FLUKE 761031
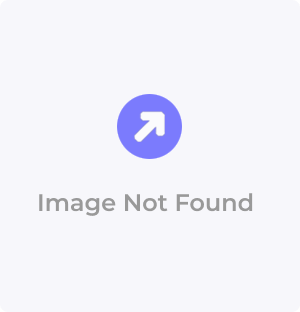
Description
Fluke 761031 REPLACEMENT PART 5700A-7602 ,FRONT PANEL & DISPLAY PCA RoHS Compliant: NA
Part Number
761031
Price
Request Quote
Manufacturer
FLUKE
Lead Time
Request Quote
Category
PRODUCTS - 7
Datasheet
Extracted Text
®
5700A/5720A Series II
Multi-Function Calibrator
Service Manual
November 2007
©2007 Fluke Corporation, All rights reserved.
All product names are trademarks of their respective companies.
LIMITED WARRANTY & LIMITATION OF LIABILITY
Each Fluke product is warranted to be free from defects in material and workmanship
under normal use and service. The warranty period is one year and begins on the date
of shipment. Parts, product repairs and services are warranted for 90 days. This
warranty extends only to the original buyer or end-user customer of a Fluke authorized
reseller, and does not apply to fuses, disposable batteries or to any product which, in
Fluke's opinion, has been misused, altered, neglected or damaged by accident or
abnormal conditions of operation or handling. Fluke warrants that software will operate
substantially in accordance with its functional specifications for 90 days and that it has
been properly recorded on non-defective media. Fluke does not warrant that software
will be error free or operate without interruption.
Fluke authorized resellers shall extend this warranty on new and unused products to
end-user customers only but have no authority to extend a greater or different warranty
on behalf of Fluke. Warranty support is available if product is purchased through a Fluke
authorized sales outlet or Buyer has paid the applicable international price. Fluke
reserves the right to invoice Buyer for importation costs of repair/replacement parts
when product purchased in one country is submitted for repair in another country.
Fluke's warranty obligation is limited, at Fluke's option, to refund of the purchase price,
free of charge repair, or replacement of a defective product which is returned to a Fluke
authorized service center within the warranty period.
To obtain warranty service, contact your nearest Fluke authorized service center or send
the product, with a description of the difficulty, postage and insurance prepaid (FOB
Destination), to the nearest Fluke authorized service center. Fluke assumes no risk for
damage in transit. Following warranty repair, the product will be returned to Buyer,
transportation prepaid (FOB Destination). If Fluke determines that the failure was
caused by misuse, alteration, accident or abnormal condition of operation or handling,
Fluke will provide an estimate of repair costs and obtain authorization before
commencing the work. Following repair, the product will be returned to the Buyer
transportation prepaid and the Buyer will be billed for the repair and return transportation
charges (FOB Shipping Point).
THIS WARRANTY IS BUYER'S SOLE AND EXCLUSIVE REMEDY AND IS IN LIEU OF
ALL OTHER WARRANTIES, EXPRESS OR IMPLIED, INCLUDING BUT NOT LIMITED
TO ANY IMPLIED WARRANTY OF MERCHANTABILITY OR FITNESS FOR A
PARTICULAR PURPOSE. FLUKE SHALL NOT BE LIABLE FOR ANY SPECIAL,
INDIRECT, INCIDENTAL OR CONSEQUENTIAL DAMAGES OR LOSSES, INCLUDING
LOSS OF DATA, WHETHER ARISING FROM BREACH OF WARRANTY OR BASED
ON CONTRACT, TORT, RELIANCE OR ANY OTHER THEORY.
Since some countries or states do not allow limitation of the term of an implied warranty,
or exclusion or limitation of incidental or consequential damages, the limitations and
exclusions of this warranty may not apply to every buyer. If any provision of this
Warranty is held invalid or unenforceable by a court of competent jurisdiction, such
holding will not affect the validity or enforceability of any other provision.
Fluke Corporation Fluke Europe B.V.
P.O. Box 9090 P.O. Box 1186
Everett, WA 98206-9090 5602 BD Eindhoven
U.S.A. The Netherlands
5/94
Table of Contents
Chapter Title Page
1 Introduction and Specifications......................................................... 1-1
1-1. Introduction........................................................................................... 1-3
1-2. Contacting Fluke................................................................................... 1-4
1-3. About this Manual ................................................................................ 1-4
1-4. How to Use this Manual ....................................................................... 1-4
1-5. Wideband AC Voltage Module (Option 5700A-03) ............................ 1-5
1-6. Auxiliary Amplifiers............................................................................. 1-6
1-7. 5725A Amplifier .............................................................................. 1-6
1-8. Support Equipment and Services.......................................................... 1-6
1-9. 732B Direct Voltage Reference Standard ........................................ 1-7
1-10. 732B-200 Direct Volt Maintenance Program (U.S.A. Only) ........... 1-7
1-11. 742A Series Resistance Standards.................................................... 1-7
1-12. Wideband AC Module (Option 5700A-03) Calibration Support ..... 1-7
1-13. Service Centers................................................................................. 1-8
1-14. The Components of the 5700A/5720A Series II Calibrator ................. 1-8
1-15. Calibrating the 5700A/5720A Series II Calibrator ............................... 1-9
1-16. The Calibration Process.................................................................... 1-10
1-17. Establishing Traceability.................................................................. 1-10
1-18. Calibration Reports........................................................................... 1-11
1-19. Calibration Check ................................................................................. 1-11
1-20. Developing a Performance History....................................................... 1-11
1-21. Range Calibration ................................................................................. 1-12
1-22. DC Zeros Calibration............................................................................ 1-12
1-23. Specifications........................................................................................ 1-12
1-24. Specification Confidence Levels...................................................... 1-12
1-25. Using Absolute and Relative Uncertainty Specifications................. 1-12
1-26. Using Secondary Performance Specifications.................................. 1-13
1-27. General Specifications .......................................................................... 1-14
1-28. Electrical Specifications ....................................................................... 1-15
1-29. DC Voltage Specifications ............................................................... 1-15
1-30. AC Voltage Specifications ............................................................... 1-18
1-31. Resistance Specifications ................................................................. 1-29
1-32. DC Current Specifications................................................................ 1-33
1-33. AC Current Specifications................................................................ 1-36
i
5700A/5720A Series II
Service Manual
1-34. Wideband AC Voltage (Option 5700-03) Specifications................. 1-41
1-35. Auxiliary Amplifier Specifications .................................................. 1-42
2 Theory of Operation ............................................................................ 2-1
2-1. Introduction........................................................................................... 2-2
2-2. Calibrator Overview ............................................................................. 2-2
2-3. Internal References........................................................................... 2-2
2-4. Hybrid Reference Amplifiers....................................................... 2-2
2-5. Fluke Thermal Sensor (FTS)........................................................ 2-2
2-6. Digital-to-Analog Converter (DAC). ........................................... 2-3
2-7. Digital Section Overview...................................................................... 2-3
2-8. Analog Section Overview..................................................................... 2-3
2-9. Functional Description Presented by Output Function......................... 2-5
2-10. DC Voltage Functional Description ................................................. 2-6
2-11. AC Voltage Functional Description ................................................. 2-9
2-12. Wideband AC V Functional Description (Option -03) .................... 2-10
2-13. DC Current Functional Description.................................................. 2-10
2-14. AC Current Functional Description.................................................. 2-10
2-15. Ohms Functional Description........................................................... 2-11
3 Calibration and Verification................................................................ 3-1
3-1. Introduction........................................................................................... 3-3
3-2. Calibration............................................................................................ 3-4
3-3. Calibrating the 5700A/5720A Series II to External Standards............. 3-4
3-4. Calibration Requirements................................................................. 3-4
3-5. When to Adjust the Calibrator’s Uncertainty Specifications ........... 3-5
3-6. Calibration Procedure....................................................................... 3-6
3-7. Range Calibration ................................................................................. 3-12
3-8. Calibrating the Wideband AC Module (Option 5700A-03) ................. 3-15
3-9. Performing a Calibration Check ........................................................... 3-18
3-10. Full Verification.................................................................................... 3-20
3-11. Required Equipment for All Tests.................................................... 3-21
3-12. Warm-up Procedure for All Verification Tests ................................ 3-21
3-13. Resistance Verification Test............................................................. 3-23
3-14. Two-Wire Compensation Verification ............................................. 3-25
3-15. DC Voltage Verification Test........................................................... 3-26
3-16. DC Voltage One-Tenth Scale Linearity Test ................................... 3-27
3-17. Direct Current Accuracy Verification Test ...................................... 3-28
3-18. AC Voltage Frequency Accuracy Test............................................. 3-29
3-19. Output Level Tests For AC V Ranges.............................................. 3-29
3-20. AC Current Test, 22 mA to 11A Ranges.......................................... 3-31
3-21. AC Current Test, 2 mA and 200 μA Ranges.................................... 3-34
3-22. Rationale for Using Metal-Film Resistors to Measure AC Current . 3-35
3-23. Wideband Frequency Accuracy Test................................................ 3-36
3-24. Wideband AC Voltage Module Output Verification........................ 3-36
3-25. Wideband Output Accuracy at 1 kHz Test ........................................... 3-37
3-26. Wideband Output Flatness Test............................................................ 3-38
3-27. Wideband Flatness Calibration Procedure ....................................... 3-39
3-28. Optional Tests....................................................................................... 3-40
3-29. DC Voltage Load Regulation Test ................................................... 3-40
3-30. DC Voltage Linearity Test ............................................................... 3-41
3-31. DC Voltage Output Noise (10 Hz to 10 kHz) Test........................... 3-41
3-32. DC Voltage Output Noise (0.1 to 10 Hz) Test ................................. 3-43
ii
Contents (continued)
3-33. AC Voltage Distortion Test.............................................................. 3-43
3-34. Wideband Distortion Testing ........................................................... 3-43
3-35. AC Voltage Overshoot Test ............................................................. 3-44
3-36. Minimum Use Requirements ................................................................ 3-44
3-37. Determining Test Limits for Other Calibration Intervals ..................... 3-46
4 Maintenance......................................................................................... 4-1
4-1. Introduction........................................................................................... 4-3
4-2. Accessing the Fuse................................................................................ 4-3
4-3. Cleaning the Air Filter .......................................................................... 4-3
4-4. General Cleaning .................................................................................. 4-4
4-5. Cleaning PCA's..................................................................................... 4-5
4-6. Access Procedures................................................................................ 4-5
4-7. Top and Bottom Covers.................................................................... 4-5
4-8. Digital Section Cover ....................................................................... 4-5
4-9. Analog Section Covers..................................................................... 4-5
4-10. Rear Panel Removal and Installation................................................ 4-5
4-11. Rear Panel Assembly Access ........................................................... 4-6
4-12. Front Panel Removal and Installation .............................................. 4-6
4-13. Display Assembly Removal and Installation ............................... 4-7
4-14. Keyboard Assembly Removal and Installation............................ 4-7
4-15. Analog Assembly Removal and Installation .................................... 4-8
4-16. Digital Assembly Removal and Installation..................................... 4-10
4-17. Power Transformer Removal and Installation.................................. 4-10
4-18. Hybrid Cover Removal..................................................................... 4-10
4-19. Front/Rear Binding Post Reconfiguration ............................................ 4-10
4-20. Installing a Wideband AC Module (Option -03) .................................. 4-12
4-21. Clearing Ghost Images from the Control Display ................................ 4-12
4-22. Replacing the Clock/Calendar Backup Battery .................................... 4-12
4-23. Using Remote Commands Reserved for Servicing............................... 4-13
4-24. Using the ETIME Command............................................................ 4-13
4-25. Fault Codes ........................................................................................... 4-15
5 List of Replaceable Parts.................................................................... 5-1
5-1. Introduction........................................................................................... 5-3
5-2. How to Obtain Parts.............................................................................. 5-3
5-3. Service Centers ..................................................................................... 5-3
5-4. Parts List ............................................................................................... 5-3
iii
5700A/5720A Series II
Service Manual
iv
List of Tables
Table Title Page
1-1. Auxiliary Amplifier Data ....................................................................................... 1-6
3-1. Standards for Calibrating 5700A/5720A Series II ................................................. 3-5
3-2. List of Required Equipment for Main Output........................................................ 3-22
3-3. Equipment Required for Resistance Testing.......................................................... 3-23
3-4. Low Value Resistance Calibration Using a Current Source .................................. 3-25
3-5. Equipment Required for DC Voltage Testing........................................................ 3-26
3-6. Equipment Required for Direct Current Test......................................................... 3-28
3-7. Equipment Required for AC V Output Level Tests............................................... 3-29
3-8. 5790A Adjustment Counts..................................................................................... 3-31
3-9. Equipment Required for 22 mA to 11A Alternating Current Test Using the
5790A Input 1 ........................................................................................................ 3-31
3-10. Equipment Required for Alternating Current Accuracy Test for the 2 mA and
200 uA Ranges ....................................................................................................... 3-34
3-11. Equipment Required for Testing and Calibrating the Wideband Option............... 3-37
3-12. Wideband Adjustment Tolerance........................................................................... 3-38
3-13. Equipment Required For DC V Optional Tests ..................................................... 3-40
3-14. Equipment Required for Distortion Test................................................................ 3-43
3-15. Minimum Use Requirements.................................................................................. 3-45
3-16. 5720A Resistance Test Record .............................................................................. 3-48
3-17. 5700A Resistance Test Record .............................................................................. 3-50
3-18. DC Voltage Test Record for 5720A....................................................................... 3-52
3-19. DC Voltage Test Record for 5700A....................................................................... 3-53
3-20. Direct Current Accuracy Test Record (5720A) ..................................................... 3-54
3-21. Direct Current Accuracy Test Record (5700A) ..................................................... 3-55
3-22. AC Voltage Frequency Accuracy Test Record ...................................................... 3-55
3-23. 5720A AC Voltage Output Test Record ................................................................ 3-56
3-24. 5700A AC Voltage Output Test Record ................................................................ 3-58
3-25. AC Voltage 2 mV Range Test Record ................................................................... 3-59
3-26. 5720A AC Current 20 mA to 10A Accuracy Test Record..................................... 3-60
3-27. 5700A AC Current 20 mA to 10A Accuracy Test Record..................................... 3-61
3-28. 5720A AC Current 2 mA and 200 mA Accuracy Test Record.............................. 3-62
3-29. 5700A AC Current 2 mA and 200μA Accuracy Test Record................................ 3-62
3-30. Wideband Frequency Accuracy Testi Record........................................................ 3-63
v
5700A/5720A Series II
Service Manual
3-31. Wideband Accuracy at 1 kHz Test Record ............................................................ 3-64
3-32. Wideband Flatness Test Record............................................................................. 3-64
3-33. Wideband Absolute Error 10 Hz to 500 kHz ......................................................... 3-66
3-34. Load Regulation Test Record................................................................................. 3-67
3-35. DC Voltage Linearity Test Record........................................................................ 3-67
3-36. DC Voltage Output Noise Test .............................................................................. 3-67
3-37. AC V Distortion Test Summary............................................................................. 3-68
3-38. Test Record for Flatness Check of the AC 2 mV Range........................................ 3-68
5-1. Front Panel Final Assembly ................................................................................... 5-4
vi
List of Figures
Figure Title Page
1-1. Time and Costs: Calibrator Calibration.................................................................. 1-10
2-1. Digital Section Block Diagram .............................................................................. 2-4
2-2. Analog Section Block Diagram, Part ..................................................................... 2-7
2-3. Analog Section Block Diagram, Part ..................................................................... 2-8
3-1. 732B External Calibration Connections................................................................. 3-7
3-2. 742A-1 and 742A-10k External Calibration Connections ..................................... 3-10
3-3. 220V DC Range Calibration Connections ............................................................. 3-15
3-4. Wideband Module Calibration Connection............................................................ 3-17
3-5. Overview of Verification Tests .............................................................................. 3-20
3-6. 1 Ohm and 10 Ohm Resistor Verification.............................................................. 3-24
3-7. Direct Current Accuracy Test Setup ...................................................................... 3-28
3-8. 1 MHz Low Pass Filter........................................................................................... 3-29
3-9. AC Voltage Test Setup........................................................................................... 3-30
3-10. Alternating Current Test Setup .............................................................................. 3-33
3-11. Alternating Current Test Setup2 mA and 200 μA.................................................. 3-34
3-12. Metal Film Resistor Equivalent Circuit.................................................................. 3-35
3-13. Metal Film Resistor in Test Circuit........................................................................ 3-35
3-14. Wideband Accuracy at 1 kHz Test Setup............................................................... 3-37
3-15. Wideband Flatness Test Setup ............................................................................... 3-38
3-16. DC Voltage Linearity Test ..................................................................................... 3-41
3-17. DC Voltage Output Noise Test Setup .................................................................... 3-42
3-18. Determining Other Test Limits .............................................................................. 3-47
4-1. Accessing the Fuse................................................................................................. 4-3
4-2. Air Filter................................................................................................................. 4-4
4-3. Rear Panel Removal............................................................................................... 4-5
4-4. Rear Panel Assembly Access................................................................................. 4-6
4-5. Front Panel Removal.............................................................................................. 4-7
4-6. Analog and Digital Assemblies.............................................................................. 4-9
5-1. Front Panel Final Assembly ................................................................................... 5-5
5-2. Chassis Final Assembly ......................................................................................... 5-7
5-3. Rear Panel Final Assembly ................................................................................... 5-10
vii
5700A/5720A Series II
Service Manual
viii
Interference Information
This equipment generates and uses radio frequency energy and if not installed and used in strict
accordance with the manufacturer’s instructions, may cause interference to radio and television
reception. It has been type tested and found to comply with the limits for a Class B computing
device in accordance with the specifications of Part 15 of FCC Rules, which are designed to
provide reasonable protection against such interference in a residential installation.
Operation is subject to the following two conditions:
• This device may not cause harmful interference.
• This device must accept any interference received, including interference that may cause
undesired operation.
There is no guarantee that interference will not occur in a particular installation. If this equipment
does cause interference to radio or television reception, which can be determined by turning the
equipment off and on, the user is encouraged to try to correct the interference by one of more of
the following measures:
• Reorient the receiving antenna
• Relocate the equipment with respect to the receiver
• Move the equipment away from the receiver
• Plug the equipment into a different outlet so that the computer and receiver are on different
branch circuits
If necessary, the user should consult the dealer or an experienced radio/television technician for
additional suggestions. The user may find the following booklet prepared by the Federal
Communications Commission helpful: How to Identify and Resolve Radio-TV Interference
Problems. This booklet is available from the U.S. Government Printing Office, Washington, D.C.
20402. Stock No. 004-000-00345-4.
Declaration of the Manufacturer or Importer
We hereby certify that the Fluke Model 5700A/5720A Series II Calibrator is in compliance with
BMPT Vfg 243/1991 and is RFI suppressed. The normal operation of some equipment (e.g.
signal generators) may be subject to specific restrictions. Please observe the notices in the users
manual. The marketing and sales of the equipment was reported to the Central Office for
Telecommunication Permits (BZT). The right to retest this equipment to verify compliance with
the regulation was given to the BZT.
Bescheinigung des Herstellers/Importeurs
Hiermit wird bescheinigt, daβ Fluke Models 5700A/5720A Series II Calibrator in Übereinstimung
mit den Bestimmungen der BMPT-AmtsblVfg 243/1991 funk-entstört ist. Der vorschriftsmäßige
Betrieb mancher Geräte (z.B. Meßsender) kann allerdings gewissen Einschränkungen
unterliegen. Beachten Sie deshalb die Hinweise in der Bedienungsanleitung. Dem Bundesamt für
Zulassungen in der Telekcommunikation wurde das Inverkehrbringen dieses Gerätes angezeigt
und die Berechtigung zur Überprüfung der Seire auf Einhaltung der Bestimmungen eingeräumt.
Fluke Corporation
OPERATOR SAFETY
SUMMARY
WARNING
HIGH VOLTAGE
is used in the operation of this equipment
LETHAL VOLTAGE
may be present on the terminals, observe all safety precautions!
To avoid electrical shock hazard, the operator should not electrically contact
the output hi or sense hi binding posts. During operation, lethal voltages of
up to 1100V ac or dc may be present on these terminals.
Whenever the nature of the operation permits, keep one hand away from
equipment to reduce the hazard of current flowing thought vital organs of
the body.
Terms in this Manual
This instrument has been designed and tested in accordance with IEC Publication 348,
Safety Requirements for Electronic Measuring Apparatus. This manual contains
information and warnings which have to be followed by the user to ensure safe operation
and to retain the instrument in safe condition.
Warning statements identify conditions or practices that could result in personal injury or
loss of life.
Caution statements identify conditions or practices that could result in damage to the
equipment or other property.
Symbols Marked on Equipment
S DANGER — High Voltage
Q Protective ground (earth) terminal
P Attention — refer to the manual. This symbol indicates that information about
the usage of a feature is contained in the manual.
Power Source
The 5700A/5720A Series II is intended to operate from a power source that will not apply more
than 264V ac rms between the supply conductors or between either supply conductor and ground.
A protective ground connection by way of the grounding conductor in the power cord is essential
for safe operation.
Use the Proper Fuse
To avoid fire hazard, use only the fuse specified on the line voltage selection switch label, and
which is identical in type voltage rating, and current rating.
Grounding the 5700A/5720A Series II
The 5700A/5720A Series II is Safety Class I (grounded enclosure) instruments as defined in IEC
348. The enclosure is grounded through the grounding conductor of the power cord. To avoid
electrical shock, plug the power cord into a properly wired earth grounded receptacle before
connecting anything to any of the 5700A/5720A Series II terminals. A protective ground
connection by way of the grounding conductor in the power cord is essential for safe operation.
Use the Proper Power Cord
Always use the power (line) cord and connector appropriate for the voltage and outlet of
the country or location in which you are working.
Always match the line cord to the instrument.
• Use the AC line cord supplied with this instrument with this instrument only.
• Do not use this line cord with any other instruments.
• Do not use any other line cords with this instrument.
Use only the power cord and connector appropriate for proper operation of a 5700A/5720A
Series II in your country.
Use only a power cord that is in good condition.
Refer cord and connector changes to qualified service personnel.
Do Not Operate in Explosive Atmospheres
To avoid explosion, do not operate the 5700A/5720A Series II in an atmosphere of explosive gas.
Do Not Remove Cover
To avoid personal injury or death, do not remove the 5700A/5720A Series II cover. Do not
operate the 5700A/5720A Series II without the cover properly installed. There are no user-
serviceable parts inside the 5700A/5720A Series II, so there is no need for the operator to ever
remove the cover.
Do Not Attempt to Operate if Protection May be Impaired
If the 5700A/5720A Series II appears damaged or operates abnormally, protection may be
impaired. Do not attempt to operate it. When in doubt, have the instrument serviced.
.SERVICING SAFETY
SUMMARY
FOR QUALIFIED SERVICE
PERSONNEL ONLY
Also refer to the preceding Operator Safety Summary
Do Not Service Alone
Do not perform internal service or adjustment of this product unless another person
capable of rendering first aid and resuscitation is present.
Use Care When Servicing With Power On
Dangerous voltage exist at many points inside this product. To avoid personal injury, do
not touch exposed connections and components while power is on.
Whenever the nature of the operation permits, keep one hand away from equipment to
reduce the hazard of current flowing through vital organs of the body.
Do not wear a grounded wrist strap while working on this product. A grounded wrist strap
increase the risk of current flowing through the body.
Disconnect power before removing protective panels, soldering, or replacing components.
High voltage may still be present even after disconnecting power.
FIRST AID FOR
ELECTRIC SHOCK
Free the Victim From the Live Conductor
Shut off high voltage at once and ground the circuit. If high voltage cannot be turned off
quickly, ground the circuit.
If the circuit cannot be broken or grounded, use a board, dry clothing, or other
nonconductor to free the victim.
Get Help!
Yell for help. Call an emergency number. Request medical assistance.
Never Accept Ordinary and General Tests for Death
Symptoms of electric shock may include unconsciousness, failure to breathe, absence of
pulse, pallor, and stiffness, and severe burns.
Treat the Victim
If the victim is not breathing, begin CPR or mouth-to-mouth resuscitation if you are
certified.
Chapter 1
Introduction and Specifications
Title Page
1-1. Introduction........................................................................................... 1-3
1-2. Contacting Fluke................................................................................... 1-4
1-3. About this Manual ................................................................................ 1-4
1-4. How to Use this Manual ....................................................................... 1-4
1-5. Wideband AC Voltage Module (Option 5700A-03) ............................ 1-5
1-6. Auxiliary Amplifiers............................................................................. 1-6
1-7. 5725A Amplifier .............................................................................. 1-6
1-8. Support Equipment and Services.......................................................... 1-6
1-9. 732B Direct Voltage Reference Standard ........................................ 1-7
1-10. 732B-200 Direct Volt Maintenance Program (U.S.A. Only) ........... 1-7
1-11. 742A Series Resistance Standards.................................................... 1-7
1-12. Wideband AC Module (Option 5700A-03) Calibration Support ..... 1-7
1-13. Service Centers................................................................................. 1-8
1-14. The Components of the 5700A/5720A Series II Calibrator ................. 1-8
1-15. Calibrating the 5700A/5720A Series II Calibrator ............................... 1-8
1-16. The Calibration Process.................................................................... 1-10
1-17. Establishing Traceability.................................................................. 1-10
1-18. Calibration Reports........................................................................... 1-10
1-19. Calibration Check ................................................................................. 1-10
1-20. Developing a Performance History....................................................... 1-11
1-21. Range Calibration ................................................................................. 1-11
1-22. DC Zeros Calibration............................................................................ 1-11
1-23. Specifications........................................................................................ 1-11
1-24. Specification Confidence Levels...................................................... 1-12
1-25. Using Absolute and Relative Uncertainty Specifications................. 1-12
1-26. Using Secondary Performance Specifications.................................. 1-12
1-27. General Specifications .......................................................................... 1-13
1-28. Electrical Specifications ....................................................................... 1-14
1-29. DC Voltage Specifications ............................................................... 1-14
1-30. AC Voltage Specifications ............................................................... 1-17
1-31. Resistance Specifications ................................................................. 1-28
1-32. DC Current Specifications................................................................ 1-32
1-33. AC Current Specifications................................................................ 1-35
1-34. Wideband AC Voltage (Option 5700-03) Specifications................. 1-40
1-35. Auxiliary Amplifier Specifications .................................................. 1-41
1-1
5700A/5720A Series II Calibrator
Service Manual
1-2
Introduction and Specifications
Introduction 1
1-1. Introduction
The Fluke Model 5700A/5720A Series II calibrators are precise instruments that calibrate
a wide variety of electrical measuring instruments. These calibrators maintain high
accuracy over a wide ambient temperature range, allowing them to test instruments in any
environment, eliminating the restrictions to calibrate only in a temperature-controlled
standards laboratory. With a 5700A/5720A Series II, you can calibrate precision
multimeters that measure ac or dc voltage, ac or dc current, and resistance. The 5720A
Series II operates in a similar manner to the 5700A Series II, the difference is that the
5720A Series II has a considerably higher specified accuracy. Option 5700A-03
Wideband AC Voltage, which is available for both the 5700A Series II and the 5720A
Series II, extends this workload to include rf voltmeters.
Specifications are provided at the end of this chapter. The calibrator is a fully-
programmable precision source of the following:
• DC voltage to 1100V
• AC voltage to 1100V, with output available from 10 Hz to 1.2 MHz.
• AC and DC current to 2.2A, with output available from 10 Hz to 10 kHz
n n
• Resistance in values of 1x10 and 1.9x10 from 1Ω to 100 MΩ, plus a short.
• Optional wideband ac voltage from 300 µV to 3.5V into 50Ω (-57 dBm to +24 dBm),
10 Hz to 30 MHz.
Features of the calibrator include the following:
• Internal environmentally-controlled references allowing the calibrator to maintain
full performance over a wide ambient temperature range.
• Automatic meter error calculation obtained through using a simple output adjust
knob; the display shows linearity, offset, and scale errors.
• Keys that multiply and divide the output value by 10 to simplify work on meters with
calibration points at decade multiples of a fraction of full-scale.
• Programmable entry limits used for restricting the levels that can be keyed into the
calibrator, preventing access to levels that may be harmful to equipment or personnel.
• A s key that provides the capability of displaying the instrument’s specification at
the selected operating point, calibration interval, and specification confidence level.
• An auxiliary current binding post that allows you to calibrate meters with separate
current inputs without moving cables.
• Real-time clock and calendar for date stamping reports.
• Offset and scaling modes that simplify linearity testing of multimeters.
• Variable phase reference signal output and phase-lock input.
• Interface for the Fluke 5725 Amplifier.
• Standard IEEE-488 (GPIB) interface, complying with ANSI/IEEE Standards 488.1-
1987 and 488.2-1987.
• Selectable normal remote mode or emulation of the Fluke 5100B and 5200A Series
calibrators in functions and response to system controller software
• EIA Standard RS-232C serial data interface for printing, displaying, or transferring
internally-stored calibration constants, and for remote control of the calibrator.
• Extensive internal self testing and diagnostics of analog and digital functions.
1-3
5700A/5720A Series II Calibrator
Service Manual
• A traceable calibration procedure for all modes and ranges that requires only 10V,
1Ω, and 10 kΩ external standards, with only occasional independent verification.
• Fast, simple, automated calibration check providing added confidence between
calibration recalls, and data that can be used to document and characterize the
calibrator’s performance between calibration recalls.
1-2. Contacting Fluke
To order accessories, receive operating assistance, or get the location of the nearest Fluke
distributor or Service Center, call:
USA: 1-888-44-FLUKE (1-888-443-5853)
Canada: 1-800-36-FLUKE (1-800-363-5853)
Europe: +31 402-675-200
Japan: +81-3-3434-0181
Singapore: +65-738-5655
Anywhere in the world: +1-425-446-5500
Or, visit Fluke's Web site at www.fluke.com.
1-3. About this Manual
This manual provides complete information for installing the calibrator and operating it
from the front panel keys and in remote. It also provides a glossary of calibration-related
terms as well as general items such as specifications and error code information. The
following topics are covered in this manual:
• Installation
• Operating controls and features
• Front panel operation
• Remote operation (IEEE-488 bus or serial port remote control)
• Serial port operation (printing, displaying, or transferring data, and setting up for
serial port remote control)
• Operator maintenance, including how to calibrate the 5700A/5720A Series II
• Options and accessories
1-4. How to Use this Manual
Use the following list to find the location of specific information.
• Quick setup procedure: 5700A/5720A Series II Operators Reference Guide
• Unpacking and setup: Chapter 2.
• Installation and rack mounting: Chapter 2; also the rack mount kit instruction sheet
• AC line power and interface cabling: Chapter 2
• Controls, indicators, and displays: Chapter 3
• Front panel operation: Chapter 4
• Cabling to a UUT (Unit Under Test): Chapter 4
• Using auxiliary amplifiers: Chapter 4
• Self calibration: Chapters 1 and 7
1-4
Introduction and Specifications
Wideband AC Voltage Module (Option 5700A-03) 1
• Remote operation (IEEE-488 or serial): Chapter 5
• Options and accessories: Chapters 2 and 8
• Instrument specifications: The end of this Chapter
• Theory of operation: Chapter 2 of the 5700A/5720A Series II Service Manual
1-5. Wideband AC Voltage Module (Option 5700A-03)
The Wideband AC Voltage Module (Option 5700A-03) can be installed in both the
5700A and 5720A Series II Calibrators. The module is a high-accuracy, low-noise,
extremely flat ac voltage source for calibrating rf voltmeters, with a frequency range of
10 Hz to 30 MHz. Output is in seven ranges from 300 µV (-57 dBm) to 3.5 V (+24 dBm)
through a Type-N coaxial connector into a 50 Ω load. The output level is selected in volts
or dBm through either the front panel controls or under remote control.
The wideband module also functions with the calibrator’s output adjust controls that let
display the error of a wideband meter in either percentage of output or in decibels.
Included with the wideband module is a Type-N output cable and a 50 Ω terminator. The
wideband module is calibrated to the end of its standard-equipment output cable.
1-5
5700A/5720A Series II Calibrator
Service Manual
1-6. Auxiliary Amplifiers
The Fluke Model 5725A Amplifier is available to extend the high voltage performance
and current range of the calibrator:
Interface connectors on the calibrator’s rear panel accept cables to directly operate a
5725A. Three amplifiers can be connected to the calibrator at the same time, but only one
output can be active at a time. Once you have connected the amplifiers and configured
the calibrator in a setup menu, amplifier operation is controlled by the calibrator.
Chapter 4 provides instructions for operating the 5725A. The general specifications at the
end of this chapter include specifications for operating the calibrator with the 5725A. For
other amplifier specifications, refer to their instruction manuals. Table 1-1 summarizes
the extended capabilities offered by the 5725A. Brief descriptions of the extended
capabilities follow.
Table 1-1. Auxiliary Amplifier Data
Model Mode Range
5725A Amplifier AC V 220 to 1100V rms up to 70 mA, 40 Hz to 30 kHz
(50 mA < 5 kHz)
220 to 750V rms up to 70 mA, 30 kHz to 100 kHz
DC Amps 0 to ±11A
AC Amps 1 to 11A rms, 40 Hz to 10 kHz
1-7. 5725A Amplifier
The Fluke 5725A Amplifier is an external unit operating under calibrator control to
extend ac voltage drive capabilities and both ac and dc current output range. The
amplifier adds the following capabilities to the calibrator’s 1100V ac range with no
compromise in accuracy:
• Frequency limits at higher voltage increase to 100 kHz at 750V, 30 kHz at 1100V.
• Load limit increases to 70 mA for frequencies above 5 kHz.
• Capacitive drive increases to 1000 pF, subject to the maximum output current.
Extended-performance voltage is available at the calibrator’s front or rear binding posts,
eliminating the need to change cables during a procedure.
A separate set of binding posts on the front panel of the 5725A supplies extended-range
ac and dc current outputs. Since most meters have a separate input terminal for the high
current ranges, this eliminates the need to change cables during a procedure. The 5725A
can also be configured to source all current (both standard calibrator-generated current
and its own current) through the 5725A binding posts.
1-8. Support Equipment and Services
Fluke supports your calibration needs with precision, high-quality equipment and a wide
range of services. Depending on your needs, location, and capabilities, you may decide to
support your 5700A/5720A Series II calibrator independently or use Fluke services for
part, or all, of your support needs. The following paragraphs describe the support
equipment and services offered by Fluke for the calibrator. For specifications and
ordering instructions for this support equipment and other Fluke instruments, refer to the
Fluke catalog, or contact a representative at a Fluke Sales and Service Center.
1-6
Introduction and Specifications
Support Equipment and Services 1
1-9. 732B Direct Voltage Reference Standard
The Fluke 732B is a rugged, easily transported solid state direct voltage reference
standard with a highly predictable 10V output. This predictability allows the Fluke
Standards Laboratory, as well as many Fluke customers, to completely eliminate fragile,
saturated standard cells. Laboratories still maintain standard cells using the 732A and
732B as a transportable voltage standard, eliminating the need to transport their standard
cells. The 732B can be short-circuited, even for extended periods of time, without
damage or loss of stability. It maintains full specified stability over a temperature span of
18 to 28 °C.
The calibrator uses a 10V reference standard such as the Fluke 732B in its semi-
automated calibration procedure to establish external voltage traceability. Chapter 7
describes this procedure.
1-10. 732B-200 Direct Volt Maintenance Program (U.S.A. Only)
The Fluke 732B-200 Direct Volt Maintenance Program provides your laboratory with
NIST-traceable 10V calibration uncertainty as low as 0.6 parts per million.
The program maintains the 732B that you keep in your laboratory. To accomplish this,
the following occurs:
1. Fluke sends you a calibrated Fluke-owned 732B standard, together with all necessary
connecting cables and instructions for comparison with your 10V reference standard.
2. You take a series of readings over a five-day period, and return the results to the
Fluke Standards Laboratory.
3. The Fluke Standards Laboratory assigns a value to your 10V standard relative to the
NIST legal volt and sends you a report of calibration.
1-11. 742A Series Resistance Standards
The calibrator uses 1Ω and 10 kΩ resistor standards such as the 742A Series in its semi-
automated calibration procedure to establish external traceability of resistance and
current. Chapter 7 describes this procedure.
The 742A Resistance Standards, which are constructed of arrays of Fluke wirewound
precision resistors, are ideally suited as support standards for the calibrator. Stability of
the resistance transfer standards and their temperature coefficients make them ideal for
easy transport to and operation in the calibrator's working environment.
1-12. Wideband AC Module (Option 5700A-03) Calibration Support
The Wideband AC Module (Option 5700A-03) requires two kinds of calibration: gain
and flatness. Gain constants are checked and recalibrated as a part of the normal
calibrator semi-automated calibration process.
Since frequency flatness is determined by such stable parameters as circuit geometry and
dielectric constants, flatness of the Wideband AC module has excellent long-term
stability. This stability gives the Wideband AC Module a two-year calibration cycle for
flatness calibration. Flatness calibration is required only infrequently, and can be done
when the calibrator is returned to a standards laboratory for periodic verification. The
5700A/5720A Series II Service Manual contains the wideband flatness calibration
procedure. Chapter 7 of this manual contains the wideband gain calibration procedure.
1-7
5700A/5720A Series II Calibrator
Service Manual
1-13. Service Centers
A worldwide network of Fluke service centers supports Fluke instruments and assists
customers in many ways. Most service centers have standards and calibration laboratories
certified by local national standards organizations. The following is a partial list of the
services provided by most service centers:
• Repair and certified traceable calibration of all Fluke products.
• Certified traceable calibration of many non-Fluke standards and calibrators.
• Worldwide exchange of calibrator internal modules. Delivery inside the U.S.A. is
typically within 48 hours.
• Service agreements with the flexibility to suit your needs. These can be a simple
warranty extension or an agreement that includes on-site support. Calibration service
agreements are also available in many areas.
• Training programs and seminars, including laboratory metrology, system
applications, and product maintenance.
• Application help and consulting, including system design, hardware selection,
custom software, site evaluation and installation.
• Replacement parts inventory, including recommended spare parts and module kits.
• Visit www.fluke.com for locations and phone numbers of authorized Fluke service
centers.
1-14. The Components of the 5700A/5720A Series II Calibrator
The calibrator is configured internally as an automated calibration system, with process
controls and consistent procedures. Internal microprocessors control all functions and
monitor performance, using a switching matrix to route signals between modules.
Complete automatic internal diagnostics, both analog and digital, confirm operational
integrity.
Reference amplifiers maintain dc accuracy and stability. Of all technologies available,
reference amplifiers have the lowest noise and best stability. Reference amplifiers in the
calibrator go through special selection processes including long-term aging to ensure high
reliability and performance well within specifications.
The calibrator achieves its exceptional ac voltage accuracy by using a patented Fluke rms
sensor to make real-time ac/dc comparison measurements. The Fluke rms sensor is
similar in principle to the traditional thermal voltage converter, but has a shorter time
constant, virtually no reversal error, higher signal-to-noise ratio, and better frequency
response. In the calibrator, one Fluke rms sensor serves as an ac/dc transfer standard to
develop gain and flatness correction constants during calibration. The second Fluke rms
sensor continuously monitors and corrects output voltage during operation.
A patented 26-bit digital-to-analog converter (dac) provides the calibrator with the ability
to precisely vary its output. This is a pulse-width modulated dac with linearity typically
better than 0.2 ppm of full scale. As with the other internal functions, the linearity of the
dac is automatically checked during calibration and analog diagnostics.
1-15. Calibrating the 5700A/5720A Series II Calibrator
The traditional practice of returning a calibrator to a standards laboratory at regular
intervals for a full calibration is time consuming, expensive, and disruptive to the task to
1-8
Introduction and Specifications
Calibrating the 5700A/5720A Series II Calibrator 1
which the calibrator is being applied. Moreover, it leaves gaps in confidence. You must
rely on manufacturer's specifications to determine if a calibrator will perform acceptably
in an operating environment outside the lab. Also, you must assume that drift is
predictable enough so that performance is within limits between recalls.
The 5700A/5720A Series II Calibrator makes use of Fluke design breakthroughs in the
use of internal check standards and measurement systems. As a result, it can be
completely calibrated in place to full specifications using a small number of convenient,
portable, environmentally tolerant standards available from Fluke. As you will see below,
this procedure is traceable to military standard requirements.
When manufactured, each calibrator is calibrated and thoroughly verified with process
metrology and calibration standards traceable to the U.S. National Bureau of Standards.
A certificate of calibration is included.
A calibration verification procedure described in the 5700A/5720A Series II Service
Manual is recommended every two years, or as required by your established policies.
This procedure involves no adjustments. It simply ensures internal processes are in
control, and establishes parallel external traceability paths for internal functions such as
ac transfers that are never adjusted or corrected.
Figure 1-1 illustrates the time and money that can be saved by using the 5700A/5720A
Series II calibration support plan recommended by Fluke. Depending on your policies,
you may initially decide to perform calibration verification more often. The calibrator
makes this unnecessary and offers you a practical way to collect data unavailable with a
traditional calibrator design about performance between calibrations.
TRADITIONAL CALIBRATOR CALIBRATION
CALIBRATION CYCLE
TIME
5700A/5720A SERIES II CALIBRATION
CALIBRATION CYCLE
TIME
f1-1.eps
Figure 1-1. Time and Costs: Calibrator Calibration
1-9
COST $
COST $
5700A/5720A Series II Calibrator
Service Manual
1-16. The Calibration Process
Calibration requires only three external standards: 10V, 1Ω, and 10 kΩ.
Environmentally-controlled internal check standards provide the primary reference
points. A stored table of calibration constants defines additional reference points for
controlling the output. Traceable calibration and adjustment to the specified level of
performance is accomplished in a semi-automated process that revises this table.
When you finish calibration, but before you save the new constants, the calibrator
presents you with the proposed adjustments as +/- ppm of range and percentage change in
specification for each range and function. You can print a list of changes through the
serial (RS-232C) port, or send them to a computer through either the serial port or the
IEEE-488 port. Also on completion of calibration, the calibrator displays the largest
proposed change.
Calibration can be completed as far as deriving and printing the proposed adjustments
without changing the setting of the rear panel CALIBRATION switch; however, the
switch must be set to ENABLE to store the changes in nonvolatile memory and make
them effective. The switch is recessed to allow the metrologist to cover it with a
calibration sticker to guarantee calibrator integrity.
1-17. Establishing Traceability
Traceability to national standards is established as follows:
• Except for the internal ac/dc transfer standard, the internal check standards are
directly calibrated by traceable external standards every time the 5700A/5720A
Series II is calibrated.
• The internal ac/dc transfer standard is never adjusted, so its traceability is not
disturbed by calibration. Infrequent verification is done in the traditional way, by
comparing selected ac voltage outputs with an external dc voltage standard through
an external ac/dc transfer standard. Fluke recommends this be done every two years,
or as determined by the policy of your organization.
• Infrequent independent verification is also performed on stable parameters, such as
frequency flatness, determined more by circuit geometry and dielectric constants than
time.
1-18. Calibration Reports
The calibrator stores two sets of calibration constants: the set currently in use and the old
set from the previous calibration. This gives the calibrator the ability at any time to
produce a calibration report of the differences between the present settings and the
settings that were in effect before the last calibration. The report shows changes for each
range and function in +/- ppm of range and in percentage of specification limit. You can
print the report or send it to a host computer through either the RS-232-C or IEEE-488
interface.
If you request a calibration report after doing calibration but before saving the new
constants, the report shows proposed changes to the calibration constants relative to the
previously stored settings.
1-19. Calibration Check
Checking the calibration takes about an hour, and provides you with a means of
documenting the calibrator’s performance of a between calibrations. Calibration checking
1-10
Introduction and Specifications
Developing a Performance History 1
is similar to calibration, except internal check standards are used as primary references
(no external standards are needed), and changes cannot be stored. The process produces a
report similar to normal calibration, showing drift relative to internal check standards.
Because cal check does not change stored calibration constants, there is no need to enable
the rear panel CALIBRATION switch. Therefore, an external computer can do the
procedure unattended.
1-20. Developing a Performance History
A Fluke specification is a set of performance limits that all products must meet. To
maintain consistent quality, Fluke calibrators are specified with enough margin to include
temperature, line, and load extremes, plus additional margin for production. This means
that a typical 5700A/5720A Series II calibrator in a typical environment operates inside
50% of specification limits. For some exacting applications, it can be helpful to know just
how accurately a particular calibrator operates. The proper way to do this is to
accumulate a performance history by calibrating regularly and recording results on a
control chart.
Calibrating regularly and recording the results on a control chart is tedious and requires a
large array of equipment. The calibrator’s calibration check feature is an alternative with
some distinct advantages:
• Calibrated check standards are already programmed into the unit. You do not have to
use external standards.
• The process is consistent and automatic: it does not require an operator’s assistance.
Each calibration check produces a new set of data points for accumulating a historical
record. When this process is externally automated, significant history can be accumulated
much faster than with a manual calibration.
1-21. Range Calibration
After calibration, you can make further fine adjustments to each range. Range
adjustments are optional; they are not necessary to meet total uncertainty specifications.
However, they do allow you to align your calibrator closer to your standards.
Before you do range calibration, you must first use the calibrator’s semi-automated
calibration procedure. This is to calibrate the ranges that will not be adjusted. It also
performs an initial adjustment for each range, and supplies flatness corrections for ac
functions.
1-22. DC Zeros Calibration
To ensure the validity of the specifications, a dc zeros calibration must be performed at
least every 30 days. If more than 30 days elapse without a dc zeros calibraiton a warning
message appears. This procedure does not require any external equipment or connections
and takes approximately 2.5 minutes to complete.
1-23. Specifications
The 5700A/5720A Series II calibrators are verified and calibrated at the factory prior to
shipment to ensure they meet the accuracy standards required for all certified calibration
laboratories. By calibrating to the specifications in this chapter, you can maintain the high
performance level throughout the life of your calibrator.
1-11
5700A/5720A Series II Calibrator
Service Manual
Specifications are valid after a warm-up period of twice the time the calibrator has been
turned off, up to a maximum of 30 minutes. For example, if the calibrator has been turned
off for five minutes, the warm-up period is ten minutes.
1-24. Specification Confidence Levels
You calibrator’s performance level is ensured by regular calibration to the primary
performance specifications, which are provided at both the 99% and 95% confidence
levels. The 95% confidence level will provide an accuracy that surpasses the accuracy
requirements for meeting Tag 4 standards, or a coverage factor of 2. Calibration at the
99% confidence level is also available for those applications that require a confidence
factor for the specifications that is higher than 95%. For information on selecting the
confidence level, refer to Chapter 4.
The tables in this chapter provide specifications at both the 95% and 99% confidence
levels for the 5700A/5720A Series II calibrators. Included with these tables are operating
specifications for using the calibrator with the Wideband AC Module (Option 5700A-03)
and the 5725A Amplifier.
1-25. Using Absolute and Relative Uncertainty Specifications
To evaluate the 5700A/5720A Series II coverage of your calibration workload, use the
Absolute Uncertainty specifications. Absolute uncertainty includes stability, temperature
coefficient, linearity, line and load regulation, and the traceability to external standards.
You do not need to add anything to absolute uncertainty to determine the ratios between
the calibrator’s uncertainties and the uncertainties of your calibration workload.
Relative uncertainty specifications are provided for enhanced accuracy applications.
These specifications apply when range constants are adjusted (see “Range Calibration”).
To calculate absolute uncertainty, you must combine the uncertainties of your external
standards and techniques with relative uncertainty.
1-26. Using Secondary Performance Specifications
Secondary performance specifications and operating characteristics are included in
uncertainty specifications. They are provided for special calibration requirements such as
stability or linearity testing.
1-12
Introduction and Specifications
General Specifications 1
1-27. General Specifications
Standard Interfaces .............................................. IEEE-488, RS-232, 5725A, 5205A or 5215A, 5220A, phase lock in
(BNC), phase reference out (BNC).
Temperature Performance
Operating ............................................................ 0 °C to 50 °C
Calibration........................................................... 15 °C to 35 °C
Storage ............................................................... -40 °C to 75 °C
Relative Humidity
Operating ............................................................ <80 % to 30 °C, <70 % to 40 °C, <40 % to 50 °C
Storage ............................................................... <95 %, non-condensing. A power stabilization period of four days may
be required after extended storage at high temperature and humidity.
Safety ..................................................................... Designed to comply with UL3111; EN61010; CSA C22.2 No. 1010;
ANSI/ISA S82.01-1994
Guard Isolation...................................................... 20 V
EMI/RFI................................................................... Designed to comply with FCC Rules Part 15, Subpart B, Class B;
EN50081-1, EN50082-1
ElectroStatic Discharge........................................ This instrument meets criteria C for ESD requirements per EN61326
Line Power
Line Frequency .................................................. 47 to 63 Hz; ±10 % 100 V, 110 V, 115 V, 120 V, 200 V, 220 V, 230 V,
240 V
Maximum Power
5700A/5720A .................................................. 300 VA
5725A ............................................................. 750 VA
Weight
5700A/5720A ...................................................... 27 kg (62 lb)
5725A.................................................................. 32 kg (70 lb)
Size
5700A/5720A
Height ............................................................. 17.8 cm (7 in), standard rack increment, plus 1.5 cm (0.6 in) for feet
Width............................................................... 43.2 cm (17 in), standard rack width
Depth .............................................................. 63.0 cm (24.8 in), overall; 57.8 cm (22.7 in), rack depth
5725A
Height ............................................................. 13.3 cm (5.25 in)
Width and Depth ............................................. Same as 5700A/5720A. Both units project 5.1 cm (2 in) from rack front.
43.2 cm (17 in)
17.8 cm (7 in)
6.35 cm (2.5 in)
63 cm (24.8 in)
FOR CABLE
ACCESS
1-13
5700A/5720A Series II Calibrator
Service Manual
1-28. Electrical Specifications
Note
Fluke guarantees performance verification using specifications stated to
99% confidence level.
1-29. DC Voltage Specifications
5720A Series II DC Voltage Specifications
Relative Uncertainty
Absolute Uncertainty
[1]
± 1 °C
± 5 °C from calibration temperature
Range Resolution
24 Hours 90 Days 180 Days 1 Year 24 Hours 90 Days
± (ppm output + μV)
99 % Confidence Level
220 mV 10 nV 5 + 0.5 7 + 0.5 8 + 0.5 9 + 0.5 2 + 0.4 2.5 + 0.4
2.2 V 100 nV 3.5 + 0.8 4 + 0.8 4.5 + 0.8 6 + 0.8 2 + 0.8 2.5 + 0.8
11 V 2.5 + 3 3 + 3 3.5 + 3 4 + 3 1 + 3 1.5 + 3
1 μV
22 V 1 μV 2.5 + 5 3 + 5 3.5 + 5 4 + 5 1 + 5 1.5 + 5
220 V 10 μV 3.5 + 50 4 + 50 5 + 50 6 + 50 2 + 50 2.5 + 50
5 + 500 6 + 500 7 + 500 8 + 500 2.5 + 400 3 + 400
1100 V 100 μV
95 % Confidence Level
220 mV 10 nV 4 + 0.4 6 + 0.4 6.5 + 0.4 7.5 + 0.4 1.6 + 0.4 2 + 0.4
2.2 V 100 nV 3 + 0.7 3.5 + 0.7 4 + 0.7 5 + 0.7 1.6 + 0.7 2 + 0.7
2 + 2.5 2.5 + 2.5 3 + 2.5 3.5 + 2.5 0.8 + 2.5 1.2 + 2.5
11 V 1 μV
22 V 2 + 4 2.5 + 4 3 + 4 3.5 + 4 0.8 + 4 1.2 + 4
1 μV
220 V 3 + 40 3.5 + 40 4 + 40 5 + 40 1.6 + 40 2 + 40
10 μV
1100 V 4 + 400 4.5 + 400 6 + 400 6.5 + 400 2 + 400 2.4 + 400
100 μV
Notes:
DC Zeros calibration required every 30 days.
1. For fields strengths >1 V/m but ≤3 V/m, add 0.01 % of range.
1-14
Introduction and Specifications
Electrical Specifications 1
5700A Series II DC Voltage Specifications
Absolute Uncertainty Relative Uncertainty
[1]
± 5 °C from calibration temperature ± 1 °C
Range Resolution
24 Hours 90 Days 180 Days 1 Year 24 Hours 90 Days
± (ppm output + μV)
99 % Confidence Level
220 mV 10 nV 6.5 + .75 7 + .75 8 + .75 9 + .8 2.5 + .5 4 + .5
2.2 V 100 nV 3.5 + 1.2 6 + 1.2 7 + 1.2 8 + 1.2 2.5 + 1.2 4 + 1.2
11 V 3.5 + 3 5 + 4 7 + 4 8 + 4 1.5 + 3 3.5 + 4
1 μV
22 V 3.5 + 6 5 + 8 7 + 8 8 + 8 1.5 + 6 3.5 + 8
1 μV
220 V 5 + 100 6 + 100 8 + 100 9 + 100 2.5 + 100 4 + 100
10 μV
1100 V 7 + 600 8 + 600 10 + 600 11 + 600 3 + 600 4.5 + 600
100 μV
95 % Confidence Level
220 mV 10 nV 5.5 + 0.6 6 + 0.6 7 + 0.6 8 + 0.6 2 + 0.4 3.5 + 0.4
2.2 V 100 nV 3.5 + 1 5 + 1 6 + 1 7 + 1 2 + 1 3.5 + 1
11 V 1 µV 3 + 3.5 4 + 3.5 6 + 3.5 7 + 3.5 1.2 + 3 3 + 3.5
22 V 1 µV 3 + 6.5 4 + 6.5 6 + 6.5 7 + 6.5 1.2 + 6 3 + 7
220 V 10 µV 4 + 80 5 + 80 7 + 80 8 + 80 2 + 80 3.5 + 80
1100 V 100 µV 6 + 500 7 + 500 8 + 500 9 + 500 2.4 + 500 4 + 500
Notes:
DC Zeros calibration required every 30 days.
1. For fields strengths >1 V/m but ≤ 3 V/m, add 0.01 % of range.
1-15
5700A/5720A Series II Calibrator
Service Manual
DC Voltage Secondary Performance Specifications and Operating Characteristics
Temperature Coefficient
Noise
[2]
[1]
Adder
Stability
Linearity
± 1 °C
0 - 10 °C Bandwidth Bandwidth
± 1 °C
Range
24 Hours and 0.1-10 Hz 10 Hz-10 kHz
10 - 40 °C
40 - 50 °C pk-pk RMS
± (ppm output + μV) ± (ppm output + μV) / °C ± (ppm output + μV) μV
220 mV 0.3 + 0.3 0.4 + 0.1 1.5 + 0.5 1 + 0.2 0.15 + 0.1 5
2.2 V 0.3 + 1 0.3 + 0.1 1.5 + 2 1 + 0.6 0.15 + 0.4 15
11 V 0.3 + 2.5 0.15 + 0.2 1 + 1.5 0.3 + 2 0.15 + 2 50
22 V 0.4 + 5 0.2 + 0.4 1.5 + 3 0.3 + 4 0.15 + 4 50
220 V 0.5 + 40 0.3 + 5 1.5 + 40 1 + 40 0.15 + 60 150
1100 V 0.5 + 200 0.5 + 10 3 + 200 1 + 200 0.15 + 300 500
Notes:
1. Stability specifications are included in the Absolute Uncertainty values in the primary specification tables.
2. Temperature coefficient is an adder to uncertainty specifications that does not apply unless operating more than ±5 °C from
calibration temperature.
Minimum Output .................................................. 0 V for all ranges, except 100 V for 1100 V range
Maximum Load ..................................................... 50 mA for 2.2 V through 220 V ranges; 20 mA for 1100 V range; 50 Ω
output impedance on 220 mV range; all ranges <1000 pF, >25 Ω
Load Regulation ................................................... <(0.2 ppm of output + 0.1 ppm of range), full load to no load
Line Regulation .................................................... <0.1 ppm change, ± 10 % of selected nominal line
Settling Time ........................................................ 3 seconds to full accuracy; + 1 second for range or polarity change; + 1
second for 1100 V range
Overshoot ............................................................. <5 %
Common Mode Rejection .................................... 140 dB, DC to 400 Hz
Remote Sensing .................................................. Available 0 V to ±1100 V, on 2.2 V through 1100 V ranges
1-16
Introduction and Specifications
Electrical Specifications 1
1-30. AC Voltage Specifications
5720A Series II AC Voltage Specifications: 99% Confidence Level
Absolute Uncertainty Relative Uncertainty
± 5 °C from calibration temperature ± 1 °C
Frequency
Range Resolution
24 Hours 90 Days 180 Days 1 Year 24 Hours 90 Days
(Hz)
± (ppm output + μV)
2.2 mV 1 nV 10 - 20 250 + 5 270 + 5 290 + 5 300 + 5 250 + 5 270 + 5
20 - 40 100 + 5 105 + 5 110 + 5 115 + 5 100 + 5 105 + 5
40 - 20 k 85 + 5 90 + 5 95 + 5 100 + 5 60 + 5 65 + 5
20 k - 50 k 220 + 5 230 + 5 240 + 5 250 + 5 85 + 5 95 + 5
50 k - 100 k 500 + 6 540 + 6 570 + 6 600 + 6 200 + 6 220 + 6
100 k - 300 k 1000 + 12 1200 + 12 1250 + 12 1300 + 12 350 + 12 400 + 12
300 k - 500 k 1400 + 25 1500 + 25 1600 + 25 1700 + 25 800 + 25 1000 + 25
500 k - 1 M 2900 + 25 3100 + 25 3250 + 25 3400 + 25 2700 + 25 3000 + 25
22 mV 10 nV 10 - 20 250 + 5 270 + 5 290 + 5 300 + 5 250 + 5 270 + 5
20 - 40 100 + 5 105 + 5 110 + 5 115 + 5 100 + 5 105 + 5
40 - 20 k 85 + 5 90 + 5 95 + 5 100 + 5 60 + 5 65 + 5
20 k - 50 k 220 + 5 230 + 5 240 + 5 250 + 5 85 + 5 95 + 5
50 k - 100 k 500 + 6 540 + 6 570 + 6 600 + 6 200 + 6 220 + 6
100 k - 300 k 1000 + 12 1200 + 12 1250 + 12 1300 + 12 350 + 12 400 + 12
300 k - 500 k 1400 + 25 1500 + 25 1600 + 25 1700 + 25 800 + 25 1000 + 25
500 k - 1 M 2900 + 25 3100 + 25 3250 + 25 3400 + 25 2700 + 25 3000 + 25
220 mV 100 nV 10 - 20 250 + 15 270 + 15 290 + 15 300 + 15 250 + 15 270 + 15
20 - 40 100 + 8 105 + 8 110 + 8 115 + 8 100 + 8 105 + 8
40 - 20 k 85 + 8 90 + 8 95 + 8 100 + 8 60 + 8 65 + 8
20 k - 50 k 220 + 8 230 + 8 240 + 8 250 + 8 85 + 8 95 + 8
50 k - 100 k 500 + 20 540 + 20 570 + 20 600 + 20 200 + 20 220 + 20
100 k - 300 k 850 + 25 900 + 25 1000 + 25 1100 + 25 350 + 25 400 + 25
300 k - 500 k 1400 + 30 1500 + 30 1600 + 30 1700 + 30 800 + 30 1000 + 30
500 k - 1 M 2700 + 60 2900 + 60 3100 + 60 3300 + 60 2600 + 60 2800 + 60
2.2 V 1 µV 10 - 20 250 + 50 270 + 50 290 + 50 300 + 50 250 + 50 270 + 50
20 - 40 95 + 20 100 + 20 105 + 20 110 + 20 95 + 20 100 + 20
40 - 20 k 45 + 10 47 + 10 50 + 10 52 + 10 30 + 10 40 + 10
20 k - 50 k 80 + 12 85 + 12 87 + 12 90 + 12 70 + 12 75 + 12
50 k - 100 k 120 + 40 125 + 40 127 + 40 130 + 40 100 + 40 105 + 40
100 k - 300 k 380 + 100 420 + 100 460 + 100 500 + 100 270 + 100 290 + 100
300 k - 500 k 1000 + 250 1100 + 250 1150 + 250 1200 + 250 900 + 250 1000 + 250
500 k - 1 M 1600 + 400 1800 + 600 1900 + 400 2000 + 400 1200 + 400 1300 + 400
22 V 10 µV 10 - 20 250 + 500 270 + 500 290 + 500 300 + 500 250 + 500 270 + 500
20 - 40 95 + 200 100 + 200 105 + 200 110 + 200 95 + 200 100 + 200
40 - 20 k 45 + 70 47 + 70 50 + 70 52 + 70 30 + 70 40 + 70
20 k - 50 k 80 + 120 85 + 120 87 + 120 90 + 120 70 + 120 75 + 120
50 k - 100 k 110 + 250 115 + 250 117 + 250 120 + 250 100 + 250 105 + 250
100 k - 300 k 300 + 800 310 + 800 320 + 800 325 + 800 270 + 800 290 + 800
300 k - 500 k 1000 + 2500 1100 + 2500 1150 + 2500 1200 + 2500 900 + 2500 1000 + 2500
500 k - 1 M 1500 + 4000 1600 + 4000 1700 + 4000 1800 + 4000 1300 + 4000 1400 + 4000
± (ppm output + mV)
[2]
10 - 20 250 + 5 270 + 5 290 + 5 300 + 5 250 + 5 270 + 5
220 V 100 µV
20 - 40 95 + 2 100 + 2 105 + 2 110 + 2 95 + 2 100 + 2
40 - 20 k 57 + 0.7 60 + 0.7 62 + 0.7 65 + 0.7 45 + 0.7 50 + 0.7
20 k - 50 k 90 + 1.2 95 + 1.2 97 + 1.2 100 + 1.2 75 + 1.2 80 + 1.2
50 k - 100 k 160 + 3 170 + 3 175 + 3 180 + 3 140 + 3 150 + 3
100 k - 300 k 900 + 20 1000 + 20 1050 + 20 1100 + 20 600 + 20 700 + 20
300 k - 500 k 5000 + 50 5200 + 50 5300 + 50 5400 + 50 4500 + 50 4700 + 50
500 k - 1 M 8000 + 100 9000 + 100 9500 + 100 10,000 + 100 8000 + 100 8500 + 100
[1]
15 - 50 300 + 20 320 + 20 340 + 20 360 + 20 300 + 20 320 + 20
1100 V 1 mV
1-17
5700A/5720A Series II Calibrator
Service Manual
50 - 1 k 70 + 4 75 + 4 80 + 4 85 + 4 50 + 4 55 + 4
5725A Amplifier:
1100 V 1 mV 40 - 1 k 75 + 4 80 + 4 85 + 4 90 + 4 50 + 4 55 + 4
1 k - 20 k 105 + 6 125 + 6 135 + 6 165 + 6 85 + 6 105 + 6
20 k - 30 k 230 + 11 360 + 11 440 + 11 600 + 11 160 + 11 320 + 11
750 V 30 k - 50 k 230 + 11 360 + 11 440 + 11 600 + 11 160 + 11 320 + 11
50 k - 100k 600 + 45 1300 + 45 1600 + 45 2300 + 45 380 + 45 1200 + 45
Notes:
1. Maximum output 250 V from 15-50 Hz.
2. See Volt-Hertz capability in Figure A.
1-18
Introduction and Specifications
Electrical Specifications 1
5720A Series II AC Voltage Specifications: 95 % Confidence Level
Absolute Uncertainty Relative Uncertainty
± 5 °C from calibration temperature ± 1 °C
Frequency
Range Resolution
(Hz)
24 Hours 90 Days 180 Days 1 Year 24 Hours 90 Days
± (ppm output + μV)
2.2 mV 1 nV 10 - 20 200 + 4 220 + 4 230 + 4 240 + 4 200 + 4 220 + 4
20 - 40 80 + 4 85 + 4 87 + 4 90 + 4 80 + 4 85 + 4
40 - 20 k 70 + 4 75 + 4 77 + 4 80 + 4 50 + 4 55 + 4
20 k - 50 k 170 + 4 180 + 4 190 + 4 200 + 4 70 + 4 80 + 4
50 k - 100 k 400 + 5 460 + 5 480 + 5 500 + 5 160 + 5 180 + 5
100 k - 300 k 300 + 10 900 + 10 1000 + 10 1050 + 10 280 + 10 320 + 10
300 k - 500 k 1100 + 20 1200 + 20 1300 + 20 1400 + 20 650 + 20 800 + 20
500 k - 1 M 2400 + 20 2500 + 20 2600 + 20 2700 + 20 2100 + 20 2400 + 20
22 mV 10 nV 10 - 20 200 + 4 220 + 4 230 + 4 240 + 4 200 + 4 220 + 4
20 - 40 80 + 4 85 + 4 87 + 4 90 + 4 80 + 4 85 + 4
40 - 20 k 70 + 4 75 + 4 77 + 4 80 + 4 50 + 4 55 + 4
20 k - 50 k 170 + 4 180 + 4 190 + 4 200 + 4 70 + 4 80 + 4
50 k - 100 k 400 + 5 460 + 5 480 + 5 500 + 5 160 + 5 180 + 5
100 k - 300 k 300 + 10 900 + 10 1000 + 10 1050 + 10 280 + 10 320 + 10
300 k - 500 k 1100 + 20 1200 + 20 1300 + 20 1400 + 20 650 + 20 800 + 20
500 k - 1 M 2400 + 20 2500 + 20 2600 + 20 2700 + 20 2100 + 20 2400 + 20
220 mV 100 nV 10 - 20 200 + 12 220 + 12 230 + 12 240 + 12 200 + 12 220 + 12
20 - 40 80 + 7 85 + 7 87 + 7 90 + 7 80 + 7 85 + 7
40 - 20 k 70 + 7 75 + 7 77 + 7 80 + 7 50 + 7 55 + 7
20 k - 50 k 170 + 7 180 + 7 190 + 7 200 + 7 70 + 7 80 + 7
50 k - 100 k 400 + 17 420 + 17 440 + 17 460 + 17 160 + 17 180 + 17
100 k - 300 k 700 + 20 750 + 20 800 + 20 900 + 20 280 + 20 320 + 20
300 k - 500 k 1100 + 25 1200 +25 1300 + 25 1400 + 25 650 + 25 800 + 25
500 k - 1 M 2400 + 45 2500 + 45 2600 + 45 2700 + 45 2100 + 45 2400 + 45
2.2 V 1 mV 10 - 20 200 + 40 220 + 40 230 + 40 240 + 40 200 + 40 220 + 40
20 - 40 75 + 15 80 + 15 85 + 15 90 + 15 75 + 15 80 + 15
40 - 20 k 37 + 8 40 + 8 42 + 8 45 + 8 25 + 8 35 + 8
20 k - 50 k 65 + 10 70 + 10 73 + 10 75 + 10 55 + 10 60 + 10
50 k - 100 k 100 + 30 105 + 30 107 + 30 110 + 30 80 + 30 85 + 30
100 k - 300 k 300 + 80 340 + 80 380 + 80 420 + 80 230 + 80 250 + 80
300 k - 500 k 800 + 200 900 + 200 950 + 200 1000 + 200 700 + 200 800 + 200
500 k - 1 M 1300 + 300 1500 + 300 1600 + 300 1700 + 300 1000 + 300 1100 + 300
22 V 10 mV 10 - 20 200 + 400 220 + 400 230 + 400 240 + 400 200 + 400 220 + 400
20 - 40 75 + 150 80 + 150 85 + 150 90 + 150 75 + 150 80 + 150
40 - 20k 37 + 50 40 + 50 42 + 50 45 + 50 25 + 50 35 + 50
20k - 50k 65 + 100 70 + 100 73 + 100 75 + 100 55 + 100 60 + 100
50k - 100k 90 + 200 95 + 200 97 + 200 100 + 200 80 + 200 85 + 200
100k - 300k 250 + 600 260 + 600 270 + 600 275 + 600 250 + 600 270 + 600
300k - 500k 800 + 2000 900 + 2000 900 + 2000 1000 + 2000 700 + 2000 800 + 2000
500k - 1M 1200 + 3200 1300 + 3200 1400 + 3200 1500 + 3200 1100 + 3200 1200 + 3200
± (ppm output + mV)
[2]
220 V 100 mV 10 - 20 200 +4 220 + 4 230 + 4 240 + 4 200 + 4 220 + 4
20 - 40 75 + 1.5 80 + 1.5 85 + 1.5 90 + 1.5 75 + 1.5 80 + 1.5
40 - 20 k 45 + 0.6 47 + 0.6 50 + 0.6 52 + 0.6 35 + 0.6 40 + 0.6
20 k - 50 k 70 + 1 75 + 1 77 + 1 80 + 1 60 + 1 65 + 1
50 k - 100 k 120 + 2.5 130 + 2.5 140 + 2.5 150 + 2.5 110 + 2.5 120 + 2.5
100 k - 300 k 700 + 16 800 + 16 850 + 16 900 + 16 500 + 16 600 + 16
300 k - 500 k 4000 + 40 4200 + 40 4300 + 40 4400 + 40 3600 + 40 3800 + 40
500 k - 1 M 6000 + 80 7000 + 80 7500 + 80 8000 + 80 6500 + 80 7000 + 80
[1]
1100 V 1 mV 15 - 50 240 + 16 260 + 16 280 + 16 300 + 16 240 + 16 260 + 16
50 - 1 k 55 + 3.5 60 + 3.5 65 + 3.5 70 + 3.5 40 + 3.5 45 + 3.5
1-19
5700A/5720A Series II Calibrator
Service Manual
5725A Amplifier:
1100 V 1 mV 40 - 1 k 75 + 4 80 + 4 85 + 4 90 + 4 50 + 4 55 + 4
1 k - 20 k 105 + 6 125 + 6 135 + 6 165 + 6 85 + 6 105 + 6
20 k - 30 k 230 + 11 360 + 11 440 + 11 600 + 11 160 + 11 320 + 11
750 V 30 k - 50 k 230 + 11 360 + 11 440 + 11 600 + 11 160 + 11 320 + 11
50 k - 100 k 600 + 45 1300 + 45 1600 + 45 2300 + 45 380 + 45 1200 + 45
Notes:
1. Maximum output 250 V from 15-50 Hz.
2. See Volt-Hertz capability in Figure A.
1-20
Introduction and Specifications
Electrical Specifications 1
5700A Series II AC Voltage Specifications: 99 % Confidence Level
Absolute Uncertainty Relative Uncertainty
± 5 °C from calibration temperature ± 1 °C
Frequency
Range Resolution
(Hz) 24 Hours 90 Days 180 Days 1 Year 24 Hours 90 Days
± (ppm output + μV)
2.2 mV 1 nV 10 - 20 500 + 5 550 + 5 600 + 5 600 + 5 500 + 5 550 + 5
20 - 40 200 + 5 220 + 5 230 + 5 240 + 5 200 + 5 220 + 5
40 - 20 k 100 + 5 110 + 5 120 + 5 120 + 5 60 + 5 65 + 5
20 k - 50 k 340 + 5 370 + 5 390 + 5 410 + 5 100 + 5 110 + 5
50 k - 100 k 800 + 8 900 + 8 950 + 8 950 + 8 220 + 8 240 + 8
100 k - 300 k 1100 + 15 1200 + 15 1300 + 15 1300 + 15 400 + 15 440 + 15
300 k - 500 k 1500 + 30 1700 + 30 1700 + 30 1800 + 30 1000 + 30 1100 + 30
500 k - 1 M 4000 + 40 4400 + 40 4700 + 40 4800 + 40 400 + 30 4400 + 30
22 mV 10 nV 10 - 20 500 + 6 550 + 6 600 + 6 600 + 6 500 + 6 550 + 6
20 - 40 200 + 6 220 + 6 230 + 6 240 + 6 200 + 6 220 + 6
40 - 20 k 100 + 6 110 + 6 120 + 6 120 + 6 60 + 6 65 + 6
20 k - 50 k 340 + 6 370 + 6 390 + 6 410 + 6 100 + 6 110 + 6
50 k - 100 k 800 + 8 900 + 8 950 + 8 950 + 8 220 + 8 240 + 8
100 k - 300 k 1100 + 15 1200 + 15 1300 + 15 1300 + 15 400 + 15 440 + 15
300 k - 500 k 1500 + 30 1700 + 30 1700 + 30 1800 + 30 1000 + 30 1100 + 30
500 k - 1 M 4000 + 40 4400 + 40 4700 + 40 4800 + 40 4000 + 30 4400 + 30
220 mV 100 nV 10 - 20 500 + 16 550 + 16 600 + 16 600 + 16 500 + 16 550 + 16
20 - 40 200 + 10 220 + 10 230 + 10 240 + 10 200 + 10 220 + 10
40 - 20 k 95 + 10 100 + 10 110 + 10 110 + 10 60 + 10 65 + 10
20 k - 50 k 300 + 10 330 + 10 350 + 10 360 + 10 100 + 10 110 + 10
50 k - 100 k 750 + 30 800 + 30 850 + 30 900 + 30 220 + 30 240 + 30
100 k - 300 k 940 + 30 1000 + 30 1100 + 30 1100 + 30 400 + 30 440 + 30
300 k - 500 k 1500 + 40 1700 + 40 1700 + 40 1800 + 40 1000 + 40 1100 + 40
500 k - 1 M 3000 + 100 3300 + 100 3500 + 100 3600 + 100 3000 + 100 3300 + 100
2.2 V 1 mV 10 - 20 500 + 100 550 + 100 600 + 100 600 + 100 500 + 100 550 + 100
20 - 40 150 + 30 170 + 30 170 + 30 180 + 30 150 + 30 170 + 30
40 - 20 k 70 + 7 75 + 7 80 + 7 85 + 7 40 + 7 45 + 7
20 k - 50 k 120 + 20 130 + 20 140 + 20 140 + 20 100 + 20 110 + 20
50 k - 100 k 230 + 80 250 + 80 270 + 80 280 + 80 200 + 80 220 + 80
100 k - 300 k 400 + 150 440 + 150 470 + 150 480 + 150 400 + 150 440 + 150
300 k - 500 k 1000 + 400 1100 + 400 1200 + 400 1200 + 400 1000 + 400 1100 + 400
500 k - 1 M 2000 + 1000 2200 + 1000 2300 + 1000 2400 + 1000 2000 + 1000 2200 + 1000
22 V 10 mV 10 - 20 500 + 1000 550 + 1000 600 + 1000 600 + 1000 500 + 1000 550 + 1000
20 - 40 150 + 300 170 + 300 170 + 300 180 + 300 150 + 300 170 + 300
40 - 20 k 70 + 70 75 + 70 80 + 70 85 + 70 40 + 70 45 + 70
20 k - 50 k 120 + 200 130 + 200 140 + 200 140 + 200 100 + 200 110 + 200
50 k - 100 k 230 + 400 250 + 400 270 + 400 280 + 400 200 + 400 220 + 400
100 k - 300 k 500 + 1700 550 + 1700 550 + 1700 600 + 1700 500 + 1700 550 + 1700
300 k - 500 k 1200 + 5000 1300 + 5000 1300 + 5000 1400 + 5000 1200 + 5000 1300 + 5000
500 k - 1 M 2600 + 9000 2800 + 9000 2900 + 9000 3000 + 9000 2600 + 9000 2800 + 9000
± (ppm output + mV)
[2]
10 - 20 500 + 10 550 + 10 600 + 10 600 + 10 500 + 10 550 + 10
220 V 100 mV
20 - 40 150 + 3 170 + 3 170 + 3 180 + 3 150 + 3 170 + 3
40 - 20 k 75 + 1 80 + 1 85 + 1 90 + 1 45 + 1 50 + 1
20 k - 50 k 200 + 4 220 + 4 240 + 4 250 + 4 100 + 1 110 + 1
50 k - 100 k 500 + 10 550 + 10 600 + 10 600 + 10 300 + 10 330 + 10
100 k - 300 k 1500 + 110 1500 + 110 1600 + 110 1600 + 110 1500 + 110 1500 + 100
300 k - 500 k 5000 + 110 5200 + 110 5300 + 110 5400 + 110 5000 + 110 5200 + 110
500 k - 1 M 12,000 + 220 12,500 + 220 12,500 + 220 13,000 + 220 12,000 + 220 12,000 + 220
[1]
15 - 50 400 + 20 420 + 20 440 + 20 460 + 20 400 + 20 420 + 20
1100 V 1 mV
50 - 1 k 75 + 4 80 + 4 85 + 4 90 + 4 50 + 4 55 + 4
1-21
5700A/5720A Series II Calibrator
Service Manual
5725A Amplifier:
1100 V 1 mV 40 - 1 k 75 + 4 80 + 4 85 + 4 90 + 4 50 + 4 55 + 4
1 k - 20 k 105 + 6 125 + 6 135 + 6 165 + 6 85 + 6 105 + 6
20 k - 30 k 230 + 11 360 + 11 440 + 11 600 + 11 160 + 11 320 + 11
750 V 30 k - 50 k 230 + 11 360 + 11 440 + 11 600 + 11 160 + 11 320 + 11
50 k - 100 k 600 + 45 1300 + 45 1600 + 45 2300 + 45 380 + 45 1200 + 45
Notes:
1. Maximum output 250 V from 15-50 Hz.
2. See Volt-Hertz capability in Figure A.
1-22
Introduction and Specifications
Electrical Specifications 1
5700A Series II AC Voltage Specifications: 95 % Confidence Level
Absolute Uncertainty Relative Uncertainty
± 5 °C from calibration temperature ± 1 °C
Frequency
Range Resolution
(Hz) 24 Hours 90 Days 180 Days 1 Year 24 Hours 90 Days
± (ppm output + μV)
2.2 mV 1 nV 10 - 20 400 + 4.5 500 + 4.5 530 + 4.5 550 + 4.5 400 + 4.5 500 + 4.5
20 - 40 170 + 4.5 190 + 4.5 200 + 4.5 210 + 4.5 170 + 4.5 190 + 4.5
40 - 20 k 85 + 4.5 95 + 4.5 100 + 4.5 105 + 4.5 55 + 4.5 60 + 4.5
20 k - 50 k 300 + 4.5 330 + 4.5 350 + 4.5 370 + 4.5 90 + 4.5 100 + 4.5
50 k - 100 k 700 + 7 750 + 7 800 + 7 850 + 7 210 + 7 230 + 7
100 k - 300 k 900 + 13 1000 + 13 1050 + 13 1100 + 13 380 + 13 420 + 13
300 k - 500 k 1300 + 25 1500 + 25 1600 + 25 1700 + 25 900 + 25 1000 + 25
500 k - 1 M 2800 + 25 3100 + 25 3300 + 25 3400 + 25 2900 + 25 3200 + 25
22 mV 10 nV 10 - 20 400 + 5 500 + 5 530 + 5 550 + 5 400 + 5 500 + 5
20 - 40 170 + 5 190 + 5 200 + 5 210 + 5 170 + 5 190 + 5
40 - 20 k 85 + 5 95 + 5 100 + 5 105 + 5 55 + 5 60 + 5
20 k - 50 k 300 + 5 330 + 5 350 + 5 370 + 5 90 + 5 100 + 5
50 k - 100 k 700 + 7 750 + 7 800 + 7 850 + 7 210 + 7 230 + 7
100 k - 300 k 900 + 12 1000 + 12 1050 + 12 1100 + 12 380 + 12 420 + 12
300 k - 500 k 1300 + 25 1500 + 25 1600 + 25 1700 + 25 900 + 25 1000 + 25
500 k - 1 M 2800 + 25 3100 + 25 3300 + 25 3400 + 25 2900 + 25 3200 + 25
220 mV 100 nV 10 - 20 400 + 13 500 + 13 530 + 13 550 + 13 400 + 13 500 + 13
20 - 40 170 + 8 190 + 8 200 + 8 210 + 8 170 + 8 190 + 8
40 - 20 k 85 + 8 95 + 8 100 + 8 105 + 8 55 + 8 60 + 8
20 k - 50 k 250 + 8 280 + 8 300 + 8 320 + 8 90 + 8 100 + 8
50 k - 100 k 700 + 25 750 + 25 800 + 25 850 + 25 210 + 25 230 + 25
100 k - 300 k 900 + 25 1000 + 25 1050 + 25 1100 + 25 380 + 25 420 + 25
300 k - 500 k 1300 + 35 1500 + 35 1600 + 35 1700 + 35 900 + 35 1000 + 35
500 k - 1 M 2800 + 80 3100 + 80 3300 + 80 3400 + 80 2900 + 80 3200 + 80
2.2 V 1 mV 10 - 20 400 + 80 450 + 80 480 + 80 500 + 80 400 + 80 450 + 80
20 - 40 130 + 25 140 + 25 150 + 25 160 + 25 130 + 25 140 + 25
40 - 20 k 60 + 6 65 + 6 70 + 6 75 + 6 35 + 6 40 + 6
20 k - 50 k 105 + 16 110 + 16 115 + 16 120 + 16 85 + 16 95 + 16
50 k - 100 k 190 + 70 210 + 70 230 + 70 250 + 70 170 + 70 190 + 70
100 k - 300 k 350 + 130 390 + 130 420 + 130 430 + 130 340 + 130 380 + 130
300 k - 500 k 850 + 350 950 + 350 1000 + 350 1050 + 350 850 + 350 950 + 350
500 k - 1 M 1700 + 850 1900 + 850 2100 + 850 2200 + 850 1700 + 850 1900 + 850
22 V 10 mV 10 - 20 400 + 800 450 + 800 480 + 800 500 + 800 400 + 800 450 + 800
20 - 40 130 + 250 140 + 250 150 + 250 160 + 250 130 + 250 140 + 250
40 - 20 k 60 + 60 65 + 60 70 + 60 75 + 60 35 + 60 40 + 60
20 k - 50 k 105 + 160 110 + 160 115 + 160 120 + 160 85 + 160 95 + 160
50 k - 100 k 190 + 350 210 + 350 230 + 350 250 + 350 170 + 350 190 + 350
100 k - 300 k 400 + 1500 450 + 1500 470 + 1500 500 + 1500 400 + 1500 450 + 1500
300 k - 500 k 1050 + 4300 1150 + 4300 1200 + 4300 1250 + 4300 1000 + 4300 1100 + 4300
500 k - 1 M 2300 + 8500 2500 + 8500 2600 + 8500 2700 + 8500 2200 + 8500 2400 + 8500
± (ppm output + mV)
[2]
10 - 20 400 + 8 450 + 8 480 + 8 500 + 8 400 + 8 450 + 8
220 V 100 mV
20 - 40 130 + 2.5 140 + 2.5 150 + 2.5 160 + 2.5 130 + 2.5 140 + 2.5
40 - 20 k 65 + 0.8 70 + 0.8 75 + 0.8 80 + 0.8 40 + 0.8 45 + 0.8
20 k - 50 k 170 + 3.5 190 + 3.5 210 + 3.5 220 + 3.5 85 + 3.5 95 + 3.5
50 k - 100 k 400 + 8 450 + 8 480 + 8 500 + 8 270 + 8 300 + 8
100 k - 300 k 1300 + 90 1400 + 90 1450 + 90 1500 + 90 1200 + 90 1300 + 90
300 k - 500 k 4300 + 90 4500 + 90 4600 + 90 4700 + 90 4200 + 90 4500 + 90
500 k - 1 M 10,500 + 190 11,000 + 190 11,300 + 190 11,500 + 190 10,500 + 190 11,000 + 190
[1]
15 - 50 340 + 16 360 + 16 380 + 16 400 + 16 340 + 16 360 + 16
1100 V 1 mV
50 - 1 k 65 + 3.5 70 + 3.5 75 + 3.5 80 + 3.5 45 + 3.5 50 + 3.5
1-23
5700A/5720A Series II Calibrator
Service Manual
5725A Amplifier:
1100 V 1 mV 40 - 1 k 75 + 4 80 + 4 85 + 4 90 + 4 50 + 4 55 + 4
1 k - 20 k 105 + 6 125 + 6 135 + 6 165 + 6 85 + 6 105 + 6
20 k - 30 k 230 + 11 360 + 11 440 + 11 600 + 11 160 + 11 320 + 11
750 V 30 k - 50 k 230 + 11 360 + 11 440 + 11 600 + 11 160 + 11 320 + 11
50 k - 100 k 600 + 45 1300 + 45 1600 + 45 2300 + 45 380 + 45 1200 + 45
Notes:
1. Maximum output 250 V from 15-50 Hz.
2. See Volt-Hertz capability in Figure A.
1-24
Introduction and Specifications
Electrical Specifications 1
AC Voltage Secondary Performance Specifications and Operating Characteristics
Temperature Coefficient Maximum
Stability
Distortion
[1]
0 - 10 °C
± 1 °C
Frequency Output Impedance
Bandwidth
Range 10 - 40 °C and
24 Hours
(Hz) (Ω)
10 Hz-10 MHz
40 - 50 °C
± μV ±μV / °C ± (% output + μV)
2.2 mV 10 - 20 5 0.05 0.05 50 0.05 + 10
20 - 40 5 0.05 0.05 0.035 + 10
40 - 20 k 2 0.05 0.05 0.035 + 10
20 k - 50 k 2 0.1 0.1 0.035 + 10
50 k - 100 k 3 0.2 0.2 0.035 + 30
100 k - 300 k 3 0.3 0.3 0.3 + 30
300 k - 500 k 5 0.4 0.4 0.3 + 30
500 k - 1 M 5 0.5 0.5 2 + 50
22 mV 10 - 20 5 0.2 0.3 50 0.05 + 11
20 - 40 5 0.2 0.3 0.035 + 11
40 - 20 k 2 0.2 0.3 0.035 + 11
20 k - 50 k 2 0.4 0.5 0.035 + 11
50 k - 100 k 3 0.5 0.5 0.035 + 30
100 k - 300 k 5 0.6 0.6 0.3 + 30
300 k - 500 k 10 1 1 0.3 + 30
500 k - 1 M 15 1 1 2 + 30
± (ppm output ± (ppm output μV) / °C
+ μV)
220 mV 10 - 20 150 + 20 2 + 1 2 + 1 50 0.05 + 16
20 - 40 80 + 15 2 + 1 2 + 1 0.035 + 16
40 - 20 k 12 + 2 2 + 1 2 + 1 0.035 + 16
20 k - 50 k 10 + 2 15 + 2 15 + 2 0.035 + 16
50 k - 100 k 10 + 2 15 + 4 15 + 4 0.035 + 30
100 k - 300 k 20 + 4 80 + 5 80 + 5 0.3 + 30
300 k - 500 k 100 + 10 80 + 5 80 + 5 0.3 + 30
500 k - 1 M 200 + 20 80 + 5 80 + 5 1 + 30
Load Regulation
±(ppm output+ μV)
2.2 V 10 - 20 150 + 20 50 + 10 50 + 10 10 + 2 0.05 + 80
20 - 40 80 + 15 15 + 5 15 + 5 10 + 2 0.035 + 80
40 - 20 k 12 + 4 2 + 1 5 + 2 10 + 4 0.035 + 80
20 k - 50 k 15 + 5 10 + 2 15 + 4 30 + 10 0.035 + 80
50 k - 100 k 15 + 5 10 + 4 20 + 4 120 + 16 0.035 + 110
100 k - 300 k 30 + 10 80 + 15 80 + 15 300 ppm 0.3 + 110
300 k - 500 k 70 + 20 80 + 40 80 + 40 600 ppm 0.5 + 110
500 k - 1 M 150 + 50 80 + 100 80 + 100 1200 ppm 1 + 110
22 V 10 - 20 150 + 20 50 + 100 50 + 100 10 + 20 0.05 + 700
20 - 40 80 + 15 15 + 30 15 + 40 10 + 20 0.035 + 700
40 - 20 k 12 + 8 2 + 10 4 + 15 10 + 30 0.035 + 700
20 k - 50 k 15 + 10 10 + 20 20 + 20 30 + 50 0.035 + 700
50 k - 100 k 15 + 10 10 + 40 20 + 40 80 + 80 0.05 + 800
100 k - 300 k 30 + 15 80 + 150 80 + 150 100 + 700 0.3 + 800
300 k - 500 k 70 + 100 80 + 300 80 + 300 200 + 1100 0.3 + 800
500 k - 1 M 150 + 100 80 + 500 80 + 500 600 + 3000 2 + 800
220 V 10 - 20 150 + 200 50 + 1000 50 + 1000 10 + 200 0.05 + 10,000
20 - 40 80 + 150 15 + 300 15 + 300 10 + 200 0.05 + 10,000
40 - 20 k 12 + 80 2 + 80 4 + 80 10 + 300 0.05 + 10,000
20 k - 50 k 15 + 100 10 + 100 20 + 100 30 + .600 0.05 + 10,000
50 k - 100 k 15 + 100 10 + 500 20 + 500 80 + 3,000 0.2 + 50,000
100 k - 300 k 30 + 400 80 + 600 80 + 600 250 + 25,000 1.5 + 50,000
300 k - 500 k 100 + 10,000 80 + 800 80 + 800 500 + 50,000 1.5 + 50,000
500 k - 1 M 200 + 20,000 80 + 1000 80 + 1000 1000 + 110,000 3.5 + 100,000
±(ppm output + ±(ppm output) / °C ±(ppm output + ±(% output)
mV) mV)
1100 V 15 - 50 150 + 0.5 50 50 10 + 2 0.15
50 - 1 k 20 + 0.5 2 5 10 + 1 0.07
1-25
5700A/5720A Series II Calibrator
Service Manual
5725A Amplifier:
Temperature Coefficient Distortion
Stability
Adder
Bandwidth
[2]
[1]
Load Regulation
Range ± 1 °C
Frequency
10 Hz -10 MHz
0 - 10 °C and
(Hz)
10 - 40 °C
24 Hours
40 - 50 °C
±(% output)
±(ppm output + mV) ±(ppm output) / °C ±(ppm output + mV) 150 pF 1000 pF
1100 V 40 - 1 k 10 + .5 5 5 10 + 1 0.10 0.10
1 k - 20 k 15 + 2 5 5 90 + 6 0.10 0.15
20 k - 50 k 40 + 2 10 10 275 + 11 0.30 0.30
50 k - 100 k 130 + 2 30 30 500 + 30 0.40 0.40
Notes:
1. Stability specifications are included in Absolute Uncertainty values for the primary specifications.
2. The 5725A will drive up to 1000 pF of load capacitance. Uncertainty specifications include loads to 300 pF and 150 pF as
shown under "Load Limits." For capacitances up to the maximum of 1000 pF, add "Load Regulation."
Voltage Range Maximum Current Limits Load Limits
[2]
2.2 V
50 mA, 0 °C-40 °C >50 Ω,
22 V
20 mA, 40 °C-50 °C
220 V 1000 pF
1100 V 6 mA 600 pF
5725A Amplifier:
[1]
40 Hz-5 kHz 50 mA 1000 pF
1100 V 5 kHz-30 kHz 70 mA 300 pF
[3]
30 kHz-100 kHz 70 mA 150 pF
Notes:
1. The 5725A will drive up to 1000 pF of load capacitance. Uncertainty specifications include loads to 300 pF and 150 pF as
shown under "Load Limits." For capacitances up to the maximum of 1000 pF, add "Load Regulation."
2. 2.2 V Range, 100 kHz-1.2 MHz only: uncertainty specifications cover loads to 10 mA or 1000 pF. For higher loads, load
regulation is added.
3. Applies from 0 °C to 40 °C.
Output Display Formats ....................................... Voltage or dBm, dBm reference 600 Ω.
Minimum Output ................................................... 10 % on each range
External Sense ...................................................... Selectable for 2.2 V, 22 V, 220 V, and 1100 V ranges; 5700A/5720A
<100 kHz, 5725A <30 kHz
Settling Time to Full Accuracy
Frequency (Hz) Settling Time (seconds)
<20 7
120-120 k 5
>120 k 2
Notes:
Plus 1 second for amplitude or frequency range change
Plus 2 seconds for 5700A/5720A 1100 V range
Plus 4 seconds for 5725A 1100 V range
1-26
Introduction and Specifications
Electrical Specifications 1
Overshoot .............................................................. <10 %
Common Mode Rejection ....................................... 140 dB, DC to 400 Hz
Frequency
Ranges (Hz)........................................................ 10.000 - 119.99
0.1200 k - 1.1999 k
1.200 k - 11.999 k
12.00 k - 119.99 k
120.0 k - 1.1999 M
Uncertainty.......................................................... ±0.01 %
Resolution........................................................... 11.999 counts
Phase Lock (Selectable Rear Panel BNC Input)
Phase Uncertainty (except 1100 V range).......... >30 Hz: ±1 ° + 0.05 °/kHz), <30 Hz: ±3 °
Input Voltage....................................................... 1 V to 10 V rms sine wave (do not exceed 1 V for mV ranges)
Frequency Range ............................................... 10 Hz to 1.1999 MHz
Lock Range......................................................... ±2 % of frequency
Lock-In Time ....................................................... Larger of 10/frequency or 10 msec
Phase Reference (Selectable Rear Panel BNC Output)
Range ................................................................. ±180 °
Phase Uncertainty (except 1100 V range).......... ±1 ° at quadrature points (0 °, ±90 °, ±180 °) elsewhere ±2 °
Stability ............................................................... ±0.1 °
Resolution........................................................... 1 °
Output Level........................................................ 2.5 V rms ±0.2 V
Frequency Range ............................................... 50 kHz to 1 kHz, usable 10 Hz to 1.1999 MHz
10000
5700A/5720A
40 Hz 30 Hz
5725A
1000
7
2.2 x 10 V-Hz
15 Hz
100
Volt-Hertz Capability
10
5700A-03
3.5 V
0
10 Hz 50 Hz 1 kHz 100 kHz 1 MHz 30 MHz
Frequency
Figure A.
1-27
Voltage
5700A/5720A Series II Calibrator
Service Manual
1-31. Resistance Specifications
5720A Series II Resistance Specifications
Absolute Uncertainty of Characterized Value Relative Uncertainty
[1]
± 5 °C from calibration temperature ± 1 °C
Nominal Value
24 Hours 90 Days 180 Days 1 Year 24 Hours 90 Days
(Ω)
±ppm
99 % Confidence Level
0 50 μΩ 50 μΩ 50 μΩ 50 μΩ 50 μΩ 50 μΩ
1
85 95 100 110 32 40
1.9
85 95 100 110 25 33
10
23 25 26 27 5 8
19 23 25 26 27 4 7
100 10 11 11.5 12 2 4
190
10 11 11.5 12 2 4
1 k
8 9 9.5 10 2 3
1.9 k
8 9 9.5 10 2 3
10 k 8 9 9.5 10 2 3
19 k
9 9 9.5 10 2 3
100 k
9 11 12 13 2 3
190 k
9 11 12 13 2 3
1 M 16 18 20 23 2.5 5
1.9 M 17 19 21 24 3 6
10 M
33 37 40 46 10 14
19 M
43 47 50 55 20 24
100 M
100 110 115 120 50 60
95 % Confidence Level
0
40 μΩ 40 μΩ 40 μΩ 40 μΩ 40 μΩ 40 μΩ
1 70 80 85 95 27 35
1.9
70 80 85 95 20 26
10
20 21 22 23 4 7
19
20 21 22 23 3.5 6
100 8 9 9.5 10 1.6 3.5
190 8 9 9.5 10 1.6 3.5
1 k
6.5 7.5 8 8.5 1.6 2.5
1.9 k
6.5 7.5 8 8.5 1.6 2.5
10 k
6.5 7.5 8 8.5 1.6 2.5
19 k 7.5 7.5 8 8.5 1.6 2.5
100 k
7.5 9 10 11 1.6 2.5
190 k
7.5 9 10 11 1.6 2.5
1 M
13 15 17 20 2 4
1.9 M 14 16 18 21 2.5 4
10 M 27 31 34 40 8 12
19 M
35 39 42 47 16 20
100 M
85 95 100 100 40 50
Note:
1. Specifications apply to displayed value. 4-wire connections, except 100 MΩ.
1-28
Introduction and Specifications
Electrical Specifications 1
5700A Series II Resistance Specifications
Absolute Uncertainty of Characterized Value Relative Uncertainty
[1]
± 5 °C from calibration temperature ± 1 °C
Nominal Value
24 Hours 90 Days 180 Days 1 Year 24 Hours 90 Days
(Ω)
±ppm
99 % Confidence Level
0
50 μΩ 50 μΩ 50 μΩ 50 μΩ 50 μΩ 50 μΩ
1
85 95 100 110 32 40
1.9
85 95 100 110 25 33
10 26 28 30 33 5 8
19
24 26 28 31 4 7
100
15 17 18 20 2 4
190
15 17 18 20 2 4
1 k 11 12 13 15 2 3.5
1.9 k 11 12 13 15 2 3.5
10 k
9 11 12 14 2 3.5
19 k
9 11 12 14 2 3.5
100 k
11 13 14 16 2 3.5
190 k 11 13 14 16 2 3.5
1 M
16 18 20 23 2.5 5
1.9 M
17 19 21 24 3.5 6
10 M
33 37 40 46 10 14
19 M 43 47 50 55 20 24
100 M 110 120 125 130 50 60
95 % Confidence Level
0 50 μΩ 50 μΩ 50 μΩ 50 μΩ 50 μΩ 50 μΩ
1
70 80 85 95 32 40
1.9
70 80 85 95 25 33
10
21 23 27 28 5 8
19 20 22 24 27 4 7
100
13 14 15 17 2 4
190
13 14 15 17 2 4
1 k
9 10 11 13 2 3.5
1.9 k 9 10 11 13 2 3.5
10 k 7.5 9.5 10.5 12 2 3.5
19 k
7.5 9.5 10.5 12 2 3.5
100 k
9 11 12 14 2 3.5
190 k
9 11 12 14 2 3.5
1 M 13 15 17 20 2.5 5
1.9 M
14 16 18 21 3 6
10 M
27 31 34 40 10 14
19 M
35 39 42 47 20 24
100 M 90 100 105 110 50 60
Note:
1. Specifications apply to displayed value. 4-wire connections, except 100 MΩ.
1-29
5700A/5720A Series II Calibrator
Service Manual
Resistance Secondary Performance Specifications and Operating Characteristics
Maximum
Two-Wire Adder
Temperature Coefficient Difference
[2] Active
Maximum
Adder of
Stability [4]
Full Spec Load
Compensation
Peak
Nominal [1]
[3] Characterized
± 1 °C
Range
Current
Value
to Nominal
0 - 10 °C
24 Hours I - I
L U
Lead Resistance
I
(Ω) MAX
and
10 - 40 °C Value
(mA)
(mA)
40 - 50 °C
0.1 Ω 1 Ω
±ppm
±ppm ±ppm/°C ±mΩ
0 8 - 500 500
⎯ ⎯ ⎯ ⎯ 4 μV 4 μV
2 + 4 +
I I
m m
1 32 4 5 8 - 100 700 500
4 μV 4 μV
2 + 4 +
I I
m m
1.9 25 6 7 8 - 100 500 500
4 μV 4 μV
2 + 4 +
I I
m m
10 5 2 3 8 - 11 220 300
4 μV 4 μV
2 + 4 +
I I
m m
19 4 2 3 8 - 11 160 300
4 μV 4 μV
2 + 4 +
I I
m m
100 2 2 3 8 - 11 70 150
4 μV 4 μV
2 + 4 +
I I
m m
190 2 2 3 8 - 11 50 150
4 μV 4 μV
2 + 4 +
I I
m m
1 k 2 2 3 1 - 2 22 150 10 15
1.9 k 2 2 3 1 - 1.5 16 150 10 15
10 k 2 2 3 7 150 50 60
100 - 500 μA
19 k 2 2 3 5 150 100 120
50 - 250 μA
100 k 2 2 3 1 150 I = Current produced
10 - 100 μA m
by Ohmmeter (A)
190 k 2 2 3 150
5 - 50 μA 500 μA
1 M 2.5 2.5 6 200
5 - 20 μA 100 μA
1.9 M 3.5 3 10 200
2.5 - 10 μA 50 μA
10 M 10 5 20 300
0.5 - 2 μA 10 μA
19 M 20 8 40 0.25 - 1 μA 5 μA 300
100 M 50 12 100 50 - 200 nA 1 μA 500
Notes:
1. Stability specifications are included in the Absolute Uncertainty values in the primary specification tables.
2. Temperature coefficient is an adder to uncertainty specifications that does not apply unless operated more than 5 °C from calibration
temperature, or calibrated outside the range 19 °C to 24 °C. Two examples:
- Calibrate at 20 °C: Temperature coefficient adder is not required unless operated below 15 °C or above 25 °C.
- Calibrate at 26 °C: Add 2 °C temperature coefficient adder. Additional temperature coefficient adder is not required unless operated
below 21 °C or above 31 °C.
3. Refer to current derating factors table for loads outside of this range.
4. Active two-wire compensation may be selected for values less than 100 kΩ, with either the front panel or the meter input terminals as
reference plane. Active compensation is limited to 11 mA load, and to 2 V burden. Two-wire compensation can be used only with Ω-
meters that source continuous (not pulsed) dc current.
1-30
Introduction and Specifications
Electrical Specifications 1
Current Derating Factors
Value of Derating Factor K for Over or Under Current
Nominal Value
Two-Wire Comp Four-Wire Four-Wire
(Ω)
[1] [1] [2]
I < I I < I I < I < I
L L U MAX
SHORT 4.4 0.3 ⎯
-5
1 4.4 300 4 x10
-4
1.9 4.4 160 1.5 x 10
-3
10 4.4 30 1.6 x 10
-3
19 4.4 16 3 x 10
-2
100 4.4 3.5 1 x 10
-2
190 4.4 2.5 1.9 x 10
1 k 4.4 0.4 0.1
1.9 k 4.4 0.4 0.19
10 k 5000 50 2.0
19 k 5000 50 3.8
-5
100 k ⎯ 7.5 2 x 10
-5
190 k ⎯ 4.0 3.8 x 10
-4
1 M ⎯ 1.0 1.5 x 10
-4
1.9 M ⎯ 0.53 2.9 x 10
-3
10 M ⎯ 0.2 1 x 10
-3
19 M ⎯ 0.53 1.9 x 10
100 M 0.1 ⎯
Notes:
1. For I < I , errors occur due to thermally generated voltages within the 5720A. Use the following equation to determine the error,
L
and add this error to the corresponding uncertainty or stability specification.
Error = K(I - I)/( I x I)
L L
Where: Error is in mΩ for all two-wire comp values and four-wire short, and in ppm for the remaining four-wire values.
K is the constant from the above table;
I and I are expressed in mA for short to 1.9 kΩ;
L
I and I are expressed inμA for 10 kΩ to 100 MΩ
L
2. For I < I < I errors occur due to self-heating of the resistors in the calibrator. Use the following equation to determine the
U MAX
error in ppm and add this error to the corresponding uncertainty or stability specification.
2 2
Error in ppm = K(I -I )
U
Where: K is the constant from the above table;
I and I are expressed in mA for short to 19 kΩ;
U
I and I are expressed in μA for 100 kΩ to 100 MΩ
U
1-31
5700A/5720A Series II Calibrator
Service Manual
1-32. DC Current Specifications
5720A Series II DC Current Specifications
Absolute Uncertainty
Relative Uncertainty ± 1 °C
[2]
Resolution ± 5 °C from calibration temperature
Range
24 Hours 90 Days 180 Days 1 Year 24 Hours 90 Days
nA
± (ppm output + nA)
99 % Confidence Level
220 μA 0.1 40 + 7 42 + 7 45 + 7 50 + 7 24 + 2 26 + 2
1 30 + 8 35 + 8 37 + 8 40 + 8 24 + 5 26 + 5
2.2 mA
10 30 + 50 35 + 50 37 + 50 40 + 50 24 + 50 26 + 50
22 mA
μA ± (ppm output + μA)
[1]
220 mA 0.1 40 + 0.8 45 + 0.8 47 + 0.8 50 + 0.8 26 + 0.3 30 + 0.3
[1]
2.2 A 1 60 + 15 70 + 15 80 + 15 90 + 15 40 + 7 45 + 7
5725A Amplifier:
11 A 10 330 + 470 340 + 480 350 + 480 360 + 480 100 + 130 110 + 130
95 % Confidence Level
nA ± (ppm output + nA)
0.1 32 + 6 35 + 6 37 + 6 40 + 6 20 + 1.6 22 + 1.6
220 μA
1 25 + 7 30 + 7 33 + 7 35 + 7 20 + 4 22 + 4
2.2 mA
22 mA 10 25 + 40 30 + 40 33 + 40 35 + 40 20 + 40 22 + 40
μA ± (ppm output + μA)
[1]
220 mA 0.1 35 + 0.7 40 + 0.7 42 + 0.7 45 + 0.7 22 + 0.25 25 + 0.25
[1]
2.2 A 1 50 + 12 60 + 12 70 + 12 80 + 12 32 + 6 40 + 6
5725A Amplifier:
11 A 10 330 + 470 340 + 480 350 + 480 360 + 480 100 + 130 110 + 130
Note:
Maximum output from the calibrator’s terminals is 2.2 A. Uncertainty specifications for 220 mA and 2.2 mA ranges are increased
by a factor of 1.3 when supplied through 5725A terminals.
Specifications are otherwise identical for all output locations.
1. Add to uncertainty specifications:
2
±200 x I ppm for >100 mA on 220 mA range
2
±10 x I ppm for >1 A on 2.2 A range
2. For fields strengths >0.4 V/m but ≤3 V/m, add 1 % of range.
1-32
Introduction and Specifications
Electrical Specifications 1
5700A Series II DC Current Specifications
Absolute Uncertainty
[2] Relative Uncertainty ± 1 °C
± 5 °C from calibration temperature
Resolution
Range
24 Hours 90 Days 180 Days 1 Year 24 Hours 90 Days
nA ± (ppm output + nA)
99 % Confidence Level
0.1 45 + 10 50 + 10 55 + 10 60 + 10 24 + 2 26 + 2
220 μA
2.2 mA 1 45 + 10 50 + 10 55 + 10 60 + 10 24 + 5 26 + 5
10 45 + 100 50 + 100 55 + 100 60 + 100 24 + 50 26 + 50
22 mA
μA ± (ppm output + μA)
[1]
220 mA 0.1 55 + 1 60 + 1 65 + 1 70 + 1 26 + 0.3 30 + 0.3
[1]
2.2 A 1 75 + 30 80 + 30 90 + 30 95 + 30 40 + 7 45 + 7
5725A Amplifier:
11 A 10 330 + 470 340 + 480 350 + 480 360 + 480 100 + 130 110 + 130
95 % Confidence Level
nA
± (ppm output + nA)
0.1 35 + 8 40 + 8 45 + 8 50 + 8 20 + 1.6 22 + 1.6
220 μA
1 35 + 8 40 + 8 45 + 8 50 + 8 20 + 4 22 + 4
2.2 mA
10 35 + 80 40 + 80 45 + 80 50 + 80 20 + 40 22 + 40
22 mA
μA ± (ppm output + μA)
[1]
220 mA 0.1 45 + 0.8 50 + 0.8 55 + 0.8 60 + 0.8 22 + 0.25 25 + 0.25
[1]
2.2 A 1 60 + 25 65 + 25 75 + 25 80 + 25 35 + 6 40 + 6
5725A Amplifier:
11 A 10 330 + 470 340 + 480 350 + 480 360 + 480 100 + 130 110 + 130
Note:
Maximum output from the calibrator’s terminals is 2.2 A. Uncertainty specifications for 220 mA and 2.2 mA ranges are increased
by a factor of 1.3 when supplied through 5725A terminals.
Specifications are otherwise identical for all output locations.
1. Add to uncertainty specifications:
2
±200 x I ppm for >100 mA on 220 mA range
2
±10 x I ppm for >1 A on 2.2 A range
2. For fields strengths >0.4 V/m but ≤3 V/m, add 1 % of range.
1-33
5700A/5720A Series II Calibrator
Service Manual
DC Current Secondary Performance Specifications and Operating Characteristics
Temperature Noise
[2]
Coefficient
Stability
Bandwidth Bandwidth
[1] Burden Maximum
± 1 °C 0 - 10 °C
0.1-10 Hz
Voltage Load for Full
Compliance 10 Hz-10
24 Hours 10 - 40 °C and [3] [4]
Range
Adder Accuracy
Limits kHz
40 - 50 °C
(±nA/V) (Ω)
pk-pk RMS
± (ppm output + ppm output
± (ppm output + nA) / °C nA
+ nA
nA)
5 + 1 1 + 0.40 3 + 1 10 0.2 20k 6 + .9 10
220 μA
2.2 mA 5 + 5 1 + 2 3 + 10 10 0.2 2k 6 + 5 10
22 mA 5 + 50 1 + 20 3 + 100 10 10 200 6 + 50 50
8 + 300 1 + 200 10 100 20 9 + 300 500
220 mA 3 + 1 μA
[5]
3 2
2.2 A 9 + 7 μA 1 + 2.5 μA 3 + 10 μA 2 μA 12 + 1.5 μA 20 μA
± (ppm output ppm output
5725A ± (ppm output + μA) / °C μA
+ μA) + μA
11 A 25 + 100 20 + 75 30 + 120 4 0 4 15 + 70 175
Notes:
Maximum output from the calibrator’s terminals is 2.2 A. Uncertainty specifications for 220 mA and 2.2 mA ranges are increased by a factor of
1.3 when supplied through 5725A terminals.
1. Stability specifications are included in the Absolute Uncertainty values for the primary specifications.
2. Temperature coefficient is an adder to uncertainty specifications. It does not apply unless operating more than ±5 °C from calibration
temperature.
3. Burden voltage adder is an adder to uncertainty specifications that does not apply unless burden voltage is greater than 0.5 V.
0.1 x actual load
4. For higher loads, multiply uncertainty specification by: 1+
maximum load for full accuracy
5. The calibrator’s compliance limit is 2 V for outputs from 1 A to 2.2 A. 5725A Amplifier may be used in range-lock mode down to 0 A.
Minimum Output: ................................................. 0 for all ranges, including 5725A.
Settling Time: ....................................................... 1 second for mA and mA ranges; 3 seconds for 2.2 A range; 6 seconds
for 11 range; + 1 second for range or polarity change
Overshoot: ............................................................<5 %
1-34
Introduction and Specifications
Electrical Specifications 1
1-33. AC Current Specifications
5720A Series II AC Current Specifications: 99 % Confidence Level
Absolute Uncertainty Relative Uncertainty
[1]
± 5 °C from calibration temperature ± 1 °C
Frequency
Range Resolution
24 Hours 90 Days 180 Days 1 Year 24 Hours 90 Days
(Hz)
± (ppm output + nA)
10 - 20 260 + 20 280 + 20 290 + 20 300 + 20 260 + 20 280 + 20
20 - 40 170 + 12 180 + 12 190 + 12 200 + 12 130 + 12 150 + 12
220 μA 1 nA 40 - 1 k 120 + 10 130 + 10 135 + 10 140 + 10 100 + 10 110 + 10
1k - 5 k 300 + 15 320 + 15 340 + 15 350 + 15 250 + 15 280 + 15
5k - 10 k 1000 + 80 1100 + 80 1200 + 80 1300 + 80 900 + 80 1000 + 80
10 - 20 260 + 50 280 + 50 290 + 50 300 + 50 260 + 50 280 + 50
20 - 40 170 + 40 180 + 40 190 + 40 200 + 40 130 + 40 150 + 40
2.2 mA 10 nA 40 - 1 k 120 + 40 130 + 40 135 + 40 140 + 40 100 + 40 110 + 40
1k - 5 k 210 + 130 220 + 130 230 + 130 240 + 130 250 + 130 280 + 130
5k - 10 k 1000 + 800 1100 + 800 1200 + 800 1300 + 800 900 + 800 1000 + 800
10 - 20 260 + 500 280 + 500 290 + 500 300 + 500 260 + 500 280 + 500
20 - 40 170 + 400 180 + 400 190 + 400 200 + 400 130 + 400 150 + 400
22 mA 100 nA 40 - 1 k 120 + 400 130 + 400 135 + 400 140 + 400 100 + 400 110 + 400
1k - 5 k 210 + 700 220 + 700 230 + 700 240 + 700 250 + 700 280 + 700
5k - 10 k 1000 + 6000 1100 + 6000 1200 + 6000 1300 + 6000 900 + 6000 1000 + 6000
± (ppm output + μA)
10 - 20 260 + 5 280 + 5 290 + 5 300 + 5 260 + 5 280 + 5
20 - 40 170 + 4 180 + 4 190 + 4 200 + 4 130 + 4 150 + 4
220 mA 40 - 1 k 120 + 3 130 + 3 135 + 3 140 + 3 100 + 3 110 + 3
1 μA
1k - 5 k 210 + 4 220 + 4 230 + 4 240 + 4 250 + 4 280 + 4
5k - 10 k 1000 + 12 1100 + 12 1200 + 12 1300 + 12 900 + 12 1000 + 12
20 - 1 k 290 + 40 300 + 40 310 + 40 320 + 40 300 + 40 350 + 40
2.2 A 10 μA 1 k - 5 k 440 + 100 460 + 100 480 + 100 500 + 100 500 + 100 520 + 100
5 k - 10 k 6000 + 200 7000 + 200 7500 + 200 8000 + 200 6000 + 200 7000 + 200
5725A Amplifier:
40 - 1 k 370 + 170 400 + 170 440 + 170 460 + 170 300 + 170 330 + 170
11 A 1 k - 5 k 800 + 380 850 + 380 900 + 380 950 + 380 700 + 380 800 + 380
100 μA
5 k - 10 k 3000 + 750 3300 + 750 3500 + 750 3600 + 750 2800 + 750 3200 + 750
Note:
Maximum output from the calibrator’s terminals is 2.2 A. Uncertainty specifications for 220 μA and 2.2 mA ranges are increased by a factor
of 1.3 plus 2 μA when supplied through 5725A terminals. For the 5720A 220 μA range, 1 kHz through 5 kHz and 5 kHz through 10 kHz,
when the output is coming from the AUX current terminal, use the 5700A Absolute Uncertainty Specifications. Specifications are
otherwise identical for all output locations.
1. For fields strengths >0.4 V/m but ≤3 V/m, add 1 % of range.
1-35
5700A/5720A Series II Calibrator
Service Manual
5720A Series II AC Current Specifications: 95% Confidence Level
Absolute Uncertainty Relative Uncertainty
[1]
± 5 °C from calibration temperature ± 1 °C
Frequency
Range Resolution
(Hz) 24 Hours 90 Days 180 Days 1 Year 24 Hours 90 Days
± (ppm output + nA)
10 - 20 210 + 16 230 + 16 240 + 16 250 + 16 210 + 16 230 + 16
20 - 40 130 + 10 140 + 10 150 + 10 160 + 10 110 + 10 130 + 10
220 μA 1 nA 40 - 1 k 100 + 8 110 + 8 115 + 8 120 + 8 80 + 8 90 + 8
1k - 5 k 240 + 12 250 + 12 270 + 12 280 + 12 200 + 12 230 + 12
5k - 10 k 800 + 65 900 + 65 1000 + 65 1100 + 65 700 + 65 800 + 65
10 - 20 210 + 40 230 + 40 240 + 40 250 + 40 210 + 40 230 + 40
20 - 40 140 + 35 140 + 35 150 + 35 160 + 35 110 + 35 130 + 35
2.2 mA 10 nA 100 + 35 110 + 35 115 + 35 120 + 35 80 + 35 90 + 35
40 - 1 k
1k - 5 k 170 + 110 180 + 110 190 + 110 200 + 110 200 + 110 230 + 110
5k - 10 k 800 + 650 900 + 650 1000 + 650 1100 + 650 700 + 650 800 + 650
10 - 20 210 + 400 230 + 400 240 + 400 250 + 400 210 + 400 230 + 400
20 - 40 130 + 350 140 + 350 150 + 350 160 + 350 110 + 350 130 + 350
22 mA 100 nA 40 - 1 k 100 + 350 110 + 350 115 + 350 120 + 350 80 + 350 90 + 350
1k - 5 k 170 + 550 180 + 550 190 + 550 200 + 550 200 + 550 230 + 550
5k - 10 k 800 + 5000 900 + 5000 1000 + 5000 1100 + 5000 700 + 5000 800 + 5000
± (ppm output + μA)
10 - 20 210 + 4 230 + 4 240 + 4 250 + 4 210 + 4 230 + 4
20 - 40 130 + 3.5 140 + 3.5 150 + 3.5 160 + 3.5 110 + 3.5 130 + 3.5
220 mA 1 μA 40 - 1 k 100 + 2.5 110 + 2.5 115 + 2.5 120 + 2.5 80 + 2.5 90 + 2.5
1k - 5 k 170 + 3.5 180 + 3.5 190 + 3.5 200 + 3.5 200 + 3.5 230 + 3.5
5k - 10 k 800 + 10 900 + 10 1000 + 10 1100 + 10 700 + 10 800 + 10
20 - 1 k 230 + 35 240 + 35 250 + 35 260 + 35 250 + 35 300 + 35
2.2 A 10 μA 1 k - 5 k 350 + 80 390 + 80 420 + 80 450 + 80 400 + 80 440 + 80
5 k - 10 k 5000 + 160 6000 + 160 6500 + 160 7000 + 160 5000 + 160 6000 + 160
5725A Amplifier:
40 - 1 k 370 + 170 400 + 170 440 + 170 460 + 170 300 + 170 330 + 170
11 A 100 μA 1 k - 5 k 800 + 380 850 + 380 900 + 380 950 + 380 700 + 380 800 + 38
5 k - 10 k 3000 + 750 3300 + 750 3500 + 750 3600 + 750 2800 + 750 3200 + 750
Note:
Maximum output from the calibrator’s terminals is 2.2 A. Uncertainty specifications for 220 μA and 2.2 mA ranges are increased by 1.3
plus 2 μA when supplied through 5725A terminals. For the 5720A 220 μA range, 1 kHz through 5 kHz and 5 kHz through 10 kHz, when
the output is coming from the AUX current terminal, use the 5700A Absolute Uncertainty Specifications. Specifications are otherwise
identical for all output locations.
1. For fields strengths >0.4 V/m but ≤3 V/m, add 1 % of range.
1-36
Introduction and Specifications
Electrical Specifications 1
5700A Series II AC Current Specifications: 99 % Confidence Level
Absolute Uncertainty Relative Uncertainty
[1]
± 5 °C from calibration temperature ± 1 °C
Frequency(
Range Resolution
Hz)
24 Hours 90 Days 180 Days 1 Year 24 Hours 90 Days
± (ppm output + nA)
10 - 20 650 + 30 700 + 30 750 + 30 800 + 30 450 + 30 500 + 30
20 - 40 350 + 25 380 + 25 410 + 25 420 + 25 270 + 25 300 + 25
220 μA 1 nA 40 - 1 k 120 + 20 140 + 20 150 + 20 160 + 20 110 + 20 120 + 20
1k - 5 k 500 + 50 600 + 50 650 + 50 700 + 50 450 + 50 500 + 50
5k - 10 k 1500 + 100 1600 + 100 1700 + 100 1800 + 100 1400 + 100 1500 + 100
10 - 20 650 + 50 700 + 50 750 + 50 800 + 50 450 + 50 500 + 50
20 - 40 350 + 40 380 + 40 410 + 40 420 + 40 270 + 40 300 + 40
2.2 mA 10 nA 120 + 40 140 + 40 150 + 40 160 + 40 110 + 40 120 + 40
40 - 1 k
1k - 5 k 500 + 500 600 + 500 650 + 500 700 + 500 450 + 500 500 + 500
5k - 10 k 1500 + 1000 1600 + 1000 1700 + 1000 1800 + 1000 1400 + 1000 1500 + 1000
10 - 20 650 + 500 700 + 500 750 + 500 800 + 500 450 + 500 500 + 500
20 - 40 350 + 400 380 + 400 410 + 400 420 + 400 270 + 400 300 + 400
40 - 1 k 120 + 400 140 + 400 150 + 400 160 + 400 110 + 400 120 + 400
22 mA 100 nA
1k - 5 k 500 + 5000 600 + 5000 650 + 5000 700 + 5000 450 + 5000 500 + 5000
5k - 10 k 1500 + 1600 + 10,000 1700 + 10,000 1800 + 10,000 1400 + 10,000 1500 +
10,000 10,000
± (ppm output + μA)
10 - 20 650 + 5 700 + 5 750 + 5 800 + 5 450 + 5 500 + 5
20 - 40 350 + 4 380 + 4 410 + 4 420 + 4 280 + 4 300 + 4
220 mA 1 μA 40 - 1 k 120 + 4 150 + 4 170 + 4 180 + 4 110 + 4 130 + 4
1k - 5 k 500 + 50 600 + 50 650 + 50 700 + 50 450 + 50 500 + 50
5k - 10 k 1500 + 100 1600 + 100 1700 + 100 1800 + 100 1400 + 100 1500 + 100
20 - 1 k 600 + 40 650 + 40 700 + 40 750 + 40 600 + 40 650 + 40
2.2 A 10 μA 1 k - 5 k 700 + 100 750 + 100 800 + 100 850 + 100 650 + 100 750 + 100
5 k - 10 k 8000 + 200 9000 + 200 9500 + 200 10,000 + 200 7500 + 200 8500 + 200
5725A Amplifier:
40 - 1 k 370 + 170 400 + 170 440 + 170 460 + 170 300 + 170 330 + 170
11 A 100 μA 1 k - 5 k 800 + 380 850 + 380 900 + 380 950 + 380 700 + 380 800 + 380
5 k - 10 k 3000 + 750 3300 + 750 3500 + 750 3600 + 750 2800 + 750 3200 + 750
Note:
Maximum output from the calibrator’s terminals is 2.2 A. Uncertainty specifications for 220 μA and 2.2 mA ranges are increased by a factor of
1.3 plus 2 μA when supplied through 5725A terminals. Specifications are otherwise identical for all output locations.
1. For field strengths >0.4 V/m but ≤3 V/m, add 1 % of range.
1-37
5700A/5720A Series II Calibrator
Service Manual
5700A Series II AC Current Specifications: 95 % Confidence Level
Absolute Uncertainty Relative Uncertainty
[1]
± 5 °C from calibration temperature ± 1 °C
Frequency
Range Resolution
(Hz) 24 Hours 90 Days 180 Days 1 Year 24 Hours 90 Days
± (ppm output + nA)
1 nA 10 - 20 550 + 25 600 + 25 650 + 25 700 + 25 375 + 25 400 + 25
220 μA
20 - 40 280 + 20 310 + 20 330 + 20 350 + 20 220 + 20 250 + 20
40 - 1 k 100 + 16 120 + 16 130 + 16 140 + 16 90 + 16 100 + 16
1k - 5 k 400 + 40 500 + 40 550 + 40 600 + 40 375 + 40 400 + 40
5k - 10 k 1300 + 80 1400 + 80 1500 + 80 1600 + 80 1200 + 80 1200 +80
2.2 mA 10 nA 10 - 20 550 + 40 600 + 40 650 + 40 700 + 40 375 + 40 400 + 40
20 - 40 280 + 35 310 + 35 330 + 35 350 + 35 220 + 35 250 + 35
40 - 1 k 100 + 35 120 + 35 130 + 35 140 + 35 090 + 35 100 + 35
1k - 5 k 400 + 400 500 + 400 550 + 400 600 + 400 375 + 400 400 + 400
5k - 10 k 1300 + 800 1400 + 800 1500 + 800 1600 + 800 1200 + 800 1200 + 800
22 mA 100 nA 10 - 20 550 + 400 600 + 400 650 + 400 700 + 400 375 + 400 400 + 400
20 - 40 280 + 350 310 + 350 330 + 350 350 + 350 220 + 350 250 + 350
40 - 1 k 100 + 350 120 + 350 130 + 350 140 + 350 090 + 350 100 + 350
1k - 5 k 400 + 4000 500 + 4000 550 + 4000 600 + 4000 375 + 4000 400 + 4000
5k - 10 k 1300 + 8000 1400 + 8000 1500 + 8000 1600 + 8000 1200 + 8000 1200 + 8000
± (ppm output + μA)
220 mA 1 μA 10 - 20 550 + 4 600 + 4 650 + 4 700 + 4 375 + 4 400 + 4
20 - 40 280 + 3.5 310 + 3.5 330 + 3.5 350 + 3.5 220 + 3.5 250 + 3.5
40 - 1 k 100 + 3.5 120 + 3.5 130 + 3.5 140 + 3.5 90 + 3.5 100 + 3.5
1k - 5 k 400 + 40 500 + 40 550 + 40 600 + 40 375 + 40 400 + 40
5k - 10 k 1300 + 80 1400 + 80 1500 + 80 1600 + 80 1200 + 80 1200 + 80
2.2 A 20 - 1 k 500 + 35 550 + 35 600 + 35 650 + 35 500 + 35 550 + 35
10 μA
1 k - 5 k 600 + 80 650 + 80 700 + 80 750 + 80 550 + 80 650 + 80
5 k - 10 k 6500 + 160 7500 + 160 8000 + 1600 8500 + 160 6000 + 160 7000 + 160
5725A Amplifier:
11 A 40 - 1 k 370 + 170 400 + 170 440 + 170 460 + 170 300 + 170 330 + 170
100 μA
1 k - 5 k 800 + 380 850 + 380 900 + 380 950 + 380 700 + 380 800 + 380
5 k - 10 k 3000 + 750 3300 + 750 3500 + 750 3600 + 750 2800 + 750 3200 + 750
Note:
Maximum output from the calibrator’s terminals is 2.2 A. Uncertainty specifications for 220 A and 2.2 mA ranges are increased by a
factor of 1.3 plus 2 μA when supplied through 5725A terminals. Specifications are otherwise identical for all output locations.
1. For fields strengths >0.4 V/m but ≤3 V/m, add 1 % of range.
1-38
Introduction and Specifications
Electrical Specifications 1
AC Current Secondary Performance Specifications and Operating Characteristics
Temperature Maximum Noise and
[2]
Resistive Distortion
Coefficient
[1]
Stability ± 1 °C Compliance
Load
(Bandwidth
Frequency
24 Hours Limits
Range
0 - 10 °C and
For Full 10 Hz - 50 kHz
(Hz) 10 - 40 °C
[3]
(V rms)
40 - 50 °C
Accuracy
<0.5V Burden)
(Ω)
± (ppm output + nA) ± (ppm output + nA)/°C ± (% output + μA)
[6]
220 μA 10 - 20 150 + 5 50 + 5 50 + 5 7 2 k 0.05 + 0.1
20 - 40 80 + 5 20 + 5 20 + 5 0.05 + 0.1
40 - 1 k 30 + 3 4 + 0.5 10 + 0.5 0.05 + 0.1
1 k - 5 k 50 + 20 10 + 1 20 + 1 0.25 + 0.5
5 k - 10 k 400 + 100 20 + 100 20 + 100 00.5 + 1
2.2 mA 10 - 20 150 + 5 50 + 5 50 + 5 7 500 0.05 + 0.1
20 - 40 80 + 5 20 + 4 20 + 4 0.05 + 0.1
40 - 1 k 30 + 3 4 + 1 10 + 2 0.05 + 0.1
1 k - 5 k 50 + 20 10 + 100 20 + 100 0.25 + 0.5
5 k - 10 k 400 + 100 50 + 400 50 + 400 00.5 + 1
22 mA 10 - 20 150 + 50 50 + 10 50 + 10 7 150 0.05 + 0.1
20 - 40 80 + 50 20 + 10 20 + 10 0.05 + 0.1
40 - 1 k 30 + 30 4 + 10 10 + 20 0.05 + 0.1
1 k - 5 k 50 + 500 10 + 500 20 + 400 0.25 + 0.5
5 k - 10 k 400 + 1000 50 + 1000 50 + 1000 00.5 + 1
Hz ± (ppm output + μA) ± (ppm output + μA) / °C
220 mA 10 - 20 150 + 0.5 50 + 0.05 50 + 0.05 7 15 0.05 + 10
20 - 40 80 + 0.5 20 + 0.05 20 + 0.05 0.05 + 10
40 - 1 k 30 + 0.3 4 + 0.1 10 + 0.1 0.05 + 10
1 k - 5 k 50 + 3 10 + 2 20 + 2 0.25 + 50
5 k - 10 k 400 + 5 50 + 5 50 + 5 00.5 + 100
[4]
2.2 A 20 - 1 k 50 + 5 4 + 1 10 + 1 1.4 0.5 0.5 + 100
1 k - 5 k 80 + 20 10 + 5 20 + 5 0.3 + 500
5 k - 10 k 800 + 50 50 + 10 50 + 10 0 1 + 1 mA
5725A Amplifier: ± (% output)
[5]
11 A 40 - 1 k 75 + 100 20 + 75 30 + 75 3 3 0.05
[5]
1 k - 5 k 100 + 150 40 + 75 50 + 75 0.12
[5]
5 k - 10 k 200 + 300 100 + 75 100 + 75 0.5
Notes:
Maximum output from 5720A terminals is 2.2 A. Uncertainty specifications for 220 μA and 2.2 mA ranges are increased by a factor of 1.3, plus
2 μA when supplied through 5725A terminals. Specifications are otherwise identical for all output locations.
1. Stability specifications are included in the Absolute Uncertainty values for the primary specifications.
2. Temperature coefficient is an adder to uncertainty specifications that does not apply unless operating more than ±5 °C from calibration
temperature.
2
actual load
3. For larger resistive loads multiply uncertainty specifications by: ( )
maximum load for full accuracy
4. 1.5 V compliance limit above 1 A. 5725A Amplifier may be used in range-lock mode down to 1 A.
5. For resistive loads within rated compliance voltage limits.
6. For outputs from the Aux Current terminals, the maximum resistive load for full accuracy is 1 kΩ. For larger resistive loads, multiply the
uncertainty as described in Note 3.
Minimum Output ....................................................9 μA for 220 μA range, 10 % on all other ranges. 1 A minimum for 5725A.
Inductive Load Limits............................................400 μH (5700A/5720A, or 5725A). 20 μH for 5700A/5720A output >1 A.
Power Factors........................................................5700A/5720A, 0.9 to 1; 5725A, 0.1 to 1. Subject to compliance voltage
limits.
Frequency:
Range (Hz)..........................................................10.000 - 11.999, 12.00 - 119.99, 120.0 - 1199.9, 1.200 k - 10.000 k
Uncertainty ....................................................±0.01 %
Resolution .....................................................11,999 counts
Settling Time......................................................5 seconds for 5700A/5720A ranges; 6 seconds for 5725A 11 A range; +1
second for amplitude or frequency range change.
Overshoot...........................................................<10 %
1-39
5700A/5720A Series II Calibrator
Service Manual
1-34. Wideband AC Voltage (Option 5700-03) Specifications
Specifications apply to the end of the cable and 50 Ω termination used for calibration.
Absolute Uncertainty
Range ± 5 °C from calibration temperature
30 Hz - 500 kHz
Resolution
24 Hours 90 Days 180 Days 1 Year
Volts dBm
± (% output + μV)
1.1 mV 10 nV 0.4 + 0.4 0.5 + 0.4 0.6 + 0.4 0.8 + 2
−46
3 mV 10 nV 0.4 + 1 0.45 + 1 0.5 + 1 0.7 + 3
−37
11 mV 100 nV 0.2 + 4 0.35 + 4 0.5 + 4 0.7 + 8
−26
33 mV −17 100 nV 0.2 + 10 0.3 + 10 0.45 + 10 0.6 + 16
110 mV −6.2 1 μV 0.2 + 40 0.3 + 40 0.45 + 40 0.6 + 40
330 mV +3.4 1 μV 0.2 + 100 0.25 + 100 0.35 + 100 0.5 + 100
1.1 V +14 0.2 + 400 0.25 + 400 0.35 + 400 0.5 + 400
10 μV
3.5 V +24 0.15 + 500 0.2 + 500 0.3 + 500 0.4 + 500
10 μV
Amplitude Flatness, 1 kHz Reference
Settling Time
Frequency Temperature Harmonic
Voltage Range
Frequency To Full
Coefficient
Resolution Distortion
Accuracy
(Hz) 1.1 mV 3 mV > 3 mV
(Hz) ± ppm/°C (dB)
(Seconds)
± (% output + floor indicated)
10 - 30 0.01 0.3 0.3 0.3 100 7 -40
30 - 120 0.01 0.1 0.1 0.1 100 7 -40
120 - 1.2 k 0.1 0.1 0.1 0.1 100 5 -40
1.2 k - 12 k 1 0.1 0.1 0.1 100 5 -40
12 k - 120 k 10 0.1 0.1 0.1 100 5 -40
120 k - 1.2 M 100 100 5 -40
0.2 + 3 μV 0.1 + 3 μV 0.1 + 3 μV
[1]
100 k 100 0.5 -40
1.2 M - 2 M 0.2 + 3 μV 0.1 + 3 μV 0.1 + 3 μV
2 M - 10 M 100 k 100 0.5 -40
0.4 + 3 μV 0.3 + 3 μV 0.2 + 3 μV
10 M - 20 M 1 M 0.6 + 3 μV 0.5 + 3 μV 0.4 + 3 μV 150 0.5 -34
20 M - 30 M 1 M 1.5 + 15 μV 1.5 + 3 μV 1 + 3 μV 300 0.5 -34
Note:
[1] For output voltages < 50 % of full range in the 33 mV, 110 mV, 330 mV, 1.1 V , and 3.5 V ranges, add 0.1 % to the amplitude flatness
specification.
Additional Operating Information:
dBm reference = 50 Ω
Range boundaries are at voltage points, dBm levels are approximate.
Power
dBm = 10 log ( ) ; 0.22361 V across 50 Ω = 1 mW or 0 dBm
1 mW
Minimum Output ................................................... 300 μV (−57 dBm)
Frequency Uncertainty ......................................... ± 0.01 %
Frequency Resolution .......................................... 11,999 counts to 1.1999 MHz, 119 counts to 30 MHz
Overload Protection.............................................. A short circuit on the wideband output will not result in damage. After
settling time, normal operation is restored upon removal.
1-40
Introduction and Specifications
Electrical Specifications 1
1-35. Auxiliary Amplifier Specifications
For complete specifications, see the 5205A and 5220A Operators Manuals.
5205A (220V - 1100 V ac, 0 V - 1100 V dc)
Overshoot: < 10 %
Distortion (bandwidth 10 Hz - 1 MHz):
10 Hz - 20 kHz ................................................ 0.07 %
20 kHz - 50 kHz .............................................. 0.2 %
50 kHz - 100 kHz ............................................ 0.25 %
90 Day Accuracy Temperature Coefficient for
Frequency
0 - 18 °C and 28 - 50 °C
at 23 ± 5 °C
(Hz)
± (% output + % range) ± (ppm output + ppm range) / °C
0 dc 0.05 + 0.005 15 + 3
10 - 40 0.15 + 0.005 45 + 3
40 - 20 k 0.04 + 0.004 15 + 3
20 k - 50 k 0.08 + 0.006 50 + 10
50 k - 100 k 0.1 + 0.01 70 + 20
5220A (AC Current, 180-day specifications):
Accuracy:
20 Hz - 1 kHz ................................................. 0.07 % + 1 mA
1 kHz - 5 kHz .................................................. (0.07 % + 1mA) x frequency in kHz
Temperature Coefficient (0 - 18 °C and 28 - 50 °C):
(0.003 % + 100A) / °C
Distortion (bandwidth 300 kHz):
20 Hz - 1 kHz .................................................. 0.1% + 1 mA
1 kHz - 5 kHz .................................................. (0.1% + 1 mA) x frequency in kHz
Note: 5700A/5720A combined with 5220A is not specified for inductive loads.
1-41
5700A/5720A Series II Calibrator
Service Manual
1-42
Chapter 2
Theory of Operation
Title Page
2-1. Introduction........................................................................................... 2-3
2-2. Calibrator Overview ............................................................................. 2-3
2-3. Internal References........................................................................... 2-3
2-4. Hybrid Reference Amplifiers....................................................... 2-3
2-5. Fluke Thermal Sensor (FTS)........................................................ 2-3
2-6. Digital-to-Analog Converter (DAC). ........................................... 2-4
2-7. Digital Section Overview...................................................................... 2-4
2-8. Analog Section Overview..................................................................... 2-4
2-9. Functional Description Presented by Output Function......................... 2-6
2-10. DC Voltage Functional Description ................................................. 2-7
2-11. AC Voltage Functional Description ................................................. 2-10
2-12. Wideband AC V Functional Description (Option -03) .................... 2-11
2-13. DC Current Functional Description.................................................. 2-11
2-14. AC Current Functional Description.................................................. 2-11
2-15. Ohms Functional Description........................................................... 2-12
2-1
5700A/5720A Series II Calibrator
Service Manual
2-2
Theory of Operation
Introduction 2
2-1. Introduction
This section provides a block diagram discussion of the calibrator’s analog and digital
sections.
2-2. Calibrator Overview
Figures 2-1, 2-2, and 2-3 comprise the block diagram of the Calibrator. These figures are
presented further on in the Analog Section Overview and the Digital Section Overview.
The Calibrator is configured internally as an automated calibration system with process
controls and consistent procedures. Internal microprocessors control all functions and
monitor performance, using a switching matrix to route signals between modules.
Complete automatic internal diagnostics, both analog and digital, confirm operational
integrity.
The heart of the measurement system is a 5 1/2-digit adc (analog-to-digital converter),
which is used in a differential mode with the Calibrator dac. (The dac is described next
under "Internal References.")
2-3. Internal References
The major references that form the basis of the Calibrator's accuracy are the hybrid
reference amplifiers, patented Fluke solid-state thermal rms sensors, an extremely linear
dac, and two internal precision resistors.
2-4. Hybrid Reference Amplifiers
A precision source can only be as accurate as its internal references, so the dc voltage
reference for the Calibrator was chosen with extreme care. Years of data collection have
proven the ovenized reference amplifier to be the best reference device available for
modern, ultra-stable voltage standards.
In a microprocessor-controlled precision instrument such as the 5700A/5720A Series II,
the important characteristics of its dc voltage references are not the accuracy of the value
of the references, but rather their freedom from drift and hysteresis. (Hysteresis is the
condition of stabilizing at a different value after being turned off then on again.) The
5700A/5720A Series II hybrid reference amplifiers excel in both freedom from drift and
absence of hysteresis.
2-5. Fluke Thermal Sensor (FTS).
Thermal rms sensors, or ac converters, convert ac voltage to dc voltage with great
accuracy. These devices sense true rms voltage by measuring the heat generated by a
voltage through a known resistance.
Conventional thermal voltage converters suffer from two main sources of error. First,
they exhibit frequency response errors caused by component reactance. Second, they
have a poor signal-to-noise ratio because they operate at the millivolt level. The FTS has
a full-scale input and output of 2V and a flat frequency response.
After initial functional verification of the Fluke Thermal Sensors, their characteristics
only change by less than 1/10th of the allowed ac/dc error per year. External calibration
of the ac voltage function of the Calibrator consists of verifying that the Calibrator meets
its specifications.
2-3
5700A/5720A Series II Calibrator
Service Manual
2-6. Digital-to-Analog Converter (DAC).
A patented 26-bit dac is used in the calibrator as a programmable voltage divider. The
dac is a pulse-width modulated (pwm) type with linearity better than 1 ppm (part-per-
million) from 1/10th scale to full scale.
2-7. Digital Section Overview
The unguarded Digital Section contains the CPU assembly (A20), Digital Power Supply
assembly (A19), Front Panel assembly (A2), Keyboard assembly (A1), and the
unguarded portion of the Rear Panel assembly (A21). Figure 2-1 is a block diagram of
the digital section of the Calibrator.
Power for the digital assemblies and the cooling fans is supplied by the Digital Power
Supply assembly.
The CPU (central processing unit) assembly is a single-board computer based on the
68HC000 microprocessor. It controls local and remote interfaces, as well as serial
communications over a fiber-optic link to the crossing portion of the Regulator/Guard
Crossing assembly (A17). The guard crossing controls the guarded analog circuitry.
A Keyboard assembly provides the user with front-panel control of the Calibrator. It
contains four LED's, a rotary edit knob, and a forty-five key keypad. It connects to the
Front Panel assembly via a cable.
The Front Panel assembly provides information to the user on an Output Display and a
Control Display. The Front Panel also contains circuitry that scans the keyboard and
encodes key data for the CPU.
The Rear Panel assembly includes digital interfaces for the following:
• IEEE-488 bus connection
• RS-232-C DTE serial port
• Auxiliary amplifier: the 5725A
2-8. Analog Section Overview
The guarded analog section contains the following assemblies:
• Wideband Output (A5) (Part of Option -03)
• Wideband Oscillator (A6) (Part of Option -03)
• Current/Hi-Res (A7)
• Switch Matrix (A8)
• Ohms Cal (A9)
• Ohms (A10)
• DAC (A11)
• Oscillator Control (A12)
• Oscillator Output (A13)
• High Voltage Control (A14)
• High Voltage/High Current (A15)
• Power Amplifier (A16)
• Regulator/Guard Crossing (A17)
• Filter/PA Supply (A18)
2-4
Theory of Operation
Analog Section Overview 2
ahp003f.eps
Figure 2-1. Digital Section Block Diagram
2-5
5700A/5720A Series II Calibrator
Service Manual
These analog assemblies are interfaced to the Analog Motherboard assembly (A3). The
guarded digital bus generated by the guard crossing portion of the Regulator/Guard
Crossing assembly controls all analog assemblies except the Filter/PA Supply. The Guard
Crossing interfaces with the unguarded CPU assembly via a fiber-optic link. The
Transformer assembly, along with the filter portion of the Filter/PA Supply assembly and
the regulator portion of the Regulator/Guard Crossing assembly, create the system power
supply for all the analog assemblies. The Power Amplifier Supply portion of the
Filter/PA Supply assembly provides the high voltage power supplies required by the
Power Amplifier assembly. The amplitudes of these high voltage supplies are controlled
by circuitry contained on the Power Amplifier assembly.
Figures 2-2 and 2-3 are block diagrams for the analog section of the Calibrator.
2-9. Functional Description Presented by Output Function
This part of the theory section presents Calibrator operation from the perspective of each
output function. It describes which assemblies come into play, and how they interact. It
does not provide a detailed circuit description.
2-6
Theory of Operation
Functional Description Presented by Output Function 2
2-10. DC Voltage Functional Description
The DAC assembly (A11) provides a stable dc voltage and is the basic building block of
the Calibrator. DC voltages are generated in six ranges:
• 220 mV
• 2.2V
• 11V
• 22V
• 220V
• 1100V
The 11V and 22V ranges are generated by the DAC assembly, with its output, DAC OUT
HI and DAC SENSE HI routed to the Switch Matrix assembly, where relays connect it to
INT OUT HI and INT SENSE HI. Lines INT OUT HI and INT SENSE HI connect to the
Calibrator binding posts by relays on the Analog Motherboard assembly (A3).
The 2.2V range is created on the Switch Matrix assembly by resistively dividing by five
the 11V range from the DAC assembly. Relays on the Switch Matrix and Analog
Motherboard route the 2.2V range output to the Calibrator binding posts.
The 220 mV range is an extension of the 2.2V range. The Switch Matrix assembly
resistively divides by ten the 2.2V range to create the 220 mV range. Relays on the
Switch Matrix and Analog Motherboard route the 220 mV range output to the front panel
binding posts.
The 220V range is generated by the DAC and Power Amplifier assemblies. The Power
Amplifier amplifies the 11V range of the DAC assembly by a gain of -20 to create the
220V range. The output of the Power Amplifier is routed to the High Voltage Control
assembly (A14), where a relay connects it to PA OUT DC. Line PA OUT DC is routed to
the binding posts via relays on the Switch Matrix and Analog Motherboard.
2-7
5700A/5720A Series II Calibrator
Service Manual
Figure 2-2. Analog Section Block Diagram, Part 1
(File ahp33f.eps is located in pagemaker and will be inserted when book is pdf'ed)
2-8
Theory of Operation
Functional Description Presented by Output Function 2
Figure 2-3. Analog Section Block Diagram, Part 2
(File is ahp34f.eps located in pagemaker and will be inserted when book is pdf'ed)
2-9
5700A/5720A Series II Calibrator
Service Manual
The 1100V range is generated by the High Voltage/High Current assembly (A15)
operating in conjunction with the Power Amplifier assembly and the High Voltage
Control assembly. The 11V range of the DAC assembly is routed to the High
Voltage/High Current assembly which amplifies by a gain of -100 to create the 1100V
range. Basically the high voltage output is obtained by rectifying and filtering a high
voltage ac signal generated by the High Voltage Control assembly operating in
conjunction with the Power Amplifier assembly.
2-11. AC Voltage Functional Description
The Oscillator Output assembly (A13) is the ac signal source for the Calibrator. The
Oscillator Control assembly (A12), controls the amplitude of this ac signal by comparing
it with the accurate dc voltage from the DAC assembly and making amplitude corrections
via the OSC CONT line. The frequency of oscillation is phase locked to either the high
resolution oscillator on the Current/Hi-Res (A7) assembly or an external signal connected
to the PHASE LOCK IN connector on the rear panel. AC voltages are generated in the
following ranges:
• 2.2 mV
• 22 mV
• 220 mV
• 2.2V
• 11V
• 22V
• 220V
• 1100V
The 2.2V and 22V ranges are generated by the Oscillator Output assembly and routed to
the Calibrator binding posts via relays on the Switch Matrix (A8) and Analog
Motherboard assemblies.
The 220 mV range is generated on the Switch Matrix assembly, which resistively divides
by ten the 2.2V range of the Oscillator Output assembly. Relays on the Switch Matrix
and Analog Motherboard route the 220 mV range to the Calibrator binding posts.
The 2.2 mV and 22 mV ranges are generated on the Switch Matrix assembly. In this
mode, the Switch Matrix resistively divides the 2.2V range or the 22V range by 1000 to
create the 2.2 mV and 22 mV ranges respectively. Relays on the Switch Matrix and
Analog Motherboard route these ranges to the Calibrator binding posts.
The 220V range is generated on the Power Amplifier assembly. In this mode, the Power
Amplifier is set for a nominal gain of -10 to amplify the 22V range from the Oscillator
Output to the 220V range. The 220V ac range from the Power Amplifier is routed to the
Calibrator binding posts by relays on the High Voltage Control assembly and the Analog
Motherboard.
The 1100V range is generated by the High Voltage Control assembly operating in
conjunction with the Power Amplifier assembly. In this mode, the 22V range from the
Oscillator Output is amplified by the Power Amplifier and High Voltage Control
assemblies, which create an amplifier with a nominal gain of -100. Relays on the High
Voltage Control and Analog Motherboard assemblies route the 1100V ac range to the
Calibrator binding posts.
2-10
Theory of Operation
Functional Description Presented by Output Function 2
2-12. Wideband AC V Functional Description (Option -03)
The Wideband AC Voltage module (Option -03) consists of the Wideband Oscillator
assembly (A6) and the Wideband Output assembly (A5). There are two wideband
frequency ranges:
• 10 Hz to 1.1 MHz
• 1.2 MHz to 30 MHz
During operation between 10 Hz and 1.1 MHz, output from the Oscillator Output
assembly is routed to the Wideband Output assembly where it is amplified and attenuated
to achieve the specified amplitude range. The output is connected to the Calibrator front
panel WIDEBAND connector. Operation between 1.2 MHz and 30 MHz works the same
way, except the input to the Wideband Output assembly is the ac signal from the
Wideband Oscillator assembly.
2-13. DC Current Functional Description
DC current is generated in five ranges:
• 20 μA - 220 μA
• 220 μA - 2.2 mA
• 2.2 mA - 22 mA
• 22 mA - 220 mA
• 2.2A
All current ranges except 2.2A are generated by the current portion of the Current/Hi-Res
assembly. These currents are created by connecting the output of the DAC assembly, set
to the 22V range, to the input of the Current assembly. The Current assembly uses this dc
voltage to create the output current. The current output can be connected to the AUX
CURRENT OUTPUT binding post by relays on the Current assembly, to the OUTPUT
HI binding post by relays on the Current, Switch Matrix, and Analog Motherboard
assemblies, or to the 5725A via the B-CUR line by relays on the Analog Motherboard
assembly and Rear Panel assembly.
The 2.2A range is an extension of the 22 mA range. The 22 mA range output from the
Current assembly is amplified by a gain of 100 by the High Voltage/High Current
assembly operating in conjunction with the Power Amp assembly and the High Voltage
Control assembly. The 2.2A current range is routed back to the Current assembly where it
is connected to either the AUX CURRENT OUTPUT binding post, the OUTPUT HI
binding post, or the 5725A in the same manner as the lower current ranges.
2-14. AC Current Functional Description
AC current is created in the same manner as dc current, except the input to the Current
assembly is the ac voltage from the Oscillator Output assembly set to the 22V range. The
switching between ac and dc is carried out on the Switch Matrix, Oscillator Control,
Oscillator Output, and DAC assemblies.
2-11
5700A/5720A Series II Calibrator
Service Manual
2-15. Ohms Functional Description
Two assemblies function as one to supply the fixed values of resistance:
• Ohms Main assembly (A10)
• Ohms Cal assembly (A9)
All of the resistance values except the 1Ω, 1.9Ω, and short are physically located on the
Ohms Main assembly. The 1Ω, 1.9Ω, and short are physically located on the Ohms Cal
assembly. The desired resistance is selected by relays on these Ohms assemblies and is
connected to the Calibrator binding posts by relays on the Analog Motherboard. The
Ohms Cal assembly also contains the appropriate circuitry to enable the Calibrator to
perform resistance calibration. Once calibrated, the Calibrator output display shows the
true value of the resistance selected, not the nominal (e.g., 10.00031 kΩ, not 10 kΩ).
Four ohms measurement modes are available. For the two-wire configuration,
measurement with or without lead-drop compensation sensed at the binding posts of the
UUT (using the SENSE binding posts and another set of leads), or at the ends of its test
leads is available for 19 kΩ and below. Four-wire configuration is available for all but the
100 MΩ value.
2-12
Chapter 3
Calibration and Verification
Title Page
3-1. Introduction........................................................................................... 3-3
3-2. Calibration............................................................................................ 3-4
3-3. Calibrating the 5700A/5720A Series II to External Standards............. 3-4
3-4. Calibration Requirements................................................................. 3-4
3-5. When to Adjust the Calibrator’s Uncertainty Specifications ........... 3-5
3-6. Calibration Procedure....................................................................... 3-6
3-7. Range Calibration ................................................................................. 3-12
3-8. Calibrating the Wideband AC Module (Option 5700A-03) ................. 3-15
3-9. Performing a Calibration Check ........................................................... 3-18
3-10. Full Verification.................................................................................... 3-20
3-11. Required Equipment for All Tests.................................................... 3-21
3-12. Warm-up Procedure for All Verification Tests ................................ 3-21
3-13. Resistance Verification Test............................................................. 3-23
3-14. Two-Wire Compensation Verification ............................................. 3-25
3-15. DC Voltage Verification Test........................................................... 3-26
3-16. DC Voltage One-Tenth Scale Linearity Test ................................... 3-27
3-17. Direct Current Accuracy Verification Test ...................................... 3-28
3-18. AC Voltage Frequency Accuracy Test............................................. 3-29
3-19. Output Level Tests For AC V Ranges.............................................. 3-29
3-20. AC Current Test, 22 mA to 11A Ranges.......................................... 3-31
3-21. AC Current Test, 2 mA and 200 μA Ranges.................................... 3-34
3-22. Rationale for Using Metal-Film Resistors to Measure AC Current . 3-35
3-23. Wideband Frequency Accuracy Test................................................ 3-36
3-24. Wideband AC Voltage Module Output Verification........................ 3-36
3-25. Wideband Output Accuracy at 1 kHz Test ........................................... 3-37
3-26. Wideband Output Flatness Test............................................................ 3-38
3-27. Wideband Flatness Calibration Procedure ....................................... 3-39
3-28. Optional Tests....................................................................................... 3-40
3-29. DC Voltage Load Regulation Test ................................................... 3-40
3-30. DC Voltage Linearity Test ............................................................... 3-41
3-31. DC Voltage Output Noise (10 Hz to 10 kHz) Test........................... 3-41
3-32. DC Voltage Output Noise (0.1 to 10 Hz) Test ................................. 3-43
3-33. AC Voltage Distortion Test.............................................................. 3-43
3-34. Wideband Distortion Testing ........................................................... 3-43
3-35. AC Voltage Overshoot Test ............................................................. 3-44
3-1
5700A/5720A Series II Calibrator
Service Manual
3-36. Minimum Use Requirements ................................................................ 3-44
3-37. Determining Test Limits for Other Calibration Intervals ..................... 3-46
3-2
Calibration and Verification
Introduction 3
3-1. Introduction
This chapter gives procedures for 5700A/5720A Series II calibration, verification,
acceptance testing, and performance testing. Information here applies to testing the
performance of and calibrating a normally operating 5700A/5720A Series II. In case of
malfunction, refer to Chapter 5, Troubleshooting, which explains how to use self
diagnostic tests to identify a faulty module. Calibration and Performance Testing is
presented in the following three parts:
• Calibration, which is to be done at the beginning of every calibration cycle. This is
the same procedure as in Chapter 7 of the 5700A/5720A Series II Operator Manual.
It uses three external standards; 1Ω, 10 kΩ, and 10V dc. The procedure is repeated
here for convenience. Also included in this part are procedures for doing Calibration
Check and Range Calibration.
• Full Performance Verification, which is the full verification procedure, recommended
every two years. Part of this procedure is Wideband AC Module (Option 5700A-03)
flatness calibration, also recommended only every two years.
Optional Tests, which are recommended following repair or for use in acceptance testing.
These tests include such checks as load regulation, noise, and distortion. These tests are
not required on a routine basis. They are not necessary after a Calibrator passes Full
Performance Verification.
3-3
5700A/5720A Series II Calibrator
Service Manual
3-2. Calibration
This chapter provides procedures for calibrating the 5700A/5720A Series II to external
standards, adjusting the range if necessary, and for performing a calibration check.
Your calibrator is calibrated at the factory with constants that are traceable to NIST. In
order to maintain traceability, you only need to met the following requirements.
• Calibration to external standards must be completed at the beginning of the
calibration cycle
• Performance verification must be completed every two years.
• Zero Calibration must be performed every 30 days (refer to the 5700A/5720A Series
II Operators Manual).
Calibration check and range calibration are optional procedures that are provided for
enhancing the accuracy if needed for special requirements.
3-3. Calibrating the 5700A/5720A Series II to External Standards
You must calibrate to external standards at the beginning of the calibration cycle. The
length of the cycle (24 hours, 90 days, 180 days, or one year) is selected in a setup menu
described in Chapter 4 of the 5700A/5720A Operators Manual.
To calibrate the 5700A/5720A Series II, you apply three portable standards to the output
binding posts: a 10V dc voltage standard, a 1Ω resistance standard, and a 10 kΩ
resistance standard. The following standards are recommended:
• Model 732B DC Reference Standard
• Model 742A-1 1Ω Resistance Standard
• Model 742A-10k 10Ω Resistance Standard
Use the following Low Thermal Leads for all connections:
• When calibrating the 5700A, use either the connector set 5440A-7002 (banana plugs)
or the set 5440A-7003 (spade lugs).
• When calibrating the 5720A, use the set 5440A-7003 (spade lugs).
WXWarning
Operator accessible LETHAL VOLTAGES may be present on the
lugs at the end of these cables when used with instrumentation
capable of producing such voltages. These cables should be
used only when thermal emf performance is required. For other
applications, cables with operator protection form contact with
high voltages should be used.
3-4. Calibration Requirements
Both the calibrator and the recommended external standards have the ability to internally
control (or compensate for) ambient temperature variations. Therefore it is unnecessary to
keep the calibrator in tightly controlled temperatures during calibration. During the
calibration procedure, the calibrator prompts you to enter the ambient temperature, and
includes this information in specification readouts and output shift reports.
3-4
Calibration and Verification
Calibrating the 5700A/5720A Series II to External Standards 3
3-5. When to Adjust the Calibrator’s Uncertainty Specifications
Table 3-1 lists each external standard’s uncertainty limit, and the 5700A/5720A Series II
uncertainty specifications that must adjusted accordingly if that limit is exceeded.
As long as the external standards have the uncertainties listed in Table 3-1, you do not
need to adjust the calibrator’s absolute uncertainty specifications in Chapter 1. However,
if your standard’s uncertainty exceeds the value in the table you must adjust some of the
calibrator’s absolute uncertainty specifications by the algebraic difference between your
standard’s uncertainty and the uncertainty limit listed in the Table 3-1. For example, if
the dc voltage standard has an uncertainty of ±2.5 ppm, then the 5700A and the 5720A
absolute uncertainty specifications listed in Table 3-1 for the traceable quantity of voltage
must all be increased by ±1 ppm.
Table 3-1. Standards for Calibrating 5700A/5720A Series II
Fluke Traceable Nominal Uncertainty 5700A/5720A Series II
Standard Quantity Value Limit Specifications susceptible to
Uncertainty Limit
dc volts, ac volts,
732B Voltage 10V ±1.5 ppm
dc current, ac current
742A-1 Resistance 1Ω ±10 ppm 1Ω, 1.9Ω
ac current, dc current 10Ω to
742A-10k Resistance 10 kΩ ±4 ppm
100 MΩ
3-5
5700A/5720A Series II Calibrator
Service Manual
3-6. Calibration Procedure
Before you being this procedure make sure the calibrator is powered on and has
completed the appropriate warm-up period.
After you have finished calibration, but before you save the new constants, the calibrator
presents the new changes as ± ppm, and as a percentage of specifications for each range
and function. A list of changes can be sent to a computer through either the serial or
instrument control (IEEE-488) port, or printed through the serial port. The largest
proposed change will be displayed on the calibrator’s front panel.
Follow this procedure to calibrate the main output functions.
1. Press the “Setup Menus” softkey; then press the “Cal” softkey. The calibration menu
appears as shown below:
PREV
MENU
IF3-1.EPS
2. Press the “Cal” softkey. The display shows the following.
PREV
MENU
3. To calibrate the main output functions, press one of the softkeys under “Calibration.”
The display shows the following:
PREV
MENU
IF3-3.EPS
3-6
Calibration and Verification
Calibrating the 5700A/5720A Series II to External Standards 3
4. Enter the ambient temperature; then press E. The display shows:
PREV
MENU
IF3-4.EPS
5. Connect the 732B to the calibrator as shown in Figure 3-1.
VOLTAGE REFERENCE
STANDARD
732B DC STANDARD
CALIBRATOR
AC PWR IN CAL CHARGE LOW BAT
OUTPUT SENSE
V AΩΩ V
10V 1.018V CHASSIS
WIDEBAND
HI
HI
LO LO
10V COM 1.018V COM GUARD
HI
SERIAL NUMBER
AUX
GROUND
GUARD
CURRENT
F7-3.EPS
Figure 3-1. 732B External Calibration Connections.
3-7
5700A/5720A Series II Calibrator
Service Manual
6. Enter the true value of the 732B 10V output. The true value is the value printed on
the calibration sticker, plus or minus, as well as drift that has occurred since
calibration. That drift can be estimated provided control charts have been maintained
for the 732B.
If the entered value is not between 9V and 11V, and error message appears, which
lets you start over from this point with a calibrated 732B. Press E, and the
display shows the following:
PREV
MENU
IF3-5.EPS
When the calibrator’s 6.5V and 13V references have been characterized, the display
shows the following message, which lets you accept or reject the changes that are
about to be made to the calibration constants.
PREV
MENU
IF3-6.EPS
7. To reject the changes, return to the calibration menu shown in step 2 by pressing
P. Otherwise, press the softkey under “Proceed” to accept and save the changes,
and to open the display shown below, letting you continue with calibration.
PREV
MENU
IF3-7.EPS
3-8
Calibration and Verification
Calibrating the 5700A/5720A Series II to External Standards 3
8. Reverse the HI and LO connections at the 732B terminals, and press E. The
following displays appear, asking you to wait before proceeding with the 10 kΩ
standard.
PREV
MENU
IF3-8.EPS
After a few seconds, the following display appears:
PREV
MENU
IF3-9.EPS
9. Connect the calibrator to the 10 kΩ standard as shown in Figure 3-2 and enter the
true value of the standard. If the standard is not between 9 kΩ and 11 kΩ, an error
message appears, which allows you to start over from this point with a different
standard. Press E again to open the following display:
PREV
MENU
IF3-10.EPS
When the internal 10 kΩ reference has been characterized, the following message
appears, which lets you accept or reject the changes that are about to be made to the
calibration constant:
PREV
MENU
IF3-11.EPS
3-9
5700A/5720A Series II Calibrator
Service Manual
CALIBRATOR
RESISTANCE STANDARD
OUTPUT SENSE
CURRENT SENSE
V A Ω V Ω
HI WIDEBAND
HI
HI
HI
LO
LO
LO
LO
HI
CHASSIS AUX GUARD GROUND
GROUND CURRENT
F7-4.EPS
Figure 3-2. 742A-1 and 742A-10k External Calibration Connections
10. To reject the changes, return to the calibration menu shown in step 2 by pressing
P. Otherwise, press the softkey under “Proceed” to accept and save the changes,
and to open the display shown below, letting you continue with calibration.
PREV
MENU
IF3-12.EPS
3-10
Calibration and Verification
Calibrating the 5700A/5720A Series II to External Standards 3
11. Disconnect the 10 kΩ standard, and connect the calibrator to the 1Ω standard; then
enter the true value of the 1Ω standard. If the standard is not between 0.9Ω and 1.1Ω,
an error message appears, which lets you start over from this point with another
standard. Press E to bring up the following display:
PREV
MENU
IF3-13.EPS
When the internal 1Ω reference has been characterized, the following message
appears, which lets you accept or reject the changes that re about to be made to the
calibration constant:
PREV
MENU
IF3-14.EPS
12. To reject the changes, return to the calibration menu shown in step 2 by pressing
P. Otherwise, press the softkey under “Proceed” to accept and save the changes,
and let the calibrator complete the internal calibration steps.
13. The calibration is not effective until you store the newly calibrated constants in
memory. To store the constants, set the rear panel CALIBRATION switch to
ENABLE, the press the “Store Values” softkey.
Note
To review the proposed output shifts before you store the new constants,
print a listing of the proposed shifts by pressing the softkey under “Print
Output Shifts.”
14. After you store the constants, press the softkey under “DONE with Cal” to exit
calibration and resume normal operation.
15. If you press this softkey before you store the constants, the new constants will be
used temporarily for normal operation until the calibrator is powered down or reset.
(This is only true for software versions G and lower. For versions H and higher, the
process is aborted without updating existing constants.)
16. Set the rear panel CALIBRATION switch to NORMAL.
3-11
5700A/5720A Series II Calibrator
Service Manual
3-7. Range Calibration
Once calibration is complete, you may find you need to make further adjustments to the
range. Calibrating the range is accomplished by adjusting a range constant, which is an
additional gain multiplier. Although range calibration is not needed in order to meet total
uncertainty specifications, it is useful for tuning the calibrator so that its values are closer
to your own standards.
Use your own laboratory standard to adjust the range constants. The following procedure
for adjusting the range constants is designed for laboratory standard values that are
between 45% and 95% of the range’s full-scale value.
Once you adjust the range constant, the new constant remains active until the next
calibration, at which time all range constant multipliers are rest to 1. You can also erase
all range adjustments by calling up the format EEPROM menu and selecting Range
Constants (refer to Chapter 4 of the 5700A/5720A Operators Manual).
Before you begin the following procedure, make sure you have the equipment you need
on hand including your own laboratory standards where required.
The following example procedure adjusts the 220V dc range constant using the following
equipment:
• 732B DC reference standard
• 752A Reference Divider
• 845AB/845AR Null Detector
• Low Thermal Test Leads: 5440A-7002 (banana plugs) or 5440A-7003 (spade lugs)
WXWarning
Operator accessible LETHAL VOLTAGES may be present on the
lugs at the end of the 5440A-7003 cables when used with
instrumentation capable of producing such voltages. These
cables should be used only when thermal emf performance is
required. For other applications, cables with operator protection
form contact with high voltages should be used.
Proceed as follows to adjust the 220V dc range constant. You must have completed
calibration to external standards before you follow this procedure.
1. Press the “Setup Menus” softkey; the press the “Cal” softkey. The following menu
appears:
PREV
MENU
IF3-1.EPS
2. Press the “Cal” softkey to bring up the next menu shown below:
3-12
Calibration and Verification
Range Calibration 3
PREV
MENU
IF3-2.EPS
3. Press the “Range Adjust” softkey to bring up the next menu shown below:
PREV
MENU
IF3-18.EPS
4. Press the “DC V” softkey to bring up the next menu shown below:
PREV
MENU
IF3-19.EPS
5. Press the “NEXT Menu” softkey, which scrolls through all the available dc voltage
ranges, until 220V appears. Then press that selection’s softkey to open a display
similar to the following:
PREV
MENU
IF3-20.EPS
6. Connect the 732B, null detector, and 752A in a 10:1 configuration, as shown in
Figure 3-3.
7. Multiply the 732B’s value by 10, and enter this new value. (This value is the output
of the 752A, to which you will null the calibrator’s output.) Then press E to
bring up the following display.
3-13
5700A/5720A Series II Calibrator
Service Manual
PREV
MENU
IF057.EPS
8. Press O to activate the calibrator output. Then turn the output adjustment knob on
the calibrator until you achieve a null on the null detector.
9. Se the rear panel CALIBRATION switch to ENABLE. Press E on the front
panel. The calibrator will now calculate a new range constant multiplier for the 220V
dc range, and will store it in non-volatile memory.
10. The range calibration is now complete. Set the rear panel CALIBRATION switch to
the NORMAL position, disconnect the external standards, and press r to reset the
calibrator to its newly calibrated ranges.
3-14
Calibration and Verification
Calibrating the Wideband AC Module (Option 5700A-03) 3
NULL DETECTOR
HI
LO
GUARD
GND
: OFF : OFF
EX SNS EX GRD
CALIBRATOR
NC
OUTPUT SENSE
V A Ω VA
WIDEBAND
HI HI
LO
LO
HI
AUX GUARD GROUND
CURRENT
752A VOLTAGE DIVIDER STANDARD
HI LO
INPUT
NULL
LO
HI
DETECTOR GRD
OUTPUT GND
HI LO
REFERENCE
STANDARD
HI
LO
732B VOLTAGE REFERENCE
STANDARD
732B DC STANDARD
AC PWR IN CAL CHARGE LOW BAT
10V 1.018V CHASSIS
10V COM 1.018V COM GUARD
SERIAL NUMBER
F7-6.EPS
Figure 3-3. 220V DC Range Calibration Connections
3-8. Calibrating the Wideband AC Module (Option 5700A-03)
The Wideband AC Module (Option 5700A-03) can be installed in either the 5720A or
5700A Series II calibrator. The module needs to be calibrated for both gain and flatness.
The gain should be calibrated when the 5700A-03 main output functions undergo their
routine calibration.
3-15
5700A/5720A Series II Calibrator
Service Manual
Since frequency flatness is determined by stable parameters (i.e. circuit geometry and
dielectric constants), the flatness of the Wideband AC Module has excellent long-term
stability. Consequently, a two-year calibration cycle is adequate for flatness calibration,
and can be scheduled to coincide with the calibrator’s shipment to a standards laboratory
for periodic verification.
The following procedure describes how to perform the wideband gain calibration.
Note
To perform this procedure you will need, in addition to the standard
equipment supplied with the wideband option, a Type “N” female to double
banana plug adapter (e.g., Pomona 1740).
Before you start this procedure, make sure the calibrator is powered on and has
completed an appropriate warm-up period. Then proceed with this procedure to calibrate
the wideband gain.
1. Press the “Setup Menus” softkey; then press the “Cal” softkey to being up the menu
shown below:
PREV
MENU
IF3-1.EPS
2. Press the “Cal “ softkey to bring up the following menu:
PREV
MENU
IF3-2.EPS
3. Connect the wideband output cable between the WIDEBAND connector and the
SENSE binding post.
The center conductor of the 50Ω feedthrough should go to SENSE HI and shown in
Figure 3-4. The GND tab on the adapter should be on the LO side.
3-16
Calibration and Verification
Calibrating the Wideband AC Module (Option 5700A-03) 3
CALIBRATOR
OUTPUT
SENSE
V A Ω
V Ω
50 FEEDTHROUGH Ω
WIDEBAND
HI
HI
LO
LO
HI
AUX GUARD GROUND
CURRENT
GND TAB
F7-5.EPS
Figure 3-4. Wideband Module Calibration Connection
4. Press the “Gain” softkey to bring up the following display:
PREV
MENU
IF3-3.EPS
5. Enter the ambient temperature; the press E. The display shows the following:
PREV
MENU
IF3-15.EPS
As the wideband calibration proceeds, messages appear on the display identifying all
processes as they are encountered. When positive gains calibration is complete, a
message appears telling you to refer to the manual for negative gains connections.
3-17
5700A/5720A Series II Calibrator
Service Manual
6. Reverse the dual-banana connector so that the center connector is connected to LO;
then press E. The display shows the following:
PREV
MENU
IF3-16.EPS
After a short time, a message appears indicating that the wideband calibration is
complete.
7. To store the new constants, set the CALIBRATION switch to ENABLE and press
“Store Values.” To discard the constants, press “DONE with Cal” and answer “YES”
when the display asks for verification.
8. You have now completed the wideband gain calibration. Set the CALIBRATION
switch to NORMAL, disconnect the wideband cable, and press r.
3-9. Performing a Calibration Check
A calibration check is similar to the calibration, with the primary difference being that no
changes are made to the stored constants, and the internal check standards are used as the
reference points. A calibration check produces a report similar to the normal calibration
report, and shows any proposed changes.
This procedure can be performed from an external computer, and can be set to run
automatically, with no assistance (there is no need to enable the CALIBRATION switch,
since no constants are changed).
You can use the calibration check at any time to confirm the integrity of the calibrator
without connecting external standards. The calibration check is also useful for collecting
a performance history.
Before you begin this procedure, make sure the calibrator is powered on and has
completed the appropriate warm-up period. Then follow this procedure to check the
calibration.
1. Press the “Setup Menu” softkey; then press the “Cal” softkey to bring up the
following menu:
PREV
MENU
IF3-1.EPS
2. Press the “Cal Check” softkey to bring up the following display:
3-18
Calibration and Verification
Performing a Calibration Check 3
PREV
MENU
IF3-3.EPS
3. Enter the ambient temperature; then press E. As the calibration check
proceeds, the display indicates the current process of the calibration check. When the
check is complete, the largest shift that is detected appears on the display.
PREV
MENU
IF3-17.EPS
4. You can now print a list of the proposed shifts, or quit without creating a list.
To print the report, connect a printer and set up the serial interface as described in
Chapter 6 of the 5700A/5720A Operators Manual. Press the softkey under “Print
Output Changes.” To return to normal operation without printing, press the softkey
under “DONE with check.”
Press P to exit the calibration menus.
3-19
5700A/5720A Series II Calibrator
Service Manual
3-10. Full Verification
An independent external verification is recommended every two years, following normal
periodic calibration or repair of the calibrator. Verification establishes and maintains
parallel external traceability paths for the internal functions that are not adjusted or
corrected during calibration. An example is the internal ac/dc transfer standard.
Verification also serves as a check that internal calibration processes are in control.
Note
All performance limits specified in the test records apply to 90-day
specifications for the Calibrator. If limits to other specifications are
desired, the test records must be modified. A description of how to
determine a guardband test limits is included in this section.
Note
Equivalent equipment and methods, either manual or automated, may be
substituted for the following verification tests as long as the same points
are tested, and equipment and standards used are at least as accurate as
those specified. If standards are less accurate than specified, appropriate
tolerance limit and/or accuracy reductions must be made to achieve
equivalent results.
Not all of the procedures contained in this chapter need to be performed to verify your
calibrator. This chapter contains the verification procedures for the 5720A and the 5700A
Series II Calibrators. In addition, procedures are provided to verify the ac functions of the
calibrator with a 5790A. The following roadmap provides a high-level overview of the
verification tests discussed in this chapter.
5790A
5720A
DC DC AC AC Wide
Resistance Frequency
Volt Current Band
Volt Current
3-16 3-18 3-20 3-21 3-22 3-26 3-28
to
3-30
5700A 5790A
DC DC AC AC Wide
Resistance Frequency
Volt Current Band
Volt Current
3-22 3-26 3-28
3-16 3-18 3-20 3-21
to
3-30
F0-0.EPS
Figure 3-5. Overview of Verification Tests
3-20
Calibration and Verification
Full Verification 3
In Figure 3-5, the location of each test is identified by the paragraph numbers.
3-11. Required Equipment for All Tests
An abbreviated summary of required equipment for all the verification and optional tests
is given in Table 3-2. Individual lists of required equipment are included at the beginning
of each test. For substitution information, refer to Table 3-15, Minimum Use
Requirements, located near the end of this section.
3-12. Warm-up Procedure for All Verification Tests
Before performing verification, do the following preliminary steps:
1. Verify that the Calibrator has warmed up for at least thirty minutes.
Note
If the Calibrator has been powered off in an environment outside of
operating environment specifications, particularly with humidity above
70%, allow a minimum of two hours warm-up. Extended storage at high
temperatures and humidity may require up to four days of power-on
stabilization.
2. If you are doing a regularly scheduled full verification as recommended by Fluke,
calibrate the 5700A/5720A Series II as previously described before continuing with
verification.
3. Ensure that each piece of external test equipment has satisfied its specified warm-up
requirements.
4. Ensure that the Calibrator is in standby (STANDBY annunciation lit).
3-21
5700A/5720A Series II Calibrator
Service Manual
Table 3-2. List of Required Equipment for Main Output
Equipment Description Application
AC Measurement Standard or Fluke 5790A ACV, ACI
Resistance Standards Fluke 742A Series Cal, Ohms, DCI
Reference Divider Fluke 752A DC V
Null Detector EM Electronics N11 (Fluke 845A) DC V
Shunt Adapter Fluke 792A-7004 AC I
Calibrator Fluke 55X0A Ohms
Frequency Counter Philips PM6669 Frequency
Shunts Fluke A40 Series AC I
High Current Shunt Fluke Y5020 DC I
Resistance Standard L&N 0.1Ω 4221B DC I
DMM Wavetek 1281 or HP 3458A Ohms, DCI, ACI, AC V
Low Thermal Cables Fluke 5440A-7002 (5700A) or Various
5440A-7003 (5720A or 5700A)
Equipment Required for Wideband Ac Module (Option 5700-03) Verification
Equipment Description Application
AC Measurement Standard Fluke 5790A with Wideband Wideband
Option -03
Wideband Cable (supplied with Fluke Cable Wideband
5700A-03)
50Ω Termination (supplied with Fluke Termination Wideband
5700A-03)
Adapter (supplied with 5700A-03) Pomona 1269 BNC(F) to dual banana Wideband
plug
Adapter Kings KN-99-46 N(F) to BNC(M) Wideband
Equipment Required for Optional Tests
Equipment Description Application
Oscilloscope Mainframe Tektronix 7000 Series HF Noise
Differential Amplifier Tektronix 7A22 HF Noise
Distortion Analyzer Krohn-Hite 6900B AC V, ACI, Distortion
Spectrum Analyzer HP 8590A AC V, Wideband
Distortion
Kelvin Varley Divider Fluke 720A DC V Linearity
3-22
Calibration and Verification
Full Verification 3
3-13. Resistance Verification Test
The following test requires testing at the high, low and intermediate values only. This is
because the 5700A/5720A Series II creates the other values of resistance from these
values. Use Tables 3-16 (5720A) and 3-17 (5700A) for test records. For the convenience
of anyone wishing to test the intermediate values, the tolerance limits are included.
Testing these values could be done using a Hamon-type ratio device and a very stable,
high-resolution bridge or DMM, or a combination of the two. Table 3-3 lists equipment
required for this test. See Table 3-15, Minimum Use Requirements, for substitution
information.
Table 3-3. Equipment Required for Resistance Testing
Equipment Decsription
Resistance Standards Fluke 742A Series in the following values: 1Ω, 1.9Ω, 10Ω, 10 kΩ, 19 kΩ, 10 MΩ,
and 19 MΩ
Current Source Fluke 5500A or 5520A
DMM Wavetek 1281 or HP 3458A
1. Connect the equipment as shown in Figure 3-6.
2. Set the Calibrator output to 1Ω with external sensing (EX SENS indicator lit) and set
the dc DMM to read dc V. Record the 1Ω resistance standard value on the test record
as the 1Ω STD RES VALUE.
3. Multiply the certified value of the 1Ω resistance standard by 0.1 and record the result
on the test record as the 1Ω STD VOLTAGE.
4. Connect the DMM across the sense terminals of the 1Ω resistance standard.
5. Set the direct current source for a nominal 100 mA output. Vary the source until the
DMM reading is as close as possible to the 1Ω Standard Voltage recorded in the
previous step. Record the DMM voltage reading on the test record as the
MEASURED 1Ω STD VOLTAGE.
Note
If the current source used has the resolution to achieve a voltage reading
to within ±5 ppm of the value in step 3, it is not necessary to calculate the
cal current in take next step. In this case, when you come to step 9 you will
simply multiply the voltage reading from step 9 by a factor of 10, which is
the same as dividing by 100 mA (0.1A).
6. Calculate the exact current by dividing the MEASURED 1Ω STD VOLTAGE by the
1Ω STD RES VALUE; record the result on the test record as the CAL CURRENT.
7. Enter the Calibrator displayed 1Ω value on the test record as the UUT 1Ω
DISPLAYED VALUE.
8. Transfer the dc DMM leads to the Calibrator sense terminals.
9. Enter the DMM voltage reading on the test record as the UUT 1Ω VOLTAGE.
10. Calculate the UUT true 1Ω resistance by dividing the UUT 1Ω VOLTAGE by the
CAL CURRENT.
11. Adjust the output adjustment knob for a UUT Control Display reading equal to the
true 1Ω resistance value calculated in the previous step. The error from the displayed
value is also shown on the Control Display. Enter the value of the error on the test
record as the UUT DEVIATION FROM DISPLAYED VALUE.
3-23
5700A/5720A Series II Calibrator
Service Manual
DMM
INPUT SENSE
HI HI
LO LO
CURRENT SOURCE 742A-X CALIBRATOR
CURRENT SENSE OUTPUT SENSE
OUTPUT
(UUT)
HI
HI HI HI HI
LO LO LO LO LO
F3-5.EPS
Figure 3-6. 1 Ohm and 10 Ohm Resistor Verification
Note
There is no need to do the cal current calculation of step 6 if the current
source has a settability of ±3 ppm.
12. Repeat steps 3 through 11 for the 1.9Ω and 10Ω resistance values using the 1.9Ω and
10Ω resistance standards. At the 10 ohm check, use 10 mA of current and a
multiplier for step 3 of 0.01.
13. The low-value (1Ω, 1.9Ω, and 10Ω) tests are summarized in Table 3-4.
3-24
Calibration and Verification
Full Verification 3
Table 3-4. Low Value Resistance Calibration Using a Current Source
5720A (UUT) Apply Current 5720A Deviation From 5720A Displayed Value
Resistance Displayed Value (90-day)
1Ω 100 mA ±95 ppm 0.9995 to 1.0005
1.9Ω 100 mA ±95 ppm 1.89905 to 1.90095
10Ω 10 mA ±25.0 ppm 9.997 to 10.003
5700A (UUT) Apply Current 5700A Deviation From 5700A Displayed Value
Resistance Displayed Value (90-day)
1Ω 100 mA ±95 ppm 0.9995 to 1.0005
1.9Ω 100 mA ±95 ppm 1.89905 to 1.90095
10Ω 10 mA ±28.0 ppm 9.997 to 10.003
14. For the remaining tests, no current source is required. Verify that each true UUT
value is within the limits shown in Table 3-16 for 5700A and Table 3-17 for 5720A.
a. Connect the DMM, set for 4-wire resistance, first to the Resistance Standard
equal to the UUT nominal output and then to the UUT itself. In each case, record
the resistance standard DMM reading and the resistance standard certified value.
b. Calculate the DMM correction by subtracting the DMM reading from the
certified value; enter this calculated value on the test record as DMM ERROR.
c. Move the DMM to the UUT terminals; enter the DMM reading on the test record
as DMM UUT RES RDG.
d. Algebraically add the DMM ERROR and the DMM UUT RES RDG; enter the
sum on the test record as UUT TRUE RES VALUE.
e. Adjust the output adjustment knob for a UUT Control Display reading equal to
the true resistance value previously calculated. The error from the displayed
value is also shown on the Control Display. Enter this error (with polarity
reversed) on the test record as the UUT DEVIATION FROM DISPLAYED
VALUE.
3-14. Two-Wire Compensation Verification
Use the following steps to verify that two-wire compensation operates correctly:
1. Connect the UUT (output set to 100Ω, with external sensing) to the DMM (set for 4-
wire resistance measurement). Note the DMM reading.
2. Connect two shorts: DMM SOURCE HI to SENSE HI and DMM SOURCE LO to
SENSE LO.
3. Activate UUT 2-wire compensation.
4. Check that the DMM reading returns to within 4 miliohms of the reading noted in
step 1.
3-25
5700A/5720A Series II Calibrator
Service Manual
3-15. DC Voltage Verification Test
The following test checks every dc voltage range by testing the output accuracy at decade
values of voltage from 100 mV to 1000V. Use Table 3-18 (5720A) or Table 3-19 (5700)
for the test record. Table 3-5 lists equipment required for this test as well as the Linearity
Test that follows. See Table 3-15, Minimum Use Requirements, for equipment
substitution information.
Table 3-5. Equipment Required for DC Voltage Testing
Equipment Model
DC Reference Standard Fluke 732B
Reference Divider Fluke 752A
Null Detector EM Electronics 11 (Fluke 845A)
Low Thermal Cables 5440A-7002
5440A-7003
Note
The 5440A-7002 or 5440A-7003 is for the 5700A; the 5720A uses only the
5440A-7003.
Proceed as follows to perform the dc voltage verification test:
1. Self-calibrate the reference divider in accordance with its instruction manual prior to
proceeding.
2. Connect the equipment as shown in Figure 3-3.
3. Set the reference divider to 0.1V. Set the Calibrator to the certified value of the dc
reference standard divided by 100. For example, if the certified value of the dc
reference standard is 10.000007V, set the Calibrator to 100.00007 mV.
4. Press OPR/STBY. After the reading has settled, verify that the null detector reads 0V
±1.20 μV (5720A 90-day specification) or 0V ±1.45 μV (5700A 90-day
specification). Set the Calibrator to standby.
5. Repeat the above process to test each dc voltage range output listed in Tables 3-23 or
3-24. (0.1V is in the table for completeness; you do not need to repeat it.) After the
null detector reading stabilizes, ensure that any observed meter rattle (over and above
the null detector rattle in the "zero" position) over a ten-second period does not
exceed the amount shown in the last column. In each case, set the 5720A to standby
before changing to the next voltage settings and go back to operate before reading the
null detector.
6. Reverse the connections of the dc reference standard at the reference divider and
repeat the previous measurement process for the -0.1V, -1V and -10V outputs.
3-26
Calibration and Verification
Full Verification 3
3-16. DC Voltage One-Tenth Scale Linearity Test
Note
If the result of the previous test at 1V on the 11V range was less than
2.5 μV it is not necessary to perform this test.
This test uses the same equipment as the previous test. Proceed as follows to perform the
DC Voltage One-Tenth Scale Linearity Test:
1. Set the reference divider range to 10V. On the voltage reference standard, remove the
lead from the 10V high terminal and connect it under the binding post of the low
terminal along with the low lead to provide a 0V reference input to the reference
divider. Set the Calibrator output for 10V, then activate range lock for the 11V range.
Now set the Calibrator to 0V OPERATE.
2. Note the reading on the null detector. Press OFFSET on the Calibrator. Return the
lead on the voltage reference to the high output terminal.
3. Set the Calibrator to 10V. Use the Calibrator output adjustment knob to obtain the
reading previously noted on the null detector. Press SCALE on the Calibrator.
4. Set the Calibrator to 1V dc. Set the reference divider to the 1V range, and verify that
the null detector indicates less than 2.5 μV from the noted reading.
5. Press RESET on the Calibrator. This completes the DC Voltage Calibration
Verification testing.
3-27
5700A/5720A Series II Calibrator
Service Manual
3-17. Direct Current Accuracy Verification Test
Equipment required for the Direct Current Accuracy Verification Test is listed in Table
3-6. Proceed as follows to test accuracy of the dc current function:
Table 3-6. Equipment Required for Direct Current Test
Equipment Model
DC DMM, 6-1/2 digit Wavetek 1281 or HP 3458A
High-Current Shunt Fluke Y5020 (for 5725A only)
Resistance Standards L&N 4221B (0.1Ω at 2A)
Fluke 742A-1 (1Ω at 200 mA)
Fluke 742A-10 (10Ω at 20 mA)
Fluke 742A-1k (1 kΩ at 2 mA)
Fluke 742A-10k (10 kΩ at 200 μA)
Use Table 3-20 (5720A) and Table 3-21 (5700A) for the test records.
1. Connect the dc DMM to the Calibrator output and set the Calibrator for outputs of
200 mV, -200 mV, 2V, and -2V, and record the dc DMM reading at each voltage in
Table 3-20 or 3-21.
2. Refer to the resistance standard test report and enter the corrections for all the
certified values in ± ppm in column A on the test record.
Note
The STD RES CORRECTION is the difference between the nominal
standard resistor value and the certified or true resistor value. For
example, if the nominal value is 0.1Ω and the certified value is
0.0999963Ω, the difference equals 0.0000037Ω, or +37 ppm.
3. Connect the equipment as shown in Figure 3-8 using the L&N 0.1Ω resistor.
4. Set the Calibrator for a 2A dc output, and adjust the Calibrator using the output
adjustment knob to obtain the characterized voltage reading on the dc DMM. Wait 3
seconds, and record the Calibrator error display reading in ± ppm (Column B).
CALIBRATOR (UUT)
SHUNT
USE INTERNAL GUARD
DC DMM
OUTPUT SENSE
HI HI
INPUT
HI
LO LO
LO
GRD
GND
F3-7.EPS
Figure 3-7. Direct Current Accuracy Test Setup
3-28
Calibration and Verification
Full Verification 3
5. Algebraically add column B to column A. Enter the result on the test record. Verify
that it is within the test limits shown.
6. Repeat steps 2 through 5 using the Fluke 742A Resistance Standards and Calibrator
output currents shown in Tables 3-25 or 3-26.
7. If the Calibrator is attached to a 5725A Amplifier, connect the Y5020 high-current
shunt to the 5725A output terminals. Connect the dc DMM to the Y5020 high-current
shunt voltage output connector.
8. Set the Calibrator to 10A, -10A, 5A, 3A and -3A and record the dc DMM readings
on the 5725A Amplifier dc current test record. Divide these readings by the certified
value of the Y5020 high current shunt, record the resultant current and verify that it is
within the test limit shown.
3-18. AC Voltage Frequency Accuracy Test
This test requires the use of a frequency counter. Philips model PM6669 is
recommended. Use Table 3-22 for the test record. When using Philips Model PM 6666, it
is recommended to use a 1 MHz Low Pass Filter as shown in Figure 3-10. Refer to Table
3-15, Minimum Use Requirements, for substitution information.
1.59 kΩ Resister
Metal Film P/N 344341
10 pF PM6666
Calibrator Main
Capacitor Input A
Output Terminals
P/N 713875
Mount components on a duel banana adapter from ITT Pomona. Part Number 1837
F3-6A.EPS
Figure 3-8. 1 MHz Low Pass Filter
To check the Calibrator frequency accuracy, proceed as follows:
1. Connect the frequency counter to the output terminals of the Calibrator.
2. Set the Calibrator to 1V at the output frequencies listed in Table 3-22. Verify that the
counter reads within the limits shown on the test record.
3. Disconnect the counter from the Calibrator.
3-19. Output Level Tests For AC V Ranges
This test requires the use of equipment listed in Table 3-7.
Table 3-7. Equipment Required for AC V Output Level Tests
Equipment Model
AC Measurement Standard Fluke 5790A
BNC(F) to Dual-Banana Plug Adapter (2 required) Pomona 1269
Coax Cable - RG-58A/U or RG-58C/U with BNC(M)
Connectors, 12 ± 1 inch Long
3-29
5700A/5720A Series II Calibrator
Service Manual
Use Table 3-23 (5720A) or Table 3-24 (5700A) for the test records.
1. Place the 5790A on top of the Calibrator and connect the equipment as shown in
Figure 3-9.
Note
The point of measurement is at the end of the cable and adapter that
connects to the 5790A. Other cable lengths and adapters will yield different
results at high frequencies.
2. On the 5790A push UTIL MENUS button and then the MEAS CONTROL softkey.
Set the digital filter mode to FAST and the restart to MEDIUM. Push the DONE soft
key twice to return to the measurement display.
3. Set the 5790A to 2 mV at 1 kHz. Adjust the Calibrator using the output adjustment
knob for a reading of 2.0000 mV ±1 count on the 5790A. Record the Calibrator error
display reading in the 90 Day column in Table 3-23 (5720A) or 3-24 (5700A) as
appropriate for the verification interval.
4. Verify that the result is within the test limits.
5. Repeat the previous steps for the 2 mV output on all remaining frequencies on the
test record.
6. Proceed to the remaining output levels and frequencies list in Table 3-23 or 3-24 and
repeat steps 3 through 5 using the appropriate output level in each step, and the
adjustment tolerance in Table 3-8.
BNC to
Banana Adapter
5790A Side View
HI
Input 2
12 Inch LO
Coax Cable
BNC to
Banana Adapter
Calibrator Side View
HI
Output
LO
F3-6.EPS
Figure 3-9. AC Voltage Test Setup
3-30
Calibration and Verification
Full Verification 3
Table 3-8. 5790A Adjustment Counts
5700A/5720A Series II Output 5790A Display 5790A Adjustment Counts*
Level
2 mV 2.0000 ±1
20 mV 20.0000 ±1
200 mV 200.0000 ±4
2V 2.000000 ±4
2.3V 2.30000 ±1
20V 20.00000 ±4
200V 200.0000 ±4
300V 300.000 ±1
600V 600.000 ±2
1000V 1000.000 ±2
*Adjustment counts of 3 times the listed value is allowed at 1 MHz
3-20. AC Current Test, 22 mA to 11A Ranges
This test requires the use of equipment listed in Table 3-9, when using the 5790A Input 1.
Use Tables 3-33 (5720A) or 3-34 (5700A) for a test record.
Table 3-9. Equipment Required for 22 mA to 11A Alternating Current Test Using the 5790A Input 1
Equipment Model or Description
AC Measurement standard Fluke 5790A
Current Shunts Fluke A40 Series: 20 mA, 200 mA, 2A, and A40A Series: 10A (if verifying a
5725A) , with AC-DC difference corrections.
Current Shunt Adapter Fluke 792A-7004 A40 current shunt adapter
Cable Pomona 1368-A-18. Double banana to single banana plugs.
Cable (For 10A Setup) Pomona 5268-C-12. BNC(M) to single banana plugs.
Cable (For 10A Setup) Fluke A45-4003 (PN 212853) UHF(M) to UHF(M) with RG8A/U cable
Adapter (For 10A Setup) Pomona Model 1707. UHF(F) to banana adapter.
Adapter (For 10A Setup) Kings KC-99-34 UHF(M) to BNC(F)
Adapter (For 10A Setup) Pomona Model 1707. UHF(F) to banana adapter.
3-31
5700A/5720A Series II Calibrator
Service Manual
1. Connect the equipment as shown in Figure 3-10(A) use the 2A shunt.
2. Enter the ac to dc difference corrections for each shunt at each frequency in the
appropriate column of the test record (Table 3-26 or 3-27).
3. Set the Calibrator for a +2A dc output. Adjust the output so that the error display is
equal to the UUT actual error for a +2A output, as shown on the dc current test
record in Table 3-20 (5720A) or Table 3-21 (5700A).
4. Push the INPUT 1 button on the 5790A if you are using the INPUT 1 setup, or the
SHUNT button if you are using the SHUNT set up. Let the 5790A settle on a
reading.
5. Push the SET REF soft key on the 5790A.
6. Set the Calibrator for a -2A dc output. Adjust the output so that the error display is
equal to the UUT actual error for a -2A output, as shown in Table 3-20 (5720A) or
Table 3-21 (5700A).
7. Press the AVG REF soft key on the 5790A after the 5790A reading settles.
8. Set the Calibrator to 2A at 40 Hz and OPERATE.
9. Record the error displayed on the 5790A in Table 3-26 or 3-27.
10. Return to the error corrected +2A DC output that was set in step 3 and verify that the
5790A display returns to a zero reading ±10 PPM. If necessary, repeat steps 3
through 9 until the required results are obtained.
11. Algebraically add the 5790A error display reading to the A40 Shunt ac to dc
difference, and verify that the result is within the specifications of the test limits.
Record the results on Table 3-26 (5720A) or Table 3-27 (5700A).
12. Change the Calibrator frequency to 1 kHz, 5 kHz and 10 kHz. At each frequency
record the 5790A error display. Verify the results as was done in steps 8 and 9.
13. Repeat steps 3 through 12 at currents of 200 mA and 20 mA using the appropriate
A40 current shunt at the frequencies shown on the test record (Table 3-26 or 3-27).
14. For units with a 5725A Amplifier attached, use the test set up shown in Figure
3-10(B) using the 10A shunt at the frequencies listed on the test record.
3-32
Calibration and Verification
Full Verification 3
Note
When verifying the 5725A Amplifier at the 10A level, allow sufficient time
for the A40A-10 shunt to reach thermal stability after initially applying the
current.
A40 Current Shunt
Red
5790A Pomona Cable Calibrator (UUT)
1368-A-18
Hi
Input 1
Lo
Black
792A-7004
A40 Current Shunt Adapter
A. Alternating Current Test Setup, 22 mA to 2A Using 5790A Input 1
Calibrator (UUT)
A40A 10A
Pomona Cable
Current Shunt
5268-C-12
Red
5790A 5725A (UUT)
Hi
Input 1
Lo
Black
792A-7004
FLUKE A45-4003
A40 Current
P/N 212852
Shunt Adapter
Cable
UHF(M) to BNC(F) Pomona Model 1707
Adapter UHF(F) to Banana
Kings KC-99-34 Adapter
B. Alternating Current Test Setup, 10A Using 5790A Input 1
F3-8A.EPS
Figure 3-10. Alternating Current Test Setup
3-33
5700A/5720A Series II Calibrator
Service Manual
3-21. AC Current Test, 2 mA and 200 μA Ranges
The equipment required for the alternating current accuracy verification test for the 2 mA
and 200 μA ranges is listed in Table 3-10. Use Table 3-28 (5720A) or 3-29 (5700A0 for
the test record.
Table 3-10. Equipment Required for Alternating Current Accuracy Test for the 2 mA and 200 μA
Ranges
Equipment Model or Description
AC Measurement Standard Fluke 5790A
Metal Film Resistor 200Ω, 1/8w, ±1%, T9 (P/N 309724) mounted on a dual banana plug.
Metal Film Resistor 2 kΩ, 1/8w, ±1%, T9 (PN 335422) mounted on a dual banana plug
Cable Pomona 1368-A-18. Double banana to single banana plugs.
1. Connect the equipment as shown in Figure 3-11.
Metal Film Resistor
Mounted on Dual
Banana Plug
Calibrator (UUT) 5790A
Hi Hi
200
Output Input 2
Ω
Lo Lo
Pomona Cable
1362-A-18
F3-9.EPS
Figure 3-11. Alternating Current Test Setup 2 mA and 200 μA
Note
An explanation of the rationale for using metal film resistors to measure
ac current follows this procedure.
2. Set the Calibrator for precisely +2 mA dc using the correction from previously
recorded data, i.e. set the Calibrator error display to the value recorded for +2 mA dc
(Table 3-9 or 3-11).
3. When the 5790A settles on a reading, push the SET REF soft key on the 5790A.
4. Set the Calibrator for precisely -2 mA dc output using the correction from previously
recorded data, i.e., set the Calibrator error display to the value recorded for -2 mA dc,
in Table 3-10.
5. Press the AVG REF soft key on the 5790A after the 5790A reading settles.
6. Set the Calibrator to 2 mA at 10 Hz and OPERATE.
7. Record the error displayed on the 5790A in Table 3-28 or 3-29, and verify results are
within spec.
8. Return to the error corrected +2 mA DC output that was set in step 2. Verify that the
5790A display returns to a zero reading ±10 PPM. If necessary, repeat steps 2
through 6 until the required results are obtained.
3-34
Calibration and Verification
Full Verification 3
9. Change the Calibrator frequency to 20 Hz, 40 Hz, 1 kHz, 5 kHz and 10 kHz. At each
frequency record the error display on the 5790A in Table 3-28 or 3-29. Verify that
the results are within limits shown.
10. Repeat steps 2 through 9, but replace the 200Ω metal film resistor with the 2 kΩ
resistor, and use 200 μA instead of 2 mA.
3-22. Rationale for Using Metal-Film Resistors to Measure AC Current
To be able to measure alternating current, a system comprised of a suitable ac shunt and
ac detector is required. First let us consider the ac shunt. For this example we will use a 2
kΩ metal film resistor. At frequencies up to 10 kHz, the equivalent circuit of the resistor
can be illustrated as in Figure 3-12. Values typical for shunt capacitance and series
inductance are 2 pF (Cs) and 0.01 μH (Ls). For comparison, wire has approximately 0.02
μH/inch. At 10 kHz, the reactance of Cshunt is 8 MΩ, and the reactance of Lseries is 0.6
mΩ. The formulae to use are:
C
SHUNT
L
SERIES
R
F3-10.EPS
Figure 3-12. Metal Film Resistor Equivalent Circuit
2 2 2
(1/Z) = (1/R) + (1/XC) (1)
2 2 2
(Z) = (R) + (XL) (2)
Where R = resistance Xc = Capacitive Reactance
Z = network impedance XL = Inductive Reactance
We can see that these effects can be ignored, because their contribution to errors in the
measurement process is less than 1 ppm. That is, the metal film resistor's self reactance is
totally dwarfed by the reactance of the measuring circuit, which is overwhelmingly
capacitive.
If a detector as shown in Figure 3-13 has an input impedance of 10 MΩ shunted by 123
pF, then the effects of Xc must be accounted for. We can ignore the net resistance change
introduced by the 10 MΩ detector resistance.
R
SHUNT
UUT DET.
F3-11.EPS
Figure 3-13. Metal Film Resistor in Test Circuit
3-35
5700A/5720A Series II Calibrator
Service Manual
Note
The input impedance at INPUT 2 of the 5790A on the millivolt ranges is 10
MΩ shunted by 83 pF and the cable used to connect the shunt resistor to
the 5790A has 40 pF capacitance, for a total of 123 pF.
The reactance of 123 pF at 10 kHz is 129 kΩ, and using formula (1), in the case where
R=2 kΩ, the network impedance Z = 1.999760 kΩ. This produces an error of 120 PPM.
The allowable error at 10 kHz is reduced to account for this error.
Using formula (2) we get a result of Xc = 88 kΩ, and a network impedance of Z = 1.9995
kΩ. This produces an error of approximately 250 ppm, or 0.025%. However, if we are
making a measurement of 0.21% uncertainty (as in the present case), the ratio of
measurement uncertainty is about 10:1 and is not of concern. It is easy to improve
measurement uncertainty if desired, though, by measuring the actual input capacitance of
the detector and any stray capacitance from input leads, etc. and making corrections. In
this discussion, the UUT is assumed to be a high-impedance current source (like the
5700A), which can easily be verified by the manufacturer's specifications, i.e., a specified
voltage adder for current outputs above a given burden voltage.
3-23. Wideband Frequency Accuracy Test
Use Table 3-30 for the test record. Proceed as follows to test the Wideband module
frequency accuracy:
1. Connect the Philips PM 6669 to the Calibrator wideband output and measure the
output frequency at the frequencies listed in Table 3-30.
2. Verify that the frequency counter indicates frequencies within the 0.01% limits
shown.
3-24. Wideband AC Voltage Module Output Verification
The wideband tests are for units with the Option 5700A-03 Wideband AC Module only.
The verification test for the wideband module works as follows:
• Accuracy at 1 kHz: Output at 1 kHz is tested by comparing the wideband output at
the end of the cable and termination supplied with the instrument to the 5790A at
INPUT 2.
• Attenuator flatness: The attenuator flatness is tested using the 5790A wideband input
and using reduced spec limits when the TUR (Test Uncertainty Ratio) is less than
4:1.
Table 3-11 lists the equipment required for testing and calibrating the Wideband module.
3-36
Calibration and Verification
Wideband Output Accuracy at 1 kHz Test 3
Table 3-11. Equipment Required for Testing and Calibrating the Wideband Option
Equipment Model or Description
AC Measurement Standard Fluke 5790A with Wideband Option -03
Wideband cable Supplied with 5700A-03
50Ω Termination Supplied with 5700A-03
Adapter Pomona 1269 BNC(F) to dual banana plug.
Adapter Kings KN-99-46 N(F) to BNC(M)
3-25. Wideband Output Accuracy at 1 kHz Test
This test verifies the Wideband output level at 1 kHz by direct measurement with the
5790A at INPUT 2. Use Table 3-31 for a test record.
Proceed as follows to characterize the rms wideband voltmeter at 1 kHz:
1. Connect the equipment as shown in Figure 3-14.
BNC(F) to Banana Adapter
Calibrator (UUT) 5790A
Wideband
Output Cable
Input 2
Wideband
Output
50Ω Termination
N(F) to BNC(M) Adapter
F3-12.EPS
Figure 3-14. Wideband Accuracy at 1 kHz Test Setup
2. Set the Calibrator wideband output to 2.1V at 1 kHz and the 5790A to read INPUT 2.
3. Push the 2.2V RANGE button on the 5790A to lock it on the 2.2V range.
4. On the 5790A push UTIL MENUS button and then MEAS CONTROL soft key. Set
the digital filter mode to FAST and the restart to MEDIUM. Push the DONE soft key
twice to return to the measurement display.
5. Use the Calibrator output adjustment knob to obtain a reading on the 5790A
measurement display of 2.100000 ±20 counts.
6. Read the error on the Calibrator display and record it in Table 3-32 for the 2.1V level
for the appropriate verification internal. Verify that it is within spec limits shown.
7. Push the soft key under the RANGE display on the 5790A to return to AUTO
RANGE.
8. Proceed to the remaining levels shown in Table 3-32 and repeat steps 5 through 7
with the appropriate output levels set in each step, using the adjustment tolerance in
Table 3-12 in step 5.
3-37
5700A/5720A Series II Calibrator
Service Manual
Table 3-12. Wideband Adjustment Tolerance
5700A/5720A Series II Wideband 5790A Adjustment Counts
Output ± ppm
2.10000V 20
1.00000V 10
300.000 mV 3
100.000 mV 10
30.0000 mV 3
10.0000 mV 1
3.00000 mV 1
1000.00 μV 1
3-26. Wideband Output Flatness Test
Use Table 3-32 as a test record. To perform wideband output flatness test, proceed as
follows:
1. Connect the equipment as shown in Figure 3-15. Note that the Calibrator wideband
cable is connected to the 5790A directly, the termination is not used.
Calibrator (UUT) 5790A
Wideband
Output Cable
Wideband Wideband
Output Input
F3-13.EPS
Figure 3-15. Wideband Flatness Test Setup
2. Set the wideband output to 3V at 1 kHz.
3. Push the WBND button on the 5790A, when the reading has settled, push the SET
REF soft key.
4. Set the Calibrator to frequencies shown in Table 3-32 for the 3V output and record
the errors on the 5790A error display at each frequency in Table 3-32.
5. Verify that the error readings are within spec limits or reduced spec limits shown on
the test record. Reduced spec limits are used when the TUR (Test Uncertainty Ratio)
is less than 4:1.
6. Repeat steps 4 and 5 for the remaining output levels shown in Table 3-32 using the
appropriate voltage in step 4.
7. Record the 1 kHz absolute errors at each output level from Table 3-32 into the
appropriate column in Table 3-33. Record the flatness errors from Table 3-32 for
each output level and frequency into the appropriate column in Table 3-33. Add the
errors and verify that they are within spec for the appropriate time internal.
3-38
Calibration and Verification
Wideband Output Flatness Test 3
3-27. Wideband Flatness Calibration Procedure
This procedure is the only part of full verification that stores calibration constants in the
Calibrator. This is not a verification test, it is a calibration procedure. Because this part of
calibration is recommended to be done only every two years, the same interval as full
verification, it is included here and not under Calibration earlier in this chapter and in
Chapter 7 of the 5700A/5720A Series II Operator Manual.
Proceed as follows to perform wideband flatness calibration:
1. Connect the equipment as shown in Figure 3-10 and set the rear panel
CALIBRATION switch to the ENABLE position.
2. Push the WBND button on the 5790A.
3. Call up the wideband flatness calibration routine on the Calibrator front panel, by
pressing the softkey sequence SETUP MENUS, CAL, CALIBRATION and
WIDEBAND FLAT.
4. Enter the present ambient air temperature as prompted and press ENTER.
5. Place the Calibrator in OPERATE. Wideband flatness calibration starts with a 3V
output at 1 kHz.
6. Push the SET REF soft key on the 5790A when the 5790A settles to a reading. This
is the 3V reference value from which all other frequencies will be compared.
7. Push the ENTER button on the Calibrator, and, the frequency will advance to the
next value.
8. Adjust the Calibrator output adjustment knob to bring the 5790A error display to 0
and press ENTER on the Calibrator. Repeat this step for each frequency through 30
MHz.
9. Push the CLEAR REF WBND soft key on the 5790A. The Calibrator wideband
output changes to 1V at 1 kHz.
10. Push the SET REF soft key on the 5790A when the 5790A settles to a reading,. This
is the 1V reference value from which all other frequencies will be compared.
11. Repeat steps 7 and 8 above for each frequency through 30 MHz.
12. Push the CLEAR REF WBND soft key on the 5790A. The Calibrator Wideband
output changes to 300 mV at 1 kHz.
13. Push the SET REF soft key on the 5790A when the 5790A settles to a reading. This
is the 300 mV reference value from which all other frequencies will be compared.
14. Repeat steps 7 and 8 above for each frequency through 30 MHz.
15. Push the CLEAR REF WBND soft key on the 5790A. The 5790A wideband output
changes to 100 mV at 1 kHz.
16. Push the SET REF soft key on the 5790A when the 5790A settles to a reading. This
is the 100 mV reference value from which all other frequencies will be compared.
17. Repeat steps 7 and 8 above for each frequency through 30 MHz. Only the 10 MHz,
20 MHz and 30 MHz points are adjusted.
18. Push the CLEAR REF WBND soft key on the 5790A. The 5790A wideband output
changes to 30 mV at 1 kHz.
19. Push the SET REF soft key on the 5790A when the 5790A settles to a reading. This
is the 30 mV reference value from which all other frequencies will be compared.
20. Repeat steps 7 and 8 above for each frequency through 30 MHz.
3-39
5700A/5720A Series II Calibrator
Service Manual
21. Push the CLEAR REF WBND soft key on the 5790A. The 5790A wideband output
changes to 10 mV at 1 kHz.
22. Push the SET REF soft key on the 5790A when the 5790A settles to a reading. This
is the 10 mV reference value from which all other frequencies will be compared.
23. Repeat steps 7 and 8 above for each frequency through 30 MHz. Only the 10 MHz,
20 MHz and 30 MHz points are adjusted.
24. Make sure the rear panel CALIBRATION switch is in the ENABLE position. Store
the cal constants by pushing the STORE VALUES softkey. When the display returns
to normal, set the rear panel CALIBRATION switch to NORMAL. The Calibrator
wideband flatness calibration is now complete.
3-28. Optional Tests
These tests may be used in acceptance testing or following repair likely to affect the
characteristics tested here. They are not recommended to be done routinely. If the
Calibrator passes Calibration Performance Verification, you do not need to perform these
tests; verification either exercises these functions or is subject to their effects. The
Optional Tests include such checks as load regulation, noise, and distortion. Equipment
required for the optional tests is listed in Table 3-13.
Table 3-13. Equipment Required For DC V Optional Tests
Equipment Model
DMM Wavetek 1281 or HP 3458A
RMS Differential Voltmeter Fluke 5790A
Power Decade Resistor Clarostat 240C
Differential Amplifier Plug-In Tektronix 7A22
Oscilloscope Mainframe Tektronix 7000 Series
DC Voltage Reference Standard Fluke 732B
Reference Divider Fluke 752A
Null Detector EM Electronics N11(Fluke 845A)
Kelvin-Varley Divider Fluke 720A
3-29. DC Voltage Load Regulation Test
Use Table 3-34 for a test record. Proceed as follows to test the dc voltage load regulation:
1. Ensure the Calibrator is in standby. With the test setup of Figure 3-5, connect the
power decade resistor across the Calibrator OUTPUT terminals. Connect two
shorting links between the Calibrator SENSE and OUTPUT terminals and select
external sense (EX SNS indicator lit).
2. Set the reference divider to 10V. Set the Calibrator output to 10V dc. Set the power
decade resistor to 199Ω. Set the Calibrator to operate. Adjust the Calibrator as
necessary to obtain a null on the null detector. Rotate the most significant dial on the
power decade resistor to 9. Verify that the null detector indication changes less than
±2 μV. Set the Calibrator to standby.
3-40
Calibration and Verification
Optional Tests 3
3. Repeat load regulation testing at the remaining Calibrator outputs shown in Table
3-47.
4. Set the Calibrator to standby and disconnect all equipment from the Calibrator.
3-30. DC Voltage Linearity Test
Use Table 3-35 for a test record. Proceed as follows to test the dc voltage linearity:
1. Self calibrate the Kelvin-Varley (KV) divider as called for in its service manual.
2. Connect the equipment as shown in Figure 3-16.
NULL DETECTOR
HI
LO GND*
GRD
732B
720A CALIBRATOR (UUT)
10V
INPUT OUTPUT OUTPUT SENSE
HI
HI HI HI HI
LO
LO LO LO LO
GRD GND GND
GND
GRD
*NOTE: IF THE NULL DETECTOR IS NOT GROUNDED THROUGH
POWER LINE, CONNECT ITS GROUND TERMINAL
TO THE GROUND TERMINAL ONTHE 5700A.
F3-14.EPS
Figure 3-16. DC Voltage Linearity Test
3. Set the KV dials to zero by using the RANGE LOCK. Set the Calibrator to 0V on the
11V range operate. Note the null detector reading. Press OFFSET on the Calibrator.
4. Set KV dials to 0.999999X and Calibrator for a 10V output.
5. Use the Calibrator output adjustment to obtain a null detector reading equal to the
reading noted in step 3. Press SCALE on the Calibrator.
6. For each of the KV settings tabulated in Table 3-36, make the required Kelvin Varley
setting, and verify that the null detector reads within the limits shown.
3-31. DC Voltage Output Noise (10 Hz to 10 kHz) Test
Use Table 3-36 for a test record. Proceed as follows to test the dc voltage output noise
that falls in the range 10 Hz to 10 kHz:
1. Connect the equipment as shown in Figure 3-17.
3-41
5700A/5720A Series II Calibrator
Service Manual
CALIBRATOR OSCILLOSCOPE TRUE RMS
MAINFRAME*
VOLTMETER
(UUT)
7A22
VERTICAL
PLUG-IN
HI
LO
OUTPUT
GRD GND
COAX
SHIELDED
TWISTED PAIR
CLIP LEADS
3' APPROX
BNC
GR BANANA PLUGS
* OSCILLOSCOPE AND AC DIFFERENTIAL
SHIELDED TWISTED PAIR CABLE DETAIL
VOLTMETER SHOULD BE ISOLATED FROM
THE POWER LINE GROUND.
F3-15.EPS
Figure 3-17. DC Voltage Output Noise Test Setup
2. Set the Oscilloscope Differential Amplifier controls as shown below.
Low Frequency -3 dB 10 Hz
High Frequency -3 dB 10 kHz
Input Coupling AC (both inputs)
Volts/Div 50 μV (Var. to Cal.)
3. Set the Oscilloscope Time/Div for 2 ms.
4. Set the rms voltmeter range to 1V.
5. Set the Calibrator to 2.2V dc, operate. Verify that the reading on the rms voltmeter is
less than 150 mV.
NOTE
This test assumes that the amplifier plug-in and scope have a gain equal
4
to 0.5V divided by the input/div. setting, which in the above case is 1x10 .
6. Repeat the above process for the remaining tabulated settings shown in Table
3-49; verify that the rms meter indicates less than the amount shown for each
required output level.
7. Press RESET on the Calibrator and disconnect the test configuration.
3-42
OUTPUT
SENSE
Calibration and Verification
Optional Tests 3
3-32. DC Voltage Output Noise (0.1 to 10 Hz) Test
Proceed as follows to test for dc voltage output noise in the range 0.1 to 10 Hz:
1. Place the 8520A DMM into Math Program 8 with the Display Option Register set to
register 8.3 (Standard Deviation Computed Variable)as follows:
a. Press SHIFT, 8, and PROGRAM SELECTION. Then press SHIFT, 0, ., 1,
PROGRAM SELECTION, 8, ., 3, PROGRAM DATA.
b. Set the DMM to 200 mV DC Range, 20 Samples/Second, and 1000 ms Filter.
c. Set PROGRAMS IN USE to the ON position.
2. Lock the Calibrator in the 22V range and set it to 100 mV dc. Place the Calibrator in
operate.
3. Connect the DMM to the Calibrator OUTPUT binding posts and press the DMM
reset button once. Verify that after 10 seconds the DMM reads less than 0.0010E-3.
4. Lock the Calibrator in the 220V range and set it to 100 mV dc. Place the Calibrator in
operate.
5. Press the DMM reset button once. Verify that after 10 seconds the DMM reads less
than 0.0100E-3.
6. Set the Calibrator to standby.
3-33. AC Voltage Distortion Test
Equipment required for these tests is listed in Table 3-14. Proceed as follows to test for
distortion in the ac voltage function. Use Table 3-37 for test record.
Table 3-14. Equipment Required for Distortion Test
Equipment Model
DMM Wavetek 1281 or HP 3458A
Distortion Analyzer Krohn-Hite 6900B
Spectrum Analyzer (only for 5700A-03) HP 8590A
Non-wirewound load resistors Any (see *Table 3-50 for values)
1. Connect the Calibrator output terminals to the distortion analyzer.
2. Measure the Calibrator distortion at the output voltages and frequencies tabulated in
Table 3-37. Verify that the distortion measured is within the limits shown.
WXWarning
A non-reactive voltage divider may be necessary to scale the
test voltages to match the distortion analyzer characteristics.
3-34. Wideband Distortion Testing
Proceed as follows to test for distortion in the wideband output function (for units with
the Option 5700A-03 Wideband AC Module only).
1. Connect the Wideband output terminated in 50Ω to the spectrum analyzer input.
3-43
5700A/5720A Series II Calibrator
Service Manual
Note
If the spectrum analyzer input impedance is 50Ω, do not use a separate
termination.
2. With 0 dBm output programmed from the Calibrator wideband output, select
frequencies over the band of 1 MHz to 30 MHz and verify that use the spectrum
analyzer to verify that any harmonics are below -40 dBm for fundamentals up to 10
MHz and below -34 dBm for fundamentals of 10 MHz and above.
3. Disconnect the equipment from the Calibrator.
3-35. AC Voltage Overshoot Test
Proceed as follows to test for ac voltage overshoot:
1. Connect the Calibrator output to a properly compensated 10:1 probe.
2. AC couple the oscilloscope and set the sweeptime to a fairly low sweeptime
(approximately 1 sec/div).
3. Set the Calibrator to 7.07V at 1 kHz, and press OPR/STBY.
4. Set the scope vertical sensitivity for 0.05V/div. Offset the trace vertically until you
can see the top of the waveform at the approximate center of the display (must be at
least 2-3 divisions down from the top of the scope graticule).
5. Set the Calibrator to standby and then back to operate. Verify that any overshoot
visible on the oscilloscope display is less than 1.5 divisions (approximately 10% of
the peak value).
6. Repeat the test at 100 Hz and 100 kHz. This completes the Optional Tests.
3-36. Minimum Use Requirements
Table 3-15 defines specifications for test equipment needed for tests in this section of the
manual. If the specific test equipment called for in these tests is not available, you can
substitute equipment that meets these specifications.
3-44
Calibration and Verification
Minimum Use Requirements 3
Table 3-15. Minimum Use Requirements
Item Recommended
Description Minimum Use Specifications
No. Equipment
Calibration Equipment
1. Voltage Reference Fluke 732B
10V nominal, true value certified to within
±1.5 ppm
2. Resistance Standards Fluke 742A Series, 1Ω
1Ω nominal, true value certified to within 10
and 10 kΩ
ppm, 10 kΩ nominal, true value certified to
within 4 ppm
Calibration Verification Equipment
3. Reference Voltage Fluke 752A
Range uncertainty 100:1, 1 kV input, ±0.5
Divider
ppm 10:1 100V input ±0.2 ppm
12
4. Null Detector EM Electronics N11
Leakage resistance to case: 10 Ω min.
(Fluke 845A)
Resolution: 3 μV full scale
5. Low Thermal EMF Fluke 5440A-7002
Plug-in. Copper or gold-flashed copper (two
Cables
cables per set, two sets required).
Fluke 5440A-7003
Spade lug. Copper or gold-flashed copper
(two cables per set, two sets required).
6. Digital Multimeter Fluke 8508A
DC Voltage Range: 0.1 to 10V Resolution
and short-term stability: ±2 ppm Resistance
range: 1Ω to 10 MΩ Resolution and short-
term stability :±20 uΩ at 1Ω, 1.9Ω ±5 ppm at
10Ω, 19Ω ±2 ppm at 100Ω to 1.9 MΩ ±4
ppm at 10 MΩ, 19 MΩ
7. Current Source Fluke 55X0A,
Range: 10 mA and 100 mA Typical short-
5700A/5720A Series II,
term stability ±15 ppm for 5 minutes
8. AC Measurement Fluke 5790A (Option -03
Ranges: 2.2 mV through 1000V AC
Standard required for Wideband
Frequency: 10 Hz to 1 MHz
Flatness Verification)
24 to 7500 ppm, depending on amplitude
and frequency (see Table 3-9.)
Wideband Ranges: 2.2 mV through 7V
Frequency: 10 Hz to 30 MHz
Uncertainty: 0.03% to 0.9%, depending on
amplitude and frequency (see Table 3-18.)
3-45
5700A/5720A Series II Calibrator
Service Manual
Table 3-15. Minimum Use Requirements (cont)
Item Recommended
Description Minimum Use Specifications
No. Equipment
9. Current Shunt Adapter Fluke 792A-7004
Used in conjunction with 5790A and A40-
series shunts to facilitate AC Current
measurements
10. Frequency Counter Philips PM 6669
10 Hz to 30 MHz ±0.002%
11. Standard Resistors (1) Fluke 742A-1
0.1Ω nominal, true value certified to within
Fluke 742A-1.9
20 ppm, rated for 2A DC; 1Ω nominal, true
Fluke 742A-10
value certified to within 6 ppm; 1.9Ω
Fluke 742A-1k
nominal, true value certified to within 6 ppm;
Fluke 742A-10k
10Ω nominal, true value certified to within 6
Fluke 742A-19k
ppm; 1 kΩ nominal, true value certified to
Fluke 742A-10M
within 5.5 ppm; 10 kΩ nominal, true value
Fluke 742A-19M
certified to within 3.5 ppm; 19 kΩ nominal,
L&N 4221B (0.1Ω)
true value certified to within 4 ppm; 10 MΩ
nominal, true value certified to within 15
ppm; 19 MΩ nominal, true value certified to
within 28 ppm
12. DC Current Shunt (2) Fluke Y5020
Range: 10A
Uncertainty: ±0.008%
13. AC/DC Current Shunt Fluke A40-20 mA
Ranges: 20 mA, 200 mA, 2A and 10A
Fluke A40-200 mA
Frequency: 10 Hz to 10 kHz
Fluke A40-2A
Uncertainty: ±310 ppm at 10 Hz; ±100 ppm
Fluke A40A-10A (2)
at 20 Hz; ±50 ppm at 40 Hz, 1 kHz; ±100
ppm at 5 kHz, 10 kHz
14. Metal Film Resistors Stock Items
Values: 200Ω, 2 kΩ, and 1 MΩ Temperature
C°: T9 or better Power Rating: 1/4 Watt
Tolerance: ±1%
15. Differential Amplifier Sensitivity: 5 μV rms Bandwidth selectable Tektronix 7A22 w/7000-
to 10 kHz Series Mainframe
16. Distortion Analyzer Krohn-Hite 6900B
Range: 2V to 300V
Frequency: 10 Hz to 600 kHz
17. Kelvin-Varley Voltage Ratio uncertainty: ±0.1 ppm of input Fluke 720A
Divider
18. HF Spectrum Analyzer Freq. Range: 2 MHz to 120 MHz Input HP 8590A
(used in optional test Level: 3V (+20 dBm to -60 dBm)
for wideband
distortion)
1: A DMM may be used for all but the 1Ω and 1.9Ω values. For those values using the DMM, a test method
using an external current source is used for low-value resistance.
2: Needed only for 5725A Amplifier testing.
3-37. Determining Test Limits for Other Calibration Intervals
The verification procedures in this chapter test to the 90 day 99% confidence
specification limits. For other calibration intervals it is necessary to calculate new
specification limits and, if necessary, new test limits.
The following examples show how the 90 day limits were calculated. These examples
illustrate how you can calculate the specifications and test limits, if necessary, for other
calibration intervals.
3-46
Calibration and Verification
Determining Test Limits for Other Calibration Intervals 3
Example 1 shows you how to calculate a specification limit for a specific test level from a
specification listed as a percentage (or parts per million) of reading plus a floor error in
microvolts, millivolts, miroamps, or nanoamps.
The 99% confidence specification for a 5720A at 2 mA, 1 kHz is 130 ppm + 40 nA. We
can convert the floor uncertainty of 40 nA to ppm of output by dividing 40 nA by 2 mA
and multiplying by a million:
(130 + 1000000*0.000000040/0.002)=130 ppm + 20 ppm = 150 ppm
This test limit is shown in Table 3-28.
If we wanted to test to the 1 year specification of 140 ppm + 40 nA, the test limit would
be the specification of 140 ppm + 40 nA = 140 ppm + 40 ppm = 180 ppm.
Example 2 shows you how to calculate a specification limit and a tighter test limit. For
instrumentation that have the precision of the 5720A/5700A Series II calibrators, it is
difficult obtain standards which are many times more accurate than the calibrator
specifications. Therefore, for cases when the test uncertainty ratio (TUR) of the
standards is less than 4:1, guardbanding is used to set test limits which are tighter than the
specification limits. These limits provide the same risk of accepting out of tolerance
instruments as a TUR of 4:1. The statistical analysis of the guardbanding techniques used
are described in a series of technical papers referenced at the end of this chapter.
Guardbanding is used to set the test limits different than the specification limits for a
5720A at 2V, 1 kHz. The 90 day specification is 47 ppm + 10 uV. When you calculate
the specification in ppm at the 2V level in the same way as in Example 1, the
specification limit is:
(47 + 1000000*0.000010/2)=47 ppm + 5 ppm = 52 ppm.
99% Confidence Guardband Factors
1.000
0.950
0.900
0.850
0.800
0.750
1.00 1.50 2.00 2.50 3.00 3.50 4.00
Test Uncertainty Ratio
CHART.EPS
Figure 3-18. Determining Other Test Limits
3-47
Guardband Factor (K)
Table 3-16. 5720A Resistance Test Record
1Ω Std Res 1Ω Std Measured Cal UUT 1Ω UUT 1Ω UUT UUT Uncert Spec TUR GB Test Max
Value Voltage 1Ω Std Current Displayed Voltage True Dev. Std (±ppm) Factor Limit Difference of
Voltage Value Res (±ppm) Charactized to
Nominal Value
5.9 95 16.06 1.000 95 0.9995 to 1.0005
1.9Ω Std 1.9Ω Std Measured Cal UUT 1.9Ω UUT UUT UUT Spec Max
Res Value Voltage 1.9Ω Std Current Displayed 1.9Ω True Dev. (±ppm) Difference of
Voltage Value Voltage Res Characterized to
Nominal Value
5.9 95 16.06 1.000 95 1.89905 to
1.90095
10Ω Std 10Ω Std Measured Cal UUT 10Ω UUT UUT UUT Spec Max
Res Value Voltage 10Ω Std Current Displayed 10Ω True Dev. (±ppm) Difference of
Voltage Value Voltage Res Characterized to
Nominal Value
5.9 25 4.23 1.000 25 9.997 to 10.004
Resistance Accuracy Verification (19Ω And Above)
Std DMM Std DMM DMM UUT True UUT Dev. Uncert Spec TUR GB Test Max
Res Res Rdg Error UUT Res Res Value Std (±ppm) Factor Limit Difference of
Value Value (±ppm) Characterized to
Nominal Value
19Ω (1) 25 18.9943 to 19.0057
100Ω (1) 5.1 11 2.16 0.970 10.7 99.985 to 100.015
190Ω (1) 11 189.9715 to 190.0285
1 kΩ (1) 4.7 9 1.91 0.926 8.3 999.85 to 1000.15
1.9 kΩ (1) 9 1.899715k to 1.900285k
10 kΩ 3.1 9 2.92 0.978 8.8 9.9985k to 10.0015k
19 kΩ 3.5 9 2.55 0.963 8.7 18.99715k to 19.00285k
100 kΩ(1) 5.1 11 2.15 0.942 10.4 99.985k to 100.015k
190 kΩ (1) 11 189.9715k to 190.0285k
1 MΩ (1) 8.1 18 2.23 0.948 17.1 0.9998M to 1.0002M
3-48
Table 3-16. 5720A Resistance Test Record (cont)
Std DMM Std DMM DMM UUT True UUT Dev. Uncert Spec TUR GB Test Max
Res Res Rdg Error UUT Res Res Value Std (ppm) Factor Limit Difference of
Value Value (±ppm) Characterized to
Nominal Value
1.9 MΩ (1) 19 1.89962M to 1.90038M
10 MΩ) 12.0 37 3.07 0.982 36.3 9.997M to 10.003M
19 MΩ 21.9 47 2.15 0.942 44.3 18.9943M to 19.0057M
100 MΩ 110 99.95M to 100.05M
(2)
1: Not necessary to test due to 5720A Series II internal calibration process. Uncertainties and test limits are shown for other available 742A Standard Resistors.
2: Due to extremely slow settling time (approximately 5 minutes to 0.005% and sensitivity to any nearby movement, use of the DMM to test 100 megohms to the
specified 0.01% uncertainty is not practical and therefore is not recommended. For those who wish to test it, a suitable way is to use an ESI SR 1050 10M/step
Hamon-type Resistance Transfer Standard and use it in conjunction with an ESI 242-series bridge to effect the measurement to the required uncertainty.
3-49
Table 3-17. 5700A Resistance Test Record
Max
Measured UUT 1Ω
Difference of
1Ω Std Res 1Ω Std Cal UUT 1Ω UUT UUT Uncert Spec TUR GB Test
1Ω Std Displayed
Characterized to
Value Voltage Current Voltage True Dev. Std (ppm) Factor Limit
Voltage Value
Nominal Value
Res (ppm)
5.9 95 16.06 1.000 95 0.9995 to 1.0005
Spec TUR GB Test
Max
Measured UUT 1.9Ω
(ppm) Factor Limit
Difference of
1.9Ω Std 1.9Ω Std Cal UUT UUT UUT
1.9Ω Std Displayed
(ppm)
Characterized to
Res Value Voltage Current 1.9Ω True Dev.
Voltage Value
Nominal Value
Voltage Res
5.9 95 16.06 1.000 95 1.89905 to 1.90095
Spec TUR GB Test
Max
Measured UUT 10Ω
(ppm) Factor Limit
Difference of
10Ω Std 10Ω Std Cal UUT UUT UUT
10Ω Std Displayed
(ppm)
Characterized to
Res Value Voltage Current 10Ω True Dev.
Voltage Value
Nominal Value
Voltage Res
5.9 28 4.73 1.000 28 9.997 to 10.004
Resistance Accuracy Verification (19Ω And Above)
Max
Difference of
Std DMM Std DMM DMM UUT True UUT Dev. Uncert. Spec TUR GB Test
Characterized to
Res Res Rdg Error UUT Res Res Value std (±ppm) Factor Limit
Nominal Value
Value Value (±ppm)
19Ω (1) 18.9943 to 19.0057
100Ω (1) 5.1 17 3.33 0.990 16.8 99.985 to 100.015
190Ω (1) 11 189.9715 to 190.0285
1 kΩ (1) 4.7 12 2.54 0.963 11.6 999.85 to 1000.15
1.9 kΩ (1) 9 1.899715k to 1.900285k
10 kΩ 3.1 11 3.57 0.994 10.9 9.9985k to 10.0015k
19 kΩ 3.5 11 3.11 0.984 10.8 18.99715k to 19.00285k
100 kΩ(1) 5.1 13 2.54 0.963 12.5 99.985k to 100.015k
190 kΩ (1) 11 189.9715k to 190.0285k
1 MΩ (1) 8.1 18 2.23 0.948 17.1 0.9998M to 1.0002M
3-50
Table 3-17. 5700A Resistance Test Record (cont)
Max
Difference of
Std DMM Std DMM DMM UUT True UUT Dev. Uncert. Spec TUR GB Test
Characterized to
Res Res Rdg Error UUT Res Res Value std (±ppm) Factor Limit
Nominal Value
Value Value (±ppm)
1.9 MΩ (1) ±19 1.89962M to 1.90038M
10 MΩ 12.0 ±37 3.07 0.982 36.3 9.997M to 10.003M
19 MΩ) 21.9 ±47 2.15 0.942 44.3 18.9943M to 19.0057M
100 MΩ ±110 99.95M to 100.05M
(2)
1: Not necessary to test due to 5720A Series II internal calibration process. Uncertainties and test limits are shown for other available 742A Standard Resistors.
2: Due to extremely slow settling time (approximately 5 minutes to 0.005% and sensitivity to any nearby movement, use of the DMM to test 100 megohms to the
specified 0.01% uncertainty is not practical and therefore is not recommended. For those who wish to test it, a suitable way is to use an ESI SR 1050 10M/step
Hamon-type Resistance Transfer Standard and use it in conjunction with an ESI 242-series bridge to effect the measurement to the required uncertainty.
3-51
5700A/5720A Series II Calibrator
Service Manual
Table 3-18. DC Voltage Test Record for 5720A
5720A Null Detector
Divider 5720A Null Det Limit Meter Limit
Output Reading(μV)
Setting Range (μV) Rattle (μV)
(1) (2)
0.1V 0.22V 0.1V ±1.20 (2) NA
1V 2.2V 1V ±4.8 μV (2) 0.55
1V 11V 1V (3) ±6 (2) 2.2
10V 11V 10V (4) ±33 3.5
10V 22V 10V (3) ±35 5.5
100V 220V 100V ±45 7.5
1000V 1100V 1000V ±65 4.5
0.1V 0.22V -0.1V ±1.20 (2) NA
1V 2.2V -1V ±4.8 (2) 0.55
10V 11V -10V ±6.0 (2) 2.2
1: Mathematically, the true 5700A/5720A Series II output programmed is the certified value of the
reference standard divided by the reference standard nominal value, multiplied by the required
5700A/5720A Series II nominal output. In other words, the 5700A/5720A Series II output is always
programmed for the nominal output adjusted up or down by the same percentage as the certified value
of the reference standard.
2: On the 752A 0.1 and 1V ranges, the null detector polarity is reversed. A low input (5700A/5720A
Series II output) causes a positive null detector reading.
3: Use Range Lock to obtain 1V on 11V and 10V on 22V range. Deactivate Range Lock before setting
the next voltage output.
4: Line regulation can be verified at this time by adjusting the autotransformer for a ±10% change in line
voltage. The null detector reading must remain constant within ±1 μV.
3-52
Calibration and Verification
Determining Test Limits for Other Calibration Intervals 3
Table 3-19. DC Voltage Test Record for 5700A
5700A Null Detector
Divider 5700A Null Det Limit Meter Limit
Output Reading(μV)
Setting Range (μV) Rattle (μV)
(1) (2)
0.1V 0.22V 0.1V ±1.45 (2) NA
1V 2.2V 1V ±7.2 (2) 0.55
1V 11V 1V (3) ±9 (2) 2.2
10V 11V 10V (4) ±54 3.5
10V 22V 10V (3) ±58 5.5
100V 220V 100V ±70 7.5
1000V 1100V 1000V ±86 4.5
0.1V 0.22V -0.1V ±1.45 (2) NA
1V 2.2V -1V ±7.2 (2) 0.55
10V 11V -10V ±54 3.5
1: Mathematically, the true 5700A/5720A Series II output programmed is the certified value of the
reference standard divided by the reference standard nominal value, multiplied by the required
5700A/5720A Series II nominal output. In other words, the 5700A/5720A Series II output is always
programmed for the nominal output adjusted up or down by the same percentage as the certified value
of the reference standard.
2: On the 752A 0.1 and 1V ranges, the null detector polarity is reversed. A low input (5700A/5720A
Series II output) causes a positive null detector reading.
3: Use Range Lock to obtain 1V on 11V and 10V on 22V range. Deactivate Range Lock before setting
the next voltage output.
4: Line regulation can be verified at this time by adjusting the autotransformer for a ±10% change in line
voltage. The null detector reading must remain constant within ±1 μV.
3-53
5700A/5720A Series II Calibrator
Service Manual
Table 3-20. Direct Current Accuracy Test Record (5720A)
Characterizing dc DMM @ ±200 mV and ±2.0V
Column A Column B
DC DMM
Std UUT Actual Test Limit,
Output Rdg.
Std Res UUT Error
Setting
Res Error (A+B) 90-day
Current
Correction Reading
Value (ppm) (±ppm)
(ppm) (ppm)
+2A 0.1Ω (200 mV) 118
-2A 0.1Ω (200 mV) 118
+200 mA 1.0Ω (200 mV) 57
-200 mA 1.0Ω (200 mV) 57
+20 mA 10Ω (200 mV) 38
-20 mA 10Ω (200 mV) 38
+2 mA 1 kΩ (2V) 39
-2 mA 1 kΩ (2V) 39
+200 μA 10 kΩ (2V) 49
-200 μA 10 kΩ (2V) 49
3-54
Calibration and Verification
Determining Test Limits for Other Calibration Intervals 3
Table 3-21. Direct Current Accuracy Test Record (5700A)
Characterizing dc DMM @ ±200 mV and ±2.0V
Column A Column B
Std UUT Actual Test Limit,
Output DC DMM Rdg
Std Res UUT Error
Res Error (A+B) 90-day
Current Setting
Correction Reading
Value (ppm) (ppm)
(ppm) (ppm)
+2A 0.1Ω (200 mV) 135
-2A 0.1Ω (200 mV) 135
+200 mA 1.0Ω (200 mV) 73
-200 mA 1.0Ω (200 mV) 73
+20 mA 10Ω (200 mV) 55
-20 mA 10Ω (200 mV) 55
+2 mA 1 kΩ (2V) 55
-2 mA 1 kΩ (2V) 55
+200 μA 10 kΩ (2V) 100
-200 μA 10 kΩ (2V) 100
5725A Amplifier DC Current Test
Output DC DMM Certified Shunt Cal Actual Test Limits, 90-
Current Value Current day
Reading
(±ppm)
+10A 388 ppm
-10A 388 ppm
+5A 436 ppm
+3A 500 ppm
-3A 500 ppm
Table 3-22. AC Voltage Frequency Accuracy Test Record
Frequency Tolerance Actual
10 Hz 99.99 ms - 100.01 ms
15 Hz 66.673 ms - 66.66 ms
100 Hz 9.999 ms - 10.001 ms
200 Hz 199.98 Hz - 200.02 Hz
500 Hz 499.95 Hz - 500.05 Hz
1 kHz 999.9 Hz - 1000.1 Hz
5 kHz 4999.5 Hz - 5000.5 Hz
10 kHz 9.999 kHz - 10.001 kHz
140 kHz 139.986 kHz - 140.014 kHz
200 kHz 199.98 kHz - 200.02 kHz
500 kHz 499.95 kHz - 500.05 kHz
1 MHz 0.9999 MHz - 1.0001 MHz
3-55
5700A/5720A Series II Calibrator
Service Manual
Table 3-23. 5720A AC Voltage Output Test Record
5790A
Error
Output Spec
1-Year
Frequency TUR GB Test Limit (4)
Display
Level (± ppm )
Spec
Factor (± ppm)
Reading
(± ppm)
90-Day Test Record
2 mV 1 kHz 2590 1070 2.42 0.958 2480
2 mV 20 kHz 2590 1070 2.42 0958 2480
2 mV 50 kHz 2730 1810 1.51 0.882 2408
2 mV 100 kHz 3540 2450 1.44 0.874 3093
2 mV 300 kHz 7200 4300 1.67 0.903 6498
2 mV 500 kHz 14000 6400 2.19 0.945 13223
2 mV 1 MHz 15600 7500 2.08 0.938 14637
2 mV 40 Hz 2950 1070 2.42 0.958 2480
2 mV 20 Hz 2605 1390 1.87 0.923 2403
2 mV 10 Hz 2770 2350 1.18 0.823 2280
20 mV 1 kHz 340 175 1.94 0.928 316
20 mV 20 kHz 340 175 1.94 0.928 316
20 mV 50 kHz 480 310 1.55 0.887 426
20 mV 100 kHz 840 435 1.93 0.928 779
20 mV 300 kHz 1800 1010 1.78 0.914 1646
20 mV 500 kHz 2750 1290 2.13 0.942 2789
20 mV 1 MHz 4350 2100 2.07 0.938 4079
20 mV 40 Hz 340 175 1.94 0.928 316
20 mV 20 Hz 355 255 1.94 0.866 307
20 mV 10 Hz 520 355 1.46 0.877 456
200 mV 1 kHz 130 45 2.89 0.977 127
200 mV 20 kHz 130 45 2.89 0.977 127
200 mV 50 kHz 270 79 3.42 0.990 267
200 mV 100 kHz 640 172 3.72 0.996 638
200 mV 300 kHz 1025 270 3.80 0.997 1022
200 mV 500 kHz 1650 420 3.93 0.999 1648
200 mV 1 MHz 3200 1040 3.08 0.982 3143
200 mV 40 Hz 130 45 2.89 0.977 127
200 mV 20 Hz 245 92 1.58 0.891 129
200 mV 10 Hz 345 217 1.59 0.892 308
2V 1 kHz 52 24 2.17 0.943 49
2V 20 kHz 52 24 2.17 0.943 49
2V 50 kHz 91 46 1.98 0.931 85
2V 100 kHz 145 71 2.04 0.936 136
2V 300 kHz 470 160 2.94 0.978 460
2V 500 kHz 1225 260 4.70 1.000 ⎯
2V 1 MHz 2100 900 2.23 0.953 2001
2V 40 Hz 52 24 2.17 0.943 49
2V 20 Hz 110 66 1.67 0.901 99
2V 10 Hz 295 200 1.48 0.878 259
2.3V(1) 1 kHz 81 24 3.37 0.989 80
20V 1 kHz 52 27 1.87 0.923 47
20V 20 kHz 52 27 1.87 0.923 47
20V 50 kHz 91 48 1.90 0.924 84
20V 100 kHz 128 81 1.57 0.891 114
20V 300 kHz 350 190 1.84 0.920 322
20V 500 kHz 1225 400 3.06 0.982 1203
20V 1 MHz 1800 1200 1.50 0.881 1585
20V(2) 40 Hz 52 27 1.87 0.923 47
20V 20 Hz 110 67 1.64 0.899 99
20V 10 Hz 295 200 1.48 0.878 259
3-56
Calibration and Verification
Determining Test Limits for Other Calibration Intervals 3
Table 3-23. 5720A AC Voltage Test Record (cont)
5790A
Error
Output Spec
1-Year
Frequency TUR GB Test Limit (4)
Display
Level (± ppm )
Spec
Factor (± ppm)
Reading
(± ppm)
200V 1 kHz 64 31 2.05 0.936 59
200V 20 kHz 64 31 2.05 0.936 59
200V 50 kHz 101 69 1.46 0.875 88
200V 100 kHz 185 98 1.89 0.923 171
200V(2) 40 Hz 64 31 2.05 0.936 59
200V 20 Hz 110 68 1.62 0.896 99
200V 10 Hz 295 200 1.48 0.878 259
300V(3) 20 kHz 145 41 3.54 .993 144
600V(3) 50 kHz 378 130 2.91 .977 369
600V(3) 100 kHz 1375 500 2.21 .945 1299
1 kV 1 kHz 79 38 2.08 0.938 74
1 kV 50 Hz 79 38 2.08 0.938 74
1 kV 300 Hz 79 38 2.08 0.938 74
1 kV(3) 20 kHz 131 38 3.45 .991 130
1 kV(3) 30 kHz 371 130 2.85 .975 362
1 kV(3) 40 Hz 84 38 2.21 .945 79
1: This is a test of the bottom of the 20V range .
2: Observe the Calibrator output for 10 minutes and verify that it remains stable within ±7.5 ppm.
3: Perform only for units that are used with a 5725A Amplifier.
4: When the TUR (Test Uncertainty Ratio) is less than 4:1, the spec is reduced to give the same
Consumer Risk as a 4:1 TUR as described later in this chapter.
3-57
5700A/5720A Series II Calibrator
Service Manual
Table 3-24. 5700A AC Voltage Output Test Record
5790A
Error
Output Spec
1-Year
Frequency TUR GB Test Limit (4)
Display
Level (± ppm )
Spec
Factor (± ppm)
Reading
(± ppm)
90-Day Test Record
2 mV 1 kHz 2610 1070 2.44 0.958 2500
2 mV 20 kHz 2610 1070 2.44 0.958 2500
2 mV 50 kHz 2870 1810 1.59 0.892 2561
2 mV 100 kHz 4900 2450 2.00 0.932 4568
2 mV 300 kHz 8700 4300 2.02 0.932 8128
2 mV 500 kHz 16700 6400 2.61 0.966 16132
2 mV 1 MHz 24400 7500 3.25 0.987 24078
2 mV 40 Hz 2610 1070 2.44 0.958 2500
2 mV 20 Hz 2720 1390 1.96 0.928 2524
2 mV 10 Hz 3050 2350 1.30 0.848 2586
20 mV 1 kHz 410 175 2.34 0.953 391
20 mV 20 kHz 410 175 2.34 0.953 391
20 mV 50 kHz 670 310 2.16 0.943 632
20 mV 100 kHz 1300 435 2.99 0.980 1274
20 mV 300 kHz 1950 1010 1.93 0.927 1808
20 mV 500 kHz 3200 1290 2.48 0.960 3072
20 mV 1 MHz 6400 2100 3.05 0.982 6280
20 mV 40 Hz 410 175 2.34 0.950 390
20 mV 20 Hz 520 255 2.04 0.935 486
20 mV 10 Hz 850 355 2.39 0.956 813
200 mV 1 kHz 150 45 3.33 0.988 148
200 mV 20 kHz 150 45 3.33 0.988 148
200 mV 50 kHz 380 79 4.81 1.000 ⎯
200 mV 100 kHz 950 172 5.52 1.000 ⎯
200 mV 300 kHz 1150 270 4.26 1.000 ⎯
200 mV 500 kHz 1900 420 4.52 1.000 ⎯
200 mV 1 MHz 3800 1040 3.65 0.995 3781
200 mV 40 Hz 150 45 3.33 0.988 148
200 mV 20 Hz 270 92 2.93 0.978 264
200 mV 10 Hz 630 217 2.90 0.977 616
2V 1 kHz 78 24 3.25 0.987 77
2V 20 kHz 78 24 3.25 0.987 77
2V 50 kHz 140 46 3.04 0.980 137
2V 100 kHz 290 71 4.08 1.000 ⎯
2V 300 kHz 515 160 3.22 0.986 508
2V 500 kHz 1300 260 5.00 1.000 ⎯
2V 1 MHz 2700 900 3.00 0.980 2646
2V 40 Hz 78 24 3.25 0.987 77
2V 20 Hz 185 66 2.80 0.974 180
2V 10 Hz 600 200 3.00 0.980 588
2.3V(1) 1 kHz 105 24 4.38 1.000 ⎯
20V 1 kHz 78 27 2.89 0.977 77
20V 20 kHz 78 27 2.89 0.977 77
20V 50 kHz 140 48 2.92 0.978 137
20V 100 kHz 270 81 3.33 0.988 267
20V 300 kHz 635 190 3.34 0.988 627
20V 500 kHz 1550 400 3.88 0.998 1547
20V 1 MHz 3250 1200 2.71 0.970 3153
20V(2) 40 Hz 78 27 2.89 0.977 77
20V 20 Hz 185 67 2.76 0.972 180
20V 10 Hz 600 200 3.00 0.980 588
3-58
Calibration and Verification
Determining Test Limits for Other Calibration Intervals 3
Table 3-24. 5700A AC Voltage Output Test Record (cont)
5790A
Error
Output Spec
1-Year
Frequency TUR GB Test Limit (4)
Display
Level (± ppm )
Spec
Factor (± ppm)
Reading
(± ppm)
200V 1 kHz 85 31 2.74 0.971 83
200V 20 kHz 85 31 2.74 0.971 83
200V 50 kHz 240 69 3.48 0.991 238
200V 100 kHz 600 98 6.12 1.00 ⎯
200V(2) 40 Hz 85 31 2.74 0.972 83
200V 20 Hz 185 68 2.72 0.970 179
200V 10 Hz 600 200 3.00 0.980 588
300V(3) 20 kHz 145 41 3.54 0.993 144
600V(3) 50 kHz 378 130 2.91 0.977 369
600V(3) 100 kHz 1375 500 2.21 0.945 1299
1 kV 1 kHz 84 38 2.21 0.945 79
1 kV 50 Hz 84 38 2.21 0.945 79
1 kV 300 Hz 84 38 2.21 0.945 79
1 kV(3) 20 kHz 131 38 3.45 0.991 130
1 kV(3) 30 kHz 371 130 2.85 0.975 362
1 kV(3) 40 Hz 84 38 2.21 0.945 79
1: This is a test of the bottom of the 20V range .
2: Observe the Calibrator output for 10 minutes and verify that it remains stable within ±7.5 ppm.
3: Perform only for units that are used with a 5725A Amplifier.
4: When the TUR (Test Uncertainty Ratio) is less than 4:1, the spec is reduced to give the same
Consumer Risk as a 4:1 TUR as described later in this chapter.
Table 3-25. AC Voltage 2 mV Range Test Record
Characterized 1.9 mV Reading Error Display Reading Limits
±0.26%
3-59
5700A/5720A Series II Calibrator
Service Manual
Table 3-26. 5720A AC Current 20 mA to 10A Accuracy Test Record
2A, 200 mA, 20 mA and 10A Test Record
A40 Shunt UUT Error Calculated
Output Freq Spec
AC-DC Diff Display Error
Current ± ppm
2A 40 Hz 320
2A 1 kHz 320
2A 5 kHz 510
2A 10 kHz 7100
200 mA 10 Hz 305
200 mA 20 Hz 200
200 mA 40 Hz 145
200 mA 1 kHz 145
200 mA 5 kHz 240
200 mA 10 kHz 1160
20 mA 10 Hz 305
20 mA 20 Hz 200
20 mA 40 Hz 150
20 mA 1 kHz 150
20 mA 5 kHz 255
20 mA 10 kHz 1400
10A (1) 40 Hz 417
10A (1) 1 kHz 417
10A (1) 5 kHz 888
10A (1) 10 kHz 3375
1: If a 5725A is attached.
3-60
Calibration and Verification
Determining Test Limits for Other Calibration Intervals 3
Table 3-27. 5700A AC Current 20 mA to 10A Accuracy Test Record
2A, 200 mA, 20 mA and 10A Test Record (10A Only for 5725A)
A40 Shunt UUT Error Calculated
Output Freq Specs
AC-DC Diff Display Error
Current ±ppm
2A 40 Hz 670
2A 1 kHz 670
2A 5 kHz 800
2A 10 kHz 9100
200 mA 10 Hz 725
200 mA 20 Hz 400
200 mA 40 Hz 170
200 mA 1 kHz 170
200 mA 5 kHz 850
200 mA 10 kHz 2100
20 mA 10 Hz 725
20 mA 20 Hz 400
20 mA 40 Hz 160
20 mA 1 kHz 60
20 mA 5 kHz 850
20 mA 10 kHz 2100
10A (1) 40 Hz 417
10A (1) 1 kHz 417
10A (1) 5 kHz 888
10A (1) 10 kHz 3375
1: If a 5725 is attached.
3-61
5700A/5720A Series II Calibrator
Service Manual
Table 3-28. 5720A AC Current 2 mA and 200 μA Accuracy Test Record
5790A
Test Limits
Output Spec.
Transfer
Frequency Error TUR GB
± ppm
Current ± ppm
Spec
Factor
(90-day)
± ppm
2 mA 10 Hz 305 210 1.45 0.874 267
2 mA 20 Hz 200 73 2.74 0.971 194
2 mA 40 Hz 150 27 5.56 1.000 150
2 mA 1 kHz 150 27 5.56 1.000 150
2 mA 5 kHz 285 27 10.56 1.000 285
2 mA 10 kHz 1500 27 55.56 1.000 1500
200 μA 10 Hz 380 210 1.81 0.916 348
200 μA 20 Hz 240 73 3.29 0.988 237
200 μA 40 Hz 180 27 6.67 1.000 180
200 μA 1 kHz 180 27 6.67 1.000 180
200 μA 5 kHz 395 27 14.63 1.000 +365/-425 (1)
200 μA 10 kHz 1500 27 55.56 1.000 +1380/-1620
(1)
1: The spec is modified because of the capacitive loading of the 2K resistor by the cable and input of the
5790A.
Table 3-29. 5700A AC Current 2 mA and 200 μA Accuracy Test Record
5790A
Test Limits
Output Spec
Transfer
Frequency Error TUR GB
± ppm
Current ± ppm
Spec
Factor
(90-day)
± ppm
2 mA 10 Hz 725 210 3.45 0.991 718
2 mA 20 Hz 400 73 1.000 400
5.48
2 mA 40 Hz 160 27 5.93 1.000 160
2 mA 1 kHz 160 27 5.93 1.000 160
2 mA 5 kHz 850 27 31.48 1.000 850
2 mA 10 kHz 2100 27 77.8 1.000 2100
4.05
200 μA 10 Hz 850 210 1.000 850
200 μA 20 Hz 505 73 1.000 505
6.92
200 μA 40 Hz 240 27 8.89 1.000 240
200 μA 1 kHz 240 27 8.89 1.000 240
200 μA 5 kHz 850 27 31.48 1.000 +820/-880 (1)
200 μA 10 kHz 2100 27 77.8 1.000 +1980/-2220
(1)
1: The spec is modified because of the capacitive loading of the 2K resistor by the cable and input of the
5790A.
3-62
Calibration and Verification
Determining Test Limits for Other Calibration Intervals 3
Table 3-30. Wideband Frequency Accuracy Test Record
Frequency ( Hz ) Frequency Measured Tolerance Limits
10 Hz 99.99 ms to 100.01 ms
100 Hz 9.999 ms to 10.001 ms
300 Hz 299.97 Hz to 300.03 Hz
500 Hz 499.95 Hz to 500.05 Hz
800 Hz 799.92 Hz to 800.08 Hz
900 Hz 899.91 Hz to 900.09 Hz
1 kHz 999.0 Hz to 1.0001 kHz
1.19 kHz 1.189881 kHz to 1.190119 kHz
2.2 MHz 2.19978 MHz to 2.20022 MHz
3.5 MHz 3.49965 MHz to 3.50035 MHz
3.8 MHz 3.79962 MHz to 3.80038 MHz
10 MHz 9.990 MHz to 10.001 MHz
20 MHz 19.998 MHz to 20.002 MHz
30 MHz 29.997 MHz to 30.003 MHz
3-63
5700A/5720A Series II Calibrator
Service Manual
Table 3-31. Wideband Accuracy at 1 kHz Test Record
5790A
Output Measured Spec Test
TUR GB
1-Year Spec
Level Error ± ppm (90-day) Limit
Factor
± ppm
2.1V 2238 24 93 1.000 2238
1.0V 2900 24 121 1.000 2900
0.3V 2833 38 74.5 1.000 2833
0.1V 3400 53 64.1 1.000 3400
30 mV 3333 115 29.0 1.000 3333
10 mV 3900 240 16.2 1.000 3900
3 mV 4833 643 7.5 1.000 4833
1 mV 5400 1720 3.14 0.980 5292
Table 3-32. Wideband Flatness Test Record
5790A
Output Measured Spec
Test Limit
Frequency TUR GB
1-Year
Level Flatness Error ± ppm
± ppm
Factor
Spec
(90-day)
3V 10 Hz 3000 1000 3.00 0.980 2940
30 Hz 1000 300 3.33 0.988 988
10 kHz 1000 300 3.33 0.988 988
120 kHz 1000 300 3.33 0.988 988
500 kHz 1000 300 3.33 0.988 988
2 MHz 1000 500 2.00 0.932 932
5 MHz 2000 1000 2.00 0.932 1864
10 MHz 2000 1000 2.00 0.932 1864
20 MHz 4000 1500 2.67 0.968 3872
30 MHz 10000 3500 2.86 0.975 9750
1V 10 kHz 1000 300 3.33 0.988 988
120 kHz 1000 300 3.33 0.988 988
500 kHz 1000 300 3.33 0.988 988
2 MHz 1000 500 2.00 0.932 932
5 MHz 2000 1000 2.00 0.932 1864
10 MHz 2000 1000 2.00 0.932 1864
20 MHz 4000 1500 2.67 0.968 3872
30 MHz 10000 3500 2.86 0.975 9750
300 mV 10 kHz 1000 300 3.33 0.988 988
120 kHz 1000 300 3.33 0.988 988
500 kHz 1000 300 3.33 0.988 988
2 MHz 1000 500 2.00 0.932 932
5 MHz 2000 1000 2.00 0.932 1864
10 MHz 2000 1000 2.00 0.932 1864
20 MHz 4000 1500 2.67 0.968 3872
30 MHz 10000 3500 2.86 0.975 9750
100 mV 10 kHz 1000 400 2.50 0.961 961
120 kHz 1000 400 2.50 0.961 961
500 kHz 1030 400 2.58 0.964 993
2 MHz 1030 500 2.06 0.936 964
5 MHz 2030 1000 2.03 0.933 1894
10 MHz 2030 1000 2.03 0.933 1894
20 MHz 4030 1500 2.69 0.970 3909
30 MHz 10030 3500 2.87 0.976 9789
3-64
Calibration and Verification
Determining Test Limits for Other Calibration Intervals 3
Table 3-32. Wideband Flatness Test Record (cont)
5790A
Output Measured Spec
Test Limit
Frequency TUR GB
1-Year
Level Flatness Error ± ppm
± ppm
Factor
Spec
(90-day)
30 mV 10 kHz 1000 500 2.00 0.932 932
120 kHz 1000 500 2.00 0.932 932
500 kHz 1100 500 2.20 0.945 1040
2 MHz 1100 500 2.20 0.945 1040
5 MHz 2100 1000 2.10 0.939 1972
10 MHz 2100 1000 2.10 0.939 1972
20 MHz 4100 1500 2.73 0.972 3985
30 MHz 10100 3500 2.89 0.977 9868
10 mV 10 kHz 1000 500 2.00 0.932 932
120 kHz 1000 500 2.00 0.932 932
500 kHz 1300 700 1.86 0.920 1196
2 MHz 1300 700 1.86 0.920 1196
5 MHz 2300 1000 2.30 0.950 2185
10 MHz 2300 1000 2.30 0.950 2185
20 MHz 4300 1700 2.53 0.962 4137
30 MHz 10300 3700 2.78 0.972 10012
3 mV 10 kHz 1000 500 2.00 0.932 932
120 kHz 1000 500 2.00 0.932 932
500 kHz 2000 1033 1.94 0.928 1856
2 MHz 2000 1033 1.94 0.928 1856
5 MHz 4000 1333 3.00 0.980 3920
10 MHZ 4000 1333 3.00 0.980 3920
20 MHz 6000 2033 2.95 0.978 5868
30 MHz 16000 4033 3.97 0.999 15984
1 mV 10 kHz 1000 500 2.00 0.932 932
120 kHz 1000 500 2.00 0.932 932
500 kHz 5000 1700 2.94 0.978 4890
2 MHz 5000 1700 2.94 0.978 4890
5 MHZ 7000 2700 2.59 0.965 6755
10 MHz 7000 2700 2.59 0.965 6755
20 MHz 9000 4000 2.25 0.948 8532
30 MHz 30000 9000 3.33 0.988 29640
3-65
5700A/5720A Series II Calibrator
Service Manual
Table 3-33. Wideband Absolute Error 10 Hz to 500 kHz
1 kHz Absolute Flatness Error Error Sum 90-Day
Output Frequency
Error ppm ppm Spec Limit
Level
ppm
(±ppm)
2.1V 10 Hz 5238
30 Hz 2238
10 kHz 2238
120 kHz 2238
500 kHz 2238
1V 10 kHz 2900
120 kHz 2900
500 kHz 2900
300 mV 10 kHz 2833
120 kHz 2833
500 kHz 2833
100 mV 10 kHz 3400
120 kHz 3400
500 kHz 3400
30 mV 10 kHz 3333
120 kHz 3333
500 kHz 3333
10 mV 10 kHz 3900
120 kHz 3900
500 kHz 3900
3 mV 10 kHz 4833
120 kHz 4833
500 kHz 4833
1 mV 10 kHz 5400
120 kHz 5400
500 kHz 5400
3-66
Calibration and Verification
Determining Test Limits for Other Calibration Intervals 3
Table 3-34. Load Regulation Test Record
5700A/5720A Series II
Div. Setting 5700A/5720A Series II Change In Null Change In
Out/Full Load
Range Measured Null Limit
10V 11V 10V/199Ω ±3.1 μV
100V 220V 100V/1999Ω ±42 μV
1000V 1100V 1000V/49.99 kΩ ±310 μV
Table 3-35. DC Voltage Linearity Test Record
Kelvin-Varley Setting 5700A/5720A Series II Null Detector Null Detector
Output Reading Reading limit
0.1 1V ±2.3 μV
0.2 2V ±2.6 μV
0.3 3V ±2.9 μV
0.4 4V ±3.2 μV
0.5 5V ±3.5 μV
0.6 6V ±3.8 μV
0.7 7V ±4.1 μV
0.8 8V ±4.4 μV
0.9 9V ±4.7 μV
Table 3-36. DC Voltage Output Noise Test
Differential Amplifier Rms Meter Maximum rms Meter
Calibrator (UUT)
Sensitivity Reading Reading
50 μV/division 2.2V 150 mV
50 μV/division 10V 500 mV
50 μV/division 20V 500 mV
100 μV/division 200V 750 mV
500 μV/division 1000V 500 mV
3-67
5700A/5720A Series II Calibrator
Service Manual
Table 3-37. AC V Distortion Test Summary
5700A/5720A Series Load Resistors Frequency Measured Max.
II Output Distortion Distortion
2V 100Ω, 1/8W 10 Hz, 20 Hz 0.054%
1 kHz, 20 kHz, 50 kHz, 0.044%
100 kHz, 200 kHz, 500 kHz 0.355%
20V 1 kΩ, 1/2W 10 Hz, 20 Hz 0.0535%
20 kHz, 100 kHz 0.0385%
200 kHz, 500 kHz 0.304%
200V 10 kΩ, 5W 10 Hz, 20 Hz 0.055%
50 kHz, 100 kHz 0.1065%
300V(1) 15 kΩ, 5W 40 Hz 0.1%
300V(1) 15 kΩ, 5W 50 kHz 0.3%
300V(1) 15 kΩ, 5W 70 kHz 0.4%
7
(1) The 5700A/5720A Series II maximum volt-Hertz product is (2.2 x 10 ) The 300V level assumes that a
Fluke 5725A Amplifier is attached.
Table 3-38. Test Record for Flatness Check of the AC 2 mV Range
Frequency UUT Error Display Reading Limits
10 Hz
20 Hz ±0.26%
40 Hz
1 kHz ±0.26%
20 kHz ±0.29%
50 kHz ±0.49%
100 kHz ±0.87%
300 kHz
500 kHz ±1.83%
1 MHz
3-68
Chapter 4
Maintenance
Title Page
4-1. Introduction........................................................................................... 4-3
4-2. Accessing the Fuse................................................................................ 4-3
4-3. Cleaning the Air Filter .......................................................................... 4-3
4-4. General Cleaning .................................................................................. 4-4
4-5. Cleaning PCA's..................................................................................... 4-5
4-6. Access Procedures................................................................................ 4-5
4-7. Top and Bottom Covers.................................................................... 4-5
4-8. Digital Section Cover ....................................................................... 4-5
4-9. Analog Section Covers..................................................................... 4-5
4-10. Rear Panel Removal and Installation................................................ 4-5
4-11. Rear Panel Assembly Access ........................................................... 4-6
4-12. Front Panel Removal and Installation .............................................. 4-6
4-13. Display Assembly Removal and Installation ............................... 4-7
4-14. Keyboard Assembly Removal and Installation............................ 4-7
4-15. Analog Assembly Removal and Installation .................................... 4-8
4-16. Digital Assembly Removal and Installation..................................... 4-10
4-17. Power Transformer Removal and Installation.................................. 4-10
4-18. Hybrid Cover Removal..................................................................... 4-10
4-19. Front/Rear Binding Post Reconfiguration ............................................ 4-10
4-20. Installing a Wideband AC Module (Option -03) .................................. 4-12
4-21. Clearing Ghost Images from the Control Display ................................ 4-12
4-22. Replacing the Clock/Calendar Backup Battery .................................... 4-12
4-23. Using Remote Commands Reserved for Servicing............................... 4-13
4-24. Using the ETIME Command............................................................ 4-13
4-25. Fault Codes ........................................................................................... 4-15
4-1
5700A/5720A Series II Calibrator
Service Manual
4-2
Maintenance
Introduction 4
4-1. Introduction
Because this is a high performance instrument, it is not recommended that the user
service the boards to the component level. In many different ways it is easy to introduce a
subtle long-term stability problem by handling the boards. Access procedures are
provided for those who want to replace a faulty module.
4-2. Accessing the Fuse
The fuse is accessible from the rear panel. The fuse rating label to the right of the fuse
holder shows the correct replacement fuse ratings for each operating voltage. To access
the fuse, refer to Figure 4-1 and proceed as follows:
1. Disconnect line power.
2. Using a standard screwdriver, turn the fuse holder counterclockwise until the cap and
fuse are disengaged.
VOLTAGE VOLTAGE
FUSE-F1 FUSE-F1
SELECTION SELECTION
S2 S3 S4 S2 S3 S4
100V 200V
T 3A T 1.5A
110V 220V
250V 250V
115V (SB) 230V (SB)
120V 240V
CHASSIS
GROUND
!
FUSE -F1
S2 S3 S4
f7-1.eps
Figure 4-1. Accessing the Fuse
4-3. Cleaning the Air Filter
WCaution
Damage caused by overheating may occur if the area around
the fan is restricted, the intake air is too warm, or the air filter
becomes clogged.
The air filter must be removed and cleaned every 30 days or more frequently if the
calibrator is operated in a dusty environment. The air filter is accessible from the rear
panel of the calibrator.
4-3
5700A/5720A Series II Calibrator
Service Manual
To clean the air filter, refer to Figure 4-2 and proceed as follows:
CHASSIS
GROUND
!
FUSE -F1
S2 S3 S4
F4-1.EPS
Figure 4-2. Air Filter
1. Disconnect line power.
2. Remove the filter element.
a. Unscrew the knurled screw at the top of the air filter (counterclockwise).
b. Pull the air filter retainer downward; it hinges at the bottom.
c. Remove the filter element.
3. Clean the filter element.
a. Wash the filter element in soapy water.
b. Rinse the filter element in fresh running water.
c. Shake out the excess water, then allow the filter element to dry thoroughly before
reinstalling it.
4. Reinstall the filter element, its retainer, and the knurled screw.
4-4. General Cleaning
To keep the Calibrator looking like new, clean the case, front panel keys, and lens using a
soft cloth slightly dampened with water or a non-abrasive mild cleaning solution that
does not harm plastics.
WCaution
Do not use aromatic hydrocarbons or chlorinated solvents for
cleaning. They can damage the plastic materials used in the
calibrator.
4-4
Maintenance
Cleaning PCA's 4
4-5. Cleaning PCA's
Printed circuit assemblies only need cleaning after repair work. After soldering on a pca,
remove flux residue using isopropyl alcohol and a cotton swab.
4-6. Access Procedures
WXWarning
Servicing described in this section is to be performed by
qualified service personnel only. To avoid electrical shock, do
not perform any servicing unless qualified to do so.
4-7. Top and Bottom Covers
Check that power is not connected to the Calibrator; the power control must be off, and
the line power cord must be disconnected. Top and bottom covers are each secured with
eight Phillips head screws (four front, four rear).
4-8. Digital Section Cover
The Digital Section is accessed through one top cover that is secured by six Phillips head
screws.
4-9. Analog Section Covers
The Analog Section is enclosed with separate covers on top and bottom. The top cover is
secured with seven Phillips head screws. The bottom Analog Section cover is secured
with eight Phillips head screws (three short, five longer).
4-10. Rear Panel Removal and Installation
Detach the Rear Panel by removing the six hex head screws (three on each rear handle
side) and the two Phillips head screws found along the side of the Fan Assembly. Refer to
Figure 4-3 for screw locations.
REMOVE
Figure 4-3. Rear Panel Removal
4-5
5700A/5720A Series II Calibrator
Service Manual
4-11. Rear Panel Assembly Access
Refer to Figure 4-4 during the following procedure:
REMOVE
1
1
1
1
REMOVE
1 REMOVE FACK SCREWS TO SEPARATE THE REAR PANEL CIRCUIT BOARD FROM
THE METAL HOUSING.
F4-3.EPS
Figure 4-4. Rear Panel Assembly Access
1. Remove the six securing screws for the Rear Panel assembly housing.
2. Gently pull the rear panel housing from the Rear Panel.
3. Allow the rear panel housing to lay flat on the work surface by removing the two
ribbon cables from the Rear Panel board.
4. Remove the two nuts at TB1 and TB2 on the paddle board; separate the associated
wires from the paddle board.
5. Remove P11 from J11. Then remove the two paddle board mounting screws and
separate the paddle board from the Rear Panel assembly.
6. Remove the jack screws for each connection on the rear panel housing, then gently
lift the Rear Panel assembly out from the housing.
7. Reverse this procedure to install the Rear Panel assembly.
4-12. Front Panel Removal and Installation
Refer to Figure 4-5 during the following procedure:
4-6
Maintenance
Access Procedures 4
F4-4.EPS
Figure 4-5. Front Panel Removal
1. Remove the Calibrator top and bottom covers.
2. Remove the single screw at the top of the Front Panel and the six hex screws on the
front handle sides. Then grasp both handles and gently tilt the Front Panel down and
away from the mainframe, disengaging the green power button. Position the Front
Panel on its handles, in front of the instrument.
3. If you need to completely detach the Front Panel from the Calibrator, one, or possibly
two, cables must be disconnected. The output cable must be detached in all
configurations. If the Wideband Option is installed, you must also detach the related
connector from the Front Panel.
Reverse this procedure to install the Front Panel.
4-13. Display Assembly Removal and Installation
Once the Front Panel has been removed, use the following procedure to access the
Display assembly.
1. Remove the ribbon cable connecting the Display assembly to the Motherboard.
2. Remove the six screws securing the Front Panel Display assembly cover shield.
Three of these screws are accessed from the inside, and the other three are accessed
along the top of the front panel.
3. Remove the seven screws securing the Front Panel Display assembly to the Front
Panel. Gently lift the Front Panel Display assembly up, and remove the keyboard
ribbon cable. Now remove the Front Panel Display assembly.
Reverse this procedure to install the Front Panel Display assembly.
4-14. Keyboard Assembly Removal and Installation
The following procedure assumes that the Display Assembly Removal procedure has
already been completed.
1. Remove all output cable connections (including GROUND-to-metal) from the front
panel binding posts. Save all removed hardware.
2. Remove the two hex screws at the front of each handle. Then remove the front
handles.
3. Gently release the eight plastic hook catches, and separate the front panel plastic
from the sheet metal.
4-7
5700A/5720A Series II Calibrator
Service Manual
4. Remove the output adjustment knob flywheel by taking out its center screw. Hold the
wheel in place by inserting a pencil in one of the flywheel holes and pressing on one
of the plastic standoffs.
5. Remove the nine self-tapping screws connecting the Keyboard assembly to the front
panel plastic.
6. Remove the Keyboard assembly by gently releasing the seven plastic hook catches.
Work from one side of the board to the other. Start at either side by simultaneously
releasing a catch and lifting on the board.
Reverse this procedure to install the Keyboard assembly. When reconnecting the wires to
the binding posts, be sure to include a washer on each side of the ring terminals. Refer to
the nearby decal or see sheet 4 of the Analog Motherboard schematic in Section 8 of this
manual for proper connection of the output cable to the front binding posts.
WCaution
Do not tighten the nuts that hold the wires to the binding posts
more than 7 in-lb. Force exceeding 7 in-lb can destroy the
binding posts.
4-15. Analog Assembly Removal and Installation
The analog assemblies are installed in the sequence shown in Figure 4-6. Note that each
module cannot be positioned in any other slot and that identifying information on the tab
for each module faces forward. In most cases, the component side of each module also
faces forward. The component side faces to the rear for three modules: Current/High
Resolution Oscillator (A7), Ohms Cal (A9), and High Voltage Control (A14). All
modules except the High Voltage Control pull straight up to disengage from the Digital
Motherboard. For the High Voltage Control module, two Phillips head captive screws at
the outer corners of the High Voltage Transformer must be removed before the module
can be removed.
4-8
Maintenance
Access Procedures 4
IEEE
RS232
A21 REAR PANEL PCA
VOLTAGE SELECT
SWITCHES
A18 FILTER/PA SUPPLY PCA
A17 REGULATOR/GUARD CROSSING PCA
CAPTIVE
A16 POWER AMPLIFIER PCA
SCREWS
A15 HIGH VOLTAGE/HIGH
CURRENT PCA
(COMPONENTS
FACE REAR) A14 HIGH VOLTAGE CONTROL PCA
A13 OSCILLATOR OUTPUT PCA
A12 OSCILLATOR CONTROL PCA
A11 DAC PCA
A10 OHMS MAIN PCA
(COMPONENTS
FACE REAR)
A9 OHMS CAL PCA
A8 SWITCH MATRIX PCA
(COMPONENTS
A7 CURRENT/HIGH-RESOLUTION
FACE REAR)
OSCILLATOR PCA
A6 WIDEBAND OSCILLATOR PCA
A5 WIDEBAND OUTPUT PCA
A4 DIGITAL
MOTERBOARD PCA
A2 FRONT PANEL PCA
A1 KEYBOARD ASSEMBLY
FRONT PANEL
F4-5.EPS
Figure 4-6. Analog and Digital Assemblies
WCaution
Do not touch any circuit area on an analog assembly.
Contamination from skin oil can produce high resistance paths,
with resulting leakage currents and possible erroneous
readings. Always grasp an analog assembly by its upper corner
ears.
4-9
A22 POWER TRANSFORMER
A19 DIGITAL POWER SUPPLY PCA
A20 CPU PCA
5700A/5720A Series II Calibrator
Service Manual
4-16. Digital Assembly Removal and Installation
Remove the CPU Assembly or the Digital Power Supply Assembly by pulling straight up
at the top corners of the assembly. In relation to the chassis side, the CPU Assembly
components face toward, and the Digital Power Supply Assembly components face away.
See Figure 4-6.
4-17. Power Transformer Removal and Installation
Use the following procedure to remove the Power Transformer assembly:
1. Remove the Calibrator Front and Rear Panels.
2. Remove the Digital Power Supply (A19) and CPU (A20) assemblies.
3. Detach the five connectors leading from the Power Transformer assembly to the
Digital Motherboard. The three connectors at the rear of the assembly may not be
accessible without first removing the rear fan. With the two digital assemblies (A19
and A20) removed, the four Phillips head screws securing this fan can be accessed
through holes in the chassis side.
Note that no two Power Transformer connectors are the same size and that each
connector is keyed; re-connection only involves matching appropriate connectors.
4. Working from the bottom of the instrument, remove the Digital Motherboard (A4)
assembly.
5. Remove the eleven screws securing the Power Transformer assembly, as follows:
• Rear Panel: two screws, which were removed along with the Rear Panel.
• Front Panel: two screws.
• Top Edge: four screws.
• Bottom Edge: three screws.
6. Remove the Power Transformer assembly.
To install the Power Transformer assembly, reverse the preceding six steps.
4-18. Hybrid Cover Removal
When removing the plastic covers from the hybrid assemblies, push the ends of the cover
retainer pins through from the back of the circuit board. The retainer pins can be damaged
by attempting to pull the covers off.
4-19. Front/Rear Binding Post Reconfiguration
An internal cable can be configured for output connections at either the front or rear
binding posts. The front binding posts are usually connected at the factory. If the rear
binding posts are connected at the factory, a decal describing this arrangement is attached
to the front binding posts. The procedure that follows can be used to swap an existing
binding post configuration; it is to be done only at Service Centers. The following
procedure can be used to change front-to-rear or rear-to-front.
4-10
Maintenance
Front/Rear Binding Post Reconfiguration 4
Reverse this procedure when changing from rear to front output operation.
1. Remove instrument top and bottom covers and remove bottom analog guard cover.
2. Remove the instrument front panel by removing the three hex screws on each front
handle side and a single screw on the top of the front panel. See Figure 4-5 for screw
locations. By grasping the handles gently pull the front panel away from the frame
and lay it on its handles in front of the instrument.
3. Remove all the wires connecting the ring terminals of the output cable to the front
panel binding posts. Save all hardware removed during this step.
4. Remove the two screws and restraining board attaching the toroid to the Front Panel.
Save these items.
5. Position the output cable and toroid along the bottom left side of the instrument. In a
later step, the output cable will be positioned between the Analog Motherboard and
the left side panel.
6. Install the Front Panel.
7. Detach the Rear Panel by removing six hex screws (three on each rear handle side)
and two screws near the the fan filter on the Rear Panel. See Figure 4-3 for screw
locations. Then grasp the handles and gently pull the Rear Panel away from the
frame.
8. Orient the instrument so that it is resting on its right side panel, with its bottom facing
you.
9. Route the output cable between the left side panel and the Analog Motherboard,
ending at the Rear Panel.
10. Using the items obtained during toroid removal, attach the toroid to the two rear
panel standoffs.
11. Attach the color-coded output leads to the rear output binding posts. Use one washer
on each side of each connecting ring. Verify connections by checking the decal
mounted nearby or by matching lead color to the color on the front of the binding
post. (Of the eleven wires, four are clear-insulated shield wires. If necessary, refer to
page 4 of the Analog Motherboard schematic in Section 8 to determine these
connections.)
WCaution
Do not over tighten hardware on the binding posts. Torque in
excess of seven inch-pounds can damage a binding post.
Note that the I GUARD terminal is not connected at the front binding posts; cut away
the I GUARD thermal fit covering to connect this terminal at the rear binding posts.
Also, the AUX CURRENT ring terminal is not connected at the rear binding posts;
this terminal must be insulated and tied off.
12. Replace the rear panel back, the bottom guard cover, and top and bottom covers to
complete this procedure.
4-11
5700A/5720A Series II Calibrator
Service Manual
4-20. Installing a Wideband AC Module (Option -03)
WCaution
The Wideband option circuit board assemblies contain static-
sensitive components. Use caution to avoid static discharge
when handling the modules.
The procedure that follows can be used to install a 5700A-03 Wideband AC Voltage
module in a Calibrator. The option consists of two circuit board assemblies. This
procedure is to be done only at Service Centers.
1. Remove the top and bottom covers and analog section cover. (See ACCESS
PROCEDURES this section)
2. Referring to Figure 4-6, locate the slots for the Wideband Output Module (A5) and
the Wideband Oscillator Module (A6).
3. Make sure the cable supplied with the Wideband option is connected between the
Wideband Output and Wideband Oscillator assemblies.
4. Uncoil the internal wideband output cable one turn from the Calibrator chassis and
connect it to the coaxial connector on the Wideband Output Module. Make sure the
cable is routed in such a way as to avoid shorting to ground when the board is
installed in the chassis.
5. Install the Wideband Output and Wideband Oscillator Modules and lock the nylon
ears.
6. Run the Wideband Gains Calibration procedure as described in Section 3.
7. Perform the Wideband Flatness Calibration procedure as described in Section 3. The
Wideband option is now installed and ready for use.
4-21. Clearing Ghost Images from the Control Display
After prolonged periods of displaying the same message on the Control Display, you may
notice a non-uniform brightness of pixels across the display. This phenomenon can be
cleared up by lighting up the whole display and leaving it on overnight (or at least several
hours). Proceed as follows to burn in the Control Display:
1. Turn on the Calibrator and press the "Setup Menus" softkey.
2. Press the "Self Test & Diags" softkey.
3. Press the "5700 Self Diags" softkey.
4. Press the "Front Panel Tests" softkey.
5. Under the "Display" label, press the "Control" softkey.
6. Press the "All On" softkey. This causes all Control Display pixels to light. Press the
RESET key or press PREV MENU six times to return to normal operation after an
overnight or equivalent burn in period.
4-22. Replacing the Clock/Calendar Backup Battery
To replace the lithium button-type battery on the CPU Assembly (A20), proceed as
follows:
1. Make sure the power is off and the line power cord disconnected.
4-12
Maintenance
Using Remote Commands Reserved for Servicing 4
2. Follow the access procedures to remove the digital side cover.
3. Remove the CPU Assembly (A20).
4. Desolder and remove battery BT1.
5. Solder a replacement battery in place (refer to the parts list for replacement
information if necessary.)
6. Replace the CPU Assembly. After replacing the battery, the setting of the time and
date the elapsed time counter (read by the remote query ETIME? and set by ETIME)
will need to be reprogrammed.
4-23. Using Remote Commands Reserved for Servicing
This information documents remote commands not described in the 5700A/5720A Series
II Operator Manual, Section 5. The commands described here are useful for servicing the
instrument.
4-24. Using the ETIME Command
The ETIME remote command is the companion to ETIME?, the elapsed time query,
which is documented in the Operator Manual. The ETIME? query tells you how many
minutes the Calibrator has been in the power on state since the instrument was built. If
you replace the CPU Assembly (A20), the clock/calendar battery (BT1), or the
clock/calendar IC (U33), you will lose the setting of ETIME. The ETIME command
gives you a way to set this counter to where it was before servicing the instrument. (If
possible, read the counter first using ETIME?.) The syntax for this remote command is as
follows:
ETIME
Description:
Sets the elapsed time counter to any number of minutes from 0 to 2,147,483,647. The
setting of this counter is read by the ETIME? query, described in the 5700A/5720A
Series II Operator Manual. (Sequential command.)
Parameter:
1. SET_TO
2. Integer, number of minutes
Example:
ETIME SET_TO, 4628000
Using The Fatality? and Fatalclr Commands
The FATALITY? query recovers fault codes that were logged when a fatal problem
occurred. These faults are logged into a separate fault queue. Once the faults are read
from the queue, you can clear the queue by sending the FATALCLR command. The
syntax for these remote commands are as follows:
4-13
5700A/5720A Series II Calibrator
Service Manual
FATALITY?
Description:
Returns the list of the fatal faults logged since the list was last cleared by the
FATALCLR command. (Sequential command.)
Parameter:
None
Response:
(String) The list of faults, one per line in the following format:
Frequently asked questions
What makes Elite.Parts unique?

What kind of warranty will the 761031 have?

Which carriers does Elite.Parts work with?

Will Elite.Parts sell to me even though I live outside the USA?

I have a preferred payment method. Will Elite.Parts accept it?

What they say about us
FANTASTIC RESOURCE
One of our top priorities is maintaining our business with precision, and we are constantly looking for affiliates that can help us achieve our goal. With the aid of GID Industrial, our obsolete product management has never been more efficient. They have been a great resource to our company, and have quickly become a go-to supplier on our list!
Bucher Emhart Glass
EXCELLENT SERVICE
With our strict fundamentals and high expectations, we were surprised when we came across GID Industrial and their competitive pricing. When we approached them with our issue, they were incredibly confident in being able to provide us with a seamless solution at the best price for us. GID Industrial quickly understood our needs and provided us with excellent service, as well as fully tested product to ensure what we received would be the right fit for our company.
Fuji
HARD TO FIND A BETTER PROVIDER
Our company provides services to aid in the manufacture of technological products, such as semiconductors and flat panel displays, and often searching for distributors of obsolete product we require can waste time and money. Finding GID Industrial proved to be a great asset to our company, with cost effective solutions and superior knowledge on all of their materials, it’d be hard to find a better provider of obsolete or hard to find products.
Applied Materials
CONSISTENTLY DELIVERS QUALITY SOLUTIONS
Over the years, the equipment used in our company becomes discontinued, but they’re still of great use to us and our customers. Once these products are no longer available through the manufacturer, finding a reliable, quick supplier is a necessity, and luckily for us, GID Industrial has provided the most trustworthy, quality solutions to our obsolete component needs.
Nidec Vamco
TERRIFIC RESOURCE
This company has been a terrific help to us (I work for Trican Well Service) in sourcing the Micron Ram Memory we needed for our Siemens computers. Great service! And great pricing! I know when the product is shipping and when it will arrive, all the way through the ordering process.
Trican Well Service
GO TO SOURCE
When I can't find an obsolete part, I first call GID and they'll come up with my parts every time. Great customer service and follow up as well. Scott emails me from time to time to touch base and see if we're having trouble finding something.....which is often with our 25 yr old equipment.
ConAgra Foods