CHARLES INDUSTRIES 91-360386-A
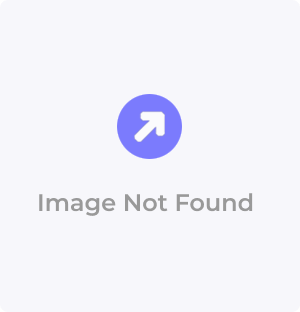
Description
E1 CONTROLLER W/SNMP
Part Number
91-360386-A
Price
Request Quote
Manufacturer
CHARLES INDUSTRIES
Lead Time
Request Quote
Category
PRODUCTS - 9
Datasheet
Extracted Text
Section 360-386-201 Equipment Issue 1 Telecommunications Group Printing 4, December 2006 E1 Controller with SNMP (3603-86) CONTENTS PAGE Part 1. GENERAL . . . . . . . . . . . . . . . . . . . . . . . . . . . . . . . . . . . . . . . . . . . . . . . . . . . . . . . . . . . . . . . . . . . . . . . . . . . . . 2 Part 2. INSPECTION . . . . . . . . . . . . . . . . . . . . . . . . . . . . . . . . . . . . . . . . . . . . . . . . . . . . . . . . . . . . . . . . . . . . . . . . . . . 4 Part 3. APPLICATION GUIDELINES . . . . . . . . . . . . . . . . . . . . . . . . . . . . . . . . . . . . . . . . . . . . . . . . . . . . . . . . . . . . . 4 Part 4. TIMESLOT ALLOCATION . . . . . . . . . . . . . . . . . . . . . . . . . . . . . . . . . . . . . . . . . . . . . . . . . . . . . . . . . . . . . . . 6 Part 5. INSTALLATION . . . . . . . . . . . . . . . . . . . . . . . . . . . . . . . . . . . . . . . . . . . . . . . . . . . . . . . . . . . . . . . . . . . . . . . . . 7 Part 6. OPTIONING . . . . . . . . . . . . . . . . . . . . . . . . . . . . . . . . . . . . . . . . . . . . . . . . . . . . . . . . . . . . . . . . . . . . . . . . . . . 10 Part 7. ALARMS . . . . . . . . . . . . . . . . . . . . . . . . . . . . . . . . . . . . . . . . . . . . . . . . . . . . . . . . . . . . . . . . . . . . . . . . . . . . . 11 Part 8. NETWORK MANAGEMENT . . . . . . . . . . . . . . . . . . . . . . . . . . . . . . . . . . . . . . . . . . . . . . . . . . . . . . . . . . . . . 11 Part 9. TECHNICAL ASSISTANCE . . . . . . . . . . . . . . . . . . . . . . . . . . . . . . . . . . . . . . . . . . . . . . . . . . . . . . . . . . . . . 12 Part 10. WARRANTY & CUSTOMER SERVICE . . . . . . . . . . . . . . . . . . . . . . . . . . . . . . . . . . . . . . . . . . . . . . . . . . . 12 Part 11. SPECIFICATIONS . . . . . . . . . . . . . . . . . . . . . . . . . . . . . . . . . . . . . . . . . . . . . . . . . . . . . . . . . . . . . . . . . . . . . 13 MON ADDRESS AR AY 3603−86 PRI + E1 TP LP ID PWR RCV XMT ACO MGMT Figure 1. E1 Controller Unit Front Panel (3603-86) �2006 Charles Industries Ltd. All rights reserved. Printed in United States of America. The availability of features and technical specifications herein subject to change without notice. Page 1 of 16 Section 360-386-201 1. GENERAL 1.1 Document Purpose This document provides general, installation and testing information for the E1 Controller Unit (E1-S), shown in Figure 1. This document covers model number 3603-86. 1.2 Equipment Function The E1-S is part of the 360-80 Intelligent Channel Bank (ICB). It combines the functions of a line interface unit (LIU) and a channel service unit (CSU), allowing direct connections to public E1 networks. 1.3 Equipment Location/Mounting Mount the E1-S in the primary slot of the 360-80. One controller unit must be installed in the primary slot for prop- er system operation. 1.4 Reference Documentation � 360-80 ICB Craft Port User’s Guide (LT360−386−C01) � SNMP Network Node Manager Guide (LT360−386−N01) � Network Management Software Guide (LT360−386−S01) � 3608−85 Secondary E1 unit (LT360−885−201) 1.5 Equipment Features This unit provides the following features: � Front panel craft interface. � Ethernet network management interface (10/100 Base-T Full/Half Duplex). � Front panel status LEDs. � Non-volatile storage of system provisioning and performance. � Front panel address switch for network management. � Front panel E1 monitor jacks. � Dry contacts for alarm indication. � Allows internal, loop (recovered from E1) or external (composite clock) timing source. � Drop and reinsert operation with additional card (3608-85). � Interfaces with HDSL/HDSL2 with adaptor kit. � Time slot assignment on a per-channel basis. � Auto framing and identification − two formats: 1. Conventional, CAS, 2. CRC4−CAS � 0 dB digital test tone for equipment level adjustments. � Tone test generation and detection on a per-channel basis. � Hot unit insertion or extraction. � 30-channel E1 multiplexing operation. � Temperature hardened (−40 to +65 C). 2 Section 360-386-201 � Performs local E1 loopback, test and performance monitoring of the E1 interface. � Complies with UL1950, FCC part 68 and FCC part 15. � Meets Bellcore 1089, 43801, 62411, TR-57 and ITU-T G.703, G704, Q.421 standards for E1. 1.6 Performance History This unit stores performance history for the last 30 days in 24 hour intervals and over the last 24 hours in 15-min- ute intervals. This performance history includes failed seconds, errored seconds (ES) and severely errored sec- onds (SES) (per E1M1.3/93-00). A reset is provided for the current 15-minute interval. A reset is also provided for the current 24 hour interval and will reset all 15-minute intervals within that 24 hour period. 1.7 Network Management Interface The ICB stores all configuration settings in the E1-S. This unit is managed through the Network Management In- terface (NMI), which controls the provisioning of the unit and obtains status information from the unit. This is achieved through the craft interface using RS232, SNMP using Ethernet or a proprietary graphical interface using Ethernet. For operation of this interface, see the Craft Port documentation, SNMP Network Node Manager docu- mentation or Network Management Software documentation. This unit is shipped with default provisioning for all units in the ICB. Provisioning is altered through the software interface. If the provisioning is changed, it will maintain the new provisioning even if power is lost. If replaced with a new unit, the new unit’s provisioning must be changed to the same provisioning as was set for the prior unit. The unit provides two levels in which provisioning can be reset. “Provisioning Reset to Stored Value” will soft re- set the ICB. “Provisioning Reset to Factory Defaults” will clear all settings for provisioning, timeslots and IP infor- mation. A Real-Time Clock (RTC) is provided through the Network Management interface. 1.8 Status Indicators This unit is able to provide a variety of status information. The following is a list of all status information available from the E1-S. Some status information is also provided through front panel LEDs. See individual channel units for additional status information. � Red (AR) Alarm Status (LED) � Yellow (AY) Alarm Status (LED) � Loss of frame (LOF) Alarm Status � Loss of signal (LOS) Alarm Status � Power status (LED) � E1 framing selected � Trunk processing (TP) status (LED) � Transmit E1 timing source � E1 loopback selected (LED) � Carrier Group Alarm Immediate (CGAI) action � Carrier Group Alarm Delayed (CGAD) action � Remote terminal status in a CO/RT configuration � Tone/pattern test generator and error detection 1.9 Loopbacks The E1-S provides the following type of loopback. � Near-End Line Loopback 3 Section 360-386-201 The near-end line loopback transmits information back to the customer or drop side. 1.10 Testing The E1-S card provides test tones for analog voice card testing that can be enabled using the network manage- ment interface. The E1-S also provides a V.54 loopback code generator for testing 64xN data cards. 2. INSPECTION 2.1 Inspect for Damages Inspect the equipment thoroughly upon delivery. If the equipment has been damaged in transit, immediately re- port the extent of damage to the transportation company. 2.2 Equipment Identification Charles Industries’ equipment is identified by a model and issue number imprinted on the front panel or located elsewhere on the equipment. Each time a major engineering design change is made on the equipment, the issue number is advanced by 1 and imprinted on subsequent units manufactured. Therefore, be sure to include both the model number and its issue number when making inquiries about the equipment. 2.3 Static Concerns Each unit is shipped in static-protective packaging to prevent damages from electrostatic charges. Use approved static-preventive measures, such as static-conductive wrist straps and a static-dissipative mat, when handling units outside of their protective packaging. A unit intended for future use should be tested as soon as possible and returned to its original protective packaging for storage. STATIC-SENSITIVE This equipment contains static-sensitive electronic devices. To prevent electrostatic charges from damaging static-sensitive units: � Use approved static-preventive measures (such as static-conductive wrist straps and static-dissipa- tive mats) at all times whenever touching units outside of their original, shipped, protective packaging. � Do not ship or store units near strong electrostatic, electromagnetic, or magnetic fields. � Always use the original static-protective packaging for shipping or storage. Return a tested unit to its original protective packaging for storage. 3. APPLICATION GUIDELINES A typical application of the 360-80 Intelligent Channel Bank (ICB) system using the E1-S is to provide an interface between the bipolar E1 signal from the public E1 network and data or voice interface units. The E1-S can inter- face to a powered line that uses line-powered repeaters. See Figure 2 and Figure 3 for typical applications. 4 Section 360-386-201 360−80 360−80 CH 1 voice CH 1 voice CH 2 voice CH 2 voice E1 CH 3 voice CH 3 voice 2.048 MB/s . . . . Facility . . voice voice CH 7 CH 7 E1−S E1−S . . . . . . 384 Kb 384 Kb CH 13 CH 13 384 Kb CH 14 384 Kb CH 14 CH 15 56 Kb CH 15 56 Kb . . . . . . 384 Kb 384 Kb CH 18 CH 18 time- 12 3 4 5678 9 10 11 12 13 14 15 17 18 19 20 21 22 23 24 25 26 27 28 29 30 31 slot: physical 7 channel: 13 3 12 18 14 15 384 Kb 64 Kb ea. 384Kb 384 Kb 56 Kb 64 Kb rate: Figure 2. Application #1, Point-Point Full E1 360−80 360−80 Fractional CH 3 CH 3 voice voice E1 voice voice CH 4 CH 4 Facility voice voice 2.048 Mb/s CH 5 CH 5 . . . . E1−S E1−S . . 9.6 Kb 9.6 Kb CH 13 CH 13 CH 14 64 Kb CH 14 64 Kb 56 Kb CH 15 CH 15 56 Kb 19.2 Kb CH 16 CH 16 19.2 Kb time- 12 3 4 56 789 10 11 12 13 14 15 17 18 19 20 21 22 23 24 25 26 27 28 29 30 31 slot: physical 3 45 14 1316 15 channel: 64 9.6 19.2 56 rate: Kb ea. Kb Kb Kb Figure 3. Application #2, Point-Point Fractional E1 3.1 Point-to-Point Applications The 360-80 ICB can be used in point-to-point applications, as shown in Figure 2, and can transport a mix of voice and data traffic. In these applications, the 360-80 ICB multiplexers are interconnected via a 2.048 Mb/s E1 facility. This facility can be a leased public network channel or a private, dedicated facility. Figure 2 shows how the 360-80 ICB maps the physical channel unit positions into E1 facility time slots. The par- ticular mapping shown is for example only; any physical slot can be mapped into any time-slot. The only restric- tion to the mapping is that channel units whose bandwidth occupies more than one 64KB time-slot must map their bandwidth into adjacent time slots and cannot use timeslot 16 (this channel is for signalling information). Figure 3 shows a similar application, except the facility is fractional “E1”. The 360-80 ICB maps the physical slots into the first eight time slots and places “all ones” in the remaining time slots. 5 Section 360-386-201 3.2 Additional Application with Optional Secondary E1 unit. When equipped with a Secondary E1 unit (SE1U) in addition to the E1−S, Drop and Re−insert is available. For additonal information, see the documentation of the Secondary E1 unit. 3.2.1. Drop and Re-Insert Mode Drop and Re-insert mode allows the primary E1 from the E1-S to be connected to a channel bank toward the net- work (west) and the secondary E1 from the SE1U to be connected to a channel bank toward a remote location (east). The data/voice on the Primary E1 can be “dropped” to any one of the cards in the 360-80. Any data/voice that is not “dropped” to a card in the 360-80 can be reinserted into the E1 on the SE1U and sent to the remote location. Data/voice from dropped channels is reinserted on the E1 in the same direction it was dropped from. For example, data/voice dropped from the west would be reinserted toward the west. The same would be true from the east. Additionally, data/voice from cards in the 360-80 can be “re-inserted” into any vacant timeslots to a remote loca- tion. This allows better use of the E1 timeslots by keeping them as full as possible between locations. See Figure 4 for an application in which the 360-80 is used to “drop” dedicated circuits on a E1 and then send the switched voice to a PBX. See Figure 5 for an application where the 360-80 is used to “drop” channels and re-in- sert channels from multiple locations to reduce the number of E1s needed between locations by keeping the E1 full. A channel that is dropped and reinserted can terminate on any ICB along it’s path. E1 Local PBX 360-80 ICB E1 Trunk Full E1 facility@ 2.048MB/s Drop and re-insert data channels to data equipment Figure 4. Drop and Re-Insert Application #1 “West” Terminal MUX “East” Site 1 Site 2 1 AB C 2 360-80 ICB 360-80 ICB 360-80 ICB 3 4 30 20 20 Channels Channels Channels “Drop & Re-Insert” “Terminate” “Drop & Re-Insert” 10 channels west 20 channels 10 channels west 29 and 10 channels east 30 Figure 5. Drop and Re-Insert Application #2 3.3 HDSL/HDSL2 Applications Using an adaptor kit (97-001787 DSL Adaptor) the ICB can house a 200-mechanics DSL converter unit. This unit plugs in to the half-size slot of the ICB and provides an interface between the DSL and the DSL to E1 converter unit. The standard DSL adaptor kit provides the interface connections between the incoming DSL and the converter card, and a E1 output jack and a cable to connect the adaptor and the E1 control unit. Note: When using HDSL modules for E1 transport, you may experience some problems with communication using the E1 facility data link (embedded operations channel) due to the E1 to DSL conversion/synchro- nization process. 6 Section 360-386-201 See the documentation for the kit for more information. 4. TIMESLOT ALLOCATION 4.1 Default Timeslot Allocation The E1−S uses timeslot allocation to control the routing of data that is sent and received on its E1 interfaces. The E1 has 30 timeslots, each timeslot can be allocated to any of the channels on any card in the 360−80 system. When a new channel card is installed in the system or a system reset to factory default values is performed, the default timeslot allocation will be used by the E1−S. When a new card is installed in a system and some of its fac- tory default timeslots have already been allocated to other channels, the timeslot allocation will be different than the factory default. For the 360−80 system, the channel number associated with a circuit on a channel card is based on the chassis slot and the circuit on the card. The table below shows the relationship between the slot, channel numbers and default timeslots for the channels. It also shows the default number of timeslots per channel (TS/Chan). See indi- vidual channel card documentation for more information on timeslot allocation. Slot 1 (lower) Slot 2 (upper) Half Size Card Slot TS/ Channel Default Channel Default Channel Default Module Chan Numbers Timeslots Numbers Timeslots Numbers Timeslots 3632−80 1 1−12 1−12 13−24 13−15, −− −− 17−25 3633−80 3652−80 3657−85 3658−85 3634−80 2 1−6 1−12 13−18 13−15, −− −− 17−25 3638−80 3 1−4 1−12 13−16 13−15, −− −− 17−25 3641−80 12 1 1−12 13 13−15, −− −− 17−25 3632−81 1 −− −− −− −− 25−30 26−31 3633−81 3652−81 3657−86 3658−86 3634−81 2 −− −− −− −− 25−27 26−31 3638−81 3 −− −− −− −− 25−26 26−31 4.2 Timeslot Allocation Timeslot allocation is done through SNMP, NMS or the craft interface. To allocate a timeslot to a channel on a card in the system, the timeslot must not be allocated to another channel. If the timeslot has already been allo- cated, the timeslot must be unallocated by selecting the channel (chassis slot) where it is currently allocated and then deleting it from the timeslot. For example, in Figure 6 timeslot 13 was allocated to channel 16. To allocate it to channel 20 it must first be unallocated from channel 16, then re-allocated to channel 20. Any non-allocated timeslots can be allocated to any non-allocated channel. A timeslot cannot be allocated to more than one channel.Timeslot allocation is done by selecting the channel (chassis slot) associated with the cir- cuit on the card and then selecting the timeslot to be allocated to that channel. As shown in Figure 6, timeslots 10 to 12 have been allocated to channels 7 to 9. Some units use multiple timeslots per circuit such as 64xN, ISDN, etc. The timeslots allocated for the circuits on these units must be consecutive. In Figure 6 channel 24 has been allocated to timeslots 23 through 25. Selecting the circuit and then the first timeslot will allocate the correct number of timeslots for the circuit. The system 7 Section 360-386-201 checks to make sure enough timeslots are available for the circuit, and if there are not enough consecutive time- slots, an error message will be displayed. The E1-S will transmit an all 1’s signal for any timeslot of the E1 that is not allocated. Any received data in a non- allocated timeslot will not be sent to a channel card. Primary E1 1 2 3 4 5 6 7 8 9 10 11 12 13 14 15 17 18 19 20 21 22 23 24 25 26 27 28 29 30 31 Timeslot 1 2 3 4 5 6 7 8 9 10 11 12 13 14 15 16 17 18 19 20 21 22 23 24 25 26 27 28 29 30 Channel Figure 6. Timeslot Allocation w/E1-S 4.3 Timeslot Allocation with a T1-S and the Secondary T1 Unit (3608-85) When the E1-S is used in conjunction with a secondary E1 unit (SE1U), 60 timeslots are available for allocation (30 for the E1-S and 30 for the SE1U). The timeslot allocation process is similar to that used for the E1-S only. See the section on timeslot allocation in the Secondary E1 documentation for more information. 5. INSTALLATION 5.1 Installing the Unit The E1-S installs in the primary slot of the 360-80. A Secondary E1 unit may be mounted in the secondary slot for Drop and Re−insert applications. See Figure 7 for a sample of the shelf layout. Multichannel unit or Secondary E1 Multichannel Unit (channels 25−30) (channels 13−24) HDSL/HDSL2 Unit with Adaptor Multichannel Unit Primary E1 Controller (E1-S) (channels 1−12) Figure 7. 360-80 ICB Common Equipment Configuration 5.1.1. Attaching the Rear Panel The rear panel of the unit should be installed before the units are installed in the shelf, and before wiring begins. 8 Section 360-386-201 CCLK ALM −48V + + IN OUT AUD VIS FUSE 4A −48VR OUT PRI NETWORK IN E1 MGMT CCLK + TERM + J1 J2 TERM 3 pin connector— Berg connector Screw terminal block normally between top and middle 4 pin screw ter- 4 pin screw ter- pin minal connector minal connector Figure 8. 3603-86 E1-S Rear Panel with Primary Slot Used ONLY 5.1.2. Installing a New Unit Use the following steps to install the E1-S. Step Action 1. If not already installed, install the rear panel, screwing it to the appropriate mounting locations on the shelf using the provided hardware. WARNING Due to mechanical differences the E1-S card can only be installed in Issue 3 or greater ICB shelves. If there is already a rear panel installed on the shelf, check for interference when installing. The rear panel may need to be removed and replaced with the rear panel that has been shipped with the new unit. 2. Insert the unit into the shelf, making sure that the unit is aligned with the card guides inside the shelf. 3. Slide the unit fully into the shelf. Use the insertion lever to fully seat the unit. 4. Once the unit is fully inserted, tighten the securing screw on the front panel of the unit. 5. When power is applied, the unit will perform a self-test. 6. Wire the unit per the wiring information in the wiring section. 7. After the self-test is performed, check the software provisioning of the card using the front panel craft interface on the front of the controller unit. 5.1.3. Installing a Replacement Unit If you are replacing a unit that is already in service, insure that the new unit is the same as the unit being re- placed. Step Action 1. Remove the wiring connectors from the front and rear of the unit (J1 & J2 if applicable). 2. Unscrew the front panel securing screw to release the unit from the shelf. 3. Using the card ejector, remove the unit from the shelf. 4. Follow the procedure for installing a new unit. 5.2 Wiring the Unit Use the following steps to wire the unit. Step Action 1. Connect E1 to the rear panel RJ48 jack (J1). If a coax (75 Ohm) connection is needed, a Balun 97−001811 is available to convert from twisted pair (120 Ohm) to coax (75 Ohm). 2. If using the Ethernet interface, connect the Ethernet to J2 at the rear of the unit. 9 Section 360-386-201 Step Action 3. Set composite clock termination for your system as described under Hardware Optioning, page 12. 4. If you are using composite clock, remove the connector and wire the signal to the connector CCLK IN. 5. Reinstall the connector with the composite clock signal wires. 6. Power and alarm should already be wired. If not, see the documentation for the ICB shelf. 5.3 Front Panel Switch and LED Definitions The Audible Alarm Cut Off (ACO) switch is a pushbutton used to open the audible alarm contacts from the 360-80 system. This switch will only mask audible indications of present alarm conditions—it does NOT clear the alarm. If a new alarm occurs, the audible indication will re-enable. The Address ID switch on the front panel is a multi-section switch for setting the system address on the system management bus. This switch is used if the system is connected together with other 360-80 systems into a man- agement control center. This switch allows the control center to ‘address’ the individual systems. See section on network management for more information. Table 1. LED Definitions Label Color Status Indicates that... POWER Green ON The unit is receiving power. OFF The unit is not powered. AR Red ON The unit is detecting a red alarm on the E1 interface caused by a loss of signal (LOS) or a loss of framing (LOF) or out of frame (OOF) condition. OFF Normal operation. AY Yellow ON The unit is receiving a YELLOW alarm condition on the E1. This indicates that a problem is upstream at some other device or network node. OFF Normal operation. TP Yellow ON The system is processing trunk signaling data based on detected alarm conditions. OFF Normal operation. LP LP Green Green ON ON The unit is in a loopback condition The unit is in a loopback condition. This indication onl This indication only occurs during testing y occurs during testing. OFF Normal operation. 5.4 Connector Definitions 5.4.1. Bantam Jacks The two bantam jacks on the front of the unit allow monitoring of the transmit (XMT) and receive (RCV) sides of the primary E1 signal without interfering with operation. 5.4.2. Front Panel RJ11 Jack The RJ-11 jack on the front of the unit is the local craft/control port. The default interface is an RS-232 connection that defaults to 9600 baud, 8 bits, 1 stop and no parity. The interface through the control port is VT-100. VT-100 operation on a PC requires VT-100 emulation software. A cable (03-200542-0) is available to connect the front panel RJ11 jack to a DB-9 connector. 10 Section 360-386-201 Table 2. Front Panel RJ11 Jack Pinouts Pin # Use DB9 Pinouts 1 NC 123456 1 2 3 4 5 6 2 GND 5 3 RCV (ICB − input) 3 4 XMIT (ICB + output) 2 5 Enable PC (ICB input) 7 6 NC 5.4.3. E1 Jack The RJ48 connector on the rear of the E1-S is for the primary E1. Table 3. RJ-48C E1 Jack Pinouts Pin # Use 1 R (RCV from network) 2 T (RCV from network 12345678 1 2 3 4 5 6 7 8 3 — 4 R1 (XMIT to network) 5 T1 (XMIT to network) 6 — 7 — 8 — 5.4.4. Rear Panel RJ45 Jack The J2 RJ45 jack on the rear of the unit is for interfacing to a network management control center using SNMP or proprietary NMS/GUI software over Ethernet. An IP address and IP subnet mask must be configured through the craft interface before the unit will communicate with the NMS/GUI or SNMP. To communicate with SNMP, the SNMP community table must also be configured. See the network management section or the network manage- ment interface documentation for more information. The proprietary graphical user interface (GUI) is available through the Ethernet control port. Using the GUI inter- face requires that GUI software be loaded on the controller PC. The front panel craft interface requires only VT-100 emulation software loaded on the controller PC. Table 4. RJ45 Jack Pinouts Pin # Use 1 XMIT (TD+) 2 XMIT (TD−) 1 2 3 4 5 6 7 8 3 RCV (RD+) 4 NC 5 NC 6 RCV (RD−) 7 NC 8 NC 11 Section 360-386-201 6. OPTIONING 6.1 Hardware Optioning Option Type Choices Description Composite 3-pin Termination Place the Berg connector between the middle and bottom pins clock termina- connector to terminate the composite clock input wired to the ICB. This is tion done for a single ICB, or on the last ICB in a “daisy-chained” series. No termina- Place the Berg connector between the top and middle pins to tion remove termination from the composite clock input. This is done when the clock will be connected to additional equipment with a termination. ICB Address Switch set- The default is 00. (address= 1 + tings 00 switch setting) through 15 6.2 Software Optioning This unit comes from the factory with default provisioning, which can be changed through the Network Manage- ment or the craft terminal interface. See the NMS or craft terminal interface documentation for procedures. The provisioning options are as follows with the default optioning noted: Option Choices Default Frame format Conventional CAS, CRC4-CAS CRC4-CAS Transmit E1 Timing Source External, Internal, Looped Internal Test Generator (per channel) Tone Test, 1 KHz 0 dBm0, None None E1 Loopback Selection Loopback, Release None CGA Process Mode Normal, CM2, CM3 Normal Remote Control Method None, Occupy One Channel, Facility Data Link Facility Data Link 7. ALARMS Alarms provide an audible and visual indication that there is something functioning improperly within the system. There are three alarm modes, Normal, CM2 and CM3 on the 360-80 shelf. The E1-S will generate an alarm based on its configuration. If an alarm occurs, pressing the Audible Alarm Cut-off (ACO) switch stops the audible alert associated with the alarm. However, it does not clear the alarm. To clear an alarm, the source of the alarm must be identified. Appar- ent indication of the source will be the unit with the RED alarm displayed. The other units in the network will dis- play a yellow alarm indicating there is a problem somewhere, but not here. 7.1 Alarm Trunk Processing When a loss of signal occurs for 1 to 2.5 seconds, depending on the alarm mode used, a red alarm condition is triggered. The unit where the error occurred will display the red alarm. When using the normal alarm mode and a red condition is present, the other units in the network will display a yellow alarm. CM2 and CM3 modes do not transmit a yellow alarm signal during a red alarm condition. When loss of E1 or a yellow alarm signal is detected in normal mode, CGAI trunk conditioning occurs immediate- ly. CGAD trunk conditioning occurs 2.5 seconds after the alarm is declared. Individual card provisioning deter- mines the conditioning state during CGAI and CGAD. During red alarm conditions in CM2 mode, individual card provisioning determines the conditioning state during CGAI and CGAD. During red alarm conditions in CM3 mode, trunk conditioning is done to “busy” the circuits and ignores the CGAI and CGAD card provisioning. 12 Section 360-386-201 During yellow alarm conditions in CM2 or CM3 modes, no trunk conditioning occurs. Table 5. Duration of Alarms Alarm Normal CM2 CM3 E1 loss to Red Alarm declared 2.5 Sec. 1 Sec. 1 Sec. E1 restore to Trunk Processing (TP) retired 15 Sec. 1 Sec. 1 Sec. Yellow alarm detected to declared < 1 Sec. < 1 Sec. < 1 Sec. Yellow alarm not detected to Trunk Processing (TP) retired < 1 Sec. < 1 Sec. < 1 Sec. Yellow alarm transmitted during alarm Yes No No 8. NETWORK MANAGEMENT The 360-80 channel bank can be managed via three different interfaces. Each interface has a slightly different look and feel however each of them offers similar capabilities. The interfaces available include: � Craft Interface � The Network Management System (NMS) � Network Node Manager (NNM) 8.1 Craft Interface The craft interface is a menu based ASCII interface that utilizes the RS-232 port on the front of the E1-S. This interface utilizes any generic terminal emulation program loaded on a PC or similar equipment to operate. In this configuration the craft interface can only provision and monitor the 360-80 channel bank it is connected to. Visibil- ity to other remote or local 360-80 channel banks is not provided. The craft interface is used to establish the IP address required by the other management interfaces. It is also used to establish the SNMP community parameters required when using the NNM interface. A cable adaptor is available to connect between the RJ-11 connector on the card front panel and a standard DB-9 connection to a terminal or PC serial port. See the documentation provided with the craft interface for more infor- mation. 8.2 Network Management System Interface The NMS interface is a Graphical User Interface (GUI) based software package that is shipped with each unit on CD-ROM. This interface assumes that the NMS software package is loaded and running on a PC connected to the same Ethernet network as the E1-S card. Up to 16 local 360-80 channel banks can be provisioned and moni- tored with the NMS interface. Each local 360-80 can support up to 7 remote 360-80s connected to each local 360-80. To use this interface the IP address for the local E1-S card must be provisioned using the craft interface. A local 360-80 channel bank is a 360-80 that is connected directly to the same network as the managing PC. A remote 360-80 channel bank is a 360-80 that is connected to a local 360-80 over a E1 and the E1 has been provi- sioned for remote control between the local and remote 360-80s. Remote control can utilize either the Embedded Operations Channel (EOC) or can utilize a timeslot on the E1. This is done through the optioning of the E1-S card. For drop and reinsert applications where a remote 360-80 may be connected to another remote 360-80, each 360-80’s E1-S and Secondary E1 card must be optioned for a remote control method between each 360-80. Each remote 360-80 is identified through an addressing scheme utilizing the NMS address of the local 360-80 and the Address ID switch setting on the remote E1-S card. See the NMS documentation for more information. 8.3 Network Node Manager Interface The NNM interface is a Simple Network Management Protocol (SNMP) based interface that utilizes a central SNMP manager software package. This interface assumes that an SNMP manager is present on the same Ether- net network as the E1-S card. In order for the SNMP manager to operate correctly, the Management Information Base (MIB) file included on the CD-ROM that was shipped with the product must be loaded. The NNM interface allows provisioning and monitoring of as many local 360-80s as can be supported by the Ethernet network. Each 13 Section 360-386-201 local 360-80 can support up to 7 remote 360-80s connected to each local 360-80. To use this interface the IP ad- dress and the community information for the E1-S card must be provisioned using the craft interface. A local 360-80 channel bank is a 360-80 that is connected directly to the same network as the managing PC. A remote 360-80 channel bank is a 360-80 that is connected to a local 360-80 over a E1 and the E1 has been provi- sioned for remote control between the local and remote 360-80s. Remote control can either utilize the Embedded Operations Channel (EOC) or can utilize a timeslot in the E1. This is done through the optioning of the E1-S card. For drop and reinsert applications where a remote 360-80 may be connected to another remote 360-80, each 360-80’s E1-S and Secondary E1 card must be optioned for a remote control method between each 360-80. Each remote 360-80 is identified through an addressing scheme utilizing the community information of the local 360-80 and the Address ID switch setting on the remote E1-S card. See the NNM documentation for more information. 9. TECHNICAL ASSISTANCE If technical assistance is required, contact Charles Technical Services Center at: 847-806-8500 847-806-8556 (FAX) 800-607-8500 techserv@charlesindustries.com (e-mail) 10. WARRANTY & CUSTOMER SERVICE 10.1 Warranty Charles offers a 2-year warranty on this product. Contact your local Sales Representative at the address or tele- phone numbers below for warranty details. The warranty provisions are subject to change without notice. The terms and conditions applicable to any specific sale of product shall be defined in the resulting sales contract. Charles 5600 Apollo Drive Rolling Meadows, Illinois 60008-4049 U.S.A. 847-806-6300 (Main Office) 847-806-6231 (FAX) 10.2 Field Repairs (In-Warranty Units) Field repairs involving the replacement of components within a unit are not recommended and may void the war- ranty and compatibility with any applicable regulatory or agency requirements. If a unit needs repair, contact Charles for replacement or repair instructions, or follow the Repair Service Procedure below. 10.3 Advanced Replacement Service (In-Warranty Units) Charles offers an “advanced replacement” service if a replacement unit is required as soon as possible. With this service, the unit will be shipped in the fastest manner consistent with the urgency of the situation. In most cases, there are no charges for in-warranty repairs, except for the transportation charges of the unit and for a testing and handling charge for units returned with no trouble found. Upon receipt of the advanced replacement unit, return the out-of-service unit in the carton in which the replacement was shipped, using the pre-addressed shipping label provided. Call your customer service representative at the telephone number above for more details. 10.4 Standard Repair and Replacement Service (Both In-Warranty and Out-Of-Warranty Units) Charles offers a standard repair or exchange service for units either in- or out-of-warranty. With this service, units may be shipped to Charles for either repair and quality testing or exchanged for a replacement unit, as deter- mined by Charles. Follow the Repair Service Procedure below to return units and to secure a repair or replace- ment. A handling charge applies for equipment returned with no trouble found. To obtain more details of this ser- vice and a schedule of prices, contact Charles at 217-932-5292 (FAX 217-932-2943). Repair Service Procedure 1. Prepare, complete, and enclose a purchase order in the box with the equipment to be returned. 14 Section 360-386-201 2. Include the following information: − Company name and address − Contact name and phone number − Inventory of equipment being shipped − Particulars as to the nature of the failure − Return shipping address 3. Ship the equipment, purchase order, and above-listed information, transportation prepaid, to the ser- vice center address shown below. Charles 503 N.E. 15th St, P.O. Box 339 Casey, IL 62420-2054 4. Most repaired or replaced units will be returned within 30 or 45 days, depending on the product type and availability of repair parts. Repaired units are warranted for either 90 days from the date of repair or for the remaining unexpired portion of the original warranty, whichever is longer. 11. SPECIFICATIONS 11.1 Electrical Parameter Specification Carrier Mode Pulse Code Modulation (PCM) Sampling Frequency 8000/s Bits per Channel 8 bits 2.048Mb/S Framing Format E1 interface is compliant with the ITU-T G.703 Convention- al CAS, CRC4-CAS standard Line code HDB3 Input/output impedances 120 Ohms Transmission Rate 2.048 Mb/s ± 32 ppm Channel bank input timing (software selectable) 1: free running timing and composite clock output 2: loop timing (recovered from Receive E1) 3: external timing: composite clock input terminal (on rear panel). E1 connector (rear panel.) RJ-48C PC control interface: RJ11 (RS-232) craft interface (directly connect PC on front panel) Two types of connectors. (RS232 with RJ-11 on the front and RJ45 Ethernet on the rear of the Default: data rate 9600, 8 data bit, 1 stop bit, No parity. ICB) RJ45 network management interface (10/100 Base-T, Half/Full Duplex, auto-detection Ethernet connection) The network management PC interface can control and monitor functionality for both local and remote environ- ments. E1 monitor bantam jacks (On front panel only) This is to monitor the primary E1 signal (monitor transmit and monitor receive) without interference. 15 Section 360-386-201 Parameter Specification Alarm interface and contacts The alarm contact connector is a 4-lead connector rated for 1 amp. One set of isolated contacts each for the audible and visual alarms per PUB-43801. A typical connection is expected to be 18 or 22 gauge wire. The system provides visual and audible alarm contact clo- sure when the channel bank is in alarm or there is a loss of power. When the ACO (Audible Alarm Cut Off) is activated, the audible alarm contacts return to open circuit. Composite clock termination (jumper selectable, IN—135 Ohm termination on composite clock input. rear panel) OUT—No termination on composite clock input. ACO switch (front panel) Use to silence the audible alarm contacts Voice port test pattern generator and detector DTMF tone test sequence for channel testing or 1 KHz 0 (software selectable on a per-channel basis) dBm0 test tone for calibration Power supply input voltage range −42V to −56V Power supply current 0.100 amp Heat dissipation 4.8 watts 11.2 Physical See Table 6 for the physical characteristics of the unit. Table 6. Physical Specifications Feature U.S. Metric Height 0.75 inch 1.9 centimeters Width 5.64 inches 14.32 centimeters Depth 9.25 inches 23.49 centimeters Weight 10.8 ounces 306 grams Temperature −40� to +149� F −40� to +65� C Humidity to < 95% � � � 16
Frequently asked questions
What makes Elite.Parts unique?

What kind of warranty will the 91-360386-A have?

Which carriers does Elite.Parts work with?

Will Elite.Parts sell to me even though I live outside the USA?

I have a preferred payment method. Will Elite.Parts accept it?

What they say about us
FANTASTIC RESOURCE
One of our top priorities is maintaining our business with precision, and we are constantly looking for affiliates that can help us achieve our goal. With the aid of GID Industrial, our obsolete product management has never been more efficient. They have been a great resource to our company, and have quickly become a go-to supplier on our list!
Bucher Emhart Glass
EXCELLENT SERVICE
With our strict fundamentals and high expectations, we were surprised when we came across GID Industrial and their competitive pricing. When we approached them with our issue, they were incredibly confident in being able to provide us with a seamless solution at the best price for us. GID Industrial quickly understood our needs and provided us with excellent service, as well as fully tested product to ensure what we received would be the right fit for our company.
Fuji
HARD TO FIND A BETTER PROVIDER
Our company provides services to aid in the manufacture of technological products, such as semiconductors and flat panel displays, and often searching for distributors of obsolete product we require can waste time and money. Finding GID Industrial proved to be a great asset to our company, with cost effective solutions and superior knowledge on all of their materials, it’d be hard to find a better provider of obsolete or hard to find products.
Applied Materials
CONSISTENTLY DELIVERS QUALITY SOLUTIONS
Over the years, the equipment used in our company becomes discontinued, but they’re still of great use to us and our customers. Once these products are no longer available through the manufacturer, finding a reliable, quick supplier is a necessity, and luckily for us, GID Industrial has provided the most trustworthy, quality solutions to our obsolete component needs.
Nidec Vamco
TERRIFIC RESOURCE
This company has been a terrific help to us (I work for Trican Well Service) in sourcing the Micron Ram Memory we needed for our Siemens computers. Great service! And great pricing! I know when the product is shipping and when it will arrive, all the way through the ordering process.
Trican Well Service
GO TO SOURCE
When I can't find an obsolete part, I first call GID and they'll come up with my parts every time. Great customer service and follow up as well. Scott emails me from time to time to touch base and see if we're having trouble finding something.....which is often with our 25 yr old equipment.
ConAgra Foods