827.7 93/7 90/16 engine as well as for high 204 C-NS/204 NS-G 827.054 agglomerated 45/10 temperature applications ZRO-113/114/154/182/ 827.238 sintered MTS 1352 B ! thermal shock resistant 196/196-5/210 827.289 GE A50TF278 ! hot corrosion resistant Al-1075 CI.A ! low heat conductivity #203/#204/#204 F/#204 PR 827.290 GE A50TF278 ! max. service temperature: Sulzer Metco 6600 CI.B 1300 °C 1484 J 827.423 PWA 1375 827.772 GE A50A557* 827.773 GE A50A558* 827.774 GE A50TF278 Cl.C 827.853 PM 819-20 827.864 PM 819-57 ® 832.6 ZrO -Y O 125/45 ! dense, spherical, see AMPERIT 827 2 2 3 ® 832.7 93/7 90/16 see AMPERIT 827 agglomerated sintered 849.054 Y O sintered 45/10 ! heat resistant in aggressive 2 3 atmospheres *for G.E. Power Generation, only Additional grain sizes on request 11 ® AMPERIT Thermal Spray Powders Pure Metals, Alloys and Blends, Miscellaneous Alternative to ... Grain Size in µm ® Powder Type AMPERIT Application or Specification (Chemistry only) ® 105.2 Molybdenum 90/45 ! preferrred bond coat for steel AMDRY 313X 105.054 agglomerated 45/10 substrates MO-102/103 sintered ! excellent sliding and emer- gency running properties 109.2 Molybdenum 90/45 ! high coating hardness agglomerated ! in oxidizing atmosphere max. sintered service temperature 300 °C ® ! AMPERIT 105: C max. 0,2 % ® ! AMPERIT 109: C max. 1 % 106.2 Molybdenum 90/45 ! sintered and crushed alternative 63 NS ® 106.062 sintered 53/10 to AMPERIT 105/109 106.158 PWA 1313 106.222 MTS 1054 B ® 119.075 Mo/NiSF 90/15 ! piston ring coating material with AMDRY 1371 75/25 excellent sliding properties and Al-1054 blended wear resistant (4) 140.1 Tungsten 45/22 ! high temperature melting Al-1061/1061F 140.067 sintered 15/5 material ! resistant to molten zinc and copper ! adhesion to graphite, alumina and quartz 146.3 Chromium 45/5 ! corrosion resistant -/- (4) 150.2 Tantalum 90/45 ! corrosion protection in chemical -/- 150.074 fused 45/15 apparatus (4) 155.086 Titanium <63 ! material for biomedical -/- 155.093 125/90 applications ! good corrosion resistance 160.3 Niob fused 45/5 (8) 175.2 Nickel 90/45 ! corrosion protection 56 C-NS/F-NS atomized ! ingredient as matrix material NI-101/118 in blends 1166 F ! repair and bond coat for Ni-based alloys ( ) Numbers in paranthesis: Classification exclusively according to German law. ( ) Einstufung gem. Chemikaliengesetz §§ 3a Abs. 1, 15a. Einzelheiten entnehmen Sie bitte unserem EU (4) (8) Sicherheitsdatenblatt. = leicht entzündlich, = gesundheitsschädlich Additional grain sizes on request 12 Pure Metals, Alloys and Blends, Miscellaneous Alternative to ... Grain Size in µm ® Powder Type AMPERIT Application or Specification (Chemistry only) 205.5 106/32 ! abradable-clearance control 307 NS/NS-2/NS-3 205.415 Nickel Graphite PWA 1352/1 on turbine components NI-114/120 75/25 ! usually flame sprayed dense coated ! operating temp. up to 480 °C 250.1 NiCr 80/20 45/22 ! repair, bond coat and corrosion 43 C-NS/F-NS/ 250.2 water atomized 90/45 protection material 43 VF-NS 250.3 45/5 ! good machinability NI-105/106/107 250.071 25/5 ! bond coat for ceramics 1262 F 250.354 MSRR 9507/8 ! resists oxidation and corrosion 250.410 PWA 1317 up to 980 °C ® 251.1 NiCr 80/20 45/22 ! spherical alternative to see AMPERIT 250 ® 251.2 gas atomized 90/45 AMPERIT 250 ! oxidation and corrosion resistant 273.2 NiMoAl 90/5/5 90/45 ! moderate hard coatings 447 NS ® porous coated ! repair material with extreme AMDRY 387 toughness NI-453 ! excellent bonding 280.2 NiAl 95/5 90/45 ! high temperature and NI-185 280.3 water 45/5 corrosion resistant 280.241 atomized MTS 1309 B bond coat up to 800 °C ! excellent machinability ® 281.0 NiAl 95/5 22/5 ! see AMPERIT 280 480 NS 281.2 gas atomized 90/45 4008 NS 281.3 45/5 NI-357/357-1 281.420 PWA 1380 281.863 PM 819-56 ® 282.2 NiAl 95/5 90/45 ! see AMPERIT 280 450 NS ® 282.296 porous coated GE B50TF56 ! exothermic reaction AMDRY 956 Cl.A during spray process NI-109 282.353 MSRR 9507/5 Al-1037 282.369 MSRR 9507/43 282.438 PWA 1337 282.856 PM 819-37 Additional grain sizes on request 13 ® AMPERIT Thermal Spray Powders Pure Metals, Alloys and Blends, Miscellaneous Alternative to ... Grain Size in µm ® Powder Type AMPERIT Application or Specification (Chemistry only) 290.3 NiAl 69/31 45/5 ! used as bond coat for -/- water various applications atomized ! corrosion resistant ! high bond strength 299.6 NiCr-Al 95/5 125/45 ! oxidation and corrosion 443 NS ® 299.297 porous GE B50TF119 resistant material for AMDRY 960 coated Cl.A turbine applications NI-122 299.859 PM 819-47 335.063 NiCrBSi 75/45 ! self-fluxing alloys for flame 15 E/F 335.066 gas atomized 53/15 spraying and subsequent 2001 or simultaneous fusing 1660-02/1160-02 ! ingredient in powder blends NI-167/167-1 with Mo as piston ring coating 1275 H 410.1 NiCoCrAlY 45/22 ! protection in hot gas corrosive NI-130/171 ® 410.424 gas atomized PWA 1365-1 and oxidizing environments at AMDRY 365-1/-2 410.429 PWA 1365-2 high temperatures of approx. 410.860 PM 819-51 850 °C ® ® 413.1 NiCrAlY 45/22 ! see AMPERIT 410 AMDRY 962 413.6 gas atomized 125/45 NI-164/164-2/211/343 413.284 GE B50TF192 Cl.B ® 415.1 CoNiCrAlY 45/22 ! Co-based MCrAlY AMDRY 9954/9951/995C ® 415.6 gas atomized 125/45 ! see AMPERIT 410 CO-210-1/210-24/211/ 415.220 MTS 1262 B ! fine cuts VPS and HVOF 211-3/127/159 415.221 MTS 1273 B sprayable 415.288 GE B50TF195 Cl.A 421.087 NiCoCrAlTaReY 38/15 ! Ta and Re containing -/- 421.761 gas atomized GE B50TF242 MCrAlY to improve hot Cl.C gas corrosion resistance 416.107 Other MCrAlY SV-30 ! proprietary MCrAlY for NI-548 416.110 gas atomized SL-30 stationary gas turbine 418.109 SV-20 applications NI-535 418.111 SL-20 ! availability only to OEM Sulzer Metco 4409 422.801 Sicoat 2231 approved users CO-301, Sulzer Metco 4201 428.806 Sicoat 2453 NI-666, Sulzer Metco 4485 Additional grain sizes on request 14 Conversion Tables Particle Size Bond Strength 1 MPa = 1 N/mm² = 0.145 x 10³ psi 1 psi = 6.895 x 10³ MPa µm mesh (ASTM) MPA psi 38 400 10 1450 45 325 25 3625 53 270 30 4350 63 230 35 5075 75 200 40 5800 90 170 50 7250 106 140 60 8700 125 120 70 10150 150 100 Temperature Coating Thickness 5 °C = (°F - 32) x 0.55; °F = 1.8 x °C + 32 1 µm = 4 x 10 inch = 0.04 mil 1 mil = 1/1000 inch = 25.4 µm °C °F µm mil 350 660 10 0,4 480 900 20 0,8 500 930 50 2 540 1000 100 4 650 1200 200 8 750 1380 300 12 800 1470 850 1560 900 1650 1000 1830 1100 2010 1200 2190 1300 2370 1600 2910 ® ® AMPERIT belongs to the AMPERE product line, whose trademarks are protected for H.C. Starck GmbH, Goslar ® AMDRY is a registered trademark of Sulzer Metco AG, Switzerland 15 Die vorstehenden technischen Angaben und Beschreibungen entsprechen unserem gegenwärtigen Kenntnisstand. Hierin enthaltene Angaben gelten im Fall von Vertragsabschlüssen nicht als zugesicherte Eigenschaften. Bei Bestellungen mit Bezug auf dieses Produktdatenblatt ist die Revisionsnummer anzugeben. Lieferungen erfolgen nach dem jeweiligen aktuellen Produktdatenblatt und der aktuellen Fassung unserer Allgemeinen Geschäftsbedingungen. The conditions of your use and application of our products, technical assistance and information (whether verbal, written or by way of production evaluations), including any suggested formulations and recommendations, are beyond our control. Therefore, it is imperative that you test our products, technical assistance and information to determine to your own satisfaction whether they are suitable for your intended uses and applications. This application-specific analysis at least must include testing to determine suitability from a technical as well as health, safety, and environmental standpoint. Such testing has not necessarily been done by H.C. Starck. All information is given without warranty or guarantee. It is expressly understood and agreed that the customer assumes and hereby expressly releases H.C. Starck from all liability, in tort, contract or otherwise, incurred in connection with the use of our products, technical assistance and information. Any statement or recommendation not contained herein is unauthorized and shall not bind H.C. Starck. Nothing herein shall be construed as a recommendation to use any product in conflict with patents covering any material or its use. No license is implied or in fact granted under the claims of any patent. In case of order please refer to issue number of this product data sheet. All deliveries are based on the latest issue of the product data sheet and the latest version of our General Conditions of Sale and Delivery. H.C. Starck GmbH H.C. Starck, Liaison Office Benelux H.C. Starck Canada P.O. Box 25 40, D-38615 Goslar Postbus 80, NL-3640 AB Mijdrecht Bayer Inc., P.O. Box 30 01, Phone +49/53 21/7 51-39 63, Phone +31/2 97/28 04 25, 1265 Vidal Street South, Sarnia, Telefax +49/53 21/7 51-49 63 Telefax +31/2 97/28 06 41 Ontario/Canada N7T 7M2, E-mail: hans-juergen.schommartz.hs@hcstarck.de E-mail: andre.geerts.ag@baymyd.bayer.nl Phone +1 /519/ 339-7845, Telefax +1 /519/ 339-7851 H.C. Starck GmbH H.C. Starck, Liaison Office Scandinavia P.O. Box 13 46, D-79721 Laufenburg/Baden P.O. Box 52 37, S-40224 Göteborg H.C. Starck - V TECH Ltd. Phone +49/77 63/82-5 97, Phone +46/31/83 98 61, Ohmori NM Bldg., Telefax +49/77 63/82-3 33 Telefax +46/31/83 25 75 1-1, Ohmori Kita 2-chome E-mail: hans.keller.hk@hcstarck.de E-mail: tina.malander.tm@bayer.se Ohta-ku, Tokyo 143-0016/Japan, Phone +81/3/57 62-20 40, H.C. Starck GmbH, H.C. Starck, Liaison Office South East Asia, Telefax +81/3/57 62-20 22 UK Liaison Office No. 9 Benoi Sector, Singapore 629844 E-mail: hajime.nakadate.hn@bayer-ag.de Aizlewood’s Mill, Phone +65/66 22-4 28, Nursery Street Sheffield S3 8GG, UK. Telefax +65/2 61-96 09 H.C. Starck (Thailand) Co., Ltd. Phone +44 /114/ 2823156, E-mail: kennywaichong.wong.kw@bayer-ag.de 5, I-3A Road, Map Ta Phut Industrial Estate, Telefax +44 /114/ 2823244 Rayong 21150/Thailand, E-mail: mike.thompson.mt@bayer-co.uk H.C. Starck, Liaison Office Italy Phone 66/38/ 683-077, Bayer S.p.A. Telefax 66/38/ 683-043 H.C. Starck, Bureau de Liaison France, Viale Certosa, 130, 20156 Milan/Italy 49-51, Quai de Dion Bouton Phone +39/023978/2219 F-92815 Puteaux Cedex, Telefax +39/023978/4958 Phone +33/1/49 06 58 15, E-mail: silke.bothe.sb1@bayer-ag.de Telefax +33/1/49 06 58 16 E-mail: herve.rousseau.hr@bayer-ag.de H.C. Starck Inc. 45 Industrial Place, Newton, MA. 02461-1951/USA Phone +1 /617/ 630-5910, Telefax +1 /617/ 630-5908 E-mail: hamid.haider.b@bayer.com A Bayer Company L 02/02
Frequently asked questions
What makes Elite.Parts unique?

What kind of warranty will the Thermal Spray Powder have?

Which carriers does Elite.Parts work with?

Will Elite.Parts sell to me even though I live outside the USA?

I have a preferred payment method. Will Elite.Parts accept it?

What they say about us
FANTASTIC RESOURCE
One of our top priorities is maintaining our business with precision, and we are constantly looking for affiliates that can help us achieve our goal. With the aid of GID Industrial, our obsolete product management has never been more efficient. They have been a great resource to our company, and have quickly become a go-to supplier on our list!
Bucher Emhart Glass
EXCELLENT SERVICE
With our strict fundamentals and high expectations, we were surprised when we came across GID Industrial and their competitive pricing. When we approached them with our issue, they were incredibly confident in being able to provide us with a seamless solution at the best price for us. GID Industrial quickly understood our needs and provided us with excellent service, as well as fully tested product to ensure what we received would be the right fit for our company.
Fuji
HARD TO FIND A BETTER PROVIDER
Our company provides services to aid in the manufacture of technological products, such as semiconductors and flat panel displays, and often searching for distributors of obsolete product we require can waste time and money. Finding GID Industrial proved to be a great asset to our company, with cost effective solutions and superior knowledge on all of their materials, it’d be hard to find a better provider of obsolete or hard to find products.
Applied Materials
CONSISTENTLY DELIVERS QUALITY SOLUTIONS
Over the years, the equipment used in our company becomes discontinued, but they’re still of great use to us and our customers. Once these products are no longer available through the manufacturer, finding a reliable, quick supplier is a necessity, and luckily for us, GID Industrial has provided the most trustworthy, quality solutions to our obsolete component needs.
Nidec Vamco
TERRIFIC RESOURCE
This company has been a terrific help to us (I work for Trican Well Service) in sourcing the Micron Ram Memory we needed for our Siemens computers. Great service! And great pricing! I know when the product is shipping and when it will arrive, all the way through the ordering process.
Trican Well Service
GO TO SOURCE
When I can't find an obsolete part, I first call GID and they'll come up with my parts every time. Great customer service and follow up as well. Scott emails me from time to time to touch base and see if we're having trouble finding something.....which is often with our 25 yr old equipment.
ConAgra Foods