CYBEROPTICS SEMICONDUCTOR WaferSense
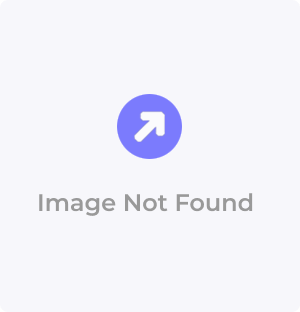
Description
CyberOptics Semiconductor WaferSense Auto Teaching System (ATS) | for 200 mm and 300 mm TEL CLEAN TRACK ACT and Mark Tools
Part Number
WaferSense
Price
Request Quote
Manufacturer
CYBEROPTICS SEMICONDUCTOR
Lead Time
Request Quote
Category
PRODUCTS - W
Datasheet
Extracted Text
Innovating measurement technology™ ® Using WaferSense Auto Teaching System (ATS) on 200 mm and 300 mm TEL CLEAN TRACK ACT and Mark Tools Why Precision Calibration and Handoff Teaching is Critical on TEL CLEAN TRACK ACT and Mark Tools 1. Better resist uniformity 2. Recommended or required as part of routine PM’s 3. Required after robot, lift-pin, platen or other component replacements 4. Increased yield due to reduced particle generation with proper alignments and setups 5. Reduced scrap and wafer damage due to misalignments and mishandling 6. Required when system reports wafer placement errors 7. Necessary when troubleshooting unexplained problems such as excessive particles, unexpected tool noises, or unexplained abnormal Wafer placements must be exactly within 0.75 mm of each of 6 spacers – A difficult, imprecise, and time consuming procedure without ATS considering each chamber & Pinset combination must be independently taught 1 | Page CyberOptics Semiconductor WaferSense ATS on TEL Clean Track ACT and Mark Tools Legacy TEL CLEAN TRACK Position Teaching & Quick-check Methods CCD Wired CCD with cross-hair painted on lens on attached to a wafer with video & power wires running to a small 3” low resolution handheld portable TV. Manually placed into each chamber and/or Pinset chamber CCD Centering Tool Dummy Wafer Dummy wafer is ran though tool while tech listens for scraps and “where possible” watches for misalignments Centering Tool Consists of a centering pin that fits in the Chiller/heater center hole and a special wafer with a round indentation in the center where the wafer is placed on the pin. ® ® IIn nt tr ro od du uc ciin ng g W Wa af fe er rS Se en ns se e Automatic Teaching System (ATS) Teaches CLEAN TRACK Wafer Automatic Teaching System (ATS) Teaches CLEAN TRACK Wafer Hand-off Positions & Performs Quick-Checks Hand-off Positions & Performs Quick-Checks Wafer-like, wireless hardware Intuitive software Image of Target Feature acquired by ATS camera 2 | Page CyberOptics Semiconductor WaferSense ATS on TEL CLEAN TRACK ACT and Mark Tools ATS vs. Legacy Method Feature and Benefit Comparison Benefit ATS CCD Centering Tool 1. Can be passed YES: Passed through tool NO:Device is thick (approx NO: Requires tool dismantling to each chamber automatically without tool 28 mm), wired and and hand placement of wafer or teach location dismantling or bringing off‐line requires tool dismantling and centering pin into each automatically like and hand placement into chamber a wafer each chamber or Pinset 2. Objective and YES: Precision calibrated to 100um NO:No objective output NO: Trial and error processing accurate accuracy and powerful vision and users routinely report where one tech operates numerical system locates pedestal center & cross‐hair painted on CCD robot and the other watches “Answers Out” displays Z, X & Z offsets with ultra‐ lens inaccurate. until the wafer “appears” to high 100um precision accuracy be properly placed 3. Chambers and YES: Discrete X, Y & Z offsets NO:Tool must be NO: Tool must be dismantle Pinsets easily instantly calculated, one chamber dismantle; power and and wafer hand placed then taught by one typically taught in 3 minutes by video cables routed, CCD two techs, one at console and tech one tech without taking tool hand placed and then two one at chamber necessary to offline techs, one at console and perform teaching by trial‐&‐ one at chamber required error 4. Repeatable YES: ATS provides same identical NO:Quality of results NO: Quality of results results objective precision result dependant on skill of tech dependant on skill of tech regardless of tech performing performing procedure and performing procedure and procedure limited by poor accuracy of limited by poor accuracy of device device 5. Chambers YES: 3‐5 minutes average per NO:15 to 20 minutes per NO: 15 to 20 minutes per taught quickly chamber with special maintenance chamber‐ includes tool chamber‐ includes tool recipes disassembly, running disassembly, hand‐placing device wires, hand‐placing wafer, trial‐&‐error wafer CCD and tool re‐assembly placements and tool re‐ assembly 6. Entire tool YES: Typically completed in 2 NO:Typically 8 to 12 hours NO: Typically 8 to 12 hours hand‐off teaching hours or less with maintenance depending on experience depending on experience of procedure recipes to move ATS from of Techs performing Techs performing procedure completed chamber to chamber procedure quickly 7. Guaranteed YES: 100um accuracy regardless of NO:Accuracy limited by NO: Accuracy limited by accurate results tech technology and tech technology and tech experience experience 8. Accurate YES: Typically completed in 15 NO:Quick‐checks not NO: Quick‐checks not possible Quick‐checks minutes or less with 100um possible with CCD with centering wafer possible accuracy (using maintenance recipes) 3 | Page CyberOptics Semiconductor WaferSense ATS on TEL CLEAN TRACK ACT and Mark Tools ATS Procedure for Tel Track 200 mm and 300 mm Module Position Teaching: 1. Power down tool and hookup teaching laptop 2. Power-up tool in Position Teaching mode 3. Place ATS in FI cassette 4. Select predefined ATS teach recipe for Pinset 1 5. To get ATS past load-port, place target wafer in cassette and pickup with FI robot, then before going into chamber, pause robot and swap with ATS before going into slit valve. 6. Follow TEL procedures for position teaching of all chambers. Teach Pinset 1 and Pinset 2 on all Hot-plates and Chill-plate spinners. Note: If using ATS to teach Spinner, DO NOT SPIN ATS. This risks damaging ATS and/or tool No need to open No need to open tool or hand-place tool or hand-place device with ATS device with ATS 4 | Page CyberOptics Semiconductor WaferSense ATS on TEL CLEAN TRACK ACT and Mark Tools Using ATS for Quick-checks: Background: • Dummy wafer is transferred though the tool by one tech while another tech listens for suspicious noises and when possible watches for wafer-misplacements. • NOT an effective or a repeatable method for identifying and correcting wafer placement issues. • Neither the CCD or Centering wafers are used for quick-checks since they must be “hand- placed” and consequently do not simulate actual wafer placements Quick-check Procedure with ATS 1. Place ATS load-port cassette and load into tool (see previous slide step 5 for instructions on getting ATS into tool). 2. Using a predefined ATS maintenance recipe which alternates Pinset 1, Pinset 2, send ATS into each chamber and check for wafer placement. 3. Using a predefined ATS maintenance recipe which alternates Pinset 2, Pinset 1, send ATS into each chamber and check for wafer placement 4. Using a predefined ATS maintenance recipe which checks Pinset 3 placement. 5. Typically 15 seconds per chamber and 10 minutes for the entire tool is all that is necessary with ATS Benefit Summary of Using ATS for CLEAN TRACK Handoff Teaching Event ATS Benefit Over Old Method Quick-checks • Quick-checks not possible with CCD or Centering wafer • ATS provides precision X, Y, and Z offsets accurate to 100um with-in 15 seconds Tool dismantling • Not necessary, ATS travels to all tool locations just like a wafer Manpower requirements • Only one tech needed with ATS. All TEL legacy methods require two techs Accessing difficult tool • ATS transferred via tool automation and goes all places that a wafer goes locations Time required to teach • Position teaching of entire tool completed in 2 hours or less compared to 6 entire tool to 12 hours with legacy Tool alignments and quick • High accuracy: Quick real-time hand-off teaching accurate to 100um handoff checks made with • Repeatable: Quick and easy teaching performed to same high standards ATS regardless of tech performing the procedure • Calibrations performed under ACTUAL closed chamber production conditions • Real-time feedback, no more trial and error • Discrete Go/No go and Data logging, standards can now be established Reassemble tool • No longer necessary to dismantle tool with ATS Restore production • No longer necessary to take off-line with ATS process 5 | Page CyberOptics Semiconductor WaferSense ATS on TEL CLEAN TRACK ACT and Mark Tools WaferSense® ATS Tel Track Use-Case Testimonial Interview with a TEL ACT, Mark Photo Department Manager and Active ATS User 1. What tasks are ATS used for on your TEL Mark and ACT tools? We use ATS for a number of tool maintenance tasks including routine PM’s, quick-checks, and troubleshooting mechanical or process yield related problems 2. How often is the WaferSense® ATS used for TEL Track setup, maintenance and quick-checks? Typically used once per month per tool for routine PM’s Due to the fact that the ATS makes it quite a bit easier to perform the checks plus provides “instant” results we use ATS several time per month “on the fly” to perform quick-checks. ATS is particularly useful for not only troubleshooting wafer placement related system alarms, but also correcting them in real-time without having to take the tool off-line 3. What is the time saving per TEL ACT or Mark Track tool taught using the WaferSense system vs. the old Legacy CCD or Centering Wafer Method? With ATS one tech can typically teach the average Track or Mark tool in about 2 hours compared to two techs in 8 to 12 hours using the CCD method. With the TEL CCD, every chamber had to be opened up, video and powers ran such that the did get tangled, then one tech needed to observe wafer movement while the other operated to the console laptop in teach mode. This is all very time consuming and no reliable. There have been a number of occasions where the power and video wires got hung-up in the tool and actually caused damage. With ATS, we just place the ATS in the tool, move it to each teach position, teach and the move on. 4. What quantifiable benefits have been observed using the ATS system as a result of the increased accuracy of the setups? Consistency is one of the biggest factors. We no longer have to depend on ability of individual techs to determining the accuracy and quality of the position teaching. All techs will achieve the same quick and accurate results Ease of use due to form factor allows for quick-checks and troubleshooting of issues which were previously never checked before because no adequate method existed to perform these checks 5. Have you observed other benefits such as reduced particles, reduced wafer damage, increased yield, or reduced tool down-time? If so, what types of specific quantifiable benefits have you had? Reduced down time would be greatest factor so far. Other less quantifiable benefits, but certainly and important benefit is fewer defects or problem passed down-line. For example, if resist uniformity is off due to poor wafer placement, this wafer could be passed on down the production line and the problem not identified until some later step. 6 | Page CyberOptics Semiconductor WaferSense ATS on TEL CLEAN TRACK ACT and Mark Tools
Frequently asked questions
What makes Elite.Parts unique?

What kind of warranty will the WaferSense have?

Which carriers does Elite.Parts work with?

Will Elite.Parts sell to me even though I live outside the USA?

I have a preferred payment method. Will Elite.Parts accept it?

What they say about us
FANTASTIC RESOURCE
One of our top priorities is maintaining our business with precision, and we are constantly looking for affiliates that can help us achieve our goal. With the aid of GID Industrial, our obsolete product management has never been more efficient. They have been a great resource to our company, and have quickly become a go-to supplier on our list!
Bucher Emhart Glass
EXCELLENT SERVICE
With our strict fundamentals and high expectations, we were surprised when we came across GID Industrial and their competitive pricing. When we approached them with our issue, they were incredibly confident in being able to provide us with a seamless solution at the best price for us. GID Industrial quickly understood our needs and provided us with excellent service, as well as fully tested product to ensure what we received would be the right fit for our company.
Fuji
HARD TO FIND A BETTER PROVIDER
Our company provides services to aid in the manufacture of technological products, such as semiconductors and flat panel displays, and often searching for distributors of obsolete product we require can waste time and money. Finding GID Industrial proved to be a great asset to our company, with cost effective solutions and superior knowledge on all of their materials, it’d be hard to find a better provider of obsolete or hard to find products.
Applied Materials
CONSISTENTLY DELIVERS QUALITY SOLUTIONS
Over the years, the equipment used in our company becomes discontinued, but they’re still of great use to us and our customers. Once these products are no longer available through the manufacturer, finding a reliable, quick supplier is a necessity, and luckily for us, GID Industrial has provided the most trustworthy, quality solutions to our obsolete component needs.
Nidec Vamco
TERRIFIC RESOURCE
This company has been a terrific help to us (I work for Trican Well Service) in sourcing the Micron Ram Memory we needed for our Siemens computers. Great service! And great pricing! I know when the product is shipping and when it will arrive, all the way through the ordering process.
Trican Well Service
GO TO SOURCE
When I can't find an obsolete part, I first call GID and they'll come up with my parts every time. Great customer service and follow up as well. Scott emails me from time to time to touch base and see if we're having trouble finding something.....which is often with our 25 yr old equipment.
ConAgra Foods