GIDDINGS & LEWIS M.1017.3095
Specifications
DC source requirements
Nominal 24V DC; range 20 to 30 VDC
Field side connector
Two 12-pin connectors, screw terminals
Grouping of outputs
Two groups of 8 solid-state switches. Each group may use its own DC supply, or one supply may be daisy-chained. These must be referenced to 0V.
Humidity
5 to 95%, non-condensing
Leakage current in off state
0.5 mA max
Logic side LED, short circuit
status A red LED lights to indicate a short circuit condition
Logic side LEDs, module status
Data In LED Data Out LED Configured LED Power LED
Logic side LEDs, output status
A yellow LED for each output
Maximum current per group
4 A of continuous current for the group;each switch is rated at .5 A continuous
Module power requirements
100 mA from an external 24V DC supply
Operating Temperature Range
7° C to 55° C (45° F to 131° F)
Physical Size
4.05" wide x 4.825" high x 3" deep 102.9 mm x 122.6 mm x 76.2 mm
Protection of logic circuits
Optical isolation between the logic and field side, transient suppression on the 24V external supply
Response to scan loss
All outputs are reset to the OFF state
Shock
(per IEC 68-2-27) Four shocks per axis (15g/11 msec)
Storage Temperature Range
-40° C to 85° C (-40° F to 185° F)
Surge current, maximum
25 A for 130 µsec, every 100 msec
Switch characteristics
Solid-state switches
Switch voltage, maximum ON
1 VDC max
Time delay off for resistive loads
50 µsec max
Time delay on for resistive loads
50 µsec max
Vibration
(per IEC 68-2-6) 10-57 Hz (constant amplitude .15 mm)57 - 2000 Hz (acceleration 2 g)
Datasheet
Extracted Text
Block I/O Modules Manual Version 2.0 Giddings & Lewis Controls, Measurement and Sensing NOTE Progress is an on-going commitment at Giddings & Lewis. We continually strive to offer the most advanced products in the industry; therefore, information in this document is subject to change without notice. The illustrations and specifications are not binding in detail. Giddings & Lewis shall not be liable for any technical or editorial omissions occurring in this document, nor for any consequential or incidental damages resulting from the use of this document. DO NOT ATTEMPT to use any Giddings & Lewis product until the use of such product is completely understood. It is the responsibility of the user to make certain proper operation practices are understood. Giddings & Lewis products should be used only by qualified personnel and for the express purpose for which said products were designed. Should information not covered in this document be required, contact the Customer Service Department, Giddings & Lewis, 660 South Military Road, P.O. Box 1658, Fond du Lac, WI 54936- 1658. Giddings & Lewis can be reached by telephone at (920) 921–7100. Release 2002 © 2001-2002 Giddings & Lewis, Controls, Measurement, and Sensing, A Company of Thyssen Krupp Technologies Windows 95, 98, NT, Microsoft, and MS-DOS are registered trademarks of Microsoft Corporation. Pentium and PentiumPro are trademarks of Intel Corporation. PiC900, PiCPro, MMC, MMC for PC, PiCServoPro, PiCTune, PiCProfile, LDO Merge, PiCMicroTerm and PiC Programming Pendant are trademarks of Giddings & Lewis, LLC Table of Contents: Block I/O Modules 1 Safety Precautions.................................................................................................... 1-1 1.1 System Safety ................................................................................................... 1-1 1.1.1 User Responsibility .............................................................................. 1-1 1.1.2 Safety Instructions................................................................................ 1-2 1.2 Safety Signs ...................................................................................................... 1-2 1.3 Warning Labels................................................................................................. 1-3 1.4 Safety First........................................................................................................ 1-4 1.5 Safety Inspection............................................................................................... 1-4 1.5.1 Before Starting Operations................................................................... 1-4 1.6 After Shutdown................................................................................................. 1-4 1.7 Operating Safely ............................................................................................... 1-5 1.8 Electrical Service & Maintenance Safety ......................................................... 1-6 1.9 Safe Cleaning Practices .................................................................................... 1-7 2 Guide to Using Block I/O ........................................................................................ 2-1 2.1 Attaching a Block I/O Module to the DIN Rail................................................ 2-1 2.2 Safety Concerns ................................................................................................ 2-2 2.3 Wiring Guidelines............................................................................................. 2-3 2.4 Troubleshooting ............................................................................................... 2-6 2.4.1 Troubleshooting Table ......................................................................... 2-6 2.4.2 Troubleshooting Communication Problems - LEDs and Blink Codes 2-7 3 Block Output 24V DC Source Module (16 Points) ............................................... 3-1 3.1 Introduction....................................................................................................... 3-1 3.2 Connections ...................................................................................................... 3-2 3.2.1 Communications Connections.............................................................. 3-4 3.2.1.1 LEDs ................................................................................... 3-4 3.2.2 Protecting from an Inductive Load....................................................... 3-5 3.3 Theory of Operation.......................................................................................... 3-6 3.4 Specification Table .......................................................................................... 3-7 4 Block Input 24V DC Module (16 points) ............................................................... 4-1 4.1 Introduction....................................................................................................... 4-1 4.2 Connections ...................................................................................................... 4-2 4.2.1 Communications Connections.............................................................. 4-4 4.2.1.1 LEDs ................................................................................... 4-4 4.3 Theory of Operation.......................................................................................... 4-5 4.4 Specification Table ........................................................................................... 4-7 5 Block 24V DC 8 In/8 Out Module .......................................................................... 5-1 5.1 Introduction....................................................................................................... 5-1 5.2 Connections ...................................................................................................... 5-2 5.2.1 Communications Connections.............................................................. 5-5 5.2.1.1 LEDs ................................................................................... 5-5 5.2.2 Protecting from an Inductive Load....................................................... 5-6 5.3 Theory of Operation.......................................................................................... 5-7 5.3.1 Outputs ................................................................................................. 5-7 5.3.2 Inputs.................................................................................................... 5-7 5.4 Specification Table ........................................................................................... 5-10 GIDDINGS & LEWIS Block I/O Manual TOC-1 6 Block Output 120V AC Module (8 points) ............................................................ 6-1 6.1 Introduction....................................................................................................... 6-1 6.2 Connections ...................................................................................................... 6-2 6.2.1 Fusing................................................................................................... 6-3 6.2.1.1 Fuse Monitor....................................................................... 6-3 6.2.2 Communications Connections.............................................................. 6-4 6.2.2.1 LEDs ................................................................................... 6-4 6.2.3 Protecting from an Inductive Load....................................................... 6-5 6.3 Theory of Operation.......................................................................................... 6-5 6.4 Specification Table ........................................................................................... 6-6 7 Block Relay Module (8 points)................................................................................ 7-1 7.1 Introduction....................................................................................................... 7-1 7.2 Connections ...................................................................................................... 7-2 7.2.1 Normally Open Contact Form C Type................................................. 7-3 7.2.2 Normally Closed Contact Form C Type .............................................. 7-3 7.2.3 Normally Open Contact Form A Type................................................. 7-4 7.2.4 Contact Noise Suppression................................................................... 7-5 7.2.5 Communications Connections.............................................................. 7-6 7.2.5.1 LEDs ................................................................................... 7-6 7.3 Theory of Operation.......................................................................................... 7-7 7.4 Specification Table ........................................................................................... 7-9 8 Block Input 120V AC Module (8 points) ............................................................... 8-1 8.1 Introduction....................................................................................................... 8-1 8.2 Connections ...................................................................................................... 8-2 8.2.1 Communications Connections.............................................................. 8-4 8.2.1.1 LEDs ................................................................................... 8-4 8.3 Theory of Operation.......................................................................................... 8-5 8.4 Specification Table ........................................................................................... 8-7 9 Block Input Resolver Module (6 channel) ............................................................. 9-1 9.1 Introduction....................................................................................................... 9-1 9.2 Connections ...................................................................................................... 9-2 9.2.1 Adding an External Potentiometer ....................................................... 9-5 9.2.2 Communications Connections.............................................................. 9-6 9.2.2.1 LEDs ................................................................................... 9-6 9.3 Resolvers........................................................................................................... 9-7 9.4 Theory of Operation.......................................................................................... 9-7 9.5 Specification Table ........................................................................................... 9-8 TOC-2 Block I/O Manual GIDDINGS & LEWIS 10 Block Output Stepper/Input Encoder/Input 24V DC Module (2/2/2 Channel) . 10-1 10.1 Introduction....................................................................................................... 10-1 10.1.1 Output Stepper...................................................................................... 10-2 10.1.2 Input Encoder ....................................................................................... 10-2 10.1.3 Input 24V DC....................................................................................... 10-2 10.2 Connections ...................................................................................................... 10-3 10.2.1 Stepper Connections............................................................................. 10-3 10.2.2 Connecting the Block Module to Stepper Drives................................. 10-5 10.2.2.1 Opto-Coupler Drive Inputs ................................................. 10-6 10.2.2.2 Opto-Coupler with Common Source Drive Inputs ............. 10-7 10.2.2.3 Single-Ended Drive Inputs.................................................. 10-8 10.2.2.4 Differential Drive Inputs..................................................... 10-10 10.2.3 Block Module Encoder Connections.................................................... 10-12 10.2.3.1 Encoder Drivers .................................................................. 10-14 10.2.4 Block Module DC Input Connections.................................................. 10-15 10.2.5 Power Connections............................................................................... 10-15 10.2.6 Communications Connections.............................................................. 10-16 10.2.6.1 LEDs ................................................................................... 10-16 10.3 Theory of Operation.......................................................................................... 10-17 10.3.1 Stepper Theory of Operation................................................................ 10-17 10.3.2 Block Module Encoder Theory of Operation....................................... 10-18 10.3.2.1 Incremental Encoders ......................................................... 10-18 10.3.3 DC Input Theory of Operation ............................................................. 10-20 10.4 Specification Table .......................................................................................... 10-22 11 Block Input Analog Module (4 Channel)............................................................... 11-1 11.1 Introduction....................................................................................................... 11-1 11.2 Connections ...................................................................................................... 11-2 11.2.1 Communications Connections.............................................................. 11-7 11.2.1.1 LEDs ................................................................................... 11-7 11.3 Theory of Operation.......................................................................................... 11-8 11.4 Specification Table .......................................................................................... 11-9 12 Block Output 4-20mA Module (4 Channel) .......................................................... 12-1 12.1 Introduction....................................................................................................... 12-1 12.2 Connections ...................................................................................................... 12-2 12.2.1 Communications Connections.............................................................. 12-4 12.2.1.1 LEDs ................................................................................... 12-4 12.3 Theory of Operation.......................................................................................... 12-5 12.4 Specification Table ........................................................................................... 12-6 13 Block Output +10V DC Module (4 Channel) ........................................................ 13-1 13.1 Introduction....................................................................................................... 13-1 13.2 Connections ...................................................................................................... 13-2 13.2.1 Communications Connections.............................................................. 13-3 13.2.1.1 LEDs ................................................................................... 13-3 13.2.2 Analog Output Receiving Devices....................................................... 13-4 13.3 Theory of Operation.......................................................................................... 13-5 13.4 Specification Table ........................................................................................... 13-6 GIDDINGS & LEWIS Block I/O Manual TOC-3 14 Block Input 24V DC Module/J (16 points) ............................................................ 14-1 14.1 Introduction....................................................................................................... 14-1 14.2 Connections ...................................................................................................... 14-2 14.2.1 Communications Connections.............................................................. 14-5 14.2.1.1 LEDs ................................................................................... 14-5 14.3 Theory of Operation.......................................................................................... 14-6 14.4 Specification Table ........................................................................................... 14-8 15 Block 24V DC 8 In/8 Out Module/J ....................................................................... 15-1 15.1 Introduction....................................................................................................... 15-1 15.2 Connections ...................................................................................................... 15-2 15.2.1 Communications Connections.............................................................. 15-5 15.2.1.1 LEDs ................................................................................... 15-5 15.2.2 Protecting from an Inductive Load....................................................... 15-6 15.3 Theory of Operation.......................................................................................... 15-7 15.3.1 Outputs ................................................................................................. 15-7 15.3.2 Inputs.................................................................................................... 15-7 15.4 Specification Table ........................................................................................... 15-10 16 Block Input/Output Analog Module (4 In 4 Out) ................................................. 16-1 16.1 Introduction....................................................................................................... 16-1 16.2 Connections ...................................................................................................... 16-2 16.2.1 Analog Output Receiving Devices....................................................... 16-7 16.2.2 Communications Connections.............................................................. 16-8 16.2.2.1 LEDs ................................................................................... 16-8 16.3 Theory of Operation.......................................................................................... 16-9 16.4 Specification Table .......................................................................................... 16-10 INDEX ............................................................................................................................ IND-1 TOC-4 Block I/O Manual GIDDINGS & LEWIS Safety Precautions 1 Safety Precautions READ AND UNDERSTAND THIS SECTION IN ITS ENTIRETY BEFORE UNDERTAKING INSTALLATION OR ADJUSTMENT OF BLOCK I/O MODULES The advice contained in this section will help users to operate and maintain the equipment in a safe manner at all times. PLEASE REMEMBER THAT SAFETY IS EVERYONE'S RESPONSIBILITY 1.1 System Safety The basic rules of safety set forth in this section are intended as a guide for the safe operation of equipment. This general safety information, along with explicit service, maintenance and operational materials, make up the complete instruction set. All personnel who operate, service or are involved with this equipment in any way should become totally familiar with this information prior to operating. 1.1.1 User Responsibility It is the responsibility of the user to ensure that the procedures set forth here are followed and, should any major deviation or change in use from the original specifications be required, appropriate procedures should be established for the continued safe operation of the system. It is strongly recommended that you contact your OEM to ensure that the system can be safely converted for its new use and continue to operate in a safe manner. GIDDINGS & LEWIS Block I/O Manual 1-1 Safety Precautions 1.1.2 Safety Instructions 1. Do not operate your equipment with safety devices bypassed or doors removed. 2. Only qualified personnel should operate the equipment. 3. Never perform service or maintenance while automatic con- trol sequences are in operation. 4. To avoid shock or serious injury, only qualified personnel should perform maintenance on the system. 5. ATTENTION- DANGER TO LIFE Do not touch the main power supply fuses or any components internal to the power modules while the main power supply switch is ON. Note that when the main power switch is OFF, the incoming supply ca- ble may be live. 6. GROUNDING (Protective Earth) The equipment must be grounded (connected to the protective earth connection) according to OEM recommendations and to the latest local regulations for electrical safety. The grounding (protective earth) conductor must not be interrupted inside or outside the equipment enclosures. The wire used for equip- ment grounding (connection to protective earth) should be green with a yellow stripe. 7. If there is any doubt at all as to the safety of the equipment, you should set the main power switch to OFF and contact your OEM for advice. 1.2 Safety Signs The purpose of a system of safety signs is to draw attention to objects and situations which could affect personal or plant safety. It should be noted that the use of safety signs does not replace the need for appropriate accident prevention measures. Always read and follow the instructions based upon the level of hazard or potential danger. 1-2 Block I/O Manual GIDDINGS & LEWIS Safety Precautions 1.3 Warning Labels Hazard warning Danger Electric Shock Risk When you see this safety sign on a system, it gives a warning of a hazard or possibility of a hazard existing. The type of warning is given by the pictorial representation on the sign plus text if used. The safety color is black on a yellow background with a black symbol. To ignore such a caution could lead to severe injury or death arising from an unsafe practice. If voltage levels are included in the text they must indicate the maximum level of the hazard in normal or fault condition. Danger, Warning, or Caution warning Symbol plus DANGER, WARNING or CAUTION: These notices provide information intended to prevent potential personal injury and equipment damage. Hot Surface warning Hot Surface GIDDINGS & LEWIS Block I/O Manual 1-3 Safety Precautions 1.4 Safety First Giddings & Lewis equipment is designed and manufactured with consideration and care to generally accepted safety standards. However, the proper and safe performance of the equipment depends upon the use of sound and prudent operating, maintenance and servicing procedures by trained personnel under adequate supervision. For your protection, and the protection of others, learn and always follow these safety rules. Observe warnings on machines and act accordingly. Form safe working habits by reading the rules and abiding by them. Keep these safety rules handy and review them from time to time to refresh your understanding of them. 1.5 Safety Inspection 1.5.1 Before Starting Operations 1. Ensure that all guards and safety devices are installed and operative and all doors which carry warning labels are closed and locked. 2. Ensure that all personnel are clear of those areas indicated as potentially hazardous. 3. Remove (from the operating zone) any materials, tools or other objects that could cause injury to personnel or damage the system. 4. Make sure that the control system is in an operational condi- tion. 5. Make certain that all indicating lights, horns, pressure gauges or other safety devices or indicators are in working order. 1.6 After Shutdown Make certain all controlled equipment in the plant is safe and the associated electrical, pneumatic or hydraulic power is turned off. It is permissible for the control equipment contained in enclosures to remain energized provided this does not conflict with the safety instructions found in this section. 1-4 Block I/O Manual GIDDINGS & LEWIS Safety Precautions 1.7 Operating Safely 1. Do not operate the control system until you read and understand the operating instructions and become thoroughly familiar with the system and the controls. 2. Never operate the control system while a safety device or guard is removed or disconnected 3. Where access to the control system is permitted for manual operation, only those doors which provide that access should be unlocked. They should be locked immediately after the particular operation is com- pleted. 4. Never remove warnings that are displayed on the equipment. Torn or worn labels should be replaced. 5. Do not start the control system until all personnel in the area have been warned. 6. Never sit or stand on anything that might cause you to fall onto the con- trol equipment or its peripheral equipment. 7. Horseplay around the control system and its associated equipment is dangerous and should be prohibited. 8. Know the emergency stop procedure for the system. 9. For maximum protection when carrying out major servicing requiring the system to be powered down, the power source should be locked using a lock for which only you have the key. This prevents anyone from accidentally turning on the power while you are servicing the equipment. 10. Never operate the equipment outside specification limits. 11. Keep alert and observe indicator lights, system messages and warnings that are displayed on the system. 12. Do not operate faulty or damaged equipment. Make certain proper ser- vice and maintenance procedures have been performed. GIDDINGS & LEWIS Block I/O Manual 1-5 Safety Precautions 1.8 Electrical Service & Maintenance Safety 1. ALL ELECTRICAL OR ELECTRONIC MAINTENANCE AND SERVICE SHOULD BE PERFORMED BY TRAINED AND AUTHORIZED PERSONNEL ONLY. 2. It should be assumed at all times that the POWER is ON and all condi- tions treated as live. This practice assures a cautious approach which may prevent accident or injury. 3. To remove power: LOCK THE MAIN SWITCH IN THE OPEN POSITION. USE A LOCK TO WHICH ONLY YOU HAVE THE KEY. 4. Make sure the circuit is safe by using the proper test equipment. Check test equipment regularly 5. Capacitors take time to discharge. Care should be taken in manual dis- charging of capacitors 6. There may be circumstances where troubleshooting on live equipment is required. Under such conditions, special precautions must be taken: • Make sure your tools and body are clear of the areas of equipment which may be live. Extra safety measures should be taken in damp areas. Be alert and avoid any outside distractions. Make certain another qualified person is in attendance. 7. Before applying power to any equipment, make certain that all per- sonnel are clear of associated equipment. 8. Control panel doors should be unlocked only when checking out elec- trical equipment or wiring. On completion, close and lock panel doors. 9. All covers on junction panels should be fastened closed before leav- ing any job. 10. Never operate any controls while others are performing maintenance on the system. 11. Do not bypass a safety device. 12. Always use the proper tool for the job. 13. Replace the main supply fuses only when electrical power is OFF (locked out). 1-6 Block I/O Manual GIDDINGS & LEWIS Safety Precautions 1.9 Safe Cleaning Practices 1. Do not use toxic or flammable solvents to clean control system hardware. 2. Turn off electrical power (lock out) before cleaning control system assemblies. 3. Keep electrical panel covers closed and power off when cleaning an enclosure. 4. Always clean up spills around the equipment immediately after they occur. 5. Never attempt to clean a control system while it is operating. 6. Never use water to clean control equipment unless you are certain that the equipment has been certified as sealed against water ingress. Water is a very good conductor of electricity and the single largest cause of death by electrocution. GIDDINGS & LEWIS Block I/O Manual 1-7 Safety Precautions NOTES 1-8 Block I/O Manual GIDDINGS & LEWIS Guide to Using Block I/O 2 Guide to Using Block I/O This section covers the following: Attaching a block I/O module to a DIN rail Wiring guidelines Troubleshooting guide 2.1 Attaching a Block I/O Module to the DIN Rail 1. Hook the top edge of the module’s DIN rail slot (see Back View below) onto the top of the DIN rail. 2. Insert a small flatheaded screwdriver into the latch slot (located on the lower right-hand side - see Front View below) angling upwards in order to catch the latch handle. 3. Gently pull the latch handle down by leveraging the screwdriver toward the module. Press the module in place and release the latch handle. 4. To remove the module from the DIN rail, reverse the above procedure. NOTE: The metal strap must make a good connection to the DIN rail when the module is pressed into place. This ensures a good elec- trical connection to chassis ground (assuming the DIN rail is making good electrical connection to chassis). Figure 2-1 Attaching Module to DIN Rail F F Back View Front View Metal Strap for Chassis Ground DIN Rail Top Edge IN OUT CONF PWR ® GIDDINGS & LEWIS DIN Rail Slot OUTPUT 24V DC SOURCE Bottom Edge with Latch DIN Rail Latch Latch Handle Latch Slot Latch Handle Screwdriver Latch Slot GIDDINGS & LEWIS Block I/O Manual 2-1 (110.00 mm) 4.33" (122.6 mm) 4.825" Guide to Using Block I/O Use the mounting dimensions in Figure 2-2 when not using a DIN rail. Figure 2-2 Mounting Dimensions (12.00 mm) .472" (6.00 mm) .236" Diameter 0.176" (4.47 mm) IN OUT CONF PWR ® GIDDINGS & LEWIS NOTE: All tolerances + .005" OUTPUT 24V DC SOURCE (+ 0.127 mm) Module Depth = 3.00" (76.2 mm) Diameter 0.176" (4.47 mm) 4.05" (102.9 mm) 2.2 Safety Concerns The following information is provided to ensure compliance to the low voltage directive (73/23/EEC) when using block I/O modules. 1. Each block I/O module has an internal 24 V to 5 V converter for its logic circuitry. In the unlikely event of a certain component failure within this converter and unlimited current from the 24 V power supply, there is a possibility of a momentary flame inside the module. If this is a concern, the 24 V to the module must be fused to limit current to below 10 amps. (Use a slow blow type to allow for power-on inrush). One or more modules may be on the same fuse. 2. Block I/O DC outputs are protected from short circuits but not from con- tinuous overloads. For example, it is acceptable for a group of outputs to source 4 amps, with each output sourcing .5 amps each. Any of those out- puts can safely handle a continuous short circuit. However, there is a pos- sibility of a momentary flame inside the module if an output is allowed to draw more than 10 amps continuously. If continuous overloads are con- sidered a possibility in a given application, it is recommended to fuse each group of outputs at 5 amps or less. 2-2 Block I/O Manual GIDDINGS & LEWIS Guide to Using Block I/O 2.3 Wiring Guidelines The wiring practices specified in Appendix O.1 - EMC Guidelines should be followed when working with the block I/O modules. NOTE Giddings & Lewis continues to recommend separation of low level signals (encoder, analog, communications, fast DC inputs) from high voltage or high current lines from any of the above. More specifical- ly, maintain at least one inch of separation around encoder signals and around communication signals. Use Belden 9729 or equivalent for Block I/O communication wiring. This cable has a characteristic impedance of 100 ohms and has a nominal conductor/conductor capacitance of 12.5 pF/ft, 4 pF/m. The following additional information is provided because of the many possible ways to distribute block I/O modules. It is important to maintain the concept of a single point ground (SPG) with any distribution pattern used. Any ground loop(s) will compromise the use of chassis ground by each block I/O module to reduce emissions and to provide immunity to electrical noise. The shields and I/O lines are capacitively coupled to the metal strap located on the back of the module and also to the chassis pin located on the terminal block in the front of the module. Chassis ground connection is made through the metal strap to the DIN rail (which requires a good electrical connection to 2 chassis) or through a six inch (or less) 14 AWG (2 mm )wire from the chassis pin. Figure 2-3 illustrates a basic block I/O setup. The block I/O modules are distributed around a machine assembly. It is assumed that the metal structure of the assembly provides the best common chassis ground. Modules are connected to this chassis ground via a DIN rail or a separate wire to the chassis pin of the module. GIDDINGS & LEWIS Block I/O Manual 2-3 Guide to Using Block I/O A heavy gauge wire or flat braided cable is used to connect the machine assembly chassis to the SPG of the main control enclosure. When a variable frequency drive or similar noisy device is installed on the machine assembly, maintaining the SPG concept is more difficult. The frame of the drive is usually connected to the structure of the machine assembly. This can introduce noise between the chassis of the machine assembly and the SPG. However, this noise can be reduced by ensuring that a ground wire is run parallel with the drive’s power wires and is connected to the SPG. This is typically the green safety ground wire specified by the drive manufacturer and should be of the same gauge as the power wires. Figure 2-3 Remote Block I/O distributed around One Machine Assembly Main Control Enclosure Controller T R SPG Block I/O Modules Machine Assembly Chassis T R T R T R T R Ground R R T R T T R T The distance between Block I/O can be up to 200 feet 2-4 Block I/O Manual GIDDINGS & LEWIS Guide to Using Block I/O Figure 2-4 illustrates the distribution of the block modules around several sites that do not have the same common chassis ground. The chassis ground of each site should be connected to the SPG in the main control enclosure. Regardless of these connections to SPG, noise sources in the main control and/or in the remote sites may cause momentary potential differences between chassis grounds. If the differences are too great, some communication messages will be corrupted and will have to be retransmitted. To reduce or eliminate communication retries associated with momentary ground differences, use .1 µf capacitors to connect shield to chassis for communication cables entering and leaving a remote site. NOTE: The shield connection to the PiC900/90 CPU is already internally connected to SPG through a .1 µf capacitor. For MMC and MMC for PC products, the shield is internally connected directly to SPG. Figure 2-4 Remote Block I/O Distributed around Several Sites Main Control Enclosure Controller SHLD T R SPG Chassis Chassis Ground Ground Block 2 Block 1 Block 3 Block 4 R R T T R R T T R R R T R T T T SHLD SHLD SHLD SHLD .1 µf .1 µf .1 µf Remote Site 1 Remote Site 2 The distance between block I/O modules can be up to 200 feet. GIDDINGS & LEWIS Block I/O Manual 2-5 Guide to Using Block I/O 2.4 Troubleshooting 2.4.1 Troubleshooting Table Problem Indication or Solution Communication/configuration error: Generally, the diagnostic LED on the CPU blinks a block communication circuitry failure three digit error code to indicate the block location open communication cable of the first error detected. The first digit flashes a "3" shorted communication cable to indicate it is a block I/O problem. The number of wrong block (ID) at given location flashes in the second and third digits indicates the block I/O module (01 through 77). The second digit will flash a 1 - 7, 10 for 0. The third digit will flash a 1 - 9, 10 for 0. For example, if the second digit flashes 3 times and the third digit flashes 10 times, the module is 30. See the next section for more information on troubleshooting communication problems. 24V missing Block module power LED is off. 24V reversed Block module power LED is off. Circuitry is diode protected. 24V too high (over the 30V specification) Block I/O circuitry is protected against high voltage transients by on-board varistors. However, the module may be damaged by steady-state excessive high voltage. 24V too low (below the 20V specification) After voltage drops below an non-guaranteed safety margin, there will be communication errors. An even lower voltage will cause the on-board voltage monitor to hold the circuitry in reset and the green power LED off. However, there is a voltage level which allows communications to function but prevents proper operation of the I/O. When in doubt, check the 24V level. Intermittent communication errors due to CPU blinks the 232 communication error code. noise Field side failure Use normal ladder troubleshooting methods. 2-6 Block I/O Manual GIDDINGS & LEWIS Guide to Using Block I/O 2.4.2 Troubleshooting Communication Problems - LEDs and Blink Codes The status of the configuration and power LEDs for each block module provides the most basic information for locating a communication problem. In general, a good troubleshooting technique is to turn the RUN/STOP switch on the PiC to the STOP position, turn off the 24V DC power to the block I/O modules, and then turn the 24V DC supply back on again. (Note: Power may have to be turned on sequentially to groups of modules if the power supply can not handle the approximate 100 µsec inrush of 2.5A per module. The green power LED of each module should be on as soon as 24 Vdc is applied to each module. The green configuration LED should go on for each properly wired module in the configuration after the scan has started. This LED will be off for all modules beyond the location of any module with a wiring problem. If none of the configuration LEDs illuminate on, the problem may be a reversal of the receive wires at the CPU. If "Data in and Data out" LEDs illuminate, there may be a problem in the return path connections. The "Data in" and "Data out" LEDs indicate data flow with respect to the CPU. During operation, these LEDs emit a faint glow indicating normal communications. When a failure occurs, they can either be "OFF" or in a steady "ON" state A block’s "Data out" LED is an indication of data flow from the CPU or from the previous block. The "Data in" LED indicates data flow from the block to the CPU or data flow from the next block. Figure 2-5 Transmission of Data Between Controller and Block Modules 5 4 2 1 5 4 2 1 5 4 2 1 5 4 2 1 5 4 2 1 5 4 2 1 3 4 5 6 R T R T R T T T R T R R TR CC2 CC2 CC1 CC2 CC1 CC1 Block 1 Block 2 Block 3 Controller NOTE: CC represents the communication connections at the top of the block modules. T = Transmit R = Receive GIDDINGS & LEWIS Block I/O Manual 2-7 Guide to Using Block I/O The "Data in" and "Data out" LED status for several types of wiring errors is shown in Table 1-1 that follows. This can be used as a guideline for what could happen at other locations. It is assumed that the 24VDC power has been cycled off/on to ensure that each block can be configured. IMPORTANT When a communication error occurs, a three digit error code is flashed on the CPU’s diagnostic LED. This indi- cates the location of the module where communication was interrupted. It is not necessarily the location of the error itself. Therefore, it is important to restart the pro- gram by turning the RUN/STOP switch to stop and back to run. The diagnostic LED will provide information to help locate where there is an error. FIRMWARE NOTICE Firmware for PiCPro 11.0 or higher should be installed on CPUs with Block I/O. This version allows the user to accurately troubleshoot Block I/O. 2-8 Block I/O Manual GIDDINGS & LEWIS Guide to Using Block I/O Table 1-1 LEDs and Blink Codes Block 1 LEDs Block 2 LEDs Data Data Data Data Failure/Error @ CC2 of block 1 or Blink CC1 of In Out CFG PWR In Out CFG PWR Codes block 2* 301 4 and 5 reversed on Off Off On On Off Off On On (3-10-1) CC1 of Block 1 301 4 and 5 shortened Off Off On On Off Off On On (3-10-1) on CC1 of Block 1* 301 4 or 5 open on CC1 Off Off On Off Off Off On On (3-10-1) of Block 1 1 or 2 open, 301 reversed, or Off On On On Off Off On On (3-10-1) shortened on CC1 of Block 1* 4 and 5 reversed on 301 On Off On On Off Off On On CC2 of Block 1 or (3-10-1) CC1 of block 2 302 4 or 5 shortened on Off Off On On Off Off On On (3-10-2) CC2 of Block 2* 4 or 5 open on CC2 302 Off Off On On Off Off On On of block 1 or CC1 of (3-10-2) block 2 1 or 2 open, reversed, or 302 Off Off On On Off On On On shortened on CC2 (3-10-1 of Block 1 or CC1 of Block 2* 302 CC1 and CC2 Off Off On On Off On** On On (3-10-2) reversed at Block 2 301 Off CC1 failed on Block Off On Off On Off Off On (3-10-1) *** 1 CC2 failed on Block 302 Off Off Off On On Off On On 1 or CC1 failed on (3-10-2) *** Block 2 * The communications drivers are internally short circuit protected. ** The data out LED of block 3 will also be illuminated. *** If "Data In" LED is Bright or if "Data In" and "Data Out" are pulsing with equal intensity, monitor "Data Out" of each Block starting with Block 1. Check the wiring between blocks whose "Data Out" signals are opposite (ON vs. OFF). **** CFG of next block will also be OFF. GIDDINGS & LEWIS Block I/O Manual 2-9 Guide to Using Block I/O The following flowchart provides an alternative troubleshooting guide. The flowchart assumes that the 24VDC power has been cy cled off/on to ensure each block can be configured. 3XX Flash Code Wrong module? Verify that module matches module declared in hardware declarations table. No Are Pins 4 and 5 swapped or open? Yes If the flash code is 3-10-1, If yes, the wiring error is located between is the Data In LED of the the last block module that has its first block on? Data In LED on and the next module. No No Is the communications cable installed on the wrong connector? If yes, wiring error is between the module indicated in the flash code and previous block. Verify that the communications cable from the previous block (or the CPU) is installed in the CC1 connector (left connector) and the cable going to the next block is installed in the CC2 connector (right connector) of the module. No Are pins 1 and 2 either swapped, open, or shorted together? If yes, the Data Out LED will be glowing on the module identified by the flash code. Wiring error is between the module indicated in the flash code and the previous block module. No Are pins 4 and 5 open or shorted together? If yes, the wiring error is between the module indicated in the flash code and the previous block module. Example: If the flash code is 331 (block 31), then the open wire is between blocks 30 and 31. No Block module may be defective. Defective module is either the module indicated by the flash code or the previous block. END 2-10 Block I/O Manual GIDDINGS & LEWIS Block Output 24V DC Source Module (16 Points) 3 Block Output 24V DC Source Module (16 Points) 3.1 Introduction The 16 point 24V DC block output module sources voltage for individual loads from one or more DC power supplies. Each external supply is nominally 24 volts, but can be between 20 and 30 volts. 16 LEDs near the field terminal connector of the module indicate the logic state that drives each output. Another LED labeled SC turns on if any output attempts to drive a short circuit. Figure 3-1 Block Output 24V DC Source Module (16 point) Communications Receive/Transmit IN OUT CONF PWR Communications/Status LEDs ® GIDDINGS & LEWIS Output Status OUTPUT 24V DC SOURCE LEDs Cover (shown open) Screw Terminal Connector GIDDINGS & LEWIS Block I/O Manual 3-1 Block Output 24V DC Source Module (16 Points) 3.2 Connections A screw terminal connection is provided for each output and for each external power supply connection. The outputs are isolated in two groups of eight as shown in Figure 3-2. The external DC supply that powers the output signals should have a wire connected from its 0V (COMMON) terminal directly to the single point ground used for the system rack. Figure 3-2 Screw Terminal Connection Assignments 1 2 3 4 5 6 7 8 9 10 11 12 13 14 15 16 17 18 19 20 21 22 23 24 Line 1 Out1 Out3 Out5 Out7 Line2 Out9 Out11 Out13 Out15 24V Com1 Out2 Out4 Out6 Out8 Com2 Out10 Out12 Out14 Out16 0V Chassis Group 1 Group 2 Each group has its own short circuit protection. However, there is just one short circuit LED indicator. Connections for one group of outputs are illustrated in Figure 3-3. The common side of each load must be connected to the 0V terminal of the supply. This 0V terminal is connected to the SPG used by the system rack. Use up to 14 AWG for field side wiring. 3-2 Block I/O Manual GIDDINGS & LEWIS Block Output 24V DC Source Module (16 Points) Figure 3-3 Connections for One Group of Outputs 123 4 5 13 14 15 16 17 Line 1 Com1 Out1 Out2 Out3 Out4 Out5 Out6 Out7 Out8 V+ 0V DC To SPG Power Supply GIDDINGS & LEWIS Block I/O Manual 3-3 Block Output 24V DC Source Module (16 Points) 3.2.1 Communications Connections There are two 5-pin communications connectors and four logic LEDs on the top of the block I/O module as shown in Figure 3-4 below. Figure 3-4 Pinouts for Communication Connectors In (from CPU) Out (to next block I/O module) Pin # 5 4 3 2 1 Pin # 5 4 3 2 1 Communications Receive/Transmit IN OUT CONF PWR ® GIDDINGS & LEWIS 3.2.1.1 LEDs LED Color State Definition DATA IN Yellow FAINT Data being passed through the block module BRIGHT No activity through the block or OFF module DATA OUT Yellow FAINT Data is being passed through the block module BRIGHT No activity through the block or OFF module CONFG Green ON Communication established with this block I/O module OFF Communication not established PWR Green ON Internal +5V logic power supply OK OFF No external 24V applied or internal 5V logic supply not OK 3-4 Block I/O Manual GIDDINGS & LEWIS Driver - (twisted pair output) Driver + (twisted pair output) Shield Receiver - (twisted pair input) Receiver + (twisted pair input) Receiver - (twisted pair input) Receiver + (twisted pair input) Shield Driver - (twisted pair output) Driver + (twisted pair output) Block Output 24V DC Source Module (16 Points) 3.2.2 Protecting from an Inductive Load Resistive loads can be connected to the module and controlled by the system with no precautions other than making sure they have a connection to the common of the DC power supply. Inductive loads have an electrical "kickback" when current is stopped. This can damage or destroy the output switching device. Each output in the Output 24V DC module has a diode through which reverse current can be safely routed. Figure 3-5 shows how the internal diode works with an inductive load. When an output is energized, represented in Figure 3-5a by a closed switch, current passes through the load into the common line. When the output is de-energized, represented in Figure 3-5b by an open switch, current stops and the inductive field collapses. The state of the outputs is controlled by the CPU module. This creates a reverse voltage across the load called "kickback" which tries to continue the current. The voltage is in series with the DC power supply. The combined voltage appears across the output switching device in the module. If this were the only path available, voltage across the device would peak at several hundred volts. The internal diode provides another path for current. This limits the peak reverse voltage across the load to less than 1 V. Every switch in the Output 24V DC module has this protection so you can connect an inductive load to any terminal. Figure 3-5 Diagram of Internal Protection for Inductive Loads DC Power Supply DC Power Supply 0V V+ OUTPUT MODULE 0V V+ OUTPUT MODULE DCL1 DCL1 DCCOM1 Output DCCOM1 Switching Output INDUCTIVE Device Switching LOAD INDUCTIVE Device DCOUT1 LOAD DCOUT1 a) Output Energized b) Output De-energized GIDDINGS & LEWIS Block I/O Manual 3-5 Block Output 24V DC Source Module (16 Points) 3.3 Theory of Operation Each output point is a solid state switch rated at .5 A. It turns on or off according to the logic state sent to it by the CPU. If the CPU sends it a logic 1, the switch closes and the device is powered. If the CPU sends a logic 0, the switch opens and power to the device is cut off. The CPU updates the logic state for each switch every time it scans the program. The logic side of the switch is optically isolated from the field side. An LED gives the logic state of each switch. If you need to know whether voltage is actually present at the field side, use a voltmeter on the terminal screws. Each group has a .1 ohm series sensing resistor to protect against current overload in case the outputs are shorted to ground. When a short circuit condition is sensed, all outputs are pulsed on for approximately 130 microseconds every 100 millisecond. Normal operation resumes after the short is removed. In addition, each output is protected with internal clamping diodes. Without clamping, high voltage transients (kickback) from inductive loads might damage the module. 3-6 Block I/O Manual GIDDINGS & LEWIS Block Output 24V DC Source Module (16 Points) 3.4 Specification Table Characteristic Block Output 24V DC module specifications Function Sources an external DC supply to 16 loads Part number M.1017.3095 (old # 503-25908-01) DC source requirements Nominal 24V DC; range 20 to 30 VDC Field side connector Two 12-pin connectors, screw terminals Protection of logic circuits Optical isolation between the logic and field side, transient suppression on the 24V external supply Grouping of outputs Two groups of 8 solid-state switches. Each group may use its own DC supply, or one supply may be daisy-chained. These must be referenced to 0V. Short circuit protection for each group Pulses output for about 130 µsec every 100 msec until short is removed Maximum current per group 4 A of continuous current for the group; each switch is rated at .5 A continuous Logic side LEDs, module status Data In LED Data Out LED Configured LED Power LED Logic side LEDs, output status A yellow LED for each output Logic side LED, short circuit status A red LED lights to indicate a short circuit condition Switch characteristics Solid-state switches Time delay on for resistive loads 50 µsec max Time delay off for resistive loads 50 µsec max Leakage current in off state 0.5 mA max Switch voltage, maximum ON 1 VDC max Surge current, maximum 25 A for 130 µsec, every 100 msec Response to scan loss All outputs are reset to the OFF state Module power requirements 100 mA from an external 24V DC supply (20 to 30V DC range) NOTE: 2.5A, 250 microsecond inrush at power on GIDDINGS & LEWIS Block I/O Manual 3-7 Block Output 24V DC Source Module (16 Points) CE Marked Conforms to Directives 73/23/EEC, 89/336/EEC, 92/31/ EEC, 93/68/EEC by conforming to the following stan- dards: EN 50081-2:1993 EMC Generic Industrial Emissions EN 50082-2:1995 EMC Generic Industrial Immunity EN 61131-2:1994/A11:1996 Low voltage directive requirements for programmable controllers Operates with emissions below EN55011/ CISPR 11 Class A limits Immune to: Electrostatic discharge (4K V contact mode, 8K V air discharge) per EN61000-4-2 RF electromagnetic fields per EN61000-4-3, ENV 50141, and ENV50204 Electrical fast transients per EN61000-4-4 Magnetic fields per EN61000-4-8 Refer to the EMC Guidelines for more information. UL and C/UL Listed File No. E126417 NRAQ Programmable Controllers Operating temperature range 7° C to 55° C (45° F to 131° F) Storage temperature range -40° C to 85° C (-40° F to 185° F) Humidity 5 to 95%, non-condensing Physical size 4.05" wide x 4.825" high x 3" deep 102.9 mm x 122.6 mm x 76.2 mm Vibration (per IEC 68-2-6) 10-57 Hz (constant amplitude .15 mm) 57 - 2000 Hz (acceleration 2 g) Shock (per IEC 68-2-27) Four shocks per axis (15g/11 msec) 3-8 Block I/O Manual GIDDINGS & LEWIS Block Input 24V DC Module (16 points) 4 Block Input 24V DC Module (16 points) 4.1 Introduction The input 24V DC module converts DC signals from devices into logic levels that the CPU can use. Each signal is converted into a corresponding logic 1 or 0 which is transmitted through the communication interface to the CPU module. An "on" signal is nominally 24 VDC, but can be any level between 15 and 30 volts. An "off" signal is any level below 5V. The wiring configurations may be sink or source. Figure 4-1 Block Input 24V DC Module 16 point Communications Receive/Transmit IN OUT CONF PWR Communication/Status LEDs ® GIDDINGS & LEWIS Output Status LEDs OUTPUT 24VDC SINK SOURCE Cover (shown open) Screw Terminal Connector GIDDINGS & LEWIS Block I/O Manual 4-1 Block Input 24V DC Module (16 points) 4.2 Connections A screw terminal connector is provided for each input and for each external power supply connection. The inputs are isolated in two groups of eight, with one additional terminal per group for the DC source/sink connection. The devices connected to terminals in the same group have a common DC supply and are wired in the same configuration, sink or source (Figure 4-2). The external DC supply that powers the input signals should have a wire connected from its 0V (COMMON) terminal directly to the single-point ground used for the system rack. Figure 4-2 Screw Terminal Connector Assignments 1 2 3456789 10 11 12 13 14 15 16 17 18 19 20 21 22 23 24 25 26 27 28 29 30 31 32 33 34 35 36 In11 In1 In3 24V 24V In9 In13 In15 In5 24V 24V 24V 24V In7 24V 24V 0V In10 In12 0V In14 In16 0V 0V Chassis 0V In2 In4 0V In6 In8 0V Group 1 SS Group 2 SS Typically, an external 24V DC supply is connected to pins 18 and 35. These pins are internally jumpered so that the supply is available at the other pins labeled as 24V and 0V. This makes it convenient to connect a 3-wire device (e.g., a proximity switch) which requires a voltage and ground connection. Also, 24V or 0V can be easily jumpered to a group’s sink/source connection. Figure 4-3 illustrates two groups of inputs using the same power supply. Each group can work independently of the other; one group may be sink and the other source. The DC power supply for each group may be different if required, but must be referenced to the same ground. Typically just one DC power supply is used, daisy-chained from one group to the next. In Figure 4-3a, one group of eight inputs is shown with devices "sinking" current through the block DC Input module. The HOT terminal of the power supply is connected internally to the module by the jumper between 24V and Group 1 or 2 SS. The second group of eight inputs is shown with devices "sourcing" current through the block DC Input module. The COMMON terminal of the power supply is connected internally to the module by the jumper between 0V and Group 2 or 1 SS. In Figure 4-3b, the first group is shown with devices "sourcing" current through the block DC Input module. The second group is shown with devices "sinking current through the block DC Input module. In both examples the DC power supply is the same for Group 1 and 2. Use up to 14 AWG for field side wiring. 4-2 Block I/O Manual GIDDINGS & LEWIS Block Input 24V DC Module (16 points) Figure 4-3 Connectors for Two Groups of Inputs a. Group 1 Sink (Pins 8 and 9 Jumpered) and Group 2 Source (Pins 33 and 34 Jumpered) 7 15 2 3 45 6 8 9 10 11 12 13 14 16 17 18 1 25 33 36 20 21 22 23 24 26 27 28 29 30 31 32 34 35 19 Hot Common Group 1 Group 2 Sink Source 0V V+ DC Power Supply b. Group 1 Source (Pins 25 and 26 Jumpered) and Group 2 Sink (Pins 16 and 17 Jumpered) 7 3 45 6 8 9 10 11 12 13 14 15 16 17 18 1 2 25 34 35 22 23 24 26 27 28 29 30 31 32 33 36 19 20 21 Common Hot Group 1 Group 2 Source Sink 0V V+ DC Power Supply GIDDINGS & LEWIS Block I/O Manual 4-3 IN 1 IN 1 IN 2 IN 2 IN 3 IN 3 IN 4 IN 4 IN 5 IN 5 IN 6 IN 6 IN 7 IN 7 IN 8 IN 8 0V Group1 SS Group1 SS 24V IN 9 IN 9 IN 10 IN 10 IN 11 IN 11 IN 12 IN 12 IN 13 IN 13 IN 14 IN 14 IN 15 IN 15 IN 16 IN 16 0V Group2 SS Group2 SS 24V Block Input 24V DC Module (16 points) 4.2.1 Communications Connections There are two 5-pin communications connectors and four logic LEDs on the top of the block I/O module as shown in Figure 4-4. Figure 4-4 Pinouts for Communication Connectors In (from CPU) Out (to next block I/O module) Pin # 5 4 3 2 1 Pin # 5 4 3 2 1 Communications Receive/Transmit IN OUT CONF PWR ® GIDDINGS & LEWIS 4.2.1.1 LEDs LED Color State Definition DATA IN Yellow FAINT Data being passed through the block module BRIGHT No activity through the block module or OFF DATA Yellow FAINT Data is being passed through the OUT block module BRIGHT No activity through the block module or OFF CONFG Green ON Communication established with this block I/O module OFF Communication not established PWR Green ON Internal +5V logic power supply OK OFF No external 24V applied or internal 5V logic supply not OK 4-4 Block I/O Manual GIDDINGS & LEWIS Driver - (twisted pair output) Driver + (twisted pair output) Shield Receiver - (twisted pair input) Receiver + (twisted pair input) Receiver - (twisted pair input) Receiver + (twisted pair input) Shield Driver - (twisted pair output) Driver + (twisted pair output) Block Input 24V DC Module (16 points) 4.3 Theory of Operation Each input is guaranteed "on" at 15 to 30 VDC and guaranteed "off" at 0 to 5 VDC; polarity doesn't matter. Its on/off state is converted to a corresponding logic 1 or 0. This logic state is transmitted through the communication interface to the CPU module, where the processor uses it as data in the ladder program. The logic side of the input is optically isolated from the field side. An LED in the upper section of the module indicates the logic state of each input. Each group is represented by a horizontal row of LEDs. If you need to know whether voltage is present at the field side, use a voltmeter on the terminal screws. The shaded blocks in Figure 4-5 show the limits specified by the IEC. The lines show the maximum and minimum V/I of the inputs in this module. The voltage/current curve in this graph shows that the input module is well within the IEC Type 1 limits. Figure 4-5 Input Characteristics Compared to IEC Standards U in Volts MIN MAX UH MAX 30 "ON" REGION 25 U NOM 24 20 UH MIN 15 (UT ) MAX TRANSITION REGION 10 UL MAX 5 (UT ) MIN 0 "OFF" REGION I in -5 mAMPS 4 .5 2 6 8 10 12 14 15 I IT IH MAX MIN MIN INPUT CURRENT GIDDINGS & LEWIS Block I/O Manual 4-5 INPUT VOLTAGE Block Input 24V DC Module (16 points) IMPORTANT Switching devices can sometimes have a leakage current that ex- ceeds the IT (current allowed when off) of an input module. In or- min der to use such a device, an impedance (typically, a resistor) needs to be used in parallel with the input. For example, some of the newer proximity switches use two wires in- stead of three. The third wire was used for a power or ground line. Without the third wire, the switch is easier to install. However, it re- quires more leakage current in the off state to power its internal cir- cuitry. As a conservative estimate, use the following formula to calculate an external resistance value. It keeps the input voltage at or below 2.4V when the switching device is in the "off" state. 2.4V -- --- -- --- --- --- -- --- --- --- --- -- --- --- --- --- -- --- --- --- --- -- -- - ≥R Switch Leakage – 0.75mA If the switch leakage specification is ≤ 1.7 mA, then: 2.4V - - - --- --- --- -- --- --- --- --- -- --- - ≥ 2.5KΩ 1.7 – 0.75mA Use a resistor less than or equal to 2.5 KΩ. Be sure that the wattage is adequate for the resistor when the switching device is in the "on" state remembering that: 2 V ON P = --- --- --- - R 4-6 Block I/O Manual GIDDINGS & LEWIS Block Input 24V DC Module (16 points) 4.4 Specification Table Characteristic Block Input 24V DC module specifications Function Monitors on/off states from DC voltage inputs Part number M.1017.3092 (old # 503-25907-01) Field side connector Two 18-pin connectors, screw terminals Input signals (meet IEC standards) Nominal 24 VDC on, 0 VDC off UH Max (max. allowed voltage) 30 VDC IH Max (max. current @ 30 VDC) 7.5 mA UL Min Polarity independent Guaranteed on 15 VDC IH Min (min. current @ UH Min) 2.8 mA Guaranteed off 5 VDC IT Min (current allowed when off) .75 mA Time delay on 1 ms max. Time delay off 1 ms max. Protection of logic circuits Optical isolation between the logic and field sides, tran- sient suppression on the 24V external supply Logic side LEDs, module status Data In LED Data Out LED Configured LED Power LED Logic side LEDs, input circuits A yellow LED for each input Module power requirements 100 mA from an external 24V DC supply (20 to 30V DC range) NOTE: 2.5A, 250 microsecond inrush at power on GIDDINGS & LEWIS Block I/O Manual 4-7 Block Input 24V DC Module (16 points) CE Marked Conforms to Directives 73/23/EEC, 89/336/EEC, 92/31/ EEC, 93/68/EEC by conforming to the following stan- dards: EN 50081-2:1993 EMC Generic Industrial Emissions EN 50082-2:1995 EMC Generic Industrial Immunity EN 61131-2:1994/A11:1996 Low voltage directive requirements for programmable controllers Operates with emissions below EN55011/ CISPR 11 Class A limits Immune to: Electrostatic discharge (4K V contact mode, 8K V air discharge) per EN61000-4-2 RF electromagnetic fields per EN61000-4-3, ENV 50141, and ENV50204 Electrical fast transients per EN61000-4-4 Magnetic fields per EN61000-4-8 Refer to the EMC Guidelines for more information. UL and C/UL Listed File No. E126417 NRAQ Programmable Controllers Operating temperature range 7° C to 55° C (45° F to 131° F) Storage temperature range -40° C to 85° C (-40° F to 185° F) Humidity 5 to 95%, non-condensing Physical size 4.05" wide x 4.825" high x 3" deep 102.9 mm x 122.6 mm x 76.2 mm Vibration (per IEC 68-2-6) 10-57 Hz (constant amplitude .15 mm) 57 - 2000 Hz (acceleration 2 g) Shock (per IEC 68-2-27) Four shocks per axis (15g/11 msec) 4-8 Block I/O Manual GIDDINGS & LEWIS Block 24V DC 8 In/8 Out Module 5 Block 24V DC 8 In/8 Out Module 5.1 Introduction The Block 24V DC 8/8 module provides eight output points and eight input points. The eight point output section sources voltage for individual loads from a DC power supply. The external supply is nominally 24 volts, but can be between 20 and 30 volts. Eight LEDs near the field terminal connector of the module indicate the logic state that drives each output. Another LED labeled SC turns on if any output attempts to drive a short circuit. The eight point input section converts DC signals from devices into logic levels that the CPU can use. Each signal is converted into a corresponding logic 1 or 0 which is transmitted through the communication interface to the CPU module. An "on" signal is nominally 24 VDC, but can be any level between 15 and 30 volts. An "off" signal is any level below 5V. The wiring configurations may be sink or source. Eight LEDs near the field terminal connector of the module indicate the logic state of each input. Figure 5-1 Block 24V DC Output/Input Module (8/8 Point) Communications Receive/Transmit IN OUT CONF PWR Communication/Status LEDs ® GIDDINGS & LEWIS Output Status LEDs OUTPUT 24V DC Short Circuit LED Cover (shown open) Field Side Input LEDs Screw Terminal Connector GIDDINGS & LEWIS Block I/O Manual 5-1 Block 24V DC 8 In/8 Out Module 5.2 Connections A screw terminal connection is provided for each output, input, and external power supply connection. The group of eight outputs and the group of eight inputs are isolated. The output group has its own short circuit protection with a short circuit LED indicator. The input group has additional terminal connections for the DC sink/source configuration. The external DC supply that powers the output and/or input signals should have a wire connected from its 0V (COMMON) terminal directly to the single point ground used for the system rack. Figure 5-2 Screw Terminal Connection Assignments Outputs Inputs 1 2 345 6789 10 11 12 13 14 15 16 17 18 19 20 21 22 23 24 25 26 27 28 29 30 31 32 33 34 35 36 Typically, an external 24V DC supply is connected to pins 18 and 35. These pins are internally jumpered so that the supply is available at the other pins labeled as 24V and 0V. This makes it convenient to connect a 3-wire device (i.e., a proxim- ity switch) which requires a voltage and ground connection. Also, 24V or 0V can be easily jumpered to the input sink/source connection. 5-2 Block I/O Manual GIDDINGS & LEWIS DC Line 1 DC Com1 DC Out1 DC Out2 DC Out3 DC Out4 DC Out5 DC Out6 DC Out7 DC Out8 0V DC IN1 DC IN2 DC IN3 DC IN4 24V 0V DC IN5 DC IN6 DC IN7 DC IN8 24V 0V DC IN SS DC IN SS 24V 0V 24V Chassis Block 24V DC 8 In/8 Out Module Connections for the outputs are illustrated in Figure 5-3. The common side of each load must be connected to the 0V terminal of the supply. This 0V terminal is connected to the SPG used by the system rack. Use up to 14 AWG for field side wiring. Figure 5-3 Connections for the Outputs 123 4 5 19 20 21 22 23 Line 1 Com1 Out1 Out2 Out3 Out4 Out5 Out6 Out7 Out8 V+ 0V DC To SPG Power Supply GIDDINGS & LEWIS Block I/O Manual 5-3 Block 24V DC 8 In/8 Out Module Connections for the inputs are illustrated in Figure Figure 5-4. The eight inputs on the left are shown with devices "sourcing" current through the block module. The COMMON terminal of the power supply is connected inter- nally to the module by the jumper between 0V and the DC IN SS. The eight inputs in the example on the right are shown with devices "sinking" cur- rent through the block module. The HOT terminal of the power supply is con- nected internally to the module by the jumper between 24V and DC IN SS. Use up to 14 AWG for field side wiring. Figure 5-4 Connectors for Inputs 15 18 10 11 12 13 14 16 17 10 11 12 13 14 15 16 17 18 33 36 28 29 30 31 32 34 35 28 29 30 31 33 34 35 36 32 Common Hot Sink Source 0V V+ 0V V+ DC Power DC Power Supply Supply 5-4 Block I/O Manual GIDDINGS & LEWIS DC IN 1 DC IN 2 DC IN 3 DC IN 4 DC IN 5 DC IN 6 DC IN 7 DC IN 8 0V DC IN SS DC IN 1 DC IN 2 DC IN 3 DC IN 4 DC IN 5 DC IN 6 DC IN 7 DC IN 8 DC IN SS 24V Block 24V DC 8 In/8 Out Module 5.2.1 Communications Connections There are two 5-pin communications connectors and four logic LEDs on the top of the block I/O module as shown in Figure 5-5. Figure 5-5 Pinouts for Communication Connectors In (from CPU) Out (to next block I/O module) Pin # 5 4 3 2 1 Pin # 5 4 3 2 1 Communications Receive/Transmit IN OUT CONF PWR ® GIDDINGS & LEWIS 5.2.1.1 LEDs LED Color State Definition DATA IN Yellow FAINT Data being passed through the block module BRIGHT No activity through the block module or OFF DATA Yellow FAINT Data is being passed through the OUT block module BRIGHT No activity through the block module or OFF CONFG Green ON Communication established with this block I/O module OFF Communication not established PWR Green ON Internal +5V logic power supply OK OFF No external 24V applied or inter- nal 5V logic supply not OK GIDDINGS & LEWIS Block I/O Manual 5-5 Driver - (twisted pair output) Driver + (twisted pair output) Shield Receiver - (twisted pair input) Receiver + (twisted pair input) Receiver - (twisted pair input) Receiver + (twisted pair input) Shield Driver - (twisted pair output) Driver + (twisted pair output) Block 24V DC 8 In/8 Out Module 5.2.2 Protecting from an Inductive Load Resistive loads can be connected to the module and controlled by the system with no precautions other than making sure they have a connection to the common of the DC power supply. Inductive loads have an electrical "kickback" when current is stopped. This can damage or destroy the output switching device. Each output in the Output 24V DC module has a diode through which reverse current can be safely routed. Figure 5-6 shows how the internal diode works with an inductive load. When an output is energized, represented in Figure Figure 5- 6a by a closed switch, current passes through the load into the common line. When the output is de-energized, represented in Figure 5-6b by an open switch, current stops and the inductive field collapses. The state of the outputs is controlled by the CPU module. This creates a reverse voltage across the load called "kickback" which tries to continue the current. The voltage is in series with the DC power supply. The combined voltage appears across the output switching device in the module. If this were the only path available, voltage across the device would peak at several hundred volts. The internal diode provides another path for current. This limits the peak reverse voltage across the load to less than 1 V. Every switch in the Output 24V DC module has this protection so you can connect an inductive load to any terminal. Figure 5-6 Diagram of Internal Protection for Inductive Loads DC Power Supply DC Power Supply 0V V+ OUTPUT MODULE 0V V+ OUTPUT MODULE DCL1 DCL1 DCCOM1 Output DCCOM1 Switching Output INDUCTIVE Device Switching LOAD INDUCTIVE Device DCOUT1 LOAD DCOUT1 a) Output Energized b) Output De-energized 5-6 Block I/O Manual GIDDINGS & LEWIS Block 24V DC 8 In/8 Out Module 5.3 Theory of Operation 5.3.1 Outputs Each output point is a solid state switch rated at .5 A. It turns on or off according to the logic state sent to it by the CPU. If the CPU sends it a logic 1, the switch closes and the device is powered. If the CPU sends a logic 0, the switch opens and power to the device is cut off. The CPU updates the logic state for each switch every time it scans the program. The logic side of the switch is optically isolated from the field side. An LED gives the logic state of each switch. If you need to know whether voltage is actually present at the field side, use a voltmeter on the terminal screws. The group of outputs has a .1 ohm series sensing resistor to protect against current overload in case the outputs are shorted to ground. When a short circuit condition is sensed, all outputs are pulsed on for approximately 130 microseconds every 100 milliseconds. Normal operation resumes after the short is removed. In addition, each output is protected with internal clamping diodes. Without clamping, high voltage transients (kickback) from inductive loads might damage the module. 5.3.2 Inputs Each input is guaranteed "on" at 15 to 30 VDC and guaranteed "off" at 0 to 5 VDC; polarity doesn't matter. Its on/off state is converted to a corresponding logic 1 or 0. This logic state is transmitted through the communication interface to the CPU module, where the processor uses it as data in the ladder program. The logic side of the input is optically isolated from the field side. An LED in the upper section of the module indicates the logic state of each input. The group of inputs is represented by a horizontal row of LEDs. If you need to know whether voltage is present at the field side, use a voltmeter on the terminal screws. The shaded blocks in Figure 5-7 show the limits specified by the IEC. The lines show the maximum and minimum V/I of the inputs in this module. The voltage/current curve in this graph shows that the input module is well within the IEC Type 1 limits. GIDDINGS & LEWIS Block I/O Manual 5-7 Block 24V DC 8 In/8 Out Module Figure 5-7 Input Characteristics Compared to IEC Standards U in Volts MIN MAX UH MAX 30 "ON" REGION 25 U NOM 24 20 UH MIN 15 (UT ) MAX TRANSITION REGION 10 UL MAX 5 (UT ) MIN 0 "OFF" REGION I in -5 mAMPS .5 2 4 10 6 8 12 14 15 I IT IH MAX MIN MIN INPUT CURRENT 5-8 Block I/O Manual GIDDINGS & LEWIS INPUT VOLTAGE Block 24V DC 8 In/8 Out Module IMPORTANT Switching devices can sometimes have a leakage current that ex- ceeds the IT (current allowed when off) of an input module. In or- min der to use such a device, an impedance (typically, a resistor) needs to be used in parallel with the input. For example, some of the newer proximity switches use two wires in- stead of three. The third wire was used for a power or ground line. Without the third wire, the switch is easier to install. However, it re- quires more leakage current in the off state to power its internal cir- cuitry. As a conservative estimate, use the following formula to calculate an external resistance value. It keeps the input voltage at or below 2.4V when the switching device is in the "off" state. 2.4V -- --- -- --- --- --- -- --- --- --- --- -- --- --- --- --- -- --- --- --- --- -- -- - ≥R Switch Leakage – 0.75mA If the switch leakage specification is ≤ 1.7 mA, then: 2.4V - - - --- --- --- -- --- --- --- --- -- --- - ≥ 2.5KΩ 1.7 – 0.75mA Use a resistor less than or equal to 2.5 KΩ. Be sure that the wattage is adequate for the resistor when the switching device is in the "on" state remembering that: 2 V ON P = --- --- --- - R GIDDINGS & LEWIS Block I/O Manual 5-9 Block 24V DC 8 In/8 Out Module 5.4 Specification Table Characteristic Block 24V DC module (8 In/8Out) specifications Function Monitors on/off states from eight DC voltage inputs and sources an external DC supply to eight loads Part number M. 1017.3090 (old # 503-25906-01) Field side connector Two 18-pin connectors, screw terminals Protection of logic circuits Optical isolation between the logic and field sides, tran- sient suppression for the 24V external supply Logic side LEDs, module status Data In LED Data Out LED Configured LED Power LED Logic side LEDs, input status A yellow LED for each input Logic side LEDs, output status A yellow LED for each output Logic side LED, short circuit status A red LED lights to indicate a short circuit condition Module power requirements 100 mA from an external 24V DC supply (20 to 30V DC range) NOTE: 2.5A, 250 microsecond inrush at power on CE Marked Conforms to Directives 73/23/EEC, 89/336/EEC, 92/31/ EEC, 93/68/EEC by conforming to the following stan- dards: EN 50081-2:1993 EMC Generic Industrial Emissions EN 50082-2:1995 EMC Generic Industrial Immunity EN 61131-2:1994/A11:1996 Low voltage directive requirements for programmable controllers Operates with emissions below EN55011/ CISPR 11 Class A limits Immune to: Electrostatic discharge (4K V contact mode, 8K V air discharge) per EN61000-4-2 RF electromagnetic fields per EN61000-4-3, ENV 50141, and ENV50204 Electrical fast transients per EN61000-4-4 Magnetic fields per EN61000-4-8 Refer to the EMC Guidelines for more information. UL and C/UL Listed File No. E126417 NRAQ Programmable Controllers Operating temperature range 7° C to 55° C (45° F to 131° F) Storage temperature range -40° C to 85° C (-40° F to 185° F) Humidity 5 to 95%, non-condensing 5-10 Block I/O Manual GIDDINGS & LEWIS Block 24V DC 8 In/8 Out Module Physical size 4.05" wide x 4.825" high x 3" deep 102.9 mm x 122.6 mm x 76.2 mm UL Listing and CE Marking File No. E126417 NRAQ Programmable Controllers Input Section Input signals Nominal 24 VDC on, 0 VDC off, conforming to IEC Type 1 inputs per IEC 1131-2 UH Max (max. allowed voltage) 30 VDC IH Max (max. current @ 30 VDC) 7.5 mA UL Min Polarity independent Guaranteed on 15 VDC IH Min (min. current @ UH Min) 2.8 mA Guaranteed off 5 VDC IT Min (current allowed when off) .75 mA Time delay on 1 ms max. Time delay off 1 ms max. Output Section DC source requirements Nominal 24V DC; range 20 to 30V DC Output group One group of eight solid-state switches. The group uses an external DC supply. It must be referenced to SPG. Short circuit protection for the group Pulses output for about 130 µsec every 100 msec until short is removed Maximum current per group 4 A of continuous current for the group; each switch is rated at .5 A continuous Switch characteristics Solid-state switches Time delay on for resistive loads 50 µsec max Time delay off for resistive loads 50 µsec max Leakage current in off state 0.5 mA max Switch voltage, maximum ON 1 VDC max Surge current, maximum 25 A for about 130 µsec every 100 msec Response to scan loss All outputs are reset to the OFF state Vibration (per IEC 68-2-6) 10-57 Hz (constant amplitude .15 mm) 57 - 2000 Hz (acceleration 2 g) Shock (per IEC 68-2-27) Four shocks per axis (15g/11 msec) GIDDINGS & LEWIS Block I/O Manual 5-11 Block 24V DC 8 In/8 Out Module NOTES 5-12 Block I/O Manual GIDDINGS & LEWIS Block Output 120V AC Module (8 points) 6 Block Output 120V AC Module (8 points) 6.1 Introduction The 120V AC block output module switches voltage for eight individual loads from one or two AC power sources. Each external AC source is nominally 115VAC, but can be between 48 and 138 volts. 8 LEDs in the lower section of the module indicate the logic state that drives each output. Another LED labeled SC turns on if the AC power is not connected. Figure 6-1. Block Output 120V AC Source Module (8 points) Communications Receive/Transmit IN OUT CONF PWR Communication/Status LEDs ® GIDDINGS & LEWIS Short Circuit/Open Fuse Output Status LEDs OUTPUT 120V AC Cover (shown open) Screw Terminal Connector GIDDINGS & LEWIS Block I/O Manual 6-1 Block Output 120V AC Module (8 points) 6.2 Connections A screw terminal is provided for each output and for power connections. The outputs are optically isolated and separated into two groups of four. The external devices in each group must use the same power source. The outputs must not be paralleled or tied together. The power to operate the module is brought in through pins 12 and 23, +24 volt and 24 volt COM, repectively. Pin 24 Chassis GND need not be connected if the block is DIN rail mounted. Figure 6-2. Screw Terminal Connections 12 4 6 3 5 7 8 910 11 12 13 15 16 17 18 22 24 14 19 23 20 21 + 24 V Chassis 24V COM GND Fuse Relay Relay Relay Relay Fuse Relay Relay Relay 120 VAC Relay Group 2 Group 1 ACIN1-ACCOM1 ACIN2-ACCOM2 NOTE To conform to CE requirements for a positive earth connection, con- nect a 6 inch (or less) #14 AWG (2 mm wire) from the chassis pin to earth. 6-2 Block I/O Manual GIDDINGS & LEWIS ACIN 1 ACIN 2 ACC0M 1 ACC0M 2 ACOUT 1 ACOUT 2 ACOUT 3 ACOUT 4 ACOUT 5 ACOUT 6 ACOUT 7 ACOUT 8 Block Output 120V AC Module (8 points) 6.2.1 Fusing External fuses are required (see fusing recommedations) and each of the two AC inputs should be fused separately unless current requirements are less than 3 amps total. 6.2.1.1 Fuse Monitor If AC power is disrupted to the unit, a short circuit/ blown fuse LED indicator will be lit and a software monitoring bit will be enabled in the block I/O data message. For the fuse monitor to work correctly when only the first block of 4 outputs is used, jumper ACIN1 to ACIN2 and ACCOM1 to ACCOM2. GIDDINGS & LEWIS Block I/O Manual 6-3 Block Output 120V AC Module (8 points) 6.2.2 Communications Connections There are two 5-pin communications connectors and four logic LEDs on the top of the block I/O module as shown in Figure 6-3. Figure 6-3. Pinouts for Communication Connectors In (from CPU) Out (to next block I/O module) Pin # 5 4 3 2 1 Pin # 5 4 3 2 1 Communications Receive/Transmit IN OUT CONF PWR ® GIDDINGS & LEWIS 6.2.2.1 LEDs LED Color State Definition DATA IN Yellow FAINT Data being passed through the block module BRIGHT No activity through the block module or OFF DATA Yellow FAINT Data is being passed through the OUT block module BRIGHT No activity through the block module or OFF CONFG Green ON Communication established with this block I/O module OFF Communication not established PWR Green ON Internal +5V logic power supply OK OFF No external 24V applied or internal 5V logic supply not OK 6-4 Block I/O Manual GIDDINGS & LEWIS Driver - (twisted pair output) Driver + (twisted pair output) Shield Receiver - (twisted pair input) Receiver + (twisted pair input) Receiver - (twisted pair input) Receiver + (twisted pair input) Shield Driver - (twisted pair output) Driver + (twisted pair output) Block Output 120V AC Module (8 points) 6.2.3 Protecting from an Inductive Load Arc suppression is not required for a non-inductive load or for an inductive load switched only by the Output 120V AC module. 6.3 Theory of Operation Each output point is a solid state switch rated at .75A continuous for the 8 point module. It turns on or off according to the logic state sent to it by the CPU. If the CPU sends it a logic 1, the switch closes and the load is powered. If the CPU sends a logic 0, the switch opens and power to the load is removed. The CPU updates the logic state for each switch every time it scans the program. The logic side of the switch is optically isolated from the field side. An LED gives the logic state of each output. If you need to know whether voltage is actually on at the field side, use a voltmeter on the terminal screws. The output switch is turned on near the zero voltage crossing of the AC power source and is turned off at zero current. Each group requires an external fuse in series with the source to protect against current overload in case the outputs are shorted to ground. GIDDINGS & LEWIS Block I/O Manual 6-5 Block Output 120V AC Module (8 points) 6.4 Specification Table Characteristic BlockOutput 120V AC module (8 Point) Function Switches an external AC source to 8 loads Part number M.1300.4948 AC source requirements Nominal 115 VAC, range 48 to 138 VAC Field side connector Two 12-pin connectors, screw terminals Protection of logic circuits Optical isolation between the logic and field side; Transient protection on outputs. Arrangement of outputs Two groups of 4 solid-state switches. Each group can use its own AC source, or one source can be daisy-chained. UL 508 spacing Fuse per group of 4 Fast-acting, UL rated 3A Maximum current per group 2A of continuous current for the group; 4 points each switch is rated at .75 A continuous Indicator lights, output circuits An LED for each output Indicator light, module A DIAG LED turns OFF when the module passes its diagnos- tic tests at power-on. Indicator light, fuses A logic side LED lights to indicate a condition when power to a group is missing or has an open fuse. Switch characteristics Solid-state switches. Switch voltage, maximum ON 1V AC @ .75A RMS Surge current, maximum 20 A for 2 cycles, every 2 seconds; fuse blows if this is exceeded. Frequency 50 / 60 Hz. ± 5% Time delay on, maximum 1/2 cycle (turns on at zero voltage) Time delay off, maximum 1/2 cycle (turns off at zero voltage) Minimum load current 50 mA Leakage current in OFF state, maxi- 4 mA @ 120 VAC mum Logic side LEDs, module status Data In LED Data Out LED Configured LED Power LED Logic side LEDs, input circuits A yellow LED for each input 6-6 Block I/O Manual GIDDINGS & LEWIS Block Output 120V AC Module (8 points) Module power requirements 65 mA from an external 24V DC supply (20 to 30V DC range) NOTE: 2.5A, 250 microsecond inrush at power on CE Marked Conforms to Directives 73/23/EEC, 89/336/EEC, 92/31/EEC, 93/68/EEC by conforming to the following standards: EN 50081-2:1993 EMC Generic Industrial Emissions EN 50082-2:1995 EMC Generic Industrial Immunity EN 61131-2:1994/A11:1996 Low voltage directive require- ments for programmable controllers Operates with emissions below EN55011/ CISPR 11 Class A limits Immune to: Electrostatic discharge (4K V contact mode, 8K V air dis- charge) per EN61000-4-2 RF electromagnetic fields per EN61000-4-3, ENV 50141, and ENV50204 Electrical fast transients per EN61000-4-4 Magnetic fields per EN61000-4-8 Refer to the EMC Guidelines for more information. UL and C/UL Listed File No. E126417 NRAQ Programmable Controllers Operating temperature range 7° C to 55° C (45° F to 131° F) * Storage temperature range -40° C to 85° C (-40° F to 185° F) Humidity 5 to 95%, non-condensing Physical size 4.05" wide x 4.825" high x 3" deep 102.9 mm x 122.6 mm x 76.2 mm Vibration (per IEC 68-2-6) 10-57 Hz (constant amplitude .15 mm) 57 - 2000 Hz (acceleration 2 g) Shock (per IEC 68-2-27) Four shocks per axis (15g/11 msec) GIDDINGS & LEWIS Block I/O Manual 6-7 Block Output 120V AC Module (8 points) NOTES 6-8 Block I/O Manual GIDDINGS & LEWIS Block Relay Module (8 points) 7 Block Relay Module (8 points) 7.1 Introduction The relay output module can switch eight relay contacts. Four relays are normally open(NO)/normally closed(NC) form C type and four are normally open (NO) form A type. Eight LEDs in the upper section of the module indicate the logic state that drives each relay. Figure 7-1 Block Relay Module (8 Point) Communications Receive/Transmit IN OUT CONF PWR Communication/Status LEDs ® GIDDINGS & LEWIS Output Status LEDs BLOCK RELAY Cover (shown open) Screw Terminal Connector GIDDINGS & LEWIS Block I/O Manual 7-1 Block Relay Module (8 points) 7.2 Connections A screw terminal connection is provided for each side of the contact. The form C type has three connections; normally open (NO), normally closed (NC), and the common terminal (CT). Only two of the connections can be wired at any time. The common terminal connection must be wired with either the normally open or the normally closed connection depending on the application. The form A type has two connections; one for each side of the contact. Figure 7-2 Screw Terminal Connector Assignments 1 2 3 4 5 6 7 8 9 10 11 12 13 14 15 16 17 18 19 20 21 22 23 24 + 24 V NO 1 NO 1 NO 2 NO 3 NO 2 CT 3 NC 3 CT 4 NC 4 NO 4 Chassis NO 5 NO 6 CT 7 24 COM NO 5 NO 6 NO 7 NC 7 CT 8 NO 8 GND NC 8 NOTE To conform to CE requirements for a positive earth connection, con- nect a 6 inch (or less) #14 AWG (2 mm wire) from the chassis pin to earth. 7-2 Block I/O Manual GIDDINGS & LEWIS Block Relay Module (8 points) 7.2.1 Normally Open Contact Form C Type If the normally open contact of the form C type is required for the application, wire as shown in Figure 7-3 Figure 7-3 Connections for Form C Normally Open Relay Module Power Supply CT3 AC or DC 5 6 NO 3 Load Common 7 NC 3 SPG 7.2.2 Normally Closed Contact Form C Type If the normally closed contact of the form C type is required for the application, wire as shown in Figure 7-4. Figure 7-4 Connections for Form C Normally Closed Relay Module 5 Power Supply CT3 AC or DC 7 NC 3 Load Common SPG GIDDINGS & LEWIS Block I/O Manual 7-3 Block Relay Module (8 points) 7.2.3 Normally Open Contact Form A Type To wire the normally open contact of form A, refer to Figure 7-5. Figure 7-5 Connections for Form A Normally Open Relay Module Power Supply 1 NO 1 AC or DC 2 NO 1 Load Common SPG 7-4 Block I/O Manual GIDDINGS & LEWIS Block Relay Module (8 points) 7.2.4 Contact Noise Suppression All inductive loads should be noise suppressed. They should include motors, relay coils, solenoids etc. Resistive loads need not be suppressed such as lamps, heating elements etc. The suppression will reduce the system electrical noise and contribute to system longevity and reliability. DC suppression is usually a diode or zener across the coil as shown in Figure 7-6. The diode will increase the time for the relay to de- energize. If this is a problem a zener or similar device may be used. Figure 7-6 DC Suppression Example ON/OFF DC + Inductive device Diode 1N4002 24V DC (relay coil, solenoid, (example) motor etc..) DC AC suppression is usually done with an RC network across the inductive device. Examples of AC inductive suppression are shown in Figure 7-7. Figure 7-7 AC Suppression Example ON/OFF AC - HOT 220 1W Resistor Inductive device 120V AC .22 to 1.0uF (relay coil, solenoid, 200V AC motor etc..) Capacitor AC - COM GIDDINGS & LEWIS Block I/O Manual 7-5 Block Relay Module (8 points) 7.2.5 Communications Connections There are two 5-pin communications connectors and four logic LEDs on the top of the block I/O module as shown in Figure 7-8. Figure 7-8 Pinouts for Communication Connectors In (from CPU) Out (to next block I/O module) Pin # 5 4 3 2 1 Pin # 5 4 3 2 1 Communications Receive/Transmit IN OUT CONF PWR ® GIDDINGS & LEWIS 7.2.5.1 LEDs LED Color State Definition DATA IN Yellow FAINT Data being passed through the block module BRIGHT No activity through the block module or OFF DATA Yellow FAINT Data is being passed through the block OUT module BRIGHT No activity through the block module or OFF CONFG Green ON Communication established with this block I/O module OFF Communication not established PWR Green ON Internal +5V logic power supply OK OFF No external 24V applied or internal 5V logic supply not OK 7-6 Block I/O Manual GIDDINGS & LEWIS Driver - (twisted pair output) Driver + (twisted pair output) Shield Receiver - (twisted pair input) Receiver + (twisted pair input) Receiver - (twisted pair input) Receiver + (twisted pair input) Shield Driver - (twisted pair output) Driver + (twisted pair output) Block Relay Module (8 points) 7.3 Theory of Operation A relay is composed of a coil and a set of contacts. When current is passed through the coil, the relay is energized. When no current flows through the coil, the relay is de-energized. The contacts close or open depending on the state of the coil. When the contacts are closed, current can pass through them. When the contacts are open, no current passes. There are three configurations for contacts referred to as form A, B and C as illustrated in Figure 7-9. The relay output module has form A and form C available. Figure 7-9 Relay Forms A, B, and C Normally Open Normally Closed Normally Open/Normally Closed Form A Form C Form B Normally Normally Normally open open closed Coil Coil contact contact contact Common Coil Normally closed contact A relay is energized or de-energized according to the logic state sent to it by the CPU. If the CPU sends a logic 1, the relay is energized. If the CPU sends a logic 0, the relay is de-energized. The logic state for each relay is updated every time the CPU scans the ladder program. The names of the two types of contacts, normally open and normally closed, reflect the state of the contacts when the coil is de-energized. For example, a normally open contact will not pass current when the coil is de-energized. If the coil is energized, the contacts close and current will pass. The normally closed contact will pass current when the coil is de-energized. If the coil is energized the contacts open and no current will pass. These states are summarized in Table 6-1 GIDDINGS & LEWIS Block I/O Manual 7-7 Block Relay Module (8 points) Table 6-1 Summary of NO and NC Relays Normally Open Normally Closed contacts closed/current flow contacts open/no current flow Energized (LED on) contacts open/no current flow contacts closed/current flow De-energized (LED off) The LED for each output reflects the state of the coil. The LED is on when the coil is energized and off when the coil is de-energized. 7-8 Block I/O Manual GIDDINGS & LEWIS Block Relay Module (8 points) 7.4 Specification Table Characteristic Output relay (8) module specification Function Switches eight relay contacts Part number M.1300.4981 Field side connector Two 12 pin connectors, screw terminals Output channels 4 NO, 4 NO/NC Relay characteristics Four form C (NO/NC) Contact types Four form A (NO) Maximum switching voltage 150 VAC resistive load; 150 VDC resistive load Minimum switching current 100 mA Maximum switching power (DC) 200 watts @ 4 Amps maximum Maximum switching current (AC) 0-120 VAC @ 4 Amps maximum Initial contact resistance 100 mΩ Turn on time (resistive load) 6 msec typical Turn off time (resistive load) 2.5 msec typical Expected life, electrical 5 10 operations minimum Expected life, mechanical 7 10 operations minimum Breakdown voltage between contacts 1000 V rms Logic side LEDs, module status Data In LED Data Out LED Configured LED Power LED Logic side LEDs, input circuits A yellow LED for each input Module power requirements 120 mA from an external 24V DC supply (20 to 30V DC range) NOTE: 2.5A, 250 microsecond inrush at power on EMC Compliant Emissions Operates with emissions below EN55011/ CISPR 11 Class A limits Noise immunity Immune to: Electrostatic discharge (4K V contact mode, 8KV air dis- charge) per NEC 1000-4-2 RF electromagnetic fields per IEC 1000-4-3 Electrical fast transients per IEC 1000-4-4 on incoming power lines CE Marked (Pending) Refer to the EMC Guidelines for more information. GIDDINGS & LEWIS Block I/O Manual 7-9 Block Relay Module (8 points) UL and C/UL Listed File No. E126417 NRAQ Programmable Controllers Breakdown voltage between 4000 V rms contacts and coil Maximum switching frequency 20 energize/de-energize cycles/min. (to satisfy expected life ratings) Indicator light, module A logic side LED for each relay turns on when the logic side energizes the relay. Isolation Electromechanical relay provides protection between logic and field side 24 Volts power requirements 205 mA max Operating temperature range 7° C to 55° C (45° F to 131° F) * Storage temperature range -40° C to 85° C (-40° F to 185° F) Humidity 5 to 95%, non-condensing Physical size 4.05" wide x 4.825" high x 3" deep 102.9 mm x 122.6 mm x 76.2 mm Vibration (per IEC 68-2-6) 10-57 Hz (constant amplitude .15 mm) 57 - 2000 Hz (acceleration 2 g) Shock (per IEC 68-2-27) Four shocks per axis (15g/11 msec) * To conform to temperature specifications, the unit must be mounted vertically. 7-10 Block I/O Manual GIDDINGS & LEWIS Block Input 120V AC Module (8 points) 8 Block Input 120V AC Module (8 points) 8.1 Introduction The input 120V AC module converts AC signals from 8 devices into logic levels that the CPU can use. Each signal is converted into a corresponding logic 1 or 0 which is transmitted through the system bus to the CPU module. An "on" signal is nominally 120 VAC, but can be any level between 79 and 132 volts. An "off" signal is any level below 20 VAC. The wiring configurations may be sink or source. 8 LEDs in the upper section of the module indicate the logic state of each input. The DIAG LED goes on briefly while the diagnostic tests are running. Figure 8-1 Block Input 120V AC Module (8 Point) Communications Receive/Transmit IN OUT CONF PWR Communication/Status LEDs ® GIDDINGS & LEWIS Output Status LEDs INPUT 120V AC Cover (shown open) Screw Terminal Connector GIDDINGS & LEWIS Block I/O Manual 8-1 Block Input 120V AC Module (8 points) 8.2 Connections A screw terninal is provided for each input and for power connections. The inputs are optically isolated and separated into two groups of four. The external devices in each group must use the same power source, and be wired in the same configuration "sink source". If an external device supplies current to the module it is a source, if it draws from the module it is a sink. The external pin connections are shown in Figure 8-2. The power to operate the module are brought in through pins 12 and 23, +24 volt and 24 volt ground, respectively. Pin 24 Chassis ground need not be connected if block is DIN rail mounted (see Note below). Figure 8-2 Screw Terminal Connection Assignments 1 2 3 4 5 6 7 8 9 10 11 12 13 14 15 16 17 18 19 20 21 22 23 24 ACSS2 ACIN5 ACSSI ACIN 1 ACIN 3 AC IN 4 ACIN6 ACIN2 ACIN7 ACIN8 + 24 V Chassis 24 COM GND NOTE To conform to CE requirements for a positive earth connection, con- nect a 6 inch (or less) #14 AWG (2 mm wire) from the chassis pin to earth. 8-2 Block I/O Manual GIDDINGS & LEWIS Block Input 120V AC Module (8 points) The power connections ACSSI and ACSS2 are connected to AC common if devices in the group are sources and to 120 VAC if the external devices are sink- ing. Figure 8-3 shows the first group of four being used as sinking external devices and the second group as sources. Figure 8-3 Power Connections 12 3 4 5 6 7 8 9 10 11 12 13 14 15 16 17 18 19 20 21 22 24 23 + 24 V Chassis 24 COM GND AC HOT AC COM SINK AC COM AC HOT SOURCE GIDDINGS & LEWIS Block I/O Manual 8-3 ACSS 1 ACIN 1 ACIN 2 ACIN 3 ACIN 4 ACSS 2 ACIN 5 ACIN 6 ACIN 7 ACIN 8 Block Input 120V AC Module (8 points) 8.2.1 Communications Connections There are two 5-pin communications connectors and four logic LEDs on the top of the block I/O module as shown in Figure 8-4. Figure 8-4 Pinouts for Communication Connectors In (from CPU) Out (to next block I/O module) Pin # 5 4 3 2 1 Pin # 5 4 3 2 1 Communications Receive/Transmit IN OUT CONF PWR ® GIDDINGS & LEWIS 8.2.1.1 LEDs LED Color State Definition DATA IN Yellow FAINT Data being passed through the block module BRIGHT No activity through the block module or OFF DATA Yellow FAINT Data is being passed through the block OUT module BRIGHT No activity through the block module or OFF CONFG Green ON Communication established with this block I/O module OFF Communication not established PWR Green ON Internal +5V logic power supply OK OFF No external 24V applied or internal 5V logic supply not OK 8-4 Block I/O Manual GIDDINGS & LEWIS Driver - (twisted pair output) Driver + (twisted pair output) Shield Receiver - (twisted pair input) Receiver + (twisted pair input) Receiver - (twisted pair input) Receiver + (twisted pair input) Shield Driver - (twisted pair output) Driver + (twisted pair output) Block Input 120V AC Module (8 points) 8.3 Theory of Operation Each input is guaranteed "on" between 79 and 132 VAC and guaranteed "off" between 0 and 20 VAC. Its on/off state is converted to a corresponding logic 1 or 0. This logic state is transmitted through the system bus to the CPU module, where the processor uses it as data in the ladder program. The logic side of the input is optically isolated from the field side. An LED in the upper section of the module indicates the logic state of each input. The four LEDs representing each group are in a horizontal row. If you need to know the voltage at the field side, use a voltmeter on the terminal screws. Figure 8-5 shows the input characteristics of the module compared to IEC standards. The shaded blocks show the limits specified by the IEC, and the lines show the maximum and minimum V/I of the inputs in this module. This voltage/ current curve in this graph shows that the AC input module is well within the IEC Type 1 limits. Figure 8-5 Input Characteristics Compared to IEC Standards U in Volts MIN MAX UH MAX 132 125 U NOM 120 "ON" REGION 100 UH MIN 79 (UT ) 75 MAX TRANSITION REGION 50 25 UL MAX 20 (UT ) MIN "OFF" REGION I in 0 mAMPS 1 4 2 6 8 10 12 14 15 I IH IT MAX MIN MIN INPUT CURRENT GIDDINGS & LEWIS Block I/O Manual 8-5 INPUT VOLTAGE Block Input 120V AC Module (8 points) IMPORTANT Switching devices can sometimes have a leakage current that exceeds the IT (current allowed when off) of an input module. In order to min use such a device, an impedance (typically, a resistor) needs to be used in parallel with the input. For example, some of the newer proximity switches use two wires in- stead of three. The third wire was used for a power or ground line. Without the third wire, the switch is easier to install. However, it re- quires more leakage current in the off state to power its internal cir- cuitry. As a conservative estimate, use the following formula to calculate an external resistance value. It keeps the input voltage at or below 12V when the switching device is in the "off" state. 12V --- --- --- -- --- --- --- --- -- --- --- --- --- -- --- --- --- -- --- -- - ≥R Switch Leakage – 1mA If the switch leakage specification ≤ 1.7 mA, then: 12V -- --- -- --- --- --- --- -- --- - ≥ 17.1KΩ 1.7 – 1mA Use a 16 K Ω, 2W or any lower resistance and higher wattage resistor. Be sure that the wattage is adequate for the resistor remembering that: 2 V rms P = --- --- --- - - R It would be acceptable to use a .15 µF (or greater) capacitor rated for 120V AC. The advantage of the capacitor is minimal power dissipa- tion. 1 Xc = -- --- --- --- - - 2πfC 8-6 Block I/O Manual GIDDINGS & LEWIS Block Input 120V AC Module (8 points) 8.4 Specification Table Characteristic Block Input 120V AC Module Function Monitors on/off states from up to 8 AC voltage inputs Part number M.1017.4298 (old # 503-26897-00) Field side connector Two 12 pin connectors connectors, screw terminals Input signals Nominal 120 VAC on, 0 VAC off, conforming to IEC Type 1 inputs per IEC 1131-2 (two groups of four inputs) UH Max (max. allowed voltage) 132 VAC IH Max (max. current @ 132 VAC) 8.7 mA UL Min 0 V Guaranteed on 79 VAC IH Min (min. current @ UH Min) 4.6 mA Guaranteed off 20 VAC IT Min (current allowed when off) 1 mA Frequency 50/60 Hz ± 5% Time delay on, max. 14 ms Time delay off, max. 20 ms Protection of logic circuits Optical isolation between the logic and field sides, 1780 VAC Field side power dissipation, worst case 9.2 W Module power requirements 45 mA from an external 24V DC supply (20 to 30V DC range) NOTE: 2.5A, 250 microsecond inrush at power on GIDDINGS & LEWIS Block I/O Manual 8-7 Block Input 120V AC Module (8 points) CE Marked Conforms to Directives 73/23/EEC, 89/336/EEC, 92/31/ EEC, 93/68/EEC by conforming to the following stan- dards: EN 50081-2:1993 EMC Generic Industrial Emissions EN 50082-2:1995 EMC Generic Industrial Immunity EN 61131-2:1994/A11:1996 Low voltage directive requirements for programmable controllers Operates with emissions below EN55011/ CISPR 11 Class A limits Immune to: Electrostatic discharge (4K V contact mode, 8K V air discharge) per EN61000-4-2 RF electromagnetic fields per EN61000-4-3, ENV 50141, and ENV50204 Electrical fast transients per EN61000-4-4 Magnetic fields per EN61000-4-8 Refer to the EMC Guidelines for more information. UL and C/UL Listed File No. E126417 NRAQ Programmable Controllers Operating temperature range 7° C to 55° C (45° F to 131° F) * Storage temperature range -40° C to 85° C (-40° F to 185° F) Humidity 5 to 95%, non-condensing Physical size 4.05" wide x 4.825" high x 3" deep 102.9 mm x 122.6 mm x 76.2 mm Vibration (per IEC 68-2-6) 10-57 Hz (constant amplitude .15 mm) 57 - 2000 Hz (acceleration 2 g) Shock (per IEC 68-2-27) Four shocks per axis (15g/11 msec) 8-8 Block I/O Manual GIDDINGS & LEWIS Block Input Resolver Module (6 channel) 9 Block Input Resolver Module (6 channel) 9.1 Introduction The block input resolver module can interface to 6 independent resolvers (or equivalent transducers). Feedback information from the resolvers is used to update the on-board memory. The position of each resolver can be read at any time by the PiC. The module generates two sine waves (RPO and QPO) 90° out of phase with each other and each channel receives a signal whose phase represents the angular position of the resolver. The resolution of the angular position is 4000 counts per revolution or 0.09 degrees. Figure 9-1 Block Input Resolver Module (6 Channel) Communications Receive/Transmit IN OUT CONF PWR Communication/Status LEDs ® GIDDINGS & LEWIS Output Status LEDs INPUT RESOLVER Cover (shown open) Screw Terminal Connector GIDDINGS & LEWIS Block I/O Manual 9-1 Block Input Resolver Module (6 channel) 9.2 Connections Figure Figure 9-2 shows the screw terminal connections for the block input resolver module. Figure 9-2 Connections for the Block Input Resolver Terminals 12 3 4 5 6 7 8 9 10 11 12 13 14 15 16 17 18 19 20 21 22 23 24 RPO RPO GND SHIELD FDBK1+ FDBK1- SHIELD FDBK2+ FDBK2- SHIELD FDBK3+ FDBK3- 24V QPO QPO GND FDBK4+ FDBK4- SHIELD FDBK5+ FDBK5- SHIELD FDBK6+ FDBK6- 0V Chassis To connect six resolvers to the block resolver module, a user-supplied external terminal block must be used. Each resolver has three signal pairs. The signals and where they are connected are listed below. Signal pairs to resolver Connection RPO and /shield To terminal block QPO and /shield To terminal block Signal pair from resolver Connection FDBK and /shield To block input resolver module All signals from the resolvers must come to the screw terminal connectors (either on the block resolver module or on the terminal block) through shielded twisted pair wires. These wires must be protected against electrical noise because of the speed and/or voltage levels of the signals transmitted through them. The maximum length of the twisted pair wire from the resolver to the terminal block is 100 feet. 9-2 Block I/O Manual GIDDINGS & LEWIS Block Input Resolver Module (6 channel) The feedback from each resolver is brought back to the appropriate feedback channel connections on the block resolver module. The module has five screw connections for terminating the feedback shields. All are connected inside the module so they are the same point electrically. If all six resolvers are connected, some of the feedback shields will have to be doubled up on the shield connections. The shields from the RPO and QPO signals are terminated on shield screw connections on the terminal block. The shield at the device end of the cable is not connected. Figure 9-3 shows how to wire a terminal block and the first resolver. With the terminal block shown, the RPO, QPO, and outputs from the module are each connected to the terminal block. Each is then jumpered so that there are three signals of each type available for the six resolvers (RPO1, RPO2,... QPO1, QPO2,... , ,... etc.). To connect six resolvers on this terminal block, two connections would be made to the same screw terminal. 18 AWG wire is recommended for these connections. The maximum wire length between the block input resolver module and the terminal block is 6 feet. The feedback signal from the resolver and its shield are wired directly to the module, not the terminal block. GIDDINGS & LEWIS Block I/O Manual 9-3 Block Input Resolver Module (6 channel) Figure 9-3 Connecting Resolver, Terminal Block, and Module Block Input Resolver Module Screw Terminals 12 3 4 5 6 7 8 9 10 11 12 13 14 15 16 17 18 19 20 21 22 23 24 DC Com +24V DC 0V +24V Power Supply To SPG External Terminal Block Make appropriate connections for remaining resolvers. Resolver 4 Resolver 5 Resolver 6 Resolver 2 Resolver 3 Color Key R1 Red/White R2 Yellow/White S1 Red S3 Black Resolver 1 S2 Yellow S4 Blue NOTE: If the count direction is incorrect after making the connections (i.e. cloc- wise rotation is counting down when it should be counting up), swap S1 with S3 or S2 with S4. 9-4 Block I/O Manual GIDDINGS & LEWIS RPO (R1) FDBK+ QPO (R2) FDBK- RPO GND (S1) RPO QPO GND (S3) RPO GND SHIELD (S2) QPO FDBK4+ (S4) QPO GND FDBK1+ FDBK4- FDBK1- SHIELD SHIELD FDBK5+ FDBK2+ FDBK5- FDBK2- SHIELD SHIELD FDBK6+ FDBK3+ FDBK6- FDBK3- Chassis Block Input Resolver Module (6 channel) 9.2.1 Adding an External Potentiometer External digitizing potentiometers can be connected to the block input resolver module. This can produce a total count deviation of 1000 from full clockwise to full counter-clockwise. Count values will be in the approximate range of 2000 to 3000. Count values will vary from module to module (for example, 2137 to 3137). Therefore, a reference to the value in the full clockwise or full counter-clockwise position should be performed. Figure 9-4 illustrates one potentiometer connected to the block input resolver module through the external terminal strip. Figure 9-4 Potentiometer Connected to the Block Input Resolver Block Input Resolver Module Screw Terminals 12 3 4 5 6 7 8 9 10 11 12 13 14 15 16 17 18 19 20 21 22 23 24 DC Com +24V DC +24V 0V Power Supply QPO RPO To SPG External Terminal Block NC Potentiometer Connections CW GIDDINGS & LEWIS Block I/O Manual 9-5 RPO QPO RPO GND QPO GND SHIELD FDBK4+ FDBK1+ FDBK4- FDBK1- SHIELD SHIELD FDBK5+ FDBK2+ FDBK5- FDBK2- SHIELD SHIELD FDBK6+ FDBK3+ FDBK6- FDBK3- Chassis Block Input Resolver Module (6 channel) 9.2.2 Communications Connections There are two 5-pin communications connectors and four logic LEDs on the top of the block I/O module as shown in Figure 9-5. Figure 9-5 Pinouts for Communication Connectors In (from CPU) Out (to next block I/O module) Pin # 5 4 3 2 1 Pin # 5 4 3 2 1 Communications Receive/Transmit IN OUT CONF PWR ® GIDDINGS & LEWIS 9.2.2.1 LEDs LED Color State Definition DATA IN Yellow FAINT Data being passed through the block module BRIGHT No activity through the block module or OFF DATA OUT Yellow FAINT Data is being passed through the block module BRIGHT No activity through the block module or OFF CONFG Green ON Communication established with this block I/O module OFF Communication not established PWR Green ON Internal +5V logic power supply OK OFF No external 24V applied or internal 5V logic supply not OK 9-6 Block I/O Manual GIDDINGS & LEWIS Driver - (twisted pair output) Driver + (twisted pair output) Shield Receiver - (twisted pair input) Receiver + (twisted pair input) Receiver - (twisted pair input) Receiver + (twisted pair input) Shield Driver - (twisted pair output) Driver + (twisted pair output) S2 S4 Block Input Resolver Module (6 channel) 9.3 Resolvers A resolver (see Figure 9-6) is a servo feedback device which provides absolute position over one electrical revolution. It receives RPO (reference phase output) and QPO (quadrature phase output) signals from the interface module. RPO and QPO signals are sine waves 90° out of phase with each other. They energize two stator coils positioned at 90° to each other. The stator coils induce a sine wave signal called FDBK (feedback) in the rotor coil. The phase of this signal, with respect to RPO, depends on the rotor coil's position. Figure 9-6 Diagram of a Resolver Feedback QPO RPO S1 S3 The recommended resolver has a part number in the specification sheet at the end of this section. Other resolvers may be used if they conform to the interface module specifications. 9.4 Theory of Operation The module sends out two sine wave signals, RPO and QPO. These signals have the same voltage amplitude and frequency but are 90° out of phase. The module then receives a FDBK sine wave signal whose phase is a measure of the angular rotation of the resolver. A phase shift of 360° corresponds to 4,000 counts of resolution, so one count represents 5.4 arc-minutes of rotation of the resolver. The value in the on-board memory represents the current position of the resolver. The on-board memory position is updated every 1.5 msec for each of the 6 resolvers. There is a loss of feedback indicator for each resolver. GIDDINGS & LEWIS Block I/O Manual 9-7 R1 R2 Block Input Resolver Module (6 channel) 9.5 Specification Table Characteristic Block Input Resolver (6 ch) Module Specifications Function Measures the position of a transducer that accepts a 2- phase quadrature excitation, such as a resolver or potenti- ometer Part number M.1017.3138 (old # 503-25986-01) Field side connector 24 pin card edge connector, screw terminals Excitation method 2-phase quadrature for control transformer type of resolver RPO and QPO outputs Frequency 4KHz Output voltage 15 V (5.3V ) P-P RMS Current per output channel, max. 100 mA Resolver transformer ratio .5 to 1.0 Resolution, resolver 4000 Feedback Units (FUs) per electrical revolution Resolution, potentiometer 1000 Feedback Units (FUs) per electrical revolution Accuracy at constant temperature ± 12 arc minutes Accuracy over temperature range ± 5.4 arc minutes /10°F Velocity, max. 15000 electrical RPM (1M FU/Sec.) Cable length, max. 6 ft. from module to terminal block (18 AWG) 100 ft. from terminal block to resolvers (twisted pair) Stored position value range 0-3999 Logic side LEDs, module status Data In LED Data Out LED Configured LED Power LED Module power requirements 200 mA from an external 24V DC supply (20 to 30V DC range) NOTE: 2.5A, 250 microsecond inrush at power on Recommended resolver Giddings & Lewis part number 501-98409-00 Harowe 11BRW 300-F-1/10 Other suggested resolvers Clifton 11BHW-0IE/A004 Kearfott CR410959 9-8 Block I/O Manual GIDDINGS & LEWIS Block Input Resolver Module (6 channel) CE Marked Conforms to Directives 73/23/EEC, 89/336/EEC, 92/31/ EEC, 93/68/EEC by conforming to the following stan- dards: EN 50081-2:1993 EMC Generic Industrial Emissions EN 50082-2:1995 EMC Generic Industrial Immunity EN 61131-2:1994/A11:1996 Low voltage directive requirements for programmable controllers Operates with emissions below EN55011/ CISPR 11 Class A limits Immune to: Electrostatic discharge (4K V contact mode, 8K V air discharge) per EN61000-4-2 RF electromagnetic fields per EN61000-4-3, ENV 50141, and ENV50204 Electrical fast transients per EN61000-4-4 Magnetic fields per EN61000-4-8 Refer to the EMC Guidelines for more information. UL and C/UL Listed File No. E126417 NRAQ Programmable Controllers Operating temperature range 7° C to 55° C (45° F to 131° F) Storage temperature range -40° C to 85° C (-40° F to 185° F) Humidity 5 to 95%, non-condensing Physical size 4.05" wide x 4.825" high x 3" deep 102.9 mm x 122.6 mm x 76.2 mm Vibration (per IEC 68-2-6) 10-57 Hz (constant amplitude .15 mm) 57 - 2000 Hz (acceleration 2 g) Shock (per IEC 68-2-27) Four shocks per axis (15g/11 msec) GIDDINGS & LEWIS Block I/O Manual 9-9 Block Input Resolver Module (6 channel) NOTES 9-10 Block I/O Manual GIDDINGS & LEWIS Block Output Stepper/Input Encoder/ Input 24V DC Module (2/2/2 Channel) 10 Block Output Stepper/Input Encoder/ Input 24V DC Module (2/2/2 Channel) 10.1 Introduction This block I/O module provides the following: Two output stepper channels Two input encoder channels Two 24V DC inputs Figure 10-1 Block Output Stepper/Input Encoder/Input 24V DC Module (2/2/2 Ch) Communications Receive/Transmit IN OUT CONF PWR Communication/Status LEDs ® GIDDINGS & LEWIS INPUT ENCODER OUTPUT STEPPER Output Status LEDs Cover (shown open) Screw Terminal Connector GIDDINGS & LEWIS Block I/O Manual 10-1 Block Output Stepper/Input Encoder/ Input 24V DC Module (2/2/2 10.1.1 Output Stepper Each stepper channel can control one stepper drive. The maximum step rate is one million steps per second. An external power supply (4.5 VDC to 20 VDC) or the internal +5V DC can be used to power each stepper output. Commands and control data are sent to the module, and status and position information are received from the module, via software. 10.1.2 Input Encoder Each encoder channel can interface to one independent quadrature incremental encoder or equivalent device. Information from each encoder is used to update a separate position counter and latch within the module. For each channel, a 24-bit counter is incremented or decremented based on signals it receives from the A, A, B, and B outputs of a quadrature encoder. The counter value can be latched (stored) if the module receives an I or I output signal from the encoder. 10.1.3 Input 24V DC The 24V DC inputs convert DC signals from devices into logic levels that the CPU can use. Each signal is converted into a corresponding logic 1 or 0 which is transmitted through the communication interface to the CPU module. An "on" signal is nominally 24V DC, but can be any level between 15V and 30V. An "off" signal is any level below 5V. The wiring configurations may be sink or source. Two field side LEDs indicate the state of the inputs. 10-2 Block I/O Manual GIDDINGS & LEWIS Block Output Stepper/Input Encoder/ Input 24V DC Module (2/2/2 Channel) 10.2 Connections A screw terminal connector is provided for each connection as shown in Figure 10-2. Use up to 14 AWG for field side wiring. Figure 10-2 Screw Terminal Connector Assignments 1 2 345678 9 10 11 12 13 14 15 16 17 18 19 20 21 22 23 24 25 26 27 28 29 30 31 32 33 34 35 36 10.2.1 Stepper Connections For the stepper outputs, the DC power supply can be provided by any combination of the following: The stepper drive An external DC supply daisy-chained to both outputs Separate external DC supplies for each output The +5V supply available on the block module An external DC supply that powers the output signals should have a wire connected from its 0V (COMMON) terminal directly to the controller’s single point ground. The power disconnect switch should be the same one used for the system. The following connections for one output are illustrated in Figure 10-3. ST1+VIN to the +V terminal of the external power supply or the +5V OUT terminal of the internal power supply ST1 STEP/CW to the step or clockwise input of the drive ST1 DIR/CCW to direction or counterclockwise input of the drive ST1 +VINCOM to the 0V terminal of the external power supply NOTE: When the drive inputs are optically iso- lated, tie the 0V of the external power supply to SPG or to pin 35. SHIELD All shield pins on the module are connected to each other internally and to the chassis screw terminal and the metal strip on the base of the module. GIDDINGS & LEWIS Block I/O Manual 10-3 ST1 STEP/CW ST2 STEP/CW ST1 DIR/CCW ST2 DIR/CCW ST1 +VIN ST2 +VIN +5V OUT +5V OUT ST1 +VINCOM ST2 +VINCOM +5V OUTCOM +5V OUTCOM SHIELD SHIELD +5V OUT +5V OUT ENC1A ENC2A ENC1A ENC2A ENC1B ENC2B ENC1B ENC2B ENC1INDEX ENC2 INDEX ENC1INDEX ENC2 INDEX DC IN1 DC IN 2 0V DC IN SS 24V 0V 24V CHASSIS Block Output Stepper/Input Encoder/ Input 24V DC Module (2/2/2 Figure 10-3 Connections for One Stepper Output Block Module Internal Circuitry CHASSIS (SPG) 1 2 34567 19 20 21 22 23 V+ 0V External SPG DC Supply 1 2 345 67 NOTE: As an alternative to an 19 20 21 22 23 external DC power supply, you can use the +5V available on the block module. See in- sert for wiring. WARNING The +5V OUT internal power supply available at the terminal screws is also used by the module’s logic circuitry. If problems are encoun- tered, use an external power supply instead. 10-4 Block I/O Manual GIDDINGS & LEWIS ST1 sTEP/CW ST1 DIR/CCW ST1 +VIN +5V OUT ST1 +VINCOM +5V OUTCOM ST1 STEP/CW ST1 DIR/CCW SHIELD ST1 +VIN +5V OUT ST1+VINCOM +5VOUTCOM SHIELD Block Output Stepper/Input Encoder/ Input 24V DC Module (2/2/2 Channel) 10.2.2 Connecting the Block Module to Stepper Drives Consult your drive manual regarding the proper connection of an indexer. Four types of drive inputs and the proper connection techniques are shown in Figure 10-4, Figure 10-5, Figure 10-6 and Figure 10-7. When working with opto-coupler drive inputs, be sure the input diode is protected by a current-limiting resistor as stated in the following important note. IMPORTANT There is a limit to the amount of current the input diode of the drive opto-coupler can withstand. If this current is exceeded, the device will be destroyed. The block module is capable of sinking considerably more current than the 15 mA specified. Most drives having opto-coupler inputs have a series current-limit resistor sized properly for a +5V external supply. If the drive being used has an opto-coupler input but does not have a current-limit resistor or if the current-limit resistor is too small, then one will have to be added externally. Consult your drive manual for in- formation regarding this topic. Following the wiring guidelines listed below will increase the reliability of the block module/drive system. 1. Route the wiring from the block module separately from any high current or electrically noisy wiring. 2. Keep the wires connecting the block module to the drive less than 10 feet in length. 3. Shield the wiring from the block module. Tie shields to the block module shield terminal screw and leave the other end of the shield unconnected. GIDDINGS & LEWIS Block I/O Manual 10-5 Block Output Stepper/Input Encoder/ Input 24V DC Module (2/2/2 10.2.2.1 Opto-Coupler Drive Inputs The inputs for this type of drive will be: Step + Step - Direction + Direction - Make the following connections as shown in Figure 10- 4. External Power Block Module Supply Drive ST1 STEP/CW to N/C to Step - ST1 DIR/CCW to N/C to Direction - ST1 +VIN to +V to Step + and Direction + ST1 +VINCOM to 0V to N/C 10-6 Block I/O Manual GIDDINGS & LEWIS Block Output Stepper/Input Encoder/ Input 24V DC Module (2/2/2 Channel) Figure 10-4 Block Module (Stepper) Connections to Opto-Coupler Drive Inputs 1 2 34567 Block Module 19 20 21 22 23 V+ 0V +5V SPG External DC Supply Step+ Step- Dir+ Dir- Drive with opto-coupler inputs 10.2.2.2 Opto-Coupler with Common Source Drive Inputs The inputs for this type of drive will be: Opto power input Step Direction Make the following connections as shown in Figure 10- 5: External Power Block Module Supply Drive ST1 STEP/CW to N/C to Step ST1 DIR/CCW to N/C to Direction ST1 +VIN to +V to Opto power input ST1 +VINCOM to 0V to N/C GIDDINGS & LEWIS Block I/O Manual 10-7 220 ohm ST1 STEP/CW ST1 DIR/CCW 220 ohm ST1 +VIN +5V OUT ST1 +VINCOM +5V OUTCOM SHIELD Block Output Stepper/Input Encoder/ Input 24V DC Module (2/2/2 Figure 10-5 Block Module (Stepper) Connections to Opto-Coupler Drive Inputs 1 2 34567 Block Module 19 20 21 22 23 Shown with common source V+ 0V +15V SPG External DC Supply Opto Step Dir Power Drive with opto-coupler inputs (common source) 10.2.2.3 Single-Ended Drive Inputs The inputs for this type of drive will be: Step Direction Signal ground Make the following connections as shown in Figure 10- 6. Power Block Module Supply Drive ST1 STEP/CW to N/C to Step ST1 STEP/CCW to N/C to Direction ST1 +VIN to +V to N/C ST1 +VINCOM to 0V to Signal ground 10-8 Block I/O Manual GIDDINGS & LEWIS 220 ohm 680 ohm ST1 STEP/CW 680 ohm ST1 DIR/CCW 220 ohm ST1 +VIN +5V OUT ST1 +VIN +5V OUTCOM SHIELD Block Output Stepper/Input Encoder/ Input 24V DC Module (2/2/2 Channel) Figure 10-6 Block Module (Stepper) Connections to Single-Ended Drive Inputs 1 2 34567 Block Module 19 20 21 22 23 V+ 0V +5V SPG External DC Supply Step Dir Signal Ground +5V 1K ohm 1K ohm +5V Drive with single-ended inputs If the pull-up resistors internal to the drive are inadequate, you may need to add external pull-up resistors. Install them as close as possible to the drive. GIDDINGS & LEWIS Block I/O Manual 10-9 ST1 STEP/CW ST1 DIR/CCW ST1 +VIN +5V OUT ST1 +VINCOM +5V OUTCOM SHIELD Block Output Stepper/Input Encoder/ Input 24V DC Module (2/2/2 10.2.2.4 Differential Drive Inputs The inputs for this type of drive will be: Step + Step - Direction + Direction - Signal ground Make the following connections as shown in Figure 10- 7. Power Block Module Supply Drive ST1 STEP/CW to N/C to Step + ST1 DIR/CCW to N/C to Direction + ST1 +VIN to +V to N/C ST1 +VINCOM to 0V to Signal ground 10-10 Block I/O Manual GIDDINGS & LEWIS Block Output Stepper/Input Encoder/ Input 24V DC Module (2/2/2 Channel) Figure 10-7 Block Module (Stepper) Connections to Differential Drive Inputs 1 2 34567 Block Module 19 20 21 22 23 NOTE: If the Step - and Direction - are not biased to one half the external supply by the drive, external voltage dividers will be required. Install the voltage dividers as close to the drive V+ 0V as possible. +5V SPG External DC Supply Signal Step+ Step- Dir+ Dir- Ground +5V +5V +5V +5V + - + - Drive with differential inputs GIDDINGS & LEWIS Block I/O Manual 10-11 ST1 STEP/CW ST1 DIR/CCW ST1 +VIN +5V OUT ST1 +VINCOM +5V OUTCOM SHIELD Block Output Stepper/Input Encoder/ Input 24V DC Module (2/2/2 10.2.3 Block Module Encoder Connections All signals to the encoder inputs of the block module must come to its screw terminal connector through shielded twisted pair wires. These wires must be protected against electrical noise because of the speed and/or voltage levels of the signals transmitted through them. See the discussion on "Preventing electrical noise in data lines" in the Hardware chapter. Each encoder module channel has three signal pairs, each of which has two screw terminal connections. The signal pairs are: encoder input A and A encoder input B and B index input and index In addition the module has screw connections for terminating the shields. All shield pins on the module are connected to each other internally and to the chassis screw terminal and the metal strip on the base of the module. IMPORTANT The power supply to the encoder (or signal source device) must have its common connected to the SPG. Figure 10-8 shows the assignments for all the screw terminal connections on the module. To make the diagram more readable, the shielded twisted pair wires are shown with transparent shields. WARNING The +5V OUT internal power supply available at the ter- minal screws is also used by the module’s logic circuitry. If problems are encountered, use an external power sup- ply instead. 10-12 Block I/O Manual GIDDINGS & LEWIS Index Index B B A A Block Output Stepper/Input Encoder/ Input 24V DC Module (2/2/2 Channel) Figure 10-8 Block Module (Encoder) Connections Encoder 1 0V +V SPG Encoder 1 using block module +5V for power supply 6789 10 11 12 13 14 Block Module Screw Terminals 24 25 26 27 28 29 30 31 32 Encoder 2 using external power supply Encoder Power Supply 4V to 6V DC +V 0V Encoder 2 SPG GIDDINGS & LEWIS Block I/O Manual 10-13 +5V OUTCOM +5V OUTCOM SHIELD SHIELD +5V OUT +5V OUT ENC1A ENC2A ENC1A ENC2A A ENC1B A ENC2B ENC1B B ENC2B B ENC1INDEX Index ENC2 INDEX Index ENC1INDEX ENC2INDEX Block Output Stepper/Input Encoder/ Input 24V DC Module (2/2/2 10.2.3.1 Encoder Drivers Acceptable drivers provided by encoder manufacturers include: Differential voltage drivers 75183 8830 75114 9614 26LS31 NOTE Encoders with differential drivers are required. They provide better noise immunity and capability for the module to detect "loss of feedback." See the section in the Hardware chapter on "Preventing electrical noise in data lines" for a comparison be- tween differential and single-ended interfaces. The three encoder outputs are paired: A and A B and B index and index 10-14 Block I/O Manual GIDDINGS & LEWIS Block Output Stepper/Input Encoder/ Input 24V DC Module (2/2/2 Channel) 10.2.4 Block Module DC Input Connections The external DC supply used to power the input signals should have a wire connected from its 0V (common) terminal directly to the single-point ground used for the system rack. Its power disconnect switch should be the same one used for the system rack. The DC inputs can be set up as sinking or sourcing. The drawing on the left side of Figure 10-9 shows devices "sinking" current through the DC inputs. The HOT terminal of the power supply must be connected to the module at DCInSS. The drawing on the right side of Figure 10-9 shows devices "sourcing" current through the DC inputs. The COMMON terminal of the power supply must be connected to the module at DCInSS. Figure 10-9 Sinking or Sourcing Connections for DC Input 15 16 17 18 15 16 17 18 33 34 35 36 33 34 35 36 Hot Common OR Hot Common +V 0V +V 0V DC DC Power Power Supply Supply Sink Source 10.2.5 Power Connections An external 24V DC supply must be connected to pins 18 and 35 as shown in Figure 10-9. GIDDINGS & LEWIS Block I/O Manual 10-15 DC In1 DC In 2 DC In SS 0V 24V DC In1 DC In 2 DC In SS 0V 24V Block Output Stepper/Input Encoder/ Input 24V DC Module (2/2/2 10.2.6 Communications Connections There are two 5-pin communications connectors and four logic LEDs on the top of the block I/O module as shown in Figure 10-10 below. Figure 10-10 Pinouts for Communication Connectors In (from CPU) Out (to next block I/O module) Pin # 5 4 3 2 1 Pin # 5 4 3 2 1 Communications Receive/Transmit IN OUT CONF PWR ® GIDDINGS & LEWIS 10.2.6.1 LEDs LED Color State Definition DATA IN Yellow FAINT Data being passed through the block module BRIGHT No activity through the block module or OFF DATA Yellow FAINT Data is being passed through the OUT block module BRIGHT No activity through the block module or OFF CONFG Green ON Communication established with this block I/O module OFF Communication not established PWR Green ON Internal +5V logic power supply OK OFF No external 24V applied or internal 5V logic supply not OK 10-16 Block I/O Manual GIDDINGS & LEWIS Driver - (twisted pair output) Driver + (twisted pair output) Shield Receiver - (twisted pair input) Receiver + (twisted pair input) Receiver - (twisted pair input) Receiver + (twisted pair input) Shield Driver - (twisted pair output) Driver + (twisted pair output) Block Output Stepper/Input Encoder/ Input 24V DC Module (2/2/2 Channel) 10.3 Theory of Operation 10.3.1 Stepper Theory of Operation The stepper section of the block module is part of an open loop control system used to position from one to two axes. The diagram in Figure 10-11 illustrates one axis being controlled by the block module. Digital signals from the block module are converted into fixed increments of motion via the stepper drive. This allows the stepper motor to move the load accurately and reliably by following the number of input steps. Figure 10-11 Open Loop Stepper System PiC900 CPU Block Data L Module Stepper Transfer Stepper O Drive Motor A D The block module controls the position, velocity, and acceleration of the stepper motor. The number of pulses generated by the block module provides distance information (steps) and the rate of these pulses provides velocity information (steps/sec). The rate of change of the pulse rate provides acceleration/deceleration information (steps/sec/sec). Commands (acc/dec rates, maximum velocity, reference position, distance, position, and velocity moves) and control data (E-stop, C- stop, start, pause, continue, modes) are sent to the module and status and position information are received from the module via software. Each channel can have up to 500 commands queued up on the module. The step rate programmed by you for a velocity command (or calculated by the block module during acceleration or deceleration) versus the actual rate output from the block module is defined by the following equation: 6 10 × 10 ActualRate = -- --- -- --- --- --- --- - X 6 10 × 10 -- --- --- -- --- --- --- --- -- --- --- --- --- -- --- --- -- - where X is the integer quotient of ProgrammedRate Refer to the PiCPro for Windows Software Manual for information on controlling the block module via software. GIDDINGS & LEWIS Block I/O Manual 10-17 Block Output Stepper/Input Encoder/ Input 24V DC Module (2/2/2 10.3.2 Block Module Encoder Theory of Operation The encoder section of the block module uses differential type inputs to interface with up to two independent incremental encoders. 10.3.2.1 Incremental Encoders An incremental encoder is a position transducer. It transmits signals through its "A" and "B" outputs with a frequency proportional to the rotational velocity of its shaft. It transmits a pulse through its index output once per revolution of the device. There are two types of incremental encoders, quadrature and pulse. Only quadrature encoders can be used with the block module. A quadrature encoder sends square wave type signals. When the shaft rotates at a constant velocity, the A and B outputs are square waves and are at the same frequency. However they are out of phase with each other by 90°. When the encoder shaft rotates in one direction, each A pulse leads the corresponding B pulse by 90°. When it rotates the other direction each A pulse lags its B pulse by 90°. The signals illustrated in Figure 10-12 indicate that the encoder shaft rotates in one direction at first. Its speed of rotation decreases to 0 and then it starts rotating in the other direction. The signals are shown as differential. A is the inverse of the signal A and B is the inverse of signal B. Figure 10-12 Signals Transmitted by a Quadrature Encoder with Differential Outputs ROTATION SPEED OUTPUT 0 A A B B 10-18 Block I/O Manual GIDDINGS & LEWIS Block Output Stepper/Input Encoder/ Input 24V DC Module (2/2/2 Channel) Quadrature Type Encoder The signal at output A or B from the encoder has a frequency that is the product of the resolution of the encoder in pulses (lines) per revolution and the speed of the encoder in revolutions per second. Thus an encoder that generates 2,000 pulses (lines) per revolution and rotates at 10 revolutions per second generates 20,000 pulses (lines) per second. In a quadrature type encoder, the interface module would supply 80,000 Feedback Units per second. The maximum input frequency is 250,000 lines per second, which results in 1,000,000 Feedback Units (FUs) per second in the encoder module. Figure 10-13 Counting Quadrature Pulses The module counts positive A transitions at both channel A and channel B. One quadrature cycle in this case gives 4 feedback units. B 1 3 12 Encoder Count 2 4 7 10 56 89 11 For each encoder channel, there is a 24-bit up/down counter. It is incremented or decremented in accordance with the signals received from the differential quadrature encoder. There is also a 24-bit latch associated with each encoder input channel. The module can be programmed so that the counter value is "latched" or stored upon receiving an index pulse from the encoder. GIDDINGS & LEWIS Block I/O Manual 10-19 Block Output Stepper/Input Encoder/ Input 24V DC Module (2/2/2 10.3.3 DC Input Theory of Operation Each input is guaranteed "on" at 15 to 30 VDC and guaranteed "off" at 0 to 5 VDC; polarity doesn't matter. Its on/off state is converted to a corresponding logic 1 or 0. This logic state is transmitted through the communication interface to the CPU module, where the processor uses it as data in the ladder program. The logic side of the input is optically isolated from the field side. The logic state of each input is represented by an LED. If you need to know whether voltage is present at the field side, use a voltmeter on the terminal screws. The shaded blocks in Figure 10-14 show the limits specified by the IEC. The lines show the maximum and minimum V/I of the inputs in this module. The voltage/current curve in this graph shows that the input module is well within the IEC Type 1 limits. Figure 10-14 Input Characteristics Compared to IEC Standards U in Volts MIN MAX UH MAX 30 "ON" REGION 25 U NOM 24 20 UH MIN 15 (UT ) MAX TRANSITION REGION 10 UL MAX 5 (UT ) MIN 0 "OFF" REGION I in -5 mAMPS 4 .5 2 6 8 10 12 14 15 I IT IH MAX MIN MIN INPUT CURRENT 10-20 Block I/O Manual GIDDINGS & LEWIS INPUT VOLTAGE Block Output Stepper/Input Encoder/ Input 24V DC Module (2/2/2 Channel) IMPORTANT Switching devices can sometimes have a leakage current that ex- ceeds the IT (current allowed when off) of an input module. In or- min der to use such a device, an impedance (typically, a resistor) needs to be used in parallel with the input. For example, some of the newer proximity switches use two wires in- stead of three. The third wire was used for a power or ground line. Without the third wire, the switch is easier to install. However, it re- quires more leakage current in the off state to power its internal cir- cuitry. As a conservative estimate, use the following formula to calculate an external resistance value. It keeps the input voltage at or below 2.4V when the switching device is in the "off" state. 2.4V -- --- -- --- --- --- -- --- --- --- --- -- --- --- --- --- -- --- --- --- --- -- -- - ≥R Switch Leakage – 0.75mA If the switch leakage specification is ≤ 1.7 mA, then: 2.4V - - - --- --- --- -- --- --- --- --- -- --- - ≥ 2.5KΩ 1.7 – 0.75mA Use a resistor less than or equal to 2.5 KΩ. Be sure that the wattage is adequate for the resistor when the switching device is in the "on" state remembering that: 2 V ON P = --- --- --- - R GIDDINGS & LEWIS Block I/O Manual 10-21 Block Output Stepper/Input Encoder/ Input 24V DC Module (2/2/2 10.4 Specification Table Block Output Stepper/Input Encoder/Input 24V Characteristic DC (2/2/2 ch) specifications Function Includes two stepper outputs, two encoder inputs and two DC inputs Part number M.1017.3143 (old # 503-25988-01) Field side connector Two 18-pin connectors, screw terminals Logic side LEDs, module status Data In LED Data Out LED Configured LED Power LED Module power requirements 300 mA from an external 24 VDC supply (20 to 30 VDC range) NOTE: 1.1 A, 250 microsecond inrush at power on Current output from +5V Out pins 500 mA total available from the module Operating temperature range 7° C to 55° C (45° F to 131° F) Storage temperature range -40° C to 85° C (-40° F to 185° F) Humidity 5 to 95%, non-condensing CE Marked Conforms to Directives 73/23/EEC, 89/336/EEC, 92/31/ EEC, 93/68/EEC by conforming to the following stan- dards: EN 50081-2:1993 EMC Generic Industrial Emissions EN 50082-2:1995 EMC Generic Industrial Immunity EN 61131-2:1994/A11:1996 Low voltage directive requirements for programmable controllers Operates with emissions below EN55011/ CISPR 11 Class A limits Immune to: Electrostatic discharge (4K V contact mode, 8K V air discharge) per EN61000-4-2 RF electromagnetic fields per EN61000-4-3, ENV 50141, and ENV50204 Electrical fast transients per EN61000-4-4 Magnetic fields per EN61000-4-8 Refer to the EMC Guidelines for more information. UL and C/UL Listed File No. E126417 NRAQ Programmable Controllers Physical size 4.05" wide x 4.825" high x 3" deep 102.9 mm x 122.6 mm x 76.2 mm 10-22 Block I/O Manual GIDDINGS & LEWIS Block Output Stepper/Input Encoder/ Input 24V DC Module (2/2/2 Channel) Stepper Section +V input (from external supply) 4.5 VDC to 20 VDC, 45 mA per connected channel Step/CW output rating Totem pole, 15 mA sink, 5 mA source Direction/CCW output rating Protection of logic circuits Optical isolation between the logic and field side Position range ±2,147,352,575 steps Step rate 0 to 1,000,000 steps/sec Step rate accuracy 6 10 × 10 ActualRate = -- --- -- --- --- --- --- - X 6 10 × 10 -- --- --- -- --- --- --- --- -- --- --- --- --- -- --- --- -- - where X is the integer quotient of ProgrammedRate Acceleration/deceleration rate 1 to 16,777,215 steps/sec/sec Reference range ±2,147,352,575 steps Response to scan loss Pulse output halted Encoder Section Encoder (A, B, and index) 2231 Differential Receiver Guaranteed on, min. 2.5 VDC @ 2.5 mA Input voltage, max. 7 VDC Input current, max. 22 mA @ 7 VDC Signal pulse width, min. .6 µs(600 ns) Quad signal freq, max. 250 KHz for A or B input (1 M FU count rate) Encoder device Quadrature type incremental encoder Position range 24-bit up/down counter Cable length, max. 200 ft. @ 250 KHz and 45° quad error GIDDINGS & LEWIS Block I/O Manual 10-23 Block Output Stepper/Input Encoder/ Input 24V DC Module (2/2/2 DC Input Section Input signals (meet IEC standards) Nominal 24 VDC on, 0 VDC off UH Max (max. allowed voltage) 30 VDC IH Max (max. current @ 30 VDC) 7.5 mA UL Min Polarity independent Guaranteed on 15 VDC IH Min (min. current @ UH Min) 2.8 mA Guaranteed off 5 VDC IT Min (current allowed when off) .75 mA Time delay on 1 ms max. Time delay off 1 ms max. Protection of logic circuits Optical isolation between the logic and field sides, tran- sient suppression on the 24V external supply DC inputs IEC Type 1 inputs per IEC 1131-2. UL 508 spacing Logic side LEDs, input circuits A yellow LED for each input Vibration (per IEC 68-2-6) 10-57 Hz (constant amplitude .15 mm) 57 - 2000 Hz (acceleration 2 g) Shock (per IEC 68-2-27) Four shocks per axis (15g/11 msec) 10-24 Block I/O Manual GIDDINGS & LEWIS Block Input Analog Module (4 Channel) 11 Block Input Analog Module (4 Channel) 11.1 Introduction The block analog input module is designed to interface the PiC with voltage or current output devices to monitor such things as pressure, flow, speed, position, or temperature. The module has four independent analog conversion channels. Each channel converts a unipolar or bipolar analog input voltage or current into a 14- bit digital value. This data is transmitted to the PiCs CPU for processing. There is an internal current sense resistor for each channel for use with 0 to 20 mA or 4 to 20 mA devices. This module contains no user adjustable potentiometers or hardware switches. All necessary gain adjustments are done in software. Figure 11-1 Block Input Analog Module (4 Channel) Communications Receive/Transmit IN OUT CONF PWR Communication/Status LEDs ® GIDDINGS & LEWIS INPUT ANALOG Cover (shown open) Screw Terminal Connector GIDDINGS & LEWIS Block I/O Manual 11-1 Block Input Analog Module (4 Channel) 11.2 Connections All signals to the block input module must come to the screw terminal connectors through shielded twisted pair wires. See the discussion in the Hardware chapter on "Preventing electrical noise in data lines". Each input channel has three connection pins as shown in Figure 11-2. The signals are: +voltage input -voltage input 250 ohm current sense resistor for 0/20 mA and 4/20 mA applica- tions The block module has four screw connections for terminating the shields. All four are interconnected within the module so they are the same point electrically. These pins are internally connected to SPG. The shield at the device end of the cable is not connected. Figure Figure 11-2 shows the assignments for all the screw terminal connections on the module. Figure 11-2 Connections for the Input Terminals 1 2 3 456789 10 11 12 13 14 15 16 17 18 19 20 21 22 23 24 24V DC COM Ch1+ Ch1- Ch1R Shield Ch2+ Ch2- Ch2R Shield Chassis Ch3+ Ch3- Ch3R Shield Shield Ch4+ Ch4- Ch4R 11-2 Block I/O Manual GIDDINGS & LEWIS Block Input Analog Module (4 Channel) When connecting an analog voltage output device to the module, the positive wire of the twisted pair goes to the + screw terminal and the negative wire goes to the - screw terminal. Figure 11-3 illustrates these connections for channel one. Notice that no connection is made to the screw terminal with the internal 250Ω resistor when connecting a voltage source device. Figure 11-3 Voltage Input Connections 1 2 3 456789 10 11 12 13 14 15 16 17 18 19 20 21 22 23 24 Ch1+ Ch1- Ch1R Shield To SPG +- Voltage Signal Source GIDDINGS & LEWIS Block I/O Manual 11-3 Block Input Analog Module (4 Channel) When using a 0 to 20 mA or 4 to 20 mA current output device, the positive wire of the twisted pair is connected to the + input and the negative wire is connected to the 250Ω resistor input. A jumper is placed between the - input and the 250Ω resistor input as shown in Figure 11-4 (from pin 5 to pin 6 for channel 1). This connects a 250Ω internal resistor across the input. Figure 11-4 Current Input Connections (0 to 20 or 4 to 20 mA) 1 2 3 456789 10 11 12 13 14 15 16 17 18 19 20 21 22 23 24 Ch1+ Ch1- Ch1R Shield To SPG +- Current Signal Source 0 to 20 or 4 to 20 mA +- Power Supply 11-4 Block I/O Manual GIDDINGS & LEWIS Block Input Analog Module (4 Channel) An alternative method of connecting a two wire 4 to 20 mA current device is shown in Figure 11-5. Place a jumper between the - input and the 250Ω resistor input. Figure 11-5 Current Input Connections (4 to 20 mA) 1 2 3456789 10 11 12 13 14 15 16 17 18 19 20 21 22 23 24 Ch1+ Ch1- Ch1R Shield Current Signal Source 4 to 20 mA +Input from power supply Output + Power Supply - To SPG GIDDINGS & LEWIS Block I/O Manual 11-5 Block Input Analog Module (4 Channel) Figure 11-6 illustrates an example of wiring an external potentiometer to the module using twisted pair wire. For this example, set up the channel initialization function (A_INCHIT) in software for 5 V unipolar. The 5 V power supply output voltage adjustment can be set for the maximum potentiometer output value. For example, the supply could be adjusted until the VALU output of the analog input channel read function (A_INCHRD) reads 16383 with the pot at its maximum position. Figure 11-6 Adding an External Potentiometer 1 2 3 456789 10 11 12 13 14 15 16 17 18 19 20 21 22 23 24 Ch1+ Ch1- Ch1R Shield 1K to 50K Pot To SPG + - +5 Volt Adjustable Regulated Power Supply 11-6 Block I/O Manual GIDDINGS & LEWIS Block Input Analog Module (4 Channel) 11.2.1 Communications Connections There are two 5-pin communications connectors and four logic LEDs on the top of the block I/O module as shown in Figure 11-7. Figure 11-7 Pinouts for Communication Connectors In (from CPU) Out (to next block I/O module Pin # 5 4 3 2 1 Pin # 5 4 3 2 1 Communications Receive/Transmit IN OUT CONF PWR ® GIDDINGS & LEWIS 11.2.1.1 LEDs LED Color State Definition DATA IN Yellow FAINT Data being passed through the block module BRIGHT No activity through the block mod- or OFF ule DATA Yellow FAINT Data is being passed through the OUT block module BRIGHT No activity through the block mod- or OFF ule CONFG Green ON Communication established with this block I/O module OFF Communication not established PWR Green ON Internal +5V logic power supply OK OFF No external 24V applied or internal 5V logic supply not OK GIDDINGS & LEWIS Block I/O Manual 11-7 Driver - (twisted pair output) Driver + (twisted pair output) Shield Receiver - (twisted pair input) Receiver + (twisted pair input) Receiver - (twisted pair input) Receiver + (twisted pair input) Shield Driver - (twisted pair output) Driver + (twisted pair output) Block Input Analog Module (4 Channel) 11.3 Theory of Operation A 14- bit A/D converter samples each channel in sequence at the input scan rate. These values are stored in memory on the module so that any channel value can be read while the A/D converter is processing another channel sample. Each channel can be set up for a maximum input sensitivity of 5 V or 10 V, bipolar or unipolar, or for 4 to 20 mA or 0 to 20 mA current input. The internal 250Ω resistor must be connected as shown in Figure 11-4 or Figure 11-5 to sense the current. All inputs are differential and filtered noise filter time constant of 1 ms. 11-8 Block I/O Manual GIDDINGS & LEWIS Block Input Analog Module (4 Channel) 11.4 Specification Table Characteristic Block Input Analog (4 ch) module specification Function Converts an analog input signal into a 14-bit digital word for each of four channels. Part number M.1017.3098 (old # 503-25909-01) Field side connector 24-pin card edge connector, screw terminals Input channels 4 Resolution 14 bits, or 16384 steps over the full input range Input sensitivity (software selectable) Voltage ranges Unipolar Bipolar 0 to 10 V ±10 V 0 to 5 V ±5 V Current range 0 to 20 mA, 4 to 20 mA Common mode maximum voltage ±35V with power on (The maximum voltage that can safely be ±20V with power off applied between either input terminal and circuit common.) Internal current sense resistor 250 ohms Maximum current sense resistor power .12 W Differential input resistance (each input to 1 M Ohms ground) Filter time constant 1 ms Accuracy of 4-20 mA range o 14-bit - .15% of FSR at 25 C o ± 100 PPM / C Accuracy of all other ranges o 14-bit - .2% of FSR at 25 C o ± 100 PPM / C 0 Offset ±5 counts @ 10V Logic side LEDs, module status Data In LED Data Out LED Configured LED Power LED Module power requirements 160 mA from an external 24V DC supply (20 to 30V DC range) NOTE: 2.5A, 250 microsecond inrush at power on GIDDINGS & LEWIS Block I/O Manual 11-9 Block Input Analog Module (4 Channel) CE Marked Conforms to Directives 73/23/EEC, 89/336/EEC, 92/31/ EEC, 93/68/EEC by conforming to the following stan- dards: EN 50081-2:1993 EMC Generic Industrial Emissions EN 50082-2:1995 EMC Generic Industrial Immunity EN 61131-2:1994/A11:1996 Low voltage directive requirements for programmable controllers Operates with emissions below EN55011/ CISPR 11 Class A limits Immune to: Electrostatic discharge (4K V contact mode, 8K V air discharge) per EN61000-4-2 RF electromagnetic fields per EN61000-4-3, ENV 50141, and ENV50204 Electrical fast transients per EN61000-4-4 Magnetic fields per EN61000-4-8 Refer to the EMC Guidelines for more information. UL and C/UL Listed File No. E126417 NRAQ Programmable Controllers Operating temperature range 7° C to 55° C (45° F to 131° F) Storage temperature range -40° C to 85° C (-40° F to 185° F) Humidity 5 to 95%, non-condensing Physical size 4.05" wide x 4.825" high x 3" deep 102.9 mm x 122.6 mm x 76.2 mm Vibration (per IEC 68-2-6) 10-57 Hz (constant amplitude .15 mm) 57 - 2000 Hz (acceleration 2 g) Shock (per IEC 68-2-27) Four shocks per axis (15g/11 msec) 11-10 Block I/O Manual GIDDINGS & LEWIS Block Output 4-20mA Module (4 Channel) 12 Block Output 4-20mA Module (4 Channel) 12.1 Introduction The block 4-20mA output module has four independent 4-20mA conversion chan- nels. Each channel converts a 15-bit digital value into a single ended type 4-20mA analog current output signal. The full range of the output signal is 4mA to 20mA, with a 15-bit resolution of one part in 32,768. A typical use for this module is to supply a control signal to valves. This module contains no user adjusted potentiometers or hardware switches. All necessary adjustments are done in software. Figure 12-1 Block Output 4-20mA Module (4 Channel) Communications Receive/Transmit IN OUT CONF PWR Communication/Status LEDs ® GIDDINGS & LEWIS OUTPUT 4-20 mA Cover (shown open) Screw Terminal Connector GIDDINGS & LEWIS Block I/O Manual 12-1 Block Output 4-20mA Module (4 Channel) 12.2 Connections Two screw terminal connections are assigned to each channel to carry the signals (see Figure 12-2). The negative outputs of each channel are connected internally to the +V Common. In addition, the module has four screw terminal connections for terminating the shields. All four are connected internally, so they are the same point electrically. Two connections are used to connect an external power supply. Figure 12-2 Screw Terminal Connector Assignments 1 2 3 456789 10 11 12 13 14 15 16 17 18 19 20 21 22 23 24 Ch1+ Ch1- Shield Ch2+ Ch2- Shield +24V DC Chassis Ch3+ Ch3- Shield Shield DC Com Ch4+ Ch4- Ground Each 4-20mA output channel is connected to a receiving device with twisted pair wires (see Figure 12-3). For extremely noisy environments, use shielded twisted pair wire. The shield connections are internally connected to the Single Point Ground (SPG) to which the system rack is connected. No external connection should be made. 12-2 Block I/O Manual GIDDINGS & LEWIS Block Output 4-20mA Module (4 Channel) Figure 12-3 Receiving Devices and Power Supply Connections Ch2+ Ch 2- Receiving Devices Ch1+ Ch1- Ch2+ Ch2- Shield Ch1+ Ch1- Shield 1 2 3456789 10 11 12 Screw 13 14 15 16 17 18 19 20 21 22 23 24 Terminals Ch4+ Ch4- Shield DC Com Ch3+ Ch3- Shield +24V DC 0V +24V Power Supply To SPG Receiving Devices Ch3+ Ch3- Ch4+ Ch4- GIDDINGS & LEWIS Block I/O Manual 12-3 Block Output 4-20mA Module (4 Channel) 12.2.1 Communications Connections There are two 5-pin communications connectors and four logic LEDs on the top of the block I/O module as shown in Figure 12-4. Figure 12-4 Pinouts for Communication Connectors In (from CPU) Out (to next block I/O module Pin # 5 4 3 2 1 Pin # 5 4 3 2 1 Communications Receive/Transmit IN OUT CONF PWR ® GIDDINGS & LEWIS 12.2.1.1 LEDs LED Color State Definition DATA IN Yellow FAINT Data being passed through the block module BRIGHT No activity through the block module or OFF DATA Yellow FAINT Data is being passed through the block OUT module BRIGHT No activity through the block module or OFF CONFG Green ON Communication established with this block I/O module OFF Communication not established PWR Green ON Internal +5V logic power supply OK OFF No external 24V applied or internal 5V logic supply not OK 12-4 Block I/O Manual GIDDINGS & LEWIS Driver - (twisted pair output) Driver + (twisted pair output) Shield Receiver - (twisted pair input) Receiver + (twisted pair input) Receiver - (twisted pair input) Receiver + (twisted pair input) Shield Driver - (twisted pair output) Driver + (twisted pair output) Block Output 4-20mA Module (4 Channel) 12.3 Theory of Operation The CPU module sends the output module a 16-bit digital word for each channel used. Each digital word is converted to a corresponding current within the range 4-20mA. The current is brought out to a pair of screw terminal connections as a single-ended type current output. You can adjust each channel in software for offset adjustments and gain scaling. For safety reasons, all outputs are automatically reset to 4mA when a scan loss condition occurs. All outputs have clamping diodes and a capacitor to permit the driving of non- resistive (i.e. inductive) loads. All outputs can drive loads whose impedance is less than or equal to: V – 2.5V EXT - --- --- -- --- --- --- -- --- --- -- - = R LOAD 20mA Example: If V = 24V, then the maximum impedance equals: EXT 24V – 2.5V EXT -- -- --- --- --- --- -- --- --- --- --- -- --- - = 1075Ω 20mA The load range in this example is from 0 to 1075 Ω. Anytime the load impedance is exceeded, the OPEN flag is set in software. Nor- mally, it is an open circuit that causes this flag to be set. GIDDINGS & LEWIS Block I/O Manual 12-5 Block Output 4-20mA Module (4 Channel) 12.4 Specification Table Characteristic Block Output 4-20mA (4 ch) specification Function Converts a 15-bit digital value into a 4-20mA analog current signal for each of four channels Part number M.1017.3101 (old # 503-25910-01) Field side connector 24 pin card edge connector, screw terminals Output channels 4 Resolution 15 bits, or 32,768 steps over the full output range Output characteristics @24V DC supply, with temperature = 25° (77°F) Accuracy .25% FSR (Full Scale Range) Output current, max. 20 mA V = 4mA R Output voltage after power up OUT * LOAD Response to "scan loss" All outputs reset to 4mA Current is limited to: Short circuit protection I = where I = 4 to 20mA OUT OUT Logic side LEDs, module status Data In LED Data Out LED Configured LED Power LED Module power requirements 200 mA from an external 24V DC supply (20 to 30V DC range) NOTE: 2.5A, 250 microsecond inrush at power on 12-6 Block I/O Manual GIDDINGS & LEWIS Block Output 4-20mA Module (4 Channel) CE Marked Conforms to Directives 73/23/EEC, 89/336/EEC, 92/31/ EEC, 93/68/EEC by conforming to the following stan- dards: EN 50081-2:1993 EMC Generic Industrial Emissions EN 50082-2:1995 EMC Generic Industrial Immunity EN 61131-2:1994/A11:1996 Low voltage directive requirements for programmable controllers Operates with emissions below EN55011/ CISPR 11 Class A limits Immune to: Electrostatic discharge (4K V contact mode, 8K V air discharge) per EN61000-4-2 RF electromagnetic fields per EN61000-4-3, ENV 50141, and ENV50204 Electrical fast transients per EN61000-4-4 Magnetic fields per EN61000-4-8 Refer to the EMC Guidelines for more information. UL and C/UL Listed File No. E126417 NRAQ Programmable Controllers Operating temperature range 7° C to 55° C (45° F to 131° F) Storage temperature range -40° C to 85° C (-40° F to 185° F) Humidity 5 to 95%, non-condensing Physical size 4.05" wide x 4.825" high x 3" deep 102.9 mm x 122.6 mm x 76.2 mm Vibration (per IEC 68-2-6) 10-57 Hz (constant amplitude .15 mm) 57 - 2000 Hz (acceleration 2 g) Shock (per IEC 68-2-27) Four shocks per axis (15g/11 msec) GIDDINGS & LEWIS Block I/O Manual 12-7 Block Output 4-20mA Module (4 Channel) NOTES 12-8 Block I/O Manual GIDDINGS & LEWIS Block Output +10V DC Module (4 Channel) 13 Block Output +10V DC Module (4 Channel) 13.1 Introduction The output ±10V DC module has four independent D/A conversion channels. Each channel converts a 16-bit digital word into a differential type analog output signal. The full range of the output signal is - 10 V to + 10 V, with a resolution of 1 part in 65,536. This module contains no potentiometers or hardware switches. All necessary adjustments are done in software. Figure 13-1 Block Output ±10V DC Module (4 Ch) Communications Receive/Transmit IN OUT CONF PWR Communication/Status LEDs ® GIDDINGS & LEWIS OUTPUT ±10VDC Cover (shown open) Screw Terminal Connector GIDDINGS & LEWIS Block I/O Manual 13-1 Block Output +10V DC Module (4 Channel) 13.2 Connections Two screw terminal connections are assigned to each channel to carry the signals as shown in Figure 13-2. In addition, the module has four screw terminal connections for terminating the shields. All four are connected internally, so they are the same point electrically. Two connections are used to connect an external power supply. Figure 13-2 Screw Terminal Connector Assignments 1 2 3 456789 10 11 12 13 14 15 16 17 18 19 20 21 22 23 24 Ch1+ Ch1- Shield Ch2+ Ch2- Shield +24V DC Chassis Ch3+ Ch3- Shield Shield DC Com Ch4+ Ch4- Ground Each output channel is connected to a receiving device with twisted pair wires as shown in Figure 13-3. For extremely noisy environments, use shielded twisted pair wire. The shield connections are internally connected to the Single Point Ground (SPG) to which the system rack is connected. No external connection should be made. 13-2 Block I/O Manual GIDDINGS & LEWIS Block Output +10V DC Module (4 Channel) 13.2.1 Communications Connections There are two 5-pin communications connectors and four logic LEDs on the top of the block I/O module as shown in Figure 13-3. Figure 13-3 Pinouts for Communication Connectors In (from CPU) Out (to next block I/O module) Pin # 5 4 3 2 1 Pin # 5 4 3 2 1 Communications Receive/Transmit Communications Receive/Transmit IN OUT CONF PWR ® GIDDINGS & LEWIS 13.2.1.1 LEDs LED Color State Definition DATA IN Yellow FAINT Data being passed through the block module BRIGHT No activity through the block mod- or OFF ule DATA Yellow FAINT Data is being passed through the OUT block module BRIGHT No activity through the block mod- or OFF ule CONFG Green ON Communication established with this block I/O module OFF Communication not established PWR Green ON Internal +5V logic power supply OK OFF No external 24V applied or internal 5V logic supply not OK GIDDINGS & LEWIS Block I/O Manual 13-3 Driver - (twisted pair output) Driver + (twisted pair output) Shield Receiver - (twisted pair input) Receiver + (twisted pair input) Receiver - (twisted pair input) Receiver + (twisted pair input) Shield Driver - (twisted pair output) Driver + (twisted pair output) Block Output +10V DC Module (4 Channel) 13.2.2 Analog Output Receiving Devices It was assumed in Figure 13-2 that all the receiving device inputs were differential. However, you may connect the differential type output from this module to a single-ended input device. Figure 13-4 shows the difference between the two types of connections. Note that one wire in the twisted pair is connected to the 0 V terminal on the receiving device. This 0V terminal must be referenced to the SPG through the device's ground connection. It is recommended that the receiving device have a differential input for best noise immunity. Figure 13-4 Differential and Single-Ended Receiving Devices Single-Ended Input Differential Input GND GND Receiving Devices Ch2+ 0V Ch1+ Ch 1- To SPG To SPG Ch2+ Ch2- Shield Ch1+ Ch1- Shield 1 2 3456789 10 11 12 Screw 13 14 15 16 17 18 19 20 21 22 23 24 Terminals DC Com +24V DC 0V +24V Power Supply To SPG 13-4 Block I/O Manual GIDDINGS & LEWIS Block Output +10V DC Module (4 Channel) 13.3 Theory of Operation The CPU module sends the output module a 16-bit digital word for each channel used. Each digital word is converted to a corresponding voltage within the range of ±10 V. The voltage is buffered and brought out to a pair of screw terminal connections as a differential type voltage output. This output is less subject to interference from electrical noise than a single-ended output would be. You can adjust each channel in software for offset adjustments, gain scaling, and unipolar outputs. For safety reasons, all outputs are automatically reset to 0 V when a scan loss condition occurs. GIDDINGS & LEWIS Block I/O Manual 13-5 Block Output +10V DC Module (4 Channel) 13.4 Specification Table Characteristic Output ±10V DC module specification Function Converts a 16-bit digital word into a ±10 V analog signal for each of the four channels. Part number M.1017.3140 (old # 503-25987-01) Field side connector 24 pin card edge connector, screw terminals Output channels 4 Resolution 16 bits, or 65536 steps over the full output range Output voltage characteristics [@24V DC supply, with temperature = 25°C(77°F)] Nominal voltage range ± 10 VDC Voltage accuracy ±1% FSR (Full Scale Range) Output current, max. @ ±10V ± 10 mA (1K Ω resistor) Output voltage after power up 0 V ± 50 mV Response to scan loss All outputs reset to 0 V ± 50 mV Short circuit protection Current limited outputs Logic side LEDs, module status Data In LED Data Out LED Configured LED Power LED Module power requirements 200 mA from an external 24V DC supply (20 to 30V DC range) NOTE: 2.5A, 250 microsecond inrush at power on 13-6 Block I/O Manual GIDDINGS & LEWIS Block Output +10V DC Module (4 Channel) CE Marked Conforms to Directives 73/23/EEC, 89/336/EEC, 92/31/ EEC, 93/68/EEC by conforming to the following stan- dards: EN 50081-2:1993 EMC Generic Industrial Emissions EN 50082-2:1995 EMC Generic Industrial Immunity EN 61131-2:1994/A11:1996 Low voltage directive requirements for programmable controllers Operates with emissions below EN55011/ CISPR 11 Class A limits Immune to: Electrostatic discharge (4K V contact mode, 8K V air discharge) per EN61000-4-2 RF electromagnetic fields per EN61000-4-3, ENV 50141, and ENV50204 Electrical fast transients per EN61000-4-4 Magnetic fields per EN61000-4-8 Refer to the EMC Guidelines for more information. UL and C/UL Listed File No. E126417 NRAQ Programmable Controllers Operating temperature range 7° C to 55° C (45° F to 131° F) Storage temperature range -40° C to 85° C (-40° F to 185° F) Humidity 5 to 95%, non-condensing Physical size 4.05" wide x 4.825" high x 3" deep 102.9 mm x 122.6 mm x 76.2 mm Vibration (per IEC 68-2-6) 10-57 Hz (constant amplitude .15 mm) 57 - 2000 Hz (acceleration 2 g) Shock (per IEC 68-2-27) Four shocks per axis (15g/11 msec) GIDDINGS & LEWIS Block I/O Manual 13-7 Block Output +10V DC Module (4 Channel) NOTES 13-8 Block I/O Manual GIDDINGS & LEWIS Block Input 24V DC Module/J (16 points) 14 Block Input 24V DC Module/J (16 points) 14.1 Introduction The input 24V DC module converts DC signals from devices into logic levels that the CPU can use. Each signal is converted into a corresponding logic 1 or 0 which is transmitted through the communication interface to the CPU module. An "on" signal is nominally 24 VDC, but can be any level between 15 and 30 volts. An "off" signal is any level below 5V. The wiring configurations may be sink or source. Figure 14-1 Block Input 24V DC Module/J 16 point Communications Receive/Transmit IN OUT CONF PWR Communication/Status LEDs ® GIDDINGS & LEWIS Output Status LEDs OUTPUT 24VDC SINK SOURCE Cover (shown open) Screw Terminal Connector GIDDINGS & LEWIS Block I/O Manual 14-1 Block Input 24V DC Module/J (16 points) 14.2 Connections A screw terminal connector is provided for each input and for each external power supply connection. The inputs are isolated in two groups of eight, with one additional terminal per group for the DC source/sink connection. The devices connected to terminals in the same group have a common DC supply and are wired in the same configuration, sink or source (Figure 14-2). The external DC supply that powers the input signals should have a wire connected from its 0V (COMMON) terminal directly to the single-point ground used for the system rack. Figure 14-2 Screw Terminal Connector Assignments 1 2 3456789 10 11 12 13 14 15 16 17 18 19 20 21 22 23 24 25 26 27 28 29 30 31 32 33 34 35 36 In11 In1 In3 In9 In13 In15 AUX AUX In5 AUX AUX 24V In7 AUX 24V AUX 24V 24V 24V 24V 24V 24V 0V In10 In12 0V In14 In16 0V 0V Chassis 0V In2 In4 0V In6 In8 0V Group 1 SS Group 2 SS Typically, an external 24V DC supply is connected to pins 18 and 35. NOTE Using the supplied jumper, connect pin 17 to pin 18. This con- nection provides functionality identical to that of M.1017.3092 (503-25907-01). In an earlier version of this module (M.1017.3092, 503-25907-01) 24V on pin 18 was internally connected to the pins now labeled as AUX 24V. This Block Input 24V DC Module/J requires an external jumper to provide this same functionality. 0V is still internally jumpered from pin 35 to pins labeled as 0V. These pins labeled as AUX24V and 0V make it convenient to connect 3-wire devices (e.g. a proximity switch) that require a voltage and ground connector. Also, AUX24V or 0V can be easily jumpered to a group’s sink/ source connnection. 14-2 Block I/O Manual GIDDINGS & LEWIS Block Input 24V DC Module/J (16 points) The external jumpered connection using pin 17 and pin 18 provides the option of connecting an external fuse in series with the AUX24V intended for the external 3-wire devices. Essentially, connect pin 17 and pin 18 with a fuse instead of a jumper. If a short-circuit occurs in an external device, the block I/O communications will continue to function properly and only the devices connected to the fused 24V line will be shut down. Figure 14-3 illustrates two groups of inputs using the same power supply. Each group can work independently of the other; one group may be sink and the other source. The DC power supply for each group may be different if required, but must be referenced to the same ground. Typically just one DC power supply is used, daisy-chained from one group to the next. In Figure 14-3a, one group of eight inputs is shown with devices "sinking" current through the block DC Input module. The HOT terminal of the power supply is connected internally to the module by the jumper between 24V and Group 1 or 2 SS. The second group of eight inputs is shown with devices "sourcing" current through the block DC Input module. The COMMON terminal of the power supply is connected internally to the module by the jumper between 0V and Group 2 or 1 SS. In Figure 14-3b, the first group is shown with devices "sourcing" current through the block DC Input module. The second group is shown with devices "sinking current through the block DC Input module. In both examples the DC power supply is the same for Group 1 and 2. Use up to 14 AWG for field side wiring. GIDDINGS & LEWIS Block I/O Manual 14-3 Block Input 24V DC Module/J (16 points) Figure 14-3 Connectors for Two Groups of Inputs a. Group 1 Sink (Pins 8 and 9 Jumpered) and Group 2 Source (Pins 33 and 34 Jumpered) 7 15 2 3 45 6 8 9 10 11 12 13 14 16 17 18 1 25 33 36 20 21 22 23 24 26 27 28 29 30 31 32 34 35 19 Hot Common Group 1 Group 2 Sink Source 0V V+ DC Power Supply b. Group 1 Source (Pins 25 and 26 Jumpered) and Group 2 Sink (Pins 16 and 17 Jumpered) 7 3 45 6 8 9 10 11 12 13 14 15 16 17 18 1 2 25 34 35 22 23 24 26 27 28 29 30 31 32 33 36 19 20 21 Common Hot Group 1 Group 2 Source Sink 0V V+ DC Power Supply 14-4 Block I/O Manual GIDDINGS & LEWIS IN 1 IN 1 IN 2 IN 2 IN 3 IN 3 IN 4 IN 4 IN 5 IN 5 IN 6 IN 6 IN 7 IN 7 IN 8 IN 8 0V Group1 SS Group1 SS AUX 24V IN 9 IN 9 IN 10 IN 10 IN 11 IN 11 IN 12 IN 12 IN 13 IN 13 IN 14 IN 14 IN 15 IN 15 IN 16 IN 16 0V Group2 SS Group2 SS AUX 24V Block Input 24V DC Module/J (16 points) 14.2.1 Communications Connections There are two 5-pin communications connectors and four logic LEDs on the top of the block I/O module as shown in Figure 14-4. Figure 14-4 Pinouts for Communication Connectors In (from CPU) Out (to next block I/O module) Pin # 5 4 3 2 1 Pin # 5 4 3 2 1 Communications Receive/Transmit IN OUT CONF PWR ® GIDDINGS & LEWIS 14.2.1.1 LEDs LED Color State Definition DATA IN Yellow FAINT Data being passed through the block module BRIGHT No activity through the block module or OFF DATA Yellow FAINT Data is being passed through the OUT block module BRIGHT No activity through the block module or OFF CONFG Green ON Communication established with this block I/O module OFF Communication not established PWR Green ON Internal +5V logic power supply OK OFF No external 24V applied or internal 5V logic supply not OK GIDDINGS & LEWIS Block I/O Manual 14-5 Driver - (twisted pair output) Driver + (twisted pair output) Shield Receiver - (twisted pair input) Receiver + (twisted pair input) Receiver - (twisted pair input) Receiver + (twisted pair input) Shield Driver - (twisted pair output) Driver + (twisted pair output) Block Input 24V DC Module/J (16 points) 14.3 Theory of Operation Each input is guaranteed "on" at 15 to 30 VDC and guaranteed "off" at 0 to 5 VDC; polarity doesn't matter. Its on/off state is converted to a corresponding logic 1 or 0. This logic state is transmitted through the communication interface to the CPU module, where the processor uses it as data in the ladder program. The logic side of the input is optically isolated from the field side. An LED in the upper section of the module indicates the logic state of each input. Each group is represented by a horizontal row of LEDs. If you need to know whether voltage is present at the field side, use a voltmeter on the terminal screws. The shaded blocks in Figure 14-5 show the limits specified by the IEC. The lines show the maximum and minimum V/I of the inputs in this module. The voltage/current curve in this graph shows that the input module is well within the IEC Type 1 limits. Figure 14-5 Input Characteristics Compared to IEC Standards U in Volts MIN MAX UH MAX 30 "ON" REGION 25 U NOM 24 20 UH MIN 15 (UT ) MAX TRANSITION REGION 10 UL MAX 5 (UT ) MIN 0 "OFF" REGION I in -5 mAMPS 4 .5 2 6 8 10 12 14 15 I IT IH MAX MIN MIN INPUT CURRENT 14-6 Block I/O Manual GIDDINGS & LEWIS INPUT VOLTAGE Block Input 24V DC Module/J (16 points) IMPORTANT Switching devices can sometimes have a leakage current that ex- ceeds the IT (current allowed when off) of an input module. In or- min der to use such a device, an impedance (typically, a resistor) needs to be used in parallel with the input. For example, some of the newer proximity switches use two wires in- stead of three. The third wire was used for a power or ground line. Without the third wire, the switch is easier to install. However, it re- quires more leakage current in the off state to power its internal cir- cuitry. As a conservative estimate, use the following formula to calculate an external resistance value. It keeps the input voltage at or below 2.4V when the switching device is in the "off" state. 2.4V -- --- -- --- --- --- -- --- --- --- --- -- --- --- --- --- -- --- --- --- --- -- -- - ≥R Switch Leakage – 0.75mA If the switch leakage specification is ≤ 1.7 mA, then: 2.4V - - - --- --- --- -- --- --- --- --- -- --- - ≥ 2.5KΩ 1.7 – 0.75mA Use a resistor less than or equal to 2.5 KΩ. Be sure that the wattage is adequate for the resistor when the switching device is in the "on" state remembering that: 2 V ON P = --- --- --- - R GIDDINGS & LEWIS Block I/O Manual 14-7 Block Input 24V DC Module/J (16 points) 14.4 Specification Table Characteristic Block Input 24V DC Module/J specifications Function Monitors on/off states from DC voltage inputs Part number M.1300.7372 Field side connector Two 18-pin connectors, screw terminals Input signals (meet IEC standards) Nominal 24 VDC on, 0 VDC off UH Max (max. allowed voltage) 30 VDC IH Max (max. current @ 30 VDC) 7.5 mA UL Min Polarity independent Guaranteed on 15 VDC IH Min (min. current @ UH Min) 2.8 mA Guaranteed off 5 VDC IT Min (current allowed when off) .75 mA Time delay on 1 ms max. Time delay off 1 ms max. Protection of logic circuits Optical isolation between the logic and field sides, tran- sient suppression on the 24V external supply Logic side LEDs, module status Data In LED Data Out LED Configured LED Power LED Logic side LEDs, input circuits A yellow LED for each input Module power requirements 100 mA from an external 24V DC supply (20 to 30V DC range) NOTE: 2.5A, 250 microsecond inrush at power on 14-8 Block I/O Manual GIDDINGS & LEWIS Block Input 24V DC Module/J (16 points) CE Marked Conforms to Directives 73/23/EEC, 89/336/EEC, 92/31/ EEC, 93/68/EEC by conforming to the following stan- dards: EN 50081-2:1993 EMC Generic Industrial Emissions EN 50082-2:1995 EMC Generic Industrial Immunity EN 61131-2:1994/A11:1996 Low voltage directive requirements for programmable controllers Operates with emissions below EN55011/ CISPR 11 Class A limits Immune to: Electrostatic discharge (4K V contact mode, 8K V air discharge) per EN61000-4-2 RF electromagnetic fields per EN61000-4-3, ENV 50141, and ENV50204 Electrical fast transients per EN61000-4-4 Magnetic fields per EN61000-4-8 Refer to the EMC Guidelines for more information. UL and C/UL Listed File No. E126417 NRAQ Programmable Controllers Operating temperature range 7° C to 55° C (45° F to 131° F) Storage temperature range -40° C to 85° C (-40° F to 185° F) Humidity 5 to 95%, non-condensing Physical size 4.05" wide x 4.825" high x 3" deep 102.9 mm x 122.6 mm x 76.2 mm Vibration (per IEC 68-2-6) 10-57 Hz (constant amplitude .15 mm) 57 - 2000 Hz (acceleration 2 g) Shock (per IEC 68-2-27) Four shocks per axis (15g/11 msec) GIDDINGS & LEWIS Block I/O Manual 14-9 Block Input 24V DC Module/J (16 points) NOTES 14-10 Block I/O Manual GIDDINGS & LEWIS Block 24V DC 8 In/8 Out Module/J 15 Block 24V DC 8 In/8 Out Module/J 15.1 Introduction The Block 24V DC 8/8 module provides eight output points and eight input points. The eight point output section sources voltage for individual loads from a DC power supply. The external supply is nominally 24 volts, but can be between 20 and 30 volts. Eight LEDs near the field terminal connector of the module indicate the logic state that drives each output. Another LED labeled SC turns on if any output attempts to drive a short circuit. The eight point input section converts DC signals from devices into logic levels that the CPU can use. Each signal is converted into a corresponding logic 1 or 0 which is transmitted through the communication interface to the CPU module. An "on" signal is nominally 24 VDC, but can be any level between 15 and 30 volts. An "off" signal is any level below 5V. The wiring configurations may be sink or source. Eight LEDs near the field terminal connector of the module indicate the logic state of each input. Figure 15-1 Block 24V DC 8In/8 Out Module/J Communications Receive/Transmit IN OUT CONF PWR Communication/Status LEDs ® GIDDINGS & LEWIS Output Status OUTPUT 24V DC Short Circuit LED LEDs Cover (shown open) Field Side Input LEDs Screw Terminal Connector GIDDINGS & LEWIS Block I/O Manual 15-1 Block 24V DC 8 In/8 Out Module/J 15.2 Connections A screw terminal connection is provided for each output, input, and external power supply connection. The group of eight outputs and the group of eight inputs are isolated. The output group has its own short circuit protection with a short circuit LED indicator. The input group has additional terminal connections for the DC sink/source configuration. The external DC supply that powers the output and/or input signals should have a wire connected from its 0V (COMMON) terminal directly to the single point ground used for the system rack. Figure 15-2 Screw Terminal Connection Assignments Outputs Inputs 1 2 345 6789 10 11 12 13 14 15 16 17 18 19 20 21 22 23 24 25 26 27 28 29 30 31 32 33 34 35 36 Typically, an external 24V DC supply is connected to pins 18 and 35. NOTE Using the supplied jumper, connect pin 17 to pin 18. This con- nection provides functionality identical to that of M.1017.3090 (503-25906-01). In an earlier version of this module (M.1017.3090, 503-25906-01) 24V on pin 18 was internally connected to the pins now labeled as AUX 24V. This Block 24V DC 8In/Out Module/J requires an external jumper to provide this same functionality. 0V is still internally jumpered from pin 35 to pins labeled as 0V. These pins labeled as AUX24V and 0V make it convenient to connect 3-wire devices (e.g. a proximity switch) that require a voltage and ground connector. Also, AUX24V or 0V can be easily jumpered to a group’s sink/ source connnection. The external jumpered connection using pin 17 and pin 18 provides the option of connecting an external fuse in series with the AUX24V intended for the external 3-wire devices. Essentially, connect pin 17 and pin 18 with a fuse instead of a jumper. If a short-circuit occurs in an external device, the block I/O communications will continue to function properly and only the devices connected to the fused 24V line will be shut down. 15-2 Block I/O Manual GIDDINGS & LEWIS DC Line 1 DC Com1 DC Out1 DC Out2 DC Out3 DC Out4 DC Out5 DC Out6 DC Out7 DC Out8 0V DC IN1 DC IN2 DC IN3 DC IN4 AUX 24V 0V DC IN5 DC IN6 DC IN7 DC IN8 AUX 24V 0V DC IN SS DC IN SS AUX 24V 0V 24V Chassis Block 24V DC 8 In/8 Out Module/J Connections for the outputs are illustrated in Figure 15-3. The common side of each load must be connected to the 0V terminal of the supply. This 0V terminal is connected to the SPG used by the system rack. Use up to 14 AWG for field side wiring. Figure 15-3 Connections for the Outputs 123 4 5 19 20 21 22 23 Line 1 Com1 Out1 Out2 Out3 Out4 Out5 Out6 Out7 Out8 V+ 0V DC To SPG Power Supply GIDDINGS & LEWIS Block I/O Manual 15-3 Block 24V DC 8 In/8 Out Module/J Connections for the inputs are illustrated in Figure Figure 15-4. The eight inputs on the left are shown with devices "sourcing" current through the block module. The COMMON terminal of the power supply is connected inter- nally to the module by the jumper between 0V and the DC IN SS. The eight inputs in the example on the right are shown with devices "sinking" cur- rent through the block module. The HOT terminal of the power supply is con- nected internally to the module by the jumper between 24V and DC IN SS. Use up to 14 AWG for field side wiring. Figure 15-4 Connectors for Inputs 15 18 10 11 12 13 14 16 17 10 11 12 13 14 15 16 17 18 33 36 28 29 30 31 32 34 35 28 29 30 31 33 34 36 32 35 Common Hot Sink Source 0V V+ 0V V+ DC Power DC Power Supply Supply 15-4 Block I/O Manual GIDDINGS & LEWIS DC IN 1 DC IN 2 DC IN 3 DC IN 4 DC IN 5 DC IN 6 DC IN 7 DC IN 8 0V DC IN SS DC IN 1 DC IN 2 DC IN 3 DC IN 4 DC IN 5 DC IN 6 DC IN 7 DC IN 8 DC IN SS AUX 24V Block 24V DC 8 In/8 Out Module/J 15.2.1 Communications Connections There are two 5-pin communications connectors and four logic LEDs on the top of the block I/O module as shown in Figure 15-5. Figure 15-5 Pinouts for Communication Connectors In (from CPU) Out (to next block I/O module) Pin # 5 4 3 2 1 Pin # 5 4 3 2 1 Communications Receive/Transmit IN OUT CONF PWR ® GIDDINGS & LEWIS 15.2.1.1 LEDs LED Color State Definition DATA IN Yellow FAINT Data being passed through the block module BRIGHT No activity through the block module or OFF DATA Yellow FAINT Data is being passed through the OUT block module BRIGHT No activity through the block module or OFF CONFG Green ON Communication established with this block I/O module OFF Communication not established PWR Green ON Internal +5V logic power supply OK OFF No external 24V applied or inter- nal 5V logic supply not OK GIDDINGS & LEWIS Block I/O Manual 15-5 Driver - (twisted pair output) Driver + (twisted pair output) Shield Receiver - (twisted pair input) Receiver + (twisted pair input) Receiver - (twisted pair input) Receiver + (twisted pair input) Shield Driver - (twisted pair output) Driver + (twisted pair output) Block 24V DC 8 In/8 Out Module/J 15.2.2 Protecting from an Inductive Load Resistive loads can be connected to the module and controlled by the system with no precautions other than making sure they have a connection to the common of the DC power supply. Inductive loads have an electrical "kickback" when current is stopped. This can damage or destroy the output switching device. Each output in the Output 24V DC module has a diode through which reverse current can be safely routed. Figure 15-6 shows how the internal diode works with an inductive load. When an output is energized, represented in Figure Figure 15-6a by a closed switch, current passes through the load into the common line. When the output is de-energized, represented in Figure 15-6b by an open switch, current stops and the inductive field collapses. The state of the outputs is controlled by the CPU module. This creates a reverse voltage across the load called "kickback" which tries to continue the current. The voltage is in series with the DC power supply. The combined voltage appears across the output switching device in the module. If this were the only path available, voltage across the device would peak at several hundred volts. The internal diode provides another path for current. This limits the peak reverse voltage across the load to less than 1 V. Every switch in the Output 24V DC module has this protection so you can connect an inductive load to any terminal. Figure 15-6 Diagram of Internal Protection for Inductive Loads DC Power Supply DC Power Supply 0V V+ OUTPUT MODULE 0V V+ OUTPUT MODULE DCL1 DCL1 DCCOM1 Output DCCOM1 Switching Output INDUCTIVE Device Switching LOAD INDUCTIVE Device DCOUT1 LOAD DCOUT1 a) Output Energized b) Output De-energized 15-6 Block I/O Manual GIDDINGS & LEWIS Block 24V DC 8 In/8 Out Module/J 15.3 Theory of Operation 15.3.1 Outputs Each output point is a solid state switch rated at .5 A. It turns on or off according to the logic state sent to it by the CPU. If the CPU sends it a logic 1, the switch closes and the device is powered. If the CPU sends a logic 0, the switch opens and power to the device is cut off. The CPU updates the logic state for each switch every time it scans the program. The logic side of the switch is optically isolated from the field side. An LED gives the logic state of each switch. If you need to know whether voltage is actually present at the field side, use a voltmeter on the terminal screws. The group of outputs has a .1 ohm series sensing resistor to protect against current overload in case the outputs are shorted to ground. When a short circuit condition is sensed, all outputs are pulsed on for approximately 130 microseconds every 100 milliseconds. Normal operation resumes after the short is removed. In addition, each output is protected with internal clamping diodes. Without clamping, high voltage transients (kickback) from inductive loads might damage the module. 15.3.2 Inputs Each input is guaranteed "on" at 15 to 30 VDC and guaranteed "off" at 0 to 5 VDC; polarity doesn't matter. Its on/off state is converted to a corresponding logic 1 or 0. This logic state is transmitted through the communication interface to the CPU module, where the processor uses it as data in the ladder program. The logic side of the input is optically isolated from the field side. An LED in the upper section of the module indicates the logic state of each input. The group of inputs is represented by a horizontal row of LEDs. If you need to know whether voltage is present at the field side, use a voltmeter on the terminal screws. The shaded blocks in Figure 15-7 show the limits specified by the IEC. The lines show the maximum and minimum V/I of the inputs in this module. The voltage/current curve in this graph shows that the input module is well within the IEC Type 1 limits. GIDDINGS & LEWIS Block I/O Manual 15-7 Block 24V DC 8 In/8 Out Module/J Figure 15-7 Input Characteristics Compared to IEC Standards U in Volts MIN MAX UH MAX 30 "ON" REGION 25 U NOM 24 20 UH MIN 15 (UT ) MAX TRANSITION REGION 10 UL MAX 5 (UT ) MIN 0 "OFF" REGION I in -5 mAMPS .5 2 4 10 6 8 12 14 15 I IT IH MAX MIN MIN INPUT CURRENT 15-8 Block I/O Manual GIDDINGS & LEWIS INPUT VOLTAGE Block 24V DC 8 In/8 Out Module/J IMPORTANT Switching devices can sometimes have a leakage current that ex- ceeds the IT (current allowed when off) of an input module. In or- min der to use such a device, an impedance (typically, a resistor) needs to be used in parallel with the input. For example, some of the newer proximity switches use two wires in- stead of three. The third wire was used for a power or ground line. Without the third wire, the switch is easier to install. However, it re- quires more leakage current in the off state to power its internal cir- cuitry. As a conservative estimate, use the following formula to calculate an external resistance value. It keeps the input voltage at or below 2.4V when the switching device is in the "off" state. 2.4V -- --- -- --- --- --- -- --- --- --- --- -- --- --- --- --- -- --- --- --- --- -- -- - ≥R Switch Leakage – 0.75mA If the switch leakage specification is ≤ 1.7 mA, then: 2.4V - - - --- --- --- -- --- --- --- --- -- --- - ≥ 2.5KΩ 1.7 – 0.75mA Use a resistor less than or equal to 2.5 KΩ. Be sure that the wattage is adequate for the resistor when the switching device is in the "on" state remembering that: 2 V ON P = --- --- --- - R GIDDINGS & LEWIS Block I/O Manual 15-9 Block 24V DC 8 In/8 Out Module/J 15.4 Specification Table Characteristic Block 24V DC 8 In/8 Out Module/J Specifications Function Monitors on/off states from eight DC voltage inputs and sources an external DC supply to eight loads Part number M. 1017.6042 Field side connector Two 18-pin connectors, screw terminals Protection of logic circuits Optical isolation between the logic and field sides, tran- sient suppression for the 24V external supply Logic side LEDs, module status Data In LED Data Out LED Configured LED Power LED Logic side LEDs, input status A yellow LED for each input Logic side LEDs, output status A yellow LED for each output Logic side LED, short circuit status A red LED lights to indicate a short circuit condition Module power requirements 100 mA from an external 24V DC supply (20 to 30V DC range) NOTE: 2.5A, 250 microsecond inrush at power on Input Section Input signals Nominal 24 VDC on, 0 VDC off, conforming to IEC Type 1 inputs per IEC 1131-2 UH Max (max. allowed voltage) 30 VDC IH Max (max. current @ 30 VDC) 7.5 mA UL Min Polarity independent Guaranteed on 15 VDC IH Min (min. current @ UH Min) 2.8 mA Guaranteed off 5 VDC IT Min (current allowed when off) .75 mA Time delay on 1 ms max. Time delay off 1 ms max. Output Section DC source requirements Nominal 24V DC; range 20 to 30V DC Output group One group of eight solid-state switches. The group uses an external DC supply. It must be referenced to SPG. Short circuit protection for the group Pulses output for about 130 µsec every 100 msec until short is removed 15-10 Block I/O Manual GIDDINGS & LEWIS Block 24V DC 8 In/8 Out Module/J Maximum current per group 4 A of continuous current for the group; each switch is rated at .5 A continuous Switch characteristics Solid-state switches Time delay on for resistive loads 50 µsec max Time delay off for resistive loads 50 µsec max Leakage current in off state 0.5 mA max Switch voltage, maximum ON 1 VDC max Surge current, maximum 25 A for about 130 µsec every 100 msec Response to scan loss All outputs are reset to the OFF state CE Marked Conforms to Directives 73/23/EEC, 89/336/EEC, 92/31/ EEC, 93/68/EEC by conforming to the following stan- dards: EN 50081-2:1993 EMC Generic Industrial Emissions EN 50082-2:1995 EMC Generic Industrial Immunity EN 61131-2:1994/A11:1996 Low voltage directive requirements for programmable controllers Operates with emissions below EN55011/ CISPR 11 Class A limits Immune to: Electrostatic discharge (4K V contact mode, 8K V air discharge) per EN61000-4-2 RF electromagnetic fields per EN61000-4-3, ENV 50141, and ENV50204 Electrical fast transients per EN61000-4-4 Magnetic fields per EN61000-4-8 Refer to the EMC Guidelines for more information. UL and C/UL Listed File No. E126417 NRAQ Programmable Controllers Operating temperature range 7° C to 55° C (45° F to 131° F) Storage temperature range -40° C to 85° C (-40° F to 185° F) Humidity 5 to 95%, non-condensing Physical size 4.05" wide x 4.825" high x 3" deep 102.9 mm x 122.6 mm x 76.2 mm Vibration (per IEC 68-2-6) 10-57 Hz (constant amplitude .15 mm) 57 - 2000 Hz (acceleration 2 g) Shock (per IEC 68-2-27) Four shocks per axis (15g/11 msec) GIDDINGS & LEWIS Block I/O Manual 15-11 Block 24V DC 8 In/8 Out Module/J NOTES 15-12 Block I/O Manual GIDDINGS & LEWIS Block Input/Output Analog Module (4 In 4 Out) 16 Block Input/Output Analog Module (4 In 4 Out) 16.1 Introduction The analog input section is designed to interface the PiC with voltage output devices to monitor such things as pressure, flow, speed, position, or temperature. This section has four independent analog conversion channels. Each channel converts a unipolar or bipolar analog input voltage or current into a 14- bit digital value. This data is transmitted to the PiCs CPU for processing. An external current sense resistor can be added for each channel for use with 0 to 20 mA or 4 to 20 mA devices. This analog input section of the module contains no user adjustable potentiometers or hardware switches. The analog output section has four independent D/A conversion channels. Each channel converts a 16-bit digital word into an analog output signal. The full range of the output signal is - 10 V to + 10 V, with a resolution of 1 part in 65,536. This analog output section of the module contains no potentiometers or hardware switches. Figure 16-1 Block Input/Output Analog Module (4 In 4 Out)) Communications Receive/Transmit IN OUT CONF PWR Communication/Status LEDs ® GIDDINGS & LEWIS INPUT/OUTPUT ANALOG Cover (shown open) Screw Terminal Connector GIDDINGS & LEWIS Block I/O Manual 16-1 Block Input/Output Analog Module (4 In 4 Out) 16.2 Connections All signals to/from the block input/output module must be connected to the screw terminal connectors through shielded twisted pair wires. See the discussion in the Hardware chapter on "Preventing electrical noise in data lines". There is one shield connection for each pair of inputs and one for each pair of outputs. All shield connections are interconnected within the module so they are the same point electrically. These pins are internally connected to SPG. The shield at the device end of the cable is not connected. Figure Figure 16-2 shows the assignments for all the screw terminal connections on the module. Figure 16-2 Connections for the Input/Output Terminals 1 2 3 45678 9 10 12 13 14 15 16 17 18 11 19 20 21 22 23 24 25 26 27 28 29 30 31 32 33 34 35 36 Analog Analog Analog NC Analog Analog NC NC NC + 24 DC NC Analog NC NC NC Analog Analog NC Output Input Input Output Output Input Input Output Channel Channel Channel Channel Channel Channel Channel Channel 3 + 2 + 4 + 1 + 2 + 1+ 3 + 4 + Analog Shield Analog Shield Analog Analog Shield Analog Analog Shield Analog Shield Analog Shield Chassis Shield Shield 0V Output Output Output Input Output Input Input Input Channel Channel Channel Channel Channel Channel Channel Channel 1 - 2 - 3 - 4 - 1 - 4 - 2 - 3 - NC - no connection 16-2 Block I/O Manual GIDDINGS & LEWIS Block Input/Output Analog Module (4 In 4 Out) When connecting an analog voltage output device to the module, the positive wire of the twisted pair goes to the + screw terminal and the negative wire goes to the - screw terminal. Figure 16-3 illustrates these connections for channel two. Figure 16-3 Voltage Input Connections 1 2 345 67 89 10 12 14 15 16 17 18 11 13 19 20 21 22 23 24 25 26 27 28 29 30 31 32 33 34 35 36 Ch2R Ch 2+ Shield Ch 2- To SPG +- Voltage Signal Source GIDDINGS & LEWIS Block I/O Manual 16-3 Block Input/Output Analog Module (4 In 4 Out) When using a 0 to 20 mA or 4 to 20 mA current output device, the positive wire of the twisted pair is connected to the + input and the negative wire is connected to the - input. In addition, an external 250 Ω resistor is connected to the same inputs as illustrated below. Figure 16-4 Current Input Connections (0 to 20 or 4 to 20 mA) 250 Ω 4 1 2 5 678 9 10 12 14 15 16 17 18 3 11 13 19 20 22 23 24 25 26 27 28 29 30 31 32 33 34 35 36 21 Ch2R Shield Ch 2+ Ch 2- To SPG +- Current Signal Source 0 to 20 mA or 4 to 20 mA +- Power Supply NOTE: The accuracy of the currrent input can be no more accurate than the accuracy of the 250 Ω resistor used. 16-4 Block I/O Manual GIDDINGS & LEWIS Block Input/Output Analog Module (4 In 4 Out) An alternative method of connecting a two wire 4 to 20 mA current device is shown in Figure 16-5. Figure 16-5 Current Input Connections (4 to 20 mA) 250 Ω 4 1 2 3 5 678 9 10 11 12 13 14 15 16 17 18 19 20 22 23 24 25 26 27 28 29 30 31 32 35 36 33 34 21 Ch2R Ch 2+ Shield Current Signal Ch 2- Source 4 to 20 mA +Input from power supply Output + Power Supply - To SPG GIDDINGS & LEWIS Block I/O Manual 16-5 Block Input/Output Analog Module (4 In 4 Out) Figure 16-6 illustrates an example of wiring an external potentiometer to the module using twisted pair wire. Figure 16-6 Adding an External Potentiometer 4 1 2 56 78 9 10 12 13 14 15 16 17 18 3 11 19 20 22 23 24 25 26 27 28 30 31 29 32 33 34 35 36 21 Ch2R Ch 2+ Shield Ch 2- 1K to 50K Pot To SPG + - +10 Volt Adjustable Regulated Power Supply 16-6 Block I/O Manual GIDDINGS & LEWIS Block Input/Output Analog Module (4 In 4 Out) 16.2.1 Analog Output Receiving Devices It was assumed in Figure 16-2 that all the receiving device inputs were differential. It is possible (but not recommended) to connect the single ended output from this module to a single-ended input device. Figure 16-7 shows the difference between the two types of connections. Note that one wire in the twisted pair is connected to the 0 V terminal on the receiving device. This 0V terminal must be referenced to the SPG through the device's ground connection. It is recommended that the receiving device have a differential input for best noise immunity. Figure 16-7 Differential and Single-Ended Receiving Devices Differential Input Single-Ended Input GND GND Recieving Devices Ch2+ Ch 2- Ch4+ 0V To SPG To SPG Ch 2- Ch 4- Ch2R Ch4R Ch 2+ Ch 4+ Shield Shield 8 4 1 2 567 910 12 14 15 16 17 18 3 11 13 19 20 23 24 26 27 28 29 30 31 22 25 32 33 34 35 36 21 0V +24V Power Supply To SPG GIDDINGS & LEWIS Block I/O Manual 16-7 Block Input/Output Analog Module (4 In 4 Out) 16.2.2 Communications Connections There are two 5-pin communications connectors and four logic LEDs on the top of the block I/O module as shown in Figure 16-8. Figure 16-8 Pinouts for Communication Connectors In (from CPU) Out (to next block I/O module Pin # 5 4 3 2 1 Pin # 5 4 3 2 1 Communications Receive/Transmit IN OUT CONF PWR ® GIDDINGS & LEWIS 16.2.2.1 LEDs LED Color State Definition DATA IN Yellow FAINT Data being passed through the block module BRIGHT No activity through the block mod- or OFF ule DATA Yellow FAINT Data is being passed through the OUT block module BRIGHT No activity through the block mod- or OFF ule CONFG Green ON Communication established with this block I/O module OFF Communication not established PWR Green ON Internal +5V logic power supply OK OFF No external 24V applied or internal 5V logic supply not OK 16-8 Block I/O Manual GIDDINGS & LEWIS Driver - (twisted pair output) Driver + (twisted pair output) Shield Receiver - (twisted pair input) Receiver + (twisted pair input) Receiver - (twisted pair input) Receiver + (twisted pair input) Shield Driver - (twisted pair output) Driver + (twisted pair output) Block Input/Output Analog Module (4 In 4 Out) 16.3 Theory of Operation A 14- bit A/D converter samples each channel sequentially. These values are stored in memory on the module so that any channel value can be read by a PiC CPU while the A/D converter is processing another channel sample. Each channel has a range of - 10V to + 10V. All inputs are differential and filtered. The PiC CPU module sends the output module a 16-bit digital word for each channel used. Each digital word is converted to a corresponding voltage within the range of ±10 V. The voltage is buffered and brought out to a pair of screw terminal connections as a single ended voltage output. However, each output line has series inductance to improve noise immunity. For safety reasons, all outputs are automatically reset to 0 V when a scan loss condition occurs. GIDDINGS & LEWIS Block I/O Manual 16-9 Block Input/Output Analog Module (4 In 4 Out) 16.4 Specification Table Block Input/Output Analog Module (4 In 4 Out) Characteristic Specification Function Converts an analog input signal into a 14-bit digital word for each of four channels. Converts a 16-bit digital word into a ±10 V analog signal for each of four channels. Part number M.1301.4145 Output channels 4 Input channels 4 Resolution 14 bits, or 16384 steps over the full input range, 16 bits, or 65536 steps over the full output range. Voltage Range Output ±10 V, Input ±10 V Maximum Output Current (1KΩ ±10 mA load) Power on output voltage 0V ±100 mV Scan loss output voltage 0V ±100 mV Accuracy Analog Output ±0.375% of FSR Drift ± 50ppm/°C, Analog Input ±.25 % of FSR Sample Rate 800 µsec (200 µsec per channel) Update rate 200 µsec (50 µsec per channel) Common mode filter 3 dB @ 10 KHz Differential mode filter 3 dB @ 475 Hz Field side connector Two 18 pin card edge connectors, screw terminals Logic side LEDs, module status Data In LED Data Out LED Configured LED Power LED Module power requirements 120 mA from an external 24V DC supply (20 to 30V DC range) 16-10 Block I/O Manual GIDDINGS & LEWIS Block Input/Output Analog Module (4 In 4 Out) CE Marked Conforms to Directives 73/23/EEC, 89/336/EEC, 92/31/EEC, 93/68/EEC by conforming to the following standards: EN 50081-2:1993EMC Generic Industrial Emissions EN 50082-2:1995EMC Generic Industrial Immunity EN 61131-2:1994/A11:1996 Low voltage directive requirements for programmable controllers Operates with emissions below EN55011/ CISPR 11 Class A limits Immune to: Electrostatic discharge (4K V contact mode, 8K V air discharge) per EN61000-4-2 RF electromagnetic fields per EN61000-4-3, ENV 50141, and ENV50204 Electrical fast transients per EN61000-4-4 Magnetic fields per EN61000-4-8 Refer to the EMC Guidelines for more information. UL and C/UL Listed File No. E126417 NRAQ Programmable Controllers Operating temperature range 7° C to 55° C (45° F to 131° F) Storage temperature range -40° C to 85° C (-40° F to 185° F) Humidity 5 to 95%, non-condensing Physical size 4.05" wide x 4.825" high x 3" deep 102.9 mm x 122.6 mm x 76.2 mm Vibration (per IEC 68-2-6) 10-57 Hz (constant amplitude .15 mm) 57 - 2000 Hz (acceleration 2 g) Shock (per IEC 68-2-27) Four shocks per axis (15g/11 msec) GIDDINGS & LEWIS Block I/O Manual 16-11 Block Input/Output Analog Module (4 In 4 Out) NOTES 16-12 Block I/O Manual GIDDINGS & LEWIS block output 24V DC source 3-1 INDEX connections 3-2 Symbols LEDs 3-1, 6-1 specifications 3-7 ±10V DC theory of operation 3-6 block output 13-1 block output 4-20mA ±10V DC block output LEDs 12-4 connections 13-2 specifications 12-6 specifications 13-6 block output 4-20mA input theory of operation 13-5 connections 12-2 A block output 4-20mA Module theory of operation 12-5 analog output receiving devices 13-4 block output stepper/input encoder/input B 24VDC theory of operation 10-17 block ±10V DC output block output4-20mA LEDs 13-3 connections 12-4 block 24V DC 8/8 5-1 block resolver 9-7 LEDs 5-1, 15-1 connections 9-6 specifications 5-10, 15-10 LEDs 9-6 block 24V DC 8/8/J 15-1 block stepper 10-2 block 4-20mA output 12-1 connections 10-3, 10-16 block analog input 11-1 LEDs 10-16 connections 11-2, 11-4, 11-7, 16-2, 16-4, specifications 10-22 16-8 theory of operation 10-17 analog output device 11-3, 16-3 LEDs 11-7, 16-8 C specifications 11-9, 16-10 clamping diode 12-5 theory of operation 11-8, 16-9 common source block I/O connections 10-7 connections 3-4, 4-4, 5-5, 6-4, 7-6, 8-4, drive inputs 10-7 14-5, 15-5 common terminal 7-2 guidelines 2-1 communications LEDs 3-4, 4-4, 5-5, 6-4, 7-6, 8-4, 14-5, connections 15-5 ±10V DC block output 13-3 safety 2-2 block analog input 11-7, 16-8 troubleshooting guide 2-6 block I/O 3-4, 4-4, 5-5, 6-4, 7-6, 8-4, wiring guidelines 2-3 14-5, 15-5 block input 24V DC 4-1 block output 4-20mA 12-4 connections 4-2, 14-2 block resolver 9-6 specifications 4-7, 14-8 block stepper 10-16 theory of operation 4-5, 5-7, 14-6, 15-7 connections block input 24V DC/J 14-1 ±10V DC block output 13-2 block input connections 10-15 block analog input 11-2, 16-2 block input/output analog 16-1 block input 10-15 block output ±10V DC block input 24V DC 4-2, 14-2 connections 13-3 GIDDINGS & LEWIS Block I/O Manual IND-1 block output 24V DC source 3-2 I block output 4-20mA 12-2 IEC 4-5, 5-7, 8-5, 10-20, 14-6, 15-7 block stepper 10-3 incremental input 120V AC 8-2 encoder 10-18 output 120/240V AC 6-2 inductive load 12-5 relay output 7-2 internal diode 3-5, 5-6, 15-6 counter protection from 3-5, 5-6, 15-6 up/down 10-19 input 120V AC 8-1 current connections 8-2 leakage 4-6, 5-9, 8-6, 10-21, 14-7, 15-9 LEDs 8-5 sinking 4-2, 5-4, 14-3, 15-4 specifications 8-7 sourcing 4-2, 5-4, 14-3, 15-4 theory of operation 8-5 current output device 11-4, 16-4 input sensitivity current-limiting resistor 10-5 block analog input 11-8 D inspection safety 1-4 D/A conversion channels internal diode ±10V DC block output 13-1, 16-1 and inductive loads 3-5, 5-6, 15-6 differential drivers 10-14 connections 10-10 K inputs 10-10 kickback 3-5, 5-6, 15-6 diode L clamping 12-5 input 10-5 latch distribution of block I/O modules 2-5 counter value 10-19 drivers LEDs differential 10-10, 10-14 block ±10V DC output 13-3 encoder 10-14 block 24V DC 8/8 5-1, 15-1 recommended 10-14 block analog input 11-7, 16-8 single-ended 10-8, 10-14 block I/O 3-4, 4-4, 5-5, 6-4, 7-6, 8-4, 14- 5, 15-5 E block input 24V DC 4-5, 5-7, 14-6, 15-7 electrical service & maintenance safety 1-6 block output 24V DC source 3-1, 6-1 encoder block output 4-20mA 12-4 drivers 10-14 block resolver 9-6 incremental 10-18 block stepper 10-16, 10-20 quadrature 10-18, 10-19 input 120V AC 8-5 F relay output 7-1, 7-8 loss of feedback feedback 9-3 detection 9-7, 10-14 frequency 10-19 M G manual cleaning procedure 1-7 grounding modules protective earth 1-2 block 24V DC 8/8 5-1 guidelines block 24V DC 8/8/J 15-1 block I/O 2-1 IND-2 Block I/O Manual GIDDINGS & LEWIS block 4-20mA output 12-1 differential 13-4 block analog input 11-1 single-ended 13-4 block input 24V DC 4-1 reference phase output 9-7 block input 24V DC/J 14-1 relay output 7-1 block input/output 16-1 connections 7-2 block output ±10V DC 13-1 LEDs 7-1, 7-8 block output 24V DC source 3-1 specifications 7-9 block stepper 10-2 relays input 120V AC 8-1 form A type 7-1, 7-2 relay output 7-1 form C type 7-1 resolver block input 9-1 common terminal 7-2 normally closed 7-2 N normally open 7-2 noise resistive load 3-5, 5-6, 15-6 filter resistor block analog input 11-8 current sensing 11-1, 16-1 normally closed 7-2, 7-7 current-limiting 10-5 normally open 7-2, 7-7 pull-up 10-9 resolver block input 9-1 O specifications 9-8 operation theory of operation 9-7 safety 1-5 rotor coil 9-7 opto-coupler S connections 10-6 drive inputs 10-5 safety output 120/240V AC cleaning 1-7 connections 6-2 electrical service & maintenance 1-6 specifications 6-6 inspection 1-4 theory of operation 6-5 operation 1-5 signs 1-2 P system 1-1 peak reverse voltage 3-5, 5-6, 15-6 safety concerns procedure block I/O 2-2 manual cleaning 1-7 signal protective earth pairs 9-2, 10-12 grounding 1-2 sine wave 9-1, 9-7 pull-up resistor 10-9 square wave 10-18 signs Q safety 1-2 quadrature sine wave signal 9-1, 9-7 counting pulses 10-19 single-ended drivers 10-8, 10-14 encoder 10-18, 10-19 specifications phase output 9-7 ±10V DC block output 13-6 R block 24V DC 8/8 5-10, 15-10 block analog input 11-9, 16-10 receiving devices block input 24V DC 4-7, 14-8 analog output 13-4 GIDDINGS & LEWIS Block I/O Manual IND-3 block ouput 4-20mA 12-6 V block output 24V DC source 3-7 voltage block stepper 10-22 peak reverse 3-5, 5-6, 15-6 input 120V AC 8-7 W output 120/240V AC 6-6 relay output 7-9 warning labels 1-3 resolver block input 9-8 wiring square wave signal 10-18 ±10V DC block output 13-2 stator coil 9-7 block analog input 11-2, 16-2 block input 24V DC 4-2, 14-2 T block output 24V DC source 3-2 troubleshooting block output 4-20mA 12-2 block I/O 2-6 input 120V AC 8-2 U output 120/240V AC 6-2 relay output 7-2 up/down counter 10-19 wiring guidelines block I/O 2-3 IND-4 Block I/O Manual GIDDINGS & LEWIS
Frequently asked questions
What makes Elite.Parts unique?

What kind of warranty will the M.1017.3095 have?

Which carriers does Elite.Parts work with?

Will Elite.Parts sell to me even though I live outside the USA?

I have a preferred payment method. Will Elite.Parts accept it?

Why buy from GID?
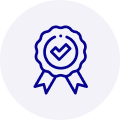
Quality
We are industry veterans who take pride in our work
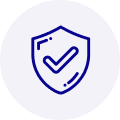
Protection
Avoid the dangers of risky trading in the gray market
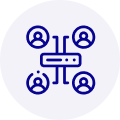
Access
Our network of suppliers is ready and at your disposal
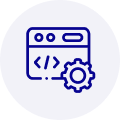
Savings
Maintain legacy systems to prevent costly downtime
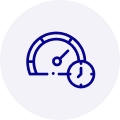
Speed
Time is of the essence, and we are respectful of yours
What they say about us
FANTASTIC RESOURCE
One of our top priorities is maintaining our business with precision, and we are constantly looking for affiliates that can help us achieve our goal. With the aid of GID Industrial, our obsolete product management has never been more efficient. They have been a great resource to our company, and have quickly become a go-to supplier on our list!
Bucher Emhart Glass
EXCELLENT SERVICE
With our strict fundamentals and high expectations, we were surprised when we came across GID Industrial and their competitive pricing. When we approached them with our issue, they were incredibly confident in being able to provide us with a seamless solution at the best price for us. GID Industrial quickly understood our needs and provided us with excellent service, as well as fully tested product to ensure what we received would be the right fit for our company.
Fuji
HARD TO FIND A BETTER PROVIDER
Our company provides services to aid in the manufacture of technological products, such as semiconductors and flat panel displays, and often searching for distributors of obsolete product we require can waste time and money. Finding GID Industrial proved to be a great asset to our company, with cost effective solutions and superior knowledge on all of their materials, it’d be hard to find a better provider of obsolete or hard to find products.
Applied Materials
CONSISTENTLY DELIVERS QUALITY SOLUTIONS
Over the years, the equipment used in our company becomes discontinued, but they’re still of great use to us and our customers. Once these products are no longer available through the manufacturer, finding a reliable, quick supplier is a necessity, and luckily for us, GID Industrial has provided the most trustworthy, quality solutions to our obsolete component needs.
Nidec Vamco
TERRIFIC RESOURCE
This company has been a terrific help to us (I work for Trican Well Service) in sourcing the Micron Ram Memory we needed for our Siemens computers. Great service! And great pricing! I know when the product is shipping and when it will arrive, all the way through the ordering process.
Trican Well Service
GO TO SOURCE
When I can't find an obsolete part, I first call GID and they'll come up with my parts every time. Great customer service and follow up as well. Scott emails me from time to time to touch base and see if we're having trouble finding something.....which is often with our 25 yr old equipment.
ConAgra Foods