ALLEN BRADLEY 1766-L32BWA
Specifications
Battery Backup
Yes
Certifications
UL Listed Industrial Control Equipment for use in Class 1, Division 2, Hazardous Locations, Groups A, B, C, D, CE marked for all applicable directives, C-Tick marked for all applicable acts
Data Elements
configurable, user-defined file structure, 10 KB max. data size
Data Logging
128 KB (without recipe), 64 KB recipe storage
Embedded LCD
Yes
Ethernet Port
(1) 10/100 EtherNet/IP port
Ethernet Protocols
EtherNet/IP messaging only, Modbus TCP/IP, DNP3 Over IP
Floating Point Math
Yes
High-Speed Inputs (Pulse Catch)
Up to 6 channels @ 100 kHz
Line Voltage
120/240V AC
Memory Size and Type
20 KB battery-backed RAM:10 KB user program, 10 KB user data
Nonoperating Shock
Panel mount: 50 g, DIN mount: 40 g
Nonoperating Temperature
-40…85 °C (-40…185 °F)
Number of Inputs
(12) Fast 24V DC, (8) Normal 24V DC
Number of Outputs
(12) Relay
Online Editing
Yes
Operating Shock
30 g
Operating Temperature
-20…60 °C (-4…140 °F)
PID
Yes (limited by loop and stack memory)
Real-time clock
Yes, embedded
Relative Humidity
5…95% noncondensing
Serial Port
(1) RS-232C/RS-485‡ , (1) RS-232C§
Serial Protocols
DF1 full-duplex, DF1 half-duplex master/slave, DF1 radio modem
Trim Potentiometers
2 digital
Vibration
3 g at 10... 500 Hz
Features
- Built-in LCD with backlight allows you to view controller and I/O status, and provides a simple interface for messages, bit/integer monitoring and manipulation.
- Ethernet port provides web server and e-mail capability.
- Expand your application capabilities through support of up to seven expansion I/O modules (1762 I/O) with 256 digital I/O.
Datasheet
Extracted Text
Installation Instructions MicroLogix 1400 Programmable Controllers Catalog Number(s) 1766-L32AWA, 1766-L32AWAA, 1766-L32BWA, 1766-L32BWAA, 1766-L32BXB, 1766-L32BXBA http://literature.rockwellautomation.com/idc/groups/literature/documents/in/1 766-in001_-mu-p.pdf Cette publication est disponible en français sous forme électronique (fichier PDF). Pour la FR télécharger, rendez-vous sur la page Internet indiquée ci-dessus. Questa pubblicazione è disponibile in Italiano in formato PDF. Per scaricarla collegarsi al sito IT Web indicato sopra. Diese Publikation ist als PDF auf Deutsch verfügbar. Gehen Sie auf die oben genannte DE Web-Adresse, um nach der Publikation zu suchen und sie herunterzuladen. Esta publicación está disponible en español como PDF. Diríjase a la dirección web indicada ES arriba para buscar y descarga esta publicación. Esta publicação está disponível em portugués como PDF. Vá ao endereço web que aparece PT acima para encontrar e fazer download da publicação. Installation Instructions MicroLogix 1400 Programmable Controllers Catalog Number(s) 1766-L32AWA, 1766-L32AWAA, 1766-L32BWA, 1766-L32BWAA, 1766-L32BXB, 1766-L32BXBA Topic Page Important User Information 4 Additional Resources 7 Overview 8 Controller Description 9 Hazardous Location Considerations 11 Mount the Controller 13 Connect 1762 I/O Expansion Modules 18 Wire the Controller 19 Specifications 28 4 MicroLogix 1400 Programmable Controllers Important User Information Solid state equipment has operational characteristics differing from those of electromechanical equipment. Safety Guidelines for the Application, Installation and Maintenance of Solid State Controls (Publication SGI-1.1 available from your local Rockwell Automation sales office or online at http://literature.rockwellautomation.com) describes some important differences between solid state equipment and hard-wired electromechanical devices. Because of this difference, and also because of the wide variety of uses for solid state equipment, all persons responsible for applying this equipment must satisfy themselves that each intended application of this equipment is acceptable. In no event will Rockwell Automation, Inc. be responsible or liable for indirect or consequential damages resulting from the use or application of this equipment. The examples and diagrams in this manual are included solely for illustrative purposes. Because of the many variables and requirements associated with any particular installation, Rockwell Automation, Inc. cannot assume responsibility or liability for actual use based on the examples and diagrams. No patent liability is assumed by Rockwell Automation, Inc. with respect to use of information, circuits, equipment, or software described in this manual. Reproduction of the contents of this manual, in whole or in part, without written permission of Rockwell Automation, Inc., is prohibited. Throughout this manual, when necessary, we use notes to make you aware of safety considerations. WARNING Identifies information about practices or circumstances that can cause an explosion in a hazardous environment, which may lead to personal injury or death, property damage, or economic loss. Identifies information that is critical for successful application and understanding of IMPORTANT the product. ATTENTION Identifies information about practices or circumstances that can lead to personal injury or death, property damage, or economic loss. Attentions help you identify a hazard, avoid a hazard and recognize the consequences. SHOCK HAZARD Labels may be on or inside the equipment (for example, drive or motor) to alert people that dangerous voltage may be present. BURN HAZARD Labels may be on or inside the equipment (for example, drive or motor) to alert people that surfaces may reach dangerous temperatures. Publication 1766-IN001C-EN-P - October 2009 MicroLogix 1400 Programmable Controllers 5 Environment and Enclosure This equipment is intended for use in a Pollution Degree 2 industrial ATTENTION environment, in overvoltage Category II applications (as defined in IEC publication 60664-1), at altitudes up to 2000 meters (6562 ft) without derating. This equipment is considered Group 1, Class A industrial equipment according to IEC/CISPR Publication 11. Without appropriate precautions, there may be potential difficulties ensuring electromagnetic compatibility in other environments due to conducted as well as radiated disturbance. This equipment is supplied as open-type equipment. It must be mounted within an enclosure that is suitably designed for those specific environmental conditions that will be present and appropriately designed to prevent personal injury resulting from accessibility to live parts. The enclosure must have suitable flame-retardant properties to prevent or minimize the spread of flame, complying with a flame spread rating of 5VA, V2, V1, V0 (or equivalent) if non-metallic. The interior of the enclosure must be accessible only by the use of a tool. Subsequent sections of this publication may contain additional information regarding specific enclosure type ratings that are required to comply with certain product safety certifications. Preventing Electrostatic Discharge This equipment is sensitive to electrostatic discharge, which can cause internal ATTENTION damage and affect normal operation. Follow these guidelines when you handle this equipment: • Touch a grounded object to discharge potential static. • Wear an approved grounding wriststrap. • Do not touch connectors or pins on component boards. • Do not touch circuit components inside the equipment. • Use a static-safe workstation, if available. • Store the equipment in appropriate static-safe packaging when not in use. Publication 1766-IN001C-EN-P - October 2009 6 MicroLogix 1400 Programmable Controllers North American Hazardous Location Approval The following modules are North American Hazardous Location approved: 1766-L32AWA, 1766-L32AWAA, 1766-L32BWA, 1766-L32BWAA, 1766-L32BXB, 1766-L32BXBA The following information applies when Informations sur l’utilisation de cet operating this equipment in hazardous équipement en environnements locations: dangereux: Products marked "CL I, DIV 2, GP A, B, C, D" are Les produits marqués "CL I, DIV 2, GP A, B, C, D" ne suitable for use in Class I Division 2 Groups A, B, C, conviennent qu’à une utilisation en environnements D, Hazardous Locations and nonhazardous locations de Classe I Division 2 Groupes A, B, C, D dangereux et only. Each product is supplied with markings on the non dangereux. Chaque produit est livré avec des rating nameplate indicating the hazardous location marquages sur sa plaque d’identification qui temperature code. When combining products within indiquent le code de température pour les a system, the most adverse temperature code environnements dangereux. Lorsque plusieurs (lowest "T" number) may be used to help determine produits sont combinés dans un système, le code de the overall temperature code of the system. température le plus défavorable (code de température Combinations of equipment in your system are le plus faible) peut être utilisé pour déterminer le code subject to investigation by the local Authority Having de température global du système. Les combinaisons Jurisdiction at the time of installation. d’équipements dans le système sont sujettes à inspection par les autorités locales qualifiées au moment de l’installation. EXPLOSION HAZARD RISQUE D’EXPLOSION AVERTISSEMENT WARNING •Do not disconnect while the • Couper le courant ou s’assurer circuit is live or unless the area que l’environnement est classé is known to be free of ignitible non dangereux avant de concentrations. débrancher l'équipement. •Do not disconnect connections • Couper le courant ou s'assurer to this equipment unless power que l’environnement est classé has been removed or the area is non dangereux avant de known to be nonhazardous. débrancher les connecteurs. Fixer Secure any external connections tous les connecteurs externes that mate to this equipment by reliés à cet équipement à l'aide using screws, sliding latches, de vis, loquets coulissants, threaded connectors, or other connecteurs filetés ou autres means provided with this moyens fournis avec ce produit. product. • La substitution de composants • Substitution of components may peut rendre cet équipement impair suitability for Class I, inadapté à une utilisation en Division 2. environnement de Classe I, Division 2. • Do not remove or replace lamps, fuses or plug-in modules (as • S’assurer que l’environnement applicable) unless power has est classé non dangereux avant been disconnected or the area is de changer les piles. known to be free of ignitible concentrations of flammable gases or vapors. Publication 1766-IN001C-EN-P - October 2009 MicroLogix 1400 Programmable Controllers 7 Additional Resources Resource Description MicroLogix 1400 Programmable Controllers User A more detailed description of how to install and use Manual 1766-UM001 your MicroLogix 1400 programmable controller and expansion I/O system. MicroLogix 1400 Instruction Set Reference A reference manual that contains data and function Manual 1766-RM001 files, instruction set, and troubleshooting information for MicroLogix 1400. Installation Instructions 1762-INxxx Information on installing and using 1762 expansion I/O modules. Industrial Automation Wiring and Grounding More information on proper wiring and grounding Guidelines 1770-4.1 techniques. If you would like a manual, you can: • download a free electronic version from the internet: http://literature.rockwellautomation.com • purchase a printed manual by contacting your local Allen-Bradley distributor or Rockwell Automation representative Publication 1766-IN001C-EN-P - October 2009 8 MicroLogix 1400 Programmable Controllers Overview MicroLogix 1400 controllers are suitable for use in an industrial environment when installed in accordance with these instructions. Specifically, this equipment is intended for use in clean, (1) dry environments (Pollution degree 2 ) and with circuits not exceeding Over Voltage (2) (3) Category II (IEC 60664-1) . AC powered products must be connected to the secondary of an isolating transformer. Install your controller using these installation instructions. Debris strip 44513 ATTENTION Do not remove the protective debris strip until after the controller and all other equipment in the panel near the controller are mounted and wiring is complete. Once wiring is complete, remove protective debris strip. Failure to remove strip before operating can cause overheating. ATTENTION Electrostatic discharge can damage semiconductor devices inside the controller. Do not touch the connector pins or other sensitive areas. (1) Pollution Degree 2 is an environment where, normally, only non-conductive pollution occurs except that occasionally a temporary conductivity caused by condensation shall be expected. (2) Over Voltage Category II is the load level section of the electrical distribution system. At this level transient voltages are controlled and do not exceed the impulse voltage capability of the product's insulation. (3) Pollution Degree 2 and Over Voltage Category II are International Electrotechnical commissions (IEC) designations. Publication 1766-IN001C-EN-P - October 2009 MicroLogix 1400 Programmable Controllers 9 Controller Description 125 3 4 6 7 ESC 1 OK 44514 44515 13 12 11 10 9 8 Left side view Top view Description 1 Comm port 2 - 9-pin D-Shell RS-232C connector 2 Memory module (refer to MicroLogix 1400 Memory Module Installation Instructions, publication 1766-IN010 for instructions on installing the memory module). 3 User 24V (for 1766-L32BWA and 1766-L32BWAA only) 4 Input terminal block 5 LCD Display Keypad (ESC, OK, Up, Down, Left, Right) 6 Battery compartment 7 1762 expansion bus connector 8 Battery connector 9 Output terminal block 10 LCD Display 11 Indicator LED panel 12 Comm port 1 - RJ45 connector 13 Comm port 0 - 8-pin mini DIN RS-232C/RS-485 connector Publication 1766-IN001C-EN-P - October 2009 10 MicroLogix 1400 Programmable Controllers Controller Input and Output Description Catalog Description Number Input User Embedded Embedded Comm. Power Power Discrete I/O Analog I/O Ports 12 Fast 24V DC Inputs 1766-L32BWA 24V DC 8 Normal 24V DC Inputs 12 Relay Outputs 100/240V AC 20 120V AC Inputs 1766-L32AWA 12 Relay Outputs None 12 Fast 24V DC Inputs None 8 Normal 24V DC Inputs 1766-L32BXB 24 V DC 6 Relay Outputs 3 Fast DC Outputs (1) 1 RS232 /RS485 3 Normal DC Outputs 1 Ethernet/IP 12 Fast 24V DC Inputs (2) 1 RS232 1766-L32BWAA 24V DC 8 Normal 24V DC Inputs 12 Relay Outputs 100/240V AC 20 120V AC Inputs 1766-L32AWAA 4 Voltage Inputs 12 Relay Outputs 2 Voltage 12 Fast 24V DC Inputs Outputs None 8 Normal 24V DC Inputs 1766-L32BXBA 24V DC 6 Relay Outputs 3 Fast DC Outputs 3 Normal DC Outputs (1) Isolated RS-232/RS-485 combo port. Same as ML1100 Comm 0 (2) Non-isolated RS-232. Standard D-sub connector Publication 1766-IN001C-EN-P - October 2009 MicroLogix 1400 Programmable Controllers 11 Hazardous Location Considerations This equipment is suitable for use in Class I, Division 2, Groups A, B, C, D or non-hazardous locations only. The following WARNING statement applies to use in hazardous locations. EXPLOSION HAZARD WARNING • Substitution of components may impair suitability for Class I, Division 2. • Do not replace components or disconnect equipment unless power has been switched off. • Do not connect or disconnect components unless power has been switched off. • This product must be installed in an enclosure. All cables connected to the product must remain in the enclosure or be protected by conduit or other means. • All wiring must comply with N.E.C. article 501-10(b) and/or in accordance with Section 18-1J2 of the Canadian Electrical Code, and in accordance with the authority having jurisdiction. Use only the following communication cables in Class I, Division 2 hazardous locations. Environment Classification Communication Cables Class I, Division 2 Hazardous Environment 1761-CBL-AC00 Series C or later 1761-CBL-AM00 Series C or later 1761-CBL-AP00 Series C or later 1761-CBL-PM02 Series C or later 1761-CBL-HM02 Series C or later 2707-NC9 Series C or later 1763-NC01 Series A or later 1747-CP3 Series Publication 1766-IN001C-EN-P - October 2009 12 MicroLogix 1400 Programmable Controllers Environnements dangereux Cet équipement est conçu pour une utilisation en environnements dangereux de Classe I, Division 2, Groupes A, B, C, D ou non dangereux. La mise en garde suivante s’applique à utilisation en environnements dangereux. DANGER D’EXPLOSION WARNING • La substitution de composants peut rendre cet équipement impropre à une utilisation en environnement de Classe I, Division 2. • Ne pas remplacer de composants ou déconnecter l’équipement sans s’être assuré que l’alimentation est coupée. • Ne pas connecter ou déconnecter des composants sans s’être assuré que l’alimentation est coupée. • Ce produit doit être installé dans une armoire. Tous les câbles connectés à l’appareil doivent rester dans l’armoire ou être protégés par une goulotte ou tout autre moyen. • L’ensemble du câblage doit être conforme à la réglementation en vigueur dans les pays où l’appareil est installé. Utilisez uniquement les câbles de communication suivants dans les environnements dangereux de Classe I, Division 2. Classification des environnements Câbles de communication Environnement dangereux de Classe I, Division 2 1761-CBL-AC00 série C ou ultérieure 1761-CBL-AM00 série C ou ultérieure 1761-CBL-AP00 série C ou ultérieure 1761-CBL-PM02 série C ou ultérieure 1761-CBL-HM02 série C ou ultérieure 2707-NC9 série C ou ultérieure 1763-NC01 série A ou ultérieure série 1747-CP3 UNSUPPORTED CONNECTION ATTENTION Do not connect the Comm0 port on the MicroLogix 1400 controller to another MicroLogix family controller such as MicroLogix 1000, MicroLogix 1200, or MicroLogix 1500 using a 1761-CBL-AM00 (8-pin mini-DIN to 8-pin mini-DIN) cable or equivalent. This type of connection will cause damage to the RS-232/485 communication port (Channel 0) of the MicroLogix 1400 and/or the controller itself. Communication pins used for RS-485 communications are alternately used for 24V power on the other MicroLogix controllers. Publication 1766-IN001C-EN-P - October 2009 MicroLogix 1400 Programmable Controllers 13 Mount the Controller General Considerations Most applications require installation in an industrial enclosure to reduce the effects of electrical interference and environmental exposure. Locate your controller as far as possible from power lines, load lines, and other sources of electrical noise such as hard-contact switches, relays, and ac motor drives. For more information on proper grounding guidelines, see the Industrial Automation Wiring and Grounding Guidelines, publication 1770-4.1. ATTENTION Mount the controller horizontally only. Vertical mounting is not supported due to thermal considerations. ATTENTION Be careful of metal chips when drilling mounting holes for your controller or other equipment within the enclosure or panel. Drilled fragments that fall into the controller could cause damage. Do not drill holes above a mounted controller if the protective debris strips have been removed. WARNING Do not place the MicroLogix 1400 Programmable Controller in direct sunlight. Prolonged exposure to direct sunlight could degrade the LCD display. WARNING The local programming terminal port is intended for temporary use only and must not be connected or disconnected unless the area is assured to be nonhazardous. Publication 1766-IN001C-EN-P - October 2009 14 MicroLogix 1400 Programmable Controllers Mounting Dimensions C 44516 A B 1766-L32BWA, 1766-L32AWA, 1766-L32BXB, 1766-L32BWAA, 1766-L32AWAA, 1766-L32BXBA Dimension Height A 90 mm (3.5 in.) B 180 mm (7.087 in.) C 87 mm (3.43 in.) Controller Spacing The controller mounts horizontally, with the expansion I/O extending to the right of the controller. Allow 50 mm (2 in.) of space on all but the right side for adequate ventilation, as shown below. Top ESC Side OK Bottom 44517 Publication 1766-IN001C-EN-P - October 2009 MicroLogix 1400 Programmable Controllers 15 DIN Rail Mounting The maximum extension of the latch is 14 mm (0.55 in.) in the open position. A flat-blade screwdriver is required for removal of the controller. The controller can be mounted to EN50022-35x7.5 or EN50022-35x15 DIN rails. DIN rail mounting dimensions are shown below. B A C 44518 Dimension Height A 90 mm (3.5 in.) B 27.5 mm (1.08 in.) C 27.5 mm (1.08 in.) Follow these steps to install your controller on the DIN rail. 1. Mount your DIN rail. Make sure that the placement of the controller on the DIN rail meets the recommended spacing requirements (see Controller Spacing on page 14 for more information). Refer to the mounting template inside the back cover of this document. 2. If it is open, close the DIN latch. 3. Hook the top slot over the DIN rail. 4. While pressing the controller down against the top of the rail, snap the bottom of the controller into position. 5. Leave the protective debris strip attached until you are finished wiring the controller and any other devices. Follow these steps to remove your controller from the DIN rail. 1. Place a flat-blade screwdriver in the DIN rail latch at the bottom of the controller. Publication 1766-IN001C-EN-P - October 2009 16 MicroLogix 1400 Programmable Controllers 2. Holding the controller, pry downward on the latch until the latch locks in the open position. 3. Repeat steps 1 and 2 for the second DIN rail latch. 4. Unhook the top of the DIN rail slot from the rail. ESC OK 44519 Open Closed 44520 Panel Mounting Mount to panel using #8 or M4 screws. Follow these steps to install your controller using mounting screws. 1. Remove the mounting template from inside the back cover of this document. 2. Secure the template to the mounting surface. Make sure your controller is spaced properly (see Controller Spacing on page 14 for more information). 3. Drill holes through the template. 4. Remove the mounting template. Mounting Template 5. Mount the controller. 6. Leave the protective debris strip in place until you are finished wiring the controller and any other devices 44521 Publication 1766-IN001C-EN-P - October 2009 ESC OK MicroLogix 1400 Programmable Controllers 17 Using the Battery The MicroLogix 1400 controller is equipped with a replaceable battery (catalog number 1747-BA). The Battery Low indicator on the LCD display of the controller shows the status of the replaceable battery. When the battery is low, the indicator is set (displayed as a solid rectangle). This means that either the battery wire connector is disconnected, or the battery may fail within 2 days if it is connected. The MicroLogix 1400 controller ships with the battery wire connector connected. IMPORTANT Ensure that the battery wire connector is inserted into the connector port if your application needs battery power. For example, when using a real-time clock (RTC). Replacing the battery when the controller is powered down will lose all user application memory. Replace the battery when the controller is powered on. Refer to the SLC 500 Lithium Battery Installation Instructions, publication , for more information on installation, handling, usage, storage, and 1747-IN515 disposal of the battery. When you connect or disconnect the battery an electrical arc can occur. This WARNING could cause an explosion in hazardous location installations. Be sure that the area is nonhazardous before proceeding. For Safety information on the handling of lithium batteries, including handling and disposal of leaking batteries, see Guidelines for Handling Lithium Batteries, . publication AG 5-4 Follow these steps to connect the replaceable battery. 1. Insert the replaceable battery wire connector into the controller’s battery connector. Publication 1766-IN001C-EN-P - October 2009 18 MicroLogix 1400 Programmable Controllers 2. Secure the battery connector wires so that it does not block the 1762 expansion bus connector as shown below. Battery compartment Battery 1762 I/O expansion bus connector Battery wire connector Battery connector Battery wires twisted pair 44522 Connect 1762 I/O Expansion Modules ATTENTION Remove power from the system before installing or removing expansion I/O or damage to the controller may result. Connect 1762 I/O after mounting the controller. 1. Remove the expansion port cover to install expansion I/O modules. 2. Plug the ribbon cable connector into the bus connector. Publication 1766-IN001C-EN-P - October 2009 MicroLogix 1400 Programmable Controllers 19 3. Replace the cover as shown below. 44523 The MicroLogix 1400 controller is designed to support up to any seven 1762 expansion I/O modules. For detailed information on using expansion I/O, refer to the installation instructions for your expansion module. Wire the Controller The shading in the following terminal block illustrations indicates which terminal groups are tied to which commons. Terminal Block Layouts WARNING When you connect or disconnect the Removable Terminal Block (RTB) with field side power applied, an electrical arc can occur. This could cause an explosion in hazardous location installations. Be sure that power is removed or the area is nonhazardous before proceeding. When used in a Class I, Division 2, hazardous location, this equipment must be WARNING mounted in a suitable enclosure. All wiring must be in accordance with Class I, Division 2 wiring methods of Article 501 of the National Electrical Code and/or in accordance with Section 18-1J2 of the Canadian Electrical Code, and in accordance with the authority having jurisdiction. Publication 1766-IN001C-EN-P - October 2009 20 MicroLogix 1400 Programmable Controllers 1766-L32BWA/L32BWAA Input Terminal Block IN0 IN2 COM 1 IN5 IN7 IN8 IN10 COM 3 IN13 IN15 IN17 IN19 IV0(+) IV2(+) COM 0 IN1 IN3 IN4 IN6 COM 2 IN9 IN11 IN12 IN14 IN16 IN18 COM IV1(+) IV3(+) ANA COM VAC VAC VAC OUT0 ANA L1 L2/N OUT1 OUT2 OUT3 OUT4 DC5 OUT7 OUT8 OUT10 OV1 DC0 DC1 DC2 DC3 DC4 OUT5 OUT6 DC6 OUT9 OUT11 OV0 VAC VAC VAC VAC VAC VAC Group 0 Group 1 Group 2 Group 3 Group 4 Group 5 Group 6 44524 Output Terminal Block 1766-L32AWA/L32AWAA Input Terminal Block IN0 IN2 COM 1 IN5 IN7 IN8 IN10 COM 3 IN13 IN15 IN17 IN19 IV0(+) IV2(+) COM 0 IN1 IN3 IN4 IN6 COM 2 IN9 IN11 IN12 IN14 IN16 IN18 COM IV1(+) IV3(+) ANA COM VAC VAC VAC L1 L2/N OUT0 OUT1 OUT2 OUT3 OUT4 DC5 OUT7 OUT8 OUT10 ANA OV1 DC0 DC1 DC2 DC3 DC4 OUT5 OUT6 DC6 OUT9 OUT11 OV0 VAC VAC VAC VAC VAC VAC Group 0 Group 1 Group 2 Group 3 Group 4 Group 5 Group 6 44525 Output Terminal Block Publication 1766-IN001C-EN-P - October 2009 MicroLogix 1400 Programmable Controllers 21 1766-L32BXB/L32BXBA Input Terminal Block IN0 IN2 COM 1 IN5 IN7 IN8 IN10 COM 3 IN13 IN15 IN17 IN19 IV0(+) IV2(+) COM 0 COM 2 IN1 IN3 IN4 IN6 IN9 IN11 IN12 IN14 IN16 IN18 COM IV1(+) IV3(+) ANA COM VDC VDC OUT0 ANA +24 NEUT OUT1 OUT2 OUT4 OUT6 COM 2 OUT8 OUT9 OUT10 OV1 DC0 DC1 VDC2 OUT3 OUT5 OUT7 DC3 DC4 DC5 OUT11 OV0 VAC VAC VAC VAC VAC Group 0 Group 1 Group 2 Group 3 Group 4 Group 5 44526 Wire Type Wire Size Solid wire Cu-90°C (194°F) 14…22 AWG Stranded wire Cu-90°C (194°F) 16…22 AWG Wiring torque = 0.791Nm (7 in-lb) rated. Output Terminal Grouping Outputs Controller Output Group Description Voltage Terminal Output Terminal 1766-L32BWA Group 0 Isolated relay output VAC/DC0 OUT 0 1766-L32BWAA Group 1 Isolated relay output VAC/DC1 OUT 1 Group 2 Isolated relay output VAC/DC2 OUT 2 Group 3 Isolated relay output VAC/DC3 OUT 3 Group 4 Isolated relay output VAC/DC4 OUT 4, OUT 5 Group 5 Isolated relay output VAC/DC5 OUT 6, OUT 7 Group 6 Isolated relay output VAC/DC6 OUT 8…11 Publication 1766-IN001C-EN-P - October 2009 22 MicroLogix 1400 Programmable Controllers Output Terminal Grouping Outputs Controller Output Group Description Voltage Terminal Output Terminal 1766-L32AWA Group 0 Isolated relay output VAC/DC0 OUT 0 1766-L32AWAA Group 1 Isolated relay output VAC/DC1 OUT 1 Group 2 Isolated relay output VAC/DC2 OUT 2 Group 3 Isolated relay output VAC/DC3 OUT 3 Group 4 Isolated relay output VAC/DC4 OUT 4, OUT 5 Group 5 Isolated relay output VAC/DC5 OUT 6, OUT 7 Group 6 Isolated relay output VAC/DC6 OUT 8…11 1766-L32BXB Group 0 Isolated relay output VAC/DC0 OUT 0 1766-L32BXBA Group 1 Isolated relay output VAC/DC1 OUT 1 Group 2 FET output VDC2/COM 2 OUT 2…7 Group 3 Isolated relay output VAC/DC3 OUT 8 Group 4 Isolated relay output VAC/DC4 OUT 9 Group 5 Isolated relay output VAC/DC5 OUT 10, OUT 11 WARNING If you connect or disconnect wiring while the field-side power is on, an electrical arc can occur. This could cause an explosion in hazardous location installations. Be sure that power is removed or the area is nonhazardous before proceeding WARNING The local programming terminal port is intended for temporary use only and must not be connected or disconnected unless the area is free of ignitable concentrations of flammable gases or vapors. Publication 1766-IN001C-EN-P - October 2009 MicroLogix 1400 Programmable Controllers 23 Wiring Recommendation When wiring without spade lugs, keep the finger-safe covers in place. Loosen the terminal screw and route the wires through the opening in the finger-safe cover. Tighten the terminal screw, making sure the pressure plate secures the wire. Finger-safe cover 44527 ATTENTION Be careful when stripping wires. Wire fragments that fall into the controller could cause damage. Once wiring is complete, be sure the controller is free of all metal fragments before removing the protective debris strip. Failure to remove the strip before operating can cause overheating. Publication 1766-IN001C-EN-P - October 2009 24 MicroLogix 1400 Programmable Controllers Spade Lug Recommendation The diameter of the terminal screw head is 5.5 mm (0.220 in.). The input and output terminals of the MicroLogix 1400 controller are designed for the following spade lugs. The terminals will accept a 6.35mm (0.25 in.) wide spade (standard for #6 screw for up to 14 AWG) or a 4 mm (metric #4) fork terminal. When using spade lugs, use a small, flat-blade screwdriver to pry the finger-safe cover from the terminal blocks, then loosen the terminal screw. Finger-safe cover 44528 If you wire the terminal block with the finger-safe cover removed, you may not TIP be able to put it back on the terminal block if the wires are in the way. Surge Suppression Inductive load devices such as motor starters and solenoids require the use of ATTENTION some type of surge suppression to protect the controller output. Switching inductive loads without surge suppression can significantly reduce the life of relay contacts or damage transistor outputs. By using suppression, you also reduce the effects of voltage transients caused by interrupting the current to that inductive device, and prevent electrical noise from radiating into system wiring. Refer to the MicroLogix 1400 Programmable Controller User Manual, publication 1766-UM001, for more information on surge suppression. Publication 1766-IN001C-EN-P - October 2009 MicroLogix 1400 Programmable Controllers 25 Grounding the Controller In solid-state control systems, grounding and wire routing helps limit the effects of noise due to electromagnetic interference (EMI). Run the ground connection from the ground screw of the controller to the ground bus prior to connecting any devices. Use AWG #14 wire. For AC-powered controllers, this connection must be made for safety purposes. You must also provide an acceptable grounding path for each device in your application. For more information on proper grounding guidelines, refer to the Industrial Automation Wiring . and Grounding Guidelines, publication 1770-4.1 Wiring Your Analog Channels Analog input circuits can monitor voltage signals and convert them to serial digital data as shown in the following illustration. Analog Input Sensor 2 (V) Voltage Sensor 0 (V) Voltage Input Terminal Block /7 I/8 I/10 COM 3 I/13 I/15 I/17 I/19 IV0(+) IV2(+) COM 2 I/9 I/11 I/12 I/14 I/16 I/18 COM IV1(+) IV3(+) ANA Sensor 1 (V) Voltage Sensor 3 (V) Voltage 44529 Publication 1766-IN001C-EN-P - October 2009 26 MicroLogix 1400 Programmable Controllers The controller does not provide loop power for analog inputs. Use a power supply that matches the transmitter specifications as shown. The analog output can support a voltage function as shown in the following illustration. Analog Output Voltage Load COM VAC O/3 O/4 DC5 O/7 O/8 O/10 ANA OV1 3 DC4 O/5 O/6 DC6 O/9 O/11 OV0 C VAC VAC Output Terminal Block Voltage Load 44680 Analog Input Transmitter Specifications 2-Wire Transmitter Transmitter Controller +- IV0(+), IV1(+), IV2(+) or IV3(+) + - COM ANA Transmitter 3-Wire Transmitter Supply Signal Controller GND Power + IV0(+), IV1(+), IV2(+) or IV3(+) Supply - COM ANA Transmitter 4-Wire Transmitter Controller Supply Signal IV0(+), IV1(+), IV2(+) or IV3(+) Power + + + Supply COM ANA - - - 44530 Publication 1766-IN001C-EN-P - October 2009 MicroLogix 1400 Programmable Controllers 27 Minimizing Electrical Noise on Analog Channels Inputs on analog channels employ digital high-frequency filters that significantly reduce the effects of electrical noise on input signals. However, because of the variety of applications and environments where analog controllers are installed and operated, it is impossible to ensure that all environmental noise will be removed by the input filters. Several specific steps can be taken to help reduce the effects of environmental noise on analog signals: • Install the MicroLogix 1400 system in a properly rated (NEMA) enclosure. Make sure that the MicroLogix 1400 system is properly grounded. • Use Belden cable #8761 for wiring the analog channels, making sure that the drain wire and foil shield are properly earth grounded, (see Grounding Your Analog Cable on page 27 for more information). • Route the Belden cable separately from any AC wiring. Additional noise immunity can be obtained by routing the cables in grounded conduit. Grounding Your Analog Cable Use shielded communication cable (Belden #8761). The Belden cable Foil Shield Black Wire has two signal wires (black and clear), one drain wire, and a foil Insulation shield. The drain wire and foil Drain Wire shield must be grounded at one end of the cable. Clear Wire 44531 IMPORTANT Do not ground the drain wire and foil shield at both ends of the cable. Publication 1766-IN001C-EN-P - October 2009 28 MicroLogix 1400 Programmable Controllers Specifications General Specifications Description 1766-L32AWA 1766-L32BWA 1766-L32BXB 1766-L32AWAA 1766-L32BWAA 1766-L32BXBA Dimensions 90 x 180 x 87 mm HxWxD 3.5 x 7.087 x 3.43 in. Shipping weight 0.9 kg (2.0 lbs) Number of I/O 24 inputs (20 digital and 4 analog) and 14 outputs (12 digital and 2 analog) Power supply voltage 100…240V AC (-15%, +10%) @ 47…63 Hz 24V DC (-15%, +10%) Class 2 SELV Heat dissipation Refer to the MicroLogix 1400 Programmable Controllers User Manual, Publication 1766-UM001. Power supply inrush 120V AC: 25 A for 8 ms 24V DC: current 240V AC: 40A for 4 ms 15 A for 20 ms Power consumption 100 VA 120 VA 50W 7.5W (with no 1762 expansion I/O) 24V DC sensor power none 24V DC @ 250 mA none 400 µF max. Input circuit type Digital: 120V AC Digital: 24V DC Digital: 24V DC sink/source sink/source (standard and high-speed) (standard and high-speed) Analog: 0…10V DC Analog: 0…10V DC Analog: 0…10V DC Output circuit type Relay Relay/FET 5 Relay life - Electrical 2 x 10 operations min (2.5 A, 250V AC / 30V DC) Enclosure type rating None (open-style) 2 Wire size 0.25… 2.5 mm (22…14 AWG) solid or stranded copper wire rated @ 90 °C (194 °F) or greater. (1) 2 - on signal ports Wiring category 2 - on power ports 3 - on communications ports Terminal screw torque 0.79 Nm (7.0 in-lb) rated Pilot duty rating R300, C300 Expansion bus Supports up to seven 1762 modules, up to a maximum of 5V, 1500 mA and 24 V, 1500 mA. North American temp code T3C (1) Use this Conductor Category information for planning conductor routing. Refer to Industrial Automation Wiring and Grounding Guidelines, publication 1770-4.1. Publication 1766-IN001C-EN-P - October 2009 MicroLogix 1400 Programmable Controllers 29 Specifications for Inputs Digital Inputs Description 1766-L32AWA 1766-L32BWA, 1766-L32BWAA, 1766-L32BXB, 1766-L32AWAA 1766-L32BXBA Inputs 0 through 11 Inputs 12 and higher (12 high-speed DC inputs) (8 standard DC inputs) On-state voltage 79…132 V AC 4.5…24V DC, Class 2 10…24V DC, Class 2 range (4.5…26.4V DC @ 60°C/140°F) (10…26.4V DC @ 60°C/140°F) (4.5…30V DC @ 30°C/86°F) (10…30V DC @ 30°C/86°F) Off-state voltage 0…20 V AC 0…1.5V DC 0…5V DC range Operating 47…63 Hz 0 Hz…100 kHz 0 Hz…1 kHz frequency (scan time dependent) On-state current min 5.0 mA @ 79 V AC 7.1 mA @ 4.5V DC 3.2 mA @ 10V DC nom 12 mA @ 120 V AC 9.9 mA @ 24V DC 5.3 mA @ 24V DC max 16.0 mA @ 132 V AC 10.5 mA @ 30V DC 5.5 mA @ 30V DC Off-state leakage 2.5 mA max. 0.2 mA max. 1.5 mA max. current Nominal 12 kΩ @ 50 Hz 2.4 kΩ 4.5 kΩ impedance 10 kΩ @ 60 Hz Inrush current 250 mA (max.) @ 120V AC Analog Inputs Description 1766-L32AWAA, -L32BWAA, -L32BXBA Voltage input range 0…10.0V DC - 1 LSB Type of data 12-bit unsigned integer Input coding (0…10.0V DC - 1 LSB) 0…4,095 Voltage input impedance >199 kΩ Input resolution 12 bit Non-linearity ±1.0% of full scale Overall accuracy ±1.0% of full scale -20…60 °C (-4…140 °F) Voltage input overvoltage protection 10.5 V DC Field wiring to logic isolation Non-isolated with internal logic Publication 1766-IN001C-EN-P - October 2009 30 MicroLogix 1400 Programmable Controllers Analog Outputs Description 1766-L32AWAA, -L32BWAA, -L32BXBA Number of inputs 2 single-ended Voltage output range 0…10 V DC - 1 LSB Type of data 12 bit unsigned integer Step response 2.5 ms @ 95% Load range Voltage output 1 KΩ Output resolution 12 bit Analog output setting time 3 ms (max.) Overall Accuracy -20…60 °C (-4…140 °F) ±1.0% of full scale Electrical isolation Non-isolated with internal logic Cable length 30 m (98 ft) shielded cable Relay and FET Outputs Description 1766-L32AWA, 1766-L32AWAA, 1766-L32BXB, 1766-L32BWA, 1766-L32BWAA 1766-L32BXBA Maximum controlled load 1440 VA 1080 VA Maximum Continuous Current: Current per channel and group common 2.5 A per channel 2.5 A per channel 8A max channel 8…11 common Current per controller at 150V max 28 A or total of per-point loads, whichever is less at 240V max 20 A or total of per-point loads, whichever is less Relay Outputs Description 1766-L32AWA, 1766-L32AWAA, 1766-L32BWA, 1766-L32BWAA, 1766-L32BXB, 1766-L32BXBA (1) Turn On Time/Turn Off Time 10 ms (maximum) Load current 10 mA (minimum) (1) Scan time dependent Publication 1766-IN001C-EN-P - October 2009 MicroLogix 1400 Programmable Controllers 31 Maximum Volts Amperes Amperes Volt-Amperes Continuous Make Break Make Break 240V AC 7.5 A 0.75 A 2.5 A 1800 VA 180 VA 120V AC 15.0 A 1.5 A 2.5 A 1800 VA 180 VA 250V DC 0.11 A 1.0 A 28 VA 125V DC 0.22 A 1.0 A 28 VA 1766-L32BXB, 1766-L32BXBA FET Output Maximum output current (temperature dependent): FET Current per Point FET Total Current 2.0 8.0 1.75 7.0 1.5A, 30°C (86°F) 1.5 6.0A , 30°C (86°F) 6.0 1.25 5.0 1.0 4.0 0.75A, 60°C (140°F) Valid Valid 0.75 3.0 3.0A , 60°C (140°F) Range Range 0.5 2.0 0.25 1.0 10°C 30°C 50°C 70°C 80°C 10°C 30°C 50°C 70°C 80°C (50°F) (86°F) (122°F) (158°F) (176°F) (50°F) (86°F) (122°F) (158°F) (176°F) Temperature 44532 Temperature 44533 (1) Description General Operation High Speed Operation (Output 2, 3 and 4 Only) Power supply voltage 24V DC (-15%, 10%) Class 2 On-state voltage drop: at max load current 1V DC Not Applicable at max surge current 2.5V DC Not Applicable Current rating per point max load See graphic above 100 mA min load 1.0 mA 20 mA max leakage 1.0 mA 1.0 mA Surge current per point: peak current 4.0 A Not Applicable max surge duration 10 ms Not Applicable max rate of repetition @ 30 °C (86 °F) once every second Not Applicable max rate of repetition @ 60 °C (140 °F) once every 2 seconds Not Applicable Publication 1766-IN001C-EN-P - October 2009 Current (Amps) Current (Amps) 32 MicroLogix 1400 Programmable Controllers (1) Description General Operation High Speed Operation (Output 2, 3 and 4 Only) Turn-On Time (maximum) 11 µs 28 ns Turn-Off Time (maximum) 89 µs2.3 µs (1) Output 2, 3 and 4 are designed to provide increased functionality over the other FET outputs. Output 2, 3 and 4 may be used like the other FET transistor outputs, but in addition, within a limited current range, they may be operated at a higher speed. Output 2, 3 and 4 also provide a pulse train output (PTO) or pulse width modulation output (PWM) function. Working Voltage Working Voltage for 1766-L32AWA, 1766-L32AWAA Description Recommendation Power supply input to Verified by one of the following dielectric tests: 1836V AC for 1 second or backplane isolation 2596V DC for 1 second 265V AC Working Voltage (IEC Class 2 reinforced insulation) Input group to backplane Verified by one of the following dielectric tests:1517V AC for 1 second or isolation 2145V DC for 1 second 132V AC Working Voltage (IEC Class 2 reinforced insulation) Input group to input group Verified by one of the following dielectric tests:1517V AC for 1 second or isolation 2145V DC for 1 second 132V AC Working Voltage (basic insulation) Output group to backplane Verified by one of the following dielectric tests: 1836V AC for 1 second or isolation 2596V DC for 1 second 265V AC Working Voltage (IEC Class 2 reinforced insulation) Output group to output Verified by one of the following dielectric tests: 1836V AC for 1 second or group isolation 2596V DC for 1second 265V AC Working Voltage (basic insulation), 150V AC Working Voltage (IEC Class 2 reinforced insulation) Publication 1766-IN001C-EN-P - October 2009 MicroLogix 1400 Programmable Controllers 33 Working Voltage for 1766-L32BWA, 1766-L32BWAA Description Recommendation Power supply input to Verified by one of the following dielectric tests:1836V AC for 1 second or backplane isolation 2596V DC for 1 second 265V AC Working Voltage (IEC Class 2 reinforced insulation) Input group to backplane Verified by one of the following dielectric tests: 1100V AC for 1 second or isolation and input group to 1697V DC for 1 second input group isolation 75V DC Working Voltage (IEC Class 2 reinforced insulation) Output group to backplane Verified by one of the following dielectric tests: 1836V AC for 1 second or Isolation 2596V DC for 1 second 265V AC Working Voltage (IEC Class 2 reinforced insulation). Output group to output Verified by one of the following dielectric tests: 1836V AC for 1 second or group isolation 2596V DC for 1 second 265V AC Working Voltage (basic insulation) 150V Working Voltage (IEC Class 2 reinforced insulation) Working Voltage for 1766-L16BXB, 1766-L16BXBA Description Recommendation Input group to backplane Verified by one of the following dielectric tests: 1100V AC for 1 second or isolation and input group to 1697V DC for 1 second input group isolation 75V DC Working Voltage (IEC Class 2 reinforced insulation) FET output group to Verified by one of the following dielectric tests: 1100V AC for 1 second or backplane isolation 1697V DC for 1 second 75V DC Working Voltage (IEC Class 2 reinforced insulation) Relay output group to Verified by one of the following dielectric tests: 1836V AC for 1 second or backplane isolation 2596V DC for 1 second 265V AC Working Voltage (IEC Class 2 reinforced insulation) Relay output group to relay Verified by one of the following dielectric tests: 1836V AC for 1 second or output group and FET output 2596V DC for 1 second group isolation 265V AC Working Voltage (basic insulation), 150V Working Voltage (IEC Class 2 reinforced insulation) Publication 1766-IN001C-EN-P - October 2009 34 MicroLogix 1400 Programmable Controllers Environmental Specifications Description 1766-L32AWA 1766-L32BWA 1766-L32BXB 1766-L32AWAA 1766-L32BWAA 1766-L32BXBA Temperature, operating IEC 60068-2-1 (Test Ad, Operating Cold), IEC 60068-2-2 (Test Bd, Operating Dry Heat), IEC 60068-2-14 (Test Nb, Operating Thermal Shock): -20… 60 °C (-4…140 °F) Temperature, storage IEC 60068-2-1 (Test Ab, Unpackaged Non-operating Cold), IEC 60068-2-2 (Test Bb, Unpackaged Non-operating Dry Heat), IEC 60068-2-14 (Test Na, Unpackaged Non-operating Thermal Shock): -40…85 °C (-40…185 °F) Relative humidity IEC 60068-2-30 (Test Db, Unpackaged Damp Heat): 5…95% non-condensing Vibration IEC 60068-2-6 (Test Fc, Operating): 3 g @ 10… 500 Hz Shock, operating IEC 60068-2-27 (Test Ea, Unpackaged Shock): 30 g Shock, nonoperating IEC 60068-2-27 (Test Ea, Unpackaged Shock): Panel mount - 50 g DIN mount - 40 g Emissions CISPR 11 Group 1, Class A ESD immunity IEC 61000-4-2: 4 kV contact discharges 8 kV air discharges Radiated RF immunity IEC 61000-4-3: 10V/m with 1 kHz sine-wave 80% AM from 80…1000 MHz 3 V/m with 1 kHz sine-wave 80% AM from 1.4…2.0 GHz 1 V/m with 1 kHz sine-wave 80% AM from 2.0…2.7 GHz EFT/B immunity IEC 61000-4-4: ±2 kV @ 5 kHz on power ports ±2 kV @ 5 kHz on signal ports ±1 kV @ 5 kHz on communications ports Publication 1766-IN001C-EN-P - October 2009 MicroLogix 1400 Programmable Controllers 35 Description 1766-L32AWA 1766-L32BWA 1766-L32BXB 1766-L32AWAA 1766-L32BWAA 1766-L32BXBA Surge transient IEC 61000-4-5: immunity ±1 kV line-line(DM) and ±2 kV line-earth(CM) on AC power ports ±1 kV line-line(DM) and ±2 kV line-earth(CM) on signal ports ±1 kV line-earth(CM) on communications ports Conducted RF immunity IEC 61000-4-6: 10V rms with 1 kHz sine-wave 80% AM from 150 kHz…80 MHz Voltage variation IEC 6100-4-11: 60% dip for 10 periods on AC supply ports 30% dips for 25 periods @ 0° and 180° on AC supply ports 100% dip for 250 periods @ 0° and 180° on AC supply ports 100% dip for 0.5 periods, arbitrary angle, on AC supply ports Certifications for 1766-L32AWA, 1766-L32AWAA, 1766-L32BWA, 1766-L32BWAA, 1766-L32BXB, 1766-L32BXBA Certification (when Value (1) product is marked) UL UL Listed for Class I, Division 2 Group A,B,C,D Hazardous Locations. See UL File E10314. c-UL UL Listed for Class I, Division 2 Group A,B,C,D Hazardous Locations, certified for Canada. See UL File E10314. CE European Union 2004/108/EC EMC Directive, compliant with: EN 61000-6-2; Industrial Immunity EN 61000-6-4; Industrial Emissions EN 61131-2; Programmable Controllers (Clause 8, Zone A & B) EN 61131-2; Programmable Controllers (Clause 11) C-Tick Australian Radiocommunications Act, compliant with: AS/NZS CISPR 11; Industrial Emissions (1) See the Product Certification link at http://www.ab.com for Declaration of Conformity, Certificates, and other certification details. Publication 1766-IN001C-EN-P - October 2009 36 MicroLogix 1400 Programmable Controllers Publication 1766-IN001C-EN-P - October 2009 180.0 mm 25.81 mm (7.087 in.) (1.016 in.) 165.8 mm (6.528 in.) 0.164 DIN rail center line. Expansion I/O Ligne médiane du rail DIN. Mittellinie der DIN-Schiene. Extension d'E/S Línea central del riel DIN. E/A - Linea centrale della guida DIN. Erweiterungsmodule linha de centro do trilho DIN. Espansione dei moduli I/O Expansión de E/S 100.06 mm (3.939 in.) Expansão de E/S 1766-L32AWA, 1766-L32AWAA 1766-L32BWA, 1766-L32BWAA 1766-L32BXB, 1766-L32BXBA INPUTS 0 1 2 3 4 5 6 7 8 9 10 111213 1415 16 17 1819 01 2345 6 78 9 10 11 OUTPUTS INPUTS 0 1 2 3 4 5 6 7 8 9 10 111213 1415 16 17 1819 01 2345 6 78 9 10 11 OUTPUTS L32AWA L32AWAA VAC VAC OUT OUT OUT OUT OUT VAC OUT OUT OUT NC NC L1 L2/N 0 1 2 3 4 DC5 7 8 10 VAC VAC 1766-L32AWA VAC VAC VAC VAC OUT OUT OUT OUT NC DC3 DC6 9 DC0 DC1 DC2 DC4 5 6 11 COM COM IN0 IN2 IN5 IN7 IN8 IN10 IN13 IN15 IN17 IN19 NC NC 1766-L32AWA 1 3 COM COM IN1 IN3 IN4 IN6 IN9 IN11 IN12 IN14 IN16 IN18 NC NC NC 0 2 VAC VAC OUT OUT OUT OUT OUT VAC OUT OUT OUT COM OV1 L1 L2/N 0 1 4 2 3 DC5 7 8 10 ANA VAC VAC VAC VAC VAC OUT 1766-L32AWAA VAC OUT OUT OUT OV0 DC3 DC6 DC0 DC1 DC2 6 9 11 DC4 5 COM COM IN0 IN2 IN5 IN7 IN8 IN10 IN13 IN15 IN17 IN19 IV0 IV2 1 3 1766-L32AWAA COM COM COM IN1 IN3 IN4 IN6 IN9 IN11 IN12 IN14 IN16 IN18 IV1 IV3 0 2 ANA L32AWAA L32AWA 953203-16 INPUTS 0 1 2 3 4 5 6 7 8 9 10 111213 1415 16 17 1819 01 2345 6 78 9 10 11 OUTPUTS INPUTS 0 1 2 3 4 5 6 7 8 9 10 111213 1415 16 17 1819 01 2345 6 78 9 10 11 OUTPUTS L32BWA L32BWAA VAC VAC OUT OUT OUT OUT OUT VAC OUT OUT OUT NC NC L1 L2/N 0 1 2 3 4 DC5 7 8 10 VAC VAC 1766-L32BWA VAC VAC VAC VAC OUT OUT OUT OUT NC DC3 DC6 9 DC0 DC1 DC2 DC4 5 6 11 COM COM IN0 IN2 IN5 IN7 IN8 IN10 IN13 IN15 IN17 IN19 NC NC 1766-L32BWA 1 3 COM COM IN1 IN3 IN4 IN6 IN9 IN11 IN12 IN14 IN16 IN18 NC NC NC 0 2 VAC VAC OUT OUT OUT OUT OUT VAC OUT OUT OUT COM OV1 L1 L2/N 0 1 2 3 4 7 8 10 DC5 ANA VAC VAC VAC VAC VAC OUT 1766-L32BWAA VAC OUT OUT OUT OV0 DC3 DC6 DC0 DC1 DC2 6 9 11 DC4 5 COM COM IN0 IN2 IN5 IN7 IN8 IN10 IN13 IN15 IN17 IN19 IV0 IV2 1 3 1766-L32BWAA COM COM COM IN1 IN3 IN4 IN6 IN9 IN11 IN12 IN14 IN16 IN18 IV1 IV3 0 2 ANA L32BWAA L32BWA 953203-16 INPUTS 0 1 2 3 4 5 6 7 8 9 10 111213 1415 16 17 1819 01 2345 6 78 9 10 11 OUTPUTS INPUTS 0 1 2 3 4 5 6 7 8 9 10 111213 1415 16 17 1819 01 2345 6 78 9 10 11 OUTPUTS L32BXBA L32BXB +24 VDC OUT OUT OUT OUT OUT COM OUT OUT OUT COM OV1 VDC NEUT 0 1 2 4 6 2 8 9 10 ANA OUT VAC 1766-L32BXBA VAC VAC VDC OUT OUT VAC VAC OUT OV0 DC0 DC1 2 3 DC4 DC5 5 7 DC3 11 COM COM IN0 IN2 IN5 IN7 IN8 IN10 IN13 IN15 IN17 IN19 IV0 IV2 1 3 1766-L32BXBA COM COM COM IN1 IN3 IN4 IN6 IN9 IN11 IN12 IN14 IN16 IN18 IV1 IV3 0 2 ANA +24 VDC OUT OUT OUT OUT OUT COM OUT OUT OUT NC NC VDC NEUT 0 1 6 2 4 2 8 9 10 OUT VAC 1766-L32BXB VAC VAC VDC OUT OUT VAC VAC OUT NC DC0 DC1 2 3 DC4 DC5 5 7 DC3 11 COM COM IN0 IN2 IN5 IN7 IN8 IN10 IN13 IN15 IN17 IN19 NC NC 1 3 1766-L32BXB COM COM IN1 IN3 IN4 IN6 IN9 IN11 IN12 IN14 IN16 IN18 NC NC NC 0 2 L32BXB L32BXBA 953203-16 Publication 1766-IN001C-EN-P - October 2009 Rockwell Automation Support Rockwell Automation provides technical information on the Web to assist you in using its products. At http://support.rockwellautomation.com, you can find technical manuals, a knowledge base of FAQs, technical and application notes, sample code and links to software service packs, and a MySupport feature that you can customize to make the best use of these tools. For an additional level of technical phone support for installation, configuration and troubleshooting, we offer TechConnect support programs. For more information, contact your local distributor or Rockwell Automation representative, or visit http://support.rockwellautomation.com. Installation Assistance If you experience a problem with a hardware module within the first 24 hours of installation, please review the information that's contained in this manual. You can also contact a special Customer Support number for initial help in getting your module up and running: United States 1.440.646.3434 Monday – Friday, 8am – 5pm EST Outside United States Please contact your local Rockwell Automation representative for any technical support issues. New Product Satisfaction Return Rockwell Automation tests all of its products to ensure that they are fully operational when shipped from the manufacturing facility. However, if your product is not functioning and needs to be returned, follow these procedures. United States Contact your distributor. You must provide a Customer Support case number (see phone number above to obtain one) to your distributor in order to complete the return process. Outside United States Please contact your local Rockwell Automation representative for return procedure. Allen-Bradley, Rockwell Automation, MicroLogix, and TechConnect are trademarks of Rockwell Automation, Inc. Trademarks not belonging to Rockwell Automation are property of their respective companies. Publication 1766-IN001C-EN-P - October 2009 PN 953203-13(04) Supersedes publication 1766-IN001B-EN-P - November 2008 Copyright © 2009 Rockwell Automation, Inc. All rights reserved. Printed in Singapore.
Frequently asked questions
What makes Elite.Parts unique?

What kind of warranty will the 1766-L32BWA have?

Which carriers does Elite.Parts work with?

Will Elite.Parts sell to me even though I live outside the USA?

I have a preferred payment method. Will Elite.Parts accept it?

Why buy from GID?
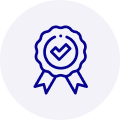
Quality
We are industry veterans who take pride in our work
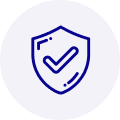
Protection
Avoid the dangers of risky trading in the gray market
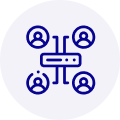
Access
Our network of suppliers is ready and at your disposal
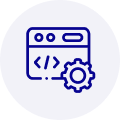
Savings
Maintain legacy systems to prevent costly downtime
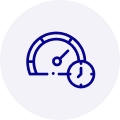
Speed
Time is of the essence, and we are respectful of yours
What they say about us
FANTASTIC RESOURCE
One of our top priorities is maintaining our business with precision, and we are constantly looking for affiliates that can help us achieve our goal. With the aid of GID Industrial, our obsolete product management has never been more efficient. They have been a great resource to our company, and have quickly become a go-to supplier on our list!
Bucher Emhart Glass
EXCELLENT SERVICE
With our strict fundamentals and high expectations, we were surprised when we came across GID Industrial and their competitive pricing. When we approached them with our issue, they were incredibly confident in being able to provide us with a seamless solution at the best price for us. GID Industrial quickly understood our needs and provided us with excellent service, as well as fully tested product to ensure what we received would be the right fit for our company.
Fuji
HARD TO FIND A BETTER PROVIDER
Our company provides services to aid in the manufacture of technological products, such as semiconductors and flat panel displays, and often searching for distributors of obsolete product we require can waste time and money. Finding GID Industrial proved to be a great asset to our company, with cost effective solutions and superior knowledge on all of their materials, it’d be hard to find a better provider of obsolete or hard to find products.
Applied Materials
CONSISTENTLY DELIVERS QUALITY SOLUTIONS
Over the years, the equipment used in our company becomes discontinued, but they’re still of great use to us and our customers. Once these products are no longer available through the manufacturer, finding a reliable, quick supplier is a necessity, and luckily for us, GID Industrial has provided the most trustworthy, quality solutions to our obsolete component needs.
Nidec Vamco
TERRIFIC RESOURCE
This company has been a terrific help to us (I work for Trican Well Service) in sourcing the Micron Ram Memory we needed for our Siemens computers. Great service! And great pricing! I know when the product is shipping and when it will arrive, all the way through the ordering process.
Trican Well Service
GO TO SOURCE
When I can't find an obsolete part, I first call GID and they'll come up with my parts every time. Great customer service and follow up as well. Scott emails me from time to time to touch base and see if we're having trouble finding something.....which is often with our 25 yr old equipment.
ConAgra Foods