GEMS SENSORS 85350
Specifications
General
20VA 120-240VAC 20W
Datasheet
Extracted Text
® SureSite Magnetic Liquid Level Indicator Instruction Bulletin No. 177664-1 (Rev. F) Section 1: Weldments Thank you for purchasing the GEMS SureSite Magnetic Level Indicator. Please read this document prior to installing your SureSite and store it where it may be readily referred to for familiarization and maintenance purposes. If you require any additional information, you are welcome to call GEMS at the number shown below. 1-800-321-6070 (Outside of the Continental U.S., call 860-747-3000) Record the Part Number of your SureSite here to use when ordering spare or replacement parts: Part Number:____________________ SureSite Operating Principle The liquid level of a tank is made visible, even at great distances, Magnetic Flags through the use of a shock and vibration-proof magnetic level indica- Flag Channel (Plain Side Out) tor that employs “flags” arranged within a specially constructed exter- nal housing: the flag assembly. The two sides of each pivoting flag Liquid are marked with contrasting colors. A permanent magnet is encapsu- Magnetic lated inside each flag and forms a secure magnetic interlock with the Float adjacent flags. As the liquid level rises, a float equipped with a per- manent magnet causes each of the flags to begin rotating in turn. This action exposes the contrasting (fluid level indicating) color on the other side of the flag. As the float and liquid level rise, each flag below the level of the float completes a 180 degree rotation, while Magnetic Flags remaining magnetically interlocked with the other lower flags. Together, (Colored the rotated flags display a band or column of color, the height of which Side Out) corresponds with the liquid level within the tank. An exclusive feature of the SureSite is the magnetic guide that is integrated into the flag assembly. This magnetic attraction ensures that the float is always aligned for optimum performance and exactness, regardless of any Weldment shock, vibration, or rapid change to the level of fluid in the tank. Standard and Mini-SureSites are supplied with the floats packed either separately, or securely strapped to the unit. Top-mounted SureSites are typically supplied with the floats installed and secured by a support tube. The float supplied with each unit has been de- signed to the specific gravity of the fluid being monitored, so that the permanent bar magnet will always seek and indicate the fluid surface. Tank Because of the attraction of the permanent bar magnet in the float and the patented magnetic guide, the SureSite flag assembly can be rotated to a position which will allow for optimum viewing. (See the Maintenance Section on page 5 for instructions on how to rotate your SureSite flag assembly.) - 1 - Important! Read the following instructions completely - BEFORE installing the SureSite. Installation Precautions and Preparation Failure to observe these precautions could affect the operation of your unit. 1. When locating the tank ports for the SureSite, make sure that no strong magnetic fields or magnetic materials (such as railings, protective cages, I-beams, etc.) will be any closer than 6 inches (153 mm) from the SureSite. 2. Make necessary efforts to ensure that all tank-side modifications and equipment; i.e., the mating flanges, NPT ports or shut-off valves (if used) will align properly with the SureSite connections. Improper alignment could cause distortion and may damage welds and compromise the integrity of the SureSite and/or the tank. 3. After any necessary tank modifications are completed, the tank should be cleaned to remove contaminants. This will ensure that the installation is free of foreign particles; especially those which could be magnetic and which could impair the performance of the SureSite. 4. Do not begin the installation of the SureSite until all necessary tools and materials are obtained. (Such as mating flange gaskets, bolting hardware, etc. ) 5. Gasket material typically supplied with the standard SureSite unit is either Viton or nitrile rubber, Garlock 3000 TM style. Higher pressure units are typically supplied with Flexitallic gaskets. For replacement gaskets, please consult GEMS Sensors for your specific material type. 6. All supplied flag assembly clamps are intended to be installed with a torque on the clamp screw not to exceed 5 lb.-inches. Installation Caution Handle the SureSite with care to avoid damaging the threaded areas, flange surfaces, etc. Note If you have a top-mounted alloy or top-mounted plastic SureSite, skip to Page 4 for instructions. For Standard SureSites (Alloy, Mini and Plastic) 1. Remove the protective packing materials from your SureSite. 2. Position the unit horizontally on a level surface. 3. Unpack the float assembly or, with the aid of a wire-cutter or similar device, remove the strapping that secures the float to the exterior of the SureSite Unit. - 2 - Warning D0 NOT: 1) Hold the SureSite in a vertical position or 2) Drop the float assembly into the unit. Avoid this or any action which could damage or dent the float. Such damage could cause the float to crush under normal working pressures. TOP Float Float TOP Float Weldment Weldment TOP Flange Flange Weldment Threaded Remove Bolts Remove Bolts End Cap Standard SureSite Mini SureSite Plastic SureSite 4. Remove the end cap or flange attaching bolts, as indicated in the appropriate drawing. Then remove the end cap or flange. 5. With the unit still in a horizontal position, insert the float assembly into the weldment, with the “TOP” indication on the float assembly moving in the same direction as the “UP” arrows that are located on each side of the externally mounted flag assembly. 6. With the gasket or O-ring properly positioned, reassemble the end cap or flange to the weldment. Tighten the end cap or flange bolts securely, using the proper recommended torque value as supplied in Figure A, page 5. 7. Slowly raise the top end of the SureSite, while the bottom end remains on the level surface, permitting the float to slowly slide to the bottom, avoiding any sudden impact damage to the float assembly. 8. Move the SureSite to the tank and position the unit with the end marked “TOP” pointing upwards. Install any 2 necessary mounting gaskets or seals , and align the mating port flanges, NPT’s or connections of the tank with those of the SureSite. DO NOT ATTEMPT TO FORCE ALIGNMENT. To do so may damage the welds or compromise the integrity of the SureSite. While following standard practices and procedures, tighten the flange bolts, NPT’s or connections. Recommended torque values are supplied in Figure A, page 5. 9. Before Filling the Tank . . . . Be sure that the installation is free of foreign particles, especially any that are magnetic. Check that all connections are secure. A hydrostatic pressure test of the complete assembly is recommended. NOTE GEMS recommends that you include at least one support bracket in your installation for SureSite units greater than 10 feet (120 inches, 3048 mm) in length. Depending on the specific installation, a load-bearing support at the base of the SureSite may be beneficial. ______________________________________ 2 Gaskets or seals for the port flanges are not supplied with the SureSite. - 3 - Installation for Top-Mounted Alloy SureSites 1. After removing any protective packing materials from your Float top-mounted SureSite and positioning it horizontally on a level surface, remove and discard the protective cap from the bottom of the SureSite and carefully withdraw the cardboard support tube. Float Chamber 2. Slowly raise the top end of the SureSite, while the bottom end remains on the level surface; permitting the float to slowly slide to the bottom and avoiding any sudden impact damage to the float assembly. Cardboard 3 Support Tube 3. Position the necessary gasket or O-ring seal on the tank mounting flange and align the unit so that the bolt holes of the mating flange match. The indicating face of the flag assembly should be directed towards your desired point of observation. Do not attempt to force alignment. To do so may damage the welds or compromise the integrity of the SureSite. Protective 4. While following standard practices and procedures, tighten the Cap flange bolts with the recommended torque values as supplied in Figure A, page 5. Float Installation for Top-Mounted Plastic SureSites 1. Remove the threaded stop pin from the bottom of the top-mounted Float SureSite and slowly withdraw the support tube. Reinstall the stop Chamber pin. 2. Slowly raise the top end of the SureSite, while the bottom end remains on the level surface; permitting the float to slowly slide to the bottom and avoiding any sudden impact damage to the float assembly. Cardboard 3 3. Position the necessary gasket or O-ring seal on the tank mounting Support Tube flange and align the unit so that the bolt holes of the mating flange match. The indicating face of the flag assembly should be directed towards your desired point of observation. Do not attempt to force alignment. To do so may damage the welds or compromise the Stop integrity of the SureSite. Pin 4. While following standard practices and procedures, tighten the flange bolts with the recommended torque values as supplied in Figure A, page 5. _____________________________ 3 Gaskets or seals for the port flanges are not supplied with the SureSite. - 4 - Figure A (Recommended Torque Values are for Lubricated Threads, Only) Fastener Nominal Indicator Type Torque Value Description Size 70 - 80 Lb.-Inches NTE (Not to Exceed) 120 Lb.-Inches 3/8 Inch 1/2 Inch 30 Lb-Feet 5/8 Inch Standard Alloy, 60 Lb-Feet Bolt, Nut Top-Mount Alloy 3/4 Inch 100 Lb-Feet 7/8 Inch 150 Lb-Feet 1 Inch 250 Lb-Feet 1-1/8 Inch 350 Lb-Feet 15-20 Lb-Feed (Valid for bolts with flat washers under both bolt- Standard Plastic, Bolt, Nut heads and nuts) Top-Mount Plastic Mini Bolt, Nut 70 - 80 Lb-Inches 5/16 Inch Flag Installation General Notes Under normal circumstances, it should not be necessary to reposition the flag assembly on your SureSite. However, if you find it desirable or necessary to reposition the flag assembly, we strongly recommend that you first mark the distance from the top of the weldment to the top of the flag assembly. Before securing the flag assembly in a new radial position, ensure that the distance from the top of the flag assembly to the top of the weldment is the same as the previously noted dimension. Making a temporary or permanent mark on the weldment can ease the process. Maintenance The only maintenance typically required is to ensure that the internal walls of the weldment and the float are free of foreign matter. This may be accomplished by removing the float assembly from the unit and wiping both the float and the inside wall of the float chamber or weldment. Any maintenance interval is to be established by the user of the SureSite and would depend upon the characteristics of the application. Maintenance could coincide with tank cleaning or flushing. Float Installation Mini SureSite Float: (To set magnet position, please go to page 8.) To accomplish the removal and subsequent reinstallation of the float assembly, follow the appropriate instructions provided on page 6 for the SureSite type and mounting configuration you have selected. Caution Make sure that the tank is depressurized and that liquid has been emptied prior to removal of the float assembly. - 5 - SureSite with Side Connections (Alloy, Mini and Plastic) The float assembly can be removed without disturbing the mounting of the SureSite unit to the tank. 1. Carefully remove the end cap (access to the float assembly) which may be retained by bolts, NPT threads or held in place by setscrews. The float assembly should be resting on the end cap as it is being lowered. Support the float assembly while setting the end cap aside. Note: For units supplied with top float access, the float assembly must be extracted from the top of the weldment by engaging the hooking ring provided on the top of the float. 2. Withdraw the float assembly from the unit, exercising caution not to damage the float. Note the “TOP” indication marking on the float assembly. 3. Wipe down the weldment and the float assembly with a clean, lint-free cloth. 4. Carefully reinsert the float assembly into the weldment, ensuring that the “TOP” indication marking on the float assembly is positioned in the same manner as when it was removed. 5. Remove the old gasket or O-ring from the end cap assembly and replace it with a new gasket or O-ring. 6. With the new gasket or O-ring properly positioned, reassemble the end cap assembly to the weldment. Tighten the end cap or secure flange fasteners, using the proper recommended torque value, as supplied in Figure A -page 5. SureSite with Top and Bottom Connections (Alloy, Mini and Plastic) The SureSite unit should be adequately supported when removing it from the tank. 1. Disconnect the top and bottom flange/socket or NPT connections. 2. Remove any other fasteners that retain the unit and/or support bracket(s) to the tank. 3. Remove the SureSite unit from the tank, while avoiding any motion that will cause damage to the float assembly. 4. With the SureSite placed in a horizontal position on a level surface, remove the end cap or flange and withdraw the float assembly from the unit; noting the relative position of the portion of the float assembly marked “TOP”. 5. Wipe down the weldment and the float assembly with a clean, lint-free cloth. 6. Carefully reinsert the float assembly into the bottom of the float chamber or weldment, ensuring that the “TOP” indication marking on the float assembly is positioned the same as when it was removed. 7. Remove the old gasket or O-ring from the end cap assembly and replace it with a new gasket or O-ring. 8. With the new gasket or O-ring properly positioned, reassemble the end cap assembly to the bottom of the weldment. Tighten the end cap or flange bolts securely, using the proper recommended torque value, as supplied in Figure A, page 5. 9. Complete installation of the unit by following the Installation Instructions for Standard SureSites (Page 3, Steps 7, 8 and 9). - 6 - SureSites Mounted on Top of Tank The construction of top-mounted SureSites varies with the material selected, and each requires a slightly different procedure than those preceding for “wipe-down”. It is advisable to mark or index mating flanges and other parts so that the relative positions of the components are maintained upon reassembly. Alloy 1. Remove the attaching bolts that secure the SureSite unit to the top of the tank. Lift the SureSite vertically from the tank and set it aside on a level work area, in horizontal position. Exercise caution so that the float assembly will not be dented or damaged. Remove any gasket material from the tank and SureSite mounting flanges. Flag External Assembly Weldment 2. Remove the attaching bolts securing the external weldment (with the attached flag assembly) to the mounting flange that was secured to your tank, and carefully remove the weldment and gasket from the float chamber, taking care not to damage the sphere-shaped magnet carrier. 3. While lightly supporting the magnet carrier, remove the upper (first) cotter pin attaching it to the float rod. Set the magnet carrier and cotter pin aside. Attaching Bolts 4. Remove the lower (second) cotter pin from the float rod and set it aside. Gasket 5. Withdraw the float and float rod from the bottom of the float chamber. 6. Wipe the inside of the float chamber and the exposed float assembly with a clean, lint-free cloth. Magnet Carrier 7. After completing the “wipe-down” cleaning, the unit can be reassembled. Cotter Pins Float Rod 8. Obtain new gaskets for: a) Installation between the weldment and float 1 2 chamber , and b) Installation between the mounting flange of your tank and that of the unit. Obtain new cotter pins for the float rod. 9. Insert the float assembly and rod into the float chamber, passing the float Mounting rod up through the opening in the mounting flange. Secure the rod to the Flange float chamber by installing a cotter pin in the lower (second) hole and securing it. Reinstall the magnet carrier to the float rod. Insert and Float secure a cotter pin in the upper (first) hole to retain it. Chamber Float 10. Complete the remainder of the reassembly and installation by reversing the process described in Steps 1 and 2. Refer to Figure A, page 5 for Protective recommended torque values for bolts. Use a new gasket: a) Between Cap the weldment and mounting flange of the float chamber, and b) Between the mounting flange of your tank and that of the SureSite unit. _____________________________________________ 1 Contact Gems Sensors for spare or replacement parts 2 Customer-Supplied - 7 - Plastic 1. Remove the attaching bolts that secure the SureSite Flag unit to the top of the tank and lift the indicator unit Assembly (with its float chamber) vertically from the tank. Set External Weldment it aside on a level work area, horizontally. Handle the float assembly with care to prevent damage. Remove any gasket material from the tank and Magnet Carrier SureSite mounting flanges. 2. Unscrew and remove the stop pin from the bottom of Mounting the float chamber. Flange 3. Carefully withdraw the float, float rod, and attached magnet assembly from the bottom of the float chamber. 4. Wipe the inside of the float chamber and the exposed float assembly with a clean, lint-free cloth. Float Chamber 5. After completing the “wipe-down” cleaning, the unit Float can be reassembled. Obtain a new gasket for installation between the mounting flange of your tank Stop Pin and that of the SureSite unit. Prepare the mating surfaces for reassembly. 6. Insert the float assembly and rod into the float chamber, passing the magnet assembly and float rod Hold the float vertical. A paper clip will attach to the up through the bottom of the float chamber. Secure magnet to show its position. Adjust the magnet the float assembly and rod to the float chamber by position by gently tapping the end of the float. reinstalling the stop pin. Basic Float Part No. 807100 Basic Float Part No. 807200 (Liquid Specific Gravity Range: 0.8 to 1.2) (Liquid Specific Gravity Range: 1.5 to 3.8) Liquid Liquid Float “X” Float Part No. Float “X” Float Part No. Specific Specific Part Number Dimension W/Lift Ring Part Number Dimension W/Lift Ring Gravity Gravity 85206 0.8 5” 810919 88111 1.9 2” 810928 83453 0.9 4.5” 810917 801708 1.5 2.6875” 810927 85208 1 4” 810916 85209 1.2 3.312” 810915 84158 0.85 4.75” 810918 TOP 807200 “X” Æ Dimension TOP 807100 “X” Dimension Æ - 8 - Æ Æ Troubleshooting Condition Possible Cause Solution Install float No Float Clean the float and weldment Float sticking, due to contamina- No change in Media tion in the fluid level Level Indication Remove the ferrous materials Float attracted, due to external from close proximity ferrous materials within close proximity. Replace the float The float is damaged Remove blockage Port is blocked Clean the float and weldment Float attracted, due to contami- nation in the media Remove the ferrous materials Float sticking, due to external Incorrect Fluid Level from close proximity ferrous materials within close Indication proximity Replace the float The float is damaged Invert the float The float is upside down Rotate the flag assembly 180 Flag assembly is upside-down. Incorrect Color degrees (with the end marked (The wrong color is indicating the Indicating Fluid Level “TOP” uppermost) liquid level) Note: Increased viscosity increases the response time of the SureSite indicator Warnings/Cautions 1. The SureSite Magnetic Level Indicator must be maintained and installed in strict accordance with this Instruction Bulletin. Failure to observe this warning could result in serious injuries or damages. 2. The liquids to be monitored must be compatible with the materials of construction. Specifications of these materials will be provided upon request. - 9 - âââââ SureSite Magnetic Liquid Level Indicator Installation, Operation and Maintenance Bulletin No. 177664-2 (Rev. B) Section 2: Switches Operation The SureSite Switch Module, available for use with the SureSite Magnetic Liquid Level Indicator, is a sealed assembly containing a magnetically actuated “latching-reed” switch assembly. The reed switch is actuated by the movement of the magnet contained in the SureSite float. The design of the reed switch permits the switch module to perform as either a “normally open” or “normally closed” switch. When installed with the lead wires (or junction box) installed at the top, the switch module is “normally open” and the reed switch will close with the rising fluid level in the tank; remaining closed until a falling fluid level in the tank causes the float to drop below the indicating position, opening the reed switch. When installed with the lead wires (or junction box) at the bottom, the switch module is “normally closed” and the reed switch will open with the rising fluid level in the tank, and remain open until a falling fluid level in the tank causes the float to drop below the indicating position, closing the reed switch. (See sketches below) For electrical schematics of the switch module, please refer to the Wiring Diagrams, located on pages 5 and 6. - Normally Closed Operation - - Normally Closed Operation - - Normally Closed Operation - - Normally Closed Operation - - Normally Closed Operation - - Normally Open Operation - - Normally Open Operation - - Normally Open Operation - - Normally Open Operation - - Normally Open Operation - Lead W Lead W Lead W Lead W Lead Wires and Junction Box Positioned at T ires and Junction Box Positioned at T ires and Junction Box Positioned at T ires and Junction Box Positioned at T ires and Junction Box Positioned at Top op op op op Lead W Lead W Lead W Lead W Lead Wires and Junction Box Positioned at Bottom ires and Junction Box Positioned at Bottom ires and Junction Box Positioned at Bottom ires and Junction Box Positioned at Bottom ires and Junction Box Positioned at Bottom Installation o General: The SureSite switch module must be mounted 180 opposite the flag assembly of the SureSite Magnetic Level Indicator and within its operating range. The installation of the switch module varies, depending on the switch module housing and the type of SureSite Magnetic Level Indicator. The chart on the next page is intended to provide an overview of the various switch modules and to indicate which diagram(s) should be referred to for installation instructions. 1 of 6 Installation (Cont.) If it is necessary to locate two switch-points close together, two switch modules can be positioned o side-by-side and located 180 opposite of the flag assembly, as shown. Flag Assembly T T T T Top V op V op V op V op View iew iew iew iew Switch Modules Switch Modules Switch Modules Switch Modules Switch Modules Switch Switch Mounting Hardware Mounting Hardware Mounting Hardware Mounting Hardware Mounting Hardware Switch Switch Switch Part Part Part Part Part SureSite SureSite SureSite SureSite SureSite Switch Rating / Switch Rating / Switch Rating / Switch Rating / Switch Rating / Max. Fluid Max. Fluid Max. Fluid Max. Fluid Max. Fluid Housing Housing Housing Housing Housing Bracket / Spacer T Type ype Configuration Configuration T Temp (°F / °C) emp (°F / °C) Number Number Number Number Number T T Type ype ype Configuration Configuration Configuration T T Temp (°F / °C) emp (°F / °C) emp (°F / °C) Clamp J-Box Material Material Material Material Material Block Standard Standard Standard Standard Standard 85350 Standard 20 VA SPST, N.O. or N.C. 300 / 148 N/A N/A N/A Polysulfone 86435 Standard 20 VA SPST, N.O. or N.C. 300 / 148 N/A Incl. N/A Polysulfone 86567 Mini 20 VA SPST, N.O. or N.C. 300 / 148 N/A Incl. N/A Polysulfone 87480 Mini / Plastic 20 VA SPST, N.O. or N.C. 300 / 148 N/A N/A N/A Polysulfone 80469 Plastic 20 VA SPST, N.O. or N.C. 300 / 148 N/A N/A N/A Polysulfone High T High T High T High T High Temperature emperature emperature emperature emperature 83140 All 20 VA SPST, N.O. or N.C. 750 / 398 Incl. N/A N/A 316 SS 83150 All 20 VA SPST, N.O. or N.C. 750 / 398 Incl. N/A N/A 316 SS 84320 All 20 VA SPDT, N.O. or N.C. 750 / 398 Incl. N/A N/A 316 SS 803430 All 220 VDC, 5 Amp 750 / 398 Incl. Incl. Incl. 316 SS Explosion-Proof / High T Explosion-Proof / High T Explosion-Proof / High T Explosion-Proof / High T Explosion-Proof / High Temperature emperature emperature emperature emperature 83100* All 120 VDC, 10 Amp 750 / 398 Incl. Incl. Incl. 316 SS 83110* All 24 VDC, 10 Amp 750 / 398 Incl. Incl. Incl. 316 SS 83120* All 20 VA SPST, N.O. or N.C. 750 / 398 Incl. Incl. Incl. 316 SS 83130* All 20 VA SPST, N.O. or N.C. 750 / 398 Incl. Incl. Incl. 316 SS 84330 All 20 VA SPDT, N.O. or N.C. 750 / 398 Incl. Incl. Incl. 316 SS Factory Mutual approved for: Factory Mutual approved for: Factory Mutual approved for: * Factory Mutual approved for: Factory Mutual approved for: Explosion-proof for Class 1, Division 1, Groups C & D and Class 1, Division 2, Groups B, C & D; Dust ignition proof per Class 2, Division 1, Groups E, F & G and suitable for Class 3, Division 1, Hazardous Location, Indoors (Ref. File #J.I. 0A8A3.AE). Also CSA certified for Class 1, Division 1, Groups B, C & D (Ref. Files LR22666-22 and LR22666-24). Note Note Note Note Note For Standard Unit installation instructions, see Mounting Diagram “A” For all other part numbers listed above, see Mounting diagram “B”, “C” or “D” 2 of 6 Õ Õ Õ Õ Õ Õ Õ Õ Õ Õ - Mounting Diagrams - - Mounting Diagrams - - Mounting Diagrams - - Mounting Diagrams - - Mounting Diagrams - Diagram A Diagram A Diagram A Diagram A Diagram A ® Standard SureSite Switch Part Numbers 80469, 85350, 86435, 86567, 87480 1. Position the switch module 180° from the flag assembly and within indicating range. 2. Slide the switch clamp between the flag assembly and the weldment of your SureSite Magnetic Level Indicator. 3. With the switch module located at the desired fluid level, tighten the clamp screw securely; not to exceed a torque of 10 lb-inches. 4. Connect the switch module leads to the load circuit. ® Mini SureSite J-Box Not Diagram B Diagram B Diagram B Diagram B Diagram B Included 1-1/4” On Type 1. Position the switch module 180° from O.D. Switch 83140 the flag assembly and within indicating Tubing Part Numbers range. Flag 83100, 83110, Assembly 83120, 83130. 2. Slide the tabs of the switch clamps 83140, 83150, between the flag assembly and the 84320, 84330 weldment of the Mini SureSite Magnetic 2-1/2” Level Indicator; wrapping the retaining Ref. Switch Module screw-end around the upper and lower stem of the switch, as shown. #24 Clamp (P/N 85576) -2 Required 3. With the switch module located at the desired fluid level, tighten the clamp 1-1/4” screw securely; not to exceed a torque of O.D. 120 lb-inches. Tubing Flag Switch 4. Connect the switch module leads to the Assembly Module load circuit. Switch Part Numbers 83150, 84320 2-1/2” Ref. #24 Clamp (P/N 85576) -2 Required 3 of 6 Õ Õ Õ Õ Õ Õ Õ Õ Õ Õ J-Box Not Mounting Diagrams (Cont.) ® Alloy SureSite Included On Type Tubing 83140 or Diagram C Diagram C Diagram C Diagram C Diagram C Switch Pipe Flag Part Numbers Assembly 1. Slide the switch into the support 83100, 83110, bracket. 83120, 83130. 83140, 83150, 2. Position the switch module 180° from 84320, 84330 the flag assembly and within indicating Switch Module range. #48 Clamp 3. Slide the switch clamp between the (P/N 85577) switch bracket and the stem of the switch, then between the flag assembly and the weldment of your SureSite Magnetic Level Indicator. Tubing or 4. With the switch module located at Pipe Flag the desired fluid level, tighten this Assembly clamp screw securely, not to exceed a Switch torque of 120 lb-inches. Part Numbers 83150, 84320 5. Connect the switch module leads to Switch the load circuit. Module #48 Clamp (P/N 85577) ® Plastic SureSite J-Box Not Included Diagram D Diagram D Diagram D Diagram D Diagram D Tubing On Type or 83140 1. Slide the switch into the plastic spacer Switch Pipe block. Flag Part Numbers Assembly 83100, 83110, 2. Position the switch module 180° from 83120, 83130. the flag assembly. 83140, 83150, 84320, 84330 3. Slide the tabs of the switch clamps Switch between the flag assembly and the Module weldment of your SureSite Magnetic Level Indicator, wrapping the retaining P/N 802265 #48 Clamp screw-ends around the stem of the switch, Spacer Block (P/N 85577) above and below the spacer block and the desired indication/activation level, as shown. 4. With the switch module located at the Tubing desired fluid level, tighten both clamp or Switch screws securely, not to exceed a torque of Pipe Part Numbers 120 lb-inches. 83150, 84320 5. Connect the switch module leads to the load circuit. Switch Flag Module Assembly P/N 802265 #48 Clamp Spacer Block (P/N 85577) 4 of 6 Wiring Diagrams Part Numbers Part Numbers Part Number 83100 Part Number 83100 Part Number 83100 Part Number 83100 Part Number 83100 Part Numbers Part Numbers Part Numbers - Dry Condition - 80469, 87480, 85350, 86435, 86567 120 VAC _ RED + YELLOW RED GREEN BLUE SPST, N.O. or N.C. (Dry) ORANGE BROWN WHITE Part Numbers Part Numbers Part Number 831 Part Number 831 Part Number 831 Part Number 831 Part Number 83110 10 10 10 10 Part Numbers Part Numbers Part Numbers - Dry Condition - 83120, 83140, 83150 - Dry Condition - 2-COND. 24 VDC CABLE _ + YELLOW GREEN BLUE ORANGE BROWN WHITE Part Number 83130 Part Number 83130 Part Number 83130 Part Numbers Part Numbers Part Numbers Part Numbers Part Numbers Part Number 83130 Part Number 83130 - Dry Condition - 84320, 84330 DPDT - Dry Condition / J-Box at Top - 3-PIN 3-PIN TERM TERM. 3-COND. CABLE 5 of 6 Wiring Diagrams (Cont.) Part Numbers Part Numbers Part Numbers Part Numbers Part Numbers 84320, 84330 - Dry Condition / J-Box at BTM - 3-PIN TERM. 3-COND. CABLE Switch Module Troubleshooting Condition Condition Condition Condition Condition Possible Cause Possible Cause Possible Cause Possible Cause Possible Cause Solution Solution Solution Solution Solution Positioned Incorrectly Reposition Switch Modules Switch not in Indicating Range Reposition Switch Modules Intermittent Switching or Incorrect Mounting Hardware See Appropriate Mounting Diagram Not Latching Incorrect Wiring Between Correct Wiring Switch & Load (See Wiring Diagrams) Positioned Incorrectly Reposition Switch Modules Switch Not in Indicating Range Reposition Switch Modules Switch Not Switching Incorrect Mounting Hardware See Appropriate Mounting Diagram Switch Remains Open Incorrect Wiring Between Correct Wiring or Switch & Load (See Wiring Diagrams) Closed At All times Switch Rating Exceeded Replace Switch (See Appropriate Rating Diagram) 6 of 6 SureSite Magnetic Liquid Level Indicator Installation, Operation and Maintenance Bulletin No. 177664-3 Rev. E Section 3: Transmitters Operating Principle The Gems SureSite Transmitter is a 3-wire device, externally mounted on the Gems SureSite Magnetic Level Indicator. The maximum and minimum level indication position is marked on the transmitter housing. The maximum indicator mark is red; the minimum indicator mark is blue. The SureSite Transmitter is a voltage divider which extends the full length of visual indication, consisting of magnetic reed switches tapped in at regular intervals. As the SureSite float moves with the liquid level, it magnetically closes a series of staggered reed switches in a sequence that varies the resistance. A regulated DC voltage applied to this voltage divider network will result in a proportional voltage output. Standard High Temp 2-Pc. High Temp Mini Transmitter EP Transmitter EP Transmitter Transmitter 316 SS Body Material Black Polysulfone Plastic Rated Temperature 300°F, 148°C 750°F, 398°C 300°F, 148°C (Process Media) Max. Ind. Length 120 “ (305 cm) 276 “ (701 cm) 240 “ (610 cm) 180 “ (457 cm) Input Voltage 10 - 30 VDC 3/8” Resolution Standard Pipe / Adjacent Standard Tubing / 90° Mounting 180° Location / Position Standard Pipe / Adjacent Standard Pipe / 125° (From Flag Ass’y1234567890123456789012345678901212345678901234567890123456789 1234567890123456789012345678901212345678901234567890123456789 1234567890123456789012345678901212345678901234567890123456789 1234567890123456789012345678901212345678901234567890123456789 Plastic / 90° 1234567890123456789012345678901212345678901234567890123456789 - Figure A - Installation Gems SureSite transmitter is typically installed on the SureSite Magnetic Level Indicator at the factory; however, if you purchased your transmitter separately, refer to Figure A above. Read all information carefully, before beginning installation. *** Warning: To prevent ignition of flammable or combustible atmospheres, disconnect power before servicing. Standard Transmitter Rotational Positioning 1. The SureSite transmitter is externally mounted and positioned either to the left or right of the flag assembly, per Figure A. 2. Using the alignment guide (supplied), determine if the existing flag assembly position can be used or if the flag assembly needs to be rotated to accommodate the transmitter. (See Figure B) 3. Using the flag assembly as a reference, position the SureSite transmitter using the red (maximum) and blue (minimum) indication marks. Each indication mark should be placed approximately the same distance from the top and bottom of the flag assembly. 1 of 6 Rotational Positioning (Cont.) 4. Outline the location of the transmitter and flag assembly on the SureSite 90° Must housing. Be Maintained 5. Loosen the clamps around the flag assembly to allow for installation of the transmitter clamps. The flag assembly clamps should only be loosened enough to permit the transmitter clamps to be inserted between the flag assembly and the SureSite housing. Max. Ind. Mark (Red) 6. Install the transmitter and loosely clamp it in the location outlined in step 4. 7. Tighten flag assembly clamps. Do not exceed 5 lb-inches. 8. Verify that the red (maximum) and blue (minimum) indication marks are centrally located between the ends of the flag assembly. 9. Using the alignment guide, verify that the SureSite transmitter is positioned correctly in relation to the flag assembly. Reposition if necessary. 10. Tighten the transmitter clamps securely. Do not exceed 5 lb-inches. Min. Ind. Mark (Blue) 11. Wire to appropriate signal conditioner/converter or controller. Note To ensure continuous electrical output, the transmitter must lay flat against the SureSite housing over the entire length. - Figure B - High Temp/Explosion-Proof Transmitter Rotational Positioning 1. The high temperature/explosion-proof SureSite transmitter is externally mounted and positioned either to the left or right of the flag assembly, per Figure A. 2. Using the flag assembly as a reference, position the high temperature/explosion-proof SureSite transmitter using the Max. Ind. red (maximum) and blue (minimum) indication marks. Each Mark (Red) indication mark should be placed approximately the same distance from the top and bottom of the flag assembly. 3. The high temperature/explosion-proof SureSite transmitter is secured to the SureSite Magnetic Level Indicator housing using two mounting clamps. One clamp is positioned at the top of the high temperature/explosion-proof transmitter and the other clamp is positioned at the bottom. Position clamps as shown in the Figure C. 4. Tighten clamps securely. Min. Ind. Mark (Blue) - Figure C - 2 of 6 2-Piece Transmitter - High Temperature/Explosion-Proof Rotational Positioning 1. The 2-section high temperature/explosion-proof SureSite transmitter is externally mounted to the left or right of (and adjacent to) the flag assembly and is positioned with the transmitter standoffs against the SureSite weldment or housing. The lower section mounts to the right of the flag assembly - the upper section mounts to the left; as indicated in Figure D. 2. Taking the upper section of the high temperature/explosion-proof SureSite transmitter and using the flag assembly as a reference, position the transmitter section so that the red (maximum) indication mark is one 1” below and to the left of the top of the SureSite flag assembly. 3. Loosely clamp the upper section of the high temperature/explosion-proof SureSite transmitter by placing one clamp around the top and bottom of the transmitter section at the same location as the transmitter standoffs. (See Figure D) 4) Taking the lower section of the high temperature/explosion-proof SureSite transmitter and using the flag assembly as a reference, position the transmitter section so that the blue (minimum) indication mark is 1” above and to right of the bottom of the SureSite flag assembly. 5. Loosely clamp the lower section of the high temperature/explosion- proof SureSite transmitter by placing one clamp around the top and bottom of the transmitter section at the same locations as the transmitter stand-offs. (See Figure D) 6. If the blue (minimum) indication mark of the upper section and the Max. Ind. red (maximum) indication mark of the lower section (the centered Mark (Red) indication marks) are not aligned as shown in Figure D, reposition both sections by sliding each section of the transmitter up or down equally. Max. Ind. Min. Ind. 7. With the centered indication marks aligned, verify that the red Mark (Blue) Mark (Red) (maximum) indication mark of the upper section and the blue (minimum) indication mark of the lower section are centrally located between the top and bottom of the SureSite flag assembly. Min. Ind. Note Mark (Blue) If the red (maximum) and blue (minimum) indication marks are not centrally located between the top and bottom of the SureSite flag assembly, reposition the transmitter accordingly. - Figure D - *Reminder* The centered indication marks must remain aligned as shown for continuous indication. 8. Tighten clamps securely. 9. Wire per supplied diagram. Due to many different wiring combinations for the 2-piece high temperature/explosion-proof SureSite transmitter, the wiring diagram is supplied with the unit. If using a Gems explosion-proof SureSite transmitter, use the appropriate wiring method (per N.E.C. Article 500). 3 of 6 Mini-Transmitter Rotational Positioning 1. The Mini-SureSite transmitter is externally mounted and positioned 180° from the SureSite flag assembly, per Figure E. 2. Before installing the Mini-SureSite transmitter on your Max. Ind. SureSite Magnetic Level Indicator, outline the location of Mark (Red) the flag assembly on the indicator housing. 3. Remove the existing flag assembly clamps from the flag assembly, one at a time. Replace these clamps with the new flag assembly/transmitter clamps provided. When replacing the old flag assembly clamps with the new flag assem- bly/ transmitter clamps, the Mini-Transmitter should be loosely clamped 180° from the flag assembly. The new clamp secures both the Mini-SureSite transmitter and the SureSite flag assembly. 4. With all the clamps replaced, reposition the flag assem- bly to the previously outlined location. Also, vertically position the Mini-SureSite transmitter so that the red (maximum) and Min. Ind. blue (minimum) indication marks are centrally located Mark (Blue) between the top and bottom of the SureSite flag assem- bly. 5. Verify that the Mini-SureSite transmitter is 180° from the flag assembly. Reposition as necessary. 6. Tighten the flag assembly/transmitter clamps securely. Do not exceed 5 lb-inches. - Figure E - Service Because the transmitter is not field-serviceable, the unit must be returned for repair or replacement. 4 of 6 Transmitter Troubleshooting Solution Condition Possible Cause Positioned Incorrectly Reposition Transmitter (See appropriate installation section) No Output or Incorrect Wiring Between Correct Wiring Transmitter & Load Loss of Signal (See wiring diagrams) Transmitter Faulty* Repair or Replace Transmitter * To Determine if Your Transmitter is Faulty: 1. Disconnect the transmitter from the signal conditioner/converter or controller. 2. With an ohmmeter, check the total resistance between the red and black wire of the high temperature/ explosion-proof Suresite transmitter. The resistance should read typically between 1200W and 1600W. - If the resistance between the red and black wires reads as an open, contact Gems Sensors for further assistance. - If the resistance total between the red and black wires is verified, the SureSite float must be removed from the SureSite magnetic level indicator. If you are unable to remove the float from your Suresite,you must remove the transmitter from the Suresite housing. 3. With an ohmmeter, check the resistance between the red and white & the black and white wires of the high temperature/explosion-proof SureSite transmitter. The resistance between both sets of wires should read ∞ Ω. If you are reading any resistance across either set of wires other than ∞Ω, contact Gems Sensors for further assistance. 4. If all of the resistance readings and the transmitter’s position are verified as correct, but the SureSite transmitter is still not operating correctly, contact Gems Sensors for further assistance. If Your 2-Piece Transmitter is Faulty, Follow the Steps Below to Determine Which Section to Replace: 1. Disconnect the upper section from the lower section of the 2-piece high temperature/explosion-proof Suresite transmitter. 2. With an ohmmeter, check the total resistance between the red and black wires of the upper section of the 2-piece high temperature/explosion-proof SureSite transmitter. The resistance should read typically between 600Ω and 800Ω. If the resistance between the red and black wires reads as an open, contact Gems Sensors for further assistance. If the resistance total between the red and black wires on the upper section is verified: 3. With an ohmmeter, check the total resistance between the red and black wires of the lower section of the 2-piece high temperature/explosion-proof SureSite transmitter. The resistance should read typically between 600 Ω and 800 Ω. If the resistance between the red and black wires reads as an open, contact Gems Sensors for further assistance. 5 of 6 If the resistance total between the red and black wires on the lower section is verified: 4. The SureSite float must be removed from the Suresite magnetic level indicator. If you are unable to remove the float from your SureSite, you must remove the transmitter from the SureSite housing. 5. With an ohmmeter, check the resistance between the red & white and the black & white wires of the upper section of the 2-piece transmitter. The resistance between both sets of wires should read ∞ Ω. If you are reading any resistance across either set of wires other than ∞ Ω, contact Gems Sensors for further assistance. If the resistance total between the red and black wires on the upper section is verified: 6. With an ohmmeter, check the resistance between the red & white and the black & white wires of the lower section of the 2-piece transmitter. The resistance between both sets of wires should read ∞ Ω. If you are reading any resistance across either set of wires other than ∞ Ω, contact Gems Sensors for further assistance. 7. If all of the resistance readings and the transmitter’s position are verified as correct, but the SureSite transmitter is still not operating correctly, contact Gems Sensors for further assistance. 6 of 6 ® ® ® ® ® SureSite SureSite SureSite SureSite SureSite Magnetic Liquid Level Indicator Magnetic Liquid Level Indicator Magnetic Liquid Level Indicator Magnetic Liquid Level Indicator Magnetic Liquid Level Indicator Installation, Operation and Maintenance Installation, Operation and Maintenance Installation, Operation and Maintenance Installation, Operation and Maintenance Installation, Operation and Maintenance Bulletin No. 177664-4 (Rev Bulletin No. 177664-4 (Rev Bulletin No. 177664-4 (Rev Bulletin No. 177664-4 (Rev Bulletin No. 177664-4 (Rev. . . . . E E E E E) ) ) ) ) Section 4: Signal Conditioners Section 4: Signal Conditioners Section 4: Signal Conditioners Section 4: Signal Conditioners Section 4: Signal Conditioners Signal conditioners provide a regulated output (voltage or current) when used with Gems SureSite transmitters. The signal conditioner is housed within a junction box with two or three ports. The ports allow for mounting and customer wiring. Your signal conditioner’s part number can be found on the identification plate located on the back of the junction box. Your unit has the operating and electrical characteristics indicated in the chart (for reference purposes) below: Input V Input V Input Voltage oltage oltage Output Signal Output Signal Output Signal Output Output Output Input V Input Voltage oltage Conditioner Accuracy Conditioner Accuracy Conditioner Accuracy Conditioner Accuracy Conditioner Accuracy Output Signal Output Signal T T Transient V ransient V ransient Voltage oltage oltage Output Output TTransient V ransient Voltage oltage Source Source Source Source Source Loading Loading Loading Loading Loading Part Number Part Number Part Number Part Number Part Number Signal Signal Signal Signal Signal W W W W W ith T ith T ith T ith T ith Transmitter ransmitter ransmitter ransmitter ransmitter Protection Protection Protection Protection Protection 4K Ohms/V Max Metal Oxide Varistor 86156 8 to 24 VDC 0 to 5 VDC ± 0.4% of Full (.25 mA) Rated @ 30 VDC Scale or ± 1” - 15 to 30 VDC 85997 0 to 12 VDC - Whichever is greater Metal Oxide Varistor 2K Ohms/V Max Rated @ 38 VDC 20 to 30 VDC (.5 mA) 0 to 12 VDC 86157* *** * 4 to 20 mA 86158 Metal Oxide Varistor ± 1.0% of Full Range: Rated @ 68 VDC 10 to 40 VDC 4 to 20 mA Scale or ± 1” - 100 - 1200 Ohms 112300 250 Amps - Whichever is greater 4 to 20 mA 152800 * * *Note Note * *Note Note Note 1. Lower Alarm Point for P/N 86157 varies. The default setting is 2% to 50% of full scale. 2. Upper Alarm Point for P/N 86157 varies. The default setting is 50% to 98% of full scale. General Note General Note General Note General Note General Note Converter/signal conditioner Part Numbers 86158, 1 86158, 1 86158, 1 86158, 1 86158, 112300, 12300, 12300, 12300, 12300, Minimum Excitation Required for Loop Resistance and 152800 152800 152800 152800 152800 require calibration to maintain the accuracy of SureSite transmitter readings. Converter calibration can be accomplished, using your transmitter or a transmitter simu- 40 lator. 30 Calibration is simplified when using a transmitter simulator in place of the SureSite transmitter. Because the output volt- 20 age of the signal conditioner is stepped down to a fixed DC voltage, the transmitter and the transmitter simulator act 10 as identical electrical loads, as interpreted by the converter. For the purpose of calibration, rotating the shaft (wiper) of 0 the transmitter simulator performs the same function as 0 400 600 800 1200 200 1000 moving the SureSite float up and down inside the weldment. In each case, the changing resistance will provide the proper R (Ohms) Termination Plus DC Loop Resistance output to calibrate the signal conditioner. A transmitter simu- lator has been supplied with your converter/signal condi- tioner. 1 of 7 +Vs (Volts) Installation Precautions and Preparations W ith the exception of P/N 112300, all signal conditioners are typically installed on the SureSite magnetic level indicator at the factory. For those units so designated, the customer will have to provide electrical grounding, with an effective resistance of 1W or less. Please refer to the Wiring Diagram(s) for your particular signal conditioner part number. Calibration of the signal conditioner can be accomplished using your SureSite transmitter or the transmitter simulator (supplied). Signal Conditioner Part Numbers 86156 (0 to 5 VDC) and 85997 (0 to 12 VDC) Signal Conditioner Part Numbers 86156 (0 to 5 VDC) and 85997 (0 to 12 VDC) Signal Conditioner Part Numbers 86156 (0 to 5 VDC) and 85997 (0 to 12 VDC) Signal Conditioner Part Numbers 86156 (0 to 5 VDC) and 85997 (0 to 12 VDC) Signal Conditioner Part Numbers 86156 (0 to 5 VDC) and 85997 (0 to 12 VDC) Terminal Blocks Terminal Blocks (Ref.) (Ref.) +8 to 24 VDC 7 7 7 7 7 77777 +15 to 30 VDC #1 8 8 8 8 8 #1 8 8 8 8 8 #2 Rm #2 Rm - + - + 9 9 9 9 9 9 9 9 9 9 10 10 10 10 10 10 10 10 10 10 Blk Blk 1 1 1 1 11 1 1 1 1 Transmitter 1 1 1 1 11 1 1 1 1 Transmitter Wht 12 12 12 12 12 Wht 12 12 12 12 12 Red Red 13 13 13 13 13 13 13 13 13 13 #1: Remove wire from terminal 9 and connect it to #1: Remove wire from terminal 9 and connect to terminal 8 to provide “full” reference of the system. terminal 8 to provide “full” reference of the system. #2: Output signal loading (Rm): 4K Ohms/V Max #2: Output signal loading (Rm): 2K Ohms/V Max (.5 mA) (.25 mA) W W W W W iring Diagram iring Diagram iring Diagram iring Diagram iring Diagram W W iring Diagram iring Diagram W W W iring Diagram iring Diagram iring Diagram P/N 86156 P/N 86156 P/N 86156 P/N 86156 P/N 86156 P/N 85997 P/N 85997 P/N 85997 P/N 85997 P/N 85997 Installation Specifics Installation Specifics Installation Specifics Installation Specifics Installation Specifics The signal conditioner is typically installed on the SureSite magnetic level indicator at the factory. If your signal conditioner was purchased separately, you may use one of the ½” FNPT ports for mounting. Calibration Requirements Calibration Requirements Calibration Requirements Calibration Requirements Calibration Requirements None. Both of these units are calibrated at the factory. 2 of 7 Part Number 86157, 0 to 12 VDC Part Number 86157, 0 to 12 VDC Part Number 86157, 0 to 12 VDC Part Number 86157, 0 to 12 VDC Part Number 86157, 0 to 12 VDC This unit contains two relays intended to provide a high and low alarm signal for process control. These relays are K1 and K2, respectively, in the wiring diagram. Standard alarm functions are K1 (High Alarm) and K2 (Low Alarm). Other configurations are available upon request. Unless specified otherwise, the trip-point for the Low Alarm relay has been set at 5% of full scale, while that of the High Alarm relay has been set at 95% of full scale. Signal Conditioner Part Numbers 86157 (0 to 12 VDC) Signal Conditioner Part Numbers 86157 (0 to 12 VDC) Signal Conditioner Part Numbers 86157 (0 to 12 VDC) Signal Conditioner Part Numbers 86157 (0 to 12 VDC) Signal Conditioner Part Numbers 86157 (0 to 12 VDC) - W - W - W - W - Wiring Diagram - iring Diagram - iring Diagram - iring Diagram - iring Diagram - Terminal Blocks (Ref.) K 1A 1 1 1 1 1 Alarms Alarms Alarms Alarms Alarms High K 1B 2 2 2 2 2 High K 1 3 3 3 3 3 Low Alarm Contacts Shown With Relay De-energized K 2A 4 4 4 4 4 Low K 2B High 5 5 5 5 5 K 2 Low 6 6 6 6 6 #1: Remove wire from terminal 9 and +20 to 30 VDC 7 7 7 7 7 connect to terminal 8 to provide “full” reference of the system. #1 8 8 8 8 8 #2 Rm #2: Output signal loading (Rm): - + 9 9 9 9 9 2K Ohms/V Max (.5 mA) 10 10 10 10 10 Blk 1 1 1 1 11 1 1 1 1 Transmitter Wht 12 12 12 12 12 13 13 13 13 13 Installation Specifics Installation Specifics Installation Specifics Installation Specifics Installation Specifics The 86157 86157 86157 86157 86157 Signal Conditioner is typically installed on the SureSite magnetic level indicator at the factory. If your signal conditioner has been purchased separately, you may use one of the ½” FNPT ports for mounting. Calibration Requirements Calibration Requirements Calibration Requirements Calibration Requirements Calibration Requirements None. This unit is calibrated at the factory. If it is necessary to change the high and/or low alarm settings, you may follow the procedure provided below. Alarm Calibration Procedure (P/N 86157) Alarm Calibration Procedure (P/N 86157) Alarm Calibration Procedure (P/N 86157) Alarm Calibration Procedure (P/N 86157) Alarm Calibration Procedure (P/N 86157) The alarm trip-points are adjusted by means of two separate twenty-turn potentiometers, through either the upper or lower 50% of the indicated range. The approximate set-point adjustment can be made by counting the number of revolutions from the end-stops of the pots. As a general ‘Rule of Thumb,’ you may expect 2.5% of the indicated range per turn. After you have established the desired trip-point(s) for the alarm relay(s), the adjusting knob(s) may be fixed with a small amount of RTV or other semi- permanent material. 3 of 7 Signal Conditioner Part Numbers 86158 and 152800 (4 to 20 mA) Signal Conditioner Part Numbers 86158 and 152800 (4 to 20 mA) Signal Conditioner Part Numbers 86158 and 152800 (4 to 20 mA) Signal Conditioner Part Numbers 86158 and 152800 (4 to 20 mA) Signal Conditioner Part Numbers 86158 and 152800 (4 to 20 mA) HEX Nut Threaded #8-32 Span Adjust Rod Flat Washer P.C. Board Spacer See Detail “A” - P Detail “A” - P Detail “A” - P.C. Board Mounting .C. Board Mounting .C. Board Mounting Detail “A” - P Detail “A” - P.C. Board Mounting .C. Board Mounting Detail (T (T (T (T (Typ. 3 Places) yp. 3 Places) yp. 3 Places) yp. 3 Places) yp. 3 Places) “A” Null Adjust SureSite Standard Visual Indicator Transmitter Span Adjust Potentiometer This Unit Incorporates a Linear This Unit Incorporates a Linear This Unit Incorporates a Linear This Unit Incorporates a Linear This Unit Incorporates a Linear 6 5 4 3 V V V V Voltage to Current Converter oltage to Current Converter oltage to Current Converter oltage to Current Converter oltage to Current Converter 2 1 Null Adjust Potentiometer Calibration Requirements Calibration Requirements Calibration Requirements Calibration Requirements Calibration Requirements The calibration procedure should be conducted with a potenti- ometer (transmitter simulator) which has a resistance value of 1.0 k Ohm , minimum, to a maximum of 2.5 k Ohm . The transmitter simulator supplied with the signal conditioner has Maximum an adjustment range of 0 to 1000 ohms. Indication Mark (Red) Calibration Procedure Calibration Procedure Calibration Procedure Calibration Procedure Calibration Procedure (Note Note Note Note Note: Calibration should be performed with the signal High T High T High T High T High Temperature T emperature T emperature T emperature T emperature Transmitter ransmitter ransmitter ransmitter ransmitter conditioner disconnected from the SureSite transmitter. ) 1. Make the connections as shown in the calibration wiring diagram with the power supply turned off . 2. Set and apply the D. C. power supply voltage at 24 VDC, with a 250 Ohm load resistance, as shown. 3. Adjust the span and null potentiometers at approximately mid-range. 4. Set the transmitter/simulator potentiometer adjusting screw to its fully clockwise position, for a maximum indication on the digital multimeter (DMM). 5. With the span adjust potentiometer (see illustration), set the output current to 20 mA. 6. Turn the transmitter/simulator potentiometer adjusting screw to its fully counter-clockwise position, for a minimum indication on the DMM. 7. With the null adjust potentiometer, set the output current to 4 mA. 8. Repeat steps #4 through #7 for the final fine adjustment. No further adjustments will be required. 9. After calibration, the converter/signal conditioner can be mated permanently to the transmitter assembly. Any adjustments for null and span (4mA & 20 ma), due to D. C. loop resistance, are achieved by adjusting the potentiometer screws 4 of 7 Signal Conditioner Part Numbers 86158 (4-20mA) Signal Conditioner Part Numbers 86158 (4-20mA) Signal Conditioner Part Numbers 86158 (4-20mA) Signal Conditioner Part Numbers 86158 (4-20mA) Signal Conditioner Part Numbers 86158 (4-20mA) +24V +24V +24V +24V +24V D.C. Power D.C. Power D.C. Power D.C. Power D.C. Power Supply Supply Supply Supply Supply CW CW CW CW CW __ ___ Red Red Red Red Red + +++ + 1 1 1 1 1 5 5 5 5 5 White White T T T T Transmitter ransmitter ransmitter ransmitter ransmitter White White White 3 3 3 3 3 6 6 6 6 6 Simulator Pot Simulator Pot Simulator Pot Simulator Pot Simulator Pot Black Black Black Black Black 2 2 2 2 2 4 4 4 4 4 (1000 - 2500 OHMS) (1000 - 2500 OHMS) (1000 - 2500 OHMS) (1000 - 2500 OHMS) (1000 - 2500 OHMS) 250 250 250 250 250 OHMS OHMS OHMS OHMS OHMS Calibration Procedure Calibration Procedure Calibration Procedure Calibration Procedure Calibration Procedure 4-1/2 Digit 4-1/2 Digit 4-1/2 Digit 4-1/2 Digit 4-1/2 Digit dmm Digital Multi-Meter Digital Multi-Meter Digital Multi-Meter Digital Multi-Meter Digital Multi-Meter - W - W - W - W - Wiring Diagram - iring Diagram - iring Diagram - iring Diagram - iring Diagram - 4-20 mA 4-20 mA 4-20 mA 4-20 mA 4-20 mA T TTT Tank Level T ank Level T ank Level T ank Level T ank Level Transmitter ransmitter ransmitter ransmitter ransmitter Stainless Steel Stainless Steel Stainless Steel Stainless Steel Stainless Steel Housing Housing Housing Housing Housing Red Red Red Red Red 1 1 1 1 1 White White White White White 3 3 3 3 3 Black Black Black Black Black 2 2 2 2 2 P P.C. Board .C. Board P P P.C. Board .C. Board .C. Board (P/N 152842) (P/N 152842) (P/N 152842) (P/N 152842) (P/N 152842) 4 4 4 4 4 6 6 6 6 6 O +V O +V O +V O +V O +VA AAA A R RRR R LL LLL V VVV Voltage oltage oltage oltage oltage 5 5 5 5 5 Source Source Source Source Source Process Process Process Process Process J/Box J/Box J/Box J/Box J/Box Control Control Control Control Control Loop Loop Loop Loop Loop Installation Specifics The signal conditioner is typically installed on the Gems SureSite magnetic level indicator at the factory. If your signal conditioner was purchased separately, you may use one of the FNPT ports for mounting. 5 of 7 Signal Conditioner Part Number 1 Signal Conditioner Part Number 1 Signal Conditioner Part Number 112300 (4 to 20 mA) 12300 (4 to 20 mA) 12300 (4 to 20 mA) Signal Conditioner Part Number 1 Signal Conditioner Part Number 112300 (4 to 20 mA) 12300 (4 to 20 mA) - Panel Mounted V - Panel Mounted V - Panel Mounted V - Panel Mounted V - Panel Mounted Version - ersion - ersion - ersion - ersion - This unit incorporates a Linear Voltage to Current Converter. Red ----- TTTTTop V op V op V op V op View - iew - iew - iew - iew - - Calibration Wiring Diagram - 1 3 +V P.C. White 8 4 Source Board 5 2 250W Black DMM Transmitter Process Control 4 to 20 mA Loop Tank Level Transmitter Calibration Requirements The calibration procedure should be conducted with a potentiometer (transmitter simulator) which has a resistance value of 1.0 kW minimum to a maximum of 2.5 kW . The transmitter simulator is supplied. Calibration Procedure Note: Calibration should be performed with the signal conditioner disconnected from the SureSite transmitter. 1. Make connections as shown in the Calibration Wiring Diagram with the power supply turned off. 2. Set and apply the D.C. power supply voltage at 24 VDC with a 250W load resistance, as shown in the diagram. 3. Adjust both the span and null potentiometers at approximately mid-range. 4. Set the transmitter/simulator potentiometer adjusting screw to its fully clock-wise position, for a maximum indication on the digital multimeter (DMM). 5. With the span adjust potentiometer screw (see “Top View” diagram above), set the output current to 20.00 mA. 6. Turn the transmitter/simulator potentiometer adjusting screw to its fully counter-clock-wise position, for a minimum indication on the DMM. 7. With the null adjust potentiometer (see “Top View” diagram above), set the output current to 4.00 mA. 8. Repeat steps 4 through 7 for the final fine adjustment. No further adjustments will be required. 9. After calibration, the converter/signal conditioner can be installed at the desired location. Any adjustments for null and span (4.00 & 20.00 mA), due to DC loop resistance, are achieved by adjusting the potentiometer screws. 6 of 7 Span Null Installation Specifics The panel-mount design of this unit permits remote installation. For mounting purposes, it is possible to remove the body of the unit from the terminal base. This permits the terminal base to be installed on two 3/16” studs or with two 3/16” screws, at the slotted holes provided. After installation of the terminal base, reinstall the body of the unit in its socket. - Wiring Diagram - 6 7 R L Wht +V 8 5 Source Red 1 4 4-20 mA Loop Transmitter Blk 2 3 - Signal Conditioner T - Signal Conditioner T - Signal Conditioner Troubleshooting - roubleshooting - roubleshooting - - Signal Conditioner T - Signal Conditioner Troubleshooting - roubleshooting - Condition Condition Solution Solution Solution Solution Solution Condition Condition Condition Possible Cause Possible Cause Possible Cause Possible Cause Possible Cause Loose or Improperly Connected Correct Connections Wires At Terminal Screws No Output Incorrect Wiring Correct Wiring (See Wiring Diagrams) Transmitter Positioning Incorrect See SureSite Transmitter Troubleshooting Section High or Low Alarm Points Alarm Setpoints Incorrect Recalibrate Alarm Setpoints Not Alarming at Desired (See Calibration Procedure) Setpoints 7 of 7 1 112300 12300 1 1 112300 12300 12300 Converter Converter Converter Converter Converter âââââ SureSite Magnetic Liquid Level Indicator Installation, Operation and Maintenance Bulletin No. 177664-5 Section 5: Power Supplies The SureSite power supply is designed to provide regulated DC input voltage when only AC voltage is available. This DC voltage can be used to supply the required input voltage to the Gems signal conditioner. Designed to accept a nominal 115 VAC or 230 VAC input (depending upon the unit ordered), the power supply’s output is 50 mA at 24 VDC, nominal. The power supply has an operating temperature range of -15°C to +70°C (-5°F to +158°F) and its output is thermally and short circuit protected against damage. Installation In most cases, the power supply is attached and wired to the signal conditioner at the Factory; requiring only to be wired to your AC voltage source. You may utilize any of the junction box 1/2” NPT ports to mount the unit in a fixed position. - --- - T TTT Typical Installation - ypical Installation - ypical Installation - ypical Installation - ypical Installation - 1. With the power turned off and the circuit 4 to20mA Signal Conditioner disabled, remove the cover from the junction box Transmitter Power housing of the power supply, and remove the Supply thread protector from the port you have selected for wiring. (See Installation Diagram). 2. Run your voltage source wiring through the appropriate strain relief device and into the 1 junction box. 1/2” NPT Nipple - W - W - W - W - Wiring Diagrams - iring Diagrams - iring Diagrams - iring Diagrams - iring Diagrams - In Out In Out _____ _ _ _ _ _ 11111 22222 33333 44444 55555 + 2 2 1 1 1 1 1 2 2 2 3 3 3 3 3 4 4 4 4 4 5 5 5 5 5 + 230 VAC ** Ground*** 115 Ground* * * * * VAC P/N 52560 - 1 P/N 52560 - 1 P/N 52560 - 1 P/N 52560 - 1 P/N 52560 - 115 V 15 V 15 V 15 V 15 VAC AC AC AC AC P/N 52570 - 230 V P/N 52570 - 230 V P/N 52570 - 230 V P/N 52570 - 230 V P/N 52570 - 230 VAC AC AC AC AC ***Negative output is not junction box grounded. A ground may be made, if required. ** 3. For 115 VAC Input Only Connect your wiring to terminals 1 and 2 of Terminal Block-1. (See the wiring diagram for your power supply.) 4. For 230 VAC Input Only Connect your wiring to terminals 1 and 4 of Terminal Block-1. (See the wiring diagram for your power supply.) The Strain Relief Device is Not Not N Not Not ot Factory-Supplied 1 1 of 2 5. If your power supply is remotely mounted and has not been connected to the signal conditioner: Power Supply to Signal Conditioner Power Supply to Signal Conditioner Power Supply to Signal Conditioner Power Supply to Signal Conditioner Power Supply to Signal Conditioner a) Remove the thread protector(s) from the ports b) Connect the lead wires to the power supply Blk output terminals. Run the wires through appropriate strain relief device(s) and into Red 1 the signal conditioner. (See the “Power Supply to Signal Conditioner” sketch.) Signal Power c) See the appropriate signal conditioner Conditioner Supply wiring diagram for proper wiring instructions. 6. Reinstall the cover with its required O-ring on the junction box. 7. Enable the circuit and turn power on. Power Supply Troubleshooting Condition Condition Condition Condition Condition Possible Cause Possible Cause Solution Solution Possible Cause Possible Cause Possible Cause Solution Solution Solution Input Voltage Not Correct Apply the Proper Input Voltage - 115 VAC or 230 VAC Incorrect Wiring Between Signal Correct Wiring 24 VDC Conditioner and Power Supply (See Appropriate Wiring Diagrams) Output Bad Loose or Improperly Connected Correct Connections W ires at Terminal Screws The Strain Relief Device is Not Not N Not Not ot Factory-Supplied 1 2of 2 P/N 177664-5 (Rev. A) ® ® ® ® ® SureSite SureSite SureSite SureSite SureSite Magnetic Magnetic Liquid Liquid Level Level Indicator Indicator Magnetic Magnetic Magnetic Liquid Liquid Liquid Level Level Level Indicator Indicator Indicator Installation, Installation, Installation, Installation, Installation, Operation Operation Operation Operation Operation and and and and and Maintenance Maintenance Maintenance Maintenance Maintenance Bulletin Bulletin Bulletin No. No. No. 177664-6 177664-6 177664-6 Bulletin Bulletin No. No. 177664-6 177664-6 Rev Rev Rev Rev Rev. . . . . B B B B B Section Section Section Section Section 6: 6: 6: 6: 6: Indicating Indicating Indicating Indicating Indicating Scale Scale Scale Scale Scale This Indicating Scale provides a numerical readout of the liquid level in the tank, in addition to the visual level displayed by the flag assembly. The indicating scale is mounted alongside the flag assembly with special clamps. The scale is normally graduated in inches and feet, but may be graduated in other dimensional or volumetric units. Scales that have an overall length of more than 24 inches will be provided in two or more sectional lengths. Side Side Side Side Side V V V V View iew iew iew iew Front Front Front Front Front V V V V View iew iew iew iew Installation Installation Installation Installation Installation Scales ordered with the SureSite Magnetic Level Indicator are factory-installed. If ordered separately, please follow the instructions below. Mounting Mounting Mounting Mounting Mounting The scale is simply installed on your SureSite Magnetic Level Indicator using the bracketed clamps supplied. 1. Attach the scale onto the SureSite Magnetic Level Indicator, wrapping the clamps around the flag assembly and the weldment. 2. Tighten the clamps securely, with a torque not to exceed 5 lb.-inches. P/N 177664-6 Rev. B SureSite Magnetic Liquid Level Indicator Installation, Operation and Maintenance Bulletin No. 177664-7 (Rev A) Section 7: Insulation Blankets Installation Insulation Blankets are provided to minimize the possibility of personal injury and heat loss. Blankets have been designed for various SureSite Magnetic Level Indicators and mounting configurations, as indicated below: Description Indicator Type Mounting Configuration 1-Piece Mini Top and Bottom Mount 2-Piece Mini Side Mount 1-Piece Standard Top and Bottom Mount 3-Piece Standard Side Mount 4-Piece Standard Side Mount with Switches Insulation Cable Tie Blanket Mini-SureSite Heat Portion of Heater Cable to be approx. XXX - Top and Bottom Mount from Flag Assembly. (1-Piece Blanket) (Either side of flag assembly is fine.) The optional Heat Trace cable should be installed according to the supplied instruc- tions prior to wrapping the Insulation Blanket around the SureSite,as described below: 1. Wrap the long section of the Insulation Blanket around the SureSite Magnetic Cable Tie Level Indicator so that the area on either side of the flag assembly is covered. The flag assembly alone remains visible. Heat Cable Extended Length 2. Using non-ferrous lock-wire, secure the Insulation Blanket to the Mini-SureSite at intervals of approximately 12 inches (30 cm), as shown in the illustration. Twist the wire ends to secure. SureSite with (See Figure A) SureSite with Optional Heat Trace Heat Trace & Insulation - Figure A - 1 of 3 Mini-SureSite Side-Mount (2-Piece Blanket) The optional Heat Trace Cable should be installed according to the supplied instructions prior to wrapping the insulation blanket around the SureSite, as described in the instructions below: 1. Wrap each of the two long sections of the insulation blanket around half of the SureSite Magnetic Level Indicator so that the areas between the side connections and the flag assembly are covered. The flag assembly remains visible. 2. Using non-ferrous lock-wire, secure the insulation blanket to the Mini-SureSite at intervals of approximately 12 inches (30 cm), as shown in Figure A. Twist the wire ends to secure. Standard SureSite Top and Bottom Mount (1-Piece Blanket) The optional heat trace Cable should be installed according to the supplied instructions prior to wrapping the insulation blanket around the SureSite, as described below. 1. Wrap the long section of the insulation blanket around the SureSite, so that the area on either side of the flag assembly is covered. The flag assembly alone remains visible. 2. Using non-ferrous lock-wire, secure the insulation blanket to the SureSite, as shown in the illustration below (Figure B), at the “hog-ring”locations. Twist the wire ends to secure, drawing the insulation blanket together, surrounding the flag assembly. Standard SureSite Side-Mount Insulation (3-Piece Blanket) Blanket The optional heat trace cable should be installed according to the supplied instructions prior to wrapping the insulation blanket around the SureSite, as described below: 1. Wrap the long section of the insulation blanket around the SureSite, between the side connectors and position the edges so that the flag assembly alone remains visible. 2. Using non-ferrous lock-wire, secure the insulation blanket to the SureSite, as shown in the Figure B, at the “hog-ring” locations. Twist the wire ends to secure, drawing the insulation blanket together, surrounding the flag assembly. 3. The remaining two pieces (the top and bottom collars) are to be wrapped around the SureSite, and likewise secured as in step 2. See Figure B for clarity. - Figure B - 2 of 3 Standard SureSite (4-Piece Blanket) The optional heat trace cable, should be installed according to the supplied instructions prior to wrapping the insulation blanket around the SureSite, as described below: 1. Wrap each of the two long sections of Cable Tie the insulation blanket around half of Insulation the SureSite, so that the areas Blanket between the side connectors and the flag assembly are covered. The flag assembly alone remains visible. Heat Portion of Heater Cable to be approx. XXX 2. Using non-ferrous lock-wire, secure from Flag Assembly. the insulation blanket to the (Either side of flag SureSite,as shown in the Figure C, assembly is fine.) at the “hog-ring” locations. Twist the wire ends to secure, drawing the insulation blanket together, surrounding the flag assembly. 3. The remaining two pieces (the top and bottom collars) are to be wrapped around the SureSite, and likewise Cable Tie secured, as in step 2. See Figure C for clarity. Heat Cable Extended Length (Coil for Shipping) - Figure C - 3 of 3 SureSite Magnetic Liquid Level Indicator Installation, Operation and Maintenance Bulletin No. 177664-8 (Rev A) Section 8: Heat Trace Operating Principle The Heat Trace is a self-regulating length of heating cable intended for use with the SureSite Magnetic Level Indicator. The cable is provided with a nominal six-foot (183 cm) power lead length. The heater cable portion (or length) is typically rated at 10 Watts per foot, operating at 120 Volts. Power consumption is directly proportional to the length ordered. Power Lead Heater Cable Cable Tie Heat portion of heater cable to be approx. 90° from flag assembly. Installation (Either side of flag assembly is fine.) The Heat Trace may be installed on either side of the flag assembly. 1. Position the Heat Trace heater cable end at the top of the SureSite and approximately 90 degrees from the flag assembly, as shown. 2. Using two cable ties (supplied), attach the Heat Trace at the top and bottom of the SureSite unit, as shown. 3. Attach power leads to voltage source. Cable Tie Heat Cable Extended Length SureSite Magnetic Liquid Level Indicator Installation, Operation and Maintenance Bulletin No. 177664-9 (Rev A) Section 9: Cold Service Installation Standard SureSite Cold service insulation has been completely installed on the SureSite Magnetic Level Indicator at the factory; except for the insulated cap assembly, which must be installed in conjunction with the installation of the Gems SureSite. For Top and/or Bottom NPT Connections: 1. Remove the flange and install the float into the unit. Refer to “Section 1: Weldments” of Instruction Bulletin #177664 for detailed instructions. 2. After the float has been installed, reinstall the flange, using the gasket and bolts. Refer to the torque chart in the “Weldments” section for the appropriate torque value for the bolts. Lens Note The insulated cap assembly must first be installed on the connecting pipe from the tank, prior to starting the pipe-joint connections. 3. Before mating the SureSite Magnetic Level Indicator to your connecting piping, slide the insulated cap assembly back (toward the tank), far enough to permit completion of the pipe joint assembly, using the appropriate pipe thread sealant. 4. With the top and bottom pipe joint completed, slide the insulated cap assembly until it is flush with the SureSite insulation, and wrap the circumferential joint with the special tape supplied. 5. Apply an appropriate cold service sealant around the pipe/insulation interface. 1 of 2 For NPT/Flange Side Branch Connections: 1. Remove the flange and install the float into the unit. Refer to Section 1 of this Instruction Bulletin (“Weldments”) for detailed instructions. 2. After the float has been installed, reinstall the flange, using the gasket and bolts. Refer to the torque chart in the “Weldments” section for the appropriate torque value for the bolts. 3. Place the insulation end cap assembly over the bottom flange, flush with the SureSite insulation. Note If the top or bottom NPT connection is plugged (i.e., welded cap with plugged NPT), remove the tape from the cap, apply the appropriate pipe thread sealant and complete the pipe joint. Using an appropriate cold service sealant, seal around the pipe and insulation interface. 4. Wrap the circumferential joint with the special tape supplied. 5. Complete the installation of your SureSite Indicator according to the instructions provided, using an appropriate thread sealant and/or gasket material. 2 of 2
Frequently asked questions
What makes Elite.Parts unique?

What kind of warranty will the 85350 have?

Which carriers does Elite.Parts work with?

Will Elite.Parts sell to me even though I live outside the USA?

I have a preferred payment method. Will Elite.Parts accept it?

Why buy from GID?
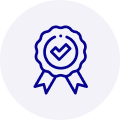
Quality
We are industry veterans who take pride in our work
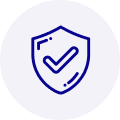
Protection
Avoid the dangers of risky trading in the gray market
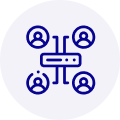
Access
Our network of suppliers is ready and at your disposal
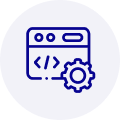
Savings
Maintain legacy systems to prevent costly downtime
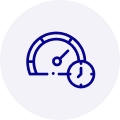
Speed
Time is of the essence, and we are respectful of yours
What they say about us
FANTASTIC RESOURCE
One of our top priorities is maintaining our business with precision, and we are constantly looking for affiliates that can help us achieve our goal. With the aid of GID Industrial, our obsolete product management has never been more efficient. They have been a great resource to our company, and have quickly become a go-to supplier on our list!
Bucher Emhart Glass
EXCELLENT SERVICE
With our strict fundamentals and high expectations, we were surprised when we came across GID Industrial and their competitive pricing. When we approached them with our issue, they were incredibly confident in being able to provide us with a seamless solution at the best price for us. GID Industrial quickly understood our needs and provided us with excellent service, as well as fully tested product to ensure what we received would be the right fit for our company.
Fuji
HARD TO FIND A BETTER PROVIDER
Our company provides services to aid in the manufacture of technological products, such as semiconductors and flat panel displays, and often searching for distributors of obsolete product we require can waste time and money. Finding GID Industrial proved to be a great asset to our company, with cost effective solutions and superior knowledge on all of their materials, it’d be hard to find a better provider of obsolete or hard to find products.
Applied Materials
CONSISTENTLY DELIVERS QUALITY SOLUTIONS
Over the years, the equipment used in our company becomes discontinued, but they’re still of great use to us and our customers. Once these products are no longer available through the manufacturer, finding a reliable, quick supplier is a necessity, and luckily for us, GID Industrial has provided the most trustworthy, quality solutions to our obsolete component needs.
Nidec Vamco
TERRIFIC RESOURCE
This company has been a terrific help to us (I work for Trican Well Service) in sourcing the Micron Ram Memory we needed for our Siemens computers. Great service! And great pricing! I know when the product is shipping and when it will arrive, all the way through the ordering process.
Trican Well Service
GO TO SOURCE
When I can't find an obsolete part, I first call GID and they'll come up with my parts every time. Great customer service and follow up as well. Scott emails me from time to time to touch base and see if we're having trouble finding something.....which is often with our 25 yr old equipment.
ConAgra Foods